植绒印花落毛常见的故障
面料印花过程中常见问题及产生原因

面料印花过程中常见问题及产生原因面料印花过程中常见问题及产生原因问题一丝网印花对花不准定义:两种以上颜色的花型,印在织物上以后有一种或几种颜色的花纹脱开或压叠、错位,未印在该印的位置,这种现象叫做对花不准。
产生原因:1.印花版与印花台或印花机上的定位器配合间隙过大。
当印花版上定位器产生松动时,刮板的运行与版面产生的力度会使印花版偏移,花纹不能印在该印的位置。
2. 当印花版框变形,粘贴在版框上的丝网有局部松动现象时,版上部分花纹就会移离出原来的位置。
3.同一个花型中的每个印花版版面干湿程度相差较大,湿度大的版面较松涨或局部松驰严重,在刮板运行时使版面的`花纹向受力方向移动,织物上花纹的局部或全部就会发生不同程度的错位现象。
4. 在印花版运行期间,牵动了被印的衣片或布匹,使已印的花纹在印台上产生移动。
5. 印花版绷网时的丝网张力相差较大或不均匀,在受温度、湿度影响时,丝网张力小或不均匀的版面花纹容易发生移位。
问题二渗化(扩散、色)定义:织物上一种或几种颜色、花纹的轮廓边缘向外扩展,在花纹边缘的全部或局部形成了与花纹颜色相同,色泽较淡的毛糙色边。
两种不同颜色的花纹相接或邻近时出现第三色相,这些现象都称为渗化。
产生原因:1. 涂料印花色浆中增稠剂含量不足或水量过多,印浆粘稠度达不到应有的要求。
由于印浆的流动速度较快,使织物上的花纹色浆向花纹边缘以外流动较多,形成花纹轮廓不清晰现象。
2. 印花操作时,刮板运行的速度慢、压力大、带浆量多、往返次数频繁等,都会使花纹给浆量过多。
由于超过了织物的载浆量,色浆就会向花纹以外渗色。
3. 当花纹面积大,织物得浆量多时,印花后的织物在较长时间层叠放置后,湿度会增大,花纹色浆容易向外扩散。
4. 配制印花色浆时搅拌不均匀或印浆被直接加水稀释,这些都会影响或破坏印浆在乳化状态时的稳定性。
5. 在合成纤维织物、合成纤维与天然纤维混纺织物或交织织物上印花时,由于合成纤维具有疏水性,印浆很容易向花纹外渗化。
关于印花材料使用过程中的三个常见问题及解决方案

(本文转自 如需用于商业用途 请务必征求允许)关于印花材料使用过程中的三个常见问题及解决方案:1:塞网,及阴影很多印花厂都是用简易厂房,气温比较高。
有的在5-8月份可以达到40℃气温比较高,容易出现塞网。
印花时可适当添加5%以内的纯净水或3%以内的保湿剂。
不可以添加自来水,因为每个地方的自来水的PH值都不一样,有可能会造成浆料反粗或胶化,反而更塞网。
因为目前的布料的成份很杂,化纤料在印花布的比例越来越多,部分生产商在夏季的配方中添加有保湿剂成份,在印化纤成份比较重的布料时要注意出现阴影或渗油的情况,因为化纤布的吸油量小,如果胶浆的保湿剂加多了就会出现阴影或渗油现象。
打板时注意弟二天看印花的反面或边缘有没有出现阴影或渗油现象。
2:布料升华现在做体育运动服的品牌90%以上的布料都是化纤布,大部分深颜色的化纤布都有可能会产生布料升华现象。
测试布料是否会升华的方法:在布料上直接印100%的白胶浆,自然干燥后150 ℃过热2-3分钟或150 ℃烫压20秒,24小时后如果没有产生升华现象代表这种布料的安全的,如果有升华现象的就要用防升华打底浆做处理了。
水浆常见的问题及解决方案固色牢度及干湿擦差水浆的固色成份是固浆,在同一比例的色种,固浆的份量越多固色牢度越好,同时手感就越差,一般按颜色深浅添加量在10 -20%,如果添加量到了20%色牢度仍然达还到要求可以添加1-3%的固色剂并充分做好热处理.水浆的干湿擦是没法像胶浆一样可以达到4级以上的。
如果处理得好可以达到3级。
3:印花时出现花边在印化纤布及TC布时容易出现花边或空气湿度大时也容易出现花边。
水浆也叫乳化浆,是靠乳化剂将水和印花水乳化达到水油平衡的原理,如果水油没有达到平衡点就会容易出现花边,可以适当增加印花水和松节水的比例或者增加水浆的粘度.另外,热烫印工艺的另一个发展趋势就是先烫后印,即烫印之后再在烫印箔上进行叠印。
先烫后印工艺同样得益于烫印箔化学性能的改善和提高,从而可以采用UV油墨在烫印箔上进行印刷。
如何解决印花生产中常见故障(3)

如何解决印花生产中常见故障(3)在柔印生产中经常会出现印刷品的实地部位白点特别多,擦版后白点依旧存在。
遇到这种情况时:首先应该立即检查静电消除器、除尘部分是否有故障需要处理;其次要检查油墨(uv)黏度是否过高,再测量一下油墨的温度,若黏度较大、温度在30℃以下,我们就应该加点撤黏剂进去,同时多搅拌使油墨的流动性增强。
生产中温度在33℃时油墨的印刷适性较好。
还有一种情况就是实地部分的白点都集中在固定部位的圆周上,特别是在两边,此时就需要重新调节压力,调节三辊平衡可以解决此问题。
再有就是增加车间的湿度,可以降低空气中的粉尘,也可以降低白点的出现几率。
