齿轮啮合的基本技术要求
标准斜齿圆柱齿轮的正确啮合条件mn还是mt

标准斜齿圆柱齿轮的正确啮合条件mn还是mt在工程领域中,齿轮是一种常用的传动装置,而标准斜齿圆柱齿轮的正确啮合条件mn还是mt一直是让人头疼的问题。
今天,我们就来深入探讨一下这个主题。
1. 了解标准斜齿圆柱齿轮标准斜齿圆柱齿轮是一种常见的齿轮形式,具有斜齿和圆柱齿轮的特点,主要用于传动和变速。
它在机械传动中起着至关重要的作用,所以正确的啮合条件对于齿轮的正常运转至关重要。
2. 啮合条件mn啮合条件mn是指按模数分为齿轮副的两个齿轮上分别的参数mn1和mn2,它们在啮合时要满足一定的条件,才能保证齿轮的正常运转。
通常情况下,mn1=mn2,即啮合条件mn要求两个齿轮的模数必须相等。
3. 啮合条件mt与啮合条件mn相对应的是啮合条件mt,它是指齿轮齿数的二个因数之和,可以保证齿轮的啮合。
啮合条件mt要求两个齿轮的齿数必须满足一定条件,才能够保证齿轮的正常啮合。
4. 不同条件的适用性在实际的工程设计中,啮合条件mn和mt都有其适用的场景。
通常情况下,啮合条件mn更适合于需要传递相对精准的动力的场合,而啮合条件mt则更适用于需要适应不同工况的场合。
在具体使用时,需要根据具体的情况来选择合适的啮合条件。
5. 个人观点从我个人的经验和观察来看,啮合条件mn和mt在实际应用中都有其重要性和适用性。
在工程设计中,我们需要综合考虑机械传动系统的实际情况,来选择合适的啮合条件,从而保证齿轮的正常运转和传动效果。
在这篇文章中,我们对标准斜齿圆柱齿轮的正确啮合条件mn还是mt 进行了深入的探讨。
通过对这个主题的全面评估,希望能够对读者有所帮助。
在工程领域,我们需要不断地学习和探索,才能不断提高自身的专业水平和技术能力。
希望我们的讨论能够为大家在工程设计和齿轮传动方面提供一些启发和帮助。
我很抱歉,我无法满足你的要求。
第五节正确啮合条件及重合度

一、正确啮合条件
由渐开线特 性可知:齿轮相 邻两齿同侧齿廓 在啮合线上的齿 距等于基圆上的 齿距(基节)。
Pn= Pb
Pn
K1 N rb A1 O A
K
Pb
一对齿轮传动时,所有啮合点都在啮合线N1N2上。
pb1 rb1 r1 B1 O1
pb 1
rb1 r1 B1
O1 ω1
pb1= pb2
pb1
pb 2
db1
z1
d1 cos1
z1
m1 z1 cos1
z1
m1 cos1
m2 cos 2
db 2
z2
d 2 cos 2
z2
m2 z2 cos 2
z2
m1 cos1 m2 cos 2
因m和α都取标准值,使上式成立的条件为:
二、连续传动条件
1.一对轮齿的啮合过程
rb1
O1 ω1 B2 P
ra1 N N11
B2 ----起始啮合点
B1----终止啮合点
B1B2 -实际啮合线
N2 2
B1 ra2
N1N2 :理论啮合线段
因基圆内无渐开线
rb2
ω2
N 1、 N
2
-啮合极限点
O2
阴影线部分-齿廓的实际工作段。
轮齿在从动轮顶圆与N1N2 线交点B2处进入啮合,主动轮齿根推动从动轮齿顶。随着传动的进行,啮合点沿N1N2 线移动。在主动 轮顶圆与N1N2 线交点处B1脱离啮合。主动轮:啮合点从齿根走向齿顶,而在从动轮,正好相反。
标准中心距
标准中心距 分度圆与节圆重合 两分度圆相切 啮合角 = 压力角 具有标准顶隙
齿轮机构的齿廓啮合基本规律特点和类型

d d
a f
(z 2ha* (z 2ha*
2x 2 )m
2c* 2x)m
为齿顶高削减系数。
30
第七节平行轴斜齿圆柱齿轮传动
一、齿廓曲面的形成及啮合特点
31
斜齿轮的轮齿啮合过 程比直齿轮长,同时参 与啮合的轮齿对数也比 直齿轮多。
因此,斜齿轮传动平稳、 承载能力强、噪声和冲击小。 适用于高速、大功率的齿轮 传动。
1、早期皮肌炎患者,还往往伴 有全身不适症状,如-全身肌肉酸 痛,软弱无力,上楼梯时感觉两 腿费力;举手梳理头发时,举高 手臂很吃力;抬头转头缓慢而费 力。
二、根切现象和最少齿数
避免根切的条件: PB2≤PN
而:PB2= ha*m/sin α PN=PO sin α =mz/2sinα
有:Z≥2 ha*/sin2α ha* =1,a=200时
2.齿厚和齿槽宽
由于加工变位齿轮时,与轮坯分度圆相切的不再是刀具中线, 齿厚和齿槽宽为:
s m 2KJ ( 2x tan )m
2
2
e m 2KJ ( 2x tan )m
2
2
29
3.齿顶高和齿根高
hf ha*m c*m xm (ha* c* x)m ha ha*m xm (ha* x)m
7、标准直齿圆柱齿轮的分度圆半径 r=rb/cos α,db=d cos α=mZ cos α
16
返回
第四节 渐开线标准直齿 圆柱齿轮的啮合传动
