杠杆课程设计说明书
杠杆1课程设计

杠杆 1 课程设计一、课程目标知识目标:1. 学生能理解并掌握杠杆的定义、分类和基本原理;2. 学生能运用杠杆原理解决实际问题,如计算力的大小和作用点;3. 学生了解杠杆在日常生活中的应用,并能举例说明。
技能目标:1. 学生能运用所学知识,分析并解决简单杠杆问题,提高解决问题的能力;2. 学生能通过实验观察和数据分析,培养科学探究能力和实验操作能力;3. 学生能运用数学知识,进行杠杆问题的计算和推导。
情感态度价值观目标:1. 学生通过学习杠杆,培养对物理学科的兴趣和好奇心,激发学习热情;2. 学生在小组合作中,培养团队协作精神和沟通能力;3. 学生认识到杠杆在生活中的重要性,增强对科学技术的尊重和热爱。
课程性质分析:本课程为物理学科的一章内容,旨在帮助学生掌握杠杆的基本原理和应用,培养学生的科学素养和实际操作能力。
学生特点分析:六年级学生对物理现象充满好奇心,具备一定的数学基础和实验操作能力,但需要进一步引导和激发学习兴趣。
教学要求:1. 教师需关注学生的个体差异,因材施教,确保每个学生都能掌握课程内容;2. 教学过程中,注重理论与实践相结合,提高学生的实际操作能力;3. 注重培养学生的合作精神和创新意识,提高学生的综合素质。
二、教学内容1. 杠杆的定义与分类:介绍杠杆的基本概念,包括一级杠杆、二级杠杆和三级杠杆的特点和应用。
2. 杠杆原理:讲解力臂、力点、支点等基本概念,阐述杠杆平衡条件及其计算方法。
3. 实际生活中的杠杆应用:分析生活中常见的杠杆实例,如撬棍、剪刀、筷子等,并探讨其原理。
4. 杠杆问题的计算:教授如何运用数学知识解决杠杆问题,包括力的合成与分解、力的作用点与力臂的计算等。
5. 实验探究:安排杠杆实验,让学生通过实际操作,观察并验证杠杆原理。
教学大纲安排:第一课时:杠杆的定义与分类,了解不同类型杠杆的特点。
第二课时:杠杆原理,学习力臂、力点、支点等概念,掌握杠杆平衡条件。
第三课时:实际生活中的杠杆应用,分析实例并探讨原理。
CA6140杠杆课程设计说明书

CA6140杠杆课程设计说明书1.引言机械专业课程设计是以机械专业知识为基础的设计,在课程设计中能发现很多问题,同时也能学会很多。
理论与实践的结合,才是最完美的。
通过对此门学科的课程设计,我们在各方面得到了锻炼。
L能熟练运用机械专业的基本理论以及在生产实习中学到的实践知识,正确的解决一个零件在加工中的定位、夹紧以及工艺路线的安排、工艺尺寸的确定等问题,保证零件的加工质量。
2.提高结构设计能力。
通过设计夹具的训练,获得根据被加工零件的加工要求,设计出高效、省力、既经济合理又能保证加工质量的夹具的能力。
3.学会使用手册及图表资料。
4.对所学的知识得到了复习,在此基础上有了一定的创新能力。
通过对CA6140杠杆831009的工艺及夹具设计,汇总所学专业知识如一体(如互换性与测量技术基础、机械设计、机械制造技术基础、塑料成型工艺与模具设计、材料成型基础、机械制造装备设计等)。
让我们对所学的专业课得以巩固、复习及实用,在理论与实践上有机结合;使我们对各科的作用更加深刻的熟悉与理解,并为以后的实际工作奠定坚实的基础!5.提高解决问题的能力。
机械专业在社会上的应用以深入到各个方面,正确掌握专业知识与社会实践的应用已十分重要。
同时在遇到问题时,解决问题的能力也是非常重要的。
2.杠杆加工工艺规程设计2.1.零件的分析2.1.1零件的作用题目给出的零件是CA6140的杠杆。
它的主要的作用是用来支承、固定的。
要求零件的配合要符合要求。
2.1.2零件的工艺分析零件的材料为HT于铸铁生产工艺简单,铸造性能优良,但塑性较差、脆性高,为此参考文献【1】孙XX.机械制造工艺及专用夹具设计指导.冶金工业出版社【2】艾X,肖诗纲.切削用量简明手册.机械工业出版社【3】崇凯.机械制造技术基础课程设计指南.化学工业出版社【4】毛平淮.互换性与测量技术基础.机械工业出版社【5】龚XX,蔡建国.机床夹具设计原理.陕西XX.1981【6】成大先.机械设计手册.化学工业出版社【7】黄如林.切削加工简明实用手册.化学工业出版社【8】张XX.机械加工工艺设计实用手册.航空工业出版社.1993 【9】吕XX机械制造技术基础.武汉理工大学出版社【10】胡城立,朱X.材料成型基础.武汉理工大学出版社【11】孟少农.机械加工工艺手册.机械工业出版社.1991 【12】冯XX.机械制造装备设计.机械工业出版社。
杠杆(一)课程设计
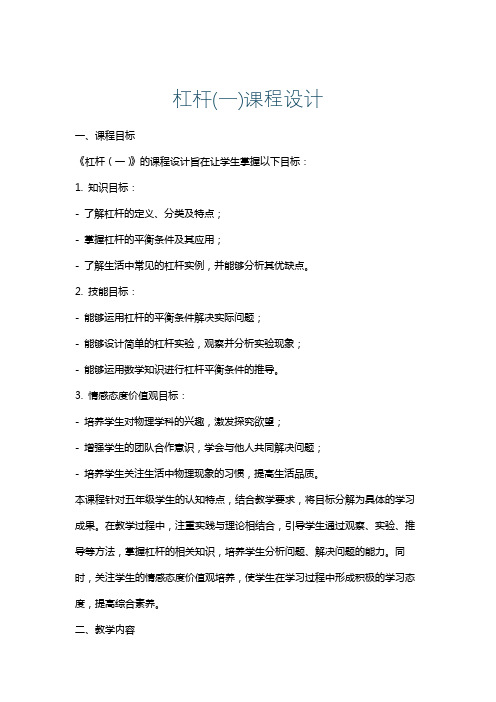
杠杆(一)课程设计一、课程目标《杠杆(一)》的课程设计旨在让学生掌握以下目标:1. 知识目标:- 了解杠杆的定义、分类及特点;- 掌握杠杆的平衡条件及其应用;- 了解生活中常见的杠杆实例,并能够分析其优缺点。
2. 技能目标:- 能够运用杠杆的平衡条件解决实际问题;- 能够设计简单的杠杆实验,观察并分析实验现象;- 能够运用数学知识进行杠杆平衡条件的推导。
3. 情感态度价值观目标:- 培养学生对物理学科的兴趣,激发探究欲望;- 增强学生的团队合作意识,学会与他人共同解决问题;- 培养学生关注生活中物理现象的习惯,提高生活品质。
本课程针对五年级学生的认知特点,结合教学要求,将目标分解为具体的学习成果。
在教学过程中,注重实践与理论相结合,引导学生通过观察、实验、推导等方法,掌握杠杆的相关知识,培养学生分析问题、解决问题的能力。
同时,关注学生的情感态度价值观培养,使学生在学习过程中形成积极的学习态度,提高综合素养。
