单螺杆挤出机温度设置原则
单螺杆挤出机操作规程

单螺杆挤出机操作规程一、开机前的检查工作1.确认设备处于完好待用状态。
2.查阅停机前的工艺记录,了解设备的工艺参数情况。
3.开启水、电、气源,检查设备是否漏水,漏气;试运行各辅机(真空泵、水泵、牵引机、切割机等),确认辅机均处于良好状态。
4.按生产任务的要求检查所用模具是否完好,确认模心、模口、定径套、定型板、切割机夹具的规格尺寸是否与生产要求相符。
二、换模操作一)、挤出模具的安装1.小心拆出模具,用干净擦布将模具流道内的余料及油污擦拭干净。
小心检查流道是否有生锈、存料、损伤、不光滑等缺陷。
2.检查过渡环或多孔板两端面是否清洁平整,与机台与模具配合是否良好,模具气孔是否通畅,多孔板孔眼是否有杂质或碳化料堵塞。
3.小心将模具连接装上紧固挤出机,各螺丝须涂抹高温防卡油,锁紧连接螺丝。
锁紧连接螺丝时应对角逐步均匀锁紧。
4.清理干净模具各部分的配合面,按顺序装上模具的各个部分,平衡地锁紧连接螺丝。
安装调整模具时要做到口模与芯模的圆周间距一致。
5.装上各区电热圈,接好电源线,插上电热耦。
电热圈应紧贴模具表面,电热偶应插电热偶孔内并与电热圈一一对应。
二)、定型套的安装管材定型部分由定型套和定型板组成,管材的定型套主要分PE和PP-R两大类;PP-R定径套分冷水定径套和热水定径套,安装时应注意调平,定型板内孔尺寸及其橡胶圈内孔尺寸按生产的管径尺寸而定,必须要安装紧密、牢固以防漏气。
(三)切割机夹具的安装根据管径规格大小对应安装切割机哈夫块,调整进刀行程、公转速度及气缸气压以接近正常切割时的参数值,再放置一条同管径尺寸的管材进行试切割,继续调整各参数以达到最佳工作状态。
三、升温操作1.升温操作应根据设备与模具情况不同适当调整开启电源的时间,以确保须加热的各部分均同时达到生产所需温度。
2.升温时先接通挤出机电源,开启温控开关,然后将各区设定温度调整为正常生产温度高5至10℃。
检查各发热圈发热是否正常。
待模具达到设定温度后恒温约30至50分钟后方可开机,恒温时间是视模具大小而定,大模具的恒温时间比小模具长。
挤出机调试技巧

挤出机调试技巧挤出机是一种广泛应用于塑料制品生产中的机器设备,而调试是使用挤出机时必不可少的环节。
以下是一些挤出机调试技巧,希望能对您有所帮助:1. 清洗和维护:在使用挤出机之前,必须彻底清洗和维护设备。
这包括清洗料斗、螺杆、筒体和模头等部件,并确保它们没有任何损坏或磨损。
2. 调整温度:正确的温度设置是保证挤出机正常运行的关键因素。
在调整温度时,需要根据材料类型和生产要求来设置合适的温度范围。
3. 调整速度:挤出机的速度也需要根据生产要求进行调整。
如果速度过快,可能会导致产品质量下降或设备故障;如果速度过慢,则会影响生产效率。
4. 调整压力:正确的压力设置可以确保产品质量稳定,并减少设备故障的风险。
在调整压力时,需要注意避免过高或过低的情况发生。
5. 检查模头:模头是影响产品质量的重要因素之一。
在使用挤出机时,需要定期检查模头是否干净、损坏或磨损。
6. 调整送料系统:挤出机的送料系统也需要根据生产要求进行调整。
如果送料过多,可能会导致产品质量下降或设备故障;如果送料过少,则会影响生产效率。
7. 检查电气系统:电气系统是挤出机运行的关键组成部分。
在使用挤出机时,需要定期检查电气系统是否正常工作,并及时维修或更换损坏的部件。
8. 做好安全措施:在使用挤出机时,必须做好安全措施,避免发生意外事故。
这包括佩戴适当的个人防护装备、保持设备清洁和整洁、及时维修设备等。
以上是一些常用的挤出机调试技巧,希望能对您有所帮助。
在使用挤出机时,请务必注意安全,并按照操作规程进行操作。
单螺杆挤出机(PVC软管)安全操作规程
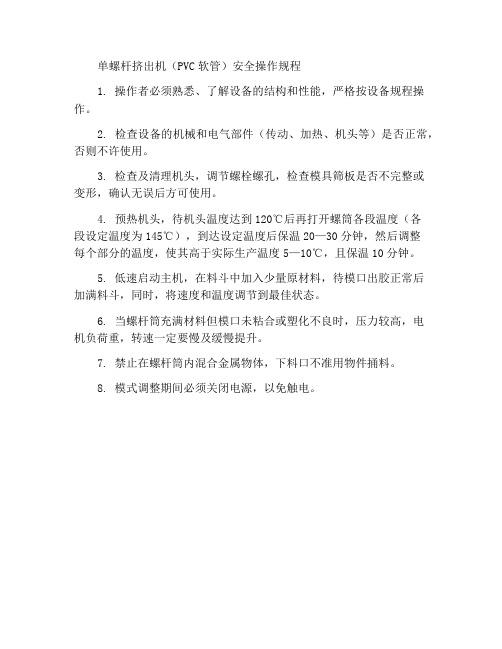
单螺杆挤出机(PVC软管)安全操作规程
1. 操作者必须熟悉、了解设备的结构和性能,严格按设备规程操作。
2. 检查设备的机械和电气部件(传动、加热、机头等)是否正常,否则不许使用。
3. 检查及清理机头,调节螺栓螺孔,检查模具筛板是否不完整或
变形,确认无误后方可使用。
4. 预热机头,待机头温度达到120℃后再打开螺筒各段温度(各
段设定温度为145℃),到达设定温度后保温20—30分钟,然后调整
每个部分的温度,使其高于实际生产温度5—10℃,且保温10分钟。
5. 低速启动主机,在料斗中加入少量原材料,待模口出胶正常后
加满料斗,同时,将速度和温度调节到最佳状态。
6. 当螺杆筒充满材料但模口未粘合或塑化不良时,压力较高,电
机负荷重,转速一定要慢及缓慢提升。
7. 禁止在螺杆筒内混合金属物体,下料口不准用物件捅料。
8. 模式调整期间必须关闭电源,以免触电。
单螺杆挤出机操作规程

单螺杆挤出机操作规程一、开机前的检查工作1.确认设备处于完好待用状态。
2.查阅停机前的工艺记录,了解设备的工艺参数情况。
3.开启水、电、气源,检查设备是否漏水,漏气;试运行各辅机(真空泵、水泵、牵引机、切割机等),确认辅机均处于良好状态。
4.按生产任务的要求检查所用模具是否完好,确认模心、模口、定径套、定型板、切割机夹具的规格尺寸是否与生产要求相符。
123.4.5.(二)12.至10℃。
250生产线约需6小时,φ110生产线(包括PP-R线)约需3小时,φ63生产线(包括PP-R线)约需2.5小时。
3.升温过程中应注意观察各区升温速度是否正常,并且要用玻璃温度计校核各区温度是否准确。
四、开机操作1.再次确认各区温度是否达到所需温度。
2.检查模具各连接螺丝是否紧固。
3.根据所生产的产品规格标重设置好称重系统的参数。
3.再次确认各辅机均处于待用状态,料架与切割机系统已调到位。
