丰田生产方式TPS培训资料
(丰田管理)丰田生产方式(TPS)

(丰田管理)丰田生产方式(TPS)丰田生产方式(TPS)丰田生产方式(TPS)是提高企业生命力的一整套概念和方法的体系。
它是丰田公司通用的制造方法,其基本思想是“彻底杜绝浪费”,通过生产的整体化,追求产品制造的合理性以及品质至上的成本节约。
本书是丰田汽车公司前副社长大野耐一先生最经典的作品,它系统揭开了丰田公司卓越的秘密,涵盖其及时化(JIT)、自动化、看板方式、标准作业、精益化等等生产管理的各种理念。
它堪称是丰田核心竞争力的名著,也是全球生产管理的最为重要的标杆,成为国际通用的企业教科书。
丰田的生产管理现在取得了巨大的成果,利润超出世界三大汽车厂利润的总和,竞争力最强。
丰田生产方式已经不仅仅是一个管理方法,更变成了一种企业文化。
——张瑞敏(海尔集团CEO)学习丰田精益生产是格兰仕的必由之路。
——梁昭贤(格兰仕总裁)为提升自主创新力而学习丰田生产方式。
——罗振璧(清华大学教授、博士生导师)我们虚心地研究TPS,最终极的愿望是将来超越丰田生产模式,创造、振兴自己的CPS(ChinaProductionSystem——中国生产模式)——齐二石(天津大学管理学院院长、教授丰田汽车公司在国际市场竞争中成功的秘诀之一,就是开创了一种全新的管理模式——丰田生产方式(TPS)——程远(《中国青年报》汽车周刊主编、国务院国家突出贡献专家没有精益,戴尔不可能超越IBM;没有精益,丰田不可能取代通用。
——詹姆斯?沃麦克(《改变世界的机器》作者)一汽三十多年对丰田生产方式的推广应用,使TPS的核心实质及灵魂已在我头脑里生根、开花、结果,它不但改变了我的价值观和经营理念,而且运用TPS取得了可喜成果和质的飞跃。
实践证明,TPS是企业在激烈市场竞争中取胜的法宝。
——汪玉春(一汽大众汽车有限公司轿车厂厂长)丰田生产方式使得丰田汽车在全世界获得成功。
从更高的意义上说,丰田生产方式代表了一种崇尚创新的企业文化和企业精神。
——孟嗣宗(中国汽车工程学会汽车技术教育分会理事长,上汽教育基金会副理事长兼秘书长,上海汽车集团工业培训中心校长)多年以来,丰田生产方式被奉为汽车生产制造宝典真经,理论界研究,实业界效仿。
TPS(JIT) 生产方式培训资料

TPS(JIT) 生产方式培训资料TPS(JIT)生产方式培训资料(一)本文旨在介绍TPS(JIT)生产方式的培训资料,包括其基本概念、主要原则以及实施过程。
希望通过本文的阅读,能让读者对TPS(JIT)生产方式有更深入的了解,并能够在实践中应用这一生产方式,提高生产效率和质量。
一、什么是TPS(JIT)生产方式TPS(Toyota Production System,丰田生产方式),又称JIT (Just-in-Time)生产方式,是丰田汽车公司发展而来的生产方式,其核心理念是"同时制造,零库存"。
其主要目标是通过消除浪费、优化生产流程,以实现缩短生产周期、减少库存、提高质量和降低成本等效果。
二、TPS(JIT)生产方式的原则1. 浪费的消除TPS(JIT)生产方式强调消除各类浪费,包括过产、等待、运输、库存、过程中的损耗和不合格品等。
通过减少这些浪费,企业可以提高生产效率、降低成本、优化资源利用。
2. 拉动式生产TPS(JIT)生产方式以顾客需求为导向,采取拉动式生产,即按照订单来生产产品,避免过去的"推动式"生产方式中产生的过剩和库存。
拉动式生产可以提高生产的敏捷性,降低产出的滞后性。
3. 灵活性和变动适应性TPS(JIT)生产方式要求企业具备灵活性和变动适应性,即能够及时调整生产线,以适应市场需求的快速变化。
