车门装饰板技术规范
汽车门内饰板嵌饰板制造工艺分析及质量控制

汽车门内饰板嵌饰板制造工艺分析及质量控制汽车门内饰板是车门内部的装饰板,通常由塑料制成,用于美化车门内部环境和提升车内舒适度和豪华感。
门内饰板的制造工艺和质量控制对于确保它的美观、耐用和安全性能至关重要。
下面将对汽车门内饰板的制造工艺和质量控制进行分析。
第一,模具制造。
汽车门内饰板的制造首先需要制作适应其形状和尺寸的模具,通常采用金属材料制作。
制作模具过程中需要考虑到内饰板的曲线和空间要求,确保模具的精度和可靠性。
同时,模具制造也需要合理安排冷却系统,以确保塑料注塑过程中的均匀冷却和收缩。
第二,塑料注塑。
制造汽车门内饰板通常采用塑料注塑工艺。
注塑过程中,需要选择适合内饰板的塑料材料,并通过控制注塑温度、注塑压力和注塑时间等参数,确保内饰板的成型质量。
此外,还需要考虑塑料流动路径设计,避免产生破损、缩孔、热胀冷缩等缺陷。
第三,表面处理。
汽车门内饰板的表面需要经过处理以提升其质感和耐用性。
常见的表面处理方法包括喷涂和贴膜。
喷涂过程需要注意底漆和面漆的选择和涂装工艺的控制,确保饰板的颜色、光泽和附着力。
贴膜过程则需要注意膜的选择和贴合工艺的控制,确保膜的平整度和附着力。
第四,装配过程。
制造完成的汽车门内饰板需要进行装配到车门上。
在进行装配过程中,需要确保饰板与车门的尺寸和形状完全匹配,同时需要注意装配零件的固定和连接方法,确保饰板的安全性和稳定性。
以上是汽车门内饰板制造工艺的基本分析,下面将对其质量控制进行讨论。
首先,原材料的质量控制。
选择合适的塑料材料,并进行合格供应商的认证和质量检测,确保原材料的可靠性和符合相关标准。
其次,注塑成型工艺的质量控制。
通过在线监测和离线检测等手段,对注塑过程中的温度、压力和时间等参数进行监控和调整,确保内饰板的成型质量和一致性。
第三,表面处理的质量控制。
对表面处理过程中的涂装或贴膜工艺进行监测和调整,确保饰板的颜色、光泽和质感符合要求,并进行耐候性和耐磨性的测试和评估。
车门护板技术要求

Q/FT 北汽福田车辆股份有限公司企业标准Q/FT A001—20002000—12—20发布2001—01—01实施北汽福田车辆股份有限公司发布车辆产品车门护板技术条件Q/FT A001—2000前言本标准是根据有关国家标准和行业标准制定的。
在确定车门护板各项性能时,针对不同产品市场定位及成本控制的需要,进行了差别化确定。
本标准自2001年1月1日开始实施。
本标准由北汽福田车辆股份有限公司技术标准化委员会提出。
本标准由北汽福田车辆股份有限公司技术标准化委员会秘书处归口。
本标准起草单位:北汽福田车辆股份有限公司技术研究院产品管理部。
本标准主要起草人:袁军成、石同军、赵淑珍。
本标准于2000年12月首次发布。
北汽福田车辆股份有限公司企业标准Q/FT A001—2000车辆产品车门护板技术条件1范围本标准规定了车门护板的技术要求、试验方法、检验规则、标志、包装、运输、贮存及质量保证。
本标准适用于本公司汽车、农用车(含拖拉机变型运输机,下同)产品注塑成型的车门护板(以下简称护板)。
2引用标准下列标准所包含的条文,通过在本标准中引用而构成为本标准的条文。
本标准出版时,所示版本均为有效。
所有标准都会被修订,使用本标准的各方应探讨使用下列标准最新版本的可能性。
GB/T1040-1992塑料拉伸性能试验方法GB/T1634-1989塑料弯曲负载热变形温度(简称热变形温度)试验方法GB/T1843-1996塑料悬臂梁冲击试验方法GB/T2828-1987逐批检查计数抽样程序及抽样表(适用于连续批的检查)GB8410-1994汽车内饰材料阻燃特性GB/T9341-1988塑料弯曲性能试验方法GB/T9344-1988塑料氙灯光源曝晒试验方法QC/T15-1992汽车塑料制品通用试验方法Q/FT B102-2000车辆产品零部件标识规定3技术要求3.1护板应按经规定程序批准的图样及技术文件制造,并应符合本标准的规定。
J013_车门内护板设计规范标准

Q/XRFxxxxx公司Q/XRF-J013-2015xxxx车门护板设计规编制:日期:校对:日期:审核:日期:批准:日期:2015-03-15发布 2015-03-15实施xxxxx公司发布前言随着汽车工业的日新月异,人们对汽车饰的追求也在不断提高。
作为汽车饰重要的组成部分—车门饰板,舒适性、可靠性、美观性越来越成为人们追求的目标。
对车门护板的正确设计,将会给试制、批量生产、整车商品性带来事半功倍的效果。
本文对我公司车型车门护板的设计进行详细介绍。
1.吸能块和周边零件间隙序号容基准值(mm)1 与车窗玻璃的间隙102 与车门板便面的间隙 53 与车门板孔的间隙104 与车门饰的间隙 22.扣手的设定标准序号容基准值(mm)参考1 I/S扣手长度<685 最大限度760mm2 从OPONING开始的位置>480 最小限度420mm3 竖立把手开始位置120~1404 扣手盖板周围间隙(前后方向) 25 扣手盖板周围搭接量 16 扣手盖板周围间隙(上下方向) 37 扣手盖板周围间隙(上下方向) 23.M/W调节器手柄设定标准序号容基准值(mm)参考1 调节器手柄的长度<6702 从乘坐参考点开始到扣手中心高度>1303 与车门储物盒的距离>1604 与肘靠的距离>904 与肘靠的距离>60 应用参考手册表面高度5 与仪表板的距离>1306 从坐姿的距离参照左图4.电动控制钮的设定标准5.肘靠的设定标准序号 容基准值(mm ) 参考1 对应室冲击必要条件的场合>2 in纵面倾斜15°以 2对应室部突出物必要条件的场合>R3.5适合围清参考上图*1 推荐高度=(0.6+30)+SEAT BACK ANGLE 修正值±10上限高度=0.6d+50 下限高度=0.6d1 电动控制钮的长度 625~7252 从把手开始的距离 >1403 从把手开始的角度<184 前后倾斜角 0~10° 前面提升至10°5 左右倾斜角 0~5° ARM 表面高度6 与饰表面的距离 ≥25序号容基准值(mm)参考1 肘靠上面的高度(H)根据*1计算式从SRP(JM50%)开始2 肘靠长度(SRP的前侧)170±20 SRP(JM50%)3 同上(SRP的后侧)110±20 同上4 ARMREST上面的前后倾斜5~6度5 ARMREST上面的左右倾斜0~5度6 ARMREST上面的宽度>707 室冲击吸收方式侧面宽度15 θ3<15°6.