(整理)常一线油生产溶剂油流程改造方案
镇海-利用重整抽余油生产溶剂油 精品
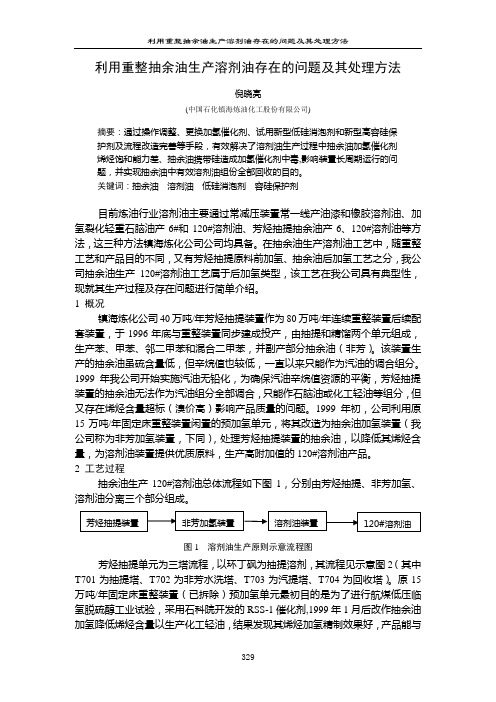
利用重整抽余油生产溶剂油存在的问题及其处理方法倪晓亮(中国石化镇海炼油化工股份有限公司)摘要:通过操作调整、更换加氢催化剂、试用新型低硅消泡剂和新型高容硅保护剂及流程改造完善等手段,有效解决了溶剂油生产过程中抽余油加氢催化剂烯烃饱和能力差、抽余油携带硅造成加氢催化剂中毒,影响装置长周期运行的问题,并实现抽余油中有效溶剂油组份全部回收的目的。
关键词:抽余油溶剂油低硅消泡剂容硅保护剂目前炼油行业溶剂油主要通过常减压装置常一线产油漆和橡胶溶剂油、加氢裂化轻重石脑油产6#和120#溶剂油、芳烃抽提抽余油产6、120#溶剂油等方法,这三种方法镇海炼化公司公司均具备。
在抽余油生产溶剂油工艺中,随重整工艺和产品目的不同,又有芳烃抽提原料前加氢、抽余油后加氢工艺之分,我公司抽余油生产120#溶剂油工艺属于后加氢类型,该工艺在我公司具有典型性,现就其生产过程及存在问题进行简单介绍。
1 概况镇海炼化公司40万吨/年芳烃抽提装置作为80万吨/年连续重整装置后续配套装置,于1996年底与重整装置同步建成投产,由抽提和精馏两个单元组成,生产苯、甲苯、邻二甲苯和混合二甲苯,并副产部分抽余油(非芳)。
该装置生产的抽余油虽硫含量低,但辛烷值也较低,一直以来只能作为汽油的调合组分。
1999年我公司开始实施汽油无铅化,为确保汽油辛烷值资源的平衡,芳烃抽提装置的抽余油无法作为汽油组分全部调合,只能作石脑油或化工轻油等组分,但又存在烯烃含量超标(溴价高)影响产品质量的问题。
1999年初,公司利用原15万吨/年固定床重整装置闲置的预加氢单元,将其改造为抽余油加氢装置(我公司称为非芳加氢装置,下同),处理芳烃抽提装置的抽余油,以降低其烯烃含量,为溶剂油装置提供优质原料,生产高附加值的120#溶剂油产品。
2 工艺过程抽余油生产120#溶剂油总体流程如下图1,分别由芳烃抽提、非芳加氢、溶剂油分离三个部分组成。
图1 溶剂油生产原则示意流程图芳烃抽提单元为三塔流程,以环丁砜为抽提溶剂,其流程见示意图2(其中T701为抽提塔、T702为非芳水洗塔、T703为汽提塔、T704为回收塔)。
石油炼化常用工艺流程

石油炼化常用工艺流程(一)常减压:1、原料:原油等;2、产出品:石脑油、粗柴油(瓦斯油)、渣油、沥青、减一线;3、生产工艺:第一阶段:原油预处理原油预处理:原油一般是带有盐份和水,能导致设备的腐蚀,因此原油在进入常减压之前首先进行脱盐脱水预处理,通常是加入破乳剂和水。
原油经过流量计、换热部分、沏馏塔形成两部分,一部分形成塔顶油,经过冷却器、流量计,最后进入罐区,这一部分是化工轻油(即所谓的石脑油);一部分形成塔底油,再经过换热部分,进入常压炉、常压塔,形成三部分,一部分柴油,一部分蜡油,一部分塔底油;剩余的塔底油在经过减压炉,减压塔,进一步加工,生成减一线、蜡油、渣油和沥青。
各自的收率:石脑油(轻汽油或化工轻油)占1%左右,柴油占20%左右,蜡油占30%左右,渣油和沥青约占42%左右,减一线约占5%左右。
常减压工序是不生产汽油产品的,其中蜡油和渣油进入催化裂化环节,生产汽油、柴油、煤油等成品油;石脑油直接出售由其他小企业生产溶剂油或者进入下一步的深加工,一般是催化重整生产溶剂油或提取萃类化合物;减一线可以直接进行调剂润滑油;4、常减压设备:常压塔、减压塔为常减压工序的核心设备尤其是常压塔,其也合称蒸馏塔,两塔相连而矗,高瘦者为常压塔,矮胖的为减压塔120吨万常减压设备评估价值4600万元。
(二)催化裂化:催化裂化是最常用的生产汽油、柴油生产工序,汽油柴油主要是通过该工艺生产出来。
这也是一般石油炼化企业最重要的生产的环节。
1、原料:渣油和蜡油70%左右-------,催化裂化一般是以减压馏分油和焦化蜡油为原料,但是随着原油日益加重以及对轻质油越来越高的需求,大部分石炼化企业开始在原料中搀加减压渣油,甚至直接以常压渣油作为原料进行炼制。
2、产品:汽油、柴油、油浆(重质馏分油)、液体丙烯、液化气;各自占比汽油占42%,柴油占21.5%,丙烯占5.8%,液化气占8%,油浆占12%。
3、生产工艺:常渣和腊油经过原料油缓冲罐进入提升管、沉降器、再生器形成油气,进入分馏塔,一部分油气进入粗汽油塔、吸收塔、空压机进入凝缩油罐,经过再吸收塔、稳定塔、最后进行汽油精制,生产出汽油。
优化溶剂油系统工艺,增效降耗

优化溶剂油系统工艺,增效降耗溶剂油系统是一种常见的工业生产系统,主要用于溶剂回收和再利用。
在实际工程应用中,优化溶剂油系统工艺可以显著提高生产效率,并降低能耗,降低生产成本。
本文将从以下几个方面探讨如何优化溶剂油系统工艺,增效降耗。
一、优化溶剂回收系统溶剂回收系统是溶剂油系统的核心部分,对其进行优化可以有效提高溶剂的回收率,降低能耗。
要合理设计溶剂油系统的结构,包括溶剂存储罐、回收设备、循环管道等,确保系统稳定运行。
优化溶剂回收过程中的操作参数,比如温度、压力、流量等,以提高溶剂回收率,减少溶剂损失。
可采用先进的溶剂回收设备和技术,如膜分离、蒸馏、浓缩等,以提高回收效率、降低能耗。
二、改善溶剂油系统的热能利用溶剂油系统往往需要大量的热能来完成溶剂回收和再利用过程。
改善热能利用是提高系统效率的关键。
一方面,要采用高效的热能回收技术,如余热利用装置、热交换器等,将系统中产生的热量充分利用,减少对外能源的依赖。
可优化热能利用方案,选择合适的加热方式和供热温度,以实现最佳的能量利用效果,降低系统能耗。
