现场合理化改善技巧
精益生产现场改善的方法

现场改善可以理解为现场管理优化,运用现场管理的手法对生产现场的人、机、料、法、环等各生产要素进行持续的改善。
实行现场改善活动,可以保证产品质量;消除各个环节的浪费,降低成本;改善工作环境,提高工作效率,达到生产线平衡。
那么企业要怎样进行现场管理了,共益根据自己的实践经验,总结出几点现场改善的办法:1、现场评估、作业测量在生产现场改善前,应该对生产现场进行现场评估和作业测量,其中,包括后现场LAYOUT、人员配置与生产状况、工序能力调查、现状物与情报流等的人、机、物、法、环的评估。
只有对生产现场进行实事求是的评估和测定,全面掌握和认识现况,才能对生产现场进行有目的、有方向的改进。
2、5S活动的应用实施"5s"现场管理,要不断进行整理、整顿、清扫、清洁、素养,并逐步循环和提高。
整理就是要妥善处理现场的停滞物品,分离废弃物和保留物;整顿是将整理后需要的物品定点摆放,把有用物归类,各就各位,以期达到合理布置、方便使用,且提高安全性、实现目标管理;清扫就是要求全体人员自己动手清扫,创造一个干净、明快舒适的工作环境;清洁是对整理、整顿、清扫这3项工作的保持和坚持;素养是规范人的行为,养成自觉执行制度和作业标准的良好习惯。
3、生产现场的改善只有做好前期的作业测定、5s活动、定置管理、目视管理、班组管理等各环节的基础上,才能谈到真正意义上的生产现场的改善。
因为只有真正把现场的实况完全掌握好,才能把现场的方方面面的问题的源头掌握住;只有把现场真正目视化了,问题才一目了然地呈现出来。
当然,某些难以用肉眼、用感觉或凭经验就解决的问题,就需要借助于一些数学统计分析技术、工业工程技术等等,如X-R图、时间观察表、工程山积表、CT/TT分析等,以下为某企业的一条生产线利用该方法体系进行改善的应用。
4、残留问题点及后续改善方向通过前期的改善,无论品质、生产效率、还是在制品库存,各方面都有了很大的改善效果;但同时也找到了不足之处和残留问题点,这也为后续改善提供了方向。
现场改善的技巧

现场改善的技巧
现场改善是指在实际工作场景中进行的改善工作,旨在提高工作效率、降低成本、提升质量等方面的综合改进。
以下是一些现场改善的技巧:
1. 制定明确的目标:在开始改善之前,需要明确所要解决的问题、目标和预期结果。
这可以帮助团队在改善过程中保持聚焦,并衡量改善的成效。
2. 进行现场观察:在改善之前,对现有的工作场景进行现场观察和调研。
这样可以帮助发现问题、瓶颈和潜在的改进机会。
3. 采用持续改进的方法:现场改善需要持续不断地进行,而不是一次性的改进活动。
可以采用Kaizen(改善)方法,通过持续小步改进来不断优化工作流程。
4. 制定改进计划:根据观察结果和团队的共识,制定具体的改进计划。
计划应该包括具体的行动步骤、责任人和时间表。
5. 培养改进文化:现场改善需要全员参与和支持。
可以通过培训和认识活动来激发员工对改进的热情,并建立一个积极的改进文化。
6. 使用适当的工具和方法:在改进过程中,可以使用一些常见的工具和方法,如5S整理、流程图、因果图、统计分析等,以帮助团队更好地分析问题、找出根本原因和制定解决方案。
7. 进行试点和持续监控:在进行一项改进之前,可以选择一个小范围的试点项目来验证改进效果。
同时,要持续监控改进措施的实施情况和效果,并及时调整。
8. 推广和分享成果:在成功实施改进之后,要及时向整个团队推广和分享改进成果。
通过分享案例和经验,可以激励其他团队成员进行类似的改进工作。
9. 持续学习和改进:现场改善是一个不断学习和改进的过程。
团队成员应该时刻保持学习的心态,并定期进行回顾和反思,以寻找进一步的改进机会。
现场管理改善的七大手法(精)

