高速机车构架侧梁的焊接顺序
最新整理梁板安装施工工艺流程图.doc

梁板安装施工工艺图一、架桥机架梁一)工艺图二)架桥机架梁施工工艺说明1、场地准备架桥机在桥头路基上完成拼装。
路基要求平整、密实,2、架桥机拼装及试运行架桥机拼装程序为:测量定位→平衡对称拼装两侧主桁梁→安装前后联系框架、临时支撑→安装前、中、后支腿及中、后顶高支腿→铺设纵向轨道→安装起吊小车、液压系统、操作台、接通电源→检查调试初步运行。
架桥机安装完成以后应检查各部尺寸是否正确,各系统的运行是否正常,然后试运行。
3、架桥机前移架桥机试运行完成后开始架梁,首先架桥机空载前移,两起吊小车退至后支腿附近,收起前支腿就位,在盖梁上铺设横移轨道,然后将行走箱落在轨道上。
4、喂梁用自行式电动平车运梁,龙门吊将箱梁吊至电动平车上,再由电动平车将梁运至架桥机后跨内,两起吊小车将梁吊起。
5、支座安装箱梁架设前先施工支座,支座安装前应逐一检查其标高,符合设计规范要求后,在临时支座上用墨线弹出梁中心线,然后再检查梁跨是否符合设计要求。
6、落梁喂梁后,两起吊小车开始运梁,将梁运至架桥机前跨位置,横移架桥机,将梁运至待架梁支座的上方,使梁体中心线与支座中心线对正,然后下落就位。
梁体就位后用垂球吊线法检查梁体安装垂直度,合格后再架设第二片梁。
7、架桥机前移第一孔梁的架设完成后,对架桥机进行检查,确认无故障后,将中、后顶高支腿顶起,中、后行走箱由横向转为纵向,中、后顶高支腿下落使行走箱落至纵向轨道上,两起吊小车退至后支腿附近,收起前支腿,铺设延伸轨道,架桥机前移就位,开始架设下一孔梁。
二、汽车吊架梁一)工艺筐图二)汽车吊架梁施工工艺说明1、场地准备平整场地,并修建临时便道,满足吊机行驶及吊梁需要。
场地准备完成后,吊机在适当的位置就位。
2、梁体运输梁采用平板拖车运输至现场。
3、支座安装先测量放线,在墩台顶放出支座中心线,然后安装永久支座或临时支座。
4、架梁采用两台汽车吊吊装梁体,两台吊机各吊住梁的一端,同步提升将梁吊起架设安装,注意两台吊机应互相配合。
高速铁路6跨一联连续梁施工工法
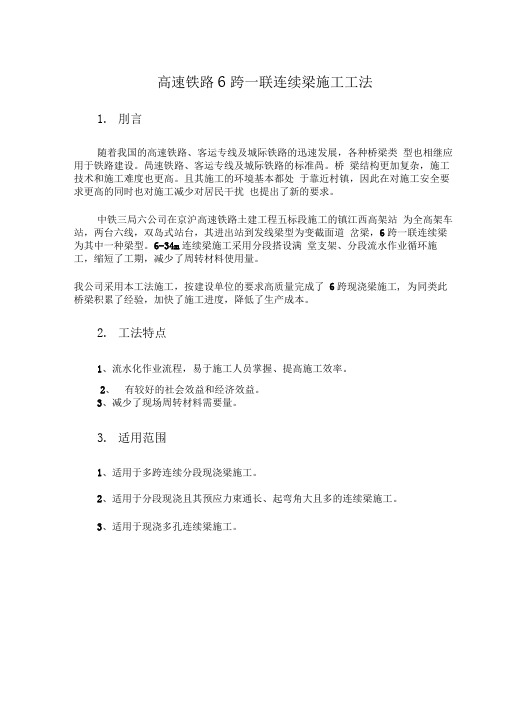
高速铁路6跨一联连续梁施工工法1.刖言随着我国的高速铁路、客运专线及城际铁路的迅速发展,各种桥梁类型也相继应用于铁路建设。
咼速铁路、客运专线及城际铁路的标准咼。
桥梁结构更加复杂,施工技术和施工难度也更高。
且其施工的环境基本都处于靠近村镇,因此在对施工安全要求更高的同时也对施工减少对居民干扰也提出了新的要求。
中铁三局六公司在京沪高速铁路土建工程五标段施工的镇江西高架站为全高架车站,两台六线,双岛式站台,其进出站到发线梁型为变截面道岔梁,6跨一联连续梁为其中一种梁型。
6-34m连续梁施工采用分段搭设满堂支架、分段流水作业循环施工,缩短了工期,减少了周转材料使用量。
我公司采用本工法施工,按建设单位的要求高质量完成了6跨现浇梁施工, 为同类此桥梁积累了经验,加快了施工进度,降低了生产成本。
2.工法特点1、流水化作业流程,易于施工人员掌握、提高施工效率。
2、有较好的社会效益和经济效益。
3、减少了现场周转材料需要量。
3.适用范围1、适用于多跨连续分段现浇梁施工。
2、适用于分段现浇且其预应力束通长、起弯角大且多的连续梁施工。
3、适用于现浇多孔连续梁施工。
4. 工艺原理4.1.工艺流程步骤一、对梁体施工投影范围内地基进行处理。
步骤二、搭设A 节段支架,并按120%梁体重量进行预压;安装 A 节段梁体混凝土;张拉并锚固B 节段纵向预应力钢束,拆除 A 节段支架。
I(S )步骤四、搭设C 节段支架,并按120%梁体重量进行预压,浇筑 C 节段梁体混凝土;张拉并锚固C 节段纵向预应力钢束,拆除B 节段支架。
tjv'i ———步骤五、搭设D 节段支架,并按120%梁体重量进行预压,浇筑 D 节VTj 1_- 段施工模板,绑扎钢筋,浇筑梁体混凝土;混凝土达到强度及龄期后,张步骤三、搭设B 节段支架,并按120%梁体重量进行预压,浇筑B 节7, "段段梁体混凝土;张拉并锚固D 节段纵向预应力钢束,拆除 C 节段支架。
构架侧-横梁全对接焊接结构设计与组焊工艺研究

摘 要 :通过 对 C R H 3 、 C R H 5型 车 、 城 轨 车 以及 2 0 9 系列 等 车 型 构 架 侧 粱 与 横 梁连 接 形 式 进 行 分
析, 提 出新 的 构 架侧 一 横 粱全 对接 接 头 形 式 的焊 接 结 构 , 并针对所设计 的全对接焊接 结构 , 给 出侧
粱、 横 梁及构架的组焊工艺。
关键词 : 横梁 ; 侧 梁; 对接 接 头 ; 构 架
中 图分 类 号 : U 2 7 0 . 6
文 献 标识 码 : B
1 构 架侧 一横 梁 连 接 形 式 介 绍
国产城 轨客 车和普 通铁 路客 车 的构 架侧 梁与 横
结构 外形不 连续 , 可 能 导 致 承载 能 力 和抗 疲 劳 能 力
冷 热 工 艺
文章编号 : 1 0 0 7 40 3 4 ( 2 0 1 3 ) 0 4 _ 0 0 1 O - 0 2
机车车辆工艺 第 4期 2 0 1 3年 8月
构 架 侧 一横 粱 全 对 接 焊 接 结 构 设 计 与 组 焊 工 艺 研 究
孙 志 鹏 ,常 力 ,宫 平
系列 铁路 客车 构架 , 如 图 2所 示 。这 2种 连接 形 式
均 为 T型接 头组 合 焊缝 形 式 , 焊接 接 头 处 容 易 出现
应力 集 中 , 同时焊接 填充 量也 比较 大 , 焊接 引起 的变
形也 大 。
图3 C R H 5型 车构 架 侧 一 图4 C R H3 型 车 构架 侧 一