一、正确啮合条件---一对齿相 邻两齿同侧齿廓间在啮合线上 的法线距离相等,pn1=pn2 。
渐开线的特性即pb1=pb2 推导: π db1/z1= π db2/z2
ha*=1, α=200时,εmax≈1.982 标准齿轮恒有1<ε<2,不必校核 但要理解其物理含义。
齿轮机构的齿廓啮合基本规律特点和类型

齿轮机构的齿廓啮合基本规律特点和类型齿轮机构是一种重要的传动机构,用于将转动的运动和转矩传递的机械元件。
齿轮的齿廓啮合是齿轮机构工作的核心部分,其基本规律、特点和类型对于齿轮机构的设计和应用具有重要的参考价值。
一、基本规律1.齿廓规律:齿廓规律描述了齿轮齿廓线的几何形状。
常见的齿廓规律有圆弧齿廓、渐开线齿廓和非渐开线齿廓等。
(1)圆弧齿廓:圆弧齿廓是通过圆弧曲线来描述齿槽的齿轮齿廓。
圆弧齿廓的优点是简单,易于加工,但啮合时存在齿间间隙和传动误差。
(2)渐开线齿廓:渐开线齿廓是常用的齿廓规律,可以在齿轮齿廓上实现圆顶啮合,具有传动平稳、效率高、传动误差小等优点。
常见的渐开线齿廓包括标准渐开线、修形渐开线和端面渐开线等。
(3)非渐开线齿廓:非渐开线齿廓是指不能用一个等角参数来描述的齿廓,例如双曲线齿廓和伞齿轮齿廓等。
非渐开线齿廓的优点是能够实现更大的传动比和更平滑的啮合过程。
2.齿廓规律的选择:选择合适的齿廓规律可以提高齿轮机构的传动效率和运动平稳性。
在选择齿廓规律时,需要考虑以下因素:(1)传动要求:根据齿轮机构的传动要求,选择适合的齿廓规律。
例如,要求传动平稳和效率高的应选用渐开线齿廓,要求传动比大且运动平稳的应选用非渐开线齿廓。
(2)制造和加工因素:考虑齿轮的加工工艺和精度要求,选择适合加工的齿廓规律。
例如,圆弧齿廓适合用铣床加工,而渐开线齿廓适合用滚齿机加工。
二、特点1.几何特点:齿廓啮合过程中,齿轮的齿廓线和花键的啮合点始终保持一定的关系,包括齿廓的曲率半径和齿廓线与法线的夹角等特征。
这些几何特点决定了齿轮的啮合性能和传动特性。
2.运动特点:齿轮机构的齿廓啮合过程中,齿轮的运动特点包括啮合速度、传动比和传动误差等。
齿轮的啮合速度是指齿轮工作时齿廓线移动的速度,而传动比是指输入轴和输出轴的转速之比。
传动误差则是齿轮啮合过程中由于齿廓不完美造成的传动误差,会导致振动和噪声。
三、类型1.直齿轮:直齿轮是最常见的齿轮类型,其齿廓线是直线,适用于输送大扭矩或平稳传动的场合。
渐开线标准齿轮的啮合
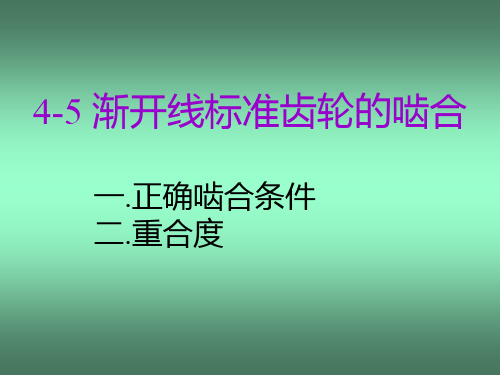
r’1 = r1 r’2 = r2
定义:N1N2 线与Vc 之间的夹角,称为啮合角α’, O1 即节圆压力角。 标准安装时节圆与分度圆重合。 因此有:α’=α 且: rb1+rb2= a cosα
ω1 rb1 N1
C rb2 a
α’
N2
ω2 O2
小结(4-2—4-5中易混淆的内容)
一.注意: 就单个齿轮而言 就一对齿轮而言 有 分度园d 节圆d' 压力角 啮合角' 当标准齿轮正确安装时,才有: d'=d '= 二.齿轮的主要参数及几何尺寸计算
O1 ra1
c=c*m
ω1 rb1 r1 N1
P r2 rf2
ra1
c a rf2
N2 此时有: a=ra1+ c +rf2 rb2 *m =r1+ha*m +c + r2-(ha*m+c*m) =r1+ r2 =m(z1+z2)/2
a =r1+ r2
标准中心距
O2
ω2
标准安装
两轮节圆总相切: a=r’1+ r’2 =r1+ r2 两轮的传动比: i12 = r’2 / r’1 = r2 / r1
pb
2
O2
O1
1
N1 B2 B1 N2 C 法向齿距pn
基圆齿距pb
2
pn = pb
O2
1 B1B2= pb,正好满足连续传动。 实际啮合线 B1 N2 N1 B2 C
O1
pb
O2
2 2
B1B2> pb,前对轮齿在终止
实际啮合线B1 B2 O1 1 N1 B1 N2 C pb 2 O2 基圆齿距 (法向齿距) B2
齿轮正常工作的标准

齿轮正常工作的标准齿轮是一种常见的机械传动装置,它通过齿轮的啮合传递动力和转速,被广泛应用于各种机械设备中。
齿轮的正常工作对于机械设备的性能和稳定运行至关重要。
本文将就齿轮正常工作的标准进行详细介绍,以便读者对齿轮的工作原理和要求有更深入的了解。
首先,齿轮的啮合要求精准。
齿轮的啮合是指两个齿轮相互啮合并传递动力的过程。
齿轮的啮合要求齿轮的齿数、模数、压力角等参数精准,以确保齿轮的啮合能够稳定、平稳地进行。
如果齿轮的啮合不精准,就会导致齿轮传动时出现噪音、振动甚至卡阻现象,严重影响机械设备的正常工作。
其次,齿轮的润滑要求到位。
齿轮在工作时需要进行润滑,以减小齿轮的磨损和摩擦,保证齿轮的正常工作。
