类筒纱成型不良的原因分析
织物原因分析及整改措施

织物原因分析及整改措施1. 引言织物作为一种常见的纺织材料,在服装、家居用品和工业领域得到广泛应用。
然而,在织物生产和使用的过程中,可能会出现一些质量问题,例如织物皱褶、糙洁、色差等。
本文将针对织物质量问题进行原因分析,并提出相应的整改措施。
2. 织物质量问题的原因分析2.1 原材料问题织物质量问题的一个重要原因是原材料的质量不合格。
原材料中可能存在纤维短、纤维混杂、纤维扭曲等问题,这些问题会直接影响到织物的质量。
此外,原材料的选择和配比不当也会导致织物质量下降。
2.2 织造工艺问题织物质量问题还与织造工艺有关。
织造工艺中可能存在的问题包括织机调整不当、纬纱张力不均匀、织物密度过大或过小等。
这些问题会导致织物的不均匀、开裂、变形等问题。
2.3 后整理问题织物在后整理过程中也可能出现质量问题。
例如,过度的物理力以及温度和湿度的变化可能导致织物尺寸缩水、变形等问题。
此外,后整理中使用的化学药剂如果选择不当或使用不当,则会影响到织物的手感和外观。
3. 织物质量问题的整改措施为解决织物质量问题,以下是几项有效的整改措施:3.1 强化原材料质量管理加强对原材料的质量控制是预防织物质量问题的关键。
建议与供应商建立稳定的合作关系,并进行定期的原材料质量检查。
对原材料进行严格的筛选和测试,确保其质量符合要求。
此外,制定合理的原材料配比标准,确保原材料的稳定性和一致性。
3.2 完善织造工艺流程改进织造工艺是提高织物质量的关键。
建议对织机进行定期的维护和调整,确保其正常运行。
在织造过程中,监测纬纱张力,保持其均匀分布。
此外,根据织物的用途和要求,合理调整织物的密度,确保织物的均匀性和稳定性。
3.3 优化后整理流程改进后整理工艺能够有效改善织物的质量。
建议在后整理过程中控制物理力的大小,避免对织物造成过度的拉伸和挤压。
对于温度和湿度的控制,要根据织物的类型和原材料的特性进行合理调整,避免造成织物的尺寸缩水和变形。
此外,选择合适的化学药剂,确保其与织物的相容性,并按照正确的方法和浓度使用,避免对织物产生不良影响。
常见织疵形成的原因及预防措施
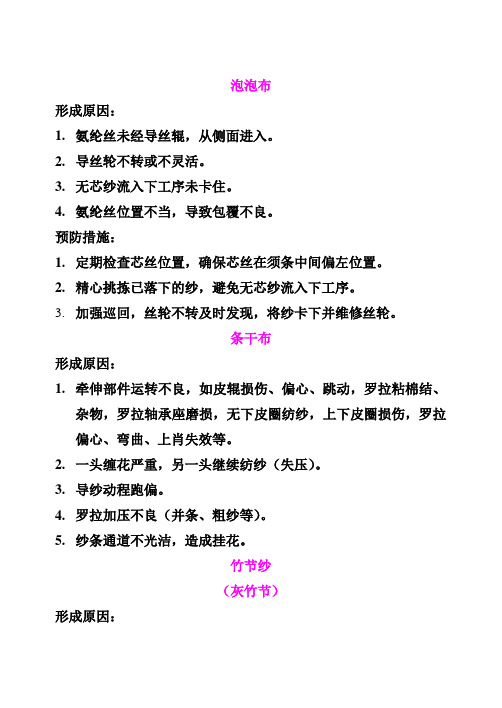
泡泡布形成原因:1.氨纶丝未经导丝辊,从侧面进入。
2.导丝轮不转或不灵活。
3.无芯纱流入下工序未卡住。
4.氨纶丝位置不当,导致包覆不良。
预防措施:1.定期检查芯丝位置,确保芯丝在须条中间偏左位置。
2.精心挑拣已落下的纱,避免无芯纱流入下工序。
3.加强巡回,丝轮不转及时发现,将纱卡下并维修丝轮。
条干布形成原因:1.牵伸部件运转不良,如皮辊损伤、偏心、跳动,罗拉粘棉结、杂物,罗拉轴承座磨损,无下皮圈纺纱,上下皮圈损伤,罗拉偏心、弯曲、上肖失效等。
2.一头缠花严重,另一头继续纺纱(失压)。
3.导纱动程跑偏。
4.罗拉加压不良(并条、粗纱等)。
5.纱条通道不光洁,造成挂花。
竹节纱(灰竹节)形成原因:1.清梳工序漏底花堆积太多,带入棉层。
2.各工序通道粘、缠、挂、堵带入(三角区、龙头,并粗、细纱牵伸通道)3.绒板、绒套、绒辊花带入(并条、粗纱、精梳、细纱)。
4.高空清洁积花掉入半成品或正在纺纱机内。
5.各工序清洁方法不当。
6.卡疵把关不严,疵点流入下工序。
7.清洁不彻底(例如粗纱斜坡、车面清洁不及时,巡回吹吸风吹入,打擦板时的飞花卷入纱条等)。
8.各工序揩车不良,油飞花粘附纱条,半成品棉条、粗纱掉地,造成污染。
三丝疵布形成原因:1.拣花间未拣净,后工序未卡住。
2.个别员工在工作场所梳头,清洁工具破损掉毛仍在使用。
应对措施:1.加强员工拣色杂责任心教育,后续工序严格执行卡疵把关制度。
2.加强管理,严格要求,杜绝在工作场所梳头现象;同时,车间定期对清洁工具检查,发现掉毛立即停止使用。
粗经、粗纬形成原因:1.粗纱断头、烂纱后未及时停车,飘入邻纱未处理干净。
2.条子粘连,机后换条子破条或机后双条喂入。
3.接头不符合操作法要求(并条、粗纱、细纱等工序)。
4.细纱断头飘入邻纱(主要是混纺纱)5.细纱续粗纱或粗纱纱尾飘入邻纱,细纱机车顶板的粗纱尾巴下垂,被卷入上排粗纱。
疵点条子形成原因:粗细条:生条:1、棉卷片段重量差异大或粘卷、破洞、头码过厚、双层卷。
筒子染色时内外色差原因及预防措施

筒子染色时内外色差原因及预防措施1 简纱染色色差色花的形成原因1.1 筒纱质量络筒时要保证筒纱卷绕密度一致,卷绕硬度一般为27±2(肖氏硬度)。
若卷绕硬度过小,染色过程中受气流的冲击会损伤纱,导致成形不良,也会造成染液局部短路,使筒纱染色深浅不一,产生染花;若卷绕硬度过大,染液不易渗透造成内外色差。
1.2 设备运行状况在设备方面,主泵泵力不足,换向装置不到位,电脑指示灯失灵,染缸法兰盘漏液,都会降低流速,严重时就会造成色花。
1.2.1 泵力不足及换向装置不到位操作时盐未被溶化就投入染缸,进泵后泵叶与盐摩擦,与泵体之间的间隙增大,而造成泵力不足;鹅颈管式换向装置活塞运行不良,行程不到位,致使染色压力达不到。
1.2.2 染缸部件漏液因装纱后,纱架重量很重,起吊过程中与染缸底部发生碰撞,使染缸底部盘管的焊接点开裂、螺丝松动,纱杆与底盘密封不好,导致漏流。
1.2.3 控温系统由于缸内液体淋渗到感温针上,使感温针运作失灵,造成控温系统所显示的`温度与实际温度不符,导致染色温度不准确,使色相发生偏差。
1.3 工艺1.3.1 前处理前处理的除杂、毛效、白度、洗后pH值和双氧水的去除情况都会影响染色的均匀性。
1.3.2 染色选择合适的染料与助剂,设计合理的染色工艺可以保证染色质量。
工艺设计不好,选择三原色的配伍性差,也会造成色花。
2 防止色差色花的措施2.1 筒纱质量筒纱成形要严格把关,杜绝哑铃纱、喇叭纱、重叠纱、漏眼纱及硬边纱,卷绕密度要控制在要求范围之内,过硬过松的要挑出,筒纱大小一致。
2.2 设备维修为保证设备正常运行,对上述所存在的问题要定期检查,这样才能保证设备运转良好和染色质量稳定。
定期对水、汽阀门进行检查,看有无开启不灵活和关闭不严现象,加强设备维护。
2.3 前处理工艺选择前处理工艺要煮透、煮匀,以便于染色。
为缩短时间,采用煮练漂白同浴法。
工艺处方(g/L)3O%氢氧化钠 4精练剂 2渗透剂 2双氧水 6稳定剂 3前处理工艺曲线(见图1)。
