车身焊装线
车身焊装工艺

第3篇车身焊装工艺第10章车身焊装工艺概述冲压将板料加工成外形各异的成形件,是分散、独立的,必须经过装配焊接才能成为车身,所以焊装是车身整体成形的关键工艺,焊装工艺是车身制造工艺中的重要环节。
10.1 车身焊装工艺特点(1) 连接特点设计车身时,考虑到制造工艺性,将车身分成若干个分总成,各分总成又可由若干个合件或冲压件组成,合件由若干个冲压件组成。
车身装焊过程是将若干个零件装焊成合件,再将若干个合件和零件装焊成分总成,最后将分总成、合件、零件装焊成车身总成。
例如图10-1所示的轿车车身主要是按图10-2的制造顺序装焊的。
因车身材料是薄钢板,所以车身部件之间为搭焊连接。
一辆载货汽车车身有2000多个焊点,轿车车身的焊点达5000多个、累计焊缝长达40m以上,螺母、螺栓焊100~200个,CO2气体保护焊焊缝累计长2~3m。
(2) 焊接方法车身零件连接特点决定了对焊接工艺设备的要求,长期实践表明最适合薄钢板连接的就是电阻焊。
采用电阻焊,车身焊接变形小。
由于电阻点焊为内部热源,冶金过程简单,且加热集中,热影响区较小,容易获得优质接头。
表10-1为车身制造中常用焊接方法及典型应用实例。
电阻焊是车身制造应用最广泛的焊接工艺,占整个焊接工作量的70%以上。
二氧化碳气体保护焊,主要用于车身骨架和车身总成中点焊不能进行的连接部位的补焊。
如有些焊接件的组成结构较为复杂或接头在车身底部等,点焊焊钳无法达到,只能用CO2焊进行焊接。
10.2 电阻焊原理与分类10.2.1 电阻焊原理电阻焊的物理本质是利用焊接区金属的电阻热和在压力作用下的塑性变形,使结合面的金属原子之间达到晶格距离,形成金属键,产生足够的共同晶粒,在外压力作用下得到焊点、焊缝或对接接头。
如图10-3所示,将置于两电极之间的工件施加压力F,并在焊接处通以电流I,利用电流通过工件本身的电阻产生的热量使温度升高造成局部熔化,断电冷却时,在压力继续作用下该熔化处立即凝固,形成牢固接头。
车身焊装工艺规划方法及分析

摘要:焊装工艺规划是焊接同步工程的一项主要工作内容,是焊装生产线设计的基础规划文件。
焊装工艺规划是指在产品设计阶段结合车型的生产纲领、自动化率及投资规模等对车身的上件流程、焊点分配、节拍计算等方面进行分析和验证,以达到在保证产品工艺可行性的同时确定出最优化的生产线结构的目的。
焊装工艺规划的结果将直接影响到生产线的技术可行性和投资成本。
本文主要介绍了焊装工艺规划的意义、流程、方法及主要工作内容。
关键词:车身焊装 工艺规划 方法 分析中图分类号:U463.82+1.06 文献标识码:B车身焊装工艺规划方法及分析安徽江淮汽车股份有限公司 杜 坤 魏庆丰 赵 涛 姜海涛1 焊装工艺规划的重要性及目的1.1 焊装工艺规划焊装工艺规划又称焊装工艺设计,是新车型车身开发焊装同步工程工作最重要的一环,是焊装生产线的核心技术。
其概念是指结合产品的生产纲领、自动化率、生产方式及投资规模等总体规划要求,结合车身数模对产品的工艺性如上件流程、焊点分配、节拍计算、物流、设备等方面进行分析和验证,在保证产品工艺可行性的同时确定最优化的生产线结构。
焊装工艺规划要求具有明确的输入条件:工艺设计输入如生产纲领及自动化程度等;产品设计输入如零件三维数模、BOM清单、产品结构树等。
任何一项输入数据的准确性都会影响到焊装工艺规划的结果。
1.2 焊装工艺规划的作用与意义焊装工艺规划的作用就是为了使设计具有生产可行性,优化生产线结构,减少投资成本。
a.优化产品设计,提升车身整体质量。
b.优化生产线布局,降低开发成本。
c.规范上件流程,平衡节拍,提高生产线效率。
d.三维仿真验证,缩短开发周期。
所以,焊接工艺规划对于生产线的设计有着很重要的意义。
工艺规划的准确与否将关系到产品的可实现性,以及后期的品质培育工作的难易程度,直接影响车型开发的周期和投资成本。
1.3 进行焊装工艺规划应具备的基本素质开展焊装工艺规划的工作人员应具备以下专业知识[1]。
焊装生产线的节拍分析及优化分解课件

工艺流程优化分解
工序分析
对焊接工序进行详细分析,找出瓶颈工序,进行优化改进。
工艺流程优化
优化焊接工艺流程,减少焊接次数和焊接变形,提高焊接质量和 效率。
引入自动化
引入自动化焊接设备和技术,实现焊接过程的自动化和智能化, 提高生产效率和质量。
操作方式优化分解
操作规范
01
制定详细的焊接操作规范,确保操作人员掌握正确的焊接技能
减少设备空闲时间,提高设备 利用率,降低设备投资成本。
产品质量提升
优化生产线节拍可以降低人为 操作失误率,从而提高产品质
量。
交付周期缩短
通过优化生产线节拍可以缩短 产品交付周期,提高客户满意
度。
优化效益评估方法
数据统计法
通过收集生产线相关数据,进行统计分析,评估优化效益 。
对比分析法
将优化前后的生产线数据进行对比分析,评估优化效益。
焊装生产线的节拍分析及优化分解 课件
目录
• 焊装生产线概述 • 焊装生产线节拍分析 • 焊装生产线优化方向 • 焊装生产线优化分解 • 焊装生产线优化实施方案 • 焊装生产线优化效益评估
01
焊装生产线概述
焊装生产线简介
01
02
03
定义
焊装生产线是指将焊接工 艺应用于车身制造的生产 线。
组成
包括焊接设备、夹具、传 输系统、控制系统等。
分析现状
对焊装生产线的现状进行详细的分析,包括设备 状况、人员配置、工艺流程等方面,找出存在的 问题和瓶颈。
制定优化方案
根据优化目标和现状分析结果,制定具体的优化 方案,包括设备更新、工艺改进、人员培训等方 面。
落实优化措施
设备更新
根据优化方案,对焊装生产线上的设备进行更新或升级,提高设备 的性能和稳定性。
白车身焊装生产线输送方式的应用及比较

车辆工程技术53车辆技术 汽车焊装生产线是汽车白车身全部成形工位的总称,其由车身总成线与多条分总成线构成,每一条总成线或分总成线又由多种焊装工构成。
每一个工位均由部分定位夹具、供水供气构成。
线间、工位间通过搬运机、机器人等搬送设备实现上下料与零部件的传送工作,以此来确保生产线中各项工作的连续性。
汽车焊装生产线主要包含了地板总成线、侧围总成线、车身合成线以及车身装配完成线。
因此,焊装生产线能否实现高速柔性化,其输送设备方式就显得尤为重要。
1 往复杆输送系统 往复杆的输送系统通常安设在夹具的平台之上,与夹具共同构成了焊装生产线。
往复杆输送系统通常由升降机构、同步机构、运动机构、定位机构、电控系统、平衡助力机构等组成。
