车身外观间隙面差设计定义规范
(吉利)间隙与面差DTS设计规范

2.0
+0.5 - 0.5
+0.5
0.0 - 0.0
5.0
+1.0 - 1.0
+0.5
-1.0 -0.5
+0.0
-0.5 - 1.0
+1.0
-1.0- 1.0
22
T/Lamp X T/Gate
23
T/Lamp X Bumper
24
T/Gate garnish X Bumper
25
T/Gate garnish X Bumper
提取圆角根部的线 并投影到角度为0
的面上
NL1 Gap & Offset - Overall
4.做与已有件等距离包边
理论依据: 先把已知零件的面偏置Gap+R,再把Skin偏置R与前一个面 做出相交线,用交线Sweep出与偏置Skin垂直的面,将此面 偏置R,然后剪切倒角即可ll
3D数模和Skin间隙面差不一致的例子
Skin
3D数模
NL1 Gap & Offset - Overall
发生原因:
当翻边角度发生 改变时,最小间 隙也会随之改变; 数模间隙结果便 会与要求产生差 异.
NL1 Gap & Offset - Overall
二、间隙面差值的测量方法 1.间隙的测量方法
Depend on style
4
H/Lamp X Bumper
+0.5
3.0 - 0.5
5
Hood X H/Lamp
+1.0
5.0 - 0.0
6
Roof X W/shield
4.0 +1.0 - 1.0
车身外观间隙面差设计定义规范
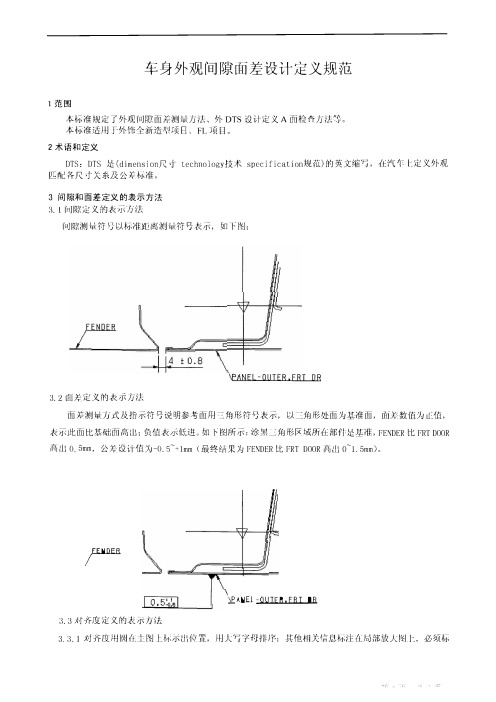
3间隙和面差定义的表示方法 :3. l ['Fl]隙定义的表示方法
问隙测量符号’以标准距离测量符号表示,如F图:
3. 2面主定义的表示方法
面差测量方式及指示符号说明参考面用三角形符号表示, 以三角形处面为基准面, 面茸j数值为一ti:值,
表示此面比基础面高山:负值表示低进。如F国所示:涂黑二角形区域所在部1!J:是基准,FENDER比FRT DOOR
接;2豆 浆?
卒
变, 交点到R 角内侧根部的距离作为两个面c l!X部件)的问隙, 间隙测量方法示意;如卜 :
y
I
(a)
( Lυ 、,,
4.1.3当夕阳见面在同 一 -适用平面内且两件的配合面中仅有一个零1'1'与本苓件外观面角度大于90度时, 以两
个外观R角面最短距离作为两个面(或部件)的间隙, 间隙测量方法示意如 r-.·:
f- 1. 5mmo
3.4基准的选取
基准j在取原则:1)车身开启件以:牛身骨架为基准:2)开启件Lj开启件之间以先安装部件
沟基准, 如前I j以后「J为基准、 费子板以前门为基准:3)总装支装件以东身为基准:4)叫个总装安装件
之间以尺、f易控制、同lj度比较好的1l)J基准, 同时尽量选抨大平面作为测量基准。 如前后人灯与前后保之
/t,、 a 、、,/
( 10 )
某车型间隙面差定义实例
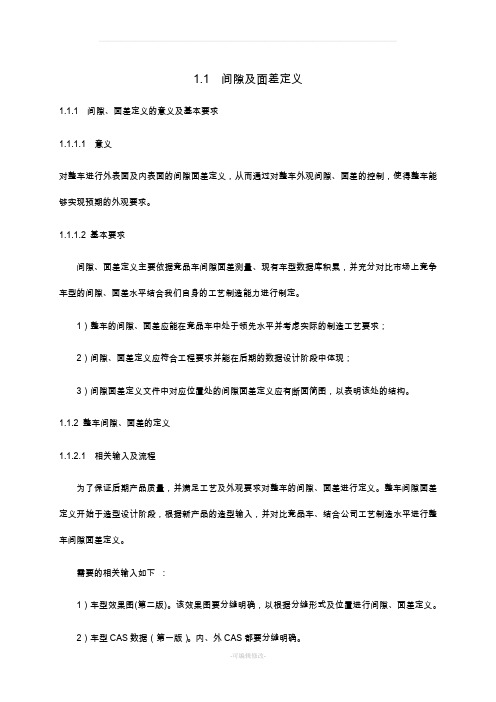
1.1 间隙及面差定义1.1.1 间隙、面差定义的意义及基本要求1.1.1.1 意义对整车进行外表面及内表面的间隙面差定义,从而通过对整车外观间隙、面差的控制,使得整车能够实现预期的外观要求。
1.1.1.2 基本要求间隙、面差定义主要依据竞品车间隙面差测量、现有车型数据库积累,并充分对比市场上竞争车型的间隙、面差水平结合我们自身的工艺制造能力进行制定。
1)整车的间隙、面差应能在竞品车中处于领先水平并考虑实际的制造工艺要求;2)间隙、面差定义应符合工程要求并能在后期的数据设计阶段中体现;3)间隙面差定义文件中对应位置处的间隙面差定义应有断面简图,以表明该处的结构。
1.1.2 整车间隙、面差的定义1.1.2.1 相关输入及流程为了保证后期产品质量,并满足工艺及外观要求对整车的间隙、面差进行定义。
整车间隙面差定义开始于造型设计阶段,根据新产品的造型输入,并对比竞品车、结合公司工艺制造水平进行整车间隙面差定义。
需要的相关输入如下:1)车型效果图(第二版)。
该效果图要分缝明确,以根据分缝形式及位置进行间隙、面差定义。
2)车型CAS数据(第一版)。
内、外CAS都要分缝明确。
3)竞品车间隙及面差分析报告。
应包括竞品车车身表面及内饰表面主要断面及搭接处的间隙、面差统计及分析。
该报告可以作为新车型间隙、面差定义的参考。
间隙、面差定义流程如下:通过上述输入,科室内完成的间隙面差的定义,并需要与相关部门一起对定义进行评审。
评审通过的定义需要在CAS及A面中体现。
后期三维数据的制作、工程车制造生产均要以此为标准。
间隙面差定义及控制流程见图1-1。
评审材料为PPT格式,实例见附录A-1。
图1-1 整车减息面差定义及控制流程图1.1.2.2 间隙、面差定义内容主要包括内饰表面及车身表面两大部分的间隙、面差定义。