二、教学内容《杠杆(一)》的教学内容依据课程目标进行选择和组织,主要包括以下部分:1. 杠杆的定义与分类:- 杠杆的概念、要素及分类;- 简单杠杆、复杂杠杆的特点。
2. 杠杆的平衡条件:- 力臂的概念及其计算方法;- 杠杆平衡的原理及其表达式;- 实际杠杆平衡条件的应用。
3. 生活中的杠杆实例:- 案例分析:剪刀、钳子、撬棍等;- 杠杆在生活中的应用及其优缺点。
教学大纲安排如下:第一课时:杠杆的定义与分类,简单杠杆与复杂杠杆的特点;第二课时:力臂的概念及计算方法,杠杆平衡原理;第三课时:杠杆平衡条件的应用,生活中的杠杆实例分析。
教学内容参考教材相关章节,确保科学性和系统性。
在教学过程中,教师将结合学生实际情况,适度调整教学内容和进度,确保学生能够扎实掌握杠杆相关知识。
三、教学方法《杠杆(一)》的教学方法选择注重多样化,旨在激发学生的学习兴趣和主动性,主要包括以下几种:1. 讲授法:- 在介绍杠杆的定义、分类及平衡条件等基本概念时,采用讲授法进行教学,为学生奠定扎实的理论基础。
《杠杆》教案(通用6篇)
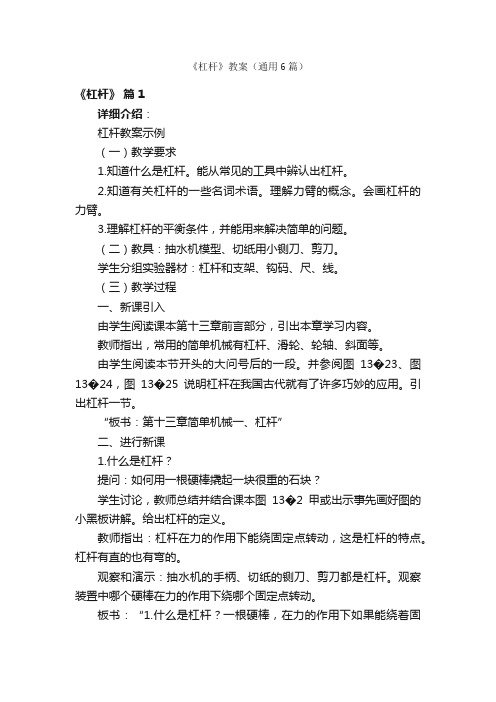
《杠杆》教案(通用6篇)《杠杆》篇1详细介绍:杠杆教案示例(一)教学要求1.知道什么是杠杆。
能从常见的工具中辨认出杠杆。
2.知道有关杠杆的一些名词术语。
理解力臂的概念。
会画杠杆的力臂。
3.理解杠杆的平衡条件,并能用来解决简单的问题。
(二)教具:抽水机模型、切纸用小铡刀、剪刀。
学生分组实验器材:杠杆和支架、钩码、尺、线。
(三)教学过程一、新课引入由学生阅读课本第十三章前言部分,引出本章学习内容。
教师指出,常用的简单机械有杠杆、滑轮、轮轴、斜面等。
由学生阅读本节开头的大问号后的一段。
并参阅图13�23、图13�24,图13�25说明杠杆在我国古代就有了许多巧妙的应用。
引出杠杆一节。
“板书:第十三章简单机械一、杠杆”二、进行新课1.什么是杠杆?提问:如何用一根硬棒撬起一块很重的石块?学生讨论,教师总结并结合课本图13�2甲或出示事先画好图的小黑板讲解。
给出杠杆的定义。
教师指出:杠杆在力的作用下能绕固定点转动,这是杠杆的特点。
杠杆有直的也有弯的。
观察和演示:抽水机的手柄、切纸的铡刀、剪刀都是杠杆。
观察装置中哪个硬棒在力的作用下绕哪个固定点转动。
板书:“1.什么是杠杆?一根硬棒,在力的作用下如果能绕着固定点转动,这根硬棒就叫杠杆。
”2.描述杠杆的几个有关名词术语(1)教师以讲什么是杠杆时所画的撬杠撬石头的板图为基础,边讲下列名词边在图中规范标画出三点、两力、两臂。
并板书写出各名词及其定义。
板书:“2.名词术语:”支点:杠杆(撬杠)绕着转动的点,用字母o标出。
动力:使杠杆转动的力画出力的示意图,用字母f1或f动标出。
阻力:阻碍杠杆转动的力画出力的示意图,用字母f2或用f阻标出。
注意:动力和阻力使杠杆转动方向相反,但它们的方向不一定相反。
动力臂:从支点到动力作用线的距离。
用字母l1或l动标出。
(简介力的作用线概念。
)教师说明力臂的画法:首先确定杠杆的支点,再确定力的作用线。
然后使用直角三角板画出从支点到力的作用线的垂线,垂足要落在力的作用线上,符号指明哪个线段是力臂,并写出字母l1或l动。
c1350杠杆课程设计

c1350杠杆课程设计一、课程目标知识目标:1. 学生能够理解并掌握杠杆的定义、分类及基本原理;2. 学生能够运用杠杆原理解决简单的实际问题;3. 学生能够描述杠杆在生活中的应用及其对人类生产、生活的影响。
技能目标:1. 学生能够通过观察、实验等方法,分析并归纳杠杆的特点;2. 学生能够运用所学的杠杆知识,设计并制作简单的杠杆模型;3. 学生能够运用数学知识,对杠杆的力臂、力的大小进行计算和比较。
情感态度价值观目标:1. 学生能够认识到科学知识在实际生活中的重要性,增强学习科学技术的兴趣;2. 学生能够通过合作、讨论等方式,培养团队协作精神和问题解决能力;3. 学生能够养成观察生活、发现问题的习惯,培养创新意识和实践能力。
课程性质:本课程为自然科学领域的物理学科,以杠杆原理为主题,注重理论与实践相结合。
学生特点:五年级学生具有一定的观察能力、动手能力和逻辑思维能力,对新鲜事物充满好奇心,喜欢探索和发现。
教学要求:教师应注重启发式教学,引导学生通过观察、实验、讨论等方法,自主探究杠杆原理,将知识应用于实际生活,提高学生的实践能力和创新能力。
同时,关注学生的个体差异,因材施教,确保每个学生都能达到课程目标。
二、教学内容1. 杠杆的定义与分类:通过课本内容,介绍杠杆的概念、种类(一、二、三类杠杆)及其特点;- 理解杠杆的支点、力臂、作用力和阻力等基本概念;- 分析不同种类杠杆在实际生活中的应用。
2. 杠杆原理:讲解杠杆的平衡条件,即力的大小与力臂的乘积相等;- 通过实验和实例,让学生感受并理解力与力臂的关系;- 学习并掌握杠杆原理在实际问题中的应用。
3. 杠杆的计算:运用数学知识,对杠杆的力臂、力的大小进行计算;- 学习如何测量力的大小和力臂长度;- 掌握杠杆计算公式,解决实际问题。
4. 杠杆的应用:介绍杠杆在生活中的广泛应用,如撬棍、剪刀、杠杆秤等;- 分析杠杆在工具和机械中的作用,体会其重要性;- 讨论杠杆对人类生产、生活的影响。
《杠杆》教学设计(五篇范文)

《杠杆》教学设计(五篇范文)第一篇:《杠杆》教学设计《杠杆》教学设计与反思江桥中心中学陈海峰教学目标: [知识与技能]:1、认识杠杆,能画出杠杆的五要素。
2、能用杠杆的平衡条件解决一些简单问题。
[过程与方法]:1、通过观察和实验、了解杠杆的结构。
2、通过探究、了解杠杆的平衡条件。
