BTS工具系统在数控车床中的应用
机械制造自动化技术试题加答案

1.一个零部件(或产品)的制造从原材料到______________的全过程都不需要人工干预时就形成了制造过程的自动化。
2.制造过程的基本动作是由_______________ 代替人力劳动来完成时这就是机械化。
3.机械制造中采用自动化技术可以有效____________劳动条件。
4. 机械制造中采用自动化技术可以显着___________劳动生产率。
5. 机械制造中采用自动化技术可以有效___________生产周期。
6. 机械制造中采用自动化技术可以显着___________制造成本。
7. 刚性自动化单机是在刚性半自动化单机的基础上增加了自动__________装置而形成的。
8. 凸轮式、非凸轮式和____________式等控制方式是自动化单机的主要控制形式。
9. 提高零件切削加工精度和__________是切削加工自动化的根本目的之一。
10. 数控机床用来完成零件__________个工序的自动化循环加工。
11. 数控机床是用代码化的____________量来控制机床的。
12. 所谓适应能力,就是系统本身能够随着环境条件或结构的不可预计的变化,_____________调整或修改系统的参量。
13. 自动控制系统包括实现自动控制功能的装置及其控制对象,通常由指令存储装置、指令控制装置、_____________,传递及转换装置等部分构成。
14. 自动控制系统应能保证各执行机构的使用性能、_______________、生产效率及工作可靠性。
15. 自动控制系统中的指令存储装置大体上可分为集中存储方式和___________存储方式两大类。
16. 自动控制系统中的指令存储装置的作用是将存在指令存储装置中的指令信息,在_____________的时候发出。
17. 按照预定的程序来控制各执行机构使之自动进行工作循环的程序控制系统可分为固定程序控制和__________程序控制两种控制方式。
18. 在电气控制系统中,按联锁信号在电路中所起的作用可以分为联锁、_________、互锁、短时联锁、长时联锁等。
单片机在机床数控系统中的应用

单片机在机床数控系统中的应用随着工业自动化的不断发展,数控技术在机械加工领域中得到了广泛的应用。
其中,单片机在机床数控系统中的应用尤为重要。
本文将从单片机在机床数控系统中的基本原理、应用场景、发展趋势等方面进行详细探讨。
一、单片机在机床数控系统中的基本原理单片机是一种集成了中央处理器、存储器、输入输出接口等功能的微型计算机。
在机床数控系统中,单片机作为控制核心,接收输入的指令,根据预设的程序进行计算和控制,最终输出控制信号,实现机床的自动化加工。
单片机在机床数控系统中的基本原理如下:1.输入信号处理:单片机通过输入接口接收来自传感器、编码器等设备的信号,并进行处理和转换,以便于后续的程序控制。
2.程序编写:机床数控系统需要根据加工要求编写相应的程序。
程序可以通过编程语言、图形化界面等方式进行编写。
程序中包括加工路径、速度、刀具选择等参数。
3.控制计算:单片机接收程序后,进行计算和控制。
根据预设的程序,单片机计算出控制信号,并通过输出接口输出给执行机构。
4.执行机构控制:执行机构根据单片机输出的控制信号进行动作,实现机床的自动化加工。
二、单片机在机床数控系统中的应用场景单片机在机床数控系统中的应用场景非常广泛,主要包括以下几个方面:1.数控铣床:数控铣床是一种广泛应用的机床,可以用于加工各种复杂的工件。
单片机可以控制铣刀的移动和旋转,实现精确的加工。
2.数控车床:数控车床是一种用于加工圆形工件的机床。
单片机可以控制车刀的移动和旋转,实现高精度的加工。
3.数控钻床:数控钻床可以用于加工各种孔洞,包括直径、深度等参数。
单片机可以控制钻头的移动和旋转,实现精确的加工。
4.数控激光切割机:数控激光切割机可以用于加工各种材料,包括金属、塑料、木材等。
单片机可以控制激光头的移动和功率,实现高效的切割。
5.数控冲床:数控冲床可以用于加工各种形状的金属板材。
单片机可以控制冲头的移动和旋转,实现高精度的加工。
三、单片机在机床数控系统中的发展趋势随着科技的不断发展,单片机在机床数控系统中的应用也在不断升级。
简述数控车床的组成部分及其应用

简述数控车床的组成部分及其应用数控车床是一种利用数控技术来控制车床加工的机床,它具有高精度、高效率、高自动化程度等特点,在工业生产中得到广泛应用。
本文将从数控车床的组成部分和应用方面进行详细介绍。
一、组成部分数控车床主要由以下几个部分组成:1.主机部分:主机是数控车床的核心部分,包括床身、主轴、主轴箱等。
床身是数控车床的基础结构,用于支撑和固定各个部件。
主轴是数控车床的主要工作部件,通过电机驱动实现旋转,完成工件的加工。
2.数控系统:数控系统是数控车床的智能核心,负责对车床的加工过程进行控制和管理。
它由硬件和软件两部分组成。
