工厂管理中常见的八大浪费
工厂八大浪费
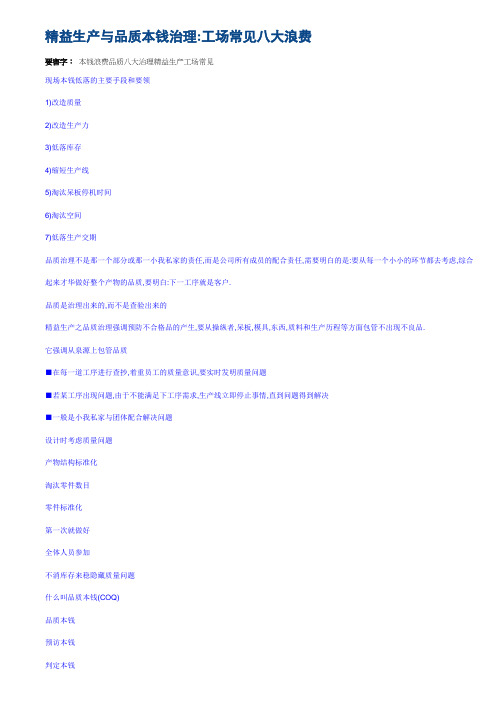
精益生产与品质本钱治理:工场常见八大浪费要害字:本钱浪费品质八大治理精益生产工场常见现场本钱低落的主要手段和要领1)改造质量2)改造生产力3)低落库存4)缩短生产线5)淘汰呆板停机时间6)淘汰空间7)低落生产交期品质治理不是那一个部分或那一小我私家的责任,而是公司所有成员的配合责任,需要明白的是:要从每一个小小的环节都去考虑,综合起来才华做好整个产物的品质,要明白:下一工序就是客户.品质是治理出来的,而不是查验出来的精益生产之品质治理强调预防不合格品的产生,要从操纵者,呆板,模具,东西,质料和生产历程等方面包管不出现不良品.它强调从泉源上包管品质■在每一道工序进行查抄,着重员工的质量意识,要实时发明质量问题■若某工序出现问题,由于不能满足下工序需求,生产线立即停止事情,直到问题得到解决■一般是小我私家与团体配合解决问题设计时考虑质量问题产物结构标准化淘汰零件数目零件标准化第一次就做好全体人员参加不消库存来稳隐藏质量问题什么叫品质本钱(COQ)品质本钱预访本钱判定本钱内部损失本钱外部损失本钱自检与互检在事情中通常被称做"双检",主要是实施自主治理.(1)对工序实施自检和互检A,教诲训导操纵者,贯注实施"双检"的重要性;B,不定时的在现场抽查,监督"双检"实施状况;C,有问题出现时强调"双检"是关联双方的责任.D,制定明确的责任制度,实施考核与奖罚一线主管应怎样配合公司做好品质a) 较强的反响能力与处理惩罚品质的能力;b) 明白下一工序就是客户;c) 按范例标准作业;d) 车间做好自主查验;e) 异常现象实时上报与通报;f) 设备,东西,检测仪器正确使用及维护保养;g) 物料管束与周围情况整理;h) 热爱事情,有高度责任心;现场品质改进与提升1) 生产车间采取种种指示灯,告白牌来显示生产历程正常与否,以提升品质快速反响能力2) 创建品质异常信息反馈机制3) 同品质,工程,采购等部分紧密相助4) 创建品质改进跨部分小组5) 利用PDCA 改进与提升品质现场品质改进---七大手法查抄表层别法因果图柏拉图控制图散布图6 sigma的东西统计历程控制(SPC)、质量成果展开(QFD)、失效模式及结果阐发(FMEA)、因果矩阵(Cause and effects matrix)、英国标准(British Standard)、流程能力阐发(Process capability analysis)、多元变量阐发(Multi-Vari studies)、可靠度阐发(Reliability Analysis)、实验设计(DOE)、丈量系统阐发(MSA)、代价链阐发(Value Chain Analysis)、KJ图(KJ Methodology)、流程图(Process map)、统计推论(inferential statistics)、叙述统计(Descriptive statistics)、鱼骨图、直方图、柏拉图、干系图、抽样查验、控制图、相关阐发、回归阐发、散布法、方差阐发Full factorial experiments、Modular Design、Tolerance Design、Concept Engineering、Stage/Gate Process、SIPOC(Supplier Input Process Output Customer)、JMP、VOC、Screening studies、Hypothesis testing浪费的界说在JIT生产方法中,浪费的寄义与社会上通常所说的浪费有所区别。
八大浪费是指什么

八大浪费是指什么八大浪费是生产过程中所造成的物料、设备、人力、场地和时间等的浪费。
分别是:不良、修理的浪费,过分加工的浪费,动作的浪费,搬运的浪费,库存的浪费,制造过多过早的浪费,等待的浪费和管理的浪费。
1、等待浪费。
由于生产原料供应中断、作业不平衡和生产计划安排不当等原因造成的无事可做的等待,被称为等待的浪费。
2、加工过剩浪费。
加工的浪费也叫过分加工的浪费,主要是指多余的加工和过分精确的加工或是需要多余的作业时间和辅助设备,这样增加了生产用电、气压、油等能源的浪费,另外还增加了管理的工时。
3、管理浪费。
管理浪费指的是问题发生以后,管理人员才采取相应的对策来进行补救而产生的额外浪费。
4、不良修正浪费。
不良修正浪费指的是由于工厂内出现不良品,需要进行处置的时间、人力、物力上的浪费,以及由此造成的相关损失。
5、动作浪费。
动作的浪费现象在很多企业的生产线中都存在,常见的动作浪费主要有以下几种:两手空闲、单手空闲、作业动作突然停止、作业动作过大、左右手交换、步行过多、转身的角度太大等等。
6、库存浪费。
按照过去的管理理念,人们认为库存虽然是不好的东西,但却是必要的。
JIT的观点认为,库存是没有必要的,甚至认为库存是万恶之源。
由于库存很多,将故障、不良品、缺勤、点点停、计划有误、调整时间过长、品质不一致、能力不平衡等问题全部掩盖住了。
7、搬运浪费。
搬运的浪费具体表现为放置、堆积、移动、整列等动作浪费,由此而带来物品移动所需空间的浪费、时间的浪费和人力工具的占用等不良后果。
8、制造过多浪费。
制造过多或过早,提前用掉了生产费用,不但没有好处,还隐藏了由于等待所带来的浪费,失去了持续改善的机会。