三、优化溶剂回收过程中的操作控制在溶剂回收过程中,操作控制是关键因素之一。
优化操作控制可以提高系统运行效率,降低能耗。
要对系统进行智能化改造,引入先进的自动控制系统和设备,实现对溶剂回收过程的精准控制。
需加强对操作人员的培训和管理,提高其对系统运行状态的监控和调控能力,以减少人为误操作对系统性能的影响。
四、加强对溶剂油系统的维护和管理溶剂油系统的正常运行和效率提高离不开对系统的维护和管理。
加强对系统的维护管理,可及时发现和排除系统故障,保障系统稳定运行。
要建立系统的日常巡检和定期维护制度,以延长设备的使用寿命,减少故障率。
还需加强对原材料和产品质量的监控和管理,确保溶剂油系统生产的产品符合质量要求。
以上几点是优化溶剂油系统工艺、增效降耗的一些方法和措施。
通过合理设计和结构优化、加强热能利用、优化操作控制和加强维护管理,可以提高系统的生产效率,降低系统的能耗,从而达到增效降耗的目的。
优化溶剂油系统工艺,增效降耗

优化溶剂油系统工艺,增效降耗溶剂油是一种用于在石油化工行业中进行脱碳、制造沥青、切割和清洗等工艺的重要溶剂。
然而,使用溶剂油系统也存在一些问题,例如能源消耗、溶剂回收和再利用等方面的困难。
因此,优化溶剂油系统工艺是必要的,以确保高效率和低能耗的生产过程。
一、增加预加热器在溶剂油系统中,使用预加热器可以提高能源利用率。
通过将冷却的回收溶剂油回加热器进行热交换,可以在加热油的同时降低新鲜流入的溶剂油的温度。
这种方法可以减少对加热器提供的热量需求,从而减少工厂对燃气和电力的依赖,降低能耗和成本。
二、增加回收系统回收和再利用溶剂油是在优化溶剂油系统中最重要的一步。
通过精确测量和控制流量,可以避免温度过低的过程中产生低质量的废弃物。
退回的原料油可以通过再生过滤系统进行清洗,以去除杂质和沉淀。
回收溶剂油也可以作为新鲜溶剂油的补充,以减少成本和能源消耗。
三、优化蒸汽回收系统在溶剂油的生产过程中,一些热能会以蒸汽的形式产生。
蒸汽回收装置可以帮助利用这种热能,以降低工厂的能源成本。
在回收系统中,对蒸汽进行加压和转换,以产生电力或再次转化为热能供给溶剂油生产过程中的需求。
这种方法可以大大减少生产过程中的能源消耗和成本。
四、使用高效循环泵在溶剂油生产过程中,流量和压力通常需要精确控制,以确保生产过程的有效性。
使用标准泵的限制在于其流量范围通常是固定的,而使用高效率循环泵可以改善流量和压力的控制。
高效率循环泵使用变频器驱动,可通过调整电机的转速来调整流量。
这样可以确保流量和压力的准确控制,从而减少能耗和成本,并提高溶剂油的生产效率。
综上所述,通过在溶剂油系统中使用预加热器、回收系统、蒸汽回收系统和高效循环泵等优化措施,可以提高生产效率,降低能源消耗和成本,并减少废弃物的产生。
随着未来节能环保的大趋势,进一步优化溶剂油系统工艺将是不可或缺的生产方式。
石油炼化常用的七种工艺设计流程
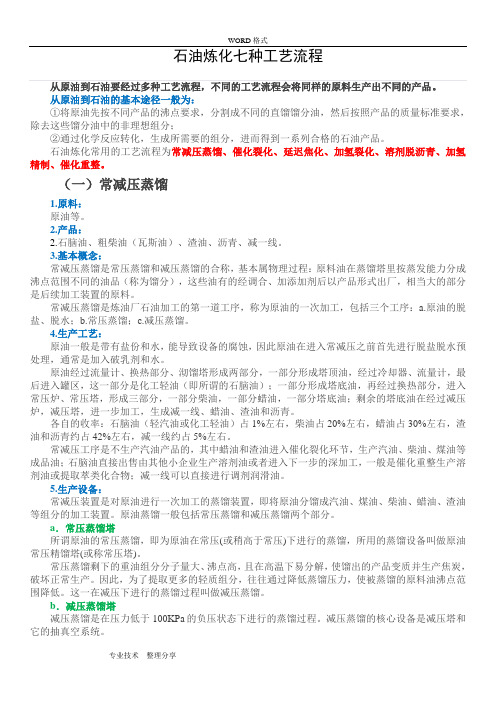
石油炼化七种工艺流程从原油到石油要经过多种工艺流程,不同的工艺流程会将同样的原料生产出不同的产品。
从原油到石油的基本途径一般为:①将原油先按不同产品的沸点要求,分割成不同的直馏馏分油,然后按照产品的质量标准要求,除去这些馏分油中的非理想组分;②通过化学反应转化,生成所需要的组分,进而得到一系列合格的石油产品。
石油炼化常用的工艺流程为常减压蒸馏、催化裂化、延迟焦化、加氢裂化、溶剂脱沥青、加氢精制、催化重整。
(一)常减压蒸馏1.原料:原油等。
2.产品:2.石脑油、粗柴油(瓦斯油)、渣油、沥青、减一线。
3.基本概念:常减压蒸馏是常压蒸馏和减压蒸馏的合称,基本属物理过程:原料油在蒸馏塔里按蒸发能力分成沸点范围不同的油品(称为馏分),这些油有的经调合、加添加剂后以产品形式出厂,相当大的部分是后续加工装置的原料。
常减压蒸馏是炼油厂石油加工的第一道工序,称为原油的一次加工,包括三个工序:a.原油的脱盐、脱水;b.常压蒸馏;c.减压蒸馏。
4.生产工艺:原油一般是带有盐份和水,能导致设备的腐蚀,因此原油在进入常减压之前首先进行脱盐脱水预处理,通常是加入破乳剂和水。
原油经过流量计、换热部分、沏馏塔形成两部分,一部分形成塔顶油,经过冷却器、流量计,最后进入罐区,这一部分是化工轻油(即所谓的石脑油);一部分形成塔底油,再经过换热部分,进入常压炉、常压塔,形成三部分,一部分柴油,一部分蜡油,一部分塔底油;剩余的塔底油在经过减压炉,减压塔,进一步加工,生成减一线、蜡油、渣油和沥青。
各自的收率:石脑油(轻汽油或化工轻油)占1%左右,柴油占20%左右,蜡油占30%左右,渣油和沥青约占42%左右,减一线约占5%左右。
常减压工序是不生产汽油产品的,其中蜡油和渣油进入催化裂化环节,生产汽油、柴油、煤油等成品油;石脑油直接出售由其他小企业生产溶剂油或者进入下一步的深加工,一般是催化重整生产溶剂油或提取萃类化合物;减一线可以直接进行调剂润滑油。
炼厂装置运行调整及总流程协同优化

炼厂装置运行调整及总流程协同优化于 博(中国石化 石油化工科学研究院,北京 100083)[摘要]以国内某炼厂为研究对象,从总流程角度对炼厂主要装置运行情况进行联合诊断,发现由于三环芳烃组分在重油加工系统恶性循环,导致生产中出现催化裂化柴油处理困难、柴油池个别批次十六烷值不达标等问题。
采用Aspen 公司的过程工业模型系统软件建立了全厂总流程模型,并进行原油保本价测算,提出了原油加工的优化结构;同时对优化前后的全厂流程进行模拟测算,提出了总流程优化方案。
