煤矿主井装卸载自动控制系统设计模板
主井装卸载系统的自动化改造
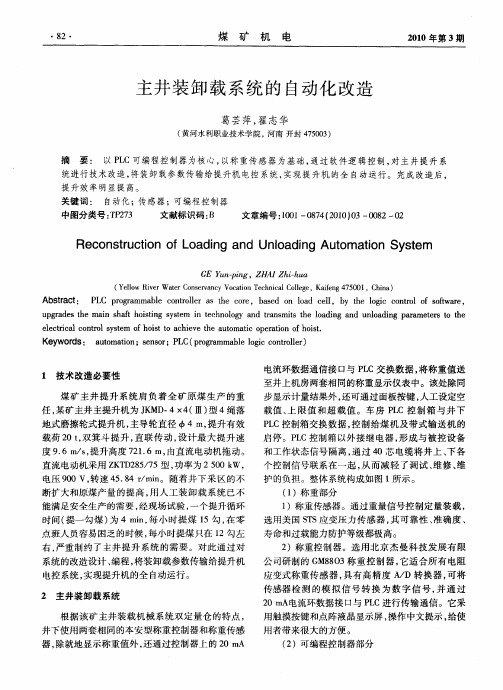
( )称 重部分 1 1 )称重 传感器 。通过 重量信 号控 制定 量装 载 ,
选用美 国 S S应 变压 力 传 感器 , 可 靠 性 、 T 其 准确 度 、
时间 ( 一勾 煤 ) 4 mi, 提 为 n 每小 时提 煤 1 5勾 , 零 在 点 班人员 容易 困乏 的时候 , 每小 时提煤 只在 1 2勾左 右, 严重 制约 了主 井 提 升 系统 的 需 要 。对 此通 过 对
K y od : atm t n e sr L ( r a m bel i cnrl r e w rs uo a o ;sno;P C po m a l o c o t l ) i r g g oe
1 技术 改造 必要性 煤 矿 主 井 提 升 系 统 肩 负 着 全 矿 原 煤 生 产 的 重 任, 某矿 主井 主提 升机为 J MD 4X ( 型 4绳 落 K - 4 Ⅲ) 地 式磨擦 轮式 提升 机 , 导轮 直径 4m, 主 提升 有效 载荷 2 , 0t双箕 斗 提 升 , 直联 传 动 , 计 最 大 提 升 速 设 度 96m s提升高度 7 16m, . / , 2 . 由直 流电动机 拖 动 。
寿命 和过载 能力 防护等级都 极 高 。 2 )称重 控 制器 。选 用 北京 杰 曼科 技 发 展 有 限
公 司研 制 的 G 8 3 重控 制 器 , 适合 所 有 电阻 M8 0 称 它
系统的改造设计 、 编程, 将装卸载参数传输给提升机
电控系统 , 现提升 机 的全 自动 运行 。 实 2 主井 装卸载 系统 根据 该 矿 主井 装 载 机械 系 统双 定 量仓 的特点 ,
u g a e h i h f h itn y t m n tc n lg nd ta s t h o dig a d u la i g paa t r o t e p r d st e man s a t osi g s se i e h oo y a r n mis t e la n n no d n r me e st h ee tia o to y tm fhos o a hiv h u o tc o e ain o o s. l crc lc n r ls se o itt c e e t e a t mai p r to fh it
主井卸载装置电控系统PLC改造设计
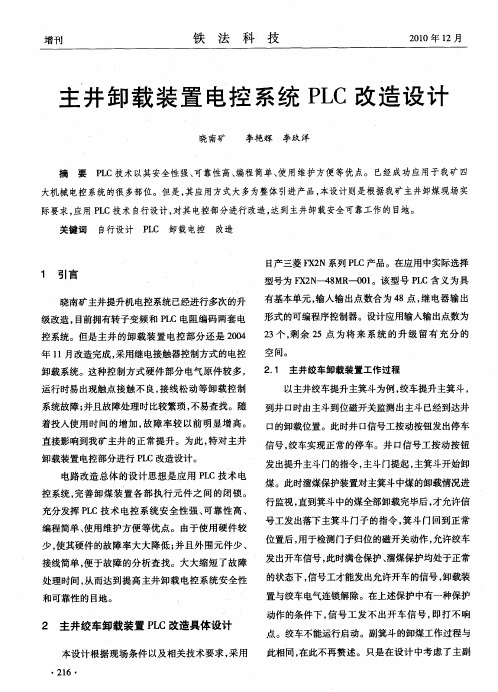
的状态下 , 信号工才能发出允许开车的信号 , 卸载装
置与绞车电气连锁解除。在上述保护 中有一种保护
动作 的条件下 , 信号 工发不 出开 车信 号 , 即打不响
2 主井绞车卸载装置 P C改造具体设计 L
本设计根据现场条件以及相关技术要求 , 采用
・
点。绞车不能运行启动。副箕斗的卸煤工作过程与
日 产三菱 F 2 X N系列 P C产品。在应用中实际选择 L
1 引言
晓南矿主井提升机电控系统 已经进行多次的升 级改造 , 目前拥有转子变频和 P C电阻编码两套电 L 控系统 。但是主井 的卸载装置 电控 部分还是 20 04 年 1 月改造完成 , 1 采用继电接触器控制方式的电控
要求。主井卸载装置工作过程如图 1 所示。 2 2 主井绞车卸载装置 系统 P C电路原理 . L P C使用交流 20 L 2 V电源 , 其输入部分共有 l 3 个输入点 , 电源有 P C内部 的直 流 2 V电源提 其 L 4
绞车正常停车
一
l 信号工发出 提主斗门 I 指令。 ‘
煤。此时溜煤保护装置对主箕斗中煤的卸载情况进
行监视 , 直到箕斗中的煤全部卸载完毕后 , 才允许信 号工发出落下主箕斗 门子的指令 , 箕斗门回到正常 位置后 , 用于检测门子归位的磁开关动作 , 允许绞车
少, 使其硬件的故障率大大降低 ; 并且外 围元件少、
此时满仓保护、 溜煤保护均处于正常 接线简单 , 便于故障的分析查找 。大大缩短 了故障 发出开车信号 , 处理时间, 从而达到提高主井卸载 电控系统安全性
!! Q XO O O E!1 茸 1 D Q1 r D
一
YP P O 叫}. [ 】 T O 叫鲁_£ " [虬 】
矿井综合自动化信息系统设计文档
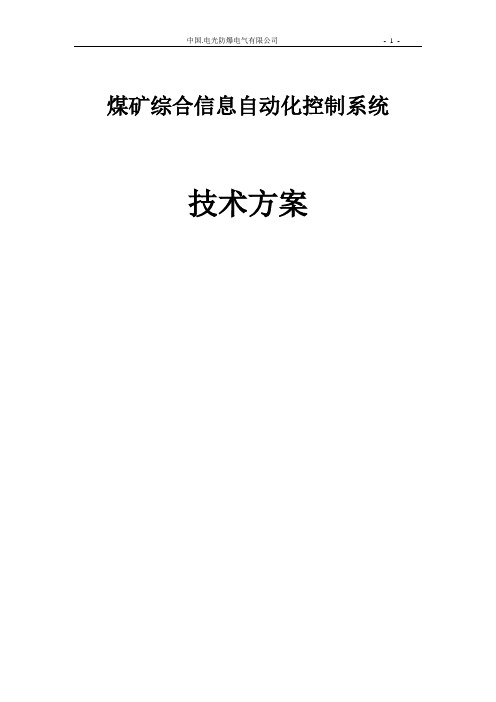
煤矿综合信息自动化控制系统技术方案第一章综合自动化控制系统1、概述1.1、简介为加快应用高新技术和先进适用技术改造和提升传统产业,加速煤炭企业的信息化建设,更好地发挥各自动化系统的作用,协调生产过程中系统间的关系,提高机械设备的利用效率,提高安全生产和管理水平,开发信息资源的价值,需要对多个自动化系统进行整合,并进行综合自动化信息系统集成建设。
综合自动化信息系统将集成当今先进的计算机信息化、自动化和监测监控等技术,针对煤矿高危险、恶劣环境的特点,通过系统优化和创新,开发煤矿综合自动化技术,在现场控制为主的局部控制系统基础上,实现以地面集中操作、分布控制为主的全过程控制。
即通过生产现场的设备层、控制层与信息层的集成,实现控制与管理的数据通讯与共享;通过开发基于中间件技术的控制软件,将对生产过程的控制、监测能力随网络的扩展而自然延伸,直至实现通过互联网络进行的异地远程监测与维护。
综合自动化系统采用现场总线技术将通用或专用微处理器置入传统的测量控制仪表,使它们具有数字计算和数字通信能力,采用一定的通信介质作为总线,按照公开、规范的通信协议,在位于现场的多个微机化测量控制设备之间及现场仪表与远程监控计算机之间,实现数据传输与信息交换,形成适应实际需要的自控系统。
简而言之,它把分散的测量控制设备变成网络节点,以现场总线为纽带,把它们连接成可以相互沟通信息、共同完成自控任务的网络系统。
现场总线将控制功能彻底下放到现场,节省了硬件数量与投资,降低了安装成本和维护费用。
同时用户具有高度的系统集成主动权,用户可以自由选择不同厂商所提供的设备来集成系统。
避免因选择了某一品牌的产品而限制了使用设备的选择范围,不会为系统集成中不兼容的协议、接口而一筹莫展,使系统集成过程中的主动权牢牢掌握在用户手中。