依照不同的标准分级,往复杆输送线能够进行不同的分类,分类的方式可以以安装形式进行,主要分为空中往复杆输送与地面腹杆输送线;依照往复杆输送线梭结构进行分类,可以分为双往复杆树洞与单往复杆输送线;依照往复杆输送形式进行分类,可以分为水平往复杆输送线与升降往复杆输送线;依照往复杆输送线的举升机构进行分类,可以分为独立升降往复杆输送线与同步升降往复杆输送线[1]。
往复杆输送系统的工作原理主要是通过伺服变频电机带动齿轮与齿条来进行一段距离的往复运动;其举升、降低运动为达到一工位之后落下,能够便于夹具进行夹紧工作,在焊接结束之后,顶升能够促使工件离开夹具,进而使得工件与夹具不会互相干涉,便于输送工作[2]。
往复杆输送系统的主要特点在于机构简单、机械化程度较高、输送定位精度高,而缺点则是设备投资较大、输送机结构较为复杂、输送车型的柔性较差。
2 滑撬输送系统 滑撬输送系统属于白车身焊装车间中应用最为广泛的一种输送设备,多用于车身总成线工序间的输送、调整线输送、焊装车间空中储运线车身储存输送。
这种输送系统主要由滑撬、普通输送滚床、升降输送滚床、旋转滚床、垂直升降机以及电控系统所构成。
滑撬输送系统的主要优点为自动化程度高,能够用于多种批量生产的生产线上,同时其能够在一条生产线中进行间歇、连续输送,以此能够实现生产线中的联线输送,能够将下车身总成线、车身总成焊装线、调整线、车身储运线联系为一个整体,更加便于实现一个车间多车型生产线之间的联线,能够将不同车型的下车身总成线、车身主线独立布置[3],共同构建补焊线、调整线,更加容易实现生产线的分期投入,且输送速度较快、定位精度较高。
汽车车身焊装线涂胶质量控制研究
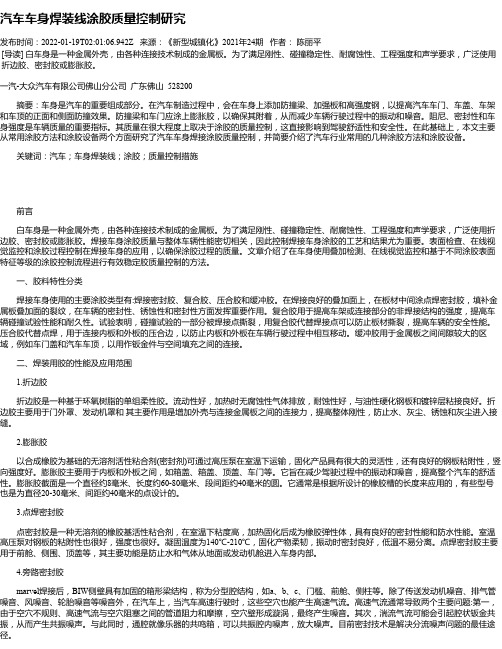
汽车车身焊装线涂胶质量控制研究发布时间:2022-01-19T02:01:06.942Z 来源:《新型城镇化》2021年24期作者:陈丽平[导读] 白车身是一种金属外壳,由各种连接技术制成的金属板。
为了满足刚性、碰撞稳定性、耐腐蚀性、工程强度和声学要求,广泛使用折边胶、密封胶或膨胀胶。
一汽-大众汽车有限公司佛山分公司广东佛山 528200摘要:车身是汽车的重要组成部分。
在汽车制造过程中,会在车身上添加防撞梁、加强板和高强度钢,以提高汽车车门、车盖、车架和车顶的正面和侧面防撞效果。
防撞梁和车门应涂上膨胀胶,以确保其附着,从而减少车辆行驶过程中的振动和噪音。
阻尼、密封性和车身强度是车辆质量的重要指标。
其质量在很大程度上取决于涂胶的质量控制,这直接影响到驾驶舒适性和安全性。
在此基础上,本文主要从常用涂胶方法和涂胶设备两个方面研究了汽车车身焊接涂胶质量控制,并简要介绍了汽车行业常用的几种涂胶方法和涂胶设备。
关键词:汽车;车身焊装线;涂胶;质量控制措施前言白车身是一种金属外壳,由各种连接技术制成的金属板。
为了满足刚性、碰撞稳定性、耐腐蚀性、工程强度和声学要求,广泛使用折边胶、密封胶或膨胀胶。
焊接车身涂胶质量与整体车辆性能密切相关,因此控制焊接车身涂胶的工艺和结果尤为重要。
表面检查、在线视觉监控和涂胶过程控制在焊接车身的应用,以确保涂胶过程的质量。
文章介绍了在车身使用叠加检测、在线视觉监控和基于不同涂胶表面特征等级的涂胶控制流程进行有效稳定胶质量控制的方法。
一、胶料特性分类焊接车身使用的主要涂胶类型有:焊接密封胶、复合胶、压合胶和缓冲胶。
在焊接良好的叠加面上,在板材中间涂点焊密封胶,填补金属板叠加面的裂纹,在车辆的密封性、锈蚀性和密封性方面发挥重要作用。
复合胶用于提高车架或连接部分的非焊接结构的强度,提高车辆碰撞试验性能和耐久性。
试验表明,碰撞试验的一部分被焊接点撕裂,用复合胶代替焊接点可以防止板材撕裂,提高车辆的安全性能。
汽车车身焊装生产线和焊装夹具简介

汽车车身焊装生产线和焊装夹具简介赵静1张俊华2李春植2邓早春3(1.烟台大学机电汽车工程学院04级研究生,烟台264005;2.烟台大学机电汽车工程学院,烟台264005;3.烟台富士沃森技术有限公司,烟台264005)摘要:对汽车车身焊装生产线和车身焊装中的夹具进行综述,其中包括焊装生产线的发展、组成等和焊装夹具的作用、特点、分类和设计要求等。
关键词:车身焊接焊装生产线焊装夹具ProductionLineofWeldingforAutoBodyandWeldingJigZHAOJing1,ZHANGJunhua2,LIChunzhi2,DENGZaochun3(1.SchoolofElectromechanicalandAutomobileEngineering,YantaiUniversity,Yantai264005;2.SchoolofElectromechanicalandAutomobileEngineering,YantaiUniversity,Yantai264005;3.FUJIWILSONENGINEERINGCO.LTD)Abstract:Thepapersimplyintroducedtheproductionlineofweldingforautobodyandweldingjig,includingdevelopment,makingupoftheformerandthefunction,characteristic,classanddesignrequireofthelatter.Keywords:Body,Welding,Productionlineofwelding,Weldingjig引言汽车是重要的运输工具,是科学技术发展水平的标志。
汽车工业在世界制造业的进步中起着特别重要的作用。
由于它的超大生产规模、资金和技术的高度密集以及强大的经济和辐射带动作用,使它在机械制造业中扮演着举足轻重的角色。
基于 Tecnomatix Plant Simulation 进行车身焊装线的物流仿真

基于 Tecnomatix Plant Simulation 进行车身焊装线的物流仿真作者:张鹿强来源:《今日财富》2017年第20期摘要:物流仿真是目前对汽车焊装生产线进行投资、规划、生产、调度的一种有效工具。
选用仿真软件Tecnomatix Plant Simulation作为仿真平台,通过汽车车身焊装线工艺流程的研究,建立层次清晰的系统仿真模型;根据仿真结果,进行瓶颈分析、设备利用率分析以及故障分析,对缓存区域,评估生产线的能力为生产调度策略的制定以及生产线的规划与布局提供依据。
关键词:焊装线;仿真建模;Tecnomatix Plant Simulation一、仿真模型的分析(一)物流仿真现状简介。
物流仿真是借助计算机技术,数学手段,采用虚拟现实方法,对物流系统进行实际模仿的一项应用技术,它需要借助计算机仿真技术对现实物流系统进行系统建模与求解算法分析,通过仿真实验得到各种动态活动及其过程的瞬间仿效记录,进而研究物流系统的性能和输出效果。
