数控工具系统(改)
数控机床的自动换刀系统操作指南

数控机床的自动换刀系统操作指南数控机床的自动换刀系统是现代机床中重要的工具,它的作用是实现多种刀具的自动切换,提高生产效率和加工精度。
本文将为您介绍数控机床的自动换刀系统的操作指南。
1. 系统概述数控机床的自动换刀系统由控制单元、刀库、刀臂、刀具以及相关传感器组成。
通过控制单元的指令,刀库中的刀具可以自动切换到刀臂上,实现刀具的自动更换。
2. 操作前的准备在操作数控机床的自动换刀系统之前,首先要进行以下的准备工作:- 确认机床的电源是否正常,机床内部是否处理干净。
- 确认自动换刀系统的刀库是否存放有足够的刀具。
- 确认程序中的执行代码是否正确,不会发生刀具碰撞。
3. 操作步骤以下是数控机床的自动换刀系统的操作步骤:(1) 手动操作模式:首先将机床设置为手动操作模式,确保机床处于不会自动运行的状态。
(2) 加载刀具:通过控制单元的操作指令,将所需刀具从刀库中选取出来。
(3) 位置定位:使用机床的控制面板或相关软件对刀臂进行位置定位,使其准确匹配刀具的安装位置。
(4) 刀具安装:将选取的刀具正确安装到刀臂上,确保刀具牢固固定,避免出现松动的情况。
(5) 参数设定:在机床的控制面板或相关软件中设定刀具的相关参数,如切削速度、进给速度等。
(6) 刀具校对:在刀具安装完成后,进行刀具校对的操作,确保刀具位置的准确性。
(7) 确认操作:在进行自动换刀操作之前,要仔细确认刀具的安装是否正确,刀具是否符合加工要求。
(8) 运行程序:确认刀具安装正确后,将机床切换到自动运行模式,在控制单元中选择相应的程序,运行自动换刀操作。
(9) 监测切换:在自动换刀操作过程中,通过机床的控制面板或相关软件实时监测刀具的切换过程,确保刀具的准确切换。
(10) 完成切换:当刀具切换完成后,机床会自动停止,并显示切换完成的提示信息。
4. 常见问题及解决方法在使用数控机床的自动换刀系统时,可能会遇到以下的问题,下面为您提供一些建议的解决方法:- 刀具松动:检查刀具安装是否正确,确保刀具紧固螺母牢固固定。
数控车床系统结构改造设计书

数控车床系统结构改造设计书数控车床系统结构改造设计书1. 设计目标本次数控车床系统结构改造的设计目标为:提高数控车床加工精度和稳定性,增加数控系统的功能和扩展性,提升生产效率和生产质量。
2. 现有车床结构分析数控车床的结构包括机身、进给系统、主轴系统、控制系统和刀具系统。
其中,机身的刚性决定着数控车床的加工精度和稳定性,而进给系统和主轴系统的精度和稳定性则是数控车床能否实现全自动加工的关键。
控制系统则决定了数控车床的加工精度和工作范围,刀具系统则决定了数控车床的工作效率和加工质量。
现有数控车床的结构不够合理,机身的刚性不够强,容易发生振动和位移,影响加工精度和稳定性。
进给系统和主轴系统的精度和稳定性也不够理想,容易产生误差和变形,导致加工品质下降。
控制系统的功能不能满足当前的加工需求,需要扩展出更多的加工功能。
刀具系统的切割效率不理想,加工速度不够快,切割质量不如人意。
3. 改造方案3.1 机身结构改造考虑到机身的刚性对加工精度的影响,本次改造将对现有机身结构进行增强和加固,利用更高强度的材料重新设计机身结构,并采用加强支撑和支撑背板的方式,使数控车床的结构更加稳定和牢固。
3.2 进给系统和主轴系统改造进给系统和主轴系统的精度和稳定性对数控车床的全自动加工有着至关重要的影响,因此,本次改造将针对进给系统和主轴系统的问题进行改进。
首先,更新进给系统的控制部分和传动设备,采用更加精密的减速器和伺服电机实现进给速度更加稳定和精确。
其次,针对主轴系统的问题,采用更加精密的轴承和主轴,实现主轴的转速稳定和运转平稳。
3.3 控制系统扩展控制系统的扩展将是本次改造的关键所在。
针对现有控制系统的不足,本次改造将引入更加先进的数控系统和相应的控制软件,实现更加灵活和多样化的加工需求,并提供更加人性化的操作界面,方便操作和管理。
3.4 刀具系统改进刀具系统的改进将提升数控车床的工作效率和加工质量。
本次改造将增加多条刀架,增强切割效率,并更新切割软件,实现更加高效和精准的切割操作。
数控工程屏幕改装方案

数控工程屏幕改装方案一、需求分析随着数控机床的不断发展,其控制系统也不断更新。
而数控机床的控制系统主要包括机床控制器、运动控制系统、工具控制系统等,其中的一部分常常会被设计成触摸屏界面操作。
当然,也有许多老旧的数控机床,其控制系统可能并不是触摸屏界面操作,而是采用之前的按键式操作,这样一来就会限制了机床的操作便利性,也会降低了工作效率。
因此,我们需要对这些老旧的数控机床进行屏幕改装,将原有的按键式操作系统进行升级,改成更加现代化的触摸屏界面操作系统。
这样一来,不仅可以提高机床的操作便利性,也可以提高工作效率,加快生产节奏,提高生产效率。
二、改装原则1.操作性原则改装后的触摸屏界面操作系统必须方便快捷,使操作员在熟悉机床操作的同时,能够更加便利地进行操作,提高效率。
2.稳定性原则改装后的触摸屏界面操作系统必须稳定可靠,不能出现卡顿、死机等情况,以免影响生产进度。
3.通用性原则改装后的触摸屏界面操作系统应该具备通用性,能够兼容多种不同型号的数控机床,以便在整个生产线上使用。
三、改装方案1.选型首先,我们需要选用适合的触摸屏设备,以满足不同数控机床对操作界面的需求。
常用的触摸屏主要有电阻触摸屏和电容触摸屏。
电阻触摸屏相对来说价格更低,但灵敏度和清晰度上不如电容触摸屏。
电容触摸屏的价格相对较高,但是操作更加流畅,触摸灵敏度更好。
因此,我们需要根据具体情况选用合适的触摸屏设备。
2.界面设计在选择触摸屏设备之后,我们需要进行界面设计。
界面设计应该符合人机工程学原则,使得操作员在第一次接触到新的触摸屏界面操作系统时,能够迅速上手。
界面设计需要简洁明了,按钮大小适中,排列合理,这样一来就可以降低误操作的风险,提高操作的准确性。
3.软件开发界面设计完成后,我们需要进行软件开发。
软件开发应该充分考虑数控机床的特殊性,能够在兼容多种型号的数控机床的同时,保证稳定性和可靠性。
软件开发的主要任务是将触摸屏界面操作系统和数控机床的控制系统进行有效地整合,确保操作界面的准确性和稳定性。
数控工具系统(下)

