影响所需体积(THR体积模型)的锡膏相关因素
锡膏印刷最重要的因素
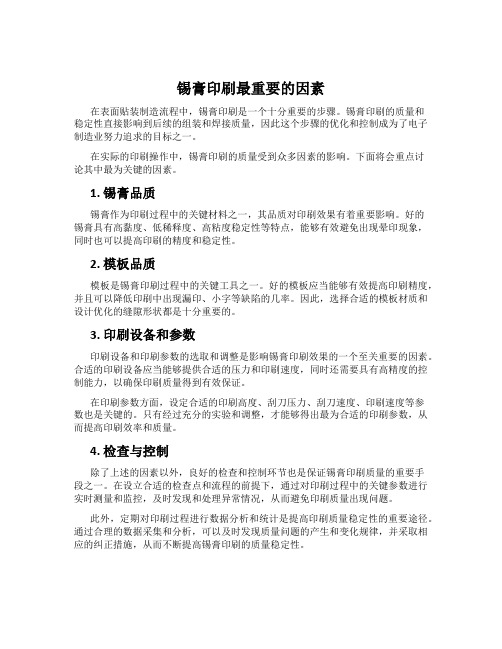
锡膏印刷最重要的因素在表面贴装制造流程中,锡膏印刷是一个十分重要的步骤。
锡膏印刷的质量和稳定性直接影响到后续的组装和焊接质量,因此这个步骤的优化和控制成为了电子制造业努力追求的目标之一。
在实际的印刷操作中,锡膏印刷的质量受到众多因素的影响。
下面将会重点讨论其中最为关键的因素。
1. 锡膏品质锡膏作为印刷过程中的关键材料之一,其品质对印刷效果有着重要影响。
好的锡膏具有高黏度、低稀释度、高粘度稳定性等特点,能够有效避免出现晕印现象,同时也可以提高印刷的精度和稳定性。
2. 模板品质模板是锡膏印刷过程中的关键工具之一。
好的模板应当能够有效提高印刷精度,并且可以降低印刷中出现漏印、小字等缺陷的几率。
因此,选择合适的模板材质和设计优化的缝隙形状都是十分重要的。
3. 印刷设备和参数印刷设备和印刷参数的选取和调整是影响锡膏印刷效果的一个至关重要的因素。
合适的印刷设备应当能够提供合适的压力和印刷速度,同时还需要具有高精度的控制能力,以确保印刷质量得到有效保证。
在印刷参数方面,设定合适的印刷高度、刮刀压力、刮刀速度、印刷速度等参数也是关键的。
只有经过充分的实验和调整,才能够得出最为合适的印刷参数,从而提高印刷效率和质量。
4. 检查与控制除了上述的因素以外,良好的检查和控制环节也是保证锡膏印刷质量的重要手段之一。
在设立合适的检查点和流程的前提下,通过对印刷过程中的关键参数进行实时测量和监控,及时发现和处理异常情况,从而避免印刷质量出现问题。
此外,定期对印刷过程进行数据分析和统计是提高印刷质量稳定性的重要途径。
通过合理的数据采集和分析,可以及时发现质量问题的产生和变化规律,并采取相应的纠正措施,从而不断提高锡膏印刷的质量稳定性。
结论综上所述,锡膏印刷的质量受到众多的影响因素,其中最重要的因素包括锡膏品质、模板品质、印刷设备和参数以及检查与控制等方面。
对于电子制造行业来说,只有通过针对每个因素的详尽分析和实验优化,才能够不断提高印刷质量和效率,达到高品质的表面贴装成果。
【干货】您知道SMT制程中影响印刷的主要因素有那些吗?,一步步助你成为SMT工艺大咖!

【干货】您知道SMT制程中影响印刷的主要因素有那些吗?,一步步助你成为SMT工艺大咖!引言:在SMT制造过程中,锡膏印刷结果对SMT制造品质有着举足轻重的影响。
影响锡膏印刷质量的因素有很多,如钢网的制造工艺,钢网的开孔设计,PCB的平整度,印刷参数的设置,锡膏本身的特性等等。
本文将对影响印刷的因素进行详细解析!影响印刷的主要因素锡膏(Solderpaste)钢网(Stencils)PCB板(Printed circuit board)刮刀(Squeegees)一、锡膏锡膏是一种焊球和焊剂的混合物,通过加热可以连接两个金属表面就重量而言,90%是金属就体积而言,50%金属 / 50%焊剂–10 mil厚的锡膏,过完回流炉后只有5 mil焊球–主要功能:在两个或多个金属表面形成永久的金属连接–球形合金粉末焊剂:提供两个主要功能:1.使焊球混合能够保持均匀2.它的化学作用可以将元件、PCB焊盘以及焊球表面的氧化物清除。
–基材、活性剂、触变剂、溶剂最常用的焊球:–63% 锡 (Sn)–37% 铅 (Pb)焊球合金成分不同,回流温度也不同焊料球的尺寸不同,应用也不同焊剂成分基材:由松香或松香酯组成,提供粘接性和焊接表面的净化作用溶剂:由乙二醇、二甘醇组成,用来调整焊膏的粘度活性剂:胺、胺氢氯化物组成,用来净化焊接表面的氧化物触变剂:乳化石蜡,防止焊料粉末和焊剂分离焊剂类型RMA: Rosin Mildly Activated(中等活性松香)RA: Rosin Activated(活性松香)WS/OA: Water Soluble/Organic Acids(水溶性/有机酸)LR: Low Residue/No Cleans(低残留/免清洗)RMA和RA焊剂不一定要清洗,但是当PCB或元件的温度升高到助焊剂的活化温度时(大约150°)它们开始形成可以导电的卤化物和盐,引起短路。
所以通常也要清洗WS/OA必须要清洗,因为酸会腐蚀掉焊点二、Stencils(钢网)有四种常用钢网:Chemical Etched(化学腐蚀)Laser Cut(激光切割)Electro-formed(电铸)nanometer(纳米)钢网设计钢网的开孔尺寸要小于焊盘尺寸的20%,但是必须保证钢网开宽度与钢网厚度的比值(宽厚比)不能小于1.5(25mil以下间距)三、PCB板设计PCB要求有好的钢性(否则需要定做夹具)PCB要求有最小的弯曲PCB焊盘的金属化PCB包装PCB上的阻焊膜四、刮刀刮刀材料类型–复合材料–金属复合材料刮刀通过刮挖作用改变锡膏的印刷量比金属刮刀便宜对于细间距的印刷,推荐使用90以上硬度的复合材料刮刀金属刮刀使用寿命要长于复合材料比较脆弱最流行刮挖效应的影响较小五、环境因素合适的环境条件对于好的印刷质量是非常必要的:–温度: 维持锡膏的使用条件(要求70~76华氏度)·不适条件会引起锡膏粘稠或过干–湿度: 要求在50%左右·小于50%会使锡膏变干(挥发性材料会蒸发)·大于50%会使锡膏吸收潮气,结果会使锡膏失效或是产生锡球通风: 在印刷区保持最小的通风,也是得到最好印刷质量的保证洁净度: 对机器和印刷质量同样重要SMT助手1、内容搜索2、SMT云盘3、SMT人才网。
锡膏中有机物的影响
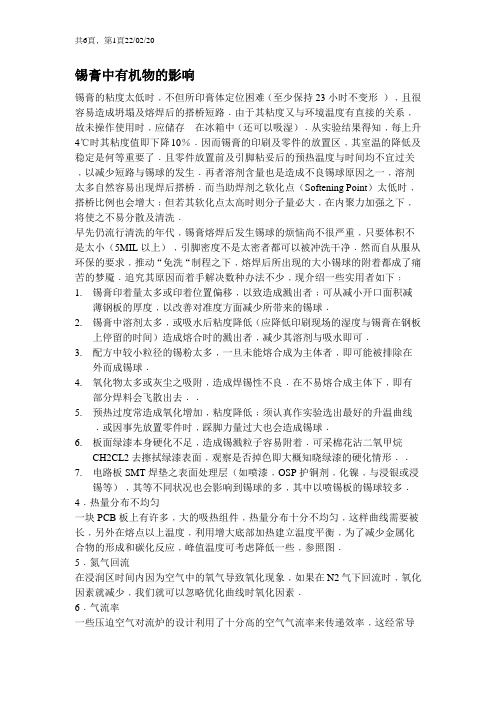