1.1.2.2.1内饰表面间隙、面差定义由于内饰件普遍采用塑料成型,其尺寸、形状等受模具、塑料件本身材料特性、外界气候条件影响比较大。
某车型间隙面差定义实例

1.1 间隙及面差定义1.1.1 间隙、面差定义的意义及基本要求1.1.1.1 意义对整车进行外表面及内表面的间隙面差定义,从而通过对整车外观间隙、面差的控制,使得整车能够实现预期的外观要求。
1.1.1.2 基本要求间隙、面差定义主要依据竞品车间隙面差测量、现有车型数据库积累,并充分对比市场上竞争车型的间隙、面差水平结合我们自身的工艺制造能力进行制定。
1)整车的间隙、面差应能在竞品车中处于领先水平并考虑实际的制造工艺要求;2)间隙、面差定义应符合工程要求并能在后期的数据设计阶段中体现;3)间隙面差定义文件中对应位置处的间隙面差定义应有断面简图,以表明该处的结构。
1.1.2 整车间隙、面差的定义1.1.2.1 相关输入及流程为了保证后期产品质量,并满足工艺及外观要求对整车的间隙、面差进行定义。
整车间隙面差定义开始于造型设计阶段,根据新产品的造型输入,并对比竞品车、结合公司工艺制造水平进行整车间隙面差定义。
需要的相关输入如下:1)车型效果图(第二版)。
该效果图要分缝明确,以根据分缝形式及位置进行间隙、面差定义。
2)车型CAS数据(第一版)。
内、外CAS都要分缝明确。
3)竞品车间隙及面差分析报告。
应包括竞品车车身表面及内饰表面主要断面及搭接处的间隙、面差统计及分析。
该报告可以作为新车型间隙、面差定义的参考。
间隙、面差定义流程如下:通过上述输入,科室内完成的间隙面差的定义,并需要与相关部门一起对定义进行评审。
评审通过的定义需要在CAS及A面中体现。
后期三维数据的制作、工程车制造生产均要以此为标准。
间隙面差定义及控制流程见图1-1。
评审材料为PPT格式,实例见附录A-1。
图1-1 整车减息面差定义及控制流程图1.1.2.2 间隙、面差定义内容主要包括内饰表面及车身表面两大部分的间隙、面差定义。
1.1.2.2.1内饰表面间隙、面差定义由于内饰件普遍采用塑料成型,其尺寸、形状等受模具、塑料件本身材料特性、外界气候条件影响比较大。
车型间隙面差定义实例
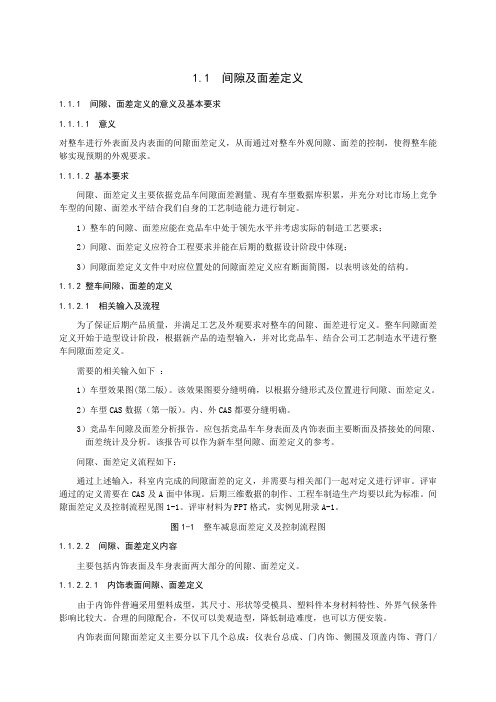
1.1 间隙及面差定义1.1.1 间隙、面差定义的意义及基本要求1.1.1.1 意义对整车进行外表面及内表面的间隙面差定义,从而通过对整车外观间隙、面差的控制,使得整车能够实现预期的外观要求。
1.1.1.2 基本要求间隙、面差定义主要依据竞品车间隙面差测量、现有车型数据库积累,并充分对比市场上竞争车型的间隙、面差水平结合我们自身的工艺制造能力进行制定。
1)整车的间隙、面差应能在竞品车中处于领先水平并考虑实际的制造工艺要求;2)间隙、面差定义应符合工程要求并能在后期的数据设计阶段中体现;3)间隙面差定义文件中对应位置处的间隙面差定义应有断面简图,以表明该处的结构。
1.1.2 整车间隙、面差的定义1.1.2.1 相关输入及流程为了保证后期产品质量,并满足工艺及外观要求对整车的间隙、面差进行定义。
整车间隙面差定义开始于造型设计阶段,根据新产品的造型输入,并对比竞品车、结合公司工艺制造水平进行整车间隙面差定义。
需要的相关输入如下:1)车型效果图(第二版)。
该效果图要分缝明确,以根据分缝形式及位置进行间隙、面差定义。
2)车型CAS数据(第一版)。
内、外CAS都要分缝明确。
3)竞品车间隙及面差分析报告。
应包括竞品车车身表面及内饰表面主要断面及搭接处的间隙、面差统计及分析。
该报告可以作为新车型间隙、面差定义的参考。
间隙、面差定义流程如下:通过上述输入,科室内完成的间隙面差的定义,并需要与相关部门一起对定义进行评审。
评审通过的定义需要在CAS及A面中体现。
后期三维数据的制作、工程车制造生产均要以此为标准。
间隙面差定义及控制流程见图1-1。
评审材料为PPT格式,实例见附录A-1。
图1-1 整车减息面差定义及控制流程图1.1.2.2 间隙、面差定义内容主要包括内饰表面及车身表面两大部分的间隙、面差定义。
1.1.2.2.1内饰表面间隙、面差定义由于内饰件普遍采用塑料成型,其尺寸、形状等受模具、塑料件本身材料特性、外界气候条件影响比较大。
(吉利)整车部设计手册-间隙面差
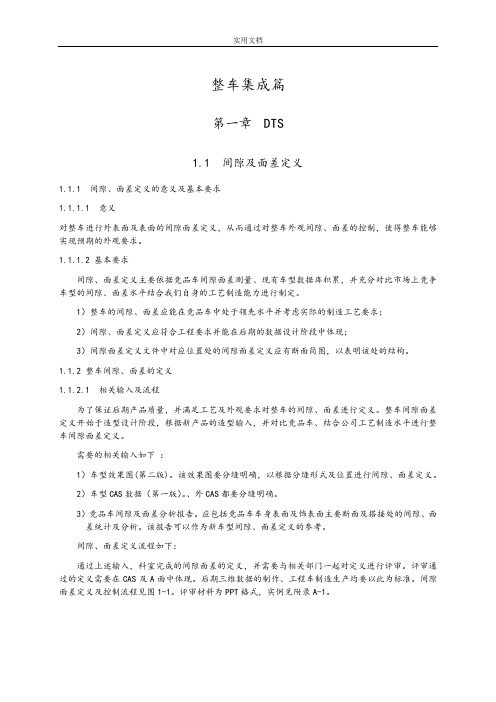
整车集成篇第一章 DTS1.1 间隙及面差定义1.1.1 间隙、面差定义的意义及基本要求1.1.1.1 意义对整车进行外表面及表面的间隙面差定义,从而通过对整车外观间隙、面差的控制,使得整车能够实现预期的外观要求。
1.1.1.2 基本要求间隙、面差定义主要依据竞品车间隙面差测量、现有车型数据库积累,并充分对比市场上竞争车型的间隙、面差水平结合我们自身的工艺制造能力进行制定。