硬件包括数控装置、编码器、伺服驱动器等,用于实现信号转换和运动控制。
软件包括数控程序和操作界面,实现对加工过程的编程和监控。
3.刀具系统:刀具系统是数控车床上用于切削的工具,包括刀柄、刀片、刀座等。
刀具系统的选择和调整对加工质量和效率有着重要影响。
4.辅助装置:辅助装置包括液压系统、冷却系统、切屑排除装置等,用于提供加工过程中所需的液压力、冷却液和切屑排除等功能。
二、应用领域数控车床在各个工业领域都有广泛应用,特别是在精密加工领域具有独特优势。
以下是数控车床的一些应用领域:1.航空航天:在航空航天领域,需要对航空发动机零部件、飞行器结构件等进行精密加工。
数控车床可以实现高精度、复杂形状的加工要求,提高零部件的质量和性能。
2.汽车制造:在汽车制造过程中,数控车床被广泛应用于发动机缸体、缸盖、曲轴等零部件的加工。
它可以实现高效率、高精度的加工,提高汽车零部件的质量和性能。
3.模具制造:模具制造要求高精度、高表面质量,数控车床可以满足这些要求。
它可以加工各种复杂形状的模具,提高模具的生产效率和质量。
4.光学仪器:在光学仪器制造过程中,需要对镜片、棱镜等光学元件进行精密加工。
数控车床可以实现高精度、光滑度要求高的加工,提高光学元件的质量和性能。
5.医疗设备:在医疗设备制造领域,数控车床被应用于人工关节、骨钉等医疗器械的加工。
国外先进数控工具系统
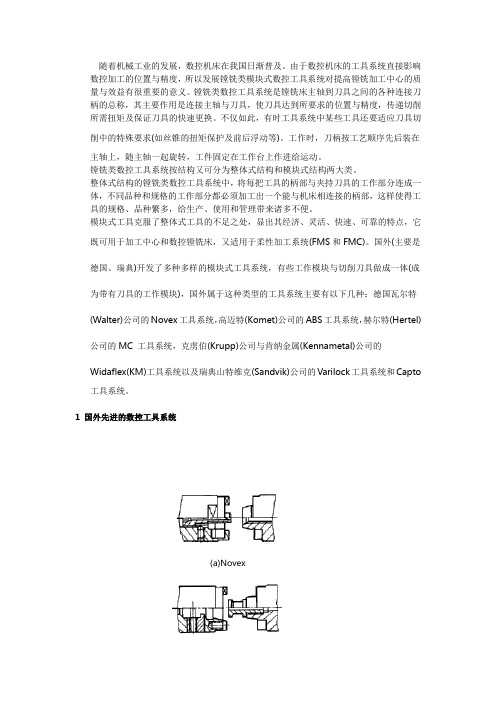
随着机械工业的发展,数控机床在我国日渐普及。
由于数控机床的工具系统直接影响数控加工的位置与精度,所以发展镗铣类模块式数控工具系统对提高镗铣加工中心的质量与效益有很重要的意义。
镗铣类数控工具系统是镗铣床主轴到刀具之间的各种连接刀柄的总称,其主要作用是连接主轴与刀具,使刀具达到所要求的位置与精度,传递切削所需扭矩及保证刀具的快速更换。
不仅如此,有时工具系统中某些工具还要适应刀具切削中的特殊要求(如丝锥的扭矩保护及前后浮动等)。
工作时,刀柄按工艺顺序先后装在主轴上,随主轴一起旋转,工件固定在工作台上作进给运动。
镗铣类数控工具系统按结构又可分为整体式结构和模块式结构两大类。
整体式结构的镗铣类数控工具系统中,将每把工具的柄部与夹持刀具的工作部分连成一体,不同品种和规格的工作部分都必须加工出一个能与机床相连接的柄部,这样使得工具的规格、品种繁多,给生产、使用和管理带来诸多不便。
模块式工具克服了整体式工具的不足之处,显出其经济、灵活、快速、可靠的特点,它既可用于加工中心和数控镗铣床,又适用于柔性加工系统(FMS和FMC)。
国外(主要是德国、瑞典)开发了多种多样的模块式工具系统,有些工作模块与切削刀具做成一体(成为带有刀具的工作模块),国外属于这种类型的工具系统主要有以下几种:德国瓦尔特(Walter)公司的Novex工具系统,高迈特(Komet)公司的ABS工具系统,赫尔特(Hertel)公司的MC 工具系统,克虏伯(Krupp)公司与肯纳金属(Kennametal)公司的Widaflex(KM)工具系统以及瑞典山特维克(Sandvik)公司的Varilock工具系统和Capto工具系统。
1 国外先进的数控工具系统(a)Novex(b)Novex-Radial(c)ABS(d)MC(e)Widaflex(KM)(f)Rotaflex(g)Varilock(轴向拉紧)1Novex 工具系统Novex 工具系统是由德国Walter 公司开发的,其接口型式为圆锥定心,锥孔、锥体与所在模块同轴,轴线上用螺钉拉紧,锥孔端面与锥孔轴线垂直,锥体根部环形端面与锥体轴线垂直,并可与锥孔端面贴合,如图(a)所示。
数控车床厂家对于球杆仪的应用介绍
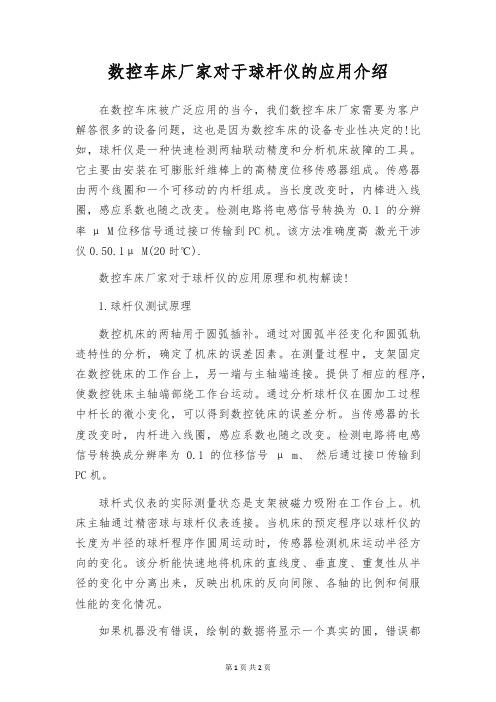
数控车床厂家对于球杆仪的应用介绍在数控车床被广泛应用的当今,我们数控车床厂家需要为客户解答很多的设备问题,这也是因为数控车床的设备专业性决定的!比如,球杆仪是一种快速检测两轴联动精度和分析机床故障的工具。
它主要由安装在可膨胀纤维棒上的高精度位移传感器组成。
传感器由两个线圈和一个可移动的内杆组成。
当长度改变时,内棒进入线圈,感应系数也随之改变。
检测电路将电感信号转换为0.1的分辨率μ M位移信号通过接口传输到PC机。
该方法准确度高激光干涉仪0.50.1μ M(20时℃).数控车床厂家对于球杆仪的应用原理和机构解读!1.球杆仪测试原理数控机床的两轴用于圆弧插补。
通过对圆弧半径变化和圆弧轨迹特性的分析,确定了机床的误差因素。
在测量过程中,支架固定在数控铣床的工作台上,另一端与主轴端连接。
提供了相应的程序,使数控铣床主轴端部绕工作台运动。
通过分析球杆仪在圆加工过程中杆长的微小变化,可以得到数控铣床的误差分析。
当传感器的长度改变时,内杆进入线圈,感应系数也随之改变。
检测电路将电感信号转换成分辨率为0.1的位移信号μ m、然后通过接口传输到PC机。
球杆式仪表的实际测量状态是支架被磁力吸附在工作台上。
