数控车床的程序编制(新)
cnc数控机床编程与操作步骤【新】

数控机床程序编制(又称数控编程)是指编程者(程序员或数控机床操作者)根据零件图样和工艺文件的要求,编制出可在数控机床上运行以完成规定加工任务的一系列指令的过程。
具体来说,数控编程是由分析零件图样和工艺要求开始到程序检验合格为止的全部过程。
一般数控编程步骤如下(见图19-22)。
图19-22 一般数控编程顺序图1.分析零件图样和工艺要求分析零件图样和工艺要求的目的,是为了确定加工方法、制定加工计划,以及确认与生产组织有关的问题,此步骤的内容包括:1)确定该零件应安排在哪类或哪台机床上进行加工。
2)采用何种装夹具或何种装卡位方法。
3)确定采用何种刀具或采用多少把刀进行加工。
4)确定加工路线,即选择对刀点、程序起点(又称加工起点,加工起点常与对刀点重合)、走刀路线、程序终点(程序终点常与程序起点重合)。
5)确定切削深度和宽度、进给速度、主轴转速等切削参数。
6)确定加工过程中是否需要提供冷却液、是否需要换刀、何时换刀等。
2.数值计算根据零件图样几何尺寸,计算零件轮廓数据,或根据零件图样和走刀路线,计算刀具中心(或刀尖)运行轨迹数据。
数值计算的最终目的是为了获得编程所需要的所有相关位置坐标数据。
3.编写加工程序单在完成上述两个步骤之后,即可根据已确定的加工方案(或计划)及数值计算获得的数据,按照数控系统要求的程序格式和代码格式编写加工程序等。
编程者除应了解所用数控机床及系统的功能、熟悉程序指令外,还应具备与机械加工有关的工艺知识,才能编制出正确、实用的加工程序。
4.制作控制介质,输入程序信息程序单完成后,编程者或机床操作者可以通过CNC机床的操作面板,在EDIT方式下直接将程序信息键入CNC系统程序存储器中;也可以根据CNC系统输入、输出装置的不同,先将程序单的程序制作成或转移至某种控制介质上。
控制介质大多采用穿孔带,也可以是磁带、磁盘等信息载体,利用穿孔带阅读机或磁带机、磁盘驱动器等输入(输出)装置,可将控制介质上的程序信息输入到CNC系统程序存储器中。
数控车床的程序编制

数控车床的程序编制一、数控车床的编程特点数控车床的编程有如下特点:(1)在一个程序段中,依据图样上标注的尺寸,可以采纳肯定值编程、增量值编程或二者混合编程。
(2)由于被加工零件的径向尺寸在图样上和测量时都是以直径值表示,所以用肯定值编程时,X以直径值表示;用增量值编程时,以径向实际位移量的二倍值表示,并附上方向符号(正向可以省略)。
(3)为提高工件的径向尺寸精度,X向的脉冲当量取Z向的一半。
(4)由于车削加工常用棒料或锻料作为毛坯,加工余量较大,所以为简化编程,数控装置常具备不同形式的固定循环,可进行多次重复循环切削。
(5)编程时,常认为车刀刀尖是一个点,而实际上为了提高刀具寿命和工件表面质量,车刀刀尖常做成一个半径不大的圆弧,因此为提高加工精度,当编制圆头车刀程序时,需要对刀具半径进行补偿。
数控车床一般都具有刀具半径自动补偿功能(G41,G42),这时可直接按工件轮廓尺寸编程。
(6) 很多数控车床用X、Z表示肯定坐标指令,用U、W表示增量坐标指令。
而不用G90、G91指令。
数控车床的机床原点定义为主轴旋转中心线与车床端面的交点,图3-1中的O即为机床原点。
主轴轴线方向为Z轴,刀具远离工件的方向为Z轴正方向。
X轴为水平径向,且刀具远离工件的方向为正方向。
为了便利编程和简化数值计算,数控车床的工件坐标系原点一般选在工件的回转中心与工件右端面或左端面的交点上。
二、车削固定循环功能由于车削的毛坯多为棒料和铸锻件,因此车削加工多为大余量多次走刀。
所以在车床的数控装置中总是设置各种不同形式的固定循环功能。
如内外圆柱面循环,内外锥面循环,切槽循环和端面循环,内外螺纹循环以及各种复合面的粗车循环等。
各种数控车床的掌握系统不同,因此这些循环的指令代码及其程序格式也不尽相同。
必需依据使用说明书的详细规定进行编程。
1. 圆柱面切削循环编程格式: G90 X(U) — Z(W) — F—;其中:X、Z — 圆柱面切削的终点坐标值;U、W— 圆柱面切削的终点相对于循环起点坐标重量。
数控机床的加工程序编制
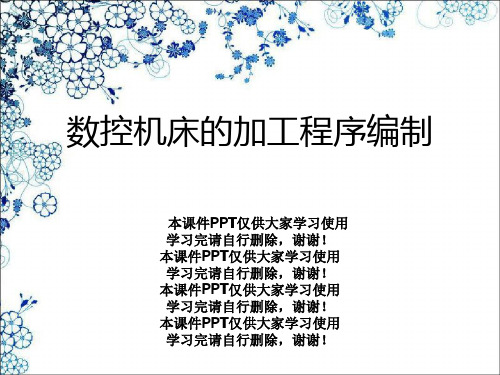
顺序号又称程序段号或程序段序号。位于程序 段之首,由地址符N和后续2~4数字组成。
顺序号的作用:对程序的校对和检索修改;作为 条件转向的目标,即作为转向目的程序段的名称。有 顺序号的程序段可以进展复归操作,指加工可以从程 序的中间开场,或回到程序中断处开场。
顺序号的使用规那么:为正整数,编程时将第 一程序段冠以N10,以后以间隔10递增,以便于修改。