现场设备的智能化、数字化,与模拟信号相比,从根本上提高了测量与控制的精确度,减少了传送误差,提高了系统的准确性与可靠性。
系统采用PROFIBUS-DP传输类型的PROFIBUS现场总线,最大传输速率可达12Mbps,可应用于现场级,高速、廉价的传输形式的自控系统与现场设备之间的实时通信。
主井装卸载系统的自动化改造
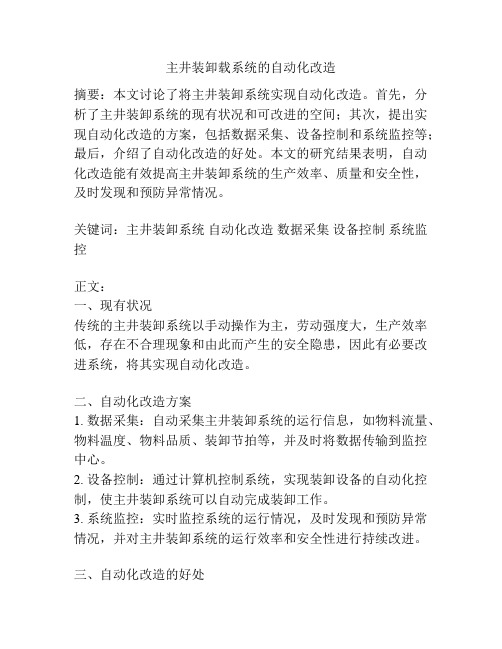
主井装卸载系统的自动化改造摘要:本文讨论了将主井装卸系统实现自动化改造。
首先,分析了主井装卸系统的现有状况和可改进的空间;其次,提出实现自动化改造的方案,包括数据采集、设备控制和系统监控等;最后,介绍了自动化改造的好处。
本文的研究结果表明,自动化改造能有效提高主井装卸系统的生产效率、质量和安全性,及时发现和预防异常情况。
关键词:主井装卸系统自动化改造数据采集设备控制系统监控正文:一、现有状况传统的主井装卸系统以手动操作为主,劳动强度大,生产效率低,存在不合理现象和由此而产生的安全隐患,因此有必要改进系统,将其实现自动化改造。
二、自动化改造方案1. 数据采集:自动采集主井装卸系统的运行信息,如物料流量、物料温度、物料品质、装卸节拍等,并及时将数据传输到监控中心。
2. 设备控制:通过计算机控制系统,实现装卸设备的自动化控制,使主井装卸系统可以自动完成装卸工作。
3. 系统监控:实时监控系统的运行情况,及时发现和预防异常情况,并对主井装卸系统的运行效率和安全性进行持续改进。
三、自动化改造的好处1. 提高主井装卸的效率:显著减少人工操作次数,提高装卸节拍,从而提升生产效率。
2. 提高装卸质量:通过系统数据采集和监控,及时发现生产上存在的问题,并及时采取对策,从而提高装卸产品的质量。
3. 提高工作安全性:自动化改造可以减少可能导致意外状况的人为操作,从而提高工作安全性。
本文调研了主井装卸系统的自动化改造,并提出了实现自动化改造的方案,以及自动化改造的优点。
研究结果表明,自动化改造有助于提高主井装卸系统的生产效率、质量和安全性,及时发现和预防异常情况。
四、实施自动化改造的要点1. 确定改造目标:首先要明确主井装卸系统自动化改造的目标,明确改造方案,并制定出实施计划。
2. 购买和安装设备:根据确定的改造方案,采购所需的设备和相关材料,并安装上线。
3. 系统调试:对改造后的主井装卸系统进行调试,保证设备功能正常,实现系统的有效运行。
煤矿井下主运自动化系统改造设计

煤矿井下主运自动化系统改造设计摘要:带式输送机以其效率高、结构简单、维修方便等优点成为煤矿运输的核心设备,在矿井井下开采过程中发挥着重要作用。
一个安全、高效、集成化、自动化的运输控制系统可显着提高煤矿工人的工作效率、矿井的管理水平和经济效益。
目前,煤矿的主要运输系统因站线长、人员多、控制设备老化、通讯系统陈旧、自动化程度低,很大程度上制约影响着企业的生产效能。
因此,探索以PLC控制为核心的集成化方案对矿井主运输系统进行改造,通过以太网通信链实现主运输系统的各条皮带的集中控制,提高生产运输效率。
关键词:主运输系统;集中控制;远程监控1煤矿井下主运输系统介绍某煤矿主运输系统控制的主要运输设备为5条输送带(地面上仓皮带、转载皮带、主斜井强力皮带、井下胶带大巷一部皮带、胶带大巷二部皮带),缓冲煤库2个,除铁机2台,运输距离总长约8550米。
存在主要运输路线长,设备布置散现象,主要由现场岗位作业人员控制。
部分设备由保护箱控制,保护箱没有通讯接口,无法实现集中控制,虽大部分设备预留通讯接口,但连续运输的输送机之间没有形成联动集中控制。
现有胶带输送机驱动方式仍采用液力偶合器软起动方式,存在不能长时间低速运行,无法满足低速验带要求,且设备存在传动效率低,能耗大,维护成本高且维护量大等现状。
由于上述因素,主要运输系统的自动化程度不高,使得整体联动效率和现场安全管理效能不能有效提高。
2煤矿井下主运输系统改造设计随着自动控制技术、计算机信息技术、信号检测/传输技术、通信技术、现场总线技术的快速发展,带式运输的集中控制系统技术已经成熟,生产的安全性和效率有了很大提高。
通过对系统的集中控制改造以及驱动方式采用交流变频软起动,我们可以提高自动化程度,实现矿井主运输系统的高效控制管理。
2.1集控系统基于结构简单、性价比高、安全可靠、功能齐全、维护方便等特点,井下输送带均采用集中控制方式,并配有PLC主机集中控制。
该集中控制系统可实现单机,集中控制控制(主机和辅机),为将来的扩展提供空间。
煤矿主井提升信号及自动装卸载系统的改造

煤矿主井提升信号及自动装卸载系统的改造针对煤矿主井提升信号及自动装载系统存在的问题,采用西门子可编过程控制器(PLC)及其DP_PROFIBUS、MPI网络通讯技术和建立在WINCC平台上的上位工控计算机,对系统进行改造,解决重复装载、上井口煤满仓、单勾提升、装卸载动态模拟监视等问题,实现提升信号和装载自动化。
标签:DP-PROFIBUS网络MPI网络WINCC 提升信号自动装卸载重复装载单勾提升物位仪1 概述曲江公司主井于2003年投产,设计矿井年产量90万吨,是我国江南原煤产量最高的矿井,号称“江南第一大井”。
主井装备一套JKMD-3.25X4塔式多绳摩擦式提升机,主导轮和导向轮直径3.25米,提升有效载荷10吨,钢丝绳柔性罐道,双箕斗提升,电机与主导轮直联传动,设计最大提升速度10米/秒,提升高度900米,由低速直流电动机驱动。
直流电动机功率1300KW,电枢电压800V,额定转速59转/分。
电控系统采用天津天控生产的TZK全数字直流提升机电控设备,其中核心控制器使用了西门子公司6RA70调速装置及S7-300 PLC。
主井井深1000米,地面为井塔式结构,卸载方式为曲轨自动卸载。
井下设计有一个中央原煤仓,对应两套装载机构,给两只箕斗装煤。
每套装载机构包括一台给煤机、一台胶带机、一套定量斗。
定量斗下部有闸门和定重传感器,装载站还设置一台双油泵液压站,电气控制电磁阀,打开、关闭定量斗闸门,定重传感器称量定量斗原煤重量,实现装载过程的自动控制。
2 改造的原因和目的原提升信号及自动装卸载系统存在以下问题:2.1 重复装煤现象。
设备运行多年来,经常出现重复装煤现象,结果导致主电动机以最大力矩无法提升,必须采取人为打开箕斗卸煤于井筒方法,或设法在另一只箕斗(一般在卸载位置)装配重铁,强行开车。
