闪光对焊的基本原理及方法和工艺
钢筋闪光对焊
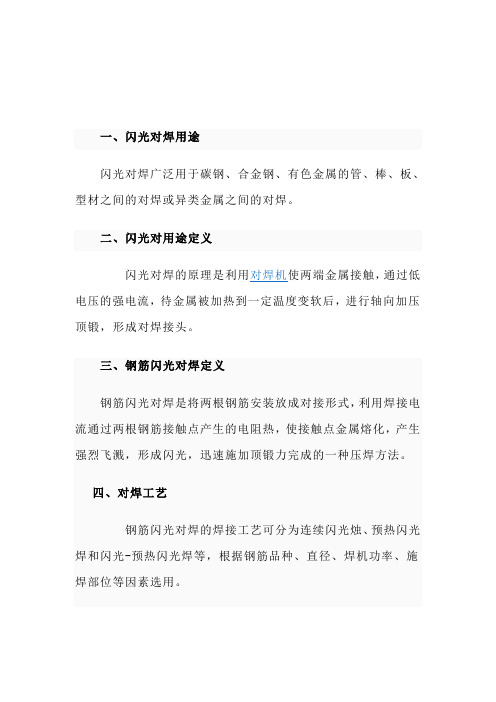
一、闪光对焊用途闪光对焊广泛用于碳钢、合金钢、有色金属的管、棒、板、型材之间的对焊或异类金属之间的对焊。
二、闪光对用途定义闪光对焊的原理是利用对焊机使两端金属接触,通过低电压的强电流,待金属被加热到一定温度变软后,进行轴向加压顶锻,形成对焊接头。
三、钢筋闪光对焊定义钢筋闪光对焊是将两根钢筋安装放成对接形式,利用焊接电流通过两根钢筋接触点产生的电阻热,使接触点金属熔化,产生强烈飞溅,形成闪光,迅速施加顶锻力完成的一种压焊方法。
四、对焊工艺钢筋闪光对焊的焊接工艺可分为连续闪光烛、预热闪光焊和闪光-预热闪光焊等,根据钢筋品种、直径、焊机功率、施焊部位等因素选用。
1、连续闪光对焊连续闪光对焊的工艺过程包括:连续闪光和顶锻过程。
施焊时,先闭合一次电路,使两根钢筋端面轻微接触,此时端面的间隙中即喷射出火花般熔化的金属微粒---闪光,接着徐徐移动钢筋使两端面仍保持轻微接触,形成连接闪光。
当闪光到预定的长度,使钢筋端头加热到将近熔点时,就以一定的压力迅速进行顶锻。
先带电顶锻,再元电顶锻到一定长度,焊接接头即告完成。
2、预热闪光对焊预热闪光对焊是在连续闪光焊前增加一次预热过程,以扩大焊接热影响区。
其工艺过程包括:预热、闪光和顶锻过程。
施焊时先闭合电源,然后使两根钢筋端面交替地接触和分开,这时钢筋端面的间隙中发出断续的闪光,而形成预热过程。
当钢筋达到预热温主后进入闪光阶段,附后顶锻而成。
3、闪光-预热闪光焊闪光-预热闪光焊是在预热闪光焊前加一次闪光过程,目的是使不平整的钢筋端面烧化平整,使预热均匀。
其工艺过程包括:一次闪光、预热、二次闪光及顶锻过程。
施焊时首先连续闪光,使钢筋端部闪平,然后同预热闪光焊。
编辑本段五、闪光对焊原理闪光对焊工艺常用的连续闪光焊、预热闪光焊和闪光-预热-闪光焊。
对Ⅳ级钢筋有时在焊接后还进行通电热处理。
闪光对焊可分为连续闪光对焊和预热闪光对焊。
连续闪光对焊主要有两个主要阶段组成:闪光阶段和顶锻阶段。
闪光对焊

闪光对焊技术交底定义:电阻焊件装配成对接接头,接通电源,并使其端面逐渐移近达到局部接触,利用电阻热加热这些接触点(产生闪光),使端面金属熔化,直至端部在一定深度范围内达到预定温度时,迅速施加顶锻力完成焊接的方法。
一、闪光对焊用途二、闪光对用途定义三、钢筋闪光对焊定义四、对焊工艺1、连续闪光对焊2、预热闪光对焊3、闪光-预热闪光焊五、闪光对焊原理六、见证取样一、闪光对焊用途闪光对焊广泛用于碳钢、合金钢、有色金属的管、棒、板、型材之间的对焊或异类金属之间的对焊。
二、闪光对用途定义闪光对焊的原理是利用对焊机使两端金属接触,通过低电压的强电流,待金属被加热到一定温度变软后,进行轴向加压顶锻,形成对焊接头。
三、钢筋闪光对焊定义钢筋闪光对焊是将两根钢筋安装放成对接形式,利用焊接电流通过两根钢筋接触点产生的电阻热,使接触点金属熔化,产生强烈飞溅,形成闪光,迅速施加顶锻力完成的一种压焊方法。
四、对焊工艺钢筋闪光对焊的焊接工艺可分为连续闪光烛、预热闪光焊和闪光-预热闪光焊等,根据钢筋品种、直径、焊机功率、施焊部位等因素选用。
1、连续闪光对焊连续闪光对焊的工艺过程包括:连续闪光和顶锻过程。
施焊时,先闭合一次电路,使两根钢筋端面轻微接触,此时端面的间隙中即喷射出火花般熔化的金属微粒---闪光,接着徐徐移动钢筋使两端面仍保持轻微接触,形成连接闪兴。
当闪光到预定的长度,使钢筋端头加热到将近熔点时,就以一定的压力迅速进行顶锻。
先带电顶锻,再元电顶锻到一定长度,焊接接头即告完成。
2、预热闪光对焊预热闪光对焊是在连续闪光焊前增加一次预热过程,以扩大焊接热影响区。
其工艺过程包括:预热、闪光和顶锻过程。
施焊时先闭合电源,然后使两根钢筋端面交替地接触和分开,这时钢筋端面的间隙中发出断续的闪光,而形成预热过程。