这种从零件图分析到制成控制介质的全部过程, 称为数控加工的程序编制。
数控加工的过程演示如下:加工动画
数控加工流程:
2〕数控程序样本:
O10 N10 G55 G90 G01 Z40 F2000 N20 M03 S500 N30 G01 X-50 Y0 N40 G01 Z-5 F100 N50 G01 G42 X-10 Y0 H01 N60 G01 X60 Y0 N70 G03 X80 Y20 R20 … N80 M05 N90 M30
3〕尺寸字 尺寸字用于确定机床上刀具运动终点的坐标位
置。表示时间暂停的指令也包含在内。其中,用的 较多的尺寸地址符号有3组:
第一组 X,Y,Z,U,V,W,P,Q,R 用 于指令到达点的直线坐标尺寸;
第二组 A,B,C,D,E 用于指令到达点的的 角度坐标尺寸;
第三组 I,J,K 用于指令零件圆弧轮廓的圆心 坐标尺寸。
对于数控车床,其后的数字还兼作指定刀具长 度补偿和刀尖半径补偿用。T后面的数字分2位、4 位、6位。对于4位数字来说,如:
T XX
XX
当前刀具号 刀补地址号
7〕辅助功能字 辅助功能字的地址符是M,后续数字一般为1~3
位正整数,又称为M功能或M指令,用于指定数控 机床辅助装置的开关动作,常用M00~M99见表1 -2。
数控机床的程序编写
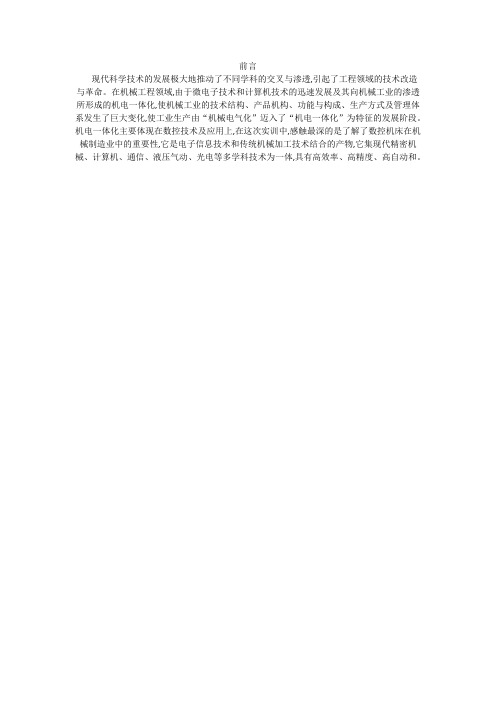
前言现代科学技术的发展极大地推动了不同学科的交叉与渗透,引起了工程领域的技术改造与革命。
在机械工程领域,由于微电子技术和计算机技术的迅速发展及其向机械工业的渗透所形成的机电一体化,使机械工业的技术结构、产品机构、功能与构成、生产方式及管理体系发生了巨大变化,使工业生产由“机械电气化”迈入了“机电一体化”为特征的发展阶段。
机电一体化主要体现在数控技术及应用上,在这次实训中,感触最深的是了解了数控机床在机械制造业中的重要性,它是电子信息技术和传统机械加工技术结合的产物,它集现代精密机械、计算机、通信、液压气动、光电等多学科技术为一体,具有高效率、高精度、高自动和。
摘要数控技术是机械加工自动化的基础,是数控机床的核心技术,其水平高低关系到国家战略地位和体现国家综合国力的水平,近年来,PLC在工业自动控制领域应用愈来愈广,它在控制性能、组机周期和硬件成本等方面所表现出的综合优势是其它工控产品难以比拟的。
随着PLC技术的发展, 它在位置控制、过程控制、数据处理等方面的应用也越来越多。
在机床的实际设计和生产过程中,为了提高数控机床加工的精度,对其定位控制装置的选择就显得尤为重要。
FBs系列PLC的NC定位功能较其它PLC更精准,且程序的设计和调试相当方便。
本文提出的是如何应用PLC的NC定位控制实现机床数控系统控制功能的方法来满足控制要求,在实际运行中是切实可行的。
整机控制系统具有程序设计思路清晰、硬件电路简单实用、可靠性高、抗干扰能力强,具有良好的性能价格比等显著优点,其软硬件的设计思路可供工矿企业的相关数控机床设计改造借鉴。
目录第一章:概述1.1、数控机床的发展趋势 (1)1.2、数控机床的发展历史 (2)第二章:数控加工的特点与刀具2.1、数控机床的特点 (3)2.1.1、数控车床的5大特点 (4)2.2、数控机床的常用种类 (4)2.3、数控机床的刀具选择与应用 (5)第三章:数控机床的程序编写3.1、数控机床的编程 (6)3.1.1、数控机床的自动编程内容与步骤 (6)3.1.2、数控机床编程的基本概览 (9)3.2、数控机床常用术语 (9)第四章:数控车床程序编程 (11)第一章概述1.1、数控机传递个发展趋势数控机床数字控制机床是用数字代码形式的信息(程序指令),控制刀具按给定的工作程序、运动速度和轨迹进行自动加工的机床,简称数控机床。
第四讲 数控车床的程序编制(G70、G71复合循环指令)

(4)精车循环指令(G70) 功能:用于G71、G72、G73粗车完毕后,精加工。
格式:
G70 P(Ns)Q(Nf)
举例:请编制图下图所示零件的加工程序,已知毛坯为Ф35*80的棒 料,材料为45钢
编程前准备工作
(1)工艺分析:该零件由外圆柱面、外圆锥面及圆弧面组成,材料切削性能较好,无热处理和硬度要 求 (2)加工过程 1)对刀,设置编程原点在右端面中心处 2)用G71指令编程粗车外形,X向单边留余量0.25,Z向单边留余量0.2 3)用G70指令编程精车外形 (3)选择刀具 选择硬质合金93°右偏车刀,用于粗精车零件各面,位于T01刀位 (4)确定切削用量
9、说明循环指令G71、G72、G73的区别。 10、说明螺纹切削循环指令G76的使用格式。 11、车刀刀尖半径补偿的意义何在? 12、什么时候应用子程序调用功能?