无论采取何种方法解决问题,都需要人工花几小时时间完成,同时,存在着安全风险,严重影响安全生产。
究其原因,重复装煤现象,有时是装载站操作工误操作造成的;有时是井下原煤含水分较大,卸载时,粘附于箕斗而卸不干净产生的。
主井装卸载及提升信号综合控制系统

主井装卸载及提升信号综合控制系统技术文件常熟市新虞电器有限责任公司我公司是原煤炭部定点生产提升信号通信设备: KXT7A矿用提升信号及操车监控装置、KJD10主井自动装卸载控制与提升信号装置的厂家,自九十年代以来,我公司独立研发出以PLC为核心的自动化控制设备产品。
目前国内多家绞车电控生产厂家(如:天水电控传动研究所、天津电控设备厂、天津津友联有限责任公司(原天津民意)、洛阳中信重机自动化工程有限责任公司、徐州煤安公司、泰安煤机厂、中国矿大都有着紧密的合作关系),与国际跨国公司:ABB、西门子公司均有合作经验,我公司以诚信为原则,以质量为保证,来满足不同用户的要求。
为了满足矿方要求,系统整套采用KJD10主井装卸载控制与提升信号装置,特制订如下方案:1、主井装卸载及提升信号综合控制系统设备符合下列规定和要求: 1.1、《煤矿安全规程》(2009版)1.2、《电液设备第二部分:装有电子器件的电控设备》(GB3797—1989)的要求及相应的IEC标准执行1.3、《电液设备的抗干扰特性基本测量方法》(GB4859-84)1.4、《电工控制设备造型设计导则》(GB/T10217-1988)1.5、《电工设备结构总技术条件》(GB/T15193-1994)1.6、进口电液设备遵守国际电工委员会IEC标准1.7、《爆炸性环境用防爆电液设备通用要求》(GB3836.1-1983)1.8、《矿用一般型电液设备》(GB/12173-1990)1.9、《煤矿井下用电器设备通用技术条件》、(MT/T661-1997)1.10、《电力装置的继电保护和自动装置的设计规范》(GB50062-92) 1.11、《矿山电力设计规范》(GB50070-94)1.12、《工业过程测量和控制装置的电磁兼容性》(GB/T13926-1992) 1.13、《低压配电设计规范》(GB50054-95)1.14、《煤矿安全规程》(2009年版)1.15、《煤炭工业矿井设计规范》(GB50215-2005)1.16、《煤矿井下供配电设计规范》(GB50417-2007)2、主井装卸载及提升信号综合控制系统配置说明:装载称重系统与提升信号系统合为一体,设计安装在同一个操作台上,称重仪表安装在装载站的控制柜上,但两套系统的核心PLC互为独立,井筒提升信号系统与装卸载控制系统,在硬件和软件上整体独立,与绞车电控只存在闭锁和控制上的I/O接口,其I/O接口有:1.装载站的信号闭锁信号。
主井定重装卸载及信号控制系统技术改造
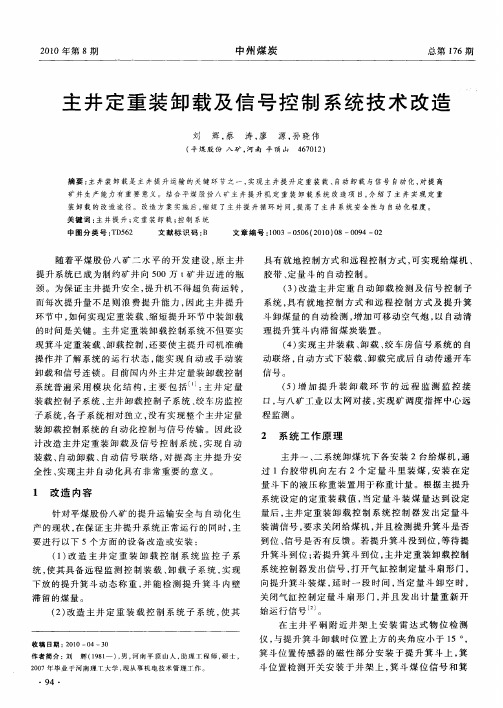
() 2 改造 主 井 定 重 装 载 控 制 系统 子 系统 , 其 使
在 主 井 平 硐 附 近 井 架 上 安 装 雷 达 式 物 位检 测
程监 测 。
系统普 遍采 用 模 块 化 结 构 , 要 包 括 : 井 定 量 主 主 装载控 制子 系统 、 井卸载 控制子 系统 、 主 绞车房 监控
子系统 , 子 系统相对 独立 , 各 没有实 现整个 主井定 量
装 卸载控 制系统 的 自动化控 制与信 号传输 。因此 设 计 改造主井 定重装 卸 载 及 信 号控 制 系统 , 现 自动 实 装载 、 自动 卸载 、 自动 信 号联 络 , 提 高 主井 提 升安 对
颈 。为保证 主井 提升安 全 , 升机不 得超 负荷运转 , 提
而 每 次 提 升 量 不 足 则 浪 费 提 升 能 力 , 此 主 井 载 、 缩短 提升环 节 中装 卸载 的时 问是关键 。主井 定重装 卸载控 制 系统不但 要实 现箕斗定 重装 载 、 卸载 控制 , 还要使 主提 升司机 准确 操作 并 了解 系统 的运 行 状 态 , 实现 自动 或手 动 装 能
全 性 、 现 主 井 自动 化 具 有 非 常 重 要 的 意 义 。 实
2 系 统 工 作 原 理
主井 一 、 系统 卸煤 坑下各 安装 2台给煤 机 , 二 通 过 1台胶 带机 向左 右 2个 定 量 斗里 装 煤 , 装 在定 安
量 斗 下 的 液 压 称 重 装 置 用 于 称 重 计 量 。 根 据 主 提 升
煤矿主井装卸载自动控制系统设计

煤矿主井装卸载自动控制系统设计煤矿主井装卸载自动控制系统设计随着煤炭需求的不断增加,煤矿生产也日益重要,成为了国民经济的重要组成部分。
而在这个行业中,煤矿主井的建设则是一个非常重要的问题。
在这个环节中,装卸载的自动控制系统设计也尤为关键。
一、煤矿主井的作用煤矿主井是一个井口。
它是煤矿的出入口,也是矿工下井的地方。
煤矿的生产将从这里开始,而安全、效率、稳定的操作则可以带来巨大收益。
二、煤矿主井装卸载自动控制系统设计的现状当前,煤矿主井的运营大多采用人工控制模式,这种模式虽然经验丰富,但是存在一定的问题:1.装卸束管作业不方便,装卸效率低。
2.作业人员作业强度大,存在工作疲劳问题。
3.操作风险巨大,存在重大安全隐患。
三、煤矿主井装卸载自动控制系统设计的要求1.实现自动化控制:煤矿主井装卸载自动控制系统的首要要求是实现装卸作业的自动化控制,减少人工参与,提升装卸操作效率。
2.提高操作安全性:设计的系统还应具有安全性较高的特点。
实现操作自动化的同时,需要提供严密的安全保障,避免中间出现异物或人员操作失误对系统和人员造成伤害。
3.规模性能要稳定:煤矿主井装卸载自动控制系统的规模性能不仅要稳定,而且还要实现不同设备之间的一体化管理,不同模块之间的高效联通,确保系统的有序运转。
四、煤矿主井装卸载自动控制系统设计的技术支撑为了实现自动化控制,可以考虑使用PLC控制器和传感器来实现煤矿主井装卸载自动控制系统的设计。
在设计前需要具备以下技术支撑:1.自动化控制技术:煤矿主井装卸载自动控制系统涉及到PLC控制器、传感器和相应的计算机网络交互等方面的自动控制技术的应用。
2.数据处理和存储技术:利用计算机系统对数据进行处理和存储,可以更有效地监测装卸工作、记录操作数据。
