电石生产工艺流程图
电石生产工艺流程

目录
第一节:电石生产基础知识 第二节:电石生产的基本原理及工艺流程 第三节:电石生产所需原料 第四节:原料中杂质对电石生产的影响 第五节:电石炉本体设备简介 第六节:电石生产操作中的事故及不正常现象
• 第一节:电石生产基础知识
• 概念:
电石化学名称为碳化钙,工业名称为电石,分子式为CaC2,分子量为64.10
电石的化学性质
电石的化学性质很活泼,在适当温度下能与许多的气体、液体 发生化学反应。 ①碳化钙不仅能被液态的或气态的水所分解,而且也能被物 理的或化学结合的水所分解。 在水过剩条件下,即将碳化钙浸于水中,反应依下式进行: CaC2+H2O=Ca(OH)2+C2H2 被滴加水分解时,还发生如下反应: CaC2+Ca(OH)2=CaO+C2H2 吸收空气中水份而分解: CaC2+H2O=CaO+C2H2 ② 在没有任何水份条件下,将电石在氢气流中加热至2200℃ 以上时,就有相当量的乙炔发生: CaC2+H2=Ca+C2H2 当加热到2275℃时,所生成的钙开始升华。
SiO2+2C=Si+2CO-574kJ Fe2O3+3C=2Fe+3CO-452kJ Al2O3+3C=2Al+3CO-1218kJ MgO+C=Mg+CO-486kJ 上述反应不仅消耗电能和碳材,而且影响操作,破坏炉底,特别是氧 化镁在熔融区迅速还原成金属镁,而使熔融区成为一个强烈的高温还原 区,镁蒸气从这个炽热的区域大量逸出时,其中一部分镁与一氧化碳立 即起反应,生成氧化镁: Mg+CO=MgO+C+489kJ 此时,由于反应放出强热形成高温,局部硬壳遭到破坏,使带有杂质 (Si、Fe、Al、Mg)的液态电石侵蚀了炉底。 另一部镁上升到炉料表面,与一氧化碳或空气中的氧反应: Mg+ O2=MgO+614kJ 当镁与氧反应时,放出大量的热,使料面结块,阻碍炉气排出,并产 生支路电流。还破坏局部炉壳,甚至使熔池遭到破坏,堵塞电石流出口 。实践证明,石灰中氧化镁含量每增加1%,则功率发气量将下降10~ 15L/kW·h。
电石的生产原理及过程

电石生成原理及过程(一)电石生产工艺过程烧好的石灰经破碎、筛分后,送入石灰仓贮藏,待用。
把符合电石生产需求的石灰和焦炭按规定的配比进行配料,用斗式提升机将炉料送至电炉炉顶料仓,经过料管向电炉内加料,炉料在电炉内经过电极电弧垫和炉料的电阻热反应生成电石。
电石定时出炉,放至电石锅内,经冷却后,破碎成一定要求的粒度规格,得到成品电石。
在电石炉中,电弧和电阻所产生的热把炉料加热至1900-2200℃,其总的化学反应式为:CaO+3C=CaC2+CO+10800千卡(二)电石炉生产工艺1、配料、上料和炉顶布料合格的原料由原料加工车间经计量、配料后,由斗式提升机送入电炉车间料仓内,由炉顶布料设施、固定胶带输送机和环形布料机将料送入炉顶环形料仓。
炉顶布料设施按需要把炉料布入料仓,由电炉加料管分批加入电炉内。
2、电炉半封闭电石炉是由炉体、炉盖、电极把持器、电极压放和电极升降装置等组成,是生产电石的主体设备。
电炉由变压器供电,炉料在电炉内经高温反应生成电石,并放出一氧化碳气体,生成的电石由出炉口排出,用烧穿器打开炉口,熔融电石流到冷却小车上的电石锅内。
