第二章 数控加工工艺基础
数控加工工艺的主要内容

可调支承
第二节 零件在数控机床的定位与装夹
(4)辅助支承 为提高工件的安装刚度及稳定性,防止工件的切削振动及 变形,或者为工件的预定位而设置的非正式定位支承。
a)铣削工件的顶平面 b)铣削变速箱壳体的顶面
第二节 零件在数控机床的定位与装夹
2.孔类定位元件
(3)自为基准原则 选择加工表面本身作为定位基准。 (4)互为基准原则 采取两个加工表面互为基准反复加工的方法。 (5)便于装夹原则 所选精基准应能保证工件定位准确稳定,装夹方便可靠, 夹具结构简单适用,操作方便灵活。
第二节 零件在数控机床的定位与装夹
3.辅助基准的选择
辅助基准是为了便于装夹或易于实现基准统一而人为制成 的一种定位基准。
第一节 数控加工工艺的制定
四、工序的划分
1.工序划分的原则
(1)工序集中原则——每道工序包括尽可能多的 加工内容,从而使工序的总数减少。
(2)工序分散原则——将工件的加工分散在较多 的工序内进行,每道工序的加工内容很少。
第一节 数控加工工艺的制定
2.工序划分方法
(1)数控车削工序的划分方法 1)按零件加工表面划分。将位置精度要求较高的表
第二章 数控加工工艺基础
第一节 数控加工工艺的制定 第二节 零件在数控机床上的定位与装夹 第三节 数控加工用刀具 第四节 加工余量与确定方法 第五节 工序尺寸及其公差的确定 第六节 机械加工精度及表面质量 第七节 数控加工工艺文件
第一节 数控加工工艺的制定
一、数控加工工艺的主要内容
(1)选择适合在数控车床上加工的零件。 (2)分析被加工零件的图样,明确加工内容及技术要求。 (3)确定零件的加工方案,制定数控加工工艺路线。 (4)加工工序的设计。 (5)数控加工程序的调整。
《数控技术第3版》_(习题解答)机工版
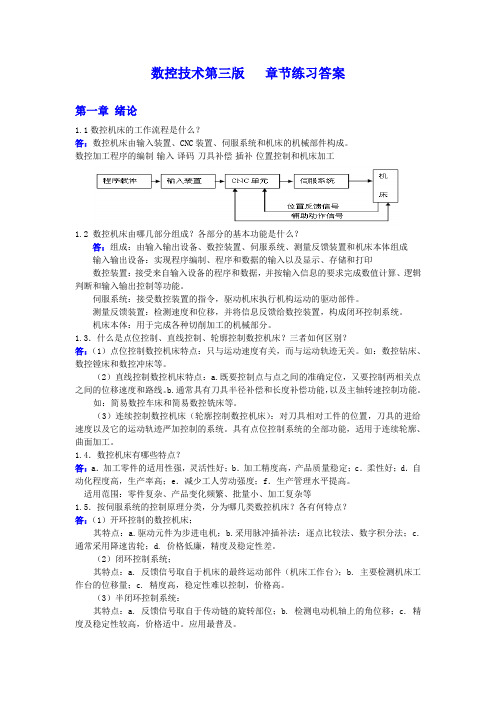
数控技术第三版章节练习答案第一章绪论1.1数控机床的工作流程是什么?答:数控机床由输入装置、CNC装置、伺服系统和机床的机械部件构成。
数控加工程序的编制-输入-译码-刀具补偿-插补-位置控制和机床加工1.2 数控机床由哪几部分组成?各部分的基本功能是什么?答:组成:由输入输出设备、数控装置、伺服系统、测量反馈装置和机床本体组成输入输出设备:实现程序编制、程序和数据的输入以及显示、存储和打印数控装置:接受来自输入设备的程序和数据,并按输入信息的要求完成数值计算、逻辑判断和输入输出控制等功能。
伺服系统:接受数控装置的指令,驱动机床执行机构运动的驱动部件。
测量反馈装置:检测速度和位移,并将信息反馈给数控装置,构成闭环控制系统。
机床本体:用于完成各种切削加工的机械部分。
1.3.什么是点位控制、直线控制、轮廓控制数控机床?三者如何区别?答:(1)点位控制数控机床特点:只与运动速度有关,而与运动轨迹无关。
如:数控钻床、数控镗床和数控冲床等。
(2)直线控制数控机床特点:a.既要控制点与点之间的准确定位,又要控制两相关点之间的位移速度和路线。
b.通常具有刀具半径补偿和长度补偿功能,以及主轴转速控制功能。
如:简易数控车床和简易数控铣床等。
(3)连续控制数控机床(轮廓控制数控机床):对刀具相对工件的位置,刀具的进给速度以及它的运动轨迹严加控制的系统。
具有点位控制系统的全部功能,适用于连续轮廓、曲面加工。
1.4.数控机床有哪些特点?答:a.加工零件的适用性强,灵活性好;b.加工精度高,产品质量稳定;c.柔性好;d.自动化程度高,生产率高;e.减少工人劳动强度;f.生产管理水平提高。
