IE七大手法、精益生产
IE工业工程七大手法的实施技巧
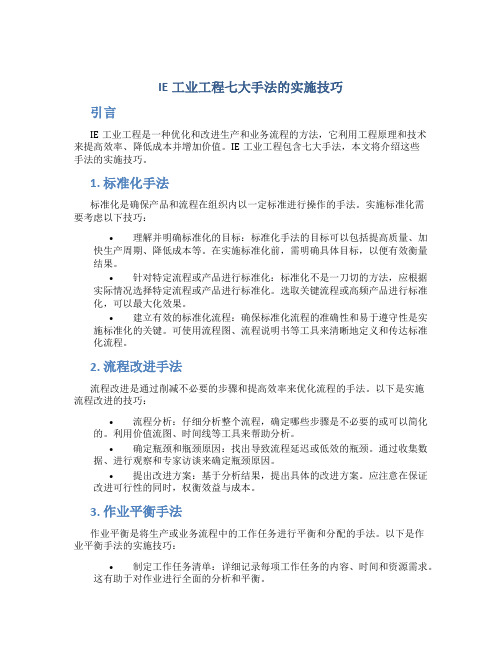
IE工业工程七大手法的实施技巧引言IE工业工程是一种优化和改进生产和业务流程的方法,它利用工程原理和技术来提高效率、降低成本并增加价值。
IE工业工程包含七大手法,本文将介绍这些手法的实施技巧。
1. 标准化手法标准化是确保产品和流程在组织内以一定标准进行操作的手法。
实施标准化需要考虑以下技巧:•理解并明确标准化的目标:标准化手法的目标可以包括提高质量、加快生产周期、降低成本等。
在实施标准化前,需明确具体目标,以便有效衡量结果。
•针对特定流程或产品进行标准化:标准化不是一刀切的方法,应根据实际情况选择特定流程或产品进行标准化。
选取关键流程或高频产品进行标准化,可以最大化效果。
•建立有效的标准化流程:确保标准化流程的准确性和易于遵守性是实施标准化的关键。
可使用流程图、流程说明书等工具来清晰地定义和传达标准化流程。
2. 流程改进手法流程改进是通过削减不必要的步骤和提高效率来优化流程的手法。
以下是实施流程改进的技巧:•流程分析:仔细分析整个流程,确定哪些步骤是不必要的或可以简化的。
利用价值流图、时间线等工具来帮助分析。
•确定瓶颈和瓶颈原因:找出导致流程延迟或低效的瓶颈。
通过收集数据、进行观察和专家访谈来确定瓶颈原因。
•提出改进方案:基于分析结果,提出具体的改进方案。
应注意在保证改进可行性的同时,权衡效益与成本。
3. 作业平衡手法作业平衡是将生产或业务流程中的工作任务进行平衡和分配的手法。
以下是作业平衡手法的实施技巧:•制定工作任务清单:详细记录每项工作任务的内容、时间和资源需求。
这有助于对作业进行全面的分析和平衡。
•根据员工技能和能力进行任务分配:利用员工的专业技能和能力,合理地分配任务。
确保任务的复杂程度和员工的技能匹配。
•定期监控和调整:监控作业的执行情况,及时调整任务分配以实现平衡。
4. 工作测量手法工作测量是通过收集和分析数据来评估工作任务的工作量、效率和效果的手法。
以下是实施工作测量的技巧:•确定测量指标:根据工作任务的目标和要求,选择合适的测量指标。
IE工业工程改善七大手法

IE工业工程改善七大手法概述IE工业工程是指以科学方法为基础,运用系统工程理论和方法,在生产过程中对人、机、料、法、环境进行综合优化的一门工程学科。
IE工业工程改善七大手法是指在IE工业工程领域中常用的七种改善方法,本文将详细介绍这七大手法。
1. 横向流程优化横向流程优化是指通过对生产过程中不同环节进行分析,找出其中存在的瓶颈和浪费,并采取相应的措施来优化流程。
这种方法可以提高生产效率,减少物料和资源浪费,同时还能提升产品质量。
横向流程优化通常包括以下几个步骤: - 流程分析:对生产流程进行细致的分析,了解每个环节的具体操作和所需资源。
- 瓶颈分析:找出流程中的瓶颈环节,即造成生产效率降低和浪费的主要原因。
- 流程改善:通过重新设计流程或引入新的技术和设备,解决瓶颈环节问题,从而提升整体流程效率。
2. 垂直流程优化垂直流程优化是指在生产过程中,对整个生产线上下游环节进行优化,以实现生产过程的高效协同。
垂直流程优化的关键是实现信息的及时传递和合理协调,以确保每个环节对上下游环节的要求和交接点的协调。
垂直流程优化通常包括以下几个方面: - 信息流优化:通过引入信息化系统或升级现有系统,实现信息的实时传递和共享,从而提高生产过程中的响应速度和准确性。
- 协调改善:通过改善沟通和协作机制,减少生产过程中的延误和误解,提高协同效率。
- 质量管理:在生产过程中引入全面质量管理的理念和方法,强调各个环节的质量控制和持续改进。
3. 设备改善设备改善是指通过技术改进和设备优化来提高生产效率和产品质量。
设备改善可以通过以下方式实现: - 技术创新:引入新的生产技术和设备,提高生产过程中的效率和自动化程度。
- 设备维护:建立定期维护和保养计划,保证设备的正常运行和延长使用寿命。
- 能源节约:优化设备的能源使用,减少能源消耗和环境污染。
4. 物料管理物料管理是指对生产过程中的原材料和半成品进行有效的控制和管理,以确保生产过程的顺利进行。
IE工程(七大手法)
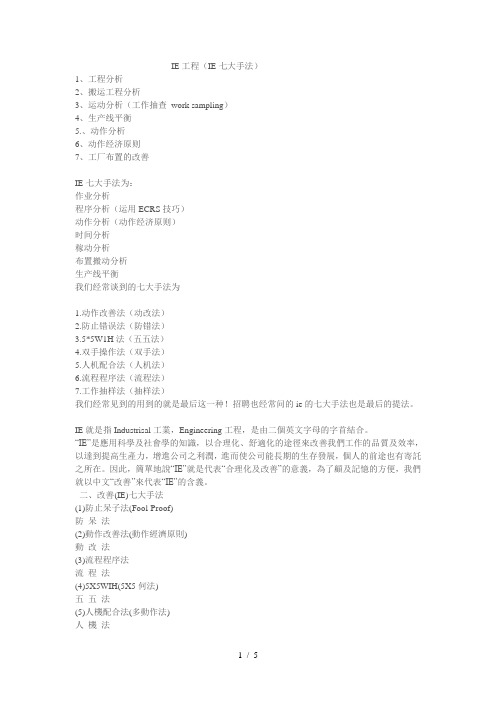
IE工程(IE七大手法)1、工程分析2、搬运工程分析3、运动分析(工作抽查work sampling)4、生产线平衡5.、动作分析6、动作经济原则7、工厂布置的改善IE七大手法为:作业分析程序分析(运用ECRS技巧)动作分析(动作经济原则)时间分析稼动分析布置搬动分析生产线平衡我们经常谈到的七大手法为1.动作改善法(动改法)2.防止错误法(防错法)3.5*5W1H法(五五法)4.双手操作法(双手法)5.人机配合法(人机法)6.流程程序法(流程法)7.工作抽样法(抽样法)我们经常见到的用到的就是最后这一种!招聘也经常问的ie的七大手法也是最后的提法。
IE就是指Industrisal工業,Engineering工程,是由二個英文字母的字首結合。
“IE”是應用科學及社會學的知識,以合理化、舒適化的途徑來改善我們工作的品質及效率,以達到提高生產力,增進公司之利潤,進而使公司能長期的生存發展,個人的前途也有寄託之所在。
因此,簡單地說“IE”就是代表“合理化及改善”的意義,為了顧及記憶的方便,我們就以中文“改善”來代表“IE”的含義。