鉴 于 以上侧 一横 梁连 接 形 式存 在 的不 足 , 有 必 要设 计一 种新 的侧 一横 梁 连接 形 式 , 以适 应 于 当前 及未 来 轨道车 辆转 向架 构架结 构 的需 要 。
高铁转向架七部焊接法
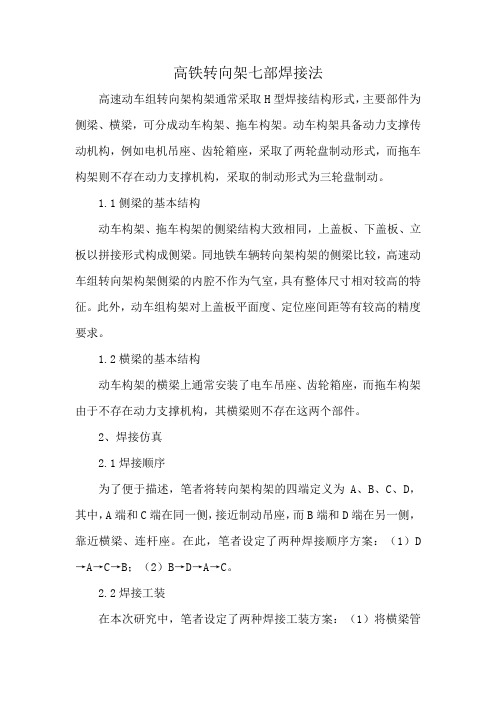
高铁转向架七部焊接法高速动车组转向架构架通常采取H型焊接结构形式,主要部件为侧梁、横梁,可分成动车构架、拖车构架。
动车构架具备动力支撑传动机构,例如电机吊座、齿轮箱座,采取了两轮盘制动形式,而拖车构架则不存在动力支撑机构,采取的制动形式为三轮盘制动。
1.1侧梁的基本结构动车构架、拖车构架的侧梁结构大致相同,上盖板、下盖板、立板以拼接形式构成侧梁。
同地铁车辆转向架构架的侧梁比较,高速动车组转向架构架侧梁的内腔不作为气室,具有整体尺寸相对较高的特征。
此外,动车组构架对上盖板平面度、定位座间距等有较高的精度要求。
1.2横梁的基本结构动车构架的横梁上通常安装了电车吊座、齿轮箱座,而拖车构架由于不存在动力支撑机构,其横梁则不存在这两个部件。
2、焊接仿真2.1焊接顺序为了便于描述,笔者将转向架构架的四端定义为A、B、C、D,其中,A端和C端在同一侧,接近制动吊座,而B端和D端在另一侧,靠近横梁、连杆座。
在此,笔者设定了两种焊接顺序方案:(1)D →A→C→B;(2)B→D→A→C。
2.2焊接工装在本次研究中,笔者设定了两种焊接工装方案:(1)将横梁管固定并压紧;(2)将侧梁四个帽筒进行固定。
2.3焊接仿真方案设定了两种焊接顺序方案及焊接工装方案后,笔者进行交叉组合,得到四种仿真方案:(1)采用第一种焊接顺序方案和第一种焊接工装方案;(2)采用第一种焊接顺序方案和第二种焊接工装方案;(3)采用第二种焊接顺序方案和第一种焊接工装方案;(4)采用第二种焊接顺序方案和第二种焊接顺序方案。
3、焊接仿真的建模3.1构建仿真模型之所以进行焊接仿真,是因为需要探究焊接顺序对焊接变形的影响。
仿真内容为横梁管和横向止档之间的阻焊、制动衡量和制动横梁之间的焊接。
根据其焊缝分布特点,笔者决定采用实体—壳单元混合模型构建模型。
完成模型构建后,笔者对各个散热单元进行了调整。
3.2仿真结构分析利用了平台对四种焊接方案进行分析。
分析完毕后,发现以下几点:(1)第三种方案造成的变形最大,第二种方案造成的变形最小,前者采用的焊接顺序为B→D→A→C,而焊接工装方案为固定横梁管,后者采用的焊接顺序为D→A→C→B,焊接工装方案为固定帽筒;(2)第一种方案和第二种方案产生的横向变形和纵向变形相对较小,而这两种方案的焊接顺序均为D→A→C→B;(3)四种方案造成变形的位置基本一致。
二建公路每跨架梁顺序规定
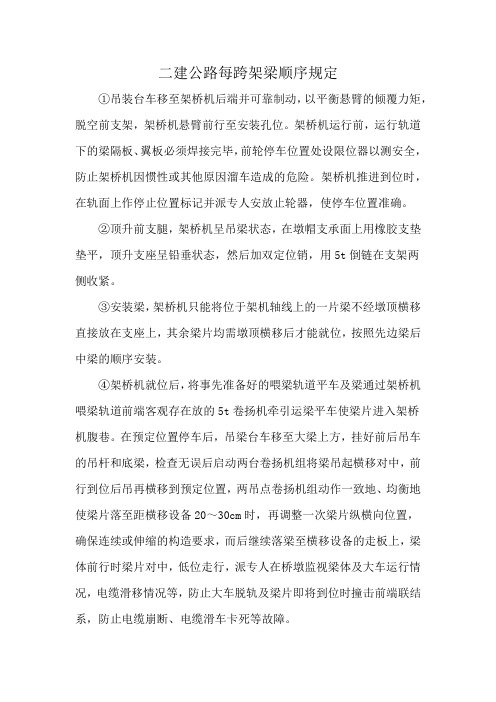
二建公路每跨架梁顺序规定①吊装台车移至架桥机后端并可靠制动,以平衡悬臂的倾覆力矩,脱空前支架,架桥机悬臂前行至安装孔位。
架桥机运行前,运行轨道下的梁隔板、翼板必须焊接完毕,前轮停车位置处设限位器以测安全,防止架桥机因惯性或其他原因溜车造成的危险。
架桥机推进到位时,在轨面上作停止位置标记并派专人安放止轮器,使停车位置准确。
②顶升前支腿,架桥机呈吊梁状态,在墩帽支承面上用橡胶支垫垫平,顶升支座呈铅垂状态,然后加双定位销,用5t倒链在支架两侧收紧。
③安装梁,架桥机只能将位于架机轴线上的一片梁不经墩顶横移直接放在支座上,其余梁片均需墩顶横移后才能就位,按照先边梁后中梁的顺序安装。
④架桥机就位后,将事先准备好的喂梁轨道平车及梁通过架桥机喂梁轨道前端客观存在放的5t卷扬机牵引运梁平车使梁片进入架桥机腹巷。
在预定位置停车后,吊梁台车移至大梁上方,挂好前后吊车的吊杆和底梁,检查无误后启动两台卷扬机组将梁吊起横移对中,前行到位后吊再横移到预定位置,两吊点卷扬机组动作一致地、均衡地使梁片落至距横移设备20~30cm时,再调整一次梁片纵横向位置,确保连续或伸缩的构造要求,而后继续落梁至横移设备的走板上,梁体前行时梁片对中,低位走行,派专人在桥墩监视梁体及大车运行情况,电缆滑移情况等,防止大车脱轨及梁片即将到位时撞击前端联结系,防止电缆崩断、电缆滑车卡死等故障。
⑤墩顶横移就位:在导梁下弦杆上装设液压泵站供油,采用液压滚道系统分次顶推的方法实现预制梁在墩顶上的横移,其主要作法是,浆滚杠用钢框固定起来作为滚架,放在沿盖梁通长布置分段拼装在滚道上,滚道在盖梁支撑垫石上位置留槽。
滚架上方放置走板,走板上的销座甲与走道上的销座乙用液压顶杠连接,以销座甲作为反力架,形成液压滚道系统作为架桥机附属设置,梁落在走板上后,两边架斜撑并用木楔打紧,根据每片梁横移距离,分次在滚道上调整销座甲的位置至使梁片横移就位。
⑥落梁换支座:利用液压框顶进横移。
高速铁路框架桥施工技术交底
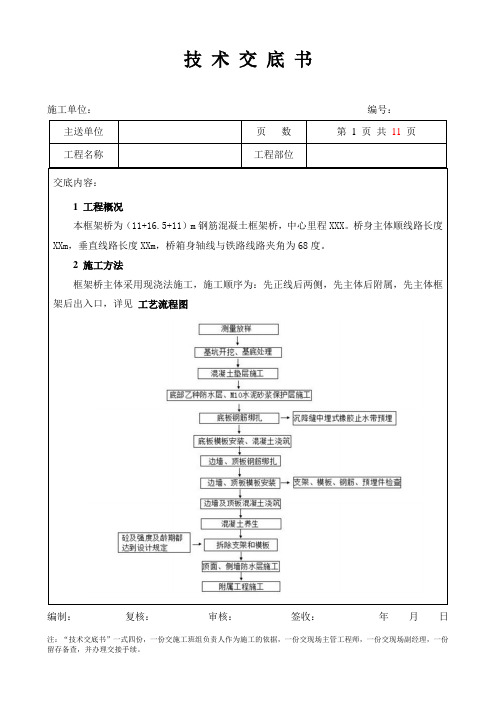
施工单位:编号:交底内容:1 工程概况本框架桥为(11+16.5+11)m钢筋混凝土框架桥,中心里程XXX。
桥身主体顺线路长度XXm,垂直线路长度XXm,桥箱身轴线与铁路线路夹角为68度。
2 施工方法框架桥主体采用现浇法施工,施工顺序为:先正线后两侧,先主体后附属,先主体框架后出入口,详见工艺流程图编制:复核:审核:签收:年月日施工单位:编号:编制:复核:审核:签收:年月日施工单位:编号:边墙下部钢筋绑扎→底板模板安装和边墙下部及下肋内模板安装→底板、边墙下部混凝土浇筑→混凝土养护及拆除模板。
边坡喷锚示意图2.4 钢筋安装钢筋由钢筋加工场集中制作,现场临时存放钢筋的场地必须保证平整、干燥。