适用范围:零件复杂、产品变化频繁、批量小、加工复杂等1.5.按伺服系统的控制原理分类,分为哪几类数控机床?各有何特点?答:(1)开环控制的数控机床;其特点:a.驱动元件为步进电机;b.采用脉冲插补法:逐点比较法、数字积分法;c.通常采用降速齿轮;d. 价格低廉,精度及稳定性差。
第二章_数控加工编程基础
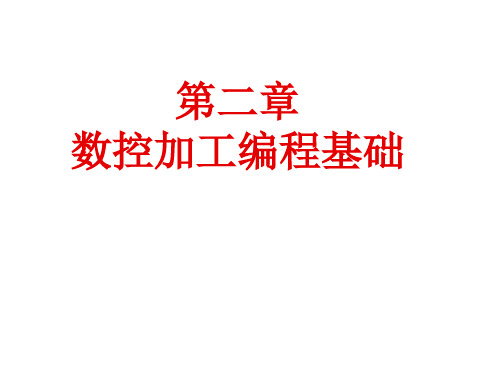
2.2 编程的基础知识
2.辅助功能M代码 M指令构成:
地址码M后跟2位数字组成,从M00-M99共100种。
(1) M00—程序停止。
(2) M01—计划(任选)停止。 程序运行前,在操作面板上按下“任选停止” 键时,
才执行M01指令,主轴停转、进给停止、冷却液关 断、程序停止执行。若“任选停止”处于无效状态 时,M01指令不起作用。利用启动按钮才能再次自 动运转,继续执行下一个程序段。
零件图纸
图纸工艺分析 确定工艺过程
数值计算
修
编写程序
改
制备控制介质
校验和试切 错误
4、制备控制介质
将程序单上的内容,经转 换记录在控制介质上,作为 数控系统的输入信息。 注意:若程序较简单,也可 直接通过键盘输入。
零件图纸
图纸工艺分析 确定工艺过程
数值计算
修
编写程序
改
制备控制介质
校验和试切 错误
5、程序的校验和试切
轴转动的圆进给坐标轴分别 用A、B、C表示。
坐标轴正向:由右手螺旋 法则而定。
右手直角笛卡尔坐标系
数控机2.床2的进编给程运动的是基相对础运动知。Y识
具体规定:
①坐标系是假定工件 不动,刀具相对于 工件做进给运动的 坐标系。
+B
X、Y、Z
Y
+A X
Z +C
②以增大工件与刀具
之间距离的方向为 坐标轴的正方向。 Z
a. 在刀具旋转的机床上(铣床、钻床、镗床)
Z轴水平时(卧式),则从刀具(主轴)向工件看时, X坐标的正方向指向右边。
+X
Z轴垂直时(立式),对单立柱机床,面向刀具主轴 向立柱看时, X轴的正方向指向右边
第二章 数控加工工艺基础2

2.7.2 基准不重合时,工序尺寸和公差的计算
在零件加工过程中,由一系列相互联系的工艺尺寸按一定 顺序首尾相连形成的封闭尺寸系统称为工艺尺寸链。 很显然,工艺尺寸链的主要特征是:封闭性和关联性。 封闭性——尺寸链中各个尺寸的排列呈封闭形式,不封闭 就不成为尺寸链。 关联性——任何一个直接保证的尺寸及其精度的变化,必 将影响间接保证的尺寸和其精度。如上尺寸链中A1、A2的 变化,都将引起A0变化。
表转换成尺寸公差,如表2-15——18。
2.7 工序尺寸和公差的确定 2.7.1 基准重合时,工序尺寸和公差的计算
生产上绝大部分加工面都是在基准重合(工艺基准和设计
基准重合)的情况下进行加工的,基准重合情况下工序尺寸与
公差的确定过程如下: (1)确定毛坯总余量和各加工工序的工序余量 (2)确定工序基本尺寸 (3)确定工序公差 (4)标注工序尺寸公差 最终加工工序尺寸的公差按设计尺寸标注,其余工序尺寸 公差按“入体原则”标注。
hll(
)
Ra1.5
ф 60.410 ф
4.49
h13(
0 0.046
)
Ra16
61.510 0.046
锻造
数据 确定 方法
6
±2
第一项为图样规定, 毛 坯 公 差 查表 , 其 余 按 经 济 加工 精 度 及入体原则定 第一项为 图样规定, 其余查表 确定
ф66 ±2
查表确 定
工序尺寸及其公差的确定实例4
第二章 数控加工工艺基础
教学目的:
通过本章的学习,掌握数控加工工艺的有关基本概念,了解工件获取 加工精度、加工质量的方法,掌握制定机械零件加工过程中有关尺寸 (加工余量、工序尺寸、公差等)的计算方法,进而能够制定简单机 械零件加工的工艺规程。
第二章数控加工工艺基础知识

第一节 基 本 概 念