当钢筋达到预热温主后进入闪光阶段,附后顶锻而成。
3、闪光-预热闪光焊闪光-预热闪光焊是在预热闪光焊前加一次闪光过程,目的是使不平整的钢筋端面烧化平整,使预热均匀。
U对焊机N系列闪光闪光对焊的主要焊接工艺及原理

U对焊机N 系列闪光闪光对焊的主要焊接工艺及原理:1.焊接电极加紧工件,在工件尚未完全接触时,开始闪光。
2.接下来,焊接电极夹紧的工件缓慢接近,随着电流密度的增加,工件间接触处开始熔化,同时有部分金属熔液溢出,形成初始的对焊节点。
3.焊接区域变得越来越热,对焊的速度也随着加速。
4.闪光和飞溅使两个接触面完全焊接在一起。
5.最后再利用高压进行顶锻,切断电流,焊接完成。
主要应用领域:1.各种餐具,厨房和餐具刀具的焊接;2.自行车,摩托车,汽车车圈,及其他金属环的对焊;3.各种金属丝,金属带,铁棒,建筑用钢筋对焊;4.各种圆管,方管的“L”形与“T”形焊接;5.窗框与门框的对角焊接。
主要技术参数:参数额度功率额度电压额定频率最大短路电流负载持续率最大加紧力最大顶锻力冷却水流量平均重量外形尺寸型号UN-50 50KVA 380V/420V50/60Hz19000A50% 4000N 2000N 150L/H350Kg 100*90*150CMUN-75 75KVA 380V/420V50/60Hz24000A50% 6500N 3000N 150L/H450Kg 100*90*150CMUN-100 100KV A 380V/420V50/60Hz28000A50% 6500N 3000N 150L/H550Kg 100*90*150CMUN-150 150KV A 380V/420V50/60Hz32000A50% 8500N 4000N 300L/H1200Kg140*100*170CMUN-200 200KV A 380V/420V50/60Hz37000A50% 8500N 4000N 300L/H1400Kg140*100*170CMUN Series Pneumatic Flash Butt Welder。
闪光对焊机工作原理

闪光对焊机工作原理
闪光对焊机是一种利用激光或者弧光的瞬间高温作用将接头部分迅速加热并连接在一起的焊接设备。
其工作原理如下:
1. 准备工作:将待焊接的两个金属接头部分准备好,确保表面干净和平整。
2. 瞬间高温:闪光对焊机通过激光或者弧光产生一股高温瞬时热能,将焊点部分暴露在高温中。
这个过程一般只需要极短的时间,通常在毫秒级别。
3. 熔化和热工学效应:高温作用下,金属接头部分迅速熔化并形成熔池。
熔池内部的金属通过热传导迅速扩散,将相邻的金属接头部分加热至接近熔点。
4. 压力和接合:在高温下,闪光对焊机施加一定的压力,使得熔池内部的金属接头部分贴合在一起。
压力的运用有助于消除气体和杂质,同时也有助于提高焊接质量。
5. 冷却和固化:在熔池形成后,闪光对焊机停止加热并保持压力,等待熔池自然冷却和固化。
这个过程可以保证焊接接头部分具有良好的强度和密封性。
闪光对焊机工作原理的关键在于瞬间高温的作用,将金属接头部分迅速加热至熔点,然后通过压力和冷却使其接合成一体。
此方法具有快速、高效、高质量的特点,广泛应用于工业生产中的焊接工艺。
闪光对焊施工工艺处理标准规定
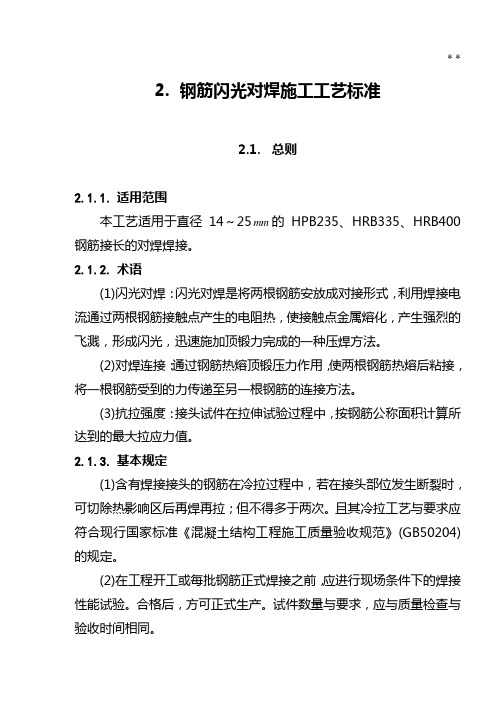
2.钢筋闪光对焊施工工艺标准2.1.总则2.1.1.适用范围本工艺适用于直径14~25mm的HPB235、HRB335、HRB400钢筋接长的对焊焊接。
2.1.2.术语(1)闪光对焊:闪光对焊是将两根钢筋安放成对接形式,利用焊接电流通过两根钢筋接触点产生的电阻热,使接触点金属熔化,产生强烈的飞溅,形成闪光,迅速施加顶锻力完成的一种压焊方法。
(2)对焊连接:通过钢筋热熔顶锻压力作用,使两根钢筋热熔后粘接,将一根钢筋受到的力传递至另一根钢筋的连接方法。