加工内容
背吃刀量ap/mm
进给量f/mm·rˉ¹
主轴转速s/r·minˉ¹
粗车各外形面
2
0.2
800
精车各外形面
0.25
0.08
数控车床编程实例详解(30个例子)完整

车床编程实例一半径编程图3.1.1 半径编程%3110 (主程序程序名)N1 G92 X16 Z1 (设立坐标系,定义对刀点的位置)N2 G37 G00 Z0 M03 (移到子程序起点处、主轴正转)N3 M98 P0003 L6 (调用子程序,并循环6次)N4 G00 X16 Z1 (返回对刀点)N5 G36 (取消半径编程)N6 M05 (主轴停)N7 M30 (主程序结束并复位)%0003 (子程序名)N1 G01 U-12 F100 (进刀到切削起点处,注意留下后面切削的余量)N2 G03 U7.385 W-4.923 R8(加工R8 园弧段) N3U3.215 W-39.877 R60 (加工R60 园弧段) N4G02 U1.4 W-28.636 R40(加工切R40 园弧段) N5G00 U4 (离开已加工表面)N6 W73.436 (回到循环起点Z轴处)N7 G01 U-4.8 F100 (调整每次循环的切削量)N8 M99 (子程序结束,并回到主程序)1直线插补指令编程%3305车床编程实例二图3.3.5 G01 编程实例N1 G92 X100 Z10 (设立坐标系,定义对刀点的位置)N2 G00 X16 Z2 M03 (移到倒角延长线,Z 轴2mm 处)N3 G01 U10 W-5 F300 (倒3×45°角)N4 Z-48 (加工Φ26 外圆)N5 U34 W-10 (切第一段锥)N6 U20 Z-73 (切第二段锥)N7 X90 (退刀)N8 G00 X100 Z10 (回对刀点)N9 M05 (主轴停)N10 M30 (主程序结束并复位)圆弧插补指令编程车床编程实例三%3308N1 G92 X40 Z5 (设立坐标系,定义对刀点的位置)N2 M03 S400 (主轴以400r/min 旋转)N3 G00 X0 (到达工件中心)N4 G01 Z0 F60 (工进接触工件毛坯)N5 G03 U24 W-24 R15 (加工R15 圆弧段)N6 G02 X26 Z-31 R5 (加工R5 圆弧段)N7 G01 Z-40 (加工Φ26 外圆)N8 X40 Z5 (回对刀点)N9 M30 (主轴停、主程序结束并复位图3.3.8 G02/G03 编程实例2倒角指令编程%3310车床编程实例四图3.3.10.1 倒角编程实例N10 G92 X70 Z10 (设立坐标系,定义对刀点的位置)N20 G00 U-70 W-10 (从编程规划起点,移到工件前端面中心处)N30 G01 U26 C3 F100 (倒3×45°直角)N40 W-22 R3 (倒R3 圆角)N50 U39 W-14 C3 (倒边长为3等腰直角)N60 W-34 (加工Φ65 外圆)N70 G00 U5 W80 (回到编程规划起点)N80 M30 (主轴停、主程序结束并复位)倒角指令编程%3310车床编程实例五N10 G92 X70 Z10 (设立坐标系,定义对刀点的位置)N20 G00 X0 Z4 (到工件中心)N30 G01 W-4 F100 (工进接触工件)N40 X26 C3 (倒3×45°的直角)N50 Z-21 (加工Φ26 外圆)N60 G02 U30 W-15 R15 RL=3(加工R15 圆弧,并倒边长为4的直角)N70 G01 Z-70 (加工Φ56 外圆)N80 G00 U10 (退刀,离开工件)N90 X70 Z10 (返回程序起点位置)M30 (主轴停、主程序结束并复位)图3.3.10.2 倒角编程实例3车床编程实例六圆柱螺纹编程螺纹导程为1.5mm,δ=1.5mm,δ '=1mm ,每次吃刀量(直径值)分别为0.8mm、0.6 mm 、0.4mm、0.16mm图3.3.12 螺纹编程实例%3312N1 G92 X50 Z120 (设立坐标系,定义对刀点的位置)N2 M03 S300 (主轴以300r/min 旋转)N3 G00 X29.2 Z101.5 (到螺纹起点,升速段1.5mm,吃刀深0.8mm)N4 G32 Z19 F1.5 (切削螺纹到螺纹切削终点,降速段1mm)N5 G00 X40 (X 轴方向快退)N6 Z101.5 (Z 轴方向快退到螺纹起点处)N7 X28.6 (X 轴方向快进到螺纹起点处,吃刀深0.6mm)N8 G32 Z19 F1.5 (切削螺纹到螺纹切削终点)N9 G00 X40 (X 轴方向快退)N10 Z101.5 (Z 轴方向快退到螺纹起点处)N11 X28.2 (X 轴方向快进到螺纹起点处,吃刀深0.4mm)N12 G32 Z19 F1.5 (切削螺纹到螺纹切削终点)N13 G00 X40 (X 轴方向快退)N14 Z101.5 (Z 轴方向快退到螺纹起点处)N15 U-11.96 (X 轴方向快进到螺纹起点处,吃刀深0.16mm)N16 G32 W-82.5 F1.5 (切削螺纹到螺纹切削终点)N17 G00 X40 (X 轴方向快退)N18 X50 Z120 (回对刀点)N19 M05 (主轴停)N20 M30 (主程序结束并复位)4恒线速度功能编程%3314车床编程实例七图3.3.14 恒线速度编程实例N1 G92 X40 Z5 (设立坐标系,定义对刀点的位置)N2 M03 S400 (主轴以400r/min 旋转)N3 G96 S80 (恒线速度有效,线速度为80m/min)N4 G00 X0 (刀到中心,转速升高,直到主轴到最大限速)N5 G01 Z0 F60 (工进接触工件)N6 G03 U24 W-24 R15 (加工R15 圆弧段)N7 G02 X26 Z-31 R5 (加工R5 圆弧段)N8 G01 Z-40 (加工Φ26 外圆)N9 X40 Z5 (回对刀点)N10 G97 S300 (取消恒线速度功能,设定主轴按300r/min 旋转)N11 M30 (主轴停、主程序结束并复位)车床编程实例八%3317M03 S400 (主轴以400r/min 旋转)G91 G80 X-10 Z-33 I-5.5 