熔铸车间工艺流程
熔铸车间工艺流程
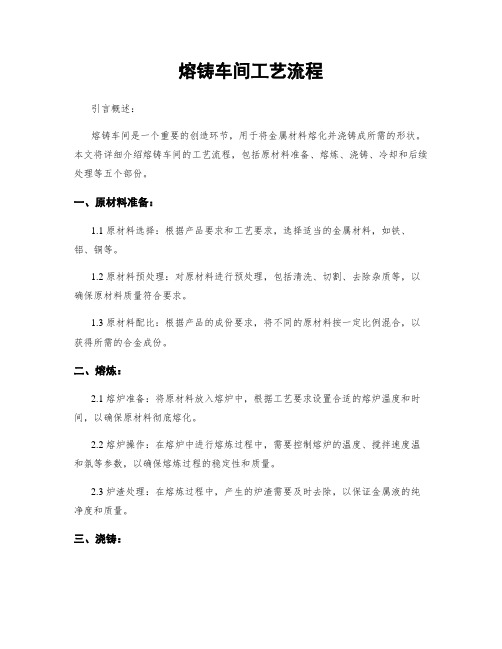
熔铸车间工艺流程引言概述:熔铸车间是一个重要的创造环节,用于将金属材料熔化并浇铸成所需的形状。
本文将详细介绍熔铸车间的工艺流程,包括原材料准备、熔炼、浇铸、冷却和后续处理等五个部份。
一、原材料准备:1.1 原材料选择:根据产品要求和工艺要求,选择适当的金属材料,如铁、铝、铜等。
1.2 原材料预处理:对原材料进行预处理,包括清洗、切割、去除杂质等,以确保原材料质量符合要求。
1.3 原材料配比:根据产品的成份要求,将不同的原材料按一定比例混合,以获得所需的合金成份。
二、熔炼:2.1 熔炉准备:将原材料放入熔炉中,根据工艺要求设置合适的熔炉温度和时间,以确保原材料彻底熔化。
2.2 熔炉操作:在熔炉中进行熔炼过程中,需要控制熔炉的温度、搅拌速度温和氛等参数,以确保熔炼过程的稳定性和质量。
2.3 炉渣处理:在熔炼过程中,产生的炉渣需要及时去除,以保证金属液的纯净度和质量。
三、浇铸:3.1 浇注系统准备:准备好浇注系统,包括浇注杯、浇注管、浇注口等,以确保金属液能够顺利流入模具。
3.2 浇注操作:将熔化的金属液从熔炉中倒入浇注杯,然后通过浇注管流入模具,控制浇注速度和角度,以获得所需的铸件形状。
3.3 模具冷却:待金属液充满模具后,需要进行冷却,以使铸件逐渐凝固,并保持所需的形状。
四、冷却:4.1 自然冷却:待铸件充分凝固后,进行自然冷却,以降低温度,使铸件达到可处理的状态。
4.2 机械冷却:为了加快冷却速度,可以采用机械冷却方法,如水冷却、风冷却等,以提高生产效率。
4.3 检验铸件质量:在冷却过程中,需要对铸件进行质量检验,包括尺寸、表面质量、内部缺陷等,以确保铸件符合要求。
五、后续处理:5.1 去除支撑材料:对于需要支撑材料的铸件,需要进行支撑材料的去除,以获得完整的铸件。
5.2 表面处理:根据产品要求,对铸件进行表面处理,如抛光、喷涂等,以提高铸件的外观质量和耐腐蚀性。
5.3 检验和包装:最后,对铸件进行最终的质量检验,包括外观、尺寸、材质等,然后进行包装,以便运输和储存。
熔铸车间工艺流程

熔铸车间工艺流程一、概述熔铸车间是金属制造企业中重要的生产环节之一,它负责将金属材料熔化并铸造成所需的产品。
本文将详细介绍熔铸车间的工艺流程,包括原料准备、熔炼、浇注、冷却和成品处理等环节。
二、原料准备1. 原料选择:根据产品要求,选择适当的金属材料作为原料,如铁、铝、铜等。
2. 原料清洁:对原料进行清洁处理,去除表面的杂质和氧化物,确保原料质量。
三、熔炼1. 熔炉准备:将原料放入熔炉中,并根据产品要求添加适量的合金元素。
2. 熔炉加热:启动熔炉加热系统,将熔炉内的原料加热至熔点以上,使其熔化。
3. 炉渣处理:在熔炉中形成的炉渣需要定期清理,以保证熔炼过程的顺利进行。
四、浇注1. 浇注模具准备:根据产品要求,选择适当的模具,并对其进行清洁和涂层处理。
2. 熔融金属倒入模具:将熔融的金属倒入模具中,确保金属充分填满模具的空腔。
3. 模具冷却:待金属冷却凝固后,将模具从浇注设备中取出,进行冷却处理。
五、冷却1. 自然冷却:将铸件放置在通风良好的区域,让其自然冷却至室温。
2. 机械冷却:对一些大型铸件,可以采用机械冷却设备进行加速冷却,以缩短冷却时间。
六、成品处理1. 去除毛刺:对冷却后的铸件进行去毛刺处理,以提高产品的表面质量。
2. 清洗和抛光:对铸件进行清洗和抛光处理,使其表面光滑、亮丽。
3. 检验和测试:对成品进行检验和测试,确保产品符合质量要求。
4. 包装和贮存:对合格的成品进行包装,并妥善贮存,以备发货或下一步加工使用。
七、安全措施1. 熔炉操作时需佩戴防护设备,如防火服、防护眼镜等。
2. 操作人员应接受相关培训,熟悉操作规程和应急处理措施。
3. 定期检查和维护设备,确保其正常运行和安全性。
4. 严格遵守相关环保法规,做好废渣和废气的处理工作。
以上即为熔铸车间工艺流程的详细描述。
在实际操作中,需要根据具体产品要求和生产设备的特点进行调整和优化。
同时,为确保生产过程的安全和产品质量的稳定性,需要严格遵守操作规程和安全措施,并定期进行设备维护和检查。
熔铸车间工艺流程

熔铸车间工艺流程一、工艺流程概述熔铸车间是一个关键的生产环节,主要用于将金属材料熔化并浇铸成特定形状的零件或者产品。
本文将详细介绍熔铸车间的工艺流程,包括原料准备、熔炼、浇铸、冷却和检验等环节。
二、原料准备1. 原料采购:根据生产需求,采购适当的金属材料,如铁、铝、铜等。
2. 原料检验:对采购的原料进行质量检验,确保其符合生产要求。
三、熔炼1. 熔炉准备:将原料送入熔炉,并根据要求设定炉温和熔炼时间。
2. 炉内熔化:通过高温加热,将原料熔化成液态金属。
3. 杂质处理:在熔化过程中,对液态金属进行除杂处理,以去除杂质温和泡。
4. 成份调整:根据产品要求,对液态金属的成份进行调整,以获得所需的合金成份。
四、浇铸1. 模具准备:根据产品的形状和尺寸,准备相应的模具。
2. 液态金属注入:将熔化的金属倒入模具中,确保金属充分填充整个模具空间。
3. 冷却:待金属冷却固化后,取出模具,得到铸件。
五、冷却处理1. 自然冷却:将铸件放置在通风良好的区域,自然冷却至室温。
2. 人工冷却:对于大型铸件或者特殊要求的产品,可采用人工冷却方法,如水冷却或者气体冷却。
六、检验与质量控制1. 外观检验:对铸件的表面进行外观检查,确保无明显缺陷或者损伤。
2. 尺寸检验:测量铸件的尺寸和几何形状,与设计要求进行比对。
