空气燃油加热器安装使用手册(附原理图)
FVO-200RC 燃油取暖器使用说明书

OPERATING INSTRUCTIONS MANUAL(Please retain for future reference)ForFVO-200RC INDIRECT FIRED SPACE HEATERSCERTIFIED FOR USE IN CANADA AND U.S.A.As per CSA B140.8 Portable Oil Fired Heaters / CSA B140.02003 Oil Burning EquipmentUL733 Oil fired heatersConstruction Heaters Unattended Type.Issue date:2003325FLAGRO INDUSTRIES LIMITEDST. CATHARINES, ONTARIOCANADAGENERAL HAZARD WARNING:FAILURE TO COMPLY WITH THE PRECAUTIONS AND INSTRUCTIONS PROVIDED WITH THIS HEATER, CAN RESULT IN DEATH, SERIOUS BODILY INJURY AND PROPERTY LOSS OR DAMAGE FROM HAZARDS OF FIRE, EXPLOSION, BURN, ASPHYXIATION, CARBON MONOXIDE POISONING, AND/OR ELECTRICAL SHOCK.ONLY PERSONS WHO CAN UNDERSTAND AND FOLLOW THE INSTRUCTIONS SHOULD USE OR SERVICE THIS HEATER.IF YOU NEED ASSISTANCE OR HEATER INFORMATION SUCH AS AN INSTRUCTIONS MANUAL, LABELS, ETC. CONTACT THE MANUFACTURER.WARNING:FIRE, BURN, INHALATION, AND EXPLOSION HAZARD. KEEP SOLID COMBUSTIBLES, SUCH AS BUILDING MATERIALS, PAPER OR CARDBOARD, A SAFE DISTANCE AWAY FROM THE HEATER AS RECOMMENDED BY THE INSTRUCTIONS. NEVER USE THE HEATER IN SPACES WHICH DO OR MAY CONTAIN VOLATILE OR AIRBORNE COMBUSTIBLES, OR PRODUCTS SUCH AS GASOLINE, SOLVENTS, PAINT THINNER, DUST PARTICLES OR UNKNOWN CHEMICALS.WARNING:NOT FOR HOME OR RECREATIONAL VEHICLE USE.WARNING:INTENDED USE IS PRIMARILY THE TEMPORARY HEATING OF BUILDINGS UNDER CONSTRUCTION, ALTERATION, REPAIR OR EMERGENCIES ONLY.This heater is designed and approved for use as aconstruction heater under CSA B140.8 Portable OilFired Heaters / CSA B140.02003 Oil Burning Equipment& UL733 Oil Fired heaters.We cannot anticipate every use which may be madeof our heaters. CHECK WITH YOU LOCAL FIRESAFETY AUTHORITY IF YOU HAVE QUESTIONSABOUT APPLICATIONS.Other standards govern the use of fuel gases and heatproducing products in specific applications. Your localauthority can advise you about these.SPECIFICATIONSModel …………………………………………………….…. FVO-200RC Input ………………………………………………... BTUH Range185,000 Btu Fuel …………………………………………………………. No.1, No. 2,diesel orkerosene Fuel Pressure …………………………………………….... 180 psi Nozzle ………………………………………………………. 1.10 x 70A Electrical …………………………………………………… 115V 15 AMP Ignition ………………………………………………………. Direct SparkIgnition …….……………………………………………...…. ThermostatControlAir Circulation ………………………………………………. 2600 cfm Fuel Consumption ………………………………………...... 1.30 Gal/hr Approved …………………………………………………...... cETLus listedINSTALLATION:The installation of this heater for use with No.1, No.2, Diesel or Kerosene and shall conform with local codes or, in the absence of codes, with the National Fuel Gas Code ANSI Z223.1/NFPA 54. For recommended installation practices refer to CSA Standard B139.CLEARANCE TO COMBUSTIBLES:TOP FRONT SIDES REAR FLUE PIPE3 ft 10 ft 1 ft 2 ft 3 ft FUEL:This heater will operate with No.1, No.2, Diesel or Kerosene.Note:No.1 Fuel Oil or Kerosene must be used fortemperatures less than –10º C (8º F).ELECTRICAL:WARNINGElectrical Grounding InstructionsThis appliance is equipped with a three-prong (grounding)plug for your protection against shock hazard and should beplugged directly into a properly grounded three-prongreceptacle.115v supply must be available. Please note that the heaterrequires 15 amps for proper operation. Ensure appropriategauge extension cord is used.• 12/3 AWG at 50 Feet• 10/3 AWG at 100 FeetPOWER SUPPLY INDICATOR LIGHT:The power supply indicator light will help detect any faulty power supplied to the heater such as; grounding issues, reverse polarity or missing/poor connections.Warning Light IndicationsGreen Light ……………… Meets Power RequirementsSolid Red Light………….. Reverse PolaritySolid Red & Green Light… Ground IssueATTENTION: IF SOLID RED & GREEN IS INDICATED, MAKE CORRECTIONS TO POWER SUPPLY BEFORE TURNING HEATER ON. FAILURE TO DO SO WILL VOID ANY WARRANTY.FLUE PIPE: Flue pipe connection must terminate with a vertical run at least 2ft long. Horizontal runs should have a rise ratio of 1 in10 away from the heater. The chimney should have a 0.2”W.C. draft to ensure safe operation of the unit.The vent outlet on the heater is 6” diameter. Certified ventingmust be used at all times. Vent cap should be installed insituations where downdrafts occur. All venting mustcorrespond with the CSA B149 standard or in its absence,local codes.FV SERIES CONSTRUCTION HEATER – VENTINGREQUIREMENTS1. VERTICAL FLUE TERMINATIONSFLUE OUTLET OF HEA2. HORIZONTAL FLUE TERMINATIONSFLUE OUTLET OF HEAALLA - VENT TERMINATION MUST BE A MINIMUM OF 2FT HIGHER THAN ANY POINTWITHIN 10FT.B - MAXIMUM HORIZONTAL RUN IS 30FT.NOTE: 90deg ELBOW = 10ft HORIZONTAL VENT ALLOWANCE45deg ELBOW = 5ft HORIZONTAL VENT ALLOWANCEC - VENT TERMINATION IN HORIZONTAL POSITION MUST BE MINIMUM 4ft FROM ANYCOMBUSTABLE SURFACED - EXTERIOR VERTICAL VENT TERMINATION MUST BE A MINIMUM OF 2ft.NOTE: ALL VENT TERMINATIONS MUST HAVE A RAIN CAP INSTALLED AS PER LOCAL CODE REQUIREMENTS..OUTLET DUCTING:Hitex heater duct with a minimum temperature handling of300 deg F including wire reinforcement to prevent collapsing.Heater is designed for use with 1 x 12” (FV-HD12) or 1 x 16”(FV-HDG16) diameter ducting equipped with pin lock or cuff& buckle provided on collar of ducting. Ducting should beinspected periodically for tearing and/or wear marks.Ducting should be stored in a dry area when not in use. INLET DUCTING:Inlet ducting can be used on the return air inlet of heater.The heater is designed for 12” inlet diameter ducting with pinlock or cuff and buckle system.MAINTENANCE:1. Every construction heater should be inspected before each use, and atleast annually by a qualified service person. Incorrect maintenance my result in improper operation of the heater and serious injury could occur.2. The hose assemblies shall be visually inspected prior to each use of theheater. If it is evident there is excessive abrasion or wear, or the hose is cut, it must be replaced prior to the heater being put into operation. The replacement hose assembly shall be that specified by the manufacturer.3. The flow of combustion and ventilation air must not be obstructed. Be sure tocheck the fan assembly and ensure that the motor and blade are operating properly.4. Compressed air should be used to keep components free of dust and dirtbuild up. Note: Do not use the compressed air inside any piping or regulator components.5. Change fuel filter insert (Part# FVO-418) once per month. Change fuel filtercartridge (Part# FVO-419) once every 6 months.6. Change oil nozzle (Part# FV-235B) once per year.7. Fan Limit Switch (Part# FV-407A) should be replaced if the fan motor doesnot shut off after the heat exchanger has cooled down.8. The High Limit Switch (Part# FV-406) should be checked each season. Thislimit switch will ensure the burner shuts down if the temperature exceeds 250ºF at the outlet.9. Fuel tank should be drained on a regular basis by removing drain plug.10. CAUTION– Do not have any source of ignition near the heater whendraining tank.NOTE:No.1 fuel oil or kerosene is recommended for temperatures below-10º C / 8º F.11. Heat Exchanger should be cleaned if smokey conditions continue even afterthe air adjustments on the burner are made.START UP INSTRUCTIONS:1. Position heater properly on a level surface.2. Be sure the toggle switch in is the “OFF” position.3. Ensure burner “air gate” is properly set at 3.4. Ensure electrical cord is grounded and plugged into a 120V 15AMPoutlet. Verify cord size (12/3AWG at 50ft & 10/3AWG at 100ft)5. The power indicator light on the control box will engage. If the greenlight illuminates, you have proper power supply. If not, refer to stickeron heater to verify warning problem. Correct power supply problembefore operating heater.6. Move toggle switch to “MANUAL” position for manual control.7. Move toggle switch to “THERMOSTAT” position for thermostat control.Thermostat must be plugged into heater first.Please Note:1. If using Thermostat on unit, unit must be started in Thermostat position.2 When changing between manual and thermostat operation, the heatermust be left in the “OFF” position for 30 seconds to prevent the burner from locking out.3. When using a generator for electrical supply, make sure the generatoris properly grounded and generator is at a 60Hz frequency.4. In the event that a Generator is being used and the generator runs out offuel, make sure the heater switch is in the “OFF” position before restarting generator, failure to do so may damage heater.TO SHUT DOWN:1. Move toggle switch to “OFF” position. Do not disconnect power supplyuntil the heat exchanger cools downNOTE: Fan will continue to operate after the burner shuts down. Once the unit cools down, the fan will stop.IF HEATER FAILS TO START:1. Press manual reset button at rear of burner.2. Check fuel level. There must be 2-4 gallons of fuel in the tank for theheater to start properly.3. Make sure there are no air locks in fuel lines or filter.4. Ensure proper power supply and extension cord is being used.5. Check for dirty fuel filter or blocked fuel supply line.6. Check burner nozzle assembly.NOTE: IF THE BURNER HAS BEEN RESET SEVERAL TIMES THERE MAY BE AN ACCUMULATION OF OIL IN THE CHAMBER! DO NOT CONTINUE TO TRY AND START THE HEATER!DRAIN OIL FROM HEAT EXCHANGER USING DRAIN HOLE AT FRONT OF HEAT EXCHANGER FOR 