1)整车的间隙、面差应能在竞品车中处于领先水平并考虑实际的制造工艺要求;2)间隙、面差定义应符合工程要求并能在后期的数据设计阶段中体现;3)间隙面差定义文件中对应位置处的间隙面差定义应有断面简图,以表明该处的结构。
1.1.2 整车间隙、面差的定义1.1.2.1 相关输入及流程为了保证后期产品质量,并满足工艺及外观要求对整车的间隙、面差进行定义。
整车间隙面差定义开始于造型设计阶段,根据新产品的造型输入,并对比竞品车、结合公司工艺制造水平进行整车间隙面差定义。
需要的相关输入如下:1)车型效果图(第二版)。
该效果图要分缝明确,以根据分缝形式及位置进行间隙、面差定义。
2)车型CAS数据(第一版)。
、外CAS都要分缝明确。
3)竞品车间隙及面差分析报告。
应包括竞品车车身表面及饰表面主要断面及搭接处的间隙、面差统计及分析。
该报告可以作为新车型间隙、面差定义的参考。
间隙、面差定义流程如下:通过上述输入,科室完成的间隙面差的定义,并需要与相关部门一起对定义进行评审。
评审通过的定义需要在CAS及A面中体现。
后期三维数据的制作、工程车制造生产均要以此为标准。
间隙面差定义及控制流程见图1-1。
评审材料为PPT格式,实例见附录A-1。
图1-1 整车减息面差定义及控制流程图1.1.2.2 间隙、面差定义容主要包括饰表面及车身表面两大部分的间隙、面差定义。
1.1.2.2.1饰表面间隙、面差定义由于饰件普遍采用塑料成型,其尺寸、形状等受模具、塑料件本身材料特性、外界气候条件影响比较大。
某车型间隙面差定义实例
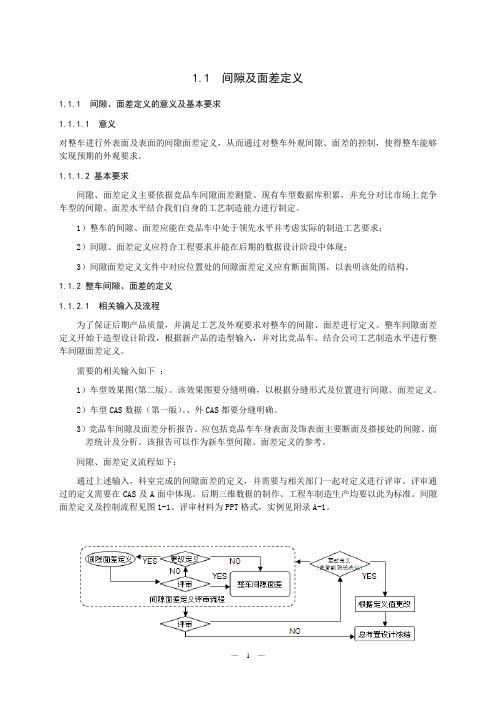
1.1 间隙及面差定义1.1.1 间隙、面差定义的意义及基本要求1.1.1.1 意义对整车进行外表面及表面的间隙面差定义,从而通过对整车外观间隙、面差的控制,使得整车能够实现预期的外观要求。
1.1.1.2 基本要求间隙、面差定义主要依据竞品车间隙面差测量、现有车型数据库积累,并充分对比市场上竞争车型的间隙、面差水平结合我们自身的工艺制造能力进行制定。
1)整车的间隙、面差应能在竞品车中处于领先水平并考虑实际的制造工艺要求;2)间隙、面差定义应符合工程要求并能在后期的数据设计阶段中体现;3)间隙面差定义文件中对应位置处的间隙面差定义应有断面简图,以表明该处的结构。
1.1.2 整车间隙、面差的定义1.1.2.1 相关输入及流程为了保证后期产品质量,并满足工艺及外观要求对整车的间隙、面差进行定义。
整车间隙面差定义开始于造型设计阶段,根据新产品的造型输入,并对比竞品车、结合公司工艺制造水平进行整车间隙面差定义。
需要的相关输入如下:1)车型效果图(第二版)。
该效果图要分缝明确,以根据分缝形式及位置进行间隙、面差定义。
2)车型CAS数据(第一版)。
、外CAS都要分缝明确。
3)竞品车间隙及面差分析报告。
应包括竞品车车身表面及饰表面主要断面及搭接处的间隙、面差统计及分析。
该报告可以作为新车型间隙、面差定义的参考。
间隙、面差定义流程如下:通过上述输入,科室完成的间隙面差的定义,并需要与相关部门一起对定义进行评审。
评审通过的定义需要在CAS及A面中体现。
后期三维数据的制作、工程车制造生产均要以此为标准。
间隙面差定义及控制流程见图1-1。
评审材料为PPT格式,实例见附录A-1。
图1-1 整车减息面差定义及控制流程图1.1.2.2 间隙、面差定义容主要包括饰表面及车身表面两大部分的间隙、面差定义。
1.1.2.2.1饰表面间隙、面差定义由于饰件普遍采用塑料成型,其尺寸、形状等受模具、塑料件本身材料特性、外界气候条件影响比较大。
汽车车身外表面DTS定义

NO.项目责任人间隙 5.0 1.5 3.0 2.02 1.0 5.0间隙偏差±1.0±1.0±1.0±1.0±10/-0.8±1.0平行性 1.0 1.0 1.0 1.0 1.0— 1.0间隙左右差--------111—1面差造型特征造型特征造型特征造型特征造型特征造型特征造型特征面差偏差--------—————一致性--------—————其它前格栅圆角由造型定义前舱盖R1.05前保险杠及格栅圆角由造型定义前组合灯R2前格栅R角造型特征前组合灯R2前保险杠造型特征前雾灯R2前保险杠R造型特征前组合灯R2翼子板R2机舱盖R1.05前组合灯R2参考车型5 123前舱盖前格栅略图4前格栅前保险杠前组合灯前格栅前组合灯翼子板前组合灯前保险杠7位置前雾灯前保险杠/雾灯装饰板6前组合灯机舱盖2734615NO.