精益生产八大浪费
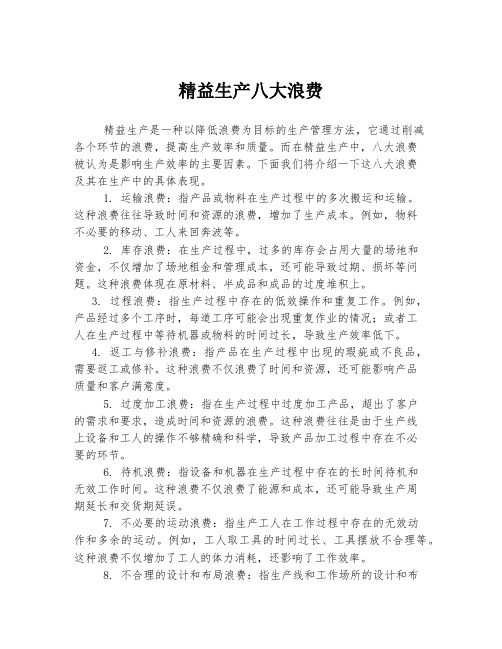
精益生产八大浪费精益生产是一种以降低浪费为目标的生产管理方法,它通过削减各个环节的浪费,提高生产效率和质量。
而在精益生产中,八大浪费被认为是影响生产效率的主要因素。
下面我们将介绍一下这八大浪费及其在生产中的具体表现。
1. 运输浪费:指产品或物料在生产过程中的多次搬运和运输。
这种浪费往往导致时间和资源的浪费,增加了生产成本。
例如,物料不必要的移动、工人来回奔波等。
2. 库存浪费:在生产过程中,过多的库存会占用大量的场地和资金,不仅增加了场地租金和管理成本,还可能导致过期、损坏等问题。
这种浪费体现在原材料、半成品和成品的过度堆积上。
3. 过程浪费:指生产过程中存在的低效操作和重复工作。
例如,产品经过多个工序时,每道工序可能会出现重复作业的情况;或者工人在生产过程中等待机器或物料的时间过长,导致生产效率低下。
4. 返工与修补浪费:指产品在生产过程中出现的瑕疵或不良品,需要返工或修补。
这种浪费不仅浪费了时间和资源,还可能影响产品质量和客户满意度。
5. 过度加工浪费:指在生产过程中过度加工产品,超出了客户的需求和要求,造成时间和资源的浪费。
这种浪费往往是由于生产线上设备和工人的操作不够精确和科学,导致产品加工过程中存在不必要的环节。
6. 待机浪费:指设备和机器在生产过程中存在的长时间待机和无效工作时间。
这种浪费不仅浪费了能源和成本,还可能导致生产周期延长和交货期延误。
7. 不必要的运动浪费:指生产工人在工作过程中存在的无效动作和多余的运动。
例如,工人取工具的时间过长、工具摆放不合理等。
这种浪费不仅增加了工人的体力消耗,还影响了工作效率。
8. 不合理的设计和布局浪费:指生产线和工作场所的设计和布局不合理,导致生产过程中存在的种种浪费。
例如,工作场所狭小、设备布局不合理、工人交通流线不畅等。
这种浪费不仅降低了工作效率,还增加了生产事故的风险。
精益生产的核心就是减少这八大浪费,提高生产效率和质量。
为了达到这个目标,企业可以采取很多措施。
工厂常见的八大浪费对应海报课件

3. 设备维护不当
设备的维护和保养不到位,容易出现 故障,影响物料流动的稳定性,进而 产生搬运浪费。
4. 库存管理不善
工厂库存管理不规范,导致物料积压 在仓库或生产线,增加了搬运的负担。
减少搬运浪费的对策
1. 优化工厂布局
根据物料流动的特点和需求,合理规划工 厂布局,减少物料在不同环节之间的传递 距离和时间。
06
八大浪费五:加工
浪费
加工浪费的定义
加工浪费是指在对产品或服务进行加 工的过程中,由于不合理的加工方式、 过多的加工步骤、或者重复加工等导 致的浪费。
加工浪费通常会导致增加生产成本、 降低生产效率,同时也会增加产品的 质量风险。
加工浪费的成因
不合理的工艺流程设计
如果工艺流程设计不合理,就会导致加工过程中的浪费。
生产效率下降:生产过程中的八大浪 费会导致生产效率低下,无法按时完 成生产任务。
成本增加:八大浪费会导致原材料、 能源、人力等资源的浪费,从而增加 生产成本。
产品质量下降:八大浪费会导致产品 不良率上升,从而影响产品质量和客 户满意度。
企业竞争力下降:八大浪费会导致企 业在市场上失去竞争优势,难以与竞 争对手抗衡。
过度的加工精度
过度的加工精度可能会导致产品性能过剩,同时也增加了制造成本。
缺乏有效的生产计划和调度
如果生产计划和调度不够准确,就会导致生产过程中的瓶颈和浪费。
减少加工浪费的对策
1 2 3
优化工艺流程设计 通过优化工艺流程设计,减少加工步骤和重复性 工作,提高生产效率。
合理安排生产计划和调度 通过准确预测市场需求,合理安排生产计划和调 度,确保生产线的平衡和连续性。
沟通障碍等。
八大浪费的普遍性
精益生产管理八大浪费与解决方法
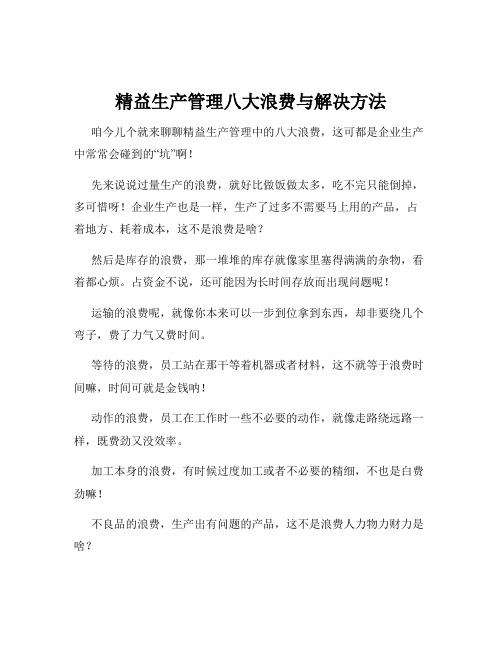
精益生产管理八大浪费与解决方法咱今儿个就来聊聊精益生产管理中的八大浪费,这可都是企业生产中常常会碰到的“坑”啊!先来说说过量生产的浪费,就好比做饭做太多,吃不完只能倒掉,多可惜呀!企业生产也是一样,生产了过多不需要马上用的产品,占着地方、耗着成本,这不是浪费是啥?然后是库存的浪费,那一堆堆的库存就像家里塞得满满的杂物,看着都心烦。
占资金不说,还可能因为长时间存放而出现问题呢!运输的浪费呢,就像你本来可以一步到位拿到东西,却非要绕几个弯子,费了力气又费时间。
等待的浪费,员工站在那干等着机器或者材料,这不就等于浪费时间嘛,时间可就是金钱呐!动作的浪费,员工在工作时一些不必要的动作,就像走路绕远路一样,既费劲又没效率。
加工本身的浪费,有时候过度加工或者不必要的精细,不也是白费劲嘛!不良品的浪费,生产出有问题的产品,这不是浪费人力物力财力是啥?最后是管理的浪费,管理人员要是没把事儿管好,那下面的人不就跟着乱套啦?那怎么解决这些浪费呢?咱得有针对性的办法呀!对于过量生产,得做好计划,按需生产,别一股脑儿地瞎搞。
库存呢,要合理控制,别堆得跟小山似的。
运输方面,优化流程,让东西能顺顺溜溜地到达该去的地方。
等待的问题,就得让各个环节衔接好,别出现空当。
动作方面,好好设计工作流程,去掉那些多余的动作。