4.严格按照配方单要求进行混配料,保持料斗里的料位高度,根据不同原料的烘干温度开启料斗干燥机。
仅供个人学习参考5.准备好合适的引管(或引绳),并确保前后操作人员已到位。
6.开启水源和气源,将定型箱水位调到合适高度,开启冷水机。
7.启动挤出主机马达,将转速调节为约为6至12转。
启动色线机马达,将转速调节到约1.5至3转。
注意观察主机电流和运转响声。
8.待模具出料后,迅速将料坯与引管粘接起来,开启牵引机并调整牵引速度使之与挤出速度相匹配,开启1号喷淋水泵。
引管初期应注意保护引管料坯的粘接部分,避免卡在定型板上,待牵引稳定后启动2号喷淋水泵和1号、2号定型真空泵,使方管定型,逐步提高挤出速度和牵引速度至接近生产速度。
9.待生产基本正常后调出设置好的喷码信息进行喷码。
10.根据称重系统的下料参数调整产品壁厚及重量。
10.继续调整各工艺参数,使稳定地生产出合格产品。
11234.5定,行维修。
12345123底部。
4.清理模具流道时必须小心操作,不能使用螺丝刀等硬质工具,不能用粗纱纸打磨流道表面,模具的修理应交专业人员处理。
螺杆挤出机温度控制

挤出温度控制主要有温度设定、控制和调整三个局部构成。
设定温度是控制温度的依据和基准,调整温度是对设定温度的修正和完善。
2.1 温度设定设定温度的目的是为了控制物料挤出成型过程,始终在熔融温度与分解温度区间(即160~180℃)进展。
要正确设定温度,则需充分考虑制约物料成型温度的相关因素。
(1)配方组分、剂量和原料质量。
据文献介绍和生产实践验证,不同配方或同一配方不同厂家生产的物料(PVC、CPE、热稳定剂等),挤出成型温度往往有很大差异,有的达10℃左右,这一点在没有实验条件或生产经历的情况下,是不可预知的。
只有通过生产实践,依据塑料型坯的质量,适时调整设定温度。
开场设定温度时不易过高,应从低向高逐步调整。
(2)塑料挤出亦是一个能量守恒的过程。
单位体积的固体转化为熔体所需的总能量相对是恒定的,物料的输送速率根本上平衡于物料的熔化速率。
因受口模物料流速和定型模冷却条件的限制,不同规格的异型材单位时间挤出量差异亦很大。
因物料输送速率不同,物料熔融所需热量亦不同。
对于单螺杆挤出机或双螺杆挤出机没有内热存在的加热区域,即机头、大小过渡段、口模等部位,生产大规格型材时,设定温度宜高一些;生产小规格异型材,设定温度宜低一些。
对于双螺杆挤出机有内热存在的加热区域,由于内热的作用,挤出速率反过来又直接影响物料的熔融速率。
设定温度应视该段物料的形态、承受温度程度及对热量的需求情况而定。
(3)塑料挤出需经历一定时间历程。
在这一历程的不同阶段,由物料的加工特性和挤出机职能所决定,不同形态的物料承温情况和对热量的需求有所不同。
要正确设定温度亦有必要深入了解物料在挤出不同阶段的形态、承受温度程度及对热量的需求情况。
双螺杆挤出机温控系统由10个温控点组成。
依据物料在挤出过程各个阶段的形态、承受温度程度及对热量的需求情况,可将10个温控点归纳为加温、恒温、保温三个区域。
其中加温与恒温区主要在挤出机内,以排气孔为界划分为两个相对独立又互为关联的局部;保温区主要由机头、大小过渡段、口模局部构成。
冷喂料挤出机转速及各段温度控制
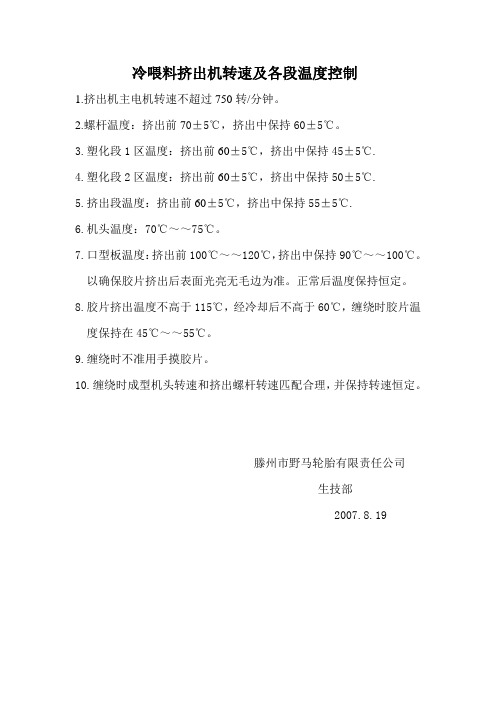
冷喂料挤出机转速及各段温度控制
1.挤出机主电机转速不超过750转/分钟。
2.螺杆温度:挤出前70±5℃,挤出中保持60±5℃。
3.塑化段1区温度:挤出前60±5℃,挤出中保持45±5℃.
4.塑化段2区温度:挤出前60±5℃,挤出中保持50±5℃.
5.挤出段温度:挤出前60±5℃,挤出中保持55±5℃.
6.机头温度:70℃~~75℃。
7.口型板温度:挤出前100℃~~120℃,挤出中保持90℃~~100℃。
以确保胶片挤出后表面光亮无毛边为准。
正常后温度保持恒定。
8.胶片挤出温度不高于115℃,经冷却后不高于60℃,缠绕时胶片温度保持在45℃~~55℃。
9.缠绕时不准用手摸胶片。
10.缠绕时成型机头转速和挤出螺杆转速匹配合理,并保持转速恒定。
滕州市野马轮胎有限责任公司
生技部
2007.8.19。
螺杆挤出机温度控制
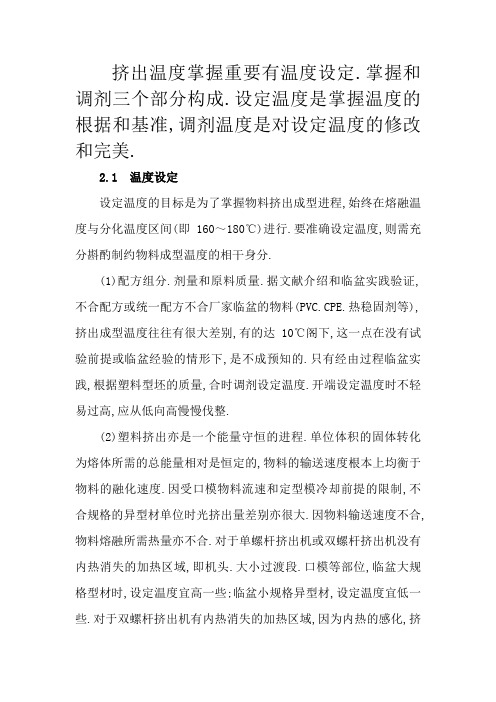
挤出温度掌握重要有温度设定.掌握和调剂三个部分构成.设定温度是掌握温度的根据和基准,调剂温度是对设定温度的修改和完美.2.1 温度设定设定温度的目标是为了掌握物料挤出成型进程,始终在熔融温度与分化温度区间(即160~180℃)进行.要准确设定温度,则需充分斟酌制约物料成型温度的相干身分.(1)配方组分.剂量和原料质量.据文献介绍和临盆实践验证,不合配方或统一配方不合厂家临盆的物料(PVC.CPE.热稳固剂等),挤出成型温度往往有很大差别,有的达10℃阁下,这一点在没有试验前提或临盆经验的情形下,是不成预知的.只有经由过程临盆实践,根据塑料型坯的质量,合时调剂设定温度.开端设定温度时不轻易过高,应从低向高慢慢伐整.(2)塑料挤出亦是一个能量守恒的进程.单位体积的固体转化为熔体所需的总能量相对是恒定的,物料的输送速度根本上均衡于物料的融化速度.因受口模物料流速和定型模冷却前提的限制,不合规格的异型材单位时光挤出量差别亦很大.因物料输送速度不合,物料熔融所需热量亦不合.对于单螺杆挤出机或双螺杆挤出机没有内热消失的加热区域,即机头.大小过渡段.口模等部位,临盆大规格型材时,设定温度宜高一些;临盆小规格异型材,设定温度宜低一些.对于双螺杆挤出机有内热消失的加热区域,因为内热的感化,挤出速度反过来又直接影响物料的熔融速度.设定温度应视该段物料的形态.推却温度程度及对热量的需求情形而定.