F100(加工第一次循环,吃刀深3mm)X-13 Z-33 I-5.5(加工第二次循环,吃刀深3mm)X-16 Z-33 I-5.5(加工第三次循环,吃刀深3mm)M30 (主轴停、主程序结束并复位)图3.3.17 G80 切削循环编程实例5车床编程实例九G81 指令编程(点画线代表毛坯)图3.3.20 G81 切削循环编程实例%3320N1 G54 G90 G00 X60 Z45 M03 (选定坐标系,主轴正转,到循环起点)N2 G81 X25 Z31.5 K-3.5 F100 (加工第一次循环,吃刀深2mm)N3 X25 Z29.5 K-3.5 (每次吃刀均为2mm,)N4 X25 Z27.5 K-3.5 (每次切削起点位,距工件外圆面5mm,故K值为-3.5)N5 X25 Z25.5 K-3.5 (加工第四次循环,吃刀深2mm)N6 M05 (主轴停)N7 M30 (主程序结束并复位车床编程实例十G82 指令编程(毛坯外形已加工完成)%3323N1 G55 G00 X35 Z104(选定坐标系G55,到循环起点)N2 M03 S300 (主轴以300r/min 正转)N3 G82 X29.2 Z18.5 C2 P180 F3(第一次循环切螺纹,切深0.8mm)N4 X28.6 Z18.5 C2 P180 F3(第二次循环切螺纹,切深0.4mm)N5 X28.2 Z18.5 C2 P180 F3(第三次循环切螺纹,切深0.4mm)N6 X28.04 Z18.5 C2 P180 F3(第四次循环切螺纹,切深0.16mm)N7 M30 (主轴停、主程序结束并复位)图3.3.23 G82 切削循环编程实例6车床编程实例十一外径粗加工复合循环编制图3.3.27 所示零件的加工程序:要求循环起始点在A(46,3),切削深度为 1.5mm(半径量)。
数控车床程序编制的基本方法
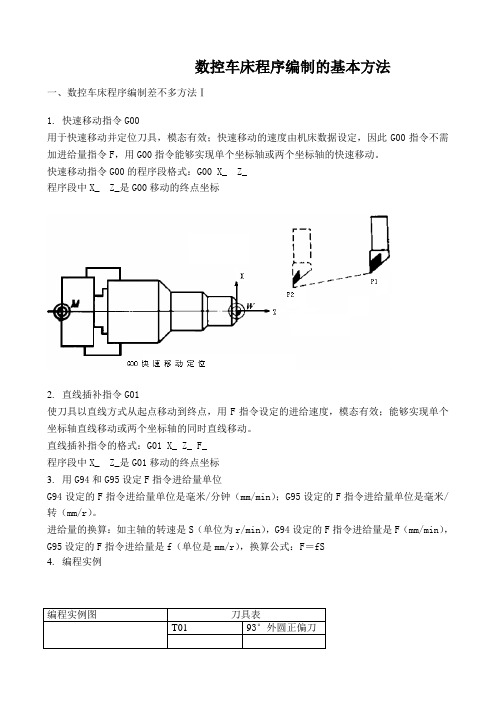
数控车床程序编制的基本方法一、数控车床程序编制差不多方法Ⅰ1.快速移动指令G00用于快速移动并定位刀具,模态有效;快速移动的速度由机床数据设定,因此G00指令不需加进给量指令F,用G00指令能够实现单个坐标轴或两个坐标轴的快速移动。
快速移动指令G00的程序段格式:G00 X_ Z_程序段中X_ Z_是G00移动的终点坐标2.直线插补指令G01使刀具以直线方式从起点移动到终点,用F指令设定的进给速度,模态有效;能够实现单个坐标轴直线移动或两个坐标轴的同时直线移动。
直线插补指令的格式:G01 X_ Z_ F_程序段中X_ Z_是G01移动的终点坐标3.用G94和G95设定F指令进给量单位G94设定的F指令进给量单位是毫米/分钟(mm/min);G95设定的F指令进给量单位是毫米/转(mm/r)。
进给量的换算:如主轴的转速是S(单位为r/min),G94设定的F指令进给量是F(mm/min),G95设定的F指令进给量是f(单位是mm/r),换算公式:F=fS4.编程实例编程实例图刀具表T01 93°外圆正偏刀切削用量主轴速度S 500r/min进给量F 0.2mm/r切削深度a p小于4mm 加工程序程序注释SK01.MPF 主程序名N10 G90 G54 G95 G23 S500 M03 T01 设定工件坐标系,主轴转速为500 r/min,选择1号刀,用G95设定进给量F单位(N10 G90G54G94G23S500 M03 T01)或用G94设定进给量F单位N20 G00 X18 Z2 快速移动点定位N30 G01 X18 Z-15 F0.2 车ø18外圆,进给量F=0.2mm/r(N30 G01 Z-15 F100) 车ø18外圆,进给量F=100mm/minN40 X24 车台阶面N50 Z-30 车ø24外圆长30mm(比零件总长加割刀宽度略长)N60 X26 车出毛坯外圆N70 G00 X50 Z200 快速移动点定位至换刀点N80 M05 主轴停止N90 M02 程序终止二、数控车床程序编制差不多方法Ⅱ1.绝对尺寸G90和增量尺寸G91分别代表绝对尺寸数据输入和增量尺寸数据输入,模态有效。
数控车床的程序编制

数控车床的程序编制数控车床是一种高精度、高效率的现代化机械设备,广泛应用于各种制造行业中。
作为一种数控设备,它需要通过编写程序来实现对零件的加工。
因此,程序编制是数控车床加工过程中不可或缺的一部分。
下面,我们将详细介绍数控车床的程序编制。
一、基本概念数控车床的程序编制其实就是将机床轴的位置、刀具路径、加工参数等信息输入到计算机中,使计算机能够自动控制车床进行加工。
其中,程序包括几何程序和加工参数程序。
几何程序是指需要加工零件的图形和轮廓,也就是加工轨迹;而加工参数则包括切削速度、切削深度、进给速度等。
在程序编制过程中,需要使用数控编程软件。
常见的数控编程软件有EdgeCAM、MasterCAM、PowerMill 等。
这些软件种类繁多,但它们的作用都是一样的。
用户通过这些软件可以编制出符合机床条件的加工程序,并输出G代码到数控机床中,即可自动进行加工操作。
二、程序编制步骤数控车床的程序编制主要包括以下步骤:1. 绘制零件图形:首先需要将需要加工的零件进行绘图,用计算机辅助设计(CAD)软件绘制出准确的零件图形。
在绘制的过程中,需要按照一定的标准进行绘制,包括设计尺寸、精度等方面。
2. 确定坐标系:将零件图形中的坐标系与机床坐标系进行对应,确定数控机床中的X、Y、Z三个坐标轴与设计图中的坐标轴的对应关系。
在编程过程中,需要明确这些坐标的位置、初始值、相对数值等参数。
3. 编写几何程序:将零件图形转化为机床轴的运动轨迹,编写出G代码。
这个过程中需要考虑机床加工的工艺,包括加工方式、刀具方向、切削方式、刀具规格等。
4. 编写加工参数程序:根据要加工的材料,确定加工参数,包括进给速度、切削速度、切削深度、冷却液的使用等参数,并将这些参数编写成M代码。
5. 存储程序:将编写好的几何程序和加工参数程序存储到机床中,可以直接使用或在需要时进行修改。
三、常见的几个注意点1. 选取合适的加工路径:加工路径的选取需要考虑到机床刀具和工件的特性,比如刀具材质、切削方向,工件的形状、材料。
