KEM快速热导仪QTM -500
高导热耐高温型环氧灌封胶的制备与性能

高导热耐高温型环氧灌封胶的制备与性能周锦强;潘仕荣;何秀冲【摘要】A epoxy resin potting sealant with high thermal conductivity and high temperature resistance was prepared with the novolac epoxy resin and anhydride curing agent, using the boron nitride (BN) micro particles as the basic packing. The result showed that with increasing the mass fraction of BN, the thermal conductivity of epoxy sealant was increased, however,its temperature resistance was decreased. The addition of right amount coupling agent enhanced the thermal conductivity and temperature resistance of epoxy potting sealant.%以氮化硼为主填料,采用酚醛型环氧树脂与酸酐类固化剂,制备了一种高导热耐高温型环氧灌封胶。
研究了填料用量与硅烷偶联剂改性对胶粘剂热导率与耐高温性的影响。
结果表明,随着填料量的增加,热导率增强,但耐温性能有所降低。
偶联剂的适量加入也增强了环氧胶的导热与耐温性能。
【期刊名称】《粘接》【年(卷),期】2015(000)008【总页数】3页(P57-58,54)【关键词】环氧树脂;氮化硼;导热;耐高温;灌封胶【作者】周锦强;潘仕荣;何秀冲【作者单位】上海回天新材料有限公司,上海201600;上海回天新材料有限公司,上海 201600;上海回天新材料有限公司,上海 201600【正文语种】中文【中图分类】TQ433.437+环氧树脂具有较高的强度和优良的粘接性能,它以复合材料用树脂、胶粘剂、灌封材料等形式用于许多工业领域 [1]。
Maxi-Heat MH500iQ 双热水热器系统说明书

■ Caterpillar or Optional Isuzu Liquid-Cooled Diesel Engine
■ 16" or Dual 12" Duct Flange Outlets ■ GPS Ready (Customer Supplied)
Output @ Rated Speed (1,800 RPM) - HP
18.8
19.9
Engine Electrical System (V)
12Voltage Regulator (VAC)
120 / 240
120 / 240
Frequency (Hz) / Phase
60 / 1-phase
60 / 1-phase
Maxi-Heat®
MH500iQ™
iQ SYSTEM CALIBRATES AND MONITORS THE HEATER TWIN HEATER UNITS CAN BE USED INDEPENDENTLY HEATERS CAN BE POWERED BY MACHINE'S ENGINE / GENERATOR OR UTILITY POWER
SINCE 1938
Reliability, Performance and Integrity.
Maxi-Heat®
MH500iQ™
The Maxi-Heat® MH500iQ™ FCS is designed to provide heat in harsh conditions with two independently operating heater units providing up to a combined 1,000,000 BTU’s of heat. The iQ system automatically calibrates each heater unit so you don't have to change nozzles or test and retest with a smoke spot tester. The iQ system continuously monitors the heater, producing a higher degree of fuel efficiency with less soot and smoke. With a Fluid Containment System (FCS) and a single cell, double wall steel fuel tank, this heater is a top choice for worry free jobsites.
STRESSTECH QZ1500-8 加热设备操作指南和配件清单 安全说明书