二、改善(IE)七大手法(1)防止呆子法(Fool-Proof)防呆法(2)動作改善法(動作經濟原則)動改法(3)流程程序法流程法(4)5X5WIH(5X5何法)五五法(5)人機配合法(多動作法)人機法(6)雙手操作法雙手法(7)工作抽查法抽查法改善(IE)七大手法與品管(QC)七大手法之差別“品管(QC)七手法”較著重於對問題的分析與重點的選擇,但對如何加以改善則較少可應用。
“改善(IE)七手法”較著重於客觀詳盡瞭解問題之現象,以及改善方法的應用,以期達到改善的目標。
有了“改善(IE)七手法”正可彌補品管(QC)手法的缺陷而達到相輔相成之效果,使得改善的效果更為落實也更容易實現。
同時最重要的是改善(IE)七手法亦可單獨使用,因其本身具有分析、發掘問題的技巧之故。
防呆法(Fool-Proof)一、目的認識“防呆法”的意義,及學習如何應用“防呆法”的原理於我們的工作上,以避免工作錯誤的發生,進而達到“第一次就把工作做對”之境界。
IE精益生产的七大手法
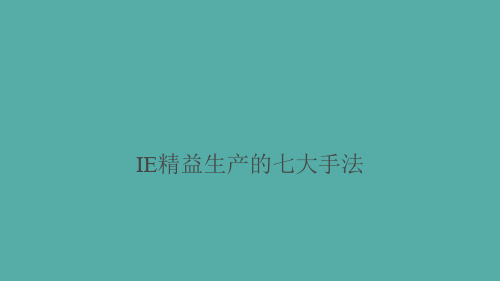
IE精益生产的七大手法
前言
1
质量代表了一个国家的科学技术、生产水平、管理水平和文化 水平.
产品质量的提高,意味着经济效益的提高.当今世界经济的发展正 经历着由数量型增长向质量型增长的转变,市场竟争也由人格竟争 为主转向质量竟争为主.
而所有企业的目的均系希望以最小的投入(INPUT)得到最大的产 出(OUTPUT),以致独得最大的效益.那么如何在质量保证的基础上, 使企业独得最大的效益呢?只有降低成本和提高企业的生产力,把 这些“投入”做最有效的组合,以达到质量稳定、效率高、交期准、 浪费少、成本低.这就是近代工业界工业工程(IE)所要做
IE七大手法之四 — 五五法
17
1.手法名称: 5 * 5W 1H法;又称5 * 5何法;又称质疑创意法;简称五五法.
2.目的: 学习本手法的目的是在:
熟悉有系统的质问的技巧,以协助吾人发掘出问题的真正 根源所在以及可能的创造改善途径. 3.名词释义 3.1 基本观念 * 头脑就像降落伞,○○○只有在开放的情况下才工作○○○. * 工作改善最大的阻碍,并不在于技术不足,而是在于一个人的想法~当他觉得是以最好的方 法在工作着,并且以为满足. * 当您认为工作已无法改善了,那就代表您已落伍了,虽然您是专家,拥有高深的学识. * 一个虽没有多大学识的人,只要他认为工作仍有改善的可能,那么他就比您更 适合这工作.
现场管理改善(IE)的七大手法

现场管理改善(IE)的七大手法前言现场生产管理的重点在于持续不断的改善,通过改善现场的不良状况以使工作变得“轻松、良好、迅速、低廉、安全”,可是在我们的实际工作中有相当一部分现场管理干部和员工不知道何为改善、为什么要改善、怎么样改善,或者说没有良好的改善理念和改善意识,怎么样才能发挥员工的主观能动性呢? 基于此,本人籍由工作经验及相关参考总结出了一些改善的思维和方法,借以抛砖引玉。
1. 什么是改善?改而使之善: 使原来的状况变得更好.2. 改善是谁的责任? 什么样的人才可以从事改善?改善是每个人份内之事.工作改善其中九成,只要有常识就可以做到-------(国际劳工组织改善课课长说)3. 改善的目的是什么?改善的目的------使工作更“轻松、良好、迅速、低廉、安全”.轻松------熟练的作业,疲劳的减轻; 良好------品质的维护提升;迅速------时间的缩短低廉------成本的降低;安全------伤害的防止4. 正确的改善思想a) 现状必定有值得改善的地方;b) 只要目前的工作稍有改善,就有所获得;c) 绝对要拚弃“小小的改善又有什么用”的观念----向前看,积少成多,积沙成塔;d) 本身的工作,自己是一等一的专家(工作中学习,学习后工作);5. 改善从哪里开始?改善开始于“这样做妥当吗?”的问题意识----心不在焉,视而不见,食而不知其味;小小的巧思, 可能就是改善的开始------信其当然, 顺其自然, 不惑对日常工作关心, 时时想改善, 才会触发改善的灵感;6. 改善从何处入手?容易疲劳危险而容易受伤作业环境不良布置不善错误失败多费时费力工夹检具不良耗料较多改善(IE)七大手法简述1. 防呆法(防错法): 如何避免做错事, 使工作第一次就做好的精神能够具体实现.2. 动改法(动作改善法&动作经济原则): 改善人体的动作方法,减少疲劳使工作更为舒适,更有效率,不要蛮干.3. 流程法(流程程序法): 研究探讨牵涉到几个不同的工站(序)或地点的流动关系, 藉以发掘可供改善的地方;4. 五五法(5*5W1H):凭借问的技巧来发觉改善的构想;5. 人机法(人机配合法&多动作法): 研究探讨操作人员与机械工作的过程, 藉以发觉可以改善的地方;6. 双手法(左.右手法): 研究人体在工作时的过程, 藉以发掘可以改善的地方;7. 抽查法(工作抽查法): 藉着由抽样观察察的方法迅速有效的了解问题的真象;一防呆法(防错法)1. 防错法的意义: 如何去防止错误发生的方法. 將发生的可能性降至最低/杜绝其发生;2. 目的:2.1 具有即使人为疏忽也不会发生错误的构造-----不需要注意力;2.2 具有外行人来做也不会发生错误的构造-----不需要经验与直2.3 具有不管是谁或何时工作都不会出错的构造-----不需要高度的技能或专门的知识;3. 功用:积极----绝不会在发生;消极----发生率降至最低;4. 