现场管理改善(IE的七大手法高尚泽前言现场生产管理的重点在于持续不断的改善,通过改善现场的不良状况以使工作变得“轻松、良好、迅速、低廉、安全”,可是在我们的实际工作中有相当一部分现场管理干部和员工不知道何为改善、为什么要改善、怎么样改善,或者说没有良好的改善理念和改善意识,怎么样才能发挥员工的主观能动性呢? 基于此,本人籍由工作经验及相关参考总结出了一些改善的思维和方法,借以抛砖引玉。
1. 什么是改善?改而使之善: 使原来的状况变得更好.2. 改善是谁的责任? 什么样的人才可以从事改善?改善是每个人份内之事.工作改善其中九成,只要有常识就可以做到-------(国际劳工组织改善课课长说3. 改善的目的是什么?改善的目的------使工作更“轻松、良好、迅速、低廉、安全”.轻松------熟练的作业,疲劳的减轻; 良好------品质的维护提升;迅速------时间的缩短低廉------成本的降低;安全------伤害的防止4. 正确的改善思想a 现状必定有值得改善的地方;b 只要目前的工作稍有改善,就有所获得;c 绝对要拚弃“小小的改善又有什么用”的观念----向前看,积少成多,积沙成塔;d 本身的工作,自己是一等一的专家(工作中学习,学习后工作;5. 改善从哪里开始?改善开始于“这样做妥当吗?”的问题意识----心不在焉,视而不见,食而不知其味;小小的巧思, 可能就是改善的开始------信其当然, 顺其自然, 不惑偶然;对日常工作关心, 时时想改善, 才会触发改善的灵感;6. 改善从何处入手?容易疲劳危险而容易受伤作业环境不良布置不善错误失败多费时费力工夹检具不良耗料较多改善(IE)七大手法简述1. 防呆法(防错法: 如何避免做错事, 使工作第一次就做好的精神能够具体实现.2. 动改法(动作改善法&动作经济原则: 改善人体的动作方法,减少疲劳使工作更为舒适,更有效率,不要蛮干.3. 流程法(流程程序法: 研究探讨牵涉到几个不同的工站(序或地点的流动关系, 藉以发掘可供改善的地方;4. 五五法(5*5W1H: 凭借问的技巧来发觉改善的构想;5. 人机法(人机配合法&多动作法: 研究探讨操作人员与机械工作的过程, 藉以发觉可以改善的地方;6. 双手法(左.右手法: 研究人体在工作时的过程, 藉以发掘可以改善的地方;7. 抽查法(工作抽查法: 藉着由抽样观察察的方法迅速有效的了解问题的真象;进一步认清问题,抓住重点了解问题真象ScanDisk: Return: 0相综合运用:抽查法双手法. 人机法. 流程法对质问及已知问题探寻改善方法五五法. 防错法. 动改法实现改善目标与QC七大手法的区别:QC七大手法: 注重在问题的分析,抓重点;改善七大手法: 注重在了解问题,应用改善方法解决问题;一防呆法(防错法1. 防错法的意义: 如何去防止错误发生的方法. 將发生的可能性降至最低/杜绝其发生;2. 目的:2.1 具有即使人为疏忽也不会发生错误的构造-----不需要注意力;2.2 具有外行人来做也不会发生错误的构造-----不需要经验与直觉;2.3 具有不管是谁或何时工作都不会出错的构造-----不需要高度的技能或专门的知识;3. 功用:积极----绝不会在发生;消极----发生率降至最低;4. 进行步骤:调查发现人为疏忽----> 设定目标,制定实际计划----->调查人为疏忽的原因----->提出防错的改善方案-----> 实施改善方案-----> check 实施效果-----> 维持管制状态*技巧* 排除法: 剔除会造成问题的原因;替代法: 利用更切实的方法替代;容易化: 使作业变得更容易,更合适,集中化,使其更具共性以减低失败;异常检出: 前站虽有不良, 后站可以挑出,以降低其危害性;缓和影响: 作业失败的影响在其波及过程中, 用正确的方法使其缓和或吸收;*观念* 要求捕捉更多的鱼, 首先必须讲究捕鱼技术的传授与使用;(授之以鱼不如授之以渔: 给某人几条鱼不如教给他捕鱼的方法*引申* 以不教而战, 谓杀之. 不教其方法, 做错是主管之错*防呆法的应用*✧断根原理: 将原因从根本上排除, 使之不会发生错误;如: 下水道盖板/防护栏加高✧保险原理: 籍由2个以上的动作或依序才能完成工作;如: 冲床双按钮/保险丝使用✧相符原理: 籍用检核是否相符的动作,来防止错误的发生;如: 角度检测器/自动机转向机构✧隔离原理: 分割不同的方式,保护某些地区使其不造成危险或错误发生;如: 不良品盒的使用/材料区的划分✧曾别原理: 线条粗细,不同的颜色如: 工艺颜色/特别管制线(斑马线二动改法對”不可能”的人而言,就是”不可能”.對”可能”的人而言就是”可能”原因:他動了腦子,想出了可能的點子出來省力动作原则动改法省时动作原则动作舒适原则动作简化原则A. 有关人体运用的原则原则一: 两手同时开始及完成动作(试想独臂作业?原则二: 除休息时间外,两手不能同时空闲;原则三: 双臂的动作应尽量同时平衡对称;同时动作能使心理和生理上产生平衡的感觉,减少应用身体的应力机会,工作起来较轻松愉快.原则四: 尽可能以最低等级动作工作(动作等级分类:如下表人体动作共分五级,愈低等级的动作所耗时间愈短,愈不容易疲劳级别一二三四五运动枢纽指节手腕肘肩身区人体运动部分手指+手掌+前臂+上臂+肩动作范围手指节长度手掌长度前臂长度上臂长度上臂+身区长度速度 1 2 3 4 5 体力消耗最少少中多最多动作力量最弱弱中強最强疲劳度最小小中大最大原则五: 物体的动量尽可能运用之(比如搬动大模板尽量滑动或滚动所谓动量=质量X速度(亦可理解为冲量原则六: 运动方向应连续有规律,不宜突变.研究表明: 方向突变不但浪费时间,而且容易疲劳.原则七: 动作宜轻松有节奏.韵律节奏指: 有定期性的重复动作发生;原则八: 弹道式运动较轻快总结省力的动作及姿势,形成习惯;B. 有关工作场所布置与环境之原则原则一: 工具物料置于固定处所整理整顿的重要性: 减少寻找时间物料摆放五定: 定点、定位、定品、定型、定量原则二: 工作物料装置应依工作顺序排列并置于近处(就近原则,便于取放),使工作物料在使用过程中活动范围减至最小。
现场合理化改善技巧

现场所理化改善技巧目录一、办理与改善不雅念 (1)二、现场办理的核心位置 (2)三、现场办理合理化改善 (3)四、现场所理化改善的目标 (3)五、现场所理化改善的原则 (4)六、现场改善的意识 (5)七、现场所理化改善的实务工作 (6)八、现场所理化改善的根本技术 (7)九、现场所理化改善的根本技巧 (11)十、WORK SHOP (21)一、办理与改善不雅念办理:维持质量程度改善:使质量程度向上提升没有改善办理情况: (一)做重复改善工作(二)技术无法累积(三)程度无法提升二、现场是办理的核心位置→现场应位于办理布局的顶层→现场是所有信息的来源及改善活动的核心位置→现场办理人员必需承当达成QCD的责任→经理人员经常将现场视为掉败的来源,无视了对这些掉败的问题所应提供的协助及应负的责任。
问题:1.你的工作场地址那里?2.你如何了解现场的实情?三、现场所理化改善之屋四、现场所理化改善的目标五、现场所理化改善的原则1. 现状必定有值得改善的处所。
2. 常常为「无法做」找理由,不如以「如何做」而想方法。
3. 经常的提出「为什么?为什么?为什么?」的问题意识。
4. 只要目前的工作稍有改善,就有所获了。
5. 切勿有「小小的改善有什么用?」的不雅念。
6. 本身的工作,本身才是真正的专家。
7. 小小的巧思,可能就是改善的开始。
8. 反复的思索「有没有更好的方法?」。
9. 不要想「一步登天」,要一步步地改善。
六、现场改善的意识1.利润意识〔A〕售价 = 本钱 + 利润〔B〕利润 = 售价–本钱〔C〕本钱 = 售价–利润本钱=〔材料+人工+设备+办理〕本钱2.消除浪费〔1〕消除无效〔没有附加价值〕的动作而不是增加作业者的工作份量〔2〕消除七种浪费:等待、搬运、不良品、动作、加工、库存、制造过多〔过早〕3.提高效率〔1〕真效率与假效率〔2〕个别效率与全体效率〔3〕稼动率与可动率七、现场所理化改善的实务工作(一)专题研究,工程研究(二)提案改善(三)小组活动(四)设备点窜或更新(五)制程改善,动作改善,工作简化(六)制度改善(七)技术创新,产物创新或价值革新工作改善三层次:(一)专业层次:着重产物特性改进(二)统计层次:重整群体可信度提升(三)人性层次:人的尊重推展到事与物质量结合八、现场所理化改善的根本技术1. 最好的改善技术就是「排除」(1) 为什么这样做?(2) 有没有更好的方法?(目的与手段)(3) 能否排除…?2. 逆向思考,尝尝看(1) 倒转的设想(汽车、电视选台器)(2) 将卡车装卸货地址降低如何(3) 反向螺钉的效用(4) 今天上班的人数3. 现场改善是「合合、分分」交互运用的艺术(1) 有时将不同机能整合在一起而到达改善目的。
现场工作改善技巧