STRESSTECHQZ1500-8OPERATING INSTRUCTIONS AND PARTS LISTSAFETY INSTRUCTIONSAlways wear protective clothing, including safety glasses and steel toe boots.Keep work site neat and clean.Run the secondary cables overhead or clearly mark the area for trip hazards.Ensure adequate clearance around the area to be heat treated, is free of any material that could be a fire hazard.Check to be sure the work piece is adequately supported before starting the heat cycle. Clearly mark the work area to inform others of ongoing heating.Inform other workers of the heated area and of the heating element tails on the work piece.Do not operate or use the heat treating equipment, unless you have read and understand the operating manuals that came with your equipment.A Division of MactechTable of ContentsGeneral Information 1 Post Weld Heat Treatment Set-up 2-4Top Temperature Controller 5Operating Instructions 6-10 Trouble Shooting 11-12 Service and Maintenance 13Welding Supply Instructions 14 Voltage Change-Over Diagram 15Parts List 16-19 Wiring Diagrams 20-22Electrical Specifications:Input Requirements 150 amps @ 480/575v 3ph 100% 122 KVACurrent Capacity (per zone) 300 AMPS DC80 VOLTS DCOutput Available 1500 amps @ 80 VDC 100% duty cycle Physical Dimensions:Height: 40"Width: 27"Length: 40"Weight: 1050 lbs.General Information:The STRESSTECH QZ 1500-8 is an eight zone temperature controller which can be operated semi-automatically (auto-ramping up and down, hold at temperature), or manually (manual ramping, no hold temperature). It consists of eight 300 amp contactors, 0-2000 deg. F. temperature controllers, percentage timers for controlling the rate of heating and cooling, if desired. The QZ 1500-8 also has a 0-500 and a 0-1500 DC ammeter, to aid in monitoring the current supplied to the heating elements being used.(Each element will use approximately 50 amps @ 80 DC volts.) The top temperature controller will maintain any selected temperature between ambient and 2000 deg. for as long a period of time required. The controller will control the heating and cooling rate by opening or closing the contactor as needed.The contactor, normally open, will close providing current to the heating elements up to a maximum of 300 amps, at 80 DC volts.Post Weld Heat Treatment Set-up:1. Prepare thermocouple wire for attachment to work piece:a) Cut two thermocouple wires 24" or longer (thermocouplewires should extend beyond insulation).b) Strip insulation back approximately 1/4" - 3/8" on bothends of each wire.c) On one end of each wire, trim lead ends to a fine pointand bend the last 1/8" at a 90 degree angle.d) On the opposite end of one wire, install a malethermocouple plug. Yellow wire (+), Red wire (K).e) Lightly twist the two wires together. The wire without theplug will be a spare.2. Attach the prepared thermocouple wires onto the work piece using the capacitor-discharge spot welder (ZAP GUN). Operating instructions, for attachment of thermocouple wires, are on the inside of the Zapgun lid.3. Thermocouples shall be attached in the following minimum location(s):ON A HORIZONTAL WORK PIECE:a) Always at the bottom-dead-center.b) For component diameters 12 inches or more, add a secondthermocouple at the top-dead-center.c) For component diameters over 24 inches, placethermocouples at each 90 degree intermediate location.ON A VERTICAL WORK PIECE:a) The same number of thermocouples as above shall beattached, spaced evenly.4. Thermocouples shall be attached in each zone where heaters are separately controlled.5. Thermocouples should be placed so that the anticipated coolest and hottest areas within the heating band are monitored.Post Weld Heat Treatment Set-up Cont:6. When the component wall thickness adjacent to the wall vary significantly (such as by the thicker side being more than about 25% or 1/2" greater than the thinner) then:a) Additional thermocouples shall be attached so that each ofthe above required locations have thermocouples close tothe weld, but both on the thin and thick materials thatwill be under the heating band (e.g., for a pipe welded toa heavy valve) and,b) for even larger thickness differences (such as for a pipeto a very heavy vessel nozzle), even more thermocouplesshould be attached on the thicker material, at a distance from the weld equal to about 3 times the wall thickness at the weld. If such thermocouples are beyond the heating band, the gradient should be controlled if and as required by the Specific Project Instructions.7. A system shall be established for positive identification of each thermocouple with the location on the work piece. A sketch or written description of thermocouple locations should be made, identifying each thermocouple.8. Select the heating element(s) that best cover the area to be heat treated.9. Tape the heating element(s) onto the work piece using fiberglass strapping tape, and then use stainless steel banding to fasten them securely.10. Insulation shall completely cover the heating elements, and extend beyond their edges somewhat. If possible, the insulation should be at least twice as wide as the heating band.11. Fasten the insulation securely to the work piece by using tie wire or banding.12. Heating element tails should be brought directly out of the insulation, so as not to overheat the connectors.13. Connect thermocouple(s), using thermocouple extension leads, to the thermocouple jack strip on control unit. MAKE SURE thermocouples are plugged into proper jacks; i.e., thermocouple #1 on work piece must be connected to thermocouple jack #1, etc.Post Weld Heat Treatment Set-up Cont:14. Connect heating elements to splitter cables: (figure 1)a) Heating elements associated with thermocouple zone #1,must be connected to circuit #1. This sequence followsthrough for each zone of control.b) Connect a tail from each heating element in circuit #1,to a splitter cable.c) Connect the other tail from each heating element incircuit #1, to a different splitter cable.d) Using 2/0 power cable extension leads, connect the twosplitter cables from circuit #1 to the two correspondingjacks on the control unit.e) Repeat steps b-d, if connecting more thanone zone of control.15. Using 6 ft. male to male thermocouple jumper wires, you can connect a temperature recorder to the thermocouple jack strip on the control unit.(figure 1)TOP TEMPERATURE CONTROLLEROperating Instructions:1. Be sure the main power and control power switches onthe QZ 1500-8 are in the OFF position.2. Position the unit in desired location and connect a 480 volt, three phase, 150 amp service to the line cord. Service line should have a fused safety disconnect switch on the feeder side. Wire in accordance with all applicable local and national electrical codes. Make sure unit is properly grounded before placing into service.3. Connection of 80 vdc power leads: (figure 2)ZONE #1a) Connect a lead from the heating elements to the femalecam-lok on the side of the unit marked "1".b) To complete the circuit, connect the remaining lead fromthe heating elements to the other female cam-lokmarked "1".4. Insert the thermocouple lead, from the work piece, into one of the (#1) thermocouple jacks on the side of the QZ. The second (#1) jack is used for connecting a temperature recorder.(figure 2)5. Repeat steps 3 and 4 using Zone #2, 3, 4, 5 or 6 for heating more than one controlled area.Operating Instructions Cont:MANUAL OPERATION6. Make sure all the individual heating circuits are off. Turn on the main power switch and then the control power switch. Set the percentage timers at 50%. (Heating circuits work on a full on or off principal. 50% power is obtained by turning contactors on for half a minute then off for half a minute.)7. Push the auto/manual switch to the manual position. In the manual position only the percentage timers are used, the top temperature controller does not affect the output.8. Check the ammeters on front panel. Each circuit is capable of switching 300 amps, but do not exceed 1500 amps total for all eight zones. Overloading will cause a fuse to blow inside the unit, which could mean losing a heating cycle.9. Check the slope of the temperature chart to determine the rate of rise of the temperature and increase or decrease the setting on the percentage timers as needed to maintain proper heating or cooling rate.- 8 -Operating Instructions Cont:AUTO OPERATION10. Make sure all the individual heating circuits are off. Turn on the main power switch and then the control power switch. Set the percentage timers at 0% (while setting the top temperature controllers).11. Push the auto/manual switch to the auto position and set the top temperature controller to the desired holding temperature (set value):a) The controller runs through a self test for about threeseconds and then displays the measured value.This is called the HOME display.b) To view the set value, press and release the UP or DOWNkey. The set value will be shown for approximately2 seconds.c) To change the set value, press the UP or DOWN keyuntil the desired soak temperature is displayed. After two seconds the new value will be accepted and the controller will return to the HOME display.12. Set the top temperature controller to the desired heating ramp rate:a) Press the SCROLL key twice and an indication of "SPrr"(set point ramp rate) appears.b) To view the ramp rate value, press the UP or DOWN key.The value shown is in degrees per minute.After two seconds the display will return to "SPrr".For example,If you wish to enter a ramp rate of 300 degrees/hour,you perform the following calculation:300 degrees/hour divided by 60 minutes = 5 degrees/minute.c) Change the data indication to the desired ramp rate, usingthe up and down-keys.d) The display will return to "SPrr" after two seconds.e) After 45 seconds the controller will return to the HOMEdisplay. Or you can press the PAGE or SCROLL key once toreturn to the HOME display.Operating Instructions Cont:13. Once you have the desired set value, and ramp rate entered into the controller, push the auto/manual switch to the off position.14. Turn the percentage timer to 100%.15. Push the auto/manual switch to the auto position. This enables the unit to use both the top temperature controller and the percentage timer. In the manual position only the percentage timer is used, the top temperature controller does not effect the output.16. The controller will ramp from the present temperature, at the rate you entered into the "SPrr" parameter, to the soak temperature you entered for the set value.17. While the controller is ramping, the display may flash "1dLo".Which is a low deviation alarm, to let you know the workpiece is not keeping up with the controller.18. The display may also flash "2dHi". Which is a high deviation alarm to let you know the workpiece is not keeping up.19. The controller will hold the workpiece temperature at the set value until you change it to a new value.20. At the end of the soak time you will need to change the set point ramp rate "SPrr", if the cooling rate is different than the heating rate. If the rates are the same you won't have to change it.21. Once the correct cooling rate is entered into the "SPrr", you will need to change the set value to 0 degrees.22. The controller will now ramp from the soak temperature down to 0 degrees.Operating Instructions Cont:23. The weldment area shall be first brought up to about 200 degrees. The temperature recorder shall be checked then for temperature readings of each thermocouple, and for correct chart speed.24. During the PWHT cycle, the current should be occasionally checked, especially if any abnormal temperature readings are obtained. A significant drop, such as by the rating of one heater (about 50 amps), would indicate that a heater may be burned out.25. At no time shall any two thermocouples, within the heating band, be allowed to differ by more than 150 degrees. If this temperature difference is approached during heating, the heating rate should be slowed.26. Heating shall continue until reaching the holding temperature required by the applicable Welding Procedure.27. At the completion of the holding time, begin the cooling.28. The power shall not be completely shut off until the temperature cools down to below 600 degrees, unless it is determined by continuous monitoring that the maximum cooling rate will not be exceeded, or that the temperature difference between any two thermocouples will not differ by more than 150 degrees.29. Insulation coverings shall not be removed until the temperature drops below 200 degrees, although any stuffed in the ends to fill gaps may be removed if the work piece is in still air and will not exceed the maximum allowable cooling rate.30. Check all equipment for damage or wear. Any damaged equipment should be repaired immediately or replaced.Trouble Shooting:1. Temperature does not increase on controller:a) Check voltmeter on front panel to be sure it isreading 80 vdc.b) Percentage timer is turned up to 100%.c) Check for correct connections of the cables.d) Check ammeters on front panel. (each heating elementdraws approximately 50 amps)d) Check the set value and set point ramp rate "SPrr"settings on the controller.2. Temperature does not increase on recorder:a) Check male to male thermocouple wire for a badconnection at one of the plugs.3. Temperature decreases on recorder or controller:a) The thermocouple wires have been reversed in one ofthe plugs. The yellow wire should be in the positive(+) slot and the red wire in the negative (-) slot.4. Contactor chatters:a) Check the thermocouple connections first. If all theconnections are ok, the contactor may be worn out. 5. Temperature swings when holding at a set point with the top temperature controller:a) Thermocouples are located too far from heatingelements. The swing can be reduced by turning thepercentage timer down, if the full power is notneeded to maintain the temperature.6. Temperature does not stop rising after reaching the set value:a) Be sure the auto/manual switch is in the autoposition.Trouble Shooting Cont:7. Fault indication on top temperature controller:a) The controller has a fault indicating function sothat the cause of fault can be removed quickly.These warn that a fault exists in either thecontroller or the connected devices.INDICATION : WHAT IT MEANS1dLo : Deviation low alarm-------------------------------------------------------2dHi : Deviation high alarm-------------------------------------------------------S.br : Thermocouple sensor break-------------------------------------------------------LLLL : Out of range low reading-------------------------------------------------------HHHH : Out of range high reading-------------------------------------------------------EE.Er :----------------Err1 :----------------Err2 : Return for repair----------------Err3 :----------------Err4 :REPAIR AND CALIBRATIONDue to the nature of its design, if a controller fails tooperate correctly consult STRESSTECH. Special equipment isrequired for calibration and unit MAY have to be returned forrepair.Service And Maintenance:NEVER work on a unit unless primary power has been disconnected or locked out.1. Keep control unit clean and dry.2. Periodically check all thermocouple wires and power cables for loose connections or damage. Any damage should be repaired immediately or replaced.3. Every six months remove the cover from the unit and, using clean dry air, blow out all dust and dirt from the inside. Do not exceed 25 psi.4. Keep cam-lok connectors clean using scotchbrite pads.5. Contactor maintenance:a) The main contacts should be given regular attention,especially where heavy loads are involved or a highnumber of operations per hour.b) These contacts are plated with silver cadmium oxidegiving it the same corrosion protection as puresilver, but greater resistance against contactwelding.c) Contact surfaces should not be polished or greased.d) Worn-off contact dust should be carefully brushedoff the insulating parts at each inspection. The de-ionizing laminations of the arc shield are made ofsteel plate to which beads of fused metal may stickso that the laminations become electricallyconnected. If this has occurred, the beads must beremoved by means of a smooth file or suchlike. Ifthere are layers of sintered contact dust on theinside of the arc shield, these should also bescraped off.e) Change all three contact points if any one becomesbadly worn or pitted.For further information or parts contact STRESSTECH,4079 Pepin Avenue, Unit 4, Red Wing, Minnesota 55066;or call toll free 1-800-328-1488.STRESSTECH QZ1500-8AS A POWER SOURCE FOR WELDINGTo use:1. Turn main power switch on.2. Turn control power switch on.3. Push auto/manual switch to manual.4. Turn percentage timer to 100%.5. Plug in cable from welding grid to unit.(If more than 300 amps is required per weldingstation use a "Y" cable between two zones.)To weld straight polarity:1. Connect the male cam-lok from the welding grid tothe negative cam-lok receptacle on the side of theQZ.2. Connect the ground clamp to the work piece and tothe positive cam-lok receptacle of the same zoneon the side of the QZ.To weld reverse polarity:1. Connect the male cam-lok from the welding grid tothe positive cam-lok receptacle on the side of theQZ.2. Connect the ground clamp to the work piece and tothe negative cam-lok receptacle of the same zone onthe side of the QZ.A second welding grid can be used simultaneously byconnecting it to different zone, providing the samepolarity is used for both welding units.INPUT VOLTAGE CHANGE-OVER DIAGRAM(figure 1)Parts List (figure 1):1. Voltmeter (0-100vdc) 120057362. Ammeter (0-1500amp) 120057273. Main Power Switch &Control Power Switch 12008441ON/OFF Plate 120084604. Ammeter (0-500amp) 120057215. Selector Switch Assy.Rotary Switch 12008415 Aluminum Knob 12009959 6. 110v. Outlet Fuse Assy.Fuse Holder 12003930 AGC 3 Amp Fuse 12003940 7. 110v. Transformer Fuse Assy.Fuse Holder 12003930 ABC 15 Amp Fuse 12003947 8. Main Power Light Assy. (1)Contactor Light Assy. (8)Pilot Lamp Housing 12005231 Pilot Lamp 12005220 Red Lens 120052329. Auto/Manual Switch (8) 1200841010. Top Temperature Controller (8)Eurotherm 2116 Controller 12008645 11. Percentage Timer Assy. (8)Aluminum Knob 12009959 Adjusting Pot. 12009984 Solid State Timer 12006702 Dial Plate 12009995 12. Front panel 12002070I(figure 2)Parts List (figure 2):1. Rectifier Assy.Rectifier Diode (6) 12009890 Diode Clamp-Cross Bar (6) 12009891 Diode Clamp-Spring Assy. (6) 120098922. 16” Exhaust Fan120022273. Zone Contactor (6) 12002760 Contactor Bussbar 120019284. 1500 Amp DC Shunt 120078505. 1600 Amp Fuse 120039256. Thermocouple Terminal Strip (2) 120089107. Female Connector 12 Position 120084718. Female Connector 15 Position 120084739. 110v. Panel Mount Outlet 1200704510. Panel Mount Cam-lok (16) 1200216011. 480/110v. Transformer 1200933112. Main Contactor 1200276513. 300 Amp Fuse (8) 1200391014. 500 Amp DC Shunt (8) 1200782015. 50W 1 Ohm Resistor 1200995516. 50W 150 Ohm Resistor 1200995617. 9800UF 100v. Capacitor 1200992918. Main Transformer 12009361CONTROL DRAWER WIRING DIAGRAMCONTROL DRAWER WIRING DIAGRAMBASE UNIT WIRING DIAGRAM。
TC500A商务温度仪式装置安装说明书

