挤出成型工艺流程
结构陶瓷挤出成型工艺流程

结构陶瓷挤出成型工艺流程
结构陶瓷挤出成型是一种常用的工艺流程,其具有成本低、成型精度高、工艺适应性强等优点。
下面我们来了解一下结构陶瓷挤出成型的具体工艺流程。
1.原材料配制:首先要将原材料进行配制,根据产品的要求精确称取各种原材料,并进行混合搅拌,以得到均匀的料浆。
2.料浆挤出:将混合好的料浆注入挤出机中,通过挤出机的旋转螺杆将料浆挤出成型,并通过模具进行成型。
3.切割成型:将挤出成型的陶瓷经过切割、切断和折弯等工序,以得到所需的形状和尺寸。
4.干燥:将制成的陶瓷放入炉中进行干燥,以去除水分,达到陶瓷结构的稳定。
5.烧结:将干燥后的陶瓷进行烧结处理,以使其产生一定的结晶,提高其硬度和密度,并使其具有良好的化学稳定性和耐高温性能。
6.表面处理:根据产品要求进行表面处理,如涂覆釉料、喷涂等。
7.质量检验:对成品进行全面的质量检验,确保其符合产品要求,并进行包装和运输。
以上就是结构陶瓷挤出成型的工艺流程,需要注意的是,在生产过程中要严格控制各个环节的质量和工艺,以保证成品的质量和稳定性。
- 1 -。
hdpe挤出成型工艺流程详解

hdpe挤出成型工艺流程详解英文回答:High-Density Polyethylene (HDPE) Extrusion Process.High-density polyethylene (HDPE) extrusion is a manufacturing process that converts HDPE plastic into various products. The process involves melting the plastic and forcing it through a die to create the desired shape. HDPE extrusion is commonly used to produce pipes, bottles, sheets, and films.Process Flow.The HDPE extrusion process typically involves the following steps:1. Raw Material Preparation: HDPE pellets are heated toa specific temperature to make them pliable.2. Extruder: The heated pellets are fed into an extruder, which is a machine that melts and pressurizes the plastic.3. Die: The molten plastic is forced through a die that gives it the desired shape.4. Cooling: The extruded product is cooled using air or water to solidify it.5. Finishing: The finished product may undergo additional processing, such as cutting, printing, or coating.HDPE Extrusion Equipment.The key equipment used in HDPE extrusion includes:Extruder.Die.Cooling system.Haul-off unit.Cutter.Advantages of HDPE Extrusion.HDPE extrusion offers several advantages:Versatility: HDPE can be extruded into a wide range of shapes and sizes.High Strength and Durability: HDPE products are known for their strength and resistance to chemicals and abrasion.Low Cost: HDPE extrusion is a relatively low-cost manufacturing