VHT系列五轴联动立式车铣复合加工中心的设计
五轴联动数控雕刻机结构设计

五轴联动数控雕刻机结构设计在数控雕刻机的设计中,五轴联动结构是目前较为常见的设计方案之一。
它可以实现对工件的多角度切削和精细加工,广泛应用于各种工业生产领域。
本文将主要介绍五轴联动数控雕刻机的结构设计和相关技术。
五轴联动数控雕刻机是一种高精度的加工设备,它可以在三维空间内沿着任意轴线进行加工,具有以下特点:1.高精度:五轴联动数控雕刻机具有较高的机床刚性和运动精度,可以保证加工精度和表面质量。
2.高效率:五轴联动数控雕刻机可以在一次装夹的情况下完成多个加工面,提高了生产效率。
3.广泛适用:五轴联动数控雕刻机可以加工各种难加工的工件,如曲面、复杂零件等。
4.易于操作:五轴联动数控雕刻机采用计算机控制和程序编写,具有灵活性和易操作性。
1.机床底座:机床底座是整个数控雕刻机的主要承重部分,它需要具有足够的刚性和稳定性,以保证加工精度和表面质量。
底座材料通常为优质铸铁、钢铁等。
2.主轴箱体:主轴箱体是数控雕刻机的核心部分,它包括主轴、伺服电机、减速器等部分。
主轴箱体需要具有较大的承载能力和刚性,以能够承受高速转动的主轴和高速切削力。
3.工作台:工作台是安装工件的平台,它需要具有足够的刚性和平整度,以保证工件的精确定位和加工精度。
在五轴联动数控雕刻机中,工作台可以沿着X、Y、Z三个方向移动,并且可以绕着A、C两个轴旋转。
4.五轴联动部分:五轴联动部分是数控雕刻机的核心部分,它由数控系统控制,可以实现对工件的多角度切削和精细加工。
五轴联动部分通常包括A轴、C轴、AB轴、BC轴等各个轴的伺服电机、减速器、轴承等部分。
5.数控系统:数控系统是五轴联动数控雕刻机的控制核心,它负责控制机床各个部分的运动和加工过程。
数控系统通常由计算机、控制卡、数控软件等部分组成,可以直接对加工程序进行编程和调整。
五轴联动数控雕刻机的工作原理是由数控系统对五个轴的运动进行控制,从而实现对工件的多角度切削和精细加工。
具体工作流程如下:1.准备工作:将工件固定在工作台上,并进行定位、检测等工作。
五轴联动立式加工中心结构设计
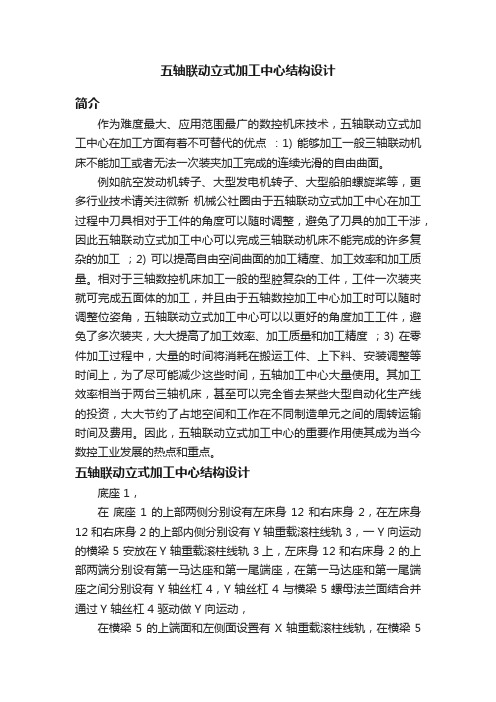
五轴联动立式加工中心结构设计简介作为难度最大、应用范围最广的数控机床技术,五轴联动立式加工中心在加工方面有着不可替代的优点:1) 能够加工一般三轴联动机床不能加工或者无法一次装夹加工完成的连续光滑的自由曲面。
例如航空发动机转子、大型发电机转子、大型船舶螺旋桨等,更多行业技术请关注微新机械公社圈由于五轴联动立式加工中心在加工过程中刀具相对于工件的角度可以随时调整,避免了刀具的加工干涉,因此五轴联动立式加工中心可以完成三轴联动机床不能完成的许多复杂的加工;2) 可以提高自由空间曲面的加工精度、加工效率和加工质量。
相对于三轴数控机床加工一般的型腔复杂的工件,工件一次装夹就可完成五面体的加工,并且由于五轴数控加工中心加工时可以随时调整位姿角,五轴联动立式加工中心可以以更好的角度加工工件,避免了多次装夹,大大提高了加工效率、加工质量和加工精度;3) 在零件加工过程中,大量的时间将消耗在搬运工件、上下料、安装调整等时间上,为了尽可能减少这些时间,五轴加工中心大量使用。
其加工效率相当于两台三轴机床,甚至可以完全省去某些大型自动化生产线的投资,大大节约了占地空间和工作在不同制造单元之间的周转运输时间及费用。
因此,五轴联动立式加工中心的重要作用使其成为当今数控工业发展的热点和重点。
五轴联动立式加工中心结构设计底座 1,在底座 1 的上部两侧分别设有左床身 12 和右床身 2,在左床身12 和右床身 2 的上部内侧分别设有 Y 轴重载滚柱线轨 3,一 Y 向运动的横梁 5 安放在Y 轴重载滚柱线轨 3上,左床身 12 和右床身 2 的上部两端分别设有第一马达座和第一尾端座,在第一马达座和第一尾端座之间分别设有 Y 轴丝杠 4,Y 轴丝杠 4 与横梁 5 螺母法兰面结合并通过Y 轴丝杠 4 驱动做 Y 向运动,在横梁 5 的上端面和左侧面设置有 X 轴重载滚柱线轨,在横梁 5的 X 轴重载滚柱线轨 7 上设有可 X 向运动的滑座 11,横梁 5 的左侧斜面上安装有第二马达座,横梁5 的右侧侧斜面上安装有第二尾端座,第二马达座和第二尾端座之间安装有 X 轴丝杠 8, X 轴丝杠 8 与滑座11 的底部螺母法兰面结合并通过X 轴丝杠 8 驱动做做 X 向运动,滑座 11 的内侧侧面上设置有Z 轴重载滚柱线轨 10,滑座 11 的前端上部安装有第三马达座,下部安装有第三尾端座,第三马达座和第三尾端座之间设有 Z 轴丝杠 15,Z 轴丝杠 15 与一机头 9 右侧螺母法兰面结合并通过Z 轴丝杠 15 驱动做 Z 向运动,机头 9 内的主轴孔内装有可高速旋转的电主轴 6,机头 9 的上端安装有气缸导向板 18,滑座 11 的上端安装气缸支撑板17,气缸固定板 17 上安装有气缸 16,右床身 2 和左床身 12 之间安装有带高动态特性力矩电机的双轴转台 14,底座 1 的后部且在右床身2 和左床身 12 之间的空腔内安放有刀库 13。
车铣复合加工中心毕业设计方案
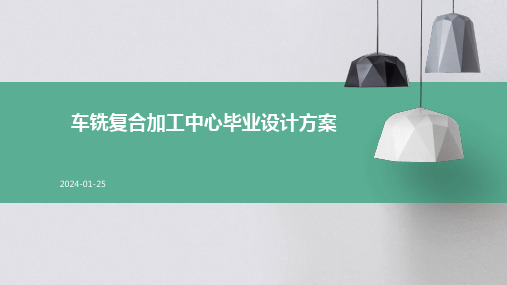