电极的压放为油压控制,采用单层油缸抱紧提升电极锥形环油缸压紧导电鄂板,电极的正常升降由四楼三台卷扬机控制,电极的升降、压放、抱紧、下料控制全部在二楼操作室按电钮控制。
电炉由变压器供电,炉料在电炉内经高温反应生成电石,并放出一氧化碳气体,生成的电石由出炉口排出,用烧穿器打开出炉口,熔融电石流到冷却小车上的电石锅内。
出口炉设有挡屏和电弧打眼架,出炉口的上方设有排烟罩,用通风机抽出出炉时产生的烟气。
3、电炉冷却、破碎及包装熔融电石在电石锅内用顶车机拉至走廊或包装间进行冷却,电石砣凝固后,用桥式吊车和单抱钳将电石砣吊出,放在铸铁地面上冷却,冷却到适度后将电石破碎到合格粒度,然后分等极进行包装,送入成品库。
电石生产工艺图示解 ppt课件

3、工艺流程图
电石生产工艺图示解
17
② MgO:氧化镁对电石生产的危害较大,在熔融区内迅速还 原成金属镁。镁蒸汽上升过程中与CO和O2再次反应放出大量 的热量导致炉面发红、炉料结成壳阻碍炉气上升,严重时熔池
外壳被破坏,高温熔融液直接与耐火砖接触烧损耐火砖、电石 流道被堵塞。
反应式: MgO+C=Mg+电C石O生产↑-工艺1图1示6解千卡。
密闭电石炉生产工 (27000KVA)
电石生产工艺图示解
1
一、原料加工及输送流程
1、原料碳素
27000KVA密闭电石炉对焦炭的需求:
①颗粒度为5---25mm
②固定碳≥84%
③灰分≤15%
④ 挥发分≤1.9%
⑤水分≤1.0%
27000KVA密闭电石炉对兰炭的需求:
①颗粒度为5---25mm
③把电流通过电极导入炉内。
⑷出炉系统设备:
①炉嘴:用耐热铁或铸铁制成,安装在炉体的出炉口,炉 嘴最好能通水冷却,一则寿命长,再则方便于炉嘴堵住。
②烧穿装置:出炉时,必须用电弧去烧穿炉眼,利用电弧 烧穿炉眼的装置叫做烧穿装置。
三、炉气净化
1、炉气的性质及组成
电式石可生以成知反道应,:在电Ca石O炉+3内C=生C成aC电2+石CO的-同1时1.1,3千伴卡随。有从大反量应的 CO气体生成。在实际生产中,炉气的回收量约为400标准 米3/吨电石,炉气组成大致如下。
沉淀在炉底造成炉底升高。
※消化石灰的影响:
石灰生产过程中与空气接触一部分氧化钙生成氢氧化
钙,还有一部分与碳材中的水分结合形成氢氧化钙。氢氧
化钙输送当中容易裂碎,粉末氢氧化钙进入电石炉后分解
工艺流程图及工艺流程叙述
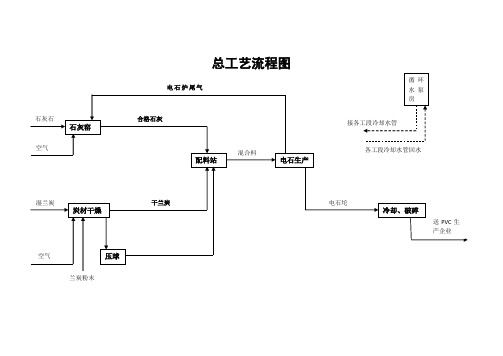
总工艺流程图碳材干燥工艺流程石灰生产工艺流程电石生产工艺流程图工艺流程经过炭材干燥工序后的兰炭与通过石灰窑石灰石烧制产生的氧化钙在电石炉内反应生成碳化钙,此过程发生的主要化学方程式为:具体工艺流程如下:(1)600t/d套筒窑工艺流程简述:①石灰石筛分系统主要是将合格粒度的石灰石进行筛分,去除5mm以下的。
将筛上物输送至窑前料仓。
②窑前料仓内装有雷达测位计用来探测仓内料位。
底部通向石灰窑的计量斗。
③上料系统当窑顶料位计指示窑内料时,仓下电振自动向计量斗内加料,达到设定值后,电振停止加料。