成型不良的原因及改善方法详解
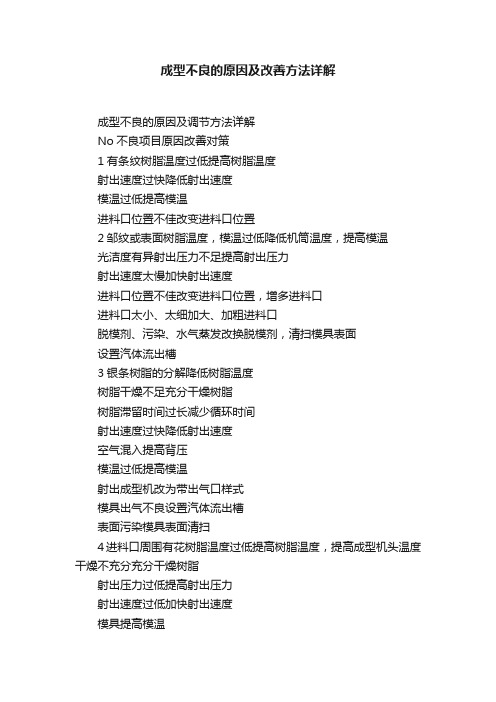
成型不良的原因及改善方法详解成型不良的原因及调节方法详解No不良项目原因改善对策1有条纹树脂温度过低提高树脂温度射出速度过快降低射出速度模温过低提高模温进料口位置不佳改变进料口位置2邹纹或表面树脂温度,模温过低降低机筒温度,提高模温光洁度有异射出压力不足提高射出压力射出速度太慢加快射出速度进料口位置不佳改变进料口位置,增多进料口进料口太小、太细加大、加粗进料口脱模剂、污染、水气蒸发改换脱模剂,清扫模具表面设置汽体流出槽3银条树脂的分解降低树脂温度树脂干燥不足充分干燥树脂树脂滞留时间过长减少循环时间射出速度过快降低射出速度空气混入提高背压模温过低提高模温射出成型机改为带出气口样式模具出气不良设置汽体流出槽表面污染模具表面清扫4进料口周围有花树脂温度过低提高树脂温度,提高成型机头温度干燥不充分充分干燥树脂射出压力过低提高射出压力射出速度过低加快射出速度模具提高模温加大进料口及流道改变进料口位置5黑条主轴、机筒、伤痕清扫主轴机筒、换轴滞留时间过长射出机筒内树脂机筒温度过高降低机筒温度射出速度过快降低射出速度轴转速快烧焦降低转速,降低背压6烧焦空气混入安装出气口装置设置汽体流出槽射出速度过快降低射出速度7云纹、光泽不良树脂过热降低机筒温度成型材料干燥不足充分干燥、改变干燥方式模温过低提高模温机筒温度过高、过低调节机筒温度脱模剂过多减少脱模剂8色差、混色颜料染料分散不良改变树脂,着色剂成型机筒温度过高、过低调节机筒温度可塑化不良降低轴转速,提高背压树脂的分解降低温度,循环时间缩短成型机清扫不良彻底清扫前产品留在机内材料冷却时间过短延长冷却时间进料口位置不佳修正进料口位置分散剂、扩散剂不能加入对该树脂不适合的添加剂等9透明料混浊材料干燥不足,异物混入充分干燥材料、变更材料树脂温度过高、过低调节树脂温度滞留时间过长成型材料滞留时间减短机筒温度过高降低机筒温度添加剂、脱模剂过多确认添加剂的适合性,减少脱模剂10气泡成型材料的分解降低成型温度材料干燥不足充分干燥材料树脂带温过长修正机筒内主轴进料行程射出压力过低提高射出压力保压过低提高保压背压过低提高背压射出速度过慢提高射出速度背压过大背压降低模温过高、过低调节模温料斗下端冷却不足注意改善料斗下端的冷却成型机改为带出气口样式11杂质、异物成型机、料斗、干燥机清扫不良充分清扫成型机、料斗、干燥机材料周围环境有尘埃用塑胶将材料部分隔开材料输送管清扫不良清扫材料输送管模具生锈模具清扫材料不良改换材料12剥离不同材料混入调节材料断裂树脂温度过低提高树脂温度模温过低提高模温材料使用不适、缓冷不足更变材料、改变缓冷条件13裂纹干燥条件不良按树脂种类决定干燥条件树脂温度过低提高树脂温度模温过低提高模温射出压力过高降低射出压力保压压力过高降低保压压力保压时间太长减少保压时间坡度不足增加坡度顶针位置不良调节顶针位置顶针数量少增加顶针数量脱模剂不足增加脱模剂14脆弱成型材料不适改变成型材料强度不够不同材料,粉碎材料混入调节材料质量干燥不适度按材料选择干燥条件树脂温度过高降低树脂温度树脂温度不适当成型温度调节滞留时间过长缩短滞留时间可塑化不良成型温度轴转速、背压调整射出压力不适当射出压力调节保压压力过低提高保压压力射出速度不适当射出速度调节冷却时间过短延长冷却时间模温调节模温模具强度不足修理模具进料口不良、数量不足改变进料口位置,增加进料口数量后处理采用缓冷方式15尺寸不均材料流动性调节成型温度有大有小材料吸湿充分干燥材料射出压力过低调节射出压力保压过低、过短调节保压的压力和时间冷却时间过短延长冷却时间背压过低选择适当背压模温不适调节模温模具关合力过少提高模具关合力模具强度不足修理模具,增加强度进料口位置不适当改变进料口位置进料口数量少增加进料口数量16变形成型材料流动性不足提高树脂温度收缩率过大改提收缩率小的树脂射出压力过高降低射出压力冷却时间短延长冷却时间,使用冷却模具模温使各部位得到冷却,改善模具17凸凹不规则工程塑料较多如PA、PET等注意改善料斗下的冷却料斗侧温度过高降低料斗下机筒温度背压过高调低背压,固定停止时间再生材料不良尽量将再生材料打碎用筛子除去粉末祛除含0.2mm以下厚度胶片的部分玻纤强化颗粒使用2.5mm -3.5mm长度的玻纤材料18毛边、飞刺树脂流动性太快降低成型温度、改变成型材料射出压力过高降低射出压力保压太慢快速保压模具关合力不良提高模具关合力模具强度不足修理模具模具表面不光滑修理模具19多边树脂流动性过剩降低树脂温度改变成型材料射出压力过高降低射出压力快速加入保压模具关合力不足提高模具关合力模具不良模具强度不足分割面密封不良20胡须树脂成型收缩率大改变成型材料树脂温度高降低树脂温度射出压力过低提高射出压力保压压力低提高保压压力射出速度过低加快射出速度模具降低胡须发生侧模温扩大模具进料口、加粗料流道改善进料口位置,壁厚均一模温过高降低模温21缺边树脂流动性不足提高树脂温度改变成型材料射出压力过低提高射出压力保压压力低慢速加入保压提高保压压力射出速度过慢增加射出进入速度计量投量不足增加计量设定值主轴不适合使用带防止逆流功能的主轴模具扩大模具进料口加粗材料流道。
筒纱成形不良原因与对策

3.5、蛛网纱筒子
3.5.1 在筒子的左侧或右侧端面有纱线甩出,形成 蛛网纱筒子。见图:
3.5.2蛛网纱筒子的解决办法
因筒纱接触压力过小、槽筒与筒子之间滑移过大 产生的蛛网纱,可适当增大筒子接触压力。 纸管严重偏心或纸管与槽筒接触面相对角度过大, 造成筒纱运行过程中跳动过大导致蛛网纱,可选 用标准纸管,调整好槽筒接触面。 槽筒沟槽回头点损伤或不光滑,沟槽内有锈点、 棉蜡等导致的蛛网纱,可修复或更换槽筒。 纱线张力过多偏离标准设定、时有时无、时大时 小造成的蛛网纱。应重新优化设定纱线张力。
金波 中国纱线网 2012年3月
一、筒纱成形不良产生的危害 二、筒纱成形不良造成的原因 三、13类筒纱成形不良的描述和解决方案 四、生产现场常见问题的图片说明
一、筒纱成形不良的危害
多年来,中国纱线网咨询团队在为广大棉纺织 企业开展服务中,我们发现有一类非纱线质量原因 让众多纺织企业较为头痛的问题:即筒纱成型不良! 筒纱成型不良的危害主要有: 1、络筒效率下降,纱线质量严重恶化! 2、产生回丝多,制成率下降,能耗、机配件消耗增 加!
