现场工作改善技巧实务PPT课件
合集下载
现场改善方法PPT演示课件

3)标牌是否正确?
4)是否有杂质?
5)进货周期是否适当? 6)材料浪费情况如何?
7)材料运输有差错吗? 8)加工过程正确吗?
9)材料设计正确吗? 10)质量标准合理吗?
•14
Methods
1)工艺标准合理吗? 2)工艺标准提高了吗? 3)工作方法安全吗? 4)此方法能保证质量吗? 5)此方法是否高效? 6)工序安排合理吗? 7)工艺卡是否正确? 8)温度和湿度适宜吗? 9)通风和光照良好吗? 10)前后工序衔接好吗?
•12
Machine
1)设备能力足够吗? 3)是否正确润滑? 5)是否经常出现故障? 7)设备布置是否正确? 9)设备数量是否足够?
2)能否按工艺要求加工? 4)保养情况如何? 6)工作准确度如何? 8)噪音如何? 10)运转是否正常?
•13
Material
1)数量是否足够或过多? 2)是否符合质量要求?
•
工序分析
工序分析是工序管理、搬运管理、布局研究、作业编制、顺序 规划等基础资料获取的必要手法。
步骤: 1.整理工序流程 2.工序流程中是否存在不均衡、不合理现象 3.工序顺序是否合理 4.工序流程是否顺畅,设备配置、搬运方法是否合理 5.工序中的作业是否必要,是否可以取消,是否有更好的作业方法
•15
改善的概念
全体员工在各自的工作区域内进行: 小规模的 持续的 增值的 改变以产生积极影响。
•16
改善的概念
-是否可以消除 -如果不能消除,可否减少 -如果消除和减少,会出现何种现象 -什么、有多少、怎样变好
改善使操作变得 更容易、更方便 更安全、更稳定
第五要素
第一要素
持续不断地变化 更容易地
•8
现场问题解决及改善实践PPT课件

04 现场问题解决的案例分析
案例一:生产线故障解决
总结词
迅速响应、团队协作
详细描述
生产线突发故障导致生产中断,团队迅速响应,组织技 术专家进行故障诊断,各部门协同合作,短时间内恢复 生产。
案例二:产品质量问题解决
总结词
深入分析、持续改进
详细描述
产品出现质量问题,团队深入分析原因,针对性地制定改进措施,持续跟踪改进 效果,确保问题得到根本解决。
定有效的解决方案提供依据。
PDCA循环
要点一
总结词
PDCA循环是一种科学的问题解决方法,通过计划、执行、 检查和行动四个阶段的循环,不断优化和改进管理过程。
要点二
详细描述
PDCA循环包括Plan(计划)、Do(执行)、Check(检查) 和Act(行动)四个阶段,通过不断循环这四个阶段,可以逐 步优化管理过程,提高工作效率和质量。
案例三:设备维护问题解决
总结词
预防为主、定期维护
详细描述
设备维护不当导致运行故障,团队总结经验教训,加强设备日常巡检,制定定期维护计划,提高设备运行稳定性。
05 现场改善实践的策略和技 巧
5S管理
整理
识别现场需要的和不 需要的物品,将不需 要的物品移出工作区 域。
整顿
对留下的物品进行有 序摆放,明确标识, 方便查找和使用。
鱼骨图
总结词
鱼骨图是一种用于问题分析和解决的图形化工具,通过 将问题分解为若干个相关因素,帮助人们更好地理解和 解决复杂问题。
详细描述
鱼骨图由主干和分支组成,主干表示问题,分支表示与 问题相关的因素。通过逐一分析每个因素,可以找出问 题的根本原因,并制定相应的解决方案。鱼骨图有助于 人们系统地思考问题,避免遗漏重要信息。
现场改善的方法(PPT31张)

改善的概念
1.是否可以消除, 2.是否可以消除,可否减少 3.如果消除和减少,会出现何钟现象 4.什么,有多少,怎样变好
改善使操作变得 更容易,更方便 更安全,更稳定
寻找浪费的4M方法
Man(人)
1.是否遵循标准? 2.工作效率如何? 3.有解决问题意识吗? 4.责任心怎样? 5.还需要培训吗? 6.有足够的经验吗? 7是否适合于该工作? 8.有改进意识吗? 9.人际关系怎样? 10.身体健康吗?
能力 不平衡 调 整时间长
水平面
故障 不良 品 点点停
能力 不平衡 调 整时间长 水平面 品质 不一致
点点停 缺勤
品质 不一致
计划 有误
缺勤
计划 有误
库存水平高问题被淹盖
减少库存发现问题
连续改进的基本思想
任何一个组织,在任何环境下,都有改进的 余地 改进的对象:产品与服务质量,工作效率, 业务流程,作业现场……. 贵在“连续” 全员参与
现代的定义 所有一切不增值的活动(顾客角度)
八大浪费/12种动作浪费
八大浪费
12种动作浪费 1.两手空闲 2.单手空闲 3.作业动作停止 4.动作太大 5.左右手交换 6.步行多 7.转身角度大 8.移动中变换“变态” 9.不明技巧 10.伸背动作 11.弯腰动作 12.重复/不必要的动作
操作
搬运
ECRS(四巧)技术
E: 取消 C: 合并
ECRS(四巧) 技 术
R: 重排 S: 简化
流程图
混合 原材料 混合 成形 烘烤 成形 烘烤 WIP 包装 完成品
数 据 & 计划 信息流 物流 市场需求,订 单
流程图
60分钟/100个
混合 原材料
工作改善方法及工作关系工作改善实务课件

实例
会议进行方法(问题议案)
(问题、议题)
目的(目标)
场所
时间(计划)
方法(对策内容)
担当
确认
WHAT
WHY
WHERE
WHEN
WHO
HOW
在库品数量不清(卷材,实心带)
把握在库
材料仓库
3月10~15日
1、实心带每日存库 2、卷材每日存库
付张
周肖邦
材料发单跟催
③问题意识形成的条件
★存在着目标意识,具有明确的目标,并能够掌握现状。★强烈实现目标的信念乃至意愿。★目标明确化。★目标达成期限。★掌握解决问题的步骤
2、问题的分析与解决
①问题的表达方式 要将问题用5W1H具体化◆What→什么事? Why →为什么发生◆Who →责任人是谁? Where →发生地点◆When →发生时间? ◆ How →状况、程度如何?
