红酸果案例分析
红酸果案例分析报告_第九组_周开谦
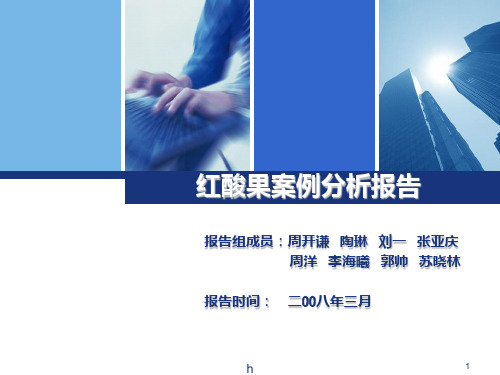
报告组成员:周开谦 陶琳 刘一 张亚庆 周洋 李海曦 郭帅 苏晓林
报告时间: 二00八年三月
h
1
目录
1
红酸果案例简述
2
问题及解决方案
3
成本测算及决策
4
远期展望及探索
2
h
红酸果案例简述(一)
安·希金斯
“红酸果之角”加工厂,负责生产的副总裁
1.运送浆果的卡车无法及时卸货,长时间滞留 2.厂内员工长时间的加班,经常至深夜
处理完当天酸果:5400/600=9小时;从19点至次日早上4点总共所需时间
=12600/600=21小时
7
h
湿酸果库存图(三)
假设:生产18000×70%(湿酸果占70%)=12600桶/天12600/12=1050桶/小 时;早上7:00工厂开始生产;烘干的瓶颈值是800桶/小时
+250桶/小时
1.卡车等候补偿费 2.员工加班费
生产成本大幅提高
红酸果产量逐年的提高,今后企业的生产将会更加困难,因 此必须尽快拿出一个行之有效的方案提交给董事会。
3
h
红酸果案例简述(二)
07:00
11:00
19:00
05:00
600桶/小时*5
卸货
1-16 250桶/箱
干
装箱
1500桶/小时*3
去石子
1500桶/小时*2
卡车等待时间=0!
3000/800=3.75小时=20:45加工完成小时
处理完当天酸果:3000/800=3.75小时;从19点至20:45点总共所需时间 =12600/800=15.75小时;烘干酸果加工能力降为400桶/小时
8
红酸果案例报告-第8小组
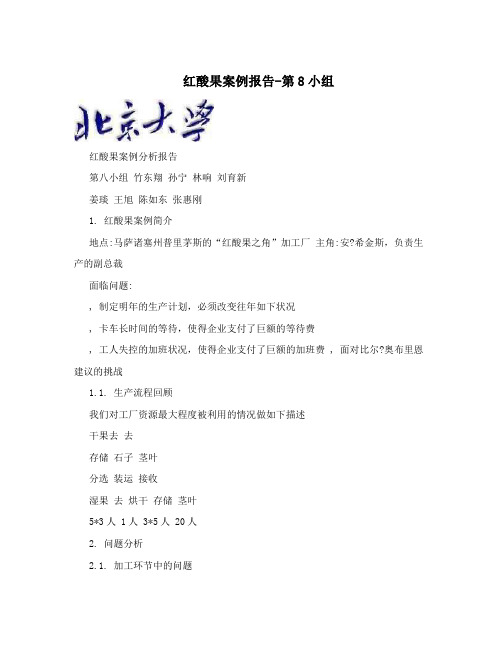
红酸果案例报告-第8小组红酸果案例分析报告第八小组竹东翔孙宁林响刘育新姜琰王旭陈如东张惠刚1. 红酸果案例简介地点:马萨诸塞州普里茅斯的“红酸果之角”加工厂主角:安?希金斯,负责生产的副总裁面临问题:, 制定明年的生产计划,必须改变往年如下状况, 卡车长时间的等待,使得企业支付了巨额的等待费, 工人失控的加班状况,使得企业支付了巨额的加班费 , 面对比尔?奥布里恩建议的挑战1.1. 生产流程回顾我们对工厂资源最大程度被利用的情况做如下描述干果去去存储石子茎叶分选装运接收湿果去烘干存储茎叶5*3人 1人 3*5人 20人2. 问题分析2.1. 加工环节中的问题分析高峰时期加工情况,条件假设:到货在7:00—19:00的分布情况假定为平均分布。
2.1.1. 到货情况1500桶/小时,其中干果:450桶/小时,湿果1050桶/小时2.1.2. 加工环节分析专用干果存储去石子去茎叶4000桶 4500桶/小时 3000桶/小时分选包装接收公共存储 1200桶/小时能力充足2000桶 3000桶/小时去茎叶烘干1500桶/小时 600桶/小时专用湿果存储1200桶当到货如2.1描述,, 湿果到货速度大于烘干速度,所以烘干是加工瓶颈。
, 同时造成湿果在存储环节的堆积,当湿果存储达到最大容量时,会造成到货车的等待。
当到货并非按照2.1描述,存在干果到货速度>600桶/小时的情况,同时湿果在存储箱内有存储的情况,或湿果到货速度>600桶/小时,分选将也会成为加工瓶颈。
2.2. 条件分析假设由前面的分析,湿果的加工属于瓶颈,所以利用图形说明湿果的接收到存储清空的过程。
900078007500450桶/小时 600桶/小时 600045003200 30001050桶/小时 15007:00 9:00 11:00 13:00 15:00 17:00 19:00 21:00 23:00 1:00 3:00 5:00 7:00首先,接收从早上7:00开始。
红酸果精益分析

红酸果案例分析背景“红酸果之角”加工厂面临经营管理方面的问题。
在酸果成熟期,加工厂外,运送卡车排起了长龙;加工厂里,工人每天轮班超时加班,机器超负荷运转,给工厂带来了额外的成本支出。
但是即便如此,仍然没能改变状况,种植者抱怨不断,加班现象失去控制……分析红酸果加工流程图在高峰期的一天,有18,000桶酸果运来,从早上7点到晚上7点这12个小时内,每小时平均运到的数量就是18,000/12=1,500桶/小时倾倒效率平均每辆车的装载量是75桶,卸一车酸果平均用时7.5分钟,共有5台倾倒机,则每小时可倾倒60/7.5×75×5=3000桶/小时存贮量干贮存箱250×16=4000桶干/湿两用贮存箱250×8=2000桶湿贮存箱400×3=1200桶去石效率1500×3=4500桶/小时去茎效率1500×3=4500桶/小时烘干效率200×3=600桶/小时分选效率400×3=1200桶/小时初步分析可知,整个生产流程中“烘干”工序是最大的一个瓶颈,“分选”工序次之。
问题假定70%的果子是湿的,30%是干的,则运到干果450桶/小时,湿果1050桶/小时;一天内共运到干果5400桶,湿果12600桶。