机床主轴通过精密球与球杆仪表连接。
当机床的预定程序以球杆仪的长度为半径的球杆程序作圆周运动时,传感器检测机床运动半径方向的变化。
该分析能快速地将机床的直线度、垂直度、重复性从半径的变化中分离出来,反映出机床的反向间隙、各轴的比例和伺服性能的变化情况。
如果机器没有错误,绘制的数据将显示一个真实的圆,错误都会使圆变形。
偏离真实圆的数据反映了数控系统、驱动伺服和机床轴线的机械问题和误差。
2.球杆仪表结构球杆仪通过传感器接口盒与计算机的串口相连。
传感器接口包括一个由9V电池供电的电子电路,该电路扩展,并通过串行接口向计算机报告数据读数。
那么以上就是我们数控车床厂家为大家带来的全部内容分享了,希望大家可以作为重要的参考因素,当然还是要从自身的需求,理性的分析所面临的状况!。
BTS工具系统在数控车床中的应用

BTS工具系统在数控车床中的应用盐城工学院博雅学院BMZ机制072 陈美军摘要:主要介绍数控加工中刀具的一般使用;BTS工具系统的发展史;BTS工具系统在数控车床中的应用。
关键词:数控车床;BTS工具系统;刀具的选用和切削用量的选择在数控加工工艺中是非常重要的;它不仅关系到生产效率的高低,而且关系到加工工件的尺寸精度和表面质量的非常重要的一步;所以数控车床刀具必须具有稳定的切削性能,能够经受较高的切削速度,能够稳定的断屑和卷屑,能够较快的进行选刀和换刀。
所以数控车床应该具有像数控铣床一样的工具系统。
1.数控车床刀具的选择。
数控车床工具系统是车床刀架与刀具之间的连接环节的总称。
它的作用是能够使刀具迅速的定位和更换,以及传递回转刀具所需的动力。
数控工具系统一般的组成一部分是刀具,另一部分是刀夹片,自动换刀装置的刀库,刀具的识别装置和刀具自动检测装置。
为了适应数控机床对刀具耐用、稳定、易调、可换等的要求,近几年机夹式可转位刀具得到广泛的应用,在数量上达到整个数控刀具的30 %~40 %,金属切除量占总数的80 %~90 %。
数控刀具与普通机床上所用的刀具相比,有许多不同的要求,主要有以下特点: (1) 刚性好( 尤其是粗加工刀具) ,精度高,抗振及热变形小;(2) 互换性好,便于快速换刀;(3) 寿命高,切削性能稳定、可靠;(4) 刀具尺寸便于调整,以减少换刀调整时间;(5) 刀具可靠地断屑或卷屑,利于切屑排除;(6) 系列化,标准化,以利于编程和刀具管理。
2.数控加工切削用量的选择。
合理选择切削用量的原则是,粗加工时,一般以提高生产率为主,但也应考虑经济性,加工设备的稳定性和加工成本;半精加工和精加工时,应在保证加工质量的前提下,兼顾切削效率、经济性和加工成本。
具体数值应根据机床说明书、切削用量手册,并结合经验而定。
(1) 切削深度t :在机床、工件和刀具刚度允许的情况下,t 就等于加工余量,这是提高生产率的一个有效措施。
数控机床辅助装置的应用与调试技巧

数控机床辅助装置的应用与调试技巧数控机床在现代制造业中起着至关重要的作用,而数控机床辅助装置作为提高生产效率和加工质量的重要工具,也越来越受到广大制造业者的关注和重视。
本文将详细介绍数控机床辅助装置的应用和调试技巧,帮助读者更好地理解和掌握这一技术。
首先,我们需要了解什么是数控机床辅助装置。
数控机床辅助装置是指与数控机床配合使用,对加工过程进行监控、指导和控制的设备。
它可以提供指令和反馈信号,使得数控机床能够更加智能地完成加工任务。
常见的数控机床辅助装置有自动换刀装置、自动测量和校正装置、自动送料装置等。
其次,数控机床辅助装置的应用可以提高生产效率和加工质量。
例如,自动换刀装置可以实现快速、准确的刀具更换,大大缩短了换刀时间,提高了生产效率;自动测量和校正装置可以通过测量工件尺寸,并自动校正数控机床的加工参数,使得加工精度更高,加工质量更稳定。
另外,自动送料装置可以实现工件的自动进给,减少了操作工的劳动强度,提高了生产效率。
在使用数控机床辅助装置的过程中,我们还需要注意一些调试技巧。
首先,确保辅助装置的连接正确。
数控机床辅助装置通常需要与数控系统进行连接,因此,在使用前需要仔细检查连接线路,确保连接正确可靠。
其次,进行测试和调试。
在使用数控机床辅助装置前,需要进行测试和调试,以确保其正常工作。
可以通过手动操作数控机床和辅助装置,观察是否有异常情况,并进行相应的调整。
最后,进行操作培训。
数控机床辅助装置通常需要经过专门培训才能熟练掌握,因此,在使用前需要进行相应的操作培训,以提高操作者的技能水平。
除了应用和调试技巧,我们还需要了解数控机床辅助装置的一些注意事项。
首先,定期维护和保养。
数控机床辅助装置在长时间使用后容易出现故障,因此,我们需要定期进行维护和保养,保证其正常工作。
其次,合理使用。
在使用数控机床辅助装置时,需要根据加工任务的具体情况,合理选择合适的辅助装置,并正确设置相关参数,以提高加工效果和质量。
数控工具系统(上)

!
, - 、
一 1 ,
/
! ,
/ ! 专 ! 、 !/
1 、, ^
、 !