项目责任人间隙0.5 4.0 2.5 6.0 6.0 5.0 5.0间隙偏差 1.0/0±1.0±0.8±1±1±1.5±1.5平行性---- 1.0 1.0 1.0 1.0 1.5 1.5间隙左右差----1—————面差-0.5-0.50.0造型特征-4.0以造型为准(前门低≥2.0)以造型为准(前门低≥2.0)面差偏差0.5/-1.00.5/-1.0±0.5—±0.5——一致性———————其它保险杠R1.5翼子板R1.5前舱盖R1.05翼子板R2.0A柱R2.5翼子板R1.5A柱R3前风窗玻璃R1顶盖R3前风窗玻璃R1前门R1.1侧围R3前门X方向235mm内R1.4过渡长度3mm到后端R1.1,A柱R4.0参考车型14A柱前风窗玻璃129略图13侧围前门A柱前门顶盖前风窗玻璃前舱盖翼子板位置11A柱翼子板10前保险杠翼子板8141381011129柱间隙翼子板面差NO.项目责任人间隙 5.0 2.57.0 5.07.0 5.0 5.0间隙偏差±1.5±1.0±1.5±1.5±1.5±1.5±1.5平行性 1.5 1.0 1.5 1.5 1.5 1.5 1.5间隙左右差— 1.0—————面差00以造型为准(前门低≥2.0)0以造型为准(≥2.0)0以造型为准(≥2.0)面差偏差0/-1.0±0.5—0/-1.0—0/-1.0—一致性1——1———其它前门R1.4翼子板R2.0翼子板R2.0侧围门槛R2.5前门X方向235mm内R1.4过渡长度3mm到后端R1.1侧围门槛R5.0前门R1.1后门R2后门X方向195mm内R1.4过渡长度3mm到后端R1.1侧围门槛5.0侧窗玻璃密封条R3后门R1.1后门X方向127mm内R1.4过渡长度3mm到后端R1.1侧围R4.0参考车型1620211815后门侧围19前门侧围门槛前门后门17翼子板侧围门槛略图位置侧窗玻璃后门后门侧围门槛前门翼子板15171618192120NO.项目责任人间隙 5.0 1.0 1.0 2.0 3.0 3.0 3.0间隙偏差±1.5 1.0/0 1.0/-0.8±1.0±1.0±1.0±1.0平行性 1.5---- 1.0 1.0 1.0 1.0 1.0间隙左右差—---- 1.0————面差0-0.5(保险杠低)造型定义以造型为准以造型为准以造型为准-0.5(加油口低)面差偏差0/-1.0±1.0————0.5/-1.0一致性—1—————其它后门R1.1侧围R4后侧围R3后保险杠由造型定义后组合灯R1.5侧围R3.0侧围造型特征侧窗R1.75侧围造型特征侧窗R1.75侧围造型特征侧窗R1.75加油口门R3.5侧围R3.0参考车型侧围侧窗后组合灯侧围28后门侧围2725略图侧围侧窗加油口门侧围侧围侧窗22位置232426后保险杠后侧围28仅右侧232726242225NO.项目责任人间隙 5.0 1.0 5.08.0 3.0 1.0铰链部位8.0,中部以运动校核为准间隙偏差±1.5 1.0/-0.8±1.5±2.0±1.0±1.0±2.5平行性 1.5 1.0 1.5 2.0 1.0 1.0 2.0间隙左右差 1.51 1.5 2.0 1.0——面差以造型为准,玻璃低于侧围≥1.5mm。
车身外观间隙面差设计定义规范
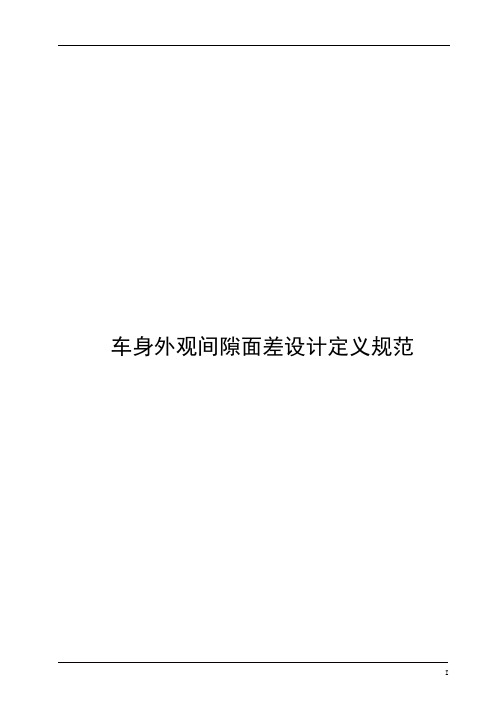
车身外观间隙面差设计定义规范I车身外观间隙面差设计定义规范1范围本标准规定了外观间隙面差测量方法、外DTS设计定义A面检查方法等。
本标准适用于外饰全新造型项目、FL项目。
2术语和定义DTS:DTS 是(dimension尺寸 technology技术 specification规范)的英文缩写,在汽车上定义外观匹配各尺寸关系及公差标准。
3 间隙和面差定义的表示方法3.1间隙定义的表示方法间隙测量符号以标准距离测量符号表示,如下图:3.2面差定义的表示方法面差测量方式及指示符号说明参考面用三角形符号表示,以三角形处面为基准面,面差数值为正值,表示此面比基础面高出;负值表示低进。
如下图所示:涂黑三角形区域所在部件是基准,FENDER比FRT DOOR 高出0.5mm,公差设计值为-0.5~+1mm(最终结果为FENDER比FRT DOOR高出0~1.5mm)。
3.3对齐度定义的表示方法3.3.1对齐度用圆在主图上标示出位置,用大写字母排序;其他相关信息标注在局部放大图上,必须标注基准:第1页共7页3.3.2“对齐度±1.5”概念:以FENDER为基准,FRT BUMPER的边界(R角切点)出入相对于FENDER不大于1.5mm。
3.4基准的选取基准选取原则:1)车身开启件以车身骨架为基准;2)开启件与开启件之间以先安装部件为基准,如前门以后门为基准、翼子板以前门为基准;3)总装安装件以车身为基准;4)两个总装安装件之间以尺寸易控制、刚度比较好的件为基准,同时尽量选择大平面作为测量基准。
如前后大灯与前后保之间,以灯为基准。