3.通信技术:对于需要远程控制的煤矿主井装卸载自动控制系统,现代通信技术的应用必不可少。
四、煤矿主井装卸载自动控制系统设计的优越性1.提高效率:自动化控制系统的应用将由人工作业模式转为自动化控制模式,减少了人工操作及运行间隔,方便了煤炭装卸搬运作业的快速完成,提高了操作效率。
全矿井综合自动化系统技术方案02

全矿井综合自动化系统技术方案02(赫思曼)嘿,大家好!今天给大家带来的是一份矿井综合自动化系统的技术方案,这个方案可是我根据10年的行业经验精心打造的,废话不多说,咱们直接进入主题。
一、矿井综合自动化系统架构1.数据采集层:利用各类传感器实时采集矿井环境参数,如温度、湿度、气体浓度等,同时监测矿井设备运行状态。
2.数据传输层:通过有线或无线网络将采集到的数据传输至数据处理层。
3.数据处理层:对采集到的数据进行处理、分析和存储,为矿井生产提供数据支持。
4.控制执行层:根据数据处理层提供的数据,自动控制矿井设备运行,实现矿井生产自动化。
5.用户体验层:通过可视化界面展示矿井运行状态,为矿井管理人员提供决策依据。
二、矿井综合自动化系统关键技术研究1.传感器技术:选用高性能、高精度的传感器,确保数据采集的准确性。
2.数据传输技术:采用有线与无线相结合的网络传输方式,实现数据的高速、稳定传输。
3.数据处理技术:运用大数据、云计算等技术对采集到的数据进行处理和分析,为矿井生产提供有力支持。
4.控制技术:采用先进的控制算法,实现矿井设备的精确控制。
5.用户界面技术:采用可视化技术,为用户提供直观、易操作的界面。
三、矿井综合自动化系统实施方案1.部署传感器:在矿井各关键部位安装温度、湿度、气体浓度等传感器,实时监测矿井环境。
2.建立数据处理中心:将采集到的数据传输至数据处理中心,进行存储、分析和处理。
3.控制矿井设备:根据数据处理中心提供的数据,自动控制矿井设备运行,实现矿井生产自动化。
4.优化用户体验:通过可视化界面,实时展示矿井运行状态,为矿井管理人员提供决策依据。
5.持续优化:根据矿井生产实际情况,不断调整和优化系统方案,提高矿井综合自动化水平。
四、矿井综合自动化系统优势1.提高生产效率:通过自动化控制,提高矿井生产效率,降低生产成本。
2.确保安全生产:实时监测矿井环境,及时发现并处理安全隐患,确保矿井安全生产。
主立井装卸载机械系统分析

主立井装卸载机械系统分析摘要对麻家梁主立井装卸载机械系统的提升容器及其布置、井底装载机械设备系统等,进行了简要分析,肯定了其在特大型矿井主立井装、卸载系统国内领先,国际先进水平的地位。
关键词主立井;装卸系统;设计分析1 概况1 矿井概况麻家梁矿井位于山西省朔州市的南部,是朔南矿区总体规划中五个特大型现代化矿井之一,隶属于大同煤矿集团有限责任公司。
井田面积104162;煤炭储量26 亿吨。
麻家梁矿井设计生产能力为10,同步建设洗选能力为10 的洗煤厂,服务年限827 年。
矿井采用立井双水平开拓,初期布置主立井、副立井、回风立井三个井筒,一个开采水平。
它是同煤集团11 个千万吨级矿井之一,是目前国内领先,世界一流的特大型立井。
2主立井概况主立井井筒净直径①9,井筒深度6028,担负全矿井原煤的提升及进风任务。
井筒内装备两对45 外动力卸载四绳提煤箕斗,一字形布置。
主立井提升设备为2台①57X4落地式多绳摩擦提升机,镜像对称布置于井筒两侧。
2设计内容简介21 提升容器主立井井筒直径① 9,提升容器选用两对45 外动力卸载四绳提煤箕斗,一字形布置,其中一对同侧装卸载,另一对异侧装卸载。
两对箕斗装载异侧,卸载同侧。
箕斗规格3080X 1500X 21600长X宽X高,箕斗总重75,分为上下两段,箕斗闸门采用上开式侧扇形结构,采用刚性罐道运行,井口上盘制动,井底下盘制动,滚轮罐耳采用浸油润滑滚轮罐耳。
为了解决多绳摩擦提升机各钢丝绳张力平衡问题, 首绳悬挂装置采用系列张力自动平衡悬挂装置, 尾绳悬挂装置采用3 个扁尾绳悬挂装置22 主立井井底工艺布置1 箕斗装载设备在井底的井筒两侧对应+665 水平东、西两条胶带大巷设有2 个井底煤仓,每个仓下设有一台甲带给料机。
煤仓下井底装载硐室内设有与2 对提煤箕斗相对应的两套独立的装载系统。
每套装载系统设有一台甲带给料机、一台装载带式输送机和一台定量斗,定量斗设带翻板的装载分岔溜槽。
城郊煤矿主井卸载系统改造

= .9 / 。据此 , 0 1 8m s 计算 出煤流 可 冲击 的水平 距 离 S :
0 6 6 m .5
E
图 1 主井提升 系统卸载装置示意图
1 一箕斗 ; 扇形 门; 2一 3一舌板 ; 4一井 口煤仓
图 2 提升箕斗卸煤水平位 置示 意图
1 一箕斗扇形门 ; 2一挡煤板 ; 3一箕斗溜煤板 ; 4一卸载 口溜煤板
21 00年第2期
煤
矿
机
电
・ 9・ 9
按实际情况城郊煤矿 可取 =1 1 .;
如一提升设备 能力 富余 系数 ,. —12 根 据提升系统 11 . ( 的设备状况 取值 , 设备较 新 、 况 良好取 小值 , 状 设备较 旧、 状
文 章 编 号 :0 1 0 7 ( 0 0 O 0 9 0 1 0 — 8 4 2 1 2— 0 9— 2 J
升机 , 而且伴 有闸皮 冒烟现象 , 闸盘偏摆超 标严重影 响提升
机的制动力 , 必须对 闸盘进行校正 。
3 制 动 盘调 整 的 方法
文 章 编 号 :0 1— 8 4 2 1 ) 2— 10一 l 10 07 【00 0 0 0 O
矿井提升机盘形制动器的偏摆量影响闸瓦间隙的调整 ,
矿 井 提升 机制 动盘 的技术 改 造
尹成迅 张建 军 ,
(. 1 山西煤炭职业技术学 院 机 电工程系 ,山西 太原 0 03 ; 30 1 2 大同煤矿集 团 青磁窑煤矿 ,山西 大同 0 70 ) . 30 3
城郊煤矿主井提升系统卸载装置如 图 1 所示 , 活动舌板
和箕斗闸 门开闭器的执行元件均为气缸 。工作环节流程为 : 箕斗到位- 舌板伸 出- 扇形 门打 开一 卸煤 完毕- 形 门关 闭- 扇 舌 板收 回. 箕斗离开 。活动舌板的主要作用是搭 接卸载煤仓 和
任楼煤矿主井提升装卸载站无人值守的设计及应用