数控工具系统 ( ) 下
哈 尔 滨理 工 大 学 ( 尔滨 哈 108 5 0 0) 刘献礼 丁 云鹏
3 .新 型 刀柄 ( ) HS 刀 柄 1 K
( ah n A ce )
这样 就实 现 了双面 同步 夹 紧 。就其 本 身 的定 位 而 言, HS K刀 柄 是 1 8 9 7年 德 国 阿 亨
一
这一 点与 B T锥 柄一致 。H K接 口的轴 向精度 由接 触 S 端 面决 定 ,这 与 B T锥 柄
明 显 不 同 , 中 空 结 构 是
种新 型的高 速短 锥刀柄 ,如图 l 示 。 0所
H K刀 柄 的 一 个 重 要 特 S 征 。要 实现 双 面接触 ,锥
面 必 须 产 生 弹 性 变 形 ,与 实 心 柄 相 比 ,空 心 柄 产 生 弹 性 变 形 容 易 得 多 ,所 消
HS — B K
H K—C S
圆柱 【没 有 机 械 手夹 持 V形 槽 ,其 余 同 A 型 f 【 『
手 动换 刀 的一 般 加 T
H K —D S
圆柱 面 没 有机 械 手 夹 持 V形 槽 ,其 余 同 B型
收 到 换 刀 的 车削 ] T. J N
与 A 型 相似 ,但 完 全 对 称 ,没 有 键 槽 和缺 口 ,扭 矩 由
H K 工 具 系 统 最 突 出 的 特 点 就 是 端 面 和 锥 面 同 S
步 接触 ,如 图 1 1所 示 。夹 紧时 ,由于 锥 部 有 过 盈 , 所 以锥 面受 压 产 生 弹性 变 形 ,同 时 刀柄 向 主轴 锥 孔 轴 向位移 ,以消除初 始 间隙 ,实 现端 面之 间 的贴合 ,
内锥孔 相差 不 大 ,有 利 于在 较 大 转 速 范 围 内保 持 锥 面 的可靠接 触 。HS K刀 柄 的 空 心 柄 部还 为夹 紧机 构 提供 了安 装 空 间 , 以实 现 由内 向 外 的 夹 紧 。这 种 夹 紧方式 可 以 把 离 心 力转 化 为 夹 紧 力 ,使 刀 柄 在 高 转 速下工 作 时 的 夹 紧 更 为 可靠 。此 外 ,H K刀 柄 的 空 S
数控机床自动换刀系统的设计与优化方法

数控机床自动换刀系统的设计与优化方法数控机床自动换刀系统作为现代制造业中的关键设备之一,其设计和优化对于提高生产效率和产品质量至关重要。
本文将讨论数控机床自动换刀系统的设计原理、关键技术以及优化方法,旨在指导工程师和研究人员进行相关工作。
首先,数控机床自动换刀系统的设计原理主要包括以下几个方面:刀具库、刀具传递机构和换刀动作控制。
刀具库是存放刀具的地方,通常设计成可自动旋转、抬升和倾斜的结构,以便于刀具的选择和取放。
刀具传递机构用于将所需刀具从刀具库传递到机床主轴上,并确保刀具的正确位置和方向。
换刀动作控制则通过编程和传感器来实现,保证换刀过程的准确性和稳定性。
在设计数控机床自动换刀系统时,我们需要注意一些关键技术。
首先是刀具库的设计,刀具库的容量和结构需要根据实际工作中所涉及到的刀具种类和数量进行合理规划。
其次是刀具传递机构的设计,传递机构需要具备快速、准确的传递能力,同时要考虑到刀具重量对传递机构的负荷影响,确保稳定性。
换刀动作控制需要精确控制刀具的位置和方向,可以采用光电传感器或编码器等传感器,通过编程实现动作的控制和判断。
为了进一步优化数控机床自动换刀系统的性能,我们可以采取一些优化方法。
首先是刀具库的优化,可以采用高效的刀具存放方案,如采用自动尺寸检测技术,将刀具按照尺寸进行分类存放,方便快速选择和取放。
其次是刀具传递机构的优化,可以采用更先进的传递机构设计,如采用电磁吸盘或气动夹持装置等,提高传递速度和准确性。
此外,还可以通过改进换刀动作控制算法,优化换刀过程的稳定性和精度。
在优化设计过程中,还需要充分考虑数控机床自动换刀系统的可靠性和安全性。
可靠性是指系统在长时间运行中的稳定性和故障率,我们可以通过选用高质量的部件和进行严格的测试来提高可靠性。
安全性是指系统在使用过程中的安全保障,我们需要设置安全装置,如机械锁或密码锁等,防止误操作或意外伤害的发生。
总结起来,数控机床自动换刀系统的设计与优化需要考虑刀具库、刀具传递机构和换刀动作控制等关键技术。
数控机床改造策划书3篇