在印品上出现圆周方向的墨丝时,首先要看刮墨后的网纹辊表面是否有墨丝,如果网纹辊表面有墨丝,可能是刮墨刀有问题(比如有缺口等),换刮刀后如果还有,再检查刮刀,如果刮刀完好再检查油墨的黏度,若黏度偏高加入撤黏剂即可。
在印刷品的实地出现奶白状丝带。
我们在生产中用到的有国产uv 油墨和进口uv油墨,用国产油墨时,在普通的四色油墨中加入透明白或加遮盖白等几种墨调配成专色油墨,会在印品上出现奶白状的丝带,初步认为是由于各种连接料及溶剂、自由体互溶稳定性差造成的,最好的方法是让厂家直接供给配好的专色油墨,效果较好。
或者在生产时配好了以后多加搅拌、或高速开车,也可以提前两三天配好油墨,均可以有效的缓解。
配墨时在未经实验的情况下不是同一厂家的油墨切不可互相调配专色,特别是国产墨和进口油墨进行调配,更是印刷中的大忌,这样做还会产生深浅不一等现象,并且油墨很快会变质胶连。
五、模切刀上的故障生产中的模切刀主要有半切透和全切透两种。
在半切透模切中,若放置在印刷张力范围以内,会对最近的印刷色组套准有影响,因此应放置在印刷张力范围以外较好。
在模切过程中压力的调节很重要,特别是快到寿命期的刀,在提高速度时应该适当的加大压力,在接纸后套准时应稍减压力,以防断纸或收废断纸。
停机后要离压吊刀,切勿撞到或接触较硬的物品,同时注意清洁齿轮、肩铁和底辊。
印花瑕疵的形态及产生的主要原因(一)

13.染料飛濺(網版彈跳、濺漿、散漿沾污)
係因色漿飛濺造成的色點沾污。
該疵點多在滾筒印花的加工速度快,篩網印花中起版動作不當,色漿粘度不合適等情況下發生。
14.紗尾沾污
係印花坯綢(布)的紗尾在印花織物上造成的紗線狀污疵。
4-2.搭色污斑(印花台板污斑)
5.雙版色差(刮漿不勻)
係在織物的橫向呈現出一定間隔的色澤深淺。
該疵病多在篩網框、刮刀安裝不良或刮漿不勻情況下發生。
6.色漿不足(脫漿)
即花紋部分顏色缺乏。
通常在色漿補充不及時,刮漿刀壓力不勻、刮漿刀硬度不當,刮漿刀繼電器故障、印花台板表面有凹凸,色漿粘度及漿料不適當等情況下發生。
多因印花坯綢(布)的紗線處理不良所致。
10.彎曲(花形歪斜)
即花紋對於織物的經緯紗線呈傾斜或彎曲狀。
通常在印花坯布(綢)本身有緯斜或縫頭不良或台板貼布歪斜等情況下發生。
11.色點
係小點狀的顏色污斑。
通常在色漿中有未溶解之染料或附著有雜質的情況下發生。
12.摩擦污點(拖色)
係在印花花紋尚未充分乾燥時接觸異物,摩擦著花紋部分的顏色、又沾污到其他部分所形成的疵點。
印花瑕疵的形態及產生的主要原因(一)
1.露白
經紗或緯紗的一部分翻轉或移動到織物的正、反面,在花紋上呈現出酷似被撓後留下的道道。
該疵病大多由於色漿滲透不良、印花後的處理不當(Fra bibliotek力不勻等)而造成。
2.印花色澤不勻(斑點)
印花的一部分變成了如同沙魚表皮形狀那樣的花斑。
該疵病多在色漿粘度不適當、篩網網眼選擇不當或貼布不勻等情況下發生。
3.滲色(化開)
制绒段常见不良及常规解决方法

可编辑版
8
片源异常及解决方法
4、线痕
线痕片大幅存在,线痕片存在的隐患为:深线痕可能导致更高碎片率,多线 线痕可能影响外观并对效率有轻微影响。
线痕表现形式:线痕可从外观直接看出,一般为一根或数根直且细的沟壑(缺照 片)。
对单晶而言,线痕分为单线线痕及多线线痕,单线线痕一般因切割断线引起,多 线线痕一般为切割浆料异常引起(如回收液的大量使用)。
黑名单:当前因各厂家自身控制以及我们采购、质量的严格把关,线痕片出现极
少。
可编辑版
9
设备异常及解决办法
设备引起的制绒异常主要有如下几个特征:
1、独立性。由于设备的损坏,尤其是制绒设备的损坏,并不会同时产生,因此,因 设备引起的异常往往仅表现为某一个槽或某一条线;
2、异常硅片的规律性。设备异常,如鼓泡管堵塞,加热器损坏,其制绒出来的硅片 往往呈现一致的特征,并且在位置方面也有规律性。
制绒段常见异常及常规解 决方法
可编辑版
1
制绒不良树状结构图
可编辑版
2
片源异常及解决方法
1、指纹及划痕
指纹区
划伤区
可编辑版
指纹片源于:硅片厂家在硅片清洗过程时进 行裸手插片,或者插片时所穿戴的手套 不能满足隔汗要求(自身来料检有时也 会引入);
划痕源于:硅片厂家在插片过程的摩擦,同 时也来源于硅片厂家的硅片检验以及我 们公司自身的来料检验。
可编辑版
17
工艺异常及常规解决办法
制绒异常及解决办法:
1、小雨点 小雨点因制绒过程IPA不足引起,IPA不足除引起小雨点外,也使跳片的概率上升, 因此,需予以及时解决。
静电植绒印花技术
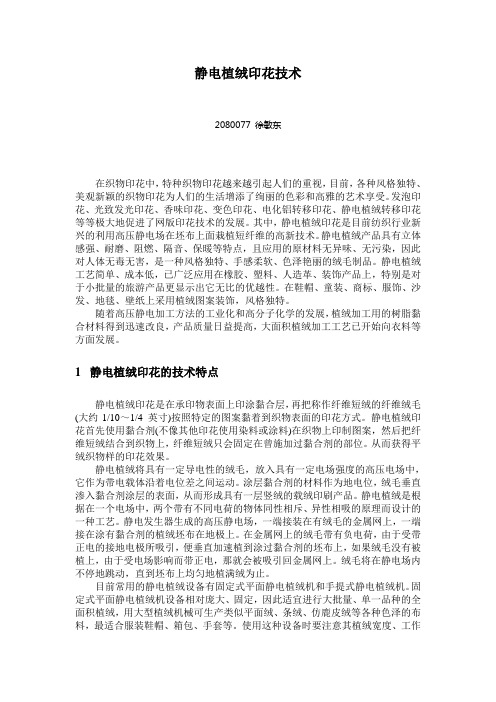
静电植绒印花技术2080077 徐敏东在织物印花中,特种织物印花越来越引起人们的重视,目前,各种风格独特、美观新颖的织物印花为人们的生活增添了绚丽的色彩和高雅的艺术享受。
发泡印花、光致发光印花、香味印花、变色印花、电化铝转移印花、静电植绒转移印花等等极大地促进了网版印花技术的发展。
其中,静电植绒印花是目前纺织行业新兴的利用高压静电场在坯布上面栽植短纤维的高新技术。