1
理程 序 较 多 ,一 般 以 MP A . S F N P T为 默 认 后 处 理 程
序 。但 对于采 用 SE N I ME S系统 的 机 床 ,则不 能 使 用 此后 处理 程序 。原 因是 两 种 系统 进 给 率 执 行 方 式 不
一
( ) 圆柱 面投 影 加 工 1
虽 然 应 用 较 多 ,但需 要
多次调 整并 需 要 逐 一 投影 处理 ,应 用 步骤 最 多 ,并 ቤተ መጻሕፍቲ ባይዱ容易 发生 人为 出错 。
致 ,如果仍 然应 用 MP AN P T后 置 处理 程序 输 出 F .S
( ) 圆柱 面缠 绕加 工 较 投影 加 工 方 式 步骤 有 2 所简化 ,但仍 需 旋 转 处 理 以 及 调整 4轴 数值 ,步 骤
联 接 系 统 ,包 括 主 轴 ( 者 刀 座 ) 或 、刀 柄 ( 及 刀 柄 以
实现刀具 刀 柄 联结 的装 置 ) 和夹 紧机 构 ,而 刀 柄
是 机 床 和 刀 具 的 最 后 联 结 环 节 ,对 整 个 工 具 系 统 的
AH 工具 系 统 o
72 : 4锥 柄结 构 H F C工 具 系统
数控 工 具 系统
3O L CK工 具系 统 WS U工 具 系统 r O锥柄 结 构 一 C T 工具 系统 1 2 AP O
新刀 f 型 柄{
lM 系筝 fs 具系 K 统 K工 H 具
【 热胀工 具系统
应对 高速 、重 载切 削 的加 工要求 。 目前工具 系统 的设计 大致 可 以分 成两 类 :其 一 ,
嵌入式系统在机床安全控制中的应用

嵌入式系统在机床安全控制中的应用嵌入式系统是一种特殊的计算机系统,其硬件和软件均为特定应用场景而设计,常常被嵌入到其他设备或系统中。
在机床安全控制领域,嵌入式系统发挥着重要的作用。
本文将重点讨论嵌入式系统在机床安全控制中的应用,并探讨其优势和挑战。
嵌入式系统在机床安全控制中的应用主要体现在以下几个方面:1. 监测与控制嵌入式系统可以通过传感器和执行器等硬件设备,实时监测机床的运行状态。
通过对机床各种参数(如温度、振动、功耗等)的实时采集和分析,嵌入式系统能够预测潜在的故障并做出相应的控制措施。
例如,当机床温度过高时,嵌入式系统可以自动调节风扇的转速,以保证机床正常工作。
此外,嵌入式系统还能够监测机床的工作负载,确保机床在合适的负载范围内运行,避免过载或过度负载所带来的风险。
嵌入式系统可以根据不同的工作场景,动态调整机床的参数和控制策略,提高机床的稳定性和可靠性。
2. 故障诊断与预防机床故障是生产线上的常见问题,而嵌入式系统可以实时监测机床的状态,并进行故障诊断和预防。
嵌入式系统能够采集和分析机床各部件的工作情况,通过与预设模型进行比对,确定是否存在异常或潜在故障。
一旦发现故障,嵌入式系统可以及时发送警报,通知相关人员进行维修或更换零部件。
此外,嵌入式系统还可以通过远程连接,将故障信息上传至云端或后台服务器,实现远程监控和远程维护。
这样可以大大提高故障诊断和维修的效率,减少生产线的停机时间。
3. 安全保护机床在运行过程中,存在着许多潜在的安全风险,如碰撞、超速、过载等。
嵌入式系统可以利用传感器和算法,监测机床的工作状态,并根据预设的安全规则进行判断和控制。
当机床工作超出安全范围时,嵌入式系统可以自动停机,避免事故的发生。
嵌入式系统还能够与其他安全设备(如安全门、光栅等)进行联动,以确保工人在接近机床时的安全。
例如,当安全门打开时,嵌入式系统能够实时检测到并立即停机,以防止工人误碰机床,保障工人的人身安全。
抗干扰技术在数控系统中的应用

抗干扰技术在数控系统中的应用
抗干扰技术在数控系统中的应用
1、干扰源抑制:数控系统中会出现各种电磁干扰源,如电源噪声、环境噪声、辐射干扰和机电振动等,应用抗干扰技术可以有效减弱干扰源的影响,保障系统的稳定性和控制的准确性。
2、干扰抑制的特性:应用抗干扰技术可以改善系统的绝缘特性和发射特性,特别是对低频电磁噪声等多见的干扰源,可以有效抑制。
3、数控系统的供电:抗干扰技术可以有效提高系统的供电供应可靠性,使其具有耐热、耐压力强和稳定可靠等特点,可以更好地满足用户的需求。
4、系统控制:应用抗干扰技术,可以将系统内部噪声抑制在可接受的范围内,确保系统的制动性能良好,有效降低系统的振动干扰,大大提高系统的控制准确性和性能。
5、信号处理:抗干扰技术还可以改进数控系统的信号处理能力,使其具有快速响应、调制快速、高级改变速度高等特点,有效提高信号处理的效率。
6、通信处理:抗干扰技术还可以提高数控系统以太网通信功能,可以更好地抑制电磁干扰源,减少信号失真,从而提高数控系统的通讯效率。
7、电子元件的耐久性:应用抗干扰技术可以改善系统的电磁兼容性,大大提高数控系统电子元件的耐久性和可靠性,减少维修和更换的频率。
总之,抗干扰技术在数控系统中的应用,有助于提高系统的稳定性、可靠性和准确性,保障用户在使用数控系统过程中能得到更好的服务帮助。
单片机技术在数控车床中的应用

单片机技术在数控车床中的应用单片机技术是现代工程领域中不可或缺的一项技术。
在制造业中,单片机技术广泛应用于数控设备,以提升机械设备的自动化程度,提高产品的生产效率和质量。
数控车床是其中一个依靠单片机技术进行控制的重要设备。
数控车床是现代机械制造中广泛采用的一种机床,其主要特点是能够通过计算机程序来进行工作材料的精确切削。
与常规机床相比,数控车床具有更快的速度、更高的精度和更复杂的加工能力。
在这项核心技术上,单片机技术发挥了重要作用。
在数控车床中,单片机技术的应用主要体现在以下三个方面:1. 控制系统数控车床的核心是控制系统,其作用是将计算机程序转换为机床动力系统能够理解的控制信号,从而实现精确控制刀具的运动。