3.6滑边筒子
3.6.1 在换管或纱线断头后接头时,纱线落在筒子左侧端面 上同时又被卷入筒子形成的,滑边筒子多形成于单锭打结 过程中。
3.6.2滑边筒子的解决办法
筒纱高速运行时纱线突然崩断,单锭在重新打结的过 程中,容易形成滑边筒子。可通过细纱工序消除管纱 成型不良和管纱脱圈。 自络生产环境空气湿度太小,静电严重,容易出现滑 边、蛛网纱筒子。可适当加大自络生产环境空气湿度。 粗支纱、弹性纱易出现滑边筒子。可降低车速,调整 好筒子刹车灵敏度。 吸风负压太低,或大吸嘴与筒子间隔距离太大。可优 化吸风负压,调整好大吸嘴与筒子的间隔距离。 发生滑边的筒纱在后道工序退绕中,有时会出现筒纱 内部有回丝现象! 细纱管纱成形不良时易发生滑边筒子,可优化细纱管 纱的成形
技术 细纱质量问题的原因分析及措施
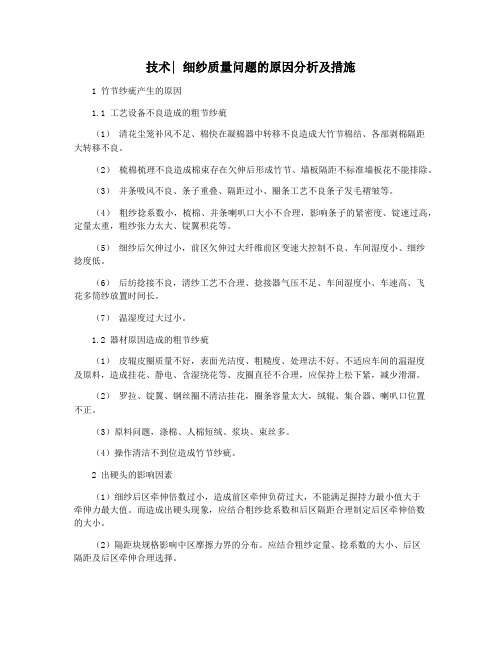
技术| 细纱质量问题的原因分析及措施1 竹节纱疵产生的原因1.1 工艺设备不良造成的粗节纱疵(1)清花尘笼补风不足、棉快在凝棉器中转移不良造成大竹节棉结、各部剥棉隔距大转移不良。
(2)梳棉梳理不良造成棉束存在欠伸后形成竹节、墙板隔距不标准墙板花不能排除。
(3)并条吸风不良、条子重叠、隔距过小、圈条工艺不良条子发毛褶皱等。
(4)粗纱捻系数小,梳棉、并条喇叭口大小不合理,影响条子的紧密度、锭速过高,定量太重,粗纱张力太大、锭翼积花等。
(5)细纱后欠伸过小,前区欠伸过大纤维前区变速大控制不良、车间湿度小、细纱捻度低。
(6)后纺捻接不良,清纱工艺不合理、捻接器气压不足、车间湿度小、车速高、飞花多筒纱放置时间长。
(7)温湿度过大过小。
1.2 器材原因造成的粗节纱疵(1)皮辊皮圈质量不好,表面光洁度、粗糙度、处理法不好、不适应车间的温湿度及原料,造成挂花、静电、含湿绕花等、皮圈直径不合理,应保持上松下紧,减少滑溜。
(2)罗拉、锭翼、钢丝圈不清洁挂花,圈条容量太大,绒辊、集合器、喇叭口位置不正。
(3)原料问题,涤棉、人棉短绒、浆块、束丝多。
(4)操作清洁不到位造成竹节纱疵。
2 出硬头的影响因素(1)细纱后区牵伸倍数过小,造成前区牵伸负荷过大,不能满足握持力最小值大于牵伸力最大值。
而造成出硬头现象,应结合粗纱捻系数和后区隔距合理制定后区牵伸倍数的大小。
(2)隔距块规格影响中区摩擦力界的分布。
应结合粗纱定量、捻系数的大小、后区隔距及后区牵伸合理选择。
(3)粗纱的定量大,在同样的胶辊状态和后区牵伸倍数及粗纱捻系数情况下,相应细纱牵伸时的胶圈钳口握持力增加,以满足牵伸力握持力的匹配。
(4)胶辊的表面处理方式和胶辊胶圈的表面摩擦系数影响握持力和牵伸力的大小匹配。
不粘缠的情况下尽量加大胶辊的表面摩擦系数,控制胶圈滑溜的情况下适当减小胶圈的表面摩擦系数,以稳定中区牵伸力。
(5)温湿度过大,使须条中纤维间的摩擦阻力相应增加,导致须条中纤维抱合力增加,造成牵伸力大小波动而造成牵伸不稳定的现象。
消除简纱成形不良的措施

络 筒是 纺 部 的最 后 一 道 工 序 , 其 将 纱 头 和纱 尾
相 连接 , 卷 成 大容 量 的筒子 , 并 利用 清 纱装 置 除去 纱 线 上 的棉结 、 杂质 、 粗 细节 等疵 点 , 但 同时 , 络纱 过 程
检 查 出来 , 下 面从 设 备 工 艺 和 生产 操 作 两 方 面 介 绍 消除 这类成 形 不 良的 几项措 施 。
少磨 损 , 缩短 高合 金 钢钢 领 和钢 丝 圈走熟 期 。
[ 3 ]徐 萍 , 王伯 健. 关 于改善 钢丝 圈组 织性 能 的探析 E J ] . 纺
织器 材 , 2 0 0 8 , 3 5 ( 6 ) : 8 - 1 0 .
E 4 ]印荣 . 环 锭 纺 气 圈理 论 研 究 E D] . 上海 : 东华大 学 , 2 0 1 1 . E 5 ]冉 梅 . 钢领钢丝 圈配套使用制 约因素 的探讨 E J ] . 纺 织 器
出这些 零件 的固定 螺丝 松 动 的 , 都应 该 及 时紧 固 ; 翻
改 品种 , 号 数跨 度 大 的 , 及 时联 系相 关 人 员 , 按 工艺
3 . 2 配 置 常州航 月 HY1 UL蓝金 刚 型 钢丝 圈和 进
口布雷 克公 司 C1 UL UDR型 钢 丝 圈 , 纺制 普 通 环 锭 纺精 梳 长 绒 棉 品 种 ( 甚 至部 分 T / C J 1 4 . 6 t e x以
调 整 清洁 器 隔距 。总 之 , 夯 实设 备基 础 管理 工 作 , 为
钢 丝 圈 国产化 配套 使 用 , 提 供优 越 条件 。
3 结 语
3 . 1 常 州航 月 HY1 uL蓝 金 刚 型 钢 丝 圈 , 采 用 原 装进 口 8 0 WV 优 质合 金 钢 钢 丝 , 优 化 了 UL 圈形 和 UD R 截面 设计 , 经 过 全 自动 高 精 设 备 生 产 , 先 进 的
筒纱常见疵点成因及预防

wo8 , p ii g f q e t p o o tc e w e h e e y r n r o e d u r e s l n r u n l o r c n a t b t e n c e s a n a d g o v r m. T c n l g e o ns o r v ni g c e y, e h oo y k y p i t f p e e t n
象, 清理 后仍 频频 发生 , 该现 象往 往 以随 机形式 且 出现 。经 分 析认 为该 现象 应是 由细纱管 纱脱 圈造
纱效果及筒纱 的卷络情况 , 我们通常 以抽检的方 式对 筒纱 进 行倒 纱检 查 。在倒 纱 的过程 中有时会 发现筒纱 内有乱纱 、 小辫子纱及夹 回丝等纱疵 , 给 后道 退绕 带来 了很 大 的影 响 。我 们在 N2 C型 络 o1
c e s a tr a se k n w n e o bi g wee ito u e .I i c n i e e a a ei g a e r d c d b e l h e e y m h e d wa t , i k, d rd u l r n rd c d t s o sd r d t t v l sc n b e u e y d a- i n h r n i g b b i an fr n e a nn n o bn y r omig. x mi i g& r p i n e so o n p ie .W i d n r c s i g s o l e a o t d r t n - e a r g t n in b x a d s l r i c n i g p o e s h u d b d p e ai a n ol l , la ig s o l e d n e l o r d c l t p s o h e e y r ee t. y ce n n h u d b o e w l t e u e al y e f e s a n d fc s c