process.Recyclability: HDPE is recyclable, making it an environmentally friendly option.Applications of HDPE Extrusion.HDPE extrusion products are used in various applications, including:Pipes for water supply, drainage, and gas distribution.Bottles and containers for liquids and food.Sheets and films for packaging, construction, and agriculture.Automotive parts.Toys.中文回答:高密度聚乙烯 (HDPE) 挤出成型工艺流程。
挤出成型类型与工艺流程

主要输送各种流体,以及用作电线套管等。硬聚氯乙烯管易切别、
焊接、钻接、加热可弯曲,因此安装使用非常方便。软聚氯乙烯
管是由聚氯乙烯树脂加入较大量增塑剂和一定量稳定剂,以及其
他助剂,经造粒后挤出成型制成。软聚氯乙烯管材具有优良的化
学稳定性,卓越的电绝缘性和良好的柔软性和着色性,此种管常
用来代替橡胶管,用以输送液体及腐蚀性介质,也用作电缆套管
(1)温度控制 如前所述,生产管材软硬品种不同其加工温 度不同.硬管比软管加工温度高10—20°C。原料状态不同 加工温度也不同,粒料比粉料加工温度高10°C左右。具体 的温度控制应根据具体配方确定。
挤出成型类型和工艺流程
聚氯乙烯管加工温度范围
挤出成型类型和工艺流程
(2)螺杆冷却 由于硬聚氯乙烯熔体粘度大,流动性差,为防 止螺杆因摩擦热过大而升温,引起螺杆粘料分解或使管材内壁 毛糙,必须降低螺杆温度,这样可使物料塑化好,管内表面光 亮,提高管材内外质量。螺杆温度一般控制在80一100 °C之 间,若温度过低反压力增加,产量大大下降,甚至会发生物料 挤不出来而损坏螺杆轴承的事故,因此,螺杆冷却应控制出水 温度不低于70一80 °C。冷却方法是在螺杆内部用通铜管的方 法进行水冷却 。
制
3.1 管材成型工艺
3.1.1 圆 管
塑料管材是塑料挤出成型的主要产品之一。塑料挤出管材就是将 粒状或粉状塑料原料从料斗加入挤出机,物料被加热成熔融的料流, 经螺杆旋转的推力使熔融料通过机头环形通道,形成管状物,经冷 却定型装置对成型的管材进行冷却定型即成为塑料管树。
可供生产管材的塑料原料有:聚乙烯、聚氯乙烯、聚丙烯、ABS、 聚酰胺、聚碳酸酯等。目前国内生产的塑料管材以聚乙烯、聚氯乙 烯、聚丙烯等材料为主。
挤出成型的原理和工艺流程
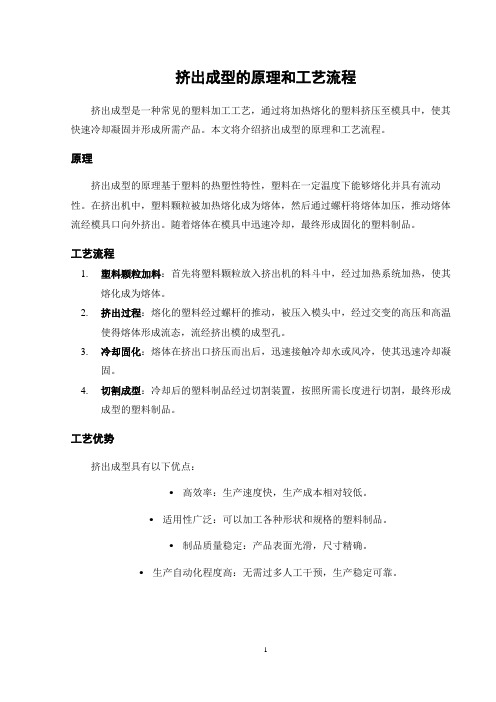
挤出成型的原理和工艺流程
挤出成型是一种常见的塑料加工工艺,通过将加热熔化的塑料挤压至模具中,使其快速冷却凝固并形成所需产品。
本文将介绍挤出成型的原理和工艺流程。
原理
挤出成型的原理基于塑料的热塑性特性,塑料在一定温度下能够熔化并具有流动性。
在挤出机中,塑料颗粒被加热熔化成为熔体,然后通过螺杆将熔体加压,推动熔体流经模具口向外挤出。
随着熔体在模具中迅速冷却,最终形成固化的塑料制品。
工艺流程
1.塑料颗粒加料:首先将塑料颗粒放入挤出机的料斗中,经过加热系统加热,使其
熔化成为熔体。
2.挤出过程:熔化的塑料经过螺杆的推动,被压入模头中,经过交变的高压和高温
使得熔体形成流态,流经挤出模的成型孔。
3.冷却固化:熔体在挤出口挤压而出后,迅速接触冷却水或风冷,使其迅速冷却凝
固。
4.切割成型:冷却后的塑料制品经过切割装置,按照所需长度进行切割,最终形成
成型的塑料制品。
工艺优势
挤出成型具有以下优点:
•高效率:生产速度快,生产成本相对较低。
•适用性广泛:可以加工各种形状和规格的塑料制品。
•制品质量稳定:产品表面光滑,尺寸精确。
•生产自动化程度高:无需过多人工干预,生产稳定可靠。
应用领域
挤出成型广泛应用于塑料制品生产行业,如管道、板材、型材、薄膜、包装材料等领域。
其高效率、高质量的特点使其成为塑料制品生产中不可或缺的一环。
总的来说,挤出成型作为一种常见的塑料加工工艺,通过简单高效的操作流程,可以生产出质量稳定的塑料制品,在工业生产中发挥着重要作用。
挤塑工艺流程