材料确保
各部门
3月16~20日
1、发单检讨书 2、P/O发单管理表
李王
黄
冲压机及模具确认修理
冲压不良 尺寸大
冲压部
3月16~20日
1、更换下模块 2、模仁两侧研磨各0.05mm
马师傅
肖
试模
确认尺寸 修模效果
冲压部 品管
改善的十种基本精神
1.舍去原有观念,凡事求新求变 2.不要找理由,而是找方法 3.不能满足现状。 4.改善对策愈多愈好,要因分析至少须50点。 5.错误立即改正。 6.改善就是赚钱。 7.问题未改善前不休息。 8.保持怀疑态度,连续追问5次为什么这样。 9.一个人的创意可十个人共享。 10.改善永无止境。
②问题的种类与要点
★发生型问题 己经发生的问题,重点是在用什么最佳 的方案解决。★控索型问题 精益求精,不断改善与强化。★设定型问题 即今后何去何从的问题,延续现状,可 预见不久会发生什么问题。
《现场改善手法》课件
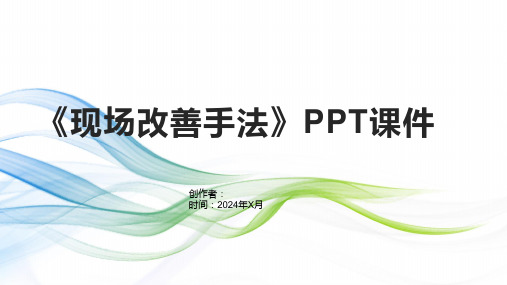
避免资源浪费
实施措施
执行改善方案,监 控效果,确保改善
效果持续
优化方案
制定针对性的改善 方案,提升生产效
率和产品质量
01 常见故障原因
分析生产中常见的故障原因,及时解决问题
02 解决方案
提出科学有效的解决方案,确保故障不再发生
03
质量控制
在生产过程中,质量控制是确保产品质量的关键。各种质量 控制方法包括质量管理体系、质量检验、质量改进等,有效 控制各个环节的质量,提升产品合格率和客户满意度。
知识回顾
在学习现场改善手法的过程中,重要的是要不断回顾已学 习的知识点,加深理解和掌握。通过知识回顾,可以更好 地应用所学的现场改善手法于实际工作中,并取得更好的 效果。
● 02
第二章 现场改善手法的基本 原理
5S原理
5S原理是现场管理的基础,包括整理、整顿、清扫、清 洁、素养。整理是根据需要保留的物品,整顿是给每个物 品找到合适的位置,清扫是保持工作环境清洁,清洁是确 保设备和工具干净,素养是养成良好的工作习惯和态度。
课程内容
现场改善手法 的定义
明确改善手法的基 本概念
现场改善手法 的应用范围
探索在不同领域中 的应用
现场改善手法 的分类
了解不同类型的改 善手法
为什么学习现场改善手法
提高工作效率
通过改善手法优化 流程,节省时间和
成本
改善工作环境
创造良好的工作氛 围,提升员工士气
减少生产成本
有效管理资源,降 低生产成本
● 03
第3章 现场改善手法的具体 应用
现场布局优化
现场布局优化是提高工作效率的重要手段,通过合理规划 生产线和设备摆放位置,可以减少生产过程中的物料移动 距离,提升生产效率和质量。规划现场布局需考虑生产流 程、人员活动及设备安置等因素,最终达到优化生产流程 的效果。
实施措施
执行改善方案,监 控效果,确保改善
效果持续
优化方案
制定针对性的改善 方案,提升生产效
率和产品质量
01 常见故障原因
分析生产中常见的故障原因,及时解决问题
02 解决方案
提出科学有效的解决方案,确保故障不再发生
03
质量控制
在生产过程中,质量控制是确保产品质量的关键。各种质量 控制方法包括质量管理体系、质量检验、质量改进等,有效 控制各个环节的质量,提升产品合格率和客户满意度。
知识回顾
在学习现场改善手法的过程中,重要的是要不断回顾已学 习的知识点,加深理解和掌握。通过知识回顾,可以更好 地应用所学的现场改善手法于实际工作中,并取得更好的 效果。
● 02
第二章 现场改善手法的基本 原理
5S原理
5S原理是现场管理的基础,包括整理、整顿、清扫、清 洁、素养。整理是根据需要保留的物品,整顿是给每个物 品找到合适的位置,清扫是保持工作环境清洁,清洁是确 保设备和工具干净,素养是养成良好的工作习惯和态度。
课程内容
现场改善手法 的定义
明确改善手法的基 本概念
现场改善手法 的应用范围
探索在不同领域中 的应用
现场改善手法 的分类
了解不同类型的改 善手法
为什么学习现场改善手法
提高工作效率
通过改善手法优化 流程,节省时间和
成本
改善工作环境
创造良好的工作氛 围,提升员工士气
减少生产成本
有效管理资源,降 低生产成本
● 03
第3章 现场改善手法的具体 应用
现场布局优化
现场布局优化是提高工作效率的重要手段,通过合理规划 生产线和设备摆放位置,可以减少生产过程中的物料移动 距离,提升生产效率和质量。规划现场布局需考虑生产流 程、人员活动及设备安置等因素,最终达到优化生产流程 的效果。
现场改善手法(PPT38页)

及至(即刻处理)的意识,就是能迅速、正 确地开展工作,遇到突发异常时不会手忙脚乱。
24
(三)“问题、方法、 协调”的意识
问题意识,就是要善于发现隐藏问题。 方法意识,就是运用合适有效的方法。 协调意识,就是需要各方面的配合。
问题意识、方法意识、协调意识,三位一体,缺一不可。
25
塑造良好的现场气氛,养成积极 的问题意识,掌握有效的改善手法, 才能充分调动和发挥人的积极作用, 形成企业进步的原动力。
37
38