现场工作改善技巧概述现场工作是指在现场进行的具体任务和操作,如制造产品、提供服务等。
在现场工作中,提高效率、减少错误是提升生产力和质量的关键。
本文将介绍一些现场工作改善技巧,帮助你提高工作效率和质量。
核心技巧1. 现场组织与布局•合理布置现场工作环境,将必要的工具、设备和材料放置在合适位置,减少不必要的移动和搜索时间。
•利用标识和标识牌等工具,标明各种设备、工具和物料的放置位置,便于查找和归还。
•为不同的工作区域设置专门的工作台和工具,以提高工作效率。
•设计合理的工作流程,减少重复步骤和不必要的等待时间。
2. 现场标准化•建立明确的现场工作标准和要求,对各个环节的操作进行标准化。
•制定详细的工作指导书或操作流程图,使每个操作人员都能清楚执行各自的工作任务。
•定期对现场操作流程进行审核和改进,及时修订工作指导书。
3. 现场问题解决•建立一个问题反馈机制,鼓励员工提出问题和改进建议。
•设置一个问题解决小组,负责处理现场问题,并及时跟进解决方案。
•追踪和记录问题解决的结果,以便后续分析和改进。
4. 应急处理和预防措施•针对常见的现场问题,制定相应的应急处理和预防措施,以降低故障发生的可能性,并尽快恢复工作。
•定期进行安全培训,提高员工的安全意识和应急处理能力。
•建立一套事故和故障报告系统,详细记录事故和故障的原因和过程,以便进行事后分析和改进。
其他技巧1. 现场沟通与协作•建立一个良好的沟通和协作机制,确保各个岗位间的信息流畅和合作紧密。
•定期组织现场会议,交流工作进展和问题,协调解决方案。
2. 现场管理与监控•使用现场管理软件或应用程序,对现场工作进行实时监控和管理。
•建立关键指标和绩效评估体系,对现场工作进行定期评估和改进。
3. 现场培训与技能提升•定期组织现场培训课程,提高员工的技能和知识水平。
•鼓励员工参加相关的职业培训和证书考试,提升自身竞争力。
4. 现场量化分析与改进•收集和分析现场工作相关的数据,进行量化分析和评估。
施工现场的安全检查与合理化改进要点

施工现场的安全检查与合理化改进要点现代建筑施工过程中,安全问题一直是人们关注的焦点。
为了保障工人的生命安全和施工的顺利进行,施工现场的安全检查和合理化改进是至关重要的工作。
本文将从不同角度探讨施工现场安全检查与合理化改进的要点。
一、提高安全意识首先,提高安全意识是施工现场安全检查与合理化改进的首要任务。
工人们在施工过程中,要时刻保持警惕,认识到施工现场存在的潜在危险,并采取相应的措施进行预防。
管理者应加强安全培训,让工人了解施工现场的安全规定和操作规程,增强他们的安全意识和自我保护能力。
二、完善安全管理制度其次,完善安全管理制度是施工现场安全检查与合理化改进的重要环节。
管理者应制定科学、合理的安全管理制度,并通过定期检查和评估的方式,对施工现场的安全工作进行监督和指导。
同时,对违反安全规定的行为要予以严厉的处罚,形成一定的震慑力,提高工人遵守规定的意识。
三、建立有效的安全检查机制第三,建立有效的安全检查机制是施工现场安全检查与合理化改进的关键。
管理者要定期派遣专业的安全检查人员对施工现场进行全面、细致的安全检查,及时发现和解决存在的安全隐患。
同时,要建立安全检查结果的反馈机制,及时对检查结果进行整理、分析和总结,为下一步的安全改进提供参考依据。
四、加强施工现场的安全设施建设第四,加强施工现场的安全设施建设是安全检查与合理化改进的重要内容。
施工现场应配备必要的防护设备和安全装备,包括安全帽、安全鞋、防护眼镜等,保障工人的人身安全。
此外,应加强施工现场的防护措施,确保施工过程中不会对周边环境和群众造成危害。
五、健全安全应急预案第五,健全安全应急预案是施工现场安全检查与合理化改进的必备条件。
施工现场应事先制定好各种安全事故的应急预案,并进行演练和培训,提高工人对应急情况的处理能力,确保在安全事故发生时,能够迅速、有效地采取措施进行应对,最大程度地减少人员伤亡和财产损失。
六、借鉴先进施工技术与经验第六,借鉴先进施工技术与经验是施工现场安全检查与合理化改进的重要手段。
现场管理改善的七大手法
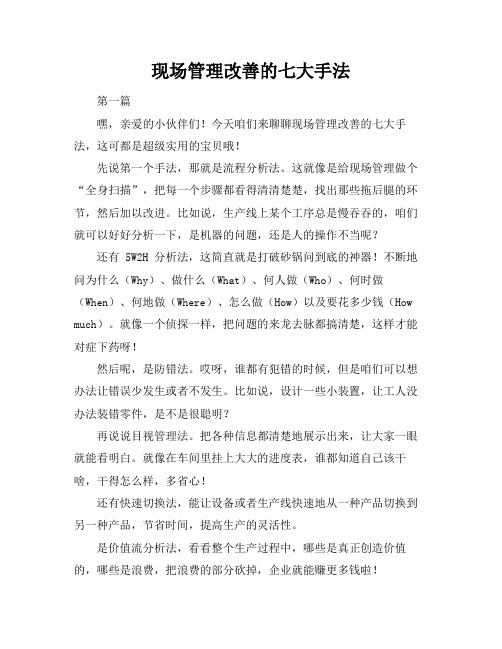
现场管理改善的七大手法第一篇嘿,亲爱的小伙伴们!今天咱们来聊聊现场管理改善的七大手法,这可都是超级实用的宝贝哦!先说第一个手法,那就是流程分析法。
这就像是给现场管理做个“全身扫描”,把每一个步骤都看得清清楚楚,找出那些拖后腿的环节,然后加以改进。
比如说,生产线上某个工序总是慢吞吞的,咱们就可以好好分析一下,是机器的问题,还是人的操作不当呢?还有 5W2H 分析法,这简直就是打破砂锅问到底的神器!不断地问为什么(Why)、做什么(What)、何人做(Who)、何时做(When)、何地做(Where)、怎么做(How)以及要花多少钱(How much)。
就像一个侦探一样,把问题的来龙去脉都搞清楚,这样才能对症下药呀!然后呢,是防错法。
哎呀,谁都有犯错的时候,但是咱们可以想办法让错误少发生或者不发生。
比如说,设计一些小装置,让工人没办法装错零件,是不是很聪明?再说说目视管理法。
把各种信息都清楚地展示出来,让大家一眼就能看明白。
就像在车间里挂上大大的进度表,谁都知道自己该干啥,干得怎么样,多省心!还有快速切换法,能让设备或者生产线快速地从一种产品切换到另一种产品,节省时间,提高生产的灵活性。
是价值流分析法,看看整个生产过程中,哪些是真正创造价值的,哪些是浪费,把浪费的部分砍掉,企业就能赚更多钱啦!小伙伴们,这七大手法学会了,现场管理就能变得井井有条,咱们一起加油吧!第二篇亲爱的朋友们,今天咱们来好好唠唠现场管理改善的七大手法,这可都是能让工作变得更轻松、更高效的妙招哦!先来讲讲流程优化法。
想象一下,咱们的工作就像一条河流,如果河道弯弯曲曲、坑坑洼洼,水流能顺畅吗?所以得把流程梳理得顺顺溜溜的,把那些阻碍的石头搬走,让工作像欢快的小溪一样流畅。
还有动作分析法,观察员工的动作,看看有没有多余的、浪费力气的动作,把这些改掉,工作就能又轻松又快啦。
头脑风暴法也很棒哦!大家坐在一起,天马行空,畅所欲言,说不定就能想出超级棒的点子来解决问题。
现场改善方案及几点建议