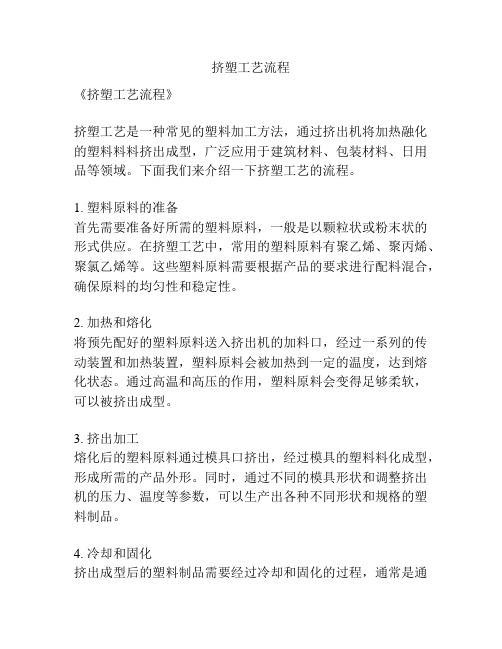
挤塑工艺流程
《挤塑工艺流程》
挤塑工艺是一种常见的塑料加工方法,通过挤出机将加热融化的塑料料料挤出成型,广泛应用于建筑材料、包装材料、日用品等领域。
下面我们来介绍一下挤塑工艺的流程。
1. 塑料原料的准备
首先需要准备好所需的塑料原料,一般是以颗粒状或粉末状的形式供应。
在挤塑工艺中,常用的塑料原料有聚乙烯、聚丙烯、聚氯乙烯等。
这些塑料原料需要根据产品的要求进行配料混合,确保原料的均匀性和稳定性。
2. 加热和熔化
将预先配好的塑料原料送入挤出机的加料口,经过一系列的传动装置和加热装置,塑料原料会被加热到一定的温度,达到熔化状态。
通过高温和高压的作用,塑料原料会变得足够柔软,可以被挤出成型。
3. 挤出加工
熔化后的塑料原料通过模具口挤出,经过模具的塑料料化成型,形成所需的产品外形。
同时,通过不同的模具形状和调整挤出机的压力、温度等参数,可以生产出各种不同形状和规格的塑料制品。
4. 冷却和固化
挤出成型后的塑料制品需要经过冷却和固化的过程,通常是通
过水浴或者风冷等方式进行。
冷却会使得塑料制品表面温度迅速下降,从而快速固化成型。
固化后的塑料制品就可以进行后续的加工、包装和使用了。
通过以上的流程,我们可以看到,挤塑工艺是一个相对简单且高效的塑料加工方法。
它能够快速、稳定地生产出各种规格、各种形状的塑料制品,满足不同行业的需求。
在工业生产中,挤塑工艺被广泛应用,并在不断地发展和改进之中。
塑料成型工艺第六章 挤出成型

c、物料全部熔融,变为粘流融的物料量逐渐减少,大约在压 缩段的结束处,全部物料熔融而转变为粘流态, 但这时各点的温度尚不很均匀。
3)均化段——均化、挤出 物料经过均化段的均化作用就比较均匀 了,最后螺杆将熔融物料定量、定压、定温地 挤入机头。 机头内的口模是个成型部件,物料通过它 便获得一定截面的几何形状和尺寸。
固体输送区:固体状态 熔融区:两相共存 熔体输送区:全部为熔体 这几个区不一定完全和前面介绍过的螺杆 的加料段,压缩段,均化段相一致。
3.塑件的定型与冷却阶段
管材的定径方法:定径套、定径环、定径板
4.塑件的牵引、卷取和切割
在冷却得同时,连续均匀地将塑件引出。
牵引速度略大于挤出速度 不同的塑件,牵引速度不同。
挤出成型所需控制的温度是机筒温度、机颈 温度、口模温度。 机筒温度分布,从喂料区到模头可能是平坦分 布,递增分布,递减分布及混合分布。主要取决 于材料物点和挤出机的结构。
表6-2
常见管材成型温度(单位:℃)
口模设臵温度,口模和芯模的温度对管子表
面光洁度有影响,在一定的范围内,口模与芯
模温度高,管子表面光洁度高。通常来讲,口
3.混合效果差,不能很好适应一些特殊塑料的加 工或混炼、着色工艺过程。
排气式螺杆 主要适用于含水和易产生挥发组分的物料。 排气原理:物料到排气段基本塑化,由于该段 螺槽突然加深,压力骤降,气体从熔体中逸处, 从排气口排出。
分离型(屏障型)螺杆 原理:在螺杆熔融段再附加一条螺纹,将原来 一个螺纹所形成的螺槽分为两个,将已熔物料和 未熔物料尽早分离,促进未熔料尽快熔融。
加热冷却系统;
螺杆转数;
螺杆和料筒的结构
研究挤出过程的压力轮廓曲线对挤出过程的了解 和改进螺杆、料筒的设计有着重要意义。
挤出成型工艺

02 挤出成型设备
(1)主机: ·单螺杆挤出机
·双螺杆挤出机
02 挤出成型设备
(2)机头:机头的型孔(口模)决定制品断面的形状,不 同的制品可以更换
03 挤出成型工艺优、缺点
优点:1、能加工绝大多数热塑性复合材料及部分热固性复合材料; 2、生产过程连续,自动化程度高,生产效率高; 3、工艺易掌握及产品质量稳定等; 4、生产线占地面积小,且生产环境清洁。 缺点:只能生产线型制品。
原材料(FRTP粒料)
03
03 原材料
树脂
增强纤维
树脂:绝大部分热塑性塑料及部分热固性塑料, 如PVC、PS、ABS、PC、PE、PP、PA、环氧 树脂、酚醛树脂及丙烯酸树脂
增强纤维:玻璃纤维
长纤维:纤维长度等于粒料长度(3mm~13mm ) 树脂及助剂 增强粒料 增强纤维 短纤维 :纤维和树脂无规混合(0.25mm~0.5mm)
挤出成型工艺
组员:刘畅 郝均雨 陈兵
目录
CONTENTS
01 03
挤出成型原理
02 工艺流程、设备及优、缺点
原材料
04 主要应用
挤出成型原理
01
01 挤出成型原理