锡膏中有机物的影响锡膏的粘度太低时﹐不但所印膏体定位困难(至少保持23小时不变形)﹐且很容易造成坍塌及熔焊后的搭桥短路﹒由于其粘度又与环境温度有直接的关系﹐故未操作使用时﹐应储存在冰箱中(还可以吸湿)﹒从实验结果得知﹐每上升4℃时其粘度值即下降10%﹒因而锡膏的印刷及零件的放置区﹐其室温的降低及稳定是何等重要了﹒且零件放置前及引脚粘妥后的预热温度与时间均不宜过关﹐以减少短路与锡球的发生﹒再者溶剂含量也是造成不良锡球原因之一﹐溶剂太多自然容易出现焊后搭桥﹒而当助焊剂之软化点(Softening Point)太低时﹐搭桥比例也会增大﹔但若其软化点太高时则分子量必大﹐在内聚力加强之下﹐将使之不易分散及清洗﹒早先仍流行清洗的年代﹐锡膏熔焊后发生锡球的烦恼尚不很严重﹐只要体积不是太小(5MIL以上)﹐引脚密度不是太密者都可以被冲洗干净﹒然而自从服从环保的要求﹐推动“免洗“制程之下﹐熔焊后所出现的大小锡球的附着都成了痛苦的梦魇﹒追究其原因而着手解决数种办法不少﹐现介绍一些实用者如下﹕1.锡膏印着量太多或印着位置偏移﹐以致造成溅出者﹔可从减小开口面积减薄钢板的厚度﹐以改善对准度方面减少所带来的锡球﹒2.锡膏中溶剂太多﹐或吸水后粘度降低(应降低印刷现场的湿度与锡膏在钢板上停留的时间)造成熔合时的溅出者﹐减少其溶剂与吸水即可﹒3.配方中较小粒径的锡粉太多﹐一旦未能熔合成为主体者﹐即可能被排除在外而成锡球﹒4.氧化物太多或灰尘之吸附﹐造成焊锡性不良﹒在不易熔合成主体下﹐即有部分焊料会飞散出去﹒﹒5.预热过度常造成氧化增加﹐粘度降低﹔须认真作实验选出最好的升温曲线﹒或因事先放置零件时﹐踩脚力量过大也会造成锡球﹒6.板面绿漆本身硬化不足﹐造成锡溅粒子容易附着﹒可采棉花沾二氧甲烷CH2CL2去擦拭绿漆表面﹐观察是否掉色即大概知晓绿漆的硬化情形﹒﹒7.电路板SMT焊垫之表面处理层(如喷漆﹐OSP护铜剂﹐化镍﹐与浸银或浸锡等)﹐其等不同状况也会影响到锡球的多﹐其中以喷锡板的锡球较多﹒4﹒热量分布不均匀一块PCB板上有许多﹐大的吸热组件﹐热量分布十分不均匀﹐这样曲线需要被长﹐另外在熔点以上温度﹐利用增大底部加热建立温度平衡﹐为了减少金属化合物的形成和碳化反应﹐峰值温度可考虑降低一些﹐参照图﹒5﹒氮气回流在浸润区时间内因为空气中的氧气导致氧化现象﹐如果在N2气下回流时﹐氧化因素就减少﹐我们就可以忽略优化曲线时氧化因素﹒6﹒气流率一些压迫空气对流炉的设计利用了十分高的空气气流率来传递效率﹐这经常导致冷焊和锡现象﹐如果不减少气流率﹐通过曲线缩短加热时间来帮助减少不良﹒7﹒曲线的调节最佳的炉温曲线的特点就是回流焊技术的功能﹐当热效率或热控率与压迫式对流回流焊系统的效率不同时﹐那么所要求的升温速率的时间﹐浸润区操作时间和所有的加热时间都要被调节﹒我们在文章中描述的最佳曲线都将被建议作为一个起点来使用﹐我们在监控温度滑坡和焊接不良改善的过程中检验它的适用性﹒例如﹐一个非常大的温度滑坡被改善了﹐然而这个回流焊炉可利用的热效率又不足够时﹐我们需要长浸润区的时间﹒结论根据对不良品缺陷的机械分析﹐炉温曲线的设计是为了促进焊接效果﹒通常﹕升温速率低的曲线可以减少热塌陷﹐短路﹐立碑﹐偏移﹐包焊﹐开路﹐锡以及元器件的破裂等不良﹒缩减吸热区(浸润区)可减少空焊﹐冷焊﹐锡﹐开路等不良﹒使用低峰值的曲线可减少碳化﹐分层﹐金属化合﹐L﹐假焊和空焊等不良﹒降温区使用快速冷却的曲线可以帮助减少金属化合﹐碳人﹐L﹒53页通过缺陷分析获得优化回流曲线概述根据对不良品缺陷的机械分析﹐炉温曲线的设计优化是可获得良好的焊接效果﹒通常﹕1.升温速率低的曲线可以减少热塌陷﹐短路﹐立碑﹐偏位﹐包焊﹐开路﹐锡沫﹐锡以及元器件的破裂等不良﹔2.缩减吸热区(浸润区)可减少空焊﹐冷焊﹐锡﹐开路等不良﹔3.使用低峰值的曲线可减少碳化﹐分层﹐金属化合﹐萃化﹐假焊和空焊等不良﹔4.降温区使用快速冷却的曲线可以帮助减少金属化合﹐碳化﹐萃化﹐假焊﹐焊接颗粒尺寸等﹔5.降温区采用缓慢冷却的曲线可以促进焊锡或焊盘的连接﹐由此得出的最佳曲线应该是﹕ι在175℃前缓慢上升﹒ι温度在20-30秒逐步上升并超过180℃﹒ι迅速上升并达到220℃﹒ι温度迅速下降﹒ι传统的炉温曲线受到过去回流焊技术的限制﹐因此要执行一个完美的曲线需要可控制且有高效的热率的回流焊技术的支持﹐气相回流焊可以提供快速加热﹐但热效率却难以控制﹒而红外线回流焊可以控制热率﹐但它受到组件特征的局限﹒但是压迫式空气对流回流焊技术的出现﹐可以实现高效﹐可控的热率﹐同时又可以满足不同特征的元器件﹐因此我们可以实现最佳的回流焊曲线﹒ι关键词﹕回流﹐曲线﹐缺陷﹐松香﹐锡浆﹐焊接﹐对流﹐红外线﹐气相﹐SMT﹒介绍1.在SMT的PCBA过程中﹐将焊膏进行回流焊是形成焊点的主要方法﹒通常条件适合﹐回流焊工艺便可做到高产出﹐高性能﹐低损耗﹒在所有工艺因素中﹐回流焊曲线是最重要的一个环节之一﹐它直接决定着焊接的不良率﹐通常受到回流曲线影响的不良现象有组件断裂﹐立碑﹐移位﹐锡﹐锡沫﹐冷焊﹐短路﹐假焊﹐空焊﹐包焊﹐碳化﹐分层﹐L﹐浸润不良等等﹒因此为了实现高产出﹐高可靠性﹐设计合适的曲线是非常重要的﹒2.通常回流焊曲线大体分为3个重要部分﹒A﹒峰值温度﹔B﹒加热阶﹔C﹔冷却阶段﹔每一部分都影响着焊接的效果﹐依据缺陷的机械分析﹐我们将集中讨论如何设计曲线的每一个部分﹐尽量减少不良﹐增大产品的可靠性﹒每一部分﹕松香作用在SMT工业中﹐焊接通常是伴随着松香清洁金属氧化物开始的﹐然后随着焊锡的浸润形成焊点﹐因此在讨论曲线的认定前﹐我们非常有必要了解一下松香作用的时间和温度要求﹒1.