悬 空 埋 弧 焊 工 艺
埋弧焊的焊接工艺

埋弧焊的焊接工艺埋弧焊(Submerged Arc Welding,SAW)是一种高效、稳定、经济的电弧焊接工艺。
它采用单面自动焊接技术,焊丝和焊接区域被埋在焊接熔渣中,以保护焊接区域免受空气污染。
埋弧焊接可用于生产钢板、管道、轮胎以及其他工业产品。
埋弧焊接的特点1. 高效:埋弧焊接速度快、连续、产量高,比手工电弧焊接效率高出数倍甚至十倍以上。
2. 稳定:埋弧焊接过程稳定,焊缝质量高,并且焊接不易产生气孔、裂纹等缺陷。
3. 经济:埋弧焊接器材简单、成本低廉,操作简单,可实现自动化生产。
4. 适用面广:埋弧焊接可用于焊接各种金属材料,包括钢、铜、铝等。
埋弧焊接的工艺埋弧焊接的基本设备包括电源、焊机、焊枪、焊丝、焊接电缆和其他辅助设备。
下面是埋弧焊接的具体工艺步骤:1. 准备工作:首先需要对待焊接的材料进行清洗和钝化处理,以便焊接区域不受腐蚀作用。
然后将工件放入夹持装置中,以便焊接。
2. 选用焊接电源:根据待焊接的材料和工件的厚度,选择合适的电源和电流大小。
通常使用直流或低频交流电源。
3. 选用焊丝和熔渣:选择合适的焊丝和熔渣,以确保焊接效果良好。
焊丝的直径通常为2.4mm、3.2mm和4mm,熔渣的成分也需要根据焊接的材料来选用。
4. 安装和调整焊机:将焊丝和熔渣装置安装在焊机上,并根据需要进行调整。
调整项包括焊丝送丝速度、熔渣的喷出速度、焊接电流和焊接电压等。
5. 启动焊接:将焊枪和焊丝放在焊件上,启动焊接过程。
焊丝和熔渣进入焊缝,形成熔池,然后熔池在熔渣的保护下冷却凝固。
6. 检查和清理:当焊接完成后,需要对焊缝进行检查,去除焊接过程中产生的熔渣和焊丝残留物。
最后进行质量检验,以确定焊接是否符合要求。
总结埋弧焊接是一种高效、稳定、经济的焊接工艺,可以用于焊接各种金属材料。
埋弧焊接要求焊接区域被熔渣保护,以保证焊接质量。
在进行埋弧焊接时,需要选用合适的焊丝和熔渣,同时保证焊机的正常工作。
进行完埋弧焊接后,需要对焊缝进行检查和清理,以确保焊接的质量。
埋弧焊焊接工艺

埋弧焊焊接工艺
1、加衬铁情况下的筒体与封头对接应留有3-4mm的缝隙,便于使用二保焊打底;对于10mm 以上板材或没有加衬铁的情况,要双面焊接(即里面电弧焊焊接,外面二保焊打底)。
2、12mm及以上板材或10mm大直径工件,里面电弧焊焊接完毕后,外边要使用气爆焊条进行气爆处理,然后二保焊打底,最后埋弧焊接。
3、在埋弧焊焊接之前,要对工件焊缝周围进行抛光处理,包括焊缝、焊缝左右约5cm范围以内,彻底去除油污、焊渣、氧化层等影响焊接工艺的杂物。
4、采用符合规定的焊丝和焊剂,调整电压、电流、焊接速度使之符合工艺要求。