持续推进5S管理及现场改善活动
总结词
提高现场管理水平,优化生产环境。
详细描述
制定5S推行计划,明确责任人和实施步骤 。定期组织5S检查和评估,及时发现和整 改问题。同时,鼓励员工参与现场改善活动 ,提出改进建议,持续优化生产环境。
建立完善的质量管理体系并持续改进
总结词
详细描述
提升产品质量,提高客户满意度。
02
问题分析与定位
对反馈的问题进行深入分析,找 出问题的根本原因,为制定改进 措施提供依据。
03
改进措施实施与跟 踪
制定具体的改进措施并加以实施 ,同时对实施效果进行跟踪和评 估,确保问题得到有效解决。
质量成本的核算与控制
核算质量成本
将质量成本进行分类和核算,包括预防成本、鉴定成本、内部故障 成本和外部故障成本等,以全面了解产品质量对企业运营的影响。
配送计划制定
根据订单信息和库存状况 ,制定合理的配送计划, 确保订单及时送达的同时 避免库存积压。
配送技术升级
采用先进的配送技术,如 智能配送系统、无人机配 送等,提高配送效率和准 确性。
05
CATALOGUE
建议与展望
加强员工培训与团队建设
总结词
提升员工技能和素质,增强团队协作能力。
详细描述
制定定期的员工培训计划,包括技能培训、安全培训、质量意识培训等,提高员 工的专业技能和安全意识。同时,加强团队建设,提高员工的归属感和团队协作 能力。
供应商分级管理
根据供应商的综合能力,将供应商进行分级管理,对关键 供应商进行重点监控和合作,以实现供应链的稳定和高效 。
供应商绩效评估
定期对供应商的绩效进行评估,包括交货准时率、质量合 格率、服务响应速度等指标,以便及时调整供应商选择策 略。
生产现场改善方案

生产现场改善方案生产现场改善是指通过不断优化和改进生产现场的各种因素,以提高生产效率、降低生产成本、提升产品质量和保障员工安全等目标的一系列措施。
在生产现场改善中,我们可以采取以下方案来提升生产效率和质量。
一、标准化工作流程标准化工作流程是生产现场改善的基础,它可以确保每一项工作都按照固定的程序进行,并且能够无差错地完成。
通过标准化工作流程,可以减少工作中的浪费和瑕疵,提高生产效率和质量。
标准化工作流程的实施需要进行详细的工作流程分析和标准操作程序的制定,包括设备设置、原材料准备、工艺操作、质量检验等各个环节。
同时,还需要进行相关员工培训,确保每一位员工都能够准确地遵循标准操作程序进行工作,并且能够熟练地应对各种工作场景。
二、自动化设备的应用在现代生产中,自动化设备的应用可以大大提高生产效率和质量。
自动化设备能够取代人工操作,减少人为的误差和疲劳,提高生产效率,减少生产时间。
同时,自动化设备能够提供更高的精确度和稳定性,减少产品瑕疵率,提高产品质量。
在引入自动化设备时,需要评估投资回报率,并进行详细的设备选型和安装调试。
同时,还需要进行相关员工培训,让员工熟练掌握自动化设备的操作和维护,确保设备的正常运转。
三、现场布局的优化现场布局是生产现场改善的重要内容之一,它能够影响到生产效率和安全性。
通过优化现场布局,可以减少物料和人员的移动距离,缩短物料和信息的传递时间,提高生产效率。
同时,优化现场布局还能够提高生产现场的安全性,减少事故发生的概率。
在优化现场布局时,需要进行详细的现场调研和分析,了解现场的工作流程和各个设备之间的关系。
同时,还需要考虑人员的工作条件和安全要求,合理分配工作空间和通道。
最后,需要进行现场布局的调整和改进,确保布局的合理性和可行性。
四、供应链管理的优化供应链管理是生产现场改善的重要组成部分,它关系到物料的准时供应、库存的控制和质量的保障。
通过优化供应链管理,可以提高物料的及时性和准确性,减少物料的浪费和停工现象。
生产现场改善8个技巧

生产现场改善8个技巧1. 价值流图法(Value Stream Mapping):通过绘制价值流图,清晰地展示了整个生产流程中的价值、非价值和浪费步骤,从而可以针对性地进行改进。
通过消除浪费,提高工作流程,使得生产现场运转更加高效。
2.5S工作法:5S工作法分别是整理、整顿、清扫、清洁、素养的五个步骤。
这种方法通过减少时间浪费和杂乱无章的情况,提高工作效率,同时还有助于改善安全和质量问题。
3. 精益生产(Lean Production):精益生产是一种以减少资源浪费为中心的生产方式。
它通过去除无价值的步骤,减少库存,实现适应性和灵活性,提高效率和质量。
该方法可以通过改进生产流程,降低生产成本,并提高客户满意度。
4. 产能平衡(Capacity Balancing):产能平衡是指在生产过程中对工作站的工作负荷进行合理分配,以实现流程平衡。
通过产能平衡,可以避免生产线上的过度和不足,提高各个工作站的效率和产品质量。
5. 标准化工作(Standardized Work):标准化工作是通过制定一系列规程和标准来规范工作流程。
这种方法可以提供一种明确的、可复制的工作流程,使生产现场的工作更加高效和一致。
6.人员培训和技能提升:通过为员工提供培训和技能提升的机会,可以提高他们的生产能力和工作效率。
这包括传授新的生产技术、培养团队合作精神和解决问题的能力等。
7. 持续改进(Continuous Improvement):持续改进是指通过定期评估和改进生产工艺和流程来提高效率和质量。
这需要建立一种改进的文化,鼓励员工提出改进建议,并与他们一起制定和实施改进计划。
8.自动化和数字化技术的应用:通过引入自动化和数字化技术,可以大大提高生产效率和质量水平。
这包括使用机器人和自动化设备来替代手工操作,使用数据分析来优化生产过程,以及使用物联网技术来实现生产过程的实时监控。
通过采用以上八个技巧,可以有效改善生产现场,提高生产效率和产品质量,并最终提高企业的竞争力和市场份额。
现场改善方案及几点建议

减少不良品率
加强原材料质量控制
01
严格把控原材料质量,从源头控制产品质量。
引入精益生产理念
02
通过引入精益生产理念,优化生产工艺,减少生产过程中的浪
费。
加强员工技能培训
03
定期对员工进行技能培训,提高员工技能水平,降低操作失误
率。
提升员工技能和素质
制定完善的培训计划
根据员工岗位需求,制定完善的培训计划,提高员工技能水平。
定期组织班组长培训学习,提高 班组长的管理能力和技能水平。
实践锻炼
让班组长参与实际管理工作,通过 实践锻炼提高管理能力。
经验交流
组织班组长之间进行经验交流,分 享管理经验和方法,共同提高。
03
员工培训与激励
加强员工技能培训
岗前培训
在新员工入职时,提供岗位技能、职责等方面的 培训,确保员工具备基本的业务能力和知识。
THANKS
感谢观看
整理
定期清理现场,去除不必要的 物品,保证现场空间的有效利 用。
清扫
保持工作区域的清洁卫生,为 员工创造良好的工作环境。
素养
提高员工素质,培养良好习惯 ,形成积极向上的工作氛围。
定期检查设备维护情况
定期检查
对设备进行定期检查,及 时发现并解决潜在问题。
维护保养
按照设备保养规范进行保 养,延长设备使用寿命。
04
结论与展望
总结现场改善方案及建议
总结方案
通过对现场进行全面细致的观察和分析,我们提出以下几项 改善方案:改进生产流程、优化设备布局、提高员工技能和 意识、加强质量控制等。这些方案旨在提高生产效率、减少 浪费、降低成本并提高产品质量。
建议
如何做好生产现场改善