松香作用的时间/温度要求ι依据图1所示﹐松香作用通常被浸润的时“S“决定﹐短时间的浸润体现了松香快速作用﹐同样我们可以通过考查焊膏的接合﹐回流等行为来研究松香作用﹐另外焊膏快速的接合工艺需要快速的松香反应配合﹒ι焊膏的回流可以在很短的时间内完成﹒这种现象很容易验证﹐我们将一点63/37的焊膏丝印在一个铜箔上﹐接着将试样放到一个有适合温度的热盘上﹐焊膏的回流展仅仅在几秒内就会完成﹒ι焊膏快速的回流和松香作用可以通过考查松香的浸润时间来验证﹒列表1显示了来自四个公司63/37焊膏的四种不同松香A﹐B﹐C﹐D在200℃和240℃的浸润时间﹒铜箔试样被放在100℃的空气对流炉中3个小时﹐用来模拟焊接的恶劣环境﹐在这次研究中﹐使用的焊锡为63/37和62/36AG2﹐结果显示在设计的温度下浸润大约为几秒钟﹐因此可以推定松香反应不需要很多秒钟当温度上升到200℃或更高时﹒简单地说﹐快速加速曲线足以完成松香作用并产生满意的回流和浸润﹒2﹒温度低于熔点温度时松香的作用为了了解在低于熔点温度时松香反应作用﹐我们测量了四种低熔点RMA焊膏中的松香F1﹐F2﹐F3﹐F4的浸润时间﹐显然这种低熔点焊锡浸润时间比63/37共晶焊锡长﹐但是不同的温度下测试出的浸润时间反映出合适温度促进松香的作用率﹐结果参照图2﹔浸润时间和温度成反比例﹐至少在150℃-240℃范围之间满足这个规律﹐在150℃时浸润时间为1-2秒﹐在210-240℃时的时间要长﹐因此我们可作出如下推断﹕(1)温度是影响松香6作用的一个重要因素﹔(2)相同的浸润时间﹐温度高低对松香作用的效果影响微乎其微﹒第二部分﹕峰值温度1﹒冷焊及较差浸润回流焊的峰值温度的偏差受到所装配的PCB和元器件的影响﹒因为自然界不同物质的影响﹐焊膏连接的时间比我们作浸润的测试的时间要长﹐因此最低的峰值温度应比焊锡的熔点温度高出30℃﹐如果峰值温度过低﹐有机会造成冷焊或润湿不良﹒如果使用的是63/37共晶焊锡﹐其最低的峰值温度大约是210℃﹒2﹒碳化﹐分层﹐金属合金最高的峰值温度大约是235℃﹐如若不然胶纸板的碳化和分层还有塑料元器件将被担忧﹐而且﹐大量的金属化合物的形成将会导致焊点脆弱﹒3﹒萃化萃化涉及到混合物的应用﹐当过量的金属被析取到焊锡中﹐萃化的程度将由峰值温度确定﹐我们可以使用较低的峰值温度减少萃化﹒如果缩短超过液相温度的时间也可以帮助减少萃化﹒第三部分﹕冷却阶段1﹒金属化合物最佳的冷却阶段很容易被确定﹒在熔点温度以上时﹐缓慢的降温将会导致过量的金属化合物产生﹐想降低金属化合物的产生﹐必须选用快速降温﹒2﹒焊接颗粒大小缓慢的降温经常受到退火的影响而导致焊点有较大的颗粒结构﹐这主要涉及温度的范围在熔点温度和稍低一点之间﹒较大的颗粒结构表现了较差的阻抗﹐是我们所有期望的﹒如果使用较快的降温我们就可以获得好的颗粒结构﹐然而减少快速降温的影响必须增大温度问题间隙﹐50℃的温度间隙足以使退火的影响显得微不足道﹒3﹒内部压力导致组件破裂最大的降温速率取决于元器件承受热冲击的能力﹐如电容之类的元器件﹐降温速率大约是4℃/SEC﹒4﹒焊点变形回流焊炉降温部分的机械结构是典型的压迫冷气操作﹐一个快速的冷却需要使用非常快速的冷气吹风到熔化的焊点上﹐通常会导致焊点变形﹐一般来讲﹐如果降温速率不超过4℃/SEC﹐焊点变形就会微不足道﹒5﹒内部压力-焊锡和焊盘分离降温速率同样影响焊盘和PCB之间分离﹐或者焊点与焊盘分离﹐一个快速的降温将导致在元器件和PCB板之间产生一个很大的温度坡﹐从而导致热张力不平衡﹐这将在焊点上产生一个很大的内部压力﹐从而导致焊点从PCB的焊盘上脱落﹐例如﹐在有些情况下BGA焊点的一角从PCB焊盘脱离﹒第四部分﹕加热阶段也许加热阶段是回流焊曲线中最复杂的一部分﹐和冷却阶段一样﹐相关因素包括时间和温度﹒1﹒塌陷和短路短路是塌陷的直接结果﹒因此我们将集中讨论焊膏的塌陷﹒因为塌陷仅仅发生在焊膏状态﹐因此在温度的讨论上将在焊锡熔点温度以下﹒通常我们用增加温度加强分子的热力运动来降低化合材料的粘度﹐在高温下降低粘度自然会产生塌陷﹒另一方面﹐增加温度将会蒸发松香中的熔剂﹐导致固体成发增多﹐粘度增加﹐这两个相对的作用﹐热力作用和熔剂挥发作用的范例参照图3﹒另外﹐热力作用是物质固有的特性﹐它只受温度而不受时间的影响﹐因此升温速率对它没有影响﹐而熔剂挥发是一个运动学现象﹐它将受升温速率的影响﹐溶剂的汽化率和热量和溶剂的温度成正比﹐溶剂挥发的数量和产品的汽相特性和汽相的时间成正比﹐换句话说﹐溶剂的总挥发量取决于温度和时间﹒因此﹐可以调校回流焊的升温速率﹐在慢的升温速率时﹐焊膏的粘度高于快升温速率时的粘度﹐因为任何温度的提升都导致大量熔剂挥发﹒所以应用一个合适的慢升温率的曲线﹐溶剂挥发的作用会掩盖热力的作用﹐这将导致粘度降低的很少﹐甚至有温度增加粘度增大的结果﹐参照图4﹒因此﹐塌陷随着降低升温速率而减少﹐参照图5﹕通常建议由室温到熔点温度之间升温速率为0﹒5℃-1℃/SEC﹒2.锡沫锡沫的产生是在预热阶段由于松香的除气作用(内部散发出气体物质)超过了焊膏本身的粘着力﹐而除气作用促使了焊膏在低空间元器件下面形成了隔离带﹐回流时﹐隔离的焊膏被融化﹐并从组件底部浮现出来进而形成锡沫﹒除气作用可以控制焊锡软融前的加热阶段来改善﹒在较慢的升温率曲线中﹐松香的除气作用由扩散形式代替了严格蒸馏形式﹐因此可以防止由除气作用形成的焊膏隔离带﹐避免锡沫的形成﹒3﹒包焊包焊现象是指焊锡在浸润元器件脚时﹐底部从焊点位置位置移开﹐在这个范围内形成开路或缺口﹐主要原因为﹕在焊锡软融阶段组件脚的温度高于焊盘温度﹐防止此类现象的方法﹐是使用更多的底部加热或在熔融阶段使用较慢的升温率﹐如果这样零件脚和焊盘在焊锡浸润前﹐就可以达到温度平衡﹐一旦焊锡浸润到焊盘上通过焊锡切片分析﹐焊接将非常稳定﹐并且不再受到升温速度的局限﹒4﹒立碑和偏位立碑和偏位由于元器件两端未充分浸润而引起的类似于包焊﹐我们可以使用较慢的升温速率曲线﹐使得零件两端在焊锡融熔前达到热平衡来改善﹒5﹒锡锡是由于锡粉飞引起的﹐在很多情况下﹐这种不良发生在预热到连接阶段升温速率超过2℃/秒时﹐慢的升温速率是防止飞的非常有效的手段﹒锡也可能是在预热到焊接过程中锡粉被过度氧化所致﹒减少预热到融熔的热量就可以改善﹒因此当飞和氧化因素同时被考虑时﹐最佳的加热工艺将锡不良降低到最少﹐而最佳的曲线是从加热到熔融阶段采用线性曲线﹒6﹒湿润不良湿润不良是由于预热到焊接过程中锡粉过度氧化引起的﹐类似于我们前面讨论的锡珠现象﹐减少预热阶段的热量来减少氧化﹐而曲线方面。