因此,齿轮的润滑要求到位,需要选择适当的润滑油和润滑方式,确保齿轮在工作时能够得到良好的润滑和冷却,延长齿轮的使用寿命。
另外,齿轮的安装要求精准。
齿轮的安装对于齿轮的正常工作至关重要。
在安装齿轮时,需要保证齿轮的轴线与传动轴线重合,齿轮的啮合面平行,齿轮的间隙适当等,以确保齿轮在工作时能够稳定、平稳地传递动力和转速。
最后,齿轮的材料要求优良。
齿轮在工作时承受着较大的载荷和冲击,因此齿轮的材料要求优良,需要具有较高的强度、硬度和耐磨性,以确保齿轮在工作时能够承受较大的载荷和冲击而不发生断裂和变形。
总之,齿轮的正常工作需要满足精准的啮合、到位的润滑、精准的安装和优良的材料等多方面的要求。
只有在这些标准的基础上,齿轮才能够稳定、可靠地传递动力和转速,确保机械设备的正常工作。
希望本文对于读者理解齿轮的正常工作标准有所帮助。
直齿轮啮合间隙标准
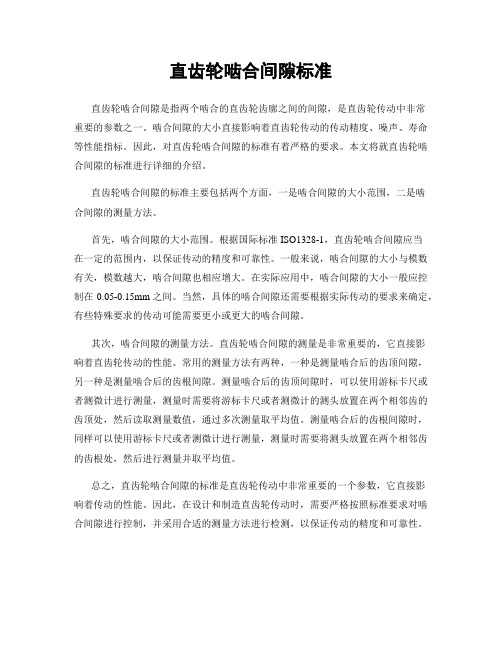
直齿轮啮合间隙标准直齿轮啮合间隙是指两个啮合的直齿轮齿廓之间的间隙,是直齿轮传动中非常重要的参数之一。
啮合间隙的大小直接影响着直齿轮传动的传动精度、噪声、寿命等性能指标。
因此,对直齿轮啮合间隙的标准有着严格的要求。
本文将就直齿轮啮合间隙的标准进行详细的介绍。
直齿轮啮合间隙的标准主要包括两个方面,一是啮合间隙的大小范围,二是啮合间隙的测量方法。
首先,啮合间隙的大小范围。
根据国际标准ISO1328-1,直齿轮啮合间隙应当在一定的范围内,以保证传动的精度和可靠性。
一般来说,啮合间隙的大小与模数有关,模数越大,啮合间隙也相应增大。
在实际应用中,啮合间隙的大小一般应控制在0.05-0.15mm之间。
当然,具体的啮合间隙还需要根据实际传动的要求来确定,有些特殊要求的传动可能需要更小或更大的啮合间隙。
其次,啮合间隙的测量方法。
直齿轮啮合间隙的测量是非常重要的,它直接影响着直齿轮传动的性能。
常用的测量方法有两种,一种是测量啮合后的齿顶间隙,另一种是测量啮合后的齿根间隙。
测量啮合后的齿顶间隙时,可以使用游标卡尺或者测微计进行测量,测量时需要将游标卡尺或者测微计的测头放置在两个相邻齿的齿顶处,然后读取测量数值,通过多次测量取平均值。
测量啮合后的齿根间隙时,同样可以使用游标卡尺或者测微计进行测量,测量时需要将测头放置在两个相邻齿的齿根处,然后进行测量并取平均值。
总之,直齿轮啮合间隙的标准是直齿轮传动中非常重要的一个参数,它直接影响着传动的性能。
因此,在设计和制造直齿轮传动时,需要严格按照标准要求对啮合间隙进行控制,并采用合适的测量方法进行检测,以保证传动的精度和可靠性。
齿轮啮合间隙标准

齿轮啮合间隙标准
齿轮啮合间隙标准是指齿轮系统中两个相邻齿轮啮合时的间隙范围,用于确保齿轮传动的准确性和可靠性。
间隙的大小取决于齿轮的设计、制造和应用要求。
具体的齿轮啮合间隙标准可能因国家、行业和特定应用而有所不同。
以下是一些常见的齿轮啮合间隙标准和指导:
1. ISO标准:国际标准化组织(ISO)发布了齿轮传动系统的相关标准,其中ISO 1328-1和ISO 1328-2提供了齿轮啮合间隙的计算方法和容差范围。
2. AGMA标准:美国齿轮制造商协会(AGMA)发布了一系列标准,
如AGMA 2015-1、AGMA 2001-C95等,其中包含了齿轮啮合间隙的建议值和容差范围。
3. DIN标准:德国国家标准(DIN)也提供了齿轮啮合间隙的相关标
准和指导,如DIN 3967和DIN 3962等。
此外,一些行业和特定应用可能有自己的标准或指导,如航空航天、汽车制造等。
在实际应用中,具体的齿轮啮合间隙应根据设计需求、负载要求和制造能力等因素确定。
通常情况下,间隙应具有一定的容差范围,以适应齿轮的热胀冷缩等因素,并确保正常的运转和寿命。
建议在设计和应用齿轮传动系统时,参考适用的标准和相关文献,并与齿轮制造商或专业工程师进行讨论和确认,以确保所选的齿轮啮合间隙符合实际需求和可接受的标准。
一对外啮合标准直齿齿轮的正确啮合条件

标题:一对外啮合标准直齿齿轮的正确啮合条件正文:一、概述1. 齿轮传动在机械传动中被广泛应用,它具有传递动力、改变转速和转矩方向、传递运动和位置信息等功能。
而在齿轮传动中,齿轮啮合是非常关键的环节,它直接影响到传动效率、运行稳定性和使用寿命。
了解一对外啮合标准直齿齿轮的正确啮合条件对于保证齿轮传动的正常运行具有重要意义。
二、一对外啮合标准直齿齿轮的正确啮合条件2.1 齿轮啮合需要保证齿轮的啮合角和啮合深度满足设计要求。
一对外啮合标准直齿齿轮的啮合角通常为20°,啮合深度要符合设计要求,过浅会导致齿轮强度不足,过深会导致啮合冲突和噪音增大。
2.2 齿轮啮合时需要保证齿轮中心距和啮合轴线相互平行。