加工嘛,得把握好度,别做无用功。
不良品的话,加强质量管控呀,从源头抓起。
管理就更不用说了,管理人员得负起责来,把团队带好。
你想想看,如果这些浪费都能解决,企业得省多少钱,提高多少效率呀!就像一个人把身上的包袱都甩掉了,那能跑得不快嘛!所以啊,精益生产管理八大浪费可不能小瞧,解决方法得认真对待。
这不仅关乎企业的效益,也关乎每个员工的利益呢!咱可不能眼睁睁看着浪费在那却不管不顾呀,得行动起来,让企业发展得更好,大家的日子也能过得更红火,不是吗?大家都努努力,把这些问题都解决掉,让企业轻装上阵,向着更好的未来前进!难道不是应该这样做吗?。
生产管理之8大浪费

■未注意部属的眼力与健康,造成不良品
■缺乏纪律,纵容粗心或不当的工作
■容许部属用不适当的材料(太好或太 差)
12
■未能追踪不良工作起何人,以致不能纠正 ■不能适才适用,特别是新人
■领料太多,多余料未退料
■领错材料,用错材料
■未能检查水、气、油等管路裂开破损, 导致遗漏
■未检查材料是否排列整齐,正确放置
生产管理中的8种浪费
1
1、时间的浪费
2
■缺乏适当的计划,使人员在换规格时产生
等待或者停工 ■班长未能彻底了解接受之命令与指示
■缺乏对全天工作内容的认识
■对班长的命令或指示不清楚 ■未能确实督导工具、材料、模具等应放
置于一定场所
■不应加班的工作,造成加班 3
■未检视每一工作是否供给合适的工具和资 源
■未研究部属个人的不同,以发挥他最大 的潜力
25
■评价一个人只重资格、种族、宗教、关 系、地域
■明知部属的的心理或者生理不适当,却 未加以调动
■生病的部属仍让他工作
■当可能且适当的时间,未能给予升迁
■未考虑影响薪资与工作条件的问题
■未训练一个后补者
26
4、欠缺对员工日常管理之数据
27
5、欠缺人员效率管理之数据
■未促使其他部属对新人表示关心、帮
助、友善的态度
23
■未尽可能的接近新人 ■没有告知新人,工厂生活情况与规划,
如安全,发薪日期,厕所位置,饮用 水,浴室等 ■未安排完整的训练计划
24
3、未使部属尽其所能
■未指导部属如何做好工作 ■未尽可能的说明工作,使其发生兴趣 ■未对部属的进步与个人生活表示关心 ■没有容纳部属错误的雅量 ■纵容部属派系存在或抱团
工厂八大浪费概述
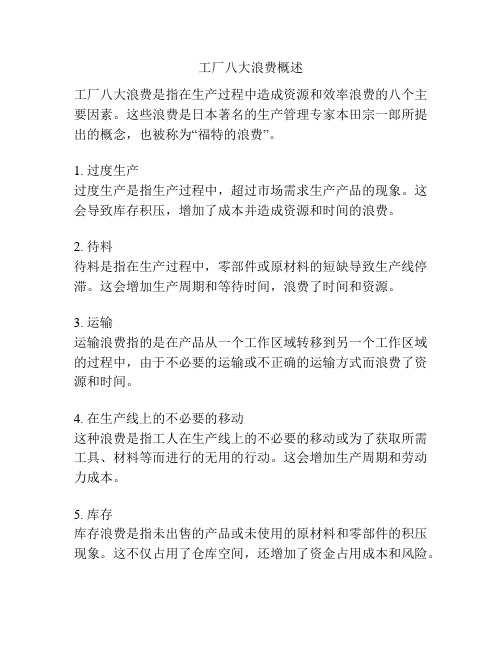
工厂八大浪费概述工厂八大浪费是指在生产过程中造成资源和效率浪费的八个主要因素。
这些浪费是日本著名的生产管理专家本田宗一郎所提出的概念,也被称为“福特的浪费”。
1. 过度生产过度生产是指生产过程中,超过市场需求生产产品的现象。
这会导致库存积压,增加了成本并造成资源和时间的浪费。
2. 待料待料是指在生产过程中,零部件或原材料的短缺导致生产线停滞。
这会增加生产周期和等待时间,浪费了时间和资源。
3. 运输运输浪费指的是在产品从一个工作区域转移到另一个工作区域的过程中,由于不必要的运输或不正确的运输方式而浪费了资源和时间。
4. 在生产线上的不必要的移动这种浪费是指工人在生产线上的不必要的移动或为了获取所需工具、材料等而进行的无用的行动。
这会增加生产周期和劳动力成本。
5. 库存库存浪费是指未出售的产品或未使用的原材料和零部件的积压现象。
这不仅占用了仓库空间,还增加了资金占用成本和风险。
6. 处理缺陷品处理缺陷品是指在生产过程中发现产品缺陷或不合格品时,需要进行修复、再加工或报废。
这会浪费时间、劳动力和材料。
7. 不必要的运动不必要的运动是指工人在生产过程中进行不必要的动作或操作,这会造成精力和时间的浪费。
8. 等待等待是指在生产过程中由于前一工序的延迟而导致的等待现象。
这会导致生产周期延长,并浪费了时间和资源。
针对这些浪费,工厂和企业可以采取一系列的措施来减少浪费,提高生产效率:1. 实施精细化生产计划,根据市场需求合理安排生产和减少过度生产所带来的浪费。
2. 加强供应链管理,确保及时供应所需的原材料和零部件,避免待料的情况发生。
3. 优化物流运输过程,合理规划运输路线,减少不必要的运输和运输过程中造成的浪费。
4. 对生产线进行布局优化,设计人性化工作站,减少工人不必要的移动。
5. 建立合理的库存管理制度,精确预测市场需求,避免库存积压。
6. 强化质量控制,提高产品质量,减少缺陷品的产生和处理。
7. 优化工作流程,减少不必要的运动和操作。
精益化管理(八大浪费)

4. 让闲置的“动”起来
5.应付现象最常见
6. 拒绝“低效”反复发生
7. 管理必须真正有“理”可依
2024/8/5
41
八﹑管理浪费
(三) 浪费的产生: 管理能力: 政策规定的执行力 技朮层次: 认知高度;把握度; 标准化: 可行度;推广度; 企业素质: 整体素质
2024/8/5
42
八﹑管理浪费
(四) 浪费的消除:
2024/8/5
13
不良浪费案例- -对策&效果
改善对策:
增加EPE泡棉隔板﹐ 避免产品与真空盘相碰
改善效果:
碰挂伤不良率为0%, 取消两名重工人员
2024/8/5
14
二. 制造过多(过早)的浪费
(一)定义:是由制程设定过长﹑生产计划未平准化 ﹑工作负荷不平衡﹑超常规设计﹑多余检验等造 成的制造过多于下一道工序需求的浪费
我可以请求你们,每天至少做一小时
有价值的工作吗?