4 间隙和面差测量定义方法4.1间隙测量定义方法4.1.1当外观面在同一造型平面内且两件的配合面分别与本零件外观面角度小于等于90度时,以外观面的法线(法线与外观R角相交)之间的距离作为两个面(或部件)的间隙,间隙测量方法示意如下:(a)(b) (c)4.1.2当外观面在同一造型平面内且两件的配合面分别与本零件外观面角度大于90度时,外观R角接近(R 角差值小于等于1),以两个R角内侧根部的距离作为两个面(或部件)的间隙,外观R角差别较大(R角差值大于1),以较大R角的面(或部件)R角内侧根部做平行外观面的直线,与另一配合面(或部件)相交,交点到R角内侧根部的距离作为两个面(或部件)的间隙,间隙测量方法示意如下:第2页共7页(a ) (b)4.1.3当外观面在同一造型平面内且两件的配合面中仅有一个零件与本零件外观面角度大于90度时,以两个外观R角面最短距离作为两个面(或部件)的间隙,间隙测量方法示意如下:4.1.4当两个件的外观面不平行(不在一个造型面上)、且翻边也不平行时,以低进去的面(或部件)的内侧翻边面做平行面,使低进去零件的内侧面R 角根部与另外零件内侧面相交,以交点到低进去零件的内侧R 角根部的距离作为两个面(或部件)的间隙,间隙测量方法示意如下:(a ) (b) 4.2面差定义4.2.1当两个件的面具有共同的造型特征时,测量一边R 角低端(R角切点处)到另外基准面的垂直距离,(释放曲率延长基本面):4.2.2当两个件的基准面之间无造型顺延特征时,平行于基准面作另一面的相切面(以谁为基准,则将基准面偏移与另一个面相切),测量切点与基准面的距离(面差仅用于造型定义,实车匹配数值不测量), 如下图:第3页 共7页5 间隙和面差的标注规范5.1间隙与平度尺寸标注要求5.1.1所有间隙值、面差值及公差值均保留一位小数5.1.2间隙(GAP)尺寸标注时,如有品质要求,须注明平行差及左右差。
车身外观间隙、面差及其公差研究
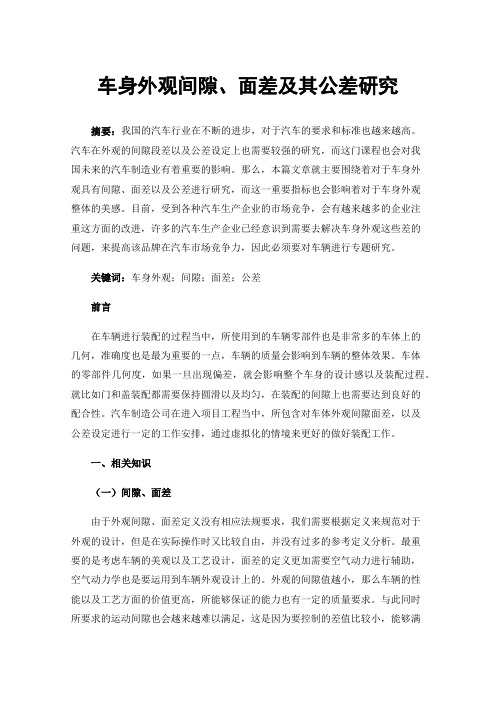
车身外观间隙、面差及其公差研究摘要:我国的汽车行业在不断的进步,对于汽车的要求和标准也越来越高。
汽车在外观的间隙段差以及公差设定上也需要较强的研究,而这门课程也会对我国未来的汽车制造业有着重要的影响。
那么,本篇文章就主要围绕着对于车身外观具有间隙、面差以及公差进行研究,而这一重要指标也会影响着对于车身外观整体的美感。
目前,受到各种汽车生产企业的市场竞争,会有越来越多的企业注重这方面的改进,许多的汽车生产企业已经意识到需要去解决车身外观这些差的问题,来提高该品牌在汽车市场竞争力,因此必须要对车辆进行专题研究。
关键词:车身外观;间隙;面差;公差前言在车辆进行装配的过程当中,所使用到的车辆零部件也是非常多的车体上的几何,准确度也是最为重要的一点,车辆的质量会影响到车辆的整体效果。
车体的零部件几何度,如果一旦出现偏差,就会影响整个车身的设计感以及装配过程。
就比如门和盖装配都需要保持圆滑以及均匀,在装配的间隙上也需要达到良好的配合性。
汽车制造公司在进入项目工程当中,所包含对车体外观间隙面差,以及公差设定进行一定的工作安排,通过虚拟化的情境来更好的做好装配工作。
一、相关知识(一)间隙、面差由于外观间隙、面差定义没有相应法规要求,我们需要根据定义来规范对于外观的设计,但是在实际操作时又比较自由,并没有过多的参考定义分析。
最重要的是考虑车辆的美观以及工艺设计,面差的定义更加需要空气动力进行辅助,空气动力学也是要运用到车辆外观设计上的。
外观的间隙值越小,那么车辆的性能以及工艺方面的价值更高,所能够保证的能力也有一定的质量要求。
与此同时所要求的运动间隙也会越来越难以满足,这是因为要控制的差值比较小,能够满足这样条件的工艺技术还比较高超。
对于前、后门之间的运动间隙也不能小于2.5mm,在制造公差方面也需要考虑间隙值,这个差值也不能太小,再满足各方面要求的情况下,也尽量满足公差值的需求。
所以对间隙值方面的要求还是比较高的。
汽车整车外观间隙、段差设计
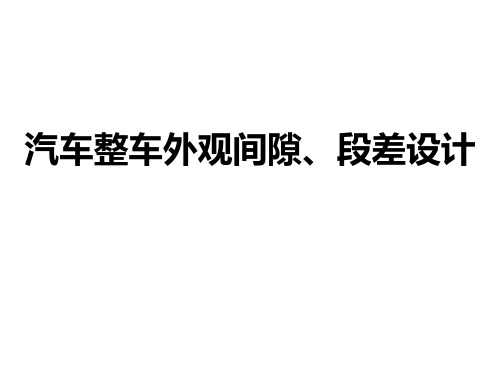
四、间隙、段差设计要求
段差设计要求 段差的设计既要考虑到造型的美观性,也要考虑到对最终产品的影响。例如为获得车身 侧部区域造型上浑然一体的效果,前后车门与侧围的段差理论值一般设计为0 mm;需要 考虑到车辆在高速行驶时段差和流体力学的关系:翼子板与前门的段差理论值为0 mm, 前门为基准,公差要求0 mm~+1 mm;前门与后门的段差尺寸为0 mm,后门为基准, 公差要求0 mm~+1 mm 。
9
四、间隙、段差设计要求
间隙设计要求 在设计开闭件与周边件配合的间隙数值时,必须考虑并且满足运 动校核对间隙数值的要求,防止发生运动干涉。 依照配合结构不同,整车所有间隙分为三类:包边——包边,包 边——折边,折边——折边。包边——包边,包边——折边,这 两类配合的间隙值为此断面两配合件的最短距离。 包边——包边 此类间隙配合有以下三类情况,分别见下图所示
11
四、间隙、段差设计要求
1. 段差方向的设计 以基准件的外观面为基准面,高于基准面为正值,低于基准面为负值。
12
四、间隙、段差设计要求
段差基准的选择
l
安装基体为基准件,安装在基体上的装配件为跟随件。例如侧围总成与加油口盖,