存放时,需下垫上盖,以免受潮或沾上泥土。
按照已布设的桥身轴线控制桩,把框架桥的墙身位置在垫层顶面弹出墨线。
墙身的轮廓线,轴线误差控制在5mm以内。
(1)钢筋现场绑扎时,其各部位尺寸和数量应符合规范及设计要求,骨架绑扎时增加点焊数量,以免变形。
为保证钢筋保护层厚度,采取在钢筋上绑扎与结构物同标号的砼垫块支垫。
(2)因框架箱身浇筑分二次,第一次浇至边墙下梗肋顶部,且在浇筑底板时,墙体竖向钢筋应同时安装完毕,墙体横向钢筋应安装至混凝土浇筑面以上至少三排。
编制:复核:审核:签收:年月日施工单位:编号:编制:复核:审核:签收:年月日施工单位:编号:编制:复核:审核:签收:年月日施工单位:编号:编制:复核:审核:签收:年月日施工单位:编号:底板砼采用一次浇捣成型,确保底板抗渗要求。
在混凝土浇筑至底板下梗肋上10cm 位置的时候,待混凝土初凝前进行拉毛处理,以保证与上部混凝土的连接。
砼应分层、整体、连续浇筑,逐层采用插人式振捣器振捣密实。
箱身砼浇筑示意图(3)侧墙墙身浇筑①墙体浇筑前,用清水湿润第一次浇筑混凝土的混凝土表面,同时在接触面上涂一层纯水泥浆,再浇筑上部砼。
②墙体混凝土浇筑时,料斗的下口距离浇筑底面不得大于2m,浇筑时要严格控制混凝土的入模速度,且应分层浇捣,每层浇筑厚度控制在30cm。
高速列车碳钢焊接工艺流程之组装施焊

碳钢焊接工艺流程之组装施焊
二、侧梁组焊步组装施焊
2、TIG焊完成制动器吊座与上盖板的打底焊,焊前预热。
碳钢焊接工艺流程之组装施焊
3、MT检查、(ET)内窥镜检查TIG打底焊道。
碳钢焊接工艺流程之组装施焊
4、安装引弧/收弧板,焊接完成侧梁底面4道对接焊缝,焊前铸件预热至150℃以上。
碳钢焊接工艺流程之组装施焊
一、CRH1动车组 转向架构架
包含侧梁、横梁、 纵向辅助梁、外端 梁(动车,M车)、 抗蛇行减振器座、 抗侧滚扭杆座、电 机吊座、齿轮箱吊 座、安全绳吊座、 横行减振器座、二 系垂向减振器座、 转臂定位销座等。
碳钢焊接工艺流程之组装施焊
碳钢焊接工艺流程之组装施焊
转向架构架侧梁的组焊步骤。
测量矫正的效果
碳钢焊接工艺流程之组装施焊
三、检测探伤、验收。 大多采用磁粉探伤(MT)、超声波探伤(UT)、射线检测(RT)、内窥镜检测
碳钢焊接工艺流程之组装施焊
四、吊运存放、进行下道工序。
侧梁存放
碳钢焊接工艺流程之组装施焊
构架整体组装, TIG打底焊接 侧梁和横梁上 盖板的对接焊 缝
碳钢焊接工艺流程之组装施焊
9、组焊空气弹簧支撑座,并完成垂向减震器座剩余焊缝。
碳钢焊接工艺流程之组装施焊
三、焊后矫正
在焊接过程中,会产生一定量的焊接变形,为了保证焊接质量,在焊接完毕之后应该 进行矫正,以消除焊接应力,减少焊接变形。此部件主要采用火焰矫正的方法来减少 变形。
碳钢焊接工艺流程之组装施焊
碳钢焊接工艺流程之组装施焊
5、安装引弧/收弧板,焊接完成端头与上盖板之间的对接焊缝,焊前铸件预热至150 度以上。
碳钢焊接工艺流程之组装施焊
焊接指导程序

1.边箱体的焊接顺序1)焊接边箱体支撑框架筋板图1:将①~④焊缝焊接完毕2)焊接边箱体两侧板与中央筋板(下部)焊接方向图2:将①~③焊缝按照焊接序号顺序由中心沿焊接方向焊接完毕(双数焊工双面同时施焊)3)焊接边箱体支撑框架(与底板焊接)焊接方向焊接方向焊接方向焊接方向图3:将①~②焊缝按照焊接序号顺序由中心沿焊接方向对称施焊4)焊接边箱体支撑框架(纵向)接方向焊接方向图4:将①~④焊缝按照焊接序号顺序由中心沿焊接方向对称施焊5)焊接边箱体支撑框架(与上板焊接)焊接方向焊接方向焊接方向焊接方向图5:将①~②焊缝按照焊接序号顺序由中心沿焊接方向对称施焊6)焊接边箱体两侧板与中央筋板(上部)焊接方向焊接方向图6:将①~③焊缝按照焊接序号顺序由中心沿焊接方向焊接完毕(双数焊工双面同时施焊)7)焊接边箱体的角铁加强筋图7:将①~⑧焊缝按照焊接序号顺序由分段中心沿焊接方向焊接完毕8)其余筋板按照对称位置由中心向两侧施焊2 中央箱体的焊接顺序1)焊接部分中央立柱(与底板焊接)图8:将①焊缝焊接完毕2)焊接中央箱体筋板(与底板焊接)图9:将①~⑧焊缝按照焊接中心对称顺序由焊缝中心沿焊接方向焊接完毕(双数焊工对称施焊)3)焊接中央箱体侧板(与底板焊接)图10:将①~④焊缝按照焊接序号顺序由中心沿焊接方向焊接完毕(双数焊工双面同时施焊)4) 焊接中央箱体筋板(与侧伴、部分中央立柱焊接)焊接方向焊接方向图11:将①~②焊缝按照中心对称位置沿焊接方向焊接完毕5)焊接中央箱体筋板(与上板焊接)图12:将①~⑧焊缝按照焊接中心对称顺序由焊缝中心沿焊接方向焊接完毕(双数焊工对称施焊)6)焊接部分中央立柱(与上板焊接)图13:将①焊缝焊接完毕7)焊接中央箱体侧板(与上板焊接)图14:将①~④焊缝按照焊接序号顺序由中心沿焊接方向焊接完毕(双数焊工双面同时施焊)8)焊接中央箱体筋板内的环板图15:将①焊缝按照中心对称位置焊接完毕。
钢梁工地焊接顺序

钢梁工地焊接顺序
一、焊接准备
在开始焊接之前,必须进行充分的准备工作。
这包括检查焊接设备是否正常,确认焊接材料(如焊条、焊丝等)的型号、规格和质量是否符合要求,以及确保工地的安全环境。
二、组装定位
钢梁的组装定位是确保焊接质量的关键步骤。
这一阶段涉及将钢梁的各个部分精确地组装在一起,并使用合适的固定装置(如夹具、支撑等)保持其位置。
组装定位的精度直接影响到最终焊接的质量。
三、焊接固定
在组装定位完成后,开始进行焊接固定。
这一步骤通常涉及使用焊接设备对钢梁的各个部分进行连接,以确保其在整个焊接过程中保持稳定。
四、焊缝质量检查