如何做好生产现场改善如何优化生产现场改善生产现场的关键是提高生产效率、减少浪费、改善工作环境和保证产品质量。
以下是一些方法,可以帮助您做好生产现场改善。
1. 分析生产现场:首先,对生产现场进行细致的分析,了解生产过程中存在的问题、瓶颈和不必要的浪费。
通过收集数据和观察员工操作,找出导致效率低下的因素。
2. 制定改善计划:根据分析结果,制定改善计划。
设定明确的目标,并确定实施方案。
确保计划中包括具体的时间表、责任人和预期成果。
3. 培训员工:进行员工培训是改善生产现场的重要一环。
通过培训,员工可以了解新的工作方法和操作规程,提高操作技能,增加生产效率。
建立一个培训计划,确保每位员工都能参与其中,并在改善过程中能够获得支持和协助。
4. 优化布局:优化生产现场的布局可以减少运输时间、改进物料流通和工作流程。
确保工作站之间的距离最短,物料和设备的位置合理,以便员工能够更快速地完成任务。
5. 实施精益生产:精益生产是一种流程优化方法,旨在消除浪费,提高生产效率。
通过使用精益方法,您可以识别和消除各种浪费,如库存过多、生产中断、生产过程中的瑕疵等。
6. 采用自动化技术:引入自动化技术可以提高生产效率和质量,减少人工操作错误和安全风险。
自动化设备可以取代部分重复、低效的任务,从而释放员工的时间和精力。
7. 实施持续改进:生产现场改善是一个持续的过程。
通过定期评估和改进当前的工作流程,您可以不断优化生产效率和质量。
定期召开会议,与员工合作,共同解决问题和改善流程。
8. 建立可视化管理:通过建立可视化管理系统,可以提高沟通和监控效率。
例如,使用看板系统、标识符和指示灯来显示生产进度、任务分配和质量指标等信息。
总而言之,通过认真分析、制定改善计划、培训员工、优化布局、实施精益生产和持续改进等措施,您可以优化生产现场,提高生产效率和质量,实现持续的改进。
生产现场改善是制造企业持续发展和竞争力提升的关键。
在如今激烈的市场竞争下,企业需要不断寻求提高生产效率、减少浪费、改善工作环境和保证产品质量的方法。
现场改善方案及几点建议
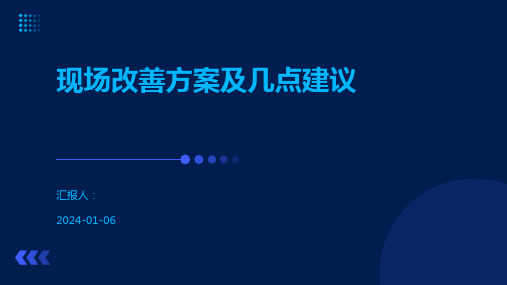
持续改进
根据评估结果和生产实际情况,对标准作业 指导书进行持续改进。
目视化管理
标识管理
对现场物品、区域、设备等进 行明确标识,方便识别。
颜色管理
利用不同颜色区分物品、区域 或状态,提高视觉效果。
图形管理
利用图表、图示等形式展示数 据、流程等信息,便于理解。
看板管理
设置看板,展示关键指标、目 标、计划等信息,提高管理效
03
设备与工装管理
设备维护保养
定期检查
制定设备检查计划,定期对设备进行全面检查,确保 设备处于良好状态。
预防性维护
实施预防性维护,定期更换易损件,清洗和润滑关键 部位,预防设备故障。
应急维修
建立应急维修机制,对突发故障进行快速响应和处理 ,尽快恢复生产。
工装夹具优化
分析和改进
对现有工装夹具进行分析,找出 存在的问题和改进点,进行优化
率。
02
人员培训与激励
培训计划
01
定期培训
制定定期培训计划,确保员工不 断更新知识和技能,提高工作效 率。
针对性培训
02
03
培训效果评估
根据员工的岗位和职责,提供针 对性的培训课程,以满足工作需 求。
对培训计划进行定期评估,了解 员工的学习成果,以便调整培训 内容和方式。
激励机制
薪酬激励
提供具有竞争力的薪酬福利,激发员工的工作积极性和创造力。
建立应急预案,组织应急演练,提高应对突发事 件的能力。
环境因素控制
识别现场环境因素,评估其对 环境的影响,制定相应的控制
措施。
加强废弃物分类、回收和处 理工作,减少对环境的污染
。
合理利用资源,降低能源消耗 ,提高能源利用效率。
现场改善方案及几点建议

合理安排生产设备、物料、工具等的布局,减少员工走动距离和时 间,提高工作效率。
加强现场沟通与协调
加强与员工的沟通与协调,及时解决现场问题,确保生产顺利进行 。
引入先进技术,提升产品质量
采用先进的生产设备和技术
引入先进的生产设备和技术,提高生产效率和 产品质量。
实施质量管理体系
建立完善的质量管理体系,确保产品质量符合 要求,提高客户满意度。
THANKS
谢谢您的观看
04
总结与展望
总结本次改善方案及建议的成果
提升生产效率
通过优化生产流程和减少浪费 ,现场改善方案成功提高了生
产效率。
提高产品质量
通过改进生产工艺和加强质量 控制,现场改善方案有助于提 高产品质量。
降低成本
通过减少原材料浪费和能源消 耗,现场改善方案有效降低了 生产成本。
增强员工参与度
通过员工参与改进过程,现场 改善方案增强了员工的归属感
通过培训和实践,提高员 工的技能水平和操作熟练 度。
培养员工安全意识
加强员工的安全培训,提 高员工的安全意识,减少 事故发生。
建立激励机制
通过建立激励机制,激发 员工的工作积极性和创造 力。
03
几点建议
加强现场管理,提高工作效率
制定合理的生产计划和流程
根据市场需求和产能,制定合理的生产计划和流程,减少生产中 的停顿和等待时间,提高工作效率。
加强质量意识培训
加强员工的质量意识培训,让员工认识到质量的重要性,提高员工对产品质量 的责任心。
加强员工培训,提高员工素质
加强技能培训
加强员工的技能培训,提高员作精神,提高团 队合作效率。
建立激励机制
现场合理化改善技巧

