锅炉清洗钝化方案
锅炉化学清洗方案

锅炉化学清洗作业指导书一、作业程序、方法1.1 化学清洗工艺与清洗技术监督指标1.1.1 碱洗介质浓度及温度、时间参数1.1.2 酸洗介质浓度及温度、时间参数1.1.3 清洗回路划分1.1.3.1水冲洗回路1.1.3.1.1 第一回路:凝汽器→凝结水泵→汽封冷却器→低加水侧及旁路→除氧水箱→临时阀门C15、C11→雨水井1.1.3.1.2第二回路:凝汽器→凝结水泵→汽封冷却器→低加水侧及旁路→除氧水箱→前置泵→临时阀门C13(C14)→高加及旁路→省煤器→汽包→水冷壁→临时阀门C1、C3→临时阀门C12→临时阀门C11→雨水井1.1.3.2 碱洗回路第一回路:凝汽器→凝结水泵→汽封冷却器→低加水侧及旁路→除氧水箱→除氧水箱事故放水管→凝汽器第二回路:除氧水箱→前置泵→临时阀门C13(C14)→高加及旁路→省煤器→汽包→水冷壁→临时阀门C1、C3→临时阀门C12→临时阀门C15→电泵入口管道→除氧水箱1.1.3.3 盐酸清洗回路1.1.3.3.1第一回路:清洗箱→清洗泵→临时阀门C5→省煤器→汽包→左、右侧水冷壁组→临时阀门C2、C4→临时阀门C8→清洗箱;1.1.3.3.2第二回路:清洗箱→清洗泵→临时阀门C1→左侧水冷壁组→汽包→右侧水冷壁组→临时阀门C4→临时阀门C8→清洗箱;1.1.3.3.3第三回路:清洗箱→清洗泵→临时阀门C3→右侧水冷壁组→汽包→左侧水冷壁组→临时阀门C2→临时阀门C8→清洗箱;1.1.3.4 过热器充保护液回路清洗箱→清洗泵→C1→左侧水冷壁组→汽包→过热器1.1.4 清洗回路流速核算1.1.5 加热方式1.1.2.1 碱洗:常温进行。
1.1.2.2 盐酸清洗、漂洗、钝化:采用清洗箱投入辅助蒸汽加热。
1.1.6 化学清洗过程中的化学监督1.1.6.1 锅炉清洗前应检查并确认化学清洗用药品的质量和数量、监视管段、金属腐蚀指示片。
指示片称重并测量表面积后挂入并紧固于监视管内。
#2锅炉酸洗方案
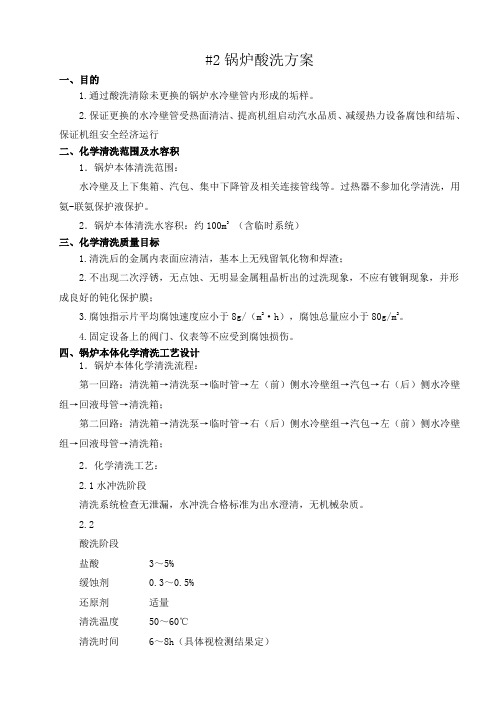
#2锅炉酸洗方案一、目的1.通过酸洗清除未更换的锅炉水冷壁管内形成的垢样。
2.保证更换的水冷壁管受热面清洁、提高机组启动汽水品质、减缓热力设备腐蚀和结垢、保证机组安全经济运行二、化学清洗范围及水容积1.锅炉本体清洗范围:水冷壁及上下集箱、汽包、集中下降管及相关连接管线等。
过热器不参加化学清洗,用氨-联氨保护液保护。
2.锅炉本体清洗水容积:约100m3(含临时系统)三、化学清洗质量目标1.清洗后的金属内表面应清洁,基本上无残留氧化物和焊渣;2.不出现二次浮锈,无点蚀、无明显金属粗晶析出的过洗现象,不应有镀铜现象,并形成良好的钝化保护膜;3.腐蚀指示片平均腐蚀速度应小于8g/(m2·h),腐蚀总量应小于80g/m2。
4.固定设备上的阀门、仪表等不应受到腐蚀损伤。
四、锅炉本体化学清洗工艺设计1.锅炉本体化学清洗流程:第一回路:清洗箱→清洗泵→临时管→左(前)侧水冷壁组→汽包→右(后)侧水冷壁组→回液母管→清洗箱;第二回路:清洗箱→清洗泵→临时管→右(后)侧水冷壁组→汽包→左(前)侧水冷壁组→回液母管→清洗箱;2.化学清洗工艺:2.1水冲洗阶段清洗系统检查无泄漏,水冲洗合格标准为出水澄清,无机械杂质。
2.2酸洗阶段盐酸 3~5%缓蚀剂 0.3~0.5%还原剂适量清洗温度 50~60℃清洗时间 6~8h(具体视检测结果定)2.3酸洗后冲洗阶段pH > 4总铁< 50mg/L2.4漂洗阶段柠檬酸 0.1~0.3% 缓蚀剂 0.1%NH3.H2O 适量pH 3.5~4.0温度 50~60℃漂洗时间 2小时2.5钝化阶段氨水适量pH 9.5~10温度 45~55℃双氧水 0.3~0.5%时间 4~6小时2.6清洗废液处理及排放清洗各阶段,其废液经中和处理pH=6-9后,排到甲方指定排污点。
2.7临时系统的拆除及干燥钝化结束后立刻排放钝化液,尽快拆除临时系统,同时将锅炉清洗系统内所有的疏水门、空气门打开,利用炉膛、炉管余热将炉管内残留水分排出、干燥。
汽包锅炉化学清洗双氧水钝化工艺

在 火力 发 电厂 锅 炉 化 学 清 洗 实 践 中 , 化 工 艺 钝
常采用 的方 法有 : 性 联氨 钝化 工 艺 、 碱 复合 磷 酸盐 钝
化 T艺 工 艺 。
1 双 氧 水 特 性
双 氧水是 一种 强氧化 剂 。高纯 度 双氧 水 的基 本
( ot C iaEetcP w r eerhIstt C . Ld , e ig10 4 C ia N r hn lc i o e sac ntue O , t. B in 0 0 5, hn ) h r R i j