15-20 MINUTES BEFORE ATTEMPTING TO RELIGHT. LET REMAINING EXCESS OIL BURN OFF BEFORE CHECKING COMBUSTION OF UNIT.SAFE OPERATION PRECAUTIONS:1. Do not fill fuel tank while heater is operation.2. Do not attempt to start heater if excess oil remains in the heatexchanger.3. Use switch to shut down the heater. Do not try to shut down the heaterby unplugging the electrical cord.4. Do not plug anything other than the thermostat into the “Thermostat”plug.5. Do not use any fuel other that those listed on rating plate.6. Follow electrical requirements shown on rating plate and/or Electricalrequirements section of this manual.7. Before removing any guards or performing any maintenance, be surethat the main power supply is disconnected.COMBUSTION AIR ADJUSTMENTS:NOTE: Proper combustion air adjustment must be achieved using a certified combustion analyzer and smoke tester to ensure completecombustion.The air adjustment should be made to achieve 10% CO2and No. 1 or “trace” smoke. (Bacharach Scale)SETTING THE AIRADJUSTMENT PLATEA) Regulation of the combustion airflow is made by adjustment of themanual AIR ADJUSTMENT PLATE (1)after loosening the FIXING SCREWS(2 & 3). The initial setting of the airadjustment plate should be madeaccording to Column 5 in the BurnerSet-up Chart.B) The proper number on the manualAIR ADJUSTMENT PLATE (1) shouldline up with the SETTING INDICATOR(4) on the fan housing cover. Once set, the air adjustment plate should be secured in place by tightening SCREWS 2 and 3.C) The final position of the air adjustment plate will vary on each installation. Use instruments to establish the proper settings for maximum CO2and a smoke reading of zero.NOTE: Variations in flue gas, smoke, CO2and temperature readings may be experienced when the burner cover is put in place. Therefore, the burner cover must be in place when making the final combustion instrument readings, to ensure proper test results.BURNER SET-UP CHART1 2 3 4 5ACTUAL FIRING RATE± 5%NOZZLESIZEPUMP PRESSURETURBULATORSETTINGAIRDAMPERSETTINGGPH GPH PSI BAR1.30 1.10 x 70°A 180 12.41 33.5* Note – Air damper setting is typically set at 3.5 for operation in colder temperatures. A combustion analyzer should always be used when setting the burner.TEMPERATURE FEELER GAUGE ADJUSTMENT(ATTACHED TO FAN SWITCH)The temperature feeler gauge is required to be always touching the heater exchanger.The temperature feeler gauge controls the air flow over the fan switch, which eliminates any unnecessary fan cycling. The temperature feeler gauge can be adjusted for different outside temperatures, by rotating the location of the temperature feeler gauge holes. This will provide maximum performance of the unit in different applications.If supply air is warm (-5º C, indoor application):Turn the temperature feeler gauge so that the holes are parallel with the heat exchanger. This will help the fan switch to remain cool and not overheat. See following:If supply air is cold (under -5ºC):Turn the temperature feeler gauge so that the holes are closed off as the air goes over the heat exchanger. This will reduce fan cycling and the unit from shutting down. See following:In extreme cold conditions, cover the holes on the temperature feeler gauge using foil tape or replace feller gauge with part# FV-433B Solid feeler gauge. Ensure that the temperature feeler gauge is readjusted for warmer weather conditions. Failure to do so may result in burning out fan switches- not covered under warranty.been made, or failure of the pump shaft seal may occur.WARNING: If a neutral or ground lead is attached to this terminal, the CONTROL BOX on the burner will be damaged should lockoutoccur.INSERTION / REMOVAL OF DRAWER ASSEMBLYA) To remove drawer assembly, loosen SCREW (3), then unplug CONTROLBOX (1) by carefully pulling it back and then up.B) Remove the AIR TUBE COVER PLATE (5) by loosening the two retainingSCREWS (4).C) Loosen SCREW (2), and then slide the complete drawer assembly out of thecombustion head as shown.D) To insert drawer assembly, reverse the procedure in items A to C above, andthen attach fuel line to the pump.NOZZLE PLACEMENTA) Remove the NOZZLE ADAPTER (2) from the DRAWER ASSEMBLY byloosening the SCREW (1).B) Insert the proper NOZZLE into the NOZZLE ADAPTER and tighten securely(Do not over tighten).C) Replace adapter, with nozzle installed, into drawer assembly and secure withscrew (1).ELECTRODE SETTINGTURBULATOR SETTINGA) Loosen NUT (1), then turn SCREW (2) until the INDEX MARKER (3) is alignedwith the correct index number as per the Burner Set-up chart, on page 12.B) Retighten the RETAINING NUT (1)NOTE: Zero and five are scale indicators only. From left to right, the first line is5 and the last line 0.OIL LINE CONNECTIONSNote:Pump pressure must be set at time of burner start-up. A pressure gauge is attached to the PRESSURE PORT (8) for pressure readings. Two PIPE CONNECTORS (5) are supplied with the burner for connection to either a single or a two-pipe system. Also supplied are two ADAPTORS (3), two female 1/4” NPT, to adapt oil lines to burner pipe connectors. All pump port threads are British Parallel Thread design. Direct connection of NPT threads to the pump will damage the pump body. Riello manometers and vacuum gauges do not require any adaptors, and can be safely connected to the pump ports. An NPT (metric) adapter must be used when connecting other gauge models.PARTS LIST FOR FVO-200Part Number Part DescriptionFV-2011/2 HP Fan MotorFV-202RC14" BC Impeller For FV-200RCFV-202RCA Venturi For 14" BC ImpellerFV-20312" WheelFV-20412" Power Cord c/w Plug EndFV-205SS Heat Exchanger40-113-D3.5GALV1/2" X 3.5" Galvanized Nipple40-108-8GALV1/2" Galvanized CapFV-406High Limit Switch (Outet) 250FFV-407A Fan Limit Switch (Adjustable)FV-407G Fan Limit Silicone GasketFV-207Lockable Caster WheelFV-270Fan Motor CanopyFV-409Toggle Switch (on control box)FV-411Red Light (on control box)FV-214Thermostat Plug (on box control) (Prior to 2011)FV-414B Thermostat Plug (on box control) (As of 2011)FV-215Female Connector for FV-TH2 (Prior to 2011)FV-415A Male Connector for FV-THB ( As of 2011)FVO-215Riello F5 Burner (Oil)FVO-21623 US Gallon Oil Tank (Steel)FVO-216G Fuel GaugeFVO-417Oil Tank Cap121-B Oil Tank Drain PlugFVO-418Fuel Filter (Complete)FVO-419Fuel Filter (insert Only)FVO-220Clear Fuel Line 6" (Tank to Filter)FVO-221Clear Fuel Line 7.5" (Filter to Burner)FVO-222Clear Fuel Return Line (Burner to Tank)48-6B Brass Fitting (Tank to inlet Fuel Line)48-6C Brass Fitting (Inlet Side of Filter)2103-C-CGA3/8" Shut Off Valve122-C3/8" Brass Hex Nipple50-6C3/8" FP X 3/8" MP Brass Elbow49-6C3/8" MP X 3/8" F.FL Brass ElbowFV-461Inlet/Outlet Burner Pump FittingFVO-2237" Copper Pick Up Tube c/w AdapterFV-231Burner GasketFV-433Feeler GaugeFV-234Front Face Plate (1 x 12")FV-235B Oil Burner Nozzle (1.10 x 70A)FV-437High Limit (Rear) 150FFV-240Wheel Axle - FV-200 SeriesFV-446Sight Glass c/w Fiber GasketFV-447Sight Glass WasherFV-449SI Smart Indicator LightFVO-3000443Pump Drive KeyFVO-3002278Sub Base for F10/F5 BurnerFVO-3002279Coil -F10/F5 BurnerFVO-3002280Photo Cell - F10/F5 BurnerFVO-3005844Capacitor F10/F5 BurnerFVO-3005855Mounting Flange for F10/F5 BurnerFVO-3005869Electrode PorcelainFVO-3005880Electrode AssemblyFVO-3006553Coil U-Bracket c/w Knurled NutFVO-3006965Nozzle Adapter F10/F5 BurnerFVO-3006966Electrode Support for F10/F5 Burner FVO-3006974Nozzle Oil Tube F5 BurnerFVO-3006977Turbulator Disc for F5 BurnerFVO-3006992Pipe Connector - SupplyFVO-3006993Pipe Connector - ReturnFVO-3007320Acoustic Liner for Burner Back Cover (F5) FVO-3008631Electrode AssemblyFVO-C7001010Pump AssemblyFVO-C700-1029Ignition Module (Oil Burner)ACCESSORIES FV-HD1212" x 12FT HiTex Ductingfv-hd12x2512" x 25FT Hitex DuctingFV-THB Thermostat c/w 25FT Cord ( As of 2011)FV-VK6" x 3FT C-Vent c/w Rain CapFVO-C7001001Emergency Service Kit (Oil Burner)FVO-C7050010Vaccum & Pressure Tester ManifoldFV-432Pressure Gauge Adapter。
燃油加热控制器产品简介

产品简介
一、产品概述 二、系统产品图示 三、工作界面示意图 四、故障情况分析及处理 五、产品使用注意事项 六、产品安装说明 七、引出线规格说明 八、电气接线原理图 九、实拍图
一、产品概述
本控制器为汽车柴油加热系统专用控制器,实时监控油箱柴油温 度,自动调节油路各节点的温度,防止油路结蜡,避免影响车辆正常 运行。控制器核心采用世界先进芯片厂家——意法半导体(ST)的汽 车级专业芯片,以保障整个系统运行的稳定、可靠,系统设计自动控 制模式,根据油箱燃油温度的变化自动启动和关闭加热系统,使整个 循环燃油温度保持在正常的温度范围内。
3
4 / / /
空
电源正极 加热输出1 加热输出2 功率电源正极
/
0.75mm² /500mm 2.5mm² 2.5mm² 4mm²
250(6.3)端子接插件 250(6.3)端子接插件 直径5mm螺栓
八、电气接线原理图
电源正极 电源负极 功率电源正极 燃油加热控制器 功率输出1
功率输出2
油 温 传 感 器 输 入
图5、第一路输出电流值显示
图6、第二路输出电流值显示
6、电池过欠压显示功能
电瓶过压保护功能, 电瓶电压实时监视功能, 在车辆运行过程中如充电 电路出现故障导致电瓶电 压高于正常值(30V), 加热系统自动停止工作并 在显示屏上提示“电池过 压”,用以保护电瓶。
电瓶欠压保护功能, 电瓶电压低于欠压保护值 (21V),加热系统自动 停止工作并在显示屏上提 示“电池欠压”,用以保 护电瓶。
图7、电池过欠压显示
四、故障情况分析及处理
1、“故障1”:加热控制输出1有故障; 原因分析:1、输出1负载开路;2、输出1负载 短路;3、功率电源输入开路。 2、“故障2”:加热控制输出2有故障; 原因分析:1、输出2负载开路;2、输出2负载 短路;3、功率电源输入开路。 3、“故障”:加热控制输出1和2都有故障; 4、“环温故障”:环境温度传感器故障; 原因分析:1、传感器开路;2、传感器短路。 5、“油温故障”:油箱燃油温度传感器故障; 原因分析:1、传感器开路;2、传感器短路。 6、 “通讯故障”:显示与功率输出系统通讯故障; 原因分析:1、通讯线开路;2、通讯线短路。
燃油加热器产品资料
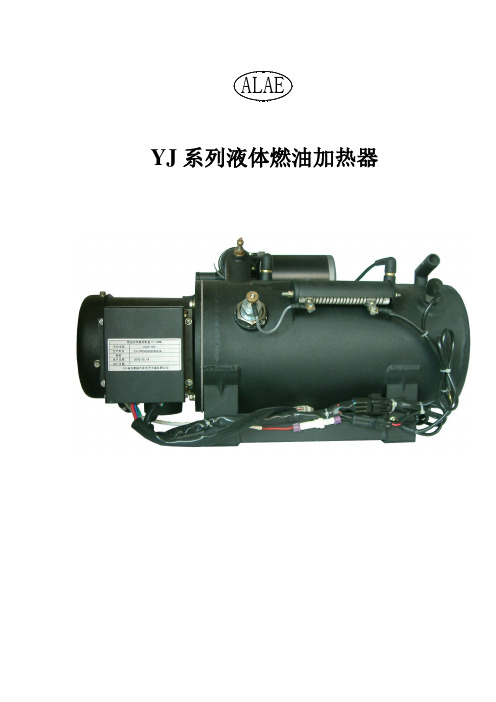
YJ系列液体燃油加热器目录一、系统介绍二、技术参数三、产品结构及工作原理四、配套安装及使用注意事项五、使用方法六、故障分析及排除措施七、维护与保养附图:管路连接图一. 系统介绍:YJ系列燃油液体加热器是与发动机相独立的采暖设备,是通过燃烧换热原理,加热循环系统内冷却介质的加热器产品。
与一般水暖暖风机不同,在发动机不开动的情况下,也可以供车厢内取暖。
它为全自动控制,其控制部分具有低温启动、高温停止、重复点火、故障报警停机等功能,整机采用不锈钢焊接,耐腐蚀性强,使用寿命长,并具有热效率高、升温快、污染小、乘坐舒适、无异味、噪音低、不干燥、节油等优点。
加热器在具有给车厢采暖功能的同时,还具有给水冷发动机作低温预热的功能,它能自动地将冷却液温度恒定在65℃~ 85℃之间。
冬季使用本机预热发动机,可显著降低发动机磨损、油耗和大气污染,延长发动机寿命。
