国内外高炉炼铁系统的能耗分析
国内外高炉炼铁技术的发展现状和趋势

国内外高炉炼铁技术的发展现状和趋势高炉炼铁技术是金属冶炼工业发展的基础,是保证金属铁质量和产量的关键技术,也是社会经济发展的重要依托。
近年来,随着金属冶炼工业的快速发展,国内外高炉炼铁技术的发展也取得了显著的成就,为保证金属铁质量、提高产量、提高经济效益发挥了重要作用。
首先,国内外高炉炼铁技术取得了重大突破,进一步提高了金属铁质量。
随着科学技术的进步,添加剂和冶炼工艺的改进,使高炉炼铁工艺取得重大进展,不仅能够有效提高铁素体组成,同时也能够改善铁水的流动性,有利于铁块的全面成型。
此外,利用新型炉料和改进的热处理技术,可以有效降低铁水的含氧量,提高铁液的液相容量,从而获得更高品质的铁。
其次,国内外高炉炼铁技术的发展,还大大提高了铁的产量。
传统的高炉炼铁工艺存在着大量的炉料损失,限制了铁的产量。
随着国内外高炉炼铁技术的发展,炉料损失大大减少,产量得到提高。
通过对炼铁工艺及其参数进行优化调整,获得合理的炉料计算和分配,进而有效提高铁的产量。
此外,结合智能技术、自动化技术和智能控制技术,还可以实现远程监控和智能化管理,可以使高炉炼铁效率更高,产量更大。
最后,国内外高炉炼铁技术的发展,对提高经济效益具有重要意义。
国内外高炉炼铁技术的发展,不仅缩短了铁的生产周期,提高了产量,而且可以减少能耗消耗和废气排放,降低了生产成本,有利于提高企业的竞争力,实现更高的经济效益。
此外,国内外高炉炼铁技术的发展还可以改善炼铁终端的工作环境,为炼铁行业的发展创造更加良好的条件。
以上是国内外高炉炼铁技术的发展现状和趋势的概述,未来的发展趋势可以简单地总结为以下几点:继续提高高炉炼铁质量和产量,推广智能技术,进一步优化炼铁工艺,合理设计炉料配比,提高炼铁效率,减少能耗和污染,改善炼铁环境,提高经济效益,实现绿色经济发展。
未来,相信国内外高炉炼铁技术将取得更好的发展,为我们社会的经济发展提供更多的依托。
国内外高炉炼铁系统的能耗分析
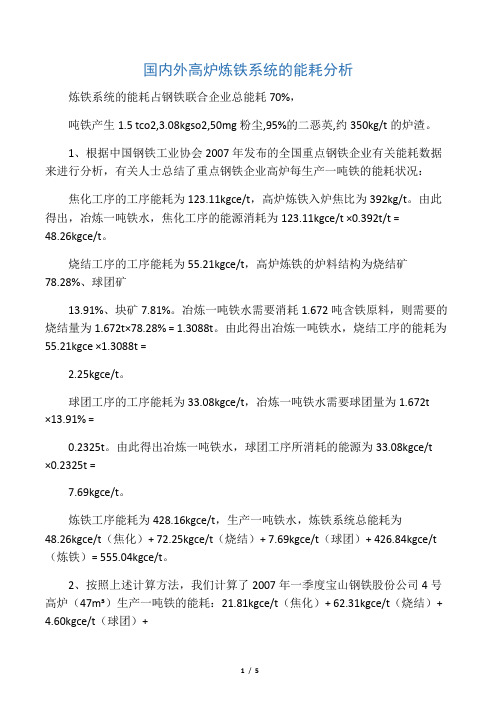
表12005年浦项制铁盒光阳厂炼铁有关能耗指标
项目工序能耗Kgce/t
烧结
66
57.4焦化
129.7
131.9炼铁
462.5
441.1入炉焦比Kgce/t炉料结构%
烧结比
76.4
70.9球团比
7.8
11.1块矿比
15.8
18.0xx
光阳494.7
492.1
表2全国重点钢铁企业能耗对比(单位Kgce/t)
高热值煤气回收利用率低是非高炉炼铁能耗高的“瓶颈”
2007年,我国重点钢铁企业的烧结、炼铁工序能耗与2006年相比进一步降低,炼铁生产部分工序能耗指标见表2。
2007年,全国重点钢铁企业高炉炼铁燃料比是529kg/t,浦项FINEX燃料比是740kg/t~750kg/t,澳大利亚Hismelt的煤耗在900kg/t(尚需1200℃风温和350kWh/t的电力)。这说明目前非高炉炼铁的能耗高于高炉冶炼生产工艺。
国内外高炉炼铁系统的能耗分析
炼铁系统的能耗占钢铁联合企业总能耗70%,
吨铁产生1.5 tco2,3.08kgso2,50mg粉尘,95%的二恶英,约350kg/t的炉渣。
1、根据中国钢铁工业协会2007年发布的全国重点钢铁企业有关能耗数据来进行分析,有关人士总结了重点钢铁企业高炉每生产一吨铁的能耗状况:
高炉冶炼节能分析

高炉冶炼节能分析摘要从高炉稳定顺行,提高喷煤比,搞好余热能的回收利用,减少煤气,氧气及高炉的鼓风放散率,开发高炉炉渣显热回收技术等几方面对武钢高炉冶炼节能进行了简要的论述。
关键词高炉冶炼节能降耗余热回收1 概述武钢高炉炼所消耗的能源约占全公司总能耗的40%~43%是公司最大的能耗大户,因此降低高炉能耗实质上是降低公司生产总能耗的主体部分,对于发展武钢这一特大型钢铁联合企业具有重要意义。
炼铁工序能耗组成中主要是燃料消耗,余下的是水、电、蒸汽、鼓风等动力消耗。
另外,消耗的辅助材料、备品备件在生产过程中都消耗了能耗,是载能体,属于社会能耗的范围。
燃料消耗占炼铁工序能耗的8 5 %左右,因而炼铁节能的重点是降低燃料消耗,提高高炉喷煤比,同时积极进行二次能源的回收利用,并对节约动力与辅助材料也要给足够的重视。
2 高炉稳定顺行是高炉冶炼节能的前提和基础高炉稳定顺行是高炉冶炼节能的前提和基础。
为确保高炉的稳定顺行,优良的原料、良好的外围条件以及先进的设备皆是提高高炉生产水平的物质基础。
而先进合理的操作制度和科学的生产组织与管理,则是高炉高产稳产的关键。
加强原燃料的管理。
改善原燃料质量,是提高精料水平的重要手段。
进一步推行槽下过筛,要求入炉矿料含粉率降低到 5%以下,炉料中小于5mm粉末减少l O%高炉产量可以提高8 %。
从而相应的降低了能耗;不断提高焦炭质量,降低并稳定焦炭水分,降低焦炭灰分,每降低焦炭灰分和提高矿石品位各1% ,高炉可降焦比约2% ,产量提高3%。
武钢对原有的操作制度进行不断地改进和提高,使高炉操作逐步适应了外部条件的变化,采甩合理的装料制度,控制合理气流分布,精心操作,高炉入炉焦比也正在一步步地降低,煤气利用率也得到了明显的改善。
煤气中的C O。
含量由1991年的16.3% 提高到1995年的18%,5年间提高了 1.7%,相当于降低焦比25kg/t左右,从而取得了较好的节能效果和较高的经济效益。
高炉炼铁的产能与运行效率分析