通过灵活的生产方式,企业可以减少因生产周期长、库存过多而导致的资源浪费。
4. 经济批量和小批量化生产TPS(JIT)生产方式倡导经济批量和小批量化生产,通过灵活的生产线布局和合理的生产计划,实现生产成本的最优化。
5. 高质量和持续改进TPS(JIT)生产方式注重产品质量,强调全员参与质量控制,通过改善生产工艺,提高产品质量。
同时,TPS(JIT)生产方式倡导持续改进,不断挑战和提高自身的生产能力和竞争力。
三、TPS(JIT)生产方式的实施过程1. 价值流分析价值流分析是TPS(JIT)生产方式实施的基础,通过对生产过程中每个环节的价值创造和浪费进行分析,找出存在的问题,确定改进方向。
TPS初级培训资料

详细描述
通过分析生产流程中的瓶颈环节,制定相应的改善措施,优化生产流程,实现 生产平衡,提高整体生产效率。
减少浪费活动
总结词
降低生产成本,提高资源利用效率。
详细描述
通过减少浪费活动,降低生产成本,提高资源利用效率。具体措施包括减少不良 品、减少库存、优化物流等。
05
TPS初级培训效果评估
TPS的五大原则
全员参与
TPS强调全员参与,包括管理层和一 线员工,每个人都应该对设备的维护 和保养负责。
目视管理
TPS采用目视管理方法,通过使用图 表、看板等工具,使设备管理信息一 目了然。
01
02
预防维修
TPS注重预防维修,通过定期检查和 预测设备故障,采取措施避免设备故 障的发生。
03
持续改进
TPS鼓励持续改进,不断优化设备维 护和保养的流程和方法,提高设备的 综合效率。
05
04
流程管理
TPS注重流程管理,通过制定和维护设 备管理流程,确保设备的维护和保养 工作有序进行。
TPS的三大支柱
自主维护
TPS的自主维护是指员工对自己 负责的设备进行日常检查、清洁、
调整和润滑等维护工作,确保设 备正常运行。
备异常情况。
维护与保养
根据设备特点和运行情 况,制定相应的维护和 保养计划,定期进行保
养和维修。
备件管理
建立备件管理制度,储 备必要的备件和易损件, 确保维修工作的及时性
和有效性。
快速换模
01
02
03
04
快速换模
通过优化换模流程和提高换模 效率,缩短换模时间,提高设
备利用率和生产效率。
丰田精益生产方式完整培训资料(PDF 200页)
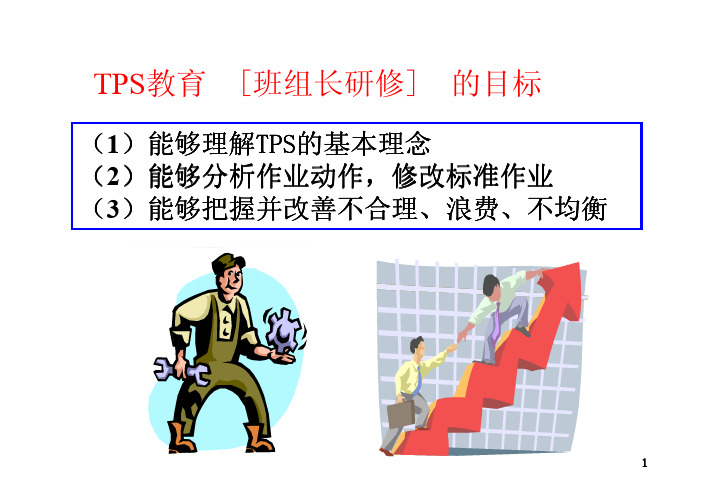
必要量: 100个/日
实际生产性
10人 120个/日 20个是过剩产品
8人 100个/日=改善
12
77.. 稼稼动动率率与与可可动动率率的的区区别别
稼动率 需求数量与班内时间的生产能力之比 →可能大于或小于100%
可动率 表示某机器能正常运转状态的百分比 →保持100%是理想状态
13
88.. 整整体体效效率率高高于于局局部部效效率率
过剩生产,库存增加, 导致问题被掩盖。应该 改善的课题就不明确
(2) 允许生产过剩就会产生新的浪费
・货架、货物箱的增加 ・搬运车、叉车的增加 ・新建仓库
产生新的浪费
成本无法降低
11
66.. 表表面面生生产产性性与与实实际际生生产产性性的的区区别别
表面生产性
10人 100个/日 10人 120个/日
17
『工程的流程化』 模拟游戏 ①
①理解制造方法改变成本的事实 ②体验流程化、逐个生产制造方法
18
Ⅱ.丰田生产方式的源流(Video)
19
Ⅲ. 丰田生产方式
如何将“顾客第一” 具体化
2大支柱
J.I.T
适时地
适时地、低成本地 生产高品质产品
资金短缺时 如何快速回收
彻底消除 “不合理、浪费、不均衡”
赛艇
14
轴承工厂的例子
超大型轴承
B Dd
内轮 1个 50万日元
内轮加工生产线
外轮加工生产线
15