5、焊枪头对准焊缝中心偏下的位置,滚轮架向焊枪头相反的一侧转动,焊丝伸出保护帽长度大约为焊丝直径的4-5倍,不小于10mm;
6、原则上对于环缝的焊接不允许有两个或以上的焊接接头,焊剂要提前添加,防止缺少焊剂额情况。
7、埋弧焊地线要牢固可靠的紧紧连接至工件本身,防止断弧的发生。
8、埋弧焊剂可循环使用,但是要筛除杂质,防止气孔或出现不溶物。
焊缝成型图例
当其他条件不变时,增大电流,溶深加大,余高加大,易产生高温裂纹;
减小电流,溶深减小,余高、宽度不足
当电压加大时,余高不足,溶深减小,宽度加大
电压减小时,溶深大,宽度小,余高大
焊接速度与溶深溶宽成反比关系。
埋弧焊最主要的焊接工艺参数有:电压、电流、焊接速度、焊丝伸出长度。
埋弧焊接工艺

埋弧焊(含埋弧堆焊及电渣堆焊等)是一种重要的焊接方法,其固有的焊接质量稳定、焊接生产率高、无弧光及烟尘很少等优点,使其成为压力容器、管段制造、箱型梁柱等重要钢结构制作中的主要焊接方法。
近年来,虽然先后出现了许多种高效、优质的新焊接方法,但埋弧焊的应用领域依然未受任何影响。
从各种熔焊方法的熔敷金属重量所占份额的角度来看,埋弧焊约占10%左右,且多年来一直变化不大。
当焊丝确定以后(通常取决于所焊的钢种),配套用的焊剂则成为关键材料,它直接影响焊缝金属的力学性能(特别是塑性及低温韧性)、抗裂性能、焊接缺陷发生率及焊接生产率等。
焊丝与焊剂的配用重量比为焊丝:焊剂=~,视焊接接头类型、所用焊剂种类、焊接规范参数而定。
与熔炼焊剂相比,烧结焊剂用量较为节省,约可少用20%左右。
我国采用焊剂量在5万吨左右波动,其中70%约为熔炼焊剂,余为非熔炼焊剂。
欧美工业发达国家以非熔炼型焊剂为主,约在80%、90%以上,但仍然有熔炼型焊剂生产销售,熔炼焊剂这种持久的生产力与其固有的一些特点有关。
近年来,在我国出现了一种钢筋的新的焊接方法,即竖向钢筋电弧——电渣压力焊。
与以前的钢筋搭接手工电弧焊法相比,可节约钢材15%以上,生产率大大提高,焊接材料消耗费用也有所降低,确有取代后者的发展趋势,应用日益广泛。
该方法主要使用熔炼焊剂,它起到维弧、电渣加热、金属凝固模体等作用。
目前我国熔炼焊剂的五分之一左右用于竖向钢筋的焊接。
我国的锰矿资源比较缺乏,特别是适于生产熔炼焊剂的品位高、磷含量低、铁含量低的锰矿就更少了。
全国仅在广西、云南、湖南等省有锰矿矿脉,经过多年开采,符合生产焊剂的锰矿商品日渐紧张。
为取代高锰渣系焊剂,研制、推广中锰、低锰焊剂已成为客观需要的紧迫任务。
随着含适量锰焊丝的生产供应的扩大,中锰、低锰渣系焊剂应该有广阔的市场。
关于商品焊剂的技术性能说明,目前在行业上的通常作法是,熔炼焊剂给出其化学成分及配一种焊丝的熔敷金属力学性能,烧结焊剂只给出其渣系构成及配一种焊丝的熔敷金属力学性能。