静电植绒产品具有立体感强、耐磨、阻燃、隔音、保暖等特点,且应用的原材料无异味、无污染,因此对人体无毒无害,是一种风格独特、手感柔软、色泽艳丽的绒毛制品。
静电植绒工艺简单、成本低,已广泛应用在橡胶、塑料、人造革、装饰产品上,特别是对于小批量的旅游产品更显示出它无比的优越性。
在鞋帽、童装、商标、服饰、沙发、地毯、壁纸上采用植绒图案装饰,风格独特。
随着高压静电加工方法的工业化和高分子化学的发展,植绒加工用的树脂黏合材料得到迅速改良,产品质量日益提高,大面积植绒加工工艺已开始向衣料等方面发展。
1静电植绒印花的技术特点静电植绒印花是在承印物表面上印涂黏合层,再把称作纤维短绒的纤维绒毛(大约1/10~1/4 英寸)按照特定的图案黏着到织物表面的印花方式。
静电植绒印花首先使用黏合剂(不像其他印花使用染料或涂料)在织物上印制图案,然后把纤维短绒结合到织物上,纤维短绒只会固定在曾施加过黏合剂的部位。
从而获得平绒织物样的印花效果。
静电植绒将具有一定导电性的绒毛,放入具有一定电场强度的高压电场中,它作为带电载体沿着电位差之间运动。
涂层黏合剂的材料作为地电位,绒毛垂直渗入黏合剂涂层的表面,从而形成具有一层竖绒的载绒印刷产品。
静电植绒是根据在一个电场中,两个带有不同电荷的物体同性相斥、异性相吸的原理而设计的一种工艺。
静电发生器生成的高压静电场,一端接装在有绒毛的金属网上,一端接在涂有黏合剂的植绒坯布在地极上。
在金属网上的绒毛带有负电荷,由于受带正电的接地电极所吸引,便垂直加速植到涂过黏合剂的坯布上,如果绒毛没有被植上,由于受电场影响而带正电,那就会被吸引回金属网上。
印花常见疵病

印花常见疵病1、刀线(1)形态:在印花织物的某个经向部位,呈现深浅宽条状刀线。
刀线在疵布中出现概率较大。
(2)产生原因:①印花刮刀质量不好,刀片不耐磨、弯曲、被碰撞卷刃。
②刮刀在圆网内接触不良,造成色浆不匀。
③圆网内壁表面局部不够光洁,使刀口受损,给浆不匀。
④色浆中糊料未充分膨化、有硬物混入或涂料色浆中粘合剂选用不当,室温结膜而粘附刮刀刀口。
稳定不溶性偶氮染料印花时,刮刀与圆网摩擦发热,也往往会粘结刀口,产生刀线或堵塞网孔。
(3)防止方法:①根据织物的品种、花型面积的大小、色浆的性能来确定刮刀刀片的规格、压力和角度,以减轻刮刀与圆网的摩擦阻力。
Stork新颖的聚四氟乙烯塑料刀口(刀口外层用聚四氟乙烯塑料嵌入,以减轻刀口与圆网的摩擦力)更适应于圆网印花,但它要求使用低粘度、流变性好的原糊。
②宜选用粘度低、成糊率高、近牛顿型流体的印花原糊。
杜绝杂质的混入,糊料膨化要充分。
③感光前应认真检查网孔的清晰度和内壁的光洁度,控制刮胶时的胶层厚度,防止胶液渗入内壁。
2、嵌圆网网孔(1)形态:印花织物上局部花纹露底。
(2)产生原因:①织物表面未除净的纤维短绒、纱头嵌入圆网的网孔。
②色江中含有杂质。
(3)防止方法:①在圆网印花机进布处加装刷毛吸尘装置,并认真搞好进布处的清洁工作。
②在色浆上机前要用高目数(120目以上)的筛网过滤。
3、露底(1)形态:印花织物上某些花纹处色浅或深浅不匀,甚至露白。
(2)产生原因:主要是织物的花纹上得不到应有的色浆所致。
原因有:①刮刀的选择和压力不适于刮印要求。
②圆网网孔不清晰、网孔大小或网孔堵塞。
③织物半制品前处理时,毛细管效应较差,丝光不足,影响织物的渗透性,易产生色泽不匀或色浅。
(3)防止方法:①印制厚重织物、大块面花型时,选用50mm*0.15mm的刮刀,调节压力和角度,以提高给色量,减轻露底。
②选用低粘度的海藻酸钠、高醚化度的植物胶类糊料或将海藻酸钠与乳化糊拼混使用。
③加强织物前处理的质量控制。
转移印花常见故障及解决方法

随着转移印花产品应用领域的不断扩大,市场对转移印花产品也提出了越来越高的要求,跨入21世纪,消费者对产品的印刷质量会提出更高的耍求,转移印花技术也越来越受到业内企业的重视。
转移印花大都是大量印刷的,如何向客户提供质量持续稳定的印花纸,对转移印花行业来说是一个严峻的课题。
要得到高质量的印花纸,就必须及时解决和预防印花过程中可能出现的任何印花加工故障。
一般来说,当发生故障时,必须抓住基本的一点,那就是看看是什么条件跟正常状态不一样了或搞错了,这些变化的条件正是故障发生的原因。
这些条件包括工艺条件,天气、气候、环境条件、机械状态或各种材料的变化等以及这些变动因素之间的相互作用。
有时,上述条件仅仅发生微小的变化也会引起好几个印刷故障‧甚至在解决一个故障的同时又会引发另一个故障。
所以最好的办法和对策就是预先了解可能引起故障的原因及其预防措施。
1‧塞版在凹版印刷中,网点中的油墨转移率通常在50%~70%,还有50%~30%的油墨总是残留在网点中。
如果该残留率始终保持一定当然没有问题,但在实际印刷过程中,由于某种原因使得网点中的油墨残留率提高时,油墨的转移率就会降低,造成凹印的塞版故障。