广泛应用于航空航天、汽车制造 、模具制造、能源装备等领域, 适用于复杂零件的高效、高精度 加工。
车铣复合加工中心的发展趋势
高速化
随着切削速度的提高,车铣复合加工 中心将向更高速度、更高效率的方向 发展。
智能化
采用环保材料、节能技术等措施,降 低车铣复合加工中心的能耗和排放, 实现绿色制造。
高精度化
关键技术与创新点
关键技术
重点解决车铣复合加工中心在高速、高精度加工过程中的关 键技术问题,如热误差补偿、动态性能优化、高精度传动等 。
创新点
提出具有自主知识产权的创新性设计,如新型主轴结构、高 性能直线电机驱动技术等,提升车铣复合加工中心的加工效 率和精度。
04
机械系统设计
主轴箱设计
主轴结构
采用高性能电主轴,具有高转速、高精度和低振动等特点。
设计目标与要求
设计要求 实现多轴联动控制,提高加工精度和效率。
优化机床结构,降低振动和噪音。
设计目标与要求
01
选用高性能切削刀具, 提高切削效率。
02
集成自动化上下料系统 ,提高生产效率。
03
完善安全防护措施,确 保操作安全。
设计流程与步骤
需求分析
明确设计任务和目标,收集相关资料,进行 需求分析。
随着制造技术的不断进步,车铣复合 加工中心的加工精度将不断提高,满 足更高精度的加工需求。
绿色化
引入人工智能、大数据等先进技术, 实现车铣复合加工中心的智能化、自 动化生产。
03
毕业设计方案总体设计
设计思路与方案选择
设计思路
基于车铣复合加工中心的加工需求, 结合现有技术和资源条件,提出一种 高效、高精度、高稳定性的设计方案 。
五轴组合零件数控加工工艺及工装设计
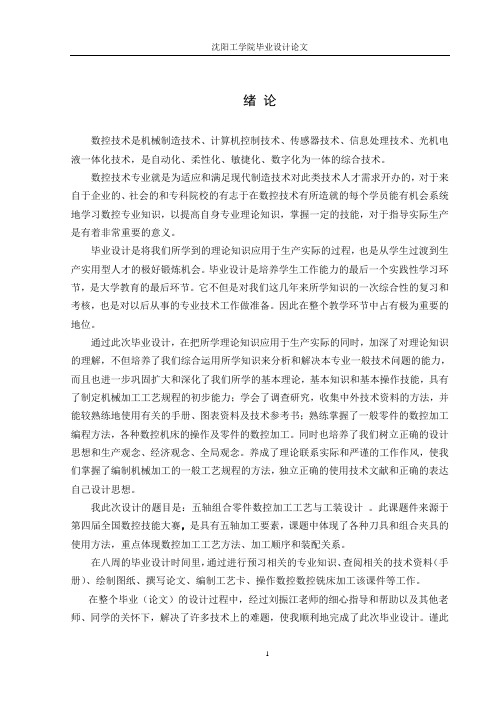
绪论数控技术是机械制造技术、计算机控制技术、传感器技术、信息处理技术、光机电液一体化技术,是自动化、柔性化、敏捷化、数字化为一体的综合技术。
数控技术专业就是为适应和满足现代制造技术对此类技术人才需求开办的,对于来自于企业的、社会的和专科院校的有志于在数控技术有所造就的每个学员能有机会系统地学习数控专业知识,以提高自身专业理论知识,掌握一定的技能,对于指导实际生产是有着非常重要的意义。
毕业设计是将我们所学到的理论知识应用于生产实际的过程,也是从学生过渡到生产实用型人才的极好锻炼机会。
毕业设计是培养学生工作能力的最后一个实践性学习环节,是大学教育的最后环节。
它不但是对我们这几年来所学知识的一次综合性的复习和考核,也是对以后从事的专业技术工作做准备。
因此在整个教学环节中占有极为重要的地位。
通过此次毕业设计,在把所学理论知识应用于生产实际的同时,加深了对理论知识的理解,不但培养了我们综合运用所学知识来分析和解决本专业一般技术问题的能力,而且也进一步巩固扩大和深化了我们所学的基本理论,基本知识和基本操作技能,具有了制定机械加工工艺规程的初步能力;学会了调查研究,收集中外技术资料的方法,并能较熟练地使用有关的手册、图表资料及技术参考书;熟练掌握了一般零件的数控加工编程方法,各种数控机床的操作及零件的数控加工。
同时也培养了我们树立正确的设计思想和生产观念、经济观念、全局观念。
养成了理论联系实际和严谨的工作作风,使我们掌握了编制机械加工的一般工艺规程的方法,独立正确的使用技术文献和正确的表达自己设计思想。
我此次设计的题目是:五轴组合零件数控加工工艺与工装设计。
此课题件来源于第四届全国数控技能大赛,是具有五轴加工要素,课题中体现了各种刀具和组合夹具的使用方法,重点体现数控加工工艺方法、加工顺序和装配关系。
在八周的毕业设计时间里,通过进行预习相关的专业知识、查阅相关的技术资料(手册)、绘制图纸、撰写论文、编制工艺卡、操作数控数控铣床加工该课件等工作。
VERICUT五轴车铣复合加工中心的应用

乐
t ‘ s Ide’ 0 0 0 pn I ‘, , '
o Mode s - I
9 1 x r《,,) 鼍 Ft e 000 l iu
St ck1 , , , ' o 0 0 0
o 事 ^ t ht 。 0, - l ac 0 0, o ’z 0 0 0 _ 2‘, , '
翟- 4 0 0 e 3 Z t, , ̄ ) l l
々冒 Z
o M o el - i r s
二、5 车铣 中心仿真 系统的构建 轴
I 床 描 述 . 机
图2 组件 数
t
x t 0 0’ 0。 ,
oIM ode m l
该5 车铣加工 中心 为奥地利W 公司生产 的斜床 身卧式 车 铣 加 工 中心 基 础 的部 件 目录 。 轴 F L 加 工 中心 ,控 制 系统 为S N M RK 8 0 , 、 Y、Z 、B 五 IU E I 4 D I 1 、 ( 机 床 实体 模 型 的建 立 。 2) 机 床 模 型 的 创 建 有 两 种 方
一
、
VE CU ..仿 真 软 件 的 应 用现 状 RI T622
o- M 0 d eI s
9 ● ct , , } 0 0 0
o Mo _ del s
目前 国内在仿 真软件 应用方 面技术 比较成 熟 ,能够 实现 9 毒r ae000 B s t ,, , 9 A t c O I 0 ta h c ,] ’ I , 四轴及 以下 功能机 床的仿真 ,对于 5 轴机床仿真 系统应 用还 不