MOUNTING INSTRUCTIONSTC500A Commercial ThermostatCONNECTED DEVICE FOR COMMERCIAL BUILDINGSINTRODUCTIONTC500A Commercial Touchscreen Thermostat is designed to be wall-mounted indoors. Mount in a clean, dry location away from windows, air ducts, and other places where environmental factors may affect temperature and humidity readings. If you mount the Thermostat on the interior of an outside wall, thoroughly insulate so outside air behind the sensor does not affect the sensor reading. To meet the requirements of the Americans withDisabilities Act, mount no higher than 48" from the floor and with a minimum clear floor space of 30" X 48" (760 X 1220 mm).Supported Documents•TC500A-N Commercial Thermostat Datasheet (31-00398M)•TC500A-N Commercial Thermostat User guide (31-00400M)•TC500A-N Commercial Thermostat Quick start guide (31-00401M)•TC500A-N Commercial Thermostat Pocket guide (31-00463M)•TC500A Deco Plate Pocket guide (31-00457M)When installing this product1.Read these instructions carefully. Failure to followthem could damage the product or cause a hazard -ous condition.2.Check the ratings given in the instructions andmarked on the product to make sure the product is suitable for your application.3.Installer must be a trained, experienced service tech -nician.4.After installation is complete, check the productoperation.5.Be sure wiring complies with all applicable codes,ordinances and regulations.WARNINGElectrical Shock Hazard.Can cause severe injury, death or property damage. Disconnect the power supply before beginning installation to prevent electrical shock andequipment damage. More than one power supply may have to be disconnected.MERCURY NOTICEIf this control is replacing a control that contains mercury in a sealed tube, do not place your old control in the trash. Dispose of properly. Contact your local waste management authority forinstructions regarding recycling and the proper disposal of an old control. If you have questions, contact Honeywell Customer Care Center.LocationDo not install the Thermostat unit where it can be affected by:—drafts or dead spots behind doors and in corners.—hot or cold air from ducts.—radiant heat from sun or appliances.—concealed pipes and chimneys.—unheated (uncooled) areas such as an outside wall behind the thermostat.IMPORTANTTo avoid electrical interference, which can cause erratic performances, keep wiring runs as short as possible and do not run thermostat wires adja -cent to the line voltage electrical distribution sys -tems. Use shielded cable. The cable shield must be grounded only at the controlled equipment case.WHEN USED TO SENSE ROOM TEMPERATUREInstall the Thermostat about 4 ft. (1.2m) above the floor in an area with good air circulation at average temperature. (See Fig. 1). Confirm mounting height meets Americans with Disabilities Act requirements.TC500A-N/TC500A-W COMMERCIAL THERMOSTAT 31-00399M-02 | Rev.03-212WHEN NOT USED TO SENSE ROOM TEMPERATURE When using the remote-mounted temperature (and humidity) sensor(s) to sense ambient conditions, install the Thermostat in an area that is accessible for setting and adjusting the temperature and settings.Fig. 1. Typical mounting location of thermostatThis symbol on our product shows a crossed-out “wheelie-bin” as required by law regarding the Waste ofElectrical and Electronic Equipment (WEEE) disposal. This indicates your responsibility to contribute in savingthe environment by proper disposal of this Waste i.e. Do not dispose of this product with your other wastes. To know the right disposal mechanism please check the applicable law.Regulation (EC) No 1907/2006According to Article 33 of Reach Regulation be informed that the substances listed below may be contained in these products above the threshold level of 0.1% by weight of the listed article.Power supply guidelines and requirementsThe thermostat uses 24VAC power from a UL Listed Class-2 24VAC transformer (not provided in the kit). It also uses a half-wave rectifier to convert the AC power supply to onboard power. This enables multiple devices with half-wave power supplies to be powered from a single, grounded transformer.WARNINGHalf wave devices and full wave devices must not use the same AC transformer.You must maintain wiring polarity. Failure to do so can result in equipment damage. If the HVAC equipment has an internal circuit board that is powered by the same transformer that will power the Thermostat, verify that it is NOT full wave.Fig. 2. Power terminalsPower supply wire sizingLong power supply wiring runs require selecting the wire gauge appropriately. If the wire gauge is inadequate the increased resistance and associated voltage drop mayresult in insufficient voltage supply to the Thermostat. The recommended wire gauge guidelines are as follows.Min. Load = 4VA (all DOs OFF, No Sylk sensor).If 18-20AWG wire is used for R, C, RC terminal,Max. Load = 4A, 96VA (all DOs ON). If 22AWG wire is used for R, C, RC terminal Max. Load = 3A, 72VA (all DOs ON).If R-Rc power jumper is not removed, then G, W1, W2, W3, Y1, Y2, Y3 are powered from the Thermostat’s transformer. Minimum load includes Thermostat and analog outputs at full load (Max. 10V voltage output with 2Kohms load).Every relay output is N.O. (Normally Open) contacts with a maximum switch rating of 24VAC @1A (24VA). The allowed maximum load is 96VA, which assumes all 8 relay output loads are powered from the controller transformer. Actual power requirements depend on connected loads.IMPORTANTTransformer sizing should never exceed the maxi -mum UL Class 2 rating.The 24VAC secondary leads are not interchangeable . Once a lead connects to the GND terminal, it is the grounded lead. Observe and maintain polarity forsubsequent connections. The GND terminal provides a reference ground for the circuit board andcommunications wiring. Use 18 AWG cable for best results.WEEEWEEE (Waste of Electrical andElectronic Equipment)•At the end of the product life, dispose of the packaging andproduct in an appropriate recycling center.•Do not dispose of the device with the usual domestic refuse.•Do not burn the device.Product/Part CodeSubstance NameCAS Number Only TC500A thermostat mainboard PCBA, thermostat wall plate board PCBALead 7439-92-1Lead oxide 1317-36-8+ DC VoltageGND24VACRCTC500A-N/TC500A-W COMMERCIAL THERMOSTAT331-00399M-02 | Rev.03-21WARNINGEnsure that all Thermostat power, communications, and I/O cabling are connected to C or COM according to these instructions. Failure to follow these instructions may result in Thermostat operational and communication failures or equipment damage.Detaching the wallplate from the displayThe thermostat is an assembly of a wallplate and a display. It must be disassembled before starting the mounting procedure.1.At bottom of the thermostat, loosen the Securityscrew using a screwdriver by turning it counter-clockwise direction.2.Hold the display unit and pull the paper tail.Fig. 3. Detaching the wallplateMounting wallplate on the drywallMount the wallplate vertically on the wall. It supports 18-22 AWG (0.5-0.75mm2) wires.NOTE:If you are using a TC500A Deco plate for thermo -stat mounting, refer to the Deco plate pocket guide (31-00457M) also.1.Before mounting the wallplate, make sure that thethermostat wires are stripped to the length marked on the wallplate.Fig. 4. Wire strip length2.Position and level the wallplate along the wall and mark the drilling location using a pencil.Fig. 5. Wallplate drilling locations3.Remove the wallplate and drill two pilot holes on the wall, on the marks. For drywall, drill 3/16-in. holes. For firmer material such as plaster, drill 7/32-in. holes.4.Gently tap anchors (provided in the kit) into the pilot holes until flush with the wall.5.Pull the wires through the wiring opening of the wall -plate and position the wallplate over the mounting holes.6.Insert the screws into the holes and tighten (screw torque 0.1Nm).Mounting the wallplate on the junction box (optional)The thermostat wallplate can be mounted vertically on a US 2”*4” or UK 75*75mm junction box.NOTE:If you are using other than US 2”*4” or UK75*75mm junction boxes, then a TC500A Deco plate can be used for thermostat mounting. Refer to the Deco plate pocket guide (31-00457M).1.Install the junction box and perform the wiring as per its manufacturer’s instruction.2.Before mounting the wallplate, make sure that the thermostat wires are stripped to the length marked on the wallplate.3.Pull the wires through the wiring opening of the wall -plate, and position the wallplate along the junction box to align the mounting holes. For junction box screw holes, refer to Fig. 5.4.Insert the screws into the holes and tighten.Paper tail4 x 11/32”2 - 3/8” (60.3mm)(UK 75X75cm junction box3 - 1/4” (82.75mm)(US 2”X4” junctionTC500A-N/TC500A-W COMMERCIAL THERMOSTAT31-00399M-02 | Rev.03-214Accessories ordering part numbersTerminal identificationFig. 6. Thermostat terminal assignmentsWARNINGDo NOT wire the thermostat to line voltage.IMPORTANTRemove R to RC jumper only for 2 transformer sys -temsTable 1. Accessories Part NumbersDecoplate-N TC500 deco plate for NA junction boxes Decoplate-WTC500 deco plate for Global junction boxesTable 2. Terminal identificationTerminalLabel Connection24VACR24VAC power from heating Class 2 transformerC24VAC common (Neutral). For 2 transformer systems, usecommon wire from the cooling transformerUIO11Universal input/output COMCommonUIO22Universal input/outputCOM Common UI11Universal input COM Common UI22Universal input COMCommonSylkSylk bus, master, power outputSylk bus, master, power outputRS485+BACnet Communications (coming soon)_BACnet Communications (coming soon)R-RCJumper between R and RC for single transformer system, remove the jumper in two transformer system.24VACRC 24VAC power from cooling Class 2 transformer G FanY1Relay output, Compressor contactor (stage1)Y2Relay output, Compressor contactor (stage2)Y3Relay output, Compressorcontactor (stage3)/Configurable OutputW1Relay output, Heat (stage1)W2Relay output, Heat (stage2)W3Relay output, Heat(stage3)/Configurable Output AuxRelay dry contact, Aux-1Relay dry contact, Aux-2Table 2. Terminal identification (Continued)TerminalLabel ConnectionTC500A-N/TC500A-W COMMERCIAL THERMOSTAT531-00399M-02 | Rev.03-21Wiring the wallplateIMPORTANTAll wiring must comply with local electrical codes and ordinances.NOTE:Supports 18-22 AWG (0.5-0.75mm 2). Solid wire isrecommended.Follow equipment manufacturer wiring instructions when available. A letter code is located near each terminal foridentification.Wiring a unit that is powered may result in electrical shock and/or equipment damage.1.Connect wires to the terminals. See Fig. 6 for terminalassignments and Table 1 for terminal descriptions.2.Insert the solid wire into the terminal hole directly.3.(optional) To insert stranded wire end into the wiringterminal, push the Release tool into the Tool hole and insert the wires.Fig. 7. Wire release4.Push excess wire back into the hole.5.Check for the loose or frayed wire that may cause ashort.Mounting the display unitAfter all wiring is completed, install the display onto the wallplate.1.Hold the display in a tilted position so the latches fit onto the rectangular slots of the wall plate as shown in the below image.2.Insert the latches onto the wallplate rectangular slots and rotate the display and push it onto wallplate.3.by turning it in the clockwise direction (screw torque0.1Nm).TC500A-N/TC500A-W COMMERCIAL THERMOSTAT® U.S. Registered Trademark© 2021 Honeywell International Inc.31-00399M-02 | Rev.03-21Honeywell Building TechnologiesHoneywell715 Peachtree Street NE Atlanta, GA DIMENSIONS(60.3mm)3 - 1/4” (82.75mm)。
MAXI-HEAT MH500iQ FCS 高温辅助系统说明书