采用先进的控制技术,如自动控制系统、 专家系统等
加强设备维护和管理,减少设备故障和停 机时间
采用节能型工艺,如富氧炼铁、熔融还原 炼铁等
高炉炼铁的环保性能分析
环保性能评估指标
废气排放量:包括二氧化硫、氮氧化物、 颗粒物等
能源消耗量:包括煤炭、电力等
废水排放量:包括重金属、有机物等
环境影响评价:包括对周边环境的影响、 生态破坏程度等
能耗:能耗是衡量高炉炼铁运行效率 的另一个重要指标,包括燃料消耗、 电力消耗等。
设备利用率:设备利用率是指高炉炼 铁设备在运行时间占总运行时间的比 例,也是衡量运行效率的重要指标。
生产成本:生产成本包括原材料成 本、人工成本、设备折旧等,是衡 量高炉炼铁运行效率的综合指标。
影响运行效率的因素
原料质量:铁矿石、 焦炭等原料的质量 直接影响炼铁效率
备正常运行
产能优化案例
案例背景:某钢铁 公司高炉炼铁产能 不足,影响公司效 益
优化措施:采用先 进的生产工艺和技 术,提高设备利用 率
优化效果:产能提 高20%,成本降低 15%
启示:通过技术创 新和设备升级,可 以有效提高产能和 运行效率
高炉炼铁的运行效率分析
运行效率评估指标
产量:高炉炼铁的产量是衡量运行效 率的重要指标之一。
会影响产能
操作水平:工人的 操作技能和经验对
产能有重要影响
市场需求:市场需 求的变化也会影响
产能
提高产能的措施
优化原料配比:合理 选择铁矿石、焦炭等 原料,提高原料质量
采用先进的冶炼技术: 如富氧鼓风、喷煤等,
提高冶炼效率
改进炉型结构:采用 先进的高炉结构,提 高炉膛温度和热效率
加强设备维护和管理: 定期对高炉设备进行 检查和维护,确保设
炼铁系统能耗分析及节能

炼铁系统能耗分析及节能摘要:随着中国经济的快速增长以及工业化、城市化进程的加快,环境退化进一步加速,虽然我国采取了一系列措施加强环境保护。
但是,目前的环境保护在一定程度上还缺乏有效性和效率。
炼铁系统能耗和污染物排放占联合钢铁企业总量的70%以上,承担着钢铁工业节能减排的重任,在炼铁系统环节上应当积极创新和推广节能减排的新技术、新工艺,新设备、新的管理方法。
因此,我国在环保问题上还需要不断地完善管理体制和方法创新。
本文主要对炼铁系统能耗进行了一定的分析,并给出了相应的对策。
关键词:炼铁系统;能耗分析;节能;绿色城市引言钢铁行业在快速发展的同时,产能释放过快、铁矿石价格大幅上涨、钢材价格持续震荡、节能减排压力大等问题日益显现。
钢铁企业作为耗能大户,耗能量占全国耗能总量的12%左右。
据冶金部门统计,在产品生产成本中,主要的可控部分是能源消耗约占25-40%,能源价格上涨后更是如此。
国家已将节能减排定为国民经济发展的基本国策,国家环境保护部、工业和信息化部均已提出了对烧结工序的烟气脱硫的具体要求和时间表。
现在节能减排已经提上日程,志在实现高效、节能、环保、低碳生活。
1.背景概述1.1环境污染加剧的原因改革开放以来,我国由计划经济转人市场经济,以“解放生产力,发展生产力”为第一要务,各地传统工业相继崛起,采用高投人、高消费、高环境代价的工业发展模式开始。
尤其是东南沿海地区私人开办的工厂和各地集体集资的乡镇企业以“小、散、乱”为特点,技术水平落后,生产效率低下,为牟取最大收益不重视环境管理。
同时政府把重心放在了经济的高速发展上,针对环境保护问题没有强制性的管理制度和管理措施,环境管理处于失控和半失控状态。
环境持续恶化的趋势至今为止没有改变。
我国的经济发展正面临着历史上罕见的机遇,同时也经受着严峻的挑战。
1.2节能减排的意义随着全球变暖的严峻形势,环境治理已刻不容缓。
联合国环境规划署提出了“绿色经济”的口号,每年6月5日选择一个成员国举行“世界环境日”纪念活动,发表《环境现状的年度报告书》及表彰“全球500佳”,并根据当年的世界主要环境问题及环境热点,有针对性地制定每年的“世界环境日”主题。
高炉炼铁过程中的能源消耗与管理

高炉炼铁过程中的能源消耗与管理一、前言与背景高炉炼铁作为现代钢铁工业的基础,自19世纪末以来,一直是铁钢生产的主要方法。
高炉炼铁技术的出现和发展,对社会、经济和科技产生了深远影响。
它使得钢铁生产实现了规模化、低成本,极大地促进了工业革命和现代工业社会的形成。
同时,高炉炼铁过程也伴随着能源的消耗,据统计,能源消耗占到了高炉炼铁成本的很大一部分。
因此,研究和分析高炉炼铁过程中的能源消耗和管理,对于提高我国钢铁工业的能源利用效率,降低生产成本,提升竞争力具有重要意义。
二、高炉炼铁行业/领域的核心概念与分类高炉炼铁的概念高炉炼铁是一种利用焦炭和氧气反应产生的高温,将铁矿石还原成铁的过程。
其基本原理是在高温下,铁矿石中的氧化铁与一氧化碳反应,生成铁和二氧化碳。
高炉炼铁过程中,能源主要用于提供热能和动力能,其中热能主要用于维持高炉内的温度,动力能主要用于推动炉内物质的流动和完成各项机械作业。
高炉炼铁的分类高炉炼铁可以根据炉型、操作方式、燃料种类等不同标准进行分类。
按炉型可分为小型高炉、中型高炉和大型高炉;按操作方式可分为连续操作高炉和间歇操作高炉;按燃料种类可分为焦炭高炉和煤气高炉。
高炉炼铁的特征与应用领域高炉炼铁具有生产规模大、原料利用率高、产品品质好、能耗高等特征。
其应用领域广泛,几乎涵盖了所有钢铁生产领域。
高炉炼铁与其他领域的交叉与融合随着科技的发展,高炉炼铁技术与自动化、信息化、环保等领域日益交叉与融合。
例如,高炉炼铁过程的自动化控制,使得生产过程更加稳定,效率更高;信息化技术的应用,使得高炉炼铁过程的监测和控制更加精细;环保技术的应用,则有助于降低高炉炼铁过程中的污染排放。
三、关键技术或性能原理剖析高炉炼铁的关键技术高炉炼铁的关键技术主要包括燃料燃烧技术、还原反应技术、热量交换技术、原料处理技术等。
其中,燃料燃烧技术是高炉炼铁过程中能源消耗的主要部分,其效率的高低直接影响到高炉炼铁的能耗。
高炉炼铁的最新技术突破与创新成果近年来,高炉炼铁技术取得了许多重要突破和创新成果,如低焦比炼铁技术、高风温技术、煤气净化技术等。
炼铁工艺中的能源消耗与节能技术探索