5)选择机床和工艺装备。 6)确定工艺路线中每一道工序的工序内容,并提供主要工序 的检验方法。 7)确定加工余量、工序尺寸及其公差。 8)确定切削用量、计算工时定额。 9)进行技术经济分析,选择最优工艺方案。 10)填写工艺文件。 八、加工余量 1.加工余量的概念 2.影响加工余量的因素
第二节பைடு நூலகம்数控加工工艺系统
4)钻削刀具。 (2)从制造所采用的材料上对数控加工刀具的分类 1)高速钢刀具。 2)硬质合金刀具。 3)陶瓷刀具。 4)立方氮化硼刀具。 5)金刚石刀具。 (3)从结构上对数控加工刀具的分类 1)整体式。 2)镶嵌式。
30
第二节 数控加工工艺系统
3)减振式。 4)内冷式。 5)特殊形式。 (4)特殊型刀具 特殊型刀具有带柄自紧夹头刀柄、强力弹 簧夹头刀柄、可逆式(自动反向)攻螺纹夹头刀柄、增速夹头 刀柄、复合刀具和接杆类等。 2.数控加工刀具的特点 1)刀片及刀柄高度通用化、规格化、系列化。 2)刀片或刀具的寿命及经济寿命指标合理化。 3)刀具或刀片几何参数和切削参数规范化、典型化。
22
第一节 基 本 概 念
2)检测反馈装置的影响。 3)刀具误差的影响。 3.提高加工精度的工艺措施 (1)减小原始误差法 这是生产中应用较广的一种基本方法。 (2)转移原始误差法 这种方法实质上是转移工艺系统的几 何误差、受力变形和热变形等。 (3)补偿原始误差法 这是人为地制造出一种新的误差,去 抵消原来工艺系统中的原始误差。
图2-3 多工位加工 6
第一节 基 本 概 念
四、生产纲领和生产类型 1.生产纲领
2.生产类型 (1)单件生产 单件生产是指产品品种多,而每一种产品的 结构、尺寸不同,且产量很少,各个工作地点的加工对象 经常改变,且很少重复的生产类型。 (2)大量生产 大量生产是指产品数量很大,大多数工作地 点长期地按一定节拍进行某一个零件的某一道工序的加工。
《数控加工工艺与编程》教案

《数控加工工艺与编程》教案全套第一章:数控加工概述1.1 课程目标了解数控加工的定义、特点和分类掌握数控系统的组成及工作原理理解数控加工的基本过程1.2 教学内容数控加工的定义和发展历程数控加工的特点和应用领域数控系统的组成和工作原理数控加工的基本过程和操作步骤1.3 教学方法讲授法:讲解数控加工的定义、特点和分类,数控系统的组成及工作原理演示法:展示数控加工过程和操作步骤实践法:学生动手操作数控机床1.4 教学资源数控机床:用于展示数控加工过程和操作步骤PPT课件:展示教学内容和实例1.5 教学评价课堂问答:检查学生对数控加工概念的理解操作演练:评估学生对数控机床操作的熟练程度第二章:数控加工工艺掌握数控加工工艺的基本概念和方法了解数控加工工艺参数的选择和优化理解数控加工刀具的选择和使用方法2.2 教学内容数控加工工艺的基本概念和方法数控加工工艺参数的选择和优化数控加工刀具的选择和使用方法数控加工工艺实例分析2.3 教学方法讲授法:讲解数控加工工艺的基本概念和方法,数控加工工艺参数的选择和优化,数控加工刀具的选择和使用方法案例分析法:分析数控加工工艺实例实践法:学生动手操作数控机床,实践数控加工工艺的应用2.4 教学资源数控机床:用于实践数控加工工艺的应用PPT课件:展示教学内容和实例数控加工工艺案例:用于案例分析2.5 教学评价课堂问答:检查学生对数控加工工艺概念和方法的理解操作演练:评估学生对数控加工工艺应用的熟练程度第三章:数控编程基础掌握数控编程的基本概念和方法了解数控编程的指令系统和编程规则掌握数控编程的基本语句和功能指令3.2 教学内容数控编程的基本概念和方法数控编程的指令系统和编程规则数控编程的基本语句和功能指令数控编程实例分析3.3 教学方法讲授法:讲解数控编程的基本概念和方法,数控编程的指令系统和编程规则,数控编程的基本语句和功能指令案例分析法:分析数控编程实例实践法:学生动手操作数控机床,实践数控编程的应用3.4 