每一次的加油,每一次的努力都是为 了下一 次更好 的自己 。20.12. 1020.1 2.10Th ursday , December 10, 2020 天生我材必有用,千金散尽还复来。1 1:04:55 11:04:5 511:04 12/10/2 020 11:04:55 AM 安全象只弓,不拉它就松,要想保安 全,常 把弓弦 绷。20. 12.1011 :04:551 1:04De c-2010 -Dec-2 0 得道多助失道寡助,掌控人心方位上 。11:04:5511:0 4:5511:04Thur sday , December 10, 2020 安全在于心细,事故出在麻痹。20.12. 1020.1 2.1011:04:5511 :04:55 December 10, 2020 加强自身建设,增强个人的休养。202 0年12 月10日 上午11 时4分20 .12.102 0.12.10 扩展市场,开发未来,实现现在。202 0年12 月10日 星期四 上午11 时4分55 秒11:0 4:5520. 12.10 做专业的企业,做专业的事情,让自 己专业 起来。2 020年1 2月上 午11时4 分20.1 2.1011:04December 10, 2020 时间是人类发展的空间。2020年12月1 0日星 期四11 时4分55 秒11:0 4:5510 December 2020 科学,你是国力的灵魂;同时又是社 会发展 的标志 。上午1 1时4分 55秒上 午11时 4分11:04:5520 .12.10 每天都是美好的一天,新的一天开启 。20.12. 1020.1 2.1011:0411:04 :5511:0 4:55De c-20 人生不是自发的自我发展,而是一长 串机缘 。事件 和决定 ,这些 机缘、 事件和 决定在 它们实 现的当 时是取 决于我 们的意 志的。2 020年1 2月10 日星期 四11时4 分55秒 Thursd ay , December 10, 2020 感情上的亲密,发展友谊;钱财上的 亲密, 破坏友 谊。20. 12.1020 20年12 月10日 星期四 11时4 分55秒2 0.12.10
24
(三)“问题、方法、 协调”的意识
问题意识,就是要善于发现隐藏问题。 方法意识,就是运用合适有效的方法。 协调意识,就是需要各方面的配合。
问题意识、方法意识、协调意识,三位一体,缺一不可。
25
塑造良好的现场气氛,养成积极 的问题意识,掌握有效的改善手法, 才能充分调动和发挥人的积极作用, 形成企业进步的原动力。
37
38
每一次的加油,每一次的努力都是为 了下一 次更好 的自己 。20.12. 1020.1 2.10Th ursday , December 10, 2020 天生我材必有用,千金散尽还复来。1 1:04:55 11:04:5 511:04 12/10/2 020 11:04:55 AM 安全象只弓,不拉它就松,要想保安 全,常 把弓弦 绷。20. 12.1011 :04:551 1:04De c-2010 -Dec-2 0 得道多助失道寡助,掌控人心方位上 。11:04:5511:0 4:5511:04Thur sday , December 10, 2020 安全在于心细,事故出在麻痹。20.12. 1020.1 2.1011:04:5511 :04:55 December 10, 2020 加强自身建设,增强个人的休养。202 0年12 月10日 上午11 时4分20 .12.102 0.12.10 扩展市场,开发未来,实现现在。202 0年12 月10日 星期四 上午11 时4分55 秒11:0 4:5520. 12.10 做专业的企业,做专业的事情,让自 己专业 起来。2 020年1 2月上 午11时4 分20.1 2.1011:04December 10, 2020 时间是人类发展的空间。2020年12月1 0日星 期四11 时4分55 秒11:0 4:5510 December 2020 科学,你是国力的灵魂;同时又是社 会发展 的标志 。上午1 1时4分 55秒上 午11时 4分11:04:5520 .12.10 每天都是美好的一天,新的一天开启 。20.12. 1020.1 2.1011:0411:04 :5511:0 4:55De c-20 人生不是自发的自我发展,而是一长 串机缘 。事件 和决定 ,这些 机缘、 事件和 决定在 它们实 现的当 时是取 决于我 们的意 志的。2 020年1 2月10 日星期 四11时4 分55秒 Thursd ay , December 10, 2020 感情上的亲密,发展友谊;钱财上的 亲密, 破坏友 谊。20. 12.1020 20年12 月10日 星期四 11时4 分55秒2 0.12.10
现场改善方案及几点建议ppt

通过采用精益生产理念和工具,加强 现场管理和人员培训,提高员工素质 和技能水平,实现生产过程的可控和 稳定,提高生产效率和产品质量。
实施改善方案后,生产效率和产品质 量得到了显著提升,缩短了产品交货 期,提高了客户满意度,为公司创造 了更大的经济效益和社会效益。
对未来工作的展望
进一步完善生产流程和设备布局,持续优化生产计划 和物料管理,实现生产过程的进一步优化和提升。
03
提高生产安全性
自动化设备可以提高生产安全性,减 少工伤和职业病的发生率。
改善方案三:优化现场布局
提高空间利用率
通过合理的现场布局设计,可以提高空间利用率 ,降低生产成本。
提高物流效率
通过合理的现场布局设计,可以提高物流效率, 降低物流成本。
提高员工工作效率
通过合理的现场布局设计,可以提高员工工作效 率,提高生产效益。
03
对改善方案的几点建议
加强员工培训和意识教育
总结词
详细描述
提升员工技能与素质
总结词
通过定期的内部培训、外部培训以及在线学 习,提高员工的专业技能和综合素质,增强 员工的生产效率意识。
详细描述
培养自主管理意识
推行员工自主管理,培养员工的主人翁意识 ,提高员工发现问题、解决问题的能力,降 低生产事故发生率。
深入推进精益生产理念和工具的应用,扩大精益管理 的覆盖面,提高公司的整体精益管理水平。
加强与供应商的合作与协调,推动供应商参与改善, 降低采购成本和库存成本。
加强员工的培训和教育,提高员工的素质和技能水平 ,培养一支高素质、高效率的优秀员工队伍。
THANK YOU.