发生塞版以后,会导致印刷图案和文字模糊不清,印刷品颜色发生变化,严重时甚至不能进行正常印刷,特别是浅版部位容易发生该故障。
故障原因:(1)油墨干固于版面虽然凹版滚筒网点中油墨的转移率(即转移到承印物表面上的比例)通常是由油墨的类型,黏度,印刷速度等因素来决定的,但不管是哪一种情况,转移后总会有50%~30%的油墨残留在网点中,当这些残余油墨受到某些因素影响发生干固(黏度增大)时,印版滚筒再次进入油墨槽时,就难以完全溶解,油墨转移率也会随之降低。
久而久之,网点就变得越来越浅,转移率也越来越低,最后发生塞版故障。
当然此类塞版故障与油墨类型、溶剂、干燥速度等因素有关,而且与印刷机的构造也有很大关系。
(2)混入杂质在凹版印刷时,印刷基材(纸张)在高速运行时往往会产生静电,在静电的吸附作用下,会使周围的尘埃及基材的切屑等杂质混入油墨中。
印花常见问题处理方法总结
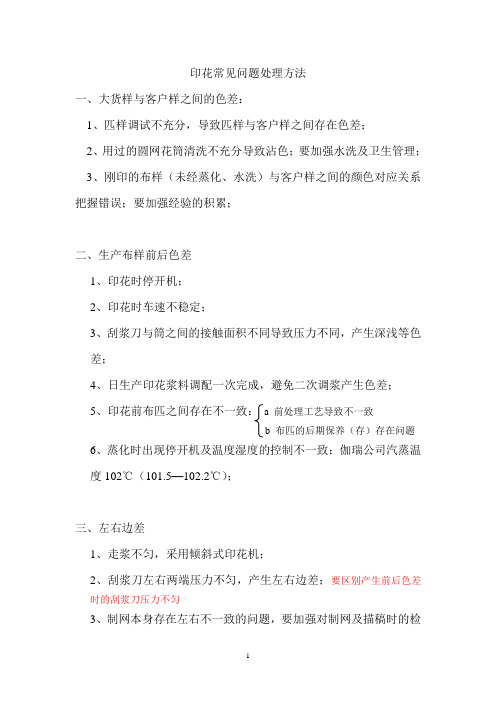
印花常见问题处理方法一、大货样与客户样之间的色差:1、匹样调试不充分,导致匹样与客户样之间存在色差;2、用过的圆网花筒清洗不充分导致沾色;要加强水洗及卫生管理;3、刚印的布样(未经蒸化、水洗)与客户样之间的颜色对应关系把握错误;要加强经验的积累;二、生产布样前后色差1、印花时停开机;2、印花时车速不稳定;3、刮浆刀与筒之间的接触面积不同导致压力不同,产生深浅等色差;4、日生产印花浆料调配一次完成,避免二次调浆产生色差;5、印花前布匹之间存在不一致:a 前处理工艺导致不一致b 布匹的后期保养(存)存在问题6、蒸化时出现停开机及温度湿度的控制不一致;伽瑞公司汽蒸温度102℃(101.5—102.2℃);三、左右边差1、走浆不匀,采用倾斜式印花机;2、刮浆刀左右两端压力不匀,产生左右边差;要区别产生前后色差时的刮浆刀压力不匀3、制网本身存在左右不一致的问题,要加强对制网及描稿时的检查;四、其他印花病疵1、S/O样颜色、制网花筒花样与客户样之间存在差异;2、漏网、漏印(无规律性和循环式出现);3、进布时不平整、有短纱线等;要加强沾污、去污过程(多加多个胶布辊沾绒毛、短纱、灰尘等);4、对花不准;5、安装花筒时错误(装反和序号不一致),要加强开机前的检查;6、花斜:布纬斜圆筒安装不正;7、导带与布之间发生相对位移(老机器容易出现);五、其他关键1、拉幅定型机:主要注意是否有纬斜;2、蒸化机:新乐产品必须进行单幅汽蒸,以免出现水印;另外印花完的布匹要尽快完成汽蒸,以免降低固色率;a 温度和湿度前后控制一致;b 加强清洗工作;3、焙烘机:涂料印花时使用,控制严格温度及升温过程;4、落布后加强保养(存);5、其他前处理:按照规定工艺流程操作;。
印花材料使用过程中常见问题及解决方案

印花材料使用过程中常见问题及解决方案色种常见的问题及解决方案1:颜色迁移色种添加在胶浆上着色,部分颜色会出现颜色迁移,深颜色迁移到浅颜色花位或者有颜色的印花迁移到白色花位,或者印花的颜色跑到没印的布料上去叫颜色迁移。
为了避免生产过程中出现颜色迁移,必须对色种进行耐胶浆迁移测试。
测试方法:色种(3%)+透明浆(97%)-印花-闪烘-盖白色胶浆(100%)-自干-130℃×3秒压烫。
分为5级用内眼能看到迁移现象的不建议用来做胶浆印花,做水浆(涂料印花)印花要注意白色或浅色布料,不同的胶浆测试结果会有出入,差异不太。
荧光色绝大部分都不胶浆迁移, 因此生产前须与客户沟通清楚。
2:热处理变色胶浆印花绝大部分都需要做热处理,部分色种耐热性能差的,做完处理后会出现严重色差,特别是和热固油墨厚板一起混合印花时最为明显。
所以对色种进行耐热测试的必要的.测试方法是:37% 白胶浆+60%透明浆+3%色种自然干燥后以180℃热处理30秒,最高5级,热处理前后肉眼无法区分的为5级3:耐光测试目前很多公司都在接品牌公司单或欧美单,对耐光要求比较严格,如客户有此要求的可以要求供应商提供颜料的耐光数据或弟三方测试报告,或者可以印好印样到弟三方检测机构测试。
一般的测试方法及标准是:JIS L-0842碳弧灯照20小时4:耐溶剂测试目前越来越多的服装拿去干洗,如果颜料耐溶剂性能差的,干洗后服装就会出现退色,变色,造成消费者的不满与投诉。
因此服装公司在收货前会抽样送检,合格后才收货。
如客户有此要求的可以要求供应商提供颜料的耐光数据或第三方测试报告,或者可以印好印样到第三方检测机构测试。
测试方法:JISL-0860(四氯乙烯,40℃30秒)5:耐拔测试在做拔印前要对色种进行耐拔测试,有的颜料不耐还原剂,过热出来就完全成了二个颜色,为了不必要的损失。
因此开货前对色种进小样耐拔测试很有必要。
测试方法:加5%的雕白粉常压105 ℃蒸汽8分钟,或170 ℃热烘3分钟。
绒布印花常见疵病及解决办法

绒布印花常见疵病及解决办法绒布品种有双面绒、单面绒,印花绒布分单面印花绒、双面印花绒。
绒布印花工艺虽然有涂料直接印花、防印工艺以及拔染印花工艺等,但大部分的印花仍以活性染料直接印花工艺为主。