(3)塑料挤出需阅历一准时光过程.在这一过程的不合阶段,由物料的加工特点和挤出机本能机能所决议,不合形态的物料承温情形和对热量的需求有所不合.要准确设定温度亦有须要深刻懂得物料在挤出不合阶段的形态.推却温度程度及对热量的需求情形.双螺杆挤出机温控体系由10个温控点构成.根据物料在挤出进程各个阶段的形态.推却温度程度及对热量的需求情形,可将10个温控点归纳为加温.恒温.保温三个区域.个中加温与恒温区重要在挤出机内,以排气孔为界划分为两个相对自力又互为联系关系的部分;保温区重要由机头.大小过渡段.口模部分构成.加温区由送料段.紧缩段两温控点构成.因为物料由室温状况经给料机螺杆输送给挤出机送料段螺杆,距物料熔融温度温差较大,同时物料经紧缩段螺杆将经由过程排气孔,挤出请求物料在该区域内完成由固体向熔体的转化进程,并紧紧包覆于螺槽概况,方不致从排气孔排出或壅塞排气孔.是以物料在加温区域须要的热量较大,送料段.紧缩段的温度宜设定的高一些.值得留意的是,如送料段温度设定过高,因为距离料斗与挤出机扭矩分派器较近,易导致物料在料斗内架桥,扭矩分派器齿轮受热变形及加快磨损,故送料段温度设定还应视料斗冷却情形和扭矩分派器油温而定(一般以油温≤60℃为宜).恒温区由熔融段和计量段两温控点构成.物料经由加温区后已根本呈熔体状况,但温度不甚平均,且并未完整塑化,还须进一步恒温并完整塑化,同时随螺杆容积削减,在机头均布盘(亦称过滤盘.导流盘)阻力感化下,物料粘度.密实度进一步进步,单位体积物料量增长,为包管物料温度,是以该区域物料还需必定热量;但该区双螺杆对物料剪切和压延感化所转化的内热,往往又超出了物料的需求,故熔融段和计量段温度的设定应留意:在挤出机开机前升温时,温度设定略高一些,以利于螺筒恒温;开机正常后要恰当下降,以防物料降解.保温区由机头.过渡段.口模等温控点构成.物料经由恒温区后已完整呈熔体状况,进入保温区将由螺旋活动转变成匀速直线活动,并经由过程均布盘.过渡段和口模树立熔体压力,使之温度.应力.粘度.密实度和流速更趋平均,为顺遂地从口模挤出做最后的预备.因为转变活动偏向,树立熔体压力需就义必定的热量为代价.同时在该区域,内热已不复消失,故仍须要必定外热做填补.该区域温度设定一般应高于前两个区域设定的温度,口模处的温度还应根据型材截面构造进行设定.截面庞杂或壁厚部位,温度设定应高一些;截面简略或壁薄部位,温度设定应低一些;截面临称或壁厚平均部位,温度设定应根本一致.2.2 温度掌握塑料异型材挤出温度掌握主如果环绕着设定温度进行的.因为锥形双螺杆挤出机具有温度自控和手动冷却掌握本能机能,一般临盆状况对所设定的温度实施主动掌握即可.当某段温控点温度跑高,主动掌握掉效,采取手动冷却掌握也可将显示温度掌握在设定温度界限之内.在挤出温度掌握时必须明白两个根本概念.其一,挤出机设定温度所掌握的各个温控点显示温度仅仅是螺筒.机头及口模的温度,并不是物料的现实温度.物料温度与显示温度在不合加热工况下消失不合的对应关系.即当螺筒.机头.口模等温控点外加热器加热时,物料温度现实上低于显示温度;当螺筒.机头.口模等温控点外加热器停滞加热时,物料温度则可能等于或高于显示温度.锥形双螺杆挤出机有两个热源:①外电加热器;②双螺杆对物料剪切与压延感化转化的内热.因为反应显示温度的测温点与外加热器和物料之间消失必定距离,故三者之间亦消失必定的温度梯度(即温差).从挤出加温.恒温.保温三个区域供热忱形剖析(图2)可知,加热区既消失外加热,又消失内加热,为双领导热,显示温度根本上等同于物料温度;恒温区在显示温度未达到设定温度值时,亦是双领导热;显示温度超出设定温度值时,热量开端由内向别传递,可称之为逆领导热,显示温度则可能低于物料温度;保温区因为内热不复消失,热量又开端由外向内传递,亦称之为正领导热,显示温度则高于物料温度.其二,双螺杆对物料的剪切与压延感化所转化的内热其实不受主动温控体系的束缚与安排.经由过程挤出实践可以发明,在塑料异型材挤出时,不消失内热的机头,过渡段和口模部位温控点显示温度一般比较稳固,根本上可掌握在设定温度的规模内;有内热消失的挤出机内各段温控点显示温度随挤出量增减往往摇动很大,有时远远偏离设定温度的掌握界限.例如要进步挤出量,送料段物料对热量需求增大,因挤出速度进步所增长的内热缺乏于均衡物料在该段逗留时光缩短所削减的热量,固然外加热器一向工作,但显示温度仍低于设定温度;熔融段和计量段的物料因为已完整转化为粘流态,所需热量有限,并由挤出速度进步所增长的内热超出物料在该段逗留时光缩短所削减的热量,固然外加热器停滞加热,但显示温度仍高于设定温度.鉴于挤出温度掌握的主体是物料温度,明白了物料温度.显示温度与设定温度在不合挤出工况下的对应关系,也就明白了设定和掌握挤出温度的根据和基准.诸如进步加温区设定温度可充分施展外加热器感化,有助于敏捷进步物料温度;下降恒温区设定温度可合时割断外加热源,防止内热和外热叠加感化,尽可能阻拦物料温度中断跑高;进步保温区设定温度,可借助外热源,保持物料在最佳塑化状况挤出,以得到高强度塑料异型材型坯.应当指出,在设定温度时固然已斟酌到内热的感化与影响,下降恒温区设定温度,但也仅可使该部位物料达到设定温度合时割断外热,而不克不及禁止因挤出速度进步所增长的内热.挤出实践证实,有内热消失的挤出机内各段物料温度与挤出量直接相干,下降与进步给料与挤出速度不但决议着挤出产量,并且是掌握挤出温度不成缺乏的须要手腕.但在采取加料与挤出速度掌握挤出温度时,还应明白,即使熔融段,计量段显示温度偏离设定温度,但仍小于180℃时,解释该段物料温度仍在熔融温度与分化温度区间,亦属正常.只有当显示温度接近180℃,采取手动冷却掌握无效时,才有须要下降给料与挤出速度进行温度掌握.