教学资源数控机床:用于实践数控编程的应用PPT课件:展示教学内容和实例数控编程案例:用于案例分析3.5 教学评价课堂问答:检查学生对数控编程概念和方法的理解操作演练:评估学生对数控编程应用的熟练程度第四章:数控编程实例分析掌握数控编程实例的基本方法和步骤了解数控编程实例的类型和特点掌握数控编程实例的分析和优化方法4.2 教学内容数控编程实例的基本方法和步骤数控编程实例的类型和特点数控编程实例的分析和优化方法数控编程实例分析实例4.3 教学方法讲授法:讲解数控编程实例的基本方法和步骤,数控编程实例的类型和特点,数控编程实例的分析和优化方法案例分析法:分析数控编程实例实践法:学生动手操作数控机床,实践数控编程实例的应用4.4 教学资源数控机床:用于实践数控编程实例的应用PPT课件:展示教学内容和实例数控编程实例案例:用于案例分析4.5 教学评价课堂问答:检查学生对数控编程实例的基本方法和步骤的理解操作演练:评估学生对数控编程实例应用的熟练程度第五章:数控加工仿真与操作掌握数控加工仿真的基本方法和步骤了解数控加工仿真的作用和意义掌握数控机床的操作方法和技巧5.2 教学内容数控加工仿真的基本方法和步骤数控加工仿真的作用和意义数控机床的操作方法和技巧数控加工仿真实例分析第六章:数控编程软件的使用6.1 课程目标掌握数控编程软件的基本功能和使用方法了解数控编程软件的类型和特点掌握数控编程软件的操作步骤和技巧6.2 教学内容数控编程软件的基本功能和使用方法数控编程软件的类型和特点数控编程软件的操作步骤和技巧数控编程软件实例操作6.3 教学方法讲授法:讲解数控编程软件的基本功能和使用方法,数控编程软件的类型和特点,数控编程软件的操作步骤和技巧演示法:展示数控编程软件的操作步骤和实例实践法:学生动手操作数控编程软件6.4 教学资源数控编程软件:用于实践数控编程软件的操作PPT课件:展示教学内容和实例数控编程软件操作实例:用于实践操作6.5 教学评价课堂问答:检查学生对数控编程软件的基本功能和使用方法的理解操作演练:评估学生对数控编程软件操作的熟练程度第七章:数控加工质量控制7.1 课程目标掌握数控加工质量控制的基本概念和方法了解数控加工质量的影响因素掌握数控加工质量的检测和优化方法7.2 教学内容数控加工质量控制的基本概念和方法数控加工质量的影响因素数控加工质量的检测和优化方法数控加工质量控制实例分析7.3 教学方法讲授法:讲解数控加工质量控制的基本概念和方法,数控加工质量的影响因素,数控加工质量的检测和优化方法案例分析法:分析数控加工质量控制实例实践法:学生动手操作数控机床,实践数控加工质量控制的应用7.4 教学资源数控机床:用于实践数控加工质量控制的应用PPT课件:展示教学内容和实例数控加工质量控制案例:用于案例分析7.5 教学评价课堂问答:检查学生对数控加工质量控制的基本概念和方法的理解操作演练:评估学生对数控加工质量控制应用的熟练程度第八章:数控加工故障分析与维护8.1 课程目标掌握数控加工故障的基本概念和分类了解数控加工故障的原因和影响掌握数控加工故障的分析方法和维护技巧8.2 教学内容数控加工故障的基本概念和分类数控加工故障的原因和影响数控加工故障的分析方法和维护技巧数控加工故障实例分析8.3 教学方法讲授法:讲解数控加工故障的基本概念和分类,数控加工故障的原因和影响,数控加工故障的分析方法和维护技巧案例分析法:分析数控加工故障实例实践法:学生动手操作数控机床,实践数控加工故障分析与维护的应用8.4 教学资源数控机床:用于实践数控加工故障分析与维护的应用PPT课件:展示教学内容和实例数控加工故障分析与维护案例:用于案例分析8.5 