工艺设计计算参考
西安市水厂工艺设计计算说明带详图概要

水质工程学课程设计专业给水排水工程专业班级给排水指导教师杨卫身、马立艳学生姓名学号2010年12月 26日目录1总论 (2)1.1设计任务及要求 (2)1.2基本资料 (2)1.2.1工程概况 (2)1.2.2地面水源 (2)1.2.3源水水质资料 (2)2总体设计概况 (3)2.1水厂规模 (3)2.2总体设计 (3)2.2.1确定给水处理厂工艺流程 (3)2.2.2处理构筑物及设备形式选择 (3)2.2.2.1取水构筑物 (3)2.2.2.2药剂溶解池 (3)2.2.2.3反应池 (4)2.2.2.4混凝 (5)2.2.2.5滤池 (11)2.2.2.6消毒 (23)2.2.3 其他设计 (24)2.2.3.1清水池 (24)2.2.3.2吸水井 (26)2.2.3.3二级泵房 (26)2.2.4 辅助建筑面积设计 (27)2.3 反水厂总体布置 (28)2.3.1水厂的平面布置 (28)2.3.2水厂的高程布置 (28)8设计体会 (28)参考文献 (28)1总论1.1设计任务及要求给水厂课程设计的目的在于加深理解所学专业理论,培养运用所学知识综合分析和解决实际工程设计问题的初步能力,在设计、运算、绘图、查阅资料和设计手册以及使用设计规范等基本技能上得到初步训练和提高。
课程设计的内容是根据所给资料,设计华东地区某给水厂设计,要求对初步方案进行设计,对主要处理构筑物的工艺尺寸进行计算,确定水厂平面布置和高程布置,最后绘出水厂平面布置图、高程布置图、管线布置图、绿化施工图和某个单项处理构筑物(澄清池或过滤池)的单体图(包括平面图、剖面图,达到施工图深度)及设备选型,并简要写出一份设计计算说明书。
1.2基本资料1.2.1 工程概况本设计为华东地区某城市给水工程设计,水厂规模:日处理水量20 万吨。
设计中采用位于城市西南的河流上游作为水源地。
城市土壤种类为亚粘土。
地下水位深度 6 m。
冰冻线深度0.2m。
A O工艺设计规范
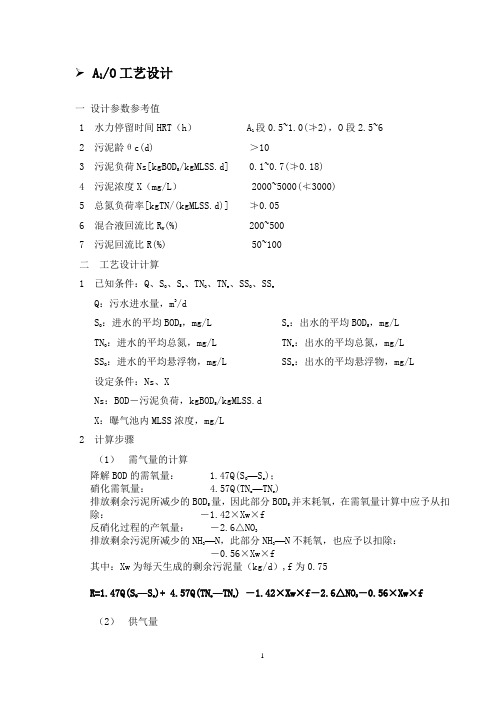
G:供气量,m3/d 几种空气扩散装置的氧的转移效率 EA 扩散装置类型 氧的转移效率 EA 陶土扩散板、管(水深 3.5m) 10~12 绿豆沙扩散板、管(水深 3.5m) 8.8~10.4 穿孔管:φ5(水深 3.5m) 6.2~7.9 穿孔管:φ10(水深 3.5m) 6.7~7.9 倒盆式扩散器(水深 3.5m) 6.9~7.5 倒盆式扩散器(水深 4.0m) 8.5 倒盆式扩散器(水深 5.0m) 10 竖管扩散器 6.2~7.1 射流式扩散装置 24~30 (3) 反应池容积计算 Vo=
ηTN × 100% 1 −ηTN
ηTN=(TNo—TNe)/ TNo
3
A1/O 工艺设计
一 设计参数参考值 1 2 3 4 5 6 7 二 1 水力停留时间 HRT(h) 污泥龄θc(d) 污泥负荷 Ns[kgBOD5/kgMLSS.d] 污泥浓度 X(mg/L) 总氮负荷率[kgTN/(kgMLSS.d)] 混合液回流比 RN(%) 污泥回流比 R(%) 工艺设计计算 已知条件:Q、SO、Se、TNO、TNe、SSO、SSe Q:污水进水量,m3/d SO:进水的平均 BOD5,mg/L TNO:进水的平均总氮,mg/L SSO:进水的平均悬浮物,mg/L 设定条件:Ns、X Ns:BOD-污泥负荷,kgBOD5/kgMLSS.d X:曝气池内 MLSS 浓度,mg/L 2 计算步骤 (1) 需气量的计算 降解 BOD 的需氧量: 1.47Q(SO—Se); 硝化需氧量: 4.57Q(TNo—TNe) 排放剩余污泥所减少的 BOD5 量,因此部分 BOD5 并末耗氧,在需氧量计算中应予从扣 除: -1.42×Xw×f 反硝化过程的产氧量: -2.6△NO3 排放剩余污泥所减少的 NH3—N,此部分 NH3—N 不耗氧,也应予以扣除: -0.56×Xw×f 其中:Xw 为每天生成的剩余污泥量(kg/d),f 为 0.75 R=1.47Q(SO—Se)+ 4.57Q(TNo—TNe) -1.42×Xw×f-2.6△NO3-0.56×Xw×f (2) 供气量
工艺流程的计算

工艺流程的计算
《工艺流程的计算》
工艺流程的计算是制造过程中至关重要的一步。
它涉及到材料的选择、成本的考量、生产效率的提高等方面。
在工艺流程的计算中,需要考虑到原材料的成本、加工过程中的耗能、生产线的布局以及最终产品的质量等因素。
首先,工艺流程的计算需要考虑到原材料的成本。