优化前后的实际运行数据对比及效益评估结果表明,产品结构得到明显改善,企业全年增效约1 514.3万元,达到了炼厂运营优化和效益提升的目的,对同类型炼厂的全流程优化具有较好的借鉴意义。
[关键词]装置运行调整;总流程优化;效益评估[文章编号]1000-8144(2021)06-0584-08 [中图分类号]TE 624 [文献标志码]AUnit operation adjustment and overall process optimization of a refineryYu Bo(Sinopec Research Institute of Petroleum Processing ,Beijing 100083,China )[Abstract ]From overall process view ,the operating status of a domestic refinery ’s main units was diagnosed. Some problems in production ,such as difficult treatment of fluid catalytic cracking diesel and insufficient cetane number of individual batches of diesel pool were found due to the vicious cycle of tricyclic aromatic hydrocarbons in heavy oil processing system. The process industry model system developed by Aspen company was used to build the overall process model of the whole plant. This model was used to calculate the breakeven price of crude oil ,and propose the optimal structure of crude oil processing. The whole plant process under current and optimized conditions was simulated and calculated ,and the overall process optimization scheme was put forward. The comparison of actual operation data before and after the optimization ,and the result of benefit evaluation show that the product distribution has been obviously improved ,and the annual benefit of the enterprise increases about 15.14 million Yuan ,which has achieved both operation optimization and benefit improvement for the refinery. This study is also important in overall process optimization for refineries with the same type.[Keywords ]unit operation adjustment ;overall process optimization ;benefit evaluationDOI :10.3969/j.issn.1000-8144.2021.06.013[收稿日期]2021-01-29;[修改稿日期]2021-03-07。
重整生成油及抽余油加氢脱烯烃生产溶剂油的新技术
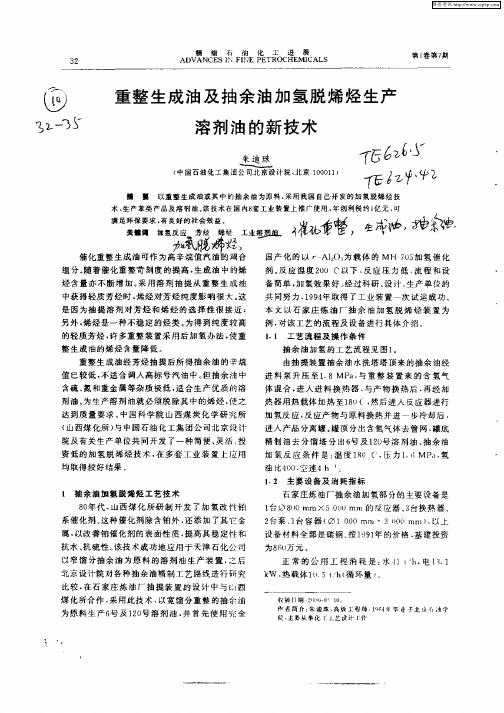
Z u Dih h zu
( ii g De i n I stueo I Bejn sg n t t f S NOPE t C。Bejn 0 0 ] ii g i 0 1 )
4 结 论
位合 作 开发 的溶 剂油 加 氢 脱烯 烃技 术使 用灵 话 , 既可用 于重整 生成 油加氢 , 可用 于抽 余油加 氢 ; 也 ( ) 技 术条件 温 和 , 2 该 对烯 烃 加氢选 择性 好 , 设 备简单 , 操作 方便 , 投资 和操作 费用 低 ;
()经多套 工 业装 置使 用 . 明该技 术可靠 、 3 证 先进 . 可满 足环保要 求 + 具有 显著的经 济效 益和社
为80 元 。 6万
8 年代 . 0 山西 煤化 所 研 制 开发 了加 氢 改 铂 系催化 剂 这种催 化 剂除 含铂外 . 添加 了其它 金 还 属. 以改 善铂催 化剂 的表 面性质 . 高其 稳定性 和 提 抗 水 、 硫性 。 抗 该技 术成功 地应用 于天 津 石化公 司 以窄馏 分抽 余 油 为原 料 的 溶剂 油 生产 装 置 , 后 之 北 京设计 院对 各种抽 余油精 制 工艺路 线进 行研 究 比较 . 石 家 庄炼 油厂 抽 提 装 置的 设 计 中与 L 西 在 I 煤 化所合作 . 采用 此技 术 . 以宽馏 分重 整 的抽余 油