Abs r c t a t:To e p u d t e a v n a e o l ai e p r xdepa sv t n tc n l g n t e b i rCh mi x o n h d a t g fa k ln e o i s ia i e h oo y i h ol e — o e c l— la i g p s ia in.Th c n mia n la l ai e peo ie p s ia in tc n lg s t a —ce n n  ̄ a sv to e e o o c la d ce n a k ln r xd a sv t e h oo y i he o c ra n te d o u b ie h mia e i r n fdr m o lrc e c l—c e n n  ̄ p s ia in t c n lg . t la i g a sv to e h o o y Ke y wor ds:e v r n n a r tc in;c e c lce n n n io me tlp o e t o h mia la i g;h drg n peo ie;p si ain y o e r xd a sv to
钝化处理资料

概述钝化处理是化学清洗中最后一个工艺步骤,是关键一步,其目的是为了材料的防腐蚀。
锅炉经酸洗、水冲洗、漂洗后,金属表面很清洁,非常活化,很容易遭受腐蚀,所以必须立即进行钝化处理,使清洗后的金属表面生成保护膜,减缓腐蚀。
用途对不锈钢全面酸洗钝化处理,清除各类油污、锈、氧化皮、焊斑等污垢,处理后表面变成均匀银白色,大大提高不锈钢抗腐蚀性能,适用于各种型号不锈钢零件、板材及其设备。
特点操作简单,使用方便、经济实用,同时添加了高效缓蚀剂、抑雾剂,防止金属出现过腐蚀和氢脆现象、抑制酸雾的产生。
特别适用于小型复杂工件,不适合涂膏的情况,优于市场同类产品。
用法根据不锈钢的材质和氧化皮严重程度不同,可以用原液或按1:1~4的比例加水稀释后使用;铁素体、马氏体和镍含量低的奥氏体不锈钢(如420、430、200、201、202、300、301等)稀释后使用,镍含量较高的奥氏体不锈钢(如304、321、316、316L等)用原液浸泡;一般常温或加热到50~60度后使用,浸泡3-20分钟或更长时间(具体时间和温度用户根据自己的试用情况确定),至表面污垢完全清除,成均匀银白色,形成均匀致密的钝化处理膜为止,处理完成后取出,用清水冲洗干净,最好再用碱水或石灰水冲洗中和。
钝化处理:用铬酸盐溶液与金属作用在其表面生成三价或六价铬化层的过程,称为钝化,亦名铬化。
多用于铝、镁及其合金的处理,对钢铁也能形成铬化层,但很少单独使用,常和磷化配套使用,以封闭磷化层的孔隙,使磷化层中裸露的钢铁钝化,以抑制残余磷化加速剂的腐蚀作用,进一步增加防护能力。
钝化时一般用重铬酸钾溶液(2~4克/升,有时也加入1~2克磷酸),在80-90摄氏度浸啧2-3分钟取出,水洗即可在蚀刻不锈钢工艺中,我们常常遇着产品发黄,这里我们需要钝化工艺来处理。
1)一次钝化液的成分及工作条件组成及条件彩色钝化钝化后要漂白组成用条件彩色钝化钝化后要漂白液及温度的浓度及温度液及温度的浓度及温度铬酸 250~300G/l 200~250G/l 硫酸 10~20ML/L 24~30ML/L30~40ML/L 15~20ML/L 温度 30~40度室温2)二次印化溶液的组成及工作条件:氨三乙酸-氯化铵锌如果采用二次钝化工艺,钝化膜色泽均匀,五彩鲜艳,膜层细致,膜与镀锌层结合力好,防腐蚀性也比一次钝化好。
锅炉酸洗技术方案

锅炉酸洗技术方案1.基本情况1.14#炉:10m3,钙镁垢,厚度约1mm。
1.25#炉:10m3,钙镁垢,厚度约1mm。
1.36#炉:14m3,钙镁垢,厚度约1mm。
2.酸洗2.1酸洗顺序为4#炉、5#炉、6#炉,挂片位置为每台锅炉的上锅筒。
2.2酸洗液为7.5%的稀盐酸溶液,采用浓度约34%的工业盐酸配制。
2.3采用俄罗斯产固体缓蚀剂,浓度0.8%,于配酸前加入配药桶的清水内。
2.4按要求配制好洗液,由排污管送入锅炉,并充满上锅筒。
2.5炉内加热,温度控制在40—50℃。
2.6采用底部进酸、上锅筒顶部出酸的方式分部循环。
4#炉、5#炉按左右联箱及对流管三个循环单元、6#炉按前后左右及对流管五个循环单元循环至酸洗终点。
2.7热动车间安排专人取样送检,取样位置为表面排污管,时间间隔为30min。
中心化验室对酸洗全程的药液进行检测,检测项目为酸浓度、Fe3+浓度、Fe2+浓度。
当酸浓度、Fe2+浓度稳定,Fe3+浓度越过峰值下降时为酸洗终点。
2.8排酸,水冲洗至PH值4—5,检查清淤,取挂片送中心化验室检测腐蚀速度。
2.94#炉的酸洗废液经40目筛过滤后进配药桶,配制7.5%的盐酸溶液酸洗5#炉。
5#炉的酸洗废液经40目筛过滤后进配药桶,配制7.5%的盐酸溶液酸洗6#炉,同时补充计算量的缓蚀剂。
3.钝化3.1钝化剂采用Na3PO4+NaOH,浓度为0.6%+0.5%,PH值10—12,4#炉、5#炉用量均为60㎏+156㎏(液碱),6#炉用量为84㎏+218㎏(液碱).3.2钝化温度80±5℃。
3.3钝化时间≥12h。
3.4排碱,水冲洗至PH值8—9。
考虑酸洗液对中段水的影响,4#炉的钝化时间可延长,钝化液与6#炉的酸洗液同步排放。
4.养护锅炉酸洗、钝化完毕后,通过除氧箱注入软水充满上锅筒,同时添加Na3PO4,浓度为0.5%,煮沸除氧,除氧水浸泡锅炉至开车。
除氧过程中注意保持溢流孔的的畅通。
锅炉碱洗方案2_实施方案_
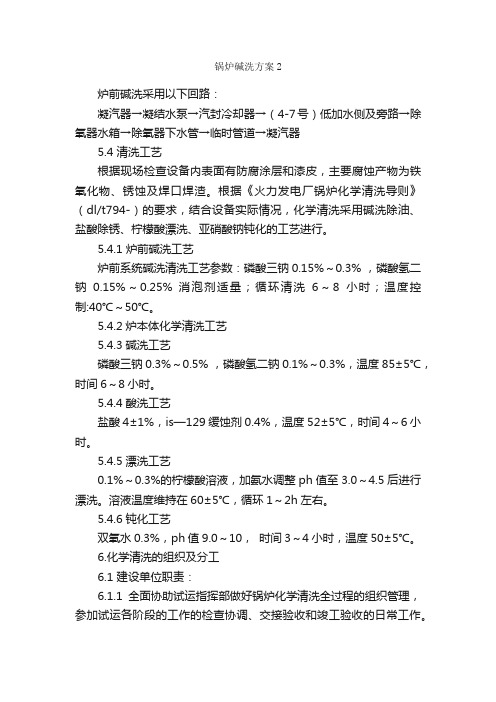