3. 材料分析:对铸件进行化学成份分析,确保合金成份符合要求。
4. 物理性能测试:对铸件进行物理性能测试,如硬度、抗拉强度等。
七、包装与出库1. 包装:对合格的铸件进行包装,以防止在运输过程中受到损坏。
2. 出库:将包装好的铸件按照定单要求进行出库,以便交付给客户或者其他生产环节。
八、安全与环保措施1. 安全保护:车间内应配备必要的安全设施,如防护网、防护服等,确保员工的人身安全。
2. 废料处理:对产生的废料进行分类、处理和回收利用,以减少对环境的影响。
以上是熔铸车间的工艺流程的详细描述,每一个环节都需要严格按照规定操作,以确保产品质量和生产效率。
熔铸车间工艺流程

熔铸车间工艺流程一、工艺概述熔铸是一种常见的金属加工方法,用于创造各种金属制品。
熔铸车间是指进行金属熔化、浇铸和冷却等工艺的生产区域。
本文将详细介绍熔铸车间的工艺流程,包括原材料准备、熔炼、浇铸、冷却和后续处理等环节。
二、原材料准备1. 原材料选择:根据产品要求和工艺要求,选择适当的金属材料,如铁、铝、铜等。
2. 原材料检验:对原材料进行检验,确保其质量符合要求。
检验项目包括化学成份、物理性能等。
3. 原材料切割:将原材料按照工艺要求进行切割,以便后续的熔炼和浇铸。
三、熔炼1. 熔炉准备:准备熔炉,并根据工艺要求进行预热和清洁。
2. 熔炼操作:将切割好的原材料放入熔炉中,加热至熔点以上,使其熔化。
同时,根据需要添加合适的合金元素,以调整金属的性能。
3. 炉渣处理:在熔炼过程中,金属表面会形成一层炉渣。
需要定期清理炉渣,以保证金属的纯净度。
四、浇铸1. 模具准备:准备合适的模具,根据产品要求和工艺要求进行设计和创造。
2. 浇注操作:将熔化的金属倒入模具中,使其充满整个模具腔体。
同时,通过振动或者压力等方式,排除气泡,确保铸件质量。
3. 冷却:待金属冷却固化后,取出模具,得到所需的铸件。
五、冷却和后续处理1. 冷却:将铸件放置在适当的环境中,进行冷却。
冷却时间根据铸件的大小和材料的特性而定。
2. 除砂:待铸件彻底冷却后,进行除砂操作,将表面的砂粒清除,以便后续处理。
3. 精修:对铸件进行精修,包括切割、打磨、修整等操作,以达到产品的要求。
4. 检验:对铸件进行检验,包括外观检查、尺寸检查、力学性能测试等。
确保产品符合质量标准。
5. 表面处理:根据产品要求,进行表面处理,如喷漆、电镀等,以提高产品的外观和耐腐蚀性能。
6. 包装和出货:将成品进行包装,并按照客户要求进行标识和出货准备。
六、安全注意事项1. 操作人员必须穿戴适当的防护装备,包括耐高温手套、防护眼镜等。
2. 熔炉操作时,要注意火源和燃气的安全,避免发生火灾和爆炸事故。
熔铸车间工艺流程

熔铸车间工艺流程引言概述:熔铸车间是金属创造工业中至关重要的一环。
它涉及到将金属材料熔化并倒入模具中进行成型的过程。
本文将详细介绍熔铸车间的工艺流程,包括原料准备、熔炼、浇注、冷却和清理等五个部份。
一、原料准备:1.1 原料选择:根据产品要求,选择适合的金属材料,如铁、铝、铜等。
1.2 原料质检:对原料进行质量检验,包括外观检查、化学成份分析、机械性能测试等。
1.3 原料预处理:根据需要,对原料进行预处理,如切割、去除杂质、加热等。
二、熔炼:2.1 熔炉选择:根据原料种类和工艺要求,选择合适的熔炉,如电炉、燃炉等。
2.2 熔炉操作:将原料放入熔炉中,加热至熔点以上,使其熔化。
2.3 熔炼控制:控制熔炉温度、熔化时间和熔炼过程中的气氛,确保熔化过程的稳定和质量的控制。
三、浇注:3.1 模具准备:根据产品要求,选择合适的模具,并进行清洁和涂抹隔离剂。
3.2 浇注操作:将熔化的金属倒入模具中,确保金属充分填充模具腔体。
3.3 浇注控制:控制浇注速度、温度和压力,以确保产品的尺寸和表面质量。
四、冷却:4.1 自然冷却:待金属充分凝固后,将模具放置在自然环境中进行冷却。
4.2 水冷:对于一些需要快速冷却的产品,可采用水冷方法,加快冷却速度。
4.3 退火处理:对于一些需要改善材料性能的产品,可进行退火处理,消除内部应力并提高材料的韧性。
五、清理:5.1 剪切和研磨:将冷却后的产品从模具中取出,并进行剪切和研磨,去除余料和表面不平整。
5.2 清洗:对产品进行清洗,去除表面的污垢和残留物。
5.3 检验和包装:对产品进行质量检验,包括尺寸、外观和性能等方面的检测,然后进行包装,以便运输和储存。
结论:熔铸车间工艺流程是一个复杂而关键的过程,它直接影响到产品的质量和性能。
通过对原料准备、熔炼、浇注、冷却和清理等五个部份的详细阐述,我们可以更好地理解熔铸车间的工艺流程,并为提高产品质量和生产效率提供参考。
在实际操作中,需要严格按照工艺要求进行操作,并加强质量控制,以确保熔铸车间的正常运行和产品质量的稳定。
熔铸车间工艺流程

熔铸车间工艺流程熔铸车间是金属加工行业中的重要环节,其工艺流程对于产品质量和生产效率具有关键影响。
下面将详细介绍熔铸车间的工艺流程,包括原料准备、熔炼、浇注、冷却和后续处理等环节。
1. 原料准备熔铸车间的原料主要包括金属合金、熔剂和其他辅助材料。
在工艺流程开始前,需要对原料进行准备和检验。
首先,检查原料的质量和数量是否符合要求。
然后,根据产品的要求,进行合金的配比和混合。
同时,根据需要,添加熔剂和其他辅助材料,以提高熔化和浇注的效果。
2. 熔炼熔炼是熔铸车间的核心环节,主要是将原料加热至熔化状态,形成可浇注的液态金属。
熔炼设备通常采用电炉、电阻炉或者感应炉等。
在熔炼过程中,需要控制炉温、炉压和炉内气氛等参数,以确保熔炼的稳定性和金属的纯度。