99.. 提提高高劳劳动动生生产产性性与与强强化化劳劳动动的的区区别别
提高劳动生产性 将“動”转化为“働”
浪费 動 働
强化劳动
不改善而加强劳动强度
浪费
動 働
10.TPS基础知识培训

问题点
3 、 搬
石子(问题点)
部品欠品 设备故障
(石:问题点) 计划未完
运
不良发生
的
浪
问题点
费
4 、 等 待 的 浪 费
加工的浪费一方面指在产品本身没有要求或要求不高时,却采取 了高于标准的加工而造成的浪费,另一方面是不合理的作业编排而造 成的浪费。
5 、 加 工 的 浪 费
6、动作的浪费
7 、 不 良 品 的 浪 费
根据后工序的领取状况推进工序的进展的机制。
平准化 拉式生产
一个流
目的:保证质量,缩短生产周期
前提条件
种类平准化 数量平准化
安排一上午的学习计划,半天全学外语和半天四小时
例 各学外语、数学、历史及语文的效果肯定是不一样的,
后者明显要好些。
非平准(不均衡)
AAAAAAAABBBBBBBCCCCC
平准化(均衡化)
必须根除浪费
生产过剩的浪费是最大的浪费
包含2层含义:
多了、快 了反而不
好
· 在规定的时间内多生产 · 提前生产出来
3 TPS的两大支柱
一、准时化
二、自働化
减少浪费、降低成本
准
自
时
働
化
化
持续改进
丰田佐吉的自働制造思想
TPS的基本思想是把发明王丰田佐吉的自働制 造思想与丰田汽车的实际创业者丰田喜一郎的 准时化思想结合起来,由大野耐一等人在生产 现场逐一具体化的产物。这种方式已被丰田公 司应用到一切经营领域,引起了全世界生产企 业的瞩目。
3-6 自働化
1、带人字旁的自働化
自働化:带有自动停止装置的机械(自停装 置、满负荷系统及防错装置),从而使机械具有 了人的智慧。
TPS初级培训资料

保持持续改进。TPS推行 是一个持续改进的过程 ,必须保持持续改进的 态度和行动,不断提高 生产水平和管理水平。
加强沟通和协调。TPS推 行需要各部门之间的沟 通和协调,必须建立良 好的沟通和协调机制, 以保证推行工作的顺利 进行。
推行tps的积极意义
意义一
提高生产效率。TPS推行可以优化生产流程和管理 模式,提高生产效率和管理效率。
tps初级培训资料
xx年xx月xx日
contents
目录
• tps理论介绍 • tps标准与规范 • tps推行与实施 • tps现场管理 • tps与生产效率 • tps与质量管理 • tps与成本控制 • tps与员工管理
01
tps理论介绍
tps定义
定义
TPS(Total Productive Maintenance,全面生产维护)是 一种以提高设备综合效率为目标,以全系统的预防维修为过 程,以全体人员参与为基础的设备保养和维修管理体系。
07
tps与成本控制
tps对成本控制的作用
优化生产过程
通过推广TPS,企业可以优化生产过程,提高生 产效率和产品质量,降低生产成本。
提高生产效益
TPS注重生产均衡和同步化,可以减少生产浪费 和库存积压,提高生产效益。
提升管理水平
TPS强调全员参与和持续改进,有助于提升企业 的管理水平,增强企业的竞争力。
重视员工安全和健康
TPS注重员工的安全和健康,要求员工遵守安全规定和健康标准,以确保员工的生命安全 和身体健康。
以员工为中心的人本管理理念
01
以人为本
以员工为中心,尊重员工的个性和需求,注重员工的职业发展和生活
质量。
02
丰田生产方式(TPS)基础知识20200428