[情感、态度与价值观]:通过了解生活中的杠杆,进一步认识物理是有用的,提高学习物理的兴趣。
教学重点:探究杠杆的平衡条件教学突破:首先认识杠杆,能抽象出杠杆的定义,在探究杠杆平衡条件时创造一种探究气氛,通过用杆秤称物体,提出猜想,激发兴趣。
教学过程:导入新课,激发兴趣。
师:人们在生活中、劳动中经常使用各种机械,同学们想一想你使用过哪些机械?或你看到别人使用过哪些机械?生1:我使用过铁锨、镊子、钳子、锤子。
生2:我使用过剪刀、指甲刀、瓶盖起子、自行车。
生3:我看见别人使用过播种机、悬耕犁、收割机、缝纫机。
生4:我看见过农民修房时用的滑轮,看见过轧制面条的面条机。
师:同学们想起很多人们常用的机械,这说明同学们平时很注意观察。
在同学们说出的机械中有的比较复杂,有的比较简单。
例如:镊子、钳子、锤子、剪刀、瓶盖起子等都属于简单机械,播种机、缝纫机等是复杂机械。
复杂机械也是由简单机械组合而成的。
这一章我们学习几种简单机械。
同学们在你们的桌上放着钳子、锤子、瓶盖起子分别试着用一用,看会有什么发现?(各小组同学分别进行操作,有的用钳子剪断铁丝,有的用锤子起木板上的钉子,有的用瓶盖起子起瓶盖,有三个小组用钳子分别把铁丝弯成了三角形、长方形、圆形。
约2分钟后平静下来。
)第五小组:我们小组发现:使用这些机械可以完成直接用手不能完成的工作。
第六小组:我们小组发现:使用这些机械都可以用一个较小的力获得一个较大的力。
师:同意他们说法的同学举手。
(全体学生举手)师:同学们的发现很好,那么谁能针对刚才的发现提出一个问题?生5:我想知道:为什么使用这些机械时可以用一个较小的力获得一个较大的力呢?师:大家想知道吗?生(齐答):想知道。
课程设计杠杆(一)

课程设计杠杆(一)一、课程目标本章节“杠杆(一)”的课程目标如下:1. 知识目标:(1)使学生理解杠杆的定义、分类和基本原理;(2)培养学生掌握杠杆的平衡条件及其应用;(3)让学生了解杠杆在生活中的应用实例。
2. 技能目标:(1)培养学生通过观察、实验等方法探究杠杆平衡条件的能力;(2)提高学生运用杠杆原理解决实际问题的能力;(3)训练学生运用数学知识分析杠杆问题的能力。
3. 情感态度价值观目标:(1)培养学生对物理学科的兴趣,激发学生探索科学原理的欲望;(2)教育学生珍惜和合理利用身边的物理资源,培养学生的节能环保意识;(3)通过杠杆原理的学习,使学生认识到科学知识在实际生活中的重要性,增强学生的实践能力。
课程性质:本课程为物理学科的基础知识课程,旨在让学生掌握杠杆的基本原理及其在实际生活中的应用。
学生特点:四年级学生具有较强的观察、实验和思考能力,对新鲜事物充满好奇心,但需引导他们将理论知识与实际应用相结合。
教学要求:教师应注重理论与实践相结合,运用多种教学手段,激发学生的兴趣,引导学生主动探究,培养学生的实践能力和解决问题的能力。
通过本课程的学习,使学生达到预期的学习成果,为后续相关知识的学习打下坚实基础。
二、教学内容本章节“杠杆(一)”的教学内容如下:1. 杠杆的定义与分类:介绍杠杆的基本概念、分类(一、二、三类杠杆)及特点;2. 杠杆的平衡条件:讲解杠杆的平衡原理,包括力臂、力的大小及关系;3. 杠杆的应用实例:分析生活中常见的杠杆应用,如撬棍、剪刀、天平等;4. 实践活动:组织学生进行杠杆平衡实验,探究平衡条件;5. 习题训练:布置与杠杆相关的习题,巩固所学知识。
教学大纲安排:第一课时:杠杆的定义与分类,介绍各类杠杆的特点;第二课时:杠杆的平衡条件,进行实验探究,解释平衡原理;第三课时:杠杆的应用实例,分析生活中常见的杠杆应用;第四课时:实践活动,分组进行杠杆平衡实验,巩固理论知识;第五课时:习题训练,针对杠杆相关知识进行练习。
杠杆(二)课程设计说明书

编写教案:详细编写 每个课时的教学内容
和教学方法
准备教学材料:准备 所需的教学资料和教
具
实施教学:按照教学 计划和教案进行教学
评估教学效果:通过考 试、作业等方式评估学 生的学习效果,并根据
评估结果进行改进
注重理论与实践相结合
理论教学:讲解杠 杆原理、分类、应 用等基础知识
实践操作:设计实 验、制作模型、操 作演示等实践活动
反馈与改进:根据评价结果, 对课程设计进行反馈和改进,
以提高教学质量和效果
课程设计要求
保证实验操作安全
实验前,学 生必须阅读 并理解实验 操作规程和 安全注意事 项
实验过程中, 学生必须遵守 实验操作规程, 不得擅自改变 实验步骤或操 作方法
实验过程中, 学生必须穿 戴好防护用 品,如防护 眼镜、手套 等
案例分析:分析生 活中的杠杆应用, 如起重机、剪刀等
创新思维:鼓励学 生提出新的杠杆应 用方案,培养创新 思维
鼓励创新思维和实践能力发挥
课程设计应注重培养学生的创新思维和实践能力 鼓励学生运用所学知识解决实际问题 课程设计应注重培养学生的团队合作精神和沟通能力 鼓励学生积极参与各类实践活动,提高实践能力
实验过程中, 学生必须保 持实验室整 洁,不得随 意丢弃实验 废弃物
实验结束后, 学生必须清 理实验台面, 关闭电源和 水源,确保 实验室安全
严格按照课程设计步骤进行
确定课程目标:明确 课程要达到的目标和
效果
设计课程内容:根据课 程目标,选择合适的教
学内容和教学方法
制定教学计划:合理 安排教学进度和课时
学生实践:学生按照自主设计 的方案进行实践操作,完成实
验任务
杠杆课程设计说明书
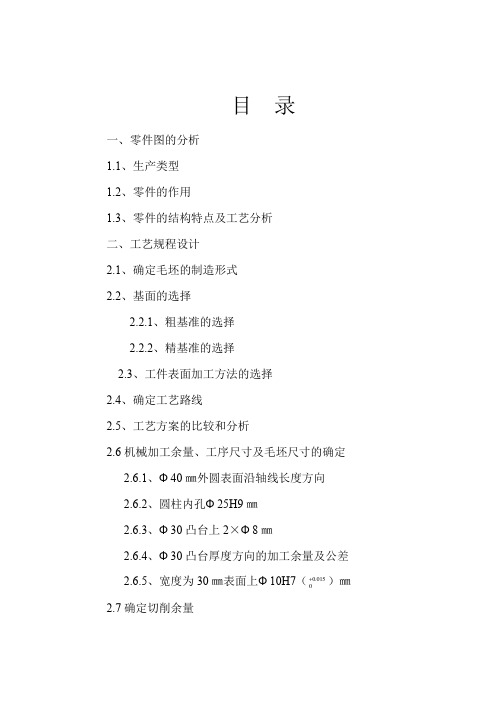