数控机床改造策划书3篇篇一《数控机床改造策划书》一、项目背景随着制造业的不断发展,数控机床在生产中的作用日益凸显。
然而,一些老旧的数控机床可能存在性能不足、精度下降等问题,影响生产效率和产品质量。
为了提升企业的竞争力,对这些数控机床进行改造具有重要意义。
二、改造目标1. 提高机床的加工精度和稳定性。
2. 提升机床的加工效率。
3. 增强机床的自动化程度。
4. 降低设备的故障率和维修成本。
三、改造内容1. 机械部分检查和修复机床的导轨、丝杠等关键部件,确保其精度和可靠性。
更换磨损严重的零部件。
对机床的结构进行优化,提高刚性和稳定性。
2. 电气部分更新控制系统,采用更先进的数控系统,提高控制精度和响应速度。
更换老化的电气元件,确保电路的稳定性和安全性。
优化机床的布线,减少干扰。
3. 液压和气动部分检查和维护液压和气动系统,确保其正常运行。
更换密封件和老化的管路。
4. 软件部分开发专用的加工工艺软件,提高加工效率和质量。
四、改造步骤1. 前期调研对现有数控机床进行全面评估,确定需要改造的具体内容。
了解市场上可供选择的改造方案和技术。
2. 方案设计根据调研结果,制定详细的改造方案,包括机械、电气、液压等方面的具体措施。
进行方案论证和优化,确保其可行性和经济性。
3. 设备采购根据改造方案,采购所需的零部件、数控系统等设备。
确保采购的设备质量可靠,符合技术要求。
4. 改造实施按照改造方案,逐步实施机床的改造工作。
对改造过程进行严格监控,确保质量和进度。
5. 调试和验收对改造后的机床进行调试,确保各项性能指标达到要求。
组织相关人员进行验收,确保机床能够正常投入使用。
五、项目预算1. 设备采购费用:[X]元。
2. 人工费用:[X]元。
3. 其他费用:[X]元。
总预算:[X]元。
六、风险评估与应对措施1. 技术风险可能存在改造技术不成熟或不适用的情况。
应对措施:在方案设计阶段充分论证,选择可靠的技术方案和供应商。
2. 进度风险改造过程中可能会出现意外情况,导致进度延误。
FANUC数控系统参数设定
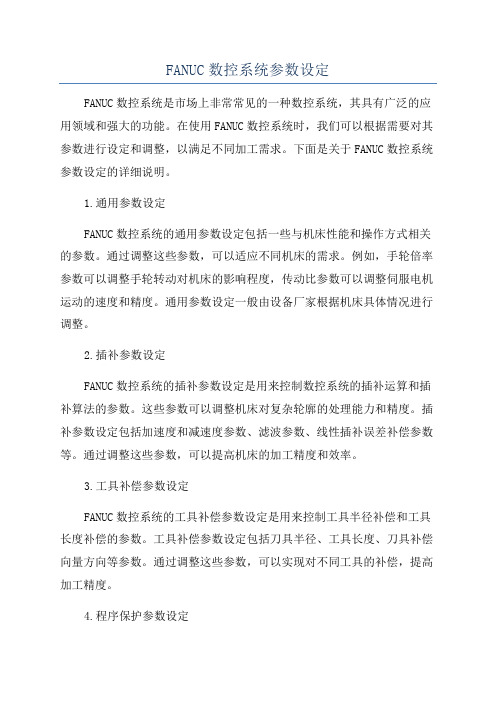
FANUC数控系统参数设定
FANUC数控系统是市场上非常常见的一种数控系统,其具有广泛的应用领域和强大的功能。
在使用FANUC数控系统时,我们可以根据需要对其参数进行设定和调整,以满足不同加工需求。
下面是关于FANUC数控系统参数设定的详细说明。
1.通用参数设定
FANUC数控系统的通用参数设定包括一些与机床性能和操作方式相关的参数。
通过调整这些参数,可以适应不同机床的需求。
例如,手轮倍率参数可以调整手轮转动对机床的影响程度,传动比参数可以调整伺服电机运动的速度和精度。
通用参数设定一般由设备厂家根据机床具体情况进行调整。
2.插补参数设定
FANUC数控系统的插补参数设定是用来控制数控系统的插补运算和插补算法的参数。
这些参数可以调整机床对复杂轮廓的处理能力和精度。
插补参数设定包括加速度和减速度参数、滤波参数、线性插补误差补偿参数等。
通过调整这些参数,可以提高机床的加工精度和效率。
3.工具补偿参数设定
FANUC数控系统的工具补偿参数设定是用来控制工具半径补偿和工具长度补偿的参数。
工具补偿参数设定包括刀具半径、工具长度、刀具补偿向量方向等参数。
通过调整这些参数,可以实现对不同工具的补偿,提高加工精度。
4.程序保护参数设定
5.通讯参数设定
总之,FANUC数控系统的参数设定可以根据实际加工需求进行灵活的
调整和配置,使数控系统更加适应不同的加工任务。
通过合理的参数设定,可以提高机床的加工精度和效率,保证加工质量。
同时,设定好的参数也
可以提高操作的安全性,保护程序的机密性。
数控车床的基本操作系统介绍

数控车床的基本操作系统介绍二、数控系统操作面板(一)面板上的键盘1、复位键:(RESET)用于使CNC复位或取消报警等。
地址和数字键:按下这些键能够输入字母、数字或其他字符。
2、输入键(INPUT):用于输入和修改参数。
3、取消键(CAN)用于删除最后一个进入输入缓存区的字符或符号。
4、程序编辑键演示操作说明2.FANUC 0i Mate 系统面板演示操作说明::(DELET)删除键。
:(INSERT)插入键。
:(ALTER)替换键。
5、光标移动键:(CURSOR)用于将光标向上或向下移动。
6、换页键:(PAGE)用于将屏幕显示的页面向前或向后翻页。
7、功能键功能键用于选择显示屏幕内容。
有如下功能键:1)、(POS)按下该键,能够显示位置屏幕。
2)、(PRGRM)按下该键,能够显示程序屏幕。
3)、:( OFFSET/SETTING )按下该键,能够显示偏置/设置屏幕。
4)、按此键显示系统画面5)、按此键显示信息画面6)、按此键显示图形画面8、软键:相当于功能键下的二级菜单。
按下功能键後,按与屏幕文字相对的软键,能够进入该菜单。
〔二〕、位置屏幕:当按下面板上的(POS)键,屏幕显示为位置。
屏幕下方有二级菜单:绝对、相对、综合。
单击二级菜单正下方的软键,就能够执行该菜单命令。
例如,单击〝综合〞正下方的软键,屏幕将显示绝对坐标、相对坐标和机械坐标〔三〕、程序屏幕:当按下面板上的(PRGRM)键,屏幕显示为程序屏幕〔如以下图〕。
屏幕下方有二级菜单:程式、整理。
单击二级菜单正下方的软键,就能够执行该菜单命令。
例如,假如事先差不多导入了或手工编写了程序,单击〝程式〞正下方的软键,屏幕将显示该程序的内容。
〔四〕.刀具偏置/设置屏幕演示操作说明:3.POS 键,显示位置屏幕及二级菜单4.按 PROG键显示序程屏幕及二级菜单当按下面板上的(OFSETSETTING)键,屏幕显示为刀具偏置/设置屏幕〔如以下图〕。
屏幕下方有二级菜单:补正、MACRO、坐标系。
数控机床ATC系统