物流仿真技术最大的优点就是不需要实际设备的安装,不需要实际实施相应的方案,即可验证如下目标:①增加新设备后给公司或企业带来的效应;②设计新的生产线的预期产能和开动率;③比较各种设计方案的优劣等等。
物流仿真对降低整个物流投资成本,是不可或缺的。
国外的汽车主机厂和配套厂商,已经在Tecnomatix Plant Simulation 开发出集成度非常高2次开发产品,可以对焊装生产线模塊化建模,和经验重复利用,(二)焊装生产线的组成。
车身焊装生产线的组成车身焊装生产线是汽车白车身装配生产线,由许多焊装工位组成。
每个工位由许多定位加紧夹具、自动焊接装置及检测装置等设备以及供电供气供水装置组成。
线间、工位间通过搬送机(自行葫芦、电动葫芦等)、机器人等搬送设备实现上下料和零部件的传送,以保证生产线内各工位工作的连贯性。
该系统包括的内容有:1.地板线,地板总成线完成发动机室、前地板和后地板的装配焊接。
车身车间又称为焊装车间
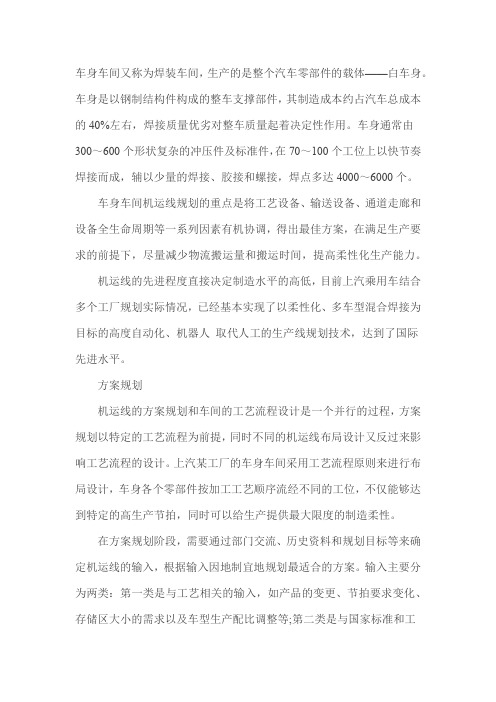
车身车间又称为焊装车间,生产的是整个汽车零部件的载体——白车身。
车身是以钢制结构件构成的整车支撑部件,其制造成本约占汽车总成本的40%左右,焊接质量优劣对整车质量起着决定性作用。
车身通常由300~600个形状复杂的冲压件及标准件,在70~100个工位上以快节奏焊接而成,辅以少量的焊接、胶接和螺接,焊点多达4000~6000个。
车身车间机运线规划的重点是将工艺设备、输送设备、通道走廊和设备全生命周期等一系列因素有机协调,得出最佳方案,在满足生产要求的前提下,尽量减少物流搬运量和搬运时间,提高柔性化生产能力。
机运线的先进程度直接决定制造水平的高低,目前上汽乘用车结合多个工厂规划实际情况,已经基本实现了以柔性化、多车型混合焊接为目标的高度自动化、机器人取代人工的生产线规划技术,达到了国际先进水平。
方案规划机运线的方案规划和车间的工艺流程设计是一个并行的过程,方案规划以特定的工艺流程为前提,同时不同的机运线布局设计又反过来影响工艺流程的设计。
上汽某工厂的车身车间采用工艺流程原则来进行布局设计,车身各个零部件按加工工艺顺序流经不同的工位,不仅能够达到特定的高生产节拍,同时可以给生产提供最大限度的制造柔性。
在方案规划阶段,需要通过部门交流、历史资料和规划目标等来确定机运线的输入,根据输入因地制宜地规划最适合的方案。
输入主要分为两类:第一类是与工艺相关的输入,如产品的变更、节拍要求变化、存储区大小的需求以及车型生产配比调整等;第二类是与国家标准和工厂规范相关的输入,如各类设备的国家标准、整车的通过性、机运技术规范和设备的选型标准等。
工艺输入中最典型和常见的是工艺变更以及工艺能力不足提出的需求。
1.工艺变更提出的需求上汽某车身车间共线生产A和B两种车型,B车型侧围分为侧围外板和内板,需要在拼合侧围和车顶板后才能拼合侧围外板,因此B车型需要有内总拼和总拼两次总拼;而A车型侧围内板和外板可在侧围分拼完成拼合,因此完成内总拼后可直接进行补焊。
汽车自动生产线的结构组成

汽车自动生产线的结构组成一、引言汽车自动生产线是利用先进的技术和设备,通过各个工作站的协调配合,实现汽车生产的自动化过程。
本文将对汽车自动生产线的结构组成进行详细介绍。
二、总体结构汽车自动生产线通常由装配线和焊接线两部分组成。
装配线主要负责汽车各个零部件的装配工作,而焊接线则负责汽车车身的焊接工作。
两者相互配合,共同完成汽车的制造任务。
三、装配线1. 车身焊装装配线的第一个工作站是车身焊装工作站。
在这个工作站上,汽车的车身零部件将被焊接在一起,形成完整的车身结构。
常见的焊接方法有气体保护焊、电弧焊等。
2. 内饰装配车身焊装完成后,汽车将进入内饰装配工作站。
在这个工作站上,汽车的座椅、仪表盘、中控系统等内饰零部件将被安装到车身上。
3. 动力总成安装内饰装配完成后,汽车将进入动力总成安装工作站。
在这个工作站上,汽车的发动机、变速器、传动系统等动力总成零部件将被安装到车身上。
4. 车身涂装动力总成安装完成后,汽车将进入车身涂装工作站。
在这个工作站上,汽车的车身将被进行喷漆和烤漆等涂装工艺,以提高汽车的外观质量和防腐能力。
5. 车辆调试车身涂装完成后,汽车将进入车辆调试工作站。
在这个工作站上,汽车的各个系统将被调试和检测,以确保汽车的性能和功能达到设计要求。
四、焊接线1. 焊接准备焊接线的第一个工作站是焊接准备工作站。
在这个工作站上,焊接设备将被准备好,焊接材料将被配送到相应的位置,以确保焊接工作的顺利进行。
2. 焊接操作焊接准备完成后,汽车将进入焊接操作工作站。
在这个工作站上,焊接工人将使用焊接设备进行焊接操作,将汽车车身的零部件焊接在一起。
3. 焊接检测焊接操作完成后,汽车将进入焊接检测工作站。
在这个工作站上,焊接工人将对焊接接头进行检测,以确保焊接质量符合要求。
五、结论汽车自动生产线的结构组成包括装配线和焊接线两部分。
装配线负责汽车零部件的装配工作,而焊接线负责汽车车身的焊接工作。
两者相互配合,共同完成汽车的制造任务。
汽车车身焊装线

各个工位的base板通过连接板连在一起构成了整个汽车焊装线的支撑装置,它既要支撑整个传输装置又要支撑焊装夹具。此外,为了保证夹具与车身零件的基准一致,在base板上按照设计基准画出基准刻度线。图中的调平装置主要起到对整个传输装置调平作用。
base板结构
1 base板2调平装置3 base板连接板
汽车车身焊装线
一、汽车车身焊装线的组成
汽车车身焊装生产线是轿车、微型客车等车型生产过程中的重要生产线之一,从汽车工业的发展历史来看,车身焊装线经历了20世纪50~60年代手工焊接线→20世纪70年代的自动化刚性焊装线→20世纪80年代以后的机器人柔性焊装线阶段。
就每条焊装线而言,它由焊接夹具、传输装置、焊接设备(焊枪、焊接机器人)构成;就整个汽车车身焊装线而言,它大体包括车身侧围总成线、车身门盖总成线、底板总成线、车身焊装主线等(目前尚无绝对的概括)。其中每部分又有相应的主线、子线、左右对称线和独立岛。根据生产节拍、自动化程度及生产方式等的不同,每条线又分为若干个工位;各工位间通过传输装置连为一体,每工位负责完成一部分工作。具体如图1:
以上所介绍的是传输装置的主要结构,通过除此以外还有一些辅助装置:
6,缓冲锁紧装置(如下图)
缓冲锁紧装置
1汽缸支撑架2限位块3汽缸4缓冲器5缓冲器支架6行程开关