单片机可以作为数控车床的控制核心,将程序中的指令转化为电子信号,对机床的各个运动部件进行控制。
通过单片机技术,控制系统可以更加精确、稳定和高速地响应程序指令,实现更高的加工效率与精度。
2. 编程和语言单片机技术还能够用于数控车床的编程和语言方面。
现代数控车床需要用到一种叫做G代码的数字控制语言,用于描述机床的各种动作和操作。
单片机技术可以使数控车床通过外部输入G代码程序,自动运行并执行相关的操作。
通过这种方式,数控车床可以在较短的时间内实现复杂的制造流程,同时还能保证加工的精度和稳定性。
3. 信息读取和处理单片机技术可以用于数控车床的信息读取和处理。
数控车床需要不断地获取工作材料的位置、状态和加工质量等信息,以进行实时的监控和控制。
这些信息可以通过传感器获取,并通过单片机进行处理分析。
通过单片机技术,数控车床可以自动调整刀具的切削参数,以确保最佳的加工效果。
总之,单片机技术在数控车床中的应用,使得机床具有更高的自动化和精确性,提高了生产效率和产品质量,成为现代制造业中不可或缺的关键技术。
在数控车床的应用中,单片机技术可以提高生产效率和产品质量。
下面列出一些相关的数据并进行分析:1. 数控车床的生产效率提高了50%以上。
信息化手段在数控车实习中的应用
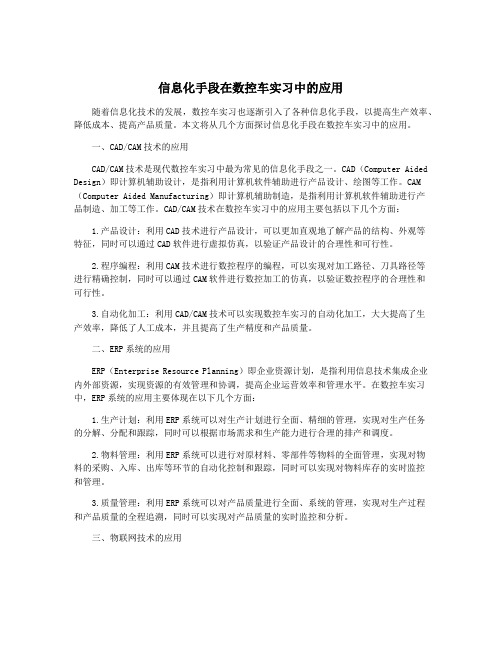
信息化手段在数控车实习中的应用随着信息化技术的发展,数控车实习也逐渐引入了各种信息化手段,以提高生产效率、降低成本、提高产品质量。
本文将从几个方面探讨信息化手段在数控车实习中的应用。
一、CAD/CAM技术的应用CAD/CAM技术是现代数控车实习中最为常见的信息化手段之一。
CAD(Computer Aided Design)即计算机辅助设计,是指利用计算机软件辅助进行产品设计、绘图等工作。
CAM (Computer Aided Manufacturing)即计算机辅助制造,是指利用计算机软件辅助进行产品制造、加工等工作。
CAD/CAM技术在数控车实习中的应用主要包括以下几个方面:1.产品设计:利用CAD技术进行产品设计,可以更加直观地了解产品的结构、外观等特征,同时可以通过CAD软件进行虚拟仿真,以验证产品设计的合理性和可行性。
2.程序编程:利用CAM技术进行数控程序的编程,可以实现对加工路径、刀具路径等进行精确控制,同时可以通过CAM软件进行数控加工的仿真,以验证数控程序的合理性和可行性。
3.自动化加工:利用CAD/CAM技术可以实现数控车实习的自动化加工,大大提高了生产效率,降低了人工成本,并且提高了生产精度和产品质量。
二、ERP系统的应用ERP(Enterprise Resource Planning)即企业资源计划,是指利用信息技术集成企业内外部资源,实现资源的有效管理和协调,提高企业运营效率和管理水平。
在数控车实习中,ERP系统的应用主要体现在以下几个方面:1.生产计划:利用ERP系统可以对生产计划进行全面、精细的管理,实现对生产任务的分解、分配和跟踪,同时可以根据市场需求和生产能力进行合理的排产和调度。
2.物料管理:利用ERP系统可以进行对原材料、零部件等物料的全面管理,实现对物料的采购、入库、出库等环节的自动化控制和跟踪,同时可以实现对物料库存的实时监控和管理。
3.质量管理:利用ERP系统可以对产品质量进行全面、系统的管理,实现对生产过程和产品质量的全程追溯,同时可以实现对产品质量的实时监控和分析。
数控车床实时冲突保护系统

数控车床实时冲突保护系统
Pilla.,U;周显印
【期刊名称】《国外电气自动化》
【年(卷),期】1989(000)006
【总页数】5页(P50-54)
【作者】Pilla.,U;周显印
【作者单位】不详;不详
【正文语种】中文
【中图分类】TG519.1
【相关文献】
1.多级安全实时数据库系统安全性与实时性需求的冲突分析 [J], 牟亚莉;曾浩
2.Nucleus实时操作系统在继电保护系统中的实时性研究 [J], 徐宇柘;钟锐
3.Nucleus实时操作系统在继电保护系统中的实时性研究 [J], 徐宇柘;钟锐
4.硬实时内核智能变电站继电保护实时数字闭环仿真系统 [J], 李非非;韩振峰;李昀;黄胜
5.Nucleus实时操作系统在继电保护系统中的实时性研究 [J], 徐宇柘;钟锐
因版权原因,仅展示原文概要,查看原文内容请购买。
第四章刀具自动化
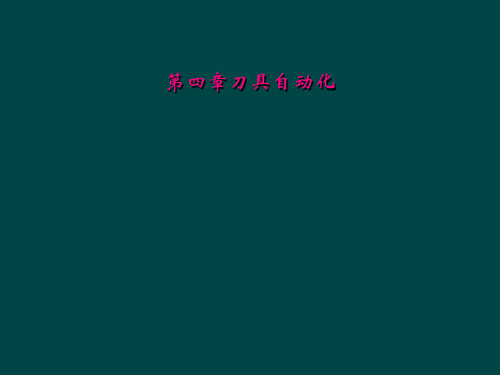
2.刀具运送装置
▪ 当刀库容量较大,布置得离机床主轴较远时,就 需要安排两只机械手和刀具运送装置来完成新旧 刀具的交换工作:
▪ 一只机械手靠近刀库,称后机械手,完成拔刀和 插刀的动作;
镗铣类数控机床工具系统
/cp.php?catid=52&nowmenuid=337&cpath=0052:
弹簧夹头刀杆
三面刃铣刀刀柄 可转位面铣刀刀柄
快换工具系统
双头微调镗杆
第二节 排屑自动化
▪ 一、切屑形成原理 ▪ 二、排屑装置类型 ▪ 1.带式排屑装置 ▪ 2.刮板式排屑装置 ▪ 3.螺旋排屑装置 ▪ 三、切屑及切削液处理装置 ▪ 1.带刮板式排屑装置的处理装置 ▪ 2.负压式纸带过滤装置
的位置;若采用显微投影仪,则让刀尖的横刃与水平线相切、 侧刃与垂直线相切(如图所示);若采用接触式测微仪,则让 千分表的测头与刀尖接触指示出预定值; ▪ (5)察看显示器上的x、Z数值,若符合要求,则操作计算机记 录该数据。
刀具监控
▪ 1.刀具直接监控 ▪ (1)图像匹配法。 ▪ (2)接触法。 ▪ 2.刀具间接监控 ▪ 其常见方法有: ▪ (1)工件表面质量监测 ▪ (2)切削温度监测 ▪ (3)超声波监测 ▪ (4)振动监测 ▪ (5)切削力监测 ▪ (6)功率监测 ▪ (7)声发射监测 ▪ 3.刀具破损声发射监测