5
2.5 数控加工自动换刀系统
内孔车刀
螺纹车刀
6
2.5 数控加工自动换刀系统 常用铣刀:
面铣刀
方肩铣刀
7
2.5 数控加工自动换刀系统 仿形铣刀
整体硬质 合金铣刀
三面刃和 螺纹铣刀
8
2.5 数控加工自动换刀系统
钻削刀具:
钻头
丝锥
铰刀
9
2.5 数控加工自动换刀系统 镗削刀具:
粗镗刀
精镗刀
V3 = 3mm;
V4 = 4mm;
等五种。
15
2.5 数控加工自动换刀系统
3)可转位刀片的夹紧方式 刀片夹紧要求:
(1)夹紧可靠,不允许松动。 (2)定位准确,确保定位精度和重复精度。 (3)排屑流畅,有足够的排屑空间。 (4)结构简单,操作方便,转位动作快,成本低。
刀片夹紧方式: (1)杠杆式; (2)楔块上压式; (3)螺钉上压式;
一个机械手将加工用毕的刀具从主轴中拔出,与 此同时,另一个机械手将在刀库待命的刀具中从 换刀位置拔出,然后两者交换位置,完成换刀过 程。刀库中的刀具可手工或机械手安装。
机械手是当主轴上的刀具完成一个工步后, 把这一工步的刀具送回刀库,并把下一工步所 需要的刀具从刀库中取出来装入主轴继续进行 加工的功能部件。
1—立柱 2—底座 3—横向工作台 4—纵向工作台 5—刀库 6—主轴箱
51
2.5 数控加工自动换刀系统 (2)主轴移动式无机械手换刀
52
2.5 数控加工待换自动换刀系统
刀具
换下 刀具
无机械手换刀过程 1—立柱 2—主轴箱 3—刀库
53
2.5 数控加工自动换刀系统
2) 带机械手交换刀具方式
新代数控系统操作基础
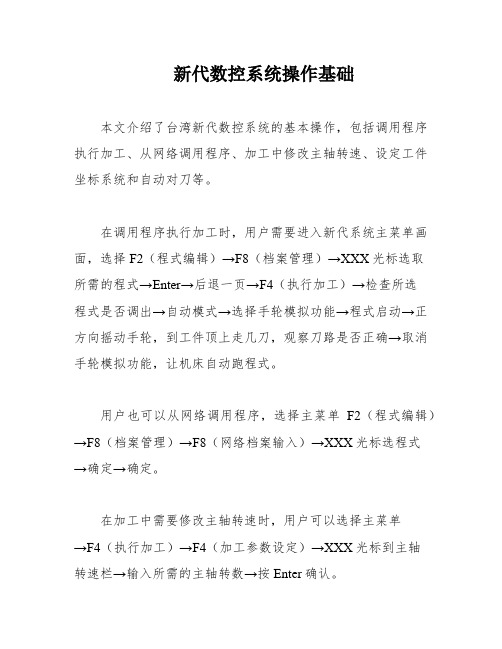
新代数控系统操作基础本文介绍了台湾新代数控系统的基本操作,包括调用程序执行加工、从网络调用程序、加工中修改主轴转速、设定工件坐标系统和自动对刀等。
在调用程序执行加工时,用户需要进入新代系统主菜单画面,选择F2(程式编辑)→F8(档案管理)→XXX光标选取所需的程式→Enter→后退一页→F4(执行加工)→检查所选程式是否调出→自动模式→选择手轮模拟功能→程式启动→正方向摇动手轮,到工件顶上走几刀,观察刀路是否正确→取消手轮模拟功能,让机床自动跑程式。
用户也可以从网络调用程序,选择主菜单F2(程式编辑)→F8(档案管理)→F8(网络档案输入)→XXX光标选程式→确定→确定。
在加工中需要修改主轴转速时,用户可以选择主菜单→F4(执行加工)→F4(加工参数设定)→XXX光标到主轴转速栏→输入所需的主轴转数→按Enter确认。
为了设定工件坐标系统,用户可以选择主菜单F1(机台设定)→F5(设定工件坐标系统)→F5(分中功能)→在工件左侧铣一刀或碰一下→按PX1→在工件右侧铣一刀或碰一下按PX2.在工件前侧铣一刀或碰一下PY1按一下→后侧铣或碰按PY2→退页→G54(或G55,56……)→F3(辅助坐标设定)。
最后,在自动对刀时,用户可以选择主菜单F1(机台设定)→F5设定工件座标系统)→F6(自动对刀)→自动模式→进给倍率打到100%—→F1(自动对刀起动)→待停止后→检查“数”是否抓到。
需要注意的是,当测量模式选1,单刀单工件时,用户需要将落差放在外部偏移Z轴坐标中。
当工件坐标号码设为空时,对刀完成后,当前的刀长会记录在辅助点坐标Z轴中。
当工件坐标号码设为1时,对刀完成后,当前的刀长会自动记录到工件坐标G54的Z轴中。
如果想跑一次当前的程式,只需将相应的改变工件坐标(如G54、G55、G56)Z轴的坐标值即可。
当测量模式选2时,对刀画面会有所变化。
当测量模式选择2时,即单刀多工件模式。
在这种模式下,主轴上只能使用一把刀,而工作台上有多个待加工工件。
数控工具系统(上)

!
, - 、
一 1 ,
/
! ,
/ ! 专 ! 、 !/
1 、, ^
、 !
1
理程 序 较 多 ,一 般 以 MP A . S F N P T为 默 认 后 处 理 程
序 。但 对于采 用 SE N I ME S系统 的 机 床 ,则不 能 使 用 此后 处理 程序 。原 因是 两 种 系统 进 给 率 执 行 方 式 不
一
( ) 圆柱 面投 影 加 工 1
虽 然 应 用 较 多 ,但需 要
多次调 整并 需 要 逐 一 投影 处理 ,应 用 步骤 最 多 ,并 ቤተ መጻሕፍቲ ባይዱ容易 发生 人为 出错 。
致 ,如果仍 然应 用 MP AN P T后 置 处理 程序 输 出 F .S
( ) 圆柱 面缠 绕加 工 较 投影 加 工 方 式 步骤 有 2 所简化 ,但仍 需 旋 转 处 理 以 及 调整 4轴 数值 ,步 骤
联 接 系 统 ,包 括 主 轴 ( 者 刀 座 ) 或 、刀 柄 ( 及 刀 柄 以
实现刀具 刀 柄 联结 的装 置 ) 和夹 紧机 构 ,而 刀 柄
是 机 床 和 刀 具 的 最 后 联 结 环 节 ,对 整 个 工 具 系 统 的
AH 工具 系 统 o
72 : 4锥 柄结 构 H F C工 具 系统
数控 工 具 系统
3O L CK工 具系 统 WS U工 具 系统 r O锥柄 结 构 一 C T 工具 系统 1 2 AP O
新刀 f 型 柄{
lM 系筝 fs 具系 K 统 K工 H 具
【 热胀工 具系统
应对 高速 、重 载切 削 的加 工要求 。 目前工具 系统 的设计 大致 可 以分 成两 类 :其 一 ,
数控系统的参数设置与修改

#5
#4
#3
#2
#1
#0
SEQ
INI ISO TVC
数据(#0~#7位的位置)
二、 参数的查询、调用、方法
二、参数类型
1.系统参数 移动轴脉冲当量分母
若此值设为 2. 则系统内部脉 冲当量为:
1/2um
旋转轴脉冲当量分母
若此值设为2, 则系统内部脉 冲当量为: 1o/(1000×2)
二、 参数的查询、调用、方法 二、参数类型
三、 参数备份和修改 二、西门子系统的数据恢复
2. 数据从硬盘中恢复
MMC
(1)“Service”
(2)按扩展键
(3)“Series Start-up”;
(4)“Read Start-up Archive”(垂直菜单)
(5)找到存档文件,并选中“OK
(6)“start”(垂直菜单)
任务七、 数控系统的参数设置与修改
三、 参数备份和修改
一、西门子系统的数据备份
4. 数据备份之系列备份 (2)数据备份到PC卡 3)数据备份过程
➢选择“Service”操作区; ➢选择存档内容NC,PLC,PCU 并定义存档文件名; ➢从垂直菜单中,选择一个作为存储目标; ➢选择备份数据到硬盘,则:“Archive”(垂直菜 单) “Start”。
情景7 数控系统的参数设置与修改
一、 数控系统的参数作用、组成与分类 二、 参数的查询、调用、方法 三、 参数备份和修改
任务七、 数控系统的参数设置与修改
一、 数控系统的参数作用、组成与分类
1.数控系统参数的作用
数控机床的参数是数控系统软件应用的外部条件,它完成数控系统 与机床结构及机床各种功能的匹配。CNC通过参数可以知道机床的 一些特定数据,识别机床上的不同部件,并能判断如何执行用户编 写的指令。 包括轴的数量、进给率、快速、螺距误差补偿、加速度、反馈、跟 随误差、比例增益、自动换刀功能等。 有些数控机床的参数需要调试后才能确定,如螺距误差补偿参数的 确定。有些数控机床的工作状态也可以通过参数的修改来调整,如 机床的位置精度调整、主轴的最高转速、坐标轴的快速等。
基于MA6025型万能工具磨床的数控系统改造