目录一、零件图的分析1.1、生产类型1.2、零件的作用1.3、零件的结构特点及工艺分析二、工艺规程设计2.1、确定毛坯的制造形式2.2、基面的选择2.2.1、粗基准的选择2.2.2、精基准的选择2.3、工件表面加工方法的选择2.4、确定工艺路线2.5、工艺方案的比较和分析2.6机械加工余量、工序尺寸及毛坯尺寸的确定2.6.1、Ф40㎜外圆表面沿轴线长度方向2.6.2、圆柱内孔Ф25H9㎜2.6.3、Ф30凸台上2×Ф8㎜2.6.4、Ф30凸台厚度方向的加工余量及公差2.6.5、宽度为30㎜表面上Ф10H7(015.0)㎜2.7确定切削余量2.7.1 工序Ⅰ的切削用量的确定2.7.2 工序Ⅱ的切削用量的确定2.7.3 工序Ⅲ的切削用量的确定2.7.4工序Ⅳ的切削用量的确定2.7.5 工序Ⅴ的切削用量的确定三、夹具的设计3.1、确定设计方案3.2、定位元件设计3.3、计算铣削力、扭矩及校验机床功率3.4、定位误差的分析四、参考文献一零件的分析1.1零件的作用题目所给的零件是CA6140车床的杠杆结构,此零件的作用是支撑、固定,传递扭矩,帮助改变机床工作台的运动方向,要求零件的配合符合要求。
1.2零件的工艺分析杠杆的Φ25052.0+㎜孔的轴线和两个端面有着垂直度的要求。
现分述如下:本夹具用于历立式铣床上,加工Φ40㎜凸台端面。
工件以Φ25052.0+㎜孔及端面和水平面底、Φ30㎜的凸台分别用定位销实现完全定位。
铣Φ40㎜端面时工件为悬臂,为了防止加工时变形,采用螺旋辅助支承与工件接触后,用螺母锁紧。
要加工的主要工序包括:粗精铣宽度为Φ40㎜的上下平台、钻Φ10H7的孔、钻2xΦ8H7(015.0+)㎜的小孔、粗精铣Φ30㎜的上下表面。
加工要求有:Φ40㎜的平台的表面粗糙度各为Ra6.3um(上平台)、Ra3.2um(下平台)、Φ10H7的孔为Ra3.2um。
2xΦ8H7(015.0+)㎜孔有平行度分别为0.1um(A)、0.15um(A)。
杠杆设计说明书

杠杆设计说明书TYYGROUP system office room 【TYYUA16H-TYY-TYYYUA8Q8-前言机械制造技术基础课程设计是我们在学完了大学的全部基础课,专业基础课以及专业课后进行的。
这是我们在进行毕业设计之前对所学的各科课程一次深入的综合性总复习,也是一次理论联系实际的训练。
因此,他在我们的大学四年生活中占有重要的地位。
就我个人而言,我希望通过这次课程设计对自己未来将从事的工作进一步适应性的训练,希望自己在设计中能锻炼自己的分析问题、解决问题、查资料的能力,为以后的工作打下良好的基础。
由于能力有限,设计尚有很多不足之处,希望各位老师给予指导。
一、零件的分析(一)零件的作用题目所给的零什是CAl340自动车床上的杠杆(见附图),它位于自动车床的自动机构中,与灵活器配介使用,起制动的作用。
经查资料得知,此零件用于机床当中,并且还承受着冲击载荷,因此就要求该零件的材料具有足够的刚度和强度同时还要有足够的塑性和韧性。
(二)零件的工艺分析分析零件图可知,该杠杆的左、右端面及上下端面的精度要求并不太高,其粗糙度在以上;故可用铣削加工。
Φ20H7mm的孔的粗糙度为,所以采用钻-扩-粗铰-精铰的工艺过程在钻床上加工。
长30mm内孔Φ8 H7对精度要求较高,由于端面为平面,可防止钻头钻偏以保证加工精度。
该零件出了内孔之外,其他加工表面精度要求均不高,因此以车床和铣床的粗加工就可达到要求。
30mm内孔较长,需以多步骤加工实现。
杠杆共有四组加工表面,现分述如下1、以中Φ20H7mrn孔为中心的加工表面这一组加工表面包括:一个Φ20H7mm的孔及其倒角,粗糙度为;尺寸为Φ35mm 且与孔Φ20H7mm相垂直的两个平面,粗糙度为Ra3. 2;一个中心轴线与Φ20H7mm 孔中心轴线平行且相距的圆弧油槽;还有一个与Φ20H7mm的孔轴线成45°的油孔Φ3mm,并锪沉头孔。
其中Φ20H7mm孔及两端面为主要加工面,并且Φ20H7mm的孔粗糙度为、两平面的粗糙度为。
“杠杆”教学设计(第1课时)

杠杆教学设计(第1课时)1. 教学目标•了解杠杆的基本概念和原理•掌握杠杆的分类和使用方法•能够使用杠杆解决简单的物理问题•发展学生的观察、实验和解决问题的能力2. 教学内容1.杠杆的概念和原理–什么是杠杆–杠杆的作用原理–杠杆的三要素:力臂、力矩、支点2.杠杆的分类–一级杠杆–二级杠杆–三级杠杆3.杠杆的使用方法–杠杆平衡条件:左力臂×左力矩 = 右力臂×右力矩–杠杆的应用举例3. 教学过程步骤1:导入杠杆概念1.引发学生的兴趣,提问引导:你们是否了解杠杆是什么?有什么作用?2.呈现一个图片或实物样例,给出定义:杠杆是一种简单机械装置,可以把作用力分解为力臂和力矩,在解决力的平衡问题和做力倍增时有很大作用。
3.简要说明杠杆的作用原理。
步骤2:介绍杠杆的三要素1.具体说明杠杆的三要素:力臂、力矩、支点。
–力臂:力作用点到支点的垂直距离。
–力矩:力的大小与力臂的乘积。
–支点:杠杆的支撑点,作用力的方向以及力臂的计算都是以支点为基准。
步骤3:分类和举例1.介绍一级、二级和三级杠杆的定义和特点。
–一级杠杆:力和支点在同一侧,力矩相等。
–二级杠杆:力和支点垂直分布,力矩不相等。
–三级杠杆:力和支点在同一直线上,力矩相等。
2.通过图片或实物演示,让学生体验不同分类杠杆的用途和作用。
步骤4:解决问题和示范1.通过简单的实例,让学生运用杠杆的知识解决问题。
–给定一个杠杆上的物体质量和支点距离,让学生计算另一侧所需的力大小和距离。
–利用杠杆平衡条件解决问题。
2.示范解决问题的方法,引导学生进行思考和实践。
步骤5:总结和归纳1.简要总结杠杆的概念和原理。
2.通过回答问题和讨论,加深学生对杠杆分类和使用方法的理解。