纱线主要疵点成因分析与改善措施

纱线主要疵点成因分析与改善措施对于纯棉精梳细号纱线,从危害程度和发生频次看影响布面的有害疵点主要是粗节、细节、条干不匀、飞花、棉结和异常疵点。
为切实满足客户的要求和控制质量成本,纺纱厂必须找到纺纱生产过程中形成这些疵点的原因,并采取有效的措施控制降低疵点,从而提高纱线的质量。
粗节、细节1成因常见的布面粗节长短不等:1 cm~2 cm居多,中间粗两头渐细,大多为细纱牵伸不良、牵伸区周围游离飞花附入、粗纱条干片断不匀、粗纱疵点附入、络筒清纱参数设置不当等原因造成;少部分为细纱接头不良或络筒机捻结不良造成。
细节主要是由细纱牵伸不良和络筒捻结不良造成。
2措施对于细纱牵伸不良引起的粗节、细节,可从以下四方面预防和解决:a)降低粗纱捻度,即在不增加断头的前提下尽量采用小的粗纱捻度;b)保证细纱和粗纱牵伸元件状态良好,保持适当的胶辊研磨周期、胶圈更换周期,并随时检查是否有起槽、划痕等问题,随时解决;c)保持恒定的温湿度,避免出现短时大幅度的波动;d)优化细纱工艺,主要是隔距、上销位置和摇架压力的一致性。
对于细纱纺纱过程中产生的粗节和细节,只能利用络筒清纱器切除,这样会引起清纱器切次的增加,需要特别关注捻接质量避免因捻接不良二次形成粗节和细节。
条干不匀1成因布面呈现有规律或无规律的条干阴影;主要因牵伸元件(胶辊、胶圈、罗拉)运转失常、表面毛糙凹凸、胶辊缠花纺纱及落后锭子等纺纱专件异常造成。
2措施牵伸区工艺优化、保持良好的胶辊胶圈状态;控制好单并与粗纱的号数偏差和条干均匀度,发现异常及时隔离;及时修理细纱的坏锭及异常锭,要求挡车工走巡回遇到胶辊、胶圈、罗拉等异常情况及时报告并通知相关人员处理。
在络筒机上对清纱器设置支数变异和珠链纱疵剪切和报警参数,可切除疵点并剔出有问题的管纱。
飞花1成因纺纱生产中因清洁不及时、集棉装置故障、断头急剧增加、空调温湿度异常或气流不畅等情况引起机台上、地面和空气中飞花增加并集聚,纺纱时附入到纱体中形成飞花疵点。
络筒环节对棉纱筒子染色成型的不良因素及防范措施
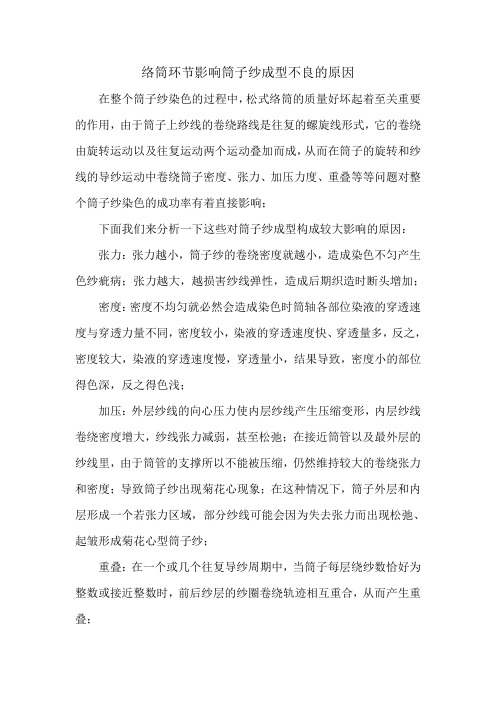
络筒环节影响筒子纱成型不良的原因
在整个筒子纱染色的过程中,松式络筒的质量好坏起着至关重要的作用,由于筒子上纱线的卷绕路线是往复的螺旋线形式,它的卷绕由旋转运动以及往复运动两个运动叠加而成,从而在筒子的旋转和纱线的导纱运动中卷绕筒子密度、张力、加压力度、重叠等等问题对整个筒子纱染色的成功率有着直接影响;
下面我们来分析一下这些对筒子纱成型构成较大影响的原因:
张力:张力越小,筒子纱的卷绕密度就越小,造成染色不匀产生色纱疵病;张力越大,越损害纱线弹性,造成后期织造时断头增加;
密度:密度不均匀就必然会造成染色时筒轴各部位染液的穿透速度与穿透力量不同,密度较小,染液的穿透速度快、穿透量多,反之,密度较大,染液的穿透速度慢,穿透量小,结果导致,密度小的部位得色深,反之得色浅;
加压:外层纱线的向心压力使内层纱线产生压缩变形,内层纱线卷绕密度增大,纱线张力减弱,甚至松弛;在接近筒管以及最外层的纱线里,由于筒管的支撑所以不能被压缩,仍然维持较大的卷绕张力和密度;导致筒子纱出现菊花心现象;在这种情况下,筒子外层和内层形成一个若张力区域,部分纱线可能会因为失去张力而出现松弛、起皱形成菊花心型筒子纱;
重叠:在一个或几个往复导纱周期中,当筒子每层绕纱数恰好为整数或接近整数时,前后纱层的纱圈卷绕轨迹相互重合,从而产生重叠;。
筒子成形不良的原因及对策

2.修复槽筒。
3.更换筒子摇架轴承。
4.校正松动摇架。
5.调节筒子摇架。
6.减少重叠卷绕。
7.使相对湿度60%以上。
8.应减少张力差异。
脱边
1.较易发生于粗支纱、易产生滑移的纱、弹性纱以及双纱。有静电。
2.槽筒罩和筒纱距离不当。
3.管纱脱圈过多。
4.管纱表面断头多。
3.筒子摇架轴承更换。
阶梯
1.槽筒有损坏。
2.槽筒罩有损坏。
3.张力过低的时候。
4.机台清洁后纱线由线路中滑出。
1.2检查破损情况并研磨修复。
3.增加张力(调刻度盘)。
4.用气做清洁时勿将纱线吹出。
细腰
1.张力过大。
2.接触压力不足。
3.筒子增量小。
1.降低纱线张力(调节张力盘)。
2.提高接触压力(增加摇架重量)。
5.管纱成形与卷绕速度不配合。
1.提高相对湿度在60%以上。
2.调节槽筒罩。
3.对脱圈采取措施。
4.改进细纱工序卷绕程序。
5.改善细纱管成形或降低卷绕速度。
条带(重叠)
1.防叠装置设定不适当。
2.接触压力过高。
3.筒子摇架回转不良。
4.管纱回潮太大。
1.改变防叠装置周期。
2.调节压力渐成器的弹簧及筒子摇架加重量以调低接触压力。
5.槽筒起动力不够。
1.检查接头动作及纱线通道,同时检查捻接器。更换清纱器。
2.调整大吸嘴限位制。
3.改变筒子摇架加压重量。
4.提高槽筒马达电压。
跨边
1.张力大小不合适。
2.槽筒有损伤。
3.筒子摇架夹头运转不良。
4.筒子摇架松动。
常见细纱疵点及产生原因

错支
粗纱用错,筒管用错,后皮辊加压失效
加强巡回检查,通知检修工处理
交于小组长统一处理
煤灰纱
室外空气浊度大,空气中的微粒进入纺纱车间
1.空调室做好恶劣天气预警工作。
严重偏心的单锭巡回中应及时拔出大小管纱记录大小并通知检修碰钢领板纱由当班处理拉去碰烂纱段方可投入下工序实锭脚回丝多造成冒纱工处理跳管单锭应及时处理拉去锭脚回丝若是纱管问题更换纱管重新生成形不良视情节在不影响络筒工序生产下投入下道使用否则须拉清不良粗纱用错筒管用错后皮辊加压失效加强巡回检查通知检修工处理交于小组长统一处室外空气浊度大空气中的微粒进入纺纱车间细纱提前落纱缩短纺纱时间
3.加快接头速度
4..及时处理锭子回丝
属锭带脱落,应拔出同带四锭管纱,集中送下工序处理。
毛羽纱
1.钢丝圈型号不当(过轻)
2.钢领不良
3.歪锭子
4.相对湿度较低
1.使用正确的钢丝圈型号
2.发现不良及时调换
3.通知维修工效正
4.控制好相对温湿度
交由小组集中,送下工序处理。
棉球(满天星)
钢丝圈磨灭
更换钢丝圈,遇到机台多锭满天星应记录,便于常日班检查钢领、钢丝圈周期。
2.细纱提前落纱,缩短纺纱时间。
按照煤灰纱污染程度分别处理