现场合理化改善技巧 Prepared on 22 November 2020现场合理化改善技巧目录一、管理与改善观念 (1)二、现场管理的核心位置 (2)三、现场管理合理化改善 (3)四、现场合理化改善的目标 (3)五、现场合理化改善的原则 (4)六、现场改善的意识 (5)七、现场合理化改善的实务工作 (6)八、现场合理化改善的基本技术 (7)九、现场合理化改善的基本技巧…………………………………1 1十、W O R KSHOP (2)1一、管理与改善观念管理:维持质量水平改善:使质量水平向上提升没有改善管理情况: (一)做重复改善工作(二)技术无法累积(三)水平无法提升二、现场是管理的核心位置→现场应位于管理结构的顶层→现场是所有信息的来源及改善活动的核心位置→现场管理人员必须承担达成QCD的责任→经理人员经常将现场视为失败的来源,忽视了对这些失败的问题所应提供的协助及应负的责任。
问题:1.你的工作场所在那里2.你如何了解现场的实情三、现场合理化改善之屋四、现场合理化改善的目标五、现场合理化改善的原则1. 现状必定有值得改善的地方。
2. 常常为「无法做」找理由,不如以「如何做」而想方法。
3. 经常的提出「为什么为什么为什么」的问题意识。
4. 只要目前的工作稍有改善,就有所获了。
5. 切勿有「小小的改善有什么用」的观念。
6. 本身的工作,自己才是真正的专家。
7. 小小的巧思,可能就是改善的开始。
8. 反复的思索「有没有更好的方法」。
9. 不要想「一步登天」,要一步步地改善。
六、现场改善的意识1.利润意识(A)售价 = 成本 + 利润(B)利润 = 售价–成本(C)成本 = 售价–利润成本=(材料+人工+设备+管理)成本2.消除浪费(1)消除无效(没有附加价值)的动作而不是增加作业者的工作份量(2)消除七种浪费:等待、搬运、不良品、动作、加工、库存、制造过多(过早)3.提高效率(1)真效率与假效率(2)个别效率与全体效率(3)稼动率与可动率七、现场合理化改善的实务工作(一)专题研究,项目研究(二)提案改善(三)小组活动(四)设备修改或更新(五)制程改善,动作改善,工作简化(六)制度改善(七)技术创新,产品创新或价值革新工作改善三层次:(一)专业层次:着重产品特性改良(二)统计层次:重整群体可信度提升(三)人性层次:人的尊重推展到事与物质量结合八、现场合理化改善的基本技术1. 最好的改善技术就是「排除」(1) 为什么这样做(2) 有没有更好的方法(目的与手段)(3) 能否排除…2. 逆向思考,试试看(1) 倒转的构想(汽车、电视选台器)(2) 将卡车装卸货地点降低如何(3) 反向螺钉的效用(4) 今天上班的人数3. 现场改善是「合合、分分」交互运用的艺术(1) 有时将不同机能整合在一起而达到改善目的。
对此工程的合理化改善建议

对此工程的合理化改善建议合理化改善是指通过科学管理和技术手段对工作过程中的不合理现象和问题进行分析和解决,以提高工程的效率和质量,降低成本。
在对一个工程进行合理化改善时,可以从以下几个方面进行考虑和改进:一、流程改善:1.优化工程流程,减少不必要的环节和手续,提高工程的高效率。
2.通过引入现代化的信息系统,实现工程各个环节之间的信息共享和实时沟通,减少工作中的重复和冗余,提高工作效率。
3.引入思维导图等工具,帮助工程人员更加清晰地理解工程流程和关键节点,减少操作错误和疏漏。
二、资源合理配置:1.对工程所需的人力、物力、财力等资源进行科学评估和合理配置,做到合理利用资源,避免资源浪费。
2.提前预估工程所需资源的需求量,并及时储备和采购,以确保工程进度的顺利进行。
三、标准化和模块化设计:1.设计成熟的标准化和模块化零部件,可以提高工程的生产效率,减少生产成本和工程周期。
2.标准化的设计可以有效降低施工的复杂性,减少施工中的操作错误和质量问题。
3.设计合理的组装、拆卸接口,方便零部件的拼装和更换,提高工程的维护性和可持续性。
四、技术改进:1.引入现代化的施工设备和技术,提速提效,降低人力成本。
例如,使用机械化施工设备可以减少人工翻地的工作量。
2.使用高效节能型设备和材料,减少资源消耗和环境污染。
3.引入先进的监控系统,对工程的施工过程和效果进行实时监测和控制,以提高施工质量和安全。
五、培训与激励:1.加强对工程人员的培训和素质提升,提高他们的业务水平和技术能力。
2.引入激励机制,鼓励工程人员创新和提出改进建议,促进团队合作和共享。
3.建立研究与开发机构,鼓励开展工程技术创新,提高工程质量和效益。
合理化改善的目标是提高工程的效率和质量,降低成本,为企业和社会创造更大的经济和社会效益。
而工程项目的合理化改善需要综合考虑工程的特点、资源的利用、技术的要求和现有的管理体系等多个方面的因素,并结合工程的实际情况制定相应的改善方案。
生产现场合理化建议

生产现场合理化建议
生产现场合理化建议是提高生产效率、降低成本、提升质量的重要手段。
以下是一些可行的建议:
1.优化生产流程:通过对生产流程进行全面分析,找出瓶颈环节和
浪费环节,通过改进工艺、调整设备布局、简化操作步骤等措施,提高生产效率。
2.引入自动化和智能化设备:采用自动化和智能化设备可以大幅度
提高生产效率、降低人力成本,同时减少人为因素对生产的影响。
3.推行5S管理:通过实施5S管理(整理、整顿、清扫、清洁、素
养),保持生产现场整洁有序,提高工作效率,减少安全隐患。
4.强化员工培训:定期对员工进行技能培训和安全培训,提高员工
的操作技能和工作安全意识。
5.实施质量控制:建立完善的质量控制体系,确保产品质量符合要
求,减少不良品率。
6.推进物料管理:优化物料采购、存储、领用等环节的管理,确保
物料供应及时、库存合理,降低库存成本。
7.建立信息共享平台:通过建立生产信息共享平台,实时收集和分
析生产数据,帮助管理人员及时发现问题、优化生产计划。
8.强化安全管理:建立完善的安全管理体系,确保生产现场符合安
全法规要求,保障员工的人身安全。
9.推行可视化管理:通过采用看板、标签、指示灯等可视化手段,
使生产现场信息一目了然,方便管理人员掌握生产情况。
10.鼓励员工创新:建立员工建议征集制度,鼓励员工提出改进生产
现场的建议和意见,激发员工的创新热情。
以上建议仅供参考,具体实施需结合企业实际情况进行调整和完善。
生产现场改善8个技巧