提高印花绒布质量就要结合“绒布”特点,采取措施和对策,克服在生产过程中经常出现的质量问题和难点,使印花绒布成品的实物质量水平不断提高,以满足客户和消费者的需要。
一、绒布印花容易出现的问题1、要保证和提高印花绒布的质量,必须要在如下方面下功夫:(1)要确保印花绒布绒毛起绒效果;(2)易产生白芯、露底、色泽不丰满、得色不匀等印花疵病;(3)注意提高湿摩擦牢度。
2、绒毛起绒效果的保证绒毛起绒效果对于绒布成品来说是关键的外观质量指标之一,同时也是产品内在质量指标之一,良好的绒毛起绒效果与良好的印制效果有着密切的关系,因此良好的绒毛起绒效果一直是绒布印花布追求的目标之一。
印花绒布要获得良好的绒毛起绒效果,必须重视从原坯原纱、漂练前处理、起绒前的辅助整理、起绒机起绒以及印花生产过程中的操作等多个方面。
二、对原坯及纬纱的要求绒毛起绒效果的优劣从原坯及纬纱来看,除决定于织物组织设计外,更取决于原纱的品质。
因绒布织物的起绒主要作用于纬纱,为便于起绒与增加绒布厚度,一般双面平纹绒布经纬纱号比例约在1:2左右,单面哗吱绒约在1:1.5~2之间。
绒布织物经拉绒后,其强力损耗较大,纬向强力一般要损失50%左右。
为保持绒布的成品强力,必须相应提高纱线强力。
绒坯纱线应具有较均匀的纱线条干。
实践证明:绒布用纱的混棉中,一般掺用5-10%精梳落棉对起绒影响不大,如果过多地掺入精梳落棉或下脚棉,则将影响纱线条干,使绒面棉粒过多,绒毛不够均匀。
因落棉的短纤维和棉结过多,纤维强力亦较差,纤维在起绒过程中易被拉断。
纬纱捻度系数,在同一原棉条件下,捻度越小起绒效果愈好,但纱线强力较低。
为兼顾织物弹力,一般纬纱捻度系数在266-285的范围以内,实践证明这既有利于起绒效果,又对织物强力影响不大。
常见印花疵点及产生原因
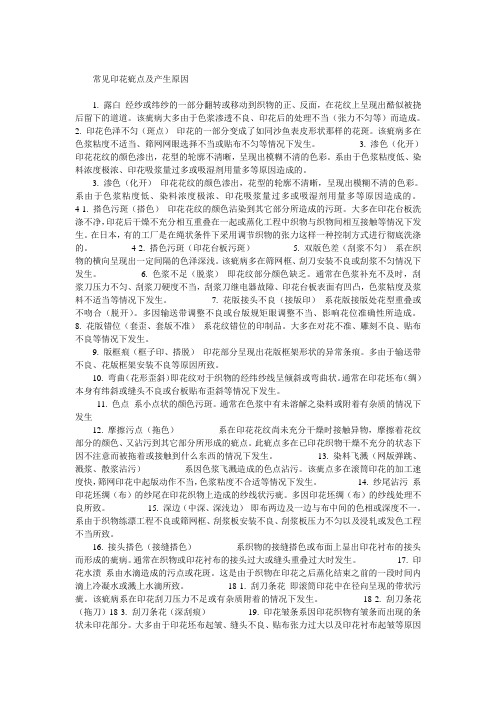
常见印花疵点及产生原因1. 露白经纱或纬纱的一部分翻转或移动到织物的正、反面,在花纹上呈现出酷似被挠后留下的道道。
该疵病大多由于色浆渗透不良、印花后的处理不当(张力不匀等)而造成。
2. 印花色泽不匀(斑点)印花的一部分变成了如同沙鱼表皮形状那样的花斑。
该疵病多在色浆粘度不适当、筛网网眼选择不当或贴布不匀等情况下发生。
3. 渗色(化开)印花花纹的颜色渗出,花型的轮廓不清晰,呈现出模糊不清的色彩。
系由于色浆粘度低、染料浓度极浓、印花吸浆量过多或吸湿剂用量多等原因造成的。
3. 渗色(化开)印花花纹的颜色渗出,花型的轮廓不清晰,呈现出模糊不清的色彩。
系由于色浆粘度低、染料浓度极浓、印花吸浆量过多或吸湿剂用量多等原因造成的。
4-1. 搭色污斑(搭色)印花花纹的颜色沾染到其它部分所造成的污斑。
大多在印花台板洗涤不净,印花后干燥不充分相互重叠在一起或蒸化工程中织物与织物间相互接触等情况下发生。
在日本,有的工厂是在绳状条件下采用调节织物的张力这样一种控制方式进行彻底洗涤的。
4-2. 搭色污斑(印花台板污斑) 5. 双版色差(刮浆不匀)系在织物的横向呈现出一定间隔的色泽深浅。
该疵病多在筛网框、刮刀安装不良或刮浆不匀情况下发生。
6. 色浆不足(脱浆)即花纹部分颜色缺乏。
通常在色浆补充不及时,刮浆刀压力不匀、刮浆刀硬度不当,刮浆刀继电器故障、印花台板表面有凹凸,色浆粘度及浆料不适当等情况下发生。
7. 花版接头不良(接版印)系花版接版处花型重叠或不吻合(脱开)。
多因输送带调整不良或台版规矩眼调整不当、影响花位准确性所造成。
8. 花版错位(套歪、套版不准)系花纹错位的印制品。
大多在对花不准、雕刻不良、贴布不良等情况下发生。
9. 版框痕(框子印、搭脱)印花部分呈现出花版框架形状的异常条痕。
多由于输送带不良、花版框架安装不良等原因所致。
10. 弯曲(花形歪斜)即花纹对于织物的经纬纱线呈倾斜或弯曲状。
通常在印花坯布(绸)本身有纬斜或缝头不良或台板贴布歪斜等情况下发生。
第17周印花常见疵病及防止方法
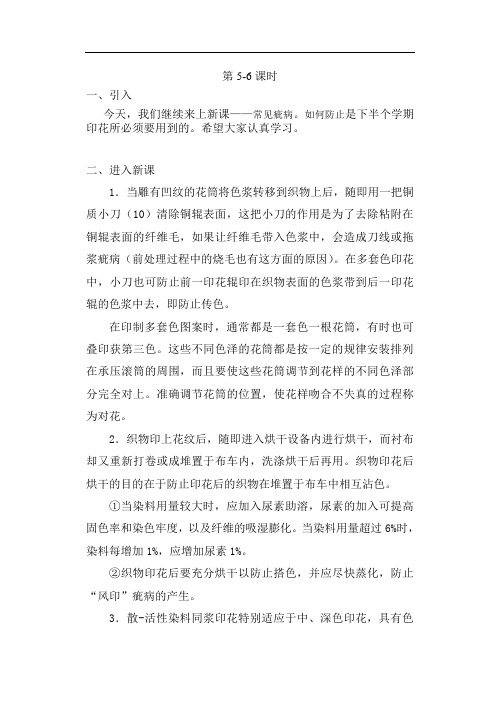
第5-6课时一、引入今天,我们继续来上新课——常见疵病。
如何防止是下半个学期印花所必须要用到的。
希望大家认真学习。
二、进入新课1.当雕有凹纹的花筒将色浆转移到织物上后,随即用一把铜质小刀(10)清除铜辊表面,这把小刀的作用是为了去除粘附在铜辊表面的纤维毛,如果让纤维毛带入色浆中,会造成刀线或拖浆疵病(前处理过程中的烧毛也有这方面的原因)。
在多套色印花中,小刀也可防止前一印花辊印在织物表面的色浆带到后一印花辊的色浆中去,即防止传色。
在印制多套色图案时,通常都是一套色一根花筒,有时也可叠印获第三色。
这些不同色泽的花筒都是按一定的规律安装排列在承压滚筒的周围,而且要使这些花筒调节到花样的不同色泽部分完全对上。
准确调节花筒的位置,使花样吻合不失真的过程称为对花。
2.织物印上花纹后,随即进入烘干设备内进行烘干,而衬布却又重新打卷或成堆置于布车内,洗涤烘干后再用。