二. 技术参数:1.热流量:11.6kw耗油量:1.23kg/h水泵流量:30L/min温度控制:防冻液温度65~85℃电瓶压降:约0.04V/h(使用180Ah、24V蓄电池)。
水泵功率120W,主电机功率30W可以直接从油箱取油,也可以配专用油箱(本机自带油泵吸油)2.外形尺寸:540×300×300mm安装尺寸:装配孔 M12螺纹孔装配尺寸:250×130mm安装在车身主车架上,可以在挂在车架两侧(油箱后侧),或者车架中间(万向十字接头上方)。
操纵面板尺寸:86×58×60mm1 2 3 4 5 6 7 8 9图310 1112 13 14 15 16 17 18 19图41.电器控制盒2.橡胶塞3.点火塞4.放气阀5.进水温度传感器6.降压电阻7.出水温度传感器8.出水口9.火焰温度传感器10.水泵及电机11.进水口12.放水塞13.主支架14.水泵支架15.电磁阀进油管16.电磁阀17.电磁阀回油管18. 电磁阀出油管19.端盖原理:电动机带动油泵、助燃风扇及雾化器转动。
燃油加热器产品资料
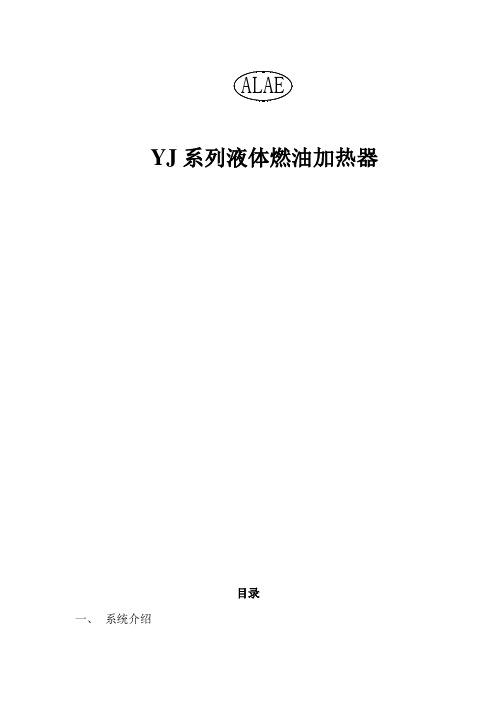
YJ系列液体燃油加热器目录一、系统介绍二、技术参数三、产品结构及工作原理四、配套安装及使用注意事项五、使用方法六、故障分析及排除措施七、维护与保养附图:管路连接图一. 系统介绍:YJ系列燃油液体加热器是与发动机相独立的采暖设备,是通过燃烧换热原理,加热循环系统内冷却介质的加热器产品。
与一般水暖暖风机不同,在发动机不开动的情况下,也可以供车厢内取暖。
它为全自动控制,其控制部分具有低温启动、高温停止、重复点火、故障报警停机等功能,整机采用不锈钢焊接,耐腐蚀性强,使用寿命长,并具有热效率高、升温快、污染小、乘坐舒适、无异味、噪音低、不干燥、节油等优点。
加热器在具有给车厢采暖功能的同时,还具有给水冷发动机作低温预热的功能,它能自动地将冷却液温度恒定在65℃~ 85℃之间。
冬季使用本机预热发动机,可显著降低发动机磨损、油耗和大气污染,延长发动机寿命。
二. 技术参数:1.热流量:11.6kw耗油量:1.23kg/h水泵流量:30L/min温度控制:防冻液温度65~85℃电瓶压降:约0.04V/h(使用180Ah、24V蓄电池)。
水泵功率120W,主电机功率30W可以直接从油箱取油,也可以配专用油箱(本机自带油泵吸油)2.外形尺寸:540×300×300mm安装尺寸:装配孔 M12螺纹孔装配尺寸:250×130mm安装在车身主车架上,可以在挂在车架两侧(油箱后侧),或者车架中间(万向十字接头上方)。
操纵面板尺寸:86×58×60mm1 2 3 4 5 6 7 8 9图310 1112 14 15 16 17 18 19图41.电器控制盒2.橡胶塞3.点火塞4.放气阀5.进水温度传感器6.降压电阻7.出水温度传感器8.出水口9.火焰温度传感器10.水泵及电机11.进水口12.放水塞13.主支架14.水泵支架15.电磁阀进油管16.电磁阀17.电磁阀回油管18. 电磁阀出油管19.端盖原理:电动机带动油泵、助燃风扇及雾化器转动。
空气预热器安装指导书

空气预热器安装指导书施工方案会签表1.工程概况 (1)2.基本建设依据 (2)3.空气预热器安装部分技术参数 (3)4.施工前准备工作 (3)5.作业进度及劳动力安排 (6)6.安装程序及步骤 (6)7.质量保证措施 (14)8.安全措施 (15)9.环境保护措施 (20)10.试运注意事项 (24)11.交底记录: (25)供热机组扩建工程,加装两台哈尔滨锅炉厂生产的hg-1165/17.5smr3型亚临界自然循环炉,搭载两台全模式三分仓容克式空气预热器。
该预热器是利用锅炉烟气中吸收热量来加热空气的一种热交换器,其作用是回收烟气余热,提高锅炉效率。
其主要有烟风道连接板,冷端连接板,热端连接板,冷端连接环,热端弓形环,主座架,侧座架(元件盒修护板),转子外壳板组件,导向轴承,支承轴承,转子,转子模式扇形仓,转子中心筒,导向端轴,支承端轴,传动装置,膨胀装置;其附属装置包括:吹灰器,水冲洗装置,观察装置;该预热器型号30.5-vi(t)-2333-smr,转子名义直径11818mm,三分式,转子旋转依次经过烟气侧、一次风侧、二次风侧,一次风开口70°逆转,传热元件总高:2804mm。
预热器布置在bh-bk排、b32.2-b19.1轴及b16.7-b3.6轴之间,预热器通过膨胀装置组件支撑在.10950mm钢结构支承梁上,膨胀装置组件焊接于钢架。
其上部钢结构在21000mm处有两根横梁(2hc52)穿过,此钢梁在安装钢结构时应预留。
安装过程中与省煤器及尾部过热器存在交叉作业。
此设备由哈尔滨锅炉厂有限责任公司提供技术支持。
2.1hg—1165/17.5—hm3型锅炉总图,预热器加装图、预热器加装说明书。
2.2《电力建设施工及验收技术规范》(锅炉机组篇,管道篇,dl/t5047—95,1996年版)。
2.3《火电施工质量检验及评定标准》(锅炉篇,1996年版)2.4东电一公司企业标准《质量、环境、职业身心健康安全管理文件》(q/nepc(2)001-024202)2.5《电力建设安全工作规程》(dl5009.1-2002)2.6采用施工机械性能表中:300t履带性能表中300t履带吊选用主臂60m,副臂36m工况。
燃油加热器简明维修手册

汽车燃油加热器 简明使用维修手册河北宏业永盛汽车加热器股份有限公司2011年7月使用燃油加热器前请仔细阅读本手册,本手册适用于YJ型、YJP型加热器的使用与维修。
一、YJ型加热器及零部件二、YJP型加热器及零部件三、燃油加热器使用注意事项四、YJ型燃油加热器常见故障与排除五、YJP型燃油加热器常见故障与排除六、日常检查与保养维护七、主要零部件的拆卸如在安装、使用、维修过程中如有疑问请拨打售后服务电话:0317-*******-8262234一、YJ 加热器与主要零部件过热传感器冷却泵二、YJP型加热器及零部件:电磁阀点火电极燃油泵预热管三、燃油加热器使用注意事项:1、加热器油路系统中应使用与环境温度相适应牌号的柴油;加热器循环系统内应使用与环境温度相适应牌号的防冻液。
(1)天气转冷时,油箱要及时更换对应标号的柴油或煤油,否则会引起加热器故障。
更换柴油后,打开加热器,使其工作至少3分钟,使油路全部充满更换后的柴油。
柴油标号参见下表:环境温度 柴油标号5℃ — -5℃ -10#-5℃ — -15℃ -20#-15℃— -30℃ -35#-35℃及其以下 -50#(2)天气转冷时,请确认更换对应标号的防冻液,否则会导致加热器损坏。
加注防冻液时,必须先打开加热器放气阀及管路放气阀,待放气阀尤其是加热器放气阀处无气体冒出时,关闭放气阀,打开加热器水泵开关,打开汽车发动机,继续加注,直至循环系统内充满冷却液介质为止。
防冻液标号参见下表:环境温度 防冻液标号5℃—— -25℃ -30#-25℃以下 -35# (或更低标号)2、冲洗车辆时,禁止用水枪对安装加热器位置冲洗,否则会引起加热器故障。
3、严禁利用车辆总电源开关关闭加热器,以防止主机内部过热,要先关闭加热器开关,3-5分钟后,待加热器开关绿色指示灯熄灭后,方可关闭车辆总电源,严禁加热器开关指示灯亮着断掉加热器电源。
四、YJ型燃油加热器常见故障与排除故障现象 原因分析 排除措施加热器开机后无法点火、排烟口滴油电热塞损坏 检查更换电热塞加热器开机后点不着火,指示灯闪一长五短1、油管堵或主油箱内缺油2、油管接头密封不良,漏气3、电磁阀打不开4、助燃风口堵塞5、点火传感器故障1、疏通油路,油箱加油2、紧固接头卡子3、检查故障,更换电磁阀4、清理助燃风口5、更换或调整点火传感器加热器在高原等地区着火,但工作过程中持续冒黑烟 进风量不足调整进风口(增大进风)加热器到温度不停机 1、水温传感器故障 1、用万用表检测水2、传感器位置不能正确感应实际循环系统的温度 温传感器两端,停机时电压超出 1.93±0.1伏,即为传感器故障。
TGH34PL-2燃气加热器使用说明书
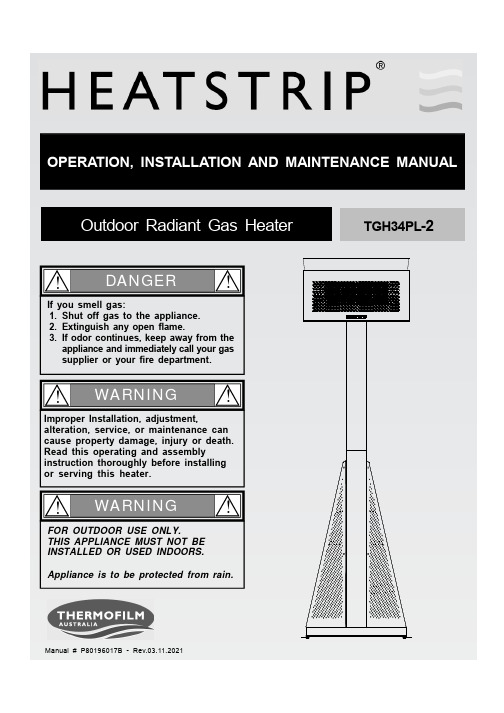
Manual # P8*******B - Rev.03.11.2021DANGER!!1.2.3.If you smell gas:Shut off gas to the appliance.Extinguish any open flame.If odor continues, keep away from the appliance and immediately call your gas supplier or your fire department .WARNING!!Improper Installation, adjustment,alteration, service, or maintenance can cause property damage, injury or death.Read this operating and assemblyinstruction thoroughly before installing or serving this heater.WARNING!!FOR OUTDOOR USE ONLY.THIS APPLIANCE MUST NOT BE INSTALLED OR USED INDOORS.Appliance is to be protected from rain.OPERATION, INSTALLATION AND MAINTENANCEMANUALOutdoor Radiant Gas HeaterTGH34PL -21. This appliance must be used only for outdoor area and shall not be used in a building, garage or any other enclosed area. This appliance must not be installed or used indoors. This appliance must be placed on level firm ground. This appliance shall only be used in an above ground open-air situation with natural ventilation, without stagnant areas, where gas leakage and products of combustion are rapidly dispersed by wind and natural convection.2. Any guard or other protective device removed for servicing (conducted by an authorized person) must be replaced before operating the heater.3. Do not install in very windy locations. Do not transport or move the heater while it is operating.4. Children and adults should be alerted to the hazards of high surface temperatures and should stay away to avoid burns or clothing ignition.5. Children should be carefully supervised when they are in the area of the heater.6. Clothing or other flammable materials should not be hung from the heater or placed on or near the heater.7. Do not perform maintenance until heater has been turned off, and heater has cooled to room temperature.8. Do not expose the burner to water or moisture. The appliance must be protected from rain.9. Do not use the heater if any parts are damaged by exposure to water until the appliance is inspected or repaired by an authorized service person.10. The installer is to ensure that the requirements of the local authority, local gas fitting regulations,municipal building codes, and any other relevant statutory regulations are carried out.11. Certain materials or items, when stored under or near the appliance, will be subjected to radiant heat and could be seriously damaged.12. All leak tests should be done with a soap solution. Never use an open flame to check for leaks.!!13. Do not use the heater until all visible gasconnections have been leak tested.Never test for leakswith an open flame. Prior to first use, at the beginning of each season, or every time your LP Gas Cylinder is changed, you must check for gas leaks.14. The radiant heater is NOT intended to be installed on recreational vehicles or boats.15. Do not attempt to alter the unit in any manner.16. Do not paint any surface of the heater or reflector.17. Burner and circulation air passageways of the heater must be kept clean. Frequent cleaning may be required as necessary.18. Check the heater immediately if any of the following occurs:- The heater does not reach temperature.- The burner makes popping noise during use (a slight noise is normal when the burner is ignited or extinguished).19. This appliance is not intended for use by young or infirm person unless they have been adequately supervised by a responsible person to ensure that they can use the appliance safely.20. Check for damage to the appliance regularly. If damage to the appliance is suspected, discontinue use immediately and contact the supplier or qualified person for repair.21. Avoid inhaling fumes emitted from the heater's first use. Smoke and odour from the burning of oils used in manufacturing will appear. Both the smoke and odour will dissipate after approximately 30minutes.22. Storage of an appliance indoors is permissible only if the cylinder is disconnected and removed from the appliance.23. Do not store a spare LP gas cylinder under or near this appliance.24. The heater head angle retaining pin must be inserted if transporting the heater to ensure no damage occurs during transit.!!Do not store or use flammable liquids or vapors inthe vicinity of this appliance.An LPG cylinder not connected for use shall not be stored in the vicinity of this appliance.1.2.!!ŸŸ!READ THIS MANUAL CAREFULLY before installing or operating this product.Failure to comply with these instructions could result in a fire or explosion that could cause serious bodily injury, death or property damage.!DO NOT PLACE ARTICLES ON OR AGAINST THIS APPLIANCE.DO NOT USE OR STORE FLAMMABLE MATERIALS NEAR THIS APPLIANCE.DO NOT SPRAY AEROSOLS OR FLAMMABLE MATERIALS IN THE VICINITY OF THIS APPLIANCE WHILE IS IN OPERATION.!!This appliance is for outdoor use only.This appliance must be placed on level firm ground.This appliance shall only be used in an above ground open-air situation with natural ventilation, without stagnant areas, where gas leakage and products of combustion are rapidly dispersed by wind and natural convection.Any enclosure in which the appliance is used shall comply with one of the following:1. An enclosure with walls on all sides, but at least one permanent opening at ground level.2. Within a partial enclosure that includes an overhead cover and no more than two walls.3. Within a partial enclosure that includes an overhead cover and more that two walls, the following shall apply:- At least 25% of the total wall area is completely open.- At least 30% of the remaining wall area is open and unrestricted.