将塑料加热呈粘流状态,加 压使之通过口模,而成为截 面与口模形状相仿的连续体, 再通过冷却,使其具有一定
几何形状和尺寸的塑料由粘
流态变为高弹态,最后定型 为玻璃态,得到所需要的制 品。
纤维平行于粒料长度排列;
04
主要应用
04 主要应用 01 生产制备管材
04 主要应用 02 生产制备棒材
04 主要应用 03 生产制备异型断面型材
04 主要应用 04
其他应用(板材、塑料薄膜、打包带、网材等)
挤出成型工艺流程

挤出成型工艺流程引言挤出成型工艺是一种常见的塑料加工方法,广泛应用于工业生产中。
该工艺通过将预先加热的塑料料料挤压经过模具后形成希望的截面形状,可以制造出各种塑料制品。
本文将详细介绍挤出成型工艺的流程和步骤。
工艺流程概述挤出成型工艺流程主要包括以下几个步骤:原料准备、塑料熔融、挤出形成、冷却固化、切割成型。
下面将依次进行详细介绍。
1. 原料准备在挤出成型工艺中,首先需要选择适合的塑料原料。
常用的塑料原料包括聚乙烯(PE)、聚丙烯(PP)、聚氯乙烯(PVC)等。
根据所需制品的特性和用途要求,选择相应的原料。
接下来,将原料进行加工和准备,通常需要将塑料颗粒进行干燥处理,以确保原料的质量和性能。
2. 塑料熔融原料准备完成后,将原料投入到挤出机的料斗中。
挤出机通过加热和搅拌将塑料颗粒加热并融化成熔体。
在熔融过程中,需要控制好温度和压力,以确保塑料的熔融状态和流动性。
3. 挤出形成当塑料完全熔化后,熔体会从挤出机的机筒中被挤出,进入挤出头部。
挤出头部的形状会决定成品的截面形状,可以根据需要选择不同的挤出头。
在挤出头部,熔体会被压力挤压通过出模孔,形成希望的截面形状。
同时,还可以通过添加模头调整流道形状,实现更复杂的截面形状。
4. 冷却固化经过挤出头后,熔体将进入冷却系统。
冷却系统通常包括水冷却和气冷却两个部分。
通过冷却系统,塑料制品的温度会迅速降低,使其固化和硬化。
冷却时间的控制对成品的受力性能和尺寸稳定性非常重要。
5. 切割成型当塑料制品完全冷却固化后,通过切割设备将制品切割成所需长度。
根据不同的产品要求,可以选择不同的切割方式,如:剪切、锯切、切削等。
切割成型后的制品可以通过其他工艺进行表面处理、组装以及包装等。
工艺优化与控制挤出成型工艺流程中,需要注意一些关键参数的控制,以获得更好的成品质量和生产效率。
下面列举了一些常见的工艺优化和控制方法。
1. 控制挤出速度挤出速度是指单位时间内挤出的熔体量,对成形过程和成品质量均有影响。
第6章挤出成型工艺

第六章挤出成型工艺第一节热塑性塑料工艺特性(一)收缩率热塑性塑料加工成型中产生的热收缩产生原因:宏观:材料的热胀冷缩行为-微观:分子间自由体积发生变化。
通常高分子材料的热膨胀系数远大于金属材料、陶瓷材料。
影响热塑性塑料成形收缩的因素如下:第六章挤出成型工艺第六章挤出成型工艺1、塑料品种热塑性塑料成形过程中由于还存在结晶化形起的体积变化,内应力强,冻结在塑件内的残余应力大,分子取向性强等因素,因此与热固性塑料相比则收缩率较大,收缩率范围宽、方向性明显。
另外成形后的收缩、退火或调湿处理后的收缩一般也都比热固性塑料大。
第六章挤出成型工艺2、塑件特性成形时融料与型腔表面接触外层立即冷却形成低密度的固态外壳。
由于塑料的导热性差,使塑件内层缓慢冷却而形成收缩大的高密度固态层。
所以壁厚、冷却慢、高密度层厚的则收缩大。
另外,有无嵌件及嵌件布局,数量都直接影响物料流动方向,密度分布及收缩阻力大小等,所以塑件的特性对收缩大小,方向性影响较大。
第六章挤出成型工艺3、进料口形式、尺寸、分布这些因素直接影响物料流动方向、密度分布、及成形时间。
直接进料口、进料口截面大(尤其截面较厚的)则收缩小但方向性大,进料口宽及长度短的则方向性小。
距进料口近的或与物料流动方向平行的则收缩大。
4、成形条件模具温度高,融料冷却慢、密度高、收缩大,尤其对结晶料则因结晶度高,体积变化大,故收缩更大。
另外,保持压力及时间对收缩也影响较大,压力大、时间长的则收缩小但方向性大。
第六章挤出成型工艺(二)流动性1、热塑性塑料流动性大小,一般可从分子量大小、熔融指数、表现粘度及流动比(流程长度/塑件壁厚)等一系列指数进行分析。
分子量小,分子量分布宽,分子结构规整性差,熔融指数高、表现粘度小;流动比大的则流动性就好。