不同的材料在市场上的价格会有所不同,因此在制定工艺流程时需要综合考虑成本与性能的平衡。
有的时候,低成本的材料可能会降低产品的质量,因此需要进行成本与性能的权衡。
其次,工艺流程的计算还需要考虑到加工过程中的耗能。
不同的加工方式会产生不同的能耗,而能源的成本又会直接影响到生产成本。
因此在制定工艺流程时,需要进行能源消耗的计算,以确保生产过程中的能源利用效率。
另外,工艺流程的计算也需要考虑到生产线的布局。
合理的生产线布局可以有效提高生产效率,减少生产过程中的浪费。
通过对生产线布局的计算,可以优化生产过程,提高生产效率,降低生产成本。
最后,工艺流程的计算也需要考虑到产品的质量。
通过对生产过程中各个环节的计算,可以确保产品的质量符合相关标准,提高产品的竞争力。
综上所述,工艺流程的计算涉及多个方面,需要综合考虑成本、能源消耗、生产效率和产品质量等因素。
只有通过科学的计算,才能够制定出最优的工艺流程,提高生产效率,降低生产成本,提高产品质量。
cass工艺设计计算书

cass工艺设计计算书CASS(循环活性污泥系统)工艺是一种常用的污水处理工艺,以下是一个简单的 CASS 工艺设计计算书的示例,供参考:1. 设计基础数据:- 设计流量:[具体数值]m³/d- 进水水质:BOD5 = [数值]mg/L,COD = [数值]mg/L,SS = [数值]mg/L- 出水水质:BOD5 ≤ [数值]mg/L,COD ≤ [数值]mg/L,SS ≤ [数值]mg/L2. 反应器容积计算:- 有效容积(V):根据进水水质和出水水质要求,按照负荷法计算有效容积。
通常 CASS 工艺的 BOD5 负荷为[数值]kgBOD5/m³·d,COD 负荷为[数值]kgCOD/m³·d。
计算得到有效容积为 V = [具体数值]m³。
- 反应器数量(n):根据有效容积和单个反应器容积确定反应器数量。
假设单个反应器容积为[数值]m³,则反应器数量为 n = V/[数值],取整得到[具体数值]个反应器。
3. 曝气系统设计:- 需氧量计算:根据进水水质和出水水质要求,按照 BOD5 去除量和氨氮硝化需氧量计算需氧量。
通常 CASS 工艺的需氧量为[数值]kgO2/kgBOD5 去除,[数值]kgO2/kgNH4-N 硝化。
计算得到总需氧量为[具体数值]kgO2/d。
- 曝气设备选择:根据需氧量和反应器布局,选择合适的曝气设备。
常见的曝气设备包括鼓风机、曝气头、曝气软管等。
- 曝气量调节:根据进水负荷和水质变化,设置曝气量调节装置,以保证反应器内的溶解氧浓度在合适范围内。
4. 沉淀系统设计:- 沉淀时间:根据反应器容积和进出水流量,确定沉淀时间。
通常 CASS 工艺的沉淀时间为[数值]h。
- 沉淀区容积:根据沉淀时间和进出水流量,计算沉淀区容积。
沉淀区容积一般为反应器容积的[数值]%。
- 排泥系统设计:设置排泥泵和排泥管道,定期将沉淀区的污泥排出。
年产十万吨合成氨变换工艺和设备设计核算参考
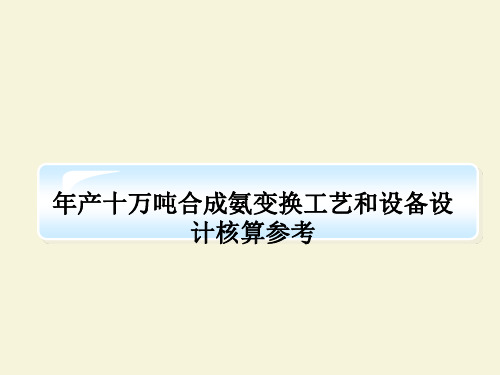
5、工艺流程
本设计主要是变换工序的工艺设计,所选流程为:
H2O
原料气
饱
和
热
水
塔
中
温 变
换热器
换
炉
低 变换气 温 变 换 炉
选用中串低工艺。从压缩工段来的变换气进入饱和
热水塔,在饱和塔出口加入水蒸汽使汽气比达3-5,以 后
再进入中变炉将转换气中一氧化碳含量降到3%以下。
再通过换热器将转换气的温度降到180℃左右,进入低
物量在设备里无物量的变化。
水带入热Q1=XCpT 变换气带入热Q2=nCpmT 同理求得变换气带出热Q3;水带出热Q4。 热量平衡:0.96×(Q1+ Q2)= Q3+ Q4 则X=288.305koml
中变炉一段催化床层的物料衡算
假设CO在一段催化床层的实际变换率为60% 求出在一段催化床层反应后剩余各组分的量 得到出中变炉一段催化床层的变换气干组分的含 进而求得出中变炉一段催化床层变换气湿组分含 量 出中变炉一段催化床层的变换气湿组分的含量 根据:Kp=(H2%×CO2%)/(H2O%×CO%) 计算得Kp,查出对应温度t
主换热器的物料与热量的计算
进出设备的变换气的量:190.97kmol 进出设备的水的量: Xkmol
变换气进设备的温度: 365℃ 变换气出设备的温度: 250℃
水进设备的温度: 水出设备的温度:
20℃ 90℃
变换气带入热Q1=nCpmT;水带入热Q2=XCpT 同理求变换气带出热Q3水带出热Q4 0.96×(Q1+Q2)=Q3+Q4
低变炉的物料计算
要将CO%降到0.2%(湿基)以下,
由CO实际变换率为:Xp=