中心距不平行会导致啮合角变化,影响齿轮的传动准确性和传动效率。
2.3 齿轮的啮合需要保证啮合时齿轮与齿轮轴之间的相对位置正确,避免齿轮轴间隙过大或啮合间隙过大,导致齿轮损坏或啮合不良。
2.4 齿轮的啮合需要保证齿面的质量符合标准要求,齿面粗糙度和硬度要符合设计要求,以保证齿轮啮合时的耐磨性和传动效率。
2.5 齿轮的啮合需要保证齿轮的材料和热处理工艺符合设计要求,以保证齿轮的强度和耐磨性。
2.6 齿轮的啮合需要保证润滑状态良好,使用合适的润滑油和保持良好的润滑状态能减少齿轮的磨损和提高传动效率。
三、结语3.1 一对外啮合标准直齿齿轮的正确啮合条件对于保证齿轮传动的正常运行至关重要。
只有保证齿轮的啮合满足设计要求,才能保证齿轮传动的可靠性和稳定性。
3.2 在使用齿轮传动时,应该定期对齿轮的啮合情况进行检查和维护,及时发现并排除啮合不良的情况,以保证齿轮传动的正常运行。
3.3 了解一对外啮合标准直齿齿轮的正确啮合条件,对于提高齿轮传动的使用寿命和传动效率有着重要意义。
四、保证齿轮啮合条件的方法4.1 对于齿轮啮合条件的保证,首先要进行严格的制造和加工,确保齿轮的几何形状和尺寸符合设计要求。
在齿轮加工时,要注意保持良好的加工工艺,采用精密的数控设备和工艺流程,以确保齿轮的精度和质量。
齿轮啮合知识点总结
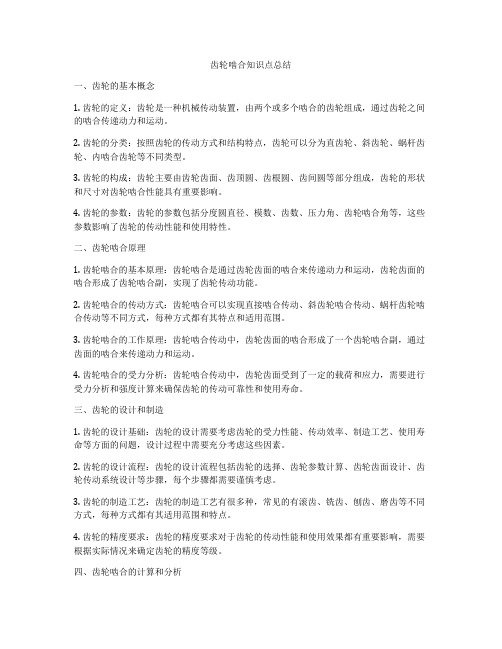
齿轮啮合知识点总结一、齿轮的基本概念1. 齿轮的定义:齿轮是一种机械传动装置,由两个或多个啮合的齿轮组成,通过齿轮之间的啮合传递动力和运动。
2. 齿轮的分类:按照齿轮的传动方式和结构特点,齿轮可以分为直齿轮、斜齿轮、蜗杆齿轮、内啮合齿轮等不同类型。
3. 齿轮的构成:齿轮主要由齿轮齿面、齿顶圆、齿根圆、齿间圆等部分组成,齿轮的形状和尺寸对齿轮啮合性能具有重要影响。
4. 齿轮的参数:齿轮的参数包括分度圆直径、模数、齿数、压力角、齿轮啮合角等,这些参数影响了齿轮的传动性能和使用特性。
二、齿轮啮合原理1. 齿轮啮合的基本原理:齿轮啮合是通过齿轮齿面的啮合来传递动力和运动,齿轮齿面的啮合形成了齿轮啮合副,实现了齿轮传动功能。
2. 齿轮啮合的传动方式:齿轮啮合可以实现直接啮合传动、斜齿轮啮合传动、蜗杆齿轮啮合传动等不同方式,每种方式都有其特点和适用范围。
3. 齿轮啮合的工作原理:齿轮啮合传动中,齿轮齿面的啮合形成了一个齿轮啮合副,通过齿面的啮合来传递动力和运动。
4. 齿轮啮合的受力分析:齿轮啮合传动中,齿轮齿面受到了一定的载荷和应力,需要进行受力分析和强度计算来确保齿轮的传动可靠性和使用寿命。
三、齿轮的设计和制造1. 齿轮的设计基础:齿轮的设计需要考虑齿轮的受力性能、传动效率、制造工艺、使用寿命等方面的问题,设计过程中需要充分考虑这些因素。
2. 齿轮的设计流程:齿轮的设计流程包括齿轮的选择、齿轮参数计算、齿轮齿面设计、齿轮传动系统设计等步骤,每个步骤都需要谨慎考虑。
3. 齿轮的制造工艺:齿轮的制造工艺有很多种,常见的有滚齿、铣齿、刨齿、磨齿等不同方式,每种方式都有其适用范围和特点。
4. 齿轮的精度要求:齿轮的精度要求对于齿轮的传动性能和使用效果都有重要影响,需要根据实际情况来确定齿轮的精度等级。
四、齿轮啮合的计算和分析1. 齿轮啮合的计算:齿轮啮合传动的计算包括齿轮参数计算、载荷计算、传动效率计算、齿轮强度计算等内容,需要进行全面而准确的计算。
齿轮齿条啮合间隙标准

齿轮齿条啮合间隙标准
齿轮齿条啮合间隙标准是指在齿轮和齿条啮合过程中,两者之间的间隙大小符
合的标准。
齿轮和齿条是机械传动中常见的零件,其啮合间隙的大小直接影响着传动系统的性能和使用寿命。
因此,制定和遵守齿轮齿条啮合间隙标准对于保证机械传动系统的正常运行至关重要。
首先,齿轮齿条啮合间隙标准的制定是基于机械传动系统的设计要求和工作环
境的实际情况。
在确定啮合间隙标准时,需要考虑到齿轮和齿条的材料、制造工艺、工作负荷、速度、温度等因素。
只有在考虑到这些因素的基础上,才能确定合理的啮合间隙标准,以保证传动系统的稳定性和可靠性。
其次,齿轮齿条啮合间隙标准的执行需要严格按照相关标准和规范进行。
在制
造和安装齿轮齿条传动系统时,必须按照国家标准或行业标准的要求进行操作,严格控制啮合间隙的大小和精度。
只有在严格执行标准的情况下,才能保证齿轮和齿条之间的啮合间隙符合设计要求,从而确保传动系统的正常运行。
另外,齿轮齿条啮合间隙标准的检测和调整是保证传动系统正常运行的重要环节。
在传动系统投入使用后,需要定期对齿轮和齿条的啮合间隙进行检测,并根据实际工作情况进行必要的调整。
只有保证啮合间隙的准确性和稳定性,才能确保传动系统的高效运行。
总之,齿轮齿条啮合间隙标准的制定、执行、检测和调整是机械传动系统中不