炼铁工艺中的能源消耗与节能技术探索炼铁工艺是钢铁生产过程中至关重要的一环,同时也是一个高能耗行业。
随着能源资源的紧张和环境污染的加剧,如何减少炼铁工艺中的能源消耗并开展节能技术探索成为了当前的重要课题。
本文将围绕炼铁工艺的能源消耗分析和节能技术探索展开讨论。
一、炼铁工艺中的能源消耗分析在炼铁工艺中,能源消耗主要来自于两方面:一是燃料的消耗,二是电力的消耗。
燃料的消耗包括焦炭、煤炭、天然气等,而电力的消耗则主要用于激活炉料、通风、冷却以及一些辅助设备等方面。
1. 燃料消耗燃料在炼铁生产过程中主要用于冶炼过程中产生高温,以及提供还原、脱氧、燃烧等化学反应所需的热能。
传统的炼铁工艺,在高炉炼铁过程中主要使用焦炭作为还原剂,而焦炭的大量消耗不仅导致能源的浪费,还对环境造成了严重的污染。
因此,如何减少燃料的消耗,提高能源利用效率成为了迫切需求。
2. 电力消耗电力在炼铁工艺中主要用于提供动力和操作设备的供电,如驱动风机、循环水泵、输送带、起重机等。
随着炼铁工艺技术的发展,电力在工艺中的比重越来越大。
同时,炼铁工艺中一些辅助设备的能耗也逐渐增加。
因此,如何减少电力的消耗,实现节能减排成为了必然选择。
二、节能技术探索为了减少炼铁工艺中的能源消耗,许多节能技术不断被引入和应用。
下面将重点介绍一些有效的节能技术。
1. 高炉炼铁节能技术高炉炼铁是传统的炼铁工艺,其能源消耗较高。
为了提高高炉炼铁的能源利用效率,可以采取一系列节能技术措施,如提高燃烧温度、增加炉渣比例、改善燃料燃烧等。
此外,高炉炼铁还可以与其他冶金工艺相结合,进行能量互补,实现能源的综合利用。
2. 氧气炼铁技术氧气炼铁技术是近年来快速发展的一种新型炼铁工艺。
相比传统高炉炼铁,氧气炼铁工艺在能源消耗上具有明显的优势。
氧气炼铁可以减少焦炭的消耗量,增加反应温度,提高还原效果,从而在一定程度上实现了降低能源消耗、提高炼钢效率的目标。
3. 余热利用技术炼铁工艺中产生的大量余热往往未能得到合理利用,导致能源的浪费。
国内外吨钢综合能耗、可比能耗和工序能耗比较

内外吨钢综合能耗、可比能耗和工序能耗比较钢铁工业是国民经济重要的基础原材料工业,也是高耗能、高污染工业。
钢铁工业节约潜力巨大,为此,国外大型钢铁企业纷纷采取先进技术,开展节能降耗和综合利用,发展循环经济,不断优化工业的能耗指标和环保指标,以期达到能耗最少,环保最优。
与国外发达水平相比,我国钢铁工业差距明显。
2004年,我国大中型钢铁企业吨钢综合能耗为761千克标煤,比国际先进水平高81千克标煤;吨钢耗新水11. 15m3,比国际先进水平高 7. 3m:,;固体废物综合利用率乩比国际先进水平低个百分点。
在此,以我国大中型钢铁企业的相关指标与国外发达水平作对比,目的是寻找差距,迎头赶上。
下表列出了2003年我国重点企业主要工序能耗与国际先进水平(1999年)的比较,数据表明,我国转炉工序能耗与国外先进水平差值最大,炼铁工序差值最小。
2003年我国钢铁工业吨钢综合能耗为770kgce,吨钢可比能耗698kgce;2003年日本钢铁工业吨钢综合能耗为656kgce, 2000年国外主要产钢国家(英、日、法、徳)平均吨钢可比能耗为642kgce。
这两项指标分别比国外先进水平高出%和觥在国外,先进企业的高炉焦比已达到300kg/t以下,燃料比小于500kg/to我国重点钢铁企业的入炉焦比为426kg/t,部分其它企业为488kg/t,燃料比为560kg/t左右。
高炉工艺的能耗(标媒)比世界先进水平高出50〜 100kg/to同时,我国重点企业之间主要工序能耗的差距很大,指标先进的(如宝钢集团)已达到或超过国际先进水平, 而落后的能耗要高出先进值的1倍或数倍。
这说明,我国钢铁工业节能的潜力还是很大的。
新制订的《钢铁产业发展政策》明确提出,要建立循环型钢铁工厂,500万吨以上规模钢铁联合企业,要努力做到电力自供有余,实现外供。
2005年,全行业吨钢综合能耗降到吨标煤、吨钢可比能耗吨标煤、吨钢耗新水12吨以下;2010年分别降到吨标煤、吨标煤、8吨以下;2020年分别降到吨标煤、吨标煤、6吨以下。
炼钢高炉系统化能耗分析与优化
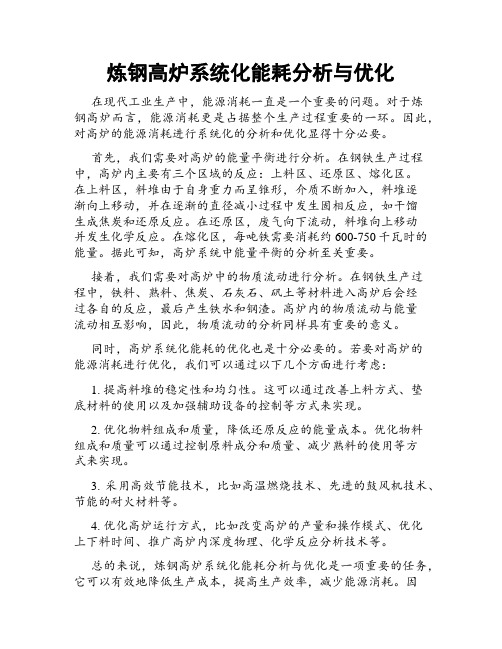
炼钢高炉系统化能耗分析与优化在现代工业生产中,能源消耗一直是一个重要的问题。
对于炼钢高炉而言,能源消耗更是占据整个生产过程重要的一环。
因此,对高炉的能源消耗进行系统化的分析和优化显得十分必要。
首先,我们需要对高炉的能量平衡进行分析。
在钢铁生产过程中,高炉内主要有三个区域的反应:上料区、还原区、熔化区。
在上料区,料堆由于自身重力而呈锥形,介质不断加入,料堆逐渐向上移动,并在逐渐的直径减小过程中发生固相反应,如干馏生成焦炭和还原反应。
在还原区,废气向下流动,料堆向上移动并发生化学反应。
在熔化区,每吨铁需要消耗约600-750千瓦时的能量。
据此可知,高炉系统中能量平衡的分析至关重要。
接着,我们需要对高炉中的物质流动进行分析。
在钢铁生产过程中,铁料、熟料、焦炭、石灰石、矾土等材料进入高炉后会经过各自的反应,最后产生铁水和钢渣。
高炉内的物质流动与能量流动相互影响,因此,物质流动的分析同样具有重要的意义。
同时,高炉系统化能耗的优化也是十分必要的。
若要对高炉的能源消耗进行优化,我们可以通过以下几个方面进行考虑:1. 提高料堆的稳定性和均匀性。
这可以通过改善上料方式、垫底材料的使用以及加强辅助设备的控制等方式来实现。
2. 优化物料组成和质量,降低还原反应的能量成本。
优化物料组成和质量可以通过控制原料成分和质量、减少熟料的使用等方式来实现。
3. 采用高效节能技术,比如高温燃烧技术、先进的鼓风机技术、节能的耐火材料等。
4. 优化高炉运行方式,比如改变高炉的产量和操作模式、优化上下料时间、推广高炉内深度物理、化学反应分析技术等。
总的来说,炼钢高炉系统化能耗分析与优化是一项重要的任务,它可以有效地降低生产成本,提高生产效率,减少能源消耗。
因此,我们需要对高炉的能量平衡和物质流动进行全面的分析,找出各种能源和物料的损失,并寻找优化措施。
只有通过不断地优化和改进,才能够将高炉系统的能源消耗最小化,从而使其更加环保、节能、经济和可持续。
高炉炼铁能耗与节能分析