Ya Ya
AO工艺标准规范标准设计计算参考材料

A1/O生物脱氮工艺一、设计资料设计处理能力为日处理废水量为30000m3废水水质如下:PH值7.0~7.5 水温14~25℃BOD5=160mg/L VSS=126mg/L(VSS/TSS=0.7) TN=40mg/L NH3-N=30mg/L根据要求:出水水质如下:BOD5=20mg/L TSS=20mg/L TN 15mg/L NH3-N 8mg/L根据环保部门要求,废水处理站投产运行后排废水应达到国家标准《污水综合排放标准》GB8978-1996中规定的“二级现有”标准,即COD 120mg/l BOD 30 mg/l NH -N<20 mg/l PH=6-9 SS<30 mg/l二、污水处理工艺方案的确定城市污水用沉淀法处理一般只能去除约25~30℅的BOD5,污水中的胶体和溶解性有机物不能利用沉淀方法去除,化学方法由于药剂费用很高而且化学混凝去除溶解性有机物的效果不好而不宜采用。
采用生物处理法是去除废水中有机物的最经济最有效的选择。
废水中的氮一般以有机氮、氨氮、亚硝酸盐氮和硝酸盐氮等四种形态存在。
生活污水中氮的主要存在形态是有机氮和氨氮。
其中有机氮占生活污水含氮量的40%~60%,氨氮占50%~60%,亚硝酸盐氮和硝酸盐氮仅占0%~5%。
废水生物脱氮的基本原理是在传统二级生物处理中,将有机氮转化为氨氮的基础上,通过硝化和反硝化菌的作用,将氨氮通过硝化转化为亚硝态氮、硝态氮,再通过反硝化作用将硝态氮转化为氮气,而达到从废水中脱氮的目的。
废水的生物脱氮处理过程,实际上是将氮在自然界中循环的基本原理应用与废水生物处理,并借助于不同微生物的共同协调作用以及合理的认为运用控制,并将生物去碳过程中转化而产生及原废水中存在的氨氮转化为氮气而从废水中脱除的过程。
在废水的生物脱氮处理过程中,首先在好氧(oxic)条件下,通过好氧硝化的作用,将废水中的氨氮氧化为亚硝酸盐氮;然后在缺氧(Anoxic)条件下,利用反硝化菌(脱氮菌)将亚硝酸盐和硝酸盐还原为氮气(N2)而从废水中逸出。
焦炉工艺计算参考(下)

5.2.3 焦炉蓄热室计算蓄热室计算的目的是求出格子砖的高度,从而进一步确定蓄热室的高度。
应该按热交换量最大的蓄热室进行计算,所以一般选焦侧煤气蓄热室来计算格子砖高度。
运算时先列出有关的原始数据,然后通过蓄热室热平衡计算,确定预热空气或高炉煤气的温度,以及蓄热室的热交换量,再按下列方法算出热交换系数p K 。
(1) 对传热系数K α的计算K α=T 0.25(0.9617+0.60.2125V d) (5.26)式中:K α——对流传热系数,kcal/m 2·h·℃;V 0——换算成标准状态下湿气体的流速,m/s ; d ——格子砖的水力直径,m (2) 辐射给热系数F α的计算 先求出辐射层厚度CC=Pd (5.27)式中:P ——三原子气体CO 2或H 2O 的体积百分数; d ——格子砖水力直径,m 。
按求得的2CO C 和2H O C 值,查《焦化设计参考资料》附录十六,分别查表得辐射给热系数2CO F α和2H OF α,kcal/m 2·h·℃。
再将此两项相加,得F α。
将K α与F α之和乘以气流通过蓄热室的不均匀系数(一般为0.7~0.8)即得总传热系数,再根据加热期和冷却期的总传热系数(查《焦化设计参考资料》附录十七),确定总热交换系数p K 。
然后算出格子砖上、下部气体温差的对数平均温度,最后按下式求出换热面积F :F=JP QTK t∆ (5.28) 式中:F ——换热面积,m 2;Q ——预热高炉煤气或空气净得的热量,kcal/min ;J P K ——格子砖的平均总热交换系数,kcal/m 2·周期·℃;T ——一个换向周期的持续时间,一般为20min ; ∆t —格子砖顶部与底部的气体对数平均温度,℃ 根据一层格子砖的蓄热面积,可以确定格子砖的高度。
(3) 原始数据表5.12 原始数据名称单位数量 备注炭化室有效容积m 3 42.3炭化室一次装入干煤量:38.5×0.8 t 40.19 干煤堆积重度:0.95t/ m 3 1Kg 干煤相当耗热量 Kcal/ Kg 728干高炉煤气的发热量 Kcal/ m 3938查《焦化设计参考资料》附录十二 湿高炉煤气组成,%:CO 2O 2COH 2CH 4N 2 H 2O10.52 0.29 26.78 2.58 0.19 55.24.36每一煤气燃烧室所需的干高炉煤气量: 40.19100065724938⨯⨯⨯m 3/h1300通过一个煤气蓄热室的高炉煤气量: m 3/h高炉煤气30℃时含饱和水汽量4.36% 