同时,还需要对熔化金属进行搅拌和除渣,以提高金属的均匀性和纯净度。
3. 浇注浇注是将熔化金属倒入模具中,形成所需产品形状的过程。
在浇注前,需要对模具进行准备,包括涂抹模具释模剂、加热模具等。
然后,将熔化金属倒入模具中,通过重力或者压力,使金属充满整个模腔。
浇注过程需要控制浇注速度、温度和压力等参数,以确保产品的尺寸精度和表面质量。
4. 冷却浇注完成后,需要将模具中的金属冷却至室温,使其固化成为实体产品。
冷却过程的时间和方式取决于金属的类型和产品的尺寸。
通常,可以采用自然冷却或者水冷却的方式,加快冷却速度。
在冷却过程中,需要注意避免产生内部应力和缺陷,以确保产品的物理性能和机械性能。
5. 后续处理冷却完成后,产品需要进行后续处理,以提高其表面质量和机械性能。
后续处理的方式包括除毛刺、修整、热处理、表面处理和检验等。
除毛刺是去除产品表面的凹凸不平和毛刺,使其具有更好的外观。
修整是对产品进行尺寸修正,以满足设计要求。
热处理是通过加热和冷却的方式,改变产品的组织结构和硬度。
表面处理是对产品进行涂层或者镀层,以提高其耐腐蚀性和装饰性。
最后,对产品进行检验,包括尺寸检验、化学成份分析和物理性能测试等,以确保产品质量符合要求。
熔铸车间工艺流程

熔铸车间工艺流程引言概述:熔铸车间是金属加工行业中重要的环节之一。
熔铸工艺流程是将金属材料加热至熔点后,通过浇注到模具中冷却凝固,最终形成所需的金属制品。
本文将详细介绍熔铸车间工艺流程的五个大点,并分别从三至五个小点进行详细阐述。
正文内容:1. 原材料准备1.1 选择合适的金属材料:根据产品要求和性能要求,选择合适的金属材料,如铁、铜、铝等。
1.2 原材料分类和分选:对原材料进行分类和分选,确保质量和成份符合要求。
1.3 温度控制:控制原材料的温度,确保熔化时达到所需的熔点。
2. 熔炼和熔化2.1 熔炼设备准备:准备熔炼设备,如电炉、高频炉等,确保设备正常运行。
2.2 熔炼操作:将原材料放入熔炼设备中,通过加热使其熔化,并控制熔化温度和时间。
2.3 熔炼温度控制:根据金属材料的特性和要求,控制熔炼温度,确保熔化的金属材料符合要求。
3. 浇注和冷却3.1 模具准备:准备模具,包括选择合适的模具材料和制作模具。
3.2 浇注操作:将熔化的金属材料倒入模具中,确保浇注过程中不浮现气泡和杂质。
3.3 冷却和凝固:等待熔化的金属材料在模具中冷却和凝固,形成所需的金属制品。
4. 清理和处理4.1 模具清理:将已凝固的金属制品从模具中取出,并进行模具的清理和维护。
4.2 修整和处理:对冷却凝固后的金属制品进行修整和处理,如切割、打磨等,以满足产品要求。
4.3 检查和质量控制:对金属制品进行检查,确保产品质量符合要求,并进行必要的质量控制措施。
5. 包装和出库5.1 包装准备:准备适当的包装材料和包装工具,确保金属制品在包装过程中不受损。
5.2 包装操作:将金属制品进行包装,并标明相关信息,如产品型号、数量等。
5.3 出库和储存:将包装好的金属制品出库,并储存到指定的地方,以备后续使用或者销售。
总结:综上所述,熔铸车间工艺流程包括原材料准备、熔炼和熔化、浇注和冷却、清理和处理以及包装和出库五个大点。
在每一个大点中,我们详细阐述了三至五个小点,从而全面介绍了熔铸车间工艺流程的具体步骤和操作要点。
熔铸车间工艺流程

熔铸车间工艺流程一、概述熔铸车间是金属制造工艺中的重要环节,它涉及到金属的熔化、浇铸、冷却等工艺过程。
本文将详细介绍熔铸车间的工艺流程,包括原料准备、熔炼、浇铸、冷却和检验等环节。
二、原料准备1. 原料选择:根据产品要求和工艺要求,选择适当的金属原料,如铝、铁、铜等。
2. 原料检验:对原料进行化学成分分析、物理性能测试等,确保原料质量符合要求。
3. 原料处理:对原料进行破碎、筛分等处理,以便于后续的熔炼工艺。
三、熔炼1. 熔炼炉选择:根据产品要求和工艺要求,选择适当的熔炼炉,如电弧炉、感应炉等。
2. 熔炼操作:将原料加入熔炼炉中,控制熔炼温度和熔炼时间,使原料完全熔化。
3. 熔炼保护:在熔炼过程中,采取适当的保护措施,如惰性气体保护,防止金属氧化和污染。
四、浇铸1. 模具准备:根据产品要求,制作适当的模具,如砂型、金属模具等。
2. 浇注准备:将熔炼好的金属液体倒入浇注容器中,以便于后续的浇铸操作。
3. 浇铸操作:将金属液体从浇注容器中倒入模具中,控制浇注速度和浇注压力,确保金属液体充分填充模具。
五、冷却1. 冷却时间:根据产品要求和金属的凝固特性,确定适当的冷却时间,使金属逐渐凝固。
2. 冷却方式:根据产品要求和工艺要求,选择适当的冷却方式,如自然冷却、水冷却等。
3. 冷却控制:监测冷却过程中的温度变化,及时调整冷却条件,以确保金属的凝固质量。
六、检验1. 外观检验:对铸件的外观进行检查,包括表面光洁度、尺寸精度等。
2. 化学成分检验:对铸件进行化学成分分析,确保成分符合要求。
3. 物理性能检验:对铸件进行物理性能测试,如硬度测试、拉伸试验等。
七、总结熔铸车间的工艺流程包括原料准备、熔炼、浇铸、冷却和检验等环节。
通过严格控制每个环节的操作和参数,可以确保金属铸件的质量和性能符合产品要求。
在实际生产中,还应根据具体情况和不同产品的要求进行调整和优化,以提高生产效率和产品质量。
熔铸车间工艺流程
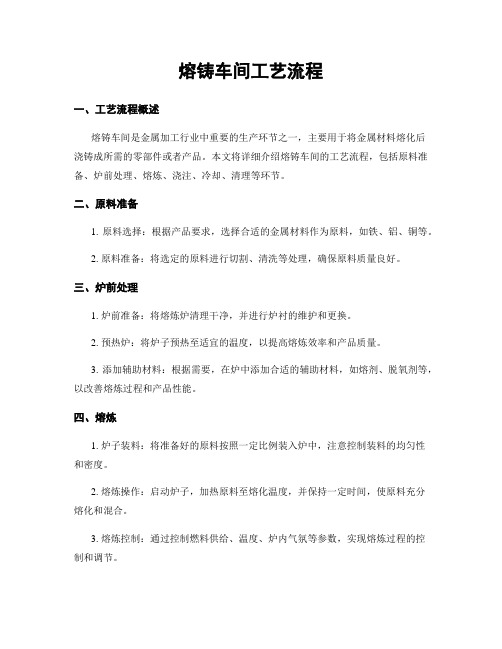
熔铸车间工艺流程一、工艺流程概述熔铸车间是金属加工行业中重要的生产环节之一,主要用于将金属材料熔化后浇铸成所需的零部件或者产品。