--大野耐一
2024/8/5
51
课程实践计划
序号 1
实践项目
具体内容5W2H
备注
识别并消 除浪费
发现八大浪费各1个以上,并 用照片、视频、数据等形式展
现;
至少提出2个浪费的解决方法
一周内完 成
2024/8/5
52
ቤተ መጻሕፍቲ ባይዱ
作业:识别生产中的八种浪费
序号 看到什么 浪费类型
双手同时进行动作
缩短动作的距离
轻松动作
2024/8/5
37
动作浪费案例-现状描述
车间抛磨工序:作业员把修整好的产品直接放置在地 面,造成重复盛装、点数,影响产品质量
重 复 动 作 浪 费 时 间
精选生产过程中的八大浪费
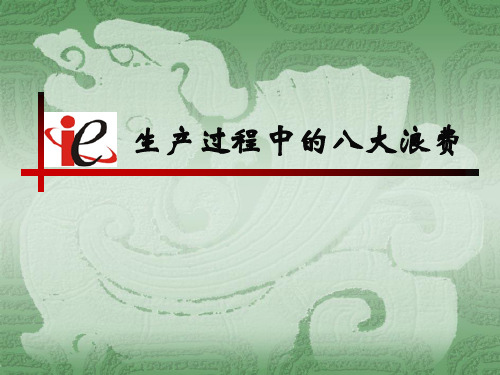
等待的浪费主要有: 1、生产线的机种、产品的切换 2、每天的工作量变动很大,当工作量少时,
便无所事事 3、 时常因缺料而使机器闲置
我等、我等、 我等等
工厂中的八大浪费
四、等待的浪费
等待的浪费主要有: 4、 因过程上游发生延误、导致下游无事可做
5、 因早会、开会而占用太多的时间 6、 机器设备时常发生故障
拿住螺丝刀。 对准螺丝。 上螺丝,固定零件。 放下螺丝刀。
これいらないん じゃないの?
本当に必要な 原価
必ずしも 必要でない 原価
有附加价值的作业 附加价值少的作业
作业
要求:
参加培训人员到自己管理区域(或制造现场)发 现最少一个浪费项目,且提出改善建义!
提交时间 : 08.3.15 提交方式 : 邮件(高巧叶)
重要性可以使他更负责任!或受到激励。
六、how to do 有时候,如果是新工作或是新下属,他可能还不知道该怎么
干,您还要告诉他。对程序和方法有些交代
七、how much 做多少?做到什么程度为好?有时您也要告诉下级,做少了不
得于工作的完成,做多了以浪费。例如:您让下属给你写一篇 稿子,没有告诉他写多少,他可能无从下笔,或必须现向您请 示,或随便写一篇这样以来要么效率低,一件简单的事情也要 多次反复才完成。既然下属知道了具体如何做,该做到何种程 度,那么事情办起来效率就要高得多了。
工厂中的八大浪费
制造过多(早)的浪费带来以下现象:
4、产生搬运、堆积的浪费,并使得先入先出 的物流作业变得困难。
5、增加中转车、中转货架的需要 6、库存量变大,管理工时增加
7、利率负担增加
工厂中的八大浪费
二、库存的浪费
工厂车间的8大浪费案例
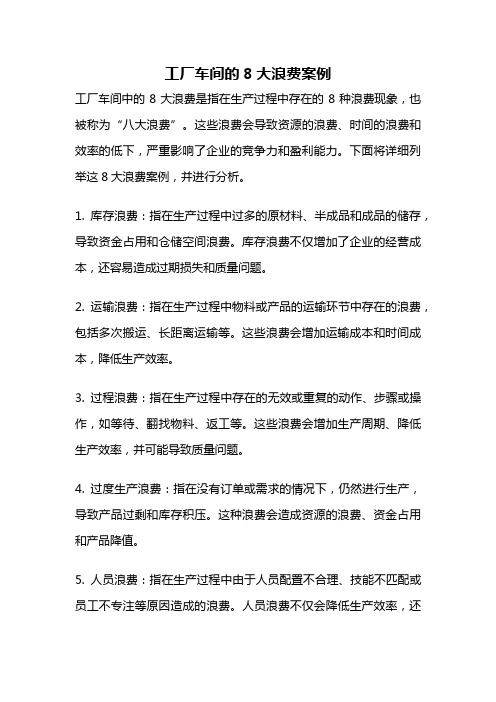
工厂车间的8大浪费案例工厂车间中的8大浪费是指在生产过程中存在的8种浪费现象,也被称为“八大浪费”。
这些浪费会导致资源的浪费、时间的浪费和效率的低下,严重影响了企业的竞争力和盈利能力。
下面将详细列举这8大浪费案例,并进行分析。
1. 库存浪费:指在生产过程中过多的原材料、半成品和成品的储存,导致资金占用和仓储空间浪费。
库存浪费不仅增加了企业的经营成本,还容易造成过期损失和质量问题。
2. 运输浪费:指在生产过程中物料或产品的运输环节中存在的浪费,包括多次搬运、长距离运输等。
这些浪费会增加运输成本和时间成本,降低生产效率。
3. 过程浪费:指在生产过程中存在的无效或重复的动作、步骤或操作,如等待、翻找物料、返工等。
这些浪费会增加生产周期、降低生产效率,并可能导致质量问题。
4. 过度生产浪费:指在没有订单或需求的情况下,仍然进行生产,导致产品过剩和库存积压。
这种浪费会造成资源的浪费、资金占用和产品降值。
5. 人员浪费:指在生产过程中由于人员配置不合理、技能不匹配或员工不专注等原因造成的浪费。
人员浪费不仅会降低生产效率,还会增加生产中的错误和事故风险。
6. 过度加工浪费:指在生产过程中对产品进行了超出需求或规范的加工处理,造成资源和时间的浪费。
过度加工浪费会增加生产成本,降低利润率。
7. 应急浪费:指由于生产过程中的故障、停机或突发事件而导致的浪费。
应急浪费会增加生产时间和成本,并可能影响产品质量和客户满意度。
8. 无价值创造浪费:指生产过程中存在的无效的、对产品无价值的活动或环节。
这些浪费不仅会消耗资源和时间,还会降低生产效率和产品质量。
针对以上8大浪费案例,工厂车间可以采取以下措施来减少或消除浪费,提高生产效率和质量:1. 实施精益生产:通过精细化管理、优化生产流程和精简不必要的环节,减少浪费现象。
2. 库存管理优化:采取合理的库存管理策略,避免库存过多或过少,降低资金占用和仓储成本。
3. 运输优化:优化物料和产品的运输方式和路径,减少搬运次数和距离,提高运输效率。
生产现场管理八大浪费

生产现场管理八大浪费生产现场管理八大浪费1、时间的浪费1)缺乏适当的计划,使人员在换规格时产生等待,或停工待料。
2)班组长未能彻底了解其所接受之命令与指示。
3)缺乏对全天工作内容的认识。
4)对班组长的命令或指示不清楚。
5)未能确实督导工具、材料、小装置等应放置于一定之处所。
6)不应加班的工作,造成加班。
7)未要求员工准时开始工作,松于监督。
8)拖延决策。
9)班组长本身不必要的请假与迟到或不守时。
10)迟交报告。
11)未检查每一工作是否供给合适的工具与装配。
12)放任员工故意逃避他们能作的工作。
13)需要的人员不足。
14 )保有太多冗员。
15)拙于填写报告及各种申请表格。
16)纵容员工养成聊天、擅离工作岗位、浪费时间之坏习惯。
17)疏于查问与改正员工临时旷职及请假的原因。
2、创意的浪费1)未能倾听员工的建议。
2)未能鼓励员工多提建议。
3)未充分向其它部门(如生技等)请教。
4)未考虑或指定适当人员处理所有有用的提案。
5)未能从会议中获取有益的意见。
6)在各种问题上不能广听部属的意见。
7) 不能广泛的研讯本身工作与业务之有关方法。
8)未询问新进人员过去之工作经验,以获取有益的意见。
3、材料与供应品的浪费?1)督导不良,造成材料的浪费。
a.对新人指导不够。
b.指派新工作时未充分指导。
c.蓝图或草图破损、难懂、看错、标准未及时更正、或自作主张。
d.机械故障或未调整好。