干煤气 1300×2 2600 湿煤气 1300×2÷0.95642719 通过一个焦侧煤气蓄热室的高炉煤气量: m 3/min焦、机侧煤气分配比为: 1.09干煤气⨯⨯2600 1.0960(1+1.09)22.60 湿煤气 22.60÷0.956422.63当α=1.25时,1m 3干高炉煤气所产生的湿废气量m 3 1.824 查《焦化设计参考资料》附录十二当α=1.25时,1m 3干高炉煤气燃烧所需的湿空气量m 3 0.933 查《焦化设计参考资料》附录十二 当α=1.25时,焦侧一对煤气、空气蓄热室通过的湿废气量 22.60×1.824 m 3/min41.22废气通过煤气与空气蓄热室的分配比:22.630.3621080-22.630.3239022.600.933(0.3411080-0.31290)⨯⨯⨯⨯⨯⨯⨯1.19查《焦化设计参考资料》附录十四煤气1080℃热容量为0.362空气1080℃热容量为0.341煤气90℃热容量为0.323空气90℃热容量为0.312当α=1.25时,通过焦侧一个煤气蓄热室的湿废气量41.22×1.19÷2.192m3/min 21.96当α=1.25时,湿废气组成,%:CO2 H2O2 N221.49 4.8 2.12 71.59360℃时,湿废气热容量(α=1.25)Kcal/ m3·℃0.349 查《焦化设计参考资料》附录十四1300℃时,湿废气热容量(α=1.25)Kcal/ m3·℃0.3915 查《焦化设计参考资料》附录十四本设计采用12孔格子砖,其参数如下[17]:①一块格子砖的蓄热面积F=0.4930 m2②焦侧一层格子砖的蓄热面积F=31.544 m2(其中包括60块格子砖的蓄热面积及相应高度的蓄热室墙面积)③焦侧蓄热室一层格子砖的总空隙面积F K=1.614 m2④焦侧蓄热室一层格子砖的总周边长度L=272.314 m⑤格子砖的水力直径d=0.0237 m(4)煤气蓄热室的热平衡1)带入热量①废气带入的显热(Q1)Q1=1300×0.3915×21.96=11177 kcal/min②高炉煤气带入的显热(Q2)Q2=90×0.323×22.63=658 kcal/min③进入总热量(Q a)Q a= Q1+ Q2=11177+658=11835 kcal/min2)带出热量①废气带出热量(Q3)Q3=360×0.349×21.96=2760 kcal/min②蓄热室墙面对周围环境的散热(Q4)取散热系数K=0.005Q 4= KQ a =0.005×11835=60 kcal/min ③ 总带出热量(Q b )Q b = Q 3+ Q 4=2760+60=2820 kcal/min 3) 煤气预热所得热量(Q 5)Q 5=Q a ―Q b =11835―2820=9015 kcal/min 4) 高炉煤气预热后温度 t=⨯预热煤气所得所得热量湿煤气量预热后温度下的煤气热容量901522.630.362=⨯≈1080 ℃(5) 热交换系数K P 的计算 用下式计算对流传热系数αK =T 0.25(0.9617+00.60.2125V d) (5.29) 1) 蓄热室加热期的对流传热系数① 蓄热室上部:格子砖温度 t G =1235℃;废气温度 t F =1300℃; 平均温度:t J =(t G + t F )/2=1267.5℃;t J =1540.5 KV 0=21.9660 1.614⨯=0.227m 3/s1S K α=T 0.25(0.9617+00.60.2125V d )=1540.50.25×(0.9617+0.60.21250.2270.0237⨯)=8.88kcal/m 2·h·℃ ② 蓄热室中部G t ,=975℃;F t ,=1035℃; J t ,=1005℃;J T ,=1278K1Z K α= T 0.25(0.9617+00.60.2125V d )=12780.25×(0.9617+0.60.21250.2270.0237⨯) =8.47kcal/m 2·h·℃ ③ 蓄热室下部G t ”=310℃;F t ”=360℃; J t ”=335℃;J T ”=608K1X K α= T0.25(0.9617+00.60.2125V d )=6080.25×(0.9617+0.60.21250.2270.0237⨯) =7.04 kcal/m 2·h·℃2) 蓄热室加热期的辐射给热系数① 蓄热室上部C CO2=Pd=21.49×0.0237/100=0.00509 m C H2O =Pd=4.8×0.0237/100=0.00114 