1.单锭导纱动程距皮辊边缘应大于3毫米。否则空锭,通知检修工处理。
2.及时掀起摇架、逐锭处理。
3.去除杂质。
4.更换裂损皮圈,无皮圈更换时,空锭处理。
5.空锭,通知检修工处理。
6.及时更换皮辊。
7.皮辊压力失效,钳爪位不正时,空锭通知检修工处理。
8.及时停机反馈。
筒纱成形不良原因与对策
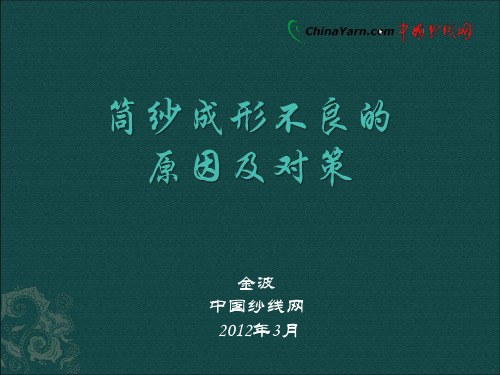
聚静电的品种容易诱发纱线缠绕槽筒,导致筒纱成型 不良。
2.2.3 一些企业使用二手自络机,如果选 择不当、把关不严,容易导致筒纱成形 不良,主要有以下原因造成:
筒纱摇架平衡压缸体,漏气、漏油; 筒纱大小夹头轴承磨损; 槽筒损伤严重; 捻结器损伤; 压力表损坏; 细纱管内孔直径与自络机插纱锭脚不匹配;
因筒纱摇架松动、夹头因轴承损坏而运转不良,导致筒 纱成形不良;
筒纱大小夹头缠绕回丝,张力盘起槽、夹花、缠回丝, 张力弹簧卡死或断裂,张力电机插座接触不良,大吸嘴 触碰筒子,插纱锭脚偏心严重等导致筒纱成形不良;
因使用劣质机配件而导致筒纱成形不良。
2.2.2 纱线缠槽筒,导致筒纱成形不良 槽筒导纱沟槽不清洁或有损伤会造成纱线缠槽筒,
2.1.7 络筒卷绕速度越高,对纸管的精度和强度 要求就越严格,否则飞筒及筒纱成形不良的问题 将大幅增加。推荐纸管的规范尺寸如下图:
2.2 设备维护保养问题带来的筒纱成形不良
2.2.1 由于设备的维护、保养不到位等原因导致的筒纱成 形不良,常见问题如下:
筒纱摇架上的平衡压油缸或气缸存在漏气、漏油现象, 连动机构不灵活、压力表破损,造成筒纱接触压力异常, 导致筒纱成形不良;
3、影响筒纱成形的美观度!
4、在整经、织造工序的高速退绕过程中, 因筒子纱线脱圈、粘连等现象导致断头多, 挡车工工作量增加,生产效率显著下降; 针织堵眼、断针量增加!
5、造成布面质量问题!
6、遭遇客户投诉甚至承受退货的巨大损失!
二、筒纱成型不良的原因
筒纱成形不良有时是一种因素造成,有时是多 种因素综合导致、有时是一种因素导致多种结果。 归纳起来,筒纱成形不良的原因大致有纸管问题、 设备维护保养问题、操作管理问题、工艺质量问题、 槽筒规格问题共五大类。下面做详细的分析:
布疵形成的原因及消除方法
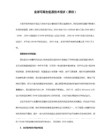
自络筒纱成形不良的原因分析
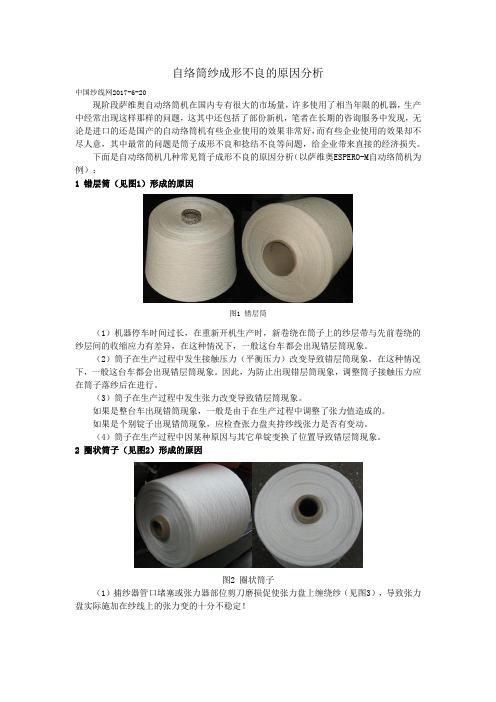
自络筒纱成形不良的原因分析中国纱线网2017-6-20现阶段萨维奥自动络筒机在国内专有很大的市场量,许多使用了相当年限的机器,生产中经常出现这样那样的问题,这其中还包括了部份新机,笔者在长期的咨询服务中发现,无论是进口的还是国产的自动络筒机有些企业使用的效果非常好,而有些企业使用的效果却不尽人意,其中最常的问题是筒子成形不良和捻结不良等问题,给企业带来直接的经济损失。
下面是自动络筒机几种常见筒子成形不良的原因分析(以萨维奥ESPERO-M自动络筒机为例):1 错层筒(见图1)形成的原因图1 错层筒(1)机器停车时间过长,在重新开机生产时,新卷绕在筒子上的纱层带与先前卷绕的纱层间的收缩应力有差异,在这种情况下,一般这台车都会出现错层筒现象。
(2)筒子在生产过程中发生接触压力(平衡压力)改变导致错层筒现象,在这种情况下,一般这台车都会出现错层筒现象。
因此,为防止出现错层筒现象,调整筒子接触压力应在筒子落纱后在进行。
(3)筒子在生产过程中发生张力改变导致错层筒现象。
如果是整台车出现错筒现象,一般是由于在生产过程中调整了张力值造成的。
如果是个别锭子出现错筒现象,应检查张力盘夹持纱线张力是否有变动。
(4)筒子在生产过程中因某种原因与其它单锭变换了位置导致错层筒现象。
2 圈状筒子(见图2)形成的原因图2 圈状筒子(1)捕纱器管口堵塞或张力器部位剪刀磨损促使张力盘上缠绕纱(见图3),导致张力盘实际施加在纱线上的张力变的十分不稳定!图3 张力盘缠纱此问题应从加强现场管理着手,经常检查和督促维修工与挡车工的维修、清洁工作!(2)由于上面(1)的问题的存在,挡车工或维修工在清洁保养时方法有误,致使张力盘固定支架严重变形(见图4),导致张力盘实际施加在纱线上的张力变小或消失!图4 张力盘固定支架变形警告!此现象还将会导致松筒、菊花芯筒、蛛网筒、乱纱层筒的发生!3 菊花芯筒纱(见图5)形成的原因当张力盘内部有纱线缠绕,应用钩刀或剪刀轻轻剔除,避免硬拉乱扯致使张力盘固定支架变形,同时做好张力盘主动与被动盘的清洁、维护工作!图5 菊花芯筒纱(1)由于纺织厂的许多不确定因素的存在,如自动络筒机配件的采购环节、人员及技术力量的不足、流动大等等,部份纺织厂对机器的维护、管理工作不到位,如张力部位从不清洁、保养,导致张力盘推杆在张力气缸内部运行受阻,致使张力盘打不开或合不上、合不实,施加在纱线上的张力无法得到保证,从而致使筒纱成形不良!张力气缸磨损严重导致漏气,气动张力功能失效,施加在纱线上的张力无法得到保证,从而致使筒纱成形不良!检查张力气缸是否磨损的方法是用肥皂水或泡泡水注入张力盘推杆处,有气泡吹出,表明此气缸或张力压杆已磨损,见图6:图6 检查张力气缸是否磨损劣质机配件无论从外形、材料、制做精度、使用寿命、使用效果等来说都很难与原厂原配件相提并论!如图7中的张力气缸制做材料是普通黄筒,制做工艺较粗糙,精度较差、张力盘器件在其内部运行不畅,易发生漏气!使用中张力值波动较大,对筒纱成形不利!其使用寿命较短!建议不要使用!图7 劣质的张力气缸优质品原材料是轴承铜或自润滑铜材料制作而成,表面光滑精致,张力盘器件在其内部运行通畅,使用寿命长!张力稳定可靠!采用轴承铜制做的张力气动器件,见图8:图8 轴承铜制做的张力气动器件(2)错误的筒倒筒方式易发生筒纱成形不良,ESPERO-M机器与SMARO机器自动络筒机筒倒筒装置设计非常不合理,此种筒倒筒装置不但会损伤纱线通道的机部件,还会对纱线质量指标及筒子成形带来不良的后果!如图9中箭头所指至处的部件易发生磨损!纱线质量指标受损!张力易时大时小,波动极大!极易发生筒子成形不良!!!正确的倒筒方法是拆下气圈破裂器,在此部位安装陶瓷环,纱线从陶瓷环中间穿过!筒纱在倒筒卷绕过程中:SMARO机型;张力或卷绕速度应低于管纱设定!(分组设定)ESPERO-M或SPERO-M机型卷绕速度应低于管纱设定!(分组设定)警告!筒子纱线运行在卷绕过程中,张力时有时无、时大时小波动大!将严重影响筒子成形!!!(金波)。
细纱成形不良的种类和消除方法