e.未对每一工序检查材料使用情形,(标准与差异分析)。
2)未让部属了解材料或供应品的价值。
3) 命令与指示不清。
4)纵容不良的物料搬运。
5)未注意部属的眼力与健康,造成不良品。
6)缺乏纪律,纵容粗心或不当的工作。
7) 容许部属用不适当的材料,如太好或太差。
8)未能追踪不良工作起自何人,以致不能纠正。
9)不能适才适用,特别是新人。
10)请领太多材料,多余却未办退料。
11)未请领正确的材料,用错材料。
12)未检查材料是否排列整齐,正确放置。
13)未能检查蒸气、水、气体、电和压缩空气等管路电线之裂开破损。
工厂生产的八大浪费

工厂生产的八大浪费1. 等待的浪費包括等待原材料,等待仓库发料,等待机器维修,等待前工序送料,等待确认样品,等待图纸资料,等待检验标准,等待生产计划下达……,都是时间的浪费,也就是生产力的巨大浪费。
解决方案:等待原材料:供应商考核及处罚;采购及物控的绩效考核等待仓库发料:仓库仓管员的绩效考核;建立至少提前一天备/发料的制度等待机器维修:每周/每月对设备部门“机器及设备完好率”的考核;每日/每周/每月对设备部/生产部“每日生产异常时间”及“异常时间占比(每日异常时间除以每日工作总时间得到的百分比)的统计/汇总/绩效考核等待前工序送料:每日被延迟工序统计时间,由责任工序补偿。
生产部门制定此详细规范。
等待确认样品,等待图纸资料,等待检验标准:对责任部门—工程部/研发部的绩效考核;明确生产计划员有协助生产部门追踪以上项目的责任等待生产计划下达:明确将准时下达发布生产计划作为计划物控部以及生产计划员的一项绩效考核指标(可以参看作者之前文章《生产计划员绩效考核浅谈》)2. 不合理庫存的浪費库存原材料分析:库存原材料,一般责任部门/责任人为计划物控部/物控员,还有采购部/采购员。
或者不合理备库,备库量过大;或者申购/采购错误导致库存。
解决:对物控及采购的绩效考核设定,设定总库存值及呆滞库存占比;明确公司安全库存物料种类/规格及相应库存设定;明确物控员的备库权限及审批流程;明确采购为执行物控员物料需求计划及申购单的岗位,无备库职能及权限成品及半成品库存:分析:一般为业务部门根据预测或者与客户的交流协商而备库,计划部门可以根据公司授权在一定限额内备库。
其他任何部门无备库权限。
解决:计划物控部门每月整理业务部门的备库记录,包括入库日期,距今仓储时间,催促其要客户下单发货。
谨慎备库:业务部门的成品及半成品备库,流程上需要先计划物控部门出具审批意见,总经理批准后才允许备库。
对超过承诺消化期限而一直未消化/发货的,报公司。
工厂中常见的八大浪费

八. 员工创造力的浪费
指未被使用的员工创造力:
由于未使员工参与、投入或未能倾听员工意见而造 成未能善用员工的时间、构想、技能,使员工失 去改善与学习机会。
中国汽车技术研究中心 上海卡达克汽车技术中心
中国汽车技术研究中心 上海卡达克汽车技术中心
七. 等待的浪费
因断料、作业不平衡、计划不当等造成无事可做的 等待,也称之为停滞的浪费。 造成等待浪费的因素包括:
• • • • • • • 上游工序发生延误; 机器设备时常发生故障; 工作计划不平衡; 换型时间长; 缺料; 材料虽已备齐,但图纸或派工单未到; 有劳逸不均的现象。
• 产生不必要的搬运、堆积、放置、防护、寻找等 浪费的动作; • 使先进先出作业困难; • 占用资金(损失利息)及额外的管理费用; • 物品的价值衰减,变成呆料、废料; • 占用空间,影响通过,且造成多余的仓库建设投 资的浪费; • 掩盖问题、能力不足被隐藏。
中国汽车技术研究中心 上海卡达克汽车技术中心
中国汽车技术研究中心 上海卡达克汽车技术中心
四. 搬运的浪费
所有的搬运(运输)都是浪费,这包括铲车、 流水线、卡车等的使用。
不合理的工程布局、不合理的单元设计、使用批量 生产、交货周期长、储存区域过大或计划问题可 能是造成浪费的根源。
中国汽车技术研究中心 上海卡达克汽车技术中心
五. 库存的浪费
库存导致:
六. 过度生产的浪费
过度生产的浪费是指在生产某一时间点生产过多, 其特点有:
• 生产多于下一工序或顾客的需求; • 生产早于下一工序或顾客的需求; • 生产快于下一工序或顾客的需求;
导致:
• • • • • • 顾客的工厂需额外场地; 生产工厂需额外场地; 使用更多材料; 额外的设备; 顾客及工厂额外的运输; 额外的计划成本。
工厂常见的八大浪费

协调不力企业丧失凝聚力
2009-6-23 16
闲置 让闲置的"动"起来
浪费
机构重叠,职能重叠┅┅形成人浮於 事,使生产经营要素不能得到有效利 用,造成了闲置的浪费.
扁平化管理、业务
流程再造、组织再造、 库存的危害:
过程管理等方法,都是 工作流程化、规范化、 职责化的有效措施,可 以从某种程度上减少
低效率产生的原因:1、管理者的低素质 ;2、方法 不当 ;3、固步自封的僵化思想.
我们允许的是创造性的失误,而不允许反
复发生低级的错误.
2009-6-23 19
不合理 浪 费 管理必须真正有"理"可依
管理中的不合理现象:
☆ 目标指标不合理 ☆ 计划编制无依据 ☆ 计划执行不严肃 ☆ 计划检查不认真 ☆ 计划考核不到位 ☆ 投入产出不匹配
☆ 固定资产的闲置 ☆ 职能的闲置或重叠 ☆ 工作程序复杂化形成的重叠
闲置的浪费.但是,更重 ☆ 物料人员的闲置
要的是思想不能闲置, ☆ 造成资讯的闲置
流水不腐.
2009-6-23 17
应付
浪费
应付现象最常见
应付就是工作虽然干了,但是不主 动、不认真,敷衍了事,不追求最好的 结果,从而缺乏实际效果,是责任心不 强的一种表现形式,这种浪费在工作 中是经常见到的.
14
无序浪 费
没有规矩,不成方圆
常见的无序现象: ☆ 职责不清造成的无序 ☆ 业务能力低下造成的无序
☆ 有章不循造成的无序 ☆ 业务流程的无序
缺乏明确的规章、制度、 流程,工作中容易产生混乱, 这是众所周知的.但如果有 令不行、有章不循,按个人 意愿行事造成的无序浪费, 更是非常糟糕的事.