焊装线传输装置共设置了4个缓冲锁紧装置分别分布于顶升框架的两端,主要是对“移动滑板”的水平运动起到缓冲和锁紧作用。具体过程是:当“移动滑板”快要运动到传输装置的末端时,便与缓冲器接触从而减缓运动速度;当“移动滑板”运动到传输装置的末端后,行程开关命令汽缸夹紧固定在移动滑板上的限位块从而起到锁紧作用。该装置实现了汽车焊装线传输装置慢启、慢停的进退动作要求,保证了传输装置运行安全、可靠。
浅析汽车白车身焊装线设计(1)

剖析汽车白车身焊装线设计随着近年来家用轿车的普及,汽车制造技术的飞速发展,自动化焊接技术在汽车白车身的生产中,起到了越来越重要的作用。
在我国,白车身焊装工艺设计的主要难点在于焊装生产线的设计,即采用哪种形式的输送系统和总拼焊接夹具,更有利于提高产能,更加环保,更加经济实惠。
白车身焊装线的结构我国目前使用的车身焊装线主要是由机器人、输送部分、工装夹具、焊接设备及其他辅助设备等部分组成,主要结构形式有:交叉臂步进式、摆臂步进式、滑橇输送式、台车输送式及高速辊床等。
1、交叉臂步进式焊装输送线图1中调频电机通过齿轮齿条传动将动力传递给往复杆,由此实现工件的水平输送。
而工件的上下运动则由双作用气缸推动楔铁平移实现交叉臂机构的升降运动来完成,因此,输送线的重复精度主要取决于楔铁的精度,但是,由于楔铁需要承受较大的摩擦,必须定期更换;同时,往复杆的升降运动靠气缸作用于楔铁运动来实现,其冲击力和噪声较大。
图12、摆臂步进式输送线从图2中可以看出,工件的水平输送是通过调频电机驱动齿轮齿条做往复运行实现的,顶升、落下装置采用电机带动曲柄旋转180度,从而实现输送线本体顶升、落下。
其运行过程与交叉臂步进式相同,只是驱动力由气缸驱动楔铁改为电机驱动曲柄,同时辅以气缸支撑,这样既保证了线体上下运动的平稳性,又消除了交叉臂步进式焊装输送线升降时带来的噪声。
这种形式的焊装线结构简单合理、稳定性好、辅助时间较短、重复定位精度较高,基本满足点、弧焊机器人的使用条件,适用于生产能力为5~10万辆/年的生产线。
目前,国内很多汽车厂采用该形式的焊装线,如东风天龙白车身总焊线、地板线;哈飞中意微面的左右侧围总成、白车身总焊线;哈飞路宝、柳微的SPARK白车身总焊线。
图23、滑橇输送线该焊装线通过采用往复杆或辊床输送滑橇来实现工件水平输送,可分为两种形式:往复杆输送滑橇式和辊床输送滑橇式。
工件上、下运动一般由固定工位的气动或液压顶升装置实现,工件的下线靠电动葫芦或自行电葫芦完成。
焊装输送线简介

焊装输送线焊装输送线车身焊装输送线是装焊生产线的一个重要组成部分;是实现各工位之间的制件传送的装置;是汽车制造过程中一个十分重要的生产环节;随着现代汽车工业的飞速发展,对制造工艺过程的机械自动化要求愈来愈高;为了提高生产率,减轻工人的劳动强度,提高汽车的质量和产量,应当尽量采用并且不断研制先进的机械自动化生产设备;输送装置提高了生产率,改善了劳动条件,保证了作为产品的汽车的质量和产量;根据输送线与装焊制件的空间相对位置,可以分为底置输送线和顶置输送线;顶置输送线又称为空中往复式,一般分为吊具直送式和上夹具平移式;吊具直送式是在每个工位上方安装一套吊具,利用这些吊具在空中轨道上的同步往复运动来输送制件;每当一个装焊循环完成后,吊具自动抓住制件使其脱离升降台,并将制件送至下一工位的升降台面上,然后吊具回位;上夹具平移式是在每个工位上方安装一套带提升装置的上夹具;每当一个制件的装焊循环完成后,提升装置下降,通过上夹具将工件夹紧提升至平移高度,平移装置带动提升装置将制件平移至下一工位;输送到位后提升装置下降,上夹具松开,将制件放入夹具体定位后,提升装置再升起,与上夹具返回初始位置;这种输送方式对于某些底面形状复杂、不宜用往复杆输送的大总成如:轿车底板、中、轻型载重车的驾驶室等,比较适用;但是,因为输送装置整体安装在空中桁架上,位于制件的上方,故对厂房高度上有要求;同时,从安全角度考虑,应该在空中设置安全护网,防止制件掉落伤害工作人员;底置输送线是常用的输送形式,根据输送线的结构形式,大体可以分为:举升直送式、滑橇输送式、工艺小车输送式、滚床输送式、自动导向小车输送式及往复杆输送;由于底置输送的常用性以及结构形式的多样性,下面着重就底置输送的各种形式进行介绍;一、举升直送式举升直送式是安装在夹具举升支架上的输送体升起后,将制件举起脱离夹具,直接将制件输送至下一工位的输送方式;根据输送体的不同,可以分为滚轮输送和皮带输送;滚轮输送式在举升支架上安装的是滚轮,在各个工位之间用滚道连接起来,通常用手工的方法将制件推送到下一工位;如图1,为华普海域506车型侧围线输送装置;这种生产线劳动强度较大,效率较低,适用于批量不大的生产;皮带输送在举升支架上安装的是同步齿型带,通过电机带动皮带输送制件,如图2,为华普海域506车型行李箱输送装置;由于制件直接与滚轮或皮带接触,因此制件形状应平滑,如果有太多的弯曲、凹凸,输送时会产生颠簸、震动,损伤制件表面;图1图2二、滑橇输送式滑橇是安装有定位装置,用来托举制件的支架;滑橇输送式就是利用滑橇在辊道移动,实现工件水平输送的方式;辊道安装在各个工位的举升支架上,当一个装焊循环结束时,各个工位的举升支架同时举起,使辊道升起到同一高度,驱动滑橇将制件输送到下一工位;到位后各工位的举升支架下降,滑橇与制件脱离,将制件放入夹具中定位;滑橇输送式根据驱动滑橇的方式,可以分为手工滑橇和摩擦轮输送式;用手工推动滑橇输送的方式称为手工滑橇;如图3,为奇瑞汽车H13商务车侧围线手工滑橇输送方式;图4为吉轻D82A主焊线手工滑橇输送方式;通过减速电机带动摩擦轮,利用摩擦轮与滑橇之间产生的摩擦力作为动力,推动滑橇输送的方式称为摩擦轮输送式;如图5,为夏利X121侧围的摩擦轮输送式滑橇;图3滑橇输送根据滑橇的运行方式可分为往复式滑橇输送和通过式滑橇输送;往复式滑橇输送在制件输送到下一工位,举升下降到位后,滑橇通过手工或摩擦轮方式返回原工位,实现往复运动;通过式滑橇输送的滑橇跟随制件从初始工位直到最后工位下线,滑橇堆积在下线工位,由人工或机械的方式运回初始工位重新装到输送线上;可见,通过式滑橇输送效率低,劳动强度大;因此,滑橇输送大多数采用的是往复式输送方式;图5为了保证滑橇运行的平稳性和定位的准确性,滑橇在加工制造过程中要保证相同的外形尺寸和加工精度;三、工艺小车输送式通过工艺小车输送托举制件,在工位间传输的形式称为工艺小车输送;工艺小车输送式与滑橇输送式的原理一样;滑橇在辊道上运行,而工艺小车通过自身带有的轮子在轨道上运行;如图6,为华普TX4的工艺小车输送方式;工艺小车通常通过手动推动,因此劳动强度大,工作效率低;不适合大批量的生产;图6四、滚床输送式滚床输送式是一种特殊的滑橇输送形式;其举升装置通常由电机带动同步齿形