影响锡膏的主要参数

影响锡膏的主要参数
锡膏是装配电路板上元件所必需的一种可熔焊状态的金属材料,它的参数对于最终产品的性能有着至关重要的影响。
锡膏的参数通常以物理和化学的属性来控制。
物理属性主要包括:粘度、流动性、悬浮性、滴状态和烘干状态。
化学属性则主要是锡膏的含锡量、锡粉的大小分布和锡的类型。
首先,锡膏的粘度是影响锡膏的主要物理性能,我们可以通过测定粘度系数,判断出锡膏的流动性和稠度,也就是锡膏在挤压时间内能够穿过屏幕窗口的能力。
其次,其流动性也是比较重要的性能,直接影响锡膏和元件之间的流动性,从而影响最终的焊接质量。
再次,锡膏的悬浮性已经控制其粒度的分布,即物料在悬浮体内的分布情况,这是影响焊接质量的重要参数,若锡粉细度过小会导致过焊。
另外,锡膏的滴状态也影响最终的焊接质量,它控制着锡膏的飞溅和提供熔断保护层。
最后,烘干状态也是一个重要的参数,它是控制熔料在连接电镀界面时发展能力的一个参数。
在这些物理性参数控制后,锡膏也具有一定的化学属性,首先是锡的含量,这是锡膏的焊接性能的主要参数,确定了熔料的量,确定了最终的焊料膏。
其次,锡粉的大小分布也影响最终的焊接质量,确定熔料的发展状态和流动性以及粘度,是影响锡膏性能的重要参数。
最后,锡膏的类型也是影响最终的焊接质量的参数,不同种类的锡膏由于其成分的不同,具有不同的属性和性能,可以符合不同使用场合的要求。
综上所述,锡膏的参数对于焊接质量具有重要的影响,要想获得优良的焊接质量,可以通过控制锡膏的物理性参数和化学性参数来实现。
SMT用焊锡膏使用过程中常见问题之原因分析报告
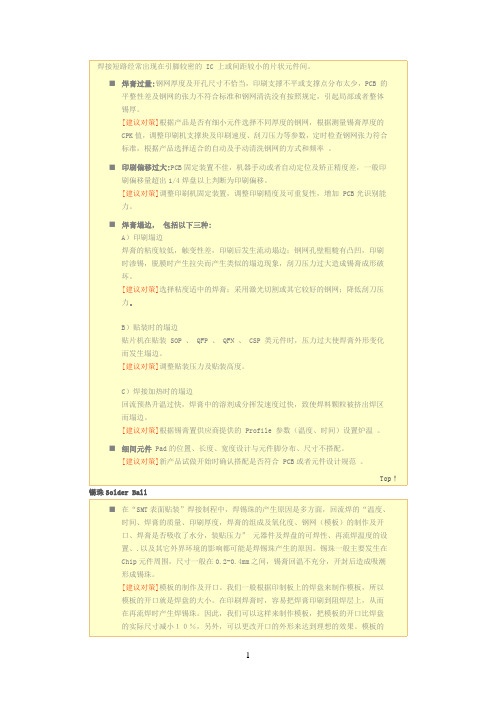
焊接短路经常出现在引脚较密的 IC 上或间距较小的片状元件间。
■焊膏过量:钢网厚度及开孔尺寸不恰当,印刷支撑不平或支撑点分布太少,PCB 的平整性差及钢网的张力不符合标准和钢网清洗没有按照规定,引起局部或者整体锡厚。
[建议对策]根据产品是否有细小元件选择不同厚度的钢网,根据测量锡膏厚度的CPK值,调整印刷机支撑块及印刷速度、刮刀压力等参数,定时检查钢网张力符合标准,根据产品选择适合的自动及手动清洗钢网的方式和频率。
■印刷偏移过大:PCB固定装置不佳,机器手动或者自动定位及矫正精度差,一般印刷偏移量超出1/4焊盘以上判断为印刷偏移。
[建议对策]调整印刷机固定装置,调整印刷精度及可重复性,增加 PCB光识别能力。
■焊膏塌边,包括以下三种:A)印刷塌边焊膏的粘度较低,触变性差,印刷后发生流动塌边;钢网孔壁粗糙有凸凹,印刷时渗锡,脱膜时产生拉尖而产生类似的塌边现象,刮刀压力过大造成锡膏成形破坏。
[建议对策]选择粘度适中的焊膏;采用激光切割或其它较好的钢网;降低刮刀压力。
B)贴装时的塌边贴片机在贴装 SOP 、 QFP 、 QFN 、 CSP 类元件时,压力过大使焊膏外形变化而发生塌边。
[建议对策]调整贴装压力及贴装高度。
C)焊接加热时的塌边回流预热升温过快,焊膏中的溶剂成分挥发速度过快,致使焊料颗粒被挤出焊区而塌边。
[建议对策]根据锡膏置供应商提供的 Profile 参数(温度、时间)设置炉温。
■细间元件 Pad的位置、长度、宽度设计与元件脚分布、尺寸不搭配。
[建议对策]新产品试做开始时确认搭配是否符合 PCB或者元件设计规范。
Top↑锡珠Solder Ball■在“SMT表面贴装”焊接制程中,焊锡珠的产生原因是多方面,回流焊的“温度、时间、焊膏的质量、印刷厚度,焊膏的组成及氧化度、钢网(模板)的制作及开口、焊膏是否吸收了水分,装贴压力” 元器件及焊盘的可焊性、再流焊温度的设置、.以及其它外界环境的影响都可能是焊锡珠产生的原因。
影响锡厚的因素
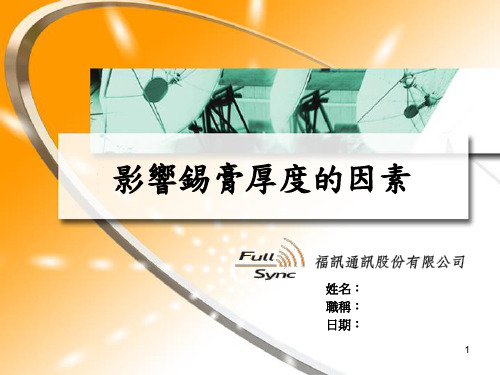
鋼板
V1
PCB
支撐治具
10
脫模時鋼板及PCB狀況示意圖 脫模時鋼板及PCB狀況示意圖 PCB
鋼板粗糙度及脫模速度
PCB
11
脫模後鋼板及PCB狀況示意圖 脫模後鋼板及PCB狀況示意圖 PCB
•鋼板清潔度 •鋼板脫模速度
V2
V3
h1 h2 h3
脫模速度
V3
PCB
V1:錫膏量在印刷後鋼板孔洞內的值 V2:錫膏殘留在鋼板孔洞內的值 V3:錫膏量在PC板上的值 V1=V2=V3, 完美的印刷
4. • • • •
PCB 平整度 變形量 厚度一致性 噴錫板或浸金板
良好的錫膏 厚度管制
5. • • • •
環境 溫度 溼度 震動 粉塵
6. • • • •
檢驗儀器 原理及精度 PCB與儀器的垂直度 檢驗錫膏的位置 歸零的準確度
7. • • •
人為因素 PCB板上的殘留物 儀器讀值之誤判 印刷機之清潔
6
錫粉形狀影響印刷性
1. 不規則型: 不規則型:印刷後易下塌造成 短路,球徑大小也難一致,較 不適合fine pitch印刷作業。 規則型:因為是球形的關係, 規則型: 球徑大小也較規則,較適合fine pitch印刷作業,另外球型粉末 在不活性氣體中製造,所以焊 錫氧化率較低。
2.