- In the case of balconies, at least 20% of the total wall area shall be and remain open and unrestricted.The following diagrams are examples of outdoor areas.These same principles apply to any other shaped area.LPG CYLINDER USE AND SAFETYHOSE AND REGULATOR SAFETYClose LPG cylinder valve whenever the heateris not in use.This heater is for outdoor use only. The LPG gas cylinder must be disconnected when the heater is not in use for prolonged periods. If the heater is to be stored indoors, you must remove and store the LPG gas cylinderoutdoors. Store in a well ventilated area and out of reach of children,The heater is designed for use with a 9KG LPG cylinder. Do not connect the heater to LPG cylinder exceeding this capacity.The gas cylinder should be filled by a reputable gas dealer, or exchanged at a reputable cylinder exchange outlet.Always keep cylinder in an upright position.Always close the cylinder valve when the heater is not in use.Do not subject the gas cylinder to excessive heat.ŸŸŸŸŸŸThe regulator and hose assembly supplied with the heater are suitable for liquefied petroleum gas.A gas regulator adjusted to have and outlet pressure of 2.75 kpa is supplied for LCC27connection to the LPG cylinder. The regulator and hose assembly supplied with the heater must be used. Replacement regulators and hose assemblies must be those specified by the appliance manufacturer.When connecting the hose and regulator assembly to the gas cylinder, take care to avoid unnecessary twisting of the flexible hose.After the assembly has been secured, turn on the gas and check for leaks by brushing a soap and water solution over all connections.The presence of bubbles will indicate a gas escape. DO NO TEST FOR GAS ESCAPES WITH AN OPEN FLAME.If you are unable to correct the leak bytightening the connections, turn off the gas and contact your place of purchase immediately.Always ensure the patio heater is kept away from flammable materials and the gas cylinder clear of any heat source.When changing over from an empty gascylinder to a full one, make sure this proce-dure is carried out in a flame-free atmosphere.Inspect the gas hose before each use and when replacing the gas cylinder. If the hose is cracked, cut, abraded or damaged in any way,the heater must not be operated. The hose must be replaced if damaged or when statutory conditions require it. Contact your place of purchase if uncertain.The hose and regulator should be disconnected from the cylinder when the heater is not in use. DO NOT DISCONNECT THE GAS HOSE FROM THE APPLIANCE.The hose assembly must be replaced prior to the appliance being put into operation if there is evidence of excessive abrasion or wear, or if the hose is damaged. The replacement hose must be purchased from Thermofilm Australia Pty Ltd.ŸŸŸŸŸŸŸŸŸNEVER OPERATE THIS HEATER WITHOUT A REGULATOR.DO NOT BYPASS THE SAFETY DEVICES.DO NOT ATTEMPT TO CONVERT THE HEATER FOR NATURAL GAS USE.FAILURE TO COMPLY WITH THESEINSTRUCTIONS COULD RESULT IN A FIRE OR EXPLOSION WHICH COULD CAUSE SERIOUS BODILY INJURY, DEATH ,OR PROPERTY DAMAGE.!!ŸŸŸŸThis appliance must only be used in a well ventilated area. The following clearance should be followed:The heater should not be installed:- Where heat ignition can cause damage to gas cylinders/lines- Near other combustible materials.- In open locations subject to rain.Heater should be installed to allow adequate:- Clearance around air openings to combustion chamber.- Clearance from combustible material- Provisions for accessibility and clearance for combustion and ventilating air supply.Installation ClearancesDimension and Clearance DetailIMPORTANT 1 : MINIMUM CLEARANCES TO COMBUSTIBLE MATERIAL, FROM TOP 500mm, SIDE 1000mm, FRONT 1000mm, REAR 300mm.IMPORTANT 2 : ALWAYS LOCATE AND OPERATE HEATER ON A FLAT-LEVEL SURFACE.Hardware Diagram for TGH34PL-2Pan Head Screw M6x10mm Qty. 29Part # S112M06102Pan Head Screw M5x10mm Qty. 7Part #S112M05102Pin Φ6 x 150mm Qty. 1Part # P0*******D Bolt M6 x 150mm Qty. 1Part #S020100223R Cotter Pin Qty. 1Part # P0*******BWing Nut M6Qty. 1Part # S411M0606AAA BatteryParts ListCAUTION : To assemble this heater, you should obtain assistance from another person when handling the larger, heavierpieces.Install the Lower PostInstall Side PanelsInstall Head Deflector and BatteryPlace two Side Panels onto the Base.Install the Left Side Panel to the Lower Post usingto the Base using 3 Pan Head Screws M6x10mm.tighten all the screws securely.Install Head Deflector to the Head Assembly using 3 Pan Head Screws M5x10mm, then tighten all the screws securely.Pan Head Screw M6x10mm Qty. 5Part # S112M06102Pan Head Screw M6x10mm Qty. 10Part # S112M06102Pan Head Screw M5x10mm Qty. 3Part # S112M05102attach 2 Pan Head Screw on Base halfway.231then tighten all the screws securely.Attach AA BatteryAA Battery4Install Heater HeadLay Heater Upper Assembly on a non-abrasive surface (carton or table).Remove pre-assembly screw from back panel of post upper.Insert the Regulator with Hose to the Upper Post and attach Back PanelInstall the Upper Rear Panel to the Lower Post using 2 Pan Head Screws M6x10mm.Install the Upper Rear Panel to the Side Panels using 4 Pan Head Screws M5x10mm, then tighten all the screws securely.Place the Lower Real Panel in position over the gas bottle enclosure area.Install Rear PanelsPan Head Screw M6x10mm Qty. 2Part # S112M06102Pan Head Screw M5x10mm Qty. 4Part # S112M051026Install Post ConnectorInsert the Upper Post with heater head and attach 6 Pan Head Screws M6x10mm, then tighten all the screws securely.5Pan Head Screw M6x10mm Qty. 6Part # S112M06102Never test for leaks with an open flame. Prior to first use, at the beginning of each season, or every time your LP Gas Cylinder is changed, you must check for gas leaks. Follow these three steps:Check for Gas Leaks!Failure to read and follow the Use and Care Instructions could result in a fire or explosion that could cause serious bodily injury, death or property damage.!Make a soap solution bymixing one part liquid detergent and four parts water.1. 1 part liquid detergent4 parts water 2.Pull "off" down, then turn on gas at3.Apply the soap solution to all visible gas connections. If bubbles appear in the soap solution the connections are not properly sealed. Check each fitting and tighten or repair as necessary.WARNING!!If you have a gas leak that cannot be repaired by tightening, turn off the gas at the source,disconnect fuel line from your heater and call (03) 9562 3455 or your gas supplier for repair assistance.Before each use, check all hoses for cracks, nicks, cuts,burns or abrasions. If a hose is damaged in any way,do not use your heater before replacing the hose with an authorized part from the Parts List. Also make sure all gas supply connections are securely tightened.Familiarize yourself with the safety and Use and Care Instructions in this Manual. Do not smoke while lighting heater or checking gas supply connections.Always light the heater standing to the side of the heater, never light the heater standing in front.(3) Once the pilot flame is established, keep pulling the trigger down for 10 seconds to ensure that the burner remains lit.(4) If the burner does not ignite, turn gas off at source and Pull the trigger "OFF" down. Wait at least 5 minutes for gas to clear, then retry. If your heater still fails to light,turn the Control Knob and gas source OFF. Wait 5 min-utes for gas to clear and then conduct a gas leak test. If no leaks are detected, repeat the lighting procedure.5. When the heater is not in use, Pull the trigger "OFF"down and turn off the gas source.Failure to replace a faulty hose, secure gas supply connections before proceeding to the LightingProcedures could result in a fire or explosion that could cause serious bodily injury, death, or property damage.!!Heater Lighting Instructions(1)LP Gas CylinderWARNING!!Failure to comply with these instructions could result in a fire or explosion that could cause serious bodily injury, death or property damage.Keep heater area clear and free from combustible materials, gasoline and other flammable vapors and liquids.Keep the ventilation openings of the cylinder enclosure cabinet free and clear of debris.CLEANING AND MAINTENANCEBefore initial use, and periodically thereafter, we suggest you wash your heater using a mild soap and warm water solution.You can use a wash cloth or sponge for this process.Never use abrasive cleaners, scrubbers or stiff wire brushes of any type on your heater. These will scratch painted surfaces during the cleaning process.Ensure the appliance is dried after cleaning to prevent rusting.It is recommended the heater be operated on high heat after cleaning to ensure the appliance is dry.Proper care and maintenance will keep your heater in top operating condition and prolong its life. Follow these cleaning procedures on a timely basis and your heater will stay clean and operate with minimum effort.CAUTION: Be sure your heater is OFF and cool before cleaning.CLEANING EXTERIOR PAINTED SURFACES。
容克式烟气加热器安装说明书
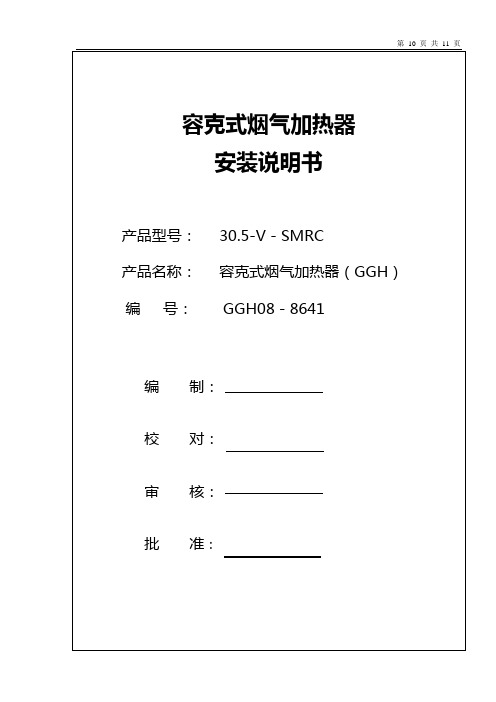
10、 安装、焊接静密封,必要时进行修割。
11、 重新安装为安装模块而未装妥的壳板、刚性环等。打开外壳大检修 门,完成转子、外壳等的焊接工作。
12、 安装上下水管组件及吹灰器等(可根据鳞片树脂施工的实际情况,调整水管的安装时间。)。
13、 安装所有径向、轴向密封片(未安装好转子壳板的模块除外)。在涂层前进行扇形板、轴向密封板的调整。
14、涂层前安装旁路密封片。
15、焊妥各撑管,焊接外壳、管路上的保温抓钉。
16、按密封间隙表调整好密封片和密封板的间隙,复查合格后,作好纪录。焊接固定好扇形板、轴向密封板,安装静密封、净化风槽口等组件。焊接时保证扇形板和轴向密封板的焊接变形量最小。
9、 用临时拉撑将中心筒和端轴装配件固定在下梁(非扇形板)上,调整并保持其垂直。
10、 起吊上梁,移去上梁上的临时支撑,使上梁中间孔穿过导向端轴。使上梁垂直就位于主支座上(注意对中)。按图进行焊接。
11、 根据导向轴承组件图安装导向轴承组件。并请按导向轴承组件图纸的要求预紧轴承。
12、 拆去端轴上的所有临时拉撑。
9、根据总包方的调试计划,对各个设备进行逐项调试。
5、启动前检查项目
6.1、加热器的位置是否正确?