织物印花后烘干的目的在于防止印花后的织物在堆置于布车中相互沾色。
①当染料用量较大时,应加入尿素助溶,尿素的加入可提高固色率和染色牢度,以及纤维的吸湿膨化。
当染料用量超过6%时,染料每增加1%,应增加尿素1%。
②织物印花后要充分烘干以防止搭色,并应尽快蒸化,防止“风印”疵病的产生。
3.散-活性染料同浆印花特别适应于中、深色印花,具有色谱齐全,色泽鲜艳,工艺简单的特点。
但由于两种染料在两种纤维的固色条件不一,而且还会对两种纤维产生干扰,存在着棉纤维被分散染料沾染,导致花色鲜艳度差、白地不白的疵病,活性染料也有沾污涤纶的可能,因此必须对染料加以选择。
4.印前处理印前处理包括地色染色和轧氧化剂。
地色染色工艺基本上与常用的冰染料染色工艺相同,但略有差异。
首先要注意尽量少生成浮色,浮色多,影响拔白效果,导致大量拔染剂消耗在浮色上,影响与地色的作用,因此要严格控制偶合工艺条件;其次显色后不能皂煮,因在皂煮过程中染料颗粒会聚集增大,使还原剂分解困难,不易拔染。
在拔染印花中,花筒表面的印花色浆很难刮净,造成没有花形的部分也会沾有少量雕白粉,从而使地色被破坏,形成浮雕或花纹的渗化。
零部件植绒主要缺陷
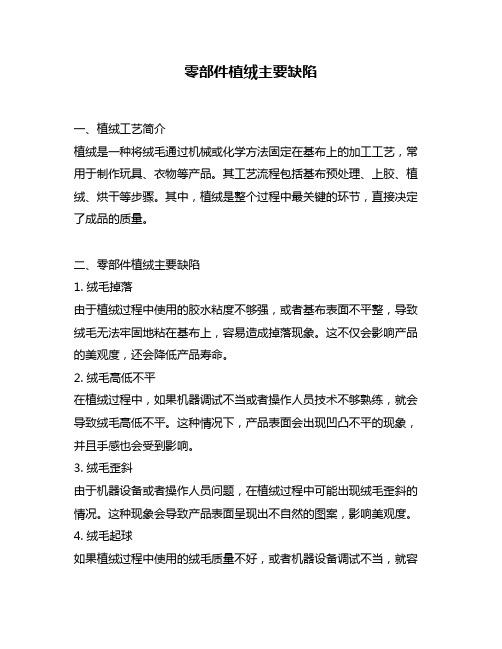
零部件植绒主要缺陷一、植绒工艺简介植绒是一种将绒毛通过机械或化学方法固定在基布上的加工工艺,常用于制作玩具、衣物等产品。
其工艺流程包括基布预处理、上胶、植绒、烘干等步骤。
其中,植绒是整个过程中最关键的环节,直接决定了成品的质量。
二、零部件植绒主要缺陷1. 绒毛掉落由于植绒过程中使用的胶水粘度不够强,或者基布表面不平整,导致绒毛无法牢固地粘在基布上,容易造成掉落现象。
这不仅会影响产品的美观度,还会降低产品寿命。
2. 绒毛高低不平在植绒过程中,如果机器调试不当或者操作人员技术不够熟练,就会导致绒毛高低不平。
这种情况下,产品表面会出现凹凸不平的现象,并且手感也会受到影响。
3. 绒毛歪斜由于机器设备或者操作人员问题,在植绒过程中可能出现绒毛歪斜的情况。
这种现象会导致产品表面呈现出不自然的图案,影响美观度。
4. 绒毛起球如果植绒过程中使用的绒毛质量不好,或者机器设备调试不当,就容易导致产品表面出现起球的现象。
这种情况下,产品寿命会受到影响,并且手感也会变得粗糙。
5. 绒毛脱落由于植绒过程中使用的胶水粘度过高,或者基布表面处理不当,就会导致绒毛无法牢固地粘在基布上,脱落现象比较明显。
这种情况下,产品寿命和美观度都会受到影响。
三、解决零部件植绒主要缺陷的方法1. 优化工艺流程通过对工艺流程进行优化,可以有效避免植绒过程中出现掉落、高低不平、歪斜等问题。
具体来说,可以加强基布处理环节、调整胶水粘度、优化机器设备等方面来改善植绒质量。
2. 选择高品质原材料选用高品质的绒毛和基布,可以有效避免植绒过程中出现起球、脱落等问题。
同时,还可以提高产品的手感和美观度。
3. 增强质量控制意识在植绒过程中,操作人员需要具备一定的技术水平和质量控制意识。
只有这样才能及时发现并解决植绒过程中出现的问题,保证产品质量。
4. 加强售后服务对于已经出现质量问题的产品,企业需要及时提供售后服务。
通过对客户反馈的问题进行分析和解决,可以不断改进产品质量,并提高客户满意度。
常见印花疵病及其防止(平网、圆网、滚筒)

Technology工艺技术常见印花疵病及其防止(平网、圆网、滚筒)平网印花常见疵病及防止措施对花不准在印制两套或两套以上印花织物上全部或部分花型中一个或几个颜色脱开或重合。
采取措施:1.贴布要平要牢。
橡胶导带表面的贴布浆必须分布均匀,厚薄一致及粘度适中,达到“粘、薄、匀”的要求,有利于对花的准确。
2.彻底清洗橡胶导带。
橡胶导带表面的贴布浆和印花色浆经水洗彻底清净,保持清洁、平坦,有利于下一个使用循环时的对花。
3.合理安排印花网版顺序。
从对花角度考虑,应将对花关系比较密切的花纹网版排列在相邻的位置上。
因为织物吸收印花色浆以后,会引起收缩,尤其吸浆量较大的花纹,其收缩程度将会更大,印花网版相隔距离越远,间隔其他花纹刮印到织物上的色浆也越多,同时增加了织物的收缩量,导致对花困难。
糊花(溢浆、渗化)当织物上呈现花纹轮廓不清,花形四周边毛糙,不光洁,色与色之间互相渗溢,胖花发糊,与原样不符时,在印花前一定要将半制品干燥,印花色浆粘度适中,印花网版的升降、移动处于恒位,在刮印时能完全重复于原来的位置上,保证良好的重现性,确保花纹轮廓的清晰。
压档痕对于精细花纹的细茎、白茎等被印花网框压糊,或压得Technology不均匀,不平整,产生鱼鳞斑时,在印花时,要处理好两网版的接版,防止接处的重叠。
如果是花型结构的关系,给开接版带来困难,可在不影响原花样的前提下,大满地花纹上可以交叉插进或其他花型适当延伸一点陪衬的点缀花型,使之避免一个网版两端对接处横向的直线重叠。
对大块面、满地大花,色浆糊料宜选用匀染性较好的糊料,有利于织物得浆均匀,花纹光洁、饱满。