7
助焊劑(Flux)種類及調配比例影響黏稠度 黏稠度亦影響印刷性
15
檢驗儀器對錫膏厚度測量的準確性
• • • • 原理及精度 PCB與儀器的垂直度 檢驗錫膏的位置 歸零的準確度
16
人為因素對錫膏厚度的影響
•PCB板上的殘留物 •儀器讀值之誤判 •印刷機之清潔
Barcode或其他殘留物
SMT锡膏印刷制造过程质量影响因素分析
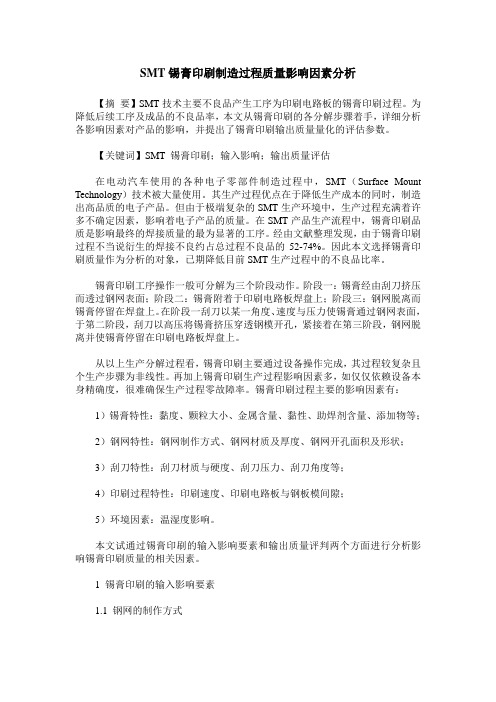
SMT锡膏印刷制造过程质量影响因素分析【摘要】SMT技术主要不良品产生工序为印刷电路板的锡膏印刷过程。
为降低后续工序及成品的不良品率,本文从锡膏印刷的各分解步骤着手,详细分析各影响因素对产品的影响,并提出了锡膏印刷输出质量量化的评估参数。
【关键词】SMT 锡膏印刷;输入影响;输出质量评估在电动汽车使用的各种电子零部件制造过程中,SMT(Surface Mount Technology)技术被大量使用。
其生产过程优点在于降低生产成本的同时,制造出高品质的电子产品。
但由于极端复杂的SMT生产环境中,生产过程充满着许多不确定因素,影响着电子产品的质量。
在SMT产品生产流程中,锡膏印刷品质是影响最终的焊接质量的最为显著的工序。
经由文献整理发现,由于锡膏印刷过程不当说衍生的焊接不良约占总过程不良品的52-74%。
因此本文选择锡膏印刷质量作为分析的对象,已期降低目前SMT生产过程中的不良品比率。
锡膏印刷工序操作一般可分解为三个阶段动作。
阶段一:锡膏经由刮刀挤压而透过钢网表面;阶段二:锡膏附着于印刷电路板焊盘上;阶段三:钢网脱离而锡膏停留在焊盘上。
在阶段一刮刀以某一角度、速度与压力使锡膏通过钢网表面,于第二阶段,刮刀以高压将锡膏挤压穿透钢模开孔,紧接着在第三阶段,钢网脱离并使锡膏停留在印刷电路板焊盘上。
从以上生产分解过程看,锡膏印刷主要通过设备操作完成,其过程较复杂且个生产步骤为非线性。
再加上锡膏印刷生产过程影响因素多,如仅仅依赖设备本身精确度,很难确保生产过程零故障率。
锡膏印刷过程主要的影响因素有:1)锡膏特性:黏度、颗粒大小、金属含量、黏性、助焊剂含量、添加物等;2)钢网特性:钢网制作方式、钢网材质及厚度、钢网开孔面积及形状;3)刮刀特性:刮刀材质与硬度、刮刀压力、刮刀角度等;4)印刷过程特性:印刷速度、印刷电路板与钢板模间隙;5)环境因素:温湿度影响。
本文试通过锡膏印刷的输入影响要素和输出质量评判两个方面进行分析影响锡膏印刷质量的相关因素。
锡膏问题集锦分析
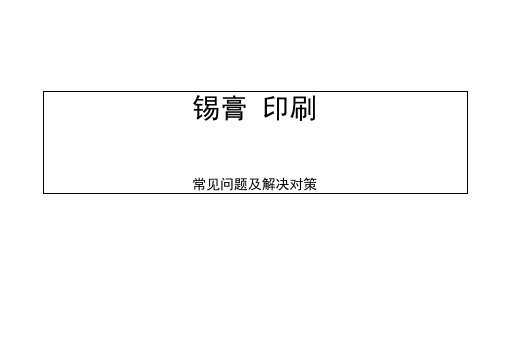
内容索引组装组件基板焊接作业上的各种问题1锡膏的印涂不完整9咼可靠性锡膏成份与特性的分类2渗锡发生的原因与对策10数种适合微细间距电路板用锡粉的颗组装组件基板的热风回焊温度区线图11粒度与其测试结果3各种颗粒度锡粉的塞孔效果4锡球12使用塑料刮刀(A)或金属刮刀时,印涂于钢板孔中的锡膏形状5芯片旁锡球13刮刀的角度与磨损以及其影响6桥接现象14锡膏在印刷时的滚动7灯芯效应15印刷后锡膏面参差不齐的问题8曼哈顿(或墓碑)效应16高可靠性锡膏成份与特性的分类数种适合微细间距电路板用锡粉的颗粒与其测试结果测试38~63 卩m38~45 卩m22~45 卩m20~38 [1 m印刷性0.5mmP00000.4mmP X0000.3mmP X X00扩散率(%)93.493.493.793.7锡球(数)*0.640.350.53 3.50氧化物含量(ppm)406070100热(预烤)垂流378490111:QFP焊垫间的锡球数量O:印刷性良好X:印刷性不良刮刀的角度与磨损以及其影刮刀磨损的判断法◎刮刀棱角磨圆.◎刮刀有裂纹?或粗糙,牵丝.◎钢版上拉出线条.◎钢版面留有参差不齐的锡膏残留◎印刷在焊垫上的锡膏参差不齐刮刀换新的频度◎24小时作业时,每约两周换新一次◎经过20万印刷次数后换新一次.◎不妨建立刮刀换新的有关数据.刮刀磨损原因◎刮刀压力过大.◎刮刀未保持水平.◎金属钢版上有裂痕,或因锡膏凝结发硬.◎清洗时或操作时手法过于粗鲁.锡膏在印刷时的滚动锡膏经刮刀推动而滚动时,.—?:■锡膏如果滚动得顺利,也发挥维持锡膏流动性的那就表示其印刷性良好效果。
效果⑴防止渗锡充分的刮刀压力产生有效剪应力=「-但,仍应避免过大的刮刀压力。
⑵防止刮伤可在金属钢版的钢孔中塞进最适量的锡膏。
⑶搅拌作用锡膏在滚动中可获得均匀的搅拌作用,以保持其良好的印刷性,同时也可使锡膏均匀转印在焊垫上锡膏的滚动也有助于消除锡膏中的气泡。
印刷后锡膏面参差不齐的问题印刷后的锡膏表面不平坦而有明显刮痕或凹凸情形⑴刮刀刀刃的锐利度不足刮刀的刀刃变钝,粗糙或起毛 锡膏表面参差不齐。
锡膏使用常见问题分析