带,驱动曲柄旋转180度,或者驱动齿轮与齿条啮合,从而实现输送线本体的举升、落下;工件的水平输送是通过电机带动同步齿形带,使摩擦轮转动,驱动滑橇运行实现的;如图7,为奇瑞汽车H13商务车主焊线滚床输送方式;图7由于滚床的结构形式已经逐渐标准化,通用性日益增强,因此有很多专业厂家可以设计生产辊床;用户只要提出举升高度、工位跨度、摩擦轮跨距等参数即可;与滚床相配的滑橇可自行制造,或由滚床厂家直接设计制造;从以上的结构介绍中可以看出,举升直送式、滑橇输送式、工艺小车输送式、滚床输送式的举升装置是独立安装在各工位夹具体上的,各工位举升装置有独立的动力源,因此各工位的举升过程并不是完全同步的,但举升到位后,其升起的高度必须是等高的,以保证滑橇水平输送过程的平稳;由于滑橇水平输送是同时进行的,因此各工位举升的时间也不能相差太多,以免出现等待的现象,影响生产效率,降低焊接节拍;五、自动导向小车输送式自动导向小车输送式也称为台车输送式;台车实际上就是定位夹具本身,工件在台车上定位,在电机的驱动下在轨道上运行,从第一工位直到最后一个工位,然后从循环的回路返回到第一工位;如图8,为轿车公司M2输送线的局部图;台车在轨道上无法保证工件定位的精度,因此焊接时气缸举升装置举起台车定位;台车输送时举升装置下降将台车落入轨道中;与其他的输送形式不同,台车在输送过程中,工件始终定位夹紧在台车中不动,直至同台车一道运行至最后一个工位下线,因此工件的定位精度高;台车输送式结构简单可靠,适应多种车型的柔性生产能力强,代表了车身制造技术的发展方向;六、往复杆输送式焊装线上各工位托举制件的定位机构,安装在贯穿全线的两条并列的滑橇上,通过这两条滑橇的往复运动,实现制件传输的输送方式称为往复杆输送;这两条滑橇外形像两根长杆,通常称为往复杆;往复杆式输送线与滑橇式输送线最大的区别在于,滑橇式输送线的各个举升装置分别安装在各自工位的夹具底板上,因此各个举升是相对独立的;而往复式输送线的举升装置尽管也分别安装在各工位的夹具底板上,但他们通过连接部件连接成一体,使各工位夹具的底板也通过输送线连接为一体;因此输送线中所有夹具的底板必须超平、找正,调整为等高,并用过梁连接,才能保证输送线举升和传输的同步性和平稳性;这对夹具的调整提出很高的要求;往复杆式输送线中往复杆行走轨迹为举升、传送、下降、返回;当往复杆升起时将制件托起脱离夹具的定位,然后向前传送,将制件输送到下一工位,往复杆下降,将制件放入夹具里定位,最后往复杆返回原位;往复杆式输送线主要由以下部分组成:举升装置、水平输送装置、举升驱动装置、辅助举升装置、水平导轮连板等;1.举升装置往复杆输送线的举升装置将制件托起脱离夹具的定位,为制件的传送做准备;举升装置是往复杆输送线的重要组成部分;根据举升装置的结构形式,往复杆输送线可分为齿轮齿条式、曲柄摆臂式、曲柄滑块式、交叉臂式等;齿轮齿条举升式齿轮齿条举升式是通过齿轮与齿条的啮合,将输送线举起,传送制件的方式;这种方式将动力系统的拉力由水平齿轮齿条传递给垂直齿轮齿条,转化为向上的举升力;垂直齿条安装在基座中,与基座中的导套配合,垂直齿条在这里既是传递举升动力的零件,也是保证举升平稳性的导杆;如图9,为华菱H08车型主焊线使用的齿轮齿条式往复杆输送线局部图;图9齿轮齿条举升式结构简单、可靠,制造调试便利;由于采用齿轮齿条传递动力,因此传递效率高,响应速度快,举升同步性好,有明显的优点,是广泛采用的形式之一;但是由于举升齿条安装在台面上,往往比夹具底板的厚度长很多,因此输送线安装前必须开挖地坑,增加了基础施工量;同时,安装和维修也必须经常进入地坑,增加了工作的难度;曲柄摆臂举升式曲柄摆臂举升式的机械原理是多平行四边形连杆机构;每个工位的举升装置都是一个平行四边形连杆,焊装线上所有工位的举升装置通过水平连杆连为一体,形成多平行四边形连杆机构;输送线动力装置拉动动力曲柄旋转,动力曲柄通过回转轴将扭矩传递给举升装置使曲柄摆臂回转,托举起整个输送线;如图10,为解放公司J6卡车曲柄摆臂举升式输送线的局部图;图10曲柄摆臂举升式结构明快、轻盈,输送线工作时震动小、噪音低,全部的装置均安装在夹具台面上,无需开挖基础,使安装和维修都很便利,是目前经常采用的形式;但是由于曲柄摆臂举升式采用的是平行四边形连杆机构,所有的曲柄摆臂及连杆的尺寸必须相等,否则无法形成平行四边形,导致举升时因别劲而无法运动甚至损坏输送线;因此曲柄摆臂举升式对输送线的加工和调试精度提出了很高的要求;曲柄滑块举升式该举升结构的机械原理相当于曲柄滑块机构;各工位的回转曲柄通过水平连杆连为一体,输送线动力装置带动曲柄转动时,曲柄通过垂直连杆传递动力,使各工位举升装置沿导向座做垂直运动;可见,各工位举升装置就相当于滑块;如图11,为大众捷达地板线的曲柄滑块举升形式;图11交叉臂举升式交叉臂是两根交叉成剪刀形状的等长的摆臂;摆臂的铰链回转点在摆臂的中点处;摆臂的两端分别安装在举升架和夹具底板上,摆臂一端是固定回转铰链,另一端是安装有滑块或滚轮的活动端;在外部动力的驱动下,活动端在导轨或滚道中移动,摆臂绕铰链回转点旋转,使交叉臂在垂直方向的高度发生变化,驱动举升架升起或下降;如图12,为交叉臂举升机构的外观图;图12交叉臂举升式的两根交叉臂必须同时动作,才能实现举升,因此交叉臂举升式是举升同步性最好的机构;但是交叉臂最好在每个工位沿着传输方向设置一个,因此交叉臂占用的空间较大,不利于使用在夹具结构较复杂的情况下;2.水平输送装置水平输送装置由调频电机带动齿轮齿条将动力传递给往复杆,实现工件的水平输送;往复杆加工的精度和材质的稳定性对于制件的定位精度影响很大;由于往复杆很长,很难整体加工制造,因此通常由带凸凹槽的连板连接而成,或者由铝型材连接而成;制件的定位装置按照工位跨距等距离的安装在往复杆上;齿条安装在滑橇的下面,通过与齿轮啮合驱动滑橇前进;电机以及齿轮等通过连接架上与输送线举升装置安装在一起,使水平输送装置与输送线同步举升下降;3.举升驱动装置举升驱动装置为输送线的举升提供动力;通常的动力形式有电动、气动和液压三种;气动和液压分别以气缸和液压缸为执行元件,以压缩空气和液压油为工作介质,推动或拉动执行元件的活塞杆,通过举升传动部件将水平方向的输出力改变为垂直方向的举升力;电动的形式是以电机和减速机作为执行元件,由滚珠丝杠将回转扭矩转变为水平方向的拉力,再通过举升传动部件将水平方向的输出力改变为垂直方向的举升力;气动形式具有结构简单、成本低、易于维修等优点;但是气动形式只能用于输送线较短、负载较小的场合;电动是一种简单的输送动力;它的主要优点是启速度动快、传递效率高;但是如果输送线负载过大,电机的功率也很大,动能消耗很大,为了防止出现“别劲”现象而烧损电机,电气设计时要增加安全设置; 液压形式在输送线负载较重,工位较多的情况下常采用;液压输出压力高,压力输出过程平稳、柔和,冲击力小,提高了输送线举升过程的平稳性,和制件定位的准确性;在输送线的设计中得到了广泛的应用;液压传输需要另外配置液压泵站;由于液压输出压力高,对于密封和安全要求高,泵站通常由专业厂家设计制造,增加了输送线的成本;三种动力形式各有其优缺点,应用在不同的场合;应根据输送线的形式、负载的大小、焊接节拍、传动精度、工作环境、经济性以及安装维修的要求等,综合分析各种因素考虑;4.