Brighter. Warmer. Safer.Reliability, Performance and Integrity Since 1938• Fluid Containment System and double-wall single-cell metal the MH500iQ FCS is ready for the harshest of conditions.• • producing a maximum of 1,000,000 combined BTUs, may be • with 9 kW transform-STANDARD FEATURESSPECIFICATIONSREV ALIGHT TOWER APP1502 West 4th Avenue Holdrege, Nebraska 68949P: (800) 562-1373F: (308) Copyright ©2015 Allmand Bros., Inc.Y our Allmand Distributor:MH500iQ ™FCSEngineCaterpillar C1.5 T4F liquid-cooled diesel (standard)Isuzu 3CE 1.6L liquid-cooled diesel (optional)Low oil pressure / high temperature automatic shutdownGenerator *Electrical output provided by Allmand testing60 Hz, 9 kW single-phase Starting12 volt electric - Group 8D battery Glow plugs (CAT)Engine block heaterIntake air heater (Isuzu)Fuel Capacity *175 gal double-wall single-cell metal fuel tankWill operate approximately 20 hrs without refueling at full load with both burners running.Heater(2) MCS500iQ indirect-fired twin heating units Up to 500,000 BTU/hr each 1-16 in. duct flange per heaterOptional flexible ducting easily connects to heater output flanges 2.3” wc static pressure allows use of 110 ft. (33.5 m) of 16 in. ducting Electronically-controlled temperature Easy-clean combustion chamber (2) automatic nozzlesiQ controls environmental temperature/pressure and suggests correct burner settingsHeated Air Output 6,200 CFM total with no ducting Temperature Rise 185° F (85° C)TrailerFluid containment system Safety chains Formed, welded steel frameFront screw jack Adjustable height combination 25/16 in. Bulldog, 3 in. pintle towing hitch Hour meterHeavy-gauge steel enclosure Interior compartment light Lockable access doorsStop/turn/tail lights 6,000 lbs. (2,722 kg) leaf spring axleElectric brakesDimensionsHeight: 87.3”(2.22 m)Length: 193.3”(4.91 m)Width: 80” (2.03 m)16 in. (40.6 cm) wheels and tiresWeight Dry: 3,675 lbs. (1,667 kg) | Wet: 6,000 lbs. (2,722 kg)OptionsFabric-elastometer ducting 16 in. x 20 ft.Remote thermostatFabric-elastometer ducting 12 in. x 24 ft.16 in. slip lock duct connectors / bands CSA/Transport Canada Package Duct storage box12 in. or 20 in. dual duct outlet end capEmergency air shutoff valve。
TH2515 仪器说明书