前者为安装基体,设计为基准;仪表板本体与通风盖板,前者为安装基体,设计为基准。
外观测量顺序: 前部:A前格栅区域(分为7处特征:A1格栅亮条与发动机罩外板;A2中网 本体与前保险杠上本体;A3中网本体与前大灯;A4格栅亮条与前大灯;A5格栅 亮条与中网本体;A6中网本体与车标…)B前大灯区域C前保险杠区域D发动机 罩区域 侧部:E翼子板区域F前风挡区域G前后三角装饰板区域H前、后门区域I侧 围窗区域J加油口盖区域 后部:K后组合灯区域L后保险杠区域M后导流板区域 顶部:N顶盖区域 内饰测量顺序: A仪表板区域B副仪表板区域C前门护面区域D后门护面区域E侧围护面区域F 后背门护面
汽车设计-车身外表面间隙段差的设计规范模板
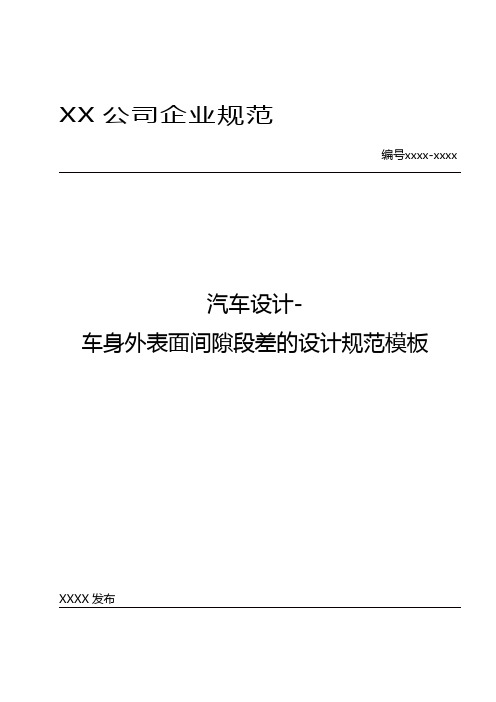
汽车设计-车身外表面间隙段差的设计规范模板车身外表面间隙段差图设计规范本规范为了规范汽车产品车身外表面间隙、段差的设计而编制,规定了车身外表面间隙、段差图的设计,并规定了车身外表面间隙、段差的代号与标准值,间隙、段差的标注方法。
本规范适用于设计各类轿车、SUV等车身外表面间隙、段差设计。
1 术语和定义下列术语和定义适用于本规范。
1.1 车身间隙车身外表面两个零件之间的可见缝隙。
1.2 段差车身外表面两个零件之间高度差。
1.3 公差允许尺寸的变动量,即最大极限尺寸与最小极限尺寸代数差的绝对值。
1.4 间隙的分类——运动件与运动件之间的间隙,如前车门与后车门的间隙。
——运动件与固定件之间的间隙,如车门与门框之间的间隙,发动机盖及行李箱盖的周边间隙。
——固定件与固定件之间的间隙,如前大灯与前翼子板之间的间隙。
2 车身间隙、段差图的基本要求2.1 车身间隙、段差图应包括以下三个内容。
2.1.1 车身间隙、段差图明细表,该表应具有间隙、段差代号、位置、规范值等内容。
2.1.2 间隙、段差布置图可用立体图或平面三视图来表示,表明各种代号的间隙、段差在车身表面的布置情况2.1.3 对关键部位的间隙、段差还需以断面形式来表示,断面型式及内容参照断面图规范执行。
2.2 所标注的间隙值为该外表面的法向实际值,所标注的段差值为外表面的切向实际值,为表达清楚该间隙、段差的性质,可用断面来表示。
2.3间隙、段差图上的数值必须与该处主断面的设计值一致。
3 车身间隙、段差设计、检验规则3.1 车身间隙、段差设计规则3.1.1 车身间隙、段差设计应能满足生产工艺要求。
3.1.2 车身间隙、段差设计应能满足性能要求,如运动干涉。
3.1.3 车身间隙、段差设计应保证整车的外观协调美观。
3.1.4 运动件与运动件,运动件与固定件之间的间隙应稍大,保证不会发生干涉,固定件与固定件之间间隙稍小,以保证外观的美观性。
3.2 车身间隙、段差检验规则3.2.1 检查间隙、段差是否符合造型设计的要求。
吉利整车部设计手册间隙面差

整车集成篇第一章 DTS1.1 间隙及面差定义1.1.1 间隙、面差定义的意义及基本要求意义对整车进行外表面及内表面的间隙面差定义,从而通过对整车外观间隙、面差的控制,使得整车能够实现预期的外观要求。
基本要求间隙、面差定义主要依据竞品车间隙面差测量、现有车型数据库积累,并充分对比市场上竞争车型的间隙、面差水平结合我们自身的工艺制造能力进行制定。
1)整车的间隙、面差应能在竞品车中处于领先水平并考虑实际的制造工艺要求;2)间隙、面差定义应符合工程要求并能在后期的数据设计阶段中体现;3)间隙面差定义文件中对应位置处的间隙面差定义应有断面简图,以表明该处的结构。
1.1.2 整车间隙、面差的定义相关输入及流程为了保证后期产品质量,并满足工艺及外观要求对整车的间隙、面差进行定义。
整车间隙面差定义开始于造型设计阶段,根据新产品的造型输入,并对比竞品车、结合公司工艺制造水平进行整车间隙面差定义。
需要的相关输入如下:1)车型效果图(第二版)。
该效果图要分缝明确,以根据分缝形式及位置进行间隙、面差定义。
2)车型CAS数据(第一版)。
内、外CAS都要分缝明确。
3)竞品车间隙及面差分析报告。
应包括竞品车车身表面及内饰表面主要断面及搭接处的间隙、面差统计及分析。
该报告可以作为新车型间隙、面差定义的参考。
间隙、面差定义流程如下:通过上述输入,科室内完成的间隙面差的定义,并需要与相关部门一起对定义进行评审。
评审通过的定义需要在CAS及A面中体现。
后期三维数据的制作、工程车制造生产均要以此为标准。
间隙面差定义及控制流程见图1-1。
评审材料为PPT格式,实例见附录A-1。
图1-1 整车减息面差定义及控制流程图间隙、面差定义内容主要包括内饰表面及车身表面两大部分的间隙、面差定义。
1.1.2.2.1内饰表面间隙、面差定义由于内饰件普遍采用塑料成型,其尺寸、形状等受模具、塑料件本身材料特性、外界气候条件影响比较大。