计量斗向小车内加料,到一定时间卷扬机自动启动,牵引小车沿斜桥到达窑顶后,通过窑顶受料装置将石灰石加入窑内。
套筒窑的装料由称量料斗、闸门、单斗提升机、密封闸板、旋转布料器、料钟及料位检测装置组成,窑顶旋转布料器、密封闸板、料钟由液压驱动。
④套筒窑主体物料经过窑内的预热带、上部逆流煅烧带、中部逆流煅烧带、下部并流煅烧带和冷却带,通过窑下出灰机进入窑底料仓,最后由振动出灰机排出窑外。
套筒窑主要由窑体、上料装置、出料装置、燃烧系统、换热器、喷射器(耐热铸钢)以及风机系统组成。
窑体由内外筒组成,内筒分上下两个独立部分,上部为上内筒,下部为下内筒。
上下内筒由双层结构形成圆柱形钢板箱,钢板箱内通入冷空气对内筒进行连续冷却防止其高温变形,预热的空气作为燃烧室的一次空气。
内筒与外筒同心布置,形成一个环形空间,石灰石就在环形区域内煅烧。
燃料的燃烧过程是通过烧嘴在燃烧室内进行的,燃烧室在窑体的中部并分上下两层,同一层均匀布置,上下两层错开布置。
燃烧产生的高温烟气通过拱下的空间进入石灰石料层。
石灰石在套筒窑内煅烧的一个显著特点是逆流煅烧与并流煅烧同时进行。
套筒窑外壳上分布的两层燃烧室将窑体分成两个逆流操作的煅烧带和一个并流操作的煅煅烧带。
上层燃烧室至下内套筒上端,以及上层燃烧室至下层燃烧室之间为两个逆流煅烧带,下层燃烧室至下内筒底部为顺流煅烧带。
电石生产工艺流程图
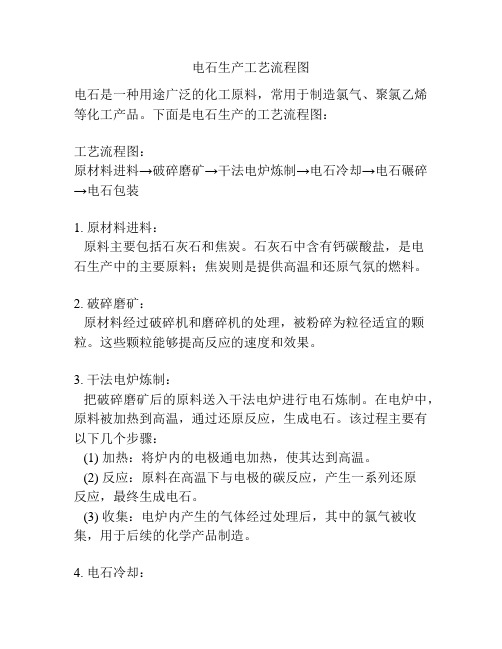
电石生产工艺流程图电石是一种用途广泛的化工原料,常用于制造氯气、聚氯乙烯等化工产品。
下面是电石生产的工艺流程图:工艺流程图:原材料进料→破碎磨矿→干法电炉炼制→电石冷却→电石碾碎→电石包装1. 原材料进料:原料主要包括石灰石和焦炭。
石灰石中含有钙碳酸盐,是电石生产中的主要原料;焦炭则是提供高温和还原气氛的燃料。
2. 破碎磨矿:原材料经过破碎机和磨碎机的处理,被粉碎为粒径适宜的颗粒。
这些颗粒能够提高反应的速度和效果。
3. 干法电炉炼制:把破碎磨矿后的原料送入干法电炉进行电石炼制。
在电炉中,原料被加热到高温,通过还原反应,生成电石。
该过程主要有以下几个步骤:(1) 加热:将炉内的电极通电加热,使其达到高温。
(2) 反应:原料在高温下与电极的碳反应,产生一系列还原反应,最终生成电石。
(3) 收集:电炉内产生的气体经过处理后,其中的氯气被收集,用于后续的化学产品制造。
4. 电石冷却:炼制后的电石需要经过冷却处理,降低温度。
冷却后的电石颗粒更易于包装和运输。
5. 电石碾碎:冷却后的电石进入碾碎设备,被粉碎成适当的颗粒大小。
这些电石颗粒可以用于制造化工产品,如聚氯乙烯、氯气等。
6. 电石包装:粉碎后的电石被分装入包装袋中,以方便运输和存储。
包装时需要注意避免潮湿和与其他物质的接触。
电石生产工艺流程的每个环节都十分关键,影响着最终产品的质量和性能。
生产过程中需要控制好各种因素,确保能够得到符合质量标准的电石产品。
同时,工艺流程中还需要进行废气处理,以保护环境和工人的健康。
电石生产工艺规程(定稿)