T 格式后 ,在V RC T E IU 系统下双击要添加的 运 行V R C T E I U ,打开F E I 创建 新项 目,保存后单 击主菜 下 创建模型 ,生成S L L  ̄B s 所 Md l 单 中 “ o f g r to ”下 的 “ o p n n T e ” ,打 开 机 目标 ( ae),弹 出图4 示对话框后 ,点击 “ o e” ,选 C n i u a in C m oe t re 床部件 数 ,如 图2 所示 。在 “ a e B S ”下依次 创建C( 主轴 )、
五轴联动机床机构设计

本科毕业设计(论文)通过答辩摘要五轴联动加工中心有高效率、高精度的特点。
若配以五轴联动的高档数控系统,还可以对复杂的空间曲面进行高精度加工,更能够适应像汽车零部件、飞机结构件等现代模具的加工。
本文设计了一台五轴联动机床主轴模型,在XY工作台的基础上叠加两层托板,步进电动机带动轴使其做旋转运动,构成类似陀螺仪的结构。
分别实现工作台绕XY轴的转动和移动,再沿Z轴装配一根丝杠完成工作台沿Z轴的上下运动最终实现刀具向各个面进行加工。
主要完成了:模型整体结构设计,各个轴的结构设计及计算、滚珠丝杠、轴承和直线滚动导轨的选择及其强度分析;步进电机的选择及分析。
关键词五轴联动丝杠传动陀螺仪1本科毕业设计(论文)通过答辩AbstractFive-axis machining center with high efficiency and precision characteristics. If accompanied by high-end CNC five-axis system, can also carry out complex curved surface precision machining, more able to adapt as automotive components, aircraft structural parts and other modern mold processing.This paper designed a five-axis machine tool spindle model, based on the XY table overlay two pallets, stepper motor drive shaft rotation to do so constitutes a similar gyro structure. Were achieved around the XY axis rotating table and move along the Z axis and then complete the table assembly of a screw up and down movement along the Z axis to the ultimate realization of the various surface processing tool.Main completed: overall structural design model, each shaft structure design and calculation, ball screws, bearings and linear motion guide the choice and strength analysis; stepper motor selection and analysis.Keywords five-axis gyro screw drive2本科毕业设计(论文)通过答辩目录摘要 (1)Abstract (2)第一章绪论 (5)第二章总体方案的设计 (6)2.1设计任务 (6)2.2设计方案的论证 (6)2.2.1传动方式的确定 (6)2.2.2 陀螺仪机构的设计 (6)2.3 总体方案的设计及结构组成 (6)第三章 XY工作台及绕XY旋转工作台的设计 (8)3.1 XY工作台的设计 (8)3.1.1主要设计参数及依据 (8)3.1.2 XY工作台部件进给系统受力分析 (8)3.1.3初步确定XY工作台尺寸及估算重 (8)3.2绕XY旋转工作台的设计 (8)3.2.1主要设计参数及依据 (8)3.2.2绕XY旋转工作台受力分析 (9)3.2.3初步选定绕XY旋转工作台的尺寸及重量估计 (9)3.3 沿Z向移动工作部分设计 (9)第四章滚珠丝杠副的选型与计算 (10)4.1滚珠丝杠的选型 (10)4.2 滚珠丝杠副导程的确定 (13)4.3 滚珠丝杠副的传动效率 (14)第五章直线滚动导轨的选型 (15)5.1定位精度高 (15)5.2降低机床造价并大幅度节约电力 (15)5.3可提高机床的运动速度 (15)5.4可长期维持机床的高精度 (15)5.5直线滚动导轨副的计算与选型 (16)5.5.1滑块承受工作载荷F max的计算及导轨型号的选取 (16)5.5.2距离额定寿命L的计算 (16)第六章步进电机的参数与选型 (17)6.1步进电动机的特点 (17)6.2 步进电动机的分类 (17)6.2.1反应式步进电动机 (17)6.2.2永磁式步进电动机 (17)6.2.3混合式步进电动机 (17)6.3步进电动机的参数及其选择 (18)6.3.1步距角的选择 (18)6.4电动机的转速与功率 (19)6.5各参素的确定 (19)3本科毕业设计(论文)通过答辩6.6初选步进电动机型号 (20)6.6.1脉冲当量的选择 (20)6.6.2等效负载转矩的计算 (20)6.6.3等效转动惯量计算 (20)6.6.4步进电动机型号选择的计算 (21)第七章轴、轴承及联轴器的选用 (26)7.1轴的材料 (26)7.1.1轴的分类 (26)7.1.2轴的材料及选择 (26)7.2 轴的结构设计 (26)7.2.1轴头、轴颈和轴身 (26)7.2.2轴上零件的轴向固定和定位 (27)7.2.3轴的周向固定: (27)7.2.4减少应力集中的措施 (27)7.3轴承的选用 (28)7.4联轴器的选用 (28)第八章连接部分 (31)8.1 螺纹紧固件的联接画法 (31)致谢 (33)参考文献 (34)4本科毕业设计(论文)通过答辩第一章绪论五轴联动数控是数控技术中难度最大、应用范围最广的技术。
五轴五联动加工中心项目需求及技术要求
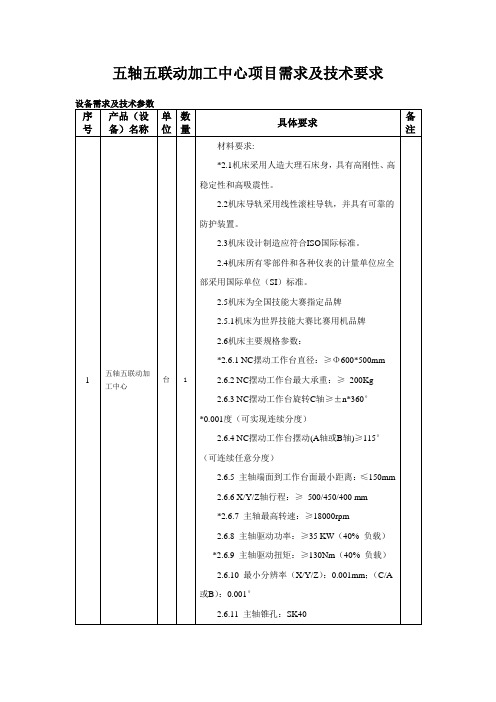
*2.7.1 CNC控制系统:选配德国SIEMENS840D控制系统,可实现五轴五联动功能,可直接打开三维视图,并可进行在线任务设定。
*2.7.2显示器:≥21″液晶彩显,全触屏操作。
2.7.3驱动系统:主轴、进给系统采用数字交流伺服电机。
2.7.4坐标、刀具直径及长度补偿
2.7.5绝对/增量编程
2.6.5主轴端面到工作台面最小距离:≤150mm
2.6.6 X/Y/Z轴行程:≥500/450/400 mm
*2.6.7主轴最高转速:≥18000rpm
2.6.8主轴驱动功率:≥35 KW(40%负载)
*2.6.9主轴驱动扭矩:≥130Nm(40%负载)
2.6.10最小分辨率(X/Y/Z):0.001mm;(C/A或B):0.001°
五轴五联动加工中心项目需求及技术要求
设备需求及技术参数
序号
产品(设备)名称
单位
数量
具体要求
备注
1
五轴五联动加工中心
台
1
材料要求:
*2.1机床采用人造大理石床身,具有高刚性、高稳定性和高吸震性。
2.2机床导轨采用线性滚柱导轨,并具有可靠的防护装置。
2.3机床设计制造应符合ISO国际标准。
2.4机床所有零部件和各种仪表的计量单位应全部采用国际单位(SI)标准。
2.6.19最大刀具直径(满库):Φ80 mm
2.6.20最大刀具直径(相邻空位):Φ130 mm
2.6.23定位精度(X/Y/Z):≤0.008mm
2.6.24重复定位精度(X/Y/Z):≤0.005mm
2.6.25 X/Y/Z轴直接测量全闭环控制。
2.6.26可完成(X、Y、Z、C、A或B)五轴五联动加工。
五轴联动数控加工中心的组成结构功能
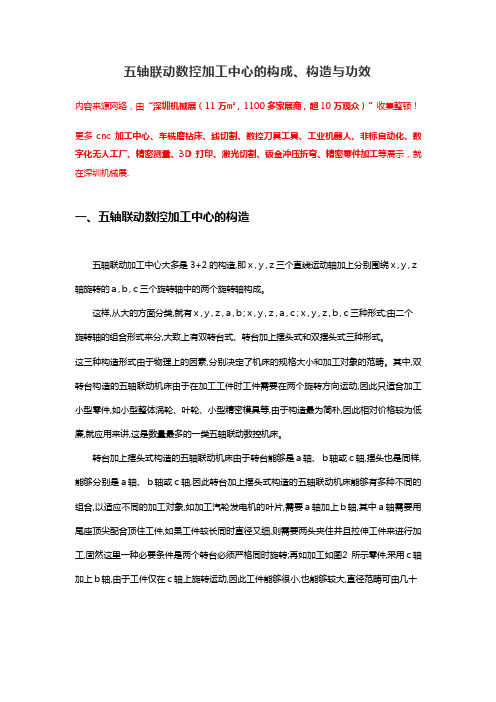
五轴联动数控加工中心的构成、构造与功效内容来源网络,由“深圳机械展(11 万㎡,1100 多家展商,超 10 万观众)”收集整顿!更多cnc 加工中心、车铣磨钻床、线切割、数控刀具工具、工业机器人、非标自动化、数字化无人工厂、精密测量、3D 打印、激光切割、钣金冲压折弯、精密零件加工等展示,就在深圳机械展.一、五轴联动数控加工中心的构造五轴联动加工中心大多是 3+2 的构造,即x,y,z三个直线运动轴加上分别围绕x,y,z轴旋转的a,b,c三个旋转轴中的两个旋转轴构成。
这样,从大的方面分类,就有x,y,z,a,b;x,y,z,a,c;x,y,z,b,c三种形式;由二个旋转轴的组合形式来分,大致上有双转台式、转台加上摆头式和双摆头式三种形式。
这三种构造形式由于物理上的因素,分别决定了机床的规格大小和加工对象的范畴。
其中,双转台构造的五轴联动机床由于在加工工件时工件需要在两个旋转方向运动,因此只适合加工小型零件,如小型整体涡轮、叶轮、小型精密模具等,由于构造最为简朴,因此相对价格较为低廉,就应用来讲,这是数量最多的一类五轴联动数控机床。
转台加上摆头式构造的五轴联动机床由于转台能够是a轴、b轴或c轴,摆头也是同样,能够分别是a轴、b轴或c轴,因此转台加上摆头式构造的五轴联动机床能够有多种不同的组合,以适应不同的加工对象,如加工汽轮发电机的叶片,需要a轴加上b轴,其中a轴需要用尾座顶尖配合顶住工件,如果工件较长同时直径又细,则需要两头夹住并且拉伸工件来进行加工,固然这里一种必要条件是两个转台必须严格同时旋转;再如加工如图2 所示零件,采用c轴加上b轴,由于工件仅在c轴上旋转运动,因此工件能够很小,也能够较大,直径范畴可由几十毫米至数千毫米,c轴转台的直径也能够从 100~200mm至 2~3m,机床的规格、质量也从几吨至十几吨甚至数十吨。
这也是一类应用十分广泛的五轴联动数控机床,其价格居中,随机器规格大小、精度和性能的不同相差很大。
毕业设计(论文)-立式铣削五轴五联动加工中心设计
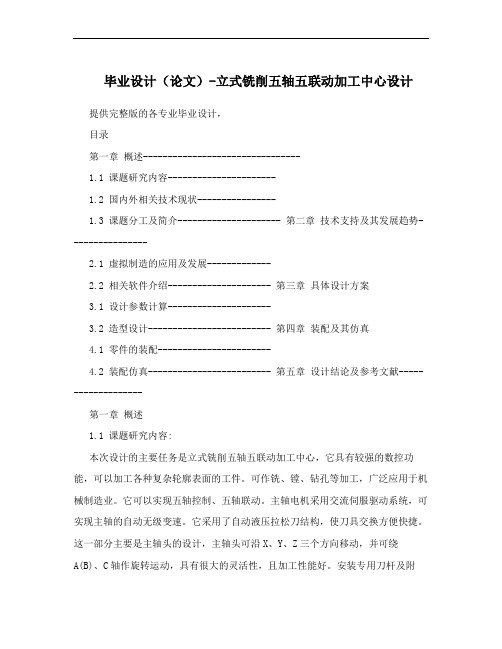