2023
现场改善方案及几点建议
目录
• 引言 • 现场改善方案 • 对改善方案的几点建议 • 结论
《现场改善技巧》课件
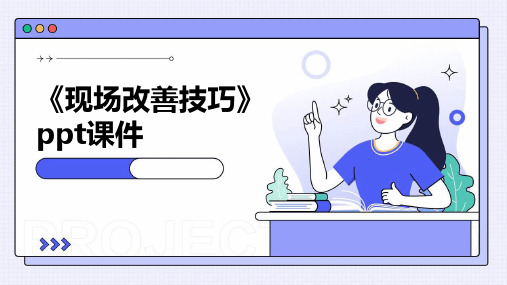
针对评估和审查中发现的问题,制定改进措施并组 织实施。
标准的更新与完善
根据改进效果和生产环境的变化,对作业标准进行 更新和完善,以保持标准的适用性和有效性。
05 目视化管理
目视化管理的定义和作用
01
目视化管理是一种利用视觉信息来管理和控制工作 场所的方法。
02
目视化管理能够提高工作效率,减少错误和浪费, 提升员工的安全意识。
认可和奖励
对积极参与改善活动的员工给予适当的认可和奖励,激发员工的积 极性。
团队合作与竞赛
组织跨部门的团队合作项目或竞赛,激发员工的团队合作精神和竞争 意识。
感谢您的观看
THANKS
作业标准的制定与实施
培训与教育
对员工进行作业标准的培训和教育,确保员工理解和 掌握标准。
监督与检查
建立监督检查机制,确保员工在实际工作中执行标准 。
反馈与改进
收集员工的反馈意见,对标准进行持续改进和优化。
作业标准的持续改进
定期评估与审查
定期对作业标准进行评估和审查,以发现存在的问 题和不足。
改进措施的实施
培养员工的问题意识
发现问题的能力
培养员工敏锐的观察力,能够及时发现现场存在的问题和改进空 间。
分析问题的能力
通过培训和引导,帮助员工学会分析问题产生的原因,并提出有 效的解决方案。
解决问题的能力
鼓励员工勇于承担责任,积极主动地解决问题,提高工作效率和 质量。
鼓励员工参与改善活动
提供培训和支持
为员工提供必要的培训和支持,使其具备参与改善活动的能力和信 心。
现场改善不仅关注单个环节的优化, 更强调整体流程的协同和整合。
现场改善的重要性
提高生产效率
标准的更新与完善
根据改进效果和生产环境的变化,对作业标准进行 更新和完善,以保持标准的适用性和有效性。
05 目视化管理
目视化管理的定义和作用
01
目视化管理是一种利用视觉信息来管理和控制工作 场所的方法。
02
目视化管理能够提高工作效率,减少错误和浪费, 提升员工的安全意识。
认可和奖励
对积极参与改善活动的员工给予适当的认可和奖励,激发员工的积 极性。
团队合作与竞赛
组织跨部门的团队合作项目或竞赛,激发员工的团队合作精神和竞争 意识。
感谢您的观看
THANKS
作业标准的制定与实施
培训与教育
对员工进行作业标准的培训和教育,确保员工理解和 掌握标准。
监督与检查
建立监督检查机制,确保员工在实际工作中执行标准 。
反馈与改进
收集员工的反馈意见,对标准进行持续改进和优化。
作业标准的持续改进
定期评估与审查
定期对作业标准进行评估和审查,以发现存在的问 题和不足。
改进措施的实施
培养员工的问题意识
发现问题的能力
培养员工敏锐的观察力,能够及时发现现场存在的问题和改进空 间。
分析问题的能力
通过培训和引导,帮助员工学会分析问题产生的原因,并提出有 效的解决方案。
解决问题的能力
鼓励员工勇于承担责任,积极主动地解决问题,提高工作效率和 质量。
鼓励员工参与改善活动
提供培训和支持
为员工提供必要的培训和支持,使其具备参与改善活动的能力和信 心。
现场改善不仅关注单个环节的优化, 更强调整体流程的协同和整合。
现场改善的重要性
提高生产效率
现场工作改善技巧实务课件
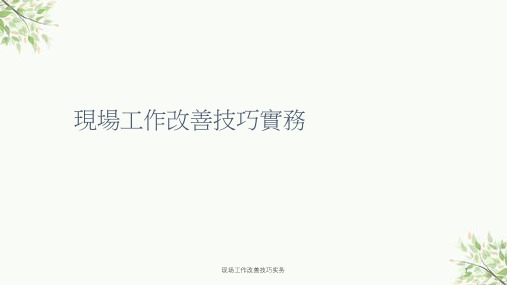
聽開的內容分配 • 3.運用科學方法,避免主觀臆測 • 4.深入檢討分析,做改善構思
现场工作改善技巧实务
17
二.科學化的稼動率分析
工作抽樣 • 1.在現場進行實際抽測,並記錄實況 --真實數據 --由大量數據歸納提煉出真相 • 2.以統計訓為背景的數據分析法 -從有效樣本推測目群體 --符合統計分析原則 --注意被觀測樣本的有效性/代表性