CHEN Hu n i a -l n
( i nj n n tue o e h ooy Habn H i n j n 0 7 C ia Hel gi g Is tt fT c n lg , ri , el gi g 1 0 2 , hn ) o a i o a 5
摆 幅 , 而 取 得 了较 好 的 效 果 。 从 关 键 词 : 床 : 控 系统 : 造 磨 数 改
中 图分 类 号 :G6 9 T 5
文献标 识码 : A
文 章 编 号 :0 6 8 3 ( 0 9)3 0 5 — 2 10 — 9 7 2 o 2 — 0 7 0
Ba e n A6 2 -t pe un v r a ute g i de nd um e ia c nt o sd o M 0 5 y i e s l c tr rn r a n rc l o r l
摘 要 : 文章在 原有 MA6 2 0 5型 万能 工具 磨床 的传 动 系统土 安 装 了一个 简 易数 控 系统 , 系统通 过控 制 步进 电机 的转速 该
和 走步数 , 而控 制 工作 台的往 复运 动 速度 和行 程 , 相 当于进 口专用磨 床 中工作 台 不动 , 进 即 电机 控 制 砂 轮 的 摆 动 频 率 和
本 次 M 6 2 万能 工 具磨 床 的数 控 系 统 改造 中 , A 05型 我
中。 由于步 进 电机 的 角位 移或 线性 位 移与 控制 脉 冲个 数成
们通过对步进 电机速度 的控制改变发 出脉 冲的时间间隔 正比, 而电机 的转速与脉冲频率成正比。因此只要通过改
来 实现 。时 间 间 隔用定 时器 控 制 , 是 因为 这样 更 能 发挥 变脉冲频率就可以调节电机的转速 , 这 从而实现电机的快速 硬 件实 时性 的优 势 , 时减轻 软 件 的任 务 。改 进 系统 采 用 同 对 步进 电机 的串行 控制 。 以下将 从 软件 和硬 件 两个 方 面来 介 绍本 课题 中步进 电机 的控 制 系统 。
车床数控化改造

车床数控化改造摘要由于目前国内的数控机床数量需求量大,达到300万台之巨,要进行全部翻新在时间,物质上尚不具有足够的条件,为了达到的条件,为达到较高精度,实现较好的经济性,对普通车床实行数控开环改造。
本次设计着重对CA6140普通车床的纵横向进给系统改造,并对纵横向进给伺服系统齿轮箱进行改造。
本次设计作了下面的一些工作:1机械部分采用了一级齿轮传动,以BF型步进电动机作为驱动源,以CBM/CDM滚珠丝杠作为重要元件,以便更好的实行软件控制;2数控部分采用MCS-51中的8031作为主控芯片建立一套单片机应用系统。
扩展I/O 接口用8155芯片及外存储器,采用地址锁存和译码器。
3 SolidWorks造型,包括软件的应用和对车床的实体建摸。
关键词:数控机床改造、单片机, 滚珠丝杠BF型步进电机SolidWorksABSTRACBecause of the great number of machine tools in our country ,the number is3,000,000.It is impossible to renew them all without enough time and materialTo reform part of old ones with Numerrical Control(nc) Open-Loop control System to get high precision and high economy is a good way.The design emphases on the reform of lengthwise and axial feed systems, the fear box of the axial system, too.some work has been in the paper:(1) Based on the one-level driving , the style BFstepper Motor which acts the Soure of power, the CDM/CBM screw ball which is the important transmission element, the part of machinery realizes the software control.(2) The numerical control partially uses in MCS-51 8031 to do primarily controls the chip to establish a set of monolithic integrated circuits application system。
数控机床改造策划书3篇
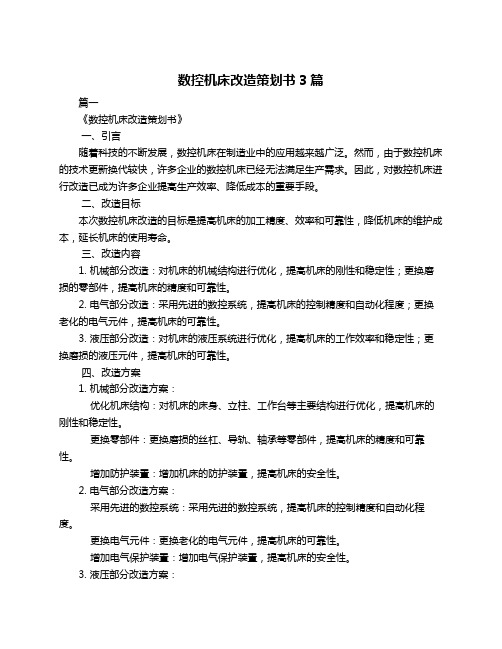
数控机床改造策划书3篇篇一《数控机床改造策划书》一、引言随着科技的不断发展,数控机床在制造业中的应用越来越广泛。
然而,由于数控机床的技术更新换代较快,许多企业的数控机床已经无法满足生产需求。
因此,对数控机床进行改造已成为许多企业提高生产效率、降低成本的重要手段。
二、改造目标本次数控机床改造的目标是提高机床的加工精度、效率和可靠性,降低机床的维护成本,延长机床的使用寿命。
三、改造内容1. 机械部分改造:对机床的机械结构进行优化,提高机床的刚性和稳定性;更换磨损的零部件,提高机床的精度和可靠性。
2. 电气部分改造:采用先进的数控系统,提高机床的控制精度和自动化程度;更换老化的电气元件,提高机床的可靠性。
3. 液压部分改造:对机床的液压系统进行优化,提高机床的工作效率和稳定性;更换磨损的液压元件,提高机床的可靠性。
四、改造方案1. 机械部分改造方案:优化机床结构:对机床的床身、立柱、工作台等主要结构进行优化,提高机床的刚性和稳定性。
更换零部件:更换磨损的丝杠、导轨、轴承等零部件,提高机床的精度和可靠性。
增加防护装置:增加机床的防护装置,提高机床的安全性。
2. 电气部分改造方案:采用先进的数控系统:采用先进的数控系统,提高机床的控制精度和自动化程度。
更换电气元件:更换老化的电气元件,提高机床的可靠性。
增加电气保护装置:增加电气保护装置,提高机床的安全性。
3. 液压部分改造方案:优化液压系统:对机床的液压系统进行优化,提高机床的工作效率和稳定性。
更换液压元件:更换磨损的液压元件,提高机床的可靠性。
增加液压保护装置:增加液压保护装置,提高机床的安全性。
五、改造实施计划1. 项目启动阶段:成立项目改造小组,制定项目改造计划,明确项目改造目标和任务。
2. 方案设计阶段:根据项目改造目标和任务,进行方案设计,包括机械部分、电气部分和液压部分的改造方案。
3. 设备采购阶段:根据方案设计,采购所需的设备和零部件。
4. 改造实施阶段:按照方案设计,进行机床的改造实施,包括机械部分、电气部分和液压部分的改造。
数控机床的数控系统操作指南
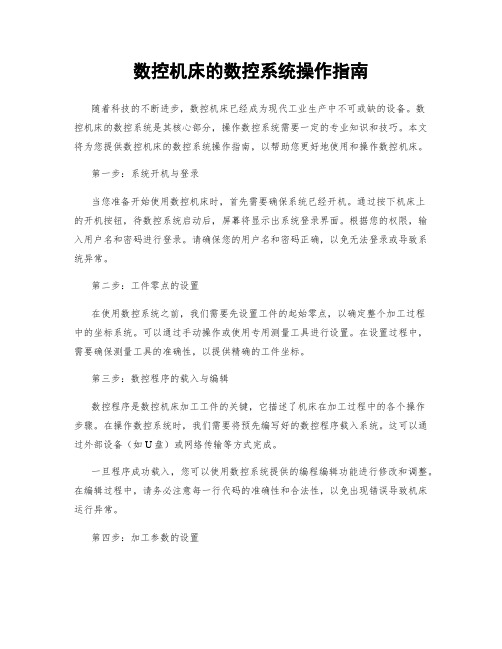
数控机床的数控系统操作指南随着科技的不断进步,数控机床已经成为现代工业生产中不可或缺的设备。
数控机床的数控系统是其核心部分,操作数控系统需要一定的专业知识和技巧。
本文将为您提供数控机床的数控系统操作指南,以帮助您更好地使用和操作数控机床。
第一步:系统开机与登录当您准备开始使用数控机床时,首先需要确保系统已经开机。
通过按下机床上的开机按钮,待数控系统启动后,屏幕将显示出系统登录界面。
根据您的权限,输入用户名和密码进行登录。
请确保您的用户名和密码正确,以免无法登录或导致系统异常。
第二步:工件零点的设置在使用数控系统之前,我们需要先设置工件的起始零点,以确定整个加工过程中的坐标系统。
可以通过手动操作或使用专用测量工具进行设置。
在设置过程中,需要确保测量工具的准确性,以提供精确的工件坐标。
第三步:数控程序的载入与编辑数控程序是数控机床加工工件的关键,它描述了机床在加工过程中的各个操作步骤。
在操作数控系统时,我们需要将预先编写好的数控程序载入系统。
这可以通过外部设备(如U盘)或网络传输等方式完成。
一旦程序成功载入,您可以使用数控系统提供的编程编辑功能进行修改和调整。
在编辑过程中,请务必注意每一行代码的准确性和合法性,以免出现错误导致机床运行异常。
第四步:加工参数的设置在开始加工之前,我们需要设置一些加工参数,以确保数控机床按照预期进行加工。
这些参数包括刀具轨迹、加工速度、进给速度、切削深度等。
不同的工件和加工过程会有不同的参数设置要求,您可以根据实际情况进行调整。
第五步:程序调试与运行在进行实际加工之前,建议进行程序调试和机床测试运行。
调试过程包括模拟运行、手动操作和单节程序运行等。
通过这些方式,您可以发现并解决潜在的问题,确保加工过程的顺利进行。
当一切准备就绪后,您可以将数控机床切换为自动运行模式,开始实际的加工操作。
请确保在加工过程中保持警惕,及时观察机床的运行状态,并根据需要进行必要的调整和干预。
第六步:加工完成与系统关闭在加工完成后,您可以将机床切换为手动模式,停止加工过程。
新代数控系统操作基础-20210914053701