细纱成形不良的种类和消除方法良好的细纱卷绕成形应符合卷绕紧密、层次清晰、便于退绕等要求,对其管纱的卷装容量应尽量大一些,以减少细纱工序落纱和后加工工序的换管次数,提高设备生产率和劳动生产率。
但实际生产过程中,往往由于机械状态不良及操作管理不严,而产生成形不良的管纱,下面列举3种主要类型及消除方法。
1冒头、冒脚纱原因:①落纱时间掌握得不好;②钢领板高低不平;③钢领板位置过低;④筒管天眼大小不一致,造成筒管高低不一;⑤小纱时跳筒管(落纱时筒管未插紧、坏筒管、锭杆上绕有回丝、锭子摇头或麻杆);⑥钢领起浮;⑦筒管插得过紧,落纱时将纱拔冒等。
消除方法:①根据冒头、冒脚情况,严格掌握落纱时间;②校正钢领板的起始位置及水平;③清除锭杆上的回丝;④加强对筒管的维修及管理等。
2葫芦纱、笔杆纱葫芦纱产生原因:①倒摇钢领板;②成形齿轮撑爪失灵;③成形凸轮磨灭过多;④钢领板升降柱套筒飞花阻塞;⑤钢领板升降顿挫;⑥由空锭(空粗纱、断锭带、断胶圈、坏胶辊、试验室拔纱取样及其他零件损坏未修理等)一段时间后再接头等因素而造成。
笔杆纱主要是某一锭子断头特别多而形成的。
消除方法:①可根据所造成的原因加强机械保养维修;②值车工严格执行操作规程,注意机台清洁工作。
3磨钢领纱磨钢领纱又称胖纱或大肚子纱,由于管纱与钢领摩擦,纱线被磨损或断裂,给后加工带来很大困难。
其产生原因:①管纱成形过大或成形齿轮选用不当;②歪锭子或跳筒管;③成形齿轮撑爪动作失灵;④钢领板升降柱轧煞;⑤弱捻纱;⑥倒摇钢领板以及个别纱锭钢丝圈用错(太轻)等。
消除方法:严格控制管纱成形使之与钢领大小相适应,一般管纱直径应小于钢领直径3mm。
消除产生跳筒管、弱捻纱的因素,执行操作法;加强巡回检修,提高机台平修质量。
本文摘自变宝网-废金属_废塑料_废纸_废品回收_再生资源B2B交易平台网站;变宝网官网:/?cjq买卖废品废料,再生料就上变宝网,什么废料都有!。
筒纱成形不良原因与对策

筒纱摇架平衡压缸体,漏气、漏油; 筒纱大小夹头轴承磨损; 槽筒损伤严重; 捻结器损伤; 压力表损坏; 细纱管内孔直径与自络机插纱锭脚不匹配;
张力盘损伤; 张力电机损伤; 槽筒与筒子夹头刹车失灵; 纱线通道变形生锈; 机部件损坏、变形、缺件、锈死、磨损、缠回丝、 积尘等; 电子清纱器严重老化,不切、漏切、乱切; 电器元件老化严重; 大吸嘴触碰筒子;
纱线较滑、回潮较小、单锭在打结过程中大吸嘴与筒子 间隔过小时,容易产生乱纱层。可适当加大筒子接触压 力和空气湿度(65%-72%间),优化大吸嘴与筒子的平 行间隔与负压。 纺纱张力在某时刻,短时间段随机变小或消失时,易产 生乱纱层。需维修、清洁张力系统、加强现场管理。 筒子摇架夹头轴承运转不良易产生乱纱层,可维修或清 洁筒子摇架夹头。 摩擦系数高、脆性纤维及易积累静电的纱线容易产生乱 纱层,可优化车速、张力与摇架压力,适当加大生产环 境空气湿度。 筒子卷绕速度过高易产生乱纱层,可适当降低络筒速度。
2.1 纸管问题带来的成形不良
主要有纸管不标准、纸管质量较差及纸管管 理不当造成的,可分为以下几种情况: 2.1.1 纸管过短,带来的后果是: 易导致飞筒现象; 易导致筒子刹车不灵敏,筒子中易夹带纱头, 大吸嘴找头成功率降低,生产效率下降; 易产生蛛网纱筒子; 易产生滑层带筒子; 筒子在刹车过程中,表面易被磨损; 筒子在高速退绕过程中断头率增加。
2.1.2 纸管过长,带来的后果是:
筒子大夹头刹车时,性能受影响。在一定程度上, 影响生产效率! 易导致筒纱纱线层面偏离纸管中心位臵,影响筒 子外观成形; 在个别品牌络筒机上,筒纱纸管易磨损、烧焦、 时而发生飞筒现象!
针织面料常见疵点及原因分析大全

针织面料常见疵点及原因分析大全针织面料常见疵点及原因分析01漏针在编织过程中,织针没有勾到毛纱或勾到毛纱后又脱出针钩而形成线圈脱散,在布面出现垂直的条痕及小孔的现象。
原因及处理方法:(1)针的原因,针钩或针舌坏、针舌长短不一、针头大小不一等。
(换针)(2)纱嘴位置不好,离针舌太高或太低、过里或过外。
(调纱嘴)(3)针槽不干净或有异物,针槽太松或太紧导致织针不能正常工作。
(清洁、修理针槽)(4)沉降片三角与三角相对位置不正确,退圈时,发生织针穿过旧线圈的现象。
(调整沉降三角与织针三角的相对位置)(5)给纱张力过小或纱过硬张力大。
(调整输线量或弯纱深度,纱线重新过蜡)卷布张力不均匀或太松。
(调整卷布张力)双面织物还分里漏针、外漏针,针盘上织针的漏针为里漏针,针筒上织针的漏针为外漏针。
02断针一条垂直的坑或较连续的孔。
原因及处理方法:(1)织针的原因,针太旧,针钩、针舌坏,或是用错针。
(换针)(2)个别针槽紧,织针运动困难。
(修理针槽)(3)纱支问题,粗纱、大纱结或乱纱卡住针钩等。
(4)布架太紧,卷布张力过大。
(调整卷布张力)(5)纱嘴位置不好。
(调纱嘴位置)03撞针在编织过程中针踵与三角组之间相互碰撞的现象,会损伤针筒(针盘)、织针等,撞针损失巨大,所以在生产中应小心避免。
原因分析:(1)缺油、车速太高;(2)上下针槽末对准,针门关不严,螺丝松动等;(3)针槽坏,棱角起毛,或针槽内有断针脚;(4)纱嘴位置错误,或探布针伸入针槽且失灵;(5)纱线张力突然增大;(6)棱角之间接缝过大,过道太窄或上下棱角位置对位不好,上下织针相碰;(7)脱布没能自停,布上浮造成撞针。
04花针成圈过程中,新旧线圈重叠在一起形成一个线圈,在布面上出现连续或不连续小坑,纱乱等,花针主要是个别织针在编织成圈过程中退圈不足或脱圈不足(包头)造成。
原因分析:(1)针的原因:针舌歪,长短不一,针发毛等;(2)棱角位置不好,压针不足等设备原因;(3)针叶太松,缺损等(增加槽壁压力)(4)织物牵拉力过小,退圈不足等;(5)纱线不均匀,粗纱脱不出;另:织针损坏而形成的花针称直花针,无规则的花针称为散花针。
筒纱成形问题的建议解决方法