埋弧焊焊接工艺及操作方法
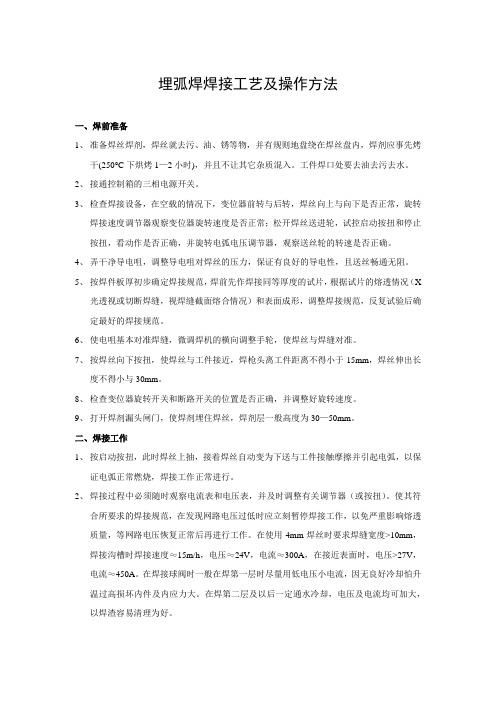
埋弧焊焊接工艺及操作方法一、焊前准备1、准备焊丝焊剂,焊丝就去污、油、锈等物,并有规则地盘绕在焊丝盘内,焊剂应事先烤干(250°C下烘烤1—2小时),并且不让其它杂质混入。
工件焊口处要去油去污去水。
2、接通控制箱的三相电源开关。
3、检查焊接设备,在空载的情况下,变位器前转与后转,焊丝向上与向下是否正常,旋转焊接速度调节器观察变位器旋转速度是否正常;松开焊丝送进轮,试控启动按扭和停止按扭,看动作是否正确,并旋转电弧电压调节器,观察送丝轮的转速是否正确。
4、弄干净导电咀,调整导电咀对焊丝的压力,保证有良好的导电性,且送丝畅通无阻。
5、按焊件板厚初步确定焊接规范,焊前先作焊接同等厚度的试片,根据试片的熔透情况(X光透视或切断焊缝,视焊缝截面熔合情况)和表面成形,调整焊接规范,反复试验后确定最好的焊接规范。
6、使电咀基本对准焊缝,微调焊机的横向调整手轮,使焊丝与焊缝对准。
7、按焊丝向下按扭,使焊丝与工件接近,焊枪头离工件距离不得小于15mm,焊丝伸出长度不得小与30mm。
8、检查变位器旋转开关和断路开关的位置是否正确,并调整好旋转速度。
9、打开焊剂漏头闸门,使焊剂埋住焊丝,焊剂层一般高度为30—50mm。
二、焊接工作1、按启动按扭,此时焊丝上抽,接着焊丝自动变为下送与工件接触摩擦并引起电弧,以保证电弧正常燃烧,焊接工作正常进行。
2、焊接过程中必须随时观察电流表和电压表,并及时调整有关调节器(或按扭)。
使其符合所要求的焊接规范,在发现网路电压过低时应立刻暂停焊接工作,以免严重影响熔透质量,等网路电压恢复正常后再进行工作。
在使用4mm焊丝时要求焊缝宽度>10mm,焊接沟槽时焊接速度≈15m/h,电压≈24V,电流≈300A,在接近表面时,电压>27V,电流≈450A。
在焊接球阀时一般在焊第一层时尽量用低电压小电流,因无良好冷却怕升温过高损坏内件及内应力大。
在焊第二层及以后一定通水冷却,电压及电流均可加大,以焊渣容易清理为好。
埋弧压力焊的焊接工艺
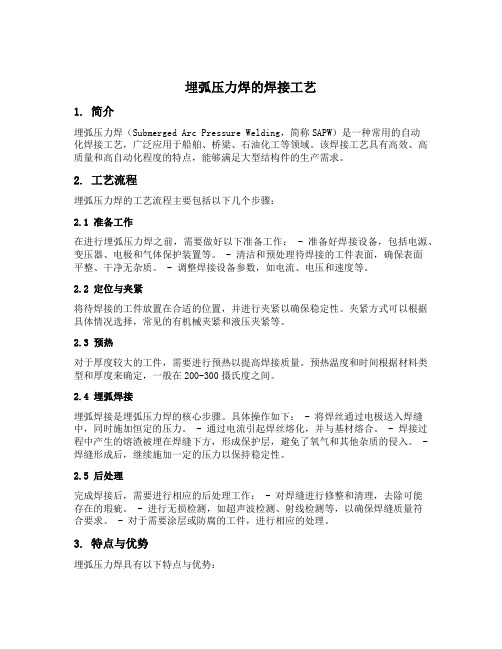
埋弧压力焊的焊接工艺1. 简介埋弧压力焊(Submerged Arc Pressure Welding,简称SAPW)是一种常用的自动化焊接工艺,广泛应用于船舶、桥梁、石油化工等领域。
该焊接工艺具有高效、高质量和高自动化程度的特点,能够满足大型结构件的生产需求。
2. 工艺流程埋弧压力焊的工艺流程主要包括以下几个步骤:2.1 准备工作在进行埋弧压力焊之前,需要做好以下准备工作: - 准备好焊接设备,包括电源、变压器、电极和气体保护装置等。