数控车床的程序编制步骤
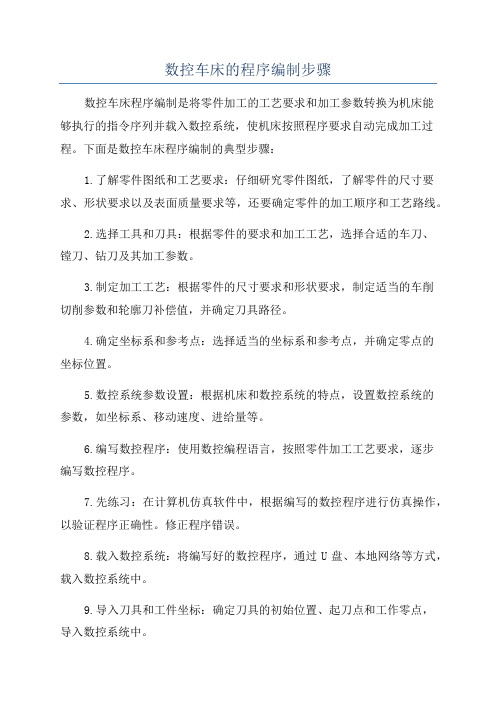
数控车床的程序编制步骤数控车床程序编制是将零件加工的工艺要求和加工参数转换为机床能够执行的指令序列并载入数控系统,使机床按照程序要求自动完成加工过程。
下面是数控车床程序编制的典型步骤:1.了解零件图纸和工艺要求:仔细研究零件图纸,了解零件的尺寸要求、形状要求以及表面质量要求等,还要确定零件的加工顺序和工艺路线。
2.选择工具和刀具:根据零件的要求和加工工艺,选择合适的车刀、镗刀、钻刀及其加工参数。
3.制定加工工艺:根据零件的尺寸要求和形状要求,制定适当的车削切削参数和轮廓刀补偿值,并确定刀具路径。
4.确定坐标系和参考点:选择适当的坐标系和参考点,并确定零点的坐标位置。
5.数控系统参数设置:根据机床和数控系统的特点,设置数控系统的参数,如坐标系、移动速度、进给量等。
6.编写数控程序:使用数控编程语言,按照零件加工工艺要求,逐步编写数控程序。
7.先练习:在计算机仿真软件中,根据编写的数控程序进行仿真操作,以验证程序正确性。
修正程序错误。
8.载入数控系统:将编写好的数控程序,通过U盘、本地网络等方式,载入数控系统中。
9.导入刀具和工件坐标:确定刀具的初始位置、起刀点和工作零点,导入数控系统中。
10.设置工件坐标系:根据图纸和实际加工需求,设置工件坐标系和坐标偏移。
11.调试程序:使用手动操作或自动操作,对数控系统进行调试,确保程序的安全性和准确性。
12.加工实践:进行实际加工操作,监控加工过程中各项参数的变化,并及时调整。
13.检验零件:完成加工后,根据图纸要求进行零件的测量和检验,确保零件质量满足要求。
14.优化程序:根据实际加工情况,调整和优化数控程序,提高加工效率和质量。
15.存档和备份:将编写好的数控程序进行保存和备份,以备后续使用。
总结起来,数控车床程序编制是一项精细的工作,需要熟悉机床、工具和数控系统的基本原理,同时要具备良好的图纸分析和数控编程能力。
通过以上步骤的严格执行,可以确保数控车床加工过程的准确性和安全性。
数控车床编程方法

注:﹡在G71、G72程序段中的F、S、T指令都无 效,只有在ns-nf之间的程序段中的F、S、T指令有 效; ﹡G70切削后刀具会回到G71-G73的开始切削点; ﹡G71、G72循环切削之后必须使用G70指令执行 精加工,以达到所要求的尺寸; ﹡在没有使用G71、G72指令时,G70指令不能使 用。
能消除残留高度。这时假想刀尖的轨迹 C2D2 与轮廓线CD 在X 向相差X, Z 向相差 Z。设刀具的半 径为r, 斜面倾角为α,可以 求出
α/2
α △Z
△X
3、圆头车刀加工圆弧面的编程和补偿 圆头车刀加工圆弧面和加工圆锥面基本相
似。如图是加工 l/4 凸凹圆弧, CD 为工件 轮廓线, 0点为圆心, 半径为R, 刀具与圆弧 轮廓起点、终点的切削点分别为C和D, 对 应假想刀尖为C1和D 1。对图( a) 所示凸圆 弧加工情况, 圆弧C1D 1为假想刀尖轨迹, 01点为圆心, 半径为( R + r); 对图( b) 所示 凹圆弧加工情况, 圆弧C2D2 为假想刀尖轨 迹, 其圆心是02点, 半径为( R - r) 。如果按 假想刀尖轨迹编程, 则要以图中所示的圆弧 C1D 1或C2D2(虚线) 有 关参数进行程序编 制。
上一页 下一页
闭环切削循环指令(G73) 格式:G73 U △i W △k R d;
G73 P ns Q nf U △u W △w(F__S__ T__) ;
其中 △i:X方向粗加工毛坯的预留量(半径值) △k:Z方向粗加工毛坯的预留量(半径值)
d:切削次数 ns:精加工程序第一个程序段的序号 nf:精加工程序最后一个程序段的序号 △U:X向的精加工余量 △W:Z向的精加工余量 G73循环指令的刀具切削路径如图所示:
数车编程 数控车床的程序编制(高级教学)

第一节 数控车床加工工艺基础
数控车床能对轴类或盘类等回转体零件自动地完成内、外圆柱面,圆锥面, 圆弧面和直、锥螺纹等工序的切削加工,并能进行切槽、钻、扩和铰等工作。 它是目前国内使用极为广泛的一种数控机床,约占数控机床总数的25%。
右 端 面 左 端 面 尖 头 切断刀 切槽刀 左螺纹
内容展示
15
❖刀尖圆弧自动补偿指令
指令格式 G41(G42)G01(G00)X(U)_ Z(W)_ G40
指令功能 G41为左偏刀具补偿; G42为右偏刀具补偿; G40是取消刀尖圆弧半径补偿。
指令说明 顺着刀具运动方向看,刀具在工件轮廓线的左边为刀尖左补偿;刀 具在工件轮廓线的右边为刀尖右补偿(与坐标轴方向有关) 。
G90 该循环主要用于轴类零件的外圆、锥面的加工。
内容展示
21
(1)圆柱面或圆锥面切削循环——外圆切削循环指令
内容展示
22
内容展示
23
圆锥面切削循环 G90 X(U)_ Z(W)_ (R)I_ F_ ;
锥度I的符号确定方法:锥面起点X坐标大于终点坐标时为正,反之为负。
内容展示
24
(2)端面切削循环G94
进给量
背吃刀量
内容展示
3第二节 数控车床程序源自制一、 数控车床编程特点 数控车床的主要编程特点如下: (1) 在一个程序段中,可以采用绝对值编程(用X、Z表示)、增量值编程(用U、
W表示)或者二者混合编程。 (2) 直径方向(X方向)用绝对值编程时,X以直径值表示;用增量值编程时,以
径向实际位移量的二倍值表示,并附方向符号(正向可以省略)。系统默认 为直径编程,也可以采用半径编程,但必须更改系统设定。
数控车床的程序编制步骤

〔三〕刀具布置:
• 刀具1:右偏刀,用于车削外圆、球面 和圆锥。
• 刀具2:尖头刀〔主偏角60°, 副偏角 60°〕,用于车削圆弧R15。
2023/2/22
〔四〕、编程分析:
φ28 R15
φ24 SR10
图2
• 1、编程原点设置的原那么是什 M03 —主轴顺时针转动;
刀具2:尖头刀〔主偏角60°, 副偏角60°〕,用于车削圆弧R15。
刀具2:尖头刀〔主偏角60°, 副偏角60°〕,用于车削圆弧R15。
(2)、辅助功能M代码: 〔5〕粗车球部至R10.
IH
2、什么是绝对值编程?什么是增量值编程?什么是混合编程?