锅炉碱洗方案2炉前碱洗采用以下回路:凝汽器→凝结水泵→汽封冷却器→(4-7号)低加水侧及旁路→除氧器水箱→除氧器下水管→临时管道→凝汽器5.4 清洗工艺根据现场检查设备内表面有防腐涂层和漆皮,主要腐蚀产物为铁氧化物、锈蚀及焊口焊渣。
根据《火力发电厂锅炉化学清洗导则》(dl/t794-)的要求,结合设备实际情况,化学清洗采用碱洗除油、盐酸除锈、柠檬酸漂洗、亚硝酸钠钝化的工艺进行。
5.4.1 炉前碱洗工艺炉前系统碱洗清洗工艺参数:磷酸三钠0.15%~0.3% ,磷酸氢二钠0.15%~0.25% 消泡剂适量;循环清洗6~8小时;温度控制:40℃~50℃。
5.4.2炉本体化学清洗工艺5.4.3碱洗工艺磷酸三钠0.3%~0.5% ,磷酸氢二钠0.1%~0.3%,温度85±5℃,时间6~8小时。
5.4.4酸洗工艺盐酸4±1%,is—129缓蚀剂0.4%,温度52±5℃,时间4~6小时。
5.4.5漂洗工艺0.1%~0.3%的柠檬酸溶液,加氨水调整ph值至3.0~4.5后进行漂洗。
溶液温度维持在60±5℃,循环1~2h左右。
5.4.6钝化工艺双氧水0.3%,ph值9.0~10,时间3~4小时,温度50±5℃。
6.化学清洗的组织及分工6.1 建设单位职责:6.1.1全面协助试运指挥部做好锅炉化学清洗全过程的组织管理,参加试运各阶段的工作的检查协调、交接验收和竣工验收的日常工作。
6.1.2协调解决执行中的问题和外部关系等。
6.1.3协调完成各项生产准备工作,包括水、汽、电等的供应。
6.1.4参加该系统分部试运后的验收签证6.2 生产单位的职责6.2.1清洗期间的供水、供汽,供电。
6.2.2锅炉化学清洗期间正式系统的操作。
6.2.3腐蚀指示片的称重、标记和保管工作。
6.3监理单位及调试单位职责:6.3.1按合同对整个酸洗工作进行检查、监督。
6.3.2监督本方案的实施,参加试运工作并验收签证。
锅炉酸洗后钝化工艺的思考

在 扬 州 某 自备 电 厂一 台 1 0/ 的锅 炉 清 洗 当 中 ,采用 邻 厂 的 lTh 3T} v O / 的工业锅炉提供蒸汽,且蒸汽管道为 07 ,采用碱液钝化方法 ( 68 磷酸三 钠)供热蒸汽 由于其他用户太多 , , 在加热五个小时的情况下 , 温度还在 5 ℃左右 , 0 根本不能进行钝化, 最后在多方协商后 , 增加一台工业锅炉供 热 , 用管 道 接 至临 时 系统 , 并 才解 决 了温 度 的问 题 。但 是也 错 过 了最 好 的 钝化时机, 延长 了工作周期 , 打乱整个 工作的安排 , 所以说工艺温度的选 择 还是 很 重要 的 。 在制 定 工艺 时 候 , 一定 要结 合 现 场 的状 况 , 虑 到 可能 发 生 的特 殊情 考 2 钝 化 工艺 简 介 况, 选择合理的钝化工艺 , 在合适的温度下完成钝化工作 。如果供热有困 经 过 酸洗 、 冲洗 或 漂洗 后 的 金属 表 面 , 水 当暴露 于 大 气 中时 非 常容 易 难的 , 尽量选择温度适 中的工艺 , 对于温度要求 高的工艺 , 操作时候还要 受到腐蚀。因此 , 应立 即进行防腐处理, 其办法就是用某些药液处理 , 使金 注 意安 全 方面 的事 情 , 防治蒸 汽 泄露 、 伤人 事 故的 发 生 。 属表 面生 成保 护 膜 , 种处 理通 常 称 为钝化 。 这 3 时间。 . 3 锅炉酸洗的时间安排通常都是很紧凑的 , 新建机组的酸洗意味 着 投 运 的倒 计 时 ;运 行 锅 炉的 酸 洗要 求 短期 内完 成 ,不 要影 响 机组 的发 目前钝化的T艺一般有以 下几种: 21 碱 液钝 , ̄ 。此 法 是 采用 1 2 . f J c %一 %的 磷 酸 三钠 和 氧氧 化 钠 的混 合 液 , 电 , 以时 间安 排 得 其 重要 性 。 所 将 其 用 酸洗 泵 打 人 到锅 炉 内 , 热 到 7 ~O 在 酸 洗 同路 中 循 环 1~ 2 加 0 9 ℃, O l 酸洗过程巾时间安排是很讲究的, 牵涉到工作的安排 , 钝化的工作相 小 时 , 除盐 水 进 行 冲洗 , 排 出 的水 的 碱度 和 磷酸 根 与 锅炉 运 行 时所 对 于 酸洗 循 环 阶段 显 得要 节 奏缓 和很 多 ,可 以 考虑 到 时 间安 排 在夜 间进 用 直至 行 容许 的 标准 相近 为 止 。将各 部 分 的水全 部 放 完 , 钝化 处 理就 结束 l r。 用此方法金属表面会产生黑色的保护膜 , 这种保护膜的防腐性能 , 一 另外 , 需要考虑 的是钝化时间的长短 , 在苏州某热 电公司的 2 基建 } } 般只 用 于 中 、 压锅 炉 。 低 炉清洗 中, 由于安装工作中出现 了一定的拖后 , 18 而 6 运行的时间 已经确 22 过 氧化 氢钝 化 法 。 氧 化氢 法 利用 过 氧化 氢 的氧 化作 用 , 般 采用 初 定 , . 过 一 酸洗工作时间非常紧张 , 酸洗方案最终确定时 , 在 经过多方协商采用 时 相对 于其 他 的方 始剂量 02 04 调节 p - %~ _ %, H到 95 l , .~O 钝化温度 4 ~ 5 时间 5 7小时, 多聚 磷 酸钠 钝 化 方法 , 间大 约 需要 两 个 小时 就 可 以 了 , 5 5 ℃, ~ 该方法工艺 比较简单 , 钝化温度低 , 氧化膜致密牢同 , 外观和保护效 果较 法 , 可以节约的时间相当可观。