企业八大浪费清单
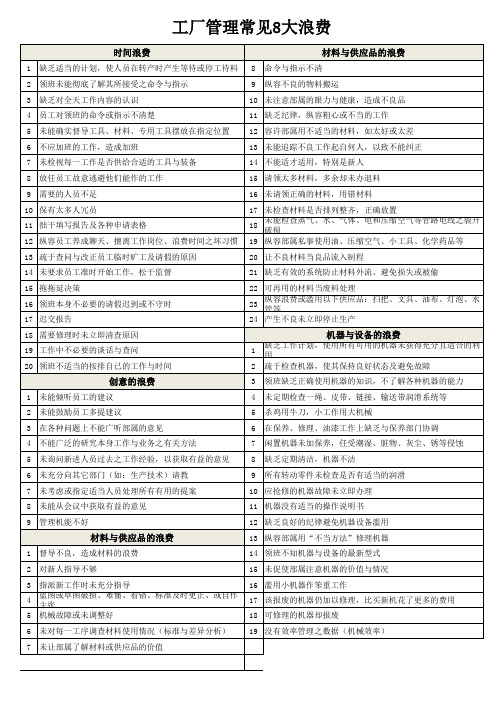
空间的浪费整理整顿
1 2 3 4 5 6 7 8 9 材料不适当排放与储存,或废料未报废, 橱柜、油筒、材料供应处等放置于不便之处 未充分注意材料在工厂中的途程计划 机械与其它永久性设备之错误安置 纵容部属丢置工具、梯子、手推车等在过道上,不能保持 走道清洁者 纵容不用的机器与设备占据重要的空间 由于未及时修理楼板、屋顶等以致需要的空间未加利用 照明不足,形成黑点,死角
工厂管理常见8大浪费
时间浪费
1 缺乏适当的计划,使人员在转产时产生等待或停工待料 2 领班未能彻底了解其所接受之命令与指示 3 缺乏对全天工作内容的认识 4 员工对领班的命令或指示不清楚 5 未能确实督导工具、材料、专用工具摆放在指定位置 6 不应加班的工作,造成加班 7 未检视每一工作是否供给合适的工具与装备 8 放任员工故意逃避他们能作的工作 9 需要的人员不足 10 保有太多人冗员 11 拙干填写报告及各种申请表格 12 纵容员工养成聊天、擅离工作岗位、浪费时间之坏习惯 13 疏于查问与改正员工临时旷工及请假的原因 14 未要求员工准时开始工作,松干监督 15 拖拖延决策 16 领班本身不必要的请假迟到或不守时 17 迟交报告 18 需要修理时未立即清查原因 19 工作中不必要的谈话与查问 20 领班不适当的按排自已的工作与时间 1 2 3浪费
1 未能倾听员工的建议 2 未能鼓励员工多提建议 3 在各种问题上不能广听部属的意见 4 不能广泛的研究本身工作与业务之有关方法 5 未询问新进人员过去之工作经验,以获取有益的意见 6 未充分向其它部门(如:生产技术)请教 7 未考虑或指定适当人员处理所有有用的提案 8 未能从会议中获取有益的意见 9 管理机能不好
机器与设备的浪费
缺乏工作计划,使用所有可用的机器未获得充分且适合的利用
工厂常见的八大浪费及解决办法

制程分割 路线迂回、曲折 混杂、孤岛
设 备 集 群
工 艺 布 局
单 元 生 产
一 个 流
产品品种、数量
车间布局
搬运的浪费
四条原则 机 械 化 自 动 化 标 准 化 均 衡 化 直 线 化
作业布局
人 机 工 程
八大浪费之五 -动作的浪费(世界上最大的浪费 ) 弯腰动作 操作不经济
动 作 浪 费 的 表 现
企业
公司利润的最大恶源 --浪费
制造过多(过早)的浪费
工 厂 常 见 的
库存的浪费 不良的浪费
浪 费
搬运的浪费
动作的浪费
加工过的浪费
等待的浪费 事后管理的浪费
八大浪费之四 -搬运的浪费
库 存 及 盘 库
人 力 损 失
工 具 及 空 间
效 率 低
物 流 拉 长
损 坏 碰 伤 空闲 动作突然停止 作业动作过多 左右手交换 步行过多 转身过多 重复、不必要 设计不合理
动 作 浪 费 的 原 因
八大浪费之五 -动作的浪费(世界上最大的浪费 ) 操作不经济 动作不精简 动作过多
动 作 浪 费 的 原 因
同时的未同时完成
不必要的被增加 设计不合理 同规格的不同规格
未考虑调整、转换等
同规格的不同规格 翻找物料
动作浪费的改善方法
针对不同动作制 定不同的方法
动作浪费
针对设计不合理产 生的浪费进行改善
动作经济原则
双手并用 对称反向
降低动作等级 减少动作限制
人体动作
排除合并 节奏轻松
手脚并用
避免动作突变 利用惯性
适当姿势
动作经济原则
利用工具 工具万能化 易于操作 工具设计
生产管理的八大浪费

生产管理的八大浪费
八大浪费是生产过程中所造成的物料、设备、人力、场地和时间等的浪费。
分别是:不良、修理的浪费,过分加工的浪费,动作的浪费,搬运的浪费,库存的浪费,制造过多过早的浪费,等待的浪费和管理的浪费。
如何减少或消除八大浪费:
1、做好自动化,防呆化的生产方式,以达到无停滞的流程作业。
2、对作业内容要进行重新的评估,对生产工具进行改善,减少加工不必要的浪费
3、改善现场管理,减少路线的浪费,改良工人动作的浪费,减少工人在生产过程中一切和工作无关的动作,以达到最省力情况下完成工作,减少不必要的动作浪费。
4、优化流程、减少搬运的浪费(最重要的是减少搬运的次数)。
5、优化库存布局、实施看板管理、提高库存周转率。
6、结合销售,合理安排生产计划、调整生产计划,以达到最小合理库存。
7、加强对原材料的管理,做到有计划。
8、对工厂各部门进行协调管理,使各部门紧密结合在一起,注重于工厂各部门的合作,以达到对工厂资源的最合理的利用。
精益生产应杜绝的8大浪费

格力电器精益生产推进小组精益生产应杜绝的八大浪费
1、生产过剩:指生产出尚未有订单的产品,造成人员过多和过多存货,从而导致储存与输送等成本的浪费:
2、在现场等候的时间:包括员工在一旁监看自动化机器,或因为各种原因造成的停工。
3、不必要的运输:如长距离搬运在制品及在流程之间搬运原材料、零部件或最终成品。
4、过度处理或不正确的处理:采取不必要的步骤以处理零部件,提供超出必要的较高品质产品所造成的浪费。
5、存货过剩:过多原料、在制品或最终成品,导致较长的前置期、陈旧过时品、毁损品、运输与存储成本及延迟。
6、不必要的移动搬运:员工在工作的过程中,任何浪费、不必要的动作,例如寻找、往前拿取,或是堆放零部件、工具等。
此外,走动也是浪费。
7、瑕疵:生产出瑕疵或必须返工的东西。
8、未使用的员工创造力:未使员工充分参与生产改进,未能善用员工时间、构想、技能使员工失去改善与学习的机会。
精益生产应杜绝的八大浪费”在我们的生产现场中也随处可见,亲爱的各位有注意到吗?如果从前没有,那从今天起我们就发现它们,消灭它们!。