任楼煤矿主井提升装卸载站无人值守的设计及应用摘要:安徽省淮北市任楼煤矿主井提升及装卸载自动化实现无人值守,通过认真分析绞车电控和信号及装载控制原理,使用光纤通讯方式把采集的各类的信号传输到监控室,采用PLC控制器进行数据处理,在原有控制系统基础上,新增保护柜及相关温度、烟雾、跑偏、急停等传感器,并实现自动连锁保护,同时将只有监视画面的监视系统,增加启动、停止、复位、控制按钮,实现由单纯的监视系统升级到可以监视并控制的远程监控系统,技术升级后,该系统操控操作界面简洁,保护动作可靠,显示及记录齐全,大幅度提高了主井提升效率,缩短故障处理时间,实现主井装载硐室及卸载站无人值守。
关键词:自动化;集中控制;无人值守一、设计实施背景安徽省淮北市任楼煤矿主井井筒净直径5.0m,提升高度612.5m,提升设备采用1台JKM-4×4(I)RL 型塔式摩擦轮提升机,滚筒直径为4米,提升机最大静张力750kN,最大静张力差180kN,提升机装备1套JDG16型箕斗, 采用电子秤定量装载,曲轨卸载方式,提升机由一台ZD120/40型直流电动机(2000kW,500r/min,770V)拖动,提升速度为9.21m/s。
主井提升机电控采用瑞典ABB生产的AC110数控自动控制及DCS800传动系统,提升信号及装卸载控制系统采用江苏常熟新虞自动化有限公司生产的KJ11型西门子S7300自动装卸载及信号控制系统,提升机电控及装卸载系统控制程序设计应用于2002年,满足自动运行条件时,能够实现数控自动运行。
由于装载系统不具备远程操控的功能,在未满足自动运行条件时,信号及装卸载控制部分只能在现场操作台进行手动操作,另外,如电机温度、设备运行情况等问题,需要现场巡查及操作。
因此,提升系统分早、中、夜三班运行,每班配备岗位工5人(主井提升系统共计18人)。
由于岗位操作工现场操作及巡查存在人为因素较多,存在误操作、巡查不到位、效率低、人员安全等一系列问题,影响着煤矿安全生产。
主井装卸载系统设备改造方案
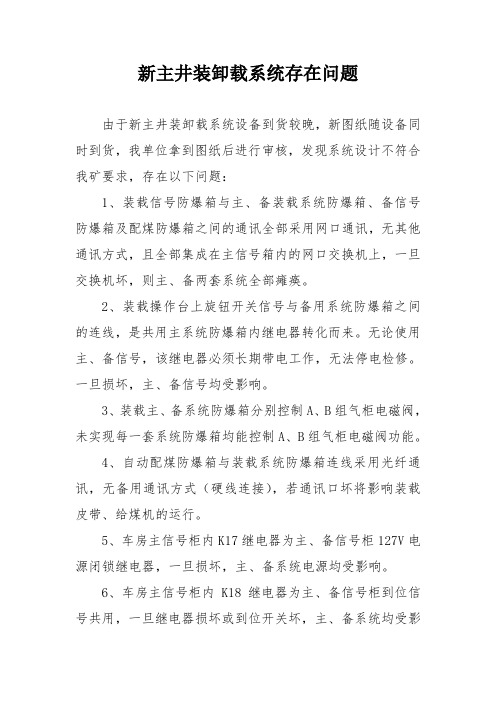
新主井装卸载系统存在问题由于新主井装卸载系统设备到货较晚,新图纸随设备同时到货,我单位拿到图纸后进行审核,发现系统设计不符合我矿要求,存在以下问题:1、装载信号防爆箱与主、备装载系统防爆箱、备信号防爆箱及配煤防爆箱之间的通讯全部采用网口通讯,无其他通讯方式,且全部集成在主信号箱内的网口交换机上,一旦交换机坏,则主、备两套系统全部瘫痪。
2、装载操作台上旋钮开关信号与备用系统防爆箱之间的连线,是共用主系统防爆箱内继电器转化而来。
无论使用主、备信号,该继电器必须长期带电工作,无法停电检修。
一旦损坏,主、备信号均受影响。
3、装载主、备系统防爆箱分别控制A、B组气柜电磁阀,未实现每一套系统防爆箱均能控制A、B组气柜电磁阀功能。
4、自动配煤防爆箱与装载系统防爆箱连线采用光纤通讯,无备用通讯方式(硬线连接),若通讯口坏将影响装载皮带、给煤机的运行。
5、车房主信号柜内K17继电器为主、备信号柜127V电源闭锁继电器,一旦损坏,主、备系统电源均受影响。
6、车房主信号柜内K18继电器为主、备信号柜到位信号共用,一旦继电器损坏或到位开关坏,主、备系统均受影响。
7、信号系统选择提人模式时,只能发4、5点和信号停止点,2、3点不能发。
8、装载操作台给煤机选择按钮为8档旋钮开关,无法同时开启两台或多台给煤机。
9、仅主信号系统配一套光纤通讯交换机,所有数据均通过该套交换机收发,备信号系统内未配备。
若交换机故障则备用系统也无法使用。
10、车房信号柜未配备主、备信号系统主电源切换的开关。
11、液压称重4-20mA无隔离栅,无法分别给主、备信号。
鉴于新主井装卸载系统存在以上问题,需对该系统设备进行改造,制定改造方案附后。
新主井装卸载系统改造方案一、主井信号系统1、信号系统(包含车房信号柜、卸载检修箱、井口提人信号箱及装载信号防爆箱)改为两套完全独立成熟的信号装置,每一套包含主信号装置及应急提升信号装置。
两套系统配置完全一致。
2、井口提人信号箱在选择提人模式时,可发2点、3点、4点、5点及信号停止点,在选择“提人”方式下,下井口发点需由上井口转发至车房,上井口具备向下井口要点功能。
煤矿主井装卸载检修通讯系统设计
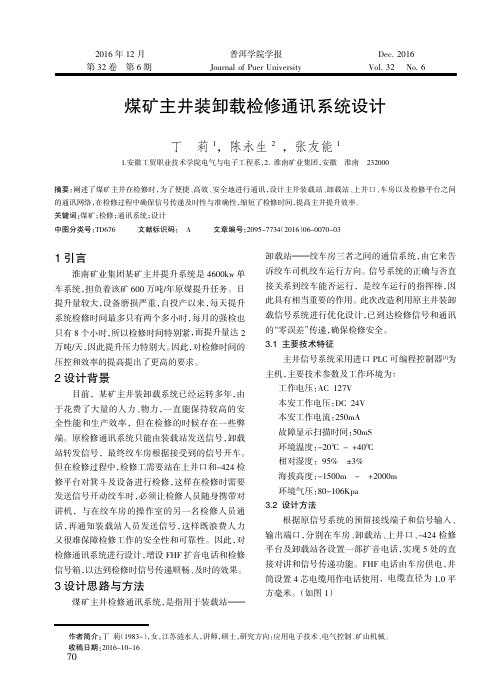
作者简介:丁莉(1983~),女,江苏涟水人,讲师,硕士,研究方向:应用电子技术、电气控制、矿山机械。
收稿日期:2016-10-162016年12月普洱学院学报Dec.20161引言淮南矿业集团某矿主井提升系统是4600kw 单车系统,担负着该矿600万吨/年原煤提升任务。
日提升量较大,设备磨损严重,自投产以来,每天提升系统检修时间最多只有两个多小时,每月的强检也只有8个小时,所以检修时间特别紧,而提升量达2万吨/天,因此提升压力特别大。
因此,对检修时间的压控和效率的提高提出了更高的要求。
2设计背景目前,某矿主井装卸载系统已经运转多年,由于花费了大量的人力、物力,一直能保持较高的安全性能和生产效率,但在检修的时候存在一些弊端。
原检修通讯系统只能由装载站发送信号,卸载站转发信号,最终绞车房根据接受到的信号开车。
但在检修过程中,检修工需要站在上井口和-424检修平台对箕斗及设备进行检修,这样在检修时需要发送信号开动绞车时,必须让检修人员随身携带对讲机,与在绞车房的操作室的另一名检修人员通话,再通知装载站人员发送信号,这样既浪费人力又很难保障检修工作的安全性和可靠性。
因此,对检修通讯系统进行设计,增设FHF 扩音电话和检修信号箱,以达到检修时信号传递顺畅、及时的效果。
3设计思路与方法煤矿主井检修通讯系统,是指用于装载站———卸载站———绞车房三者之间的通信系统,由它来告诉绞车司机绞车运行方向。
信号系统的正确与否直接关系到绞车能否运行,是绞车运行的指挥棒,因此具有相当重要的作用。
此次改造利用原主井装卸载信号系统进行优化设计,已到达检修信号和通讯的“零误差”传递,确保检修安全。