1、卡车等待问题接受工人每天7:00上班,在高峰时期,处理的工人则11:00上班,即这中间4个小时酸果运到后倾倒入贮存箱中。
干果450×4=1800桶,占7.2个贮存箱;且干果不会积压。
湿果1050×4=4200桶,但最大容量为3200桶,此时卡车需要排队等候。
湿酸果库存图(11:00开工)卡车的等待时间可以从“湿酸果库存图(11:00开工)”中看出,卡车在排队的时间是上午10:00~凌晨2:40。
通过上面的分析可知等待的卡车装载的都是湿果,干果不会堆积。
2、加班问题用分选机处理完一天运来的所有干果需要5,400/1,200=4.5(小时),即干果可以在所有工作时间内处理完。
红酸果案例
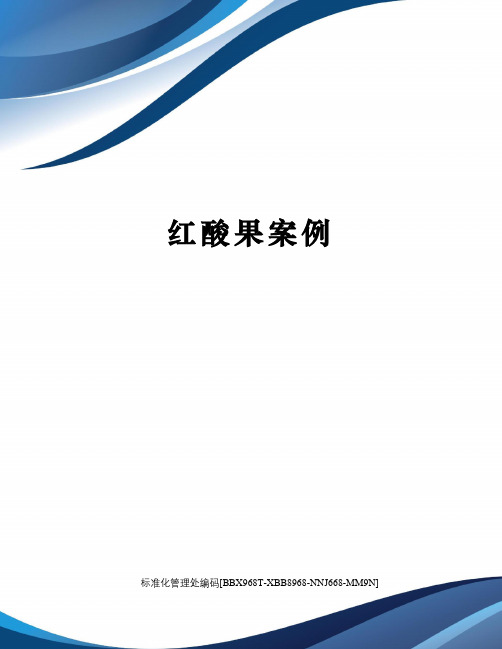
红酸果案例标准化管理处编码[BBX968T-XBB8968-NNJ668-MM9N]红酸果案例分析1、绘制红酸果处理的流程图。
主要设备产能汇总表(等待队列)2、 在高峰期此过程的瓶颈是什么工序按(9月20日~10月9日)高峰期平均每天送来酸果总量16,380桶,那么,按每天12小时工作计算,每小时酸果送达量=16,380 ÷12=1,365桶/小时。
从以上流程图可以看出,红酸果的分选(1200桶/小时),烘干(600桶/小时),都小于每小时送达量(1,365桶/小时),也与其他设备产能相差较大,因此,这两个环节首先有可能是瓶颈环节。
再看看干、湿果送达比例情况:1)由于烘干机和分选机的产能分别为600桶/小时和1200桶/小时,当湿果数在50%以下时,分选机是瓶颈工序,当湿果数量在50%以上时,烘干机是瓶颈工序。
2)在高峰期,假设每天运来酸果总数为T 桶,其中w%是湿果,分选机处理完所有红酸果的时间为S= T / 1200 (小时),烘干机处理完所有湿果的时间为D= T*w% /600 (小时)。
如果S > D,即w% < 50%,那么分选机所用时间就较长,分选机是瓶颈工序,反之,如果S < D,即w% > 50%,那么烘干机所用时间就较长,烘干机是瓶颈工序。
3)如果以高峰期某日(10月1日)为例,酸果数量为18,018桶、湿果比例69%计,则该日烘干机工作时间=18018*69%/600=21(小时),分选机工作时间=18018/1200=15(小时),显然,烘干机是瓶颈工序。
4)按照来年预测,全年湿果的比例将达到70%,那么粗略预计在来年高峰期大多数日子,烘干机是瓶颈工序。
3、计算卡车的平均等待时间截止到晚上七点,600*12=7200桶,12个小时已经处理了7200桶,12600-7200=5400桶,即还有5400桶没处理完,3200桶已装进贮存箱,2200桶还在卡车上。
红酸果案例分析报告

红酸果加工厂案例分析目录一、面临的问题二、加工流程图三、各工序生产能力及瓶颈工序四、高峰期完成所有加工的时间五、最后一辆卡车的卸货时间及等待时间六、评价奥布里恩的建议七、合理性改进建议一.案例回顾及工厂所面临的问题位于马萨诸塞州的“红酸果之角”加工厂过去都是加工干收法采集的酸果,但是近些年来湿收法采集成为主要方式,这就给工厂过去的酸果加工程序带来了挑战。
随着湿收法的推广和普及工厂面临着下面一些问题需要解决背景条件●18,000桶/天(高峰期)●湿果:70%(12,600桶/天;1050桶/小时)干果:30%(5400桶/天;450桶/小时)●卡车装载75桶/车早七点起12小时均匀到达●卡车等待成本:$10/辆小时●工人平均工资是12.50美元/小时,8小时之外工厂要多付50%所面临的问题●过多的加班问题●卡车排队现象●烘干、分选工序产能不足●存储罐容量不足二.生产流程分析红酸果的生产流程如下图所示:三. 生产能力及瓶颈分析从上面图中分析可以看出整个工序的瓶颈工序为烘干,其隐含利用率为 175%,所以整个工序湿 收法酸果的生产能力为 600 桶/小时。
四. 高峰期完成的加工时间瓶颈工序(烘干)处理时间即可确定加工时间。
倾倒机 (5 台)去石子 (3 台) 去茎叶 (3 台) 烘干 (3 台) 分选 (3 条) 可供使用能力3000 桶/小时4500 桶/小时 4500 桶/小时 600 桶/小时 1200桶/小时湿收法 需求 1050 桶/小时 01050 桶/小时 1050 桶/小时 1050桶/小时 干收法 需求 450 桶/小时 450 桶/小时 450 桶/小时 0450 桶/小时需求需要能力1500 桶/小时450 桶/小时 1500 桶/小时1050 桶/小时 1500桶/小时 隐含资源利用率1500/3000 =50%450/4500 =10%1500/4500 =33%1050/600 =175%1500/1200=125%瓶颈工序每天处理湿果所需要的时间:12600桶÷600桶/小时=21小时每天从 11 点开始不间断地加工红酸果要加工到第二天早上 8 点才能完全满足当天的需求,同时每天还需要 2 个小时来清理现场和维护设备。
生产运作与管理-红酸果案例分析