(3)抗拉强度:接头试件在拉伸试验过程中,按钢筋公称面积计算所达到的最大拉应力值。
2.1.3.基本规定(1)含有焊接接头的钢筋在冷拉过程中,若在接头部位发生断裂时,可切除热影响区后再焊再拉;但不得多于两次。
且其冷拉工艺与要求应符合现行国家标准《混凝土结构工程施工质量验收规范》(GB50204)的规定。
(2)在工程开工或每批钢筋正式焊接之前,应进行现场条件下的焊接性能试验。
合格后,方可正式生产。
试件数量与要求,应与质量检查与验收时间相同。
(3)钢筋焊接施工之前,应清除钢筋或钢板焊接部位和与电极接触的钢筋表面上的锈斑、油污、杂物等;当钢筋端部有弯折、扭曲时,应予以矫直或切除。
(4)进行闪光对焊时,应随时观察电源电压的波动情况。
当电源电压下降大于5%或小于8%时,应提高焊接变压器级数;当大于或等于8%时,不得进行焊接。
(5)焊机应经常维护保养和定期检修,确保正常使用。
(6)对从事钢筋焊接施工的班组及有关人员应经常进行安全生产教育,执行现行国家标准《焊接与切割安全》GB9448中有关规定,并应执行和实施安全技术措施,加强焊工的劳动保护,防止发生烧伤、触电、火灾、爆炸以及烧坏焊接设备等事故。
(7)钢筋连接件的混凝土保护层厚度宜符合《混凝土结构工程施工质量验收规范》(GB50204)中,关于钢筋混凝土保护层最小厚度的规定,且不得小于15mm,连接件之间的横向净距不宜小于25mm。
闪光对焊机介绍

闪光对焊机闪光对焊是广泛用于钢筋纵向连接及预应力钢筋与螺丝端杆的焊接。
钢筋闪光对焊的原理是利用对焊机使两端钢筋接触,通过低电压的强电流,待钢筋被加热到一定温度变软后,进行轴向加压顶锻,形成对焊接头。
钢筋闪光对焊工艺常用的连续闪光焊、预热闪光焊和闪光-预热-闪光焊。
对Ⅳ级钢筋有时在焊接后还进行通电热处理。
第一部分:基本分类对焊分为电阻对焊和闪光对焊两种。
1.电阻对焊电阻对焊是将两工件端面始终压紧,利用电阻热加热至塑性状态,然后迅速施加顶锻压力(或不加顶锻压力只保持焊接时压力)完成焊接的方法。
一、电阻对焊的电阻和加热对焊时的总电阻可用下式表示:R=2Rω+RC+2Reω式中Rω--一个工件导电部分的内部电阻(Ω);Rc--两工件间的接触电阻(Ω);Rω--工件与电极间的接触电阻(Ω);工件与电极之间的接触电阻由于阻值小,且离接合面较远,通常忽略不计。
成正工件的内部电阻与被焊金属的电阻率ρ和工件伸出电极的长度L比,与工件的断面积s成反比。
和点焊时一样,电阻对焊时的接触电阻取决于接触面的表面状态、温度及压力。
当接触电阻有明显的氧化物或其他赃物时,接触电阻就大。
温度或压力的增高,都会因实际接触面积的增大而使接触电阻减小。
焊接刚开始时,接触点上的电流密度很大;端面温度迅速升高后,接触电阻急剧减小。
加热到一定温度(钢600度,铝合金350度)时,接触电阻完全消失。
和点焊一样,对焊时的热源也是由焊接区电阻产生的电阻热。
电阻对焊时,接触电阻存在的时间极短,产生的热量小于总热量的10-15%。
但因这部分热量是接触面附近很窄的区域内产生的。
所以会使这一区域的温度迅速升高,内部电阻迅速增大,即使接触电阻完全消失,该区域的产热强度仍比其他地方高。
所采用的焊接条件越硬(即电流越大和通电时间越短),工件的压紧力越小,接触电阻对加热的影响越明显。
二、电阻对焊的焊接循环、工艺参数和工件准备1)焊接循环电阻对焊时,两工件始终压紧,当端面温升高到焊接温度Tω时,两工件端面的距离小到只有几个埃,端面间原子发生相互作用,在接合上产生共同晶粒,从而形成接头。
闪光对焊施工工艺

闪光对焊施工工艺本工艺标准适用于工业与民用建筑热轧钢筋的连续闪光焊、预热闪光焊、闪光一预热闪光焊。
2.1材料及主要机具:2.1.1钢筋:钢筋的级别、直径必须符合设计要求,有出厂证明书及复试报告单。
进口钢筋还应有化学复试单,其化学成分应满足焊接要求,并应有可焊性试验。