筒纱成形问题的建议解决方法成形问题成因解决方法筒子大小头凸出1) 槽筒圈数太多2) 纱线张力太大3) 筒子架太重1) 采用圈数较少的槽筒2) 减少张力/降低车速3) 减少筒子架重量/增加平衡压力菊花芯1) 纱线张力和筒子架重量不合适2) 锥度增加太大3) 筒管不好/筒管小头太软4) 筒子架大头抬得太高1) 减小纱线张力/筒子架重量2) 减小锥度增加量3) 避免使用不合格的筒管4) 检查筒子架与槽筒的平行乱纱1) 筒子刹车没有工作2) 大吸咀与筒子接触了3) 筒子架重量太轻4) 接头后的加速度太大1) 检查气囊及刹车块是否正常2) 按照说明书调节大吸咀与筒纱表面的平行及距离3) 减小平衡压力4) 减小加速度网纱,攀头首先要分析网纱是出现在打结过程中还是正常卷绕情况下A) 如果是正常卷绕过程中出现的:1) 纱线张力有变化2) 车间湿度太低B) 如果出现在打结过程中:打结前:-筒子没有刹车A)1) 检查张力装置的功能是否正常,检查张力,检查锭脚的居中,booster的功能2) 车间湿度持在 60 到 70 %B)1) 检查气囊及刹车块是否正常2) 清洁大吸咀,保证内表面光滑-减小加速度-大吸臂里面有回丝或积尘打结后:- 加速度不正确- Booster 功能不正常检查booster的功能大头或小头有绕纱1) 电清切纱后,纱头飘向两头,因此大吸咀吸到了双纱2) 筒子架小头的防止绕回丝的铁片变形或缺失3) 夹头上绕回丝1) 用直径180mm的筒子调节大吸咀与筒纱表面的平行及距离,带梳子的距离为6-8mm,不带梳子的距离为3-5mm.2) 检查防止绕回丝的铁片是否正常或完好3) 清理大小夹头上的回丝带状纱1) 筒子直径参数不正确2) 防带状纱设定有问题3) 槽筒圈数太少1) 在功能菜单中查看筒纱直径参数2) 按照说明书调节防带状纱的设定缠纱1) 湿度太高或太低2) 电脑或电清里面的防缠纱功能没打开1) 车间湿度持在 60 到 70 %,防止由于湿度太低造成的弱节,或湿度太大造成的粘连2) 打开电脑或电清里面的防缠纱功能(调节防缠纱的灵敏度)筒纱中间凹陷1) 纱线张力太大1) 减小张力/车速。
- 1、下载文档前请自行甄别文档内容的完整性,平台不提供额外的编辑、内容补充、找答案等附加服务。
- 2、"仅部分预览"的文档,不可在线预览部分如存在完整性等问题,可反馈申请退款(可完整预览的文档不适用该条件!)。
- 3、如文档侵犯您的权益,请联系客服反馈,我们会尽快为您处理(人工客服工作时间:9:00-18:30)。
14类筒纱成型不良的原因分析1、重叠筒子(1)什么是重叠筒子重叠卷绕就是纱在同一位置或附近,落在一起卷绕,形成条带卷绕。
(2)危害重叠筒子对后道工序退绕过程中产生的后果:A、因脱圈导致高速退绕中断头!B、因牵扯导致高速退绕中断头(粘连)(3)自络机通常防叠方法为下列几种:方法一、通常防叠机构是通过减少或增加槽筒的旋转速度来分散可能的重叠卷绕,(槽筒电机的开与关比时间差)借此造成槽筒和筒子滑移使纱减少重叠。
常见机型有村田7-2、7-5、7-7、21C、赐来福138、238、338、络利安、青岛SMARO等机型!方法二、此防叠机构是通过一微小左右摆动的筒子摇架幅度,即筒子与槽筒间的接触面压力变化幅度,由此造成槽筒和筒子滑移使纱减少重叠。
常见机型有早期萨维奥、青岛ESPERO 方法三、此防叠机构是通过程控变化槽筒沟槽圈数来实现筒子防叠的。
使用普通槽筒时,当筒子直径接近槽筒直径的倍数时最易发生筒子重叠现象,使用沟槽圈数不同的槽筒其筒子发生重叠现象时的直径,是有一定差异的,其变圈槽筒正是利用了其筒子发生重叠带时的直径不同,有效的避开了重叠带,通常使用2圈的槽筒比使用2.5圈的槽筒产生重叠带时的直径要小的多,常见机型有村田21C。
使用变圈槽筒生产的筒子有明显的变圈转换干扰痕迹.(4)重叠筒子的成因与解决方法槽筒直径与筒子直径形成整数比时最易发生重叠卷绕,自络机启用以上防叠机构时,正常情况下发生重叠卷绕筒子的概率较低,当筒子卷绕条件发生异常时,筒子出现重叠卷绕现象后,通常的处理方法是:(1、优化槽筒的加速与减速比(防叠干绕设定);2、设当减小筒子与槽筒的接触压力(加大摇架平衡气压,摇架平衡气压与筒子与槽筒的接触压力呈反比;3、筒子摇架或夹头运转不良;4、超大直径卷装的筒子,有可能造成重叠筒子。
5、细纱管的回潮或络筒生产环境湿度太大;6、稍稍提高卷绕张力,对重叠减少有微小作用。
2、菊花芯筒子(1)什么是菊花芯筒子在卷装头部接近筒管的区域内,纱层被挤压而造成“菊花芯”。
其原因是外层纱线以较大的压力作用在内层纱线上而造成。
(2)产生菊花芯筒子的几个因素。
纱线特性较松软的品种、纱线支数较粗的品种、纱线回潮较高时、纱线弹性较高时、转杯纺纱、毛防纱等更易、产生菊花芯(3)菊花芯筒子的成因及解决方法A、张力偏小,接触压不合适时,易发生,需优化以上参数;B、筒管偏心严重易发生,更换合格筒管;C、筒管与槽筒接触面不良,请效正筒管小头与槽筒间的相对位置。
(筒管与槽筒接触面左侧面之间有一定间隙卷装后的筒子芯部会较软);D、卷绕时的增量过大也会导致菊花芯筒子。
3、凸边筒子(1)什么是凸边筒子?凸边筒子的成因是随着筒子的卷绕直径加大,筒子对槽筒的相应接触压力加大,纱的卷绕密度也加大,致使筒子的里层纱线受压缩,从边侧挤压凸出。
(2)凸边筒子的成因及解决方法A、粗支纱、双股纱、弹性纱、膨体纱易发生此种成形不良现象;B、对以上弹性纱线而言,张力过大、接触压过大,易发生凸边筒子;C、可尝试使用张力和接触压渐减装置解决。
4、乱纱层筒子(1) 乱纱层形成及危害筒纱在高速卷绕过程中纱层之间发生轻微滑移,致使乱纱层的发生。
此种纱层之间的轻微滑移现象,有些时侯表现为筒子纱线在高速退绕过程中发生纱线粘连状态,从而断头。
(2)乱纱层的成因及解决方法A、吸风静压过大,可能导致乱纱层筒子。
适当降低静压,无吸风电机变频器的机器,建议加装!B、打结时大吸嘴碰触筒子。
在小头直径在120毫米时,调整大吸嘴与筒子间隔距离为5-6毫米C、打结动作连续反复多次。
调整好捻结质量,做好单锭维护工作!D、筒子接触压力太低。
适当加大筒子接触压力(注:平衡气压的大小与筒子接触压力呈反比)E、重叠纱层松脱。
调整防叠电机ON与OFF时间比F、纱线较滑、回潮较小时、打结时大吸嘴与筒子间隔过小时易发生。
适当加大筒子接触压力、空气湿度(65%-70%),优化大吸嘴与筒子平行间隔与负压!G、张力在某时刻短时间意外骤变小或消失。
维修、清洁、清理张力系统。
加强现场管理!H、筒子摇架夹头轴承运转不良。
维修、清洁筒子摇架夹头!I、具有高磨擦系数的纱线、脆性纤维及产生高静电积累的纱线易产生问题。
优化车速、张力与摇架压力,适当加大生产环境空气湿度!J、过高的筒子卷绕速度。
适当降低络筒速度!5、跨边(攀头)筒子(1)什么是跨边(攀头)筒子在筒子的左侧或右侧端面有纱线甩出。
见图(2)跨边(攀头)筒子成因及解决办法A、筒子接触压力过小,造成槽筒与卷装之间产生过大的滑移。
适当增大筒子接触压力B、纸管严重偏心或纸管与槽筒接触面角度过大,导致筒子运行过程中过大的跳动。
使用标准质量的纸管,调正好槽筒接触面。
C、槽筒沟槽回头点损伤或不光滑。
沟槽内有锈点、棉蜡等。
修复或更换槽筒D、纱线张力过过偏离标准设定,时有时无、时大时小。
按单纱强力的8%-12%设定强力值,找出张力波动的原因!E、筒子摇架夹头运转不良,或摇架松动。