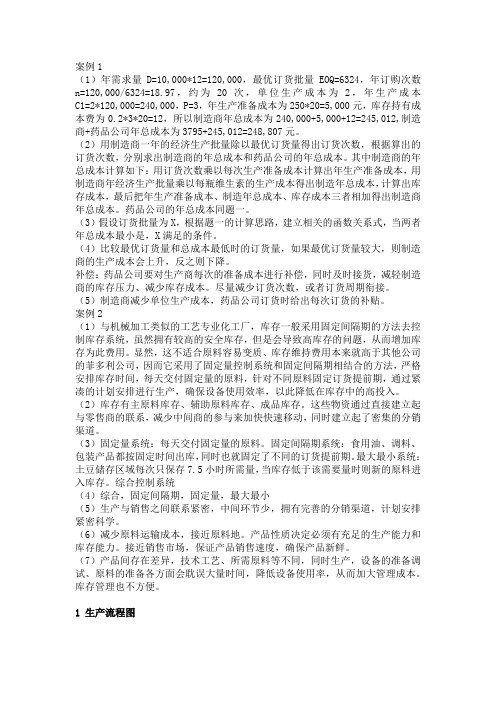
案例1(1)年需求量D=10,000*12=120,000,最优订货批量EOQ=6324,年订购次数n=120,000/6324=18.97,约为20次,单位生产成本为2,年生产成本C1=2*120,000=240,000,P=3,年生产准备成本为250*20=5,000元,库存持有成本费为0.2*3*20=12,所以制造商年总成本为240,000+5,000+12=245,012,制造商+药品公司年总成本为3795+245,012=248,807元。
(2)用制造商一年的经济生产批量除以最优订货量得出订货次数,根据算出的订货次数,分别求出制造商的年总成本和药品公司的年总成本。
其中制造商的年总成本计算如下:用订货次数乘以每次生产准备成本计算出年生产准备成本,用制造商年经济生产批量乘以每瓶维生素的生产成本得出制造年总成本,计算出库存成本,最后把年生产准备成本、制造年总成本、库存成本三者相加得出制造商年总成本。
药品公司的年总成本同题一。
(3)假设订货批量为X,根据题一的计算思路,建立相关的函数关系式,当两者年总成本最小是,X满足的条件。
(4)比较最优订货量和总成本最低时的订货量,如果最优订货量较大,则制造商的生产成本会上升,反之则下降。
补偿:药品公司要对生产商每次的准备成本进行补偿,同时及时接货,减轻制造商的库存压力、减少库存成本。
尽量减少订货次数,或者订货周期衔接。
(5)制造商减少单位生产成本,药品公司订货时给出每次订货的补贴。
案例2(1)与机械加工类似的工艺专业化工厂,库存一般采用固定间隔期的方法去控制库存系统,虽然拥有较高的安全库存,但是会导致高库存的问题,从而增加库存为此费用。
显然,这不适合原料容易变质、库存维持费用本来就高于其他公司的菲多利公司,因而它采用了固定量控制系统和固定间隔期相结合的方法,严格安排库存时间,每天交付固定量的原料,针对不同原料固定订货提前期,通过紧凑的计划安排进行生产,确保设备使用效率,以此降低在库存中的高投入。
生产与运作管理案例分析--红酸果
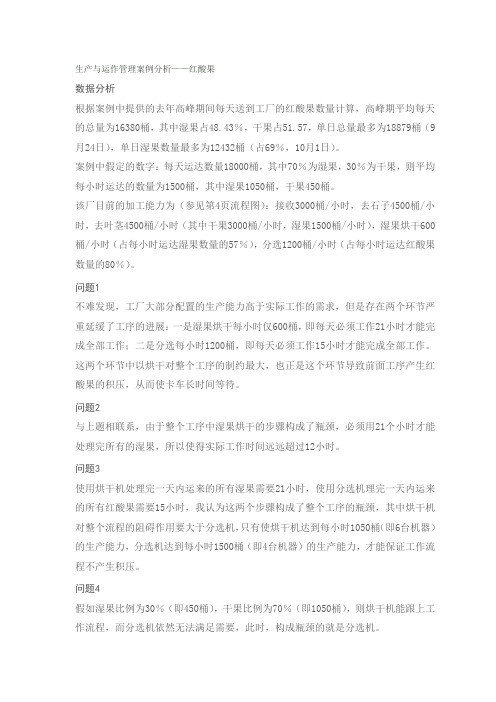
生产与运作管理案例分析——红酸果数据分析根据案例中提供的去年高峰期间每天送到工厂的红酸果数量计算,高峰期平均每天的总量为16380桶,其中湿果占48.43%,干果占51.57,单日总量最多为18879桶(9月24日),单日湿果数量最多为12432桶(占69%,10月1日)。
案例中假定的数字:每天运达数量18000桶,其中70%为湿果,30%为干果,则平均每小时运达的数量为1500桶,其中湿果1050桶,干果450桶。
该厂目前的加工能力为(参见第4页流程图):接收3000桶/小时,去石子4500桶/小时,去叶茎4500桶/小时(其中干果3000桶/小时,湿果1500桶/小时),湿果烘干600桶/小时(占每小时运达湿果数量的57%),分选1200桶/小时(占每小时运达红酸果数量的80%)。
问题1不难发现,工厂大部分配置的生产能力高于实际工作的需求,但是存在两个环节严重延缓了工序的进展:一是湿果烘干每小时仅600桶,即每天必须工作21小时才能完成全部工作;二是分选每小时1200桶,即每天必须工作15小时才能完成全部工作。
这两个环节中以烘干对整个工序的制约最大,也正是这个环节导致前面工序产生红酸果的积压,从而使卡车长时间等待。
问题2与上题相联系,由于整个工序中湿果烘干的步骤构成了瓶颈,必须用21个小时才能处理完所有的湿果,所以使得实际工作时间远远超过12小时。
问题3使用烘干机处理完一天内运来的所有湿果需要21小时,使用分选机理完一天内运来的所有红酸果需要15小时,我认为这两个步骤构成了整个工序的瓶颈,其中烘干机对整个流程的阻碍作用要大于分选机,只有使烘干机达到每小时1050桶(即6台机器)的生产能力,分选机达到每小时1500桶(即4台机器)的生产能力,才能保证工作流程不产生积压。
问题4假如湿果比例为30%(即450桶),干果比例为70%(即1050桶),则烘干机能跟上工作流程,而分选机依然无法满足需要,此时,构成瓶颈的就是分选机。
【精选】红酸果案例分析-第三小组PPT
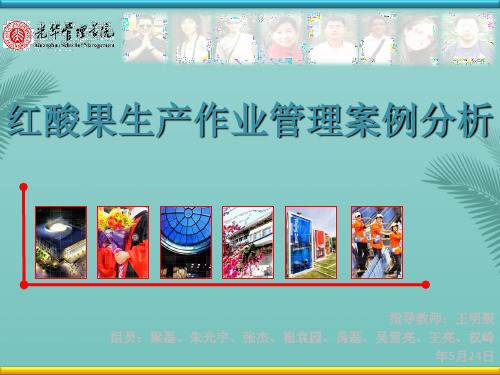
添加一台烘干机节省的成本:118599 美元
增添两台烘干机时加班及等待成本
卡车等待=0 卡车等待成本=0 接收工人加班成本=0 操作工人加班成本=(15-12)*37*(12.5*1.5)=2081.3.6 美元 总加班成本=2081.3 美元 每天加班及等待成本总计:2081.3 美元
600
3000
18000
6
1500
4500
18000
4
1500
4500
18000
4
200
600
12600
21
400
1200
18000
15
250
4000
5400
250
200012600源自4001200生产流程中卸货和存储阶段分析