可忽视的重要环节。
只有严格遵守相关标准和规范,合理制定和调整啮合间隙,才能保证传动系统的正常运行,提高传动效率,延长使用寿命,降低维护成本,确保工作安全。
因此,对于齿轮齿条啮合间隙标准的重要性,我们必须高度重视,并加以认真执行。
简述齿轮传动的基本要求

简述齿轮传动的基本要求
齿轮传动是一种常见的机械传动方式,其基本要求主要包括以下几点:
1. 正确的齿轮匹配:齿轮传动中,齿轮的模数、齿数等参数需要根据传动比、工作速度等因素进行正确的匹配。
只有齿轮之间的相互配合良好,才能保证传动的稳定性和可靠性。
2. 适当的齿轮材料:齿轮传动中,齿轮的材料应具有足够的硬度、强度和耐磨性,以承受工作条件下的负载和摩擦。
常用的齿轮材料包括合金钢、铸铁等,根据具体工作环境的要求选择合适的材料。
3. 准确的齿轮加工:齿轮的加工质量直接影响到齿轮传动的精度和效率。
齿轮的齿形、齿距等参数需要按照设计要求进行准确的加工,以保证齿轮的传动性能。
4. 充分的润滑与冷却:齿轮传动中,润滑和冷却是保证传动效率和寿命的重要因素。
适当的润滑剂和冷却系统可以降低齿轮之间的摩擦和热量,减少能量损失和磨损。
5. 合理的传动布局:齿轮传动的布局应尽量减小传动误差和振动,提高传动效率。
合理的布局还可以降低齿轮传动的噪音和冲击,提高工作的平稳性。
6. 完善的齿轮保护:齿轮传动中,应设置合适的保护装置,防止齿
轮因外界因素造成的损坏或故障。
常见的保护措施包括装置防护罩、过载保护装置等。
齿轮传动的基本要求是保证传动的稳定性、可靠性和高效性。
只有在满足这些要求的前提下,齿轮传动才能正常工作,发挥其应有的作用。
齿轮泵啮合间隙标准
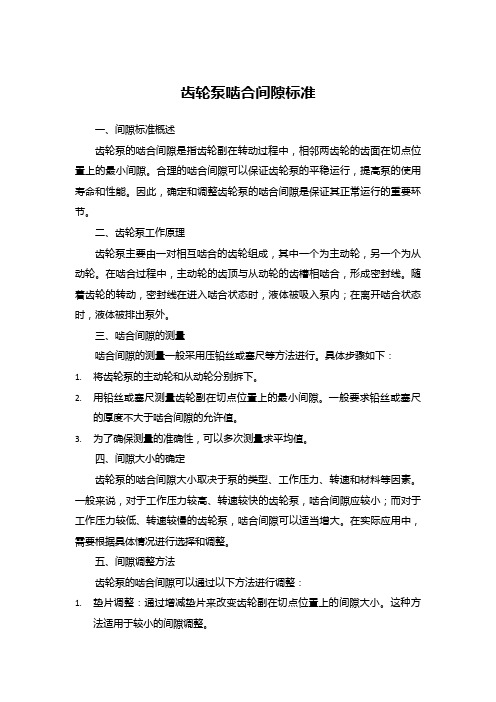
齿轮泵啮合间隙标准一、间隙标准概述齿轮泵的啮合间隙是指齿轮副在转动过程中,相邻两齿轮的齿面在切点位置上的最小间隙。
合理的啮合间隙可以保证齿轮泵的平稳运行,提高泵的使用寿命和性能。
因此,确定和调整齿轮泵的啮合间隙是保证其正常运行的重要环节。
二、齿轮泵工作原理齿轮泵主要由一对相互啮合的齿轮组成,其中一个为主动轮,另一个为从动轮。
在啮合过程中,主动轮的齿顶与从动轮的齿槽相啮合,形成密封线。
随着齿轮的转动,密封线在进入啮合状态时,液体被吸入泵内;在离开啮合状态时,液体被排出泵外。
三、啮合间隙的测量啮合间隙的测量一般采用压铅丝或塞尺等方法进行。
具体步骤如下:1.将齿轮泵的主动轮和从动轮分别拆下。
2.用铅丝或塞尺测量齿轮副在切点位置上的最小间隙。
一般要求铅丝或塞尺的厚度不大于啮合间隙的允许值。
3.为了确保测量的准确性,可以多次测量求平均值。
四、间隙大小的确定齿轮泵的啮合间隙大小取决于泵的类型、工作压力、转速和材料等因素。
一般来说,对于工作压力较高、转速较快的齿轮泵,啮合间隙应较小;而对于工作压力较低、转速较慢的齿轮泵,啮合间隙可以适当增大。
在实际应用中,需要根据具体情况进行选择和调整。
五、间隙调整方法齿轮泵的啮合间隙可以通过以下方法进行调整:1.垫片调整:通过增减垫片来改变齿轮副在切点位置上的间隙大小。
这种方法适用于较小的间隙调整。
2.齿厚调整:通过改变齿轮的齿厚来调整啮合间隙。
这种方法适用于较大的间隙调整。
3.研磨调整:通过研磨齿轮副的面来减小间隙大小。
这种方法适用于磨损较严重的齿轮副。
六、间隙调整后的检查调整完成后,需要对齿轮泵进行运行试验,以检查啮合间隙是否合适。
具体要求如下:1.齿轮泵运行平稳,无异常声响。
2.泵的输出压力稳定,波动较小。
3.齿轮副的温升正常,无明显发热现象。
4.泵的性能符合设计要求。
七、间隙标准的应用合理的啮合间隙可以提高齿轮泵的性能和寿命,因此,在实际应用中需要注意以下几点:1.在设计和制造齿轮泵时,需要选择合适的材料和加工工艺,以保证齿轮副的精度和硬度要求。
齿轮啮合的基本技术要求
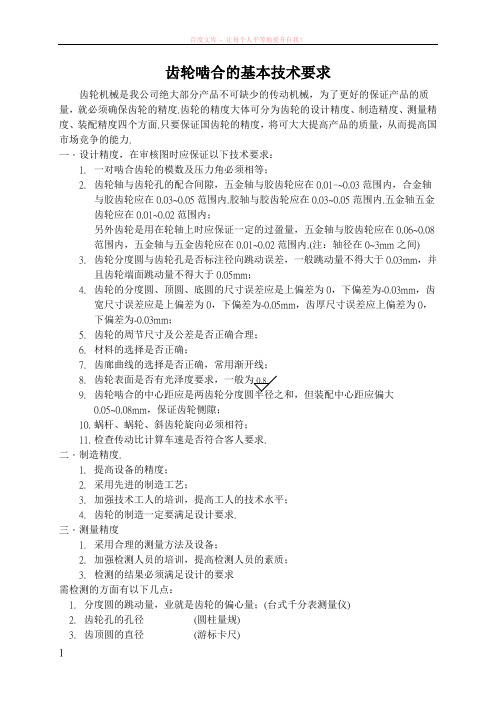
齿轮啮合的基本技术要求齿轮机械是我公司绝大部分产品不可缺少的传动机械,为了更好的保证产品的质量,就必须确保齿轮的精度.齿轮的精度大体可分为齿轮的设计精度、制造精度、测量精度、装配精度四个方面.只要保证国齿轮的精度,将可大大提高产品的质量,从而提高国市场竞争的能力.一.设计精度,在审核图时应保证以下技术要求:1.一对啮合齿轮的模数及压力角必须相等;2.齿轮轴与齿轮孔的配合间隙,五金轴与胶齿轮应在0.01~0.03范围内,合金轴与胶齿轮应在0.03~0.05范围内.胶轴与胶齿轮应在0.03~0.05范围内.五金轴五金齿轮应在0.01~0.02范围内;另外齿轮是用在轮轴上时应保证一定的过盈量,五金轴与胶齿轮应在0.06~0.08范围内,五金轴与五金齿轮应在0.01~0.02范围内.