辅助举升装置辅助举升装置是输送线举升的助力装置;辅助举升气缸平衡掉输送线一部分重量,减小了动力元件的负载;对于摆臂式、交叉臂式举升形式来说,辅助举升装置就更为重要;摆臂式和交叉臂式举升是通过摆臂的摆动角度变化举起输送线;在举升刚刚启动时,由于摆臂与夹具台面夹角较小,在垂直方向形成的举升力也较小,辅助举升气缸弥补了举升力的不足,缩短了举升的辅助时间;辅助举升气缸通常单作用使用,举升时起到助力作用;而输送线下降时,则起到了缓冲的作用,保证了线体上下运送的平稳性,又降低了升降时带来的噪声;5.水平导轮连板水平导轮连板将各个工位的举升装置连接为一体,使各工位举升时同步;连板两侧安装有导向导轮,在滑橇运行时起到导向的作用,保证滑橇水平输送的稳定性和准确性;为了降低与滑橇的冲击,减少滑橇的磨损,导向导轮外壳通常采用尼龙或聚氨酯制造,内部装有滚动轴承;同时导轮与连板的连接处应安装垫片,便于调整导轮间距,使滑橇通过时轻松、顺畅;6.往复杆输送线的设计要点升降式往复输送线的设计、制造、安装、调试及生产必须完全满足工艺要求,设计结构合理,具有足够的强度和刚性;a、输送线上升、下降时要有可靠的导向机构,使举升时平稳、安全、可靠,没有抖动、发颤现象;b、输送线上升、下降到位时要求停止位置精确,保证滑橇运行时不会与夹具或其他设备干涉;c、往复杆水平输送机构要有极限限位装置;通过普通的减速电机驱动滑橇前进或后退,到位时并不能使滑橇处于精确的定位位置,因此要在水平输送的两端安装机械限位及缓冲器;d、辅助气缸为单作用,气路设计时要考虑气缸回程时的排气装置;通常采用带溢流功能的减压阀,排气量较大的情况下也可以考虑使用储气罐;e、输送线还要有必要的安全装置;比如在维修时应有安全插销锁定输送线,防止输送线突然启动,造成对维修人员的伤害;f、对于经常转动或滑动的位置,应设置润滑点,以便于保养加油;七、装焊输送线的选择车身装焊生产线作业内容多 ,装备空间位置关系复杂、自动化程度高;对设计者提出了很高的要求;它涉及焊接工艺、机械、电器、液压等专业知识和设计经验;在静止和相对运动的状态下,诸如作业者、机器人、输送系统、自动焊钳、焊接夹具及其它辅助装置的空间布置问题都成为设计者的难点和要点;对焊装输送线结构的选择,最需要考虑的是生产纲领、产品结构和工艺特点、投资规模和夹具设计制造技术水平以及厂房等情况,在细部结构上要结合产品的寿命周期,市场定位和质量要求,并对相关因素进行综合比较来进行选择;1、生产纲领根据生产纲领的大小,确定生产节拍及工位数量;一般生产纲领越大,则焊接节拍越短;工位越多,自动化程度越高;2、经济性装焊生产线的设计要符合投资效益规律;对焊接设备、焊接夹具、自动焊接装置、输送装置等影响投资额度和生产效率的关键设备要进行价值工程分析;必须通过最佳工艺方案和优化设计装备实现以最少的投资得到最大的效益;3、焊接工艺性焊接工艺的拟订对车身焊接质量起着决定作用;要避免由于焊接过程而导致的制造误差,除了要优化装备设计外,再就是采用容易实现机械化和自动化的焊接方法;4、车身总成的装配性车身总成是由若干个分总成组成;装配方案有两种:一种是集中装配,另一种是分散装配;必须合理确定装配方案和分散装配时的分散程度及装配顺序,既要考虑总成的焊接与装配,又要有利于分总成的焊接与输送;5、质量检测车身装焊质量包括;形状、尺寸精度、焊接接头强度、密封性等方面;为了获得有互换性的车身总成,有效的控制误差分配,车身在制造过程中和成型后,均要进行检测;最长用的方法是通过检测夹具来检测关键部位及整车外型尺寸;可以有效的提高白车身质量 ,降低次品率;6、自动化程度自动化程度对生产线是一个重要的影响因素;在投资条件允许的情况下,尽可能提高自动化程度;这样可以稳定车身的焊接质量,提高生产效率,提高柔性程度,减轻工人的劳动强度;7、安全保证体系安全保证体系是汽车装焊线中不可缺少的部分;设备、产品、人员的安全都必须有精心的组织、严密的技术措施加以防范和保证;必须做到万无一失;。
轿车白车身焊装生产线的工艺规划与布局设计
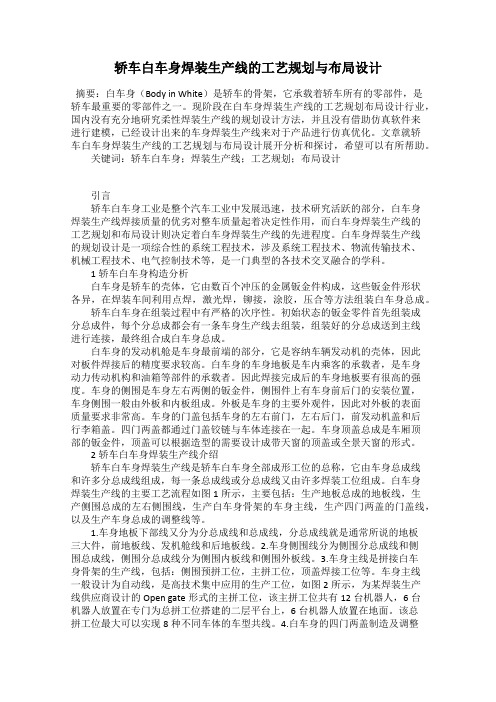
轿车白车身焊装生产线的工艺规划与布局设计摘要:白车身(Body in White)是轿车的骨架,它承载着轿车所有的零部件,是轿车最重要的零部件之一。
现阶段在白车身焊装生产线的工艺规划布局设计行业,国内没有充分地研究柔性焊装生产线的规划设计方法,并且没有借助仿真软件来进行建模,已经设计出来的车身焊装生产线来对于产品进行仿真优化。
文章就轿车白车身焊装生产线的工艺规划与布局设计展开分析和探讨,希望可以有所帮助。
关键词:轿车白车身;焊装生产线;工艺规划;布局设计引言轿车白车身工业是整个汽车工业中发展迅速,技术研究活跃的部分,白车身焊装生产线焊接质量的优劣对整车质量起着决定性作用,而白车身焊装生产线的工艺规划和布局设计则决定着白车身焊装生产线的先进程度。
白车身焊装生产线的规划设计是一项综合性的系统工程技术,涉及系统工程技术、物流传输技术、机械工程技术、电气控制技术等,是一门典型的各技术交叉融合的学科。
1轿车白车身构造分析白车身是轿车的壳体,它由数百个冲压的金属钣金件构成,这些钣金件形状各异,在焊装车间利用点焊,激光焊,铆接,涂胶,压合等方法组装白车身总成。
轿车白车身在组装过程中有严格的次序性。
初始状态的钣金零件首先组装成分总成件,每个分总成都会有一条车身生产线去组装,组装好的分总成送到主线进行连接,最终组合成白车身总成。
白车身的发动机舱是车身最前端的部分,它是容纳车辆发动机的壳体,因此对板件焊接后的精度要求较高。
白车身的车身地板是车内乘客的承载者,是车身动力传动机构和油箱等部件的承载者。
因此焊接完成后的车身地板要有很高的强度。
车身的侧围是车身左右两侧的钣金件,侧围件上有车身前后门的安装位置,车身侧围一般由外板和内板组成。
外板是车身的主要外观件,因此对外板的表面质量要求非常高。
车身的门盖包括车身的左右前门,左右后门,前发动机盖和后行李箱盖。
四门两盖都通过门盖铰链与车体连接在一起。