高炉炼铁能耗与节能分析发布时间:2008-8-21 来源: 中国钢铁企业网本网专家顾问:王维兴李忠核心提示:据统计,2005年我国生产原煤21.9亿吨(居世界第一),消费21.4亿吨原煤;生产原油1.81亿吨(居世界第六),消费原油3.0亿吨;生产天然气500亿m3(居世界第十四),消费500亿m3;全年发电24747亿千瓦时(居世界第二)。
1.我国钢铁工业能耗现状据统计,2005年我国生产原煤21.9亿吨(居世界第一),消费21.4亿吨原煤;生产原油1.81亿吨(居世界第六),消费原油3.0亿吨;生产天然气500亿m3(居世界第十四),消费500亿m3;全年发电24747亿千瓦时(居世界第二)。
2005年我国能源消费结构是:煤炭为68.7%,油气为24%,水电+核电为7.3%。
2004年我国钢铁工业能源消耗占全国能源总消费量的15.18%,其能源消费结构是:煤炭69.9%,石油类3.2%,天然气0.5%,电力26.4%。
2.钢铁工业节能情况按不变价格计算,2005年我国万元GDP能耗比1980年下降64%。
改革开放以来,累积节约和少用超过10亿吨标准煤,以能源消费翻一番支持了GDP值翻两番。
1980~2005年,我国大中型钢铁企业吨钢可比能耗从1285Kgce/t降到714Kgce/t,节约571Kgce/t,降低了44.43%。
这说明,我国钢铁工业的节能步伐是与我国经济发展中的节能力度是同步进行,也说明了钢铁工业节能工作取得巨大成绩。
据统计2006年前三季度,全国产钢3.08亿吨,比上年度同期增长18.49%,但全国重点大中型钢铁企业总能耗为14535万吨标煤,比上年度降低6.8%。
这说明,我国钢铁工业节能工作还在深化发展。
2000年,工业发达国家吨钢可比能耗平均值在642Kgce/t。
2005年,我国重点大中型钢铁企业吨钢可比能耗值为714Kgce/t。
经对比分析可看出,我国钢铁工业的能耗水平与工业发达国家相比,尚高出11.2%。
高炉与非高炉炼铁生产能耗分析

高炉与非高炉炼铁生产能耗分析王维兴(中国金属学会北京 100711)2008年全世界高炉生铁产量为94364.7万吨,直接还原铁产量为5579.5万吨, 直接还原铁产量占全世界生铁产量的5.58%.说明目前生铁生产仍是以高炉流程为主.近年来,高炉炼铁科学技术得到不断发展和完善,使高炉炼铁技术经济指标不断进步.2009年前五个月全国重点钢铁企业高炉燃料比为518kg/t,入炉焦比为374 kg/t,喷煤比为144 kg/t,热风温度为1158度, 入炉矿品位为57.57%,熟料比为91.34%,利用系数为2.599t/m3.d, 高炉炼铁工序能耗为413.30kgce/t.创造出历史最好水平.近年来,我国炼铁系统能耗不断下降,详见表1.表1. 全国重点钢铁企业炼铁系统能耗单位:kgce/t太钢高炉有四座(4350,1800,1650,380M3). 2009年前五个月全厂高炉燃料比为478kg/t,入炉焦比为301 kg/t,喷煤比为186 kg/t,热风温度为1218度, 入炉矿品位为59.97%,熟料比为93.94%,利用系数为2.489t/m3.d, 高炉炼铁工序能耗为356.92 kgce/t.这说我国高炉炼铁技术水平已达到国际先进水平,充分显示出高炉炼铁工艺的先进性.据国际钢铁协会统计,2008年全世界直接还原铁产量为6850万吨,其中气基产量为5090万吨,占总产量的74.3%,(其中:Midrex为3080万吨,HyI为1760万吨,其他为110万吨),煤基产量为1760万吨,占总产量的25.7%.增长速度最快的是印度(2015万吨),伊朗(739万吨),委内瑞拉(714万吨),墨西哥(594万吨),阿根廷(461万吨),沙特(453万吨)等国. 全世界直接还原铁产量的增长,一方面是国际钢铁市场需求增长的拉动,另一方面是直接还原铁生产工艺的技术进步也发挥了作用.一. 高炉炼铁系统的能耗分析1.2009年前五个月全国重点钢铁企业高炉炼铁系统的能耗分析焦化工序:焦化工序能耗为115.37kgce/t,焦比为374kg/t.冶炼1吨生铁消耗的能耗为115.37Χ0.374=43.148 kgce/t.烧结工序:烧结工序能耗为55.27kgce/t, 冶炼1吨生铁消耗的烧结为1256.025 kg/t(冶炼1吨生铁矿耗按1674.70 kg/t,炉料结构中烧结矿配比为75%).冶炼1吨生铁消耗的烧结工序能耗为55.27x1.256=69.42 kgce/t.球团工序:球团工序能耗为31.31kgce/t, 冶炼1吨生铁消耗的球团为418.67 kg/t(冶炼1吨生铁矿耗按1674.70 kg/t,炉料结构中球团矿配比为25%)冶炼1吨生铁消耗的烧结工序能耗为31.31Χ0.41867=13.108 kgce/t.炼铁工序能耗为413.30kgce/t.冶炼1吨生铁消耗炼铁系统的能耗为:43.148kgce/t+69.42 kgce/t+13.108 kgce/t+413.30kgce/t=538.976kgce/t.结论:按2009年前五个月全国重点钢铁各工序能耗值进行计算得出冶炼1吨生铁消耗炼铁系统的能耗为538.976 kgce/t.2.2009年前五个月太钢炼铁系统的能耗计算焦化工序:烧结焦化工序能耗为63.42kgce/t,焦比为301kg/t.冶炼1吨生铁消耗的能耗为63.42Χ0.301=19.089kgce/t.烧结工序:烧结工序能耗为48.07kgce/t, 冶炼1吨生铁消耗的烧结为1256.025 kg/t(冶炼1吨生铁矿耗按1674.70 kg/t,炉料结构中烧结矿配比为75%).冶炼1吨生铁消耗的烧结工序能耗为48.07x1.256=60.375 kgce/t.球团工序:球团工序能耗为316.90kgce/t, 冶炼1吨生铁消耗的球团为418.67 kg/t(冶炼1吨生铁矿耗按1674.70 kg/t,炉料结构中球团矿配比为25%)冶炼1吨生铁消耗的烧结工序能耗为16.90Χ0.41867=7.075kgce/t.炼铁工序能耗为356.92kgce/t.冶炼1吨生铁消耗炼铁系统的能耗为:19.089kgce/t+60.375kgce/t+7.075 kgce/t+356.92kgce/t=443.459kgce/t.结论: 按2009年前五个月太原钢铁公司各工序能耗值进行计算得出冶炼1吨生铁消耗炼铁系统的能耗为443.459 kgce/t.3. 国外一些先进的钢铁企业高炉炼铁系统的能耗据了解,国外一些先进的钢铁企业采用高炉炼铁的能耗指标也在不断进步。
炼铁系统能耗分析及节能
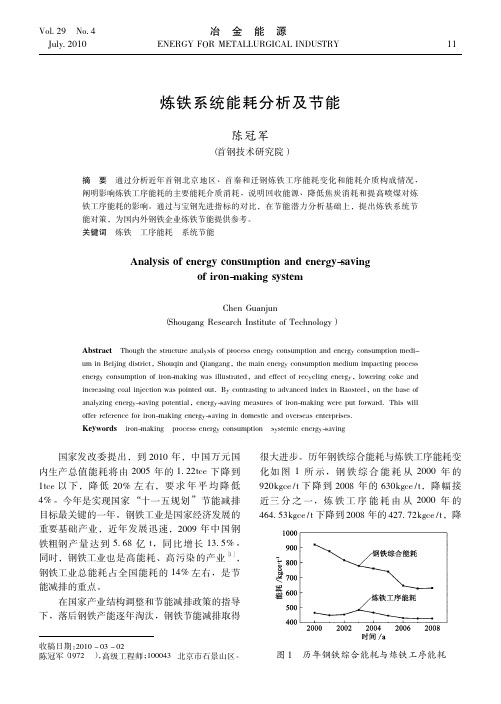
Chen Guanjun ( Shougang Research Institute of Technology)
Abstract Though the structure analysis of process energy consumption and energy consumption medium in Beijing district,Shouqin and Qiangang,the main energy consumption medium impacting process energy consumption of iron-making was illustrated,and effect of recycling energy,lowering coke and increasing coal injection was pointed out. By contrasting to advanced index in Baosteel,on the base of analyzing energy-saving potential,energy-saving measures of iron-making were put forward. This will offer reference for iron-making energy-saving in domestic and overseas enterprises. Keywords iron-making process energy consumption systemic energy-saving
国内外高炉炼铁系统的能耗分析