E GF
C
A
DB
7
Z
绝对值编程、增量值编程例图 绝对值编程、增量值编程和混合编程举例:
5
5 10 12
增量值方式:G91 G01 X-20 Z-15 F100
G00—点定位; G01 —直线插补; G02 —顺圆弧 插补; G03 —逆圆弧插补;G04 —暂停; G22— 程序循环指令;G33 —螺纹切削,等螺距;G80 — 固定循环注销;G90 —绝对尺寸;M02 —程序结束;
M03 —主轴顺时针转动; M05 —主轴停止。 请思考:
数控程序中程序段的顺序应如何确定的?
解:绝对值方式:G01 X50 Z30 F100
〔5〕精车圆弧R•15mm2。、什么是绝对值编程?什么是
增量值编程?什么是混合编程?
2023/2/22
1:5
7 5 10 12 52
绝对值编程、增量值编程和混 合编程举例:
• 例1:右图中设AB已加工完,要加工BC段,
刀具在B点,试分别写出绝对坐标、增量坐
数控车床程序编制

粗车时使用的刀具
粗加工时的主轴转速
粗加工时的进给速度
Z轴方向精加工余量 X轴方向精加工余量,直径值
精车结束程序段的顺序号
精车开始程序段的顺序号
4.2 数控车床程序编制
4.2 数控车床程序编制
G71使用方法说明: (1)在精加工程序中由循环起点C到A点只 能使用G00或G01指令,并且不能有z轴方向移 动指令。 (2)精加工程序车削的路径必须是单调增 加或减小。不能有内凹的轮廓外形。
粗车刀1号,精车刀2号,刀尖半径为0.6㎜。 精车余量x轴为0.2㎜,z轴为0.05㎜。粗车的切削速度 为150m/min,精车为180m/min。粗车的进给量为 0.2mm/r,精车为0.07mm/r。粗车时的背吃刀量为3㎜。 4.2 数控车床程序编制
例4-10
4.2 数控车床程序编制
O4010 G50 X150. Z200. T0100; G50 S3500; G96 S150 M04; T0101; G00 X84. Z3. M08; G71 U3. R1.; G71 P10 Q20 U0.2 W0.05 F0.2; N10 G00 X20.; G01 G42 Z-20. F0.07 S180; X40. W-20.; G03 X60. W-10. R10.; G01 W-20.; G01 X80.; Z-90.; N20 G40 X84.; G00 X150. Z200. T0100; T0202; X84. Z3.; G70 P10 Q20; G00 X150. Z200.T0000; M30;
4.2 数控车床程序编制
△i 和△k 为第一次车削时退离工件轮廓的距离及 方向,确定该值时应参考毛坯的粗加工余量大小,以 使第一次走刀时就有合理的切削深度。计算方法为: △i =(x轴粗加工余量)— (每一次切削深度) △k=(z轴粗加工余量)— (每一次切削深度) 例如:若x轴方向粗加工余量为6mm,分三次走 刀,每一次切削深度2mm,则: △i =6-2=4 d=3
第3章:数控加工程序的编制

刀具中心的走刀路线为:
对刀点1→对刀点2 →b→c→c’→下刀点2→下刀点1
各基点及圆心坐标如下: A(0,0) B(0,40) C(14.96,70) D(43.54,70) E(102,64) F(150,40) G(170,40) H(170,0) O1(70,40) O2(150,100)
10 20 =10
60O
17.321
N18 G90 G00 Z100.;
10 20 =10
60O
17.321
N19 X0. Y0. M05; N20 M30;
10 20 =10
60O
孔加工注意事项:
孔加工循环指令是模态指令,孔加工数据 也是模态值;
撤消孔加工固定循环指令为G80,此外, G00、G01、G02、G03也可起撤消作用;
N016 G01 X45.0 W0 F100;
切槽
N017 G04 U5.0;
延迟
N018 G00 X51.0 W0;
退刀
退刀 N019 X200.0 Z350.0 T20 M05 M09;
N020 X52.0 Z296.0 S200 T33 M03 M08;
N021 G33 X47.2 Z231.5 F1.5;
(5)复杂轮廓一般要采用计算机辅 助计算和自动编程。
二、数控铣床编程中的特殊功能指令
(1)工件坐标系设定指令 G54~G59
G54~G59无需在程序段中给出工件 坐标系与机床坐标系的偏置值,而是安 装工件后测量出工件坐标系原点相对机 床坐标系原点在X、Y、Z向上的偏置值, 然后用手动方式输入到数控系统的工件 坐标系偏置值存储器中。系统在执行程 序时,从存储器中读取数值,并按照工 件坐标系中的坐标值运动。
数控车床程序编制

轴正向还是负向,如图3.19a所示。 其编程格式为 G01 Z(W)~ I±i 。 由端面切削向轴向切削倒角,即由X轴向Z轴倒角,k的正负根据倒角是向Z
轴正向还是负向,如图3.19b所示。 编程格式 G01 X(U)~ K±k。
图3.14 数控车床坐标系
图3.15 直径编程
图3 .16切削起始点的确定
3.2数控车床的基本编程方法
数控车削加工包括内外圆柱面的车削加工、端面车削加工、钻孔加工、螺纹 加工、复杂外形轮廓回转面的车削加工等,在分析了数控车床工艺装备和数控 车床编程特点的基础上,下面将结合配置FANUC-0T数控系统的HM-077数控车 床重点讨论数控车床基本编程方法。
图3.27 刀具补偿编程
单一固定循环
图3.28圆柱面切削循环
图3.29 G90的用法(圆柱面)
图3.30 圆锥面切削循环
图3.31 端面切削循环
图3.32 锥面端面切削循环
图3.33 G94的用法(锥面)
单一固定循环可以将一系列连续加工动作,如“切入-切削-退刀-返回”,用一 个循环指令完成,从而简化程序。 1、圆柱面或圆锥面切削循环
自动对刀是通过刀尖检测系统实现的,刀尖以设定的速度向接触式传感器接近, 当刀尖与传感器接触并发出信号,数控系统立即记下该瞬间的坐标值,并自动修正刀 具补偿值。自动对刀过程如图3.13所示。
图 3.13
数控车床的编程特点
1、加工坐标系 加工坐标系应与机床坐标系的坐标方向一致,X轴对应径向,Z
轴对应轴向,C轴(主轴)的运动方向则以从机床尾架向主轴看,逆 时针为+C向,顺时针为-C向,如图3.14所示:加工坐标系的原点 选在便于测量或对刀的基准位置,一般在工件的右端面或左端面上。 2、直径编程方式