1 I 工 艺 流 程 及 操 作 条 件 .
的轻质芳 烃 , 多 重整装 置采 用后加 氢 办法 , 许 使重 整生 成油的烯 烃 含量 降低 重整生成 油经 芳烃 抽提 后所 得抽余 油 的辛烷 值 已较低 . 不适 合 调人 高标号 汽油 中。 抽余 油 中 但 含硫 、 氮和重金 属等 杂质 极低 , 适合 生产 优质 的溶 剂油 。 为生产溶 剂油 就必 须脱 除其 中的烯烃 , 之 使 达 到质量 要求 中 国科学 院山 西煤 炭 化 学研 究 所
常一线油生产溶剂油流程改造方案共19页
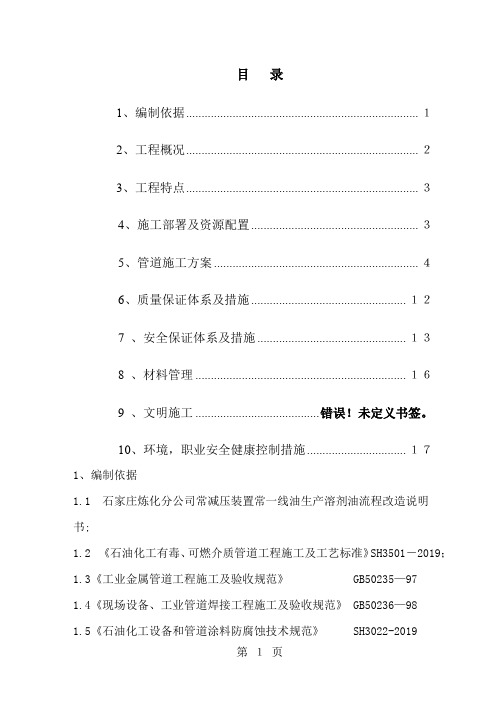
目录1、编制依据........................................................................... 12、工程概况........................................................................... 23、工程特点........................................................................... 34、施工部署及资源配置...................................................... 35、管道施工方案 .................................................................. 46、质量保证体系及措施.................................................. 127 、安全保证体系及措施................................................ 138 、材料管理 .................................................................... 169 、文明施工 ........................................ 错误!未定义书签。
10、环境,职业安全健康控制措施................................ 171、编制依据1.1 石家庄炼化分公司常减压装置常一线油生产溶剂油流程改造说明书;1.2 《石油化工有毒、可燃介质管道工程施工及工艺标准》SH3501-2019;1.3《工业金属管道工程施工及验收规范》 GB50235—971.4《现场设备、工业管道焊接工程施工及验收规范》 GB50236—981.5《石油化工设备和管道涂料防腐蚀技术规范》 SH3022-20191.6《石油化工施工安全技术规定》 SH3505-20192、工程概况2.1工程简介石家庄炼化分公司一联合车间常减压装置常一线,生产200#溶剂油,流程简单,根据客户要求溶剂油控制指标较多,尤其是脱后硫醇,水溶性酸碱,腐蚀和博士实验,故此需要流程改造,借用常二线精制进行常一线精制改造。
石油化工主要加工流程
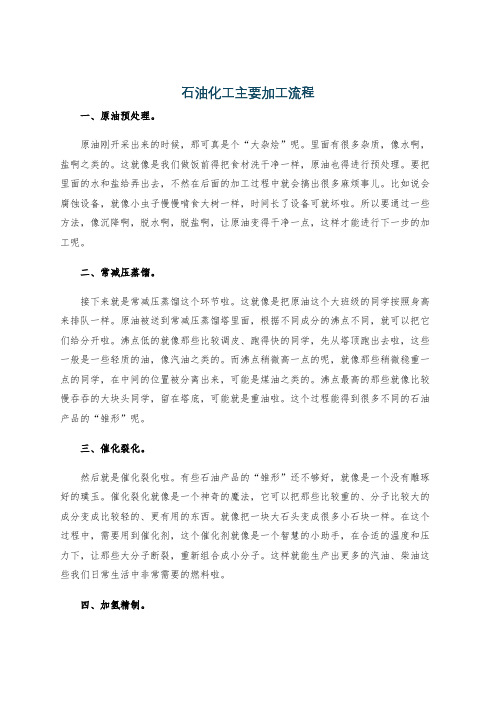
石油化工主要加工流程一、原油预处理。
原油刚开采出来的时候,那可真是个“大杂烩”呢。
里面有很多杂质,像水啊,盐啊之类的。
这就像是我们做饭前得把食材洗干净一样,原油也得进行预处理。
要把里面的水和盐给弄出去,不然在后面的加工过程中就会搞出很多麻烦事儿。
比如说会腐蚀设备,就像小虫子慢慢啃食大树一样,时间长了设备可就坏啦。
所以要通过一些方法,像沉降啊,脱水啊,脱盐啊,让原油变得干净一点,这样才能进行下一步的加工呢。
二、常减压蒸馏。
接下来就是常减压蒸馏这个环节啦。
这就像是把原油这个大班级的同学按照身高来排队一样。
原油被送到常减压蒸馏塔里面,根据不同成分的沸点不同,就可以把它们给分开啦。
沸点低的就像那些比较调皮、跑得快的同学,先从塔顶跑出去啦,这些一般是一些轻质的油,像汽油之类的。
而沸点稍微高一点的呢,就像那些稍微稳重一点的同学,在中间的位置被分离出来,可能是煤油之类的。
沸点最高的那些就像比较慢吞吞的大块头同学,留在塔底,可能就是重油啦。
这个过程能得到很多不同的石油产品的“雏形”呢。
三、催化裂化。
然后就是催化裂化啦。
有些石油产品的“雏形”还不够好,就像是一个没有雕琢好的璞玉。
催化裂化就像是一个神奇的魔法,它可以把那些比较重的、分子比较大的成分变成比较轻的、更有用的东西。
就像把一块大石头变成很多小石块一样。
在这个过程中,需要用到催化剂,这个催化剂就像是一个智慧的小助手,在合适的温度和压力下,让那些大分子断裂,重新组合成小分子。
这样就能生产出更多的汽油、柴油这些我们日常生活中非常需要的燃料啦。
四、加氢精制。
再来说说加氢精制吧。
经过前面的加工,有些石油产品里面可能还有一些不太好的东西,比如说硫啊,氮啊这些杂质。
这时候就需要加氢精制这个环节来给它们“美容”啦。
就像我们给脸上有小痘痘的皮肤做护理一样。
通过加氢的反应,把那些硫和氮这些杂质去掉,让石油产品变得更加纯净,质量更好。
这样我们用起来就更加放心啦,而且对环境也比较友好呢,不会排放出太多污染环境的东西。
石油炼化常用的七种工艺流程
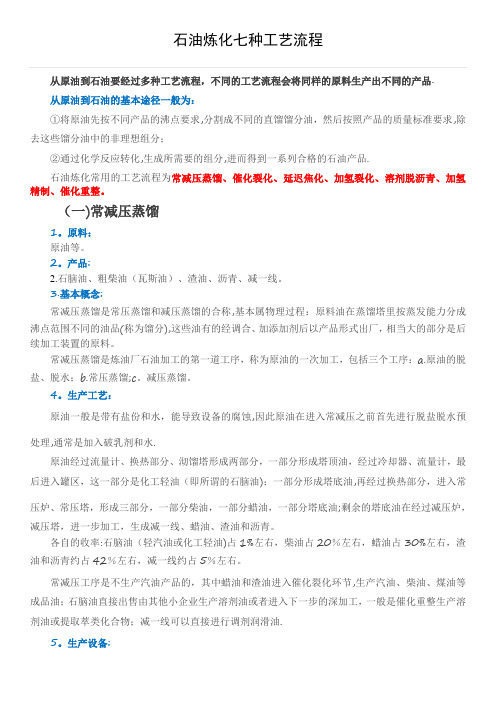