丰田生产方式(TPS)基础知识1锐意进取目录一.历史背景二.消费市场与车厂三.汽车制造工序概要四追求目标.TPS五.企业目的六.标准作业2锐意进取一.历史背景经济的出发点在于生产(制造行业的力量⇔硬件⇔软件)丰田佐吉(自動化)伏得1世(伏得系统) T型伏得丰田喜一郎(Just in time)在美国的计划性种类的増大(追求设备的生产性提高)战败从新复兴丰田生产方式的誕生批量生产方式的確立現在日本的生产方式的引进石油危机冲击NUMMI(GM)包括向异行业的所有部门都在横向展开中大野耐一(在提高生产性上追求人的附带价值)3锐意进取③最近对汽车的市场要求1)顾客的嗜好多样化※高性能化涡轮、增压器、4WS、4WD※高档化铝合金轮圈、空气拢流器、缓冲器2)高品质(感性时代)※车体的组装喷漆二.消费市场与车厂④汽车商的对策涂饰涂漆皮肤※车的触感座椅触感、坐坐席时的感觉1)因貿易摩擦而引起的总量陷入僵局走向海外2)国内市场的竞争/有魅力的商品开发/向高级车化移行3)向往海外名牌产品/通过进一步推进合理化/减低成本4)各国追赶4锐意进取(粗形材)四.TPS追求目标◆通过彻底排除浪费降低成本◆简洁保证并维持制造品质◆以尊重人格、互相信赖、互相援助为基础使全体成员都能发挥能力的工作气氛◆能够及时对应市场流动性变化的体制6锐意进取制造方法和成本制造的流程1号机械1322号机械1323号机械1324号机械132手工作业机械作业时间15″5″15″5″10″10″20″10″1号机械1422号机械33号机械124号机械手工作业机械作业时间15″5″15″5″10″10″20″10″439锐意进取不同方法不同变化半成品库存A完成品作业员B作业员A材料半成品库存B作业员C半成品库存B半成品库存A10锐意进取不同方法不同成本ABC(1)一个一个同步(2)利用节拍来控制生产材料完成品Tact time Tact time==劳动时间劳动时间//一班必要数必要数//一班11锐意进取六.标准作业标准作业的定义标准作业的目的(1)制造方法明确化制造方法决定管理的主杆,因此需考虑到品质、成本、安全、『以人为中心并以合理的顺序减少浪费提高效率的生产方式』(1)以人的动作为中心(2)重复作业再决定方法。
推进丰田生产方式学习手册培训资料

推进丰田生产方式学习手册培训资料欢迎参加丰田生产方式学习手册培训!本资料将为您介绍丰田生产方式的核心概念、原则和实施方法,帮助您了解并学习如何推进丰田生产方式。
一、丰田生产方式简介丰田生产方式(The Toyota Production System,简称TPS)是日本丰田汽车公司开发的一种生产方式和管理哲学,旨在通过高效率、低成本、高质量的生产,实现持续改进和优化。
TPS 的核心理念是以顾客价值为导向,通过减少浪费、精益求精、标准化和人员参与等手段,提升生产效率和质量。
二、丰田生产方式的核心原则1. 客户导向:满足顾客需求,提供高质量的产品和服务。
2. 流程优化:通过精益生产原则,减少无价值的活动和浪费,优化生产流程。
3. 拖拉生产:产品按需生产,减少库存和过剩产能。
4. 标准化:建立并遵循一套标准化步骤,确保产品质量和流程一致。
5. 持续改进:通过员工参与和团队合作,不断推动流程改进和创新。
三、丰田生产方式的实施方法1. 价值流映射:通过绘制流程图和识别价值流中的活动,找出并改进非价值增添环节,提高效率。
2. 加强质量控制:通过设立严格的质量标准和流程,减少产品缺陷和质量问题。
3. 即时反馈和改进:建立快速反馈机制,及时处理问题和改进流程,避免错误重复出现。
4. 小批量生产:减少库存和过剩产能,让生产线更灵活,提高响应速度。
5. 绩效管理:通过设立目标、指标和奖惩机制,激励员工参与和个人成长,推动全员质量意识。
四、丰田生产方式的学习方法1. 系统培训:参与培训课程,学习丰田生产方式的基本概念、原则和实施方法。
2. 实际操作:通过参观丰田工厂,近距离了解丰田生产方式的运作,并实际操作相关工具和方法。