并且钝化]作的时候 , 二 整个酸洗工作小组 都 已经非 常 疲 劳 , 有 一 定的 安 全隐 患 , 择 较 少 时 问的 工艺 本 身 可 以节 具 选 好 。其 排放 对环 境 污染 很 小 , 方法 的运 用 会越 来 越广 。 此 2 亚硝酸钠钝化法 。此疗法通常使用 1 2 . 3 %~ %的亚硝酸钠溶液, 并且加 约相关资源 , 尽量减少潜在的事故发生的概率, 顺利完成整个酸洗工作 。 氨水调节 p H值到 9 1 , ~ 0温度维持到 5 ~O 使溶液在系统 中循环 6 l 3 废液排放。 0 6℃, ~O . 4 酸洗过程中废液的排放是涉及到环境保护的重要项 目, 钝 小时, 排 溶液后, 钝化过程结束。此法能在酸洗后 的新鲜的金属表面 卜 化液的排放也要符合相关的规定和标准,废液处理要考虑到当地环境保 形成致密的 、 呈钢灰色的保护膜。 护的相关政策,业主的污水处理能力和条件 ,厂区的设计布局等各种因 2 联氨钝化法。此法是用配制好的 30 5 0 / . 4 0 ~ 0 mg L的联氨溶液加入到锅 素 。 炉中, 调解 p H值为 9 ~ 0 . l 左右 , 5 维持温度在 9 ~0 ℃, 0 10 使溶液在系统内 每个企业的废水池的容量及到酸洗现场的距离各不相同 , 另外 , 各种 循环 2 ~ 0 4 5 小时。此方法存应用时 , 温度高些 , 循环时间长些 , 钝化的效果 化学品都有其 自身的特性 , 必须综合考虑多方 面因素。例如, 对于亚硝酸 往往要好些 。处理结束后 , 金属表面会生成棕红色或棕褐色的保护膜。该 钠 这 样 的化 学 品 , 能 与 酸液 排 人 到同 一个 池 内 , 会 生成 大 量氮 氧 化 不 否则 方法处理结束后 , 可以将钝化液流在系统巾直 到机组启动前 , 作为防腐除 物 气 体 , 成 滚 滚 黄炯 , 重 污 染空 气 , 亚 硝 酸钠 是 很 强 的致 癌物 质 , 形 严 并且 氧 剂 , 止金属 表 面 的浮 锈的 再 次生 成 。 防 使 月 时要 非常 的小 心 , 后 必须 进 行 处理 才 能排放 。 j 最 该 方 法 钝化 温 度 要求 较 高 , 间 长 , 化 膜 耐 蚀性 较 差 , 且 联 氨 的 时 钝 并 在浙江余姚一发电厂基建锅炉清洗中,方案开始制定的时候是将废 毒性 很强 , 方 法 当属 于逐 渐 淘汰 之列 。 此 液排 放 到 中 和池 的 , 过 现 场 的勘 查 , 现 其 污水 处 理设 备 离锅 炉 距 离非 经 发 2 多聚磷酸钠钝化法。此法 又叫多聚磷酸钠漂洗钝化一步法 ,采用 常远 , . 5 达到两百多米, 给管道安装带来很大的困难 , 而且整个废液处理设 01%~ . %的 H 0 %~ _ .5 02 0 O 和 . 03 2 %的 N l溶 液 ,H 值 调 节 到 25 备未经过调试, a O0 P p .~ 这个方案的可行性很差 , 经过项 目组和多方的协 商, 最后 3 温 度维持 4 ℃左右 , . 5 5 循环漂洗 1 2 ~ 小时。漂洗结束后在溶液中加入氨 在酸洗现场附近挖 了一个 10立方左右的土坑 , 0 用塑料薄膜垫好 , 当成临 水调节 p H值 至 9 ~O升 温 至 7 ~ 5 , 循环 钝 化 12小 时 , 法 生 成 时废液处理池使用, . 1, 5 58℃ 再 ~ 此 待排放进去的废液处理合格后 , 再进行排放。 的保护膜耐蚀性不及亚硝酸钠法 , 废液处置 、 排放 比较简单。 相关废液处理的方法和标准 , 以参照 1/ 9 - 0 1火力发电厂锅 可 3 1 4 20 ( 17 ( 2 其他 方 法 。 些其 他 方法 的 清洗 方 法 , E T 酸洗钝 化 一 步就 可 以 炉化学清洗导则》 . 6 一 如 DA 及其他相关标准法规。 完 成 了 , 还 出 现 了一 些 复合 酸 清洗 剂 , 化 的 具体 工 作 就不 必 单独进 35 其他 。 最近 钝 . 钝化工艺还要考虑到酸洗单位的操作水平和人员素质 , 尽量选 行了。 择熟 悉 的易 于操 作 的 方法 , 确保 _ 的安 全 和 质量 。另外 , 关 药品 的 价 丁程 相 3 相 关 因素 的选 择 格、 运输 、 采购 、 储存 、 毒性和腐蚀性 , 现场操作 的天气条件 , 环境状况都是 在 酸洗 方 案制 定 的 时候 , 须根 据 实 际的 状 况选 择 酸 洗钝 化 的工 艺 , 值得 考 虑 的因 素 。 必 根据现场操作的具体经验 , 总结影响钝化工艺的主要因素大致如下: 结 束语 31 效果和质量。酸洗工程首先要考虑形成 良好 、 . 致密的保护膜 , 特别是 钝化_艺结束后 , T 虽然形成了临时性的保护膜 , 但这种保护膜长时间 酸洗结束到投运间隔的时间比较 长的情况下, 更强调保护膜的长期性, 一 暴露在空气中仍然会发生腐蚀。 如果机组到下次启动的时间间隔较长, 应 般情况下 , 保护膜都可 以在半个月内有效防止浮锈产生 , 亚硝酸钠钝化法 该选择采用其他相关的停用保护方法。 形成 的膜 , 观 和质 地 上都 比较 优 良。 从外 从 构建 和 谐 社 会 的 角度 来 说 , 开发 无 毒 、 公 害 、 能 的钝 化 处 理 工 无 节 32 温 度 。钝 化时 候 温度 条件 也各 不 相 同 , 别 在 电站 锅 炉钝 化 工 艺 中 , 艺 , 现绿 色 化学 的 技术 要求 , 是该 方 面技 术工 作 者的 努 力方 向 。 . 特 实 将 热源是首先提供到酸洗��
锅炉清洗方案
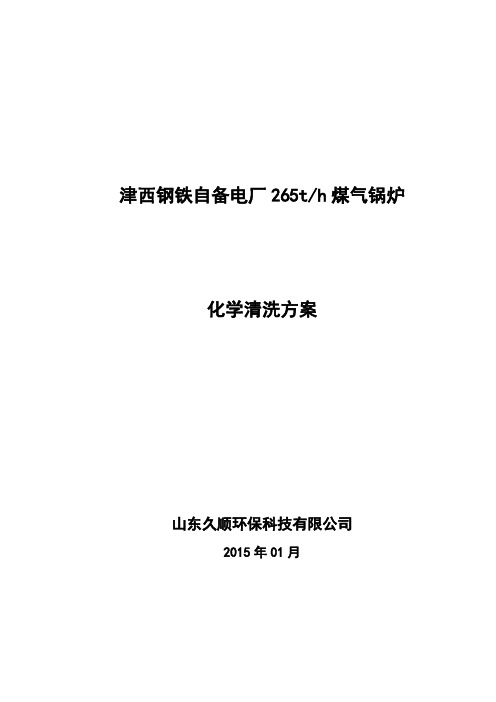
津西钢铁自备电厂265t/h煤气锅炉化学清洗方案山东久顺环保科技有限公司2015年01月目录1、概述2、编制依据3、锅炉主要参数4、锅炉运行水容积5. 化学清洗范围6、化学清洗工艺7、锅炉清洗前应具备的条件8、化学清洗临时系统的安装(详见系统图)9、锅炉化学清洗程序10、化学清洗监督项目11、清洗质量的验收标准和清洗效果的检查12、职责分工13、化学清洗的安全措施14、化学清洗用水量及所用药剂量估算15、附录附图锅炉化学清洗作业指导书1、概述该锅炉为新建锅炉,由于锅炉在制作、安装过程中锅妒内部受热面存在扎制鳞片、铁锈、防腐油脂等污物。
根据锅炉运行的技术要求,开车前必须采用化学清洗,能够有效地将这些垢物除去,从而保证受热表面经过化学清洗后的清洁。
达到改善锅炉水汽品质,保证锅炉安全运行的目的。
同时也为了减缓锅炉的腐蚀及节省能源,根据《火力发电厂锅炉化学清洗导则》2012修订本的规定,锅炉水系统和省煤器必须进行化学清洗。
根据《火力发电厂锅炉化学清洗导则》的规定,确定化学清洗工艺为:水冲洗、酸洗、酸洗后的水冲洗、漂洗,钝化。
清洗范围为汽包、省煤器及部分给水管、水冷壁及上下联箱等。
2、编制的依据2.1《火力发电厂锅炉化学清洗导则》(DL/T794-2012)2.2《电力建设施工及验收技术规范》第四部分:电厂化学(DL/T5190.4-2004)2.3《电力建设施工及验收技术规范》系列标准2.4《电力建设施工及验收技术规范》系列标准2.5《电力基本建设热力设备化学监督导则》(DL/T889-2004)2.6《电力建设安全工作规程》(火力发电厂部分)(DL5009.1-2002)2.7 《特种设备安全技术规范锅炉化学清洗规则》(TSG G5003-2004)3、锅炉主要参数4、水容积表(m3):表1 锅炉水容积表表2 酸洗范围内各部件的相关材质表5、化学清洗范围根据锅炉结构及运行状况,本次化学清洗的主要范围为省煤器、汽包、水冷壁、下降管及连接管道等。
锅炉化学清洗方法
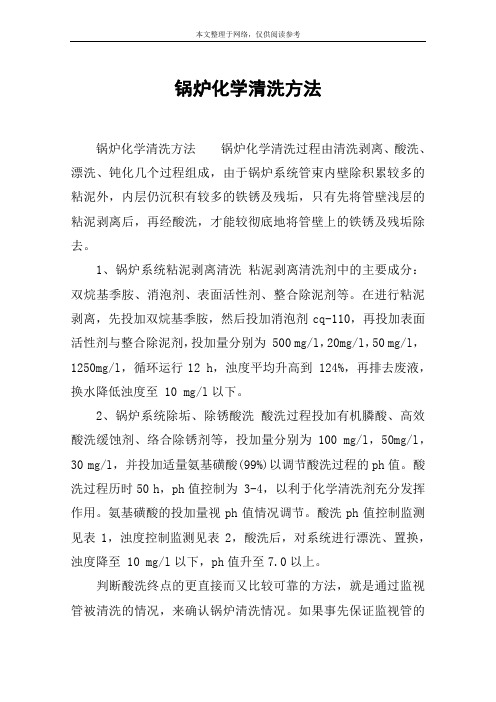
锅炉化学清洗方法锅炉化学清洗方法锅炉化学清洗过程由清洗剥离、酸洗、漂洗、钝化几个过程组成,由于锅炉系统管束内壁除积累较多的粘泥外,内层仍沉积有较多的铁锈及残垢,只有先将管壁浅层的粘泥剥离后,再经酸洗,才能较彻底地将管壁上的铁锈及残垢除去。
1、锅炉系统粘泥剥离清洗粘泥剥离清洗剂中的主要成分:双烷基季胺、消泡剂、表面活性剂、整合除泥剂等。
在进行粘泥剥离,先投加双烷基季胺,然后投加消泡剂cq-110,再投加表面活性剂与整合除泥剂,投加量分别为 500 mg/l,20mg/l,50 mg/l,1250mg/l,循环运行12 h,浊度平均升高到 124%,再排去废液,换水降低浊度至 10 mg/l以下。
2、锅炉系统除垢、除锈酸洗酸洗过程投加有机膦酸、高效酸洗缓蚀剂、络合除锈剂等,投加量分别为 100 mg/l,50mg/l,30 mg/l,并投加适量氨基磺酸(99%)以调节酸洗过程的ph值。
酸洗过程历时50 h,ph值控制为 3-4,以利于化学清洗剂充分发挥作用。
氨基磺酸的投加量视ph值情况调节。
酸洗ph值控制监测见表1,浊度控制监测见表2,酸洗后,对系统进行漂洗、置换,浊度降至 10 mg/l以下,ph值升至7.0以上。
判断酸洗终点的更直接而又比较可靠的方法,就是通过监视管被清洗的情况,来确认锅炉清洗情况。
如果事先保证监视管的垢和锅炉的垢基本一致,以及清洗条件也基本一致,那么当监视管被清洗干净的时候,也就可以认为锅炉也被清洗干净。
适当延长一些时间就可结束酸洗。
3、水冲洗酸洗结束后,应将酸洗液以最快速度排放,并以尽可能短的时间和尽可能高的流速冲洗清洗系统,使清洗水的ph 值到达4~5,水冲洗即可结束。
4、钝化将锅炉加热升温,同时按整个容积计算一次加入钝化药剂,并不断循环。
升温到预计温度后,停止加热,并开始取样分析碱的浓度,调整ph值到10~11(ph值不计超过12)后,循环或浸10~12小时,钝化结束。
5、水冲洗将钝化液排放,用水冲洗到ph值为8~9,整个化学清洗工程即告结束。
锅炉清洗后采用EDTA二钠做漂洗钝化剂试验

TM 6 - 2l 8
[ 文献 标识码 ] A
3 4 2 10 0 3 [ 章 编 号 ] 1 02—3 6 ( 01 ) 6—0 82~0 文 0
I O 编 号] 1 . 9 9 J is . 0 2—3 6 . 0 1 0 . 8 D l 0 3 6 / .sn 1 0 34 2 1.60 2 TES FoR I T US NG EDTA oDI S UM ALT NS NG S AS RI I AGENT