进行步骤:调查发现人为疏忽----> 设定目标,制定实际计划----->调查人为疏忽的原因----->提出防错的改善方案-----> 实施改善方案-----> check 实施效果-----> 维持管制状态*技巧* 排除法: 剔除会造成问题的原因;替代法: 利用更切实的方法替代;容易化: 使作业变得更容易,更合适,集中化,使其更具共性以减低失败;异常检出: 前站虽有不良, 后站可以挑出,以降低其危害性;缓和影响: 作业失败的影响在其波及过程中, 用正确的方法使其缓和或吸收;*观念*要求捕捉更多的鱼, 首先必须讲究捕鱼技术的传授与使用;(授之以鱼不如授之以渔: 给某人几条鱼不如教给他捕鱼的方法)*引申*以不教而战, 谓杀之. 不教其方法, 做错是主管之错*防呆法的应用*² 断根原理: 将原因从根本上排除, 使之不会发生错误;如: 下水道盖板/防护栏加高² 保险原理: 籍由2个以上的动作或依序才能完成工作;如: 冲床双按钮/保险丝使用² 相符原理: 籍用检核是否相符的动作,来防止错误的发生;如: 角度检测器/自动机转向机构² 隔离原理: 分割不同的方式,保护某些地区使其不造成危险或错误发生;如: 不良品盒的使用/材料区的划分² 曾别原理: 线条粗细,不同的颜色如: 工艺颜色/特别管制线(斑马线)二动改法A. 有关人体运用的原则原则一: 两手同时开始及完成动作(试想独臂作业?)原则二: 除休息时间外,两手不能同时空闲;原则三: 双臂的动作应尽量同时平衡对称;同时动作能使心理和生理上产生平衡的感觉,减少应用身体的应力机会,工作起来较轻松愉快.原则四: 尽可能以最低等级动作工作(动作等级分类:如下表)人体动作共分五级,愈低等级的动作所耗时间愈短,愈不容易疲劳级别一二三四五运动枢纽指节手腕肘肩身区人体运动部分手指+手掌+前臂+上臂+肩动作范围手指节长度手掌长度前臂长度上臂长度上臂+身区长度速度 1 2 3 4 5体力消耗最少少中多最多动作力量最弱弱中強最强疲劳度最小小中大最大原则五: 物体的动量尽可能运用之(比如搬动大模板尽量滑动或滚动)所谓动量=质量X速度(亦可理解为冲量)原则六: 运动方向应连续有规律,不宜突变.研究表明: 方向突变不但浪费时间,而且容易疲劳.原则七: 动作宜轻松有节奏.韵律节奏指: 有定期性的重复动作发生;原则八: 弹道式运动较轻快总结省力的动作及姿势,形成习惯;B. 有关工作场所布置与环境之原则原则一: 工具物料置于固定处所整理整顿的重要性: 减少寻找时间物料摆放五定: 定点、定位、定品、定型、定量原则二: 工作物料装置应依工作顺序排列并置于近处(就近原则,便于取放),使工作物料在使用过程中活动范围减至最小。
精益管理-IE7大手法

在我心目中,模具是工业之母,IE就是工业之父。母亲给你成长的基础,父亲给你茁壮的空间。
工程能力、工序时间
2
是否有不必要的延迟。
延迟时间
3
搬运的路线、方法、次数、负荷是否适当。
路线图、次数Leabharlann 频度、负荷、搬运工具4搬运距离是否可以缩短。
搬运距离、搬运时间
5
是否有等待时间,等待时间可否缩短。
等待时间、次数
6
可否同时进行加工和检查。
加工方法、加工时间、检查方法、检查时间
7
制品的品质如何。
不良率、不良项目
◆ 正常的操作条件
◆ 中等偏上水平的熟练度
◆ 标准的作业方式
◆ 普通作业者的强度与速度
◆ 符合质量标准
3.2.3 标准工时测量的最佳条件
3.2.2 标准工时的计算方法
02 IE改善的基本方法
连续测时法
重复测时法
周期测时法
摄影法(高速、普通、低速)
其他
直接法
马表法
WF法
MTM法
其他
既定时间(PTS法)
02 IE改善的基本方法
周期作业继续时间观测用约表(表11.2)
“美国值得向全世界夸耀的东西就是IE,之所以打赢第一次世界大战,又有打胜第二次世界大战的力量,就是因为美国有IE”
8
设备的配置合理与否。
设备能力、台数
9
现场有无抱怨。
抱怨项目、安全、满意度
2.1 制品流程分析 检查项目表
02 IE改善的基本方法
作业者流程分析 的对象是“人”,制品流程分析的对象是“物”。
其主要目的有以下几点: 发现是否有不必要的延迟。 发现动作路线、方法、次数或负荷是否适当。 发现动作距离是否可以缩短。 发现是否有等待时间,是否可以缩短等待时间。 发现是否可以同时进行加工和检查。 发现动作或相关的配置、顺序、组合是否适当。 发现动作对品质、效率的影响和可能的改善点。
精益生产ie之七大手法

精益生产ie之七大手法包括:
1.防呆法:如何避免做错事情,使工作第一次就做好的精神能够
具体实现。
2.动改法:改善人体动作的方式,减少疲劳使工作更为舒适、更
有效率,不要蛮干。
3.流程法:研究探讨牵涉到几个不同工作站或地点之流动关系,
藉以发掘出可资改善的地方。
4.五五法:借着质问的技巧来发掘出改善的构想。
5.人机法:研究探讨操作人员与机器工作的过程,藉以掘出可资
改善的地方。
6.双手法:研究人体双手在工作时的过程,藉以发掘出可资改善
的地方。
7.抽查法:借着抽样观察的方法能很迅速有效地了解问题的真相。
IE七大手法、精益生产
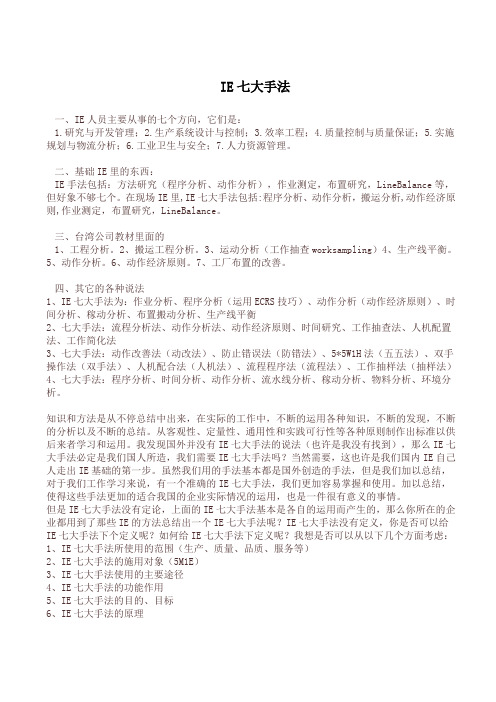
IE七大手法一、IE人员主要从事的七个方向,它们是:1.研究与开发管理;2.生产系统设计与控制;3.效率工程;4.质量控制与质量保证;5.实施规划与物流分析;6.工业卫生与安全;7.人力资源管理。