新代数控系统操作基础新代数控系统(New CNC System)以其高效、精准和易用性在工业领域获得了广泛应用。
本教程将为您介绍新代数控系统的基础操作,帮助您快速上手并提高工作效率。
一、系统启动与界面认识1. 启动系统:打开电脑,进入操作系统,找到并双击新代数控系统图标,启动系统。
菜单栏:包含文件、编辑、视图、工具、帮助等选项。
工具栏:提供常用工具的快捷按钮,如新建、打开、保存、撤销等。
操作区:用于显示和编辑加工程序、图形等。
状态栏:显示系统状态、当前坐标等信息。
二、文件操作1. 新建文件:工具栏上的“新建”按钮,或选择“文件”菜单中的“新建”选项,即可创建一个新的加工程序文件。
2. 打开文件:工具栏上的“打开”按钮,或选择“文件”菜单中的“打开”选项,在弹出的对话框中选择需要打开的文件。
3. 保存文件:工具栏上的“保存”按钮,或选择“文件”菜单中的“保存”选项,将当前文件保存到指定位置。
三、加工程序编辑1. 输入程序代码:在操作区的程序编辑区输入或粘贴加工程序代码。
2. 程序校验:工具栏上的“校验”按钮,或选择“工具”菜单中的“程序校验”选项,对输入的程序代码进行校验,确保其正确性。
3. 程序仿真:工具栏上的“仿真”按钮,或选择“工具”菜单中的“程序仿真”选项,对加工程序进行仿真,观察加工过程是否正确。
四、图形显示与编辑1. 图形显示:在操作区的图形显示区,可以显示加工程序对应的加工轨迹、刀具路径等图形。
2. 图形缩放:使用工具栏上的缩放按钮,或选择“视图”菜单中的缩放选项,对图形进行缩放,以便更清晰地观察。
3. 图形旋转:使用工具栏上的旋转按钮,或选择“视图”菜单中的旋转选项,对图形进行旋转,以便从不同角度观察。
五、系统设置1. 参数设置:选择“工具”菜单中的“系统设置”选项,打开系统设置对话框,可以设置系统参数,如坐标系、刀具补偿等。
2. 语言设置:选择“工具”菜单中的“语言设置”选项,可以设置系统界面语言。
数控系统原理介绍

数控系统原理介绍数控系统原理介绍数控系统是一种在机床加工或其他工业领域中使用的先进加工工具,可以大大提高生产效率和制造质量。
数控系统是由软件和硬件两部分组成,它的核心部分是控制器。
控制器通过图形化界面、编程语言和运算器等方式,将计算机程序转化为机器指令,控制机床进行加工操作。
下面我们来介绍数控系统的原理。
一、数控系统的基本组成数控系统由五大基本部分组成:电源系统、机床及工作台部分、传感器及执行器部分、数控装置及软件系统部分、执行机构。
电源系统提供所需的电源电压和电流,以保证数控系统运行所需的稳定电力供应。
机床及工作台部分是数控系统的重要组成部分,包括各类机床、传动装置、定位装置、夹紧装置、转载装置和其他辅助装置等,用于在不同的加工条件下完成加工操作。
传感器及执行器部分包括各种传感器和执行器,能够对各种物理量进行测量和控制。
数控装置及软件系统部分是数控系统的核心部分,由计算机、处理器、输入输出设备组成,主要负责进行控制指令的运作和数据传输。
执行机构包括各种驱动装置和执行机构,如步进电机、伺服电机等,主要用于控制零件的移动位移和加工力度。
二、数控系统的基本工作原理数控系统的基本工作原理是通过输入控制指令,驱动执行机构完成零件的加工操作。
首先,根据工件的设计图纸,制定数控程序。
数控程序一般采用高级编程语言,比如G代码和M代码。
G代码用于描述加工轨迹,M代码用于控制机床运行状态。
接下来,将数控程序输入电脑,通过计算机进行处理和解析。
计算机将程序转换为机器指令,并将其发送到数控装置。
数控装置根据指令的类型和内容,对执行机构进行控制,并将指令转换成相应的控制信号送给执行机构。
执行机构接收信号后,根据指令进行动作,控制零件的受力和轨迹,实现零件的加工操作。
加工过程中,传感器可以实时的监测加工状态,并将监测结果反馈给数控装置,以便下一步的程序控制。
最后,加工完成后,数控系统自动停机,操作人员可以通过电脑或连接到数控机床的监视系统对加工质量进行检查,以确保零件符合要求。
《2024年定梁龙门镗铣床的数控系统改造》范文