m辐射介质温度:G t =1235℃ F t =1300℃,查《焦化设计参考资料》附录十六得,21CO F α=8.4 kcal/m 2·h·℃ O H F 21α=1.2 kcal/m 2·h·℃ 1S F α=21CO F α+O H F21α=8.4+1.2=9.6 kcal/m 2·h·℃ ② 蓄热室中部辐射介质温度:G t ,=975℃ F t ,=1035℃,查《焦化设计参考资料》附录十六得,21CO F α=6.3 kcal/m 2·h·℃ O H F 21α=0.75 kcal/m 2·h·℃ 1Z F α=21CO Fα+O H F 21α=6.3+0.75=7.05 kcal/m 2·h·℃ ③ 蓄热室下部辐射介质温度:G t ”=310℃ F t ”=360℃,查《焦化设计参考资料》附录十六得,21CO F α=1.495 kcal/m 2·h·℃ O H F 21α=0.25 kcal/m 2·h·℃ 1X F α=21CO F α+O H F 21α=1. 495+0.25=1.745 kcal/m 2·h·℃ 3) 加热期的总传热系数上部:1S α=0.75(1S K α+1S F α)=0.75×(8.88+9.6)=13.86 kcal/m 2·h·℃ 中部:1Z α=0.75(1Z K α+1Z F α)=0.75×(8.47+7.05)=11.64 kcal/m 2·h·℃下部:1X α=0.75(1X K α+1X F α)=0.75×(7.04+1.745)=6.59 kcal/m 2·h·℃ 上三式中0.75为校正系数;反映了气体通过蓄热室时分布的不均匀程度。
工艺计算之塔径设计

.2.3塔的设计1、塔径的初选查有机液体的相对密度共线图可得,85.73℃时乙醇的密度ρ乙醇=738kg/m 3,水的密度ρ水=968.1kg/m 3进料料液与塔顶气体的平均温度t=(85.73+78.29)÷2=82℃,查乙醇—水平衡数据可知:82℃时,乙醇—水的平均摩尔分率为x=0.2857,y=0.5672 计算得:乙醇—水的平均质量分率为w 乙醇=0.51,w 水=0.49又查得82℃时乙醇的密度ρ乙醇=735kg/m 3,水的密度ρ水=970.5kg/m 3气体平均的摩尔质量Mv=46.07×0.5672+18.02×(1-0.5672)=33.93kg/kmol 液体平均的摩尔质量M L =46×0.2857+18×(1-0.2857)=26.03kg/kmol 混合液的平均密度ρL =735×0.51+970.5×0.49=850.395 kg/m 3 由PV=nRT 可知ρ=PM/RT ,带入数据可得: 气体的平均密度ρv =PM/RT=1.163 kg/m3气体的平均质量流量 Wv=V G M V =121.52×33.93=4123.2kg/h 液体的平均质量流量 W L =V L M L =91.14×26.03=2372.4kg/h液体平均体积流量32.790s LLhWmL ρ==气体平均体积流量33545.31s h m V =两相流动参数0.5(/)LLV V L V W F W ρρ=⨯ =0.0213设H T =0.45m , 查筛此时200.083f C =则液泛流速5..02..020]/)[()20/(V V L f f C u ρρρσ-==2.196(其中σ取18mN/m)取泛点百分率为0.8,可求出设计气速u h 和所需气体流通面积A nu h =0.8×2.196=1.757m/s V s=3600VW v ρ =0.985m 3/s A n =V S / u h =0.560 m 2按表10-2选择单流型塔板,并取堰长lw=0.7D,由图10-40查得溢流管面积和塔板总面积之比:088.0)(=-=Tn T Tf A A A A A ,0.61510.088T A n A ==-m 2D=(4A T /π)0.5 =0.89m 根据设备系统化规格,将D 圆整到D=1.0m,作为初选塔径,对此初选塔径可以标出:A T=πD 3/4=0.785m 2降液管的面积 A f =0.088A T =0.088×0.785=0.0691m 2 A n = A T -A f =0.785-0.0691=0.7159 m 2实际气速u h = V S / A n =1.376m/s实际堰长lw=0.7D=0. 