二、基础IE里的东西:IE手法包括:方法研究(程序分析、动作分析),作业测定,布置研究,LineBalance等,但好象不够七个。
在现场IE里,IE七大手法包括:程序分析、动作分析,搬运分析,动作经济原则,作业测定,布置研究,LineBalance。
三、台湾公司教材里面的1、工程分析。
2、搬运工程分析。
3、运动分析(工作抽查worksampling)4、生产线平衡。
5、动作分析。
6、动作经济原则。
7、工厂布置的改善。
四、其它的各种说法1、IE七大手法为:作业分析、程序分析(运用ECRS技巧)、动作分析(动作经济原则)、时间分析、稼动分析、布置搬动分析、生产线平衡2、七大手法:流程分析法、动作分析法、动作经济原则、时间研究、工作抽查法、人机配置法、工作简化法3、七大手法:动作改善法(动改法)、防止错误法(防错法)、5*5W1H法(五五法)、双手操作法(双手法)、人机配合法(人机法)、流程程序法(流程法)、工作抽样法(抽样法)4、七大手法:程序分析、时间分析、动作分析、流水线分析、稼动分析、物料分析、环境分析。
知识和方法是从不停总结中出来,在实际的工作中,不断的运用各种知识,不断的发现,不断的分析以及不断的总结。
从客观性、定量性、通用性和实践可行性等各种原则制作出标准以供后来者学习和运用。
我发现国外并没有IE七大手法的说法(也许是我没有找到),那么IE七大手法必定是我们国人所造,我们需要IE七大手法吗?当然需要,这也许是我们国内IE自己人走出IE基础的第一步。
虽然我们用的手法基本都是国外创造的手法,但是我们加以总结,对于我们工作学习来说,有一个准确的IE七大手法,我们更加容易掌握和使用。
加以总结,使得这些手法更加的适合我国的企业实际情况的运用,也是一件很有意义的事情。
精益生产ie七大手法

精益生产ie七大手法
精益生产是一种管理学和生产技术,旨在减少浪费,提高生产效
率和质量,其主要思想是在质量、生产力和员工安全方面提高效率,
以改善消费者的满足度,并实现持续改进。
IE七大手法是精益生产最
重要和基本的方法,用于消除浪费和提高效率。
它们包括:
1.品质控制:通过检查有效改善质量,以降低后期维修和缺陷率。
2.标准化:制定有效的标准,以改善工作流程和完成工作更快更
准确。
3.专业化:了解不同专业之间的界限,确定不同专业中最佳做法,并优化生产流程。
4.见贤思齐:借鉴成功业务的理念,应用于其他业务领域,以改
善生产效率。
5.自动化:实施自动化技术,提高生产效率,降低操作成本。
6.改善:采用改进技术,定期检查及时改进不断地改善生产效率
和质量。
7.一体化:一体化的方式生产,以改善生产力和满足客户的需求。
2024年度IE七大手法

生产线现状分析
收集生产线相关数据,分析生产线的瓶颈和 问题。
生产线平衡计算
计算生产线的平衡率和平滑指数,评估生产 线的平衡性能。
生产线改善措施
针对生产线的不平衡现象,采取相应措施进 行改善,如调整工序、增加设备等。
2024/3/23
改善效果评估
对改善后的生产线进行效果评估,验证改善 措施的有效性。
35
通过分析生产流程,取消不必要的工序、操作或动作,减少浪费。
合并(Combine)
将多个工序或操作合并为一个,提高生产效率。
重排(Rearrange)
重新安排生产流程,使工序更加合理,减少等待和空闲时间。
简化(Simplify)
简化复杂的工序或操作,降低工作难度和强度,提高生产效率。
33
案例二:人机法在设备操作改善中的应用
界面交互设计
设计符合用户心理和行为习惯的 交互方式,使人与机器的交互更 加自然、顺畅。同时,考虑不同 用户群体的需求和特点,提供个
性化的交互体验。
2024/3/23
16
04
生产线平衡
2024/3/23
17
生产线平衡的定义与意义
定义
生产线平衡是对生产线上各工序所需 时间进行平均化,使各工序时间与瓶 颈工序时间尽可能接近,进而实现生 产线的顺畅、高效运行。
2024/3/23
6
IE七大手法在工业生产中的应用
生产流程优化
通过程序分析、操作分析和动作分析 ,优化生产流程,减少浪费和无效劳 动。
生产计划和调度
利用时间研究和工作抽样等方法收集 的数据,为生产计划和调度提供科学 依据。
2024/3/23
01
02
工作效率提升
现场改善的利器IE七大手法(推荐)
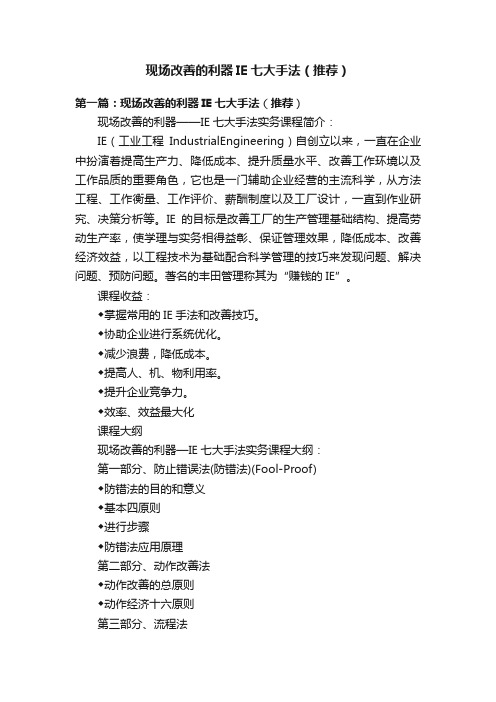
现场改善的利器IE七大手法(推荐)第一篇:现场改善的利器IE七大手法(推荐)现场改善的利器——IE七大手法实务课程简介:IE(工业工程IndustrialEngineering)自创立以来,一直在企业中扮演着提高生产力、降低成本、提升质量水平、改善工作环境以及工作品质的重要角色,它也是一门辅助企业经营的主流科学,从方法工程、工作衡量、工作评价、薪酬制度以及工厂设计,一直到作业研究、决策分析等。
IE的目标是改善工厂的生产管理基础结构、提高劳动生产率,使学理与实务相得益彰、保证管理效果,降低成本、改善经济效益,以工程技术为基础配合科学管理的技巧来发现问题、解决问题、预防问题。
著名的丰田管理称其为“赚钱的IE”。
课程收益:◆掌握常用的IE手法和改善技巧。
◆协助企业进行系统优化。
◆减少浪费,降低成本。
◆提高人、机、物利用率。
◆提升企业竞争力。