国内外高炉炼铁系统的能耗分析炼铁系统的能耗占钢铁联合企业总能耗70%,吨铁产生1.5 tco2,3.08kgso2,50mg粉尘,95%的二恶英约350kg/t的炉渣。
1、根据中国钢铁工业协会2007年发布的全国重点钢铁企业有关能耗数据来进行分析,有关人士总结了重点钢铁企业高炉每生产一吨铁的能耗状况:焦化工序的工序能耗为123.11kgce/t,高炉炼铁入炉焦比为392kg/t。
由此得出,冶炼一吨铁水,焦化工序的能源消耗为123.11kgce/t x 0.392t/t =48.26kgce/t。
烧结工序的工序能耗为55.21kgce/t,高炉炼铁的炉料结构为烧结矿78.28%、球团矿13.91%、块矿7.81%。
冶炼一吨铁水需要消耗1.672吨含铁原料,则需要的烧结量为1.672t x 78.28% = 1.3088由此得出冶炼一吨铁水,烧结工序的能耗为55.21kgce x 1.3088t =2.25kgce/t。
球团工序的工序能耗为33.08kgce/t,冶炼一吨铁水需要球团量为 1.672tx 13.91% =0.2325t。
由此得出冶炼一吨铁水,球团工序所消耗的能源为33.08kgce/tx 0.2325t =7.69kgce/t。
炼铁工序能耗为428.16kgce/t,生产一吨铁水,炼铁系统总能耗为48.26kgce/t (焦化)+ 72.25kgce/t (烧结)+ 7.69kgce/t (球团)+ 426.84kgce/t (炼铁)= 555.04kgce/t。
2、按照上述计算方法,我们计算了2007年一季度宝山钢铁股份公司4 号高炉(47m3)生产一吨铁的能耗:21.81kgce/t (焦化)+ 62.31kgce/t (烧结)+4.60kgce/t (球团)+381.22kgce/t (炼铁)二469.94kgce/t据了解,国外一些先进的钢铁企业采用高炉炼铁的能耗指标也在不断进步。
国内外高炉炼铁系统的能耗分析

国内外高炉炼铁系统的能耗分析炼铁系统的能耗占钢铁联合企业总能耗70%,吨铁产生1.5 tco2, 3.08kgso2, 50mg粉尘, 95%的二恶英, 约350kg/t的炉渣。
1、根据中国钢铁工业协会2007年发布的全国重点钢铁企业有关能耗数据来进行分析,有关人士总结了重点钢铁企业高炉每生产一吨铁的能耗状况:焦化工序的工序能耗为123.11kgce/t,高炉炼铁入炉焦比为392kg/t。
由此得出,冶炼一吨铁水,焦化工序的能源消耗为123.11kgce/t × 0.392t/t = 48.26kgce/t。
烧结工序的工序能耗为55.21kgce/t,高炉炼铁的炉料结构为烧结矿78.28%、球团矿13.91%、块矿7.81%。
冶炼一吨铁水需要消耗1.672吨含铁原料,则需要的烧结量为1.672t × 78.28% = 1.3088t。
由此得出冶炼一吨铁水,烧结工序的能耗为55.21kgce × 1.3088t =2.25 kgce/t。
球团工序的工序能耗为33.08kgce/t,冶炼一吨铁水需要球团量为1.672t × 13.91% = 0.2325t。
由此得出冶炼一吨铁水,球团工序所消耗的能源为33.08kgce/t ×0.2325t =7.69kgce/t。
炼铁工序能耗为428.16kgce/t,生产一吨铁水,炼铁系统总能耗为48.26kgce/t (焦化)+ 72.25kgce/t(烧结)+ 7.69kgce/t(球团)+ 426.84kgce/t(炼铁) = 555.04kgce/t。
2、按照上述计算方法,我们计算了2007年一季度宝山钢铁股份公司4号高炉(4747m³)生产一吨铁的能耗:21.81kgce/t(焦化)+ 62.31kgce/t(烧结)+4.60kgce/t(球团)+ 381.22kgce/t(炼铁) = 469.94kgce/t。
钢铁冶炼中的能量消耗与节能技术

钢铁冶炼中的能量消耗与节能技术钢铁冶炼作为国家重要的基础产业之一,对于国家经济发展和民生福祉都具有非常重要的意义。
然而,钢铁冶炼过程中的大量能源消耗和环境污染一直是困扰人们的难题。
因此,研究如何减少能源消耗和提高节能技术水平已经成为当前钢铁冶炼行业的重要课题。
1. 钢铁冶炼中的能量消耗1.1 能源消耗的情况钢铁冶炼过程中主要利用高炉、转炉等多种设备制造钢铁,并且这些设备需要大量的能源支持。
据统计,钢铁产业在国内工业中能源消耗量占到50%以上。
其中,焦炉煤气是钢铁行业的主要热源,其次是天然气、重油、燃料油等。
1.2 能源消耗的问题钢铁冶炼过程中的能源消耗主要存在以下问题:1.2.1 能源损失严重钢铁冶炼过程中需要大量高温高压环境,因此大量的热能被浪费。
这些能量损失导致环境污染和能源的极度浪费。
1.2.2 能源发展的制约钢铁冶炼行业对能源的需求很大,它对国家总能源消耗和消耗结构都有很大的影响。
钢铁冶炼行业需要大量的能源支持,而国内能源产能有限,这对于行业的可持续发展提出了极大的挑战。
1.2.3 能源价格的上涨钢铁冶炼行业对能源的需求指数级上升,而能源价格也在飞涨。
能源价格的不断上涨,使得钢铁行业面临着巨大的压力。
如何降低成本、提高效率已成为钢铁行业需要解决的问题。
2. 节能技术措施为了减少能源消耗并提高钢铁行业的科技含量,我国钢铁行业开始在实践中大力推广各种节能技术措施。
下面对一些重要的节能技术进行介绍。
2.1 废热回收技术废热回收技术是一种基于能源回收原理的技术,其主要目的是将钢铁生产中生产的大量废热回收利用。
该技术可以将热能转化为电能或再利用,从而减少钢铁冶炼原材料的能源消耗。
2.2 高温烟气余热回收技术钢铁冶炼过程中,高炉烟气流出温度非常高,如果能够将烟气中有效能量进行收集和利用,将会带来非常可观的节能效果。
高温烟气余热回收技术可以将钢铁冶炼的生产中排放的高温烟气进行回收与再利用,从而实现钢铁冶炼过程能源的有效回收和节能减排。
炼铁经济技术指标总结