缝隙间的设定标准序号容基准值(mm)参考1 与仪表板的缝隙 52 视觉补正上图参考3 与SASH的缝隙 24 与UPPER和LOWER的搭接尺寸上图参考序号容基准值(mm)参考1 车门饰与B柱装饰件的间隙 5 水平方向2 车门饰与B柱装饰件的间隙 5 车副方向3 抽取倾斜角10度4 车门板的突出部分与饰的间隔 5注意:1.终端在OVERHANG的时要设定漂亮的镶边2.从OPNING的缝隙不应该看见车体的颜色7.操作性的设定标准序号容基准值1 拖拽把盒水平把手区域:R1 <5002 拖拽把盒水平把手区域:R2 >4003 拖拽把盒水平把手区域:R3 <4004 拖拽把盒水平把手区域:R4 <10005 纵把手区域:R1 <5206 纵把手区域:R2 400~5007 纵把手区域:R3 <10008 纵把手高度:H 200~2709 纵把手区域:R3 68~78度序号容基准值(mm)参考1 车门饰与座椅坐垫的缝隙>60 极限值50mm2 车门饰与储物盒之间的缝西>55 极限值40mm3 门在打开情况下的乘降空间>3004 座椅靠背与扶手的间隙>255 座椅操作杆操作空间>408.扬声器网格的设定标准序号容基准值(mm)参考1 网格部位的开口率40%2 网格部位的开口率(TWEETER)50% 高音用9.踏板照明的设定标准序号容基准值(mm)参考1 开启门的可视角度15度2 脚下的可视性(着地点亮光度)3L3 脚下的可视围上图参考10.乘车性的设定标准序号容基准值(mm)参考1 从SRP到前车门饰的距离310~360 极限值290mm2 从SRP到后车门饰的距离330~380 极限值310mm3 玻璃升降器摇把与膝盖的关系上图参照11.拖拽把手的设定标准序号容基准值(mm)参考1 把手部位的长度100~1202 把手部位的宽度30~403 手抠(BOX)部位的深度>554 把手部位的粗度:h 25~354 把手部位的粗度:b 20~255 手抠(BOX)部位的角度-8度极限值13度6 拖拽把手的位置50~1507 把手部位的刚性6kg12.纵把手的设定标准序号容基准值(mm)参考1 从SRP到把手的距离350±502 角度60~70度3 把手部位的粗度20~254 有效长度>1105 到玻璃升降器摇把的距>90离6 P/W控制钮间隔的距离>807 从把手区域<52013.储物盒的设定标准序号容基准值(mm)参考1 宽(尽可能做大)40 地图的厚度+52 高度100 EU:703 长度320 地图长度+104 地图收纳状态上图参照1:加强筋一般布置5~6根,筋厚0.5mm2:在有加强筋区域可以适当的增加料厚0.3~0.4mmLD DOOR TRIMCOPOLLA DOOR TRIMXD DOOR TRIMRS FACE LIFT DOOR TRIMBL DOOR TRIMGQ DOOR TRIM14.车用密封条操作指南车用3M胶1.概述本操作指南适用于用压敏胶带把橡胶密封条装配到汽车和卡车的操作工艺。
SJR车门内饰板技术规范

T28Q丹阳盛吉瑞汽车配件有限公司企业标准Q/321181 JYJ 001-2013 车门内饰板技术规范2013-06-30发布2013-07-01实施丹阳盛吉瑞汽车配件有限公司发布前言本标准是根据有关国家标准和行业标准制定的。
在确定车门内饰板各项性能时,针对不同产品市场定位及成本控制的需要,进行了差别化确定。
本标准由丹阳盛吉瑞汽车配件有限公司技术部提出;本标准由公司负责起草;本标准主要起草人:吴堂军、顾炳宏、张理想;本标准于2013年06月30日由顾俊批准;本标准于2013年07月01日首次发布;本标准所代替标准的历次版本发布情况。
车门内饰板1 范围本标准规定了汽车车门内饰板的技术要求、试验方法、检验规则、标志、包装、运输和贮存等。
本标准适用于汽车车门内饰板。
2 规范性引用文件下列文件对于本文件的应用是必不可少的。
凡是注日期的引用文件,仅所注日期的版本适用于本文件。
凡是不注日期的引用文件,其最新版本下列文件(包括所有的修改单)适用于本文件。
GB8410-2006 《汽车内饰材料的燃烧特性》QC/T15-1992(2005) 《汽车塑料制品通用试验方法》Q/FT A001-2009 《汽车产品车门内饰板技术条件》CL03.189-2006 《技术协议》3 定义和术语3.1 燃烧速度按本标准规定测得的燃烧距离与燃烧此距离所用时间的比值,单位为毫米每分钟(mm/min)4 要求4.1 一般要求产品应符合本标准要求,并按照规定程序批准的图样和技术文件制造。
4.2 外形及安装尺寸产品的外形、安装尺寸符合订货方所同意的图样和技术文件的要求。
4.3 外观质量产品表面应无变形、缩瘪、划伤、斑点、飞边、色差等缺陷;颜色符合色板要求。
4.4 耐温度性能产品经5.3高温与低温试验后,不得有龟裂、剥离、溶胀、变形、松动脱落等现象。
4.5 耐温度交变性能产品经5.4 条款3次冷热循环试验后不得有龟裂、剥离、发粘、开裂等现象。
车门装饰板技术规范
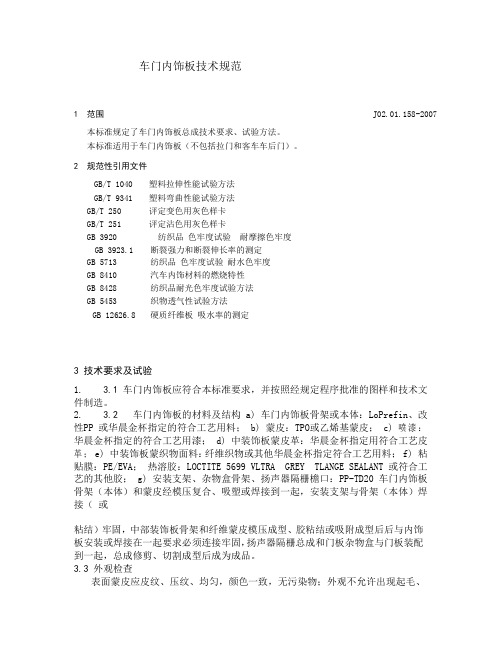
4.5
耐光色牢度 级 (氙灯照射96h) _
≥4
GB 8428
_
阻燃性
吸塑门板 注塑门板
自熄≤60 s ≤100mm/min
GB 8410
拉伸强度
注塑门板
≥19 MPa
门内饰板总成各
吸塑门板
≥25 MPa
4.6
部件焊接或粘结
强度
耐振动性
试样焊接或粘结处不发生开裂现象,试样不损
坏。
4.7
气味试验
≤3.0
a)高温箱;
b)低温箱。 1. 4.4.2 试验方法 2. 4.5 耐寒性
在-40℃和+90℃分别时效24h,及湿度95%下4 8h。
参照QC/T 29089-1992 中6.9 条。 1. 4.6 拉伸强度 2. 4.6.1 试验条件