按模具设计要求我们大致可将常用塑料的流动性分为三类:第六章挤出成型工艺(1)流动性好:尼龙、聚乙烯、聚苯乙烯、聚丙烯、醋酸纤维素;(2)流动性中等改性:聚苯乙烯(例ABS·AS)、PMMA、聚甲醛、聚氯醚;(3)流动性差:聚碳酸酯、硬聚氯乙烯、聚苯醚、聚砜、聚芳砜、氟塑料。
abs挤出工艺

一、原理
ABS挤出工艺的原理是将ABS树脂加热至熔点,然后通过螺杆挤出机将熔融的ABS树脂从模具的挤出口挤出,最后冷却固化成型。整个过程中,螺杆挤出机起到了熔化、混合和挤出的作用,而模具则负责塑料的形状和尺寸。
3. 后处理:将挤出成型的ABS制品进行冷却固化,然后进行切割、修整和表面处理等工序,最终得到符合要求的ABS制品。
三、设备要求
ABS挤出工艺需要使用挤出机、模具和辅助设备等。其中,挤出机是核心设备,主要包括料斗、螺杆、加热和冷却系统等。模具是决定产品形状的关键部件,其设计和制造需要考虑产品的尺寸、结构和表面要求。辅助设备包括原料预处理设备、冷却设备和切割设备等。
ABS挤出工艺是一种常见且重要的塑料加工工艺。通过合理的工艺流程、设备要求和模具设计,可以实现ABS树脂的熔化、挤出和成型,最终得到符合要求的ABS制品。随着ABS材料在各个领域的应用不断扩大,ABS挤出工艺也将得到进一步的发展和应用。
四、应用领域
ABS挤出工艺广泛应用于电子电器、汽车、家具等行业。在电子电器领域,ABS挤出制品常用于电视机外壳、空调面板等;在汽车行业,ABS挤出制品常用于车身零部件、内饰件等;在家具行业,ABS挤出制品常用于家具配件、把手等。由于ABS材料具有良好的耐磨性、抗冲击性和耐化学性等特点,使其在各个领域都有着广泛的应用。
二、工艺流程
ABS挤出工艺的工艺流程主要包括原料预处理、挤出成型和后处理三个步骤。
1. 原料预处理:将ABS树脂经过粉碎、干燥等处理,保证原料的质量和流动性。
2. 挤出成型:首先将经过预处理的ABS树脂放入挤出机的料斗中,由螺杆挤出机进行加热和混合。当ABS树脂完全熔化并达到一定的温度后,通过模具的挤出口挤出,形成所需的产品形状。
挤出成型工艺流程
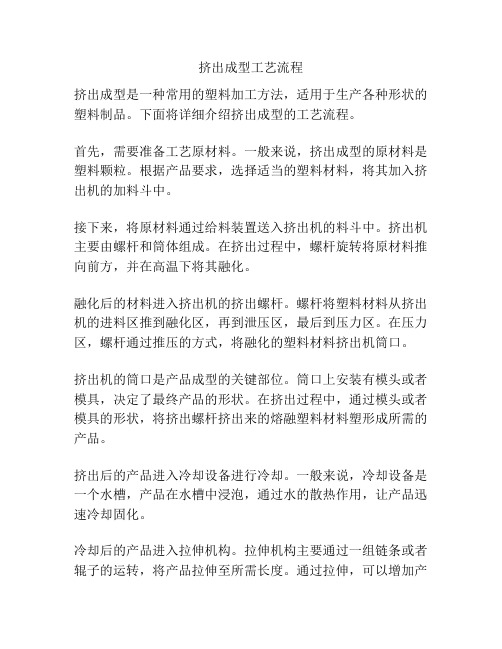
挤出成型工艺流程挤出成型是一种常用的塑料加工方法,适用于生产各种形状的塑料制品。
下面将详细介绍挤出成型的工艺流程。
首先,需要准备工艺原材料。
一般来说,挤出成型的原材料是塑料颗粒。
根据产品要求,选择适当的塑料材料,将其加入挤出机的加料斗中。
接下来,将原材料通过给料装置送入挤出机的料斗中。
挤出机主要由螺杆和筒体组成。
在挤出过程中,螺杆旋转将原材料推向前方,并在高温下将其融化。
融化后的材料进入挤出机的挤出螺杆。
螺杆将塑料材料从挤出机的进料区推到融化区,再到泄压区,最后到压力区。
在压力区,螺杆通过推压的方式,将融化的塑料材料挤出机筒口。
挤出机的筒口是产品成型的关键部位。
筒口上安装有模头或者模具,决定了最终产品的形状。
在挤出过程中,通过模头或者模具的形状,将挤出螺杆挤出来的熔融塑料材料塑形成所需的产品。
挤出后的产品进入冷却设备进行冷却。
一般来说,冷却设备是一个水槽,产品在水槽中浸泡,通过水的散热作用,让产品迅速冷却固化。
冷却后的产品进入拉伸机构。
拉伸机构主要通过一组链条或者辊子的运转,将产品拉伸至所需长度。
通过拉伸,可以增加产品的拉伸性能和物理性能。
最后,经过切割设备进行切割。
一般来说,切割设备采用刀片进行切割操作,将长条状的产品切割成所需要的长度。
切割后的产品经过处理,可用于包装和交付市场使用。
以上就是挤出成型的工艺流程。
通过挤出成型,可以制造出各种形状的塑料制品,如管道、片材、棒材等。
挤出成型是一种成本低、生产效率高的塑料加工方法,广泛应用于塑料制品领域。
随着科技的发展,挤出成型的技术也在不断创新,使得成型质量和产品性能得到了进一步提升。
图1: 挤出成型工艺流程图

3
挥其效能,减少促进剂用量,加快硫化反应速度,缩短硫化时间。 防焦剂:硫化延缓剂,其作用是防止或延缓胶料发生焦烧。 防老剂:延缓或抑制老化过程,从而延长橡胶及其制品的贮存期和使用寿命。 增塑剂:使生胶软化,增加胶料的可塑性,以便于成型加工,减少动力消耗;浸润炭黑等粉状配合剂,使其
易于在胶料中分散,缩短混炼时间,提高混炼效果;提高制品的柔软性和耐寒性;增进胶料的自粘性和粘性。 填充剂:可以分为补强填充剂和惰性填充剂两大类。惰性填充剂又称为增量剂、增容剂,对橡胶的补强效果