炼铁经济技术指标总结炼铁经济技术指标总结炼铁是钢铁行业的基础,其经济技术指标是衡量炼铁工艺质量和效率的重要指标,对于提高钢铁企业的生产效益具有非常重要的作用。
本文将从能耗、生产率、环保等几个方面总结炼铁经济技术指标。
能耗指标能耗指标是衡量钢铁企业在炼铁过程中能源消耗情况的指标,是企业科学合理利用能源,降低生产成本的重要手段。
首先是煤耗指标。
在高炉炼铁过程中,需大量燃煤来产生高温热能以熔化铁矿石并还原出铁元素。
根据统计数据,我国目前炼铁企业的平均煤耗约在450-500千克/吨左右,而国外一些先进的炼铁企业则可以控制在300-350千克/吨以下。
因此,我国炼铁企业需要进一步加大节能降耗力度,提高能源利用效率。
除了煤耗指标,还存在其他的能耗指标。
比如焦耗指标、电耗指标等。
优化这些指标,是提高钢铁企业炼铁效益的重要方法。
生产率指标生产率指标是衡量钢铁企业炼铁技术综合水平的重要指标。
通过提高生产率指标,钢铁企业可以降低生产成本,提高盈利空间。
生产率指标主要包括炉渣产量、高炉利用系数等。
其中,高炉利用系数是最为重要的生产率指标之一。
目前,我国炼铁企业的高炉利用系数已经有所提高,但仍有提高的空间。
提高高炉利用系数,需要从多个方面入手,包括加大高炉的生产规模、优化物料配比、提高高炉风温水平等。
环保指标环保指标是衡量钢铁企业在炼铁过程中对环境污染情况的指标。
自治国家以来,我国钢铁企业在环保方面一直在努力改进,包括炼铁技术方面的改进。
目前,钢铁企业需要遵守的环保指标主要有高炉烟尘排放、SO2排放、NOX排放等。
通过采用高效减排技术,钢铁企业可以减少环境污染,提升企业形象,获得社会和政府的认可。
以上是炼铁经济技术指标的三个方面的总结。
通过优化这些指标,可以提高钢铁企业的生产效益,降低生产成本,同时保证环境卫生。
王维兴:高炉炼铁与非高炉炼铁的能耗比较
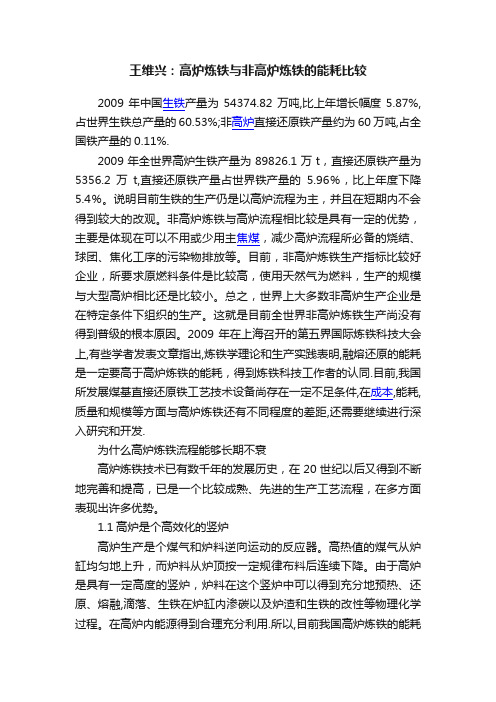
王维兴:高炉炼铁与非高炉炼铁的能耗比较2009年中国生铁产量为54374.82万吨,比上年增长幅度5.87%,占世界生铁总产量的60.53%;非高炉直接还原铁产量约为60万吨,占全国铁产量的0.11%.2009年全世界高炉生铁产量为89826.1万t,直接还原铁产量为5356.2万t,直接还原铁产量占世界铁产量的5.96%,比上年度下降5.4%。
说明目前生铁的生产仍是以高炉流程为主,并且在短期内不会得到较大的改观。
非高炉炼铁与高炉流程相比较是具有一定的优势,主要是体现在可以不用或少用主焦煤,减少高炉流程所必备的烧结、球团、焦化工序的污染物排放等。
目前,非高炉炼铁生产指标比较好企业,所要求原燃料条件是比较高,使用天然气为燃料,生产的规模与大型高炉相比还是比较小。
总之,世界上大多数非高炉生产企业是在特定条件下组织的生产。
这就是目前全世界非高炉炼铁生产尚没有得到普级的根本原因。
2009年在上海召开的第五界国际炼铁科技大会上,有些学者发表文章指出,炼铁学理论和生产实践表明,融熔还原的能耗是一定要高于高炉炼铁的能耗,得到炼铁科技工作者的认同.目前,我国所发展煤基直接还原铁工艺技术设备尚存在一定不足条件,在成本,能耗,质量和规模等方面与高炉炼铁还有不同程度的差距,还需要继续进行深入研究和开发.为什么高炉炼铁流程能够长期不衰高炉炼铁技术已有数千年的发展历史,在20世纪以后又得到不断地完善和提高,已是一个比较成熟、先进的生产工艺流程,在多方面表现出许多优势。
1.1高炉是个高效化的竖炉高炉生产是个煤气和炉料逆向运动的反应器。
高热值的煤气从炉缸均匀地上升,而炉料从炉顶按一定规律布料后连续下降。
由于高炉是具有一定高度的竖炉,炉料在这个竖炉中可以得到充分地预热、还原、熔融,滴落、生铁在炉缸内渗碳以及炉渣和生铁的改性等物理化学过程。
在高炉内能源得到合理充分利用.所以,目前我国高炉炼铁的能耗可以在410kgce/t左右.在转底炉中被还原的球,大多数是中上层受到煤气加热和还原,而在底部接触煤气就较弱。
炼铁系统能耗分析及节能