车身顶盖总成是车厢顶部的钣金件,顶盖可以根据造型的需要设计成带天窗的顶盖或全景天窗的形式。
车身焊装生产线机器人布局设计

创新视点科技创新导报 Science and Technology Innovation Herald8随着我国汽车工业的飞速发展,机器人由于的动作稳定可靠,重复精度高成为一种先进的自动化设备在汽车白车身生产中得到越来越广泛的应用。
对于机器人车身焊装生产线项目的前期工作就需要拟定一个大概的布局。
这个布局的好坏直接影响后面工作的工作量和进度[1]。
机器人布局设计需满足机器人运动学的要求和周边设备与生产环境对机器人间的约束[2]。
由于目前机器人布局设计的评价没有统一的指标,本文是基于仿真技术和现场经验对车身焊装生产线机器人布局设计进行探讨。
1 车身机器人焊装线的组成车身机器人焊装线通常由点焊机器人、弧焊机器人、搬运机器人,以及滑动拼台、转动拼台、操作人员的安全区等组成,它的布局设计相对于其它生产线来说要复杂得多。
如图1所示,一条正在规划的柔性线下车体1#工位的布局,这个工位存在工人吊装、机器人搬运、点焊机器人定位焊等多工作界面;存在上层搬运机器人,中层车体输送和下层点焊机器人多层结构布局;并且空间上必须预留总成搬运机器人的滑移空间。
(见图1)对于图1所示的多工作界面、多层结构和紧凑空间的工位,机器人的布局需要考虑到机器人运动轨迹、人机交互工作界面的安全和周边设备对布局的空间约束[3]。
在空间约束上,钢结构的高度决定了搬运机器的安装高度,而搬运机器人的高度决定着滑移拼台的高度,也决定了点焊机器人的运动空间,人机工程的好坏。
因此,需要仿真设计出最佳的机器人布局。
2 车身焊装线机器人布局设计机器人仿真项目的前期工作就需要拟定一个大概的布局。
本章节主要探讨仿真过程中,怎样去布局车身焊装生产线中各种设备与机器人的位置[4-5]。
2.1 机器人与夹具的距离工件是装在夹具上面的,故机器人与夹具之间的距离直接关系到机器人与工件之间的距离。
通常来说,机器人与夹具的距离车身焊装生产线机器人布局设计①郑宏良 覃鑫(上汽通用五菱汽车股份有限公司技术中心 广西柳州 545007)摘 要:通过分析机器人与夹具、修模器、换枪架和围栏的相对距离,以及机器人底座的高度研究机器人布局设计,并从目前的仿真项目中总结出机器人仿真项目中如何获得一个好的布局,有效地解决焊接过程中出现的干涉多、余量少等问题,同时还能够优化机器人的运动轨迹,减少工作的节拍。
白车身焊装生产线如何提升效率

白车身焊装生产线如何提升效率2016-05-26 16:541.焊装生产线概述车身是构成汽车的主要组成部分,车身制造技术也是现代汽车工业的重要组成部分,车身制造水平的优劣直接体现了一个国家汽车工业的水平。
自1913年福特汽车公司采用流水线”生产方式以来,汽车生产线在汽车工业中占据了极其重要的地位,它对提高生产效率,降低汽车成本起到了至关重要的作用,在大规模生产方式下居于核心地位。
汽车白车身焊装生产线是把各车身冲压零件装配焊接成白车身的全部成形工位的总称,它通常包含发动机舱、侧围、地板及车顶顶盖等焊接分总成线及最后合装主焊生产线。
根据生产节拍、自动化程度及生产方式等不同,主焊线及分总成线又划分为若干工位,各工位通过各种类型输送装置连接为一体,每一工位负责完成一部分工作。
单工位一般由连接设备、焊装夹具、传输装置等几部分组成(见图1)。
图1焊装总拼工位1•传输装置2•焊接设备3.车身焊装夹具2 ■焊装生产线问题(1)工位故障率问题每条白车身焊装流水线由若干工位组成,而每个工位完成车身的一道或几道工艺,因此每个工位由若干设备组成,如图1所示。
此工位为主焊接线的一个重要工艺工位,其工艺流程为:车身由升降传输辊床运输到工位内部,到位之后,由车身焊接定位夹具将车身侧围、顶盖横梁和车体主结构定位夹紧,然后机器人抓取点焊焊枪对于车身进行点焊焊接。
焊接结束之后,夹具打开,车身再由升降辊床运输到下一个工位。
整个工位的设备组成:机器人+点焊焊枪7台;左右侧围定位车身焊接夹具两台;升降辊床传输装置1台。
单台设备对应的平均故障间隔时间,平均修复间隔时间,以及可利用率参数如表1所示。
以上这些设备构成了一个可修复系统。
虽然这些设备都是独立不相关,发生故障的概率也没有联系,但是当其中任何一个设备发生故障时,整个系统将要停机用于修复,所以为了保障整条生产线效率,不仅在设计过程中就要为此工位留出修复的时间,同时在生产过程中,还要安排维修人员进行维护和及时修复。
- 1、下载文档前请自行甄别文档内容的完整性,平台不提供额外的编辑、内容补充、找答案等附加服务。
- 2、"仅部分预览"的文档,不可在线预览部分如存在完整性等问题,可反馈申请退款(可完整预览的文档不适用该条件!)。
- 3、如文档侵犯您的权益,请联系客服反馈,我们会尽快为您处理(人工客服工作时间:9:00-18:30)。
第3章车身焊接装配线
车身升降机液压系统稳定性分析
14:41
29
系统稳定性分析
1、幅值裕度
K g dB 20 lg K q Ah 2 h h 20 lg 2.3 1.13 10 2 lg 2 0.53 424.5 6.9dB
幅值裕度大于零,得出系统是稳定的。
第3章车身焊接装配线
14:41
21
2.3焊点多,工作频次高焊枪发热问题的解决
第3章车身焊接装配线
14:41
22
2.4二次电缆内脱落铜丝团阻塞焊枪水路引起 的发热故障
第3章车身焊接装配线
14:41
23
12.5工程案例
车身升降机液压系统稳定性分析
第3章车身焊接装配线
14:41
24
概
述
汽车车身流水生产焊装线一种典型布置方式:地面 →地道→地面循环式。该布置方式采用液压垂直升降机 来完成车身及工装小车的地面与地道或地道与地面的升 降任务。 传统液压升降机采用单一液压缸驱动,但实践表明单液 压缸驱动存在很多问题如:升降台单边下沉,运行卡死, 振动等。 现场证明双缸驱动式具有良好的特性。双缸驱动式 升降机在参数优化设计及系统稳定性方还需深入研究, 进一步满足生产要求。
第3章车身焊接装配线 12.1车身焊接装配线的组成
14:41
11
侧围外板装入,装后柱和 中柱,点定,焊台下降, 工件在往复杆上。
焊台托起工件,旋转 到垂直,补齐焊点, 台面回至水平并下降。
第3章车身焊接装配线 12.1车身焊接装配线的组成
14:41
12
装入后内挡泥板及 加强板
多点焊。四个点焊 机140点
31
动态刚度分析
阀控液压缸的动态速度刚度为
FL
2 Ah K ce
XP
s2 2 h 2 s 1 h h s 1 2 h h
FL
稳态时 ( 0),其频率特性的模为
XP