第四章刀具自动化
1.自动化刀具的特点
▪ 1)刀具的切削性能必须稳定可靠,应具有高的耐用 度和可靠性;
▪ 2)刀具应能可靠地断屑或卷屑; ▪ 3)刀具应具有较高的精度; ▪ 4)刀具结构应保证其能快速或自动更换和调整; ▪ 5)刀具应配有其工作状态的在线检测与报警装置; ▪ 6)应尽可能地采用标准化、系列化和通用化的刀具,
机械制造自动化技术—课后习题答案

1-1什么是机械化和自动化?它们有什么区别(见复习题)?当执行制造过程的基本动作是由机器(机械)代替人力劳动来完成时称之为机械化。
若操纵这些机构的动作也是由机器来完成时,则就可以认为这个制造过程是“自动化"了1—2机械制造中的工序自动化、工艺过程自动化和制造过程自动化的区别与联系是什么? 1)工序自动化:在一个工序中,如果所有的基本动作都机械化了,并且使若干个辅助动作也自动化起来,而工人只是对这一工序作总的操纵和监管2)工艺过程自动化:一个工艺过程通常包括着若干个工序,如果不仅每一个工序都自动化了,并且把它们有机地联系起来,使得整个工艺过程(包括加工、工序间的检验和输送)都自动进行,而工人仅只是对这一整个工艺过程作总的操纵和监督,这时就形成了某一种加工工艺的自动生产线.3)制造过程自动化:一个零部件(或产品)的制造包括着若干个工艺过程,如果不仅每个工艺过程都自动化了,而且它们之间是自动的有机联系在一起,也就是说从原材料到最终成品的全过程都不需要人工干预,这时就形成了制造过程的自动化。
机械制造自动化的高级阶段就是自动化车间甚至自动化工厂。
1-3机械制造自动化的主要内容有哪些?1)机械加工自动化技术:包含上下料自动化技术、装卡自动化技术、换刀自动化技术、加工自动化技术和零件检验自动化技术等2)物料储运过程自动化技术:包含工件储运自动化技术、刀具储运自动化技术和其它物料储运自动化技术等3)装配自动化技术:包含零部件供应自动化技术和装配过程自动化技术等4)质量控制自动化技术:包含零件检测自动化技术、产品检测自动化技术和刀具检测自动化技术等1—4机械制造自动化的作用1)提高生产率2)缩短生产周期3)提高产品质量4)提高经济效益5)降低劳动强度6)有利于产品更新7)提高劳动者素质8)带动相关技术的发展1—5自动化系统组成1)加工系统2)工件支撑系统3)刀具支撑系统4)控制与管理系统1-6机械制造自动化的类型与特点自动化的分类:1)按制造过程分:毛坯制备过程自动化、热处理过程自动化、储运过程自动化、机械加工过程自动化、装配过程自动化、辅助过程自动化、质量检测过程自动化和系统控制过程自动化。
数控车床的五大基础功能,一篇文章为你悉数详解

数控车床的五大基础功能,一篇文章为你悉数详解数控车床是计算机数字控制车床,也称为CNC车床,是当前国内工业制造领域使用量最大,覆盖面最广的一种数控机床,约占数控机床总数的四分之一。
数控机床是集信息、微电子、气动、液压、机械和电气等多项技术为一体的综合性机电一体化产品,在机械制造设备领域,是具有高精度、高效率、高柔性化和高自动化等优点的工作母机。
数控机床技术含量很高,其技术水平的高低以及总拥有量是衡量一个国家制造业整体水平和国民经济发展的重要标志,而数控车床作为数控机床的主要品种之一,在制造业中也占有非常重要的位置。
长期以来,数控车床一直都受到世界各国的高度重视,在最近数十年得到了快速发展。
数控车床在工业生产中发挥了巨大的作用,其基本功能包括5个方面:准备功能(G功能)、辅助功能( M功能)、进给功能(F功能)、刀具功能(T功能)和主轴功能(S功能)。
1.准备功能(G功能)准备功能也称为G功能(或称为G代码),它是用来指令车床工作方式或控制系统工作方式的一种命令,G功能由地址符G和其后的两位数字组成(00?99),从G00到G99共100种功能,用以指令机床不同的动作如用G01来指令运动坐标的直线进修。
G代码有单次G代码和模态G 代码之分,单次G代码只限于被指令的程序段中有效,而模态G代码在同组G代码出现之前,其代码一直有效。
目前,国内外的数控车床G代码广泛使用ISO代码,但其标准化程度不高,指定功能代码少,指(不能用于其它功能的代码),而不指定代(指在将来有可能规定其它功能的代码)和永不指定代码(指在将来也不指定其功能的代码)的较多不数控系统G代码功能并非一致,使得不同数控系统的编程差异较大,故必须按照所用数控系统的说明书的具体规定使用。
2.刀具功能(T功能)刀具功能也称为T功能,用于指令加工中所用刀具号及自动补偿编组号的地址字,其自动补偿内容主要指刀具的刀位偏差及刀具半径补偿。
在数控车床中,其地址符T的后续数字主要有以下2种规定。
对现车削工具系统的功能分析与设计思想建议

对现车削工具系统的功能分析与设计思想建议
范亚炯;范欢欢
【期刊名称】《世界制造技术与装备市场》
【年(卷),期】2013(000)006
【摘要】仅根据车床类通用不可调刀具的刀柄功能所建立的工具系统,保留了镗铣类工具系统的技术特征,未有效分解与集成车削类刀具刀头的技术功能,也未简化不可调刀具的庞杂体系,因而,不能适应工艺加工系统的集约化目标.具体说系统不能够满足刀具切削部分刀片多元化调换、刃口主偏角、前后角、刃倾角按特定工艺要求作较大幅度调整以及高精加工对断屑、流屑进一步控制的需要,也不能解决对特定工艺方案的服务要求.而车床类带修光刃的大进给精加工可调刀具综合工具系统则能基本解决了这种刀具应用工程系统的一系列问题.该工具系统突破了传统刀具刀头、刀柄、刀套和刀垫各子单元结构未有效集成,系统性不强、使用性能单一与技术含量不高的缺陷,提高了工具系统刀具几何参数可调、刀片多元化调换与随机不重复转位和可重磨的集约化水准.适应加工条件复杂、品种变化多样、工序集中并尽量复合化的刀具应用工程的系列问题.不失为车削工具系统新产品研制的新路径与方法.