- 清洁和预处理待焊接的工件表面,确保表面平整、干净无杂质。
- 调整焊接设备参数,如电流、电压和速度等。
2.2 定位与夹紧将待焊接的工件放置在合适的位置,并进行夹紧以确保稳定性。
夹紧方式可以根据具体情况选择,常见的有机械夹紧和液压夹紧等。
2.3 预热对于厚度较大的工件,需要进行预热以提高焊接质量。
预热温度和时间根据材料类型和厚度来确定,一般在200-300摄氏度之间。
2.4 埋弧焊接埋弧焊接是埋弧压力焊的核心步骤。
具体操作如下: - 将焊丝通过电极送入焊缝中,同时施加恒定的压力。
- 通过电流引起焊丝熔化,并与基材熔合。
- 焊接过程中产生的熔渣被埋在焊缝下方,形成保护层,避免了氧气和其他杂质的侵入。
- 焊缝形成后,继续施加一定的压力以保持稳定性。
2.5 后处理完成焊接后,需要进行相应的后处理工作: - 对焊缝进行修整和清理,去除可能存在的瑕疵。
- 进行无损检测,如超声波检测、射线检测等,以确保焊缝质量符合要求。
- 对于需要涂层或防腐的工件,进行相应的处理。
3. 特点与优势埋弧压力焊具有以下特点与优势:3.1 高效率埋弧压力焊是一种自动化焊接工艺,能够实现连续、高效的焊接操作。
相比手工焊接,它具有更高的焊接速度和生产效率。
3.2 高质量埋弧压力焊采用恒定的电流和压力,能够保证焊缝的质量稳定。
由于熔渣被埋在焊缝下方,可以有效避免气孔和夹杂物等缺陷的产生。
3.3 自动化程度高埋弧压力焊可实现全自动或半自动操作,减少了人工干预,提高了生产效率和一致性。
埋弧焊工艺参数及焊接技术
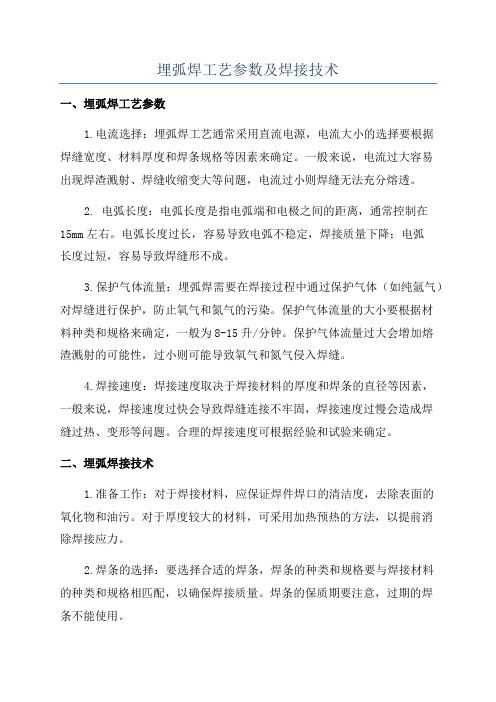
埋弧焊工艺参数及焊接技术一、埋弧焊工艺参数1.电流选择:埋弧焊工艺通常采用直流电源,电流大小的选择要根据焊缝宽度、材料厚度和焊条规格等因素来确定。
一般来说,电流过大容易出现焊渣溅射、焊缝收缩变大等问题,电流过小则焊缝无法充分熔透。
2. 电弧长度:电弧长度是指电弧端和电极之间的距离,通常控制在15mm左右。
电弧长度过长,容易导致电弧不稳定,焊接质量下降;电弧长度过短,容易导致焊缝形不成。
3.保护气体流量:埋弧焊需要在焊接过程中通过保护气体(如纯氩气)对焊缝进行保护,防止氧气和氮气的污染。
保护气体流量的大小要根据材料种类和规格来确定,一般为8-15升/分钟。
保护气体流量过大会增加熔渣溅射的可能性,过小则可能导致氧气和氮气侵入焊缝。
4.焊接速度:焊接速度取决于焊接材料的厚度和焊条的直径等因素,一般来说,焊接速度过快会导致焊缝连接不牢固,焊接速度过慢会造成焊缝过热、变形等问题。
合理的焊接速度可根据经验和试验来确定。
二、埋弧焊接技术1.准备工作:对于焊接材料,应保证焊件焊口的清洁度,去除表面的氧化物和油污。