合理的间隙配合,不仅可以美观造型,降低制造难度,也可以方便安装。
(吉利)整车部设计手册-间隙面差
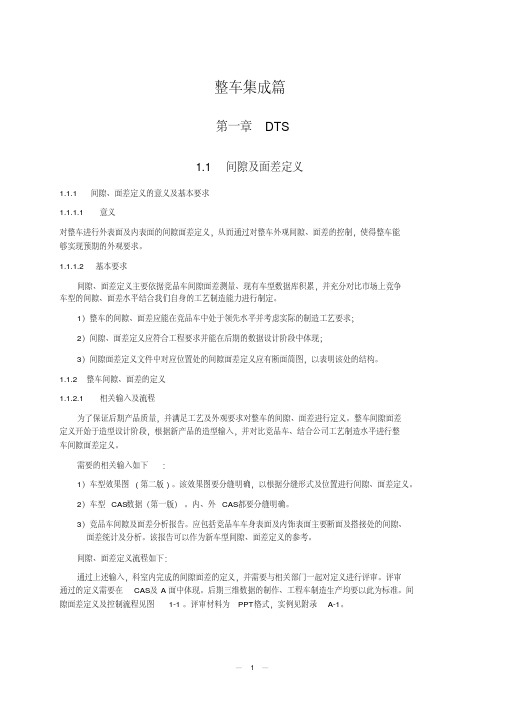
整车集成篇第一章 DTS1.1 间隙及面差定义1.1.1 间隙、面差定义的意义及基本要求1.1.1.1 意义对整车进行外表面及内表面的间隙面差定义,从而通过对整车外观间隙、面差的控制,使得整车能够实现预期的外观要求。
1.1.1.2 基本要求间隙、面差定义主要依据竞品车间隙面差测量、现有车型数据库积累,并充分对比市场上竞争车型的间隙、面差水平结合我们自身的工艺制造能力进行制定。
1)整车的间隙、面差应能在竞品车中处于领先水平并考虑实际的制造工艺要求;2)间隙、面差定义应符合工程要求并能在后期的数据设计阶段中体现;3)间隙面差定义文件中对应位置处的间隙面差定义应有断面简图,以表明该处的结构。
1.1.2 整车间隙、面差的定义1.1.2.1 相关输入及流程为了保证后期产品质量,并满足工艺及外观要求对整车的间隙、面差进行定义。
整车间隙面差定义开始于造型设计阶段,根据新产品的造型输入,并对比竞品车、结合公司工艺制造水平进行整车间隙面差定义。
需要的相关输入如下:1)车型效果图(第二版)。
该效果图要分缝明确,以根据分缝形式及位置进行间隙、面差定义。
2)车型CAS数据(第一版)。
内、外CAS都要分缝明确。
3)竞品车间隙及面差分析报告。
应包括竞品车车身表面及内饰表面主要断面及搭接处的间隙、面差统计及分析。
该报告可以作为新车型间隙、面差定义的参考。
间隙、面差定义流程如下:通过上述输入,科室内完成的间隙面差的定义,并需要与相关部门一起对定义进行评审。
评审通过的定义需要在CAS及A面中体现。
后期三维数据的制作、工程车制造生产均要以此为标准。
间隙面差定义及控制流程见图1-1。
评审材料为PPT格式,实例见附录A-1。
图1-1 整车减息面差定义及控制流程图1.1.2.2 间隙、面差定义内容主要包括内饰表面及车身表面两大部分的间隙、面差定义。
1.1.2.2.1内饰表面间隙、面差定义由于内饰件普遍采用塑料成型,其尺寸、形状等受模具、塑料件本身材料特性、外界气候条件影响比较大。
车身仪表板的外表面圆角、间隙与段差测量标准

上海同济同捷科技有限公司企业标准TJI/YJY车身仪表板的外表面圆角、间隙与段差测量标准2005-07-31发布2005-08-01实施上海同济同捷科技有限公司发布TJI/YJY前言本标准对Benchmark中车身仪表板的外表面圆角、间隙与段差测量的具体内容和要求作了较详细的规定,今后新设计的车型可参照本规定的测量方法来获取参考车的仪表板外表面圆角、间隙与段差。
使本公司的测量工作日趋规范化。
本标准的附录A为规范性附录。
本标准由上海同济同捷科技有限公司提出。
本标准由上海同济同捷科技有限公司质量与项目管理中心负责归口管理。
本标准主要起草人:邓建国张晓红TJI/YJY上海同济同捷科技股份有限公司企业标准车身仪表板的外表面圆角、间隙与段差测量规定1范围本标准规定了选择仪表板圆角、间隙及段差测量位置,测量的方法和要求。
“仪表板圆角、间隙及段差图”的设计规则。
本标准适用于公司所有车型仪表板外表面圆角、间隙及段差的测量。
2规范性引用文件3术语和定义3.1仪表板外表面圆角:和工艺结构、装配相关的圆角。
3.2仪表板外表面间隙:仪表板总成中各个配合件之间的间隙。
3.3仪表板外表面段差:仪表板总成中配合件的表面在相互配合处的落差值。
4要求4.1 选择测量位置的原则4.1.1 选择测量圆角位置的原则4.1.1.1各可见零件的周边4.1.1.2零件的可见外表面上与其他零件配合处周边4.1.2 选择测量间隙位置的原则两零件相互配合处周边4.1.3选择测量段差位置的原则“四周型”配合关系的零件外表面之间的落差4.2测量工具4.3测量方法4.3.1圆角值的测量方法4.3.1.1按照车身功能划分测量区域,并在每一个区域按特征变化设定若干测量点,原则上点的间距取100mm.4.3.1.2以车身y=0平面为基准,仪表板两侧的对称特征尽量取相同的圆角.4.3.2间隙值的测量方法4.3.2.1按照车身功能划分测量区域,并在每一个区域按特征变化设定若干测量点,原则上点的间距取100mm.4.3.2.2以车身y=0平面为基准,仪表板两侧的对称特征尽量取相同的间隙值.4.3.3按照车身功能划分测量区域,并在每一个区域按特征变化设定若干测量点,原则上点的间距取100mm.4.4测量结果4.4.1测量结果的记录测量完毕后填写测量记录表,并配合相应的图片说明以“仪表板间隙、圆角、段差图”的形式输出结果,见表V4.4.2.1“仪表板间隙、圆角、段差图示”应以线框图方式表示,并输出图片文件。
- 1、下载文档前请自行甄别文档内容的完整性,平台不提供额外的编辑、内容补充、找答案等附加服务。