2.1.2主要机具:对焊机及配套的对焊平台、防护深色眼镜、电焊手套、绝缘鞋、钢筋切断机、空压机、水源、除锈机或钢丝刷、冷拉调直作业线。
常用对焊机主要技术数据见表4-20。
常用对焊机主要技术数据表4-20焊机型号UN1?0UN1?5UN1?00UN2?50UN17?50?动夹具传动方式杠杆挤压弹簧(人力操纵)电动机凸轮气椧貉?额定容量kV A5075100150150负载持续率%2520202050电源电压V220/380220/380380380380次级电压调节范围V2.9~5.03.52~7.044.5~7.64.05~8.103.8~7.6 次级电压调节级数6881616连续闪光焊钢筋大直径mm10~1212~1616~2020~2520~25预热闪光焊钢筋最大直径20~2232~36404040每小时最大焊接件数507520~3080120冷却水消耗量L/h200200200200600压缩空气压力MPa0.550.6压缩空气消耗量m3/h1552.2作业条件:2.2.1焊工必须持有有效的考试合格证。
2.2.2对焊机及配套装置、冷却水、压缩空气等应符合要求。
2.2.3电源应符合要求,当电源电压下降大于5%,小于8%时,应采取适当提高焊接变压器级数的措施;大于8%时,不得进行焊接。
2.2.4作业场地应有安全防护设施,防火和必要的通风措施,防止发生烧伤、触电及火灾等事故。
2.2.5熟悉料单,弄清接头位置,做好技术交底。
3.1工艺流程:检查设备→选择焊接工艺及参数→试焊、作模拟试件→送试→确定焊接参数→焊接→质量检验3.1.1连续闪光对焊工艺过程:闭合电路→闪光(两钢筋端面轻微接触)→连续闪光加热到将近熔点(两钢筋端面徐徐移动接触)→带电顶锻→无电顶锻3.1.2预热闪光对焊工艺过程:闭合电路→断续闪光预热(两钢筋端面交替接触和分开)→连续闪光加热到将近熔点(两钢筋端面徐徐移动接触)→带电顶锻→无电顶锻3.1.3闪光一预热闪光对焊工艺过程:闭合电路→一次闪光闪平端面(两钢筋端面轻微徐徐接触)→连续闪光预热(两钢筋端面交替接触和分开)→二次连续闪光加热到将近熔点(两钢筋端面徐徐移动接触)→带电顶锻→无电顶锻3.2焊接工艺方法选择:当钢筋直径较小,钢筋级别较低,可采用连续闪光焊。
闪光焊接原理及其参数

闪光焊接原理及其参数一、闪光焊接原理制链机组闪光对焊是一种使一个弯曲成形的金属圆环的两个端面通过电阻焊的方法对接成一个闭环的焊接方法。
焊接的热量是由极大的电流在金属表面的若干细小接触点的电阻以及接触的拉开时产生的电弧产生的。
在断面温度达到一定高度并产生金属熔液面时对两端面施加压力,从两端面中挤出熔融金属,并通过最后快速顶锻,使已达到熔化温度的母材金属端面重新结晶,熔为一体。
将被焊接环的两端夹在与电阻焊变压器次级连接的两电极中,当启动主电源、电子控制和液压、机械设备后,形成环背电流,液压设备将活动端的端面以设定的速度移近固定端,是两端面接触和挤压,形成焊接电流(焊口电流),巨大的电流使环口两端面温度升高,街头两端面上凹凸不平点接触点产生很大的电阻热,这些接触点迅速熔化,在变压器产生的磁场作用下,熔化的金属液滴穿过焊缝间隙,以很快的速度喷射出去,并形成许多小电弧产生高热,这个过程称为“预热闪光过程”。
然后将两端面拉开一点,电弧消失,端面迅速被氧化,端面的高温向两面的母材扩散,这个过程称之为温度均衡扩散过程。
反复进行若干次向前挤压接触的预热闪光过程和拉开温度均衡扩散的过程,金属开口两端形成温度很高的热影响区,并使金属两端面形成高热,直至被熔融金属层所覆盖,直到焊口接触到一起时,由于金属熔液不断地被喷射出去,焊口电流建立不起来,或者虽建立了,但达不到设定的时间又熔化喷射出去了,进不了温度均衡扩散过程,电极只有继续前进,闪光越来越猛烈,两焊口端面中的氧化物和杂质被喷射出去,这个过程称之为“连续闪光”,当连续闪光长度达到规定的总烧化长度时,焊机活动端迅速前进,将两界面紧紧地顶在一起,这个过程称之为“顶锻”,在顶锻过程中,电流迅速被切断,焊缝中的氧化物和杂质被挤出,形成毛刺。