AND PAS I S VATOR N I CHEM I CAL CLEANI NG oF BoI LERS
CH EN a f ng Xio a
Xi a e i we ce c n c n l g d, ’ n 7 0 5 S a n iPr v n e PRC ’ n Xi l Po r S i n e a d Te h o o y Co Lt XI a 1 0 4, h n x o i c ,
目前广 泛使用 的《 力发 电厂锅 炉化学 清洗 导则 》 火 ( / 9 —2 0 ) DL T 7 4 O 1 推荐 的 电站锅 炉化 学清 洗 ( 以下 简 称 清洗 ) 钝化 工艺 普 遍 存 在 钝 化 温 度 高 、 间 长 等 问 时
此 , 对 电站锅 炉化学 清洗钝 化工 艺进行研 究 。 需
。
锅 炉 清 洗 后 采用 E T D A二 钠 做 漂洗 钝 化 剂试 验
陈晓 芳
西安 协力动 力科技 有 限公 司, 陕西 西安 7 0 5 10 4
蓄
[ 摘
要] 目前 电站锅 炉化 学清洗后 , 用传统 的化 学清洗钝 化 剂 因不能满足 环保 、 采 节能 的要 求而
锅炉清洗钝化方案

锅炉清洗钝化方案一、方案编制依据1、本方案编制依据中华人民共和国行业标准HG/T2387-92《工业设备化学清洗质量标准》。
2、中华人民共和国电力行业标准DL/T794—2001《火力发电厂锅炉化学清洗导则》;3、中华人民共和国电力行业标准GB50050—1995《工业循环冷却水处理设计规范》二、清洗的范围、目的及清洗方式1、甲方的锅炉在长期运行过程当中,形成了以碳酸钙为主要成分并含有硅酸盐、铁锈等成分的复合型垢物。
该垢物附着在锅炉壁表面,经长期积累,致使换热效果下降,不能满足正常的生产需求。
长此以往,不但会影响到该设备的正常运行,还有可能对生产造成安全隐患。
因此,对该锅炉进行化学清洗是十分必要的。
2、化学清洗是利用化学药剂与设备内表面的有机污物、铁锈、等进行反应、溶解,从而达到清洁去油污的过程。
3、对于该设备的化学清洗,根据现场分析及我们丰富的施工经验,我们决定采用水冲洗→清洗→水冲洗→人工检查复位的清洗工艺流程进行清洗。
三、化学清洗工艺过程水冲洗→化学清洗→中和→水冲洗→钝化→人工检查复位1、水力冲洗水力冲洗的目的是除去锅炉内的灰尘、浮锈、泥沙等杂物。
冲洗至目测进水与出水的澄清度相近时结束。
2、化学清洗2.1、药剂:速效除垢剂、缓蚀剂2.2、药剂用量:速效除垢剂的投加浓度为100-150Kg/T,缓蚀剂的投加浓度为50-100Kg/T2.3、工艺条件温度:45±5℃时间:12-24小时2.4、实施步骤将所需的速效除垢剂、缓蚀剂缓慢地由入口中加入到锅炉中(水温保持45±5℃)。
12-24小时后,置换清水,至水样正常。
3、中和3.1、药剂:中和剂3.2、药剂用量:中和剂的投加浓度为100-150Kg/T;3.3、工艺条件温度:常温时间:0.5-1小时3.4、实施步骤:将定量的中和剂缓慢加入到锅炉中(常温)。
循环0.5-1小时后,置换清水,至水样正常。
4、水冲洗4.1、清洗结束后水冲洗的目的是除去锅炉内药剂残液。
汽包锅炉化学清洗双氧水钝化工艺
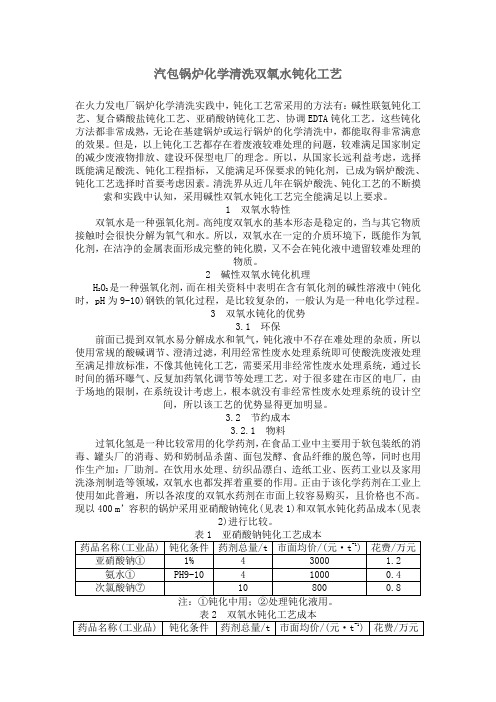
汽包锅炉化学清洗双氧水钝化工艺在火力发电厂锅炉化学清洗实践中,钝化工艺常采用的方法有:碱性联氨钝化工艺、复合磷酸盐钝化工艺、亚硝酸钠钝化工艺、协调EDTA钝化工艺。
这些钝化方法都非常成熟,无论在基建锅炉或运行锅炉的化学清洗中,都能取得非常满意的效果。
但是,以上钝化工艺都存在着废液较难处理的问题,较难满足国家制定的减少废液物排放、建设环保型电厂的理念。
所以,从国家长远利益考虑,选择既能满足酸洗、钝化工程指标,又能满足环保要求的钝化剂,已成为锅炉酸洗、钝化工艺选择时首要考虑因素。
清洗界从近几年在锅炉酸洗、钝化工艺的不断摸索和实践中认知,采用碱性双氧水钝化工艺完全能满足以上要求。
1 双氧水特性双氧水是一种强氧化剂。
高纯度双氧水的基本形态是稳定的,当与其它物质接触时会很快分解为氧气和水。
所以,双氧水在一定的介质环境下,既能作为氧化剂,在洁净的金属表面形成完整的钝化膜,又不会在钝化液中遗留较难处理的物质。
2 碱性双氧水钝化机理H 2O2是一种强氧化剂,而在相关资料中表明在含有氧化剂的碱性溶液中(钝化时,pH为9-10)钢铁的氧化过程,是比较复杂的,一般认为是一种电化学过程。
3 双氧水钝化的优势3.1 环保前面已提到双氧水易分解成水和氧气,钝化液中不存在难处理的杂质,所以使用常规的酸碱调节、澄清过滤,利用经常性废水处理系统即可使酸洗废液处理至满足排放标准,不像其他钝化工艺,需要采用非经常性废水处理系统,通过长时间的循环曝气、反复加药氧化调节等处理工艺。
对于很多建在市区的电厂,由于场地的限制,在系统设计考虑上,根本就没有非经常性废水处理系统的设计空间,所以该工艺的优势显得更加明显。
3.2 节约成本3.2.1 物料过氧化氢是一种比较常用的化学药剂,在食品工业中主要用于软包装纸的消毒、罐头厂的消毒、奶和奶制品杀菌、面包发酵、食品纤维的脱色等,同时也用作生产加:厂助剂。
在饮用水处理、纺织品漂白、造纸工业、医药工业以及家用洗涤剂制造等领域,双氧水也都发挥着重要的作用。