3.1主要技术特征主井信号系统采用进口PLC 可编程控制器[1]为主机,主要技术参数及工作环境为:工作电压:AC 127V 本安工作电压:DC 24V 本安工作电流:250mA 故障显示扫描时间:50mS 环境温度:-20℃-+40℃相对湿度:95%±3%海拔高度:-1500m -+2000m 环境气压:80-106Kpa 3.2设计方法根据原信号系统的预留接线端子和信号输入、输出端口,分别在车房、卸载站、上井口、-424检修平台及卸载站各设置一部扩音电话,实现5处的直接对讲和信号传递功能。
矿井主排水自动控制系统
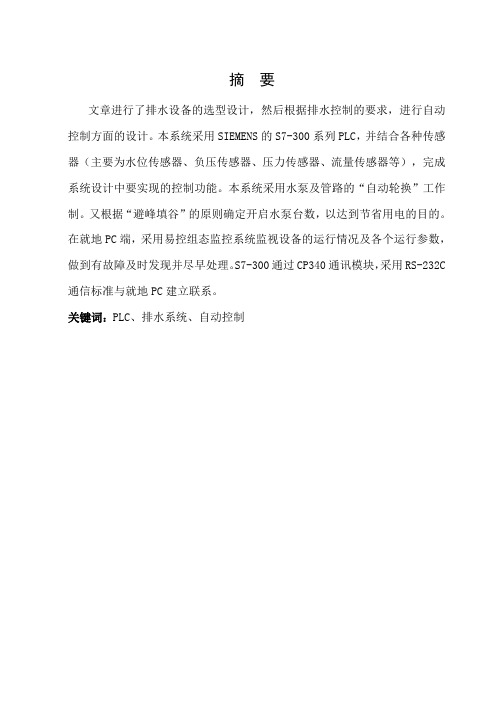
摘要文章进行了排水设备的选型设计,然后根据排水控制的要求,进行自动控制方面的设计。
本系统采用SIEMENS的S7-300系列PLC,并结合各种传感器(主要为水位传感器、负压传感器、压力传感器、流量传感器等),完成系统设计中要实现的控制功能。
本系统采用水泵及管路的“自动轮换”工作制。
又根据“避峰填谷”的原则确定开启水泵台数,以达到节省用电的目的。
在就地PC端,采用易控组态监控系统监视设备的运行情况及各个运行参数,做到有故障及时发现并尽早处理。
S7-300通过CP340通讯模块,采用RS-232C 通信标准与就地PC建立联系。
关键词:PLC、排水系统、自动控制ABSTRACTAt first this text chose and designed drainage equipments, then designed autocontrol part based on drainage control request. This system adopts S7-300 PLC series produced by SIEMENS,with many sensors(mainly incloding water line sensors,minus pressume sensors,pressme sensors,flux sensors) to complete autocontrol function demanded in this system design. Water pumps and pipelines of this system are controlled to run in turn automatically. The number of running water pumps is confirmed by the principle of avoiding apex and filling vale in order to economize electricity. On the spot of PC,it introduces controlease configuration control system to take charge of inspecting running state and parameters of equipments so that trouble can be found and dealt with in time. S7-300 used Standard RS-232 to communicate with PC on the spot through Module CP340.KEY WORDS:drainage system;PLC;autocontrol目录第一章绪论 (1)1.1 排水系统概述 (1)1.1.1 矿井生产过程中排水的重要性 (1)1.1.2 矿井排水系统的组成部分 (1)1.2 井下排水系统存在的问题 (3)1.3 排水系统为何要实现自动控制 (3)1.4 我国矿井主排水系统的现状 (4)第二章矿井自动排水系统的各种参数与检测 (4)2.1 水仓水位的检测 (5)2.1.1 液位传感器介绍 (5)2.1.2 液位检测装置选择 (8)2.2 电机即水泵温度检测 (9)2.3 水泵压力检测 (10)2.4 水泵流量检测 (12)2.4.1 流量检测仪器的安装 (12)2.4.2 流量计的要求 (13)2.4.3 流量检测传感器的使用 (15)2.5 水泵负压检测 (15)第三章基于PLC的矿井主排水自动控制系统的总体设计 (16)3.1 控制系统的总体结构 (16)3.2 基于PLC的矿井主排水控制系统设计 (17)3.2.1 PLC的主要特点 (17)3.2.2 PLC的基本工作原理 (20)3.2.3 PLC地址分配和实现控制功能 (22)3.2.4 3s7—300PLC的基本组成 (27)3.3 西门子ET200M与PROFIBUS-DP总线 (32)第四章矿井自动主排水系统设备的选型设计 (33)4.1 初始数据 (33)4.2 选型设计 (33)4.3 引水设备 (35)4.4 自动阀门 (38)4.5 高压开关柜 (40)第五章控制系统的软件设计 (41)5.1 PLC的软件设计 (41)5.1.1软件流程图 (41)5.1.2 地址分配 (43)5.1.3 水泵的自动开启、运行、故障保护流行图 (45)5.1.4 PLC的程序设计 (47)5.2 控制系统上位机的软件设计 (50)5.2.1 设计要求 (50)5.2.2 设计内容 (51)5.2.3 上位机与PLC的通信 (51)5.2.4 监控主界面 (53)5.2.5 报警界面 (55)第六章如何使矿井主排水自动控制系统抗各种干扰 (56)6.1 常见的各种干扰源 (56)6.2 如何采取措施排除这些干扰 (56)第七章总结 (57)参考文献 (58)致谢 (59)翻译部分 (60)第一章绪论井下排水系统是煤矿生产中四大系统之一,担负着井下积水排除的重要任务。
煤矿综合自动化系统方案设计-0
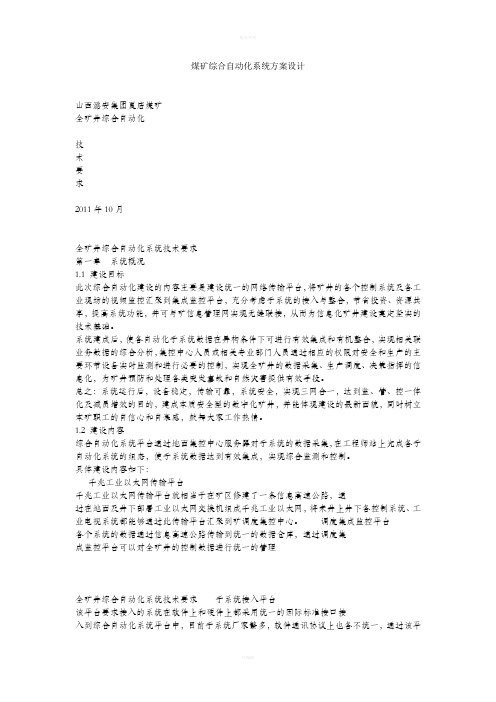
煤矿综合自动化系统方案设计山西潞安集团夏店煤矿全矿井综合自动化技术要求2011年10月全矿井综合自动化系统技术要求第一章系统概况1.1 建设目标此次综合自动化建设的内容主要是建设统一的网络传输平台,将矿井的各个控制系统及各工业现场的视频监控汇聚到集成监控平台,充分考虑子系统的接入与整合,节省投资、资源共享,提高系统功能,并可与矿信息管理网实现无缝联接,从而为信息化矿井建设奠定坚实的技术基础。