顶锻后焊口熔在一起重新结晶,待其冷却到一个稳定状态这一过程所用的时间称为冷却时间。
冷却时间到后,上电极抬起,焊接过程结束。
二、闪光焊接参数的定义、影响及注意事项:1、顶锻压力:顶锻压力通过顶锻缸传给活动台,活动台通过电极夹住链环把压力传给焊口。
钢筋闪光对焊焊接

钢筋闪光对焊焊接钢筋闪光对焊焊接是利用对焊机使两段钢筋接触,通以低电压的强电流,把电能转化为热能,当钢筋加热到一定程度后,立即施加轴向压力挤压(称为顶锻),使形成对焊接头。
本工艺具有改善结构受力性能,减轻劳动强度,提高工效和质量,施工快速,节约钢材,降低成本等优点。
本工艺标准适用于Ⅰ-Ⅳ级钢筋接长及预应力钢筋与螺丝端杆的对焊焊接。
一、材料要求钢筋用Ⅰ-Ⅳ级各种规格钢筋,具有出厂合格证,进场后经物理性能试验符合有关标准和规范要求。
二、主要机具设备常用对焊机有UN1-25、UN1-50、UN1-75、UN1-100、UN1-150、UN1-150-1等型号,根据钢筋直径和需用功率选用。
三、作业条件1.对焊机检修完好,对焊机容量、电压,符合要求并符合安全规定。
2.电源已具备,电流、电压符合对焊要求。
3.钢筋焊接部位经清理,表面平整、清洁,无油Ⅰ污、杂质等。
4.操作人员经培训、考核,可持证上岗。
四、施工操作工艺1.根据钢筋品种、直径和所用对焊机功率大小,右选用连续闪光焊、预热闪光焊、闪光-预热-闪光等对焊工艺。
对于可焊性差的钢筋,对焊后宜采用通电热处理措施,以改善接头塑性。
(1)连续闪光焊工艺过程包括:连续闪光和顶锻。
施焊时,先闪合一次电路,使两根钢筋端面轻微接触,促使钢筋间隙中产生闪光,接着徐徐移动钢筋,使两钢筋端面仍保持轻微接触,形成连续闪光过程。
当闪光达到规定程度后(烧平端面,闪掉杂质,热至深溶化),即以适当压力迅速进行顶锻挤压,焊接接头即告完成。
本工艺适用于18mm以下的Ⅰ-Ⅲ级钢筋。
(2)预热闪光焊工艺过程包括:一次闪光预热;二次闪光、顶锻。
施焊时,先一次闪光,将钢筋端面闪光;然后预热,方法是使两钢筋端面轻微接触和分开,使其间隙发生断续闪光来实现预热或使两钢筋端面一直接触,用脉冲电流或交替紧密接触与分开,产生电阻热(不闪光)来实现预热。
二次闪光与顶锻过程同连续闪光。
本工艺适用于对焊直径20mm以上的Ⅰ-Ⅲ级钢筋。
钢筋闪光对焊工艺标准

钢筋闪光对焊是将两根钢筋安放成对接形式,利用焊接电流通过两钢筋接触点产生的电阻热,使金属熔化,产生强烈飞溅,形成闪光,迅速施加顶锻力完成的一种压焊方法,是电阻焊的一种。
一、工艺1、连续闪光焊适用于钢筋直径较小,钢筋级不较低的条件,所能焊接的钢筋上限直径依据焊机容量、钢筋级不等具体情况而定,应符合表4-10的。
连续闪光焊接钢筋上限直径表4-10连续闪光焊的工艺方法:将钢筋夹紧在对焊机的钳口上,接通电源后,使两钢筋端面局部接触,现在钢筋端面的接触点在高电流密度作用下迅速熔化、蒸发、爆破,呈高温粒状金属从焊口内高速飞溅出来;当旧的接触点爆破后,又形成新的接触点,这就出现连续不断爆破过程,钢筋金属连续不断送进〔以一定送进速度适应其焊接过程的烧化速度〕。
钢筋通过一定时刻的烧化,使其焊口到达所需要的温度,并使热量扩散到焊口两边,形成一定宽度的温度区,这时,以相当压力予以顶锻,将液态金属排挤在焊口之外,使钢筋焊合,并在焊口四面形成大量毛刺。
由于热碍事区较窄,故在接合面四面形成较小的凸起,因此,焊接过程结束,两钢筋对接焊成的外形见图4-10。
2、预热闪光焊在钢筋直径或级不超出表4-10的时,要是钢筋端面较平坦,那么宜采纳预热闪光焊。
预热闪光焊的工艺方法:在进行连续闪光焊之前,对钢筋增加预热过程。
将钢筋夹紧在对焊机的钳口上,接通电源后,开始以较小的压力使钢筋端面接触,然后又离开,如此不断地离开又接触,每接触一次,由于接触电阻及钢筋内部电阻使焊接区加热,拉开时产生瞬时的闪光。