同时因为双螺杆挤出机有强迫给料的特色,挤出量是由加料速度所决议的,加料速度和挤出速度亦消失响应的匹配关系,进步或下降加料和挤出速度应同步进行.其互相调剂的幅度应视加料孔内物料在螺槽内的充斥量而定,一般应掌握物料在螺槽内2/3高度为宜.过高则会产生挤出机过载或加料孔.排气孔冒料现象;过低则易导致双螺杆非正常磨损.别的调剂加料与挤出速度时还应亲密不雅察主机电流变更,物料塑化好时,一般电流较低.主机电流变更是断定挤出温度掌握是否恰当的一个重要根据.2.3 温度调剂假如挤出温度掌握恰当,设定温度准确与否直接决议了挤出塑料型坯的质量.挤出塑料型坯的质量反过来又是对设定温度准确与否的磨练.因为挤出掌握温度是挤出临盆前设定的,其设定温度准确与否又受配方组分.剂量和原料质量以及挤出机工艺前提的制约和影响.新建企业或临盆经验.技巧程度不甚高的操纵人员,在开机设定温度时,不免消失如许或那样的误差,是以有须要在临盆进程中经由过程对挤出塑料型坯消失的质量缺点进行体系对应剖析磨练,合时调剂所设定的温度.附表挤出型坯质量缺点特点.原因与温度调剂对策挤出塑料型坯质量大致可分为外不雅质量和内涵质量.挤出质量优越的塑料型坯重要特点是:外不雅滑腻,色彩纯正呈乳白色,切片结晶细腻,瘦语平齐规整,宽度平均.由挤出机挤出后,离开口模3~5cm天然下垂.当设定或掌握温渡过高时,挤出塑料型坯色彩泛黄.内筋曲折.内壁发泡或横截面上呈气孔状,由挤出机挤出后离开口模即脆弱下垂;温渡过低或加温不平均时,挤出塑料型坯色彩发暗无光泽,瘦语结晶光滑,瘦语宽度与壁厚不均,离开口模3~5cm 后,仍坚挺不下垂,或即向一侧曲折.经笔者几年挤出实践与统计材料标明:型坯的外不雅质量一般是由机头.过渡段.口模等部位温度设定掌握不当所致;型坯内涵质量一般是由挤出机内各段温度设定掌握不当或物料现实温度跑高掉控造成的.是以在现实操纵时应有的放矢地合时对设定温度进行调剂.具体调剂办法见附表,直至挤出型坯达到尺度为止.且忌盲目或大幅度调剂,致使挤出临盆工况恶化.如调剂无效或因温度超高导致型坯消失黄线,经重复切片挤压处理仍不好转时,解释口模或机头流道内已产生“糊料”,应即时停滞加料,减速,改用清洗料进行清洗,直至口模清洗料内无糊料杂质为止.如清洗仍无效,应停机,裁撤,分化口模,对机头和口模进行卖力检讨和清算.如确诊糊料是由挤出机熔融段或计量段物料温度掉控所致,还须裁撤挤出机螺杆,检讨.清算机筒和螺杆.3 由挤出温度掌握引出的高速挤出问题要实现高速挤出,若不解决现有国产挤出机因进步挤出速度导致的送料段温度偏低与熔融段.计量段温度跑高问题,仅采取高速模具,则只能进步小规格或帮助型材的单位产量,对大规格型材产量进步是难于奏效的.高速挤出模具问题解决之后,真正制约挤出产量进一步进步的是挤出机螺杆构造,换热情势与加热前提.笔者参照国外先辈挤出机设计有关材料以为,要进步挤出机临盆才能,须要在以下三个方面临国产挤出机进行改革和更新.(1)实施超锥度双螺杆挤出.锥形双螺杆与平行双螺杆挤出机比拟最大的特色,是在须要大量热量的送料段,螺杆直径较大,对物料的传热面积和剪切速度比较大,加快了物料的塑化;在物料已完整熔融不须要太多热量的计量段,螺杆直径较小,削减了传热面积和对熔体的剪切速度,可防止物料过热降解,在同样长径比前提下,挤出才能显著进步.如对螺杆锥度进一步改良,正向效应则会更佳.(2)转变现螺杆内部换热情势.现挤出机采取的硅油自调温螺杆,构造简略,不必维修,有节能后果,但换热率不高.可采取硅油外轮回冷却换热装配,对计量段物料实施强迫冷却换热,进步螺杆换热效力.(3)增长现挤出机送料段加热圈功率.现挤出机送料段加热功率一般为3000W,临盆实践证实,因为送料段物料须要热量较大,在挤出速度进步后,即使加热圈一向处于加热状况,仍然知足不了物料所需热量,故恰当进步加热圈功率,以利送料段物料加温.。
挤出机温度设定的规律

挤出机温度设定的规律在塑料加工行业中,挤出机是一种主要的生产设备,常用于将塑料原料加热、挤压和成型。
挤出机的温度设定是影响生产效率和产品质量的重要因素之一。
正确的温度设定可以确保塑料原料充分熔化、均匀混合,从而生产出高质量的塑料制品。
在挤出机温度设定中,存在着一定的规律和技巧,下面将详细介绍挤出机温度设定的规律。
首先,挤出机的温度设定需要考虑到塑料原料的种类。
不同种类的塑料原料对应的熔化温度各不相同,因此在设定挤出机温度时需要根据具体的塑料原料种类做出相应的调整。
一般来说,生产厂家会针对不同种类的塑料原料提供相应的温度设定建议,生产操作人员可以根据这些建议作为参考进行温度设定。
其次,挤出机的温度设定还需考虑到成型产品的要求。
不同的塑料制品对温度的要求也各有不同,有的需要较高的挤出机温度以确保塑料原料充分熔化,有的则需要较低的温度以防止塑料过热变质。
因此在进行温度设定时,需要根据具体产品的要求进行调整,并在实际生产中进行适当的调试和优化。
另外,挤出机温度设定还需要考虑到挤出机本身的特点。
不同型号、不同厂家生产的挤出机可能在温度控制系统上存在一定的差异,因此需要根据具体挤出机的特点合理设定温度参数。
在实际操作中,生产操作人员需要熟悉挤出机的温度控制系统,了解各个温度控制点的作用和影响,以便更好地进行温度设定和调试。
总的来说,挤出机温度设定是一个复杂而又关键的环节,需要考虑塑料原料的种类、成型产品的要求以及挤出机本身的特点。
在进行温度设定时,需要综合考虑这些因素,并在实际操作中不断进行调试和优化,以确保挤出机的正常运行和生产出高质量的塑料制品。
通过科学合理的温度设定,可以提高生产效率、降低生产成本,为塑料加工行业的发展和进步做出贡献。
1。
单螺杆挤出机温度设置原则

单螺杆挤出机温度设置原则
挤出成型工艺挤出机螺杆分3个区段:加料段(送料段)、熔化段(压缩段)、计量段(均化段),这三段相应的对物料组成了3个功能区:固体输送区、物料塑化区、熔体输送区。