教学评价课堂问答:检查学生对数控加工故障的基本概念和分类的理解操作演练:评估学生对数控加工故障分析与维护应用的熟练程度第九章:数控加工技术的发展趋势9.1 课程目标掌握数控加工技术的发展历程和现状了解数控加工技术的未来发展趋势掌握数控加工技术的发展对行业的影响9.2 教学内容数控加工技术的发展历程和现状数控加工技术的未来发展趋势数控加工技术的发展对行业的影响数控加工技术发展实例分析9.3 教学方法讲授法:讲解数控加工技术的发展历程和现状,数控加工技术的未来发展趋势,数控加工技术的发展对行业的影响案例分析法:分析数控加工技术发展实例实践法:学生动手操作数控机床,实践数控加工技术应用9.4 教学资源数控机床:用于实践数控加工技术应用PPT课件:展示教学内容和实例数控加工技术发展案例:用于案例分析9.5 教学评价课堂问答:检查学生对数控加工技术发展历程和现状的理解操作演练:评估学生对数控加工技术应用的熟练程度第十章:综合练习与实训10.1 课程目标综合运用所学知识进行数控加工工艺与编程的实践操作重点和难点解析:1. 第一章至第五章:数控加工的基本概念、工艺、编程和仿真操作是基础知识点,需要重点关注。
第2章 数控加工基础(第二版)习题册 参考答案

第二章数控加工工艺设计一、填空题:1、数控加工编程任务书数控加工工序卡数控加工刀具明细表2、辅具刃具及切削参数切削液3、刀具明细表4、连接点5、节点6、确定控制其尺寸精度7、合理选择机床、刀具及切削用量8、一次装夹中9、同一把刀具10、加工路线11、缩短加工路线12、最后一次走刀中13、切向14、主轴转速背吃刀量进给速度15、小于16、常规模块化17、车削镗铣钻削18、尖形圆弧形成形19、直线形切削刃20、刀刃圆心21、光滑连接(凹形)的成型面22、样板刀刃23、小半径圆弧螺纹24、成形25、可转位标准化26、7∶2427、刀柄模块中间连接模块刀头模块28、粗基准精基准粗基准精基准29、不加工表面重复使用30、设计基准装配基准重合31、通用专用组合随行二、判断题:1.×2.√3.√4.×5. ×6.√7.√8.√9.×10.√11.×12.√13.×14.×15.×16.√17. ×18.×19.×20.√三、选择题:1.D2.D3.B4.A5.C6.A7.A8.B9.A10.D11.A12.C13.C14.A15.A16.C四、名词解释:1、数控加工程序单数控加工程序单是编程员根据加工工艺,经过数值计算,按照机床特点的指令代码编制的,它是记录数控加工工艺过程、工艺参数、位移数据的清单。
2、加工路线在数控加工中,刀具刀位点相对于工件运动的轨迹称为加工路线。
3、基点构成零件轮廓的几何要素之间的连接点称为基点。
4、节点用直线段或圆弧段去逼近非圆曲线,逼近线段与被加工曲线的交点称为节点。
5、粗基准以毛坯表面作为基准面的基准称为粗基准。
6、精基准以已加工过的表面作为基准面的基准称为精基准。
五、简答题1、常用的数控加工工艺文件包括哪些?答、不同的数控机床,工艺文件的内容有所不同,主要包括编程任务书、数控加工工序卡、数控加工刀具明细表、数控加工程序单等。
课件-数控加工工艺基本知识

(1)按夹具的使用特点分类
根据夹具在不同生产类型中的通用特性,机床夹具
第
可分为通用夹具、专用夹具、可调夹具、组合夹具和
二
拼装夹具5大类。
章
1)通用夹具
数 控 工
已经标准化的可加工一定范围内不同工件的夹具,称 为通用夹具,其结构、尺寸已规格化,而且具有一定
艺 通用性,如三爪自定心卡盘、机床用平口虎钳、四爪
艺 基
数控车床使用的刀具从切削方式上分为圆柱表面切削刀具、
本 端面切削刀具和中心孔类刀具3类。
知
识
2019/10/9
现代数控技术
9
第 二 章
数 控 工 艺 基 本 知 识
2019/10/9