锡膏使用常见问题分析锡膏的回流焊接是用在SMT装配工艺中的主要板级互连方法,这种焊接方法把所需要的焊接特性极好地结合在一起,这些特性包括易于加工、对各种SMT设计有广泛的兼容性,具有高的焊接可靠性以及成本低等;然而,在回流焊接被用作为最重要的SMT元件级和板级互连方法的时候,它也受到要求进一步改进焊接性能的挑战,事实上,回流焊接技术能否经受住这一挑战将决定锡膏能否继续作为首要的SMT焊接材料,尤其是在超细微间距技术不断取得进展的情况之下。
下面我们将探讨影响改进回流焊接性能的几个主要问题,为发激发工业界研究出解决这一课题的新方法,我们分别对每个问题简要介绍。
底面元件的固定双面回流焊接已采用多年,在此,先对第一面进行印刷布线,安装元件和软熔,然后翻过来对电路板的另一面进行加工处理,为了更加节省起见,某些工艺省去了对第一面的软熔,而是同时软熔顶面和底面,典型的例子是电路板底面上仅装有小的元件,如芯片电容器和芯片电阻器,由于印刷电路板(PCB)的设计越来越复杂,装在底面上的元件也越来越大,结果软熔时元件脱落成为一个重要的问题。
显然,元件脱落现象是由于软熔时熔化了的焊料对元件的垂直固定力不足,而垂直固定力不足可归因于元件重量增加,元件的可焊性差,助焊剂的润湿性或焊料量不足等。
其中,第一个因素是最根本的原因。
如果在对后面的三个因素加以改进后仍有元件脱落现象存在,就必须使用SMT粘结剂。
显然,使用粘结剂将会使软熔时元件自对准的效果变差。
未焊满(短路)未焊满是在相邻的引线之间形成焊桥。
通常,所有能引起焊膏坍落的因素都会导致未焊满,这些因素包括:1,升温速度太快;2,锡膏的触变性能太差或是焊膏的粘度在剪切后恢复太慢;3,金属负荷或固体含量太低;4,粉料粒度分布太广;5;焊剂表面张力太小。
但是,坍落并非必然引起未焊满,在软熔时,熔化了的未焊满焊料在表面张力的推动下有断开的可能,焊料流失现象将使未焊满问题变得更加严重。
SMT锡膏印刷机经验分享
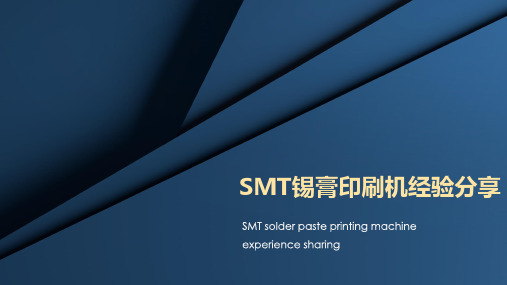
六、印刷机工艺参数的调节及影响
刮刀的速度
刮刀的速度和焊锡膏的粘度有 很大的关系,刮刀的速度越慢, 焊锡膏的粘度越大同样,刮刀 的速度越快,粘度就越小。调 节这个参数要参照焊锡膏的成 分和PCB元件的密度以及最小 元件的尺寸等相关参数。目前 我们一般选择在30~65mm/S
刮刀的压力
刮刀的压力刮刀德压力对印刷 影响很大,压力太大会导致焊 锡膏印得很薄,使得锡量不足。 我们一般都设定在8Kg左右
SMT锡膏印刷机经验分享
前言
表面贴装技术(SMT)已成为当今电子装联 技术中最为普遍通用的技术,焊膏印刷是SMT 基本工艺中的第一道关键工序,也是最重要的 环节之一。焊膏印刷质量直接影响到SMT组装 的质量和效率。
锡膏的应用涂布工艺,可分为两种方式,一 是使用掩模板(钢网)作为印刷版把锡膏印刷 到PCB,适合大批量生产应用,是最为常用的 涂布方式,一种是局部少量的注射涂布,本文 主要对第一种涂布工艺进行介绍,希望能对 SMT锡膏印刷工程的朋友起到帮助作用。
2、基板和钢网的定中心
基板和钢网的定中心包括机械定中心和光学定中心,光学定中心是机械定中心的补正,大大地提高了印刷的精度。
四、SMT印刷机
3、使用的刮刀范围
使用的刮刀包括刮刀(材料、形状)、硬度范围、长度范围等。
SMT用焊锡膏使用过程中常见问题之原因分析报告
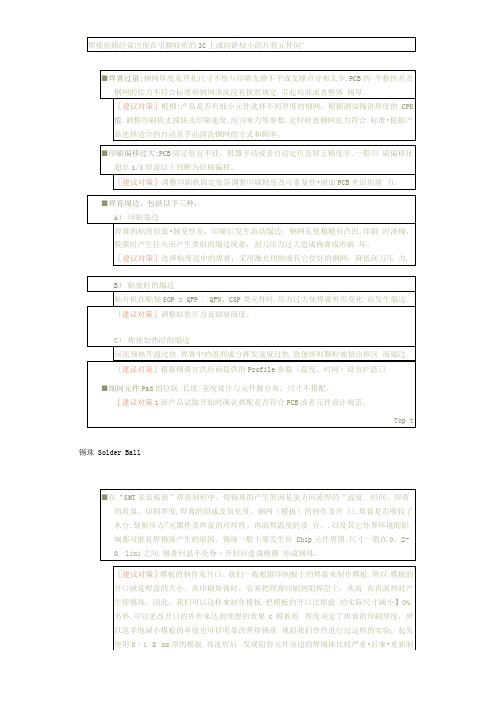
印刷时出现拖尾.粘连.图像模糊等问题印刷在匸艺控制过程中显得尤其重要.这里针对印刷问题做如下I纲述。
■锡膏的」:艺选型不对,锡膏触变性差.或者是焊锡彥保存不、”1或者已过使用期限
粘性被破坏等。
[建议对策]根据自身之工艺条件选择适合黏度等级和锡粉颗粒型号的锡膏•按规 定保存和使用锡膏
■锡膏中的金属成份偏低.助焊剂成份比例偏高所致。
[建议对策]模板的制作及开口。我们一般根据印制板上的焊盘來制作模板.所以 模板的开口就是焊盘的大小。在印刷焊膏时,容易把焊膏印刷到阻焊层上,从而 在再流焊时产生焊锡珠。因此,我们可以这样來制作模板.把模板的开口比焊盘 的实际尺寸减小】0%.另外.可以更改开口的外形來达到理想的效果c模板的 厚度决定了焊膏的印刷厚度,所以适半地减小模板的卑度也可以明显改善焊锡珠 现叙我们曾经进行过这样的实验:起先使用0・18mm厚的模板.再流烬后 发现阻容元件旁边的焊锡珠比较严重•后來•重新制作了一张模板•厚度改为0・15mm,再流焊基木上消除了焊锡珠。
〔建议对策]锡粉与助焊剂重虽比及体枳比应在规定范用内调配C
■刮刀材质、长度选用不、S刮刀损坏,刮刀水平不好,印刷机固定装宜松动或者 不平。
[建议对策]检査涮整刮刀•选用合适的刮刀,调整印刷机固定装宜。
■卬刷机参数设宜不佳,印刷机参数包括印刷速度、刮刀压力、脫膜距离及速度.