完成焊接固定后,需要对焊缝进行质量检查。
这一步骤是为了确保焊缝的强度、外观和连续性都满足要求。
如果发现任何缺陷或问题,需要进行修复或重新焊接。
五、热处理
在某些情况下,为了提高钢梁的力学性能或消除焊接过程中产生的应力,需要进行热处理。
这通常涉及将钢梁加热到特定的温度并保持一段时间,然后让其自然冷却。
六、防腐处理
完成焊接和热处理后,需要对钢梁进行防腐处理。
这可以包括涂覆防腐涂料、进行喷塑等,以增加钢梁的耐腐蚀性,延长其使用寿命。
七、质量验收
在完成所有焊接和防腐处理后,需要进行质量验收。
这一步骤是为了确认钢梁是否满足设计要求和使用性能。
如果发现任何问题,需要进行修复或调整。
八、整理资料
最后,需要整理所有与焊接过程相关的资料,如焊接工艺记录、质量检查记录等,以备后续的审计和查阅。
同时,这些资料也有助于对钢梁的质量进行追溯和管理。
构架侧梁焊接顺序与方向优化分析

构 架侧梁焊接顺序与方 向优化分析
赵 利 华 , 张 开林
( 南 交 通 大 学 牵 引 动力 国 家 重点 实验 室 ,四川 成 都 西 I 60 3 ) 1 0 1
摘
要 :构 架是 机 车 车辆 的重 要 承 载部 件 , 制 其侧 梁 的 焊 接 残余 变形 至关 重 要 。 以热 弹 塑 性 理 论 为 基 础 , 用 控 采
中 图分 类 号 :U2 0 6 T 0 7 . ; O4 4 文献标志码 பைடு நூலகம் A d i1 . 9 9 ji n 1 0 — 3 0 2 1 . 1 0 5 o :0 3 6 /.s . 0 18 6 . 0 2 0 . 0 s
An l ss o he Op i i a i n o e d n e e c n a y i n t tm z to f W l i g S qu n e a d W e di r c i n o h i e Be m fBo i a e l ng Di e to f t e S d a o g e Fr m
t e me s r d d t ,t e e r r b i g b l w . Rey n n t e a o e n me ia i u a i n mo e ,t k n h h a u e a a h ro en eo 7 l i g o h b v u rc lsm l t d l a i g t e o
i e e c n l i g die ton we e o i z d t r gh nu e i a i u a i n a d t p i u s he s ng s qu n e a d we d n r c i r ptmie h ou m rc lsm l to n he o tm m c me wa ob a n d.Theo i t ie ptmum c me wa omp r d wih t u r nts h me,t nd ng d f r a i n b i e uc d s he s c a e t hec r e c e hebe i e o m to e ng r d e a ut3 .Th ptm um c m e p o d sr la l he r tc lr f r nc s t o r lo l n e i u lde o m— bo 4 eo i s he r vi e e i b e t o e ia e e e e o c nt o fwedi g r s d a f r a i ns e e to ft l n e hn o y a d de e m i to o h e e ve f r a i n vo ume to ,s l c i n o he wedi g t c ol g n t r na in ft e r s r d de o m to l . Ke r s:sd e m ;nume ia i ul to y wo d ieb a rc lsm a i n;m e s r m e ;wedi e e ea i e to a u e nt l ng s qu nc nd d r c i n;o i ia i n l ptm z ton a a — y i ;we d ng r sdu lde o m a i n ss l i e i a f r to
高速列车铝合金焊接工艺流程之组装施焊
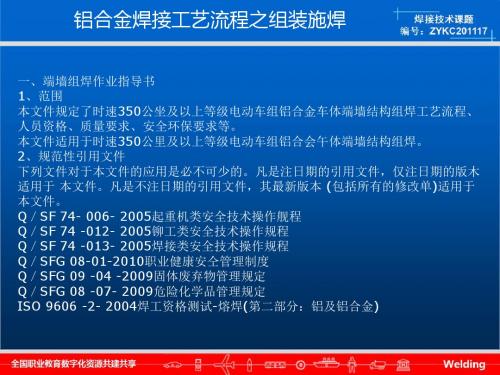
铝合金焊接工艺流程之组装施焊
3安装横向龙骨及纵向龙骨,然后使用压紧器压紧。 4清理氧化膜后进行定位焊、正式焊接。 5翻转。放置到盖板外侧焊缝组焊工作台上,将龙骨压紧,焊接外板与龙骨外侧的搭 接焊缝。 6打磨盖板骨架的焊缝。 6盖板调修 盖板调修见SFE12W-T-41-57001《端墙调修作业指导书》。 7大骨架(分体式)组焊 1大骨架(分体式)采用正组,即外侧的面朝上。组焊步骤:组装盖板与立柱横梁→ 组装外框→组焊大骨架,如图所示。 2将螺栓座于立柱眼孔对正,进行定位焊。 3用复合螺栓座和工艺螺栓将盖板与立柱和横梁固定在一起。 4组装外框,如图)所示。先步划线安装下端梁内的加强筋板、复合螺丝座等预理件。 然后将端墙下端粱、角支柱、端部弯梁、端顶弯梁组装,找正后用F卡钳和工艺木条与 工装压紧。 (1)调节端部弯梁两端与端顶弯梁、角支柱的弧线顺滑过渡。用卡弧样板测量角 支柱及端项弯梁,与样板闪缝应不大于2.5mm。 (2)使用不锈钢丝轮去除焊道两边20mm-30mm范围内的氧化膜,使表面露出 新亮金属光泽,进行定付焊。 (3)使用小锈钢缝刷清理定位焊缝的表而黑灰后正式焊接.