常温,速度5mm/min +90℃,保温4 小时后,立即进行拉力试验,速度5mm/min; -40℃,保温4 小时后,立即进行拉力试验,速度5mm/min。
耐摩擦色牢度
干摩擦
性能 ≥16 ≥140 20℃时<0.35 60℃时<3.5 <20 ±1.5
≥4 级
试验方法 4.10
4.11 4.12 4.13 4.14
表4 内饰板纤维蒙皮复合材料性能
项目
材料
密度
静态(定负荷)伸长率
纵向 % 横向 %
透气性 L/min/100cm2
抗静电性(表面电阻)Ω
断裂强度 (纵横) N/5cm
5
4.6.2 试验方法 参照GB1040 。
4.7 耐振动性试验 取试样5 块 , 以接近使用状态的条件安装在振动台上;相对于试样的安装方式依次给予上
精品CTS-01050601-A1-门板总成技术规范优秀

耐刮擦性
7.2.9
否则采用 10N 载荷,△L≤2.0
塑料内饰件:≤2mg 雾化特性
其他零件:≤2.5mg
7.2.10
挥发性有
满足 SJ-NW-51《长安车内零部件挥发性有害物质技术限值规范》中
机物
7.2.11
对门板总成 VOC 的要求
(VOC)
6.技术要求 门内饰板总成性能应满足表 1 技术要求。 表 1 门内饰板总成技术要求
评价项目
评价标准
评价方法
6.1
性能 6.2.1 6.2.2
6.2.3 6.2.4 6.2.5 6.2.6
外观
外观 产品外观应与经批准的标准样品相当或满足图纸上所规定的外观要 求。如果没有标准样品,图纸上也没有针对外观特别规定,应按以下 注塑件一般外观要求执行。 1) 产品外观表面不允许有裂纹、变形、银纹、波纹、烧焦、飞边、 毛刺、气泡、浇口痕迹、顶杆印痕、熔接痕和收缩痕等其他缺陷。 2)颜色与标准样板目视评价不得有明显色差。 3)需要做皮纹的部位表面皮纹应清晰、均匀,皮纹符合长安公司提 供皮纹样板。 4)包覆嵌饰板表面不允许有鼓泡、皱折、溢胶、颜色纹理不均匀等 缺陷。
门内饰板总成技术规范
Specification of Door Trim
本文件内容属于长安公司机密,无长安公司正式书面授权,任何单位或个人不得扩散或泄露
长安汽车工程技术规范文件
Engineering Technical Specification of Changan Automobile Co. Lt d
模板编号:CP-0199-V1
长安汽车工程技术规范文件
Engineering Technical Specification of Changan Automobile Co. Ltd
门内饰板设计规范

门内饰板总成设计规范R&D-CS-6102-001-2010门内饰板总成设计规范1 范围1.1 本规范适用于车门内饰板总成设计。
1.2 本规范适用于所有车。
2 规范性引用文件下列文件中的条款通过本规范的引用而成为本规范的条款。
凡是注日期的引用文件,其随后所有的修改单(不包括勘误的内容)或修订版均不适用于本规范,然而,鼓励根据本规范达成协议的各方研究是否可使用这些文件的最新版本。
凡是不注日期的引用文件,其最新版本适用于本规范。
GB 8410-2006 汽车内饰材料燃烧特性GB 11552-1999 轿车内部凸出物3 术语PP:聚已稀PVC:聚氯乙烯PU:聚氨酯4目标性能4.1门内饰板的主要功能是包覆金属门板,提供优美外观,并满足人机工程、舒适性、功能性和方便性等要求;为满足更多的储物功能,设置地图袋、卡片夹、烟灰盒等;在侧撞时提供适当的吸能保护,对车外噪声提供屏蔽作用;4.2符合GB 8410-2006汽车内材料的燃烧特性;4.3满足GB 11552-1999轿车内部凸出物法规要求5门内饰板总成组成门内饰板本体、上饰板、嵌饰条、储物袋、扶肘、拉手盒(盖)、门脚灯盖板及吸音绵等6 设计方法6.1 结构设计6.1.1门内饰板本体本体又称基板或门饰板骨架,是联接和安装门内饰板系统中其他功能件和装饰件的载体,应设计有定位和紧固系统使整个门饰板安装到钣金上。
本体要有足够的强度和刚度保持门饰板的形状,需有布置合理R&D-CS-6102-001-2010的紧固点位置和设计合理的紧固件使安装时插入力小而拔出力大,还必须留有一定的变形空间起到以达到乘员保护的目的。
6.1.2上饰板有硬质和软质两类。
硬质上饰板可单独分块,无造型或材料特殊要求也可与本体合为一个零件;软质上饰板通常由表皮、发泡层和骨架三部分组成。
上饰板与骨架通过孔销定位,用焊接或螺钉方式连接。
6.1.3嵌饰板嵌饰板用以提供手肘倚靠,以软质为多,分层结构由表皮(面料、革或真皮)、发泡层和骨架三部分组成。
车门内饰板技术条件
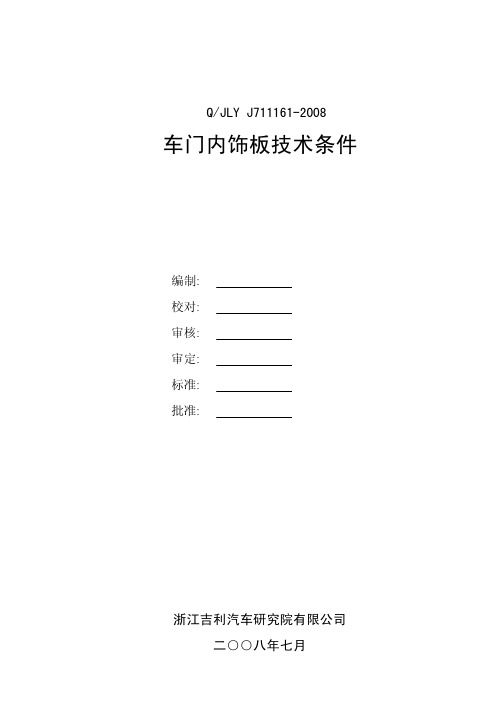
车门内饰板技术条件
编制: 校对: 审核: 审定: 标准: 批准:
浙江吉利汽车研究院有限公司 二○○八年七月
GEELY
车门内饰板技术条件
Q/JLY J711161-2008
前
言
本标准是对 JLYY-JT161-05《车门护板技术条件》的修订,与 JLYY-JT161-05 相比,其主要差异如下: ――增加了 GB 11552 《轿车内部凸出物》规定的引用; ――增加了 JLYY-JT49-08《汽车内外饰塑料件耐候性能试验规范》规定的引用; ――增加了 JLYY-JT45-08《汽车内外饰塑料件耐温性能试验规范》规定的引用; ――将 JLYY-JT139-04《汽车塑料件及合成橡胶件制品标记的规定》替换为 JL 100003-2007《汽车零
共6页第2页
GEELY
车门内饰板技术条件
Q/JLY J711161-2008
精度。 4.1.4 冲击试验球:直径 60mm,质量 0.9kg 的钢球。 4.1.5 氙光曝晒试验箱:符合 GB/T16422.2-1999 规定的设备。 4.1.6 燃烧特性测定仪 4.2 试验仪器 4.2.1 抗划伤性试验仪:该设备由具有下述特的刀具组成:
共6页第4页
GEELY
车门内饰板技术条件
Q/JLY J711161-2008