本文将详细介绍熔铸车间的工艺流程,包括原料准备、炉前处理、熔炼、浇注、冷却、清理等环节。
二、原料准备1. 原料选择:根据产品要求,选择合适的金属材料作为原料,如铁、铝、铜等。
2. 原料准备:将选定的原料进行切割、清洗等处理,确保原料质量良好。
三、炉前处理1. 炉前准备:将熔炼炉清理干净,并进行炉衬的维护和更换。
2. 预热炉:将炉子预热至适宜的温度,以提高熔炼效率和产品质量。
3. 添加辅助材料:根据需要,在炉中添加合适的辅助材料,如熔剂、脱氧剂等,以改善熔炼过程和产品性能。
四、熔炼1. 炉子装料:将准备好的原料按照一定比例装入炉中,注意控制装料的均匀性和密度。
2. 熔炼操作:启动炉子,加热原料至熔化温度,并保持一定时间,使原料充分熔化和混合。
3. 熔炼控制:通过控制燃料供给、温度、炉内气氛等参数,实现熔炼过程的控制和调节。
4. 检测和调整:定期对炉内温度、压力等参数进行检测,并根据检测结果进行必要的调整,以确保熔炼过程的稳定性和产品质量。
五、浇注1. 准备浇注工具:准备好合适的浇注工具,如浇注罐、浇注杯等。
2. 模具准备:将需要浇铸的模具进行清理和涂抹防粘剂等处理,以便顺利脱模。
3. 浇注操作:将熔化的金属液倒入模具中,注意控制浇注速度和角度,以避免产生气泡或者其他缺陷。
4. 冷却和固化:待金属液充分冷却后,模具可脱模,待产品固化后即可进入下一道工序。
六、冷却和清理1. 冷却:将浇注后的产品进行自然冷却或者采用冷却设备进行快速冷却,以确保产品的物理性能和尺寸稳定性。
2. 清理:将冷却后的产品进行清理,去除表面的氧化物、残渣等杂质,以提高产品的外观质量。
七、质量检验1. 外观检验:对产品的外观进行检查,如表面光洁度、尺寸偏差等。
2. 化学成份分析:通过化学分析方法,检测产品的化学成份是否符合要求。
熔铸车间工艺流程

熔铸车间工艺流程一、工艺流程概述熔铸车间是将金属原料加热至液态,然后通过浇铸或注射成型的工艺流程。
本文将详细介绍熔铸车间的工艺流程,包括原料准备、熔炼、浇铸或注射成型、冷却、清理和质检等环节。
二、原料准备1. 原料选择:根据产品要求选择合适的金属原料,如铁、铝、铜等。
2. 原料检验:对原料进行外观、化学成分、物理性质等方面的检验,确保原料质量符合要求。
3. 原料切割和配比:根据工艺要求,对原料进行切割和配比,以确保合金成分准确。
三、熔炼1. 加热炉准备:将炉子清理干净并预热,确保炉子达到适宜的工作温度。
2. 加入原料:按照配比将原料逐步加入炉中,注意控制加入速度和顺序。
3. 熔炼过程:通过高温加热,原料逐渐熔化并混合均匀,形成液态金属熔液。
4. 渣液分离:通过特定的工艺和设备,将熔液中的杂质和渣液分离出来,以提高金属纯度。
四、浇铸或注射成型1. 浇注模具准备:根据产品要求,准备合适的浇注模具,并进行清理和涂抹防粘剂等处理。
2. 浇注或注射过程:将熔炼好的金属熔液,通过浇注或注射的方式,倒入模具中。
3. 冷却固化:待金属熔液在模具中冷却,逐渐固化成型,形成所需的金属零件或产品。
五、冷却1. 自然冷却:待金属固化后,将模具放置在通风良好的区域,让其自然冷却至室温。
2. 辅助冷却:对于大型和厚壁产品,可以采用辅助冷却设备,如水冷却系统或风冷却系统,以加快冷却速度。
六、清理1. 模具清理:将已经冷却的模具进行清理,去除残留的金属渣滓和其他杂质。
2. 产品清理:对于成型的金属零件或产品,进行表面清理和抛光处理,以提高外观质量。
七、质检1. 外观检查:对成型的金属零件或产品进行外观检查,确保表面光滑、无瑕疵。
2. 尺寸检测:使用测量工具对产品的尺寸进行检测,确保尺寸准确。
3. 化学成分检验:取样并进行化学成分分析,确保金属材料的成分符合要求。
4. 物理性能测试:对产品进行物理性能测试,如强度、硬度等指标的测定。
熔铸车间工艺流程
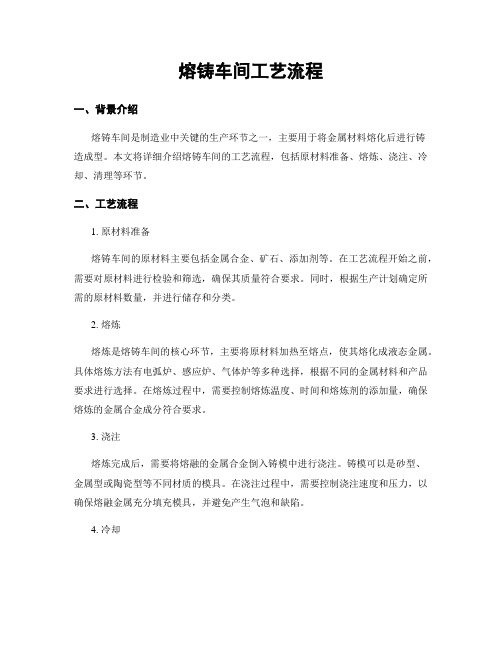
熔铸车间工艺流程一、背景介绍熔铸车间是制造业中关键的生产环节之一,主要用于将金属材料熔化后进行铸造成型。
本文将详细介绍熔铸车间的工艺流程,包括原材料准备、熔炼、浇注、冷却、清理等环节。
二、工艺流程1. 原材料准备熔铸车间的原材料主要包括金属合金、矿石、添加剂等。
在工艺流程开始之前,需要对原材料进行检验和筛选,确保其质量符合要求。
同时,根据生产计划确定所需的原材料数量,并进行储存和分类。
2. 熔炼熔炼是熔铸车间的核心环节,主要将原材料加热至熔点,使其熔化成液态金属。
具体熔炼方法有电弧炉、感应炉、气体炉等多种选择,根据不同的金属材料和产品要求进行选择。
在熔炼过程中,需要控制熔炼温度、时间和熔炼剂的添加量,确保熔炼的金属合金成分符合要求。
3. 浇注熔炼完成后,需要将熔融的金属合金倒入铸模中进行浇注。
铸模可以是砂型、金属型或陶瓷型等不同材质的模具。
在浇注过程中,需要控制浇注速度和压力,以确保熔融金属充分填充模具,并避免产生气泡和缺陷。
4. 冷却浇注完成后,需要等待熔融金属在模具中冷却凝固。
冷却时间的长短取决于金属合金的性质和产品要求。
冷却过程中,需要控制环境温度和湿度,以确保产品的尺寸精度和物理性能。
5. 清理冷却凝固后,需要将铸件从模具中取出,并进行清理和修整。
清理包括去除模具残留物、切割余料和修复表面缺陷等。
同时,还需要对铸件进行质量检验,确保其符合产品要求。
6. 后续处理根据产品要求,铸件可能需要进行后续处理,如热处理、机械加工、表面处理等。
这些处理环节可以提高产品的强度、硬度和表面质量,以满足客户的需求。