Ver 2.1目录Ver 2.0 (2)第1章仪器简介与开箱安装 (8)1.1仪器简介 (8)1.2开箱检查 (8)1.3电源连接 (8)1.4保险丝 (8)1.5环境 (8)1.6使用测试夹具 (9)1.7预热 (9)1.8仪器的其它特性 (9)第2章前面板说明及入门操作 (10)2.1前面板说明 (10)2.2后面板说明 (11)2.3显示区域的定义 (12)2.4按键及其相应的显示页面 (13)2.4.1测量主菜单按键【DISP】 (13)2.4.2系统设置主菜单按键【SETUP】 (13)2.5基本操作 (13)2.6开机 (14)第3章基本操作 (15)3.1<测量显示>页面 (15)3.1.1测试功能 (15)3.1.2测试量程 (16)3.1.3测试速度 (17)3.1.4文件管理 (17)3.1.5其他工具 (17)3.2<比较显示>页面 (18)3.2.1文件管理 (19)3.2.2工具 (19)3.2.3比较 (19)3.2.4比较模式和上下限、百分比误差设置 (19)3.3<档显示>页面 (19)3.4<统计显示>页面 (21)3.4.1边界模式和其相应值的设定 (21)3.4.2统计状态 (21)3.4.3统计分析参数说明 (21)3.4.4工具 (22)3.4.5文件 (22)3.5<测量设置>页面 (22)3.6<TC/Δt设置>页面 (24)3.6.1温度校正(Temperature Correction 简称TC) (25)3.6.2温度转换(temperature conversion 简称t ) (25)3.6.3温度传感器的类型 (26)3.6.4参数设定 (27)3.6.5文件 (27)3.7<档设置>页面 (27)3.7.1文件 (29)3.7.2工具 (29)第4章系统设置和文件管理 (30)4.1系统设置 (30)4.1.1触摸音 (30)4.1.2语言 (30)4.1.3口令 (31)4.1.4总线模式 (31)4.1.5波特率 (32)4.1.6总线地址 (32)4.1.7EOC信号 (32)4.1.8Err.OUT信号 (33)4.1.9电源频率 (34)4.1.10时间和日期设定 (34)4.2<文件管理>功能页面 (34)4.2.1存储/调用功能简介 (34)4.2.2U盘上的文件夹/文件结构 (35)4.2.3DHCP (39)4.2.4IP地址 (40)4.2.5子网掩码 (40)4.2.6网关 (40)4.2.7首选DNS、备用DNS (40)第5章性能指标 (41)5.1测量功能 (41)5.1.1测量参数及符号 (41)5.1.2测量组合 (41)5.1.3等效方式 (41)5.1.4量程 (41)5.1.5触发 (41)5.1.6测试端方式 (41)5.1.7测量中的各种时间的开销 (41)5.1.8平均 (42)5.1.9显示的位数 (42)5.2测试信号 (42)5.2.1量程电流 (42)5.2.2开路输出电压 (42)5.2.3测量显示最大范围 (42)5.3测量准确度 (43)5.3.2温度测量的准确度(Pt500) (44)5.3.3温度测量的准确度(模拟输入) (45)5.3.4温度修正系数K (45)第6章远程控制 (46)6.1RS232C接口说明 (46)6.2GPIB接口说明(选购件) (47)6.2.1GPIB接口功能 (49)6.2.2GPIB 地址 (49)6.2.3GPIB总线功能 (49)6.2.4可编程仪器命令标准(SCPI) (50)6.3LAN远程控制系统 (50)6.3.1通过浏览器访问TH2515 (52)6.3.2通过上位机软件访问TH2515 (52)6.4USBTMC远程控制系统 (53)6.4.1系统配置 (53)6.4.2安装驱动 (53)6.5USBVCOM虚拟串口 (54)6.5.1系统配置 (54)6.5.2安装驱动 (54)第7章RS232命令参考 (55)7.1SCPI系统命令 (55)7.1.1DISPlay子系统命令集 (55)7.1.2FUNCtion 子系统命令集 (56)7.1.3APERture子系统命令集 (61)7.1.4TRIGer子系统命令集 (61)7.1.5FETCh?子系统命令集 (63)7.1.6TEMPerature子系统命令集 (64)7.1.7COMParator子系统命令集 (66)7.1.8BIN子系统命令集 (69)7.1.9STA Tistics子系统命令集 (73)7.1.10IO子系统命令集 (76)7.1.11MEMory子系统命令集 (77)7.1.12SYSTem 子系统命令集 (78)7.1.13SCPI公用命令 (81)7.2MODBUS系统命令 (83)7.2.1MODBUS协议说明 (84)7.2.2公用指令操作说明 (85)7.2.3DISP指令操作说明 (86)7.2.4FUNC指令操作说明 (86)7.2.5APER指令操作说明 (87)7.2.6TRIG指令操作说明 (87)7.2.7FETC指令操作说明 (88)7.2.8TEMP指令操作说明 (88)7.2.10BIN指令操作说明 (90)7.2.11STA T指令操作说明 (93)7.2.12IO指令操作说明 (94)7.2.13SYST指令操作说明 (94)第8章Handler接口使用说明及程序升级方法 (99)第9章包装及保修 (103)9.1标志 (103)9.2包装 (103)9.3运输 (103)9.4贮存 (103)9.5保修 (103)本说明书所描述的可能并非仪器所有内容,同惠公司有权对本产品的性能、功能、内部结构、外观、附件、包装物等进行改进和提高而不作另行说明!由此引起的说明书与仪器不一致的困惑,可通过封面的地址与我公司进行联系。
QTM-500快速导热系数测定仪 说明书
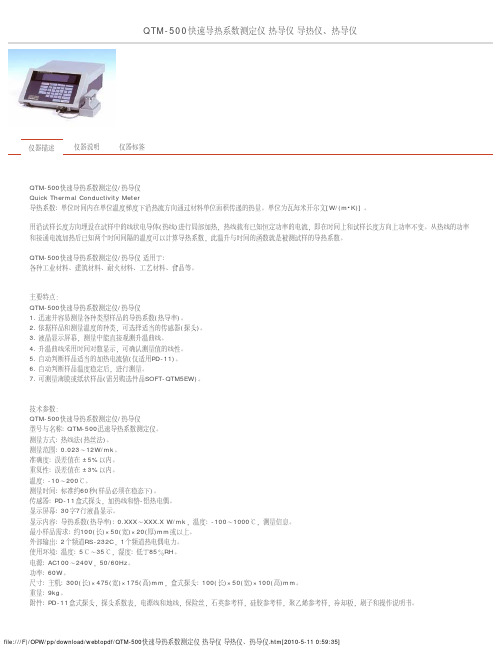
QTM-500快速导热系数测定仪热导仪导热仪、热导仪仪器描述仪器说明仪器标签QTM-500快速导热系数测定仪/热导仪Quick Thermal Conductivity Meter导热系数: 单位时间内在单位温度梯度下沿热流方向通过材料单位面积传递的热量。
单位为瓦每米开尔文[W/(m•K)] 。
用沿试样长度方向埋设在试样中的线状电导体(热线)进行局部加热,热线载有已知恒定功率的电流,即在时间上和试样长度方向上功率不变。
从热线的功率和接通电流加热后已知两个时间间隔的温度可以计算导热系数,此温升与时间的函数就是被测试样的导热系数。
QTM-500快速导热系数测定仪/热导仪适用于:各种工业材料、建筑材料、耐火材料、工艺材料、食品等。
主要特点:QTM-500快速导热系数测定仪/热导仪1. 迅速并容易测量各种类型样品的导热系数(热导率)。
2. 依据样品和测量温度的种类,可选择适当的传感器(探头)。
3. 液晶显示屏幕,测量中能直接观测升温曲线。
4. 升温曲线采用时间对数显示,可确认测量值的线性。
5. 自动判断样品适当的加热电流値(仅适用PD-11)。
6. 自动判断样品温度稳定后,进行测量。
7. 可测量薄膜或纸状样品(需另购选件品SOFT-QTM5EW)。
技术参数:QTM-500快速导热系数测定仪/热导仪型号与名称: QTM-500迅速导热系数测定仪。
测量方式: 热线法(热丝法)。
测量范围: 0.023~12W/mk。
准确度: 误差值在 ±5%以内。
重复性: 误差值在 ±3%以内。
温度: -10~200℃。
测量时间: 标准约60秒(样品必须在稳态下)。
传感器: PD-11盒式探头,加热线和铬-铝热电偶。
显示屏幕: 30字7行液晶显示。
显示内容: 导热系数(热导率): 0.XXX~XXX.X W/mk,温度: -100~1000℃,测量信息。
最小样品需求: 约100(长)×50(宽)×20(厚)mm或以上。
GEA Avapac连续热焊机 HS 500 HS 1000 HS 1200说明书

GEA Process EngineeringHS 500 / HS 1000 / HS 1200Heat Sealersengineering for a better worldHeat Sealers HS 500 / HS 1000 / HS 1200 OverviewGEA Avapac continuous heat sealers are designed to close a widerange of bags used in dairy and food ingredient plants.The bag is levelled as it enters the sealer which eliminates theneed for cutting and resulting wastage. Auto-levelling (availableon HS 1200 and HS 1000) allows for a fully automated baghandling process from bag filling through to palletising.The internal liner is sealed by application of heat, and is then scoredwithout damage to the outer paper to form a free floatinginternal pouch within the bag. This pouch can be easily removedand passed into a hygienic environment avoiding exposureof the product to contaminants or unfiltered air.The outer paper bag is then folded and closed by re-activation of thepre-glued strip. Options for alternative bag closure methodsincluding sewing and taping are available.Fold-Over SystemReactivates the pre-appliedglue strip and closes theouter paper liner of the bag. All performance data achieved under test conditions with standard packaging materials.All specifications and dimensions subject to revision without notice.Design Objectives• To be integrated in fully automated bag packinglines or, alternatively to work as a stand-alone unit using an operator interface• Avoid bag trimming• Handle a wide range of bag sizes and types• Provide a robust and reliable inner linerseal and high quality closing function• Compliance with hygiene standards• Provide integrated and extensible control forother equipment in a bag handling plant• Ease of operation and maintenance Features• Manual or powered height adjustmentfor a wide range of bag lengths• Automatic bag top levelling (HS 1000 & HS 1200)• Bag mouth cleaning and dust extraction prior to sealing • Heat sealing and Scoring of the inner liner• Automatic closing of step-top bags• Quick-release systems for heating and scoring parts • Extensible PLC control for additional line components Standards(a) EU Directives and their harmonized standards:• Machinery 2006/42/EC;• “ATEX” 94/9/EC;• Electromagnetic compatibility 2004/108/EC;• Pressure equipment 97/23/EC;• Hygiene EHEDG Guidelines; andcompliance with 1935/2004/EC(b) US standards covering:• Hygiene USDA Guidelines; FDA Codes ofFederal Regulations - (CFR series 21)• Machine Safety OSHA 1910 Subparts O&S; ANSI B11.19;ANSI/PMMI B155.1; NFPA 70 & 79; ANSI/ISA 12.10.05Bag requirements• Length = 750-950mm, width = 500-600mm• Multi-wall Kraft paper bags with PE internalliner and pre-applied glue strip• Bag over powder = 250-300mm (bag width dependent)Integrated ControlsOptional stand-alone controlor fully integrated to anautomated packing system.Heat SealingMultiple stage sealing andscoring to provide hermeticclosure of inner plastic liner.Height AdjustableManual handwheel ormotor driven system toadjust sealer height forvariable bag lengths.Seal CleaningEliminates powder fromthe seal area to ensurereliable hermetic sealing.Automatic LevellingEnsuring that the top fold closureis parallel to the top of the bag.© G E A G r o u p A G . A l l r i g h t s r e s e r v e d .GEA Group is a global engineering company with m ulti-billion euro sales and o perations in more than 50 countries. Founded in 1881, the company is one of the largest providers of i nnovative equipment andp rocess technology. GEA Group is listed in the STOXX® Europe 600 Index.We live our values.Excellence • Passion • Integrity • Responsibility • GEA-versityGEA Avapac Ltd.12-18 Foreman Road, PO Box 10266, Te Rapa, Hamilton 3241, New ZealandTel: +64 7 849 3414, Fax: +64 7 849 3494**********************GEA Nu-Con Ltd.8 Fisher Crescent, Mt Wellington, PO Box 12-264, Penrose, Auckland 1642, New ZealandTel: +64 9 276 2388, Fax: +64 9 259 0172**********************GEA Process Engineering B.V.Munsterstraat 5, 7418 EV DeventerPostbus 2064, 7420 AB Deventer, Netherlands Tel: +31 570 663 366, Fax: +31 570 663 377********************GEA Process Engineering Inc.1600 O’Keefe Road, Hudson, Wisconsin 54016, United States of AmericaTel: +1 715 386 9371, Fax: +1 715 386 9376*****************。
Omega K-56KU高精度热电压测量仪说明书