系统建成后,使各自动化子系统数据在异构条件下可进行有效集成和有机整合,实现相关联业务数据的综合分析,集控中心人员或相关专业部门人员通过相应的权限对安全和生产的主要环节设备实时监测和进行必要的控制,实现全矿井的数据采集、生产调度、决策指挥的信息化,为矿井预防和处理各类突发事故和自然灾害提供有效手段。
总之:系统运行后,设备稳定,传输可靠,系统安全,实现三网合一,达到监、管、控一体化及减员增效的目的,建成本质安全型的数字化矿井,并能体现建设的最新面貌,同时树立本矿职工的自信心和自豪感,鼓舞大家工作热情。
1.2 建设内容综合自动化系统平台通过地面集控中心服务器对子系统的数据采集,在工程师站上完成各子自动化系统的组态,使子系统数据达到有效集成,实现综合监测和控制。
具体建设内容如下:千兆工业以太网传输平台千兆工业以太网传输平台就相当于在矿区修建了一条信息高速公路,通过在地面及井下部署工业以太网交换机组成千兆工业以太网,将来井上井下各控制系统、工业电视系统都能够通过此传输平台汇聚到矿调度集控中心。
调度集成监控平台各个系统的数据通过信息高速公路传输到统一的数据仓库,通过调度集成监控平台可以对全矿井的控制数据进行统一的管理全矿井综合自动化系统技术要求子系统接入平台该平台要求接入的系统在软件上和硬件上都采用统一的国际标准接口接入到综合自动化系统平台中,目前子系统厂家繁多,软件通讯协议上也各不统一,通过该平台进行软硬件的技术改造后可以按照标准的方式实现现有系统的无缝接入。
- 1、下载文档前请自行甄别文档内容的完整性,平台不提供额外的编辑、内容补充、找答案等附加服务。
- 2、"仅部分预览"的文档,不可在线预览部分如存在完整性等问题,可反馈申请退款(可完整预览的文档不适用该条件!)。
- 3、如文档侵犯您的权益,请联系客服反馈,我们会尽快为您处理(人工客服工作时间:9:00-18:30)。
煤矿主井装卸载自动控制系统设计1山东科技大学成教学院枣矿集团分院毕业设计(论文)题目:煤矿主井装卸载自动控制系统设计专业矿山机电姓名唐维忠9月19日2摘要本设计说明书介绍了基于虚拟仪器开发平台LabVIEW 开发的主井提升监护系统。
本系统设计采用分散式控制系统, 系统由两个可编程控制器和一个上位机构成。
使用两个三菱FX2N 系列可编程控制器分别实现提升的定重装载与卸载功能。
上位机使用LabVIEW 开发提升机监护软件。
上位机与可编程控制器之间经过RS-485 串行通讯实现数据传输。
在定重装卸载控制部分, 重点介绍了本质安全型控制电路的设计; 可编.程控制器的编程, 如何根据工艺流程编制程序实现控制要求; 串行通讯程序的设计。
在上位机监护部分介绍了系统的软硬件构成。
该监护系统硬件上使用研化工业控制计算机与研化PCL- 818L 用于温度采集, 与研化PCL-836 用于定量仓定重及温度报警, 与PCL-846 用于扩展串行口, 实现上位机与可编程控制器的数据传输。
传感器的选择与电路设计。
软件上详细介绍了温度与定量仓定重方面的数据采集程序、数字量输出程序、串行通讯程序的编写。
关健词:3虚拟仪器; LabVIEW; 数据采集; 可编程控制器; 串行通讯; 定重装卸载; 监护系统4目录第一章概论..........................错误! 未定义书签。
第二章系统总体设计方案及其功能...错误! 未定义书签。
第一节现场状况与设计要求........错误! 未定义书签。
第二节系统组成与功能............错误! 未定义书签。
第三章装载控制系统的设计............错误! 未定义书签。
第一节电路设计..................错误! 未定义书签。
第二节可编程控制器的选用及程序设计错误! 未定义书签。
第四章卸载控制系统的设计............错误! 未定义书签。
第一节电路设计..................错误! 未定义书签。
第二节可编程控制器的程序设计. 错误! 未定义书签。
第五章上位机管理系统的设计..........错误! 未定义书签。
第一节LabVIEW 编程平台简介 ....错误! 未定义书签。
第二节系统硬件组成..............错误! 未定义书签。
第三节数字量输出电路的设计......错误! 未定义书签。
第四节系统软件构成..............错误! 未定义书签。
结束语...............................错误! 未定义书签。
参考文5献。
ooooooooooooooooooooooooooo566第一章概论矿井运输与提升在矿山生产中有十分重要的作用因为采掘下来的矿物只有运出矿井才有价值。
由于矿井运输线路长, 且由多个环节和各种运输设备配套而成如果线路某个环节中断, 就会使工作面和其它工作地点的作业陷于停顿.在矿井生产事故中, 运输与提升事故占很大比例.从经济角度看, 运输费用在生产成本中占很大的比重, 因为地面及井下运输设备很多, 运输工人和装载工人数几乎占全矿工人之半。
煤矿自动化是煤矿企业现代化的重要标志之一, 也是实现高产高效矿井生产的技术保障。
机电一体化技术的发展促进了煤矿自动化的发展。
煤矿自动化的本质在于扩大和延伸人类的感观和操作能力, 提高机械装置的精确性、快速性、可靠性和安全性, 以及节省能源节省劳力等, 从而解放、发展和提高劳动生产力。
而不是简单的理解为节省劳动力, 更不能仅仅是为了实现无人操作。
在现阶段的矿井生产中, 采煤工作面已经实现了完全的自动化运输及提升的自动化提到了议事日程。
主井定重装卸载控制系统就是适应煤矿自动化技术而设计, 其实现了主井装卸载的自动化, 定重装载保证了提升运行的安全。
节省了运输和7装载工人, 降低了矿井生产的成本。
在集散控制系统中, 上位机是不可缺少的部分.上位机软件必须能够有效的实现对系统数据的管理.在该设计中选用LabVIEW 作为上位机软件设计的环境。
LabVIEW 是一种主要用于开发测控系统的语言与传统编程语言, 如C 或Basic 不同之处在于: 一般编程语言是使用文本描述方式来写程序, 而LabVIEW 是以图形方式建立方块图程序。
和C 或者Basic 一样, LabVIEW 也有许多的函数库和子程序, 能够用来编写一般用途的程序。