现场工作改善技巧实务
6
• 3.由於效率低之工作方法之引起 --作業場所問題 --夾工具/輔助工具問題 --作業方法本身問題 --生產線不平衡 • 4.由於管理不良所引起 --停工待料損失工時 --機台故障損失工時 --製程安排不銜接的待工 --員工意願低落
现场工作改善技巧实务
7
六.提昇現場生產力績效的策略方向
现场工作改善技巧实务
18
•分析出真相(比率)找出重點 -先從最大的浪費下手 • 4.依重點再分析原因,找出改善對策 --特性要因圖的理念 --生產技術面/作業方法面/製造管理面的
改善對策
现场工作改善技巧实务
19
• 2.欄位說明 --A.觀測對象
作業員或機台 --B觀測[事象]內容
例如[實際作業中][準備作業中][人停閑][人不在] --C觀測時刻
注意[隨機]的統計要求
-B採取Snap Reading觀測紀錄
依照觀測紀錄表之[事象]區分 必要時問清楚[稼動]內容及[非稼動]原因 用正號做紀錄
现场工作改善技巧实务
23
五.稼動率分析的結果—問題重點實例
區分 觀測事項
比率%
稼動中 有效作業
29
準備作業
20
不良重制重修 14
非稼動 休息
4
(作業員 如廁/喝茶
现场工作改善技巧实务
17
二.科學化的稼動率分析
工作抽樣 • 1.在現場進行實際抽測,並記錄實況 --真實數據 --由大量數據歸納提煉出真相 • 2.以統計訓為背景的數據分析法 -從有效樣本推測目群體 --符合統計分析原則 --注意被觀測樣本的有效性/代表性
现场工作改善技巧实务
6
• 3.由於效率低之工作方法之引起 --作業場所問題 --夾工具/輔助工具問題 --作業方法本身問題 --生產線不平衡 • 4.由於管理不良所引起 --停工待料損失工時 --機台故障損失工時 --製程安排不銜接的待工 --員工意願低落
现场工作改善技巧实务
7
六.提昇現場生產力績效的策略方向
现场工作改善技巧实务
18
•分析出真相(比率)找出重點 -先從最大的浪費下手 • 4.依重點再分析原因,找出改善對策 --特性要因圖的理念 --生產技術面/作業方法面/製造管理面的
改善對策
现场工作改善技巧实务
19
• 2.欄位說明 --A.觀測對象
作業員或機台 --B觀測[事象]內容
例如[實際作業中][準備作業中][人停閑][人不在] --C觀測時刻
注意[隨機]的統計要求
-B採取Snap Reading觀測紀錄
依照觀測紀錄表之[事象]區分 必要時問清楚[稼動]內容及[非稼動]原因 用正號做紀錄
现场工作改善技巧实务
23
五.稼動率分析的結果—問題重點實例
區分 觀測事項
比率%
稼動中 有效作業
29
準備作業
20
不良重制重修 14
非稼動 休息
4
(作業員 如廁/喝茶
现场改善的技巧PPT课件
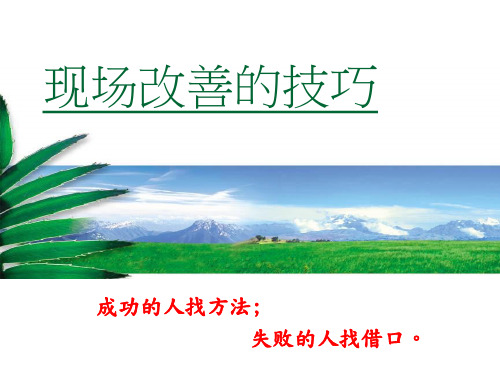
DF.SHEN
从根本解决问题
于是,请下山的和尚买回杀虫剂,从此, 每天找蛀孔灌乐将虫杀死,数日后,再开始 扫落叶,竟不到半天,便扫得一清二爽,而 有余暇可以练武功了.
其实,根干的问题并不复杂,只要耐着 性子找出来,解决之道也不难,因为,问题 本身就是答案.
从根本解决问题
一旦根干问题解决,枝叶问题自然消失,否 则,若为枝叶问题迷惑,则困在其中,永无平息 之時.
2.成本 (1).工时减少了吗? (2).经费节约了吗? (3).效率提升? (4).生产力如何? (5).材料成本? (6).动力成本? (7).损耗成本?
现场改善的出发点--QCDS
DF.SHEN
3.交期 (1).交期准确 (2).工期缩短 (3).程序简化 (4).插单,急单,小单多 (5).数量 (6).产量的衰退
束. 4. 发言内容不宜冗长,次数则愈多愈佳.