经上述反复屡次,接头温度逐渐升高,实现了预热过程。
预热后接着进行闪光与顶锻,这两个过程与连续闪光焊一样。
采纳UN2-150型或UN17-150-1型对焊机进行大直径钢筋焊接时,宜首先采取锯割或气割方式对钢筋端面进行平坦处理;然后采纳预热闪光焊工艺,并应符合以下要求:闪光过程应强烈、稳定;顶锻凸块应垫高;应正确调整并严格操纵各过程的起点和止点。
3、闪光-预热闪光焊适用于钢筋端面不平坦的情况。
钢筋闪光对焊施工工艺

钢筋闪光对焊施工工艺引言钢筋闪光对焊施工工艺是一种常用的焊接方法,广泛应用于建筑、桥梁、道路等工程项目中。
闪光对焊具有焊接速度快、焊接强度高、操作简便等优点,因此得到了广泛的推广和应用。
本文将介绍钢筋闪光对焊施工工艺的基本原理、操作步骤、注意事项等内容。
1. 基本原理钢筋闪光对焊是利用电流通过两根接触钢筋之间的空气间隙产生的电弧放电来实现焊接的方法。
通过电弧放电时产生的高温使钢筋表面达到熔化温度,并施加外力使其形成焊缝。
2. 操作步骤2.1 准备工作在进行钢筋闪光对焊施工工艺之前,需要进行一系列的准备工作,包括:•准备焊接设备:包括闪光对焊机、电源、焊接电极等。
•准备焊接材料:包括焊条、助焊剂等。
•检查焊接环境:确保焊接地点通风良好,无可燃物和易爆物。
2.2 焊接准备在进行钢筋闪光对焊施工工艺之前,需要进行一些焊接准备工作,包括:•清洁钢筋表面:使用刷子等工具清洁钢筋表面的杂质和尘土。
•确定焊接位置:根据设计图纸确定焊接位置,并做好标记。
•调整焊接设备:根据钢筋的直径和长度等参数,调整闪光对焊机的电流和电压等参数。
2.3 进行焊接进行钢筋闪光对焊施工工艺时,按照以下步骤进行:1.将焊条插入焊接电极,并使其与电源连接。
2.将焊条的焊接端对准钢筋焊接位置。
3.按下闪光对焊机的启动按钮,触发电流通过焊接电极,产生电弧放电。
4.在电弧放电时,使焊条与钢筋接触,并施加适当的外力,使钢筋表面达到熔化温度。
5.在钢筋熔化后,保持一定的施压时间,等待焊缝冷却固化。
6.若需要进行多次焊接,依次对各个焊接位置进行施焊,保证焊缝的连续性。
2.4 焊后处理焊接完成后,需要进行焊后处理工作,包括:•焊缝清理:使用钢丝刷等工具清理焊缝表面的碎渣和杂质。
•检查焊缝:检查焊缝的质量和连接情况,确保焊接工艺的可靠性。
•防腐处理:根据需要对焊缝进行防腐处理,延长钢筋的使用寿命。
3. 注意事项在进行钢筋闪光对焊施工工艺时,需要注意以下事项:•安全意识:焊接操作需佩戴防护用品,特别是焊接眼镜和防火服等。
闪光对焊文档

闪光对焊1. 简介闪光对焊(Flash Butt Welding)是一种常用于焊接金属材料的技术,它通过将两个金属相互接触并施加力量和电流来产生焊接接头。
该方法适用于焊接钢、铜、铝和其他金属材料,并被广泛应用于制造业和建筑业。
2. 工作原理闪光对焊的工作原理基于电阻加热和压力,该过程包含以下几个步骤:1.接触面准备:将待焊接的两个金属部件放置在焊接机的电极之间,确保它们能够充分接触。
2.施加压力:闪光对焊机会施加一定的压力在接触面上,以确保金属部件之间的良好接触。
3.通电加热:一旦接触面接触良好,电流将通过金属部件流动,产生电阻加热。
加热过程中,金属部件的温度会上升,直到达到焊接温度。
4.闪光:当金属部件达到焊接温度时,施加的压力会产生闪光,闪光会产生强烈的热量,使金属部件快速熔化。
5.压力维持和冷却:在闪光过程中,保持施加的压力,以确保金属部件完全连接。
随后,冷却器会降低焊接接头的温度,使其固化和冷却。
6.修整和清理:焊接完成后,对焊接接头进行修整和清理,以确保其表面光滑,无缺陷。
3. 优点闪光对焊具有以下几个优点:•高强度焊缝:由于闪光对焊过程中产生的高温,金属部件很快熔化并迅速连接,焊缝的强度通常比传统焊接方法更高。
•快速和高效:闪光对焊过程时间短,可以在短时间内完成焊接。
同时,焊接速度快,提高了生产效率。