3. 实践应用:在实际工作中,通过应用丰田生产方式,找出问题和改进的机会,并团队合作推动改变。
4. 持续学习:不断深入学习丰田生产方式的相关书籍和案例,与业内专家和同行交流,不断提升自己的理解和应用能力。
TPS相关培训资料
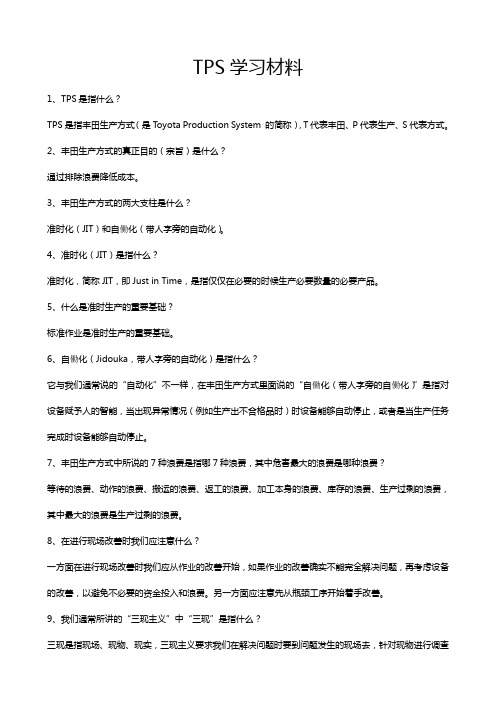
TPS学习材料1、TPS是指什么?TPS是指丰田生产方式(是Toyota Production System 的简称),T代表丰田、P代表生产、S代表方式。
2、丰田生产方式的真正目的(宗旨)是什么?通过排除浪费降低成本。
3、丰田生产方式的两大支柱是什么?准时化(JIT)和自働化(带人字旁的自动化)。
4、准时化(JIT)是指什么?准时化,简称JIT,即Just in Time,是指仅仅在必要的时候生产必要数量的必要产品。
5、什么是准时生产的重要基础?标准作业是准时生产的重要基础。
6、自働化(Jidouka,带人字旁的自动化)是指什么?它与我们通常说的“自动化”不一样,在丰田生产方式里面说的“自働化(带人字旁的自働化)”是指对设备赋予人的智能,当出现异常情况(例如生产出不合格品时)时设备能够自动停止,或者是当生产任务完成时设备能够自动停止。
7、丰田生产方式中所说的7种浪费是指哪7种浪费,其中危害最大的浪费是哪种浪费?等待的浪费、动作的浪费、搬运的浪费、返工的浪费、加工本身的浪费、库存的浪费、生产过剩的浪费,其中最大的浪费是生产过剩的浪费。
8、在进行现场改善时我们应注意什么?一方面在进行现场改善时我们应从作业的改善开始,如果作业的改善确实不能完全解决问题,再考虑设备的改善,以避免不必要的资金投入和浪费。
另一方面应注意先从瓶颈工序开始着手改善。
9、我们通常所讲的“三现主义”中“三现”是指什么?三现是指现场、现物、现实,三现主义要求我们在解决问题时要到问题发生的现场去,针对现物进行调查和分析,掌握现状,制定解决问题的对策,杜绝仅仅依靠主观想象进行判断。
10、丰田生产方式成功实施的前提条件是什么?全员参与改善是成功实施丰田生产方式的前提条件。
11、推行TPS的作用是什么?①彻底排除现场浪费,降低成本;②过程周期缩短带来资本效率提高和现金流增大;③企业内潜在能力的有效利用带来机会额度的扩大,经营资源的扩大;④人才锻造体系的确立和人才群体的培养,使企业确立持续竞争优势。
TS丰田生产方式培训手册页

TPS(Toyota Production System)丰田生产方式培训手册2007年7月第一部总体系——丰田生产方式的构思第一章丰田生产方式的体系本章目的丰田生产方式由丰田汽车公司开发、推广,1973年石油危机之后被众多的日本公司所采用。
该生产方式的主要目的是通过改善活动消除隐藏在企业里的种种浪费现象,进而降低成本。
这种生产方式,是继泰勒生产方式(科学管理法)和福特生产方式(大量装配线方式)之后诞生的生产方式。
一、生产方式的目的(一)、最终目的是通过降低生产成本产生效益丰田生产方式是生产产品的合理方法。
这里的“合理”,是指它对整个公司产生效益这个最终目的来说是行之有效的方法。
为了实现这个最终目的,丰田生产方式将降低成本作为基本的第一位的目标。
降低成本的目标,即提高生产率的目标。
成本从本质上来说,是指为了实现利润应该从销售额中扣除过去、现在以及将来的所有的现金支出。
所以,丰田生产方式中所说的成本,不仅仅是制造成本。
而且还包括销售费用、一般管理费用以及财务费用。
(二)、消除制造过剩的浪费降低成本好途径坏途径图1.1 消除浪费降低成本的过程丰田生产方式,主要着眼于消除浪费降低成本。
我们按图1.1加以说明。