西部热电电石公司2×30000kV A密闭电石炉作业指导书(暂行)编写:审核:审定:批准:二O O九年一月目录一、产品说明 (2)二、原材料技术要求 (5)三、电石生产原理 (8)四、生产工艺操作 (9)1、2×30000KVA密闭电石生产工艺流程图 (9)2、原料化验安全操作规程 (10)3、兰炭烘干岗位安全操作规程 (14)4、电石炉生产安全操作规程 (21)5、出炉工岗位安全操作规程 (34)6、加电极壳及加电极糊安全操作规程 (39)7、中控室安全操作规程 (42)8、电石冷却岗位安全操作规程 (49)9、天车工岗位安全操作规程 (51)10、循环水岗位安全操作规程 (54)11、炉气净化系统安全操作规程 (58)12、空压制氮岗位安全操作规程 (66)一、 产品说明1、名称:化学名称碳化钙,俗名电石。
其中含碳化钙约65-85%,其余为杂质。
2、分子式:CaC 23、分子量:64.1 C4、结构式:Ca5、基本理化性质 C⑪、外观:化学纯的碳化钙几乎为无色透明的晶体,极纯的碳化钙结晶为天蓝色大晶体,其色泽颇似淬火钢。
工业碳化钙为不规则块状体,其色泽与纯度有关,有灰色的、棕黄色的、黑色的,碳化钙含量较高时呈紫色,其新断面呈灰色,若暴露在潮湿的空气中则呈灰白色。
⑫、相对密度:电石的相对密度决定于碳化钙的含量、电石的纯度越高,相对密度越小。
⑬、溶解度:电石不溶于任何溶剂。
⑭、溶点:电石的熔点随电石中CaC 2含量而改变。
纯CaC 2熔点为2300℃,电石中CaC 2含量一般在80%左右,其熔点在2000℃左右,CaC 2含量为69%时,熔点最低为1750℃,影响电石熔点的因素取决于杂质的量和性质。
如图1所示:CaC 2含量(%)图1 电石熔点与其中CaC 2含量的关系⑮、导电性:其导电性与电石纯度有关,CaC 2含量越高,导电性能越好,当CaC 2含量下降到70-65%之间时,其导电性能达到最低值,通常比电阻约120000欧姆/厘米3。
电石法生产工艺流程

电石法的应用领域
合成橡胶
乙炔气体可用于合成橡胶的生 产,如氯丁橡胶、丁腈橡胶等
。
塑料
乙炔气体可用于合成各种塑料 ,如聚氯乙烯(PVC)、聚乙 烯(PE)等。
染料
乙炔气体可用于合成某些特殊 染料和颜料。
其他领域
此外,乙炔气体还可用于焊接 、切割、制造电极等领域。
02
生产原料与设备
主要原料
电石(碳化钙)
02
物理性能测试
03
不合格品处理
对产品的物理性能进行测试,如 密度、硬度、外观等,全面评估 产品质量。
对不合格产品进行分类、标识和 处置,防止不合格品流入市场或 误用。
05
安全与环保
安全生产措施
严格遵守操作规程
01
确保员工熟悉并遵守电石法生产工艺的操作规程,避免因操作
不当引发安全事故。
定期维护与检查
电石法的发展历程
起始阶段
20世纪初,德国科学家发现了电石与 水反应可以生成乙炔气体,开启了电 石法的研究和应用。
发展阶段
现状
目前,电石法仍然是乙炔气体的重要 生产工艺,但随着环保要求的提高和 新型技术的出现,其市场份额有所下 降。
随着工业化的进程,电石法逐渐成为 乙炔气体的主要生产方法,并不断改 进和优化。
03
温度控制
严格控制生产过程中的温 度,确保温度波动在工艺 要求的范围内,以保障产 品质量和稳定性。