7m实际液泛百分率u h /u f =1.376/2.196=0.790 2、塔板详细设计:选择平流溢流堰,并参考表10-3取堰高hw=0.04m ,采用垂直弓形降液管和平型受液盘,取h o =0.03m,取Ws=Ws’=0.05m(其取值范围为0.025~0.05m),并从图10-40求出弓形降液管的宽度Wd=0.145D=0.145m,于是可以标出:/2()x D W d W s =-+=0.305m r=D/2-W c =0.47m带入10-23式可得,220.521212[()(/)]0.530180A a x r x r Sin x r m π⋅=-+=鼓泡型操作的筛板塔其筛孔直径d o 在3~8mm ,t/ d o 在一般情况下在2.5~5,取d o =5mm, t/d o =3故其开孔率ψ=0.907(d o / t)2=0.101A o = A a ψ=0.530×0.101=0.054m22.4塔板的校核1、板压降的校核取板厚δ=3mm, δ/d o =3/5=0.6,φ=A o /(A T -2A f )=0.1058 m 2由图10-45查出,并用试插法计算得Co=0.75,由式10-4可求出干板压降(以液柱表示)2(1/2)(/)(/)0.034d v L o oh g U C m ρρ== 由式10-34可求出堰上液高:3/23)/(1084.2hw h owl l E ⨯=(式中的修正系数E 可由图10-48求出)=2.84×103×1.02×(2.79/0.7)2/3=0.00728m按面积(A T -2A f )计算的气体速度0.985 1.523/(2)0.78520.0691a T fVs u m s A A ===--⨯ 相应气体的动能因子0.50.51.523 1.163 1.639a v Fa u ρ=⨯=⨯=由图10-46查得液层充气系数β=0.59,由式10-31求出液层阻力(以液柱表示)()0.59(0.040.00728)0L w o wh h h m β=+=⨯+=板压降:h f =h d +h L =0.034+0.0279=0.0619m2、液沫夹带量的校核按LV F =0.0213和泛点百分率为0.8,从图10-47查得ψ=0.13,由式10-6求得: 0.0860.11s L v s VL e m V ρρψ=∙==<-ψ3、溢流液泛条件的校核溢流管中的当量清液高度可由式10-8计算,已知:hw=0.04m ,h ow =0.00728m,△=0, h f =0.0619m ∑h f =0.153(Ls/L w h o )2 =0.000208m故降液管的当量清液高度 0.109d w o w ff H h h hh m=++∆++=∑ 乙醇-水的混合物不易起泡,取Φ=0.6,降液管内气沫层的高度/0.109/0.60.1820f dd HH m =Φ==< 所以不会发生溢流液泛。
- 1、下载文档前请自行甄别文档内容的完整性,平台不提供额外的编辑、内容补充、找答案等附加服务。
- 2、"仅部分预览"的文档,不可在线预览部分如存在完整性等问题,可反馈申请退款(可完整预览的文档不适用该条件!)。
- 3、如文档侵犯您的权益,请联系客服反馈,我们会尽快为您处理(人工客服工作时间:9:00-18:30)。
A1/O 生物脱氮工艺一、设计资料设计处理能力为日处理废水量为 30000m3废水水质如下:PH 值 7.0~7.5 水温14~25°C BOD5=160mg/L VSS=126mg/L(VSS/TSS=0.7) TN=40mg/LNH3-N=30mg/L根据要求:出水水质如下:BOD5=20mg/L TSS=20mg/L TN 15mg/L NH3-N 8mg/L根据环保部门要求,废水处理站投产运行后排废水应达到国家标准《污水综合排放标准》GB8978-1996中规定的“二级现有”标准,即 COD 120mg/l BOD 30 mg/l NH -N<20 mg/lPH=6-9 SS<30 mg/l二、污水处理工艺方案的确定城市污水用沉淀法处理一般只能去除约 25~30 %的BOD5,污水中的胶体和溶解性有机物不能利用沉淀方法去除,化学方法由于药剂费用很高而且化学混凝去除溶解性有机物的效果不好而不宜采用。
采用生物处理法是去除废水中有机物的最经济最有效的选择。
废水中的氮一般以有机氮、氨氮、亚硝酸盐氮和硝酸盐氮等四种形态存在。
生活污水中氮的主要存在形态是有机氮和氨氮。
其中有机氮占生活污水含氮量的40%~60%,氨氮占50%~60%,亚硝酸盐氮和硝酸盐氮仅占 0%~5%。
废水生物脱氮的基本原理是在传统二级生物处理中,将有机氮转化为氨氮的基础上,通过硝化和反硝化菌的作用,将氨氮通过硝化转化为亚硝态氮、硝态氮,再通过反硝化作用将硝态氮转化为氮气,而达到从废水中脱氮的目的。