制造现场的浪费,第一层次是过剩的生产要素的存在。
第二层次是制造过剩的浪费。
第三层次是过剩的库存的浪费。
第四层次是1、如果库存在现场容纳不下,就要修建多余的仓库;2、雇佣搬运工将库存运到仓库(搬运的浪费);3、给每位搬运工购买一台叉车;4、为了防止产品在库房中锈蚀和管理库存,就必须增加人员;5、为了随时掌握库存的数量,管理部门需要相当数量的工时;6、需要用计算机管理库存的人员。
这四个层次的浪费存在递进关系。
所有这些第一层次、第二层次、第三层次、第四层次的浪费,都会增加直接材料费、直接劳务费、折旧费等间接经费、一般管理费,从而增大成本。
削减浪费应该先从第一层次开始,第一层次的重点为----削减过剩的人员。
- 1、下载文档前请自行甄别文档内容的完整性,平台不提供额外的编辑、内容补充、找答案等附加服务。
- 2、"仅部分预览"的文档,不可在线预览部分如存在完整性等问题,可反馈申请退款(可完整预览的文档不适用该条件!)。
- 3、如文档侵犯您的权益,请联系客服反馈,我们会尽快为您处理(人工客服工作时间:9:00-18:30)。
去半成品库
磨床 2m 磨床
67
5
铣床 2
磨床 4
10m 1
来自料堆
车床
15m 10
搓丝
1
8
8 3m 6 5m
磨床
7
1
5 10m
17m 9
2 13m
其他 设备
其他设备
11m 4
15m 3 车床
事例:作业范围
最大作业范围:使用的工具・部品要放在最大作业范围内
正常作业范围:经常使用的工具・部品要放在正常作业范围内
最佳作业范围:在最佳作业范围内进行组装作业
最佳作业范围
最大作业范围
最大作业范围
正常作业范围
正常作业范围
*人因工程(Human Factors),也称工效学、 人机工程(Human Engineering ,Ergonomics)
Ⅱ
A 反修
B 废品
C 成品
例 收垃圾桶——线路分析
房屋 房屋 房屋 房屋
垃
垃
垃
垃
圾
圾
圾
圾
桶
桶
桶
桶
4趟×4=16趟
例:物流工程
合理
不合理 不合理
车间内物流线路 车间内物流线路
例
重型机器工厂
起重机
机2 机5
手
推 车
起重机
机3
一般机器工厂
铸造车间
手推车
装配车间
总库 起重机
机4 机 轻型 1 机器厂
例
什么是丰田生产方式,就是丰田式工业工程。
(20世纪)五十年代全日本都在研究和学习美 国的工业工程这种赚钱的工具”
大野耐一
全日本都在学IE,但不是抄IE、copy美国人的IE。
TPS
IE
Total TPS
JMS
CPS
LP
IE→TPS,美国人将TPS概括为精益生产(LP)
3、精益生产(LP)的模式
TPS/LP = IE + 企业文化 = = 精益技术 + 精益文化
他们在做了大量的调查和对比后,认为日本 丰田汽车公司的生产方式是最适用于现代制造企业的一 种生产组织管理方式,称之为精益生产。它综合了大量 生产与单件生产方式的优点,力求在大量生产中实现多 品种和高质量产品的低成本生产。
可怕的对比数据
时间
项目
美国通用
劳动生产率 生产率是日本
20世纪50年代
10倍
20世纪末
推动了世界汽车工业的进步——成为必不可少的生活用品
二、中国的工业工程---管理创新技术体系
CIE—Chinese Industrial Engineering定义
用分析、设计、控制、评价等 工程技术来提高效率、降低成本、提高质 量,从而提高生产力和管理竞争力的工程 技术方法体系,不仅用于制造业,还用于 多种产业之中。
例
IE 技术体系
EI主要技术体系
设计改善类
控制管理类
分析评价类
工作研究 物流工程 人因工程
…
生产计划与 控制 质量管理 成本控制 信息控制