数控车床的程序编制
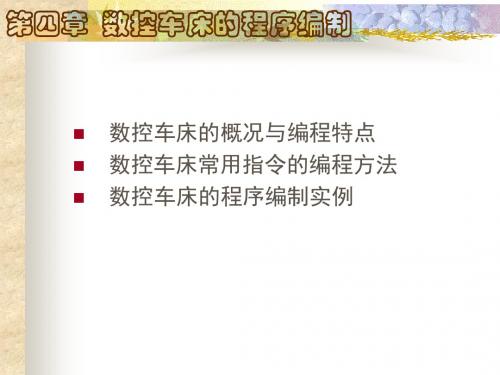
二、常用G代码的编程方法
3.刀具补偿
1)刀具偏置补偿
车刀产生偏置的原因
转位刀架上每把刀的 刀尖位置不同存在偏 置量ΔX、ΔZ
刀具刃磨重新装刀后, 刀尖位置变化;
刀具使用过程的磨损。
参考点
第二节 数控车床常用指令的编程方法
二、常用G代码的编程方法
3.刀具补偿
2) 刀尖圆弧半径补偿 (1)刀尖圆弧及其对加工的影响
直线、圆弧插补;圆柱圆锥螺纹;具备简单的外圆、端 面、车螺纹的固定循环功能,能够实现刀具偏置补偿;快速 移动速度多在10m/min以下。
第一节 数控车床的概况与编程特点
二、常用数控车床的功能
2.全功能数控车床
1)结构上 多为倾斜床身结构;采用6—8(立式)、或8—16(卧式)
工位电动或液压刀架。 2)数控系统
4.用G01倒角与倒圆
2)倒圆角 (1)Z→X
格式:G01 Z(W) b R ± r ; b为Z方向无倒角时的终点坐标; r为倒圆半径。
(2)X→Z 格式: G01 X(U) b R ± r ;
b为X方向无倒角时的终点坐标。
第二节 数控车床常用指令的编程方法
例:加工右图工件的倒角的程序编制 …… N20 G00 X10.0 Z23.0; N30 G01 Z10.0 R5.0 F ; N40 X38.0 K-4.0; N50 Z0; ……
G99——每转进给量。单位mm/r,例: G99 G01 X Z F0.14;(F=0.14mm/r)
“*”——G99为通电后优先状态 每分钟进给量(F)与每转进给量(f)的关系:
F=fn 有的FANUC系统每分钟进给量用G94、每转进给量用G95。
第二节 数控车床常用指令的编程方法
数控车床程序的编制及操作

数控车床程序的编制及操作数控车床是一种将数字化程序与机械系统相结合的机床,它可以通过程序控制工件在旋转的工作台上实现各种加工操作。
数控车床的编制和操作是现代制造业中非常重要的一环,下面将详细介绍数控车床程序的编制及操作。
一、数控车床程序的编制1.确定工件的加工要求:首先需要明确工件的尺寸、形状、加工方式等基本要求。
2.设计加工工艺:根据工件的要求,设计出合适的加工工艺,包括加工顺序、刀具的选择和切削参数的设定等。
3.编写数控程序:根据设计好的加工工艺,将其转化为数控程序。
数控程序包括程序头、工件坐标系、刀具半径补偿、各种指令和参数等。
4.数控程序的调试:将编写好的数控程序加载到数控系统中,并进行调试,确保程序的正确性和可靠性。
二、数控车床程序的操作1.将数控程序加载到数控系统中:将编写好的数控程序上传到数控系统中,通常会使用USB、网络连接等方式进行传输。
2.设置加工工件坐标系:按照数控程序中设定的工件坐标系进行相应的参数设置,包括工件起点、刀库位置等。
3.安装刀具和夹具:根据加工工艺的要求,选择适当的刀具和夹具,并进行安装和调整。
4.开始加工:调试完毕后,可以开始加工了。
通常会将机床切换到自动模式,并按照数控程序的要求进行操作。
数控系统会自动控制工件的运动轨迹、刀具进给速度等。
5.监测加工过程:在加工过程中,需要时刻监测工件的加工情况,包括切削力、切削温度等。
可以通过控制面板上的显示和报警信息来监测和调整加工过程。
6.完成加工:当加工完成后,数控系统会自动结束加工,并将机床切换到手动模式。
此时可以将加工好的工件取出,并进行检查和质量评估。
三、常见问题及解决方法在数控车床程序的编制和操作过程中,可能会出现一些问题,常见的问题及解决方法如下:1.程序错误:在编写程序时可能会出现语法错误或逻辑错误。
可以通过调试程序来查找错误所在,并进行修正。
2.程序冲突:如果多个程序同时运行可能导致程序冲突。
可以通过调整程序执行顺序或增加程序之间的时间间隔来解决冲突。
- 1、下载文档前请自行甄别文档内容的完整性,平台不提供额外的编辑、内容补充、找答案等附加服务。
- 2、"仅部分预览"的文档,不可在线预览部分如存在完整性等问题,可反馈申请退款(可完整预览的文档不适用该条件!)。
- 3、如文档侵犯您的权益,请联系客服反馈,我们会尽快为您处理(人工客服工作时间:9:00-18:30)。
薄壁零件容易变形,普通 三爪卡盘受力点少,采用开缝 套筒或扇形软卡爪,可使工件 均匀受力,减小变形。
CNC
第三章 数控加工编程方法
(3)坐标系统
+X +X' L
d
O
O'
+Z
机床原点定义为主轴旋转中心线与车床端面的交点; 为方便编程和简化数值计算,工件坐标系原点一般选 在工件的回转中心与工件右端面或左端面的交点。
F、S指令设置
G99 G98
恒切削速度的设置方法为 G96 S_ ;(S的单位为m/min) 主轴转速也可不设置成恒切削速度,指令格式为 G97 S_ ;(S的单位为r/min) 设置成恒切削速度时,为防止计算出的主轴转 速过高而发生危险,在设置前应将主轴最高转速设 置在某一最高值。指令格式为 G50 S_ ;(S的单位为r/min)
30
N30 Z-15.0;
15
O
Z
CNC
第三章 数控加工编程方法
3)螺纹切削循环 G92 X(U)_ Z(W)_
X R
螺纹 F 起点 循环 起点 螺纹起点
I_
X
F_ ;
循环 起点
R
螺纹 F 起点 NC
第三章 数控加工编程方法
X
6 P 1(35,104) 102 P 0(270,260)
1)选择零件或加工内容
2)数控工艺可行性分析,明确加工要求
3)确定工艺路线
4)工序详细设计
5)数控程序设计与调整
工艺性分析
CNC
第三章 数控加工编程方法
(1)对刀具、刀座的要求
中心钻
外圆左偏粗车刀
外圆右偏粗车刀
外圆左偏精车刀
精镗孔刀
外圆右偏精车刀
外圆切槽刀
外圆螺纹刀
粗镗孔刀
麻花钻
Z向铣刀
45 端面刀
C CN NC C
第三章 数控加工编程方法
高精度回转零件:
高精度的机床主轴
高速电机主轴
CNC
第三章 数控加工编程方法
难 于 控 制 尺 寸 的 回 转 体 零 件
CNC
第三章 数控加工编程方法
表面形状复杂的回转体零件
CNC
第三章 数控加工编程方法
非标丝杠
CNC
第三章 数控加工编程方法
三、数控车削工艺处理:
150