床。大部分熔融发生在相对长的压缩段中,需要减少槽深以改善熔融效率。计量段浅槽能合理地均化熔体,熔体 来自熔融区的部分熔态区域,能够给这些部分熔态区带来更均匀的温度。 2. 画出挤出成型工艺的流程图
见图 1。
图 1: 挤出成型工艺流程图
3. 注射机由哪几大部分组成? 这几大部分中,赋予制品一定形状与尺寸的工具称为什么? 主要由哪些部分组成, 各自包含哪些零件? 由注射系统、锁模系统、液压系统及注射模具等几部分组成。 利用本身特定形状,使塑料 (或聚合物) 成型为具有一定形状和尺寸的制品的工具称模具。 注射模具主要由浇注系统、成型零件和结构零件三大部分所组成;成型部件:成型部件是指构成型腔和制品
NPD 函数 Gk(t)
∑k Gk(t) = gj(t)
j=0
一个完整的混合物特征应该叙述为:次要组分的每个粒子、块或斑点的尺寸、形状、取向以及空间位置。三
维浓度分布函数可以提供一个稍不完整的特征。然而,对于许多应用,并不需要如此完整的混合物特征叙述;在
实践中,简单方法即可满足需求。例如,与标准样板进行颜色对比,以定性分析其均匀度,或测量某种典型的
生胶在常温下大多处于高弹态,生胶的这一宝贵性质却给制品的生产带来极大的困难,在加工过程中,各种 配合剂便无法在生胶中分散均匀,而大部分的机械能也会消耗在橡胶的弹性变形上。因此,为了满足各种成型加 工工艺的要求,必须使生胶由强韧的弹性状态变成柔软而具有可塑性的状态,这种增加橡胶可塑性的工艺过程 称为塑炼。
挤出成型工艺—管材挤出(塑料成型加工课件)
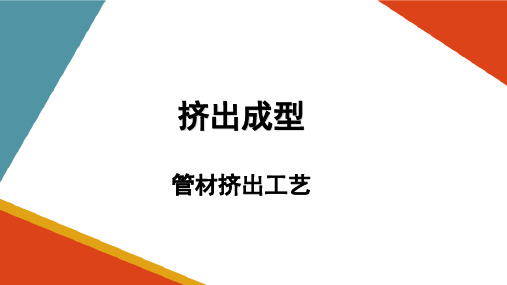
少到多,直至达到管材规格所需要的用量。
管材挤出时,在引入真空定型套(或其他形式的定型
4.定径牵引 套)及冷却器中,先校验其同心度,管材挤出口模后,若
不平直而向某一方偏斜,则易造成管壁厚度不均,应及时 矫正。
将矫正好的管材引入牵引机,牵引速度应该有慢到快 直至达到规定的速度。。
挤出成型
管材挤出工艺
一、管材挤出机组
二、工艺流程
以PVC管材挤出为例,工艺流程如图所示:
管材挤出的工艺流程还因原料和设备的不同略有差 别。原则上,几乎所有的热塑性塑料都可以用来挤出生 产管材,但常用的塑料是PVC、PE和PP。
三、操作规程
(1)根据管材要求,选择合适的机头(口模)安装好,包
1.开机准备 括分流器、模芯、口模、过滤版等。
(2)初步调整口模、模芯同心,并使机头、定径装置、牵 引装置、切割装置等装置中心一致。
2.预热
将料筒、机头和口模的温度调整到比正常挤出操作温 度高10~20摄氏度,口模出温度应该略低,以消除管材中的 气泡,防止挤出时管材因自重而下垂,而温度过低又将影 响挤出速度和制品的光泽。
待挤出机温度稳定后,缓慢调整转速,使物料熔融挤
其圆度、表面光泽度、颜色均一度等。
在刚开机到正常生产前的这一阶段,工艺参数要不断
5.工艺参数 调节,直至管材符合要求。需要调节的参数有:
调整
(1)挤出机温度
(2)冷却水温度
(3)螺杆转速
(4)牵引速度
பைடு நூலகம்
要在挤出机正常挤出管材的时候,注意牵引速度的适
中,及冷却装置的合理性。
将冷却牵引出来的管材引到切割装置,达到要求的长
挤出成型的工艺流程是

挤出成型的工艺流程是挤出成型是一种常见的塑料加工工艺,广泛应用于塑料制品的生产中。
它通过将加热融化的塑料料料在挤出机中加工成所需的截面形状,然后通过冷却使其成型固化。
挤出成型工艺流程主要包括原料准备、预处理、挤出、冷却和切割等步骤。
首先是原料准备。
生产挤出制品的第一步是准备好塑料原料,通常是将塑料颗粒放入挤出机的进料口。
在这一步,也可以根据产品要求添加颜色、添加剂等辅助材料,以满足产品的特殊需求。
接着是预处理阶段。
塑料颗粒通过进料口输入挤出机后,需要经过加热和熔化的过程。
此时,挤出机中的加热部件会将塑料颗粒加热至熔化温度,使其变成流动状,便于后续挤出成型。
在预处理阶段中,还会对塑料进行搅拌和混合,确保塑料的均匀性和稳定性。
挤出阶段是整个工艺流程的核心环节。
在挤出机中,加热熔化后的塑料通过螺杆的旋转运动被挤出模具,根据模具的设计和形状,挤出的塑料会在模具口形成所需的截面形状。
挤出速度、温度和压力等参数会对成品的质量产生重要影响,需要经过精确控制。
冷却是挤出制品成型后必不可少的步骤。
挤出出来的热塑料要迅速冷却并固化成型,以保证产品能够保持所需的形状和性能。
通常会采用水冷却或风冷却的方式,使挤出的塑料快速降温,从而完成形状的固化。