3.强调发展观察、实验和解决问题的能力。
4. 教学评估1.教师观察学生在课堂上的参与情况和回答问题的准确性。
2.教师设置小组活动,让学生合作解决杠杆问题,并进行评估。
3.收集学生课后小练习的答案,评估学生对杠杆的理解程度。
杠杆2课程设计
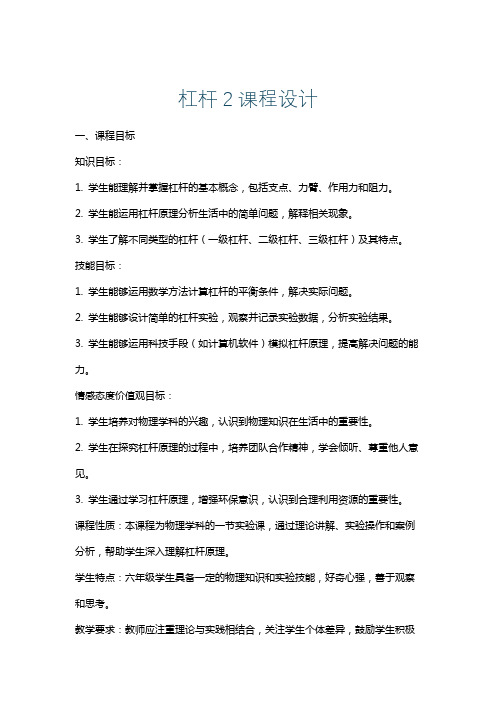
杠杆2课程设计一、课程目标知识目标:1. 学生能理解并掌握杠杆的基本概念,包括支点、力臂、作用力和阻力。
2. 学生能运用杠杆原理分析生活中的简单问题,解释相关现象。
3. 学生了解不同类型的杠杆(一级杠杆、二级杠杆、三级杠杆)及其特点。
技能目标:1. 学生能够运用数学方法计算杠杆的平衡条件,解决实际问题。
2. 学生能够设计简单的杠杆实验,观察并记录实验数据,分析实验结果。
3. 学生能够运用科技手段(如计算机软件)模拟杠杆原理,提高解决问题的能力。
情感态度价值观目标:1. 学生培养对物理学科的兴趣,认识到物理知识在生活中的重要性。
2. 学生在探究杠杆原理的过程中,培养团队合作精神,学会倾听、尊重他人意见。
3. 学生通过学习杠杆原理,增强环保意识,认识到合理利用资源的重要性。
课程性质:本课程为物理学科的一节实验课,通过理论讲解、实验操作和案例分析,帮助学生深入理解杠杆原理。
学生特点:六年级学生具备一定的物理知识和实验技能,好奇心强,善于观察和思考。
教学要求:教师应注重理论与实践相结合,关注学生个体差异,鼓励学生积极参与实验,培养他们的创新能力和实践能力。
同时,注重情感态度价值观的引导,使学生在掌握知识的同时,提升综合素质。
通过具体的学习成果分解,为后续教学设计和评估提供依据。
二、教学内容1. 杠杆基本概念:支点、力臂、作用力、阻力。
- 教材章节:第三章第二节“杠杆的基本概念”2. 杠杆的分类及特点:一级杠杆、二级杠杆、三级杠杆。
- 教材章节:第三章第三节“杠杆的分类及特点”3. 杠杆的平衡条件:力矩平衡、力的平衡。
- 教材章节:第三章第四节“杠杆的平衡条件”4. 生活中的杠杆应用实例:举例说明不同类型杠杆在实际中的应用。
- 教材章节:第三章第五节“生活中的杠杆应用”5. 实验操作:杠杆平衡实验、力矩测量实验。
- 教材章节:第三章实验“杠杆平衡实验”6. 案例分析:分析生活中杠杆应用的优点和不足,提出改进措施。
课程设计杠杆

课程设计 杠杆一、课程目标知识目标:1. 让学生理解杠杆的定义、分类及基本原理;2. 掌握杠杆的平衡条件,能运用相关公式进行简单计算;3. 了解杠杆在生活中的应用,能识别并分析实际生活中的杠杆问题。
技能目标:1. 培养学生运用杠杆知识解决实际问题的能力,提高学生的动手操作和实验能力;2. 学会使用杠杆平衡条件进行相关计算,提高学生的数学运用能力;3. 培养学生通过观察、实验、分析等方法,探索杠杆原理的能力。
情感态度价值观目标:1. 激发学生对杠杆知识的兴趣,培养学生的探究精神;2. 培养学生合作学习、积极思考的良好习惯;3. 引导学生认识到科学知识在实际生活中的重要性,提高学生的科学素养。
课程性质分析:本课程为物理学科,旨在让学生掌握杠杆的基本概念、原理和应用,培养学生的动手操作和实验能力。
学生特点分析:六年级学生具备了一定的物理基础和数学能力,对新鲜事物充满好奇心,善于观察和思考。
教学要求:1. 注重理论与实践相结合,提高学生的实际操作能力;2. 采用启发式教学,引导学生主动探究、积极思考;3. 关注学生的个体差异,因材施教,确保每个学生都能达到预期学习效果。
二、教学内容1. 杠杆的定义与分类- 杠杆的概念及其在生活中的应用实例- 杠杆的分类:一、二、三类杠杆及其特点2. 杠杆的基本原理- 力臂的概念及其作用- 杠杆平衡条件及其数学表达3. 杠杆的计算与应用- 力与力臂的关系:力的作用点、方向与力臂的关系- 实际问题中的杠杆计算:如杠杆秤、剪刀、钳子等4. 实践活动:杠杆实验- 设计并完成杠杆平衡实验,观察并记录实验数据- 分析实验结果,探讨杠杆平衡条件在实际中的应用教学内容安排与进度:第一课时:杠杆的定义与分类,介绍生活中的杠杆实例,让学生对杠杆产生直观认识;第二课时:杠杆的基本原理,学习力臂和杠杆平衡条件,为后续计算打下基础;第三课时:杠杆的计算与应用,通过实例分析,让学生掌握杠杆计算方法;第四课时:实践活动,设计并完成杠杆实验,巩固所学知识。
杠杆课程设计HT150

杠杆课程设计HT150一、课程目标知识目标:1. 学生能够理解并掌握杠杆的定义、分类及基本原理;2. 学生能够运用公式计算杠杆的力矩,并解释相关物理现象;3. 学生能够了解杠杆在生活中的应用,并举例说明。
技能目标:1. 学生能够通过实验操作,探究杠杆的平衡条件;2. 学生能够运用杠杆原理解决实际问题,提高解决问题的能力;3. 学生能够运用数学知识进行杠杆的计算,提高数学应用能力。
情感态度价值观目标:1. 学生能够认识到科学知识在实际生活中的重要性,增强学习兴趣;2. 学生能够通过小组合作,培养团队协作精神和沟通能力;3. 学生能够关注生活中的科学现象,培养探究精神和创新意识。
课程性质:本课程为物理学科的一节实验课,旨在让学生通过实验探究和理论学习,掌握杠杆的基本知识和应用。
学生特点:六年级学生具备一定的物理知识和实验操作能力,好奇心强,善于观察和思考。
教学要求:结合学生特点,采用启发式教学,引导学生主动探究,注重理论与实践相结合,提高学生的实际操作能力和解决问题的能力。
通过本课程的学习,使学生能够将杠杆知识应用于生活,提高综合素养。