三、数据示例1. 原材料准备- 金属合金:不锈钢、铝合金、铜合金等- 矿石:铁矿石、铜矿石等- 添加剂:碳素、硅等2. 熔炼- 熔炼方法:电弧炉- 熔炼温度:1500℃- 熔炼时间:2小时- 熔炼剂:石墨、石英等3. 浇注- 铸模:砂型- 浇注速度:10 kg/s- 浇注压力:0.5 MPa4. 冷却- 冷却时间:24小时- 环境温度:25℃- 环境湿度:50%5. 清理- 清理方法:机械清理、喷砂- 修整方法:切割、打磨、抛光- 质量检验:尺寸测量、无损检测四、总结熔铸车间的工艺流程涵盖了原材料准备、熔炼、浇注、冷却、清理等环节。
熔铸车间工艺流程

熔铸车间工艺流程熔铸车间是金属加工工厂中的重要环节,它涉及到金属材料的熔化和铸造过程。
本文将详细介绍熔铸车间的工艺流程,包括原料准备、熔炼、浇注、冷却和后续处理等环节。
一、原料准备熔铸车间的原料主要包括金属合金、熔剂和辅助材料。
在开始熔炼之前,首先需要对原料进行检验和筛选,确保其质量符合要求。
然后,按照配比要求将不同的原料准备好,以便后续的熔炼过程中使用。
二、熔炼1. 熔炉准备:熔炉是进行金属熔炼的设备,需要提前进行清洁和加热,以确保熔炉内部的温度和环境符合熔炼要求。
2. 加料:将准备好的原料按照配比要求逐步加入熔炉中,注意控制加料的速度和顺序,以确保熔炼过程的稳定性和均匀性。
3. 加热熔化:启动熔炉加热系统,将原料加热至熔点以上,使其完全熔化,并保持一定的熔化温度,以便后续的浇注过程。
三、浇注1. 浇注模具准备:根据产品的要求,选择合适的模具,并进行清洁和涂抹防粘剂等处理,以确保浇注过程的顺利进行。
2. 浇注操作:将熔化的金属倒入模具中,注意控制浇注速度和角度,以避免产生气泡和杂质,同时确保金属充分填充模具的每个角落。
3. 冷却:待金属在模具中冷却凝固后,将模具打开,取出铸件。
在冷却过程中,可以采取一些措施,如水冷、风冷等,以加快冷却速度和提高铸件的质量。
四、后续处理1. 除砂:将铸件从模具中取出后,需要进行除砂处理,以去除表面的砂粒和其它杂质。
2. 修整:根据产品要求,对铸件进行修整和加工,如切割、修边、打磨等,以使其达到设计要求的尺寸和表面质量。
3. 热处理:对某些金属铸件进行热处理,以改善其力学性能和组织结构。
4. 检验:对铸件进行质量检验,包括外观检查、尺寸测量、材质分析等,以确保其符合产品要求和标准。
5. 包装和出库:对合格的铸件进行包装,并按照订单要求进行出库。
总结:熔铸车间的工艺流程包括原料准备、熔炼、浇注、冷却和后续处理等环节。
通过严格控制每个环节的操作和质量要求,可以生产出符合产品要求的高质量铸件。
熔铸车间工艺流程
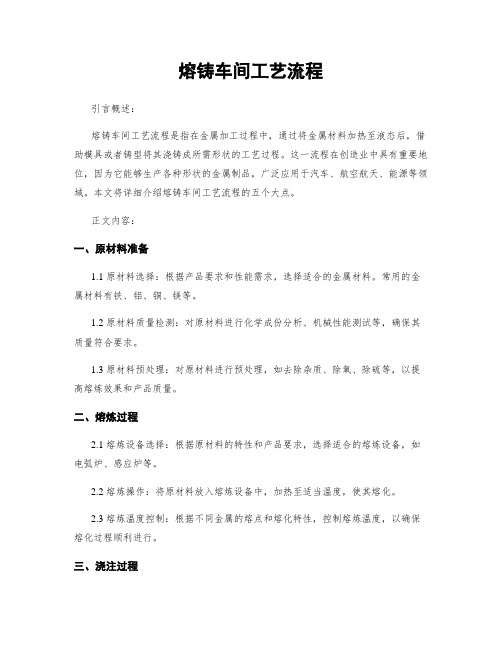
熔铸车间工艺流程引言概述:熔铸车间工艺流程是指在金属加工过程中,通过将金属材料加热至液态后,借助模具或者铸型将其浇铸成所需形状的工艺过程。
这一流程在创造业中具有重要地位,因为它能够生产各种形状的金属制品,广泛应用于汽车、航空航天、能源等领域。
本文将详细介绍熔铸车间工艺流程的五个大点。
正文内容:一、原材料准备1.1 原材料选择:根据产品要求和性能需求,选择适合的金属材料。
常用的金属材料有铁、铝、铜、镁等。
1.2 原材料质量检测:对原材料进行化学成份分析、机械性能测试等,确保其质量符合要求。
1.3 原材料预处理:对原材料进行预处理,如去除杂质、除氧、除硫等,以提高熔炼效果和产品质量。
二、熔炼过程2.1 熔炼设备选择:根据原材料的特性和产品要求,选择适合的熔炼设备,如电弧炉、感应炉等。
2.2 熔炼操作:将原材料放入熔炼设备中,加热至适当温度,使其熔化。
2.3 熔炼温度控制:根据不同金属的熔点和熔化特性,控制熔炼温度,以确保熔化过程顺利进行。
三、浇注过程3.1 铸型设计:根据产品要求和形状复杂程度,设计合适的铸型。
3.2 铸型制备:根据设计要求,制作铸型,通常采用砂型、金属型等。
3.3 浇注操作:将熔化的金属倒入铸型中,使其充满整个铸型腔体。
3.4 冷却处理:待金属冷却凝固后,取出铸件,进行后续加工处理。
四、产品加工4.1 除砂:将铸件从铸型中取出后,进行除砂处理,去除铸件表面的砂粒。
4.2 精密加工:根据产品要求,对铸件进行精密加工,如铣削、车削、钻孔等。
4.3 热处理:根据产品要求,进行热处理,如淬火、回火等,以改善铸件的力学性能。
五、质量检测5.1 尺寸检测:对铸件的尺寸进行检测,确保其符合设计要求。
5.2 化学成份分析:对铸件进行化学成份分析,检测其成份是否符合要求。
5.3 机械性能测试:对铸件进行拉伸、冲击等力学性能测试,评估其强度和韧性。
总结:熔铸车间工艺流程是创造业中重要的工艺过程,它包括原材料准备、熔炼过程、浇注过程、产品加工和质量检测。
熔铸车间工艺流程

熔铸车间工艺流程一、工艺流程概述熔铸车间是创造业中重要的生产环节之一,主要用于将金属材料熔化后浇铸成所需的零件或者产品。
本文将详细介绍熔铸车间的工艺流程,包括原材料准备、熔炼、铸造、冷却、清洁和检验等环节。
二、原材料准备1. 原材料选择:根据产品要求和工艺要求,选择适合的金属材料,如铁、铜、铝等。
2. 原材料检验:对原材料进行外观检查、化学成份分析和物理性能测试,确保原材料符合要求。
3. 原材料切割和加工:根据产品要求,将原材料切割成合适的尺寸,并进行必要的加工处理,如去除氧化层等。
三、熔炼1. 熔炼设备准备:确保熔炼设备干净、无杂质,并按照工艺要求进行预热。
2. 加热熔炼:将预处理好的原材料放入熔炼设备中,通过高温加热使其熔化。