吸浆点当织物上出现有规律的,大小不等的色浆点子,分散在花型周围的一定范围内,条件不变,其形状和距离也基本不变,出现这种情况时,网版上升速度要适当,要求网版和织物分离时有缓冲余地,防止色浆与网版脱离时瞬间的蹦溅。
在糊料选择上要注意降低色浆粘度,保证印制效果。
花纹影印(花纹双印)印花织物上花纹的经向、纬向和边缘部位出现不应有的花色影印,使花型变形时,在绷网时应按绷网工艺所需的张力,将网绷紧防止筛网伸张及刮印时随刮刀往返行进中网版出现松弛状态,保证网版稳定, 并要正确安装调制橡胶毯和刮刀和刮印压力。
印花烫金过程中常见问题及解决方法
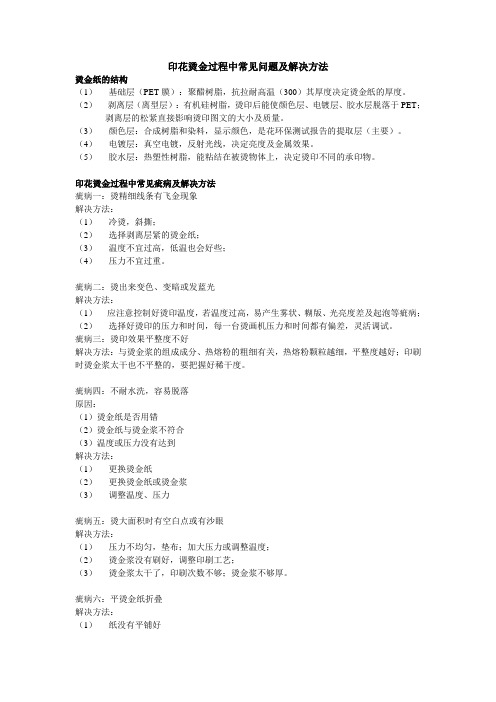
印花烫金过程中常见问题及解决方法烫金纸的结构(1)基础层(PET膜):聚醋树脂,抗拉耐高温(300)其厚度决定烫金纸的厚度。
(2)剥离层(离型层):有机硅树脂,烫印后能使颜色层、电镀层、胶水层脱落于PET;剥离层的松紧直接影响烫印图文的大小及质量。
(3)颜色层:合成树脂和染料,显示颜色,是花环保测试报告的提取层(主要)。
(4)电镀层:真空电镀,反射光线,决定亮度及金属效果。
(5)胶水层:热塑性树脂,能粘结在被烫物体上,决定烫印不同的承印物。
印花烫金过程中常见疵病及解决方法疵病一:烫精细线条有飞金现象解决方法:(1)冷烫,斜撕;(2)选择剥离层紧的烫金纸;(3)温度不宜过高,低温也会好些;(4)压力不宜过重。
疵病二:烫出来变色、变暗或发蓝光解决方法:(1)应注意控制好烫印温度,若温度过高,易产生雾状、糊版、光亮度差及起泡等疵病;(2)选择好烫印的压力和时间,每一台烫画机压力和时间都有偏差,灵活调试。
疵病三:烫印效果平整度不好解决方法:与烫金浆的组成成分、热熔粉的粗细有关,热熔粉颗粒越细,平整度越好;印刷时烫金浆太干也不平整的,要把握好稀干度。
疵病四:不耐水洗,容易脱落原因:(1)烫金纸是否用错(2)烫金纸与烫金浆不符合(3)温度或压力没有达到解决方法:(1)更换烫金纸(2)更换烫金纸或烫金浆(3)调整温度、压力疵病五:烫大面积时有空白点或有沙眼解决方法:(1)压力不均匀,垫布;加大压力或调整温度;(2)烫金浆没有刷好,调整印刷工艺;(3)烫金浆太干了,印刷次数不够;烫金浆不够厚。
疵病六:平烫金纸折叠解决方法:(1)纸没有平铺好(2)压力过重,适当调试疵病七:平烫脱离不均匀(有些地方剥离好,有些地方剥离不完全)解决方法:(1)烫画机底板不平,将低面垫平(2)压力不均匀,适当调整压力(轻一点或重一点)(3)烫金浆没有刷好,烫印时间没有掌握好疵病八:不耐水洗解决方法:(1)考虑烫金纸或烫金浆的选用,打好版后24小时再3测水洗牢度,烫金浆没干透就烫,烫激怒浆一定要干透(2)选择优质的烫金纸疵病九:烫印图案裂开解决方法:烫金浆和烫金纸不匹配,建议更换烫金浆或烫金纸。
植绒对联的缺点

植绒对联的缺点
植绒对联是一种在纸上印刷字体并通过静电植绒技术将绒毛附着在纸面上的对联,它的缺点可能包括以下几个方面:
1. 不易清洁:植绒对联表面的绒毛容易吸附灰尘和杂物,且不易清洁干净。
如果不小心弄脏,可能会影响美观。
2. 可能掉绒:在使用或清洁过程中,植绒对联的绒毛可能会脱落,导致表面不平整,影响视觉效果。
3. 不够耐用:相比于其他材质的对联,植绒对联的耐用性可能较差。
在长期使用或暴露在外界环境中,容易出现褪色、变形等问题。
4. 价格较高:由于植绒工艺的复杂性和材料成本,植绒对联的价格相对较高。
对于一些消费者来说,可能会觉得性价比较低。
5. 环保问题:植绒对联在生产过程中可能会使用一些化学物质和胶水,这些物质可能对环境造成一定的影响。
需要注意的是,以上是植绒对联可能存在的一些缺点,但并不代表所有植绒对联都具有这些问题。
在选择植绒对联时,可以关注产品的质量、品牌和口碑,以获得更好的使用体验。
同时,在使用和保养植绒对联时,也要注意遵循产品说明,以延长其使用寿命。
零部件植绒主要缺陷
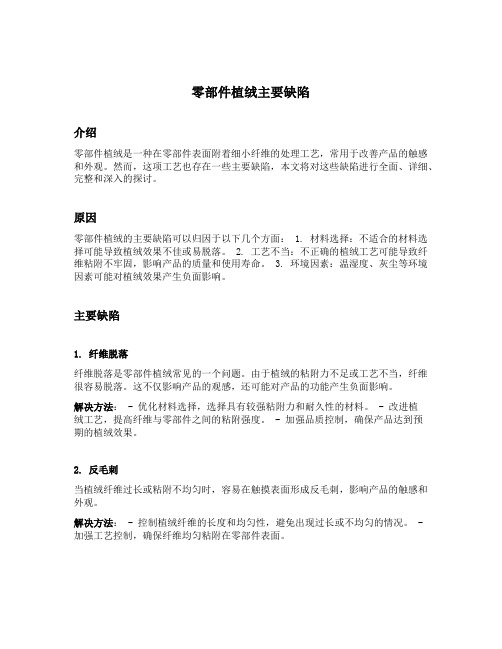
零部件植绒主要缺陷介绍零部件植绒是一种在零部件表面附着细小纤维的处理工艺,常用于改善产品的触感和外观。
然而,这项工艺也存在一些主要缺陷,本文将对这些缺陷进行全面、详细、完整和深入的探讨。
原因零部件植绒的主要缺陷可以归因于以下几个方面: 1. 材料选择:不适合的材料选择可能导致植绒效果不佳或易脱落。
2. 工艺不当:不正确的植绒工艺可能导致纤维粘附不牢固,影响产品的质量和使用寿命。
3. 环境因素:温湿度、灰尘等环境因素可能对植绒效果产生负面影响。
主要缺陷1. 纤维脱落纤维脱落是零部件植绒常见的一个问题。
由于植绒的粘附力不足或工艺不当,纤维很容易脱落。
这不仅影响产品的观感,还可能对产品的功能产生负面影响。
解决方法: - 优化材料选择,选择具有较强粘附力和耐久性的材料。
- 改进植绒工艺,提高纤维与零部件之间的粘附强度。