6.2、胀缩节和烟风道的安装情况如何?是否有加热器以外的负荷作用在加热器上?
6.3、下部梁下(中心支撑和两端)的滑动板是否装妥?定位工字钢是否焊妥?支承脚是否能自由膨胀?
6.4、扇形板和密封盘是否装妥?扇形板是否固定?
17、根据涂层敷装图及防腐厂家的有关技术要求进行外壳内部防腐施工。必要时,应当对局部区域进行二次防腐施工。
冬季施工燃油加热器安全作业指导书(2篇)

冬季施工燃油加热器安全作业指导书一、编制目的燃油加热器具有使用方便、热功率高、维护费用低等优点,已经成为冬季施工工程现场采暖的一种重要方式,但其在使用中存在较高的安全风险,如果使用不当可能引发一氧化碳中毒、火灾、爆炸、触电等各类生产安全事故。
为保证作业人员正确使用燃油加热器,减少事故隐患和违章行为,杜绝安全事故,集团公司特编制本作业指导书。
二、总体管理要求1、采购、使用燃油加热器前使用单位应提前了解设备性能,并编制专项技术方案和应急预案,明确安全措施和应急措施。
2、燃油加热器应采购有资质正规厂家生产的合格产品,不得使用“三无”产品,合格证、生产商资质资料齐全。
3、加热器的燃料必须从正规渠道购置,保证燃料质量合格。
4、直燃式燃油加热器加热期间加热场所内不得安排人员作业,除燃油加热器操作人和看护人外严禁其他人员进入。
5、燃油加热器使用期间使用单位现场安全管理人员、值班人员应定时对看护人员履职情况进行巡查、抽查,同时可采用对讲机呼叫方式随时了解看护人员作业情况。
三、作业前的准备工作1、设备、燃料及电源准备。
燃油加热设备进场应由使用单位的管理部门进行验收、编号、建档、保管,设备存储时应按操作手册排空油箱,专人保管。
验收完毕应填写《施工机具安装验收表(其它中小型)》(AQ____C9____14)。
使用单位应采购合格燃料,并符合设备使用说明书中对燃料种类和型号的要求。
燃料的储存和管理应符合易燃易爆危险化学品管理要求,设专门的危险化学品库房,并安排专人进行看管,履行进出料登记程序。
需要燃油加热设备加热的场所应按规范铺设电缆线,设置开关箱,保障每台设备均有专用开关箱、照明不足的场所要设置安全特低电压专用照明线路和照明灯具,不得将设备开关箱作为照明灯具电源。
照明灯具的设置应符合施工现场临时用电安全技术规范要求。
2、明确设备操作人和看护人(即看火人)。
设备使用前要明确每一台设备的操作人和看护人,操作人和看护人应选择安全责任意识强,具有初中以上文化程度,具备消防安全知识,年龄在20至45岁之间,身体健康,具备___年以上建筑施工经验的人员担任。
空气-油泵安装、操作与维护指南说明书

Black & Webster Assembly Equipment Division 545 Hupp Ave. · P.O. Box 831 · Jackson, Michigan 49204Phone: (517) 787-9444 · Fax: (517) 787-7585Email:**********************Serial Number: __________________Manual Part No. UM-AHCP-20170927Table of Contents Warranty (3)Press Installation (3)Controls (4)Reservoir (4)Ram Stroke (4)Machine Guardi ng (4)Air/Oil Flow & Bleeding of System...............................................................5-6 Parts List................................................................................................7-8 Machine Diag ram (8)Press Dimensions (9)General Specificat ions (9)Preventative Maintenance & Trouble Shooting.............................................. 10-13 Oil Drain for Cylinder Rebuild. (14)Schematics & Special AddendumsBooster and Ram Assembly InstructionsMachine Component Product InformationWarrantyAir-Hydraulics, Inc. warrants to the original user that all products manufactured will be free from defects in material and workmanship and will possess the characteristics represented in writing by us. Claim for breach of the above warranty must be made within a period of one year from date of delivery to the user. Upon satisfactory proof of claim, we will make any necessary repairs or corrections, or at our discretion, replace defective parts at the factory, transportation charges prepaid. Charges for correcting defects will not be allowed, nor can we accept goods returned for correction unless we are notified in writing and the return or correction is authorized by us in writing. The foregoing is in lieu of all other warranties, expressed or implied, including any warranties that extend beyond the description of the product. This paragraph set forth the extent of our liability for breach of any warranty in connection with the sale or use of our products. It is understood we will not be liable for consequential damages such as loss of profit, or expense, whether based on tort or contract. This warranty is void if the articles covered by the warranty have not been properly installed, maintained and used.NOTEThe Air Hydraulic Press has been carefully and accurately built to give long, trouble-free service if properly installed and maintained. Follow carefully the instructions, making sure no dirt or foreign materials are allowed to get into the cylinder or other working parts. If you have any unusual problems regarding controls or tooling, notify AIR-HYDRAULICS, INC., JACKSON, MICHIGAN, at 1-800-837-4355 and our Engineering Department will be glad to assist you.PRESS INSTALLATION INSTRUCTIONSInstall incoming air supply (100 P.S.I.) through an approved safety lockout valve which is upstream of FRL unit. The FRL unit consists of a filter, pressure regulating valve, and an air lubricator connected in proper order with arrows indicating the direction of air flow. It should be installed in the air line in a horizontal position as close to the press as possible with the pressure gauge visible from the opera ting position in front of the press. Connect outlet lubricator to inlet on press (tagged “air inlet”). Turn on air and make sure there are no air leaks. Operate press and verify lubricator is allowing an occasional drop of oil to pass into the air line (Note: the lubricator adjusted at the factory & should not require adjustment). If required, see Preventative Maintenance section for adjusting & adding oil to lubricator.Caution: Do not use over 100 P.S.I. air pressure.C-Series Press & Booster System ExplainedThe C-Series Press & Booster System uses a closed hydraulic system. The important thing to remember is there is air on the bottom (rod) side of the working ram cylinder & oil on the top (opposite) side. Secondly, the booster unit is a stacked cylinder assembly. The top cylinder is an intensifier or multiplier, having oil and the lower section of the booster assembly having air on both sides of the piston. A series of seals between the upper and lower cylinder sections separate and isolate the air from oil. An oil reservoir is used to assure the closed hydraulic circuit is free of air and always full of oil. Lastly, the air that returns the ram cylinder also returns or retracts the booster cylinder piston simultaneously to the home position allowing the oil to return to the top side of the booster cylinder assembly.CONTROLSPress may be operated by electrical or pneumatic anti-tie-down controls with dual palm button activators. Also available at additional cost are special controls for automatic operation (pressure switch, limit switches, etc.).RESERVOIRThe reservoir is located at the top inside of the booster cylinder and contains a reserve supply of oil. The oil level should be checked occasionally so that the reservoir is never allowed to become completely empty. Try to keep the reservoir about ¾ full at all times. The proper volume of oil in the hydraulic system is maintained from the reservoir supply. Use Mobile 24 or 25 hydraulic oil to refill the reservoir.RAM STROKEThis may be adjusted up to two-inches shorter with the downstop nut and the downstop locknut (Part Numbers 26 and 27).MACHINE GUARDINGMachine guarding is the responsibility of the user. Provisions must be made to protect the operator and other employees from injury from contact with work in progress, moving parts, mechanical motions of the press, etc. AIR-HYDRAULICS, INC. cannot provide “standard” guards for its presses due to the variety of tooling used by press owners. However, AIR-HYDRAULICS, INC. will be happy to install guards and similar safety devices for operator protection. These safety devices must be produced at the request of, and with design approval of the purchaser.NOTICEWhen shutting down the press, the ram should be left in the full up position before turning off the air supply. Should the ram not be in the full up position when the air supply is turned off, the ram may drift after the air supply is turned off until all air from the system is exhausted.Bleeding:Note: A loss of ram pressure or a jumping action of the ram indicates air in the hydraulic system.The air should be bled from the hydraulic system as follows:a.Make sure the reservoir has an adequate supply of oil.b.Turn main air line pressure on, with control valve, assure ram is in the full up position.c.Remove cap nut from hydraulic booster top cap.d.Fill system through pipe plug hole allowing air to bubble out.e.When no more signs of air bubbling out and system is full to top, replace pipe plugf.Press is now ready for operation.Do Not Short Stroke the PressThe C-Series, C-250, C-300, C400 & C-500 presses uses a sealed air/oil system. As in any press, seals in time wear and may allow air into its closed hydraulic circuit. The C-Press’s proprietary self bleeding system will remove any air trapped in the hydraulic oil on each stroke of the press. For this to happen, the working ram MUST return to the full up position after each stroke of the press, or the trapped air will build up, decreasing its effectiveness and keep the press from reaching full tonnage.AIR & OIL FLOW FOR AIR-HYDRAULIC PRESSESFOR MODEL NUMBERS C-100, C-250, C-300, C-400, and C-5001.When the valve is energized, line “B” is filled with air, causing the booster piston and ram torise.2.As the booster ram enters the oil chamber, pushing the oil out, pressure is developed andtransferred to the ram cylinder. This pressure is maintained throughout the stroke.3.Air from the downward stroke of the ram cylinder and the upward stroke of the boostercylinder is exhausted through line “A” throughout the stroke.4.The oil which is flowing through the speed control valve enters the ram cylinder and pushesthe ram down.5.When the valve is de-energized, line “A” is filled with air causing the ram cyli nder to move upand the booster cylinder to move down.6.The only function of the booster fill line is to replenish the oil in the event a leak occurssomewhere in the system. The oil enters the chamber through the middle head of the booster