3. 炉渣处理:在熔炼过程中,炉渣会产生,需要定期清理和处理,以保证熔炼质量。
四、铸造1. 模具准备:根据产品要求,选择合适的模具,并进行清洁和涂抹隔离剂等处理。
2. 熔融金属倒入模具:将熔融的金属倒入模具中,确保金属充分填充模具的每一个部份。
3. 冷却和固化:待金属在模具中冷却和固化后,取出模具,得到所需的铸件。
五、冷却1. 自然冷却:将铸件放置在通风良好的区域,让其自然冷却至室温。
2. 水冷却:对于某些需要快速冷却的铸件,可以采用水冷却的方式,加速冷却过程。
六、清洁1. 去除模具残留物:使用合适的工具和方法,将铸件表面的模具残留物清除干净。
2. 去除氧化层:对于铸件表面产生的氧化层,可以通过化学处理或者机械研磨等方式进行去除。
3. 清洗和除油:使用清洁剂和除油剂对铸件进行清洗,去除表面的污垢和油脂。
七、检验1. 外观检查:对铸件的表面进行目测检查,检查是否有裂纹、气孔、缺陷等。
2. 尺寸检验:使用测量工具对铸件的尺寸进行检测,确保其符合产品要求。
3. 物理性能测试:对铸件进行硬度测试、拉伸测试、冲击测试等,验证其物理性能是否达标。
八、记录和报告在整个熔铸车间工艺流程中,需要及时记录各个环节的数据和结果,并进行统计和分析,以便于工艺改进和质量控制。
熔铸车间工艺流程
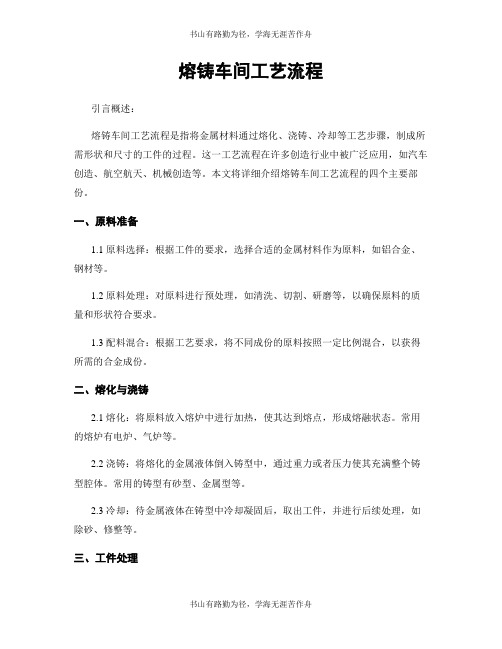
熔铸车间工艺流程引言概述:熔铸车间工艺流程是指将金属材料通过熔化、浇铸、冷却等工艺步骤,制成所需形状和尺寸的工件的过程。
这一工艺流程在许多创造行业中被广泛应用,如汽车创造、航空航天、机械创造等。
本文将详细介绍熔铸车间工艺流程的四个主要部份。
一、原料准备1.1 原料选择:根据工件的要求,选择合适的金属材料作为原料,如铝合金、钢材等。
1.2 原料处理:对原料进行预处理,如清洗、切割、研磨等,以确保原料的质量和形状符合要求。
1.3 配料混合:根据工艺要求,将不同成份的原料按照一定比例混合,以获得所需的合金成份。
二、熔化与浇铸2.1 熔化:将原料放入熔炉中进行加热,使其达到熔点,形成熔融状态。
常用的熔炉有电炉、气炉等。
2.2 浇铸:将熔化的金属液体倒入铸型中,通过重力或者压力使其充满整个铸型腔体。
常用的铸型有砂型、金属型等。
2.3 冷却:待金属液体在铸型中冷却凝固后,取出工件,并进行后续处理,如除砂、修整等。
三、工件处理3.1 精修:对浇铸后的工件进行修整,去除可能存在的缺陷,如气孔、夹杂等。
3.2 热处理:根据工件的要求,进行热处理,如淬火、回火等,以改善工件的力学性能和组织结构。
3.3 检测:对工件进行各种检测,如尺寸检测、化学成份分析、无损检测等,以确保工件的质量符合要求。
四、成品加工与质检4.1 成品加工:对工件进行机械加工,如铣削、车削等,以获得最终的形状和尺寸。
4.2 表面处理:对工件进行表面处理,如喷涂、电镀等,以提高工件的表面质量和耐蚀性。
4.3 质量检测:对成品进行全面的质量检测,包括外观检查、物理性能测试等,以确保产品的质量符合标准。
总结:熔铸车间工艺流程是一个复杂且关键的创造过程,其中的每一个环节都需要严格控制和操作。
通过原料准备、熔化与浇铸、工件处理以及成品加工与质检的四个部份,可以确保最终产品的质量和性能达到要求。
在实际应用中,需要根据具体的工件要求和材料特性,进行相应的工艺调整和优化,以提高生产效率和产品质量。
熔铸车间工艺流程
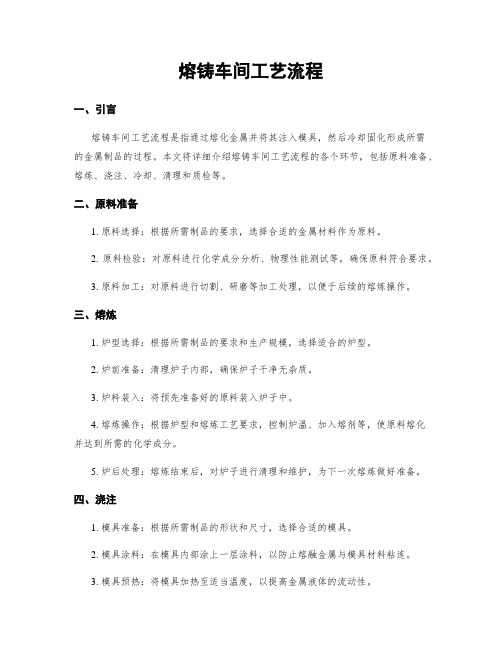
熔铸车间工艺流程一、引言熔铸车间工艺流程是指通过熔化金属并将其注入模具,然后冷却固化形成所需的金属制品的过程。
本文将详细介绍熔铸车间工艺流程的各个环节,包括原料准备、熔炼、浇注、冷却、清理和质检等。
二、原料准备1. 原料选择:根据所需制品的要求,选择合适的金属材料作为原料。
2. 原料检验:对原料进行化学成分分析、物理性能测试等,确保原料符合要求。
3. 原料加工:对原料进行切割、研磨等加工处理,以便于后续的熔炼操作。
三、熔炼1. 炉型选择:根据所需制品的要求和生产规模,选择适合的炉型。
2. 炉前准备:清理炉子内部,确保炉子干净无杂质。
3. 炉料装入:将预先准备好的原料装入炉子中。
4. 熔炼操作:根据炉型和熔炼工艺要求,控制炉温、加入熔剂等,使原料熔化并达到所需的化学成分。
5. 炉后处理:熔炼结束后,对炉子进行清理和维护,为下一次熔炼做好准备。
四、浇注1. 模具准备:根据所需制品的形状和尺寸,选择合适的模具。
2. 模具涂料:在模具内部涂上一层涂料,以防止熔融金属与模具材料粘连。
3. 模具预热:将模具加热至适当温度,以提高金属液体的流动性。
4. 浇注操作:将熔融金属倒入模具中,控制浇注速度和温度,确保金属液体充分填充模具的空腔。
5. 冷却:待金属液体冷却固化后,取出模具,得到所需的金属制品。
五、冷却和清理1. 冷却时间:根据金属制品的厚度和形状,确定适当的冷却时间。
2. 冷却方式:可以采用自然冷却或辅助冷却设备,以加快冷却速度。
3. 清理工艺:将冷却后的金属制品进行切割、研磨、抛光等,以去除可能存在的缺陷和表面不平整。
六、质检1. 外观检查:对金属制品的表面进行目测,检查是否存在瑕疵、裂纹等问题。
2. 尺寸检测:使用测量工具对金属制品的尺寸进行精确测量,确保符合要求。
3. 化学成分分析:取样金属制品,进行化学成分分析,确保符合设计要求。
4. 物理性能测试:对金属制品进行硬度、拉伸强度等物理性能测试,确保符合要求。
熔铸车间工艺流程

熔铸车间工艺流程一、工艺流程概述熔铸车间是金属制品生产过程中至关重要的一环。