毕业设计(论文)-立式铣削五轴五联动加工中心设计提供完整版的各专业毕业设计,目录第一章概述--------------------------------1.1 课题研究内容----------------------1.2 国内外相关技术现状----------------1.3 课题分工及简介--------------------- 第二章技术支持及其发展趋势----------------2.1 虚拟制造的应用及发展-------------2.2 相关软件介绍--------------------- 第三章具体设计方案3.1 设计参数计算---------------------3.2 造型设计------------------------- 第四章装配及其仿真4.1 零件的装配-----------------------4.2 装配仿真------------------------- 第五章设计结论及参考文献-------------------第一章概述1.1 课题研究内容:本次设计的主要任务是立式铣削五轴五联动加工中心,它具有较强的数控功能,可以加工各种复杂轮廓表面的工件。
可作铣、镗、钻孔等加工,广泛应用于机械制造业。
它可以实现五轴控制、五轴联动。
主轴电机采用交流伺服驱动系统,可实现主轴的自动无级变速。
它采用了自动液压拉松刀结构,使刀具交换方便快捷。
这一部分主要是主轴头的设计,主轴头可沿X、Y、Z三个方向移动,并可绕A(B)、C轴作旋转运动,具有很大的灵活性,且加工性能好。
安装专用刀杆及附件,可以加工平面,斜面、螺旋面、沟槽、花键、弧形槽等等。
通过转动的主轴头,机床可实现铣削空间前半球任意角度的加工它采用精密同步带传递主传动,采用伺服电机实现摆动,该主轴头具有较高刚度,主轴转速变换范围宽。
主轴电机为28KW,采用高速钢或硬质合金刀具可进行高速度的强力切削,主轴头与滑枕作成分离式,便于用户安装拆卸。
有关五轴联动数控车铣复合加工中心的优化分析
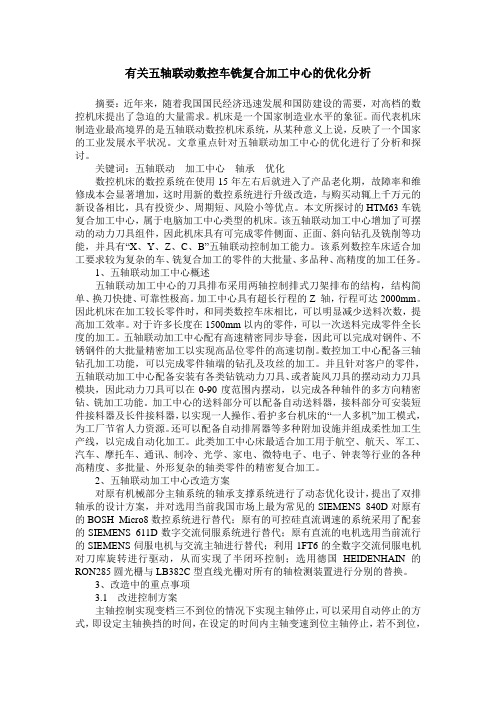
有关五轴联动数控车铣复合加工中心的优化分析摘要:近年来,随着我国国民经济迅速发展和国防建设的需要,对高档的数控机床提出了急迫的大量需求。
机床是一个国家制造业水平的象征。
而代表机床制造业最高境界的是五轴联动数控机床系统,从某种意义上说,反映了一个国家的工业发展水平状况。
文章重点针对五轴联动加工中心的优化进行了分析和探讨。
关键词:五轴联动加工中心轴承优化数控机床的数控系统在使用15年左右后就进入了产品老化期,故障率和维修成本会显著增加,这时用新的数控系统进行升级改造,与购买动辄上千万元的新设备相比,具有投资少、周期短、风险小等优点。
本文所探讨的HTM63车铣复合加工中心,属于电脑加工中心类型的机床。
该五轴联动加工中心增加了可摆动的动力刀具组件,因此机床具有可完成零件侧面、正面、斜向钻孔及铣削等功能,并具有“X、Y、Z、C、B”五轴联动控制加工能力。
该系列数控车床适合加工要求较为复杂的车、铣复合加工的零件的大批量、多品种、高精度的加工任务。
1、五轴联动加工中心概述五轴联动加工中心的刀具排布采用两轴控制排式刀架排布的结构,结构简单、换刀快捷、可靠性极高。
加工中心具有超长行程的Z 轴,行程可达2000mm。
因此机床在加工较长零件时,和同类数控车床相比,可以明显减少送料次数,提高加工效率。
对于许多长度在1500mm以内的零件,可以一次送料完成零件全长度的加工。
五轴联动加工中心配有高速精密同步导套,因此可以完成对钢件、不锈钢件的大批量精密加工以实现高品位零件的高速切削。
数控加工中心配备三轴钻孔加工功能,可以完成零件轴端的钻孔及攻丝的加工。
并且针对客户的零件,五轴联动加工中心配备安装有各类钻铣动力刀具、或者旋风刀具的摆动动力刀具模块,因此动力刀具可以在0-90度范围内摆动,以完成各种轴件的多方向精密钻、铣加工功能。
加工中心的送料部分可以配备自动送料器,接料部分可安装短件接料器及长件接料器,以实现一人操作、看护多台机床的“一人多机”加工模式,为工厂节省人力资源。
立式铣车复合加工中心的研制与应用
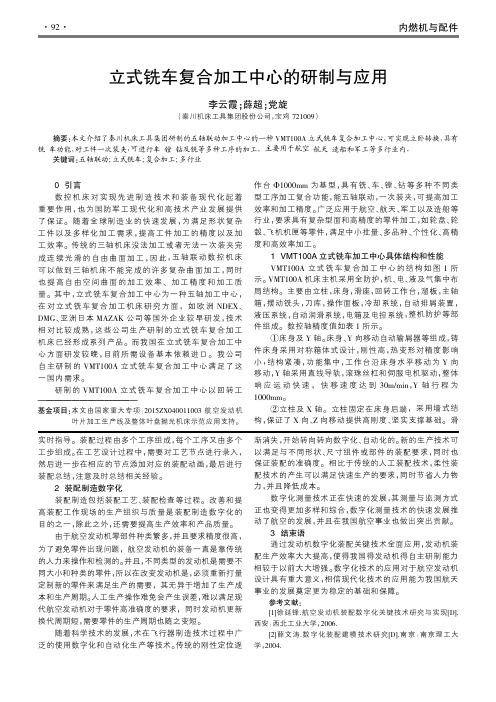
1.立柱;
2.滑座;3溜板;4.主轴箱;5铣主轴;6.床身;7.回转工作台
图1机床结构图
座沿立柱水平移动为X向移动,X轴采用直线导轨、滚珠
丝杠和伺服电机驱动结构,快移速度可达30m/min,X轴
行程为1200mm。
③滑座、主轴箱及Z轴。
Z向移动支撑部件由主轴箱
和滑座组成,主轴箱在滑座上下移动,Z轴采用直线导轨、
滚珠丝杠和伺服电机驱动结构,快移速度达到30m/min,Z
轴行程为1000mm。
④摆动铣头主轴电机和摆动电机。
摆动铣头用于五
图2机匣图3叶盘
3结论
介绍了研制出的VMT100A立式铣车复合加工中心
的结构特性,满足了我国在航空航天等制造领域的需求,
我国只要紧跟先进国家机床发展脚步,更加深入的研究,
持续不断加强自主创新能力,在对形成的具有自主知识产
权的核心技术与成熟企业技术规范协助下,这样使我们的
产品在国内外市场上将具有较强的竞争力。
参考文献:
[1]张耀满,蔡光起,等.新型五坐标加工中心的结构设计和分
析[J].机械制造,2005(12):20-21.