铝合金焊接工艺流程之组装施焊
铝合金焊接工艺流程之组装施焊
5使用天地轨吊车或天车翻转吊起外大框,正放到台位,依次清理焊根及氧化膜, 焊接反面的焊缝、清理焊接黑灰、打磨焊缝。 6将外框吊运到另一个端墙组装工作台。 7将盖板及立柱横梁的组合体,与外框进行组装,安装焊接小横粱,见图所示。 8打磨焊缝。 8大骨架(分体式)调修 大骨架(分体式)调修见SFEl2W -T -41 -57004《端墙调修作业指导书》。 9铺外板 1外板铺装采用正组点焊时反组。外板组装工作台 (允许临时用打平工作台,零件 安装作业台)。 2将骨架外侧朝上,清除骨架上杂物,使用小锈钢丝刷打磨骨架上待点焊部位。 3将外板两面的待焊部位画线,打磨该区域的氧化膜。 4铺放外板。找正位置后将外板的四周进行点固。 10外板点焊 1工装:电阻点焊机。外板电阻点焊时,车内侧朝上。
ZMA100型转向架构架侧梁焊接工艺

5 2 工 艺 放 量 及 焊 接 参 数 .
侧 梁主 焊缝 的焊接 参数见 表 2 。
图 3 侧 梁 总组 装 胎
2 3 侧 梁 附 件 组 装 胎 .
以立 板端 部 为横 向定位 基 准 , 板 内侧 面 为纵 立
向定 位基 准 , 向 以活动 螺栓 支撑 定位 ; 隔板 采用 垂 各
以下 盖板 两 端 + 6 2 0mm的 圆做 为定 位 基 准 , 定
位侧 梁体 ; 据侧 梁上 的 附件尺 寸 , 别设 计不 同 的 根 分
3 焊 接 工 艺
3 1 工 艺 放 量 .
分 焊 缝 成 型 不 好 , 部 焊 缝 有 咬边 情 况 。 局
() 2 无损 探 伤检 查 。对 焊 缝 进 行 10 磁 粉 探 0% 伤 检查 , 没有 发现裂 纹等缺 陷 。 () 3 宏观 金相 检查 。在 Z A10型构 架 侧 梁 不 M 0 同部位 割取 焊缝试 样 2 0件 并 编号 , 缝 经 加 工 、 焊 磨 削 、 光后 采用 3 % 硝 酸 酒 精 溶 液腐 蚀 , 腐 蚀 彻 抛 0 待 底 后用 清水 冲洗 , 风干后 照相 , 焊缝缺 陷见表 3 。
定位 部件 , 附件进 行定 位 。 对 上述 3个 工 装 的所 有 的定 位 装 置 采 用 活 动 装
专用 定位 装置 定 位 , 用 磁 铁 吸紧 。压 紧装 置 采 用 利
自制 通用 件 , 用 液压 系统 进 行 压 紧 。具 体 效 果 如 利
图 2所 示 。
收 稿 日期 :0 1—1 21 2—1 4 作 者 简 介 : 志 平 (9 1 陈 1 8 一) 男 , 程 师 , 科 。 , 工 本
转向架焊接构架制造工艺

转向架焊接构架制造工艺摘要:焊接工艺作为轨道车辆生产制造的核心技术,是衡量车辆装备制造能力的重要标志之一。
随着高速铁路的迅速发展和城铁车辆市场的扩大,原有的焊接制造工艺已不能满足生产提能、提质的要求。
进而使车辆的制造工艺面临新的挑战。
关键词:转向架;焊接构架;制造工艺转向架是机车的安全件之一。
而作为焊接部件的构架不仅是转向架其他部件的安装基础。
同时还要承受和传递机车在运行中产生的不同类型的动、静载荷。
是一个复杂交变载荷作用下的重要受力部件。
川因此。
其制造质量直接关系到整车运行的安全。
1构架难点(1)横梁部分:所有梁体在其上组装,横梁平面度对组装尺寸影响较大。
(2)侧梁部分:侧梁分为4部分,各部分侧梁的平行度、对称度等对于电机悬伸梁、端梁的组装尺寸影响较大。
(3)端梁部分:两端梁平行度、间距与对称度对构架尺寸影响较大。
(4)电机悬伸梁部分:作为构架加工基准,尺寸控制要求高,焊缝主要集中在一侧,易产生变形。
2关键制造技术分析2.1重要部件质量控制要点侧梁、心盘梁所有隔板与上盖板的间隙要求不大于0.5mm,且要与下盖板密贴。
腹板与上下盖板的垂直度不大于1mm,心盘粱心盘面与旁承座面处的平面度为0.5mm,侧梁轮对处平面度为1mm。
而且,2个部件的上下盖板为多折点压型件,既要控制其压型角度,又要控制其装配空间尺寸,给零部件的制造带来较大的困难。
重要部件的质量特点如下:(1)心盘梁、横梁、侧梁形成的钢构架总体要求高。
要求心盘梁、横梁、侧梁组焊后形成的钢构架整体扭曲不大于2mm,构架中部上挠度为0——3mm,构架对角线方向上同轴位导框距之差不大于2mm,同一导框之间公差为士1mm。
这种近似H形钢结构的组焊件在焊后极易出现两端向内的焊接变形,势必对总体制造尺寸造成影响。
(2)导框组焊后整体尺寸精度的控制要求高。
导框1、导框2与心盘梁、横梁、侧梁形成的钢构架组焊后,要求其固定轴距对角线(之差不大于2mm,两侧同轴位轴箱导框至中心的偏差不超过1mm,两导框距构架中心尺寸之差不大于2mm。
车架纵梁焊接作业指导书
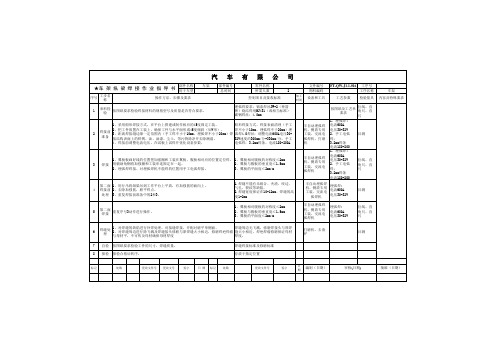
标记
处数
更改文件号 更改文号
ቤተ መጻሕፍቲ ባይዱ
签字
日 期 标记 处数
更改文件号
签字
日 期
编制(日期)
审核(日期)
批谁(日期)
焊缝周边无飞溅,修磨焊接头与原焊
2、对焊缝周边进行除飞溅及焊缝接头修磨与原焊缝大小相近,修磨焊疤焊瘤 缝大小相近,焊疤焊瘤修磨保证母材
与母材平,不可伤及母材确保母材厚度
厚度。
打磨机、去渣 铲
目测
7 自检 按图纸要求检验工件的尺寸、焊缝质量。 8 报检 报检合格后转序。
焊缝焊接标准及修磨标准 存放于指定位置
第二面 1、用行吊将纵梁吊到工作平台上平放,有加强筋的面向上。 4 焊接前 2、去除加强筋,磨平焊点。
处理 3、重复焊接前准备中的2和3。
1.焊缝不能有未熔合、夹渣、咬边、 气孔、裂纹等缺陷, 2.焊缝宽度保证在10-12mm、焊缝的高 度1-2mm