工程经济 可靠性工 程 评价技术
IE是关于设计改善创新评价的技术
例:工作研究--轴套检验(每班200件)
Ф 100±0.1
Ф 99.9
I
Ф 100.1
工业工程与精益生产管理
一,引言
卡尔·本茨 Karl Benz 德国 1844-1929
亨利·福特 Henry ford 美国 1863-1947
在本茨之后,汽车价钱昂贵和产量偏低已经成为限制汽 车业发展的桎梏,而在大洋的另一端,汽车史上另一位划 时代人物亨利·福特登场了。
BC
A
D
BC
A
D
J
E… J
E
I HGF
I HGF
Q2 m1
A
mn
……
Qn
J
大幅度地降低汽车成本 T型车刚出现的1908年,价格是$ 850,1926年为$290
社会需求的猛增,又进一步刺激了汽车工业的飞速发展
1903年—第一年生产汽车—产量1700辆 1923年—本国总产量达190万辆,占世界汽车总产量 44%
劳动生产率大幅度提高 1908年—514分钟(8.56小时)/车 1914年—流水生产线1.19分钟/车
操作者与操作器的几何关系研究与设计: 宇航器座舱设计、汽车(坦克)驾驶室设计; 运动员训练,家庭布置设计; 颜色管理设计(车间、城市、环境等); 饭店布置设计(麦当劳、中餐店等); 运动员训练;
三、精益生产的概念及其体系
1、什么是精益生产(Lean Production)
精益生产就是及时制造,消灭故障,消除 一切浪费,向零缺陷、零库存进军。它是美国麻省理工 学院在一项名为“国际汽车计划”的研究项目中提出来 的。
3
车床 1
其他 设备
例:人因工程
a的台面高度为1050~ 1150毫米,适用于精密工 作,靠肘支承的工作(如 书写、画图等);
b的台面高度为1130 毫米,虎心钳固定在工作 台上的高度;
c的台面高度为950~ 1000毫米,适用于要求灵 巧的工作,轻手工工作 (如包装、安装等);
d的台面高度为800~ 950毫米,适用于要求用劲 大的工作(如刨床,重的 钳工工作等)。
4、丰田屋及其技术体系
• 一大目标,两大支柱和一大基础
目标
准
自
时
働
化
化
JIT
改善与连续改善
(3)两大支柱
准时化
拉动生产
JIT 看板管理
均衡生产 节 拍 流程 设备质量 快速换模
目视管理 区域编码 工序编号 在制品单 电子显示
物流系统 平面布置 流程设计 工位器具 搬运方法
标准作业 操作方法 工作顺序 时间标准 工具标准
自働化和可视化的例子
工序延时停线,采取对策进行处理
呼叫灯
(节奏控制)
定位停止线
(4)注重企业文化建设
–核心:价值观→凝聚力 –IE+精益文化+本企业精益管理理念
• 危机文化:居安思危,拒绝歌功颂德。
• 问题意识:合理化建议制。
• 人本文化:德鲁克说:“企业唯一的资源就是
人均产量/年 人均创利
6辆 1400美元
日本丰田
55辆 14000美元
20世纪90年代
平均库存 资金周转
2周 6-7次/年
2小时 100次/每年
2、精益生产(LP)的本质
IE 工业工程 (美国)
TPS 丰田生产方式
(日本)
==
LP 精益生产 (国际)
IE---Industrial Engineering TPS----Toyota Production System
目标
准时化
自働化
拉动生产
看板管理
均衡生产 节拍、流程
设备与生产线可 靠性
快速换模
目视管理
区域 工序 编号 编号 在制品 电子
显示
全面 质量 管理
异常 管理
消除 浪费
物流系统
平面 流程设
布置
计
工位器具 搬运 方法
标准作业
操作方法 工位顺 序
时
工
间
具
改善与连续改善
例 可视化控制——物料移动
在制品物流拉动看板系统