【总页数】4页(P91-94)
【作者】范亚炯;范欢欢
【作者单位】兰州敖智商务与机加工信息咨询服务有限公司;兰州敖智商务与机加工信息咨询服务有限公司
【正文语种】中文
【相关文献】
1.数字化笔录系统的功能分析与设计
2.网络考试系统的功能分析与设计
3.基于空间数据库的徐州房产测绘综合管理系统的功能分析与设计
4.基于微信公众号的鼓山景区智慧化服务系统的功能需求分析与设计
5.自动崩解仪系统的功能分析与设计
因版权原因,仅展示原文概要,查看原文内容请购买。
- 1、下载文档前请自行甄别文档内容的完整性,平台不提供额外的编辑、内容补充、找答案等附加服务。
- 2、"仅部分预览"的文档,不可在线预览部分如存在完整性等问题,可反馈申请退款(可完整预览的文档不适用该条件!)。
- 3、如文档侵犯您的权益,请联系客服反馈,我们会尽快为您处理(人工客服工作时间:9:00-18:30)。
BTS工具系统在数控车床中的应用盐城工学院博雅学院BMZ机制072 陈美军摘要:主要介绍数控加工中刀具的一般使用;BTS工具系统的发展史;BTS工具系统在数控车床中的应用;圆柱柄的发展;通用型数控车削工具系统的发展关键词:数控车床;BTS工具系统;圆柱柄;通用型刀具的选用和切削用量的选择在数控加工工艺中是非常重要的;它不仅关系到生产效率的高低,而且关系到加工工件的尺寸精度和表面质量的非常重要的一步;所以数控车床刀具必须具有稳定的切削性能,能够经受较高的切削速度,能够稳定的断屑和卷屑,能够较快的进行选刀和换刀。
所以数控车床应该具有像数控铣床一样的工具系统。
1.数控车床刀具的选择。
数控车床工具系统是车床刀架与刀具之间的连接环节的总称。
它的作用是能够使刀具迅速的定位和更换,以及传递回转刀具所需的动力。
数控工具系统一般的组成一部分是刀具,另一部分是刀夹片,自动换刀装置的刀库,刀具的识别装置和刀具自动检测装置。
为了适应数控机床对刀具耐用、稳定、易调、可换等的要求,近几年机夹式可转位刀具得到广泛的应用,在数量上达到整个数控刀具的30 %~40 %,金属切除量占总数的80 %~90 %。
数控刀具与普通机床上所用的刀具相比,有许多不同的要求,主要有以下特点: (1) 刚性好( 尤其是粗加工刀具) ,精度高,抗振及热变形小;(2) 互换性好,便于快速换刀;(3) 寿命高,切削性能稳定、可靠;(4) 刀具尺寸便于调整,以减少换刀调整时间;(5) 刀具可靠地断屑或卷屑,利于切屑排除;(6) 系列化,标准化,以利于编程和刀具管理。
2.数控加工切削用量的选择。
合理选择切削用量的原则是,粗加工时,一般以提高生产率为主,但也应考虑经济性,加工设备的稳定性和加工成本;半精加工和精加工时,应在保证加工质量的前提下,兼顾切削效率、经济性和加工成本。
具体数值应根据机床说明书、切削用量手册,并结合经验而定。
(1) 切削深度t :在机床、工件和刀具刚度允许的情况下,t 就等于加工余量,这是提高生产率的一个有效措施。
为了保证零件的加工精度和表面粗糙度,一般应留一定的余量进行半精加工和精加工。
数控机床的精加工余量可略小于普通机床。
(2) 切削宽度L一般L 与刀具直径d 成正比,与切削深度成反比。
经济型数控加工中,一般L 的取值范围为: L = (0. 6~0. 9) d 。
(3) 切削速度v :提高v 也是提高生产率的一个措施,但v 与刀具耐用度的关系比较密切。
随着v 的增大摩擦随之增大,温度升高,刀具耐用度急剧下降,故v 的选择主要取决于刀具耐用度。
另外,切削速度与加工材料也有很大关系,例如用立铣刀铣削合金钢30CrNi2MoVA 时,v 可采用8m/ min 左右;而用同样的立铣刀铣削铝合金时,v 可选200m/ min 以上。
(4) 主轴转速n (r/ min) :主轴转速一般根据切削速度v 来选定。
计算公式为n = v/πd式中,d 为刀具或工件直径(mm) 。
数控机床的控制面板上一般备有主轴转速修调倍率) 开关,可在加工过程中对主轴转速进行整倍数调整。
(5) 进给速度vF :vF 应根据零件的加工精度和表面粗糙度要求以及刀具和工件材料来选择。
vF 的增加也可以提高生产效率。
加工表面粗糙度要求低时,vF 可选择得大些。
在加工过程中,vF 也可通过机床控制面板上的修调开关进行人工调整,但是最大进给速度要受到设备刚度和进给系统性能等的限制。
随着数控机床在生产实际中的广泛应用,数控编程已经成为数控加工中的关键问题之一。
编程人员必须熟悉刀具的选择方法和切削用量的确定原则。
从而保证零件的加工质量和加工效率,充分发挥数控机床的优点,提高企业的经济效益和生产水平3.工具系统的发展史。
本世纪七十年代末八十年代初,随着机械加工行业中被加工零件的形状日益复杂,精度的不断提高,以及批量少,加工品种多的要求。
在电子工业取得巨大进步的基础上,自动换刀数控车削中心机床取得了日益广泛的应用。
相应地,对于这类机床刀具也提出了一些新的要求。
模块式车削工具系统也在此基础上发展起来。
这种工具一般都可以将切削部分从刀座上卸下,其连接部分的刚性及精度均很高,为自动换刀提供了方便。