a) 变性酒精; b) 5%表面活性剂水溶液。 5.9.2 目测检查所处理的表面和所使用的棉织品状况,并做好记录。 5.10 耐光性试验 5.10.1 从被测试的产品上取下一块尽可能平的试样,试样大小约为 60mm×75mm,厚度不超过 5mm。 5.10.2 将试样按 GB/T 16422.2-1999 规定的设备和方法进行试验,时间为 300 h(一般地区);高温地区 辐照度相对一般地区辐照度提高 15%,试验结束后检查表面状况,并做好记录。应符合 JLYY-JT49-08 中的 规定。 5.11 燃烧特性试验 5.11.1 按 GB 8410 规定的设备和程序进行试验测定。 5.11.2 将试验结果及可能观察到的现象记录。 5.12 气味性试验试验 按标准 JLYY-JT146-04 中的规定进行试验。 5.13 刚性试验 5.13.1 在支撑区域,在 90mm×30mm 的面上,垂直方向上加 500N 的压力。 5.13.2 在基板中心区域,在 20mm×20mm 的面上的产品水平方向上加 500N 的力。
车门内饰板设计规范

编号代替密级商密×级▲汽车工程研究院设计技术规范车门内饰板设计规范2005-01-22制订 2005-11-22发布前言汽车的自主开发是中国汽车业健康发展的必经之路。
在汽车自主开发设计中,内外饰设计占有及其重要的位置,特别是车门内饰板设计。
在此,特编写此规范——《车门内饰板设计规范》,希望对坚持走自主开发之路的新生力量的快速成长能起到一定帮助,也希望对各位设计人员能有一定帮助。
本规范尚有许多不足之处,需要我们在实际操作中进一步完善和补充,希望大家能给予指正。
本规范由汽车工程研究院车身所负责起草;本规范由汽车工程研究院项目处进行管理和解释;本规范主要起草人员:编制:校核:审定:批准:本规范的版本记录和版本号变动及修订记录车门内饰板设计规范一、适用范围本规范规定了轿车车门内饰板在开发设计过程中应遵守一些要求和标准,规定了车门内饰板开发的一般过程、材料的选择、车门内饰板的分块、结构等。
本规范适用于M1、N1类车辆。
二、专业术语三维坐标系:指汽车制造厂在最初设计阶段确定的由三个正交的基准平面组成的系统。
三个基准平面如下:X基准平面——垂直于Y基准平面的铅垂面,通常规定通过左右前轮中心;Y基准平面——汽车纵向对称平面;Z基准平面——垂直于Y和X基准平面的水平面。
R点:汽车制造厂规定的基准点,该点具有及车辆结构相关的固定的坐标,对应于驾驶员座位在正常的最低及最后位置时的躯干和大腿旋转点(H点)的理论位置,或各座位在车辆制造厂规定的使用位置时的H点理论位置。
三、车门内饰板总成的组成车门内饰板总成通用组成件见表一,根据造形的不同、所开发车的档次不同和所选用的生产工艺的不同等,车门内饰板总成组成会有所不同,车门内饰板总成各部件间主要是采用焊接、螺钉或者卡接结构连接成整体。
表一:下图是以本公司前车门内饰板总成为例介绍门的组成:车门锁止按钮套圈车门内开手柄总成六、车门内饰板总成各部件设计要求 :1、吸能块设计要求此件根据法规要求而设计(法规需要),多采用热熔胶及门板本粘接,一般情况下为、发泡,发泡倍数协商;以下是其设计及周边配合要求: 编号 内 容 基准值 备注① 及车窗玻璃的间隙 10 ② 及车门内板表面的间隙 5 ③ 及车门内板孔的间隙 10 ④及车门内饰的间隙2门内饰杂物盒(包含扬声器孔盖) 车门内拉手(包含车门控制开关)门内饰板主体(包含扶手)门内饰板上部装饰板杂物盒盖板2、内开扳手框的设计要求内开扳手框,是一个覆盖于门板上、套在内开扳手的装饰件,多采用材料加工;它在门板总成上的位置随内开扳手而确定,一般采用螺钉联接及卡挂在内开扳手座上两种方式固定(均需要设计相的卡挂结构及门板本体固定),下表是其设计的边界要求:⑨编号内容基准值备注①扣手度<685最大限度760②从开始的位置>480最小限度420③及竖立把手开始位置120~1402④内开扳手框周围及对手件的间隙(前后方向)⑤内开扳手框周围及对手件的3搭接量(前后方向)⑥内开扳手框周围及对手件的1间隙(上下方向)3、摇窗机手柄设计要求摇窗机手柄总长度一般设计为120左右,多数情况下借用参考车件,需配合升降玻璃扭矩校核;下表是其设计的边界要求:⑦及座椅垫的距离参照图B手柄臂背面及门板距7⑧离0.3手柄臂背面及门板平⑨行度要求4、电动控制钮的布置设计要求编号内容基准值备注625~715①电动控制钮前端布置及人体模型肩部转点要求②从把手开始的距离>140③从把手开始的角度<18°④前后倾斜角0~10°前面提升至10°⑤左右倾斜角0~5°扶手表面⑥及内饰表面的距离≥255、肘靠的设计要求⑴肘靠也叫扶手,分独立加工和及门板本体一体加工两种方式,独立加工件分纯注塑、覆表皮或面料(低压注塑或包覆)、塘塑、聚胺脂发泡等类型;及门板一体成型多采用压制和低压注塑两种成型方式,这两种均需要覆面料或表皮,同时需在肘靠处表皮下增加泡沫垫或成型软垫。
轿车门内饰板总成技术条件

轿车门内饰板总成技术条件本技术条件规定了轿车门内饰板总成的技术要求,试验方法.验收规则、标识、包装、运输、储存及质量保证。
本标准适用于未未公司开发的轿车门内饰板总成。
本标准替代原JT1-6100-09-3《轿车门内饰板总成技术条件》。
2规范性引用文件GB 11552 轿车内部凸出物QC/T 29017-1991 汽车模制塑料零件未注公差尺寸的极限偏差JT1-9900-10-1 汽车内饰零件通用技术条件JTI-9900-1M 内外饰塑料标件通用技术条件3要求 3.1基本要求 3丄1门内饰板总成应符合本技术条件的要求,并按经规定程序批准的产品图样及有关技术文件制造。
3・1・2门内饰板总成应符合GB 11552的相关要求。
3.1・3外观要求a)产品外观表面不允许有裂纹、变形、银纹、波纹、烧焦.飞边、毛刺、气泡、浇口痕迹、顶杆印痕、熔接痕和收缩痕等其它缺陷。
b)喷涂或镀豁的产品,表面涂层或镀层均匀一致、色泽均匀,表面不允许有斑点、气泡、流挂等其它缺陷。
C)产品的所有可视外观面上尽可能不出现分模线,如果产品主要外观表面上的分模线应小于O.lmim非主视外观面分模线的痕迹小于0.2mm,且必须经过**公司质量部的认可。
d)产品应纹理清晰、色泽均匀。