对于厚度较大的材料,可采用加热预热的方法,以提前消除焊接应力。
2.焊条的选择:要选择合适的焊条,焊条的种类和规格要与焊接材料的种类和规格相匹配,以确保焊接质量。
焊条的保质期要注意,过期的焊条不能使用。
3.焊接过程:焊接时,要保证电弧稳定,焊条与工件的距离适当,不得与气缝直接接触。
焊接位置要选择合适,以便操作方便。
焊接方向要与主应力方向垂直。
4.焊后处理:焊接后,应采取适当的焊后处理措施,如退火、热处理等,以提高焊接接头的性能和质量。
总结:埋弧焊工艺参数及焊接技术对焊接质量和效率具有重要影响。
通过选择合适的电流、电弧长度和保护气体流量等参数,合理控制焊接速度,做好焊前准备和焊后处理工作,可以保证埋弧焊接的质量和可靠性。
同时,焊工应具备良好的焊接技术和操作经验,能够正确操作焊接设备和工具,严格按照操作规程进行焊接,以确保焊接质量和安全。
埋弧焊工艺

埋弧焊工艺一、埋弧焊工艺的内容和编制1.埋弧焊工艺的主要内容埋弧焊工艺主要包括焊接工艺方法的选择;焊接工艺装备的选用;焊接坡口的设计;焊接材料的选定;焊接工艺参数的制定;焊件组装工艺编制;操作技术参数及焊接过程控制技术参数的制定;焊缝缺陷的检查方法及修补技术的制定;焊前预处理与焊后热处理技术的制定等内容。
2.编制焊接工艺的原则和依据首先要保证接头的质量完全符合焊件技术条件或标准的规定;其次是在保证接头质量的前提下,最大限度地降低生产成本,即以最高的焊接速度,最低的焊材消耗和能量消耗以及最少的焊接工时完成整个焊接过程。
编制焊接工艺的依据是焊件材料的牌号和规格,焊件的形状和结构,焊接位置以及对焊接接头性能的技术要求等。
二、焊接工艺参数的影响及选择1.焊接工艺参数对焊缝质量的影响2.焊接工艺参数的选择方法(1)焊接工艺参数的选择依据焊接工艺参数的选择是针对将要投产的焊接结构施工图上标明的具体焊接接头进行的。
根据产品图样和相应的技术条件,如:1)焊件的形状和尺寸(直径、总长度);接头的钢材种类与板厚。
2)焊缝的种类(纵缝、环缝)和焊缝的位置(平焊、横焊、上坡焊、下坡焊)。
3) 接头的形式(对接、角接、搭接)和坡口形式(Y形、X形、U形坡口等)。
4)对接头性能的技术要求,其中包括焊后无损探伤方法,抽查比例以及对接接头强度、冲击韧度、弯曲、硬度和其它理化性能的合格标准。
5)焊接结构(产品)的生产批量和进度要求。
(2)焊接工艺参数的选择程序根据上列已知条件,通过对比分析,首先可选定埋弧焊工艺方法,单丝焊还是多丝焊或其它工艺方法,同时根据焊件的形状和尺寸可选定细丝埋弧焊,还是粗丝埋弧焊。
例如小直径圆筒的内外环缝应采用ø2mm焊丝的细丝埋弧焊;深坡口对接接头纵缝和环缝宜采用ø4mm焊丝的埋弧焊;船形位置厚板角接接头通常可采用用ø5rnm、ø6mm焊丝的粗丝埋弧焊。