2 Ah K ce
称
为稳态速度刚度 。它的倒数称为稳态速度柔
2 度,值为 K ce Ah 。是速度下降值与所加负载
K
g
2 1.7 9 10 2 6
0.0878
由正态分布可靠度计算公式:
第3章车身焊接装配线
车身升降机液压系统稳定性分析
14:41
35
F
0
1
Kg
1 xKg exp 2 Kg 2
滑轮 升降台
m1
Q Q m2 Q
F
b)受力分析
m1
m2
油缸 F
Q
Q
a)升降机1/2模型
双缸驱动原理图与受力分析
第3章车身焊接装配线
车身升降机液压系统稳定性分析
14:41
27
液压系统数学模型
1、三通阀控液压缸原理图
第3章车身焊接装配线
车身升降机液压系统稳定性分析
14:41
28
2、传函与方框图
Ka XP Xv s2 2 2 s 1 s n n
第3章车身焊接装配线
车身升降机液压系统稳定性分析
14:41
25
地道循环式车身装焊线示意图
工装小车 车身
导柱
地道循环式车身焊装线
油缸
第3章车身焊接装配线
车身升降机液压系统稳定性分析
14:41
26
等效力学模型
因双缸液压升降机结构对称取1/2模型。升降机由 三部分组成如下图, 升降台,滑轮组,油缸。升降台 速度为V1 ,质量为m1 ,滑轮和活塞速度V2 质量为m2 。
2
2 e
的选取 油液等效容积弹性模量 e 0.1 1.8 10 N / m
9 2
且认为服从正态分布,根据“三倍标准差原理”
第3章车身焊接装配线
车身升降机液压系统稳定性分析
14:41
34
求得
e
1.7 109 N m 2 。 6
g
将相关数据代入公式,求稳定裕度的标准差 K
第3章车身焊接装配线
车身升降机液压系统稳定性分析
14:41
33
可靠性设计
幅值裕度标准差计算公式
K
g
Ah 1 h ln 10 2V0 M t e
1 K ce h ln 10 2 Ah
2
Mt V0 e
第3章车身焊接装配线
14:41
16
1.引言
现场表明车身焊接质量问题与焊机发热故障有关. 焊机发热故障的四种类型: 1)焊装线焊枪依次出现“阶梯式”温升. 2)焊枪进回水管反接引起焊枪发热. 3)焊点工作频次高的焊枪发热问题. 4)二次电缆内脱落铜丝团阻塞焊枪水路引起的 发热.
第3章车身焊接装配线
14:41
17
第3章车身焊接装配线
14:41
18
2.四种焊枪故障分析及排除方法
2.1焊装线焊枪“阶梯式”温升故障.
第3章车身焊接装配线
14:41
19
2.1.2解决措施
①将恒径 式进水管 改成 "阶 梯式"结构
②加大回水管 Dg回=(1.5-2)Dg进
第3章车身焊接装配线
20
14:41
2.2焊枪进回水管错接引起的故障
(1)焊机组 (2)水冷系统 (3)悬挂导轨 (4)板式输送链
第3章车身焊接装配线
14:41
2
2.焊装线类型
(1)贯通式车身焊装线
(2)循环式焊装线
第3章车身焊接装配线
14:41
3
12.2 贯通式装焊生产线
(1)CA-10B驾驶室焊装线
2工位:电弧焊, 焊接驾驶室骨架总 成。升、转夹具。 1工位:点焊底板、 前围骨架、后围 骨架。
第3章车身焊接装配线 12.1车身焊接装配线的组成
14:41
9
(4)贯通式底板焊装线
占地小,工件前后传递,装夹、焊接装备分别固定在 各工位上。工件传送靠贯通式往复杆实现,传递装置简单。
第3章车身焊接装配线 12.1车身焊接装配线的组成
14:41
10
(5)贯通式侧围焊装线
焊装线长20 m、五个工位,工人7个、生产节拍1 min。 四立柱式多点焊机1台,悬挂式点焊机9台,焊点250点。 往复杆传送。
悬电焊机补焊, 侧围总成下线
第3章车身焊接装配线 12.1车身焊接装配线的组成
14:41
13
12.3 循环式装焊生产线
1.地道循环式
工装小车 车身
滑轮 升降台
m2
导柱
油缸
m1
Q
F
油缸
升降机原理
组成 : (1)随行夹具。 (2)液压升降及地下回程传送链。
第3章车身焊接装配线
14
14:41
2.EQ-1090前 围装焊环形线
14:41
车身升降机液压系统稳定性分析
36
通过标准正态表可查得可靠度为:
F 0.5233 dz 0.6085
z
结果基本上是符合实际,也 表明了系统在正常情况下是可靠 的。
第3章车身焊接装配线
车身升降机液压系统稳定性分析
14:41
37
结束语
双缸驱动液压升降机是一个多质量的复杂 系统,采用1/2等效力学模型进行研究分析更加 准确反映工程实际,使复杂问题得以简化,这为 多质量系统分析提供了参考。
第12章 车身焊接装配线 12.1车身焊接装配线的组成 12.2 贯通式装焊生产线 12.3 循环式装焊生产线接装配线的组成
12.1 1.车身焊装线组成和类型 1.组成:
变压器 平衡器 二次电缆 焊枪
1章黑36 1-1中36号 1.1.1黑32 1.中32 (1)黑28
线长8m,10工位,10套随行夹具,3台多点焊机和8台 悬点焊机,4人,8分/辆。占地较大,传动机构简单。 链条带动拨杆,拨杆推动大链条作环形运动,小车被 链条带动。小车到预定工位,行程开关切断电源,多点焊 机上的油缸迫使夹具强行定位。
第3章车身焊接装配线 12.3 循环式装焊生产线
14:41
15
12.4工程案例 富康轿车车身焊接质量问题研究
力之比。
第3章车身焊接装配线
车身升降机液压系统稳定性分析
14:41
32
因双缸面积比单缸面积大两倍。故双缸速 度柔度为单缸速度柔度的1/4。 双缸速度下降为:
K ce FL 6 10 12 34550 1.9 10 5 m s 2 2 2 Ah 1.13 10
从上述结果可以看出来负载力造成的速度下 降非常微小,不影响升降台的正常运 行。表 明双缸驱动液压升降机系统动态特性是良好 的。
第3章车身焊接装配线 12.1车身焊接装配线的组成
14:41
8
(3)EQ114驾驶室 焊装线
抬起步伐式往复输送方式,输送平稳,定位精度高,占 地小,分总成上线方便。 凸轮铰链式,双向气缸推动升降臂,抬起810mm,用 变频电机带动齿轮,齿条前后运动,来完成输送工作。 可编程序控制器,控制同步抬起和落下、输送装 置往复运动、车型的识别、位置监测及故障诊断等。
xKg z Kg
dx
将其转化为标准形式为
F z dz ,其中
z
选择积分区间为 ,6dB ,因此
xKg z Kg
第3章车身焊接装配线
0.3 0.346 0.5233 0.0879
2 2 1 1.13 10 424.5 ln 10 2 8 2 1.24 10 80 7 10 1 6 10 12 80 0.53 ln 10 2 1.13 10 2 1.24 10 2 7 108