二、教学内容1. 杠杆的定义与分类:介绍杠杆的概念,包括一、二、三类杠杆的特点及实例;2. 杠杆原理:讲解力矩的概念,引导学生理解力矩与杠杆平衡的关系;3. 杠杆平衡条件:通过实验探究,使学生掌握杠杆的平衡条件及其应用;4. 杠杆计算:教授杠杆计算公式,指导学生运用公式解决实际问题;5. 杠杆在生活中的应用:举例说明杠杆在日常生活和生产中的应用,提高学生学以致用的意识。
教材章节:《物理》六年级上册第四章第三节“杠杆的平衡条件”教学安排与进度:第一课时:杠杆的定义与分类,杠杆原理;第二课时:杠杆平衡条件实验,杠杆计算;第三课时:杠杆在生活中的应用,案例分析。
教学内容确保科学性和系统性,结合教材章节,由浅入深地引导学生掌握杠杆知识,强调理论与实践相结合,培养学生学以致用的能力。
杠杆(一)课程设计
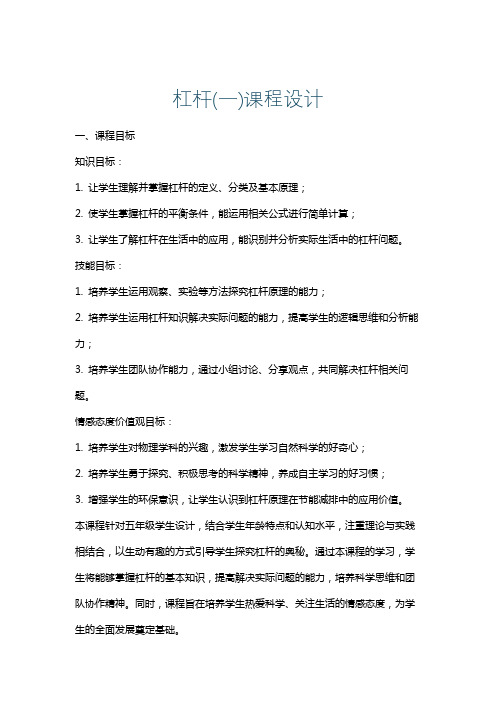
杠杆(一)课程设计一、课程目标知识目标:1. 让学生理解并掌握杠杆的定义、分类及基本原理;2. 使学生掌握杠杆的平衡条件,能运用相关公式进行简单计算;3. 让学生了解杠杆在生活中的应用,能识别并分析实际生活中的杠杆问题。
技能目标:1. 培养学生运用观察、实验等方法探究杠杆原理的能力;2. 培养学生运用杠杆知识解决实际问题的能力,提高学生的逻辑思维和分析能力;3. 培养学生团队协作能力,通过小组讨论、分享观点,共同解决杠杆相关问题。
情感态度价值观目标:1. 培养学生对物理学科的兴趣,激发学生学习自然科学的好奇心;2. 培养学生勇于探究、积极思考的科学精神,养成自主学习的好习惯;3. 增强学生的环保意识,让学生认识到杠杆原理在节能减排中的应用价值。
本课程针对五年级学生设计,结合学生年龄特点和认知水平,注重理论与实践相结合,以生动有趣的方式引导学生探究杠杆的奥秘。
通过本课程的学习,学生将能够掌握杠杆的基本知识,提高解决实际问题的能力,培养科学思维和团队协作精神。
同时,课程旨在培养学生热爱科学、关注生活的情感态度,为学生的全面发展奠定基础。
二、教学内容1. 引言:通过生活中的实例,引出杠杆的概念和作用,激发学生的兴趣。
教材章节:《物理学》第五章第一节“杠杆的概念与应用”2. 杠杆的分类与特点:- 简单杠杆:介绍其结构及特点,如撬棍、剪刀等;- 复合杠杆:介绍其结构及特点,如开瓶器、钳子等。
教材章节:《物理学》第五章第二节“杠杆的分类与特点”3. 杠杆的平衡条件:- 力臂与力的关系;- 力矩的概念及其计算方法;- 杠杆平衡条件及其应用。
教材章节:《物理学》第五章第三节“杠杆的平衡条件”4. 杠杆的计算:- 力矩的计算;- 杠杆效率的计算;- 实际问题中的应用案例分析。
教材章节:《物理学》第五章第四节“杠杆的计算”5. 杠杆在生活中的应用:- 介绍杠杆在生活中的各种应用实例,如桥梁、剪刀、钳子等;- 分析杠杆原理在节能减排中的应用。
杠杆(二)课程设计说明书
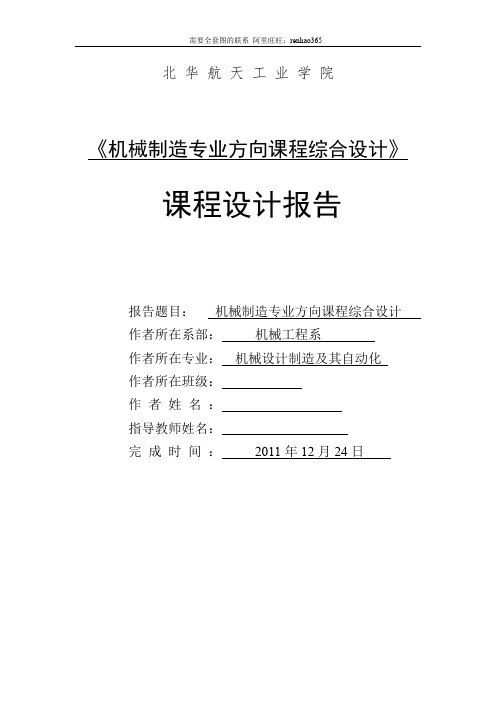
3. 根据某工序要求,确定专用夹具的定位方案、夹紧方案、对刀导引方案等等;
4. 制定合理的机床夹具的总体方案,并画出装配图;
标注夹具的技术要求。
工作内容及时间进度安排
本设计时间为 3 周,其进度和时间安排如下(供参考):
1. 熟悉零件及各种资料,对零件图进行结构和工艺分析
约 8%
2. 机械加工工艺过程设计(毛坯尺寸确定,拟定工艺路线,选择加工设备与工艺装备等)
3.制 定 零 件 工 艺 路 线 ............................................................................... 4 3.1 选 择 定 位 基 准 .............................................................................. 4 3.1.1 精 基 准 的 选 择 ...................................................................4 3.1.2 粗 基 准 的 选 择 ...................................................................4 3.2 表 面 加 工 方 法 的 确 定 ................................................................ 5 3.3 加 工 阶 段 的 划 分 ......................................................................... 6 3.4 工 序 集 中 与 分 散 ......................................................................... 6 3.5 工 序 顺 序 的 安 排 ......................................................................... 7 3.5.1 机 械 加 工 工 序 的 安 排 .....................................................7 3.5.2 热 处 理 工 序 及 表 面 处 理 工 序 的 安 排 ......................... 8 3.5.3 辅 助 工 序 安 排 ...................................................................8 3.6 确 定 工 艺 路 线 .............................................................................. 8