焊接工艺方法选定后,即可按照钢材、板厚和对接头性能的要求,选择适用的焊剂和焊丝的牌号,对于厚板深坡口或窄间隙埋弧焊接头,应选择既能满足接头性能要求又具有良好工艺性和脱渣性的焊剂。
埋弧焊工艺标准

埋弧焊工艺标准
埋弧焊是一种在焊剂层下完成电弧焊接的方法。
在进行埋弧焊之前,需要进行一系列准备工作,包括焊件的坡口加工、待焊部位的表面清理、焊件的装配以及焊丝表面的清理、焊剂的烘干等。
具体标准如下:
1. 坡口加工:坡口加工要求按GB 986—1988执行,以保证焊缝根部不出现未焊透或夹渣,并减少填充金属量。
坡口的加工可使用刨边机、机械化或半机械化气割机、碳弧气刨等。
2. 待焊部位的清理:在焊前应将坡口及坡口两侧各20mm区域内及待焊部位的表面铁锈、氧化皮、油污等清理干净。
3. 焊件的装配:装配焊件时要保证间隙均匀,高低平整,错边量小,定位焊缝长度一般大于30mm,并且定位焊缝质量与主焊缝质量要求一致。
必要时采用专用工装、卡具。
4. 预热:当埋弧焊焊接的板厚在60mm以上时,焊前必须对焊道及两侧2倍板厚范围内预热,预热温度为100~150℃,板厚为40~60mm时,预热温度宜为60~80℃。
5. 保温:焊接完成前不得中途停止超过15分钟,当必须停止时,应采取保温措施缓冷,重新施焊前必须再次预热,层间温度控制在℃,焊接完后应采用保温棉及时进行保温。
此外,在焊接工艺上主要采取气保焊打底,埋弧自动焊填充及盖面,打底厚度根据板厚而定。
以上信息仅供参考,如需获取更多详细信息,建议查阅埋弧焊工艺标准书籍或咨询专业人士。
自动埋弧焊操作规程5篇

自动埋弧焊操作规程5篇【导语】自动埋弧焊操作规程怎么写受欢迎?本为整理了5篇优秀的自动埋弧焊操作规程范文,为便于您查看,点击下面《名目》可以快速到达对应范文。
以下是我为大家收集的自动埋弧焊操作规程,仅供参考,盼望对您有所关心。
名目第1篇门型自动埋弧焊机平安操作规程第2篇工贸门型自动埋弧焊机平安操作规程第3篇工贸企业门型自动埋弧焊机平安操作规程第4篇自动埋弧焊平安维护保养操作规程第5篇悬臂式自动埋弧焊平安操作规程【第1篇】门型自动埋弧焊机平安操作规程1、操作本机的作业人员必需有电焊作业上岗证。
2、作业人员必需熟识本机的操作程序、机器性能及特点。
3、焊接前检查轨道上是否有异物阻挡,轨道是否平整,溶剂及流量是否足够、畅通。
4、检查电缆滑车是否松动,轨道是否有杂物。
5、严格根据该设备的有关操作程序进行操作。
a、焊接操作程序;b、机头气动操作程序;c、焊剂回收系统操作程序;d、机头小车操作程序。
6、焊接起弧后留意焊缝之外形,适当调整焊头高度角度,焊接边度,焊接电压、电流。
7、焊剂回收机口不应吸入焊渣,防堵塞。