[2]谢黎明,代冒浩,符卫东.车铣复合加工中心主轴结构的有
限元分析[J].组合机床与自动化加工技术,2003(2):29-30,33.
[3]燕红波,杨庆东,刘芳.五轴联动的数控加工技术的研究及
应用[J].机械工程师,2007(5):120-122.
[4]王旭.五轴数控抛光机CAM技术[J].航空制造技术,2015
(5):50-53.。
五轴联动数控加工中心的结构

五轴联动数控加工中心的结构————————————————————————————————作者:————————————————————————————————日期:五轴联动数控加工中心的结构五轴联动加工中心大多是“3+2”的结构,即X,Y,Z三个直线运动轴加上分别国绕X YZ轴旋转的A,B,C三个旋转轴中的两个旋转轴组成。
这样,从大的方面分类,就有X,Y,Z,A,B;X,Y,Z,A,C;X,Y,Z,B,C三种形式。
根据二个旋转轴的组合形式不同来划分,大体上有双转台式、转台加摆头式和双摆头式三种形式。
这三种结构形式由于物理上的原因,分别决定了五轴联动机床的规格大小和加工对象的范围。
1.双转台结构的五轴联动机床如图6—20所示,为A轴+C轴的双转台结构。
设置在床身上的工作台可以围绕X轴回转,定义为A轴,A轴一般工作范围+30°至一120°。
工作台的中间还没有一个回转台绕Z轴旋转,定义为C轴,C 轴一般能进行360°回转。
这样通过A轴与C轴的组合,固定在工作台上的工件除了底面之外,其余的五个面部可以由立式主轴进行加工。
A轴和C轴最小分度值一般为0.001°,这样又可以招工件细分成任意角度,加工出倾斜面、顾斜孔等。
A轴和C轴如与X、Y、Z三个直线轴实现联动,就可加工出复杂的空间曲面,当然这需要高档的数控系统、伺服系统以及软件的支持。
这种设置方式的优点是主轴的结构比较简单,主轴刚性非常好,制造成本比较低。
但一般工作台不能设计太大,承重也较小,特别是当A轴回转大干等于90°时,工件切削时会对工作台带来很大的承裁力矩。
2.转台加摆头式结构的五轴联动机床如图6-21所示,由于转台可以是A轴、B轴或C轴,摆头也是一样,可以分别是A轴、B轴或C轴,所以转台加上摆头式结构的五轴联动机床可以有各种不同的组合,以适应不同的加工对象。
这种设置方式的优点是主轴加工非常灵活,工作台也可以设计得非常大。
五轴联动加工中心

五轴联动数控机床编辑本段装备制造业是一国工业之基石,它为新技术、新产品的开发和现代工业生产提供重要的手段,是不可或缺的战略性产业。
即使是发达工业化国家,也无不高度重视。
近年来,随着我国国民经济迅速发展和国防建设的需要,对高档的数控机床提出了迫切的大量需求。
机床是一个国家制造业水平的象征。
而代表机床制造业最高境界的是五轴联动数控机床系统,从某种意义上说,它反映了一个国家的工业发展水平状况。
长期以来,以美国为首的西方工业发达国家,一直把五轴联动数控机床系统作为重要的战略物资,实行出口许可证制度。
特别是冷战时期,对中国、前苏联等社会主义阵营实行封锁禁运。
爱好军事的朋友可能知道著名的“东芝事件”:上世纪末,日本东芝公司卖给前苏联几台五轴联动的数控铣床,结果让前苏联用于制造潜艇的推进螺旋桨,上了几个档次,使美国间谍船的声纳监听不到潜艇的声音了,所以美国以东芝公五轴联动加工中心有高效率、高精度的特点,工件一次装夹就可完成五面体的加工。
若配以五轴联动的高档数控系统,还可以对复杂的空间曲面进行高精度加工,更能够适应像汽车零部件、飞机结构件等现代模具的加工。
立式五轴加工中心的回转轴有两种方式,一种是工作台回转轴,设置在床身上的工作台可以环绕X轴回转,定义为A轴,A轴一般工作范围+30度至-120度。
工作台的中间还设有一个回转台,在图示的位置上环绕Z轴回转,定义为C轴,C轴都是360度回转。
这样通过A轴与C 轴的组合,固定在工作台上的工件除了底面之外,其余的五个面都可以由立式主轴进行加工。
A轴和C轴最小分度值一般为0.001度,这样又可以把工件细分成任意角度,加工出倾斜面、倾斜孔等。
A轴和C轴如与XYZ三直线轴实现联动,就可加工出复杂的空间曲面,当然这需要高档的数控系统、伺服系统以及软件的支持。
这种设置方式的优点是主轴的结构比较简单,主轴刚性非常好,制造成本比较低。
但一般工作台不能设计太大,承重也较小,特别是当A轴回转大于等于90度时,工件切削时会对工作台带来很大的承载力矩。
五轴联动复合加工机床案例分析
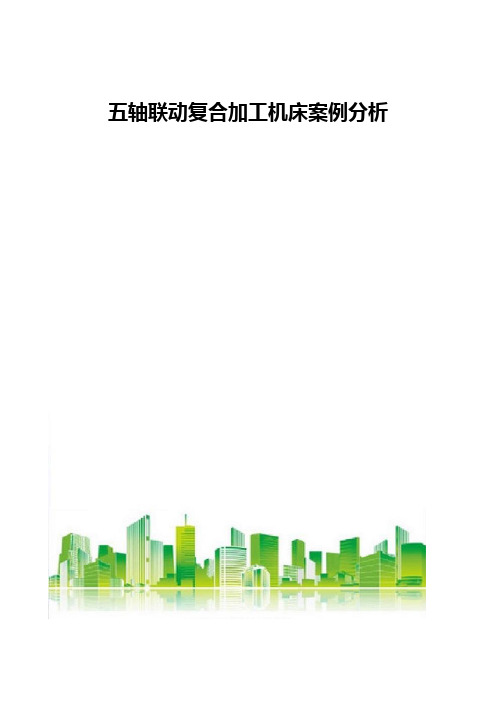
五轴联动复合加工机床案例分析一台拥有为加工复杂形状的工件而进行数道工序、不同方式的加工性能的机械称之为复合加工机床。
为达到同样目的,也有将控制坐标多轴化、扩大加工功能、多机能化的使用方法。
总之是用工序集成的方法提高生产效率,提高机床的附加价值。
于是,这里就把前者的在一台机床内实现不同品种加工的机床和后者的多坐标控制机床两者通称为复合加工机床。
而今复合加工机床成为世界机床发展方向,目前,世界上越来越多的复杂零件采用复合机床进行加工。
因为复合加工机床突出体现了工件在一次装夹中完成大部分或全部加工工序,从而达到减少机床和夹具,免去工序间的搬运和储存,提高工件加工精度,缩短加工周期和浪费作业面积的目的。