DF.SHEN
1.3.脑力激荡法的思考方向
替代:能否由他顶来替代?替代后是否与 原来一样?价格是否更低廉?
重组:作业可以重组?重组后效率会提高? 不必要的动作或移动是否减少.
交换:可否以其他方法,程序来代换?绩效 是否会因而改善?
DF.SHEN
DF.SHEN
(3).为何要如此做? (4).为何要用目前的 机器,人来做这种工作?
6. How (如何)
(1).如何使方法,手段更 简單? (2).情形到底是如何? (3).如何使作业方法简 化,以减少劳力,降低成本? (4).要如何来做?
DF.SHEN
4.防呆法
(一)防呆法又称防错法,防愚法,其义即是 防止止愚笨的人做错事.亦即,连愚笨的 人也不会做错事的设计方法. 狭義:如何设计一个东西,使错误绝不 会发生. 广義:如何设计一个东西,而使错误发 生的机会减至最低的程度.
现场工作改善技巧(PPT37张)

ME IE PE QA
MPM
PD(20%)
MPM
PD(20%)
SDCA vs. PDCA
SDCA 的目的:標準化和穩定現有的製程。 PDCA 的目的:提升製程的水準。
改 進 處 置 計 劃 處 置 維 持 標準化 A C 執 行 查 核 S D 執 行
A C
P D
查 核
PDCA循環圖 計劃執行查核處置
減少等待 減少間接作業
提 高 作 業 率
改善佈置
提高設備 使用率
減少故障
徹底點檢 迅速修理 減少更換準備作業時間 減少更換次數 改善準備作業
現場管理的五大金科玉律
• Five golden rules of gemba management---在 現場推行“現場改善”時,最實用的提醒 劑︰
– – – – – 當有問題發生時“要先去現場”。 檢查現場。 當場採取暫行處置措施。 發掘原因並排除。 標準化以防止再發。
现场工作改善技巧
----TT.HO---2007.10.03
3個主要的改善活動
• 合理化/標準化 • 各種維持廠房環境的6S工作
‧1.整理(seiri) ‧2.整頓(seiton) ‧3.清掃(seiso) ‧4.清潔(seikesn) ‧5.素養(sitswke) ‧6.安全(safety)
*消除浪費
工作人員控制範圍內之無效時間。
-VE 的方法。 C部分-IE , QC 的方法。 D/E部分-PAC 的方法。
工作改善技巧
• • • • 剔除-改善的最高原則 合併-節省辦事手續 重排-工作程序運作有序 簡化-節省人力時間設備
剔除
1.剔除所有可能的作業,步驟或動作(包括身體、足、手臂或 眼 )。 2.剔除工作中的不規律性,使動作成為自發性,並使各種物 品置放於固定地點。 3.剔除以手做為持物工具的工作。 4.剔除不方便或不正常的動作。 5.剔除需使用肌力才能維持的姿勢。 6.剔除必須使用肌力的工作,而以動力工具取代之。 7.剔除必須克服動量的工作。 8.剔除危險的工作。 9.剔除所有不必要的閒置時間。
- 1、下载文档前请自行甄别文档内容的完整性,平台不提供额外的编辑、内容补充、找答案等附加服务。
- 2、"仅部分预览"的文档,不可在线预览部分如存在完整性等问题,可反馈申请退款(可完整预览的文档不适用该条件!)。
- 3、如文档侵犯您的权益,请联系客服反馈,我们会尽快为您处理(人工客服工作时间:9:00-18:30)。
• What • Where • When • Who • Why • How
六.工作改善的著眼法則
• 1.刪除 • 2.少量化 • 3.多量化 • 4.合併 • 5.重組 • 6.替代 • 7.簡化 • 8.改換
第三章 運用稼動率分析技巧 進行改善
一.稼動率分析的背景
• 1.一目了然,掌握問題重點,不在枝節打轉. • 2.以現場實況調查為依據,分析調查操作/
四.總製造時間的構成與生產力的關係
製造基本必要時間
A
由於設計或規格問題而發生之附
B
加時間
由於低效率生產設備或工作方法
C
的浪費時間
由於製造管理問題發生之浪費
D
時間
由於作業員問題而發生之無效
時間
E
五.現場生產力浪費的根源
• 1.由於設計/工程技術面所引發 --不必要的過剩功能 --超過必要嚴格的加工/檢驗標準 --不宜的作業標準 --不必要的多餘加工 • 2.由於製程品質不良所引發 --設備/作業員問題 --作業標準問題 --製程品質問題
平常以3-10天為原則 觀測次數要約略符合統計需求
-C預測觀測,決定[事項]紀錄之具體定義
稼動/非稼動之分 必須具體,又簡潔宜觀測/紀錄
-D確定觀測次數及觀測時間/方式
例如:每天幾次,多久一次 再修訂觀測次數
-E備妥觀測次數表格
• 進行現場實地觀測 -A設定觀測時刻/觀測人/觀測路線
注意[隨機]的統計要求
第四章 運用程序分析與搬運 改善技巧