◆效率、效益最大化课程大纲现场改善的利器—IE七大手法实务课程大纲:第一部分、防止错误法(防错法)(Fool-Proof)◆防错法的目的和意义◆基本四原则◆进行步骤◆防错法应用原理第二部分、动作改善法◆动作改善的总原则◆动作经济十六原则第三部分、流程法◆目的和应用范围◆流程法的功用◆流程释义◆流程法范例第四部分、五五法◆五五法的目的和意义◆五五法与创意思考第五部分、人机分析法◆人机分析的目的与意义◆人机分析的应用范围与功用◆人机法名词释义◆人机分析图◆人机法案例分享第六部分、双手法◆双手法的目的与意义◆双手法的运用范围与功用◆双手法名词释义◆双手法应用范围介绍◆绘图注意事项◆双手法案例分享第七部分、工作抽样◆工作抽样的意义◆工作抽样之实验◆工作抽查之应用◆抽样及工作抽查之好处◆抽样的技巧◆工作抽查之要点◆不同的对象进行分类◆标准时间设定应用案例◆工作绩效衡量应用案例师资介绍专家简介:黄杰国内著名生产管理顾问、现场管理专家。
生产管理高级咨询师;多家国际国内知名培训咨询公司高级培训师、咨询顾问。
IE的七大手法
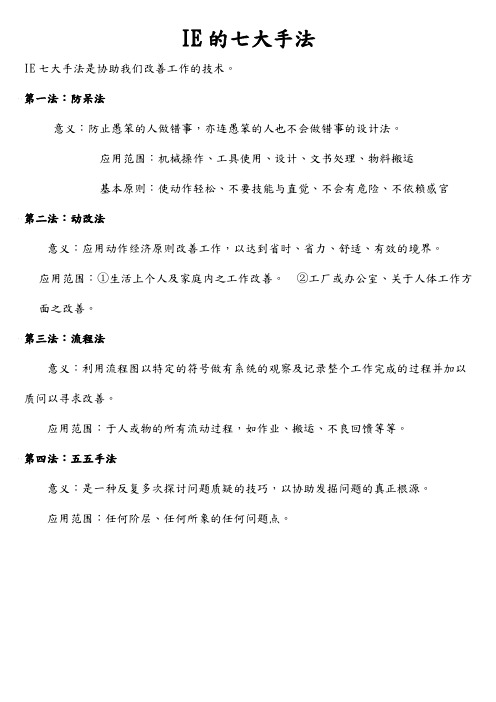
IE的七大手法IE七大手法是协助我们改善工作的技术。
第一法:防呆法意义:防止愚笨的人做错事,亦连愚笨的人也不会做错事的设计法。
应用范围:机械操作、工具使用、设计、文书处理、物料搬运基本原则:使动作轻松、不要技能与直觉、不会有危险、不依赖感官第二法:动改法意义:应用动作经济原则改善工作,以达到省时、省力、舒适、有效的境界。
应用范围:①生活上个人及家庭内之工作改善。
②工厂或办公室、关于人体工作方面之改善。
第三法:流程法意义:利用流程图以特定的符号做有系统的观察及记录整个工作完成的过程并加以质问以寻求改善。
应用范围:于人或物的所有流动过程,如作业、搬运、不良回馈等等。
第四法:五五手法意义:是一种反复多次探讨问题质疑的技巧,以协助发掘问题的真正根源。
应用范围:任何阶层、任何所象的任何问题点。
基本原则:主要是5W1H。
第五法:人机法意义:利用人机配合图来研究人员与工作机器、工治具的组合运用、改善机器与人的等待时间,提高团队的工作效率。
应用范围:所有操作机器、工治具的站位。
基本原则:发掘空间与等待时间、使工作平衡、减少周程时间、获得最大的机器利用率、合适的指派人员与机器第六法:双手法意义:利用双手操作分析图,研究双手在操作时“闲置”的状况,并寻求改善的方法以充分发挥双手的能力。
应用范围:高度重复性且以人为主的工作,研究对象为人体的双手。
基本原则:研究双手的动作,以求其相互平衡、显现出伸手找寻,以及笨拙而无效的动作、发现工具、物料、设备等不合适的位置、改善工作布置、协助操作技术的训练第七法:抽查法意义:利用抽样原理,以推测人或物之作业真象,以利进行分析改善。
应用范围:●办公室人员工作时间所占之百分率●机器设备之维修百分率或停机百分率●现场操作人员从事有生产性工作之百分率●决定标准工时之宽放时间百分率●用以决定工作之标准工时●商店顾客类别或消费者全额或光顾时刻次数等之分配比例之资料工作抽查好处:●观测时间短,并可同时观测数部机器或操作人员之状况●调查时间较长,可去除因每日不同之各别状况所造成之差异现象,其结果较为客观可靠●所被观测的对象所产生的干扰次数及时间较短我来教你!!!。
IE七大手法与精益生产

IE七大手法簡介<br><br> 什么是IE?<br> I 就是指 INDUSTRIAL工業<br> E就是指 ENGINEERING工程<br>IE的目的<br> 簡單地說“IE”就是代表“合理化”及“改善”的意議,為了顧及記憶的方便,我們就以中文“改善”來代表“IE”的含議.<br>為什么要有IE?<br> 以不教而戰,為之殺<br> 徒然要求改善而不講求方法、技巧,于事無補<br> 給人一條魚吃,不如教他捕魚的技朮<br> 要求捕更多的魚,首先必須講求捕魚技朮的傳授與使用<br> 改善七大手法(IE 7 TOOLS)就是協助我們改善工作的技朮.<br><br><br><br>(1)防錯法 <br> 如何避免做錯事情,使工作第一次就做好的精神能夠具体實現<br> (2)動改法 <br> 改善人体動作的方式,減少疲勞使工作更為舒適,更有效率,不要蠻幹.<br> (3)流程法 <br> 研究探討牽涉到几個不同工作或地點之流動關系,以發掘也可資改善的地方.<br> (4)五五法 <br> 藉著質問的技巧來發掘出改善的構想<br> (5)人機法 <br> 研究探討操作人員與机器工作的過程,藉以發掘出可資改善的地方.<br> (6)雙手法 <br> 研究人体雙手在工作進行的過程,藉以發掘出可資改善的地方.<br> (7)抽查法 <br> 藉著抽樣觀察的方法能很迅速有效地了解問題的真象 <br><br>那些工作需要改善 ?!<br>下面的幾個因素,可以做為找出那些工作需要改善的啟示.<br>成本金錢,工作時間以及机器使用上花費最多的工作<br>工作量工作量最多的工作<br>永續性需要持續很久的工作<br>人數有很多員工從事的工作<br>熟練度共大把要高孰練的人擔任的工作改由低熟度的<br>進度未能按預定的進行而需要加班的工作<br>工作品質未能達到所要求品質基准的工作<br>浪費勞力度或時間浪費較多的工作<br>危險性發生很多災害的工作,或者容易發生災害的工作<br>疲勞肉体上或者精神上很容易疲勞的工作<br>環境在灰塵,噪音,惡臭,氣溫等惡劣環境下的工作 <br>......<br><br>精益生产精益生产是多品种小批量条件下的最优生产方式,实施精益生产会给企业带来巨大的收益,因而被誉为第二次生产方式革命。