cylinder and a small hole in the top of the booster ram.7.The only function of the booster bleed off line is to return oil back to the reservoir in the eventoil does leak by the seal in the booster.8.The bleed hole which is located near the end of the ram cylinder is for the bleeding of oil inthe event any leakage occurs in the seals.Air-Hydraulics’ C-Press Parts ListDet. # Part Name PART NUMBERS Quant.C-250 C-300 C-400 C-5001 Frame C1-2-01 C3-4-01 C3-4-01 C5-01 12 Ram Guide C2-02 C3-4-02 C3-4-02 C5-02 13 Air Cyl. Piston Seal ** ** ** ** 14 Air Cyl. Body C2-04 C3-04 C4-04 C5-04 15 Air. Cyl. Top Head C2-05 C3-05 C4-05 C5-05 15A Hyd. Cyl. Body C2-05A C3-05A C4-05A C5-05A 15B Hyd. Cyl. Top Head C2-05B C3-4-05B C4-05A C5-05B 16 High Press Hose H-10-21-ASSY H-C3-4-ASSY H-C3-4-ASSY H-C500-31 17 Air Cyl. Bottom Hyd. C2-07 C3-4-07 C3-4-07 C5-07 18 Air Cyl. Piston C2-08 C3-4-08 C3-4-08 C5-08 19 Air Cyl. Ram C2-09 C3-09 C4-09 C5-09 110 Air Cyl. Tie Rods C2-10 C3-10 C4-10 C5-10 411 Ram Cyl. Bot. Head. C2-11 C3-4-11 C3-4-11 C5-11 112 Ram C2-12 C3-12 C4-12 C5-12 1 12a Ram Cyl. Piston C2-12A C3-4-12 C3-4-12 C5-12A 113 Ram Cyl. Body C2-13 C3-13 C4-13 C5-13 114 Ram Cyl. Top Head C2-14 C3-14 C3-4-14 C5-14 115 Ram Cyl. Tie Rods C2-15 C3-15 C4-15 C5-15 416 Hyd. Cyl. Tie Rods C2-16 C3-16 C4-16 C5-16 417 Air Cyl. Ram Seal ** ** ** ** 318 Ram Seal ** ** ** ** 119 Static Seal ** ** ** ** 220 Ram Piston Seal ** ** ** ** 221 Flex-loc Nut-Ram FN-0.875-14 FN-1.250-12 FN-1.250-12 FN-1.500-12 122 Ram Top Head Seal ** ** ** ** 123 Down Stop Plate C2-23 C3-4-23 C3-4-23 C5-23 124 Oil Reservoir RESERVOIR RESERVOIR RESERVOIR RESERVOIR 125 Hex Nuts-Tie Rods 36509 36509 36509 36515 1226 Down Stop Nut C2-A28-50-26 C3-4-26 C3-4-26 C5-26 127 Down Stop Lock Nut 36513 36368 36368 36372 128 Air Cyl. Gaskets ** ** ** ** 229 Ram Cyl. Gaskets ** ** ** ** 1 30a Ram Cyl. Ring Seal ** ** ** ** 1 30b Ram Cyl. Seal - B/U ~ ** ** ~ 231 Ram Guide Key C1-2-3-4-31 C1-2-3-4-31 C1-2-3-4-31 C5-3132 Hyd. Cyl. Seal ** ****** 2 32a Hyd. Cyl. Seal - B/U - ****** 2 32b Hyd. Cyl. Gasket ** **** - 233 Low Press. Hose 10LOLA 10LOLA 10LOLA 12LOLA 134 Guard Tube C2-34 C3-4-5-34 C3-4-5-34 C3-4-5-34 135 O-Ring Bumper ~ ** ** ~ 136 Reservoir Bracket C250-100 C250-100 C250-100 C250-100 137 Air Cyl. Ram O-Ring ** ** ** ** 138 Wiper seal ** ** ** ** 1**SEALS MUST BE PURCHASED VIA SEAL KITS **PLEASE CONSULT FACTORY FOR PART NUMBER, PRICING, AND AVAILABILITY*DENOTES APPROXIMATE DIMENSIONS*Air-Hydraulics PressesPress Work Area DimensionsDim. KeyPart NameC-100(discontinued)C-250 C-300 C-400 C-500 A THROAT DEPTH 6.25 6.25 6.25 6.25 8.25 B DAYLIGHT12.00 12.00 14.43 14.43 14.00 C RAM DIAMETER .875 1.000 1.500 1.500 2.750 D RAM MOUNTING ½-13x1.25 5/8-11x1.25 5/8-11x1.25 5/8-11x1.25 1 1/4-12x1.88E PLATEN WIDTH 12.50 12.50 14.00 14.00 18.00F PLATEN DEPTH 6.00 6.008.00 8.0010.00G PLATEN SLOT 5/8x1.50 .62x1.50.75x1.50 .75x1.501.25x.88H PLATEN RADIUS 2.00 2.00 2.00 2.00 2.25 J PLATEN THICKNESS 1.00 1.00 1.00 1.00 1.25 K PLATEN FLOOR 7.12 7.12 9.00 9.00 9.00 M FRAME WIDTH 9.50 9.50 11.00 11.00 15.25 N FRAME DEPTH 18.00 18.00 21.00 21.00 28.00 P FRAME HEIGHT32.12 32.12 39.00 39.00 40.00 R MOUNTING HOLE DEPTH 10.00 10.00 13.00 13.00 16.00 S MOUNTING HOLE WIDTH 11.25 11.25 12.75 12.75 17.00 T MOUNTING HOLE .53 .53 .62 .62 .65 U OVERALL WIDTH 23.75* 23.75* 25.25* 25.25* 29.50* V OVERALL HEIGHT 39.50* 39.50* 46.50* 48.00* 52.00* W OVERALL DEPTH20.00* 20.00* 23.12* 23.12* 29.75* X BACK FOOT MOUNTING 1.00 1.00 1.00 1.00 1.25 YFRONT FOOT MOUNTING5.005.00 4.004.00 6.75GENERAL SPECIFICATIONSModel No.C-100(discontinued)C-250C-300C-400C-500Tons at 100 PSI Air1 2-1/2 5-1/2 10 15 Power Ratio (No. x air line PSI= Approx. Force 20 50 110 200 300 Max. Ram Stroke (adjustable 2” shorter)5-3/16 5-3/16 6 4 6 Cubic in. of Pressurized Air Per Full Stroke Cycle 251 577 1562 1865 4521 Air Cyl. Port Pipe Size - 4 Way Control Valve 3/8 1/2 3/4 3/4 1” Return Force at 100 PSI628108010802003AIR CYLINDER Inside Diameter 4-1/2 6 8 8 12 Rod Diameter 2 2-1/8 2-1/2 1-7/8 3-1/4 Stroke8 10-1/4 15-5/8 18-1/2 20-3/16RAM CYLINDER Inside Diameter 2-1/2 3 4 4 5-3/4 Top Rod Diameter .625 .750 1.000 1.000 1.250 Bottom Rod Diameter .875 1.00 1.500 1.500 2.750 NET WEIGHT250350500650800M odel’s C-100, C-250, C-300, C-400 and C-500Preventative Maintenance and Trouble Shooting1.Before any preventative maintenance is performed, turn off air supplies to press andblock up ram, following OSHA and local Lock out/Tag out procedures.2.Keep the oiler/lubricator filled with Mobil DTE grade 24 or equivalent. Lubricator isadjusted at the factory, but it should be reviewed monthly. The larger the cylinder area, the more lubrication the press needs. Use the following chart for a general rule of thumb.Model No. Cycles per drop10C-100(discontinued)C-250 10C-300 7C-400 7C-500 5If the press ram is chattering, then you may need to increase lubrication. If you are getting too much oil out of the exhaust air muffler, then you may need to turn down the lubricator.3.Review and inspect air filter, it should be removed and replaced once the filter elementturns tan or a brownish color.4.Oil should be changed in the press if the color is dark brown or after 5 years, whichever comes first5.Oil Reservoir should be check daily and filled to proper level.6.Check press for oil leakage at the following indicators;a.Bleed off hole or ram vent hole; a small 1/8” diameter hole located in thefront of the machine, at the ram guide. If oil or air is coming out of thishole, this indicates that the seal needs replacing. Note, this hole can not beblocked or covered.b.Booster Bleed-off Line; the 1/8” tube located in the back of the machine,coming from the side of the middle of the booster, going to the TOP of theoil reservoir. If there is oil in this line, this is an indication that the sealsneed to be replaced.c.Air muffler; an excessive amount of oil coming out of the air muffler is anindicator that the lubricator needs to be turned down and/or seals need to bereplaced.d.Oil Reservoir; if you have to fill reservoir frequently, then there is apossibility that seals could be worn and need replacing.7.Check all safety devices DAILY, for proper operation. If they are not functioningproperly, DO NOT USE PRESS!8.Frequently asked questions:QUESTION: Why is hydraulic oil is coming out of the reservoir?ANSWER: There are excessive amounts of air in top side of the ram cylinder or in the top of the oil side of the booster. With the ram in the home position, bleed oil side of system by unscrewing the two caps until all air has been exhausted. Do not remove caps. See page 4 of manual sent with machine. This could be caused by short stroking the press, preventing the ram from returning to the home position. It may also be caused by ram drifting down; overtime the reservoir appears to be empty, refilling it at this time will overfill the system. If this does not solve the problem, then seals need to be replaced. They are either installed incorrectly or need replacing.QUESTION: Hydraulic oil levels in the reservoir go up and down when press is cycled. ANSWER: There is a small amount air trapped in the hydraulics system. You need to bleed the air out of the system, see page 4 of manualQUESTION: After several cycles, I lose ram pressure or force.ANSWER:The air volume to the press is not adequate or the filter(s) needs replacing. Make sure you have a minimum of 3/4" air line to the press from the drop. Check air pressure drop at inlet when press cycles; it should not drop below 75 psi. Increase air volume to press.QUESTION: Hydraulic oil is in the vent tube, the tube that comes out of "top" of the reservoir and goes down into the "side" of the air cylinder top head (middle of the booster); is that normal?ANSWER: No, this indicates that the hydraulic seals in the air cylinder top head are worn and eroded and need to be replaced. Assure that new seals are installed properly. If installed upside down or are damaged while being installed, the problem will remain. QUESTION: I'm not sure, but I think air is getting in my hydraulic system. How can I test this?ANSWER: There are two places which air can by pass seals and enter into the closed hydraulic system; through the booster or the ram. The ram cylinder can be tested in the following manner: Make sure ram is in the retracted mode. Remove the ram guide from the ram, exposing the 1/8" by- pass hole, located on the front side of the ram. Place soapy water over the 1/8'' hole (similar to finding leaks in a natural gas line). If it blows a bubble, air is "by passing" the seal and entering the hydraulic system. The bottom seal of the ram cylinder needs replacing. When assembling the ram guide, be sure the slit is in position over the hole & not plugging it. You can test the booster again by applying air to the booster through the ram retraction side. Remove the 1/4" tube going to the top of the reservoir and coming out of the side of the booster cylinder (air side) top cap. Put the tube in jar of water, if it blows a bubble, the bottom seal in the booster needs replacing.QUESTION: During the first cycle of the