现代数控技术
10
第 二 章
数 控 工 艺 基 本 知 识
2019/10/9
现代数控技术
11
2)钻削刀具
分小孔、短孔、深孔、攻螺纹、扩孔和铰孔等。
2019/10/9
现代数控技术
7
数控车刀
第 二 章
数 控 工 艺 基 本 知 识
2019/10/9
现代数控技术
8
在模块化车削工具系统中,刀盘的联接以齿条式柄体联接为
多,而刀头与刀体的联接是“插入快换式系统”。它既可以
第 二
用
章 于外圆车削又可用于内孔镗削,也适用于车削中心的自动换
数 刀系统。
控
工
第 二
4) 铣削刀具
章
a 面铣刀
数 控
面铣刀主要用于加工较大的平面。如图1-7所示,面铣刀
工 艺
圆周表面和端面上都有切削刃,圆周表面的切削刃为主
基
切削刃,端面切削刃为副切削刃。面铣刀多制成套式镶
- 1、下载文档前请自行甄别文档内容的完整性,平台不提供额外的编辑、内容补充、找答案等附加服务。
- 2、"仅部分预览"的文档,不可在线预览部分如存在完整性等问题,可反馈申请退款(可完整预览的文档不适用该条件!)。
- 3、如文档侵犯您的权益,请联系客服反馈,我们会尽快为您处理(人工客服工作时间:9:00-18:30)。
数控机床选用三因素
• 1)要保证加工零件的技术要求,加工出 合格的产品。 • 2)有利于提高生产率。 • 3)能够降低生产成本(加工费用)。
2.2.2零件的工艺分析
• 数控加工工艺性分析涉及面很广,在此 仅从数控加工的可能性和方便性两方面 加以分析。
(一)零件图样上尺寸数据的给出应符合编程方便的原则
第2章 数控加工工艺基础
2.1数控加工工艺概述
• 数控加工就是根据零件图样及工艺要求等原始 条件,编制零件数控加工程序,并输入到数控 机床的数控系统,以控制数控机床中刀具与工 件的相对运动,从而完成零件的加工。 • 虽然数控加工与传统的机械加工相比,在加工 的方法和内容上有许多相似之处,但由于采用 了数字化的控制形式和数控机床,许多传统加 工过程中的人工操作被计算机和数控系统的自 动控制所取代。
以加工中心为例划分工序
• 1)同一表面按粗加工、半精加工、精加工依次完成,或全部加工 表面按粗、精加工分开进行,前者较适合尺寸精度要求较高的零 件,后者较适合位置精度要求较高的表面。 • (2)对于既有铣面又有镗孔的零件,可按“先面后孔”的原则划 分工步,即先铣面后镗孔。因为铣削时切削力较大,工件易发生 变形,先铣面后镗孔,使其有一段时间恢复,可减少由于变形引 起的对孔的精度的影响,从而提高孔的加工质量。反之铣镗孔后 铣面,则由于铣削时在孔口极易产生飞边、毛刺,导致孔的精度 下降。 • (3)按所用刀具划分工步。某些机床工作台回转时间比刀具交换 时间短,可采用按刀具划分工步,以减少换刀次数,提高加工效 率。
• •
(二)零件各加工部位的结构工艺性应符合数控加工的特点
• 1.零件的内腔和外形最好采用统一的几何类型和尺寸。这样可以 减少刀具规格和换刀次数,使编程方便,生产效益提高。 • 2.内槽圆角的大小决定着刀具直径的大小,因而内槽圆角半径不 应过小,否则刀具刚性差。零件工艺性的好坏与被加工轮廓的高 低、转接圆弧半径的大小等有关。 • 3.零件铣削底平面时,槽底圆角半径r不应过大。 • 4.应采用统一的基准定位。在数控加工中,若没有统一基准定位, 会因工件的重新安装而导致加工后的两个面上轮廓位置及尺寸不 协调现象。因此要避免上述问题的产生,保证两次装夹加工后其 相对位置的准确性,应采用统一的基准定位。
2.2数控加工工艺分析的一般步骤