IE七大手法与口诀

IE七大手法与口诀精益与IEIE是工业工程的英文首字母缩写。
精益与IE相比,两者有共通点,也有不同点。
共通点:①都以效率提升为目标;②有共通的方法论,如防呆法、5个为什么分析;③IE早于精益诞生,精益在IE基础上发展起来。
不同点:①IE注重方法;精益则方法与文化并重。
②精益注重在改善的过程中培养人。
③方法的通用性上,IE稍胜一筹。
---张坚么是IE?IE是工业工程(Industrial Engineering)的英文简称,起源于科学管理之父泰勒的“方法研究”与“作业测定”,同时期,吉尔布雷斯夫妇对“作业动作”的细致研究,从而融合形成了工业工程这门学科。
美国工业工程师学会对IE的定义:工业工程是对人员、物料、设备、能源和信息组成的集成系统进行设计、改善和设置的一门学科。
泰勒著名的搬生铁试验、IE七大手法IE手法以人的活动为研究对象,强调尊重事实,运用科学的工具和方法对整个生产系统进行观察、记录、分析,寻找问题、发现问题并进行合理化改善,最后实现作业标准化。
IE七大手法的归纳用很多版本,其中最常用的IE七大手法为:防错法、动改法、流程法、五五法、人机法、双手法和抽查(样)法。
1.防错法也叫防呆法, 是一种有效防止人为错误的方法。
工作中的不良主要有两类,一类受限于当前科学技术的水准,如工艺、设备能力等造成的不良,还有一类不良是人为失误造成的不良,如人训练不足、紧张、疲劳等造成的不良。
据统计,人为失误造成的不良约占到80%。
前两天,我去一地方录制课程,结果忘记将翻页笔的USB接收器带回来。
这是一个人为失误吧。
于是,前台女孩用快递帮我寄了回来,我一看,怪了,只是一个空快递封,原来,女孩忘记将“USB接收器”放进快递封了。
白忙乎了一阵。
由此可见,工作生活中,人为失误是经常出现的一件事。
(张坚)2.动改法动改法的鼻祖是吉尔布雷斯夫妇,所谓动改法,即通过动作改善,减少疲劳,使人更高效地作业。
动作改善不仅可以提升效率,同时让员工有很好的获得感!3.流程法对检验、搬运、加工、仓储、滞留以符号方式,制作出流程图,从中发现浪费即不合理之处,从而进行相应的优化。
IE七大手法是指什么

IE七大手法是指什么
IE(工业工程)的七大手法也称为IE七大基本工具或IE七巧板,是工业工程领域中最常用的工具之一。
这七大手法是:
1. 工艺图。
将工艺流程中的每一道工序和操作以图形的形式展示出来,方便分析和优化。
2. 流程图。
展示工艺流程和生产流程的每一个步骤和环节,帮助分析和改进。
3. 查核表。
使用表格来帮助统计和分析每个环节或工序的数据和指标,方便改进。
4. 直线图。
用于显示一个或多个指标随时间变化的趋势和关系,方便对变化进行分析和预测。
5. 条形图。
将数据按照数量大小用条形来展示,方便比较和分析。
6. 散点图。
用于研究两个变量之间的关系,可以展示数据
之间的相关性。
7. 控制图。
用于监控和改进生产过程中的数据和指标,帮助保持过程的稳定性和在规定范围内控制变化。
精益生产主要围绕的板块

13. 增值活动是一个活动为达到客户需求或需要改变大小,形状 、方式、形式 或原料的功能或信息。
14. 非增值活动是那些花费时间或资源的活动,但却不能满足客户的需求或需要。 说明:其它基础概念将在后续精益基础部分详细介绍
10
作用: 培养员工的问题意识和改善意识。 改善员工的精神面貌,创建积极进取、文明健康的企业文化。 提升员工发现问题和解决问题的能力,提高技能水平。 改善员工的工作环境,促进员工满意。 改善生产制造条件,提高生产效率。 引导员工从细微处着眼消除各种浪费、损耗、降低成本,提高效率。
12
四、IE七大手法
1、防呆法 2、动改法 3、五五法 4、双手法 5、人机法 6、流程法 7、抽查法
总之:最小的投入(In Put)得到最大的产出(Out Put)
6
一、精益思想
精益管理应用于企业所有层面,从管理系统上能有效杜绝浪费,从文化上人人竭力追求持 续改善,并实现经营业绩卓越、持续竞争力强的企业。
1.核心:就是消除浪费,以越来越少的投入——较少的人力、较少的设备、较短的时间和 较小的场地创造出尽可能多的价值。 2. 精益五原则:根据客户需求,重新定义价值;识别价值流,重新制定企业活动;使价值 流动起来;依靠客户需求拉动价值流;持续改善,追求尽善尽美。
降低 成本
改善 品质
提高
效率
精益
精益生产
缩短 交期
JIT Lean Production
生产
自働化
FORWORD
前 言
精益生产起源于丰田生产方式,是以提高效率、改善品质、降低成本、 缩短交期为目的,以准时化(JIT)和自働化为支柱,围绕着改善活动展开 的生产管理系统。其核心是消除浪费,以最少资源投入创造出尽可能多的 价值。为让大家能更快速了解和掌握精益基础知识,并应用精益工具(如 识别八大浪费、提案改善、IE手法、线平衡等)开展改善活动,特编制精 益基础知识手册。手册从理论知识入手,结合推进实施步骤及典型案例剖 析,供各企业参考与借鉴!
精益生产-快速换线换模培训课件
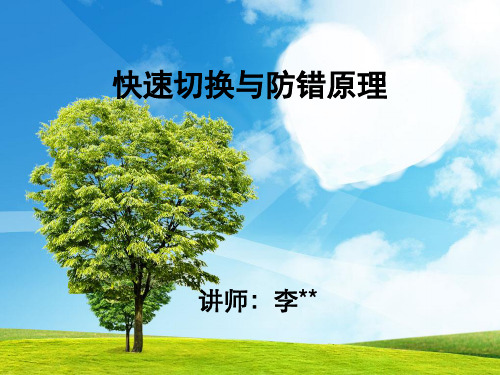
讲师:李**
课程内容:
一、IE七大手法名称简介 二、快速切换 三、防错十大原理
Page 2
一、IE七大手 法名称简介
Page 3
什么是IE?