- 1、下载文档前请自行甄别文档内容的完整性,平台不提供额外的编辑、内容补充、找答案等附加服务。
- 2、"仅部分预览"的文档,不可在线预览部分如存在完整性等问题,可反馈申请退款(可完整预览的文档不适用该条件!)。
- 3、如文档侵犯您的权益,请联系客服反馈,我们会尽快为您处理(人工客服工作时间:9:00-18:30)。
气门摇杆支座机械加工工艺规程及工艺装备设计1、零件的工艺分析及生产类型的确定1.1零件用途气门摇杆支座是柴油机一个主要零件。
是柴油机摇杆座的结合部,Φ20(+0.10—+0.16)孔装摇杆轴,轴上两端各装一进气门摇杆,摇杆座通过两个Φ13mm孔用M12螺杆与汽缸盖相连,3mm轴向槽用于锁紧摇杆轴,使之不转动。
汽缸盖内每缸四阀使燃烧室充气最佳,气门由摇杆凸轮机构驱动,摩擦力小且气门间隙由液压补偿。
这种结构可能减小燃油消耗并改善排放。
另外一个优点是减小噪音,这种结构使3.0升的TDI发动机运转极端平稳。
1.2零件的工艺分析其材料为HT200。
该材料具有较高的强度,耐磨性,耐热性及减振性,适用于承受较大应力,要求耐磨的零件。
该零件上主要加工面为上端面,下端面,左右端面,2×Φ13mm孔和Φ20(+0.1——+0.06)mm 以及3mm轴向槽的加工。
Φ20(+0.1——+0.06)mm孔的尺寸精度以及下端面0.05mm的平面度与左右两端面孔的尺寸精度,直接影响到进气孔与排气门的传动精度及密封,2×Φ13mm孔的尺寸精度,以上下两端面的平行度0.05mm。
因此,需要先以下端面为粗基准加工上端面,再以上端面为粗基准加工下端面,再把下端面作为精基准,最后加工Φ20(+0.1——+0.06)mm孔时以下端面为定位基准,以保证孔轴相对下端面的位置精度。
由参考文献(1)中有关孔的加工的经济精度机床能达到的位置精度可知上述要求可以达到的零件的结构的工艺性也是可行的。
1.3气门摇杆支座的主要技术要求:注: 1、未注明铸造圆角为R ︒⨯452- R3 2、材料:HT2001.4确定生产类型:已知此气门摇杆支座零件为小批生产,毛坯的铸造方法选用砂型机器造型。
此外,为消除残余应力,铸造后安排人工时效处理。
参考文献《典型零件机械加工生产实例》表2.3—12;该种铸造公差等级为CT10~11,MA-H 级。
所以初步确定工艺安排为:划分加工阶段;工序适当集中;加工设备以通用设备为主,采用专用夹具。
2、确定毛坯、绘制毛坯简图2.1确定毛坯种类:零件材料为HT200。
考虑零件在机床运行过程中所受冲击不大,零件结构又比较简单,生产类型为小批生产,故选择砂型机器造型铸件毛坯。
查《机械制造技术基础课程设计指南》第120页表5-3选用铸件尺寸公差等级为CT-10。
2.2确定毛坯的尺寸公差和机械加工余量:查《机械制造技术基础课程设计指南》,选用加工余量为MA-H 级,并查表 2.2-4确定各个加工面的铸件机械加工余量,铸件的分型面的选用及加工余量,如下表所示:2.3绘制毛坯简图:3、拟定零件工艺路线3.1定位基准的选择:粗基准的选择:以零件的Φ20孔为主要的定位粗基准,以两个旁孔外圆表面为辅助粗基准。
精基准的选择:考虑要保证零件的加工精度和装夹准确方便,依据“基准重合”原则和“基准统一”原则,以粗加工后的Φ20孔为主要的定位精基准,以两个旁孔外圆柱表面为辅助的定位精基准。
Φ20孔既是装配基准又是设计基准,用它作为精基准,面积大定位稳定可靠;3.2表面加工方法的确定:根据气门摇杆支座零件图上各加工表面的尺寸精度和表面粗糙度,确3.3加工阶段的划分:该零件加工质量要求较高,可将加工阶段划分成粗加工,半精加工和精加工几个阶段。
这是由于粗加工工序的切削余量大,因此切削力、夹紧力必然大,加工后容易产生变形。
粗、精加工分开后,粗加工产生的变形可以在半精加工中修正;半精加工中产生的变形可以在精加工中修正。
这样逐步减少加工余量,切削力及内应力的作用,逐步修正加工后的变形,就能最后达到零件的技术条件。
3.4工序的集中和分散:气门摇杆支座加工工序安排应注意两个影响精度的因素:(1)气门摇杆支座的刚度比较低,在外力作用下容易变形;(2)铸件切削时会产生较大的残余内应力。
因此在气门摇杆支座加工工艺中,各主要表面的粗精加工工序一定要分开,且采用小批生产,减少辅助时间,所以采用工序集中原则。
3.5工序顺序的安排:3.5.1、机械加工工序(1)先基准后其他(2)先粗后精(3)先主后次(4)先面后孔3.6确定工艺路线:表3-2 气门摇杆支座工艺路线及设备、工装的选用4、加工余量、工序尺寸和公差的确定4.1确定加工余量确定工序尺寸及其公差2×Φ13mm孔各工序尺寸及其公差(根据《机械制造技术基础课程设计指导教程》表2—29表2—30)由上可得该工序各工步的工序尺寸及工差为钻:13 mm5、切削用量、时间定额的计算5.1加工2×Φ13mm孔5.1.1 、钻2×Φ13mm孔选用钻床Z525根据《机械制造工艺设计手册》表2.4—38(41)选取数据钻头直径D = 13 mm 切削速度V = 0.66 mm/s 切削深度a p = 6.5 mm 进给量f = 0.12 mm/r 则主轴转速n = 1000V/πD = 969 r/min根据表3.1—30 按机床选取n = 960 r/min 则实际钻削速度V = πDn/1000 = 39.2m/min钻削工时为:按表2.5—7L = 78 mm L1 = 1.5 mm L2 = 2.5mm基本时间t j = L/fn = (78+1.5+2.5)/(0.12×1000) = 40.5 s按表2.5—41 辅助时间t a = 40.5×0.18=7.29s按表2.5—4 其他时间t q = 12 s6、机床夹具设计6.1 2×Φ13mm孔夹具设计:为了提高劳动生产率,保证加工质量,降低劳动强度,需要设计专用夹具。