• 程序编制人员在进行工艺分析时,要有 机床说明书、编程手册、切削用量表、 标准工具、夹具手册等资料,根据被加 工工件的材料、轮廓形状、加工精度等 选用合适的机床,制定加工方案,确定 零件的加工顺序,各工序所用刀具,夹 具和切削用量等。此外,编程人员应不 断总结、积累工艺分析方面的实际经验, 编写出高质量的数控加工程序。
具体步骤
阅 读 零 件
工 艺 分 析
制 定 工 艺
数 控 编 程
程 序 传 输
图2-1 数控加工过程
• 第一步:阅读零件图纸,充分了解图纸的技术要求,如尺寸精度、形位 公差、表面粗糙度、工件的材料、硬度、加工性能以及工件数量等; • 第二步:根据零件图纸的要求进行工艺分析,其中包括零件的结构工艺 性分析、材料和设计精度合理性分析、大致工艺步骤等; • 第三步:根据工艺分析制定出加工所需要的一切工艺信息——如:加工 工艺路线、工艺要求、刀具的运动轨迹、位移量、切削用量(主轴转速、 进给量、吃刀深度)以及辅助功能(换刀、主轴正转或反转、切削液开 或关)等,并填写加工工序卡和工艺过程卡; • 第四步:根据零件图和制定的工艺内容,再按照所用数控系统规定的指 令代码及程序格式进行数控编程; • 第五步:将编写好的程序通过传输接口或直接通过MDI操作面板,输入到 数控机床的数控装置中。调整好机床并调用该程序后,就可以加工出符 合图纸要求的零件。 • 从数控加工过程可以看出,工艺分析和制定加工工艺在数控加工中起到 了关键的作用,直接决定了数控加工的好坏与成败。
2.2.4工序与工步的划分
• 1.工序的划分 • 2.工步的划分
1.工序的划分
• 与普通机床相比,数控机床加工工序一 般比较集中,在一次装夹中尽可能完成 大部分或全部工序。首先应根据零件图 样,考虑被加工零件是否可以在一台数 控机床上完成整个零件的加工工作,若 不能则应决定其中哪一部分在数控机床 上加工,哪一部分在普通机床上加工, 即对零件的加工工序进行划分。
2.2.3加工方法与加工方案的确定
• 1.加工方法的选择 • 2.加工方案确定的原则
1.加工方法的选择
• 加工方法的选择原则是保证零件的尺寸精度、形状位 置精度和表面粗糙度的要求。由于获得同一级精度及 表面粗糙度的加工方法一般有许多,因而在实际选择 时,要结合零件的形状、尺寸大小和热处理要求等全 面考虑。例如,对于IT7级精度的孔采用镗削、铰削、 磨削等加工方法均可达到精度要求,但箱体上的孔一 般采用镗削或铰削,而不宜采用磨削。一般小尺寸的 箱体孔选择铰孔,当孔径较大时则应选择镗孔。此外, 还应考虑生产率和经济性的要求,以及工厂的生产设 备等实际情况。常用加工方法的经济加工精度及表面 粗糙度可查阅有关工艺手册。
数控机床的工序划分的方式 • • • • (1)、刀具集中分序法 (2)、粗、精加工分序法 (3)、加工部位分序法 (4)、零件装夹分序法
2.工步的划分
• 工步的划分主要从加工精度和效率两方 面考虑。合理的加工工艺,不仅要保证 加工出符合图纸要求的零件,而且要使 机床的功能得到充分发挥,在一个工序 内往往要采用不同的刀具和切削用量, 对不同的表面进行加工。为了便于分析 和描述较复杂的工序,在工序又内细分 为工步。
2、不适合数控加工的内容
• (1)占机调整时间长。如以毛坯的粗基准定 位加工第一个精基准,需用专用工装协调的内 容。 • (2)加工部位分散,需要多次安装、设置原 点。这时,采用数控加工很麻烦,效果不明显, 可安排通用机床补加工; • (3)按某些特定的制造依据(如样板等)加 工的型面轮廓。主要原因是获取数据困难,易 于与检验依据发生矛盾,增加了程序编制的难 度。
2.2.1数控机床的选用
• 选择数控机床前应了解数控机床适宜加 工的内容 • 1、适合数控加工的内容 2、不适合数控加工的内容
1、适合数控加工的内容