下面针对我公司开发的几款复合加工机床介绍如下:1. 铣削激光切割五轴联动复合加工机床一款铣削激光切割五轴联动复合加工机床,此机床采用桥式龙门框架结构,采用可重组模块化设计,主机系统划分为大跨度、高刚性、高动态特性的直线运动框架结构、多自由度旋转运动机构和可交换主轴头等功能模块,各模块具有机械、电气等标准化的接口,形成可装配的功能单元,通过配置不同加工刀具或加工装置,实现铣削和激光切割等不同工艺加工制造的复合加工。
此复合加工设备如图1所示。
图1 铣削激光切割五轴联动复合加工机床此复合加工设备特点如下:(1)复合加工功能此复合加工设备除了传统的最终铣削精加工外,和粗加工摆头来实现初级铣削粗加工过程,还具备激光切割AC 摆头实现激光切割过程。
这是一种引人注目的改革,实现了在一台机床上既能铣削加工又能激光切割的柔性制造。
此复合加工设备具有一个标准的加工中心平台并提供独有的激光切割选择包。
其中铣削粗加工、铣削精加工和激光切割分别由3个A 轴摆头组成,他们共用一个C 轴,靠自动交换A 轴摆头来实现功能切换。
(2)五轴联动功能五坐标联动加工机床的特点有很多,如A 轴可以避开切削速度为零的条件;B 轴可缩短刀具长度;C 轴可加工不重新装卸就不能进行加工的呈突出形状的工件。
五轴联动智能加工系统的设计与实现
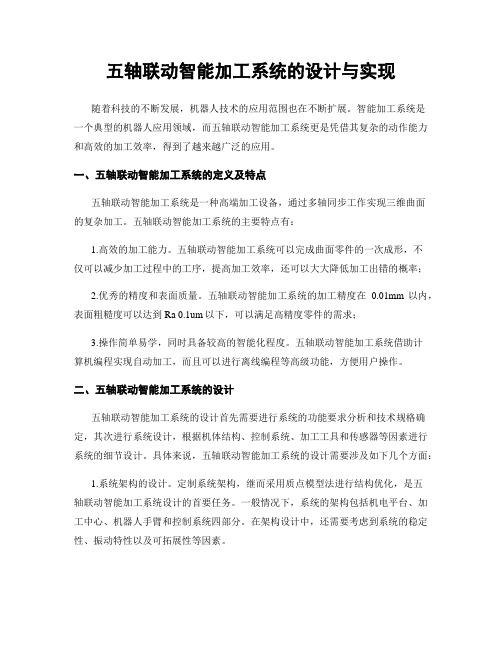
五轴联动智能加工系统的设计与实现随着科技的不断发展,机器人技术的应用范围也在不断扩展。
智能加工系统是一个典型的机器人应用领域,而五轴联动智能加工系统更是凭借其复杂的动作能力和高效的加工效率,得到了越来越广泛的应用。
一、五轴联动智能加工系统的定义及特点五轴联动智能加工系统是一种高端加工设备,通过多轴同步工作实现三维曲面的复杂加工。
五轴联动智能加工系统的主要特点有:1.高效的加工能力。
五轴联动智能加工系统可以完成曲面零件的一次成形,不仅可以减少加工过程中的工序,提高加工效率,还可以大大降低加工出错的概率;2.优秀的精度和表面质量。
五轴联动智能加工系统的加工精度在0.01mm以内,表面粗糙度可以达到Ra 0.1um以下,可以满足高精度零件的需求;3.操作简单易学,同时具备较高的智能化程度。
五轴联动智能加工系统借助计算机编程实现自动加工,而且可以进行离线编程等高级功能,方便用户操作。
二、五轴联动智能加工系统的设计五轴联动智能加工系统的设计首先需要进行系统的功能要求分析和技术规格确定,其次进行系统设计,根据机体结构、控制系统、加工工具和传感器等因素进行系统的细节设计。
具体来说,五轴联动智能加工系统的设计需要涉及如下几个方面:1.系统架构的设计。
定制系统架构,继而采用质点模型法进行结构优化,是五轴联动智能加工系统设计的首要任务。
一般情况下,系统的架构包括机电平台、加工中心、机器人手臂和控制系统四部分。
在架构设计中,还需要考虑到系统的稳定性、振动特性以及可拓展性等因素。
2.运动平台的设计。
运动平台是五轴联动智能加工系统的核心部件,它由基础、大小臂和转介轴等部分组成。
在设计运动平台的过程中,需要考虑到各个部分的匹配关系,以及运动轨迹的优化。
3.控制系统的设计。
五轴联动智能加工系统的控制系统是实现整个系统智能化的核心。
控制系统的设计应该借鉴现有先进的控制技术,例如PID算法、模糊控制、神经网络等,在系统稳定性和响应速度上做到更优。
- 1、下载文档前请自行甄别文档内容的完整性,平台不提供额外的编辑、内容补充、找答案等附加服务。
- 2、"仅部分预览"的文档,不可在线预览部分如存在完整性等问题,可反馈申请退款(可完整预览的文档不适用该条件!)。
- 3、如文档侵犯您的权益,请联系客服反馈,我们会尽快为您处理(人工客服工作时间:9:00-18:30)。
万方数据
2010年第1l期·工艺与装备·
床的x、y、z三个坐标的丝杠制成中心通孔,通人冷
却水,并对冷却水实施温度控制,使其在额定的温升
范围内变化。
中空丝杠冷却技术可以降低丝杠在切
削受力变形及快速移动过程中的热变形,保证机床
处于高精度运转状态。
同时配合使用高精度闭环控
制光栅尺,进一步提高了定位精度。
2.3双边重心驱动技术
该系列立式车铣复合加工中心的y轴为双驱动
结构,z轴为单驱动结构。
相对于y轴而言z轴滑
板质量较小且驱动力作用在中心位置,因此运动较
平稳;而在运动过程中l,轴需承载z轴的重量,故其
重心随Z轴的运动而不断地变化;若Y轴为单驱动
结构,在驱动力的作用下将会产生俯仰力矩和偏转
1.1,轴直线导轨2.立柱3.A轴刀架滑板装置4.A轴车铣7J塔力矩,在这两个力矩作用下,滑板在运动过程中将会5-中空滚珠丝杠副6·机内螺旋排屑装置7.【ⅡJ转工作台8·x轴转出现不可预知的变形和振动。
为了减小这种不确定台底座9·底座
的振动对加T的影响,基于重心驱动理论,采取了双
图1立式车铣复合,Jn3-中心的总体结构图
边驱动结构(图4)。
双边驱动的特点是在立柱的两
2关键技术侧对称施加驱动力,以便尽可能地减少驱动力臂产2.1轻量化设计生的影响。
应用双边重心驱动技术,提高了机床运为达到立式车铣复合加工中心高速移动部件的速动鬯速度黧塑速度:篓短了加!时间,擎善了毒募加度和加速度,并兼顾系统的高刚度和轻质量要求,对体
工质量和轮廓加工精度,延长了刀具的使用寿命心1。
积大、驱动要求高的运动部件一立柱单元,以结构强度、
刚度、固有频率等为约束,进行有限元分析及拓扑优化
设计(见图2,图3),使结构在满足高刚度要求的前提
下尽可能减轻移动的重量,以便减轻电机、液压系统、
丝杠、滑台等驱动部件的功率、强度要求。