压力控制
合理调节压力,保证设备 运行安全,同时确保产品 性能和质量的稳定。
流量控制
对各种原料的流量进行精 确控制,以保证投料比例 和反应速度符合工艺要求 。
产品检验与质量评估
01
化学分析
通过化学分析方法检测产品的成 分、杂质等指标,确保产品质量 符合标准。
电石生产原理及工艺流程

电石生产原理及工艺流程
电石工业诞生于19 世纪末,迄今工业生产仍沿用电热法工艺,是生石灰(CaO)和焦炭(C)在埋弧式电炉(电石炉)内,通过电阻电弧产生的高温反应制得,同时生成副产品一氧化碳(CO)。
电石生产的基本化学原理CaO+3C→CaC2+CO
式中可见电石生成反应中投入的三份C,其中二份生成CaC2,而另一份则形成CO,
即消耗了1/3 的炭素材料.
⑴石灰生产
生石灰(CaO)是由石灰石(CaCO3)在石灰窑内于1200℃左右的高温煅烧分解制得:
CaCO3→CaO+CO2
⑵电石生产
电石(CaC2)是生石灰(CaO)和焦炭(C)于(电石炉)内通过电阻电弧热在1800~2200℃的高温下反应制得:
CaO+3C→CaC2+CO
电石炉是电石生产的主要设备,电石工业发展的初期,电石炉的容量很小,只有100~300KVA,炉型是开放式的,副产品CO 在炉面上燃烧,生成CO2 白白的浪费。
电石行业是一个高耗能、高污染的行业。
在原材料的运输、准备过程及生产的过程中都有污染物生成。
现在这个行业国家规定比较严格,另外一氧化碳的回收也取得了很好的效果.。
电石生产工艺流程

电石生产工艺流程说明电石生产将分为原料贮存、石灰生产、石灰破碎、焦炭干燥、配料输送、电石生产、电石冷却储存及电极壳制造、炉气净化回收、公用工程等几个工序。
全厂流程简述外购质量合格粒度30~60mm的石灰石由自卸汽车卸到本厂石灰石储场,经装载机送入受料槽,经过筛分、胶带运输机送到石灰生产单元的石灰石储仓中。
外购质量合格粒度0~200mm的石灰由自卸汽车运到本厂,卸入带棚的石灰地下受料斗,经过往复给料机、胶带运输机、至齿辊破碎机进行破碎筛分,破碎粒度为0~45mm,经胶带运输机将0~45mm破碎后石灰送到石灰筒仓中储存,粉料外运0~5mm外运做建材销售。
质量合格粒度5~25mm的焦炭由自卸汽车运进本厂焦炭棚库中。
经装载机送入受料槽,初筛后用胶带输送机送去炭材干燥湿焦炭仓中,筛下细粉运至炭材干燥工段用做热风炉燃料,湿焦炭经振动给料机进入卧式滚筒干燥窑,在干燥窑内与500~700℃高温的热风同流换热,到干燥窑尾端其含水量降到1%以下,通过胶带输送机送入干焦仓储存。
干燥窑的热源来自热风炉,本工程选用焦粉、炉气两用炉,燃料为回收利用的0~5mm的焦炭粉和来自炉气气柜来的电石炉气。
贮存于石灰石储仓中的石灰石经振动给料机、胶带输送机、称量斗计量后送入料车并提升至气烧石灰窑顶,通过旋转布料器送入窑内以电石炉气为燃料进行锻烧,锻烧后的石灰经振动给料机、胶带输送机送入石灰储仓储存,当石灰窑开车或炉气不稳定时,可采用掺烧部分焦炭作为辅助燃料锻烧石灰石。