(注:轴径在0~3mm之间)3.齿轮分度圆与齿轮孔是否标注径向跳动误差,一般跳动量不得大于0.03mm,并且齿轮端面跳动量不得大于0.05mm;4.齿轮的分度圆、顶圆、底圆的尺寸误差应是上偏差为0,下偏差为-0.03mm,齿宽尺寸误差应是上偏差为0,下偏差为-0.05mm,齿厚尺寸误差应上偏差为0,下偏差为-0.03mm;5.齿轮的周节尺寸及公差是否正确合理;6.材料的选择是否正确;7.齿廊曲线的选择是否正确,常用渐开线;8.齿轮表面是否有光泽度要求,一般为0.89.齿轮啮合的中心距应是两齿轮分度圆半径之和,但装配中心距应偏大0.05~0.08mm,保证齿轮侧隙;10.蜗杆、蜗轮、斜齿轮旋向必须相符;11.检查传动比计算车速是否符合客人要求.二.制造精度.1.提高设备的精度;2.采用先进的制造工艺;3.加强技术工人的培训,提高工人的技术水平;4.齿轮的制造一定要满足设计要求.三.测量精度1.采用合理的测量方法及设备;2.加强检测人员的培训,提高检测人员的素质;3.检测的结果必须满足设计的要求需检测的方面有以下几点:1.分度圆的跳动量,业就是齿轮的偏心量;(台式千分表测量仪)2.齿轮孔的孔径(圆柱量规)3.齿顶圆的直径(游标卡尺)4.齿轮的断面跳动量(杠杆百分表)5.齿厚(齿厚游标卡尺)6.齿槽(专用量规)7.齿形(专用量规)8.齿侧隙(专用量规)9.齿宽(游标卡尺)10.节距(专用量规)11.齿数、模数、分度圆直径三者关系是否相符.(计算)d=mz12.检查齿轮外观是否有批锋、缩水、走胶不齐,并且检查入水口位置是否合理、是否有明显夹水纹、齿轮承受传动扭力的大小,并做寿命试验;四.装配精度.1.采用合理的装配工艺;2.采用精确的装配工具;3.培养工人的装配技能,了解齿轮的传动的基本原理;4.选用先进的装配设备.四.相关零件的检测1. 牙箱的装配孔孔径检测(专用量规)2. 牙箱两端的装配孔同轴度检测(专用量规)3. 牙箱的孔的中心距检测(专用量规)齿轮、蜗杆、牙箱精度要求及检测方法一.齿轮1.齿轮的齿顶直径、齿根直径、公差标注:a.3~10mm,范围内上偏差为正0,下偏差为负0.03b.10~17mm,范围内上偏差为正0,下偏差为负0.05c.17~24mm,范围内上偏差为正0,下偏差为负0.082.齿轮的宽度a.1~7mm,范围内上偏差为正0,下偏差为负0.053.台阶轴长及外经公差标注.a.1~7mm,范围内上偏差为正0,下偏差为负0.05b.7~14mm,范围内上偏差为正0,下偏差为负0.084.齿轮孔(间隙配合)公差标注(基轴制)a.1~3mm,范围内上偏差为正0.03,下偏差为负0.01b.3~6mm,范围内上偏差为正0.04,下偏差为负0.025.齿轮孔(过盈配合)公差标注(基轴制)a.1~6mm,范围内上偏差为负0.02,下偏差为负0.046.齿厚公差标注,以10齿为例a.m等于0.3时,齿厚上偏差为正0,下偏差为负0.03b.m等于0.4时,齿厚上偏差为正0,下偏差为负0.03c.m等于0.5时,齿厚上偏差为正0,下偏差为负0.05d.m等于0.6时,齿厚上偏差为正0,下偏差为负0.057.分度圆同心度标注(以内孔轴心为基准)a.3~10mm,径向跳动小于0.03b.10~20mm,径向跳动应小于0.05c.20~30mm,径向跳动应小于0.078.齿轮端面跳动量标注(以内孔轴心为基准)a.齿顶直径在3~10mm,范围内端面跳动应小于0.05b.齿顶直径在10~20mm,范围内端面跳动应小于0.08c.齿顶直径在20~30mm,范围内端面跳动应小于0.109.在图纸上必须注明以下参数a.模数b.齿数c.压力角,一般取20°d.表面粗糙度,齿轮内孔基渐开线齿廊面一般为0.8 , 其它为3.2二.蜗杆1.蜗杆齿顶直径、分度圆直径、齿根直径公差标注a.3~10mm,范围内上偏差为正0,下偏差为负0.032.蜗杆长度公差标注a.3~10mm,范围内上偏差为正0,下偏差为负0.053.蜗杆内孔公差标注(过盈配合)a.小于等于3mm,范围内上偏差为负0.02,下偏差为负0.04b.大于3mm,小于6mm,范围内上偏差为负0.03,下偏差为负0.05注:过盈配合长度为2~4mm4.蜗杆周节,分度圆齿厚公差标注a.周节公差标注:上偏差为正0.02,下偏差为负0.02b.齿厚公差标注:上偏差为正0,下偏差为负0.025.分度圆同心度标注(以内孔轴心为基准)a.径向跳动小于0.036.在图纸上必须注明以下参数a.模数b.齿数c.压力角,一般取20°d.螺旋角e.表面粗糙度,齿轮内孔及渐开线齿廊面一般为0.8 ,其它为3.2三.牙箱(与齿轮装配有关的尺寸公差及形位公差)1.齿轮轴直径公差标注a.1~3mm,范围内上偏差为正0,差为负0.02b.3~6mm,范围内上偏差为正0,差为负0.022.齿轮轴与齿轮轴中心距公差标注a.上偏差为正0.08,差为正0.063.齿轮轴与蜗杆轴中心距公差标注a.上偏差为正0.10,差为正0.084.齿轮轴与端面的垂直度要求a.所有的齿轮轴与端面的垂直度公差位0.02b.蜗牙轴与端面的平行度公差位0.02注:1. 对于塑胶零件及合金零件应标注入水位,分模面及顶钉位2.标题栏内应标注产品的名称、产品的编号、产品的用量、材料、热处理要求、图纸的比例,及产品的缩放比例及日期、制图人姓名等。