清洗频率及清洗方法。
〔建议对策]根据产品特性调整印刷参数C
〔建议对策]根据锡膏宜供应商提供的Profile参数(温度、时间)设宜炉温□
■细间元件Pad的位臥 长度.宽度设汁与元件脚分布、尺寸不搭配。
[建议对策1新产品试做开始时确认搭配是否符合PCB或者元件设计规范。
Top t
锡珠Solder Ball
锡膏稀释原因
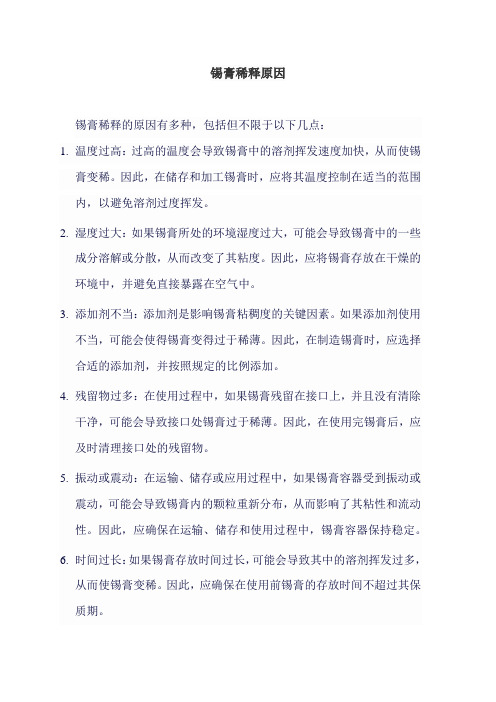
锡膏稀释原因锡膏稀释的原因有多种,包括但不限于以下几点:1.温度过高:过高的温度会导致锡膏中的溶剂挥发速度加快,从而使锡膏变稀。
因此,在储存和加工锡膏时,应将其温度控制在适当的范围内,以避免溶剂过度挥发。
2.湿度过大:如果锡膏所处的环境湿度过大,可能会导致锡膏中的一些成分溶解或分散,从而改变了其粘度。
因此,应将锡膏存放在干燥的环境中,并避免直接暴露在空气中。
3.添加剂不当:添加剂是影响锡膏粘稠度的关键因素。
如果添加剂使用不当,可能会使得锡膏变得过于稀薄。
因此,在制造锡膏时,应选择合适的添加剂,并按照规定的比例添加。
4.残留物过多:在使用过程中,如果锡膏残留在接口上,并且没有清除干净,可能会导致接口处锡膏过于稀薄。
因此,在使用完锡膏后,应及时清理接口处的残留物。
5.振动或震动:在运输、储存或应用过程中,如果锡膏容器受到振动或震动,可能会导致锡膏内的颗粒重新分布,从而影响了其粘性和流动性。
因此,应确保在运输、储存和使用过程中,锡膏容器保持稳定。
6.时间过长:如果锡膏存放时间过长,可能会导致其中的溶剂挥发过多,从而使锡膏变稀。
因此,应确保在使用前锡膏的存放时间不超过其保质期。
7.老化:随着时间的推移,锡膏可能会发生老化,其中一些成分可能发生化学变化,导致其性能下降。
因此,应定期检查锡膏的性能,以确保其符合使用要求。
8.不适当的存储条件:如高温、潮湿或直射阳光等不适当的存储条件,可能会对锡膏的性能产生负面影响。
因此,应将锡膏存放在适当的条件下,以保持其性能稳定。
综上所述,为了确保锡膏的正常使用和性能稳定,应综合考虑上述因素并采取相应的措施进行控制和管理。
锡膏体积与焊盘面积的最佳比例

锡膏体积与焊盘面积的最佳比例1. 引言1.1 研究背景锡膏体积与焊盘面积的最佳比例一直是电子制造领域的重要研究课题。
随着电子产品的日益普及和功能的不断提升,对焊接质量和性能要求也越来越高,而锡膏体积与焊盘面积的比例恰恰是影响焊接质量的重要因素之一。
在实际生产中,如果锡膏体积过大,容易造成焊盘短路或焊点偏移现象;而如果锡膏体积过小,则可能导致焊盘与焊料之间的接触面积不足,影响焊接强度和稳定性。
过去的研究主要集中在锡膏体积与焊盘间隙的关系上,对于体积与面积的最佳比例仍缺乏系统性的研究。
本研究旨在探索锡膏体积与焊盘面积的最佳比例,为提高焊接质量和稳定性提供科学依据。
通过对锡膏体积与焊盘面积的关系进行深入分析,可以为电子制造行业的生产工艺优化提供指导,并为提高电子产品的质量和性能做出贡献。
研究锡膏体积与焊盘面积的最佳比例具有重要的理论和实践意义。
1.2 问题提出在现代电子制造领域,焊接是一项至关重要的工艺。
而在焊接过程中,锡膏是不可或缺的材料之一。
锡膏的质量和使用方式直接影响到焊接质量和稳定性。
研究锡膏体积与焊盘面积的最佳比例成为了一个迫切需要解决的问题。
焊盘面积与锡膏体积的比例直接影响到焊接质量和效果。
如果锡膏体积过多或过少,都可能导致焊接不牢固或焊接质量不理想。
确定最佳的锡膏体积与焊盘面积的比例对于提高焊接质量具有重要意义。
在实际生产中,制定合理的焊接工艺参数是确保焊接质量的关键。
而锡膏体积与焊盘面积的最佳比例作为焊接工艺参数中的重要因素,对于实现稳定的焊接质量至关重要。
有必要进行深入研究,探讨锡膏体积与焊盘面积的最佳比例是多少,以提高焊接质量和效率。
1.3 研究意义锡膏体积与焊盘面积的最佳比例是电子制造领域中一个重要的研究方向。
控制好锡膏体积与焊盘面积的比例,可以显著影响焊接质量和可靠性。
在电子产品中,焊接是一个至关重要的环节,不仅影响产品的性能,还直接关系到产品的寿命和稳定性。
研究锡膏体积与焊盘面积的最佳比例,可以帮助提高焊接质量,减少焊接缺陷的发生率,提高产品的可靠性和稳定性。
【精选文档】锡膏的种类和影响锡膏特性的参数及锡膏的评估PPT

中温膏锡膏的熔回点在流15焊0℃接到峰250值℃之温间度在 锡(膏2)的按种合类金和1熔影7点响0可锡-2分膏0为特0:高性℃如的。锡参铜数或及锡锡银膏铜的系评/估常如锡银铋系/低温如锡铅铋/锡铋等锡膏
不定形颗粒的特点:组成的焊膏粘度高,印刷后焊膏图形不易塌落,但印刷性较差。
熔点为138℃的锡膏被称为低温锡膏,当贴片的元器件无法承受200℃及以上的温度且需要贴片回流工艺时,使用低温锡膏进行焊接工
细间距Sn63Pb37 -325/500
一般间距锡膏Sn62Pb36Ag2 +500
(4)按焊剂的成分可以分为免洗型(RMA 或RA)和清洗型(又分水洗和溶剂洗)
免清洗锡膏是免清洗助 焊剂和焊锡颗粒的均匀混合 体,同时也包含一些添加剂, 使之适合SMT生产的理想特 性。此种锡膏可以用任何一 种回焊设备,如气相法,热 板法,红外线法,热空气法。
(1)合金焊料成分、焊剂的组成及合金焊 料与焊剂的配比
A、合金焊料成分
要求锡膏的合金成分尽量达到共晶或近共晶。
由于共晶合金在熔化和凝固过程中没有塑性 范围(固液共存区),当温度达到共晶点时焊料全 部呈液态;冷却时,当温度降低到共晶点时焊 料立即呈固态。因此,焊点凝固时形成的结晶 颗粒最致密,焊点强度最高。
无铅锡膏,并非绝对的百分 百禁绝锡膏内铅的存在,而是要
求铅含量必须减少到低于 1000ppm(<0.1%)的水平,同时意 味着电子制造必须符合无铅的组 装工艺要求。“电子无铅化”也 常用于泛指包括铅在内的六种有
毒有害材料的含Βιβλιοθήκη 必须控制在 1000ppm的水平内。
有铅锡膏Sn63/Pb37
无铅锡膏 ROHS
影的响锡温膏度特性且的需主要要参贴数有片:回流工艺 低不时温迈锡 出,膏第使S一n步4用2,B低你i58就温无锡法走膏出进第二行步焊,生接活就是这样的。
锡膏Reflow概论
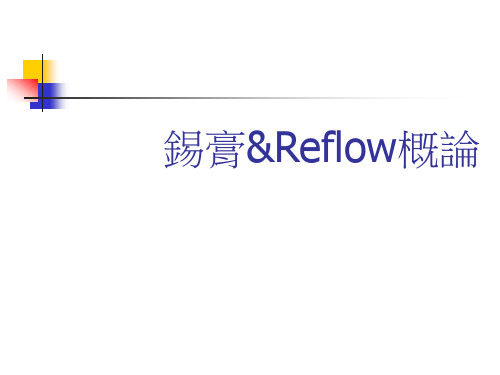
QFP 腳距 0.5mm ╳ ○ 50μm 180~220
0.18~0.15 0.22~0.25
0 30 ← 0.2~0.15
0.3mm ╳ ○
30μm 160~200 0.08~0.10 0.12~0.15
0 20~10
← 0.1
關於印刷速度