储存于干焦仓的焦炭,和储存于石灰仓(或石灰筒仓)中的石灰分别经胶带输送机送至配料站,在配料站石灰和焦炭分别经振动筛筛分,粉料进入粉料仓,经称量斗称量配料后混合送去电石生产空心电极系统,合格粒度的焦炭及石灰分别进入各自料仓,当电石炉求料时,分别经振动给料机送入自动称重料斗,按照一定的配比计量、称重;经过振动给料机按照设定的速度下料,均匀分层混合送到通往电石炉厂房的胶带运输机上。
电石生产工艺流程

电石生产工艺流程1.配料工艺流程图1.1方框流程图日料仓内的原料石灰和炭材按配比称量后按设定的下料时间落入皮运机混合均匀,由皮运机输送至环形加料机,然后再送入电石炉各料仓。
皮带起步开始的由1#、2#炉操作室配料工负责;B皮带起步开始的由3#、4#炉操作室配料工负责。
1A 2A 3A 4A 5A 1#炉(全长203.95m,皮带速度1.35m/s,从卸料到环型加料机时间为2分32秒)1A 2A 3A 5B 2#炉(全长193.75m,皮带速度1.35m/s,从卸料到环型加料机时间为2分24秒)1B 2B 6B 8A 3#炉(全长201.65m,皮带速度1.35m/s,从卸料到环型加料机时间为2分30秒)1B 2B 6B 7B 8B 4#炉(全长211.85m,皮带速度1.35m/s,从卸料到环型加料机时间为2分37秒)3B、4B、6A、7A备用1.3带控制点的流程图2.电石炉工艺流程图2.1方框流程图2.2流程简述石灰与炭材通过环形加料机进入电石炉各料仓,然后自然下落至电石炉内凭借电流通过电极产生的电弧热和电阻热在1800~2200℃的高温下反应而生成碳化钙,最后出炉。
2.3带控制点的流程图3.净化系统工艺流程图3.1方框流程图3.2流程简述电石炉产生的尾气在600℃~850℃,经过两级旋风空冷除尘器冷却,将气体冷却至200℃~260℃之间,同时将气体中大颗粒的粉尘捕集下来,温度控制在200℃~250℃之间主要原因是:一、防止焦油在低于200℃时析出并堵塞管路;二、防止温度过高,损坏过滤器及风机设备等,经过滤器除尘过的气体经风机增压送至气烧石灰窑使用。
电石炉尾气经旋风冷却器冷却后进入布袋过滤器过滤,过滤后的气体经净气风机输送至增压站,再经增压风机将气体增压至气烧石灰窑所需压力后进入气烧石灰窑燃烧,过剩气体可通过泄放烟囟排出。
经旋风空冷除尘器滤下的粉尘和布袋过滤器同滤下的粉尘由密封式链板机输送至粉尘总仓。
电石的生产原理及过程

电石的生产原理及过程电石生成原理及过程(一)电石生产工艺过程烧好的石灰经破碎、筛分后,送入石灰仓贮藏,待用。
把符合电石生产需求的石灰和焦炭按规定的配比进行配料,用斗式提升机将炉料送至电炉炉顶料仓,经过料管向电炉内加料,炉料在电炉内经过电极电弧垫和炉料的电阻热反应生成电石。
电石定时出炉,放至电石锅内,经冷却后,破碎成一定要求的粒度规格,得到成品电石。
在电石炉中,电弧和电阻所产生的热把炉料加热至1900-2200℃,其总的化学反应式为:CaO+3C=CaC2+CO+10800千卡(二)电石炉生产工艺1、配料、上料和炉顶布料合格的原料由原料加工车间经计量、配料后,由斗式提升机送入电炉车间料仓内,由炉顶布料设施、固定胶带输送机和环形布料机将料送入炉顶环形料仓。
炉顶布料设施按需要把炉料布入料仓,由电炉加料管分批加入电炉内。