U 0.3°C (0.5°F) Accuracy from 18 to 28°C (64 to 82°F)U NIST-TraceableCertificate of Calibration (No Points)U Simulates and Measures Thermocouples, RTDs, Thermistors, and ΩU 0.1°C/°F Resolution U 10 Memory Locations for Saving Meter Readings orCalibrator OutputsU Step Calibrator, Meter Hold, Thermometer FunctionsU Ramp Function(Models CL25 and CL27)High-Precision HandheldNo PointsOMEGACARE SM extended warranty program is available for models shown on this page. Ask your sales representative for full detailswhen placing an order. OMEGACARESMcovers parts, labor and equivalent loaners.S i m u l a t e s , M e a s u r e s , a n d R e c o r d s T h e r m o c o u p l e , R T D , T h e r m i s t o r , a n d R e s i s t a n c e S i g n a l s —A ll i n O n e Me t e r !CL25The OMEGA ® CL20 handheldcalibrators/thermometers simulate, measure, and record RTD, Ω, thermocouple, and thermistor signals—all in one. Featuring an accuracy of 0.3ºC (0.5ºF) at ambient temperatures from 18 to 28ºC (64 to 82ºF) and a host of powerful keypad functions, these low-cost meters outperform the competition.The 5-digit LCD indicates all active functions and has 0.1ºC/ºF resolution. Operating mode and sensor type are also displayed.Programming is a snap. The user can enter setpoints directly on the keypad or from an outside source. Ten memory locations allow for instant recall of any programmed value, and the step function lets the user navigate the test points with the push of a button.The ramp function of theCL25 and CL27 makes calibration easy. When the user enters the upper limit, lower limit, and step size, the meter automatically ramps between the limits. Ramping can also be performed manually.No matter what the input type, one of these meters can handle it. The possibilities include 100 and 1000 W RTDs and 2252 W transistors.88000 Series probe, sold separately, visit /88000_hightempPR-16 RTD handle probe, sold separately, visit /pr-16Display: 5-digit LCD; custom indicators for calibration type; units hold, recall, store, operating mode, bal, loaded memory locations (up to 10)Keypad: Momentary switches with tactile feedback, select power, thermocouple type, units, resolution, hold, store/recall (up to 10), stop/clear, operating modeConfiguration Retention: Selected operating mode,thermocouple type, units, resolution and memory contents retained on power-offDiagnostics: Low battery, open input, invalid keypad entry, out of range, internal hardware faultAccuracy: See “To Order” chart on next page for detailsAmbient Temperature: 0 to 50°C (32 to 122°F), 0 to 90% RH Reading Rate: 1/sInput Current: 50 nA typical (meter mode)Output Load: 100 Ω, min (calibrator mode)Max Common-Mode Voltage: 42V peak to earth ground Power: 9V alkaline battery (included)Battery Life: 16 hr on alkaline batteryDimensions: 178 H x 74 W x 28 mm D (7.0 x 2.9 x 1.1")Weight: 340 g (12 oz)CL25CL24CL26CL23AAll models shown smaller than actual size.** Insert Type J, K, T, or E.CL26 and CL27 Resistance Measurement CL20 Series Temperature MeasurementCL27 shown smaller than actual size.Rugged carrying case.RTD andresistance cables.Beaded wire probe.standard to mini thermocouple adaptors.Belt clip.TA4F RTD adaptor.Comes withintegral tilt stand/ handle, wrist strap and shock-resistant holster.Type J, K, T, E thermocouple calibration cable.sQ u i c k l y a n d a c c u r a t el yc a l i b r a t e s p an e l m e t e r s ,c o n t r o l l e r s , t r a ns m i t t e r s , R T D s ,a n d o t h e r t h e r m o c o u p l ei n p u t d e v i ce sOrdering Examples: CL24, J/K/T/E calibration/thermometer kit.CL26, J/K/T/E, thermistor and RTD calibration/thermometer kit. OCW-2, OMEGACARE SM extends standard 3-year warranty to a total of 5 years.。
RTP-500型快速热处理设备操作简要

RTP-500型快速热处理设备操作简要
◆安装
✧准备电源三根火线一根零线
40A空开或者加25A插座(电缆及插头有厂方配备)
✧准备水源循环水或者自来水管
水管内径12mm
开机时水的流量不宜太大,指示灯亮后即可。
✧试机前打开电源箱和炉体箱
检查电路元件有无松动,检查气路安装是否完好,线头、螺母螺钉有无松动,有问题的重新安装加固。
✧安装水管,电源,气路即可
◆开机
依次打开下列开关
✧打开计算机
✧MAIN POWER
✧POWER钥匙开关
✧FAN 炉体风扇开关
✧WATER 电磁阀开关
✧水源开关(水龙头)
✧RUN
◆试验
✧根据试验温度试温加热,测试温度是否正常。
✧操作程序设定参数,执行程序。
选择和设定程序,
点击
显示
室温显示正常,再点击Star
Evreything is ready
ok
即可。
✧温度在100℃左右,放入试验物品,合上炉门,缓缓的通入保护气体,是流量计
的浮子缓缓的上升到2L/min左右。
严禁气体流量超过2.5L./min。
执行试验程序。
✧程序结束后,合适的温度可以将样品取出,保护气体可根据试验随时关闭打开流量
计。
✧可以进行重复试验。
✧紧急关机点击程序右上角
或者关闭RUN
◆程序设定参考
第一段20s 升到200℃保持60----120s 预热段
第二段5—10s 升到目标温度保持需要的时间升温段
第三段10s 降到100℃保持30---60s 降温段。
TA Instruments Q1000和Q100热分析仪商品介绍说明书

LIQUID NITROGEN COOLING SYSTEM
The Liquid Nitrogen Cooling System (LNCS) provides the highest performance and greatest flexibility in cooling. It has the lowest operational temperature (to -180 °C), greatest cooling rate capacity (to 140 °C/min), and an upper temperature limit of 550 °C. It is ideal for isothermal crystallization studies. The LNCS uses liquid nitrogen efficiently, thus reducing operating costs. Its autofill capability allows the LNCS to be automatically refilled from a larger liquid nitrogen source for continuous DSC operation. The LNCS is available for the Q1000, Q100, and Q10 DSC modules.
ONLY 2 AVAILABLE
Q SERIES™ ACCESSORIES
4
THERMOGRAVIMETRIC ANALYZERS - DEMO INVENTORY
Q500
Q50
Prices starting at
17.000£
HDM-500恒温电热套和恒温电热套价格

标题:ZNHW-Ⅱ电热套
电热套PTHW型普通恒温电热套该系列型电热套根据联合国教科文组织“环境与人类”赠于我国的英国产品改进而成,它用无碱玻璃纤维作绝缘材料,将镊铬合金丝簧状置于其中为加热源,用轻质保温棉高压定形的半球形保温体保温,外壳用一次性高温塑料制成,上盖采用静电喷塑工艺,用大功率可控硅控温,具有外形美观、重量轻、恒温控制,形状标准,经久耐用的特点。ZNHW型智能恒温电热套该电热套采用PID智能操作控制,热电偶感温,可控硅控制输出,单键快速升降温度设定模式,设定、控制双排数字显示,并设有断偶保护功能。当设定好所需温度后,微电脑将根据温度差自动调整升温速度,通过间断供电,比例调节,快速达到最佳升温效果,使之无温冲,400℃内±1℃...
厂家:南北标题:ZNHW型电热套
电热套PTHW型普通恒温电热套该系列型电热套根据联合国教科文组织“环境与人类”赠于我国的英国产品改进而成,它用无碱玻璃纤维作绝缘材料,将镊铬合金丝簧状置于其中为加热源,用轻质保温棉高压定形的半球形保温体保温,外壳用一次性高温塑料制成,上盖采用静电喷塑工艺,用大功率可控硅控温,具有外形美观、重量轻、恒温控制,形状标准,经久耐用的特点。ZNHW型智能恒温电热套该电热套采用PID智能操作控制,热电偶感温,可控硅控制输出,单键快速升降温度设定模式,设定、控制双排数字显示,并设有断偶保护功能。当设定好所需温度后,微电脑将根据温度差自动调整升温速度,通过间断供电,比例调节,快速达到最佳升温效果,使之无温冲,400℃内±1℃...
厂家:南北套
标题:TP-380智能磁力电热套
Omega Engineering OMEGATHERM 201 高热导率硅胶说明书