纹理类型、纹理方向、纹理深度以及纹理分布应与经规定程序批准的色板或样品一致。
因脱模方向引起的非主要表面皮纹深度变化要均匀。
产品表面不允许产生纹理拉伤缺陷。
3・1・4门内饰板总成的尺寸应符合2D图纸及GD&T图纸等文件的规定。
在没有文件说明的悄况下,应满足QC/T29017-1991《汽车模制塑料零件未注公差尺寸的极限偏差》的要求。
3.2门内饰板总成性能门内饰板应满足表1的性能的要求。
表h门内饰板总成性能表4•试验方法 4.1门饰板刚度加载区域:门内饰板最薄弱区域(山工程师指定);加载力:10N;加载面积;直径20mm;测量变形量区域应在加载点20mm范圉内(图I):20 mm----------〜— -•■ *- » - ■"J测量区域j 20mm图1门饰板刚度测试4.2车门内拉手刚度、强度将门饰板总成按照实际装车状态固定。
车门装饰衬板与侧围板技术条件

Q/SQJ车门装饰衬板与侧围板技术条件四川汽车工业股份有限公司发布目次前言 (III)1 范围 (1)2 规范性引用文件 (1)3 基本要求 (1)3.1 尺寸 (1)3.2 外观 (1)3.3 间隙 (1)3.4 噪声 (1)3.5 可靠性 (1)3.6 燃烧特性 (1)3.6 气味性 (2)4 试验设备 (2)4.1 设施 (2)4.2 仪器 (2)5 试验准备 (2)5.1 设备检查 (2)5.2 试样准备 (2)5.3 测试结果 (3)5.4 测试温度 (3)6 试验方法 (3)6.1 尺寸、公差、颜色、标识、材料 (3)6.2 外观 (3)6.3 间隙 (3)6.4 车门内把手/把手凹槽的关闭试验 (3)6.5 车门把手盖板的固定力 (5)6.6 车门储物袋的尺寸稳定性 (5)6.7 车门装饰衬板的尺寸稳定性 (6)6.8 加载温度过程中测量栏杆区域的尺寸稳定性 (6)6.9 滥用试验 (7)6.10 扬声器罩的摆钟式冲击 (7)6.11 车窗凹槽连接的拉脱力F3 (8)6.12 车窗摇把到车门装饰衬板的自由移动 (9)6.13 肘靠表面的测试 (9)6.14 噪声测试 (10)6.15 紧固件的测试 (10)6.16 耐久性测试 (12)7 检验规则 (12)7.1 出厂检验 (12)7.2 型式检验 (12)8 标记 (13)9 运输及贮存 (13)附录A (14)试验结果记录表 (14)A.1 测量装置的清单见表A.1 (14)表A.1 测量装置的清单 (14)A.2 数据单见表A.2 (15)A.3 所有的项目设值见表A.3 (19)表A.3 所有的项目设值 (19)前言本标准规定了整车范围内的车门装饰衬板与侧围板的基本要求,试验设备,试验准备及评估,试验方法,检验规则,标记及贮存运输。
本标准由四川汽车工业股份有限公司技术中心提出。
本标准由四川汽车工业股份有限公司技术中心归口。
门护板设计规范-20130108

第四章 工艺细则要求
零件设计中的拔模角度要求
1.2 零件的分模线要放在料厚表面 或者看不见不影响外观质量的地方;
分模线
如右图所示,分模线一般放在 看不见的地方,以免影响外观 质量;
不能放到表面上
第四章 工艺细则要求
2、零件内部需要滑块机构脱模 成型时,需要检查滑块尺寸、 滑块滑动方向及滑动距离;
第五章 RPS系统
1、 定位系统的作用: ①产品装配工艺的方便性,有定位时,使产品装配更方便,效率更高;同样使检查更 方便,给检具提供一个基准; ②必要配合尺寸的保证,如配合间隙、配合阶差等; ③零件本身公差精度的保证,如零件的边界尺寸,开孔尺寸和位置精度等; ④降低零件的成本,可以有效地降低装配过程中因操作问题造成零件报的几率; ⑤图纸中,标注更方便、更有序;
第七章 空间布置及间隙
1、前左右门板与仪表盘的间隙最好为6~10mm。 2、门板(包括本体,掩饰板,地图袋等)与铁门内钣金的间隙两者之间最小间隙为 5mm,最好能做到大于10mm。 3、门内板总成与玻璃升降机构玻璃在运动过程中与门内板总成有足够的间隙。 4、扬声器与扬声器面罩的间隙,两者之间的间隙建议小于等于10mm,并考虑两者与内外 钣金的间隙。 5、座椅调节器与门板总成地图袋的间隙,两者间隙应该大于等于45mm。 6、门板总成边界是否与门钣金有间隙,建议有0.5mm的间隙以保证装配。 7、前门内护板周边到前门门框密封条间隙6~8㎜,周边要求间隙均匀,在前门槛处可略 大(该间隙处于不可见区,略大的间隙可消除制造误差对装配的影响)。
4、加强筋一般取0.5°以上的拔模角, 相对2.5mm厚的零件,筋的根部厚度一般 1mm,最大不超过1.2mm,端部厚度不小 于0.7mm,如果不能满足该项尺寸,考虑 调整拔模角,但最小不小于0.3°,同时 调整筋根部的厚度,使加强筋既满足拔 模角度的要求又满足厚度的要求;(如 图所示)
车门护板技术条件

~ II ~
北汽福田车辆股份有限公司企业标准
Q/FT A001—2000
车辆产品车门护板技术条件
1
范围 本标准规定了车门护板的技术要求、试验方法、检验规则、标志、包装、运输、贮存及质量保证。 本标准适用于本公司汽车、农用车(含拖拉机变型运输机,下同)产品注塑成型的车门护板(以下
简称护板) 。 2 引用标准 下列标准所包含的条文,通过在本标准中引用而构成为本标准的条文。本标准出版时,所示版本均 为有效。所有标准都会被修订,使用本标准的各方应探讨使用下列标准最新版本的可能性。 GB/T 1040-1992 塑料拉伸性能试验方法 GB/T 1634-1989 塑料弯曲负载热变形温度(简称热变形温度)试验方法 GB/T 1843-1996 塑料悬臂梁冲击试验方法 GB/T 2828-1987 逐批检查计数抽样程序及抽样表(适用于连续批的检查) GB 8410-1994 汽车内饰材料阻燃特性 GB/T 9341-1988 塑料弯曲性能试验方法 GB/T 9344-1988 塑料氙灯光源曝晒试验方法 QC/T 15-1992 汽车塑料制品通用试验方法 Q/FT B102-2000 车辆产品零部件标识规定 3 技术要求
表 3 振动耐久性
— 2 —