•不需填充材料:闪光对焊不需要额外的填充材料,减少了成本和焊接材料的浪费。
4. 应用领域闪光对焊广泛应用于以下领域:•汽车制造:闪光对焊常用于汽车制造中的底盘组件焊接,例如车轮轮毂和刹车盘等。
•铁路:铁路轨道的连接和修复往往使用闪光对焊进行。
•建筑业:使用闪光对焊将建筑领域的金属材料焊接在一起,例如钢筋的连接。
•航空航天:闪光对焊被用于航空航天行业中的飞机结构件的制造和维修。
•管道焊接:闪光对焊可用于管道的连接和修复。
5. 注意事项在使用闪光对焊进行金属材料的焊接时,需要注意以下事项:•安全措施:由于闪光对焊涉及高温和电流,焊接操作人员必须戴好防护眼镜、手套和耳塞,以确保安全。
闪光对焊名词解释

闪光对焊名词解释
闪光对焊是一种焊接方法,也称为闪光焊接。
它是利用高速短脉冲电流瞬间加热焊接金属材料,使其表面熔化,然后在压力的作用下快速冷却和凝固,从而实现精确、快速和可靠的焊接过程的方法。
该技术可应用于钢铁、铝、铜和不锈钢等金属材料的焊接。
闪光对焊是一种非常快速和有效的焊接方法,具有多项优点,例如焊接时间短、热影响区小、焊接后不需要清理等。
它被广泛应用于汽车和空间航天工业中,用于生产严格要求的紧固件、螺栓、紧固环和其他金属组件,以确保它们能够在极端条件下运行并保持高度可靠性。
闪光对焊也被广泛应用于电子、通信和计算机制造业,用于连接电子元件和半导体器件,以及其他小型金属组件。
除了在汽车、空间航天和电子制造等行业中的广泛应用之外,闪光对焊还被广泛应用于其他行业和领域中,例如医疗设备制造、船舶制造、建筑业和工业生产等。
它还可以用于制造机械零部件、精密仪器和工具,特别是那些要求高度精度和可靠性的应用。
闪光对焊技术的不断发展和优化,使其成为一种性能更好、成本更低和资源更节约的焊接方法,被广泛应用于各行各业。
闪光对焊的工艺方法
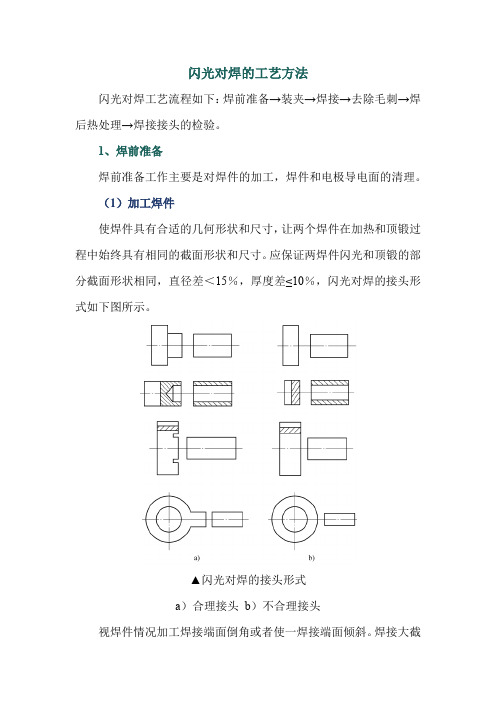
闪光对焊的工艺方法闪光对焊工艺流程如下:焊前准备→装夹→焊接→去除毛刺→焊后热处理→焊接接头的检验。
1、焊前准备焊前准备工作主要是对焊件的加工,焊件和电极导电面的清理。
(1)加工焊件使焊件具有合适的几何形状和尺寸,让两个焊件在加热和顶锻过程中始终具有相同的截面形状和尺寸。
应保证两焊件闪光和顶锻的部分截面形状相同,直径差<15%,厚度差≤10%,闪光对焊的接头形式如下图所示。
▲闪光对焊的接头形式a)合理接头b)不合理接头视焊件情况加工焊接端面倒角或者使一焊接端面倾斜。
焊接大截面焊件时,若不预热或不提高电压,激发闪光较困难,焊接过程易进入短路加热状态;若不能激发闪光,则焊接不得不中止,而且即使可以激发闪光,在短路状态的加热过程相当于增加了热输入不可控的预热阶段,使焊接质量不稳定。
大截面焊接端面的倒角尺寸如下图所示。
▲大截面焊接端部的倒角尺寸对于某些电阻率大、短路时发热快的材料,即使截面面积较小,也需加工倒角。
倒角角度一般为5°~10°,也可视具体情况取更大值。
使一焊接端面倾斜的目的与倒角相似,该方法仅适用于小截面焊件。
焊接端面可以在车床、锯床、坡口机等设备上通过机加工方法完成,也可以采用火焰切割或等离子切割方法。
焊接端面加工后稍清理即可。
(2)焊件和电极导电面的清理清理电面的目的是保持可靠的电极接触。
导电不佳时,功率消耗在焊件与电极接触处,可能引起焊接质量降低,并且可能导致焊件和电极闪光。
可采用锉刀、砂轮、金属刷等工具或酸洗方法清理焊件表面,去除焊件表面铁锈、氧化物和油脂。
用砂布或砂纸打磨电极表面,直至铜电极露出光亮的表面。
2、装夹焊件装夹不能出现歪斜、错边、装夹变形和顶锻时滑动等问题。
歪斜是指装夹时两焊件的轴线不在同一条直线上,而是呈一定的角度。
装夹时的歪斜将导致所获得的焊件弯曲。
错边是指两焊件的轴线平行但不在同一条直线上。
装夹错边会导致焊缝歪斜。
装夹歪斜和错边可通过调整夹钳进行改善,通常,闪光对焊机上的夹钳是可以微调的。