固体输送区的料筒温度一般控制在100~1400C 。
若加料温度过低,使固体输送区延长,减少了塑化区和熔体输送区的长度,会引起塑化不良,影响产品质量。
物料塑化区的温度控制在170~1900C。
控制该段的真空度是一个重要的工艺指标,若真空度较低,会影响排气效果,导致管材中存有气泡,严重降低了管材的力学性能。
为了使物料内部的气体容易逸出,应控制物料在该段塑化程度不能过高,同时还要经常清理排气管路以免阻塞。
料筒真空度一般为0.08~0.09MPa。
熔体输送区的温度应略低一些,一般为160~1800C。
在该段提高螺杆转速、减小机头阻力及在塑化区提高压力都有利于输送速率的提高,对于PVC这样的热敏塑料,不应在此段停留时间过长,螺杆转速一般为20~30r/min。
机头是挤出制品成型的重要部件,它的作用是产生较高的熔体压力并使熔体成型为所需的形状。
各部分工艺参数分别为:口模连接器温度1650C,口模温度1700C、1700C、1650C、1800C、1900C。
挤出机常识与工艺(温度、螺杆)

挤出机常识与⼯艺(温度、螺杆)⼀.挤出机分类产品代号规格参数说明:例如SHJM-Z40×25×800,指螺杆直径为40mm,长径⽐为25,牵引辊筒长为800mm 的双螺杆混合塑料挤出改塑薄膜机。
1、“SH”类别代号,指双螺杆混合型(也有写:SHSJ,SJ指塑料挤出机)2、“J”组别代号,指挤出机。
3、“M”指品种代号,指吹塑薄膜机4、“Z”指辅助代号,指主要机组,另如是“F”指辅助机。
5、“40×25×800”指规格参数,指螺杆有直径为40mm,长径⽐为25,牵引辊筒长为800mm。
6、最后⼀位为⼚商识别序号,⼀般不出现,被省略⼆、双螺杆混合挤出机的功能参数1、“D”为直径,衡量产量⼤⼩的⼀个重要参数。
2、“L/D”,指长度与直径的⽐例,直接影响到塑化度,是衡量⽤途的标志,⼀般塑料改性,⽤30-40左右,常⽤36:1或30:1。
3、“H”,螺槽深度,指其容料空间之⼤⼩。
4、“e”螺棱厚度,⼯艺上体现在剪切之⼤⼩。
5、“6”螺杆与机筒之间隙,挤出机质量的⼀个重要参数,⼀般在0.3-2mm,越过5mm挤出机是警介线。
6、“N”主机转速,指其最⾼值,指⼀个加⼯调整范围,极⼤影响产量及中⾼低速之划分。
(国产机⼀般500-600r/min)如:max:600r/min,低速:350r/min、中速230-240r/min、⾼速450-600r/min。
7、“P”,电机功率及加热功率。
三、螺杆排列及其⼯艺设定①螺杆的分段及其功能(1)螺杆⼀般分:输送段、熔融段、混炼段、排⽓段、均化段5个段。
1、输送段,输送物料,防⽌溢料。
2、熔融段,此段通过热传递和摩擦剪切,使物料充分熔融和均化。
3、混炼段,使物料组分尺⼨进⼀步细化与均匀,形成理想的结构,具分布性与分散性混合功能。
4、排⽓段,排出⽔汽、低分⼦量物质等杂质。
5、均化(计量)段,输送和增压,建⽴⼀定压⼒,使模⼝处物料有⼀定的致密度,同时进⼀步混合,最终达到顺利挤出造粒的⽬的。
挤出成型工艺介绍工艺
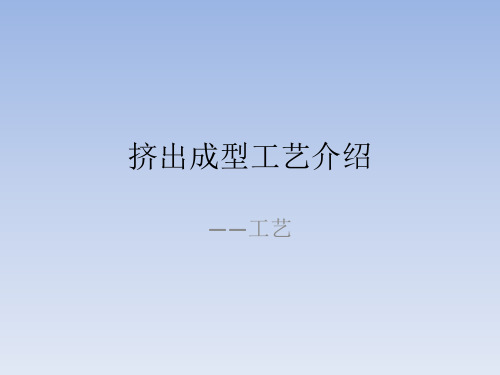
——工艺
目录
一、工艺参数设定原则 二、片材工艺流程及装置 三、工艺控制 四、常见缺陷
一、工艺参数设定原则
1、机身温度 对与普通的单组份热塑性塑料固体原料的挤出成形,挤出机机身温度设
定原则为: ①机身设定的最高温度略高于塑料的黏流温度(或熔点); ②机身设定的最低温度应至少低于塑料软化点10; ③单螺杆挤出机机身设定的最高温度与最低温度的差值不大于80; ④机身温度字加料端到熔料出口逐渐升高或与螺杆计量段对应区温度相近; ⑤在满足熔化物料的前提下,机身温度应尽可能低。
对与多层共挤出成形,除了考虑以上因素外,还应注意层间的粘接强度, 应适当提高机身温度。
一、工艺参数设定原则
2、机头温度 机头加热有三个作用: ①进一步塑化物料; ②保持熔体流动性和良好的成形性; ③熔体之间的黏合性。
熔体在机头流道中流动会产生一定的摩擦热,因此机头温度设定应考虑 满足其基本作用情况下尽可能低。通常机颈处温度略低于机身最高温度,口模各 段的温度略高于机身设定的最高温度。
对大型挤出机头,应选用内外加热装置,提高口模温度均匀性和加热效 率。
一、工艺参数设定原则
3、挤出机冷却 为了防止挤出机加料斗底部处物料因过热软化而“架桥”,导致加料不
顺畅,一般挤出机加料斗底部均设置冷却水通道,生产前应接通冷却水冷却。对 与单螺杆挤出机,可采用螺杆内部冷却方法,提高固体输送速率。 4、挤出速度
三、工艺控制
1、挤出温度 ①挤出温度应根据挤出物料的加工流变特性、热分解性能和板、片材使
用性能综合确定。挤出温度一般分6——10段控制,挤出料筒温度控制在满足均 匀塑化物料的前提下应尽可能低,机头温度除了考虑挤出产量外,还要考虑制品 表面质量要求及与结晶、取向有关的物理力学性能要求,一般比挤出料筒温度高 5—速度是决定挤出产量和质量的重要 工艺参数。
单螺杆挤出机的温度控制
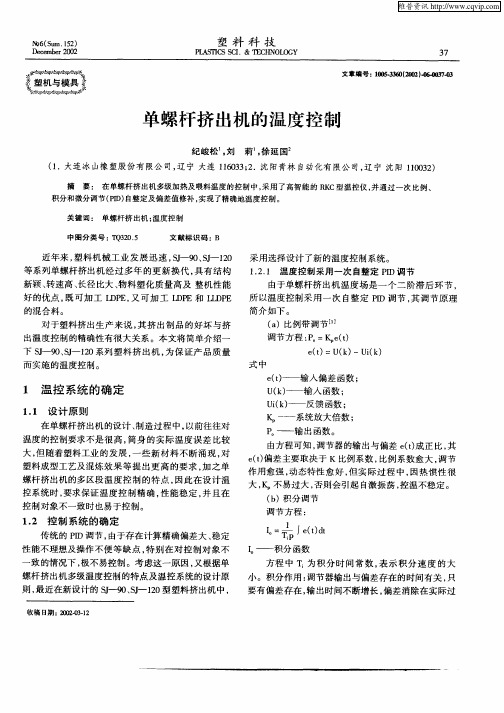
J( d tt e)
1— — 积分 函数 0
致 的情 况 下 , 不 易控 制 。考 虑 这 一原 因 , 根据单 极 又 、J 10型 塑料挤 出机 中 , S一 2
方程 中 T 为积分 时 间常数 , 表示积 分速 度 的大
小 。积 分 作用 : 节 器输 出 与偏 差存 在 的 时 间有关 , 调 只 要 有 偏差 存 在 , 出时 间不 断增 长 , 输 偏差 消 除在 实 际 过
1 温 控 系统 的确 定
1 1 设 计 原 则 .