press, after being shut down over the weekend, oil will erupt from the reservoir top. What is causing that?ANSWER: To prevent the eventual drifting down or closing, when the air supply to this press is turned OFF, the die set or tooling should be blocked in an OPEN position due to weight of tooling attached to the ram of this press. This will keep the closed hydraulic circuit of this press from becoming imbalanced, misleading the circuit to siphon oil from reservoir top unnecessarily, which could damage the press.QUESTION: After several cycles, I get oil bubbling out of the oil reservoir and there is air coming out of the vent hole of the ram.ANSWER: The problem is in your Ram Cylinder. The "U" Cup seals are installed incorrectly, damaged or worn, and/or the "O"-rings (located where the piston attaches to the ram) are in need of repair, replacement or are missing. Air is coming from the rod/bottom of the cylinder, going up through the button "U" seal on the piston, or through the "O"-rings; allowing air to enter into the closed hydraulic system, therefore, being relieved through the reservoir. If the oil is bubbling to the point of over flowing, then the seals/"O"-rings are extremely damaged, or the seals are installed backwards or are missing.QUESTION: There is air building up in my reservoir. I can feel it when I put my finger over the hole, but it is NOT bubbling up through the oil in the reservoir.ANSWER: The problem may be in the booster. You can further test this by applying air to the booster through the ram retraction side (top port). Remove the 1/4" tube going to the top of the reservoir and coming out of the side (not the top) of the booster cylinder (air side) top cap. Put the tube in jar of water, if it blows a bubble, the bottom seal in the booster needs replacing or was installed incorrectly.Force rating in Tons @ 100psiAir Pressure (PSI) at Press's Regulator Press orRam (cylinder rod) force in U.S. lbsHydraulicPSI Gauge reading Press or Ram (cylinder rod) force in U.S. lbs Hydraulic PSI Gauge reading Press orRam(cylinder rod) force in U.S. lbs HydraulicPSI Gauge reading Press or Ram (cylinder rod) force in U.S. lbs HydraulicPSI Gauge reading 402,000 319 4,400 409 8,000 728 12,000 545 452,250 359 4,950 460 9,000 819 13,500 613 502,500 399 5,500 512 10,000 910 15,000 682 552,750 438 6,050 563 11,000 1,001 16,500 750 603,000 478 6,600 614 12,000 1,092 18,000 818 653,250 518 7,150 665 13,000 1,183 19,500 886 703,500 558 7,700 716 14,000 1,274 21,000 954 753,750 598 8,250 767 15,000 1,365 22,500 1,022 804,000 638 8,800 818 16,000 1,456 24,000 1,090 854,250 677 9,350 870 17,000 1,547 25,500 1,159 904,500 717 9,900 921 18,000 1,638 27,000 1,227 954,750 757 10,450 972 19,000 1,729 28,500 1,295 1005,000 79711,0001,023 20,0001,82030,0001,363Intensifier's Multiplier 507.9711010.2320018.230013.63Notes:2-1/2C-300B-300C-400B-400C-500B-50015105-1/2Air-Hydraulics "C" Series Presses & "B" Series Booster and Cylinder PackagesTo use this table, identify press’s or cylinder’s model and hydraulics oil pressure from your gauge. Example, if youhave a Model C-400 Press and the air pressure at the Press’s regulator is reading 80 psi, the hydraulics pressure gauge, should be reading approx. 1,456 psi and the force of the press’s ram should be approx. 16,000 lbs. or 8 tons.This assumes that the hydraulics oil pressure is metered or taken from the top side of the Work (Ram) Cylinder, through the 1/4" NPT Sensor Port. Depending on what options were purchased with your machine, some machines have the hydraulic gauge already installed.Air Pressure vs. Press Force vs. Hydraulic Oil PressureModel #Not all presses have hydraulics pressure gauges. It depends on the control package purchased with the press.C-250B-250。
空气预热器介绍 ppt课件
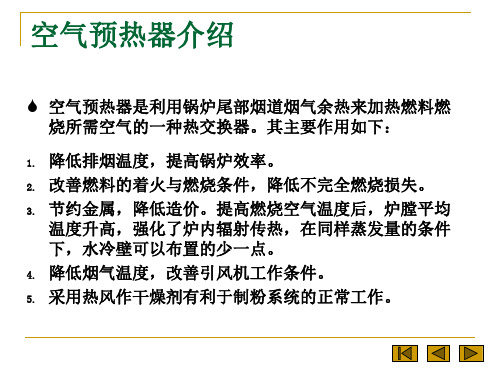
空气预热器介绍
2. 为了增强气流的扰动同时又不使气流阻力过大,波形板 的斜纹应与气流成30度角。
3. 为了防止低温段堵灰和积灰,在低温段波形板的波形被 放大,定位板则采用平板结构。
空气预热器介绍
3. 漏风及密封装置: 回转式预热器的转子与静止的外壳之间总是存在一定的间隙,由于
预热器内的空气区呈正压,而烟气区为负压,就导致一部分空气通 过交界处的间隙而漏到烟气中去,这种经动静之间间隙的漏风称为 间隙漏风。 对于三分仓空气预热器,它不但有空气区与烟气区之间的间隙漏风, 还有一次风仓与二次风仓之间漏风。 此外,外界的空气也可以通过转轴和机壳之间的间隙漏入烟气区。
垂直撞击力引起撞击磨损,斜向撞击的切向力引起摩擦磨 损。飞灰磨损易发生在烟速高和飞灰浓度较大的地方。飞
灰对受热面的磨损是不均匀的。
飞灰磨损的危害:受热面管子磨损,强度下降,引起管子 泄漏事故。
空气预热器介绍
影响磨损的因素:
1. 烟气流速:管子的磨损和烟速的三次方成正比。 2. 飞灰浓度:飞灰浓度大,磨损严重。气流转弯、烟气走
空气预热器介绍
空气预热器
传热式
蓄热式
管式空气预热器
回转式空气预热器
受热面回转式
风罩回转式
传热式预热器中热量通过受热面由烟气传给空气,烟气和空气各有自己 通路。
蓄热式预热器中烟气和空气相互交替流经受热面,当烟气通过受热面时, 热量由烟气传给受热面金属,并被金属蓄积起来,然后使空气通过受热 面,金属就将蓄积的热量传递给空气。受热面每旋转一周完成一个热交 换过程。
廊等局部地方飞灰浓度高,磨损严重。 3. 灰粒特性:灰粒越粗、越硬,撞击与切削作用越强,磨
损越严重。没烟气流向,温度降低,灰粒变硬,磨损加 重。 4. 管束结构特性:烟气纵向冲刷较横向冲刷磨损轻,错列 的第二排、顺列的第五排磨损较严重。 5. 运行中的因素:锅炉超负荷运行时,飞灰浓度及烟气流 速增大;烟道漏风造成烟速增大,均会造成磨损加重。
PRO 100系列燃气加热操作手册说明书

- Switch on the machine using the main power switch (red color) and check if the machine is rotating.
NOTE: For SPG1 models, verify that the cooling fan at the exhaust in the back of the machine is working.
AC-155LP 空气加热器用户手册说明书

AC-155LP SPACE HEATER2 Operator’s ManualPageSafety (4)Controls (9)Preparation (10)Installation (12)Operation (12)Troubleshooting (14)Service (16)Storage (17)Specifications (18)Wire Diagram (19)Warranty (20)Notes (21)All information, illustrations and specifications in this manual are based on the latest information available at the time of publication. The right is reserved to make changes at anytime without notice.Operator’s Manual 34 Operator’s ManualOperator’s Manual56Operator’s ManualOperator’s Manual78Operator’s ManualINSPECT SPACE HEATERBe sure all covers, guards and shields are tight and in place.Locate all operating controls and safety labels.Inspect power cord for damage before using. There is a hazard of electrical shock from crushing, cutting or heat damage.Remove all packing items applied to space heater for shipment. Remove all items from carton. Check items for any shipping damage. If space heater is damaged, promptly inform dealer where you bought space heater.SERVICE SPACE HEATER SAFELYBefore servicing the space heater, disconnect all equipment and battery (if equipped) and allow unit to cool down.Service space heater in a clean dry flat area.Operator’s Manual 9A -- Hot Air Outlet (Front)B -- Upper ShellC -- HandleD -- Fan GuardE -- Power CordF -- Thermostat KnobG -- Hose / Regulator Assembly H -- Inlet Connector I -- On / Off Switch J -- Lower Shell10 Operator’s ManualOperationOPERATION5. Plug extension cord into a 120 volt/60 hertz, 3-hole, grounded outlet.6. Open propane supply valve on Propane / L.P. tank(s) slowly.Note:If not opened slowly, excess-flow check valve on Propane / L.P. tank will stop gas flow. You may hear a click from the excess-flow check valve closing. If this happens, reset the excess-flow check valve by closing propane supply valve and open again slowly.7. Turn thermostat control knob fully counterclockwise to the "cooler" position. Turn ON/OFF switch to the ON position. Turn thermostat control knob slowly clockwise until electric motor and fan begin to run. Heater will start in approximately 3 seconds. Adjust thermostat control knob to warmer or cooler setting as needed.Note: If heater does not start after 3 seconds, the ignition control will automatically attempt to start heater one time. If heater fails to start on this attempt, the safety control will "lock out" and no further automatic restarts will be attempted. This could occur if air remains in fuel line. If heater fails to start on this attempt, turn ON/OFF switch to OFF position. Wait ten seconds for safety control to reset, then turn ON/OFF switch back to ON position and try to start heater again.8. Thermostat Operation Only: During normal thermostat operation, heater will cycle off when air temperature rises to thermostat setting. When air temperature drops sufficiently below thermostat setting, the electric motor and fan will begin to run. After 15 to 60 seconds, heater burner should automatically ignite and provide heat to maintain temperature setting.STOP SPACE HEATER:1. Tightly close propane supply valve on Propane / L.P. tank(s).2. Wait a few seconds. Heater will burn gas left in supply hoses.3. Turn ON/OFF switch to the OFF position.4. Unplug heater.StorageITEM SPECIFICATIONModel Size AC-155LPOutput Rating (BTU / Hr) 150,000Fuel Propane Vapor OnlyFuel Consumption:(Gal. Per Hr / Liters Per Hr) 1.6 / 6.1(Pounds Per Hr / Kilograms Per Hr) 7.0 / 3.2Supply Pressure to Regulator:Minimum (for input adjustment) 10 PSI / 65.98 kPaMaximum Tank PressureRegulator Outlet Pressure ******************"WC/31.8cm Manifold Pressure 9.8" WC / 24.9 cmHot Air Output (Approx.) 