其主要工艺流程包括原料准备、熔炼、浇注、冷却、清理和检验等环节。
本文将详细介绍熔铸车间工艺流程的每个环节。
二、原料准备1. 原料选择:根据产品要求,选择合适的原料,如金属合金、矿石等。
2. 原料预处理:对原料进行清洗、筛选、破碎等处理,以去除杂质和提高原料质量。
3. 配料:按照一定比例将不同原料混合,以获得所需的合金成分。
三、熔炼1. 熔炉选择:根据产品要求和原料特性,选择适合的熔炉类型,如电弧炉、感应炉等。
2. 熔炉预热:在熔炉投入原料前,对熔炉进行预热,以提高熔炉的工作效率和延长使用寿命。
3. 加料:将预处理好的原料逐步加入熔炉中,控制加料速度和顺序,以保证熔炉内温度和合金成分的稳定。
4. 熔炼过程控制:监控熔炉内温度、压力和气氛等参数,根据需要进行调整,以确保熔炼过程顺利进行。
5. 炉渣处理:在熔炼过程中,产生的炉渣需要及时清理和处理,以保持熔炼环境的清洁。
四、浇注1. 浇注前准备:准备好浇注工具、模具等设备,并对其进行清洁和检查。
2. 浇注温度控制:根据产品要求和合金特性,控制熔融金属的温度,以确保浇注过程的成功。
3. 浇注方式选择:根据产品形状和尺寸,选择合适的浇注方式,如重力浇注、压力浇注等。
4. 浇注过程控制:控制浇注速度和浇注压力,以避免产生气孔、缩松等缺陷,确保产品质量。
五、冷却1. 冷却介质选择:根据产品材料和形状,选择合适的冷却介质,如水、空气等。
2. 冷却时间控制:根据产品要求和合金特性,控制冷却时间,以确保产品达到所需的力学性能和尺寸精度。
3. 冷却过程监控:监测冷却过程中的温度变化和应力分布,及时采取措施,以避免产生裂纹和变形等问题。
六、清理1. 除渣:将浇注后产生的炉渣进行清理,以保持产品表面的光洁度和质量。
2. 毛刺去除:对产品表面的毛刺进行去除,以提高产品的外观质量。
3. 清洗:对产品进行清洗,去除表面的油污和杂质,以便后续处理和检验。
熔铸车间工艺流程
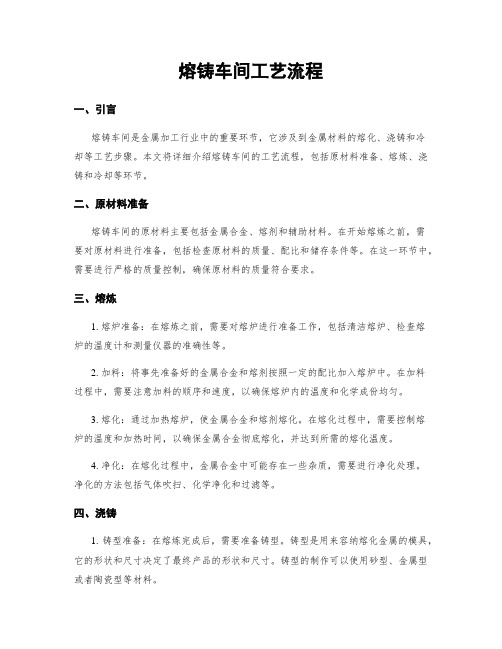
熔铸车间工艺流程一、引言熔铸车间是金属加工行业中的重要环节,它涉及到金属材料的熔化、浇铸和冷却等工艺步骤。
本文将详细介绍熔铸车间的工艺流程,包括原材料准备、熔炼、浇铸和冷却等环节。
二、原材料准备熔铸车间的原材料主要包括金属合金、熔剂和辅助材料。
在开始熔炼之前,需要对原材料进行准备,包括检查原材料的质量、配比和储存条件等。
在这一环节中,需要进行严格的质量控制,确保原材料的质量符合要求。
三、熔炼1. 熔炉准备:在熔炼之前,需要对熔炉进行准备工作,包括清洁熔炉、检查熔炉的温度计和测量仪器的准确性等。
2. 加料:将事先准备好的金属合金和熔剂按照一定的配比加入熔炉中。
在加料过程中,需要注意加料的顺序和速度,以确保熔炉内的温度和化学成份均匀。
3. 熔化:通过加热熔炉,使金属合金和熔剂熔化。
在熔化过程中,需要控制熔炉的温度和加热时间,以确保金属合金彻底熔化,并达到所需的熔化温度。
4. 净化:在熔化过程中,金属合金中可能存在一些杂质,需要进行净化处理。
净化的方法包括气体吹扫、化学净化和过滤等。
四、浇铸1. 铸型准备:在熔炼完成后,需要准备铸型。
铸型是用来容纳熔化金属的模具,它的形状和尺寸决定了最终产品的形状和尺寸。
铸型的制作可以使用砂型、金属型或者陶瓷型等材料。
2. 浇注:将熔化金属倒入铸型中,使其充满整个铸型腔。
在浇注过程中,需要控制浇注速度和温度,以防止金属在浇注过程中产生气孔或者裂纹。
3. 冷却:在金属倒入铸型后,需要等待一定的时间,让金属冷却固化。
冷却时间的长短取决于金属的类型和铸型的尺寸等因素。
在冷却过程中,需要控制冷却速度和温度,以确保最终产品的质量。
五、产品处理1. 脱模:在铸造完成后,需要将铸型从金属产品上取下。
脱模的方法可以使用机械力、化学溶解或者热处理等。
2. 修整:在脱模后,金属产品可能存在一些毛刺、气孔或者不平整的表面。
需要对产品进行修整,包括研磨、抛光和切割等。
3. 检验:对修整后的产品进行质量检验,包括外观检查、尺寸测量和材料成份分析等。
熔铸车间工艺流程

熔铸车间工艺流程熔铸车间是金属加工行业中至关重要的环节之一,它涉及到金属材料的熔化、浇铸、冷却等一系列工艺流程。
本文将详细介绍熔铸车间的工艺流程,包括原料准备、熔炼、浇铸、冷却和检验等环节。
一、原料准备熔铸车间的原料主要包括金属合金、矿石、石墨等。
在开始熔铸工艺之前,首先需要对原料进行准备。
原料的准备包括筛选、称重、配比等工作。
合理的原料配比是保证产品质量的关键。
二、熔炼熔炼是熔铸车间的核心工艺环节。
在熔炼过程中,原料被加热至其熔点以上,使其熔化成液态金属。
常用的熔炼设备包括电炉、高频感应炉等。
熔炼温度和时间的控制对于产品质量具有重要影响。
三、浇铸熔炼完成后,液态金属被倒入预先准备好的铸型中进行浇铸。
铸型可以是砂型、金属型等不同类型。
浇铸时要注意控制浇注速度和温度,以避免产生缺陷,确保产品的准确形状和尺寸。
四、冷却浇铸完成后,需要对铸件进行冷却。
冷却的方式可以是自然冷却或者通过水冷等方式进行加速冷却。
冷却的时间和速度对于产品的组织结构和性能有着重要影响,需要根据具体产品要求进行合理控制。
五、清理和检验冷却完成后,铸件需要进行清理和检验。
清理包括去除铸件表面的氧化物、砂粒等杂质。
检验则是通过外观检查、尺寸测量、力学性能测试等手段,对铸件进行质量检测。
惟独通过检验合格的产品才干进入下一道工序。
六、包装和出货经过清理和检验的合格产品将进行包装,以保证在运输过程中不受损。
包装可以采用木箱、纸箱等不同形式。