化学清洗后的钝化处理

化学清洗后的钝化处理(总4页)--本页仅作为文档封面,使用时请直接删除即可----内页可以根据需求调整合适字体及大小--化学清洗后的钝化处理摘要介绍化工设备在化学清洗后进行钝化处理的必要性以及相关的钝化处理技术的原理钝化剂性能处理工艺并指出使用环保型的钝化剂是今后钝化工艺的发展方向关键词化学清洗钝化预膜1 前言在化工行业中大量使用锅炉换热器管道贮罐反应器等设备在运行一段时间后这些设备会因工艺介质的沉积黏附和工艺介质对设备的腐蚀而结成壁垢附着在设备表面,从而引起降低传热降低流速堵塞和引起垢下腐蚀等问题给生产带来危害。
解决这些问题的有效途径是进行清洗,除去垢层。
并且随着石油化工等行业的发展需要清洗的设备越来越多因此化学清洗对于维护设备就显得非常重要。
化学清洗后,除去了垢层的金属设备表面会露出金属本体因化学清洗多为酸碱液经过化学清洗后,金属表面会变得异常活泼,在接触外界(如空气等)很容易使金属表面被再次腐蚀生锈因此在化学清洗后必须要进行钝化处理,使设备表面形成保护膜延长设备的使用寿命。
化学清洗后的钝化处理,能够有效地保护设备,所以它是整个化学清洗过程中的一个重要环节,具有重要的意义。
2 钝化原理金属设备经过化学清洗后,金属表面处于活化状态与氧接触很容易产生腐蚀通过一定的处理后来达到使它不易被腐蚀的目的。
钢铁处于活泼状态时在清洗后的水冲洗中腐蚀主要是受水的pH 氧浓度和时间的影响因此在钝化前要处理好水冲洗过程使在钝化处理之前有一个洁净度良好的金属表面。
如果水冲洗时间过长或其他因素影响,可以在钝化前对清洗设备进行漂洗处理。
各种钝化工艺其原理各有不同,总体上可分为形成氧化性膜和沉积性膜吸附膜两类钝化工艺。
氧化性膜钝化工艺主要是使用具有氧化性的钝化剂进行处理,使钢铁表面形成致密Y的氧化铁膜,合金钢中形成Y氧化铁膜和含铬的氧化性膜。
吸附膜钝化工艺,主要是利用各种无机盐的溶液对金属进行处理。
由于各种不同的金属盐在水中的溶度积不同,形成的难溶盐在金属表面沉积而形成致密的钝化膜。
5号机锅炉酸洗实例及钝化优化方案
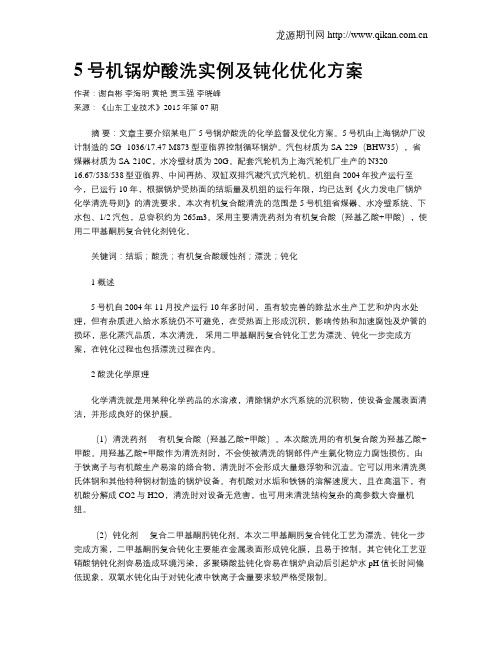
5号机锅炉酸洗实例及钝化优化方案作者:谢自彬李海明黄艳贾玉强李晓峰来源:《山东工业技术》2015年第07期摘要:文章主要介绍某电厂5号锅炉酸洗的化学监督及优化方案。
5号机由上海锅炉厂设计制造的SG--1036/17.47-M873型亚临界控制循环锅炉。
汽包材质为SA-229(BHW35),省煤器材质为SA-210C,水冷壁材质为20G。
配套汽轮机为上海汽轮机厂生产的N320-16.67/538/538型亚临界、中间再热、双缸双排汽凝汽式汽轮机。
机组自2004年投产运行至今,已运行10年,根据锅炉受热面的结垢量及机组的运行年限,均已达到《火力发电厂锅炉化学清洗导则》的清洗要求。
本次有机复合酸清洗的范围是5号机组省煤器、水冷壁系统、下水包、1/2汽包,总容积约为265m3。
采用主要清洗药剂为有机复合酸(羟基乙酸+甲酸),使用二甲基酮肟复合钝化剂钝化。
关键词:结垢;酸洗;有机复合酸缓蚀剂;漂洗;钝化1 概述5号机自2004年11月投产运行10年多时间,虽有较完善的除盐水生产工艺和炉内水处理,但有杂质进入给水系统仍不可避免,在受热面上形成沉积,影响传热和加速腐蚀及炉管的损坏,恶化蒸汽品质,本次清洗,采用二甲基酮肟复合钝化工艺为漂洗、钝化一步完成方案,在钝化过程也包括漂洗过程在内。
2 酸洗化学原理化学清洗就是用某种化学药品的水溶液,清除锅炉水汽系统的沉积物,使设备金属表面清洁,并形成良好的保护膜。
(1)清洗药剂----有机复合酸(羟基乙酸+甲酸)。
本次酸洗用的有机复合酸为羟基乙酸+甲酸。
用羟基乙酸+甲酸作为清洗剂时,不会使被清洗的钢部件产生氯化物应力腐蚀损伤。
由于铁离子与有机酸生产易溶的络合物,清洗时不会形成大量悬浮物和沉渣。
它可以用来清洗奥氏体钢和其他特种钢材制造的锅炉设备。
有机酸对水垢和铁锈的溶解速度大,且在高温下,有机酸分解成CO2与H2O,清洗时对设备无危害,也可用来清洗结构复杂的高参数大容量机组。
什么是钝化处理_注意事项

什么是钝化处理_注意事项钝化处理的目的是为了材料的防腐蚀,使清洗后的金属表面生成保护膜,减缓腐蚀。
那么你对钝化处理了解多少呢?以下是由店铺整理关于什么是钝化处理的内容,希望大家喜欢!什么是钝化处理化学清洗中最后一个工艺步骤,是关键一步,其目的是为了材料的防腐蚀。
如锅炉经酸洗、水冲洗、漂洗后,金属表面很清洁,非常活化,很容易遭受腐蚀,所以必须立即进行钝化处理,使清洗后的金属表面生成保护膜,减缓腐蚀。
在自动控制领域,还有一种专用名称“通道钝化”。
在故障安全系统(F-SYSTEM)中如果-> F-I/O 检测到故障,则将受影响的通道或所有通道切换至 -> 安全状态,即该 F-I/O的通道被钝化。
钝化处理的技术原理金属经氧化性介质处理后,其腐蚀速度比原来未处理前有显著下降的现象称金属的钝化。
其钝化机理主要可用薄膜理论来解释,即认为钝化是由于金属与氧化性介质作用,作用时在金属表面生成一种非常薄的、致密的、覆盖性能良好的、能坚固地附在金属表面上的钝化膜。
这层膜成独立相存在,通常是氧和金属的化合物。