半自动埋弧焊 机、侧放专用 工装、交流电
弧焊机
埋弧焊: 电流600A 电压30-32V
1、翼板板画好线的位置把加强圈和工装在翼板、腹板相对应的位置定位焊, 1、翼板相对腹板的对称度≤2mm
3 焊接 用辅助角钢将加强圈和工装串连固定在一起。
2、翼板与腹板的垂直度≤1.5mm
2、埋弧焊焊接。对埋弧焊机不能焊的位置用手工电弧焊接。
3、翼板的平面度≤2mm/m
半自动埋弧焊 机、侧放专用 工装、交流电 弧焊机、打磨 机
3、距离焊接缝边缘一定范围内(手工焊不小于10mm,埋弧焊不小于20mm)焊 弧焊4.0焊丝:调整电流600A电压30-
接结构表面上的铁锈、油、油漆、尘土、等污物除净并去除潮湿。
32V速度约300mm/分-330mm/分。手工
工字梁四道焊缝焊接顺序

工字梁四道焊缝焊接顺序对于工字梁四道焊缝的焊接顺序,需要先了解工字梁的结构特点和焊接原理。
工字梁是一种常用的结构材料,是由上下两个“工”字形槽和中间的连接板组成的。
因为工字梁经常用于承受大荷载,所以焊接质量尤为重要。
在焊接工字梁四道焊缝时,通常采用以下步骤:1.焊接准备焊接前需要对工字梁表面进行清洁,确保没有灰尘、油脂等杂物。
然后要进行焊缝开凿、腐蚀、校正等预备工作,以使得焊缝表面光滑,并且可以接受后续的焊接工艺处理。
2.对焊口进行预热对于工字梁的四道焊缝中的每一个焊口,在焊接开始前都需要进行预热,以提高焊接质量和焊接速度。
预热需要根据材料和焊缝宽度来确定,一般情况下需要随着梁宽度的增加而增大。
3.进行角焊缝焊接在焊接工字梁的角焊缝时,需要先进行牙形坡口切割和准备,然后通过下降角的方式使焊丝在焊缝中合理均匀填充。
注意,在角焊缝的焊接时,焊丝的直径和溢出量比较重要。
焊丝直径必须与焊缝宽度相匹配,焊丝溢出量不能太大或太小。
4.进行对接焊缝焊接对接焊缝的焊接过程与角焊缝类似,需要进行准备工作和预热,然后通过焊接方法进行填充。
在焊接过程中要注意保持稳定的焊接电弧和合适的焊接角度、速度和芯丝进给量。
5.进行T型焊缝和搭接焊缝焊接在焊接梁的T型焊缝和搭接焊缝时,需要先进行坡口切割和准备,然后通过焊丝在焊缝中均匀填充。
焊接区域的厚度需要合理控制,以保证焊接质量和强度。
总之,在焊接工字梁的四道焊缝时,需要注意对每一个焊口进行预热、控制焊丝直径和溢出量、保持焊接电弧的稳定等重要因素。
只有这样才能保证焊接质量、焊缝牢固和梁的承载能力。
高速铁路桥梁工程预应力混凝土连续梁浇筑顺序
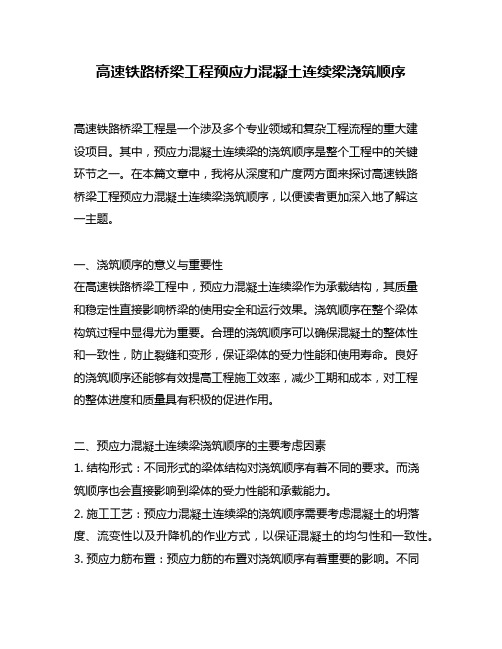
高速铁路桥梁工程预应力混凝土连续梁浇筑顺序高速铁路桥梁工程是一个涉及多个专业领域和复杂工程流程的重大建设项目。
其中,预应力混凝土连续梁的浇筑顺序是整个工程中的关键环节之一。
在本篇文章中,我将从深度和广度两方面来探讨高速铁路桥梁工程预应力混凝土连续梁浇筑顺序,以便读者更加深入地了解这一主题。
一、浇筑顺序的意义与重要性在高速铁路桥梁工程中,预应力混凝土连续梁作为承载结构,其质量和稳定性直接影响桥梁的使用安全和运行效果。
浇筑顺序在整个梁体构筑过程中显得尤为重要。
合理的浇筑顺序可以确保混凝土的整体性和一致性,防止裂缝和变形,保证梁体的受力性能和使用寿命。
良好的浇筑顺序还能够有效提高工程施工效率,减少工期和成本,对工程的整体进度和质量具有积极的促进作用。
二、预应力混凝土连续梁浇筑顺序的主要考虑因素1. 结构形式:不同形式的梁体结构对浇筑顺序有着不同的要求。
而浇筑顺序也会直接影响到梁体的受力性能和承载能力。
2. 施工工艺:预应力混凝土连续梁的浇筑顺序需要考虑混凝土的坍落度、流变性以及升降机的作业方式,以保证混凝土的均匀性和一致性。
3. 预应力筋布置:预应力筋的布置对浇筑顺序有着重要的影响。
不同的预应力筋布置要求需要有不同的浇筑顺序来满足其受力和使用要求。
三、高速铁路桥梁工程预应力混凝土连续梁的浇筑顺序根据以上考虑因素,一般高速铁路桥梁工程预应力混凝土连续梁的浇筑顺序可分为以下几个步骤:1. 梁底板浇筑:首先进行梁底板的浇筑,采用高强度混凝土,以确保梁底板具有足够的承载能力和耐久性。
2. 部分梁段浇筑:在梁底板的基础上,逐段进行梁体的浇筑,首先浇筑梁段的下部,然后进行预应力筋张拉,最后再进行梁段的上部浇筑,以确保整个梁体的预应力筋布置和浇筑质量。
3. 梁体连接浇筑:最后进行梁体的连接处浇筑,将各部分梁体浇筑成整体,形成连续梁的结构体系。
总结与回顾:高速铁路桥梁工程预应力混凝土连续梁的浇筑顺序,是整个工程中极为关键的环节。
高速公路箱梁桥钢梁制作工艺

高速公路箱梁桥钢梁制作工艺1、板单元制作工艺1.1隔板单元制作1)隔板制作工艺隔板单元为箱梁内胎、骨架,应进行首件验收,合格后方可批量生产。
每个隔板下料前需认真核对,下料完成后进行编号是、标识。
隔板翼缘板在下料时开设好坡口。
2)隔板制作工艺流程1.2主梁翼缘板和腹板组合T型梁的制作1)T型梁的制作工艺2)T型梁的制作工艺流程1.3主梁底板单元1)主梁底板制作工艺2)主梁底板制作工艺流程1.3节点板单元1)节点板单元制作工艺2)节点板单元制作工艺流程2板单元制作说明2.1下料1)下料精度要求严格按照工艺图纸规定内容执行。
2)切割前把钢板摆正放平,清除割件表面切口两侧约30~50mm内的铁锈,油漆粉尘等杂质,并在下面留出一定空隙,以利于把切割产生的熔渣从切口下部吹出3)为减少气割变形,支点必须放在割件内,切割大件时,特别要注意支点可靠,防止由于自重而产生过大的变形。
4)为确保工件加工质量,如有需要先进行试切。