OT-201OMEGATHERM®Thermally Conductive Silicone PasteIntroductionOMEGATHERM®201 is a thermally conductive, “Heat Sink”silicone grease. It has a very high thermal conductivity coupled with high insulation resistance and high dielectric strength. The term heat sink compound or thermal joint compound is used to describe this type of material. It does not harden on long exposure to elevated temperatures, but retains its past-like consistency. It is rated for continuous use between -40°F and +392°F (40°C and 200°C). OMEGATHERM®is available in four quantity sizes, from a 1⁄2oz. jar to a 2 lb. can, as outlined below.OMEGATHERM 201 provides an excellent means of conducting heat and expanding the heat-path area from a surface to a temperature measurement sensor, thus increasing the speed of response and improving accuracy. OMEGATHERM 201 improves the heat transfer between a solid state relay and its finned heat dissipating heat sink. Apply a thin layer of “201” thermal compound to the bottom of the solid state relay (SSR), then securely mount the SSR on the finned heat sink with the supplied screws.Instructions for UseAlthough OMEGATHERM 201 does not normally settle in its container, storage for long periods of time at elevated temperature may result in a slight separation of the conductive fillers from the silicone oil. If this condition is seen to exist, the fillers may be easily mixed by hand or mechanical mixing.OMEGATHERM 201 may be dispensed through a nozzle using any appropriate hand operated or automatic equipment. For some applications, it will be convenient to apply thin films with a stiff brush.To CLEAN OT-201 from surfaces, use a solvent containing Alcohol, MEK, or Xylene. Repeated use is required to completely clean silicon grease from surface.ApplicationsA. Surface Measurement Probes-dab a small amount on thesurface and push the thermocouple into this area.B. Temporary Temperature Monitoring of Surfaces and Bodies-For applications to 392°F (200°C). OT-201 workswell with insulated wire thermocouples. Simply dab this paste on the surface or into a cavity, put the sensor in the paste, and tape to hold.C. Thermocouple Wells (to 200°C)-improve the response timeof your thermowell assemblies. Simply put enoughOMEGATHERM 201 into the bottom of the wells to cover the active length of the sensor. This application holds for vertical wells or those canted down.D. NOT FOR USE IN A VACUUM. OT-201 will outgas if usedin a vacuum.HygieneMAY CAUSE IRRITATION.1. Avoid contact with skin and eyes.2. Wash thoroughly after handling.First Aid1.In case of contact, wash skin thoroughly with soap and water.2. For eyes, flush with water for 15 minutes and consult physician immediately.FOR INDUSTRIAL USE ONLY.Typical PropertiesColor:Off-whiteTemperature Range of Use:-40°to +392°F(40°to +200°C) Consistency:Thick, smooth pasteVolume Resistivity:1014ohm-cmDielectric Strength:500 volts/mil (19.7 kv/mm) Thermal Conductivity:16 (BTU) (in)/(hr) (ft2) (°F)0.0055 (cal)/(cm)/(sec)(cm2) (°C)Specific Gravity: 2.53 g/ccWeight Loss:0.2% (24 hours/100°CShelf life: 1 Year (Storage at 35°F orbelow will approximatelydouble the shelf life). Solvents:Alcohol or MEK or XyleneSolventsThis information is not a warranty and assumes no legal responsibility. Actual suitability for a particular purpose is to be determined by the user.M0066/1104It is the policy of OMEGA Engineering, Inc. to comply with all worldwide safety and EMC/EMI regulations that apply. OMEGA is constantly pursuing certification of its products to the European New Approach Directives. OMEGA will add the CE mark to every appropriate device upon certification.The information contained in this document is believed to be correct, but OMEGA accepts no liability for any errors it contains, and reserves the right to alter specifications without notice.WARNING: These products are not designed for use in, and should not be used for, human applications.WARRANTY/DISCLAIMEROMEGA ENGINEERING, INC. warrants this unit to be free of defects in materials and workmanship for a period of 13 months from date of purchase.OMEGA’s WARRANT Y adds an additional one (1) month grace period to the normal one (1) year product warranty to cover handling and shipping time. This ensures that OMEGA’s customers receive maximum coverage on each product.If the unit malfunctions, it must be returned to the factory for evaluation. OMEGA’s Customer Service Department will issue an Authorized Return (AR)number immediately upon phone or written request. Upon examination by OMEGA, if the unit is found to be defective, it will be repaired or replaced at no charge. OMEGA’s WARRANTY does not apply to defects resulting from any action of the purchaser, including but not limited to mishandling,improper interfacing, operation outside of design limits, improper repair, or unauthorized modification. This WARRANTY is VOID if the unit shows evidence of having been tampered with or shows evidence of having been damaged as a result of excessive corrosion; or current, heat, moisture orvibration; improper specification; misapplication; misuse or other operating conditions outside of OMEGA’s control. Components in which wear is not warranted, include but are not limited to contact points, fuses, and triacs.OMEGA is pleased to offer suggestions on the use of its various products. However, OMEGA neither assumes responsibility for any omissions or errors nor assumes liability for any damages that result from the use of its products in accordance with information provided by OMEGA, either verbal or written. OMEGA warrants only that the parts manufactured by the company will be as specified and free of defects. OMEGA MAKES NO OTHER WARRANTIES OR REPRESENTATIONS OF ANY KIND WHATSOEVER, EXPRESSED OR IMPLIED, EXCEPT THAT OF TITLE, AND ALL IMPLIED WARRANTIES INCLUDING ANY WARRANTY OF MERCHANTABILITY AND FITNESS FOR A PARTICULAR PURPOSE ARE HEREBY DISCLAIMED. LIMITATION OF LIABILITY : The remedies of purchaser set forth herein are exclusive, and the total liability of OMEGA with respect to this order, whether based on contract, warranty, negligence, indemnification, strict liability or otherwise,shall not exceed the purchase price of the component upon which liability is based. In no event shall OMEGA be liable for consequential,incidental or special damages.CONDITIONS: Equipment sold by OMEGA is not intended to be used, nor shall it be used: (1) as a “Basic Component” under 10 CFR 21 (NRC), used in or with any nuclear installation or activity; or (2) in medical applications or used on humans. Should any Product(s) be used in or with any nuclear installation or activity, medical application, used on humans, or misused in any way, OMEGA assumes no responsibility as set forth in our basic WARRANT Y/DISCLAIMER language, and, additionally, purchaser will indemnify OMEGA and hold OMEGA harmless from any liability or damage whatsoever arising out of the use of the Product(s) in such a manner.Servicing North America:U.S.A.:One Omega Drive, Box 4047ISO 9001 CertifiedStamford, CT 06907-0047Tel: (203) 359-1660FAX: (203) 359-7700e-mail:**************Canada:976 BergarLaval (Quebec) H7L 5A1, Canada Tel: (514) 856-6928FAX: (514) 856-6886e-mail:*************For immediate technical or application assistance:U.S.A. and Canada:Sales Service: 1-800-826-6342 / 1-800-TC-OMEGA ®Customer Service: 1-800-622-2378 / 1-800-622-BEST ®Engineering Service: 1-800-872-9436 / 1-800-USA-WHEN ®TELEX: 996404 EASYLINK: 62968934 CABLE: OMEGAMexico:En Espan ˜ol: (001) 203-359-7803e-mail:*****************FAX: (001) 203-359-7807**************.mxOMEGAnet ®Online Service Internet e-mail***********************Servicing Europe:Benelux:Postbus 8034, 1180 LA Amstelveen, The Netherlands Tel: +31 (0)20 3472121FAX: +31 (0)20 6434643Toll Free in Benelux: 0800 0993344e-mail:*****************Czech Republic:Frystatska 184, 733 01 Karviná, Czech Republic Tel: +420 (0)59 6311899FAX: +420 (0)59 6311114Toll Free: 0800-1-66342e-mail:*****************France:11, rue Jacques Cartier, 78280 Guyancourt, France Tel: +33 (0)1 61 37 2900FAX: +33 (0)1 30 57 5427Toll Free in France: 0800 466 342e-mail:**************Germany/Austria:Daimlerstrasse 26, D-75392 Deckenpfronn, GermanyTel: +49 (0)7056 9398-0FAX: +49 (0)7056 9398-29TollFreeinGermany************e-mail:*************United Kingdom:One Omega Drive, River Bend Technology CentreISO 9002 CertifiedNorthbank, Irlam, Manchester M44 5BD United Kingdom Tel: +44 (0)161 777 6611FAX: +44 (0)161 777 6622Toll Free in United Kingdom: 0800-488-488e-mail:**************.ukRETURN REQUESTS /INQUIRIESDirect all warranty and repair requests/inquiries to the OMEGA Customer Service Department. BEFORE RETURNING ANY PRODUCT (S) T OOMEGA, PURCHASER MUST OBTAIN AN AUTHORIZED RETURN (AR) NUMBER FROM OMEGA’S CUSTOMER SERVICE DEPARTMENT (IN ORDER T O AVOID PROCESSING DELAYS). T he assigned AR number should then be marked on the outside of the return package and on any correspondence.The purchaser is responsible for shipping charges, freight, insurance and proper packaging to prevent breakage in transit.FOR WARRANTY RETURNS, please have the following information available BEFORE contacting OMEGA:1.Purchase Order number under which the product was PURCHASED,2.Model and serial number of the product under warranty, and3.Repair instructions and/or specific problems relative to the product.FOR NON-WARRANTY REPAIRS,consult OMEGA for current repair charges.Have the following information available BEFORE contacting OMEGA:1. Purchase Order number to cover the COST of the repair,2.Model and serial number of the product, and3.Repair instructions and/or specific problems relative to the product.OMEGA’s policy is to make running changes, not model changes, whenever an improvement is possible. T his affords our customers the latest in technology and engineering.OMEGA is a registered trademark of OMEGA ENGINEERING, INC.© Copyright 2004 OMEGA ENGINEERING, INC. All rights reserved. This document may not be copied, photocopied, reproduced, translated, or reduced to any electronic medium or machine-readable form, in whole or in part, without the prior written consent of OMEGA ENGINEERING, INC.。
史密斯Level1温毯机介绍