印刷速度如太快,會發生虛印、漏印或錫膏量不足(錫膏印刷時 下降未完全)。相反印刷速度太慢,錫膏雖有充分時間下降,但鋼版 與基板接觸時間過長,而使錫膏流至反面,造成錫膏拉絲而出現小 錫珠。當錫膏黏度太低,再連續印刷時易造成滲漏下塌而產生短路。
錫粉末形狀:不規則 錫粉末形狀:規 則 焊錫粉末最大粒徑 錫膏黏度(Pa.s) 鋼版厚度(mm) 鋼版的開口幅(mm) 鋼版與基板間隙(mm) 刮刀速度(mm/sec) 印壓(kg/cm2) 刮刀壓力(mm)
0.65mm ○ ○
75μm 200~250
0.2 0.30~0.35
0.3~0.5 50 2~1 0.2
FLUX之主要成份
LIQUID : Solvent
SOLIDS : Rosin Activator Thixotropic agent
助焊劑(Flux)種類及比例調配
一、Flux種類 1、液態:較常用於DIP生產線上,Flow中的Flux。 2、固態:較常出現於錫絲的中間,或是BGA做 Rework中使用。 3、半固液態:較常用於錫膏中。
焊錫粉末顆粒(二)
二、粉末形狀 1、不規則型:印刷後易下
塌造成短路,球徑大小 也難一致,較不適合fine pitch印刷作業。
2、規則型:因為是球形的 關係,球徑大小也較規 則,較適合fine pitch印 刷作業,另外球型粉末 在不活性氣體中製造, 所以焊錫氧化率較低。
什么造成元件竖立,怎样防止
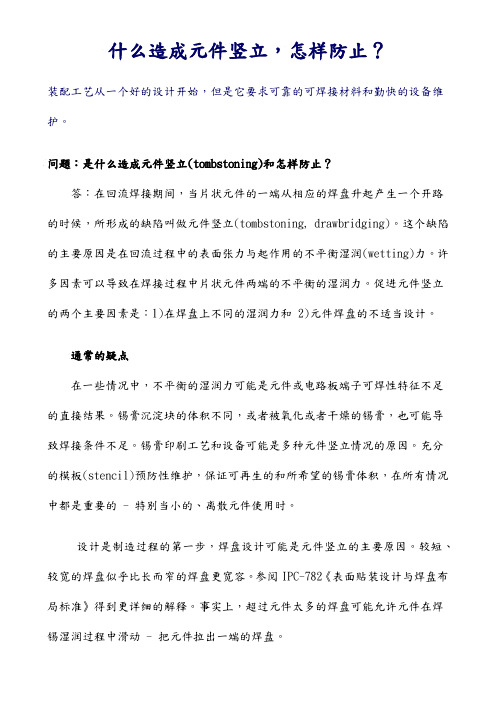
什么造成元件竖立,怎样防止?装配工艺从一个好的设计开始,但是它要求可靠的可焊接材料和勤快的设备维护。
问题:是什么造成元件竖立(tombstoning)和怎样防止?答:在回流焊接期间,当片状元件的一端从相应的焊盘升起产生一个开路的时候,所形成的缺陷叫做元件竖立(tombstoning, drawbridging)。
这个缺陷的主要原因是在回流过程中的表面张力与起作用的不平衡湿润(wetting)力。
许多因素可以导致在焊接过程中片状元件两端的不平衡的湿润力。
促进元件竖立的两个主要因素是:1)在焊盘上不同的湿润力和 2)元件焊盘的不适当设计。
通常的疑点在一些情况中,不平衡的湿润力可能是元件或电路板端子可焊性特征不足的直接结果。
锡膏沉淀块的体积不同,或者被氧化或者干燥的锡膏,也可能导致焊接条件不足。
锡膏印刷工艺和设备可能是多种元件竖立情况的原因。
充分的模板(stencil)预防性维护,保证可再生的和所希望的锡膏体积,在所有情况中都是重要的 - 特别当小的、离散元件使用时。
设计是制造过程的第一步,焊盘设计可能是元件竖立的主要原因。
较短、较宽的焊盘似乎比长而窄的焊盘更宽容。
参阅IPC-782《表面贴装设计与焊盘布局标准》得到更详细的解释。
事实上,超过元件太多的焊盘可能允许元件在焊锡湿润过程中滑动 - 把元件拉出一端的焊盘。
对于小型离散片状元件,为元件的一端设计不同的焊盘尺寸,或者将焊盘的一端连接到地线板上,也可能导致元件竖立。
不同焊盘尺寸的的使用可能造成不平衡的焊盘加热和锡膏流动时间。
在回流期间,元件简直是飘浮在液体的焊锡上,当焊锡固化时达到其最终位置。
焊盘上不同的湿润力可能造成附着力的缺乏和元件的旋转。
在一些情况中,液化温度以上时间的延长可以减少元件竖立。
演唱液化温度以上的时间可以在元件的焊盘之间得到更加均匀的温度。
其他可能的疑点元件竖立的其他被引证的原因包括制造板的情况。
元件下面不均匀的阻焊(solder mask)层厚度,可能把元件一端升起离开焊盘。
- 1、下载文档前请自行甄别文档内容的完整性,平台不提供额外的编辑、内容补充、找答案等附加服务。
- 2、"仅部分预览"的文档,不可在线预览部分如存在完整性等问题,可反馈申请退款(可完整预览的文档不适用该条件!)。
- 3、如文档侵犯您的权益,请联系客服反馈,我们会尽快为您处理(人工客服工作时间:9:00-18:30)。
影响所需体积(THR体积模型)的锡膏相关因素
简单地说,锡膏是由助焊剂和其内的金属小球构成。
添加增黏剂、流变增强剂及改变助焊剂的化学性质等都可以改变锡膏的特性。
锡膏的一项主要规格就是金属重量百分比。
就网板印刷来说,基于对黏性的考虑,通常指定使用合金重量为90%的锡膏。
对于助焊剂密度为1 g/cc、金属重量在90%的一般共晶型63Sn/37Pb合金,需要较计算出的固态体积多沉积1.92倍(体积转换系数)的焊膏。
焊膏内金属的体积部分为52%,在回流焊接时,近一半的焊膏体积会变为助焊剂蒸发和残余物而丢失。
理想焊点中焊料的体积可以用下列公式计算出来(如图1所示):
①焊点顶部圆角的半径r=焊盘半径-a;
②焊点头部重心位置=0.2234r;
③焊点头部中心位置=0.2234r+a;
④焊点头部体积Vf=o.215r2×2×3.14×(02234r+a);
⑤通孔内焊料体积Vpth=3.14×h×(R2-a2);
⑥焊点总的体积Vt=Vpth+2Vf。
其中,R=通孔半径;h=PCB厚;;L=元件脚截面长;W=元件脚截面宽。
图1 理想焊点中焊料体积计算示意图
那么,焊点所需要的锡膏量可以通过如下的公式计算得到(如图2所示):
①需要印刷的锡膏量Vs=bVt;
②通孔内的锡膏量Vh=(3.14×R2h)K;
③印刷在板表面的锡膏量Vsurf=Vs-Vh。
其中,b=锡膏经回流熔化并固化后的体积转换系数;饪锡膏在通孔内的填充系数。
图2 焊点所需锡膏量计算示意图
体积转换系数与参数锡膏中金属含量、助焊剂密度、合金成份、印刷参数、通孔及焊盘尺寸、钢网厚度和引脚特征相关,可以通过下面计算公式获得:
b=(Wm/Pm+(100—Wm)/Pf)/(Wm/Pm)
式中,Wm为金属含量(重量百分比);Pm为合金密度;Pf为助焊剂密度。
印刷在PCB通孔内和焊盘上的锡膏体积会在回流焊接后减少,如果将这种降低因素与具有相同成分和助焊剂类型的常见点胶级锡膏(金属重量占85%)相比,要使用比计算出的固态焊料多2.46倍的焊膏。
与网板印刷的焊膏相比,这个体积的增加是必须进行折中平衡,旨为减少金属成分,以增加焊膏的润滑能力。
自动点胶机虽然拥有灵活性,但也带来了由于焊膏体积增加而导致成本增加和相应残留物增加的问题。
THR体积模型与合金类型、助焊剂密度以及焊膏中的金属重量百分比相关。
金属体积百分比、密度,以及焊膏减少因素可以利用计算机自动计算。
该模型还可以包含一个部分专门用于网板印刷工艺,向用户提供网板厚度、印刷压力、印刷速度和刮刀角度等信息。
使用这些参数,配合特定的孔尺寸和焊膏特性,来预测使用多少焊膏来充填PTH,(,锡膏在通孔内的填充系数)。
稍后将介绍焊膏通孔充填的重要性。
信息来源维库电子市场网()。