最后是切割环节。
成型后的挤出产品会持续从挤出口处延伸出来,形成连续的成型体。
在切割环节中,会根据产品的需要经过切割设备进行定长的截取,从而实现产品的最终成型。
切割的精准和准确度对于挤出制品的质量影响重大。
总的来说,挤出成型工艺是一种高效、经济的塑料加工方法,通过精确的控制步骤和参数,可以生产出各种塑料制品,广泛应用于建筑、包装、交通运输等多个领域。
熟练掌握挤出成型工艺流程,对于提高产品质量和生产效率具有重要意义。
1。
挤出机生产工艺流程
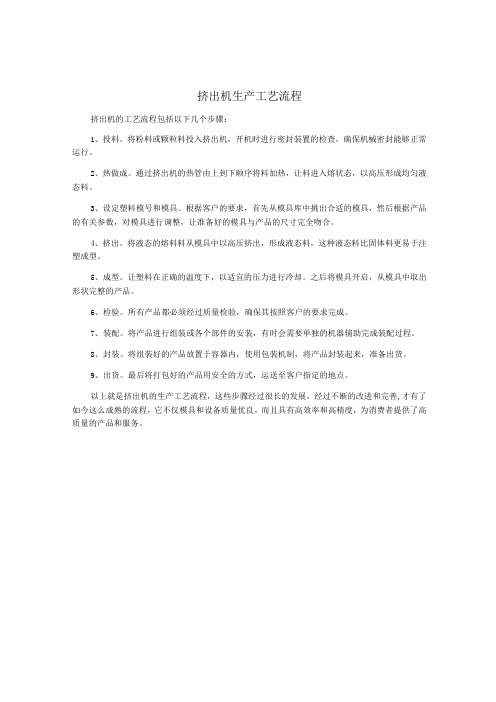
挤出机生产工艺流程
挤出机的工艺流程包括以下几个步骤:
1、投料。
将粉料或颗粒料投入挤出机,开机时进行密封装置的检查,确保机械密封能够正常运行。
2、热做成。
通过挤出机的热管由上到下顺序将料加热,让料进入熔状态,以高压形成均匀液态料。
3、设定塑料模号和模具。
根据客户的要求,首先从模具库中挑出合适的模具,然后根据产品的有关参数,对模具进行调整,让准备好的模具与产品的尺寸完全吻合。
4、挤出。
将液态的熔料料从模具中以高压挤出,形成液态料,这种液态料比固体料更易于注塑成型。
5、成型。
让塑料在正确的温度下,以适宜的压力进行冷却。
之后将模具开启,从模具中取出形状完整的产品。
6、检验。
所有产品都必须经过质量检验,确保其按照客户的要求完成。
7、装配。
将产品进行组装或各个部件的安装,有时会需要单独的机器辅助完成装配过程。
8、封装。
将组装好的产品放置于容器内,使用包装机制,将产品封装起来,准备出货。
9、出货。
最后将打包好的产品用安全的方式,运送至客户指定的地点。
以上就是挤出机的生产工艺流程,这些步骤经过很长的发展,经过不断的改进和完善,才有了如今这么成熟的流程,它不仅模具和设备质量优良,而且具有高效率和高精度,为消费者提供了高质量的产品和服务。
挤出成型工艺流程是什么
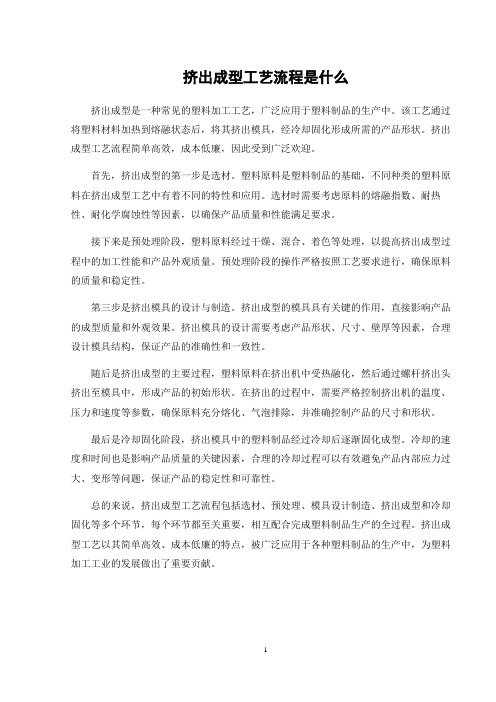
挤出成型工艺流程是什么挤出成型是一种常见的塑料加工工艺,广泛应用于塑料制品的生产中。
该工艺通过将塑料材料加热到熔融状态后,将其挤出模具,经冷却固化形成所需的产品形状。
挤出成型工艺流程简单高效,成本低廉,因此受到广泛欢迎。
首先,挤出成型的第一步是选材。
塑料原料是塑料制品的基础,不同种类的塑料原料在挤出成型工艺中有着不同的特性和应用。
选材时需要考虑原料的熔融指数、耐热性、耐化学腐蚀性等因素,以确保产品质量和性能满足要求。
接下来是预处理阶段,塑料原料经过干燥、混合、着色等处理,以提高挤出成型过程中的加工性能和产品外观质量。
预处理阶段的操作严格按照工艺要求进行,确保原料的质量和稳定性。
第三步是挤出模具的设计与制造。
挤出成型的模具具有关键的作用,直接影响产品的成型质量和外观效果。
挤出模具的设计需要考虑产品形状、尺寸、壁厚等因素,合理设计模具结构,保证产品的准确性和一致性。
随后是挤出成型的主要过程,塑料原料在挤出机中受热融化,然后通过螺杆挤出头挤出至模具中,形成产品的初始形状。
在挤出的过程中,需要严格控制挤出机的温度、压力和速度等参数,确保原料充分熔化、气泡排除,并准确控制产品的尺寸和形状。
最后是冷却固化阶段,挤出模具中的塑料制品经过冷却后逐渐固化成型。
冷却的速度和时间也是影响产品质量的关键因素,合理的冷却过程可以有效避免产品内部应力过大、变形等问题,保证产品的稳定性和可靠性。
总的来说,挤出成型工艺流程包括选材、预处理、模具设计制造、挤出成型和冷却固化等多个环节,每个环节都至关重要,相互配合完成塑料制品生产的全过程。
挤出成型工艺以其简单高效、成本低廉的特点,被广泛应用于各种塑料制品的生产中,为塑料加工工业的发展做出了重要贡献。
1。
挤出成型产品配方和工艺流程

挤出成型产品配方和工艺流程挤出成型是一种常见的制造工艺,在生产过程中可以生产各种形状和尺寸的产品。
本文将介绍挤出成型产品的配方和工艺流程,以帮助工厂提高生产效率和产品质量。
配方挤出成型产品的配方是制造过程中至关重要的一环。
一般来说,挤出成型产品的配方包括原材料、添加剂以及辅助剂三个主要部分。
原材料主要指的是基础材料,比如塑料颗粒、橡胶等;添加剂用于改善产品的性能,比如增强材料、阻燃剂等;辅助剂则用于调节产品的流动性、颜色等。
在确定配方时,需要考虑产品的用途、性能要求以及成本等因素。