生产现场改善8个技巧生产现场改善8个技巧一.工艺流程查一查即向工艺流程要效益。
分析现有生产、工作的全过程,哪些工艺流程不合理,哪些地方出现了倒流,哪些地方出现了停放,包括储藏保管、停放状态、保管手段(如储存容器配备、货架配备、设施条件)、有无积压状态?哪些工艺路线和环节可以取消、合并、简化?寻找最佳停放条件,确定经济合理的工艺路线。
二.平面图上找一找即向平面布置要效益。
仔细检查和分析工厂平面布置图、车间平面布置图和设备平面布置图,分析作业方式和设备、设施的配置,按生产流程的流动方向,有无重复路线和倒流情况,找出不合理的部分,调整和设计一种新的布局,使生产流程在新的布置图上路线最短,配置最合理。
三.流水线上算一算即向流水线要效益。
研究流水线的节拍、每个工序的作业时间是否平衡,如果发现不平衡,就要通过裁并、简化、分解等等手法,平衡流水线。
消除因个别工序缓慢而导致的窝工和堆积。
四.动作分析测一测即向动作分析要效益。
研究工作者的动作,分析人与物的结合状态,消除多余的动作、无效动作或缓慢动作,如弯腰作业、站在凳子上作业、蹲着作业、作业场所不畅、没有适合的工位器具、人与物处于寻找状态等,通过对人的动作和环境状态的分析和测定,确定合理的操作或工作方法;探讨减少人的无效劳动,消除浪费,解决现场杂乱,实现人和物紧密结合,提高作业效率。
五.搬运时空压一压即向人机联合作业要效益。
人和设备构成了人机工程,在分析时要分析作业者和机器在同一时间内的工作情况,有无窝工、等待、无效时间,通过调整工作顺序改进人机配合,寻求合理的方法,使人的操作和机器的运转协调配合,将等待时间减少到最大限度,充分发挥人和机器的效率六.人机工程挤一挤即向人机联合作业要效益。
人和设备构成了人机工程,在分析时要分析作业者和机器在同一时间内的工作情况,有无窝工、等待、无效时间,通过调整工作顺序改进人机配合,寻求合理的方法,使人的操作和机器的运转协调配合,将等待时间减少到最大限度,充分发挥人和机器的效率。
现场管理合理化建议