I 就是指 INDUSTRIAL工业 E就是指 ENGINEERING工程 IE的目的 简单地说“IE”就是代表“合理化”及“改善”的意议, 为了顾及记忆的方便,我们就以中文“改善”来代表“IE” 的含议. 为什么要有IE? 以不教而战,为之杀 徒然要求改善而不讲求方法、技巧,于事无补 给人一条鱼吃,不如教他捕鱼的技朮 要求捕更多的鱼,首先必须讲求捕鱼技朮的传授与使用
A.发掘出问题的速度
B.改善动作本身:
对造成的损失有切肤之痛的感觉来促使 改善加速
Page 22
目视管理
一看即知现场有否异常,即使现场 管理透明化,没有隐藏问题的地方。 常用道具:
一)、红单 二)、标示板
Page 23
三)、画线区分 四)、红线表示 五)、生产管理板 六)、标准作业表单:管理现场机器设备的布置
Page 4
(1)防错法 如何避免做错事情,使工作第一次就做好的精神能够具体实现 (2)动改法 改善人体动作的方式,减少疲劳使工作更为舒适,更有效率,不要蛮干. (3)流程法 研究探讨牵涉到几个不同工作或地点之流动关系,以发掘也可资改
善的地方. (4)五五法 藉着质问的技巧来发掘出改善的构想 (5)人机法 研究探讨操作人员与机器工作的过程,借以发掘出可资改善的地方. (6)双手法 研究人体双手在工作进行的过程,借以发掘出可资改善的地方. (7)抽查法
平准化
Page 14
使各月份的生产负荷一致及产能平准化
(一)、快速切换的思想步骤
- 1、下载文档前请自行甄别文档内容的完整性,平台不提供额外的编辑、内容补充、找答案等附加服务。
- 2、"仅部分预览"的文档,不可在线预览部分如存在完整性等问题,可反馈申请退款(可完整预览的文档不适用该条件!)。
- 3、如文档侵犯您的权益,请联系客服反馈,我们会尽快为您处理(人工客服工作时间:9:00-18:30)。
IE七大手法一、IE人员主要从事的七个方向,它们是:1.研究与开发管理;2.生产系统设计与控制;3.效率工程;4.质量控制与质量保证;5.实施规划与物流分析;6.工业卫生与安全;7.人力资源管理。
二、基础IE里的东西:IE手法包括:方法研究(程序分析、动作分析),作业测定,布置研究,Line Balance等,但好象不够七个。
在现场IE里,IE七大手法包括:程序分析、动作分析,搬运分析,动作经济原则,作业测定,布置研究,Line Balance。
三、台湾公司教材里面的1、工程分析。
2、搬运工程分析。
3、运动分析(工作抽查work sampling)4、生产线平衡。
5、动作分析。
6、动作经济原则。
7、工厂布置的改善。
四、其它的各种说法1、IE七大手法为:作业分析、程序分析(运用ECRS技巧)、动作分析(动作经济原则)、时间分析、稼动分析、布置搬动分析、生产线平衡2、七大手法:流程分析法、动作分析法、动作经济原则、时间研究、工作抽查法、人机配置法、工作简化法3、七大手法:动作改善法(动改法)、防止错误法(防错法)、5*5W1H法(五五法)、双手操作法(双手法)、人机配合法(人机法)、流程程序法(流程法)、工作抽样法(抽样法)4、七大手法:程序分析、时间分析、动作分析、流水线分析、稼动分析、物料分析、环境分析。
知识和方法是从不停总结中出来,在实际的工作中,不断的运用各种知识,不断的发现,不断的分析以及不断的总结。
从客观性、定量性、通用性和实践可行性等各种原则制作出标准以供后来者学习和运用。
我发现国外并没有IE七大手法的说法(也许是我没有找到),那么IE七大手法必定是我们国人所造,我们需要IE 七大手法吗?当然需要,这也许是我们国内IE自己人走出IE基础的第一步。
虽然我们用的手法基本都是国外创造的手法,但是我们加以总结,对于我们工作学习来说,有一个准确的IE七大手法,我们更加容易掌握和使用。
加以总结,使得这些手法更加的适合我国的企业实际情况的运用,也是一件很有意义的事情。
但是IE七大手法没有定论,上面的IE七大手法基本是各自的运用而产生的,那么你所在的企业都用到了那些IE的方法总结出一个IE七大手法呢?IE七大手法没有定义,你是否可以给IE七大手法下个定义呢?如何给IE七大手法下定义呢?我想是否可以从以下几个方面考虑:1、IE七大手法所使用的范围(生产、质量、品质、服务等)2、IE七大手法的施用对象(5M1E)3、IE七大手法使用的主要途径4、IE七大手法的功能作用5、IE七大手法的目的、目标6、IE七大手法的原理浅谈精益生产要点-Lean Production在制造业中,我们很多人认为“精益”就是准时生产制JIT。
国外流行最广和最通俗的说法是:精益就是消除一切浪费。
也有人使用了如“同步制造S M”、“流动制造F M”等术语。
精益思想的目标是“用尽善尽美的过程为用户创造尽善尽美的价值。
”这些说法都是有道理的,并且都企图用最精益的语言来描述这个革命性的思想。
“精益思想是人、过程和技术的集成”则是更加全面和严肃的认识按照“过程、人和技术的集成”的观点,全面的认识精益思想,将帮助企业把握建立精益企业的要点,具有较好的可操作性。
对于传统生产企业或是大批量生产企业向精益生产方式精益企业转变,在制造方面主要有以下形式:1.改进生产流程精益生产利用传统的工业工程技术来消除浪费,着眼于整个生产流程,而不只是个别或几个工序。
(1)消除质量检测环节和返工现象。
如果产品质量从产品的设计方案开始,一直到整个产品从流水线上制造出来,其中每一个环节的质量都能做到百分百的保证,那么质量检测和返工的现象自然而然就成了多余之举。
因此,必须把“出错保护”的思想贯穿到整个生产过程,也就是说,从产品的设计开始,质量问题就已经考虑进去,保证每一种产品只能严格地按照正确的方式加工和安装,从而避免生产流程中可能发生的错误。
(2)消除零件不必要的移动。
生产布局不合理是造成零件往返搬动的根源。
在按工艺专业化形式组织的车间里,零件往往需要在几个车间中搬来搬去,使得生产线路长,生产周期长,并且占用很多在制品库存,导致生产成本很高。
通过改变这种不合理的布局,把生产产品所要求的设备按照加工顺序安排,并且做到尽可能的紧凑,这样有利于缩短运输路线,消除零件不必要的搬动,节约生产时间。
(3)消灭库存。
把库存当作解决生产和销售之急的做法犹如饮鸩止渴。