其它还有一些特殊用途的函数库, 可用来实现数据采集、数据传输( GPIB) 、仪器硬件控制( VXI 、PXI) 、数据分析及显示、数据存储功能.另外, 为了方便开发人员在开发过程中进行调试和排错, LabVIEW 能够在方块图中设置断点、动态显示程序流程, 以单步执行来检查程序的运行状态和排除错误。
,本设计介绍了由上位机与两个可编程控制器( 分别控制装载与卸载) 组成的主井定重装卸载控制系统8第二章系统总体设计方案及其功能第一节现场状况与设计要求一现场状况蒋庄煤矿装载硐室内前后有1#. 2#两个井下煤仓,煤仓分别配备两个给煤机: 1#煤仓配有左1#给煤机和右1#给煤机; 2#煤仓配有左2#给煤机和右2#给煤机。
运输皮带机有左右两个: 左皮带机和右皮带机.两煤仓下给煤机把煤运送到皮带机上, 左右皮带机分别把煤运送到左右定量仓中.这样能够实现左右同时运煤, 提高了运输速度。
定量仓采用压磁传感器测量装载吨数。
当定量仓装载达到设定重量, 而且提升箕斗到位时, 定量仓仓门打开, 煤装载到提升箕斗中。
装载控制拒控制各设备, 从而实现装载自动化。
二设计要求( 1 ) 、本系统井下部分及相关电路采用本质安全型电路。
( 2) 、上位机显示内容包括:皮带机开、停, 给煤机开、停, 定量斗开、关和满、空, 箕斗运行方向, 箕斗装卸载开、关门, 箕斗到位情况。
装载定量斗重量吨数显示和体积模拟显示( 柱状图) , 卸9载仓满显示。
信号及状态显示: 点数、正常状态、检修状态等。
( 3) 装载及卸载同样能显示各设备状态.采用动态发光二极管显示。
第二节系统组成与功能一系统的总体设计方案本系统采用分散型控制系统, 结构简图如下( 详见系统流程图) :10资料内容仅供参考,如有不当或者侵权,请联系本人改正或者删除。
上位机(LabVIEW)分散型控制系统适用于多台设备的控制,在各设备设备生产线间有数据连接。
在本系统中,井下PLC为装载控制,所控制的设备有:四台给煤机、两部皮带机、两个定量斗电磁阀。
井上PLC为卸载控制,所控制设备有:提升箕斗的电磁阀。
上位机的作用是:监测提升机轴瓦温度,模拟演示装卸载及箕斗提升的工艺流程。
二系统硬件组成:研华工业控制计算机、三菱Fx2N系列可编程控制器、研华PCI-818L数据采集卡、研华PCL-836多功能记数记时、数字输入输出卡、研华PCL-846串行口扩展卡。
三系统模块图及功能系统模块图1装载控制系统的功能:可实现点动控制、 手动控制与自动闭锁控制的三工业绘制计算机按刼模块 裝裁控制台 (PLC-^MR) &路温度传感卸翊空制合(PLC —64MR)左1#给煤机左 2# 给 煤 机 t 左定戢仓满空 f 左定U 仓开关 左定 里 仓 电 阀 tr 右定埼仓开X右 右 皮 1# 帝 给 机 煤 机 右 右2# 定给域煤 仓:机 电a 阀t 右定輦仓满空t右箕斗到位左 皮 机种工作方式。
在正常工作情况下,使用自动控制;在可编程控制器发生故障时, 使用点动控制; 在检修等其它工作情况下, 可使用手动控制.2 上位机管理系统的功能:( 1) 定量仓定重。
工业控制计算机经过研华PCL- 836 多功能计数计时、数字输入输出卡采集定量仓压磁传感器的频率信号, 并经过该卡输出数字量到可编程控制器, 实现装载系统中的定重。
( 2) 温度监测。
工业控制计算机经过研华PCL-818L 数据采集卡采集提升机轴瓦温度信号, 对提升机进行温度的监测, 并具备一定的数据库功能, 能够对温度数据进行查询、显示、打印。
( 3) 数据通讯。
经过RS-485 标准串行接口从装载控制系统接收装卸载设备状态数据, 对其进行模拟演示。
并把接受到的数据传送到卸载控制系统.四串行通讯的设计:主井定重装载、卸载控制台采用LED 界面显示, 车房采用工业控制计算机界面显示, 三地同步显示设备运行状况, 均能监视到整个系统的运行状态.串行通讯接口的选择原则是1 可靠性。
如果传送错误, 将会使工业控制计算机和卸载控制拒不能正确显示各设备状态.2 通讯速度与通讯距离.大约1000m, 而且要保证一定的通讯速度。
3 通讯信道的抗干扰能力.第三章装载控制系统的设计第一节电路设计一本质安全型电路根据设计要求, 装载部分电路设计为本质安全电路。
由于本质安全型电气设备不需要隔爆外壳, 电路中的通断火花不会点燃可燃气体混合物。
因此它具有结构简单、体积小、制造维修方便、造价低、安全性可靠等特点。
本质安全电路原理: 本质安全电路是经过适当选择电气元件和系统参数, 降低电源电压, 减小线路电流, 对储能元件采取消能措施, 使电路系统或设备无论在正常工作或故障状态下所产生的电火花或元件的温度都不能点燃爆炸性混合物。
装载控制系统属于隔爆兼本质安全型的复合式电气设备.由于可编程控制器属于非本质安全型设备, 必须安装在隔爆箱内。
其余电路皆设计为本质安全电路, 直接安装在设计的控制拒内二装载控制系统原理电路及印制板的设计1 控制面板的设计控制面板采用发光二极管的亮与灭表示设备的启动与停止状态.皮带机与提升运行的显示经过多个二极管的亮与灭模拟显示。
控制面板的继电器的作用是: 当可编程控制器经过控制继电器的通与断, 从而控制左皮带机与右皮带机、左提升与右提升的动作显示灯, 这样能够大大减少了可编程控制器的输出口。
控制面板印刷电路板的设计: 总体上采用元件卧式安装一规则排列一圆形焊盘的工艺结构.在印制电路板板材、形状、尺寸和厚度的确定方面主要考虑以下因素: 在井下安装, 工作环境恶劣; 其安装在控制柜窗口形状和尺寸均由控制拒窗口决定; 印制电路板上的元件主要有发光二极管、欧姆龙G6A-274P 继电器、电阻, 电路板对元气件的承重和振动冲击较小, 本安电路电流只有7.27mA, 印制导线的载流量可按20A/mm, 则印制导线的截面积S=7.27/20=0.36* 10 -3mm22 可编程控制器输入输出信号接线板的设计可编程控制器的输入信号中, 有些不但要进入可编程控制器, 而且要控制面板上的发光二极管; 输出信号也有一些信号不但要控制设备, 而且也要控制面板上的发光二极管。
设计中采用双触点继电器解决这一问题.一个触点控制发光二极管, 另一个触点进入可编程控制器或控制设备.为了接线方便设计一个印制板电路, 该电路要符合本安要求.三设备的控制系统中控制设备采用QC810-60 型矿用隔爆兼安全火花型磁力起动器.该起动器的额定电流为60 安培, 能够控制660 伏40 千瓦以下的鼠笼电动机。