废水的生物脱氮处理过程,实际上是将氮在自然界中循环的基本原理应用与废水生物处理,并借助于不同微生物的共同协调作用以及合理的认为运用控制,并将生物去碳过程中转化而产生及原废水中存在的氨氮转化为氮气而从废水中脱除的过程。
在废水的生物脱氮处理过程中,首先在好氧(oxic)条件下,通过好氧硝化的作用,将废水中的氨氮氧化为亚硝酸盐氮;然后在缺氧(Anoxic)条件下,利用反硝化菌(脱氮菌)将亚硝酸盐和硝酸盐还原为氮气(N2)而从废水中逸出。
因而,废水的生物脱氮通常包括氨氮的硝化和亚硝酸盐氮及硝酸盐氮的反硝化两个阶段,只有当废水中的氨以亚硝酸盐氮和硝酸盐的形态存在时,仅需反硝化(脱氮)一个阶段 .♦与传统的生物脱氮工艺相比,A/O脱氮工艺则有流程简短、工程造价低的优点。
该工艺与传统生物脱氮工艺相比的主要特点如下:①流程简单,构筑物少,大大节省了基建费用;②在原污水 C/N 较高(大于 4)时,不需外加碳源,以原污水中的有机物为碳源,保证了充分的反硝化,降低了运行费用;③好养池设在缺养之后,可使反硝化残留的有机物得到进一步去除,提高出水水质;④缺养池在好养池之前,一方面由于反硝化消耗了一部分碳源有机物,可减轻好养池的有机负荷,另一方面,也可以起到生物选择器的作用,有利于控制污泥膨胀;同时,反硝化过程产生的碱度也可以补偿部分硝化过程对碱度的消耗;⑤该工艺在低污泥负荷、长泥龄条件下运行,因此系统剩余污泥量少,有一定稳定性;⑥便于在常规活性污泥法基础上改造 A1/O 脱氮工艺;⑦混合液回流比的大小,直接影响系统的脱氮率,一般混合液回流比取200%~500%,太高则动力消耗太大。
因此 A1/O 工艺脱氮率一般为 70%~80%,难于进一步提高。
三、污水处理工艺设计计算(一)、污水处理系统1、格栅设计流量:平均日流量 Qd=3000m3/d=0.35m3/s则 K2=1.42最大日流量 Qmax=K2Qd=0.50m3/s设计参数:格栅倾角 =60 栅条间隙 b=0.021m 栅条水深 h=0.4m 过栅流速 v=0.9m/s (1)栅槽宽度①栅条的间隙数 n 格栅设两组,按两组同时工作设计,一格停用,一格工作校核。
则 n= = =31 个②栅槽宽度 B 栅槽宽度一般比格栅宽0.2~0.3m取0.2m 设栅条宽度 S=10mm(0.01m)则栅槽宽度 B=S(n-1)+bn+0.2=0.01 (31-1)+0.021 31+0.2=1.15m(2) 通过格栅的水头损失 h1①进水渠道渐宽部分的L1。
设进水渠宽B仁0.85m其渐宽部分展开角进水1=20 渠道内的流速为 0.77m/sL1= = =0.41m②栅槽与出水渠道连接出的渐窄部分长宽L2,mL2= = =0.21m③通过格栅的水头损失 h1,mh1=h0k(k 一般采用 3)h0= sin , =h1= sin k=2.42 si n60 3=0.097m 设=2.42)( 3)栅后槽总高度 H ,m 设栅前渠道超高 h2=0.3m( 4)栅槽总长度 L1,m(式中 H1=h+h2 )(5)每日栅渣量 W, m/3dw= 式中, w1 为栅渣量 m3/10 m 污水,格栅间隙为 16~25mm 时w1=0.10~0.05m /10 m3 污水;格栅间隙为 30~50mm 时,w1=0.03~0.1m3/103m3污水本工程格栅间隙为21mm取W1=0.07m3/10m3污水W= =2.18(m3/d) 0.2(m3/d)采用机械清渣2、提升泵站采用A1/O 生物脱氮工艺方案,污水处理系统简单,污水只考虑一次提升。
污水经提升后入平流式沉砂池,然后自流通过缺养池、好养池、二沉池等。
设计流量Qmax=1800m3/h,采用3台螺旋泵,单台提升流量为900m3/h。
其中两台正常工作, 一台备用。
3.平流式沉池砂(1)沉沙池长度 L, mL=vt ( 取 v=0.25m/s,t=30s)则 L=0.25 30=7.5m(2) 水流端面面积 A, m2A= = =2m2(3) 池总宽度 B, mB=nb ( 取 n=2, b=0.6m)则 B=2 0.6=1.2m(4) 有效水深 h2, mh2= = =1.7m(5) 沉砂池容积 v, m3V=(取 x=30m3/106m3 污水,T=2d k2=1.42)则 V= =1.83m3(6) 每个沉斗砂容积 V0,m3设每个分格有 2 个沉沙斗,共 4 个沉砂斗则 V0= =0.46m3(7) 沉砂斗尺寸①沉砂斗上口宽 a,ma= +a1 (式中h/3为斗高取h/3=0.35m, al为斗底宽取,a仁0.5m,斗壁与水平面的倾角 55 ) 则 a= +0.5=1.0m②沉砂斗容积 