更换筒子摇架夹头轴承,修复摇架。
F、重叠卷绕造成。
优化槽筒防叠设定参数。
G、自络生产环境空气湿度太小。
(尤其对麻和腈纶)适当加大自络生产环境空气湿度K、特别滑的纱线在筒子卷绕过成中易产生。
优化车速、摇架压力、张力与自络生产环境空气湿度。
6、脱边(滑边)筒子(1)什么是脱边(滑边)筒子?在管纱卷绕结束或纱线断头时,纱线落在筒子左侧端面上又卷入筒子形成(特别是张力盘至电清检测头的那一段断头)多发于村田7-2机中脱边(滑边)筒子多发生在单锭打结过程中造成!(2)脱边(滑边)筒子成因及解决办法A、细纱管纱线突然崩断,如管纱成型不良、脱圈纱存在等。
大吸嘴内部堵塞。
B、自络生产环境空气湿度太小,易产生静电。
单锭小夹头处安装有防脱边装置,有助于减少脱边现象的发生。
C、粗支纱、弹性纱、易出现。
筒子、槽筒刹车不灵敏,电子清纱器切刀不快时易发生。
(村田7-2机易发生此种情况)D、吸风负压太低,或大吸嘴与筒子间隔距离太大。
当以上问题存在时,过高的卷绕速度使问题更严重。
7、圈条边筒子(1)什么是圈状边筒子纱线在卷绕过程中某一时间段,张力异常变小、不稳定或消失所致。
脱圈筒子易在高速退绕过程中发生筒纱脱圈而产生断头。
(2)圈状边筒子的成因及解决办法纱线在卷绕过程中某一时间段,张力异常变小不稳定或消失所致。
A、张力盘有飞花、异物积累过多使张力盘随机或未夹持住纱线。
B、张力系统有故障。
(请及时做好单锭的清洁保养工作)C、重叠卷绕导致。
优化槽筒电机的ON与OFF的时间比防叠参数。
8、葫芦筒子(1)什么是葫芦筒子?筒子端面中间部位下沉,两头翘的成形简称葫芦筒子。
(2)葫芦筒子的成因分析及解决办法:A、张力过大B、筒子接触压力不足时易发生。
C、适当增加纱线卷绕张力与筒子接触压力D、葫芦筒子在高速退绕过程中易发生纱线粘连而断头!9、腰带筒子(1)什么是腰带筒子?表面有类似腰带状的纱线隆起的筒子就是腰带筒子。
(2)腰带筒子成因及解决办法A、腰带筒子成因:通常情况下是由槽筒沟槽内部毛刺、棉蜡、锈点、槽筒防护罩边侧起槽等形成;B、腰带状筒子易使筒子纱线在高速退绕过程中发生脱圈或断头。
10、年轮筒子原因分析(1)什么是年轮筒子?筒子右侧或左侧端面有类似圈状的筒子。
(2)年轮筒子的危害易使高速退绕过程中的纱线发生断头或脱圈。
(3)年轮筒子的成因及解决办法A、筒子在卷绕过成中,纱线张力时有时无、忽大忽小行成。
B、管纱成形不良。
C、插纱锭脚严重偏离气圈破裂器中心,张力波动大。
D、纱线因故未导入张力器内。
11、筒子手感过硬的筒子(1)手感过硬的筒子(硬的向石头)A、张力非常大时,筒子外观形态的表现之一:张力过大的筒子在卷绕过程中,目视筒子端面线条是曲线!正常的张力目视筒子端面线条应是直线。
B、张力非常大时,筒子外观形态的表现之二:张力过大的筒子在卷绕过程中,特别是换管卷绕初期纱层厚度在大约15毫米左右易发生攀纱现象。
(2)筒子过硬的成因及解决办法A、除了纱体性质较硬的筒子外,手感过硬的筒子往往是张力、接触压过大的表现。
B、筒子手感过硬的筒子由于纱线密度过大,纱层之间的内应力也相应加大,纱线处于绷紧疲劳状态,筒子在存放、震动、运输等过程中纱线强力易受损,易使筒子在高速退绕过程中发生不明原因的断头、纱线粘连可能。
12、筒子手感过软的筒子(1)筒子过软的筒子(手感筒子软的象棉花)手感过软的筒子由于纱线密度过小,筒子外观显的蓬松,筒子在高速退绕过程中易发生脱圈断头的可能。
(2)筒子过软的成因与危害。
A、手感过软的筒子往往是张力、接触压过小的表现。
B、手感过软的筒子在包装、存储、运输过程中易发生成形突变的可能。
13、手感小头软、大头硬的筒子(1)在相同的生产工艺参数设定下,使用2.5圈沟槽的槽筒生产出来的筒子纱线卷绕密度,要比使用2圈沟槽的槽筒生产出来的筒子纱线卷绕密度大,当然手感硬度也相应大许多。
手感筒子小头软的象棉花,大头硬的象石头。
(2)使用2.5圈槽筒,其生产时的纱线张力也相应的要比使用2圈槽筒时的张力要小。
(正常情况下)(3)使用2.5圈槽筒生产时,因故导致纱线卷绕张力偏大、致使筒子大头纱线卷绕密度过大,大头处纱层之间的内应力也相应加大,纱线处于绷紧疲劳状态,筒子在存放、震动、运输等过程中纱线强力易受损,易使筒子在高速退绕过程中发生不明原因的断头、纱线粘连可能。
(4)使用2.5圈槽筒生产时,因故导致张力偏大,筒子手感硬度象石头状况时,生产脆性纱线时,如粘胶、粘棉、高支纱和筒子直径较大时易发生筒子大头处纱线磨损、磨断的可能。
(5)使用2圈槽筒生产出来的筒子,手感在筒子整个端面其硬度较为均匀。
(密度)14、纱线缠槽筒纱线在卷绕过程中绕槽筒的成因及解决办法A、槽筒导纱沟槽不清洁或有损伤;B、自络机处在恶劣的筒纱加湿环境下生产易发生粘性纱线;回潮高的纱线及生产易产生高静电积累的品种易发生绕槽筒的概率。
四、筒纱断头多的原因分析1、细纱管纱有弱捻纱,筒子有在高速退绕中发生断头的可能2、竹节纱易发生筒子在高速退绕中有发生断头的可能3、捻结质量有问题,筒子有在高速退绕中发生断头的可能4、纤维特别短的纱线,筒子有在高速退绕中发生断头的可能5、发生重叠筒子时,筒子在高速退绕中发生断头的可能6、因机械状况欠佳或工艺设定错误导致筒子乱纱层、磨损筒、脱圈、粘连、太硬或太软的筒子、7、细纱管纱有太多的小细节,筒子有在高速退绕中发生断头的可能8、过高的自络卷装速度筒子有在高速退绕中发生断头的可能9、因电清问题漏切的,筒子有在高速退绕中发生断头的可能10、因筒子内部附入的飞花、纱头、纽结,筒子在高速退绕中有发生断头的可能11、因挡车工操作失误,筒子有在高速退绕中发生断头的可能12、因野蛮搬运、包装,筒子有在高速退绕中发生断头的可能13、发生攀头筒子时,筒子有在高速退绕中发生断头的可能14、因筒子加湿过度,筒子有在高速退绕中发生断头的可能15、高捻度的纱线生产的筒子,在高速退绕中有发生断头的可能16、因细纱单纱强力太低,筒子有在高速退绕中发生断头的可能五、筒纱中有回丝的原因分析1、筒子夹头或槽筒刹车不及时或失灵,有发生筒子中夹带回丝的可能!2、捕纱器管口堵塞、大小吸嘴堵塞,有发生筒子中夹带回丝的可能!3、因挡车工操作失误,筒子有发生筒子中夹带回丝的能!4、因吸风负压过大或过小,筒子有发生筒子中夹带回丝的可能!5、因电子清纱器老化、故障,筒子有发生筒子中夹带回丝的可能!6、因捻结器剪刀磨损,筒子有发生筒子中夹带回丝的可能!六、二手自络筒对筒纱成型的不利影响二手车存在很多不确定因数,通常原先的厂家是因为自络存在众多这样那样的问题,被迫转让的。