一.整體製程的非效率因素
• 1.非直接有效的稼動 --準備作業 --不良重制重修
• 2.阻礙製程進行的勞動作業 --檢驗 --搬運
• 3.阻礙製程進行的停閑 --停滯 --儲存
二.程序圖所用程序符號
•
操作/加工
•
檢驗
•
•
搬運
•
停滯
•
儲存
1.操作加工
聽開的內容分配 • 3.運用科學方法,避免主觀臆測 • 4.深入檢討分析,做改善構思
二.科學化的稼動率分析
工作抽樣 • 1.在現場進行實際抽測,並記錄實況 --真實數據 --由大量數據歸納提煉出真相 • 2.以統計訓為背景的數據分析法 -從有效樣本推測目群體 --符合統計分析原則 --注意被觀測樣本的有效性/代表性
• 1.消除浪費 • 2.提高生產力 • 3.直接降低成本 —例如必要的多餘設計 • 4.縮短製程時間 —更短的交期,更具競爭力 • 5.減少摸索時間 • 6.消除無效疲勞作業 —包括危險的作業 —無效的動作 • 7.更高的成就感/高報酬
三.工作改善六大步驟
• 1.選擇改善主題對象 • 2.觀測及紀錄現狀事實 • 3.檢討現狀問題點 • 4.提出改善構想方法 • 5.建立實施計劃 • 6.推動維護新方法
• 3.由於效率低之工作方法之引起 --作業場所問題 --夾工具/輔助工具問題 --作業方法本身問題 --生產線不平衡 • 4.由於管理不良所引起 --停工待料損失工時 --機台故障損失工時 --製程安排不銜接的待工 --員工意願低落
六.提昇現場生產力績效的策略方向
• 1.從設計階段就考慮生產力 --更少的用料來組成 --更少的製造途程 • 2.從生產技術面提昇生產力 --更有效的作業方法 --模具/夾具/輔助工具設計/配置 --減少製程不良 --縮短準備作業工時
-B採取Snap Reading觀測紀錄
依照觀測紀錄表之[事象]區分 必要時問清楚[稼動]內容及[非稼動]原因 用正號做紀錄
五.稼動率分析的結果—問題重點實例
區分 觀測事項
比率%
稼動中 有效作業
29
準備作業
20
不良重制重修 14
非稼動 休息
4
(作業員 如廁/喝茶
5
原因) 交談
5
非稼動 停工待料
11
現場工作改善技巧實務
第一章 生產力與工作方法
一.工廠經營與生產力的關聯
• 製造業首先以生產力作評估 --整體產銷生產力 --現場生產力
• 生產力直接表現在績效上 --現場績效 --個人績效
• 附加價值資源 --附加價值是員工收入報酬的源泉 --所有企業的目的都是在創造附加價值
二.生產力的評估
• 1.高精密/高效率生產設備 --資方的努力 • 2.高技術/高效能的工作方法 ---生產技術幕僚/基層主管的努力 • 3.周詳嚴密的管理 --生管/物管等管理幕僚的貢獻 --基層主管也要參與 • 4.肯配合有幹勁的員工 --而且要適任/有能力
• 3.從工作方法面提昇生產力 --更少的細部作業程序 --更佳的人機作業配合 --更直接有效作業方法 --生產線平衡 • 從製造管理面提昇 --MRP物料管理方法,較少停工待料 --有效的生產排程及管制,使製程銜接良好 --預防保養機制,減少機台故障待工損失
第二章 現場工作改善的基本 理念
一.工作改善的目標
四.工作改善基本理念
• 1.五個 WHY的深入分析 --深層追求 --細分化(科學管理第一要素) • 2.以事實為基準 --要有具體證據 --至少要紀錄事實細節 • 3.從合理的懷疑下手 • 4.必須有具體的改善對策 -不能只是抱怨(或反映事實)而已 • 5.追求永遠的再改善
五.從5W1H質問法產生構想
大多一日一張表 --D觀測次數紀錄
三.稼動率調查紀錄表
1.基本格式
現象 8:15 9:25 10:10 11:20 1:30 2:35 3:15 4:25 合計 作業 準備 搬運 休息 檢驗 不在 故障
四.工作抽樣的進行程序
• 1.事前的準備 -A決定觀測對象
注意其代表性
-B決定觀測次數及進行時間
ห้องสมุดไป่ตู้
• 分析出真相(比率)找出重點 -先從最大的浪費下手 • 4.依重點再分析原因,找出改善對策 --特性要因圖的理念 --生產技術面/作業方法面/製造管理面的改
善對策
• 2.欄位說明 --A.觀測對象
作業員或機台 --B觀測[事象]內容
例如[實際作業中][準備作業中][人停閑][人不在] --C觀測時刻
(非稼動 機台故障
4
作業時
間)
六.問題的重點
• 1.有效的真正作業,才占29%(大警訊) --作業員仍很忙(稼動率占68%)
但實際生產力很低
--準備作業占20%,為何? --不良重修占14%,為何? • 2.作業員的責任很小,已夠努力 --如廁/休息僅各站5%左右
--已是世界性寬放水準之內
• 3.停工待料占11%,為何?