在 单 螺杆 挤 出机 的设 计 、 造 过程 中 , 制 以前 往 往对
U k —— 输 人 函数 ; () u ( ) — 反馈 函数 ; ik —
I —— 系统 放大 倍 数 ; < D
— —
温度的控制要求不是很 高, 筒身 的实 际温度误 差 比较 大 , 随着 塑 料工业 的 发 展 , 些 新 材 料 不 断 涌 现 , 但 一 对
螺 杆 挤 出机 多级 温 度控 制 的特 点及 温 控 系统 的 设计 原 则 , 近 在新 设计 的 最
收稿 日期 :20 - .2 020 1 3
维普资讯
3 8
纪 峻松 , 等
单螺杆 挤 出机 的温 度控制
程 中 , 控 对象 往 往 不是 单 一 的 , 制过 程 也 不 是简 单 被 控 的过 程 。 态与 动 态 间有 着较 大 的 区别 。 静 ()微分 调 节 c
近年 来 , 塑料 机 械工 业 发 展 迅 速 , 卜 9 、 一 10 S 0 2 等系列单螺杆挤出机经过多年 的更新换代 , 有结构 具
采用选择设计 了新的温度控制系统。 121 温度 控 制采 用 一次 自整 定 PD调 节 .. I
螺杆挤出机温度控制

螺杆挤出机温度控制文稿归稿存档编号:[KKUY-KKIO69-OTM243-OLUI129-G00I-FDQS58-挤出温度控制主要有温度设定、控制和调整三个部分构成。
设定温度是控制温度的依据和基准,调整温度是对设定温度的修正和完善。
2.1 温度设定设定温度的目的是为了控制物料挤出成型过程,始终在熔融温度与分解温度区间(即160~180℃)进行。
要正确设定温度,则需充分考虑制约物料成型温度的相关因素。
(1)配方组分、剂量和原料质量。
据文献介绍和生产实践验证,不同配方或同一配方不同厂家生产的物料(PVC、CPE、热稳定剂等),挤出成型温度往往有很大差异,有的达10℃左右,这一点在没有实验条件或生产经验的情况下,是不可预知的。
只有通过生产实践,依据塑料型坯的质量,适时调整设定温度。
开始设定温度时不易过高,应从低向高逐步调整。
(2)塑料挤出亦是一个能量守恒的过程。
单位体积的固体转化为熔体所需的总能量相对是恒定的,物料的输送速率基本上平衡于物料的熔化速率。
因受口模物料流速和定型模冷却条件的限制,不同规格的异型材单位时间挤出量差异亦很大。
因物料输送速率不同,物料熔融所需热量亦不同。
对于单螺杆挤出机或双螺杆挤出机没有内热存在的加热区域,即机头、大小过渡段、口模等部位,生产大规格型材时,设定温度宜高一些;生产小规格异型材,设定温度宜低一些。
对于双螺杆挤出机有内热存在的加热区域,由于内热的作用,挤出速率反过来又直接影响物料的熔融速率。
设定温度应视该段物料的形态、承受温度程度及对热量的需求情况而定。
(3)塑料挤出需经历一定时间历程。
在这一历程的不同阶段,由物料的加工特性和挤出机职能所决定,不同形态的物料承温情况和对热量的需求有所不同。
要正确设定温度亦有必要深入了解物料在挤出不同阶段的形态、承受温度程度及对热量的需求情况。
双螺杆挤出机温控系统由10个温控点组成。
依据物料在挤出过程各个阶段的形态、承受温度程度及对热量的需求情况,可将10个温控点归纳为加温、恒温、保温三个区域。
单螺杆挤出机温度
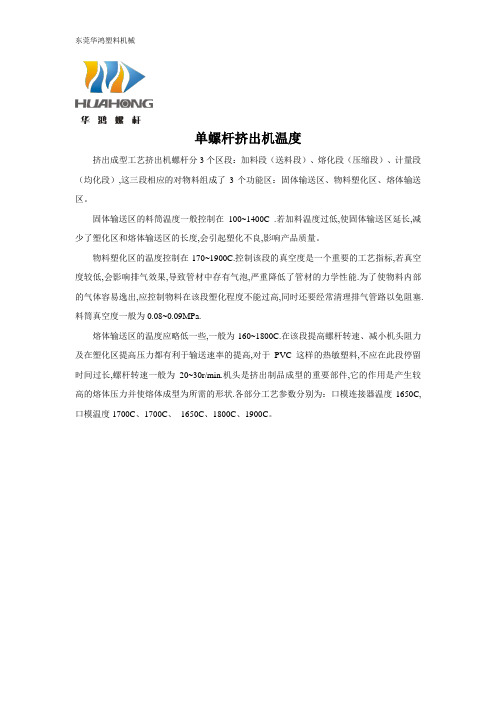
东莞华鸿塑料机械
单螺杆挤出机温度
挤出成型工艺挤出机螺杆分3个区段:加料段(送料段)、熔化段(压缩段)、计量段(均化段),这三段相应的对物料组成了3个功能区:固体输送区、物料塑化区、熔体输送区。
固体输送区的料筒温度一般控制在100~1400C .若加料温度过低,使固体输送区延长,减少了塑化区和熔体输送区的长度,会引起塑化不良,影响产品质量。
物料塑化区的温度控制在170~1900C.控制该段的真空度是一个重要的工艺指标,若真空度较低,会影响排气效果,导致管材中存有气泡,严重降低了管材的力学性能.为了使物料内部的气体容易逸出,应控制物料在该段塑化程度不能过高,同时还要经常清理排气管路以免阻塞.料筒真空度一般为0.08~0.09MPa.