处理酸果的工人上午11点上班, 在此之前所接收的酸果都必须放在 储存箱内。到11点应该可以接收 1800桶干果,4200桶湿果,但是 湿果的最大存储量为3200桶。应 此存放湿果的储存箱显得不足,无 法再接收,卡车就必须等待。
高峰期(20天)加班及等待成本总计:2081.3*20=41625 美元
添加第二台烘干机节省的成本:10406 美元
改变开工时间节省的成本:105430 美元 人员的安排(工作时间) 每星期七天从早七点至晚七点,都有(种植者租用的)卡车陆陆续续开到加工厂。 组员:梁磊、朱光宇、张杰、崔袁园、禹磊、吴雪亮、王亮、权崎 增添一台烘干机时加班及等待成本 增添一台烘干机时加班及等待成本 操作工人加班成本=(21-12)*37*(12. 添加一台烘干机节省的成本:118599 美元
注:此处会产生卡车等待时间成 本和工人加班成本。
红酸果案例分析

红酸果案例分析学号:107119 姓名:袁龙1.解释为什么卡车要等那么长时间。
答:主要是由于湿收的果子需要经过烘干的过程,存放湿果的储存罐最多可以储存3200桶,而对湿果的烘干,三台设备同时进行,每小时也只能完成600桶,倾倒流程可以每小时处理3000桶,其中的湿果每小时有2100桶,虽然可以贮存3200桶,但是两个小时以后运来的果子就没法及时处理了,所以卡车还要等很长时间。
2. 按计划,处理酸果的工人每天工作12 个小时,另外还要加班4 个小时。
为什么会有这么长的计划外加班时间?也就是说,实际工作时间为什么会大大超过12个小时?答:工人之所以要加班还在于处理酸果的烘干过程很慢,而湿酸果又不能储存过夜,必须得当天处理完,所以尽管工人工作时间很长,但是由于烘干流程的耽误工人还会有加班。
3使用烘干机处理完一天内运来的所有湿果需要多长时间?使用分选机处理一天内运来的所有酸果又需要多长时间?根据你对这两个问题的答案,哪个或哪些工序步骤是瓶颈,也就是说它(它们)会限制物流和生产速度?答:烘干机处理完所需要的时间:18000×0.7÷(200×3)=21 小时,分选机处理完所需要的时间:18000÷(400×3)=15 小时,烘干机处理时间> 分选机处理时间,所以说烘干机烘干湿果是瓶颈。
4. 我们已经假定了每天运到的酸果有70%是湿的,有30%是干的。
如果湿果的比例有变化,那又会出现什么情况?比如,如果30%是湿的、70%是干的,又会怎样呢?哪个工序步骤是瓶颈是否会有变化呢?如果湿果的比例有变化,假如30%是湿果、70%是干果,那么去石子这道工序的压力就加大,另外,存放干果的贮藏箱就紧张,而贮藏湿果的贮藏箱就有空闲。
此时,烘干机处理完所需要的时间:18000×0.3÷(200×3)=9 小时,去石子所需要的时间:18000×0.7÷(1500×3)=2.8 小时。
运营管理红酸果案例分析
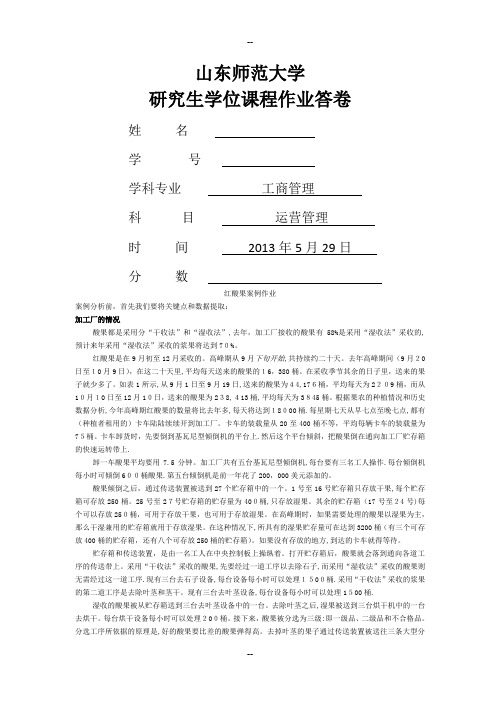
山东师范大学研究生学位课程作业答卷姓名学号学科专业工商管理科目运营管理时间2013年5月29日分数红酸果案例作业案例分析前,首先我们要将关键点和数据提取:加工厂的情况酸果都是采用分“干收法”和“湿收法”,去年,加工厂接收的酸果有58%是采用“湿收法”采收的,预计来年采用“湿收法”采收的浆果将达到70%。
红酸果是在9月初至12月采收的。
高峰期从9月下旬开始,共持续约二十天。
去年高峰期间(9月20日至10月9日),在这二十天里,平均每天送来的酸果的16,380桶。
在采收季节其余的日子里,送来的果子就少多了。
如表1所示,从9月1日至9月19日,送来的酸果为44,176桶,平均每天为2209桶,而从10月10日至12月10日,送来的酸果为238,413桶,平均每天为3845桶。
根据果农的种植情况和历史数据分析,今年高峰期红酸果的数量将比去年多,每天将达到18000桶.每星期七天从早七点至晚七点,都有(种植者租用的)卡车陆陆续续开到加工厂。
卡车的装载量从20至400桶不等,平均每辆卡车的装载量为75桶。
卡车卸货时,先要倒到基瓦尼型倾倒机的平台上.然后这个平台倾斜,把酸果倒在通向加工厂贮存箱的快速运转带上.卸一车酸果平均要用7.5分钟。
加工厂共有五台基瓦尼型倾倒机,每台要有三名工人操作.每台倾倒机每小时可倾倒600桶酸果.第五台倾倒机是前一年花了200,000美元添加的。
酸果倾倒之后,通过传送装置被送到27个贮存箱中的一个。
1号至16号贮存箱只存放干果,每个贮存箱可存放250桶。
25号至27号贮存箱的贮存量为400桶,只存放湿果。
其余的贮存箱(17号至24号)每个可以存放250桶,可用于存放干果,也可用于存放湿果。
在高峰期时,如果需要处理的酸果以湿果为主,那么干湿兼用的贮存箱就用于存放湿果。
在这种情况下,所具有的湿果贮存量可在达到3200桶(有三个可存放400桶的贮存箱,还有八个可存放250桶的贮存箱)。
如果没有存放的地方,到达的卡车就得等待。
红酸果案例分析

所以70%湿果的前提下,处理时间用的最长的是烘干工 序;
1、卡车等待的时间问题?