石油炼化七种工艺流程从原油到石油要经过多种工艺流程,不同的工艺流程会将同样的原料生产出不同的产品.从原油到石油的基本途径一般为:①将原油先按不同产品的沸点要求,分割成不同的直馏馏分油,然后按照产品的质量标准要求,除去这些馏分油中的非理想组分;②通过化学反应转化,生成所需要的组分,进而得到一系列合格的石油产品.石油炼化常用的工艺流程为常减压蒸馏、催化裂化、延迟焦化、加氢裂化、溶剂脱沥青、加氢精制、催化重整。
(一)常减压蒸馏1。
原料:原油等。
2。
产品:2.石脑油、粗柴油(瓦斯油)、渣油、沥青、减一线。
3.基本概念:常减压蒸馏是常压蒸馏和减压蒸馏的合称,基本属物理过程:原料油在蒸馏塔里按蒸发能力分成沸点范围不同的油品(称为馏分),这些油有的经调合、加添加剂后以产品形式出厂,相当大的部分是后续加工装置的原料。
常减压蒸馏是炼油厂石油加工的第一道工序,称为原油的一次加工,包括三个工序:a.原油的脱盐、脱水;b.常压蒸馏;c。
减压蒸馏。
4。
生产工艺:原油一般是带有盐份和水,能导致设备的腐蚀,因此原油在进入常减压之前首先进行脱盐脱水预处理,通常是加入破乳剂和水.原油经过流量计、换热部分、沏馏塔形成两部分,一部分形成塔顶油,经过冷却器、流量计,最后进入罐区,这一部分是化工轻油(即所谓的石脑油);一部分形成塔底油,再经过换热部分,进入常压炉、常压塔,形成三部分,一部分柴油,一部分蜡油,一部分塔底油;剩余的塔底油在经过减压炉,减压塔,进一步加工,生成减一线、蜡油、渣油和沥青。
各自的收率:石脑油(轻汽油或化工轻油)占1%左右,柴油占20%左右,蜡油占30%左右,渣油和沥青约占42%左右,减一线约占5%左右。
常减压工序是不生产汽油产品的,其中蜡油和渣油进入催化裂化环节,生产汽油、柴油、煤油等成品油;石脑油直接出售由其他小企业生产溶剂油或者进入下一步的深加工,一般是催化重整生产溶剂油或提取萃类化合物;减一线可以直接进行调剂润滑油.5。
溶剂油 生产工艺

溶剂油生产工艺
溶剂油的生产工艺主要有以下几个步骤:
1. 原料准备:根据需要生产的溶剂油种类和规格,选择适当的原料。
其中,常用的原料有石脑油、煤焦油、重油等。
原料应进行预处理,如脱硫、脱氮、脱灰等,以保证产品质量。
2. 原料加工:将经过处理的原料送入加工装置进行加工。
加工装置一般采用蒸馏装置,通过热解或蒸馏的方式将原料分离成不同的组分,得到目标产品。
3. 分离提纯:从加工装置中得到的产品需要进一步分离提纯。
常用的方法有精馏、萃取、冷却结晶等。
其中,精馏是最常用的分离提纯方法,通过升温、降温等手段,将产品中的杂质和不同组分分离,得到纯净的溶剂油。
4. 产品质量检验:对分离提纯后得到的溶剂油进行质量检验,主要检测其粘度、密度、闪点、燃点等指标。
只有通过质量检验的产品才能进入下一步的包装和销售。
5. 包装和销售:将经过质量检验的溶剂油按照规格进行包装,并进行相关标识和说明。
包装完成后,产品可以投放市场进行销售,供用户使用。
整个生产工艺中,对原料的选择、加工工艺的优化以及产品质量的控制等环节都至关重要,这些环节的合理控制可以保证产品的质量稳定,并满足用户的需求。
另外,在生产过程中要注
意安全生产,加强工艺的安全性和环境保护,避免事故发生,保护工作人员和环境的安全。
石油化工行业工艺流程改造与优化分析

石油化工行业工艺流程改造与优化分析随着时代的变迁和工业技术的不断发展,石油化工行业的工艺流程也在不断地改造和优化。
本文将介绍石油化工行业工艺流程改造与优化的一些方法和手段,以及对此的一些分析。
一、改造与优化的方法和手段(一)优化反应器设计反应器设计是石油化工行业中一个非常关键的环节。
目前构建反应器主要采用的都是传统的钢制反应器,但由于钢制反应器的制造和维护成本较高,而且操作效率较低,因此石油化工行业开发了一种新型的材料,即复合材料,用于反应器的构建。
复合材料具有重量轻、强度高、耐腐蚀、节能等优点,因此在反应器设计中应用,可以提高石油化工行业整体的生产效率和经济效益。
(二)优化催化剂的选择催化剂对石油化工过程中反应效率的影响很大,因此优化催化剂的选择是石油化工行业改善工艺流程的一项关键工作。
目前在催化剂的研发中,人工智能技术已被广泛应用,通过对反应中的数据进行分析,可以帮助科学家优化催化剂的选择,提高反应效率,从而降低生产成本。
(三)拓宽产品的范围针对单一产品生产的工艺流程,石油化工行业进行工艺流程改造和优化,可以拓宽产品的生产范围,从而提升企业的经济效益。
拓宽产品的范围可以通过两方面手段来实现,一是提高产品的质量,二是增加产品的品种。
二、改造与优化的分析(一)生产成本的降低石油化工行业的工艺流程改造和优化可以有效地降低企业的生产成本。
例如,在催化剂的优化选择上,选择更加适合工艺需求的催化剂,可以提高反应效率,降低耗能,从而降低生产成本;在反应器设计中应用复合材料,可以减少反应器的制造和维护成本,从而降低企业的生产成本。
(二)增加经济效益改造与优化工艺流程的另一个目的就是增加企业的经济效益。
优化选择催化剂可以提高反应效率,缩短反应时间,从而生产更多的产品,提高企业的生产效率,从而增加经济效益;拓宽产品的品种可以增加企业的市场份额,进一步提高企业的经济效益。
(三)提高环保水平石油化工行业是一个污染较为严重的行业。
石油炼化常用的七种工艺流程
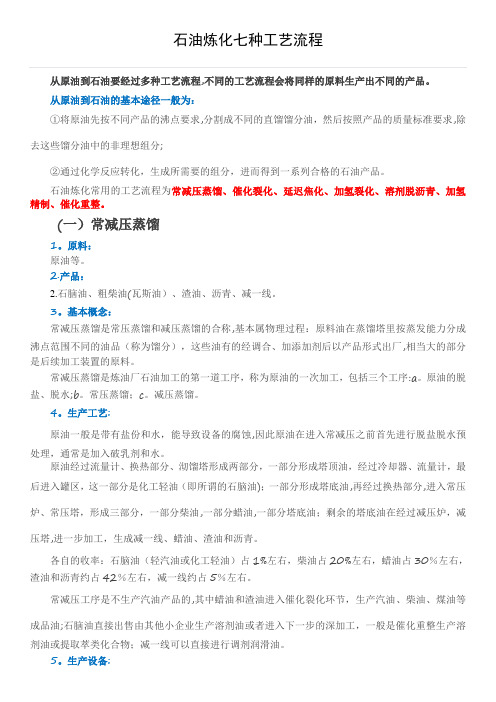
石油炼化七种工艺流程从原油到石油要经过多种工艺流程,不同的工艺流程会将同样的原料生产出不同的产品。
从原油到石油的基本途径一般为:①将原油先按不同产品的沸点要求,分割成不同的直馏馏分油,然后按照产品的质量标准要求,除去这些馏分油中的非理想组分;②通过化学反应转化,生成所需要的组分,进而得到一系列合格的石油产品。