经过与指导老师协商,钻2×Φ13mm孔的钻床专用夹具。
由气门摇杆支座工作图可知,工件材料为HT200。
根据设计任务的要求,本夹具将用于立式钻床。
刀具为麻花钻。
6.1.1问题的指出:本夹具主要钻2×Φ13mm孔,内表面有粗糙度要求,由于工艺要求不高,因此,在本道工序加工时,主要应考虑如何提高劳动生产率,降低劳动强度。
6.1.2夹具设计:(1)定位基准的选择由零件图可知,在钻2×Φ13mm孔之前,气门摇杆支座的Φ20孔、Φ13mm孔的两侧面都已加工,且表面粗糙要求较高。
为了使定位误差为零,按基准重合原则选气门摇杆支座的Φ20孔为设计基准。
对2×Φ13mm孔为对称分布的外圆柱表面再加底面进行定位,从而使各个表面和轴槽均完全定位。
为了提高加工效率,现决定采用联动夹紧工件快换装置,并采用固定钻套。
(2)夹紧方案由于零件小,所以采用开口垫圈的螺旋夹紧机构,装卸工件方便、迅速。
(3)夹具体设计夹具体的作用是将定位、夹具装置连接成一体,并能正确安装在机床上,加工时,能承受一部分切削力。
夹具体为铸造件,安装稳定,刚度好,但制造周期较长。
(4)切削力及夹紧力的计算切削力的计算:,由《组合机床》(表7-24)得:刀具:高速钢麻花钻头,尺寸为Φ13。
则轴向力:见《工艺师手册》表28.4F=CF dFz f F y kF……………………………………3.1式中:CF =420,ZF=1.0, yF=0.8, f=0.35kF=(07.1)190200()1903.1==FnHBF=420)(212307.135.05.138.00.1N=⨯⨯⨯转矩T=CT dTZ f T y kT式中: CT =0.206, ZT=2.0, yT=0.8T=0.206)(34.1707.135.05.138.00.2MN∙=⨯⨯⨯功率Pm=KWdTV726.05.133095.1634.1730=⨯⨯=在计算切削力时,必须考虑安全系数,安全系数K=K1K2K3K4式中K1—基本安全系数,1.5;K2—加工性质系数,1.1;K3—刀具钝化系数, 1.1;K4—断续切削系数, 1.1则F/=KF=1.5)(423921231.11.11.1N=⨯⨯⨯⨯夹紧力的计算:由《机床夹具设计手册》(表1-2-25)得:用扳手的六角螺母的夹紧力:M=8mm, P=1.75mm,L=140mm,作用力:F=70N,夹紧力:W0=5380N所以,由于夹紧力大于切削力,钻削时工件不会转动,故本夹具可安全工作。
6.2定位误差分析:由加工工序知,加工2×Φ13mm孔。
夹具的主要定位元件为销和Φ20孔,由于Φ20孔的设计基准与定位基准重合,故其尺寸无基准不重合度误差。
销有基准不重合误差ΔDj=δd/sina,取决于Φ20圆柱的公差,规定工件上母线为基准,制造精度和安装精度要求在合理的范围内。
而孔径尺寸为自由尺寸精度要求,可满足加工要求。
7、体会与展望:通过对气门摇杆支座的机械加工工艺及对Φ13mm孔夹具的设计,使我学到了许多有关机械加工的知识,这对于我以后的学习和实践都起到了至关重要的作用,使我对学习夹具和工艺性设计产生了浓厚的兴趣,相信这次课程设计过后我才能有夯实基础的感觉,遇到难题不放弃不胆怯的决心,对于实际的内容,我主要归纳为以下两个方面:第一方面:气门摇杆支座件外形较复杂,而刚性较差。
且其技术要求很高,所以适当的选择机械加工中的定位基准,是能否保证气门摇杆支座技术要求的重要问题之一。
在气门摇杆支座的实际加工过程中,选用气门摇杆支座的Φ20孔作为定位基面,为保证2×Φ13mm孔尺寸精度和形状精度,可采用自为基准的加工原则;保证两孔的中心距精度要求,可采用互为基准原则加工。
对于加工主要表面,按照“先基准后一般”的加工原则。
气门摇杆支座的主要加工表面为旁端面,较重要的加工表面为上表面,次要的加工表面是体表面、下表面等。
气门摇杆支座机械加工路线是围绕主要加工表面来安排的,气门摇杆支座加工路线为工序集中。
第二方面:主要是关于夹具的设计方法及其步骤。
(1)、定位方案的设计:主要确定工件的定位基准及定位基面;工件的六点定位原则;定位元件的选用等。
(2)、导向及对刀装置的设计:由于本设计主要设计的是扩大头孔夹具和铣结合面夹具,所以主要考虑的是选用钻套的类型及排屑问题,以及对刀块的类型,从而确定钻套的位置尺寸及公差。
(3)、夹紧装置的设计:针对连杆的加工特点及加工的批量,对连杆的夹紧装置应满足装卸工件方便、迅速的特点,所以一般都采用自动夹紧装置。
(4)、夹具体设计:连杆的结构特点是比较小,设计时应注意夹具体结构尺寸的大小。
夹具体的作用是将定位及夹具装置连接成一体,并能正确安装在机床上,加工时能承受一部分切削力。
所以夹具体的材料一般采用铸铁。
(5)、定位精度和定位误差的计算:对用于粗加工的夹具,都应该进行定位误差和稳定性的计算,以及设计的夹具能否满足零件加工的各项尺寸要求。
(6)、绘制夹具装备图及夹具零件图。
课程设计是对我们学习的补充和扩展,实现自我完善和独立工作的过程,是大学学习的特色和优势,展望未来,我们机械的学子必将是社会发展的有力力量,靠的就是专著的态度,良好的学习习惯和真实的设计实力。