六.工作改善的著眼法則
• 1.刪除 • 2.少量化 • 3.多量化 • 4.合併 • 5.重組 • 6.替代 • 7.簡化 • 8.改換
第三章 運用稼動率分析技巧 進行改善
一.稼動率分析的背景
• 1.一目了然,掌握問題重點,不在枝節打轉. • 2.以現場實況調查為依據,分析調查操作/
四.總製造時間的構成與生產力的關係
製造基本必要時間
A
由於設計或規格問題而發生之附
B
加時間
由於低效率生產設備或工作方法
C
的浪費時間
由於製造管理問題發生之浪費
D
時間
由於作業員問題而發生之無效
時間
E
五.現場生產力浪費的根源
• 1.由於設計/工程技術面所引發 --不必要的過剩功能 --超過必要嚴格的加工/檢驗標準 --不宜的作業標準 --不必要的多餘加工 • 2.由於製程品質不良所引發 --設備/作業員問題 --作業標準問題 --製程品質問題
平常以3-10天為原則 觀測次數要約略符合統計需求
-C預測觀測,決定[事項]紀錄之具體定義
稼動/非稼動之分 必須具體,又簡潔宜觀測/紀錄
-D確定觀測次數及觀測時間/方式
例如:每天幾次,多久一次 再修訂觀測次數
-E備妥觀測次數表格
• 進行現場實地觀測 -A設定觀測時刻/觀測人/觀測路線
注意[隨機]的統計要求
第四章 運用程序分析與搬運 改善技巧
一.整體製程的非效率因素
• 1.非直接有效的稼動 --準備作業 --不良重制重修
• 2.阻礙製程進行的勞動作業 --檢驗 --搬運
• 3.阻礙製程進行的停閑 --停滯 --儲存
二.程序圖所用程序符號
•
操作/加工
•
檢驗
•
•
搬運
•
停滯
•
儲存
1.操作加工
聽開的內容分配 • 3.運用科學方法,避免主觀臆測 • 4.深入檢討分析,做改善構思
二.科學化的稼動率分析
工作抽樣 • 1.在現場進行實際抽測,並記錄實況 --真實數據 --由大量數據歸納提煉出真相 • 2.以統計訓為背景的數據分析法 -從有效樣本推測目群體 --符合統計分析原則 --注意被觀測樣本的有效性/代表性
• 1.消除浪費 • 2.提高生產力 • 3.直接降低成本 —例如必要的多餘設計 • 4.縮短製程時間 —更短的交期,更具競爭力 • 5.減少摸索時間 • 6.消除無效疲勞作業 —包括危險的作業 —無效的動作 • 7.更高的成就感/高報酬
三.工作改善六大步驟
• 1.選擇改善主題對象 • 2.觀測及紀錄現狀事實 • 3.檢討現狀問題點 • 4.提出改善構想方法 • 5.建立實施計劃 • 6.推動維護新方法
• 3.由於效率低之工作方法之引起 --作業場所問題 --夾工具/輔助工具問題 --作業方法本身問題 --生產線不平衡 • 4.由於管理不良所引起 --停工待料損失工時 --機台故障損失工時 --製程安排不銜接的待工 --員工意願低落
六.提昇現場生產力績效的策略方向
• 1.從設計階段就考慮生產力 --更少的用料來組成 --更少的製造途程 • 2.從生產技術面提昇生產力 --更有效的作業方法 --模具/夾具/輔助工具設計/配置 --減少製程不良 --縮短準備作業工時
-B採取Snap Reading觀測紀錄
依照觀測紀錄表之[事象]區分 必要時問清楚[稼動]內容及[非稼動]原因 用正號做紀錄
五.稼動率分析的結果—問題重點實例
區分 觀測事項
比率%
稼動中 有效作業
29
準備作業
20
不良重制重修 14
非稼動 休息
4
(作業員 如廁/喝茶
5
原因) 交談
5
非稼動 停工待料
11
現場工作改善技巧實務
第一章 生產力與工作方法
一.工廠經營與生產力的關聯
• 製造業首先以生產力作評估 --整體產銷生產力 --現場生產力
• 生產力直接表現在績效上 --現場績效 --個人績效
• 附加價值資源 --附加價值是員工收入報酬的源泉 --所有企業的目的都是在創造附加價值
二.生產力的評估
• 1.高精密/高效率生產設備 --資方的努力 • 2.高技術/高效能的工作方法 ---生產技術幕僚/基層主管的努力 • 3.周詳嚴密的管理 --生管/物管等管理幕僚的貢獻 --基層主管也要參與 • 4.肯配合有幹勁的員工 --而且要適任/有能力
• 3.從工作方法面提昇生產力 --更少的細部作業程序 --更佳的人機作業配合 --更直接有效作業方法 --生產線平衡 • 從製造管理面提昇 --MRP物料管理方法,較少停工待料 --有效的生產排程及管制,使製程銜接良好 --預防保養機制,減少機台故障待工損失
第二章 現場工作改善的基本 理念
一.工作改善的目標
四.工作改善基本理念
• 1.五個 WHY的深入分析 --深層追求 --細分化(科學管理第一要素) • 2.以事實為基準 --要有具體證據 --至少要紀錄事實細節 • 3.從合理的懷疑下手 • 4.必須有具體的改善對策 -不能只是抱怨(或反映事實)而已 • 5.追求永遠的再改善
五.從5W1H質問法產生構想
大多一日一張表 --D觀測次數紀錄
三.稼動率調查紀錄表
1.基本格式
現象 8:15 9:25 10:10 11:20 1:30 2:35 3:15 4:25 合計 作業 準備 搬運 休息 檢驗 不在 故障
四.工作抽樣的進行程序
• 1.事前的準備 -A決定觀測對象
注意其代表性
-B決定觀測次數及進行時間
ห้องสมุดไป่ตู้
• 分析出真相(比率)找出重點 -先從最大的浪費下手 • 4.依重點再分析原因,找出改善對策 --特性要因圖的理念 --生產技術面/作業方法面/製造管理面的改
善對策
• 2.欄位說明 --A.觀測對象
作業員或機台 --B觀測[事象]內容
例如[實際作業中][準備作業中][人停閑][人不在] --C觀測時刻
(非稼動 機台故障
4
作業時
間)
六.問題的重點
• 1.有效的真正作業,才占29%(大警訊) --作業員仍很忙(稼動率占68%)
但實際生產力很低
--準備作業占20%,為何? --不良重修占14%,為何? • 2.作業員的責任很小,已夠努力 --如廁/休息僅各站5%左右
--已是世界性寬放水準之內
• 3.停工待料占11%,為何?