石油炼化常用的工艺流程为常减压蒸馏、催化裂化、延迟焦化、加氢裂化、溶剂脱沥青、加氢精制、催化重整。
(一)常减压蒸馏1。
原料:原油等。
2.产品:2.石脑油、粗柴油(瓦斯油)、渣油、沥青、减一线。
3。
基本概念:常减压蒸馏是常压蒸馏和减压蒸馏的合称,基本属物理过程:原料油在蒸馏塔里按蒸发能力分成沸点范围不同的油品(称为馏分),这些油有的经调合、加添加剂后以产品形式出厂,相当大的部分是后续加工装置的原料。
常减压蒸馏是炼油厂石油加工的第一道工序,称为原油的一次加工,包括三个工序:a。
原油的脱盐、脱水;b。
常压蒸馏;c。
减压蒸馏。
4。
生产工艺:原油一般是带有盐份和水,能导致设备的腐蚀,因此原油在进入常减压之前首先进行脱盐脱水预处理,通常是加入破乳剂和水。
原油经过流量计、换热部分、沏馏塔形成两部分,一部分形成塔顶油,经过冷却器、流量计,最后进入罐区,这一部分是化工轻油(即所谓的石脑油);一部分形成塔底油,再经过换热部分,进入常压炉、常压塔,形成三部分,一部分柴油,一部分蜡油,一部分塔底油;剩余的塔底油在经过减压炉,减压塔,进一步加工,生成减一线、蜡油、渣油和沥青。
各自的收率:石脑油(轻汽油或化工轻油)占1%左右,柴油占20%左右,蜡油占30%左右,渣油和沥青约占42%左右,减一线约占5%左右。
常减压工序是不生产汽油产品的,其中蜡油和渣油进入催化裂化环节,生产汽油、柴油、煤油等成品油;石脑油直接出售由其他小企业生产溶剂油或者进入下一步的深加工,一般是催化重整生产溶剂油或提取萃类化合物;减一线可以直接进行调剂润滑油。
石油炼化常用的七种工艺流程

石油炼化七种工艺流程从原油到石油要经过多种工艺流程,不同的工艺流程会将同样的原料生产出不同的产品。
从原油到石油的基本途径一般为:①将原油先按不同产品的沸点要求,分割成不同的直馏馏分油,然后按照产品的质量标准要求,除去这些馏分油中的非理想组分;②通过化学反应转化,生成所需要的组分,进而得到一系列合格的石油产品。
石油炼化常用的工艺流程为常减压蒸馏、催化裂化、延迟焦化、加氢裂化、溶剂脱沥青、加氢精制、催化重整。
(一)常减压蒸馏1。
原料:原油等。
2.产品:2.石脑油、粗柴油(瓦斯油)、渣油、沥青、减一线。
3.基本概念:常减压蒸馏是常压蒸馏和减压蒸馏的合称,基本属物理过程:原料油在蒸馏塔里按蒸发能力分成沸点范围不同的油品(称为馏分),这些油有的经调合、加添加剂后以产品形式出厂,相当大的部分是后续加工装置的原料.常减压蒸馏是炼油厂石油加工的第一道工序,称为原油的一次加工,包括三个工序:a.原油的脱盐、脱水;b。
常压蒸馏;c.减压蒸馏。
4。
生产工艺:原油一般是带有盐份和水,能导致设备的腐蚀,因此原油在进入常减压之前首先进行脱盐脱水预处理,通常是加入破乳剂和水。
原油经过流量计、换热部分、沏馏塔形成两部分,一部分形成塔顶油,经过冷却器、流量计,最后进入罐区,这一部分是化工轻油(即所谓的石脑油);一部分形成塔底油,再经过换热部分,进入常压炉、常压塔,形成三部分,一部分柴油,一部分蜡油,一部分塔底油;剩余的塔底油在经过减压炉,减压塔,进一步加工,生成减一线、蜡油、渣油和沥青。
各自的收率:石脑油(轻汽油或化工轻油)占1%左右,柴油占20%左右,蜡油占30%左右,渣油和沥青约占42%左右,减一线约占5%左右。
常减压工序是不生产汽油产品的,其中蜡油和渣油进入催化裂化环节,生产汽油、柴油、煤油等成品油;石脑油直接出售由其他小企业生产溶剂油或者进入下一步的深加工,一般是催化重整生产溶剂油或提取萃类化合物;减一线可以直接进行调剂润滑油。
溶剂油的生产流程
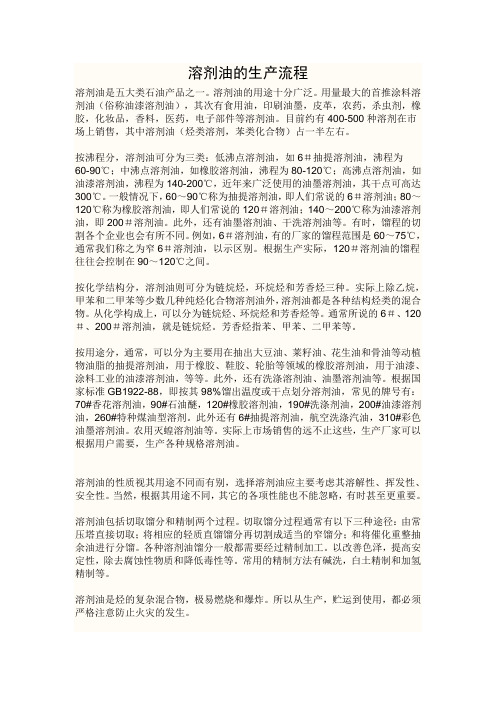
溶剂油的生产流程溶剂油是五大类石油产品之一。
溶剂油的用途十分广泛。
用量最大的首推涂料溶剂油(俗称油漆溶剂油),其次有食用油,印刷油墨,皮革,农药,杀虫剂,橡胶,化妆品,香料,医药,电子部件等溶剂油。
目前约有400-500种溶剂在市场上销售,其中溶剂油(烃类溶剂,苯类化合物)占一半左右。
按沸程分,溶剂油可分为三类:低沸点溶剂油,如6#抽提溶剂油,沸程为60-90℃;中沸点溶剂油,如橡胶溶剂油,沸程为80-120℃;高沸点溶剂油,如油漆溶剂油,沸程为140-200℃,近年来广泛使用的油墨溶剂油,其干点可高达300℃。
一般情况下,60~90℃称为抽提溶剂油,即人们常说的6#溶剂油;80~120℃称为橡胶溶剂油,即人们常说的120#溶剂油;140~200℃称为油漆溶剂油,即200#溶剂油。
此外,还有油墨溶剂油、干洗溶剂油等。
有时,馏程的切割各个企业也会有所不同。
例如,6#溶剂油,有的厂家的馏程范围是60~75℃,通常我们称之为窄6#溶剂油,以示区别。
根据生产实际,120#溶剂油的馏程往往会控制在90~120℃之间。
按化学结构分,溶剂油则可分为链烷烃,环烷烃和芳香烃三种。
实际上除乙烷,甲苯和二甲苯等少数几种纯烃化合物溶剂油外,溶剂油都是各种结构烃类的混合物。
从化学构成上,可以分为链烷烃、环烷烃和芳香烃等。
通常所说的6#、120#、200#溶剂油,就是链烷烃。
芳香烃指苯、甲苯、二甲苯等。
按用途分,通常,可以分为主要用在抽出大豆油、莱籽油、花生油和骨油等动植物油脂的抽提溶剂油,用于橡胶、鞋胶、轮胎等领域的橡胶溶剂油,用于油漆、涂料工业的油漆溶剂油,等等。
此外,还有洗涤溶剂油、油墨溶剂油等。