这种刀具模块辅以刀具测头、进给力监测技术以及刀具自动更换装置,可实现无人看管自动加工。
因此,发展这种具有自动换刀能力和刀具监测能力的模块式车削工具系统,是国外自动加工的一个重要的趋势。
近几年,一些工业发达国家的工具制造厂对车床的自动换刀工具系统进行了大量的研究工作,主要的有BTS机床工具系统。
4.BTS工具系统在数控车床中的应用。
瑞士SANDVIK公司于1980年在芝加哥机床博览会上首先推出的模块式工具系统(BTS),其切削头部有一系列不同的刀具模块,可以完成车削.镗削.钻削.切断.攻螺纹以及检测工作。
这种工具的连接部分由拉杆和拉紧“T”形孔组成。
在拉紧过程中,能使拉紧孔稍微的变形,从而获得很高的定位精度和连接刚度,实验表明,其径向定位精度可达±0.002mm,轴向定位精度可达±0.005mm。
在切削速度为1.67m/s。
进给量为0.73m/r,背吃刀量分别为1.5和10的情况下测量系统刚度、其刀尖位置变形情况是:Py和Px方向<0.005mm。
这种模块式工具可手动换刀,也可以机动换刀,手动换刀需5s,机动换刀只需2s。
5.圆柱柄的发展德国工程师协会把快换刀的几种较好的结构进行了研究,制订为标准(VD13425)。
其中的圆柱柄结构获得了日益广泛的应用。
后来,在这种圆柱柄的基础上制订了德国国家标准DIN69880。
国际标准化组织1997 年也把它制订为国际标准(I801889),目前我国等效采用的国家标准也正在制订中。
DIN69880 和I8010889,两者的主要区别有:(1)I8010889 增加了d1 = 16 和252 种小规格柄部。
(2)圆柱柄上90°齿形的尺寸及形位公差具体化了(DIN69880 没有)。
(3)圆柱柄上90°齿形的齿数比DIN69880 有所减少。
(4)圆柱柄根部空刀形状改了,更便于车削。
(5)圆柱柄根部增加了o型橡胶圈。
(6)与d2配合规格16、20 和25 时为H6;30 ~ 80 时为H5。
它的夹紧原理是:圆柱柄安装孔内的齿形夹紧块的定位尺寸L5比圆柱柄上齿形的定位尺寸L2长0. 3mm,压紧时齿形单面接触,从而获得愈来愈广泛的应用。
目前,许多车床厂和附件厂按上述标准来设计刀架,最近几年进口的数控车床及车削中心,采用这种圆柱柄刀夹的占有相当大的比重。
由此可见,数控车床工具系统与刀架的连接型式采用这种圆柱柄会成为一种发展趋势。
国内上海第二机床厂、宝鸡机床厂、云南机床厂、机床研究所等都有与此相适应的机床产品。
6.通用型数控车削工具系统的发展在圆柱柄的前端设计成夹持各种车刀和轴向刀具的工作部分就形成了较为通用的工具系统。
工具系统中夹持矩形截面车刀的称为刀夹。
车刀与圆柱柄轴线垂直的,叫做B 型刀夹。
它分为左右切、正反切、长型短型共8 种(即Bl、B2、⋯⋯B8 型),因刀具尺寸不同而形成l 个系列。
刀与圆柱柄轴线平行的,叫做C 型刀夹。
它同样分为左右切、正反切共4 种(即Cl、C2、⋯⋯C4 型),每l 种型式也都是l 个系列。
装轴向刀具的习惯上称为刀柄,有装圆柱刀杆的El 和E2 型刀柄和装带扁尾莫氏锥柄刀具的Fl 型刀柄。
有E3 和E4 型弹簧夹头刀柄和自紧钻夹头刀柄。
为了提高数控车床的加工效率,根据工序集中的原则,出现了车削中心,它不仅能完成数控车床上所加工的同轴内外圆表面,而且通过安装动力刀具的转塔刀架与主轴自动分度或慢回转联动动作,还能完成在工件轴向和径向等部位进行钻削、铣削、攻螺纹和曲面加工,在开发数控车床用工具系统时,必须与车削中心用工具———带动力刀柄有机地联系起来,使所开发的车削工具系统既可以用于数控车床也可用于车削中心,绝不应搞成2 套装夹型式各异的工具系统。
国外已有了符合DIN69800 圆柱柄的产品。
在国内,车削工具系统尚处在开发研制阶段,还没有形成较完整的系列及标准,更未形成专业化生产。
与主机相比,车削工具系统的开发已有滞后,应引起足够的重视,可以预料,在这一领域有着广阔的潜在市场。
7.结语。
随着先进科技的发展,各种先进的工具系统被应用到数控切削加工中。
然而我国却没有自己研制的一套工具系统实在让人难以接受。
机械行业在国民经济中占有非常重要的一部分,然而国家绝大部分的数控方面的技术却靠进口。
国外却对我们进行技术上的封锁。
我们是新一代的这方面的接班人,我希望在未来我某一天情况会相反,我坚信这一天的到来,坚信中国人是最棒的。
查考文献[1]曹琰主编.数控机床应用与维修.北京:电子工业出版社,1994.[2]上海式金属切削技术协会.金属切削手册[M].上海:科技技术出版社,2000.[3]李福生主编.实用数控机床技术手册.北京:北京出版社,1993.[4]陈书法. 金属削加工中切削参数好优化设计[J]. 机械研究与应用,1999(4):32 - 33.[5]吴祖育,秦鹏飞主编.数控机床.上海:上海科技出版社,1990.[6]熊光华主编.数控机床.北京:机械工业出版社,2001.作者:作者单位:(盐城工学院机械设计制造及其自动化系,江苏盐城)刊名:英文刊名:年:2011。