国家发改委提出,到 2 1 ,中国万元 国 00年 内生产总值 能耗将 由 20 05年的 12 t .2c e下降到 1 e以下 ,降 低 2 % 左 右,要 求 年 平 均 降 低 t e 0 4 %。今年是实现国家 “ 十一 五规划 ”节能减排 目标最 关 键 的一年 。钢 铁工 业是 国家 经济发展 的 重 要基 础 产 业 ,近 年 发 展 迅 速 ,20 0 9年 中 国 钢
o r n- a ng s se f io m ki y t m
C e unu hnG ajn
( hu a gR sa hIstt o eh o g ) S o gn eer tu f c nl y c ni e T o
Ab t a t T o g e src u e a a y i o rc s n r yc n u t n a d e e g o s mp o d ・ s r c h u h t t tr n lss f o e se e g o s mpi n n r c n u t n me i h u p o y i
收稿 日期 :0 0— 3 2 2 1 0 —0
陈冠军( 7 )高级工程师; 0 3北京市石 12 , 9 10 04 景山区。
图 1 历年钢铁综合能耗 与炼铁工序能耗
冶
1 2
金
能
源
Vo. 9 No 4 12 .
ENERGY FOR MET ALL URGI CAL I NDUS TRY
钢铁冶炼中的过程能耗分析与优化
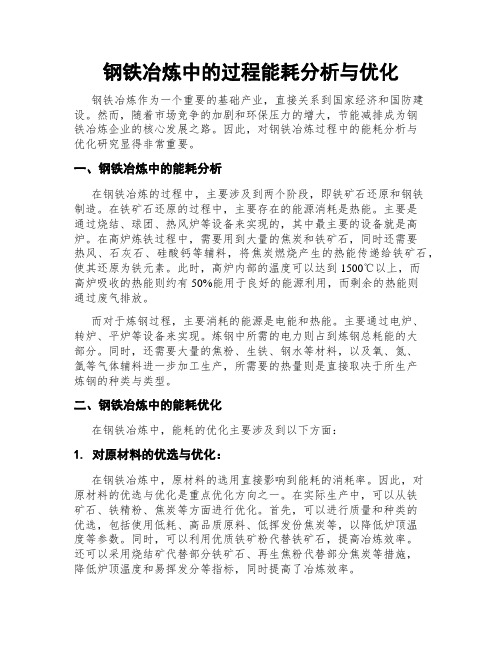
钢铁冶炼中的过程能耗分析与优化钢铁冶炼作为一个重要的基础产业,直接关系到国家经济和国防建设。
然而,随着市场竞争的加剧和环保压力的增大,节能减排成为钢铁冶炼企业的核心发展之路。
因此,对钢铁冶炼过程中的能耗分析与优化研究显得非常重要。
一、钢铁冶炼中的能耗分析在钢铁冶炼的过程中,主要涉及到两个阶段,即铁矿石还原和钢铁制造。
在铁矿石还原的过程中,主要存在的能源消耗是热能。
主要是通过烧结、球团、热风炉等设备来实现的,其中最主要的设备就是高炉。
在高炉炼铁过程中,需要用到大量的焦炭和铁矿石,同时还需要热风、石灰石、硅酸钙等辅料,将焦炭燃烧产生的热能传递给铁矿石,使其还原为铁元素。
此时,高炉内部的温度可以达到1500℃以上,而高炉吸收的热能则约有50%能用于良好的能源利用,而剩余的热能则通过废气排放。
而对于炼钢过程,主要消耗的能源是电能和热能。
主要通过电炉、转炉、平炉等设备来实现。
炼钢中所需的电力则占到炼钢总耗能的大部分。
同时,还需要大量的焦粉、生铁、钢水等材料,以及氧、氮、氩等气体辅料进一步加工生产,所需要的热量则是直接取决于所生产炼钢的种类与类型。
二、钢铁冶炼中的能耗优化在钢铁冶炼中,能耗的优化主要涉及到以下方面:1. 对原材料的优选与优化:在钢铁冶炼中,原材料的选用直接影响到能耗的消耗率。
因此,对原材料的优选与优化是重点优化方向之一。
在实际生产中,可以从铁矿石、铁精粉、焦炭等方面进行优化。
首先,可以进行质量和种类的优选,包括使用低耗、高品质原料、低挥发份焦炭等,以降低炉顶温度等参数。
同时,可以利用优质铁矿粉代替铁矿石,提高冶炼效率。
还可以采用烧结矿代替部分铁矿石、再生焦粉代替部分焦炭等措施,降低炉顶温度和易挥发分等指标,同时提高了冶炼效率。
2. 对技术的优化:钢铁冶炼的技术不断更新,为实现时间、能量的节省和质量的提高提供了途径。
技术创新可以使炉料利用率提高,残杂元素含量降低,生产能量消耗降低,并且生产质量大幅提高。
炼铁生产过程中的耗能分析与节能措施