5)工件切割完毕后切割边缘需清理打磨,对于切割时造成的崩坑等缺陷进行修补打磨。
6)下料前应检查材料的牌号、规格、质量。
并应使轧制方向与零件的受力方向一致。
7)所有零件优先用精密切割下料。
对于长宽比较大的矩形板块,下料时,沿长度方向的两边要同时切割,防止板件在板平面内侧向弯曲。
对于形状复杂的零件(如隔板),用计算机放样确定几何尺寸,并采用数控切割机精切下料,并应适当加入补偿量,消除热变形的影响。
8)下料时,主梁长度预留配切量(包括弹性压缩量及焊接收缩量等加工余量),预拼装完毕后再切割。
9)下料后应在所下料的端头标示出编号、规格、材质等,同时应在余料上标出其规格、炉批号、材质、钢板号等,并在端头板厚方向上标出编号10)精密切割的边缘表面质量达到如下要求:表4-1精密切割边缘表面质量要求2.2矫正1)零件矫正前清除下料边缘的毛刺、挂渣。
矫正后的钢料表面不应有明显凹痕和其它损伤。
2)热矫的温度控制在700~800℃,矫正后零件随空气缓慢冷却,降至室温以前,不得锤击或用水急冷。
- 1、下载文档前请自行甄别文档内容的完整性,平台不提供额外的编辑、内容补充、找答案等附加服务。
- 2、"仅部分预览"的文档,不可在线预览部分如存在完整性等问题,可反馈申请退款(可完整预览的文档不适用该条件!)。
- 3、如文档侵犯您的权益,请联系客服反馈,我们会尽快为您处理(人工客服工作时间:9:00-18:30)。
崔晓芳
0序 言
机车动力转向架的设计生产直接决定着列车的 最高时速以及能否正常运营, 因此在生产过程中确 保转向架的质量具有 十分重要的意义 [ 1] 。构架是 转向架的重要承载部件, 在构架生产过程中面临的 主要问题是如何控制焊接变形。而作者所研究的构 架侧梁又是构架焊接生产过程中控制焊接变形的关 键问题。
1 04
焊接学报
第 27卷
由表 2的结果可以看出, 主焊缝不同的焊接顺 序对于 x 方向的纵向收缩变形影响较小。而表 2和 图 8的 y 方向横向收缩结果则表明, 主焊缝不同的 焊接顺序对于 y 方向的收缩变形影响较大, 主焊缝 采用从右到左的顺序得到的横向收缩量可以比采用 另外两种焊接顺序减少近 0. 6mm; 而且主焊缝的焊 接会产生较大的横向收缩量, 这一收缩量由只焊接 内 部 焊 缝 的 1. 40 ~ 1. 48 mm 增 大 到 5. 58 ~ 6. 17mm; 另外, y 向收缩变形量的大小与隔板的位 置密切相关, 隔板所在位置, 收缩量相对较小, 而不 存在隔板的位置, y向收缩量显著增大, 图 8中峰值 均出现在隔板加强最薄弱的地方。主焊缝不同的焊 接顺序也会对 z方向的挠曲变形产生一定影响, 由 表 2和图 9的结果可知, 主焊缝采用从左到右和从 中间到两边的焊接顺 序所得 z 向变形几 乎完全一 样, 而当主焊缝采用从右到左的焊接顺序时, 上挠变 形有一定幅度的增加, 这一增 加量为 1. 13 mm; 另 外, 主焊缝的焊接同样会产生较大的 z向挠曲变形, 在焊接全部完成之后 (即主焊缝焊接完成 ), z向的 上挠变形量达到了 15. 46 ~ 16. 59 mm, 可见对于转 向架侧梁的焊接, 控制 z 向挠曲变形对于实际生产 具有十分重要的意义。但是计算结果表明, 采取不 同的内部焊缝焊接顺序只能减少 0. 78 mm 的挠曲 变形, 而采取主焊缝不同的焊接顺序则最多能减少 1. 13mm的 z向挠曲变形。因此只依靠简单地改变 焊缝焊接顺序来减小 z方向的上挠变形量效果并不 十分显著, 要控制这一变形还需配合采用其它能够 减少焊接变形量的手段共同作用。例如根据焊接残 余变形预测数据, 采用反变形装配工艺, 以达到减少 z向挠曲变形的目的。
采用以上简化技术进行侧梁的有限元建模。单 元总数为 9 387, 节点总数为 9 457, 采用有限元分析 软件 M arc, 并 采 用 了 并 行 计 算 方 法, 在 CPU 为 1. 8 G 的双 CPU 微机上进行, 每种模型所需计算时 间约为 7 h。可以发现对于侧梁这样的大型结构, 采 用上述简化技术之后, 单元和节点数目大大减少, 计 算时间也能够接受。
收稿日期: 2004- 10- 08
Marc软件, 分别研究了内部焊缝和外部主焊缝焊接 顺序对侧梁焊接变形量的影响, 得到了焊接顺序影 响变形的规律, 为实际生产过程中控制高速机车转 向架构架的焊接质量提供了可靠的依据。
1 有限元模型
该转向架构架侧梁是由上、下盖板、前、后立板 以及内部纵、横隔板及加强筋板组焊而成的箱形结 构梁, 其结构及焊缝位置如图 1、2所示。由于侧梁 的结构尺寸大 ( x 方向纵向尺寸为 4. 5 m, y 方向横 向尺寸为 0. 25 m, z方向高度尺寸为 0. 31 m ), 焊缝 多 (内部纵、横隔板 15个, 纵筋板 5个; 外部主焊缝 4条 ), 按照常规焊接过程数值模拟建立的有限元模 型会因为自由度庞大而使计算难以进行, 尤其是采 用全耦合的三维热弹塑性有限元进行数值模拟时, 庞大的计算量很容易导致计算不能进行, 为了解决 计算量大这一困难, 在建立有限元模型时采用了以 下三种技术进行模型简化, 以减小数值模拟计算量, 使数值模拟能够顺利进行
从中间到两边, 如图 3 所示 从中间到两边, 与 1 号模型相比只
有部分顺序变化 从左到右, 如图 4 所示
最大 x 向收 缩量 $L /mm
- 1. 84
- 1. 89 - 1. 89
最大 y 向收 缩量 $ B /mm
- 1. 45
- 1. 40 - 1. 48
最大 z向挠度 f /mm 7. 53