根据国家标准GB1922-88,即按其98%馏出温度或干点划分溶剂油,常见的牌号有:70#香花溶剂油,90#石油醚,120#橡胶溶剂油,190#洗涤剂油,200#油漆溶剂油,260#特种煤油型溶剂。
此外还有6#抽提溶剂油,航空洗涤汽油,310#彩色油墨溶剂油。
- 1、下载文档前请自行甄别文档内容的完整性,平台不提供额外的编辑、内容补充、找答案等附加服务。
- 2、"仅部分预览"的文档,不可在线预览部分如存在完整性等问题,可反馈申请退款(可完整预览的文档不适用该条件!)。
- 3、如文档侵犯您的权益,请联系客服反馈,我们会尽快为您处理(人工客服工作时间:9:00-18:30)。
目录1、编制依据 .......................................................................... 22、工程概况 .......................................................................... 23、工程特点 .......................................................................... 34、施工部署及资源配置...................................................... 35、管道施工方案 .................................................................. 56、质量保证体系及措施.................................................. 127 、安全保证体系及措施................................................ 148 、材料管理 .................................................................... 179 、文明施工 ........................................... 错误!未定义书签。
10、环境,职业安全健康控制措施................................ 181、编制依据1.1 石家庄炼化分公司常减压装置常一线油生产溶剂油流程改造说明书;1.2 《石油化工有毒、可燃介质管道工程施工及工艺标准》SH3501-2002;1.3《工业金属管道工程施工及验收规范》 GB50235—971.4《现场设备、工业管道焊接工程施工及验收规范》 GB50236—981.5《石油化工设备和管道涂料防腐蚀技术规范》 SH3022-19991.6《石油化工施工安全技术规定》 SH3505-19992、工程概况2.1工程简介石家庄炼化分公司一联合车间常减压装置常一线,生产200#溶剂油,流程简单,根据客户要求溶剂油控制指标较多,尤其是脱后硫醇,水溶性酸碱,腐蚀和博士实验,故此需要流程改造,借用常二线精制进行常一线精制改造。
常一线出装置流量阀前引一条管线至塔008入口进行产品精制,精制后常一线油自塔006返回流量阀前出口装置。
管道长度约为100米。
包括各种规格的管件、阀门、管道支架等。
管道施工区域主要位于一联合车间西南006#,008#塔与容007之间2.2工艺管道主要安装量如下表所示:3、工程特点3.1工程施工场地狭小,各种管道设备林立,工期紧,,而且现场组对、焊接、安装的时间比较集中,因此要重点抓好材料设备进场、各工种之间的相互协调。
3.2施工标高跨度大,0m到+5.400m,要切实做好施工安全、应急工作,严格执行有关手续和相关制度,保证施工安全。
3.3 施工的管道属于压力管道的,焊接检验采用射线探伤,检测时必须合理安排检测时间,做好必要防护,与生产密切配合。
3.4管道安装量大,多种规格,必须在现场作好管件及各类管材的堆放及保管。
3.5为确保如期完工,在安装过程中,准备充分,条件一旦成熟,在保证质量的前提下,文明施工、安全措施到位,拼抢并确保工期。
因此有关各方必须统筹兼顾、适当安排。
4、施工部署及资源配置4.1施工部署4.2资源配置(1)人力资源配置(2)主要工机具资源配置5、管道施工方案5.1管道主要施工程序熟悉图纸及有关技术资料----物料检验----支架制作及安装----管道除锈、喷涂底漆----管道预制及组装----管道敷设与安装----试压及吹扫----管道与设备连接---管道面漆及保温施工----交工验收5.2管道的安装各类管道在安装之前,必须对所进场的管材进行检查,要求必须有合格证,且经现场质检人员检查合格方可投入使用。
5.2.1管道的安装(1)施工时,首先进行常一线出装置管道的施工,依次沿蓝图布管,直至C008#然后返回常一线至塔6完成一分支回路。
最后进行与常一线自水冷器来的管道对接组焊工作。
(2)根据管道在管廊内的走向,用车间内的叉车或手拉倒链,将所需的不同口径的管材放入,进行施工作业。
(3)管道组对前应对管口周围15 mm范围内的内外表面的油漆、铁锈、毛刺等污物清理干净,并按要求制作坡口,然后打磨坡口及坡口周围15mm 范围使其露出金属光泽。
(4)管道的坡口采用氧-乙炔火焰切割,切口表面应平整,无裂纹、重皮、毛刺、凸凹。
表面的熔渣、氧化物、铁屑应磨去,切口端面倾斜偏差不应大于管子外径1%,且不得超过3mm。
(5)管子对口不得采用强力对口、加热管子、加偏垫或多层垫的方法来消除接口断面的空隙、偏差、错口或不同心等缺陷。