熔体输送区的温度应略低一些,一般为160~1800C.在该段提高螺杆转速、减小机头阻力及在塑化区提高压力都有利于输送速率的提高,对于PVC这样的热敏塑料,不应在此段停留时间过长,螺杆转速一般为20~30r/min.机头是挤出制品成型的重要部件,它的作用是产生较高的熔体压力并使熔体成型为所需的形状.各部分工艺参数分别为:口模连接器温度1650C,口模温度1700C、1700C、1650C、1800C、1900C。
挤出机温度的设定原理

挤出机温度的设定原理挤出机是塑料加工中常用的设备,其温度对于生产过程和制品质量至关重要。
挤出机温度的设定需要根据不同的塑料材料以及产品要求来进行调整,以确保塑料能够被有效地加工成所需的形状和性能。
在挤出机温度的设定过程中,通常需要考虑以下几个方面:塑料材料的熔融温度不同类型的塑料材料具有不同的熔融温度,因此在设置挤出机温度时,首先需要了解所使用的塑料材料的熔融温度范围。
将挤出机的加热区温度设定在塑料的熔融温度以上,以确保塑料材料能够被有效地熔化和挤出。
同时,过高的温度会导致塑料过度分解,影响加工质量。
挤出机的螺杆转速挤出机的螺杆转速也会影响挤出机温度的设定。
通常情况下,较高的螺杆转速会产生较高的摩擦热量,导致塑料材料更容易熔化。
因此,根据产品要求和塑料材料特性,可以适当调整螺杆转速来配合温度设定,从而实现更好的挤出效果。
模具设计和产品要求除了塑料材料的特性外,挤出机温度的设定还需要考虑模具设计和产品要求。
不同形状和尺寸的产品可能需要不同的挤出温度来保证其加工质量和外观。
通过调整挤出机温度,可以优化产品的表面光滑度、尺寸精度和强度等性能。
冷却系统的影响最后,冷却系统对于挤出机温度的设定也有重要影响。
在塑料挤出过程中,适当的冷却可以快速固化塑料,提高生产效率和产品质量。
因此,挤出机温度的设定需要考虑冷却系统的效果,确保塑料挤出后能够迅速降温并保持形状稳定。
综上所述,挤出机温度的设定原理涉及塑料材料、螺杆转速、模具设计和产品要求以及冷却系统等多个因素。
通过科学合理地设定挤出机温度,可以实现塑料材料的有效加工和生产出符合要求的制品,为塑料加工行业的发展提供保障。
1。
单螺杆挤出机操作规程
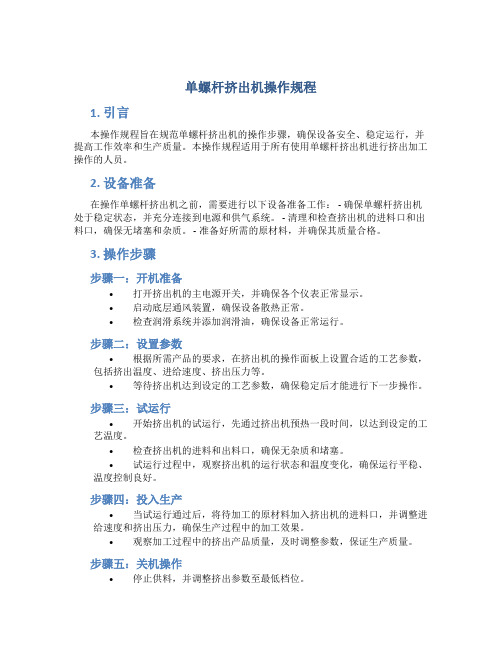
单螺杆挤出机操作规程1. 引言本操作规程旨在规范单螺杆挤出机的操作步骤,确保设备安全、稳定运行,并提高工作效率和生产质量。
本操作规程适用于所有使用单螺杆挤出机进行挤出加工操作的人员。
2. 设备准备在操作单螺杆挤出机之前,需要进行以下设备准备工作: - 确保单螺杆挤出机处于稳定状态,并充分连接到电源和供气系统。
- 清理和检查挤出机的进料口和出料口,确保无堵塞和杂质。
- 准备好所需的原材料,并确保其质量合格。
3. 操作步骤步骤一:开机准备•打开挤出机的主电源开关,并确保各个仪表正常显示。
•启动底层通风装置,确保设备散热正常。
•检查润滑系统并添加润滑油,确保设备正常运行。
步骤二:设置参数•根据所需产品的要求,在挤出机的操作面板上设置合适的工艺参数,包括挤出温度、进给速度、挤出压力等。
•等待挤出机达到设定的工艺参数,确保稳定后才能进行下一步操作。
步骤三:试运行•开始挤出机的试运行,先通过挤出机预热一段时间,以达到设定的工艺温度。
•检查挤出机的进料和出料口,确保无杂质和堵塞。
•试运行过程中,观察挤出机的运行状态和温度变化,确保运行平稳、温度控制良好。
步骤四:投入生产•当试运行通过后,将待加工的原材料加入挤出机的进料口,并调整进给速度和挤出压力,确保生产过程中的加工效果。
•观察加工过程中的挤出产品质量,及时调整参数,保证生产质量。
步骤五:关机操作•停止供料,并调整挤出参数至最低档位。
•关闭挤出机主电源,并断开电源连接。
•清理挤出机的残余物,并对设备进行基本清洁和维护。
4. 安全注意事项•操作人员应穿戴合适的工作服和防护设备,避免身体直接接触挤出机或原材料。
•操作过程中严禁随意改变设备参数,必须经过授权人员批准后方可进行调整。
•发现异常情况时,应立即停机并报告相关负责人处理,不能私自进行维修或改动。
•在操作过程中,严禁将手、手指或其他物品伸入挤出机的运动部件。
5. 总结本文档详细介绍了单螺杆挤出机的操作规程,包括设备准备、操作步骤、安全注意事项等。
挤出机温度设定的规律

挤出机温度设定的规律挤出机是塑料加工中非常重要的设备之一,它能够将塑料料粒通过加热和挤压的方式变形成所需的形状。
而在挤出机的生产过程中,挤出机温度的设定则是非常关键的一环。
那么,挤出机温度该如何进行设定呢?我们需要了解一下挤出机温度的设定规律。
一般来说,挤出机温度的设定会受到以下几个因素的影响。
第一,塑料料粒的种类。
不同种类的塑料料粒在加工过程中需要的温度是不同的。
比如说,一些高分子量的聚合物需要的加热温度比较高,而一些低分子量的聚合物则需要的加热温度比较低。
第二,挤出机模头的形状和大小。
挤出机模头的形状和大小也会影响到温度的设定。
一般来说,模头的尺寸越大、形状越复杂,需要的温度就越高。
第三,挤出机生产的产品类型和规格。
不同类型和规格的产品需要的温度也会有所不同。
比如说,一些薄壁的产品需要的温度相对较低,而一些厚壁的产品则需要的温度相对较高。
在了解了这些因素之后,我们就可以进行挤出机温度的设定了。
一般来说,挤出机温度的设定需要分为以下几个步骤。
第一步,确定塑料料粒的种类。
在生产过程中,我们需要首先确定塑料料粒的种类,从而根据不同种类的塑料料粒来设定相应的加热温度。
第二步,设定进料区温度。
进料区温度是指塑料料粒进入挤出机后的加热温度。
一般来说,进料区温度需要比塑料的熔点高10℃左右。
不过,具体的温度还需要根据塑料料粒的种类和生产规格来进行调整。
第三步,设定加热区温度。
加热区温度是指塑料料粒在挤出机内进行加热的温度。
一般来说,加热区温度需要比进料区温度高10℃左右。
但同样需要根据具体的塑料料粒种类和生产规格来进行调整。
第四步,设定模头区温度。
模头区温度是指塑料料粒通过模头挤出后的温度。
在设定模头区温度时,需要考虑到产品的具体规格和尺寸,以及模头的形状和大小等因素。
第五步,进行调整和优化。
在进行挤出机温度设定之后,需要进行实际的生产试验,从而对温度进行进一步的调整和优化,以达到最佳的生产效果。
挤出机温度的设定是一个非常重要的环节,需要考虑到多个因素的影响。
挤出成型工艺介绍工艺
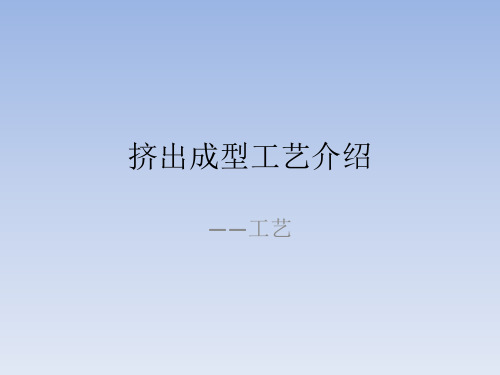
三、工艺控制
三、工艺控制
2、螺杆冷却 用单螺杆挤出机生产板、片材时,对于与螺杆表面摩擦因数较大的物料
或较易熔融并使固体输送段很短的物料,应采用螺杆冷却方法以提高固体输送速 率。 3、牵引速度