现场管理合理化建议1、建议成立设计单位、监理单位、业主、施工单位四方技术专家小组,共同研究审定重要部位的施工方案,新技术、新工艺、新材料应用及创优措施。
2、加强工程项目的成本管理,编制工程成本控制计划,增收节支,定期进行成本分析,采取降低费用开支、增加盈利。
3、编制科学合理的施工计划。
项目部根据工程总进度计划及时编制安装工程分部施工进度计划,充分采用交叉施工、流水作业等手段,科学安排施工的各要素,并严格落实,减少窝工、停工等现象,提高劳动生产率。
4、项目部在满足施工进度的前提下,科学编制月、季度要料计划;加强现场材料管理工作,做到用料计划准确无误,组织不同品种、规格的材料分批进场。
材料、设备的采购要货比三家,最后确定供货单位,批量材料争取由厂家直接供应,以减少中间流通环节,降低材料采购的成本。
进场的材料的设备要减少露天堆放的时间,防止自然损耗的丢失,减小保管费用。
施工时做到限量领料,合理用料,降低材料的损耗量。
5、采用散装水泥,节省包装费用。
6、尽量在原材料或半成品的产地完成质量验收,减少材料报废率等。
在产地进行验收合格后方能运至工地。
7、加强劳动力的调度与管理,按工程进度的需要配备劳动力,对施工班组采取比较彻底的责任承包办法,工资分配同所完成的工程挂钩,提倡一专多能,减少间歇窝工及非生产用工。
8、施工机具配备要合理,选用效率高的施工机械,提高生产率及机械化施工水平。
9、选用先进合理的施工工艺及施工方法,充分利用施工场地,扩大拌制工作面,提高拌制加工效率,减少工程费用。
10、加强对过程产品质量的控制和管理,保证产品一次成优,减少返工等现象,以质量保进度,以质量降成本。
11、认真实施各项质量制度。
在施工过程中,项目部应按公司质量手册、程序文件的要求确保质量体系的有效运行,严把各项质量检验关,对卫生间、隐蔽工程等重点部位加强监督检查,将质量隐患消除在萌芽状态,避免因质量问题而造成的整改、返工损失。
12、合理组织施工,对安装工程来说,工程前期,施工配合工期长,耗工量大,后期工程量集中,工期紧、压力大,在施工安排上要及早采取相应的措施,做到边配合,边加工,有安装条件的抓紧施工,以分散施工高峰期的工作量,减轻工程后期对安装工作的压力,做到均衡施工。
- 1、下载文档前请自行甄别文档内容的完整性,平台不提供额外的编辑、内容补充、找答案等附加服务。
- 2、"仅部分预览"的文档,不可在线预览部分如存在完整性等问题,可反馈申请退款(可完整预览的文档不适用该条件!)。
- 3、如文档侵犯您的权益,请联系客服反馈,我们会尽快为您处理(人工客服工作时间:9:00-18:30)。
现场合理化改善技巧
9.2如何避免浪费
1.发现浪费 A.过剩生产浪费 B.等待时间浪费 C.运输浪费 D.加工浪费 E.存货浪费 F.动作浪费 G.产品缺陷浪费
2.消除浪费:简化、结合和消除 A.简化案例:颜色标识能够预防错误 B.结合案例:多台机器操作 C.消除案例:模具高度标准化
现场合理化改善技巧
果 (5) 维系有效的「5S」必须依赖「纪律」
现场合理化改善技巧
8.6.「5W2H」是改善的第一步棋
(1) What与Why是将目的与必要性予以明确化
(2) Where是场所
(3) When是时间、交期 (4) Who是承办人、作业员 (5) How是方法、手段
5W1H
谁(who)
(6) How many/much是 指程度,以量化来表示
(顾客满意),从而获取竞争优势和长期成
功。
现场合理化改善技巧
PDCA循环
PDCA循环是美国著名质量管理专家戴明首先提出来的,所以又叫“戴明循环法”,它反映了 质量管理活动应遵循的科学程序。PDCA是英文Plan(计划)、Do(执行)、Check(检 查)和Action(处理)的缩写,即质量管理活动要按照计划、执行、检查和处理的顺序进 行,形成从制定计划,经过组织实施、效果检查和总结提高的管理过程。 1.PDCA循环的工作程序(四个阶段、八个步骤) (1)计划阶段 第一步,分析现状,找出存在的质量问题。 第二步,分析产生质量问题的各种原因、影响因素。 第三步,找出影响质量的主要因素,针对其采取措施,以便抓住主要矛盾,解决质量问题。 第四步,针对影响质量的主要因素,制定措施,提出改进计划,并预计效果。措施计划应 具体、明确,应包括必要性(Why)、目的性(What)、地点(Where)、时间 (When)、执行(Who)、方法(How),即5W1H。 (2)执行阶段 第五步,实施措施,执行计划。 (3)检查阶段 第六步,调查事实结果,并与预期效果对比。 (4)处理阶段 第七步,总结经验,把成功的经验和失败的教训都纳入到相应的标准或制度、规定中,以 巩固成绩,防止再犯。 第八步,提出尚未解决的遗留问题,转入下一轮PDCA循环
现场合理化改善技巧
活性分析表
堆放状态
散置地上 ↓
移动为止
动作分析
需收集一处→拿正 →抬高→移走 四项作业
活性 指数
0
收集在地上
拿正→抬高→移走 三项作业
1
拿正
需要抬高→移走 二项作业
2
抬高 还要移走的作业
3
移走 物品移动的状态
4
平均活性指数= 各制程之指数合计 制程数
项 平均活 次 性指数
意义
表示工厂零件,材料散置地上的情 1 未满0.5 形普遍,用人手处理的情形很多。
现场合理化改善技巧
工作改善三层次:
1. 专业层次:着重产品特性改良 2. 统计层次:重整群体可信度提升 3. 人性层次:人的尊重推展到事与物质量结
合
现场合理化改善技巧
八、现场合理化改善的基本技术
8.1. 最好的改善技术就是「排除」 (1) 为什么这样做? (2) 有没有更好的方法?(目的与手段) (3) 能否排除…?
以节省搬运工时。
现场合理化改善技巧
9.5改进工序以增进生产力
案例: 家电装配车间原流程图 (改善前如下流程图)
缺点:组件原经过预装配成组件后, 进行包装储存等到生产线生产时再将组件配送到主线上;造成
了无效的二次包装\储存\运输和配送的浪费; 产生了无效作业,即就等于增加产品质量隐患;等 管理成本也会上升
9.3现场库存与交期改善的技巧 9.4储运、布置改善技巧
1.「一人作业」可排除堆积的 1.制程间的合理化需要「位置
浪费
管理」
2.「MRP」可解决现场库存及 2.利用「活性分析」做物料搬
交期的困扰
运总检查
3.减少库存要重估「三种法宝」 A.生产工厂是搬运的连续
A.经济订购量
B.搬运的改善始于堆放方式
拍立得相机…等。 (2) 有时却将完整的机能分开而达到改善目的。 例:寺庙的大锺,家庭用双桶瓦斯之应用。
现场合理化改善技巧
8.4.「顺序的改变」很可能就获得改善成果 (1) 咖啡的喝法 (2) 齿轮箱、换油作业(群组技术之发展) (3) 流量计检查制程的改变
现场合理化改善技巧
8.5.「5S」是基本的现场改善技术 (1) 单是整齐是不够的 (2) 「整理、整顿」是不可分的 (3) 与质量有直接关系的「清扫」 (4) 「清洁」就是维持整理、整顿、清扫的成
现场合理化改善技巧
8.2. 逆向思考,试试看 (1) 倒转的构想(汽车、电视选台器) (2) 将卡车装卸货地点降低如何 (3) 反向螺钉的效用 (4) 今天上班的人数
现场合理化改善技巧
8.3. 现场改善是「合合、分分」交互运用的艺术 (1) 有时将不同机能整合在一起而达到改善目的。 例:铅笔与橡皮擦,老花眼用的远近两用的眼镜、
现场合理化改善技巧
四、现场合理化改善的目标
改善 的目标
安全
低廉
迅速
良好
轻松
灾害、伤 害事故 之预防
职业病 的防止
成本 的抑减
时间 的缩短
质量 的维持 与提升
熟练 的移转
疲劳 的减轻
现场合理化改善技巧
五、现场合理化改善的原则
1. 现状必定有值得改善的地方。 2. 常常为「无法做」找理由,不如以「如何做」而想方法。 3. 经常的提出「为什么?为什么?为什么?」的问题意识。 4. 只要目前的工作稍有改善,就有所获了。 5. 切勿有「小小的改善有什么用?」的观念。 6. 本身的工作,自己才是真正的专家。 7. 小小的巧思,可能就是改善的开始。 8. 反复的思索「有没有更好的方法?」。 9. 不要想「一步登天」,要一步步地改善。
谁来做 为什么由他来做
(作业员) 改变人员会如何
如何做 为什么这样做 (手段) 有更好的方法吗?
作业的排除 作业的简化 制程、步骤的变更
作业的简化
How many /much
程度 要做到什么程度 须要花多少时间或金钱
现场合理化改善技巧
8.7. 应用「动作研究分析」来发现最佳方法 (1) 目视动作分析:系以观测方式而寻求动作之改善。
B.安全库存量 C.最适当订购点
C.「活性分析」可消除堆放的 浪费
备注:MRP (Material Requirement Planning 物料需求计划)是被设计并用于制造业库存管理信息处理的系 统,它解决了如何实现制造业库存管理目标——在正确的时间按正确的数量得到所需的物料这一难题。 MRP是当今众所周知的ERP的雏形,MRP与ERP的库存管理思想又源于求解制造业基本方程。 MRP 通用计算公式:净需求=毛需求+已分配量+安全库存-计划在途-实际在途-可用库存
2.直接接触到现场的事实 3.目视管理的5M (A) 作业人员 作业人员的士气如何? 如何知道作业人员的技能? (B) 机器 如何知道机器是否正在制造良好质量的产品? 机器为什么停止运转? 机器是否定期保养? (C) 材料 如何避免取料错误? 如何知道供料短缺? (D) 方法 如何知道作业人员的工作方法是否正确?
(E) 量测 生产进度达成状况
质量目标达成状况
生产目标达成状况
4.目视管理的5S 整理、整顿、清扫、清洁、素养
5.公布标准 A.作业标准 B.处理异常的步骤 C.QCD的信息及图表 D.工时信息及图表 E.机器故障信息及图表 6.设定目标及图表
最高管理阶层设定公司的长中短期目标, 并且要以目视管理落实到每一位基层员 工都认知到相关性。
现场合理化改善技巧
六、现场改善的意识
6.1利润意识 (A)售价 = 成本 + 利润 (B)利润 = 售价 – 成本 (C)成本 = 售价 – 利润 成本=(材料+人工+设备+管理)成本
现场合理化改善技巧
6.2消除浪费 (1)消除无效(没有附加价值)的动作而不
是增加作业者的工作份量 (2)消除七种浪费:
What-目的是什么 WHY-为什么这样做 Where-在那里做最恰当 When-何时做最合宜 Who-谁来做最胜任 How-什么方法最好 How many/much-做到什么程度(可量化) (6) 找出任何浪费,就记入「备忘录」
现场合理化改善技巧
九、现场合理化改善技巧
9.1目视管理
1.让问题曝光 设计「能停止的生产线」
合理
验正
TQM为一种顾客导向的管理方法,它强调有
化改
标准
善
化
效运用人力资源及运用计量方法,从不断的 改进过程着眼,以提升产品与服务品质。 TQM是一种思想观念,一套方法、手段和技
现状
巧,通过全体员工的参与、改进流程、产品、 服务和公司文化,达到在百分之百时间内生
产百分之百的合格产品,以便满足顾客需求
现场合理化改善技巧
改善后:
优点: 组件直接放在流水线的辅线上装配,可以直接消除二次包装\储存\运输和配送的 浪费; 更可避免不必要的因二次包装\周转等产生的产品质量隐患;对管理也更为 方便.
现场合理化改善技巧
2020/11/23
现场合理化改善技巧
目录
一. 管理与改善观念………………………………… 二. 现场管理的核心位置…………………………… 三. 现场管理合理化改善…………………………… 四. 现场合理化改善的目标………………………… 五. 现场合理化改善的原则………………………… 六. 现场改善的意识…………………………….…… 七. 现场合理化改善的实务工作…………………… 八. 现场合理化改善的基本技术…………………… 九. 现场合理化改善的基本技巧…………………… 一○.WORK SHOP(车间)……………………………