它起着把金属与腐蚀介质完全隔开的作用,防止金属与腐蚀介质直接接触,从而使金属基本停止溶解形成钝态达到防止腐蚀的效果钝化处理是化学清洗中最后一个工艺步骤,是关键一步,其目的是为了材料的防腐蚀。
如锅炉经酸洗、水冲洗、漂洗后,金属表面很清洁,非常活化,很容易遭受腐蚀,所以必须立即进行钝化处理,使清洗后的金属表面生成保护膜,减缓腐蚀。
钝化处理的主要用途对不锈钢全面酸洗钝化处理,清除各类油污、锈、氧化皮、焊斑等污垢,处理后表面变成均匀银白色,大大提高不锈钢抗腐蚀性能,适用于各种型号不锈钢零件、板材及其设备。
钝化处理的基本特点操作简单,使用方便、经济实用,同时添加了高效缓蚀剂、抑雾剂,防止金属出现过腐蚀和氢脆现象、抑制酸雾的产生。
特别适用于小型复杂工件,不适合涂膏的情况,优于市场同类产品。
钝化处理的操作方法根据不锈钢的材质和氧化皮严重程度不同,可以用原液或按1:1~4的比例加水稀释后使用;铁素体、马氏体和镍含量低的奥氏体不锈钢(如420、430、200、201、202、300、301等)稀释后使用,镍含量较高的奥氏体不锈钢(如304、321、316、316L等)用原液浸泡;一般常温或加热到50~60度后使用,浸泡3-20分钟或更长时间(具体时间和温度用户根据自己的试用情况确定),至表面污垢完全清除,成均匀银白色,形成均匀致密的钝化处理膜为止,处理完成后取出,用清水冲洗干净,最好再用碱水或石灰水冲洗中和。
- 1、下载文档前请自行甄别文档内容的完整性,平台不提供额外的编辑、内容补充、找答案等附加服务。
- 2、"仅部分预览"的文档,不可在线预览部分如存在完整性等问题,可反馈申请退款(可完整预览的文档不适用该条件!)。
- 3、如文档侵犯您的权益,请联系客服反馈,我们会尽快为您处理(人工客服工作时间:9:00-18:30)。
一、方案编制依据
1、本方案编制依据中华人民共和国行业标准HG/T2387-92《工业设备化学清洗质量标准》。
2、中华人民共和国电力行业标准DL/T794—2001《火力发电厂锅炉化学清洗导则》;
3、中华人民共和国电力行业标准GB50050—1995《工业循环冷却水处理设计规范》
二、清洗的范围、目的及清洗方式
1、甲方的锅炉在长期运行过程当中,形成了以碳酸钙为主要成分并含有硅酸盐、铁锈等成分的复合型垢物。
该垢物附着在锅炉壁表面,经长期积累,致使换热效果下降,不能满足正常的生产需求。
长此以往,不但会影响到该设备的正常运行,还有可能对生产造成安全隐患。
因此,对该锅炉进行化学清洗是十分必要的。
2、化学清洗是利用化学药剂与设备内表面的有机污物、铁锈、等进行反应、溶解,从而达到清洁去油污的过程。
3、对于该设备的化学清洗,根据现场分析及我们丰富的施工经验,我们决定采用水冲洗→清洗→水冲洗→人工检查复位的清洗工艺流程进行清洗。
三、化学清洗工艺过程
水冲洗→化学清洗→中和→水冲洗→钝化→人工检查复位
1、水力冲洗
水力冲洗的目的是除去锅炉内的灰尘、浮锈、泥沙等杂物。
冲
洗至目测进水与出水的澄清度相近时结束。
2、化学清洗
2.1、药剂:速效除垢剂、缓蚀剂
2.2、药剂用量:
速效除垢剂的投加浓度为100-150Kg/T,缓蚀剂的投加浓度为50-100Kg/T
2.3、工艺条件
温度:45±5℃
时间:12-24小时
2.4、实施步骤
将所需的速效除垢剂、缓蚀剂缓慢地由入口中加入到锅炉中(水温保持45±5℃)。
12-24小时后,置换清水,至水样正常。
3、中和
3.1、药剂:中和剂
3.2、药剂用量:
中和剂的投加浓度为100-150Kg/T;
3.3、工艺条件
温度:常温
时间:0.5-1小时
3.4、实施步骤:
将定量的中和剂缓慢加入到锅炉中(常温)。
循环0.5-1小时后,置换清水,至水样正常。
4、水冲洗
4.1、清洗结束后水冲洗的目的是除去锅炉内药剂残液。
4.2清洗结束后,用大量的清水反复冲洗锅炉,在冲洗过程中应将各排污阀门开大。
当进出口及各排污口的水质澄清,即可结束清洗。
5、钝化
5.1、药剂:钝化剂
5.2、药剂用量:
钝化剂的投加浓度为150Kg/T;
5.3、工艺条件
温度:95±5℃
时间:8-12小时(注:时间越长钝化效果越好。
)
5.4、实施步骤:
将定量的钝化剂缓慢加入到锅炉中(水温保持95±5℃)。
8-12小时后,置换清水,至水样正常。
6、人工清理复位
清洗完工后,对锅炉进行详细检查,彻底清除局部死角部位的垢物残渣,合格后复位。
四、质量标准保证
除垢率应达到规定的指标或复合《锅炉化学清洗导则》中的标准。
(1)、清洗后的金属表面应清洁,基本无残留垢物;无明显金属粗晶析出的过洗现象。
(2)、用腐蚀指示剂片测量的金属平均腐蚀速度应小于6g/m2·h,腐
蚀总量小于60g/m2
五、安全措施
1、全体清洗工作人员必须认真学习、严格遵守甲方和本公司的各项安全规定。
2、施工前,由安全、技术人员为施工人员进行培训或交底,使他们掌握清洗的安全操作规程,熟悉各种药剂的性能和灼伤急救方法。
3、施工现场悬挂安全警示牌,严禁明火,备有消防设备,闲杂人员不许近前。
4、施工现场应该整洁平坦,照明充足并有救急和冲洗水源、急救药品。
5、施工人员必须穿戴安全帽、防护服、防护靴、胶皮手套,必要时戴好防护眼镜,方可操作。