• (1)加工精度要求高,形状、结构复杂, 尤其是具有复杂曲线、曲面轮廓的零件。 • (2)具有不开敞内腔的箱体或壳体零件。 • (3)通用机床无法加工的内容应作为数控 加工优先选择内容。 • (4)虽通用机床能加工但劳动强度大,效 率低,而数控机床加工却明显具备效率和 经济优势的,如集铣、镗、钻、铰、攻螺 纹等多种工序于一体的零件。
2.2.6刀具选择与切削用量的确定
• 1.刀具的选择• 2.切削用量的确定
1.刀具的选择
• 数控机床所用刀具要求切削性能好、精度高、可靠性高、耐用度高、断 屑及排屑性能好,装夹调整方便等,合理选用既能提高加工效率又能提 高产品质量。 数控机床一般优先选用标准刀具,必要时也可采用各种高生产率的复合 刀具及其它一些专用刀具。此外,根据实际情况,尽可能选用各种先进 刀具如可转位刀具,整体硬质合金刀具,陶瓷刀具等,以适应数控加工 耐用、稳定、易调、可换等要求。所选刀具的类型、规格和精度等级应 符合加工能力要求,刀具材料应与工件材料相适应。由于数控加工工件 一般较为复杂,选择刀具时还应特别注意刀具的形状,保证在切削加工 过程中刀具不与工件轮廓发生干涉。 在选择好刀具后,要把刀具的名称、规格、代号以及要加工的部位记录 下来,并填入相应的工艺文件,供编程时使用。
2.1.2数控加工工艺分析的 主要内容
• 数控加工工艺的制定包括较多的内容,而数控加工工艺分析则主 要包括以下内容: • (1)选择适合在数控机床上加工的零件,确定数控机床加工内容。 (2)分析被加工零件图样,明确数控加工的工艺内容及技术要 求,在此基础上确定零件的加工方案,制定数控加工工艺路线, 如工序的划分、加工顺序的安排、与传统加工工序的衔接等。 (3)设计数控加工工序。如工步的划分、零件的定位与夹具的选 择、刀具的选择、切削用量的确定等。 (4)调整数控加工工序的程序。如对刀点、换刀点的选择、加工 路线的确定、刀具的补偿。 (5)分配数控加工中的容差。 (6)处理数控机床上的部分工艺指令,编制工艺文件。
• 总之,工序与工步的划分要根据具体零 件的结构特点、工艺性、技术要求以及 机床的功能等实际情况综合考虑。
2.2.5零件的安装与夹具的选择
• 1.定位安装的基本原则 • 2.选择夹具的基本原则
1.定位安装的基本原则
• 在数控机床上加工零件时,定位安装的基本原 则与普通机床相同,要合理选择定位基准和夹 紧方案,为了提高数控机床的效率,在确定定 位基准与夹紧方案时应注意下列几点: • (1)力求设计、工艺与编程计算的基准统一。 • (2)尽量减少装夹次数,尽可能在一次定位 装夹后,加工出全部待加工表面。 • (3)避免采用占用机时的人工调整式加工方 案,以充分发挥数控机床的效能。
2.加工方案确定的原则
• 确定加工方案时,首先应根据零件加工精度和 表面粗糙度的要求,初步确定为达到这些要求 所需要的加工方法。零件上比较精密表面的加 工,常常是过通粗加工、半精加工和精加工逐 步达到的。对这些表面仅仅根据质量要求选择 相应的最终加工方法是不够的,还应正确地确 定从毛坯到最终成形的加工方案。采用不同加 工方案所能达到的经济精度和表面粗糙度详见 表2.1
2.选择夹具的基本原则
• 数控加工的特点对夹具提出了两个基本要求:一是要保证 夹具的坐标方向与机床的坐标方向相对固定;二是要协调 零件和机床坐标系的尺寸关系。除此之外,还要考虑以下 四点: • (1)当零件加工批量不大时,应尽量采用组合夹具、可调 式夹具及其他通用夹具,以缩短生产准备时间、节省生产 费用。 • (2)在成批生产时才考虑采用专用夹具,并力求结构简单。 • (3)零件的装卸要快速、方便、可靠,以缩短机床的准备 时间。 • (4)夹具上各零部件应不妨碍机床对零件各表面的加工, 即夹具要开敞其定位、夹紧机构元件不能影响加工中的走 刀(如产生碰撞等)。