Q/FT A001—2000 加速度 振动 次数 汽车(不含经济型) 汽车(经济型) 、农用车 5.9 6000 5400 9.8 25000 22500 13.7 7000 6300 17.7 1500 1350 23.5 300 270
3.9 整体耐冲击性能 护板整体在 23 C 温度下,加入体积 100 m×100 mm×50 mm 的低压发泡聚氨酯缓冲材料后, 将重 500 g 的重锤从 40 cm 高处下落,要求产品无裂纹、损坏。 3.10 强度及刚度性能
J013 车门内护板设计规范

Q/XRFxxxxx公司Q/XRF-J013-2015xxxx车门内护板设计规范编制:日期:校对:日期:审核:日期:批准:日期:2015-03-15发布 2015-03-15实施xxxxx公司发布前言随着汽车工业的日新月异,人们对汽车内饰的追求也在不断提高。
作为汽车内饰重要的组成部分—车门内饰板,舒适性、可靠性、美观性越来越成为人们追求的目标。
对车门内护板的正确设计,将会给试制、批量生产、整车商品性带来事半功倍的效果。
本文对我公司车型车门内护板的设计进行详细介绍。
1.吸能块和周边零件间隙序号内容基准值(mm)1 与车窗玻璃的间隙102 与车门内板便面的间隙 53 与车门内板孔的间隙104 与车门内饰的间隙 22.内扣手的设定标准3.M/W 调节器手柄设定标准序号 内容 基准值(mm ) 参考1 I/S 扣手长度 <685 最大限度760mm2 从OPONING 开始的位置 >480最小限度420mm3 竖立把手开始位置120~140 4 扣手盖板周围间隙(前后方向)2 5 扣手盖板周围搭接量1 6 扣手盖板周围间隙(上下方向)3 7扣手盖板周围间隙(上下方向)24.电动控制钮的设定标准序号内容 基准值(mm ) 参考 1 调节器手柄的长度<6702 从乘坐参考点开始到扣手中心高度>1303 与车门储物盒的距离>160 4 与肘靠的距离 >904 与肘靠的距离>60应用参考手册表面高度 5 与仪表板的距离>1306 从坐姿的距离参照左图5.肘靠的设定标准序号 内容基准值(mm ) 参考1 对应室内冲击必要条件的场合>2 in 纵面倾斜15°以内2对应室内内部突出物必要条件的场合>R3.5适合范围清参考上图*1 推荐高度=(0.6+30)+SEAT BACK ANGLE修正值±10上限高度=0.6d+50 下限高度=0.6d1 电动控制钮的长度 625~7252 从把手开始的距离 >1403 从把手开始的角度<184 前后倾斜角 0~10° 前面提升至10°5 左右倾斜角 0~5° ARM 表面高度6 与内饰表面的距离 ≥25序号内容基准值(mm)参考1 肘靠上面的高度(H)根据*1计算式从SRP(JM50%)开始2 肘靠长度(SRP的前侧)170±20 SRP(JM50%)3 同上(SRP的后侧)110±20 同上4 ARMREST上面的前后倾斜5~6度5 ARMREST上面的左右倾斜0~5度6 ARMREST上面的宽度>707 室内冲击吸收方式侧面宽度15 θ3<15°6.缝隙间的设定标准序号内容基准值(mm)参考1 与仪表板的缝隙 52 视觉补正上图参考3 与SASH的缝隙 24 与UPPER和LOWER的搭接尺寸上图参考序号内容基准值(mm)参考1 车门内饰与B柱装饰件的间隙 5 水平方向2 车门内饰与B柱装饰件的间隙 5 车副方向3 抽取倾斜角10度4 车门内板的突出部分与内饰的间5隔注意:2.从OPNING的缝隙不应该看见车体的颜色7.操作性的设定标准序号内容基准值1 拖拽把盒水平把手区域:R1 <5002 拖拽把盒水平把手区域:R2 >4003 拖拽把盒水平把手区域:R3 <4004 拖拽把盒水平把手区域:R4 <10005 纵把手区域:R1 <5206 纵把手区域:R2 400~5007 纵把手区域:R3 <10008 纵把手高度:H 200~2709 纵把手区域:R3 68~78度序号内容基准值(mm)参考1 车门内饰与座椅坐垫的缝隙>60 极限值50mm2 车门内饰与储物盒之间的缝西>55 极限值40mm3 门在打开情况下的乘降空间>3004 座椅靠背与扶手的间隙>255 座椅操作杆操作空间>408.扬声器网格的设定标准序号内容基准值(mm)参考1 网格部位的开口率40%2 网格部位的开口率(TWEETER)50% 高音用9.踏板照明的设定标准序号内容基准值(mm)参考1 开启门的可视角度15度2 脚下的可视性(着地点亮光度)3L3 脚下的可视范围上图参考10.乘车性的设定标准序号内容基准值(mm)参考1 从SRP到前车门内饰的距离310~360 极限值290mm2 从SRP到后车门内饰的距离330~380 极限值310mm3 玻璃升降器摇把与膝盖的关系上图参照11.拖拽把手的设定标准序号内容基准值(mm)参考1 把手部位的长度100~1202 把手部位的宽度30~403 手抠(BOX)部位的深度>554 把手部位的粗度:h 25~354 把手部位的粗度:b 20~255 手抠(BOX)部位的角度-8度极限值13度6 拖拽把手的位置50~1507 把手部位的刚性6kg12.纵把手的设定标准序号内容基准值(mm)参考1 从SRP到把手的距离350±502 角度60~70度3 把手部位的粗度20~254 有效长度>1105 到玻璃升降器摇把的距>90离6 P/W控制钮间隔的距离>807 从把手区域<52013.储物盒的设定标准序号内容基准值(mm)参考1 宽(尽可能做大)40 地图的厚度+52 高度100 EU:703 长度320 地图长度+104 地图收纳状态上图参照1:加强筋一般布置5~6根,筋厚0.5mm2:在有加强筋区域内可以适当的增加料厚0.3~0.4mmLD DOOR TRIMCOPOLLA DOOR TRIMXD DOOR TRIMRS FACE LIFT DOOR TRIMBL DOOR TRIMGQ DOOR TRIM14.车用密封条操作指南车用3M胶1.概述本操作指南适用于用压敏胶带把橡胶密封条装配到汽车和卡车的操作工艺。
汽车门内护板、立柱包覆产品技术条件

3.4