精益生产和工厂常见的八大浪费
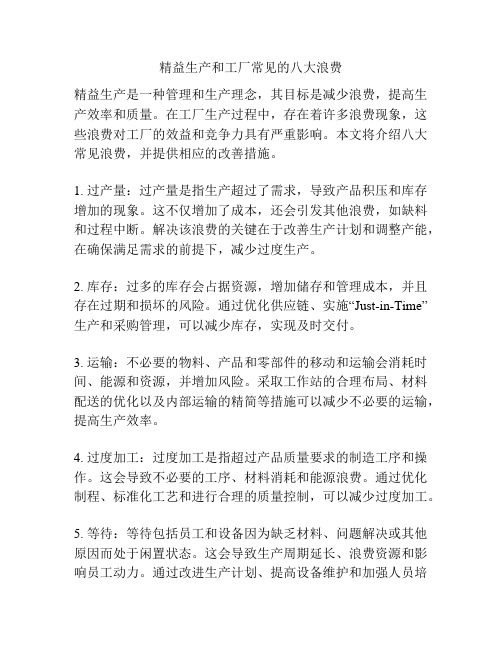
精益生产和工厂常见的八大浪费精益生产是一种管理和生产理念,其目标是减少浪费,提高生产效率和质量。
在工厂生产过程中,存在着许多浪费现象,这些浪费对工厂的效益和竞争力具有严重影响。
本文将介绍八大常见浪费,并提供相应的改善措施。
1. 过产量:过产量是指生产超过了需求,导致产品积压和库存增加的现象。
这不仅增加了成本,还会引发其他浪费,如缺料和过程中断。
解决该浪费的关键在于改善生产计划和调整产能,在确保满足需求的前提下,减少过度生产。
2. 库存:过多的库存会占据资源,增加储存和管理成本,并且存在过期和损坏的风险。
通过优化供应链、实施“Just-in-Time”生产和采购管理,可以减少库存,实现及时交付。
3. 运输:不必要的物料、产品和零部件的移动和运输会消耗时间、能源和资源,并增加风险。
采取工作站的合理布局、材料配送的优化以及内部运输的精简等措施可以减少不必要的运输,提高生产效率。
4. 过度加工:过度加工是指超过产品质量要求的制造工序和操作。
这会导致不必要的工序、材料消耗和能源浪费。
通过优化制程、标准化工艺和进行合理的质量控制,可以减少过度加工。
5. 等待:等待包括员工和设备因为缺乏材料、问题解决或其他原因而处于闲置状态。
这会导致生产周期延长、浪费资源和影响员工动力。
通过改进生产计划、提高设备维护和加强人员培训,可以缩短等待时间。
6. 不良品:不良品是指产品在生产过程中因为质量问题而被废弃或需要返工的产品。
不良品不仅浪费了原材料和劳动力,还增加了生产成本和质量风险。
通过提供员工培训、改进工艺控制和强化质量管理可以减少不良品数量。
7. 运动:运动指的是员工在工作中没有价值的移动和动作。
这会导致体力和精力的浪费,影响效率和工作满意度。
通过优化工作站布局、提供足够工具和培训以及简化工艺流程,可以减少不必要的运动。
8. 不正确的生产计划:不正确的生产计划会导致过量或不足的生产,增加库存、运输和等待时间。
通过改善生产计划和供应链管理,可以减少浪费和提高生产效率。
- 1、下载文档前请自行甄别文档内容的完整性,平台不提供额外的编辑、内容补充、找答案等附加服务。
- 2、"仅部分预览"的文档,不可在线预览部分如存在完整性等问题,可反馈申请退款(可完整预览的文档不适用该条件!)。
- 3、如文档侵犯您的权益,请联系客服反馈,我们会尽快为您处理(人工客服工作时间:9:00-18:30)。
4.搬运、堆积的浪费,管理工时 的浪费;
要把制造过多当做犯罪看待。
5.产品贬值。
管理 浪费
定义: 管理的浪费指的是问题发生以
后,管理人员才采取相应的对策来进行 补救而产生的额外浪费。
管理浪费是由于事先管理不到 位而导致的问题,科学的管理应 该是具有相当的预见性,有合理 的规划,并在事情的推进过程中 加强管理,控制和反馈,这样就 可以在很大程度上减少管理浪费 现象的发生。
低效率产生的原因: 1、管理者的低素质 ; 2、方法不当 ; 3、固步自封的僵化思
想。
我们允许的是创造性的失误,而不允许 反复发生低级的错误。
7.管理必须真正有“理”可 依
管理中的不合理现象:
☆ 目标指标不合理 ☆ 计划编制无依据 ☆ 计划执行不严肃 ☆ 计划检查不认真 ☆ 计划考核不到位 ☆ 投入产出不匹配
定义﹕由于生产原料供应中断、作 业不平衡和生产计划安排不当等原 因造成的无事可做的等待, 被称为 等待的浪費.
表现形式:
1. 生产线换线频繁;
2. 时常缺料而使人员﹑机器闲置;
3. 生产线未能取得平衡, 工序间经常发生等待; 4. 每天的工作量变动很大;
5. 机器设备时常发生故障;
6. 开会等非生产时间占用过多;
5.应付现象最常见
管理能力:素质、执行力(速度/准度/ 精度);
6.拒绝“低效”反复技发朮层生次: 认知高度;把握度;(相对)
标准化: 可行度;推广度;
7.管理必须真正有“企理业素”质可:依整体素质
1.管理工作不能“等”
常见的等待现象: ☆ 等待上级的指示
☆ 等待下级的汇报 ☆ 等待对方的回复 ☆ 等待生产现场的联系
7. 共同作业时,劳逸不均衡.
搬
浪 费 在精益生产中,搬运是一种不产生附加价值的动作,而不 运 产生价值的工作都属于浪费。搬运的浪费具体表现为放置、
堆积、移动、整理等动作浪费,由此而带来物品移动所需 空间的浪费、时间的浪费和人力工具的占用等不良后果。
合理化布局设计降低搬运浪费:
1. 辅助生产线的终点,应尽量接近供给对象的主生 产产线工序; 2. 充分探讨供应各工序零部件的方法; 3. 研究空卡板﹑包裝箱﹑夹具的返回方法; 4. 沿生产线设置大小适当的零部件暂放场所; 5. 不要忘记在生产线中设置检查工序和修理工序; 6. 确保设备的保养与修理所需空间; 7. 生产线的形状受到产品和场地的制约,可从安裝﹑零部件供应﹑
制造过多/过早
定义: 前工程之投入量, 超过后工程单位时间內之需求量,
浪 费 而造成的浪费。
导致的浪费有:
1.设备及用电,水,油等能源等增 加; 2.放置地,仓库空间增加; 3.提早耗用原材料,利率负担增 加;
在所有的浪费中, 制造过 多是最严重的浪费, 它带給人 们一个安心的错觉, 掩盖了各 种问题, 以及隐藏了由于等待 所带來的浪費, 失去了持续改 善的机会。
浪 费 动作,哪些动作是不必要的呢?是不是要拿上、拿下如此频繁?有没有必要有翻
转的动作、步行、弯腰的动作、对准、交换、调换、重复的动作等?若设计得好, 有很多动作皆可被省掉!