《定梁龙门鏜铣床的数控系统改造》篇一定梁龙门铰铣床的数控系统改造一、引言随着制造业的快速发展,数控机床已成为现代工业生产中不可或缺的重要设备。
定梁龙门铰铣床作为机床的一种,其性能和效率直接影响到企业的生产能力和产品质量。
然而,随着技术的不断进步和市场需求的变化,原有的定梁龙门铰铣床数控系统可能已无法满足现代生产的需要。
因此,对定梁龙门铰铣床的数控系统进行改造,提高其性能和效率,已成为当前制造业的重要任务。
二、数控系统改造的必要性1. 技术升级:随着数控技术的不断发展,新的数控系统具有更高的加工精度、更快的加工速度和更强的适应性。
通过改造定梁龙门铰铣床的数控系统,可以使其具备更高的技术性能,满足更复杂的加工需求。
2. 提高效率:原有的定梁龙门铰铣床数控系统可能存在反应慢、操作复杂等问题,导致生产效率低下。
通过改造,可以优化操作流程,提高机床的反应速度和加工效率。
3. 适应市场需求:随着制造业的不断发展,市场对机床的性能和效率要求越来越高。
通过改造定梁龙门铰铣床的数控系统,可以使其更好地适应市场需求,提高企业的竞争力。
三、改造方案1. 硬件改造:对定梁龙门铰铣床的硬件部分进行升级,包括采用更高性能的控制器、更精确的传感器和更稳定的驱动器等。
这些硬件的升级将直接影响到数控系统的性能和稳定性。
2. 软件改造:对原有的数控系统软件进行升级或更换,以适应新的硬件设备。
软件改造包括优化算法、改进操作界面、增加功能模块等,以提高机床的加工精度、效率和操作性。
3. 系统集成:将改造后的数控系统与定梁龙门铰铣床的其他部分进行集成,确保各部分之间的协调工作。
这包括与机床的液压系统、冷却系统、润滑系统等进行联动,以实现更高的加工效率和更好的加工质量。
四、改造效果1. 提高加工精度:改造后的定梁龙门铰铣床数控系统具有更高的加工精度,可以满足更复杂的加工需求。
2. 提高加工效率:改造后的数控系统反应更快,操作更简单,可以显著提高机床的加工效率。
- 1、下载文档前请自行甄别文档内容的完整性,平台不提供额外的编辑、内容补充、找答案等附加服务。
- 2、"仅部分预览"的文档,不可在线预览部分如存在完整性等问题,可反馈申请退款(可完整预览的文档不适用该条件!)。
- 3、如文档侵犯您的权益,请联系客服反馈,我们会尽快为您处理(人工客服工作时间:9:00-18:30)。
各种模块式工具系统之间的组要区别再也模块连接的定 心方式和锁紧方式不同。
回目录
回目录
⑴TMG数控工具系统的类型及其特点
国内常见的镗铣类模块式工具系统有TMG10、TMG21和TMG28 等。这些型号的表示中前一位表示模块连接的定心方式;后 一位表示模块连接的锁紧方式。 ①TMG10-----短圆锥定心,轴向用中心螺钉拉紧,主要 用于刀具组合后不经常拆卸或加工件具有一定批量的情况。 ②TMG21----单圆柱面定心,径向销钉锁紧。主要用于重 型机械、机床等各种行业。 ③TMG28----单圆柱面定心。具有互换性好,连接的重复 精度高,组装/拆卸方便,连接牢固可靠,结合刚性好,主要 用于高效切削
回目录
9.3.2更换刀具头部的数控车削工具系统的发展
共同优点是:换刀时所更换的体积和量都比过去小,,这 样使刀库,机械手尺寸比较紧凑,允许机床刀库有较大的容 量,更适合与多品种、较复杂零件的加工。 ⑴BTS工具系统 ⑵FTS工具系统
⑶CAPTO工具系统
回目录
9.4 刀具预调仪
9.4.1 概述
在使用CNC系统的刀具 直径和长度补偿功能时, 需要知道刀具测量直径和 测量长度(如图) 获得方法: 使用测量装置或采用 机床本身进行测量
回目录
回目录
回目录
回目录
回目录
回目录
回目录
回目录
回目录
回目录
回目录
9.2.2 TMG工具系统
模块式工具系统就是把工具柄部和工作部分分割开来, 分别制成系列化的模块,在经过中间模块,组装成一套套不 同用途、规格的模块式工具。主要由三个部分组成: ①主柄模块----直接与机床主轴连接的工具模块 ②中间模块----为了加长工具轴向尺寸和更换连接直径 的工具模块 ③工作模块----为了装夹各种切削刀具的模块
回目录
9.2.3.4空心短锥工具系统的应用 该工具系统是 一种最新的工具系统,该系统虽有诸多优 点,适合高速、高精度加工需要,但也有其局限性,并不能 完全取代目前所用的BT(7:24)锥度及ABS(圆柱+端面) 等工具系统。 下面对几个具体问题进行分析: ⑴连接精度和刚度 ⑵刀柄强度 ⑶刀柄动平衡 ⑷型号规格 ⑸造价问题
回目录
回目录
2)HSK的工作原理
①德国GUHRING公司的工具系统
*安装刀柄时,两个键槽的深度不同,安装时应该与主轴孔内相应
的端键对应
回目录
回目录
德国GUHRING公司的工具系统手动夹紧装置
HSK型 号 25
螺钉直 最大扭 夹紧力 径/mm 矩/Nm /kN 2.5 1.5 4.5
HSK型 号 50
回目录
9.2.3新型工具系统----空心短锥工具系统
9.2.3.1 概述: ⑴特点: ①定心精度高 ②静动态刚度高
(采用锥度和端面同时定位)
③适合高速加工 ④重量轻,尺寸小,结构紧凑 ⑤清理污垢方便
回目录
9.2.3.2空心短锥工具系统典型结构及型号规格 典型结构 ⑴德国HSK工具系统 (DIN 69893)
数控车削工具系统
9.3.1 通用型数控车削工具系统的发展 9.3.2 个换刀具头部的数控车削工具系统的发展
刀具预调仪
9.4.1 刀具预调概述 9.4.2 刀具预调仪器的选用与管理
刀具管理系统
9.5.1 刀具管理系统的职能 9.5.2 典型刀具管理系统介绍 9.5.2.1 AMS-TMS1.0 刀具管理系统 9.5.2.2 CCTMS 1.0刀具管理系统
注:( )内尺寸为锥柄尺寸
60
回目录
9.2.3.3空心短锥工具系统的检测 (以HSK-63为例)