版 权 所有2011 2009Smiths SmithsMedical Medical : 专 有 数 据 ©© 版 权 所有 : 专 有 数 据
对流加温 – Snuggle Warm® 加温毯
SW-2003
上半身式加温毯
大号 布单宽度较大 确保最大程度地覆盖所有身材的患者 可作为全身式加温毯用在手术前或手术后, 无需拴系 不会软化 ET 管 易于接触静脉输液部位 增强患者的舒适度 无需拴系
版 权 所有2011 2009Smiths SmithsMedical Medical : 专 有 数 据 ©© 版 权 所有 : 专 有 数 据
• Equator® 对流加温器 (EQ-5000)
操作简单
专业 精确
4 个温度设置点 软管末端温度控制
能够选择适合患者的温度 自动调节以提供选定的温度,不受环境限制
对流加温效果对比
EQUATORⓇ 加温器 (EQ-5000) 和 SW-2004
其他品牌
版 权 所有2011 2009Smiths SmithsMedical Medical : 专 有 数 据 ©© 版 权 所有 : 专 有 数 据
对流加温 - Snuggle Warm® 加温毯
SW-2001
对流加温 – Snuggle Warm® 加温毯
SW-2007
管式加温毯
“U”形 加温时可无障碍地接触患者
各种孔尺寸
确保热量分布均匀
仿织物材质
增强患者的舒适度
可用在导管室中,或配上布单,在手术中用作 BH 底垫式加温毯的代用 品
版 权 所有2011 2009Smiths SmithsMedical Medical : 专 有 数 据 ©© 版 权 所有 : 专 有 数 据
qtm-500快速热导仪原理

qtm-500快速热导仪原理
QTM-500快速热导仪是一种用于测量材料热导率的仪器。
其工作原理基于热传导定律和热电效应。
快速热导仪的测量原理如下:
1. 热传导定律:根据热传导定律,热量会沿着温度梯度从高温区域传导到低温区域。
热导仪利用这一原理,通过测量材料内部的温度梯度和传导热量来计算材料的热导率。
2. 热电效应:快速热导仪采用热电偶的测温原理。
热电偶是由两种不同金属组成的导线,当两种金属接触处存在温度差异时,会产生热电势差。
利用热电偶的温度差测量能力,可以测量材料内部的温度梯度。
3. 实验过程:在测量过程中,快速热导仪会将热量从一个加热器传导到待测材料样品上。
加热器通常是由高导热材料制成的,可快速向待测样品释放热量。
样品的一个表面接触着加热器,而另一个表面接触着冷却器。
通过热电偶测量样品的两个表面温度,再根据热传导定律推导出材料的热导率。
总结起来,QTM-500快速热导仪利用热传导定律和热电效应,通过测量材料内部的温度梯度和传导热量来计算材料的热导率。
KAM-500数据采集遥测系统及在旋翼系统载荷测试中的应用

收稿日期:2002-05-21作者简介:巫景燕(1974—),女,江西人,在职硕士研究生,研究方向为信号检测与处理;刘福华(1957—),男,江西人,研究员;杨纯葆(1941—),男,研究员。
文章编号:1000-8829(2003)01-0022-02KAM-500数据采集遥测系统及在旋翼系统载荷测试中的应用KAM-500System and lts Application in the Measurement of Rotor System(南京航空航天大学信息工程学院,江苏南京210016)巫景燕(中国直升机设计研究所,江西景德镇333001)刘福华(北京约克公司,北京100081)杨纯葆摘要:针对直升机旋翼测试的特点,详细介绍了KAM-500数据采集遥测系统的性能和功能,以及该系统在直升机旋翼测试中的实际应用。
关键词:KAM-500;数据采集遥测系统;直升机旋翼测试中图分类号:TP274文献标识码:BAbstract:The specifications and functions of KAM-500sys-tem are introduced.And its appiication in the measurement of rotor system is described in detaii.Key words:KAM-500;teiemetry system;measurement of ro-tor system旋翼系统是直升机中最关键的部分,所以在直升机研制过程中,旋翼系统各部件的载荷测试尤为重要。
传统的测试方法是通过集流环(siip ring )将旋翼系统上的旋转信号引出,再通过有线传输的方式进入机舱或地面实验间的数据采集系统,这种方法在国内外的直升机地面和飞行试验中得到了广泛的应用。
但在地面试验中,如果现场距实验间的距离过长,或者在飞行试验中因为机械的原因无法安装集流环的情况下,这种方法的效果就不是很好或根本无法实施。
KEM快速热导仪QTM -500

1个
R3-2 盒装聚乙烯
1个
6) 冷却板
1个
7) 刷子
1个
8) 操作说明书
1个
●薄片测量
上海今昊:Tel. 021-20230210 Fax. 021-20230210 Email: jojoanswer@
过, 下图的弯曲曲线表明,样品表面的瞬时导热情况。
测量结果分析 在测量结束后,立即显示测量结果。
Hale Waihona Puke 其它可选件DP-500打印机 可打印样品编 号,热导率和温 度.
.
测量结果中温度变化可以通过线性线对时间的求对数来 确定。
粉体测量箱 QTM-PA1 粉体样品可通过QTM-PA1 PD-11探头测量
上海今昊:Tel. 021-20230210 Fax. 021-20230210 Email: jojoanswer@
jojoanswerhotmailcom探头盒式探头pd11标配绝缘防湿探头pd13可选件适用于食品混凝土等含水或导电材料其它可选件dp500打印机可打印样品编号热导率和温粉体测量箱qtmpa1粉体样品可通过qtmpa1pd11探头测量液晶显示开始测量当按下开始键时电热丝就有不变的电压流通下图的弯曲曲线表明样品表面的瞬时导热情况
1) 名称:箱式探头 PD-11
2) 加热线: 3) 热电偶
设定值为±0.05%
1) 30 字符 7 线液晶暗光
2) 内容:
热传导率:0.XXXX~XXX.XW/mk 测定温度:-100—1000℃
测定标准
100W×50L×20H 以上
1) RS-232C :2 个通道
2) 热电偶发电:1 个通道
1) 温度:5~35℃ 2) 相对湿度:85%RH 以上
- 1、下载文档前请自行甄别文档内容的完整性,平台不提供额外的编辑、内容补充、找答案等附加服务。
- 2、"仅部分预览"的文档,不可在线预览部分如存在完整性等问题,可反馈申请退款(可完整预览的文档不适用该条件!)。
- 3、如文档侵犯您的权益,请联系客服反馈,我们会尽快为您处理(人工客服工作时间:9:00-18:30)。
●标准材料测量
QTM-500技术参数
测定方法 测定范围 测定精度 再现性 测定时间
传感器 加热电流精度
表示机能
样品最低范围 外部输出 使用环境 电源 电力消耗 尺寸 重量
供 应件
细线加热法
0.023~12W/mk
误差值在 5%以内
误差值在 3%以内
标准时间为 60 秒 (但样品必须在平衡状态下进行)
上海今昊科学仪器有限公司
KEM 快速热导仪 QTM-500
探头传感器可适合您所有的应用要求! 只需一台热导仪即可测量各种样品材料的热导率!
QTM500 可以快速、容易地测量许
多种样品。只需在热平衡的样品表面 粘上传导探头,然后按一下开始键, 检测结果就可以在 60 秒中显示出来。
测量原理
探头由单热线和热电偶组成。 当不变的电(压、流)加在电热丝上时,电热丝的温度会以指数 的形式上升。 温度上升曲线被绘制,线性线在下图中,时间轴刻度以对数表示。 如果样品具有低的热导率,线的角度就大,反之高热导率角度就 小。由此,热导率就可以通过角度的变化而得出。
上海今昊科学仪器有限公司
SOFT-QTM5EW
用于测量薄片热导率的软件(可选件) 典型应用 QTM-500热导仪与安装了 SOFT-QTM5EW 软件的个人计算机 (Windows® 95)联用,可测橡皮, 塑料,陶瓷,纸张,纺织物,木材等 均质材料的薄膜、薄片、薄板等结构 的热导率。 样品厚度 30µm~10mm厚度的薄片结构 测量范围 0.035~5.0w/m K
1个
R3-2 盒装聚乙烯
1个
6) 冷却板
1个
7) 刷子
1个
8) 操作说明书
1个
●薄片测量
上海今昊:Tel. 021-20230210 Fax. 021-20230210 Email: jojoanswer@
1)AC100~240V 2)50Hz/60Hz
约 60W
1) 主体:300W×475D×175Hmm
2) 箱式探头:100W×50D×100Hmm
约9克
1) PD-11 箱式探头:
1个
2) 探头定数表:
1枚
3) 带线电源:
1付
4) 电源保险丝:
2个
5) 附带:R1-2 盒装透明石英
1个
R2-2 盒装硅橡胶
上海今昊:Tel. 021-20230210 Fax. 021-20230210 Email: jojoanswer@
上海今昊科学仪器有限公司
探头
盒式探头PD1“开始”键时,电热丝就有不变的电(压、流)通
绝缘防湿探头PD13(可选件)
适用于食品、混凝土等含水或导电材料
1) 名称:箱式探头 PD-11
2) 加热线: 3) 热电偶
设定值为±0.05%
1) 30 字符 7 线液晶暗光
2) 内容:
热传导率:0.XXXX~XXX.XW/mk 测定温度:-100—1000℃
测定标准
100W×50L×20H 以上
1) RS-232C :2 个通道
2) 热电偶发电:1 个通道
1) 温度:5~35℃ 2) 相对湿度:85%RH 以上
过, 下图的弯曲曲线表明,样品表面的瞬时导热情况。
测量结果分析 在测量结束后,立即显示测量结果。
其它可选件
DP-500打印机 可打印样品编 号,热导率和温 度.
.
测量结果中温度变化可以通过线性线对时间的求对数来 确定。
粉体测量箱 QTM-PA1 粉体样品可通过QTM-PA1 PD-11探头测量
上海今昊:Tel. 021-20230210 Fax. 021-20230210 Email: jojoanswer@