常见的12种浪费动作: ① 两手空闲
② 单手空闲 ③ 作业动作停止
④ 动作幅度过大 ⑤ 左右手交换 ⑥ 步行多
⑦ 转身角度大 ⑧ 移动中变换动作 ⑨ 未掌握作业技巧 ⑩ 伸背动作
(一)七大管理浪费的表现:
生产方式中所归纳的“八种
1.管理工作不能“浪等费””,主要发生在生产现场,
但是产生这些浪费的深层次的
2.把无序变有序 原因是什么?如果仅仅关注现
场存在的浪费,而不解决被现
3.协调不力企业丧象失所凝掩聚盖力的本质问题,无疑是
舍本逐末。
4.让闲置的“动”起(二来) 浪费的产生:
管理方面考虑,采用最为合适的形状。
定义:不良修理的浪费,指的是由于 工厂内出现不良品,需要进行处置的 时间、人力、物力上的浪费,以及由 此造成的相关损失。
浪费
这类浪费具体包括:
★材料的损失、不良品变成废品; ★设备、人员和工时的损失; ★额外的修理、鉴别、追加检
查的损失; ★有时需要降价处理产品; ★由于耽误出货而导致工厂信誉的下降。
案例分析
某公司连续若干年都没有完成公司计划,但上上下下都 不以为意,让外人诧异无比。经了解后才知道:该企业所 在的集团制定了三年后销售收入突破一百亿的发展目标, 再分解成年度目标,把指标下达给下属企业。由于该公司 不是按照实际情况而是按照总公司的要求来制定经营计划 的,各主要指标都订得非常高,缺乏资料的支援,不太具 有可行性。而根据公司计划进行的职能部门计划和月度分 解计划和实际差得很远,为了编制计划而在凑数字,导致 在计划编制时就对计划的完成没有多大信心。由于目标指 标不合理,使计划不具有可实施性,在执行、检查和考核 过程中,大家都是心中有数,走个过场而已。甚至如果执 行职能计划,例如采购物资和设备,反而会造成更大的浪 费。因此,到年终时大家都完不成计划,法不责众,人人 心安理得,丧失了追求,对企业的发展危害巨大。
所谓协调,就是指组织中的一 切要素、工作或活动要和谐地配 合,以便於组织的整体目标能够 顺利实现。有了良好的协调,就 会出现1+1>2的协同效应。
☆ 工作进程的协调不力 ☆ 上级指示的贯彻协调不力 ☆ 资讯传递的协调不力 ☆ 业务流程的协调不力
协调不力企业丧失凝聚力
4.闲置
扁平化管理、业务流 程再造、组织再造、过 程管理等方法,都是工 作流程化、规范化、职 责化的有效措施,可以 从某种程度上减少闲置 的浪费。但是,更重要 的是思想不能闲置,流 水不腐。
库存的危害: ☆ 额外的搬运储存成本 ☆ 造成空间浪费
☆ 资金占用(利息及回报损失) ☆ 物料价值衰减 ☆ 造成呆料废料 ☆ 造成先进先出作业困难 ☆ 掩盖问题,造成假象
降而库低能库够存存逐过,步多就地掩能解盖将决下这问述些题问库题存彻的底浪暴费露。出见水下面图,:进
水平面
缺勤
计划有误
能力不平衡
品质不一致
让闲置的“动”起 来 机构重叠,职能重叠┅┅形成人
浮於事,使生产经营要素不能得 到有效利用,造成了闲置的浪费。
危害:☆ 固定资产的闲置
☆ 职能的闲置或重叠 ☆ 工作程序复杂化形成的重叠 ☆ 物料人员的闲置 ☆ 造成资讯的闲置
5.应付现象最常见
应付就是工作虽然干了,但是不主动、不认真,敷衍 了事,不追求最好的结果,从而缺乏实际效果,是责任 心不强的一种表现形式,这种浪费在工作中是经常见到 的。
认识什么是浪费?
定义:浪費指不增加附加价值,使成本增加的一
系列活动. 对于JIT來讲,凡是超出增加产品价值所绝对必
須的最少量的物料、设备、人力、场地和时间的 部分都是浪費。这里有两层含义﹕
不增加价值的活动﹐是浪费﹔
尽管是增加价值的活动﹐所用的资源超过 了“绝对最少”的界限﹐也是浪費。
等待 浪费
常见的应付现象:
① 应付基础工作
② 应付检查 ③ 应付导致前松後紧 ④ 应付造成虎头蛇尾
应付的浪费主要是由责任心
不强和素质低下等造成的,它实 际上是工作中的失职。应该建立 健全以绩效为中心的监督考核机 制,以减少浪费。
低
6.拒绝“低效”反复发
效 生 低效的含义包括:
损 失 1、工作的低效率或者无效率; 2、错误的工作是一种负效率。
常见的加工浪费: ☆ 加工余量
☆ 过高的精度 ☆ 不必要的加工
过剩加工造成的浪费: ☆ 设备折旧 ☆ 人工损失
☆ 辅助材料损失 ☆ 能源消耗
库存 浪费
库存量越大,资金积压越大 库存包括: 零部件、材料的库存 半成品的库存 成品的库存
常见的库存: ☆ 原材料、零部件 ☆ 半成品
☆ 成品 ☆ 在制品 ☆ 辅助材料
☆ 有章不循造成的无序 ☆ 业务流程的无序
这些无序出现的频次多了,就 会造成企业的管理混乱。
缺乏明确的规章、制度、 流程,工作中容易产生混 乱,这是众所周知的。但 如果有令不行、有章不循, 按个人意愿行事造成的无 序浪费,更是非常糟糕的 事。
3.协调不力
协调不力是管理工 作中最大的浪费之一, 它使整个组织不能形 成凝聚力,缺乏团队 意识、协调精神,导 致工作效率的低下。
员工知识培训:精益生产JIT中
主讲:蒙新波
定义 等待浪费 搬运浪费
培 不良浪费 训 内 动作浪费 容 加工浪费
库存浪费 制造过多(过早)浪费 管理浪费
JIT的定义:
JIT生产方式指的是“ 只在需要时,按需要的 量,生产所需的产品”(英文含义:Just in time )。
JIT生产方式的引入,正是帮助企业解决工厂 常见的八大浪费;提高企业的经济效率和生产效 率,为企业的发展打造良好的基础。
造成等待的常见原因: ☆ 中层管理人员缺乏责任心和主动精神,不愿意承担
责任。 ☆ 对於较重要的工作,可以用5W1H来进行计划分解,
然後进行控制、检查和考核。激励员工和加强管理不能 从根本上解决问题,激励员工和加强管理相辅相成也许 更好一些。
没有规矩,不成方圆
2.把无序变有序 常见的无序现象: ☆ 职责不清造成的无序 ☆ 业务能力低下造成的无序
在餐厅发生的故事
在某餐厅18点高峰期,服务人员不足
场景: •客人要买单(付帐时),服务员拿单结帐 •结帐后,服务员拿单给客人总金额183元 •客人核定后,给200元整 •服务员再去结帐,返回时,给17元零钱 •客人提出要发票,服务员再去拿发票
以上活动是否有浪费?有几处?如何改善?
减少浪费,降低成本; 提升品质,增创效益。
总结:
管理浪费,要比工厂常见的其它七种浪费严重得多,解 决起来也困难得多。因为生产现场中的浪费大多数可以量 化,然而管理工作大多为软性指标,具有较大的弹性,要 想进行量化和细化相对困难;而且大家司空见惯,即使上 级要求,也是紧一阵後松一阵,容易形成反复,而如果不 能对管理工作中的浪费形成共识,活动是很难持续有效地 长期开展的。因此,我们必须对消除浪费活动的艰巨性和 长期性要有清醒的认识。但是,管理工作中的浪费一旦在 某种程度上被消除,则可能会出现几何级数的放大效应, 因此,我们要鼓足勇气,从消除点滴的管理浪费做起,向 着彻底消除浪费的目标一步一步地走下去。