2、电炉半封闭电石炉是由炉体、炉盖、电极把持器、电极压放和电极升降装置等组成,是生产电石的主体设备。
电炉由变压器供电,炉料在电炉内经高温反应生成电石,并放出一氧化碳气体,生成的电石由出炉口排出,用烧穿器打开炉口,熔融电石流到冷却小车上的电石锅内。
电极的压放为油压控制,采用单层油缸抱紧提升电极锥形环油缸压紧导电鄂板,电极的正常升降由四楼三台卷扬机控制,电极的升降、压放、抱紧、下料控制全部在二楼操作室按电钮控制。
电炉由变压器供电,炉料在电炉内经高温反应生成电石,并放出一氧化碳气体,生成的电石由出炉口排出,用烧穿器打开出炉口,熔融电石流到冷却小车上的电石锅内。
出口炉设有挡屏和电弧打眼架,出炉口的上方设有排烟罩,用通风机抽出出炉时产生的烟气。
3、电炉冷却、破碎及包装熔融电石在电石锅内用顶车机拉至走廊或包装间进行冷却,电石砣凝固后,用桥式吊车和单抱钳将电石砣吊出,放在铸铁地面上冷却,冷却到适度后将电石破碎到合格粒度,然后分等极进行包装,送入成品库。
(此文档部分内容来源于网络,如有侵权请告知删除,文档可自行编辑修改内容,供参考,感谢您的配合和支持)编辑版word。
电石生产工艺规程(定稿)

电石生产工艺规程(定稿)西部热电电石公司2×30000kV A密闭电石炉作业指导书(暂行)编写:审核:审定:批准:二O O九年一月目录一、产品说明 (2)二、原材料技术要求 (5)三、电石生产原理 (8)四、生产工艺操作 (9)1、2×30000KVA密闭电石生产工艺流程图 (9)2、原料化验安全操作规程 (10)3、兰炭烘干岗位安全操作规程 (14)4、电石炉生产安全操作规程 (21)5、出炉工岗位安全操作规程 (34)6、加电极壳及加电极糊安全操作规程 (39)7、中控室安全操作规程 (42)8、电石冷却岗位安全操作规程 (49)9、天车工岗位安全操作规程 (51)10、循环水岗位安全操作规程 (54)11、炉气净化系统安全操作规程 (58)12、空压制氮岗位安全操作规程 (66)一、产品说明1、名称:化学名称碳化钙,俗名电石。
其中含碳化钙约65-85%,其余为杂质。
2、分子式:CaC 23、分子量:64.1 C4、结构式:Ca5、基本理化性质 C、外观:化学纯的碳化钙几乎为无色透明的晶体,极纯的碳化钙结晶为天蓝色大晶体,其色泽颇似淬火钢。
工业碳化钙为不规则块状体,其色泽与纯度有关,有灰色的、棕黄色的、黑色的,碳化钙含量较高时呈紫色,其新断面呈灰色,若暴露在潮湿的空气中则呈灰白色。
、相对密度:电石的相对密度决定于碳化钙的含量、电石的纯度越高,相对密度越小。
、溶解度:电石不溶于任何溶剂。
、溶点:电石的熔点随电石中CaC 2含量而改变。
纯CaC 2熔点为2300℃,电石中CaC 2含量一般在80%左右,其熔点在2000℃左右,CaC 2含量为69%时,熔点最低为1750℃,影响电石熔点的因素取决于杂质的量和性质。
如图1所示:CaC 2含量(%)图1 电石熔点与其中CaC 2含量的关系、导电性:其导电性与电石纯度有关,CaC 2含量越高,导电性能越好,当CaC 2含量下降到70-65%之间时,其导电性能达到最低值,通常比电阻约120000欧姆/厘米3。