◦ 理论上总共接收需要的时间:
接收工作从早7点到晚7点,共12小时,从7点开始处理的话,处理 湿果共600*12=7200桶 则剩余12600-7200=5400桶湿果没有处理,这个时候储存箱中 有3200桶,那么还有2200桶仍在卡车中; 2 2200桶接收需要的时间为 2200 / 600 3 3 小时 即:需要接收到10点40分才能接收完所有的湿果;
◦ 增加一台烘干机,减少接受工序人员成本为:(3.67+2) *1.5*15*12.5=1595美元;减少的倾倒工序成本为: 3.67*1.5*3*12.5=206.4美元;另还有卡车等待成本,假设为10美 元/小时,则共(2200/75)*(12+3.67-7.11)/2=126车,1年节省 20*(1595+206.4+1260)=61228美元; ◦ 烘干机成本为75000美元,收回成本需要0.82年;
综上所述,我们建议: 1. 处理工序提前到7点开始;
2.
增加1台烘干机; 增加烘干机后,分选过程为整个工艺的瓶颈,如果成 本不是很高的情况下,增加分选线为提高产能的关键, 同时需要评估烘干机的效率,持续改进;
3.
在职一班 2013组 周承 李维娜 秦萌 岳从敏 陈海慈 陈琦 杨志豪 刘斌
问题及分析 解决方案 结论
1.
2.
3.
4.
卡车等待的问题 处理工序计划外加班 时间长的问题 处理工序开始时间太 晚(11点)是否可以 提前 工序中有没有影响效 率的瓶颈
1、以高峰期每天工作12小时不加班为标准; 2、以在12小时内处理完所有的红酸果为目标;
红酸果案例
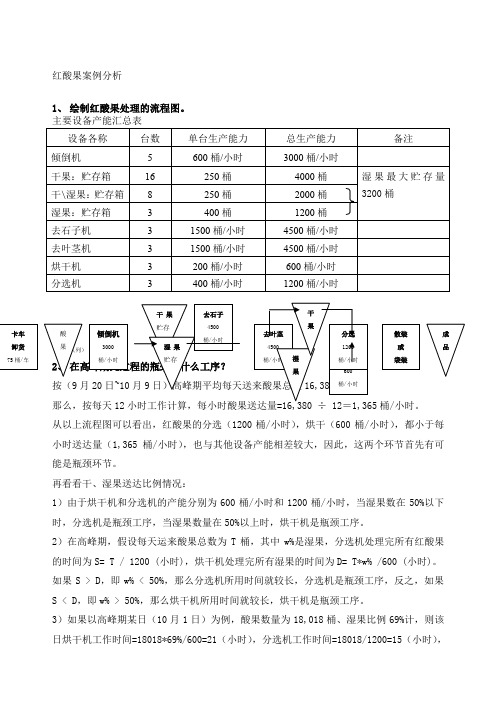
红酸果案例分析1、 绘制红酸果处理的流程图。
按(9月20日~10那么,按每天12桶/小时。
从以上流程图可以看出,红酸果的分选(1200桶/小时),烘干(600桶/小时),都小于每小时送达量(1,365桶/小时),也与其他设备产能相差较大,因此,这两个环节首先有可能是瓶颈环节。
再看看干、湿果送达比例情况:1)由于烘干机和分选机的产能分别为600桶/小时和1200桶/小时,当湿果数在50%以下时,分选机是瓶颈工序,当湿果数量在50%以上时,烘干机是瓶颈工序。
2)在高峰期,假设每天运来酸果总数为T 桶,其中w%是湿果,分选机处理完所有红酸果的时间为S= T / 1200 (小时),烘干机处理完所有湿果的时间为D= T*w% /600 (小时)。
如果S > D ,即w% < 50%,那么分选机所用时间就较长,分选机是瓶颈工序,反之,如果S < D ,即w% > 50%,那么烘干机所用时间就较长,烘干机是瓶颈工序。
3)如果以高峰期某日(10月1日)为例,酸果数量为18,018桶、湿果比例69%计,则该日烘干机工作时间=18018*69%/600=21(小时),分选机工作时间=18018/1200=15(小时),显然,烘干机是瓶颈工序。
4)按照来年预测,全年湿果的比例将达到70%,那么粗略预计在来年高峰期大多数日子,烘干机是瓶颈工序。
3、计算卡车的平均等待时间?截止到晚上七点,600*12=7200桶,12个小时已经处理了7200桶,12600-7200=5400桶,即还有5400桶没处理完,3200桶已装进贮存箱,2200桶还在卡车上。
在卡车上(12600-3200)÷600=15.67小时,湿果运来的速度为12600÷12=1050桶/小时积压情况:1050-600=450桶/小时,存储箱装满为3200÷450=7.11小时装满如图阴影面积即为卡车等待时间,贮存能力线于升降曲线之间。
红酸果案例
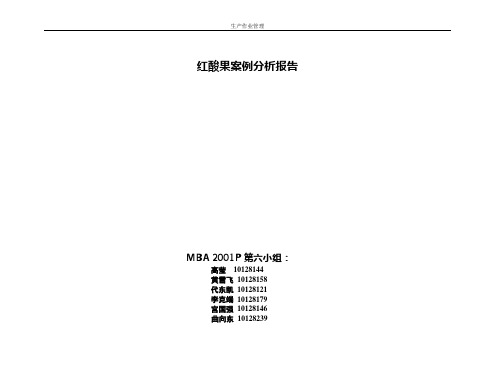
红酸果案例分析报告MBA 2001P 第六小组:高莹 10128144黄雪飞 10128158代东凯 10128121李克端 10128179宫国强 10128146曲向东 10128239红酸果加工流程图干果红酸果采湿果摘、运输打包、装运合格2、高峰期的瓶颈工序根据去年统计数据,推算今年高峰期平均每小时收到的红酸果数量:16380/12=1365桶,其中湿酸果为955桶,干酸果为410桶。
如根据案例提供的18000的数据,湿干果的数量分别为1050、450桶。
各工序每小时的最大处理能力(单位:桶):从表中可以看出,高峰期的瓶颈是湿酸果烘干工序;其次分选工序。
3、非高峰时间平均每天收到的红酸果数量分别为2209、3845桶,平均每小时为184、320桶。
各工序每小时的处理能力(单位:桶):高峰时期按照平均每天收到18000桶,70%为湿酸果,每小时收到酸果1500桶(20车次/小时),其中湿酸果1050,干酸果450。
湿酸果的最大贮存能力3200桶,每小时到货1050桶,3200/1050=3.05,所以早晨7-10点车辆不用排队等待卸货,10点以后开始排队等待卸货;干酸果贮存能力4000/450=8.89,每小时处理能力大于450桶,所以不会造成等待。
等待时间=卸车时间+排队等候时间卸车时间=7.5×18000/75=1800/60=30小时排队等候时间=549小时等待时间=549+30=579小时平均等待时间=579/240=2.413小时详细计算过程见附件4、从详细的技术过程中可以看出过程安排上存在问题,由于除接受外的其他工序上班时间偏晚,造成了卡车等待,增加了成本。
5、高峰期成本=工人工资(正常工资+加班工资)+卡车等候成本每日正常工资=12.5×8×53=$5300加班工资=15×8×12.5×1.5+1×4×12.5×1.5+(15+20+2)×4×12.5×1.5+15×9×12.5×1.5=$7632卡车等候成本=579×10=$5790每日的总成本=5300+7632+5790=$18722高峰期的总成本=18722×20=$3744406、奥布里恩的建议作如下分析:总开支=75000×2+15000×16=$390000该设备收回投资期按三年进行折旧,平均每年开支$130000。