N60 X65.0 Z110;
140
65
45
O
2
85
N70 Z90.0;
N80 X140.0 Z80.0; N90 Z60.0;N100 Xl50.0 Z40.0;
40 20 20 10 20 230 30 30 10 2
C轴控制 C轴控制加工
CNC
第三章 数控加工编程方法
●刀架 ●床身
●主轴箱 ●高精度导轨 ●滚珠丝杠 ●床座 ●尾座
CNC
第三章 数控加工编程方法
二、数控车削主要适合对象:
1.高精度回转零件
2.零件廓形复杂或难于控制尺寸的回转体零件 3.表面形状复杂的回转体零件 4.带特殊螺纹的回转零件(导程不一样)
O
M30×2
46
Z
N50 N70 N80 N90
G92 X28.9 Z56.0 F2; X28.2; X27.7; X27.3;
CNC
第三章 数控加工编程方法
外螺纹
右螺纹 右手刀柄
左螺纹 左手刀柄
CNC
第三章 数控加工编程方法
内螺纹
右螺纹 右手刀柄 左螺纹 左手刀柄
CNC
第三章 数控加工编程方法
③ 车削加工中心 是在普通数控车床的基础上,增加了C轴和铣削 动力头,有的还配备了刀库和机械手,可实现X、Z 和C三个坐标轴联动。车削中心除可以进行一般车削 外,还可以进行径向和轴向铣削、曲面铣削、中心 线不在零件回转中心的孔和径向孔的钻削等加工。
CNC
第三章 数控加工编程方法
车削中心
CNC
第三章 数控加工编程方法
30
30
10
2
110
Z
CNC
第三章 数控加工编程方法
N20 G00 Xl70.0 Z180.0 S750 T0202 M03;
N30 G71 U5.0 R1.0;
X
终点
5
起点
N35 G71 P40 Q100 U4.0 W2.0 F0.3 S500; N40 G00 X45.0 S750; N50 G01 Z140.0 F0.1;
X
刀尖
过切削
切削残留 刀尖路径 程序路径 切削残留 切削残留
假 想 Z 刀 尖 位 置
切削残留 工件精加工形状 (程序路径)
CNC
第三章 数控加工编程方法
刀尖半径补偿指令程序段格式为 G41/G42
A′ A
刀尖R 假想刀尖
X( U) _
Z( W) _ ;
G42
假想刀尖
G41
刀尖R
A′ A
CNC
第三章 数控加工编程方法
5
CNC
第三章 数控加工编程方法
2)端面切削循环 G94 X(U)_
X
切削 始点 切削 终点
2(F )
Z( W) _
F_ ;
循环起点
4(R) 3(F )
O R:快速进给 F :切削进给
X /2
U /2
1(R)
Z
CNC
第三章 数控加工编程方法
X
X 85.0 Z 5.0
3
75
2 1
N10 G94X30.0Z-5.0F50; N20 Z-8.0;
3(F ) 2(F )
1(R)
3(F )
1(R) 2(F )
X /2
R:快速进给 F :切削进给
R:快速进给 F :切削进给
X /2
U /2
CNC
第三章 数控加工编程方法
P0
(1) (2) (3)
40 25
50
(1) (2) (3)
40 30 20
30 50
60
40
N10G90X35.0Z20.0F50; N10G90X40.0Z20.0I-5.0F50; N20 X30.0; N20 X35.0; N30 X25.0; N30 X30.0;
CNC
第三章 数控加工编程方法
二、 数控车床编程特点
(1)在一个零件的加工程序段中,根据图纸上标注的尺
寸,可以按绝对坐标编程、增量坐标编程或两者混合编 程。当按绝对坐标编程时常用代码 X 和 Z 表示;按增 量坐标编程时则用代码 U 和 W 表示,一般不用G90、 G91指令。
(2)由于车削常用的毛坯为棒料或锻件,加工余量较
CNC
第三章 数控加工编程方法
暂停指令G04
在车削加工中,该指令可用于车削环槽、不通 孔以及加工螺纹等场合; 切断或切槽刀具
在槽底暂停
钻头
在孔底暂停
CNC
第三章 数控加工编程方法 G04 U_(或P_);
在G98进给模式下,指令中输入的时间即为 停止进给的时间;在G99进给模式下,则为 暂停进刀的主轴回转数。
CNC
第三章 数控加工编程方法 主要内容
概述 手工编程方法 数控车床编程方法 数控铣床编程方法 加工中心编程方法 自动编程方法
CNC
第三章 数控加工编程方法
手工编程流程图 确定加工内 容、路线 零件 图纸 数控工 艺分析 确定刀、夹 、量具 确定切削 用量 数学 处理 编程 手册
程序 编制
试切、 验证
刀具功能 刀具编号 刀具补偿编号
T 03 03
TOOL OFFSET
No. 01 02 03 XASIS 12.500 ------24.3 ZAXIS RADIUS TIP 3.400 0.800 3 --------------5.234 0.400 2
刀具补偿编号
假想刀尖位置号 刀尖半径补偿
X 轴刀具补偿量
G71P ( ns ) Q ( nf ) U ( u ) W ( w ) F_ S_ T_ 代表 刀号; Δu:x向精车余量Δw:z向精车余量 e:每次退刀量Δd:每次背吃刀量ns:精车程序段开始 一段段号nf:精车程序段开始结束段号
N(ns)…… ……
CNC
第三章 数控加工编程方法
U(d) R(e);
X向铣刀
球头铣刀
CNC
第三章 数控加工编程方法
外圆车刀
内孔车刀
CNC
第三章 数控加工编程方法
螺纹车刀
CNC
第三章 数控加工编程方法
切断(槽)车刀
CNC
第三章 数控加工编程方法
尽可能使用机夹刀和机夹刀片,以减少换刀时间和 对刀时间;数控刀具通过刀座作过渡安装在刀架上等。
CNC
第三章 数控加工编程方法
螺纹加工进刀次数及进刀量的选择
应根据螺 距来选择 走刀次数 及进给量, 以保证螺 纹的精度 及质量
CNC
第三章 数控加工编程方法
4)多重复合循环 在多重循环中,只须指定精加工路线和粗加工的背吃 刀量,系统就会自动计算出粗加工路线和走刀次数。 (a)外圆粗车循环G71 G71 U(d) R(e);
CNC
第三章 数控加工编程方法
C为粗车循环的起点,A是毛坯外径与轮廓端面的交点
C
Δd Δ u/2
B
45°
A
e
A′ Δ w
CNC
第三章 数控加工编程方法
切削深度为5mm,退刀量为1mm,X向精车余量为2mm, Z向精车余量为2mm X 起点
终点
5
150
140
65
45