挤板、片材过程中,为了避免板、片材“冷拉”导致的表面不平整,内 应力集中等缺陷,应保持牵引速度与挤出的线速度基本相等,但是比三辊压光机 快5%——10%左右。 4、板片厚度控制
三、工艺控制
1、挤出温度 ①挤出温度应根据挤出物料的加工流变特性、热分解性能和板、片材使
用性能综合确定。挤出温度一般分6——10段控制,挤出料筒温度控制在满足均 匀塑化物料的前提下应尽可能低,机头温度除了考虑挤出产量外,还要考虑制品 表面质量要求及与结晶、取向有关的物理力学性能要求,一般比挤出料筒温度高 5——10。
对大型挤出机头,应选用内外加热装置,提高口模温度均匀性和加热效 率。
一、工艺参数设定原则
3、挤出机冷却 为了防止挤出机加料斗底部处物料因过热软化而“架桥”,导致加料不
顺畅,一般挤出机加料斗底部均设置冷却水通道,生产前应接通冷却水冷却。对 与单螺杆挤出机,可采用螺杆内部冷却方法,提高固体输送速率。 4、挤出速度
——工艺
目录
一、工艺参数设定原则 二、片材工艺流程及装置 三、工艺控制 四、常见缺陷
一、工艺参数设定原则
1、机身温度 对与普通的单组份热塑性塑料固体原料的挤出成形,挤出机机身温度设
定原则为: ①机身设定的最高温度略高于塑料的黏流温度(或熔点); ②机身设定的最低温度应至少低于塑料软化点10; ③单螺杆挤出机机身设定的最高温度与最低温度的差值不大于80; ④机身温度字加料端到熔料出口逐渐升高或与螺杆计量段对应区温度相近; ⑤在满足熔化物料的前提下,机身温度应尽可能低。
挤出机常识与工艺(温度、螺杆)

挤出机常识与工艺(温度、螺杆)一、挤出机分类认识产品代号及规格参数例如:SHJM-Z40×25×800,表示:螺杆直径为40mm,长径比为25,牵引辊筒长为800mm 的双螺杆混合塑料挤出改塑薄膜机。
1、“SH”类别代号,指双螺杆混合型(也有写:SHSJ,SJ指塑料挤出机)。
2、“J”组别代号,指挤出机。
3、“M”指品种代号,指吹塑薄膜机。
4、“Z”指辅助代号,指主要机组,另如是“F”指辅助机。
5、“40×25×800”指规格参数,指螺杆有直径为40mm,长径比为25,牵引辊筒长为800mm。
6、最后一位为厂商识别序号,一般不出现,被省略。
二、双螺杆混合挤出机的功能参数1、“D”为直径,衡量产量大小的一个重要参数。
2、“L/D”,指长度与直径的比例,直接影响到塑化度,是衡量用途的标志,一般塑料改性,用30-40左右,常用36:1或30:1。
3、“H”,螺槽深度,指其容料空间之大小。
4、“e”螺棱厚度,工艺上体现在剪切之大小。
5、“6”螺杆与机筒之间隙,挤出机质量的一个重要参数,一般在0.3-2mm,越过5mm挤出机是警介线。
6、“N”主机转速,指其最高值,指一个加工调整范围,极大影响产量及中高低速之划分。
(国产机一般500-600r/min),(如:max:600r/min,低速: 230-240r/min 、中速350r/min 、高速450-600r/min。
7、“P”,电机功率及加热功率。
三、螺杆排列及其工艺设定①螺杆的分段及其功能(1)螺杆一般分:输送段、熔融段、混炼段、排气段、均化段5个段。
a、输送段,输送物料,防止溢料。
b、熔融段,此段通过热传递和摩擦剪切,使物料充分熔融和均化。
c、混炼段,使物料组分尺寸进一步细化与均匀,形成理想的结构,具分布性与分散性混合功能。
d、排气段,排出水汽、低分子量物质等杂质。
e、均化(计量)段,输送和增压,建立一定压力,使模口处物料有一定的致密度,同时进一步混合,最终达到顺利挤出造粒的目的。
挤出机常识与工艺(温度、螺杆)

作用下置换流动而实现。
•
2、分散混合,使组分破碎成微粒或使不相容的两组分分散相尺寸达至
要求范围,主靠剪切压力和接伸应力实现。
2021/6/16
3
②输送元件,螺纹式的
• 表示法:如“56/56”输送块,前一个”56”指导程为56MM,后一 个”56”指长度为56MM。
• 大导程,指螺距为1.5D~2D • 小导程,指螺距为0.4D左右。 • 其使用规律:随着导程增加,螺杆挤出量增加,物料停留时间减少,
具分布性与分散性混合功能。
•
4、排气段,排出水汽、低分子量物质等杂质。
•
5、均化(计量)段,输送和增压,建立一定压力,使模口处物料有
一定的致密度,同时进一步混合,最终达到顺利挤出造粒的目的。
•
(2)分布(分配)与分散混合之段别
•
1、分布混合,使熔体分割与重组,使各组分空间分布均匀,主要通过
分离,拉伸(压缩与膨胀交替产生)、扭曲、流体活动重新取向等应力
其熔融经历:固态床的形成、破裂、形成大量颗粒漂浮于熔体中,后逐渐融化。
2021/6/16
6
⑵温度设定原则:
• ①共混合金各组分熔点及其比列:以共混组分熔点为依据, 以连续相熔点为调整范围。
• ②塑料的热性能,如熔融吸热放热、热降解历程及热氧化 难易。
• ⑴塑料的物理变化特性: • A非结晶性塑料 • 随温度逐渐升高有三个物态特性如:
•
高弹态
粘流态
•
Tg
Tf
Td
• (玻璃化温度) ( 熔融温度) (分解温度)
• 其熔融在剪切流动引起粘性耗散下进行。
• B结晶性塑料,
• 随温度逐渐升高有二个物态特性,且变化都较为突然如:
- 1、下载文档前请自行甄别文档内容的完整性,平台不提供额外的编辑、内容补充、找答案等附加服务。
- 2、"仅部分预览"的文档,不可在线预览部分如存在完整性等问题,可反馈申请退款(可完整预览的文档不适用该条件!)。
- 3、如文档侵犯您的权益,请联系客服反馈,我们会尽快为您处理(人工客服工作时间:9:00-18:30)。
单螺杆挤出机温度设置原则
挤出成型工艺挤出机螺杆分3个区段:加料段(送料段)、熔化段(压缩段)、计量段(均化段),这三段相应的对物料组成了3个功能区:固体输送区、物料塑化区、熔体输送区。
固体输送区的料筒温度一般控制在100~1400C 。
若加料温度过低,使固体输送区延长,减少了塑化区和熔体输送区的长度,会引起塑化不良,影响产品质量。
物料塑化区的温度控制在170~1900C。
控制该段的真空度是一个重要的工艺指标,若真空度较低,会影响排气效果,导致管材中存有气泡,严重降低了管材的力学性能。
为了使物料内部的气体容易逸出,应控制物料在该段塑化程度不能过高,同时还要经常清理排气管路以免阻塞。
料筒真空度一般为0.08~0.09MPa。
熔体输送区的温度应略低一些,一般为160~1800C。
在该段提高螺杆转速、减小机头阻力及在塑化区提高压力都有利于输送速率的提高,对于PVC这样的热敏塑料,不应在此段停留时间过长,螺杆转速一般为20~30r/min。
机头是挤出制品成型的重要部件,它的作用是产生较高的熔体压力并使熔体成型为所需的形状。
各部分工艺参数分别为:口模连接器温度1650C,口模温度1700C、1700C、1650C、1800C、1900C。