贴合 joint 通过人工或设备将布基材料、复合材料或真皮等表皮通过粘结助剂(如:胶水、胶纸、化学制剂等) 贴附至待贴合体上的过程。
4 基材
基材常用PP、ABS、 PC+ABS (PC不超过40%)等材料注射成型, 也包括麻纤维或化学纤维等材料经过 浆质模压成型。 基材材料性能应满足以下要求:
I
`'
I
i::::::i
本标准由*****汽车发展有限公司塑料件开发中心提出。 本标准山**汽车股份有限公司技术中心标准化部归口。 本标准山*****汽车发展有限公司朔料件开发中心工程 一部负责起草。
本标准主要起草人:
II
汽车门内护板、 立柱包覆产品技术条件
1 范围
本标准规定了使用包覆工艺生产的汽车门内护板、立柱产品的基材要求、包覆材料、包覆工艺分类、 技术要求、 试验方法、 检验规则、 标识、 包装、 运输、 质量保证。本标准适用于本公司使用包覆来自艺生产的汽车门内护板、 立柱产品。
2 规范性引用文件
下列文件对于本文件的应用是必不可少的。凡是注日期的引用文件,仅所注日期的版本适用千本文 件。 凡是不注日期的引用文件, 其最新版本(包括所有的修改单)适用千本文件。
GB/T 191—2008 包装储运图示标志 GB/T 2918—1998 塑料试样状态调节和试验的标准环境 GB/T 4689.20—1996 皮革涂层粘着牢度测定方法 GB 8410—2006 汽车内饰材料的燃烧特性 HG/T 2-162—1965 塑料低温冲击压缩试验方法 QB/T 2537—2001 皮革色牢度试验往复式摩擦色牢度 QB/T 2710—2005 皮革物理和机械试验抗张强度和伸长率的测定 QB/T 2711—2005 皮革物理和机械试验撕裂力的测定: 双边撕裂 QB/T 2726—2005 皮革物理和机械试验耐磨性能的测定 QC/T 29017—1991 汽车模制塑料零件未注公差尺寸的极限偏差 Q/CC 007—2012 汽车产品标识规定 Q/CC JTOOl 汽车内饰材料气味散发性试验方法和限值 Q/CC JT049—2012 车门护板和内饰护板技术条件 Q/CC JT097—2010 汽车塑料件、 橡胶件和热塑性弹性体件的材料标识和标记 Q/CC JT098 汽车产品中有毒有害物质限晕要求 Q/CC JTlOO—2010 汽车内饰件用聚丙烯材料技术条件 Q/CC JT101—2010 汽车零部件用ABS材料技术条件 Q/CC JT102—2010 汽车零部件用PC+ABS材料技术条件 Q/CC JT146 汽车内饰材料雾化特性试验方法和限值 Q/CC JT321 车内非金属零部件挥发性有机物及醒类物质限值要求 Q/CC SY248—2011 车内非金属零部件挥发性有机物和酸酮类物质采样测定方法 Q/CC SY335—2012 汽车非金属部件及材料氝灯加速老化测试方法
- 1、下载文档前请自行甄别文档内容的完整性,平台不提供额外的编辑、内容补充、找答案等附加服务。
- 2、"仅部分预览"的文档,不可在线预览部分如存在完整性等问题,可反馈申请退款(可完整预览的文档不适用该条件!)。
- 3、如文档侵犯您的权益,请联系客服反馈,我们会尽快为您处理(人工客服工作时间:9:00-18:30)。
J02.03.44
散发特性
总碳散发 甲醛排放
≤50 μgc/g
/
≤10 mg/kg
/
雾翳冷凝
通用
≤1.0 mg
/
值 耐清洁剂性
粘着性
撕裂强度(纵横)KN/M
耐热老化性
漆膜厚度
饰面漆
油漆附着性及脆性 高温存放
低温存放
耐摩擦色牢 度
干摩擦
色差要求
制品表面不留下痕迹 无粘着现象 ≥40
内饰板总成任何部位或表面不允许出现裂纹
粘结)牢固,中部装饰板骨架和纤维蒙皮模压成型、胶粘结或吸附成型后后与内饰 板安装或焊接在一起要求必须连接牢固,扬声器隔栅总成和门板杂物盒与门板装配 到一起,总成修剪、切割成型后成为成品。 3.3 外观检查
表面蒙皮应皮纹、压纹、均匀,颜色一致,无污染物;外观不允许出现起毛、
磨光位置、褶皱、气泡、起层或肿块;包覆结构(蒙皮革或织物面料等)在与开关 面板、内拉手盒等装配件配合的孔边缘必须包覆到背侧3mm 以上;切口平整,切口 处无毛边、起层、破裂,不得有破碎,切口处不得有伤人的棱角、毛刺,使用中不 得出现裂纹、开裂现象。
120℃/100h 后,用手指检查无粘着现象。 4.10 拉伸强度及断裂伸长率
按GB 1040 规定试验方法,试验速度50mm/min, 沿纵、横方向各取试样5 个。试验结果以 5 个试样的算术平均值表示。 4.11 表面消光性
按JASO 7102 试验方法。 4.12 雾度
按QC/T 29089-1992 中第6.5 条。 1. 4.13 尺寸变化率 2. 4.13.1 把试片制成250mm×250mm 大小,用游标卡尺标出纵、横230mm(L0)的距离作 为试验片。 3. 4.13.2 把试验片放置在温度90℃±2℃的烘箱里,大约1 小时左右取出,在常温下冷却 30 分钟后,测出标示点距离L1 并计算收缩率。 4. 4.13.3 计算
5
4.6.2 试验方法 参照GB1040 。
4.7 耐振动性试验 取试样5 块 , 以接近使用状态的条件安装在振动台上;相对于试样的安装方式依次给予上
下、左右及前后的正交方向的简谐振动,简谐振动的谐波含有率应为振动加速度的25%以下;试 验温度定为标准温度23℃±5℃; 试验方法按表7 给定的参数进行试验。
参照GB 5453 试验方法。 4.18 抗静电性
参照 DIN 54 345 中比电阻的测试方法 4.19 断裂强度及断裂伸长率
按G B3923.1 规定,试验速度100mm/min 4.20 耐磨耗试验失重
分别沿经向和纬向取350mm×70mm 试样三块,每块试样先称重(G0) 后在摩擦色牢度 仪上进行试验。把面积为50 mm 正方形的橡皮膜或羊毛织物固定在摩擦头上,摩擦头应沿直线 往复运动,行程100mm,下压力为9.3N,摩擦头每进行一次来回摩擦运动应在1s 内完成。磨耗 100 次后取下试样用吸尘器吸清后称重(G1)(精确至0.001g),然后再安装在摩擦色牢度仪 上磨耗2500 次后取下称重(G2)。以摩擦100 次和2500 次后的失重(mg)为该块试样的耐磨 耗性能。以三块试样的平均值表示。