- 加强品质控制,确保产品达到预期的植绒效果。
2. 反毛刺当植绒纤维过长或粘附不均匀时,容易在触摸表面形成反毛刺,影响产品的触感和外观。
解决方法: - 控制植绒纤维的长度和均匀性,避免出现过长或不均匀的情况。
- 加强工艺控制,确保纤维均匀粘附在零部件表面。
3. 容易积灰植绒零部件容易积灰,特别是在灰尘较多的环境下。
这不仅降低产品的美观度,还可能影响产品的清洁和使用寿命。
解决方法: - 优化材料选择,选择不易吸附灰尘和容易清洁的纤维材料。
- 进行适当的防尘处理,减少灰尘对植绒零部件的影响。
- 提醒用户定期清洁和保养植绒零部件,延长使用寿命。
4. 不适合高温环境植绒零部件在高温环境下容易变形、褪色或失去纤维,影响产品的整体质量和寿命。
解决方法: - 选择适合高温环境的植绒材料,具有良好的耐热性和光敏性。
-加强工艺控制,确保植绒零部件经受得住高温环境的考验。
- 提醒用户避免将植绒零部件暴露在高温环境中,延长使用寿命。
结论零部件植绒是一项常用的表面处理工艺,可以改善产品的触感和外观。
如何解决印花生产中常见故障

如何解决印花生产中常见故障?发现及处理故障的复杂性为了对在机印花生产过程中的故障进行正确的检修,你必须首先具备关于潜在变量--在生产过程中发生的改变--的充分知识。
至少有50个已知变量影响着服装印花生产过程,而且几乎每一个变量都会影响印制的最终质量。
检修服装印花生产过程中的故障之所以如此复杂,其中一个最大的原因要归咎于现实--我们没有赖以生存的标准。
除了产品供应商和技术出版物所提供的有限资料外,印花商只能自己去完善生产流程,以及学会哪些是行之有效的方法。
在机生产中,检修故障的第一个步骤是提升确定某些事情从生产运行一开始就已经发生了改变的能力。
通过在印花机的卸件位置以及烘干机的末端放置已被认可的试印样本,通过实际印件与样本的对比就可以即时发现故障。
丝网张力的故障检修印花机上所有能发生改变及产生问题的变量中,那些与丝网相关的总是带来最大的麻烦。
在进行印花时,你的丝网改变了,印品也会相应地发生变化。
丝网张力是你需要关注的最大的变量。
生产过程中,当丝网的张力下降,就会产生下列问题:1、丝网张力下降,胶刮推拉力变大,网点增大,导致印花过程中出现色调偏移。
2、丝网张力下降,引起丝网剪切能力下降,导致油墨覆盖力不足。
3、丝网张力下降,胶刮阻力变小,还会在图像的刮印末端产生阴影。
4、丝网的不稳定导致套准问题。
单色印花时,张力的轻微改变对印品质量的影响很小。
但在多色(套色)印花时,印品的色调偏移很容易让人发现丝网张力的改变。
作为低张力的补偿,你必须提高胶刮的压力,并(或)增大离版间隙。
或者,你可以试图通过使用可重复绷网的网框,稳定丝网张力,预先防止问题的发生。
龟纹的发现及检修套色印花作业时,龟纹总是最令人沮丧的外观之一。
龟纹出现的形式有三种:第一种龟纹:两个或更多的半色调图案显现在阳图片上时,它们之间的冲突会导致龟纹。
第二种龟纹:产生于图像线数与加网角度之间的冲突。
第三种龟纹:这种龟纹很容易被发现,它产生于丝网上出现的图案与及服装上的织造模式之间的冲突。
- 1、下载文档前请自行甄别文档内容的完整性,平台不提供额外的编辑、内容补充、找答案等附加服务。
- 2、"仅部分预览"的文档,不可在线预览部分如存在完整性等问题,可反馈申请退款(可完整预览的文档不适用该条件!)。
- 3、如文档侵犯您的权益,请联系客服反馈,我们会尽快为您处理(人工客服工作时间:9:00-18:30)。
植绒印花落毛常见的故障
常见的故障之一,其原因较多,主要有以下几方面:
1、绒毛电着处理不当。
由于处理配方不同和染料的影响,绒毛的导电率、飞升性、分散性
等特性不同,使用不同厂家的绒毛性能不同,甚至同一厂家不同颜色的绒毛性能亦有很大差异。
由于绒毛性能差、植绒牢度低,引起落绒现象;
2、绒毛回潮率不合适。
回潮率一般认为在8%左右较为理想,低于8%绒毛飞升性差,难以
二次起跳,回收利用困难,造成基材上剩存大片浮绒;高于8%绒毛在电场中运动速度过快而不规则,由于绒毛植入不规则,经预烘、焙烘、刷毛等工序后即产生严重落绒;
3、黏合剂对落绒的影响。
黏结牢度差、黏合剂黏度不够;黏合剂涂层厚度不够(但并非越
厚越好),一般要求上胶层厚度控制在0、2mm左右;大面积植绒大多用于装饰用品,不考虑产品手感,上胶层厚度可达0、3mm以上;黏合剂的拉伸性不好。
半成品在高温焙烘时,黏合剂和交联剂在高温下发生化学交联固化成膜,在高温拉幅定型时,基布受机械拉力作用产生一定变形,会导致黏着在基布上的黏合剂膜发生断裂,断裂处的绒毛经刷毛后会脱离黏合剂膜,导致发生落绒现象;
4、烘干与焙烘温度控制不当。
植绒后烘干、焙烘温度过低,会在水洗时产生落绒。
根据上
述分析原因,防止落绒办法是电着剂处理配方要合理;控制绒毛的回潮率;尽量减少绒毛和基材的表面电阻比,在刷毛除尘时,基布表面采用蒸汽加湿,令除尘器吸除余绒。