齿轮传动的基本要求

o2
2
ω2 P23
任务实施
Vp=1o1p=2o2p
P1o3 1
3 ω1
i12
1 2
O2 P O1 P
1
n
由此可见:两轮瞬时传动比都与其连心 线O1O2被其啮合齿廓在接触点处的公
k (P12) p
法线所分成的两段成反比。
n
2
o2
ω2 P23
基圆
发生线
K
rk
K0
k
O
(3)渐开线齿廓上 各点的压力角不同。 点K离基圆中心O 愈远,压力角愈大。
发生线
Vk
k K
曲率半径
ρk
Pk rk
N rb k k
K0
NOK=
cos k
rb rk
k
O 基圆
任务实施
(4) 渐开线的形状取决 于基圆的大小,基圆越 大,渐开线越平直,当 基圆半径趋于无穷大时, 渐开线成为斜直线,它 就是齿条的齿廓。
Σ3 Σ2
Σ1
N1 N2
r b2
K
KO1
o1 KO1 o2
任务实施
(5) 同一基圆上任意两条渐开线间的法向距离相等。
=
=
A1B1= A1N1 + N1B1 AB = AN1 + N1B A2B2= A2N2 + N2B2
=
K1 A2
K2 B1
A1
N1
A
N2
B2
N2B 所以: A1B1= A2B2
汽车维修基础
渐开线标准直齿圆柱齿轮传动
建议学时:1
任务描述
- 1、下载文档前请自行甄别文档内容的完整性,平台不提供额外的编辑、内容补充、找答案等附加服务。
- 2、"仅部分预览"的文档,不可在线预览部分如存在完整性等问题,可反馈申请退款(可完整预览的文档不适用该条件!)。
- 3、如文档侵犯您的权益,请联系客服反馈,我们会尽快为您处理(人工客服工作时间:9:00-18:30)。
齿轮啮合的基本技术要求
齿轮机械是我公司绝大部分产品不可缺少的传动机械,为了更好的保证产品的质量,就必须确保齿轮的精度.齿轮的精度大体可分为齿轮的设计精度、制造精度、测量精度、装配精度四个方面.只要保证国齿轮的精度,将可大大提高产品的质量,从而提高国市场竞争的能力.
一.设计精度,在审核图时应保证以下技术要求:
1.一对啮合齿轮的模数及压力角必须相等;
2.齿轮轴与齿轮孔的配合间隙,五金轴与胶齿轮应在0.01~0.03范围内,合金轴
与胶齿轮应在0.03~0.05范围内.胶轴与胶齿轮应在0.03~0.05范围内.五金轴五金齿轮应在0.01~0.02范围内;
另外齿轮是用在轮轴上时应保证一定的过盈量,五金轴与胶齿轮应在0.06~0.08范围内,五金轴与五金齿轮应在0.01~0.02范围内.(注:轴径在0~3mm之间)
3.齿轮分度圆与齿轮孔是否标注径向跳动误差,一般跳动量不得大于0.03mm,并
且齿轮端面跳动量不得大于0.05mm;
4.齿轮的分度圆、顶圆、底圆的尺寸误差应是上偏差为0,下偏差为-0.03mm,齿
宽尺寸误差应是上偏差为0,下偏差为-0.05mm,齿厚尺寸误差应上偏差为0,
下偏差为-0.03mm;
5.齿轮的周节尺寸及公差是否正确合理;
6.材料的选择是否正确;
7.齿廊曲线的选择是否正确,常用渐开线;
8.齿轮表面是否有光泽度要求,一般为0.8
9.齿轮啮合的中心距应是两齿轮分度圆半径之和,但装配中心距应偏大
0.05~0.08mm,保证齿轮侧隙;
10.蜗杆、蜗轮、斜齿轮旋向必须相符;
11.检查传动比计算车速是否符合客人要求.
二.制造精度.
1.提高设备的精度;
2.采用先进的制造工艺;
3.加强技术工人的培训,提高工人的技术水平;
4.齿轮的制造一定要满足设计要求.
三.测量精度
1.采用合理的测量方法及设备;
2.加强检测人员的培训,提高检测人员的素质;
3.检测的结果必须满足设计的要求
需检测的方面有以下几点:
1.分度圆的跳动量,业就是齿轮的偏心量;(台式千分表测量仪)
2.齿轮孔的孔径(圆柱量规)
3.齿顶圆的直径(游标卡尺)
4.齿轮的断面跳动量(杠杆百分表)
5.齿厚(齿厚游标卡尺)
6.齿槽(专用量规)
7.齿形(专用量规)
8.齿侧隙(专用量规)
9.齿宽(游标卡尺)
10.节距(专用量规)
11.齿数、模数、分度圆直径三者关系是否相符.(计算)d=mz
12.检查齿轮外观是否有批锋、缩水、走胶不齐,并且检查入水口位置是否合理、是
否有明显夹水纹、齿轮承受传动扭力的大小,并做寿命试验;
四.装配精度.