- 2、"仅部分预览"的文档,不可在线预览部分如存在完整性等问题,可反馈申请退款(可完整预览的文档不适用该条件!)。
- 3、如文档侵犯您的权益,请联系客服反馈,我们会尽快为您处理(人工客服工作时间:9:00-18:30)。
车身外观间隙面差设计定义规范
I
车身外观间隙面差设计定义规范
1范围
本标准规定了外观间隙面差测量方法、外DTS设计定义A面检查方法等。
本标准适用于外饰全新造型项目、FL项目。
2术语和定义
DTS:DTS 是(dimension尺寸 technology技术 specification规范)的英文缩写,在汽车上定义外观匹配各尺寸关系及公差标准。
3 间隙和面差定义的表示方法
3.1间隙定义的表示方法
间隙测量符号以标准距离测量符号表示,如下图:
3.2面差定义的表示方法
面差测量方式及指示符号说明参考面用三角形符号表示,以三角形处面为基准面,面差数值为正值,表示此面比基础面高出;负值表示低进。
如下图所示:涂黑三角形区域所在部件是基准,FENDER比FRT DOOR 高出0.5mm,公差设计值为-0.5~+1mm(最终结果为FENDER比FRT DOOR高出0~1.5mm)。
3.3对齐度定义的表示方法
3.3.1对齐度用圆在主图上标示出位置,用大写字母排序;其他相关信息标注在局部放大图上,必须标注基准:
第1页共7页
3.3.2“对齐度±1.5”概念:以FENDER为基准,FRT BUMPER的边界(R角切点)出入相对于FENDER不大于1.5mm。
3.4基准的选取
基准选取原则:1)车身开启件以车身骨架为基准;2)开启件与开启件之间以先安装部件
为基准,如前门以后门为基准、翼子板以前门为基准;3)总装安装件以车身为基准;4)两个总装安装件之间以尺寸易控制、刚度比较好的件为基准,同时尽量选择大平面作为测量基准。
如前后大灯与前后保之间,以灯为基准。
4 间隙和面差测量定义方法
4.1间隙测量定义方法
4.1.1当外观面在同一造型平面内且两件的配合面分别与本零件外观面角度小于等于90度时,以外观面的法线(法线与外观R角相交)之间的距离作为两个面(或部件)的间隙,间隙测量方法示意如下:
(a)
(b) (c)
4.1.2当外观面在同一造型平面内且两件的配合面分别与本零件外观面角度大于90度时,外观R角接近(R 角差值小于等于1),以两个R角内侧根部的距离作为两个面(或部件)的间隙,外观R角差别较大(R角差值大于1),以较大R角的面(或部件)R角内侧根部做平行外观面的直线,与另一配合面(或部件)相交,交点到R角内侧根部的距离作为两个面(或部件)的间隙,间隙测量方法示意如下:
第2页共7页
(a ) (b)
4.1.3当外观面在同一造型平面内且两件的配合面中仅有一个零件与本零件外观面角度大于90度时,以两个外观R
角面最短距离作为两个面(或部件)的间隙,间隙测量方法示意如下:
4.1.4当两个件的外观面不平行(不在一个造型面上)、且翻边也不平行时,以低进去的面(或部件)的内侧翻边面做平行面,使低进去零件的内侧面R 角根部与另外零件内侧面相交,以交点到低进去零件的内侧R 角根部的距离作为两个面(或部件)的间隙,间隙测量方法示意如下:
(a ) (b) 4.2面差定义
4.2.1当两个件的面具有共同的造型特征时,测量一边R 角低端(R
角切点处)到另外基准面的垂直距离,(释放曲率延长基本面):
4.2.2当两个件的基准面之间无造型顺延特征时,平行于基准面作另一面的相切面(以谁为基准,则将基准面偏移与另一个面相切),测量切点与基准面的距离(面差仅用于造型定义,实车匹配数值不测量), 如下图:
第3页 共7页
5 间隙和面差的标注规范
5.1间隙与平度尺寸标注要求
5.1.1所有间隙值、面差值及公差值均保留一位小数
5.1.2间隙(GAP)尺寸标注时,如有品质要求,须注明平行差及左右差。
平行差用符号“//”
表示,左右差用符号“L/R”或“左右差”字样表示。
如下示意图:
“//1.0”概念:该处GAP测量值的最大值与最小值的差不大于1.0mm。
“左右差1.0”概念:该GAP 分别在车身LH及RH两个对称位置处,所测量值的差的绝对值不大于1.0mm。
5.1.3当间隙(GAP)设计值为0 时,必须标注。
如下示意图:
第4页共7页
5.1.4间隙(GAP)、平度(FLUSH)的尺寸标注方式
:
5.1.5截面中有关间隙(GAP)、平度(FLUSH)的尺寸标注,要不仅仅满足于整车的评价;还要能对焊装下线的白车身四门两盖前翼的外观匹配的合格性做出独立判定。
如下示意图,举GAP 为例:
只有判定总装整车品质的尺寸标注5±1.5。
第5页 共7页
增加判定焊装白车身品质的尺寸标注6±1.5。
5.1.6关于间隙(GAP)、平度(FLUSH)渐变、过渡的标注示意图:
在主图上有大写字母标注渐变的范围。
第6页共7页
在截面图纸中标注渐变的具体数值。
第7页共7页
编制:校对:会签:审核:标准化:批准:版本:00。