550 CFM / 15.6 cubic meter / minute Motor RPM 3450Motor HP 1/8Electric Input 120V / 60HzAmperage (Normal Run) 2.2Ignition Electronic Direct Spark, D.S.I. Ignitor Gap 0.13 in / 0.15 in (3.3 mm / 3.8 mm) Shipping Weight(Approximate Pounds /Kilograms) 35 / 15.9Space Heater Weight(Approximate Pounds /Kilograms) 27 / 12.2RECORD SERIAL NUMBERWrite you model number, machine serial number anddate of purchase in the spaces provided below. Yourdealer needs this information when ordering parts.Model No. ______________________________________________Machine Serial No. _______________________________________Date of Purchase ________________________________________(To be filled in by purchaser)STATEMENT OF WARRANTYJohn Deere warrants all parts, (except those referred to below), of your new space heater to be free from defects in materials and workmanship during the following periods: For One (1) Year from the date of original purchase.Defective parts not subject to normal wear and tear will be repaired or replaced at our option during the warranty period. In any event, reimbursement is limited to the purchase price paid.EXCLUSIONS1. This warranty does not cover parts damaged due to normal wear, misapplication,misuse, operation at other than recommended. Failure to follow recommended operating and maintenance procedures also voids warranty.2. The use of other than genuine manufacturer repair parts will void warranty.3. Warranty will be void if used in any application other than consumer / homeowner.Parts returned, prepaid to our factory or to an Authorized John Deere Service Center will be inspected and replaced free of charge if found to be defective and subject to warranty. There are no warranties which extend beyond the description of the face hereof. Under no circumstances shall the manufacturer bear any responsibility for loss of use of the unit, loss of time or rental, inconvenience, commercial loss or consequential damages.For Service or Warranty Consideration, contactMi-T-M® Corporation, 8650 Enterprise Drive, Peosta, IA 520681-877-JD-KLEEN / (1-877-535-5336) Fax 563-556-1235Monday - Friday 8:00 a.m. - 5:00 p.m. CST。
12KW燃油加热器安装使用维护说明书课件

C24LR-ZJN-12AC12LR-ZJN-12B/C智能节油暖车器使用维护说明书朝阳朗瑞车辆技术有限公司售后服务电话:400-106-0005前言感谢您使用朝阳朗瑞智能节油暖车器朝阳朗瑞智能节油暖车器是柴油机的一个附加装置,具有独立的加热功能。
暖车器以车载电瓶为热源动力,通过燃烧车辆自身的燃油产生热量。
暖车器的循环系统与发动机的冷却系统连接在一起,在发动机不工作时,暖车器自带的水泵将产生的热量传递给发动机,进行预热,从而提高发动机机体的启动温度,解决发动机在低温下启动困难,磨损严重的历史性难题,缩短发动机怠速升温的环节,节约燃油消耗,还可以提高驾驶室内的温度,给驾驶员一个温暖舒适的驾驶空间,在冰雪的世界里自由驰骋。
暖车器采用单片机进行全自动控制,产品体积小,重量轻,结构紧凑,安装方便,维护保养简单,安全可靠。
本手册内容有可能改动,恕不另行通知,但本手册内容与所购产品一致。
公司保留对说明书中描述产品进行修改而不事先通知的权利,最终功能以实际产品为准,本公司具有最终解释权。
如果在使用中出现故障,请与我公司销售部或指定的服务网点联系。
本公司竭诚为您服务。
目录警示页 (1)1暖车器的安装 (2)2暖车器电磁泵的安装 (3)3暖车器安装后的调试 (3)4暖车器主要技术参数 (4)5暖车器的功能及操作步骤 (4)6 线束连接示意图 (5)7 故障显示功能 (5)8 常见故障分析与排除 (6)9 常规维护保养 (7)10 遥控器连接及使用 (8)警示页危险!在任何加热过程中,都要在关闭暖车器控制开关3分钟后,才能关闭暖车器电源开关,否则会有激热爆炸隐患!警告!在暖车器安装后,首次进行加热前必须将放气螺栓放松,将管路中的气体排出,然后再进行加热!※暖车器严禁无水干烧 !※暖车器裸漏导线严禁拉扯,碾压 !注意!1、暖车器总成的安装必须平稳、牢固,避免暖车器在随车使用过程中出现松动现象。
2、暖车器进出水管在安装过程中要保证一一对应关系。
空气电加热器使用说明书
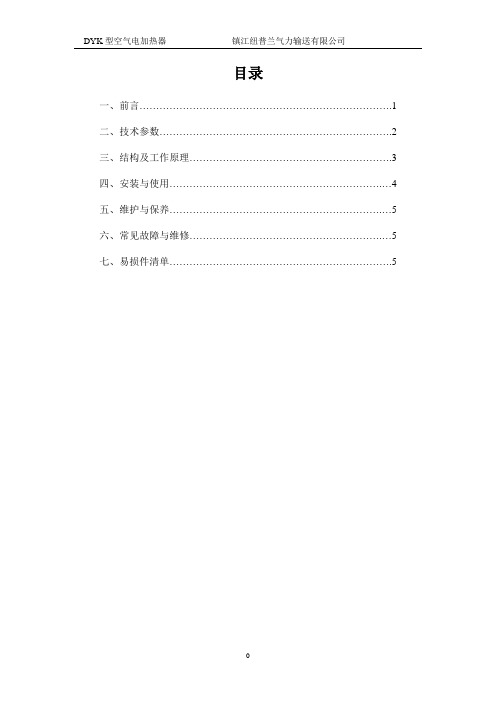
目录一、前言 (1)二、技术参数 (2)三、结构及工作原理 (3)四、安装与使用 (4)五、维护与保养 (5)六、常见故障与维修 (5)七、易损件清单 (5)前言DYK型空气电加热器是我厂近年来研制成功的专门供燃煤发电厂除灰系统使用的新型加热设备,该设备由空气电加热器本体和控制系统两部分组成。
发热元件采用1Cr18Ni9Ti不锈钢无缝钢管作保护套管,OCr27A17MO2高温电阻合金丝、结晶氧化镁粉,经压缩工艺成型,使电加热元件的使用寿命得以保证。
控制部分采用先进的数字电路、集成电路触发器、可控硅等组成可调测温、恒温系统,保证了电加热器的正常运行。
该产品适用于电站空气输送斜槽气化风加热,电除尘器灰斗气化风和贮灰库气化风加热等方面。
二、技术参数(1)空气电加热器的规格与参数(表一)(2)控制柜的主要技术指标数据1.输入电压:380V±5%(三相四线)2.额定功率:15KW~90KW3.额定电流:23A~136A(单相)4.输出电压:≤210(单相)5.控温精度:0.5级6.控温范围:0~400℃三、主要结构及工作原理(1)空气电加热器结构(一)空气电加热器是由多支管状电热元件、筒体、导流板等几部分组成,管状电热元件是在金属管内放入高温电阻丝,在空隙部分紧密地填入具有良好绝缘性和导热性能的结晶氧化镁粉,采用管状电热元件做发热体,具有结构先进,热效率高,机械强度好,耐腐、耐磨等特点。
简体内安装了导流隔板,能使空气在流通时受热均匀。
(2)控制柜外形图(图二)(3)工作原理SWK-A型数显温度控制柜采用数显温度调节仪,集成电路触发器,大功率可控硅和测温元件组成测量、调节、控制回路,在电加热过程中测温元件将空气电加热器出口温度电信号送至数显温度调节仪进行放大,比较后显示测量温度值,同时输出0-10V电压信号到可控制硅触发组件的输入端,控制输出脉冲相位,从而控制可控硅导通角度大小,使控制柜具有良好的控制精度和调节特性。
Exheat FUH型风扇辅助空气加热器安装操作指南说明书

INSTALLATION OPERATIONAND MAINTENANCE INSTRUCTIONS FOREXHEAT FUH TYPEFAN-ASSISTED AIR HEATERS1.0 GENERAL1.1 All work should be carried out by suitable qualified personnel.1.2 Carefully remove all packaging and visually inspect unit for any transit damage.1.3 Before connection ensure that the supply corresponds with that specified on the rating label.1.4 Each heater must be protected by a suitably rated over current device.1.5 All prevailing rules, regulations and bylaws in force at the time and place of installation must be observed.1.6 Any modification not carried out by Exheat Limited or its approved agent will invalidate certification and warranty.1.7 The heat exchanger unit is factory sealed and contains a mixture glycol and water. If a leak occurs, it must beisolated and Exheat contacted for further advice.1.8 No user serviceable components are contained within the motor loading, any attempt to disassemble the motor willvoid warranty and certification.2.0 INSTALLATION2.1 The Heater must be mounted upright using only the suspension points at the top of the unit (fig.1) and appropriatemounting brackets2.2 The heater must be positioned to allow unrestricted entry of air at the back and exit at the front via the adjustablelouvers. A minimum of 2 metres clearance must be maintained in front of the heater.2.3 The unit must be checked for leakage after mounting in position and before making electrical connections.SUPPLY CONNECTIONS3.0 ELECTRICAL3.1 Refer to the electrical wiring diagram (fig.2) and make all connections in accordance with it.3.2 All external connections are made in the main heater terminal box, which is accessed by removing the bottom coverof the heater.3.3 To remove the bottom cover, undo the bolts securing it (fig.1) and slide the cover down.3.4 The terminal box cover is removed by slacking the locking grub screw and then unscrewing the cover.3.5 Re-fitting is the reverse of 3.3 and 3.4 ensuring that the locking grub screw is re-tightened after re-fitting the cover.3.6 The electrical supply must be via a suitable isolator and suitable high temperature cable must enter the terminal boxvia a certified Ex d IIC cable gland (not supplied)3.7 External control may be installed via terminal 1 and 2.3.8 Any unused cable entries must be plugged using an Ex d certified plug.CONNECTION4.0 EARTH4.1 WARNING - this equipment MUST BE EARTHED4.2 Earth termination points are incorporated both internally and externally to the main heater terminal box5.0 OPERATION5.1 Ensure that all connection and covers are secure and that any dirt, debris and loose objects have been removed.5.2 Check correct rotation of fan (clockwise viewed from motor,) if it is incorrect check and change the supply phasesequence.5.3 If no external control is fitted, connect the wire link between terminals 1 and 2.5.4 Once energized, the heater will operate continuously unless optional external controls are connected.5.5 The heater is certified for operation in an ambient temperature of up to 40° C and the user must ensure that this isnot exceeded at any time. Exheat can supply from a suitable range of hazardous area thermostats if required. Please contact our sales engineers for advice.6.0 MAINTENANCE6.1 All prevailing site safety regulations shall be adhered to at all times.6.2 Before and whilst any maintenance activity is carried out, it must be ensured that there are no hazardous gasespresent.6.3 Equipment is to be fully isolated from the electrical supply before and whilst any work is being carried out.6.4 Any damage or faults should be notified to Exheat Limited immediately.6.5 For equipment certified for use in hazardous areas reference should be made to EN60079-17 (especially table 1) inaddition to the following recommendations.6.6 The motor must be cleaned at regular intervals (depending on the environment) especially the motor fan, emptydebris to guarantee sufficient cooling air flow through the motor cooling system.6.7 Any replacement parts required must be obtained directly from Exheat. The use of any other parts will void anycertification and warranty.MONTHLY6.7.1 3a. Generally, inspect the equipment for external damage.b. Ensure that the spaces between the element fins remain clear and that the airflow remains unrestricted.c. Remove bottom cover and ensure that there are no signs of fluid leakage from the heat exchanger (see 1.7above.)d. Check front louvers to ensure they have not been damaged or become loose. Should they become loose theymay be tightened individually after removing their support frame, which is secured with 4 screws (fig.1.)6.7.2 6MONTHLYa. Carry out checks as 6.7.1 above.b. Isolate the electrical supply and remove the bottom cover, heater terminal box cover and motor.c. Internals should be clean and dry.d. Ensure terminals are intact and secure.e. Heating element insulation resistance to be at least 2 megohm.f. Refit covers with new ‘O’ ring if required.6.7.3 ANNUALLYa. Carry out checks as 6.7.1 and 6.7.2 above.b. Check for element failure or low insulation resistance.6.8 Only Exheat Ltd or its approved agent may carry out repairs to the heater otherwise the Hazardous Area certificationwill be invalidated.6.9 If heaters are being left unused for a period greater than 3 months, carry out 6 monthly maintenance beforeenergizing.7.0 Marking7.1 II 2 GEx d IIC T38.0 Certification8.1 LCIE 02 ATEX 6235ModelFuses F1-F3KW/Voltage Dimensions (mm) WeightkG 380V 415V 440V 480V ‘A’ ‘B’ ‘C’ ‘D’ ‘E’ ‘F’ G ‘H’‘J’ FUH 9 3A 7 9 10 12 610290235900 146217 187 50 267120 FUH12 3A 10 12 13 16 610290235900 146217 187 50 267120 FUH15 5A 13 15 17 20 7603002601052 156242 192 50 304145 FUH20 5A 27 20 23 27 7603002601052 156242 192 50 304145 FUH30 5A2530 - - 7603002601052 156242 192 50 30414573/23/EEC89/336/EEC94/9/ECStock Code S090-00-0000-0027Issue D。