包装完成后,产品将被装车并出货。
七、设备维护和安全措施熔铸车间的设备维护和安全措施是保证工艺流程正常运行和员工安全的重要环节。
定期对熔炼设备进行检修和保养,确保其正常运行。
同时,要加强安全教育和培训,提高员工的安全意识,严格执行操作规程,防止事故的发生。
总结:熔铸车间工艺流程涉及到原料准备、熔炼、浇铸、冷却、检验、包装和出货等一系列环节。
每一个环节都需要严格控制和操作,以保证产品的质量和安全。
同时,设备维护和安全措施也是熔铸车间工作的重要方面。
熔铸车间工艺流程

熔铸车间工艺流程引言概述:熔铸车间是金属加工工业中至关重要的环节之一。
它涉及到将金属材料加热至液态状态,然后倒入模具中进行冷却和凝固,最终得到所需的金属制品。
本文将详细介绍熔铸车间的工艺流程,以帮助读者更好地了解这一重要的生产环节。
一、原料准备1.1 原材料选择:根据所需制品的要求,选择适当的金属材料。
常用的金属材料包括铁、铜、铝、锡等。
1.2 原料质量检查:对原材料进行质量检查,包括外观检查、化学成分分析、物理性能测试等,确保原材料符合工艺要求。
1.3 原料预处理:根据需要,对原材料进行预处理,如切割、研磨、清洗等,以便于后续的熔炼和铸造过程。
二、熔炼过程2.1 熔炼炉选择:根据熔炼的金属材料和工艺要求,选择合适的熔炼炉,常见的熔炼炉有电弧炉、感应炉等。
2.2 熔炼操作:将原材料放入熔炼炉中,通过加热使其达到液态状态。
在熔炼过程中,需要控制温度、搅拌熔体、除去杂质等。
2.3 熔炼结束处理:熔炼结束后,对熔体进行处理,如除去浮渣、调整化学成分等,以得到符合要求的熔体。
三、铸造过程3.1 模具准备:根据所需制品的形状和尺寸,选择合适的模具,并进行模具准备工作,如涂抹模具释模剂、安装模具芯等。
3.2 熔体倒注:将熔体倒入模具中,注意控制倒注速度、温度等参数,以确保熔体充分填充模具腔体,并避免产生气泡和缺陷。
3.3 冷却凝固:待熔体充分填充模具后,等待熔体冷却凝固,以得到所需的金属制品。
冷却时间和方式会根据金属材料的特性和制品要求进行调整。
四、后处理4.1 模具拆卸:待金属制品冷却凝固后,拆卸模具,取出金属制品。
4.2 清理和修整:对金属制品进行清理和修整工作,如去除余渣、修整表面等,以提高制品的质量和外观。
4.3 检验和质量控制:对金属制品进行检验,包括尺寸、外观、力学性能等方面的检测,确保制品符合要求。
五、产品交付5.1 包装和标识:对金属制品进行包装,并进行标识,以便于运输和使用。
5.2 存储和运输:将金属制品存储在适当的环境中,以防止腐蚀和损坏,并进行安全可靠的运输。
- 1、下载文档前请自行甄别文档内容的完整性,平台不提供额外的编辑、内容补充、找答案等附加服务。
- 2、"仅部分预览"的文档,不可在线预览部分如存在完整性等问题,可反馈申请退款(可完整预览的文档不适用该条件!)。
- 3、如文档侵犯您的权益,请联系客服反馈,我们会尽快为您处理(人工客服工作时间:9:00-18:30)。
宝鼎铝业熔铸车间工艺操作规程
一、内容与适用范围
1.本工艺操作规程适用于熔铸车间铸造6063合金直径89-178mm的铸棒要求。
二、生产工艺流程
1.铝合金的熔炼是铸棒生产过程中的主要工序,是所需要优质铝棒的关键,是铸棒生产质量控制的关键环节,工艺流程如下:
原材料及辅助材料的选择→配料计算→装炉→燃烧熔化→搅拌打渣→加硅镁→精炼打渣→炉前分析→调整成份、温度→二次精炼及除气→打渣→静置→分析→合格后铸棒。
三、工序工艺及操作规程
所使用的铝锭、镁锭中间合金及辅助材料等应按公司标准的要求,所使用的各种回炉料成份应清楚,干燥洁净。
1.各种合金配料必须符合本公司铝棒成份的标准要求,镁、硅待铝水达到740℃时,把渣扒干净后可直接加入铝水中,没炉次的各种炉料必须准确过磅记录。
2.装炉前确保设备正常运行,待炉料熔化后,温度达到740℃时,把火、风机关上,打干净炉内铝渣,投入外购炉料,并搅拌,尽量把烧损率降低。
铝液不够温时再开大火熔炼,并注意炉内烧灰,并随时准备打渣,尽量减少铁元素,待炉料加入约80%时应搅拌均匀,提取炉前分析,再按成份进行搭配。
待炉内温度达到730℃-750℃时把炉内所有杂质和铝渣清理干净,加入硅、镁,待硅镁熔化后,加入打渣剂、精炼剂精炼,完成后把铝液上面的渣、杂质打干净,再做炉前分析,结果出来后,测试温度是否达到车间要求,调整好后根据分析结果进行各元素的搭配,并进行二次精炼,分析结果合格后静止20分钟以上方
可铸棒。
3.铸棒前先检查好结晶器、水压、升降盘、电机、开关等是否正常。
确保无误后才可铸棒,吹干引锭头的积水和杂质,再将升降盘开到固定好的位置并检查有无反水现象,接好流槽并把分流盘打扫干净,装好滤布,防止杂质流入铝棒。
在打开出水口之前先启动冷却水泵,关小水套阀门,打开减压水阀门,待铝液流到各分盘的每个模具后再把减压水阀门慢慢关好,把连接水盘的水阀全部打开,进行按温度及车速的参数成对比把升降盘启动慢慢下降,在铸棒是发现表面不光滑的应及时堵塞。
铸棒是尽量不要翻动铝液,以免杂质和空气的流入,铸棒完成后,每炉次应取样做低倍试验分析,取样应切头,切尾长度≥100mm,厚度20-25mm。
4.锯棒前检查好设备,按规定的长度要求进行锯切,长短差不大于±0.2mm,按尺寸规格要求放置,不能混放,对表面不光,弯曲的不合格棒要分开放置,并如实的把炉号、规格、日期写在铝棒上。
5.熔铸车间的生产管理必须有计划、有措施、有监督检查,根据实际情况的变化,更新措施方案。
起草人:刘加宝
审核人:刘加宝
批准人:
宝鼎铝业有限公司
2012年9 月1日。