红酸果案例
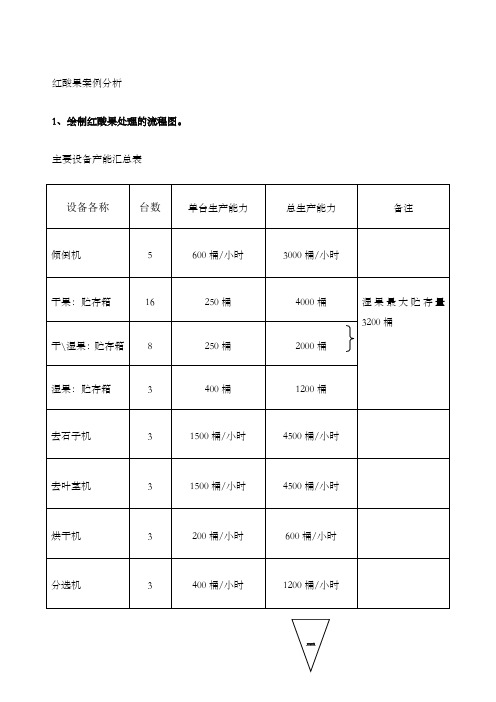
红酸果案例分析1、绘制红酸果处理的流程图。
主要设备产能汇总表(等待队列)2、在高峰期此过程的瓶颈是什么工序?按(9月20日~10月9日)高峰期平均每天送来酸果总量16,380桶,那么,按每天12小时工作计算,每小时酸果送达量=16,380÷12=1,365桶/小时。
从以上流程图可以看出,红酸果的分选(1200桶/小时),烘干(600桶/小时),都小于每小时送达量(1,365桶/小时),也与其他设备产能相差较大,因此,这两个环节首先有可能是瓶颈环节。
再看看干、湿果送达比例情况:1)由于烘干机和分选机的产能分别为600桶/小时和1200桶/小时,当湿果数在50%以下时,分选机是瓶颈工序,当湿果数量在50%以上时,烘干机是瓶颈工序。
2)在高峰期,假设每天运来酸果总数为T桶,其中w%是湿果,分选机处理完所有红酸果的时间为S= T / 1200 (小时),烘干机处理完所有湿果的时间为D= T*w% /600 (小时)。
如果S > D,即w% < 50%,那么分选机所用时间就较长,分选机是瓶颈工序,反之,如果S < D,即w% > 50%,那么烘干机所用时间就较长,烘干机是瓶颈工序。
3)如果以高峰期某日(10月1日)为例,酸果数量为18,018桶、湿果比例69%计,则该日烘干机工作时间=18018*69%/600=21(小时),分选机工作时间=18018/1200=15(小时),显然,烘干机是瓶颈工序。
4)按照来年预测,全年湿果的比例将达到70%,那么粗略预计在来年高峰期大多数日子,烘干机是瓶颈工序。
3、计算卡车的平均等待时间?截止到晚上七点,600*12=7200桶,12个小时已经处理了7200桶,12600-7200=5400桶,即还有5400桶没处理完,3200桶已装进贮存箱,2200桶还在卡车上。
在卡车上(12600-3200)÷600=15.67小时,湿果运来的速度为12600÷12=1050桶/小时积压情况:1050-600=450桶/小时,存储箱装满为3200÷450=7.11小时装满如图阴影面积即为卡车等待时间,贮存能力线于升降曲线之间。
红酸果案例讨论分析A1

红酸果案例讨论分析针对《运营管理》中提到的“红酸果案例”,我们小组通过认真、仔细的讨论,就该案例的相关问题进行了如下分析:数据分析:A、根据案例中提供的去年高峰期间每天送到工厂的红酸果数量计算,高峰期平均每天的总量为16380桶,其中湿果占48.43%,干果占51.57%,单日总量最多为18879桶(9月24日),单日湿果数量最多为12432桶(占69%,10月1日)。
如表一所示:B、以案例中提到的今年高峰期情况,运达数量18000桶,其中70%为湿果,30%为干果,则平均每小时运达的数量为1500桶,其中,湿果1050桶,干果450桶。
C、该厂目前的加工能力为(参见第3页流程图):接收3000桶/小时,去石子4500桶/小时,去叶茎4500桶/小时(其中干果3000桶/小时,湿果1500桶/小时),湿果烘干600桶/小时(占每小时运达湿果数量的57%),分选1200桶/小时(占每小时运达红酸果数量的80%)。
高峰期数据表一:去年高峰期数据问题1、绘制红酸果处理的流程图:3000桶/小时问题2、在高峰期此过程的瓶颈是什么工序?从上述流程图上不难发现,工厂大部分配置的生产能力高于实际工作的需求,但是存在两个环节严重延缓了工序的进展:一是湿果烘干每小时仅600桶,根据表一数据显示,去年高峰期内,平均每天运达的湿果数量为:7969桶,每天必须工作13.3小时才能完成全部工作;二是分选每小时1200桶,根据表一数据显示,去年高峰期内,平均每天运达的红酸果总数量为:16380桶,每天必须工作13.7小时才能完成全部工作。
这两个环节完成的时间均超过其他工序每天正常完成的时间,因此,我们认为案例中加工过程存在的瓶颈工序是:烘干和分选。
问题3、计算卡车的平均等待时间是多少?表二去年红酸果平均送达数据根据案例中给出的信息,去年高峰期时,工厂各环节的处理数据如下: A 由于卡车早上7点开始运达,除接收工序以外的工人中午11点开始上班,因此在除接收工序以外的工人上班以前的4个小时内,一共运达的红酸果数量为:16380/12 *4=5460桶,其中湿果数量为:5460*48.56%=2651桶.工厂的接收储存能力为:总数量7200桶,其中湿果的最大接收储存能力为:3200桶.因此,该阶段,卡车不存在等候情况.B 去年高峰期, 除接收工序以外的工人开始上班后,生产的瓶颈在于烘干和分选,其中分选完成全天工作的时间长于烘干工序,是现有状态下最大的瓶颈,因此,以分选工序的处理能力进行卡车等候时间的分析,从中午11点到下午7点之间,接收环节每小时新增储存的红酸果数量为:16380/12-1200=165桶.一共165*8=1320桶.连同中午11点以前,接收环节储存的红酸果5460桶,一共为6780桶,小于接收环节的最大储存能力7200桶,因此,在此阶段,卡车也不存在等候现象.同样,以烘干环节处理能力进行分析, 从中午11点到下午7点之间,接收环节每小时新增储存的湿果数量为:7969/12-600=64桶,一共64*8=512桶, 连同中午11点以前,接收环节储存的湿果2651桶,一共为3163桶,小于接收环节湿果的最大储存能力3200桶, 卡车也不存在等候现象.C 工厂卡瓦基型倾倒机的处理能力为3000桶/小时,远大于高峰期每小时运达的红酸果数量16380/12=1365桶.综上,去年高峰期,卡车并不存在排队等待现象.问题4、处理过程中的安排是符有问题?在去年高峰期时段,烘干工序每天需要13.3小时才能完成工作,分选工序每天需要13.7小时才能完成工作,这主要是由于这两个工序中,设备能力的限制造成的.在去年非高峰期间,如表二所示: 9月1日—9月19日,平均每天运来2209桶,其中湿果1193桶.平均每小时接收红酸果184桶,其中湿果100桶。