初始状态
断裂伸长率(纵横) %
剥离强度 N/5cm
表面材料与泡沫
耐光(氙灯照射
色牢度 级
400h)
耐水
耐摩擦 耐磨耗试验失重 mg
性能 100%涤纶
≥320g 22±3 21±3 ≥75 <5×1010
≥450 ≥100 ≥15 或软泡撕裂
≥4
≥4.5 ≥4.5 ≤100
表5 改性PP 制件性能
项目
J02.01.76 中的4.4
≥4 级
4.14
_
黑色调要求:|ΔL°|<0.40,|Δa°|<0.25,| Δ b°|<0.25
通用
米色调要求:|ΔL°|<0.45,|Δa°|<0.25,| Δ b°|<0.35
灰色调要求:|ΔL°|<0.45,|Δa°|<0.25,| Δ b°|<0.25
J02.01.45
4.8 4.9 QC/T 29089 中的6.3 QC/T 29089 中的6.11
>20µm >60µm
J02.01.76 中的4.1
_
喷漆件通用
撕下的胶带上不得带任何油漆颗粒 无涂层转移
外观和触感无变化,油漆附着性满足要求
J02.01.76 中的4.2 J02.01.76 中的4.3
外观和触感无变化,油漆附着性满足要求
的夹钳中,分别在四种状态下:常态、90℃/16h、55℃,95%RH/48h、-40℃/24h, 已100mm/min 的速度拉伸试样, 测量剥离力。 1. 4.2 耐高温性 2. 4.2.1 试验设备
高温箱。 4.2.2 试验方法
将门板总成置于高温箱中,当温度上升至(90±2)℃时开始计算时间,保温不得少于4h, 然后回复至室温。 1. 4.3 耐温度变化 2. 4.3.1 试验设备
4.16 静态(定负荷)伸长率 取长度为200mm,宽度为50mm 的试样,夹在试验机的夹钳上,在初始测量长度L0,(通常
为100mm) 上施加25N 负荷,历时30min,测量原初始长度上的的尺寸L1,按下试计算定负荷伸 长率:
定负荷伸长率=
J02.01.1 58-2007
×100% 4.17 透气性
a)高温箱;
b)低温箱。 1. 4.4.2 试验方法 2. 4.5 耐寒性
在-40℃和+90℃分别时效24h,及湿度95%下4 8h。
参照QC/T 29089-1992 中6.9 条。 1. 4.6 拉伸强度 2. 4.6.1 试验条件
常温,速度5mm/min +90℃,保温4 小时后,立即进行拉力试验,速度5mm/min; -40℃,保温4 小时后,立即进行拉力试验,速度5mm/min。
将摩擦白棉布浸在人工汗液里10 分钟后取出,轻轻挤后放在耐磨仪上,试验方法与干摩擦 一致。 人工汗液调剂:取磷酸钠 8g、 氯化钠 8g、 硝酸 5g加入蒸馏水制成1 升溶液使用。 1. 4.14.3 耐液性 2. 4.15 密度
按QC/T 29089-1992 中第6.10 条。
2
单位面积重量由至少5 个面积为100cm 的圆形试样来测定,取样应在整个材料的宽度上均匀分 布。
车门内饰板技术规范
1 范围
本标准规定了车门内饰板总成技术要求、试验方法。 本标准适用于车门内饰板(不包括拉门和客车车后门)。
2 规范性引用文件
GB/T 1040
GB/T 9341 GB/T 250 GB/T 251 GB 3920
GB 3923.1 GB 5713 GB 8410 GB 8428 GB 5453
喷漆不允许有漏漆、流挂、杂质等缺陷,漆膜厚度要求均匀,颜色统一与色 板一致且不褪色,喷漆
1
与本体附着力好,不能发生化学反应,喷漆边界必须整齐,过渡平缓自然;喷漆件有连接和装
配关系的,后部的喷漆件喷漆边界要超过配合边界。 1. 3.4 车门内饰板总成性能符合表1。 2. 3.5 成型后麻纤维基材机械性能符合表2。 3. 3.6 TPO 蒙皮、乙烯基蒙皮材料性能符合表3。 4. 3.7 内饰板纤维蒙皮材料性能符合表4。 5. 3.8 改性PP 制件性能符合表5。 6. 3.9 ABS 制件性能符合表6。 7. 3.10 门内饰板覆布件符合J02.01.79 标准。 8. 3.11 仿木纹装饰压条性能评价符合J02.01.47 标准。
测试项目 弯曲强度(纵、横) MPa
吸水率 厚度膨胀率
性能 ≥30 ≤5% ≤10%
试验方法 GB/T 9341
GB 12626.8
表3 TPO、乙烯基蒙皮和PP 发泡基蒙皮技术条件
项目 拉伸强度(纵横) MPa 断裂伸长率(纵横) %
表面消光性 %
雾度(100℃/5h) %
尺寸变化率(90℃/5h)%
a) 高温箱; b) 低温箱。 4.3.2 试验方法
试验环境为:温度:15℃ ~ 25℃; 相对湿度:45% ~ 85%。 以(80±2) ℃/15.5h→室温/0.5h→(-30±2)℃ /7.5h→室温/0.5h为一个周期, 对门板总成进行两个周期的试验。 1. 4.4 气候和温度时效 2. 4.4.1 试验设备
4.15 4.16 4.17 4.18
4.19 DIN 53 357
GB 8428
GB 5713 GB 3920
4.20
技术要求 10~20 >27(聚菱燕CN3034A>19)
>20 2500
42 50 20 4 8 65
技术要求 ≥1.8
拉伸强度
断裂伸长率
弯曲弹性模量
弯曲强度(3.5%)
缺口冲击韧性
熔融指数
拉伸强度
断裂伸长率
弯曲弹性模量
弯曲强度(3.5%)
冲击强度
23℃ -20℃
缺口冲击强度
23℃ -20℃
硬度
项目 熔融指数(质量)
单位 cm 3/10min
MPa %
MPa MPa kJ/m2 kJ/m2 kJ/m2 kJ/m2 N/mm2
表6 ABS 制件性能
单位 g/10min
试验方法 /
表1 车门内饰板总成性能 表2 成型后麻纤维基材机械性能
项目 剥离强度纵、横 N/5cm
耐高温性
耐温度变化性
适用范围 吸塑内饰板
性能 ≥15
表面不应有裂纹、污点、皱纹、色差、粘手、 凹
凸和松弛、无鼓泡等缺陷。
试验方法 4.1 4.2
4.3
气候和温度时效
4.4
耐寒性
通用
内饰板总成任何部位或表面不允许出现裂纹