V0,m3V0=h/3(2a2+2aa1+2a12)= (2 12 2 1 0.5 +2 0.5)2 =0.2m3(8) 沉砂室高度 h3 ,m采用重力排沙,设池底坡度为0.06,坡向砂斗,沉砂室有两部分组成:一部分为沉砂斗,另一部分为沉砂池坡向沉砂斗的过滤部分,沉砂室的宽度为2(L2+a) +0.2L2= = =2.65mh3=h/3+0.06 L2=0.35+0.06 2.65=0.51m(9) 沉砂池总高度 H,m取超高 h1=0.3mH=h1+h2+h3=0.3+1.7+0.51=2.51m(10) 验算最小流速 Vmin m/s在最小流速时,只用一格工作( n1=1 )Vmin= Qmin= = =0.25m3/s则 Vmin= = =0.25m/s > 0.15m/s(11) 砂水分离器的选择沉砂池的沉砂经排砂装置排除的同时,往往是砂水混合体,为进一步分离出砂和水,需配套砂水分离器清除沉砂的间隔时间为2d,根据该工程的排砂量,选用一台某公司生产的螺旋水分离器。
该设备的主要技术性能参数为:进水砂水分离器的流量为1〜3L/S,容积为0.6m3,进水管直径为100mm,出水管直径为100mm,配套功率为0.25KW4、A1/O 生物脱氮工艺设计计算(1)好氧区容积 V1V1= (取 Y=0.6;Kd=0.05)①出水溶解性BOD5。
为使出水所含BOD5降到20mg/L ,出水溶解性BOD5浓度S应为:S=20- 1.42 X X TSS(1—kt)=20 - 1.42 X 0.7 X 20 —e—0.23 X 5)=6.41(mg/L)-15)][ ][ ][1-0.0833(7.2-Ph)]—15) X=0.462 X 0.958 X 0.606=0.247(d —硝化反应所需的最小污泥龄= = =4 。
05(d)选用安全系数 K=3 ;设计污泥龄 =K =3 X 4.05=12.2(d)③好氧区容积 V1 ,m3V1= =7482.38(m3)⑵好氧区容积 V2V2=NW:①需还原的硝酸盐氮量。
微生物同化作用去除的总氮NW=0.124 =0.124 X =7.2(mg/L)被氧化的 NH3-N= 进水总氮量—出水氨氮量—用与合成的总氮量 =40— 8— 7.2=24.8(mg/L) 需还原的硝酸盐氮 NT=30000 X 17.8 x =534(kg/d)②反硝化速率 qdn.T=qdn,20 ( qdn20取 0.12kgNO -N/(kgMLVSS • d);取 1.0& )qdn.T=0.12X 1.0814 2-0=0.076(kgNO -N/(kgMLVSS)③缺氧区容积V2= =2509.4(m3)缺氧区水力停留时间t2= = =0.084(d)=2.0(h)⑶曝气池总容积 V 总, m3V 总=V1+V2=7482.32+2509.4=9991.78m3系统总设计泥龄 =好氧池泥龄 +缺氧池泥龄 =12.2+12.2 X =16.29d ⑷污泥回流比及混合液回流比① 污泥回流比R。
设SVI=150,回流污泥浓度计算公式:XR= 册(r2)XR= X 1.2=8000mg/L混合液悬浮固体浓度 X(MLSS)=4000mg/L污泥回流比 R= X 100 % = X 100=和0%(—般取 50% ~100%)②混合液回流比 R 内。
混合液回流比 R 内取决与所要求的脱氮率。
脱氮率可用下式粗略估算:===62.5 %r= = =167 %〜200 %⑸剩余污泥量生物污泥产量:PX= = =1523.73kg/d对存在的惰性物质和沉淀池的固体流失量可采用下式计算:PS=Q( X1 - Xe)(Q 取 30000m3/d)Ps=Q(X1-Xe)=30000 X (0.180.1-26-0.02)=1020kg/d剩余污泥量△X=PX+PS=1523.73+1020=2543.73kg/d去除每1kgBOD5产生的干泥量===0.61kgDs/kgBOD5⑹反应池主要尺寸①好氧反应池。
总容积 V仁7482。
38m3设反应池2组。
单组池容 V1 单= = =3741.19m3有效水深h=4.0m,单组有效面积S1单===935.30m3采用3廊道式,廊道宽b=6m,反应池长度L1= = =52m超高取 1.0,则反应池总高 H=4.0+1.0=5.0m② 缺氧反应池尺寸总容积 V2=2509.4m3设缺氧池 2 组,单组池容 V2 单= =1254.7m3有效水深h=4.1m,单组有效面积S2单===306.02m长度与好氧池宽度相同,为 L=18m,池宽===17m⑺反应池进,出水计算① 进水管。