红酸果案例

红酸果案例分析1、绘制红酸果处理的流程图。
主要设备产能汇总表2、按(9月20日~10月9那么,按每天12小时工作计算,每小时酸果送达量=16,380 ÷ 12=1,365桶/小时。
从以上流程图可以看出,红酸果的分选(1200桶/小时),烘干(600桶/小时),都小于每小时送达量(1,365桶/小时),也与其他设备产能相差较大,因此,这两个环节首先有可能是瓶颈环节。
再看看干、湿果送达比例情况:1)由于烘干机和分选机的产能分别为600桶/小时和1200桶/小时,当湿果数在50%以下时,分选机是瓶颈工序,当湿果数量在50%以上时,烘干机是瓶颈工序。
2)在高峰期,假设每天运来酸果总数为T桶,其中w%是湿果,分选机处理完所有红酸果的时间为S= T / 1200 (小时),烘干机处理完所有湿果的时间为D= T*w% /600 (小时)。
如果S > D,即w% < 50%,那么分选机所用时间就较长,分选机是瓶颈工序,反之,如果S < D,即w% > 50%,那么烘干机所用时间就较长,烘干机是瓶颈工序。
3)如果以高峰期某日(10月1日)为例,酸果数量为18,018桶、湿果比例69%计,则该日烘干机工作时间=18018*69%/600=21(小时),分选机工作时间=18018/1200=15(小时),显然,烘干机是瓶颈工序。
4)按照来年预测,全年湿果的比例将达到70%,那么粗略预计在来年高峰期大多数日子,烘干机是瓶颈工序。
3、计算卡车的平均等待时间截止到晚上七点,600*12=7200桶,12个小时已经处理了7200桶,12600-7200=5400桶,即还有5400桶没处理完,3200桶已装进贮存箱,2200桶还在卡车上。
在卡车上(12600-3200)÷600=小时,湿果运来的速度为12600÷12=1050桶/小时积压情况:1050-600=450桶/小时,存储箱装满为3200÷450=小时装满如图阴影面积即为卡车等待时间,贮存能力线于升降曲线之间。
MBA生产运营管理(红酸果案例分析报告)

红酸果案例分析报告1、红酸果处理的流程2、红酸果加工厂的主要问题及原因红酸果加工厂的目前表现出来的问题主要有两个方面:一是运送红酸果的车辆卸货排队时间太长;二是高峰时期加班费的支出很多。
造成这些问题的原因主要有:一是红酸果厂的加工工序上各个环节的产能安排不合理,某些环节的产能存在瓶颈,限制了整个加工厂的产能,导致运来的红酸果无法及时处理;二是对于临时工的管理不到位,缺勤率高,影响了生产效率。
3、分析瓶颈按照案例中提供的数据和讨论题给出的假设,每天运来的红酸果有18000桶,⑴其中70%的湿果:18000桶×70%=12600桶,30%的干果:18000桶×30%=5400桶。
去石子完成时间(干):5400桶÷4500桶/小时=1.2小时<12小时去茎叶完成时间(干湿):18000桶÷4500桶/小时= 4小时<12小时烘干完成时间(湿):12600桶÷600桶/小时=21小时>12小时分选完成时间(干湿):18000桶÷1200桶/小时=15小时>12小时此种情况下烘干机是瓶颈。
⑵其中30%的湿果:18000桶×30%=5400桶,70%的干果:18000桶×70%=12600桶。
去石子完成时间(干):12600桶÷4500桶/小时=2.8小时<12小时去茎叶完成时间(干湿):18000桶÷4500桶/小时= 4小时<12小时烘干完成时间(湿):5400桶÷600桶/小时=9小时<12小时分选完成时间(干湿):18000桶÷1200桶/小时=15小时>12小时此种情况下分选机是瓶颈。
⑶烘干机每天完全释放产能时能够处理的湿果为600桶/小时×12小时=7200桶,(7200桶÷18000桶)×100%=40%。
结论:当湿果所占比例小于等于40%时,分选机是瓶颈,当湿果所占比例大于40%时,烘干机都是瓶颈。
- 1、下载文档前请自行甄别文档内容的完整性,平台不提供额外的编辑、内容补充、找答案等附加服务。
- 2、"仅部分预览"的文档,不可在线预览部分如存在完整性等问题,可反馈申请退款(可完整预览的文档不适用该条件!)。
- 3、如文档侵犯您的权益,请联系客服反馈,我们会尽快为您处理(人工客服工作时间:9:00-18:30)。
红酸果加工厂案例分析
目录
一、面临的问题
二、加工流程图
三、各工序生产能力及瓶颈工序
四、高峰期完成所有加工的时间
五、最后一辆卡车的卸货时间及等待时间
六、评价奥布里恩的建议
七、合理性改进建议
一.案例回顾及工厂所面临的问题
位于马萨诸塞州的“红酸果之角”加工厂过去都是加工干收法采集的酸果,但是近些年来湿收法采集成为主要方式,这就给工厂过去的酸果加工程序带来了挑战。
随着湿收法的推广和普及工厂面临着下面一些问题需要解决
背景条件
●18,000 桶/天(高峰期)
●湿果:70%(12,600桶/天;1050桶/小时)
干果:30%(5400桶/天;450桶/小时)
●卡车装载75桶/车早七点起12小时均匀到达
●卡车等待成本:$10/辆小时
●工人平均工资是12.50美元/小时,8小时之外工厂要多付50%
所面临的问题
●过多的加班问题
●卡车排队现象
●烘干、分选工序产能不足
●存储罐容量不足
二.生产流程分析
红酸果的生产流程如下图所示:
三. 生产能力及瓶颈分析
从上面图中分析可以看出整个工序的瓶颈工序为烘干,其隐含利用率为175%,所以整个工序湿收法酸果的生产能力为600桶/小时。
四. 高峰期完成的加工时间
瓶颈工序(烘干)处理时间即可确定加工时间。
高峰期每天湿果的总量:12600桶
倾倒机 (5台) 去石子 (3台) 去茎叶 (3台) 烘干 (3台) 分选 (3条) 可供使用能力
3000 桶/小时 4500 桶/小时 4500 桶/小时 600 桶/小时 1200 桶/小时 湿收法 需求 1050 桶/小时 0