因为库存会掩盖许多生产中的问题,还会滋长工人的惰性,更糟糕的是要占用大量的资金。
在精益企业里,库存被认为是最大的浪费,必须消灭。
减少库存的有力措施是变“批量生产、排队供应”为单件生产流程(one-piece-flow)。
在单件生产流程中,基本上只有一个生产件在各道工序之间流动,整个生产过程随单件生产流程的进行而永远保持流动。
理想的情况是,在相邻工序之间没有在制品库存。
实现单件生产流程和保持生产过程的流动性还必须做到以下两点:同步------在不间断的连续生产流程里,必须平衡生产单元内每一道工序,要求完成每一项操作花费大致相同的时间。
平衡------合理安排工作计划和工作人员,避免一道工序的工作荷载一会儿过高,一会儿又过低。
但是,在某些情况下,还必须保留一定数量的在制品库存,而这个数量就取决于相邻两道工序的交接时间。
实施单件生产流程、同步和平衡这些措施,其目标是要使每项操作或一组操作与生产线的单件产品生产时间(Tact time)相匹配。
单件产品生产时间是满足用户需求所需的生产时间,也可以认为市场的节拍或韵律。
在严格的按照Tact time组织生产的情况下生产,成品的库存会降低到最低限度。
2.改进生产活动仅仅对生产流程予以持续的改善,还不足以实现精益化生产,还要进一步改善生产流程中的个别活动,以更好的配合改进过的生产流程。
在没有或很少库存的情况下,生产过程的可靠性至关重要。
要保证生产的连续性,必须通过减少生产准备时间,机器检修、待料的停工时间和减少废品的产生。
(l)减少生产准备时间。
减少生产准备时间一般的做法是,认真细致地做好开机前的一切准备活动,消除生产过程可能发生的各种隐患。
a、列举生产准备程序的每一项要素或步骤;b、辨别哪些因素是内在的(需要停机才能处理);哪些是外在的因素(在生产过程中就能处理)(推行SMED快速换线法)c、尽可能变内在因素为外在因素;d、利用工业工程方法来改进技术,精简所有影响生产准备的内在的、外在的因素,使效率提高。
(2)消除停机时间。
全面生产维修(TPM)是消除停机时间最有力的措施,包括例行维修、预测性维修、预防性维修和立即维修四种基本维修方式。
a、例行维修——操作工和维修工每天所作的维修活动,需要定期对机器进行保养。
b、预测性维修——利用测量手法分析技术预测潜在的故障,保证生产设备不会因机器故障而造成时间上的损失。
其意义在于未雨绸缪,防患于未然。
c、预防性维修——一为每一台机器编制档案,记录所有的维修计划和维修纪录。
对机器的每一个零部件都做好彻底、严格的保养,适时更换零部件,保证机器不发生意外故障。
d、立即维修——一当有故障发生时,维修人员要召之即来,随叫随到,及时处理。
由于在连续生产流程中,两道工序之间少有库存,若机器一旦发生故障,整个生产线就会瘫痪,因此消除停机时间对维持连续生产意义重大。
TPM的目标是零缺陷、无停机时间。
要达到此目标,必须致力于消除产生故障的根源,而不是仅仅处理好日常表现的症状。
(3)减少废品产生。
严密注视产生废品的各种现象(比如设备、工作人员、物料和操作方法等),找出根源,然后彻底解决。
此外,那些消除返工的措施也同样有利于减少废品的产生。
3.提高劳动利用率提高劳动利用率,有两个方面,一是提高直接劳动利用率,二是提高间接劳动利用率。
提高直接劳动利用率的关键在于一人负责多台机器或能适应多个岗位(一工多能)。
这就要求对操作工进行交叉培训,交叉培训的目的是使生产线上的操作工可以适应生产线上的任何工种。
交叉培训赋予了工人极大的灵活性,便于协调处理生产过程中的异常问题。
实现一人多机或一工多能的前提是建立工作标准化制度。
工作标准化是通过对大量工作方法和动作进行研究,以决定最有效和可以重复的方法。
工作时员工必须严格的按照标准化进行,其意义不仅在于直接劳动的利用率的提高,而且也提高了产品的质量,因为出错保护和防止废品产生等一系列技术措施的采用,确保了每一项操作只能按照惟一正确的方法进行。
在生产设备上安装自动检测的装置同样可以提高直接劳动利用率。
生产过程自始至终处在自动检测装置严密监视下,一旦检测到生产过程中有任何异常情况发生,便发出警报或自动停机。
这些自动检测的装置一定程度上取代了质量检测工人的活动,排除了产生质量问题的原因,返工现象也大大减少,劳动利用率自然提高。
间接劳动利用率随生产流程的改进和库存、检验、返工等现象的消除而提高,那些有利于提高直接劳动利用率的措施同样也能提高间接劳动率。
库存、检验、返工等环节所消耗的人力和物力并不能增加产品的价值,因而这些劳动通常被认为是间接劳动,若消除了产品价值链中不能增值的间接活动,那么由这些间接活动引发的间接成本便会显着降低,劳动利用率也相应得以提高。
总而言之,精益生产是一个永无止境的精益求精的过程,它致力于改进生产流程和流程中的每一道工序,尽最大可能消除价值链中一切不能增加价值的活动,提高劳动利用率,消灭浪费,按照顾客订单生产的同时也最大限度的降低库存。
精益是一种全新的企业文化,而不是最新的管理时尚。
由传统企业向精益企业的转变不能一蹴而就,需要付出一定的代价,并且有时候还可能出现意想不到的问题,让那些热衷于传统生产方式而对精益生产持怀疑态度的人,能举出这样或那样的理由来反驳。
但是,那些坚定不移走精益之路的企业,大多数在6个月内,有的甚至还不到3个月,就可以收回全部改造成本,并且享受精益生产带来的好处。
IE方法研究IE里“工作研究“是以生产工厂的整个制造系统为主要的活动对象,而工作研究的动作技巧主要是由”方法研究“及”作业测定“所构成。
“作业测定”又是由“时间研究”发展而来,与“方法研究”同时配合进行,或者可说是方法研究所确定的生产系统及工作方法,定量测定“多余的时间”要素及“无效的时间”要素等非生产部分,并进行削减,并作为以后管理计划及控制的依据。
针对以上对“方法研究”与“作业测定”的了解,也可说“方法研究”与“作业测定”是一体两面,具有互补性。
当在做“方法研究”时,虽然目的是要取得“最佳的方法”,而在取得后,就需把“时间”确定。
反过来说,当在做“时间”测定时,也要考虑测定的“时间”是否最佳的“方法”了。
(一)、方法研究的技巧如何进行“方法研究”,首先应从生产现场的工作系统来探讨。
生产对象(物)应经由作业过程、经由时间、空间的变化,做逐一的分析研究。