(6)施工过程中必须注意,谨防将破布、石块、泥沙等杂物落入管道内。
(7)由于管道的施工,大多是高空作业,因此,管道安装之前,所需管支架(含管支架平台)的安装已基本完成。
该部分管道的安装也是先安装主管道,后安装各支管道。
(8)管道的组对、焊接1)管道的组对:管子对口时应在距接口中心200mm处测量管子的平直度。
管子公称直径小于100mm时允许偏差为2mm以内,管道组对前应对管口周围15 mm范围内的内外表面的油漆、铁锈、毛刺等污物清理干净,并按要求制作坡口,然后打磨坡口及坡口周围15mm范围使其露出金属光泽。
管子对口时可在两节管子中的一节管外壁点焊三根长约300mm的角钢(L90*8)以辅助对口。
管子对口不得采用强力对口、加热管子、加偏垫或多层垫的方法来消除接口断面的空隙、偏差、错口或不同心等缺陷。
管道的坡口采用氧-乙炔火焰切割,切口表面应平整,无裂纹、重皮、毛刺、凸凹。
表面的熔渣、氧化物、铁屑应磨去,切口端面倾斜偏差不应大于管子外径1%,且不得超过3mm。
所有钢管焊接采用坡口焊接,管道管径DN<700时,采用单面坡口; 2)管道组对的特殊要求:管道组对前,应保证管道内部的清洁度。
在组对前,对于小于DN700的管道内部,用10号铁丝捆上棉纱,用人工反复来回在管道的两端拖动,直到管道的内口无杂物、泥砂、浮锈等物;查管道内部有无杂物。
再进行组对管道。
3)管道焊接管道的安装,主要采用焊接连接,焊接管件的端部和拼接焊缝处均应打30°坡口,为了适应误差的要求,根据现场安装的实际情况可在适当位置用包带钢板(δ10mm)连接。
管道焊接接头的坡口,经检查符合技术要求后,方可进行管道焊接,还应符合下列规定:凡参与工业管道焊接的焊工,应持有效的焊工合格证。
焊接分为转动焊和固定焊两种形式,转动焊焊接时,可利用手动葫芦等工具辅助管子转动;固定焊焊接时,对于小管径管道(Dn≤400)可利用手动葫芦等工具,将管子提高地面一段距离(h≤200mm)后焊接管子底部。
本系统对煤气管道及氮气管道的施工要求,管道焊缝按10%的抽检比例进行射线照相检验,其质量不低于Ⅲ级;要求:①焊缝外观成型美观;②表面不得有焊渣、飞溅、裂纹、气孔等现象;③按照设计、国家规范《工业金属管道工程施工及验收规范》GB50235-97、《现场设备、工业管道焊接工程施工及验收规范》 GB50236—9检验及验收。
(2)支吊架的安装支吊架的安装根据设计蓝图的分布,焊固或用膨胀螺栓固定在基础上。
(3)阀门安装阀门安装前应检查填料压盖螺栓必须有足够的调接余量,法兰或螺纹连接的阀门应在关闭状态下安装。
阀门安装前应按设计文件核对阀门的型号,规格,并应检查阀门开启是否灵活。
阀门安装前不得采用强紧螺栓的方法来缩小间距,法兰上各螺栓的受力应均匀。
(4)法兰垫片的安装安装时应对法兰密封面及密封垫片进行外观检查,不得有影响密封性能的缺陷存在,法兰连接时应保持平行,其偏差不能大于法兰外径的1.5%,且不大于2mm,不得采用强紧螺栓的方法消除歪斜,法兰连接时应保持同轴,其螺栓孔中心偏差一般不超出孔径的5%,幷保持螺栓自由穿入。
垫片安装时按设计要求涂上要求的涂剂,软垫片周边也应整齐,垫片尺寸应与法兰密封面相符。
如法兰连接应使用同一规格螺栓,安装方向一致。
紧固螺栓应对称均匀,松紧合适,紧固后外露长度不大于2倍螺距。
螺栓紧固后应与法兰紧贴,不得有锲缝,如需加垫圈时每个螺栓不应超过一个。
(5)管道及其附件的检验:管子、阀门、管件等管道组成件必须具有制造厂的产品合格证书,其材质、重量、规格、型号应符合设计规定,并按国家现行标准进行外观检验,不合格者不得使用。
(6)工业管道安装注意事项1)便于安装和拆卸。
要尽量避免管道多层相迭布置,当不可避免地要多层相迭布置时,两层之间应有足够的间距,可使扳手伸入两层之间紧固每一根管道的连接螺栓或活接头。
2)应不妨碍机械设备的正常运转与检修,不妨碍生产操作人员的正常生产操作。
3)应力求排列整齐美观。
4)根据设计要求,管道采用无缝钢管。
并考虑了管道吹扫用气。
(7)管道允许偏差1)管道组对允许偏差2)管子安装允许偏差5.3管道的压力实验各类介质管道现场(焊接)安装完毕后,应清除内部一切杂物,并进行焊缝质量检查及压力实验。
(2)本系统管道压力试验的压力为工作压力的1.15倍;其试验介质为洁净水。
1)管道压力试验的压力为1.15MPa,在进行压力试验时,当压力升至试验压力的50%时,进行检查,如无泄漏及异常现象,继续按试验压力的10%逐级升压,每级试验压力应稳定3分钟,达到试验压力后应稳定10分钟。
再将压力降至设计压力(1.0MPa),停压时间应根据查漏工作需要而定。
以发泡剂(中性肥皂水)检验无气泡为合格。
2)根据设计要求,管道做严密性试验,其试验压力为0.2mPa;保压24小时,泄露率每小时平均≮0.5%为合格。
注:泄漏率计算方法如下:A = [ 1-(273+t1)×p2/(273+t2)×p1] ×100%其中t1、t2、p1 、p2 为泄漏率试验时起始和终止的温度及压力,温度℃,压力MPa。
5.4管道系统的吹扫和清洗:(1)吹扫1)管道在压力试验合格后应进行吹扫与清洗。
2)吹洗方法应根据对管道的使用要求、工作介质及管道内表面的脏污程度进行。
公称直径小于DN700mm的气体管道宜采用空气吹扫。
3)对有特殊要求的管道应按设计规定采用相应的吹洗方法。
4)不允许吹洗的设备及管道应与吹洗系统隔离。
5)吹洗顺序应按主管、支管、疏排管等依次进行。
吹洗出的脏物不得进入已合格的管道。
6)管道吹洗前不应安装孔板、法兰连接的调节阀、安全阀等重要阀门。