1050 桶/小时 1050 桶/小时 1050 桶/小时 干收法 需求 450 桶/小时 450 桶/小时 450 桶/小时 0
450 桶/小时 需求需要能力
1500 桶/小时 450 桶/小时 1500 桶/小时 1050 桶/小时 1500 桶/小时 隐含资源利用率
1500/3000 =50%
450/4500 =10%
1500/4500 =33%
1050/600 =175%
1500/1200 =125%
瓶颈工序每天处理湿果所需要的时间:12600桶÷600桶/小时=21小时
每天从11点开始不间断地加工红酸果要加工到第二天早上8点才能完全满足当天的需求,同时每天还需要2个小时来清理现场和维护设备。
五.最后一辆卡车的卸货时间及等待时间
高峰期库存
干果储存能力4000桶,干果总量5400桶。
储能能力完全满足,无需干果卡车等待。
湿果的储存能力3200 桶,每小时到达湿果1050桶
7点起三小时(3200/1050)以后,十点开始排队,在19点达到顶峰,此时库存为7800,需要(7800-3200)/600=7.67小时
即最后一辆湿果卡车的卸货时间为凌晨2点45左右。
最后一辆卡车等待时间为从7.67小时。
六.奥布里恩的方案评价
建议一:购置两台单价为75000美元的烘干机
建议二:更换十六个单价为15000美元的干果贮存箱,将其更换为干湿两用的贮存箱。
添置两台烘干机后生产瓶颈分析
倾倒机去石去茎叶烘干
(3+2台) 分选
(3条)
可供使用能力3000
桶/小时
4500
桶/小时
4500
桶/小时
1000
桶/小时
1200
桶/小时
湿收法需求1050
桶/小时
0 1050
桶/小时
1050
桶/小时
1050
桶/小时
干收法需求450
桶/小时
450
桶/小时
450
桶/小时
0 450
桶/小时
需求需要能力1500
桶/小时
450
桶/小时
1500
桶/小时
1050
桶/小时
1500
桶/小时
隐含资源利用率1500/3000
=50%
450/4500
=10%
1500/4500
=33%
1050/1000
=105%
1500/120
0=125%
增加两台烘干机后库存情况
评价:
●分选成为新的瓶颈瓶颈工序处理能力由600桶每小时提升到1000桶每小时。
●添置两台烘干机不能完全解决工人加班问题。
根据分选工序计算,新的完成加工时间为15个小时,虽然较之前21个小时减少6个小时,但工人仍需加班至第二天凌晨2点才能完成加工工作,加上2个小时来清理现场和维护设备,凌晨四点才能完工。
●更换16个储存箱解决卡车等待问题。
成本昂贵150 000+240 000=390 000美元
七.合理性改进方案
现状
●近几年湿收法成为主要采收方法,去年58%,预计今年70%。
●原流程本身存在问题,需要优化。
●由于系统的瓶颈是烘干机,目前的生产能力是600桶/小时,与需求有较大差距,造成工人
长时间加班。
●从7点卡车开始卸货,储存箱的容量逐渐被填满,此后造成卡车排队的问题。
改进目标
●满足来年高峰期红酸果加工的需求
●解决卡车排队问题
●解决工人的加班问题
解决思路
●调整处理设备结构减少干果处理环节设备及人员,增加湿果处理环节设备
●采用倒班制两班每班工作时间8小时,共计16小时时长,解决瓶颈工序产能不足问题。
优点:解决加班和卡车等待问题
节省加班费不疲劳工作
过剩产能置换所需添置设备
节省非高峰期闲置设备的养护费用
过剩产能分析
改进方案
●除倾倒外,其他工序采用分两班轮班制,每8小时一班,7:00-15:00-23:00 共计工作时
长16小时。
湿果需求能力:12600桶/16小时=788桶/小时
干果需求能力:5400桶/16小时= 338桶/小时
●添加机器:一台烘干机
●削减过剩产能削减两台倾倒机(裁减6名操作人员)
削减两台去石子设备
削减两台去茎叶设备
削减十台干果储存箱
改造后产能分析
倾倒机(5-2台)去石子
(3-2台)
去茎叶
(3-2台)
烘干
(3+1台)
分选
(3条)
可供使用能力1800
桶/小时
1500
桶/小时
1500
桶/小时
800
桶/小时
1200
桶/小时
湿收法需求1050
桶/小时0788
桶/小时
788
桶/小时
788
桶/小时
干收法需求450
桶/小时338
桶/小时
338
桶/小时
0338
桶/小时
需求需要能力1500
桶/小时
338
桶/小时
1126
桶/小时
788
桶/小时
1126
桶/小时
隐含资源利用率1500/1800
=84%
338/1500
=23%
1126/1500
=75%
788/800
=98.5%
1126/1200
=94%
改善后库存及加工所需时间分析
●剩余库存分析:
湿果1050-788=262桶/小时共计3144桶
干果450-338=112桶/小时共计1344桶
干果储存箱容量250桶/ 个,因此仅需6个干果储存箱即可满足需求。
湿果储存能力3200桶,因此不存在卡车排队。
●完成加工时间分析:根据800桶/ 小时的湿果处理能力,加工所有湿果完成时间为
12600/800= 15.75小时,即从7点开始至22点45左右完成,无需加班。
结论:解决加班和排队问题
增加工时统计
●因改为两班制,需增加
中央控制1人;去石子、去茎叶、烘干1人;分选15人
共计17人*8小时=136个工时
●因削减了倾倒工序6人*12小时=72个工时
结论:只需增加136-72=64个工时/天
64*4=256美元/天高峰期20天仅需5120美元
研究结论:用最低成本解决高峰期加班、卡车排队、并优化流程。
●投入成本少75000+5120=80120美元
●削减过剩产能设备和冗余人员
削减设备置换资产节约成本
削减冗余人员合理安排
●高峰期两班轮班制
✓无需加班费用
✓工人不疲劳操作
✓购置固定资产在非高峰期产生的闲置资产养护费用以及产能过剩的资源浪费。