炼铁生产过程中的耗能分析与节能措施铁是不可缺少的资源之一,而炼铁生产则是一项高能耗、高排放的产业。
在我国经济建设中占据着重要的地位。
但是在制造过程中的能耗问题是制约工业发展和环境保护的重要问题之一。
因此,对炼铁生产过程中的能耗问题进行分析和研究,以实现节能降耗,具有重要的实用价值。
1. 炼铁生产过程中的能耗问题在炼铁生产过程中,最主要的能耗来自于高炉和焦炉。
高炉负责将铁矿石还原成生铁,而焦炉则是供给高炉热力能源的主要设备。
具体来看,高炉会在还原铁矿石的同时,释放出大量的热能,这些热能可以通过高炉炉顶的烟气传递给蒸汽锅炉,进而制造蒸汽驱动汽轮机发电,实现对高炉废热的利用。
但是在实际生产过程中,由于高炉运行条件复杂,热传递效果不佳,导致高炉废热的利用率较低,从而造成了不少的能源浪费。
另外,由于焦炉所需的热能来自于煤炭的燃烧,其过程中会产生大量的各种有毒有害气体,主要包括一氧化碳和二氧化碳等。
虽然目前通过改进焦炉工艺等手段,可以在一定程度上降低焦炉排放的有害气体,但仍然存在着很大的安全隐患。
除了以上两大能源,矿泉水的制备和物料输送等环节也都需要消耗大量的能源,从而增加了炼铁生产的总能耗。
2. 炼铁生产中的节能措施(1) 提高热能利用效率作为炼铁生产过程中最主要的能耗来源,高炉和焦炉的能源利用效率直接影响整个生产的能耗指标。
因此提高高炉和焦炉的热能利用效率,是炼铁生产节能的主要手段之一。
其中,提高高炉烟气能量利用率是节能降耗的关键点之一。
目前实现高炉废热的利用较为常见的方法,是通过蒸汽锅炉和汽轮机等设备实现对高炉废热的二次利用。
这种方法需要充分考虑高炉炉顶烟气的温度、烟气输送以及蒸汽锅炉等设备带来的热损失等因素。
因此,在此过程中需要合理设计设备和参数,实现烟气高温、高速、高湿的冷凝。
(2) 提高炉缸效率在炼铁生产中焦炉所产生的有害气体问题一直是亟待解决的难题。
为了减少焦炉对环境的影响,我们可以从多方面入手,如通过改进炉壁材料、调整设计参数等方式优化焦炉结构,逐步提高焦炉效率,减少有害气体的排放。
- 1、下载文档前请自行甄别文档内容的完整性,平台不提供额外的编辑、内容补充、找答案等附加服务。
- 2、"仅部分预览"的文档,不可在线预览部分如存在完整性等问题,可反馈申请退款(可完整预览的文档不适用该条件!)。
- 3、如文档侵犯您的权益,请联系客服反馈,我们会尽快为您处理(人工客服工作时间:9:00-18:30)。
国内外高炉炼铁系统的能耗分析
炼铁系统的能耗占钢铁联合企业总能耗70%,
吨铁产生1.5 tco2, 3.08kgso2, 50mg粉尘, 95%的二恶英, 约350kg/t的炉渣。
1、根据中国钢铁工业协会2007年发布的全国重点钢铁企业有关能耗数据来进行分析,有关人士总结了重点钢铁企业高炉每生产一吨铁的能耗状况:
焦化工序的工序能耗为123.11kgce/t,高炉炼铁入炉焦比为392kg/t。
由此得出,冶炼一吨铁水,焦化工序的能源消耗为123.11kgce/t × 0.392t/t = 48.26kgce/t。
烧结工序的工序能耗为55.21kgce/t,高炉炼铁的炉料结构为烧结矿78.28%、球团矿13.91%、块矿7.81%。
冶炼一吨铁水需要消耗1.672吨含铁原料,则需要的烧结量为1.672t × 78.28% = 1.3088t。
由此得出冶炼一吨铁水,烧结工序的能耗为55.21kgce × 1.3088t = 2.25 kgce/t。
球团工序的工序能耗为33.08kgce/t,冶炼一吨铁水需要球团量为1.672t × 13.91% = 0.2325t。
由此得出冶炼一吨铁水,球团工序所消耗的能源为33.08kgce/t × 0.2325t =
7.69kgce/t。
炼铁工序能耗为428.16kgce/t,生产一吨铁水,炼铁系统总能耗为48.26kgce/t(焦化)+ 72.25kgce/t(烧结)+ 7.69kgce/t(球团)+ 426.84kgce/t(炼铁)= 555.04kgce/t。
2、按照上述计算方法,我们计算了2007年一季度宝山钢铁股份公司4号高炉(4747m³)生产一吨铁的能耗:21.81kgce/t(焦化)+ 62.31kgce/t(烧结)+ 4.60kgce/t(球团)+ 381.22kgce/t(炼铁)= 469.94kgce/t。
据了解,国外一些先进的钢铁企业采用高炉炼铁的能耗指标也在不断进步。
表1是2005年韩国浦项制铁和光阳厂焦化、烧结等有关能耗指标。
由表可得,2005年浦项制铁焦化工序能耗为129.7kgce/t × 0.4947t/t = 64.16kgce/t,光阳厂为131.9kgce/t × 0.4921t/t = 64.90kgce/t;韩国高炉炼铁矿耗在1.60t/t左右,浦项制铁烧结能耗为1.60 × 76.4% × 66kgce/t = 80.67kgce/t,光阳厂烧结能耗为1.60 × 70.9% ×57.4kgce/t = 65.11kgce/t;韩国球团矿全为进口,暂不记入能耗。
最终将各项指标汇总可得,浦项制铁炼铁系统能耗为64.16kgce/t + 80.67kgce/t + 426.5kgce/t = 607.33kgce/t,光阳厂炼铁系统能耗为64.90kgce/t + 65.11kgce/t + 441.1kgce/t = 571.11kgce/t。
2005年德国蒂
森钢铁公司的焦化工序能耗为75.1kgce/t,烧结工序能耗为58kgce/t,炼铁工序能耗为
426kgce/t,由此推算出其炼铁系统的能耗低于600kgce/t。
表1 2005年浦项制铁盒光阳厂炼铁有关能耗指标
表2 全国重点钢铁企业能耗对比(单位Kgce/t)
从表2可看出,我国重点钢铁企业炼铁系统能耗在降低,说明我国炼铁系统技术在不断进步,不断完善,有较强的生命力。
非高炉炼铁系统的能耗分析
目前,非高炉炼铁工序在一些工业发达国家已经应用了一段时期,其中,主要的非高炉炼铁系统在生产中的实际能耗情况如下:
南非COREX工艺——该系统生产需要约20%的焦炭(最低可达13%的焦炭),炉料中尚有约20%的球团,冶炼所消耗的燃料比约为1050kg/t左右,扣除部分煤气回收后其工序能耗为595kgce/t~609kgce/t。
韩国浦项FINEX工艺——浦项产能为150万吨/年的FINEX系统目前正处于调试阶段,相关数据尚未透露,现已运行4年的80万吨/年FINEX(日产达2300吨,燃料比在
740kg/t~750kg/t)设备进行分析。
浦项FINEX生产需要10%左右焦炭、块煤和喷吹煤粉,煤比为250kg/t~280kg/t。
FINEX的煤气可进行循环利用(脱出CO2后),可使煤比约降低100kg/t。
澳大利亚Hismelt工艺——2006年年底,澳大利亚Hismelt工艺在实际生产中的煤耗为900kg/t,尚需要有1200℃的高风温作保障,其电耗为350kWh/t。
而2006年我国重点钢铁企业吨铁电耗仅为67.67kWh/t,焦比为395 kg/t。
高热值煤气回收利用率低是非高炉炼铁能耗高的“瓶颈”
2007年,我国重点钢铁企业的烧结、炼铁工序能耗与2006年相比进一步降低,炼铁生产部分工序能耗指标见表2。
2007年,全国重点钢铁企业高炉炼铁燃料比是529kg/t,浦项FINEX燃料比是
740kg/t~750kg/t,澳大利亚Hismelt的煤耗在900kg/t(尚需1200℃风温和350kWh/t的电力)。
这说明目前非高炉炼铁的能耗高于高炉冶炼生产工艺。
从2006年开始我国电力折标准煤系数从0.404kgce/kWh调为0.1229kgce/kWh,是我国钢铁工业能耗值下降较多,与国外炼铁能耗水平的不可比性增加。
2007年,全国重点钢铁企业炼铁系统的能耗为555.03kgce/t。
2007年1季度宝山钢铁股份公司炼铁系统的能耗为469.94kgce/t。
2005年,韩国浦项和光阳炼铁公司炼铁系统的能耗为607.22kgce/t和622.11kgce/t。
通过高炉和非高炉炼铁能耗的对比可以看出,以目前的水平,宝钢的炼铁系统能耗低于非高炉炼铁工艺的能耗,韩国浦项制铁和光阳厂炼铁系统能耗略高于南非COREX的能耗,但低于FINEX和Hismelt的能耗。
非高炉炼铁工艺的能耗高主要问题是大量高热值煤气如合科学合理充分利用。
煤气去发电的能源利用率只有32%——42%,在能源利用率和成本核算上是不合适的,且增加较大投资和运行费。
我国一些企业拟采用煤造气,建设直接还原生产线。
煤造气在技术上是过关了,但是在能源利用率和成本核算上是不合适的。
富余煤气去发电的能源利用率只有32%——42%,在总能耗上是降不下来,成本上升,经济上要亏本。
经分析可得出,目前非高炉炼铁工艺的能耗高于高炉炼铁流程的主要原因有两个方面:一个是非高炉炼铁生产过程要产生大量的高热值煤气,这些热值煤气在回收利用方面还有待进一步加强;另一个是非高炉炼铁对于铁矿石的还原大多数是直接还原(吸热反应),而高炉炼铁大多数是间接还原(放热反应)。
所以,从能源利用效率来讲,高炉炼铁能耗暂时是优于非高炉炼铁的。
但是随着科学技术的不断完善,非高炉炼铁技术也会取得新的进展,得到不断的完善。
从长远出发,一旦非高炉炼铁在短流程优势得以充分发挥的同时,又在能耗降低方面取得突破性进展,其发展前景会更加广阔。
目前,我国大多数直接还原生产线的能耗和成本较高,经营困难,说明尚有较多要改进的地方。