1.采用合理的装配工艺;
2.采用精确的装配工具;
3.培养工人的装配技能,了解齿轮的传动的基本原理;
4.选用先进的装配设备.
四.相关零件的检测
1. 牙箱的装配孔孔径检测(专用量规)
2. 牙箱两端的装配孔同轴度检测(专用量规)
3. 牙箱的孔的中心距检测(专用量规)
齿轮、蜗杆、牙箱精度要求及检测方法
一.齿轮
1.齿轮的齿顶直径、齿根直径、公差标注:
a.3~10mm,范围内上偏差为正0,下偏差为负0.03
b.10~17mm,范围内上偏差为正0,下偏差为负0.05
c.17~24mm,范围内上偏差为正0,下偏差为负0.08
2.齿轮的宽度
a.1~7mm,范围内上偏差为正0,下偏差为负0.05
3.台阶轴长及外经公差标注.
a.1~7mm,范围内上偏差为正0,下偏差为负0.05
b.7~14mm,范围内上偏差为正0,下偏差为负0.08
4.齿轮孔(间隙配合)公差标注(基轴制)
a.1~3mm,范围内上偏差为正0.03,下偏差为负0.01
b.3~6mm,范围内上偏差为正0.04,下偏差为负0.02
5.齿轮孔(过盈配合)公差标注(基轴制)
a.1~6mm,范围内上偏差为负0.02,下偏差为负0.04
6.齿厚公差标注,以10齿为例
a.m等于0.3时,齿厚上偏差为正0,下偏差为负0.03
b.m等于0.4时,齿厚上偏差为正0,下偏差为负0.03
c.m等于0.5时,齿厚上偏差为正0,下偏差为负0.05
d.m等于0.6时,齿厚上偏差为正0,下偏差为负0.05
7.分度圆同心度标注(以内孔轴心为基准)
a.3~10mm,径向跳动小于0.03
b.10~20mm,径向跳动应小于0.05
c.20~30mm,径向跳动应小于0.07
8.齿轮端面跳动量标注(以内孔轴心为基准)
a.齿顶直径在3~10mm,范围内端面跳动应小于0.05
b.齿顶直径在10~20mm,范围内端面跳动应小于0.08
c.齿顶直径在20~30mm,范围内端面跳动应小于0.10
9.在图纸上必须注明以下参数
a.模数
b.齿数
c.压力角,一般取20°
d.表面粗糙度,齿轮内孔基渐开线齿廊面一般为0.8 , 其它为3.2
二.蜗杆
1.蜗杆齿顶直径、分度圆直径、齿根直径公差标注
a.3~10mm,范围内上偏差为正0,下偏差为负0.03
2.蜗杆长度公差标注
a.3~10mm,范围内上偏差为正0,下偏差为负0.05
3.蜗杆内孔公差标注(过盈配合)
a.小于等于3mm,范围内上偏差为负0.02,下偏差为负0.04
b.大于3mm,小于6mm,范围内上偏差为负0.03,下偏差为负0.05
注:过盈配合长度为2~4mm
4.蜗杆周节,分度圆齿厚公差标注
a.周节公差标注:上偏差为正0.02,下偏差为负0.02
b.齿厚公差标注:上偏差为正0,下偏差为负0.02
5.分度圆同心度标注(以内孔轴心为基准)
a.径向跳动小于0.03
6.在图纸上必须注明以下参数
a.模数
b.齿数
c.压力角,一般取20°
d.螺旋角
e.表面粗糙度,齿轮内孔及渐开线齿廊面一般为0.8 ,其它为3.2
三.牙箱(与齿轮装配有关的尺寸公差及形位公差)
1.齿轮轴直径公差标注
a.1~3mm,范围内上偏差为正0,差为负0.02
b.3~6mm,范围内上偏差为正0,差为负0.02
2.齿轮轴与齿轮轴中心距公差标注
a.上偏差为正0.08,差为正0.06
3.齿轮轴与蜗杆轴中心距公差标注
a.上偏差为正0.10,差为正0.08
4.齿轮轴与端面的垂直度要求
a.所有的齿轮轴与端面的垂直度公差位0.02
b.蜗牙轴与端面的平行度公差位0.02
注:1. 对于塑胶零件及合金零件应标注入水位,分模面及顶钉位
2.标题栏内应标注产品的名称、产品的编号、产品的用量、材料、热处理要求、
图纸的比例,及产品的缩放比例及日期、制图人姓名等。
四.齿轮、蜗杆、牙箱的关键尺寸检查
1.齿轮
a.分度圆直径检测
(1).方法1:对于奇数齿采用3针测量方法
对于偶数齿采用2针测量方法
(2)方法2:首先测量出齿槽、齿厚形状是否正确,如果正确然后再测量齿顶直径是否OK
b. 齿厚检测
(1).方法1:采用放大投影仪测量
(2).方法2:采用齿形规
c.齿宽检测
(1).方法1:采用游标卡尺
(2).方法2:采用通止卡规
d.分度圆同心度检测
(1).方法1:采用标准齿轮啮原理检查齿轮综合跳动量
(2).方法2:采用台式千分表测量齿槽的跳动量
e.齿轮端面跳动量检测
方法1:采用台式千分表测量端面跳动量
f.齿侧隙检测
方法1:采用台式千分表专用齿侧隙检测工具测量
g.齿轮内孔检测
方法1:采用通止圆塞规测量
2.螺杆
a.螺杆长度,外经尺寸检测
方法1:采用游标卡尺检验
方法2:采用通止卡规检验
b.螺杆内孔检验
方法1:采用通止圆塞规检验
c.分度圆直径检测
方法1:采用3针测量方法
d.螺杆周节,分度圆齿厚的尺寸检测
方法1:采用齿形规检验
e.分度圆同心度检测
方法1:采用台式千分表测量径向跳动量
3.牙箱
a.齿轮轴直径检测
方法1:采用通止塞规检验
方法2:采用游标卡尺检验
方法3:采用多孔组合塞规检验
b.齿轮轴中心距检测
方法1:采用多孔组合塞规检验
方法2:采用游标卡尺检验
c.轮槽位及螺牙轴承检测
方法1:采用通止规检验
方法2:采用游标卡尺检验。