优化设计后
的立柱变形量减少20%,重量减少220Kg。
图2立柱有限元分析结果
图3立柱拓扑优化前后的内部结构图
2.2滚珠丝杠中空冷却技术
在直线驱动轴上采用循环冷却技术的中空滚珠丝杠,使丝杠温升得到有效控制。
基本原理是将机
图4Y轴双边重心驱动结构
2.4双功能车铣转台
工作台采用力矩电机直接驱动的双功能车铣转台,这种转台可以连续回转、实现立式车削功能,也可实现分度定位、铣削插补等功能。
力矩电机直接驱动负载,省去了减速传动齿轮,把机床进给传动链的长度缩短为零,使其具有扭矩大、旋转平稳、转速高、效率高、结构简单、可靠性高等特点。
由于直驱力矩电动机本身就是高发热元件,如果散热不好,极易形成热量累积,导致自身和关联部件的温升,引起机床的热变形。
因此必须设计出高效的冷却系统将热量及时导出,否则将直接影响机床的加工精度、电机推力,甚至会烧毁电机。
车铣转台的另一热源产生于轴承和电机转子的高速旋转。
根据发热源和部件的热敏感性,在定子和转台本体之间设置了水冷循环系统,并在轴承附近安装了温度传感器,即可保持电机长时间工作温度变化小,从而保证转台的大
力矩和高精度。
万方数据
·工艺与装备·组合机床与自动化加工技术
际上也属前沿。
本课题的成功实施,不仅促进多
轴联动加工设备的设计与制造水平,而且为相关
T程和项目提供满足生产丁艺需求的高档复合加
工中心机床,满足复杂、精密零部件加工设备的批
量产业化需求,进而提升相关产品的技术水平、精
度稳定性、可靠性,增强市场竞争能力。
I.工作台2.轴承3.电机4.锁紧套5.接f16.编码器7.底座8.温度传感器
图5车铣转台结构简图
2.5摆头动力刀塔
摆头动力刀塔(A轴)是车铣复合加T中心的核
心部件,由A轴丁作台和刀具主轴两部分组成,其工
作特点是主轴铣削时动态旋转,车削时不转。
车削
时卸荷齿形联轴节将主轴固定到旋转壳体上,消除图6[黝刀塔
主轴轴承负载,提供防铰定位精度,并吸收切削力。
[1]王立平.关于国产数控机床发展的几点思考[J].航空刀具则由碟簧夹紧,液压释放,通过液压系统压力差制造技术,2010(4):51—52.
值监视刀具夹紧情况。
在换刀时利用压缩空气清洁[2]刘强,陈静,吴文静,等.高性能数控机床几项关键设计技主轴锥面,并采用迷宫式密封结构防止主轴受到污术的研究应用进展[J].航空制造技术,2009(5):42—45.染。
同时该刀具主轴E有外冷却和内冷却两个冷却[3]张耀满,蔡光起·李家霁·新型五坐标加-丁中心的结构设
液出口,分别可实现刀具的外冷却和内冷却。
计和分析[J]·机械制造,2005(12):20-21.
[4】朱育权,干学明,林晓萍.1CL50型机床立柱振动模态分
3结束语
析[J].西安|丁业大学学报,2007,27(3):215—217.该设备采用的一些技术在国内尚属空白,在国(编辑李秀敏)
(上接第73页)可以认为1、16、68、72、77变速器N一3挡同步器换捎性能稍逊,其余换挡性能优良。
对换挡性能稍逊的变速器进行N一3挡人_T换挡亦能感觉明显的不平顺现象,由此可见,可以用该换挡机械手对变速器同步器换挡性能进行测试,并可以得出优良质量的标准。
图6正态分布曲线图
4结束语
同步器是汽车机械式变速器的核心部件,其性能对汽车变速器以及汽车性能的提高具有重要的意
·82·义。
本文在对同步器工作原理分析的基础上引出同步器换挡冲量的概念,并对换挡机械手进行设计,试验结果表明,借助该换挡机械手用换挡冲量指标来评价同步器换挡性能是可行性,为今后做同步器性能测试试验提供技术支持。
[参考文献]
[1]何忠波,梁宪福,等.AMT换挡过程动力学建模及换挡品质影响因素分析[J].军械丁程学院学报,2004,16(6):45—49.
[2]陈宁,赵丁选,于微波.改善动力换挡变速箱换挡品质的研究[J].机床与液压,2004(10):29—31.
[3]赵世琴,黄宗益,陈明。
等.同步器换挡接合过程的数学模型[J].同济大学学报,1999,26(6):676—680.
[4]兰燕东.汽车同步器换挡性能的评价[C].汽车工程学会传动委员会第五届年会论文,1990.
[5]张为公,翟羽健,倪江生.汽车驾驶机器人换挡机械手的优化设计[J].中国机械工程,1995,6(1):36—38.[6]成崎.同步器换挡冲量计算方法初探[J】.綦齿传动,2002(2):11—16.
[7]陈家瑞.汽车构造(第二版)[M】.北京:机械工业出版社。
2005.
(编辑李秀敏)万方数据
VHT系列五轴联动立式车铣复合加工中心的设计
作者:高莹, 赵宏安, 董建军, GAO Ying, Zhao Hong-an, DONG Jian-jun 作者单位:大连机床(数控)股份有限公司,辽宁,大连,116620
刊名:
组合机床与自动化加工技术
英文刊名:MODULAR MACHINE TOOL & AUTOMATIC MANUFACTURING TECHNIQUE
年,卷(期):2010(11)
1.王立平关于国产数控机床发展的几点思考 2010(4)
2.刘强.陈静.吴文镜.袁松梅高性能数控机床几项关键设计技术的研究应用进展 2009(5)
3.张耀满.蔡光起.李家霁新型五坐标加工中心的结构设计和分析 2005(12)
4.朱育权.千学明.林晓萍1CL50型机床立柱振动模态分析 2007(3)
本文链接:/Periodical_zhjc201011024.aspx。