⑴HSK刀柄圆锥的测量----锥度尺 寸由两个截面上的直径确定 ⑵主轴锥孔的测量 ⑶HSK主轴与刀柄的配合----配合 的最佳状态是在配合长度内, 锥孔与锥柄有充分的过盈,紧 密结合。配合的最差状态是大 端有较小的过盈,小端出现间 隙; ⑷刀柄夹紧面(30o锥面)的测量 ----加工和检测比较困难,需 用专用量具检测,如图。
和ST等三种
2)柄部尺寸——对锥柄表示相应ISO锥度号,对圆柱柄表示直径 3)工具用途代码——表示工具的用途 4)工具规格——表示工具的工作特性;eg 轮廓直径尺寸D和L/
应用范围
5)工作长度——表示工具的设计工作长度(锥柄大端直径处到
端面的距离)
回目录
回目录
⑵
7:24锥柄标准形式: JT
、 BT
回目录
9.2.1 TSG工具系统
TSG工具系统属于整体式结构,是专门为加工中心和镗铣类数 控机床配套的工具系统。特点是锥柄和连杆连成一体;其优点是 结构简单、整体刚性强、使用方便、工作可靠、更换迅速等;缺 点是锥柄的品种和数量较多。 ⑴表示方法:
1)工具柄部形式——一般采用7:24圆锥柄,常用形式有JT、BT
回目录
⑶日本日研(NIKKEN)公司的NC5工具系统
日研公司开发的NC5工具系 统如图所示。定位原理与 其他系统相同,不同的时 把1:10锥柄分成锥套和圆 柱柄两部分套在一起,锥 套端面有碟形弹簧,锥柄 尾端是螺钉孔,用于安装 拉钉。这种夹紧机构可靠 简单 NC5刀柄重复定位精度;径向(X,Y)为 0.003mm,轴向(Z)为0.002mm
回目录
9.2 镗铣类数控工具系统
是镗铣类主轴到刀具之间的各种连接刀柄的总称,其 主要作用是连接主轴与刀具,使刀具达到所要求的位置与 精度,传递切削所需扭矩及保证刀具的快速更换。 按结构可以分为 1:整体式结构(TSG工具系统) 刀具柄部与夹持刀具工作部分连成一体, 使得品种 繁多,管理不便 2:模块式结构(TMG工具系统) 经济、灵活、快速、可靠,通用性强
主要由两部分组成:一部分是刀具;另一部分是刀夹 (夹刀器)。更完善的包括自动换刀装置、刀库、刀具 识别装置和刀具自动自动检测装置。
回目录
9.3.1 通用型数控车削工具系统的发展
(1)圆柱柄的发展 与DIN69880相比,ISO10889有以下特点: ①ISO10889增加了d1=16mm和d1=25mm两种小规格柄部。 ②圆柱柄上90o齿形的尺寸及形位公差具体化了。
⑵美国KENNAMETAL公司的KM工具系统
⑶日本日研(NIKKEN)公司的NC5工具系统
⑷瑞典SANDVIK COROMANT公司的工具系统 ⑸型号规格
回目录
图示为HSK-A63刀柄及主轴锥孔,这是其中一种规格,锥度 为1:10,锥体尾部有端面键槽以传递扭矩,锥体内孔有30o锥 面,夹紧机构的夹爪钩在此面以拉紧刀柄。锥体与主轴锥孔有 微小过盈,夹紧时薄壁锥体产生弹性变形,示锥体与端面同时 靠紧。 HSK系统分为6种型号,刀柄上有供内冷却的冷却液孔
螺钉直 径/mm 4
最大扭 矩/Nm 14.0
夹紧力 /kN 20.0
32
40
2.5
3
3.0
6.0
7.0
12.0
63
805Βιβλιοθήκη 627.054.0
28.0
40.0
回目录
GUHRING公司手动夹紧装置扳手扭矩及夹紧力
②德国MAPAL公司的工具系统
HSK型号 32 40 50
扳手扭矩 /Nm 8 8 15
扳手头宽 度/mm 3 3 4
第九章:数控工具系统
9.1 9.2 概述 镗铣类数控工具系统
9.2.1 TSG工具系统 9.2.2 TMG工具系统 9.2.3 新型工具系统 9.2.3.1 概述 9.2.3.2 空心短锥工具系统典型结构及型号规格 9.2.3.3 空心短锥工具系统的检测 9.3.3.4 空心短锥工具系统的应用
9.3 9.4 9.5
HSK型 号 63 80 100
扳手扭矩 /Nm 20 30 40
扳手头宽 度/mm 5 6 8
回目录
MAPAL公司夹紧扳手扭矩
⑵美国KENNAMETAL公司的KM工具系统
KM工具系统刀柄的基本形状与HSK相似,但其夹紧机构不 同, 下图是其中的一种形式 KM系统的特点时转速高,精度高。最高转速可达 50000r/min重复定位精度在0.002mm以内。静刚度和动刚度 都比HSK系统高,但相比之下,KM系统刀柄显得单薄,有些 零件的强度较差。
回目录
1)HSK工具系统的类型
①HSK-A型 用于加工中心,转速超过40000r/min 时,刀杆需要进行东平衡。 ②HSK-B型 B型圆柱部分直径比A型大一号,锥体 直径比A型小 一号,适于径向切削力较大的工作条件。 ③HSK-C型 A型的变形,圆柱面上没有自动换刀 用的沟槽 ④HSK-D型 B型的变形 ,圆柱面上没有自动换刀 用的沟槽 ⑤HSK-E型 与A型相似,无端面键槽和圆柱面上 的缺口,靠摩擦力传递扭矩,动平衡性能好 ⑥HSK-F型 形状与E型相似,圆柱部分直径比E型 大一号,锥体直径比E型小 一号,适于径向切削力较大的工 作条件。
回目录
回目录
⑵TMG模块型号的表示方法: 表达内容依顺序为:模块接口形式、模块所属种类、 用途或有关特性参数。 ①模块连接的定心方式----即TMG类型代号的十位数字 (0―5) ②模块连接的锁紧方式----即TMG类型代号的个位数字 (0―6、TMG28为8) ③模块所属种类----模块类别标示,一共有5种 ④柄部形式代号----标示锥柄形式 ⑤锥度规格----表示柄部尺寸(锥度号) ⑥模块接口处直径----标示主柄模块和刀具模块接口处外 径 ⑦装在主轴上悬伸长度----是主柄圆锥大端直径只前端面 的距离或者是中间模块前端到其与中间模块接口处的距离
回目录
⑶国外镗铣类模块式数控工具系统简介
1)NOVEX工具系统 2)ABS工具系统 3)WIDAFLEX UTS(KM)工具系统 4)MC工具系统 5)VARILOCK工具系统 6)CAPTO工具系统
回目录
⑷镗铣类模块式数控工具系统的选用