摘 要: 控制高速机车转向架构架侧梁的焊接变 形是控制构 架生产质 量的关键。以 热 弹塑性理论为基础, 基于热 - 机 耦合算法创建了侧梁热弹塑性仿 真模型, 采用 M arc 软 件, 分别研究了内部焊缝和外部主焊缝焊接顺序对侧梁焊接变形量 的影响, 得到了焊 接 顺序影响变形的规律, 为实际生产过程 中控制 高速机车 转向架 构架的 焊接质 量提供 了 可靠的依据。为了避免计算仿真模型过于 庞大, 计算效率低下等问 题, 在创 建该数值 仿 真模型中, 采用了分段移动的串热源模型和并行计算技术等, 从而使数值仿 真领域中 最 复杂的焊接过程仿真得 以直接应用工程中。 关键词: 高速动力车; 转向架构架 ; 焊接变形; 焊接顺序; 数值仿真 中图分类号: U292. 91+ 4 文献标 识码: A 文章编号: 0253- 360X( 2006) 01- 101- 05
变形情况 对比
y, z向变形对 比见图 8、9
图 6 4 号模型主焊缝焊接顺序 (图中所标 序号 为焊接顺序, 6号模型方向相反 )
F ig. 6 W e ld ing se que nc e o f fourth m ode l
图 7 5号模型主焊缝焊接顺序 F ig. 7 W e ld ing se que nce o f fifth m ode l
5
从中间到两边, 如图 7 所示
6
从右到左, 与 4 号模型相反
注: 内部焊缝焊接顺序固定为从左到右。
最大 x 向 收缩量 $L /mm
- 4. 42
- 4. 38 - 4. 41
最大 y 向 收缩量 $ B /mm
- 6. 17
- 6. 17 - 5. 58
最大 z向挠度 f /mm
15. 46
15. 47 16. 59
目前, 对于焊接变形的控制主要靠多年积累的 经验和多次的试验。在新产品试制或制造中, 有时 会出现焊接变形超出设计尺寸要求而不得不采用火 焰或机械等方法矫正变形, 这样做不仅增加成本, 而 且会改变残余应力的 分布状态 [ 2 ] 。残余应力的存 在对高速机车构架的疲劳强度和疲劳寿命均有很大 的影响 [ 3] 。因此研究侧梁的焊接过程, 找到可以减 小侧梁焊接残余变形量的生产方法, 对于实际的生 产具有十分重要的意义。
鉴于内部焊缝采取从左到右的焊接顺序可以减
少残余变形量, 在研究主焊缝焊接顺序对焊接残余 变形的影响时, 内部焊缝采取了从左到右的相同焊 接顺序进行分析计算。所建立的三种不同主焊缝焊 接顺序的计算模型为 4号模型采取从左到右的焊接 顺序焊接, 如图 6所示; 5号模型采取从中间到两边 的焊接顺序焊接, 如图 7所示; 6号模型采取从右到 左的焊接顺序焊接, 与 4 号模型 焊接顺序相反, 如 图 6所示; 各模型计算所得各个方向的最大变形量 如表 2所示。
表 1 内部焊缝不同焊接顺序下的残余变形计算结果
Tab le 1 C a lc ula te d de fo rm a tion re su lts o f inne r w e lds unde r d iffe re n t we ld ing se que nce
模型编号 1 2 3
内部焊缝焊接顺序
( 2) 单元类型选用四边形壳单元。壳单元的节 点数目明显少于实体单元, 自由度数目也有所减少, 同时考虑到四边形单元较之三角形单元的计算精度 有所提高, 因此采用四边形的壳单元进行建模, 从而 使三维热弹塑性分析的计算效率大幅度提高。
( 3) 应用分段串热源对焊接热源进行模拟。焊 接过程数值模拟计算量庞大的重要原因就是因为焊 接移动热源的存在, 而采用不同的焊接热源进行数 值模拟计算量差别很大, 此处采用了一种分段移动 串热源模型 [ 6] 进行模 拟计算。这种 热源模型的一 个 最大特点就是计算效率极高, 并且应用这种热源
表 2 主焊缝不同焊接顺序下的残余变 形计算结果 Ta b le 2 C a lcu la te d de fo rm a tion re su lts o fm a in we lds w ith diffe re n twe ld ing se que nce
模型编号
主焊缝焊接顺序
4
从左到右, 如图 6 所示
( 1) 采用较粗大的单元进行较均匀的网格划 分。由 于 焊 接 残 余 变 形 是 一 个 宏 观 量, 根 据 文献 [ 5]可知, 采用较粗大的网格划分进行 残余变 形量的模拟计算, 经过实践证明能够满足精度要求, 因此采用了粗大的单元尺寸进行网格划分, 单元尺 寸约为 25 mm @25 mm。
d iffe re n t we ld ing se que nce
图 4 3 号模型内部焊缝焊接顺序 F ig. 4 W e ld ing se que nce of third m ode l
的计算结果还可以发现, 内部焊缝焊接顺序较小的 变化并不会影响最终的残余变形结果。因此对于内 部焊缝, 采取从左到右的焊接顺序更为合理。 2. 2 主焊缝焊接顺序对焊接变形的影响
7. 45 6. 75
变形情况 对比
z 向挠曲变形对 比见图 5
由表 1的变形计算结果可以发现, 内部焊缝的 焊接不会产生很大的 x 方向的纵向收缩和 y方向的 横向收缩, 但会产生较大的 z向挠曲变形, 改变内部 焊缝的焊接顺序对 x 向和 y 向的收 缩量影响都很 小; 内部焊缝焊接顺序的改变只对 z 向的挠曲变形
第 27卷 第 1期
焊接学报
Vo.l 27 No. 1
2 0 0 6 年 1 月 TRAN SACTIONS OF TH E CH INA WELD ING INST ITUTION January 2 0 0 6
高速机车构架侧梁的焊接顺序