合理的配方可以确保产品质量稳定,生产成本降低。
工艺流程挤出成型的工艺流程一般包括原料预处理、挤出成型和后处理三个主要阶段。
1.原料预处理: 在这个阶段,需要对原料进行预处理,包括原料混合、加热融化等。
确保原料的质量和均匀性对最终产品的质量至关重要。
同时,还需要根据产品要求添加相应的添加剂和辅助剂。
2.挤出成型: 在挤出机中,原料被加热至熔化状态后,通过螺杆将熔化的原料挤出成型。
挤出机的温度、挤压速度和压力等参数需要根据产品的要求进行调节,确保产品的成型质量和外观。
3.后处理: 成型后的产品需要经过冷却、切割、拉伸等后处理工艺。
通过这些步骤可以使产品的尺寸、外观等达到设计要求。
在整个工艺流程中,操作员需要不断监控和调节各道工序的参数,确保产品的质量稳定。
同时,定期对挤出机及相关设备进行维护保养,延长设备的使用寿命。
结语挤出成型产品的配方和工艺流程对产品的质量和生产效率具有重要影响。
通过优化配方和工艺流程,可以提高产品的品质,降低生产成本。
工厂在实际生产中应根据具体情况,不断改进和优化,提升企业竞争力。
注塑成型工艺流程

注塑成型工艺流程
熔融挤出成型工艺流程一般包括料斗进料、挤出、剥离、冷却、成型和收线六个步骤。
1、料斗进料:可以使用电动、气动或空压机,将加筋和颗粒料从料斗中输送到挤出
机中。
挤出器的口径大小,可根据需要调整。
2、挤出:将加入塑料的物料挤压至满足要求的厚度,从而形成塑料带。
3、剥离:挤出塑料带的两端形成的聚合物,由刀片直接截断所形成的挤出分层物料,并将剥离的物料送回混料中,进行熔融处理。
4、冷却:当塑料带冷却到可以加工的温度时,会通过喷射空气或涂散冷却水,从而
冷却塑料带,以便加工。
5、成型:塑料带经过冷却后,会按照图纸要求,通过切割压模机对塑料带进行压模,然后可得到成型品。
6、收线:塑料成型件将穿过收线辊拖着,以完成收线工艺。
收线的效率高,一次性
完成条、环形等形状的成型品收线,易于操作、快速收箱等功能。
2、预热:当颗粒料进入挤出机,首先被送入加热腔中进行预热,以熔断熔融合金属
颗粒。
3、熔融:熔融的加筋和颗粒料进入挤出口杆内,经过加热挤出头、分流器或定型腔后,进入挤出压力室内。
- 1、下载文档前请自行甄别文档内容的完整性,平台不提供额外的编辑、内容补充、找答案等附加服务。
- 2、"仅部分预览"的文档,不可在线预览部分如存在完整性等问题,可反馈申请退款(可完整预览的文档不适用该条件!)。
- 3、如文档侵犯您的权益,请联系客服反馈,我们会尽快为您处理(人工客服工作时间:9:00-18:30)。
挤出成型工艺流程
挤出成型工艺流程是一种常用的塑料加工方法,适用于生产各种形状的塑料制品。
以下是一篇关于挤出成型工艺流程的700
字的介绍。
挤出成型是将加热熔融的塑料通过挤压机挤压成具有一定断面形状的物体的加工方法,适用于生产线型、板型、片材、管材、棒材等各种塑料制品。
挤出成型工艺流程一般包括原料处理、挤出机挤出、模具设计、模具制造、成型制品加工等环节。
首先,是原料处理。
挤出成型的原料通常是塑料颗粒或粉末,经过称重、筛分、混合等处理,使其符合生产要求。
重量调节是为了保证挤出机正常工作,筛分是为了除去塑料中的杂质,混合则是为了使塑料均匀,提高加工质量。
接下来,是挤出机挤出。
挤出机是将加热熔融的塑料通过螺杆挤出成型的设备。
首先,将预先称好的塑料颗粒或粉末放入进料口,通过机械能将其加热熔化,然后由螺杆推进,经过一段时间和一定的压力,将塑料挤出机的机筒中。
挤出时需要控制好挤出速度、温度和压力等参数,以保证挤出成型的质量。
然后,是模具设计和制造。
挤出成型需要使用模具,模具通常由金属材料制成,根据要生产的产品形状和尺寸来设计制造。
模具一般包括进料口、螺纹道、冷却系统等。
进料口用于接受挤出机挤出的塑料,螺纹道用于将塑料引导到合适的流道中,冷却系统用于降低塑料的温度并保持形状。
最后,是成型制品加工。
成型制品是挤出成型的最终产品,根据需要,可以对其进行表面处理,如切割、修整、打孔、冷却等。
这些步骤需要根据产品的要求来进行操作,以确保成型制品的质量和形状。
总结起来,挤出成型是一种常用的塑料加工方法,其工艺流程主要包括原料处理、挤出机挤出、模具设计制造和成型制品加工等环节。
通过合理控制各个环节的参数和操作,可以得到质量稳定、形状规整的塑料制品。
挤出成型工艺的应用广泛,可以生产各种形状的塑料制品,满足不同领域的需求。