闪光对焊工作原理

闪光对焊工作原理
闪光对焊工作原理是指利用高能量的瞬间光强对金属进行焊接的一种焊接方式。
该焊接方式通常需用到特殊的设备。
在闪光对焊过程中,先将需要焊接的金属零件放置在合适的位置上,并施加足够的压力保持稳定。
然后,通过设备向金属表面投放能量高强度、频率较高的闪光光束。
这些光束可以在极短时间内升高金属的温度,形成瞬时的融合。
此时,要根据材料的特性和焊接需要,将闪光光束的功率、能量、宽度等参数进行精细的调整。
最终,闪光对焊工艺可以实现高强度、高速度、高质量和无需额外处理的焊缝效果。
闪光对焊工作原理是一种非常常见的焊接方式,通常用于金属板材、电子零部件、汽车制造、医疗器械等领域。
其中,它的优点主要表现在焊接快速、效率高、不产生污染和不影响材料的物理性能等方面。
不过,在应用中,我们也需要注意闪光强度、功率等参数的设置,以及特殊设备的使用和保养。
- 1、下载文档前请自行甄别文档内容的完整性,平台不提供额外的编辑、内容补充、找答案等附加服务。
- 2、"仅部分预览"的文档,不可在线预览部分如存在完整性等问题,可反馈申请退款(可完整预览的文档不适用该条件!)。
- 3、如文档侵犯您的权益,请联系客服反馈,我们会尽快为您处理(人工客服工作时间:9:00-18:30)。
闪光对焊的基本原理及方法和工艺闪光对焊是一种高效、节能的焊接方法,广泛应用于各种金属材料的焊接。
这种焊接方法的原理是利用电流通过两个对接工件时产生的电阻热效应,将工件加热到熔化或塑性状态,然后施加顶锻压力,实现工件的连接。
闪光对焊的基本原理
当两个金属工件对接时,电流通过这两个工件形成一个回路。
由于金属的导电性和电阻,电流会受到阻碍。
这些阻碍电流的效应会产生热量,使工件的温度升高并达到熔化或塑性状态。
这种电阻热效应的现象被称为“焦耳热”,是闪光对焊的基本原理。
闪光对焊的方法
闪光对焊主要分为两种方法:闪光焊和脉冲闪光焊。
1.闪光焊
闪光焊是最常用的闪光对焊方法,其工作原理是利用大电流通过工件接头,使工件迅速加热并达到熔化或塑性状态。
在工件接头处,液态金属由于表面张力和重力作用会向下流动,形成“闪光”现象。
在顶锻压力的作用下,液态金属被挤出接头间隙,形成焊接接头。
2.脉冲闪光焊
脉冲闪光焊是另一种常用的闪光对焊方法,其工作原理是通过交替改变电流的方向和大小,产生间断性的闪光和液滴喷射。
这种焊接方法可以更好地控制加热过程和顶锻过程,提高焊接质量和效率。
闪光对焊的工艺
闪光对焊的工艺流程可以分为以下几个步骤:
1.准备对接工件
对接前需要将两个工件进行清理和修整,确保对接面平整、无杂质、无氧化膜等。
同时,要保证两个工件的厚度、材质、直径等参数一致。
2.对接工件
将两个清理和修整好的工件按照一定的要求对接在一起,确保对接间隙均匀、无错位。
3.通电加热
将对接好的工件放置在焊接夹具中,然后通过通电的方式加热工件。
加热时间、电流大小、通电方式等因素需要根据不同的焊接要求进行选择和调整。
4.顶锻压力
当工件加热到一定温度后,施加一定大小的顶锻压力将工件对接接头挤压在一起。
顶锻压力的大小、时机等因素需要根据不同的焊接要求进行选择和调整。
5.冷却和取件
顶锻完成后,需要将工件自然冷却一段时间,以确保焊接接头质量稳定。
然后就可以将焊接好的工件从焊接夹具中取出。
闪光对焊的特点
闪光对焊具有以下特点:
1.高效节能:闪光对焊的加热时间短,能量消耗低,生产效率高。
2.适用范围广:闪光对焊可以焊接各种金属材料,包括低碳钢、中碳钢、合金
钢、不锈钢等。
3.焊接质量稳定:通过合理的工艺调整和控制,可以获得高质量的焊接接头。
4.劳动强度低:与其他的焊接方法相比,闪光对焊的劳动强度较低。
5.环境影响小:闪光对焊的焊接过程没有弧光辐射和飞溅,对操作人员和环境
的影响小。
总的来说,闪光对焊是一种高效、节能、环保的焊接方法,在金属加工和制造领域有着广泛的应用前景。