8、每日下班前清理埋弧焊机轨道下的焊渣。
【第2篇】工贸企业门型自动埋弧焊机平安操作规程1.操作本机的作业人员必需有电焊作业上岗证。
2.作业人员必需熟识本机的操作程序、机器性能及特点。
3.焊接前检查轨道上是否有异物阻挡,轨道是否平整,溶剂及流量是否足够、畅通。
4.检查电缆滑车是否松动,轨道是否有杂物。
5.严格根据该设备的有关操作程序进行操作。
a、焊接操作程序; b.机头气动操作程序;c、焊剂回收系统操作程序; d.机头小车操作程序。
6.焊接起弧后留意焊缝之外形,适当调整焊头高度角度,焊接边度,焊接电压、电流。
7.焊剂回收机口不应吸入焊渣,防堵塞。
8.每日下班前清理埋弧焊机轨道下的焊渣。
【第3篇】工贸门型自动埋弧焊机平安操作规程1.操作本机的作业人员必需有电焊作业上岗证。
2.作业人员必需熟识本机的操作程序、机器性能及特点。
埋弧横焊工艺

埋弧横焊工艺埋弧横焊工艺是一种高效、节能的焊接方法,广泛应用于各类金属结构的制造和维修领域。
该工艺在我国得到了广泛的应用,并在很大程度上提高了焊接质量和生产效率。
本文将从埋弧横焊工艺的原理、特点、应用领域以及注意事项等方面进行详细介绍。
一、埋弧横焊工艺原理埋弧横焊工艺是一种自动化焊接方法,其原理是利用焊丝在焊接过程中自动送入焊缝,并通过焊接电源和控制系统实现焊接过程的自动化。
在焊接过程中,焊丝与工件之间的电弧长度自动调整,使焊接过程稳定。
由于焊丝的送入和电弧长度的自动调整,使得焊接过程具有良好的焊接质量稳定性和生产效率。
二、埋弧横焊工艺特点1. 高效率:埋弧横焊工艺采用自动化焊接设备,使焊接过程更加高效,生产效率得到显著提高。
2.高质量:由于焊丝与工件之间的电弧长度自动调整,使得焊接过程稳定,从而保证了焊接质量。
3.节能环保:与传统的焊条焊接相比,埋弧横焊工艺减少了焊接过程中的能耗和焊条废弃物,具有较好的环保性能。
4.广泛应用:埋弧横焊工艺适用于各种金属材料的焊接,广泛应用于钢结构、船舶制造、桥梁工程等领域。
三、埋弧横焊工艺应用领域1.钢结构工程:埋弧横焊工艺在钢结构工程中具有广泛的应用,如桥梁、压力容器、重型机械等领域。
2.船舶制造:船舶制造行业对焊接质量要求极高,埋弧横焊工艺在此领域具有显著优势,可提高船舶结构的焊接质量。
3.桥梁工程:桥梁工程中的箱梁、T梁等结构采用埋弧横焊工艺,可确保焊接质量达到优良等级。
4.其它领域:此外,埋弧横焊工艺还广泛应用于石油、化工、电力等行业的设备制造和维修领域。
四、埋弧横焊工艺注意事项1.选择合适的焊接参数:根据工件材料、厚度等因素,合理选择焊接电源、焊接电流、焊接速度等参数,以确保焊接质量。
2.焊丝的选择:根据工件材料和焊接要求,选择合适的焊丝,以满足焊接质量要求。
3.焊接过程中的监控:在焊接过程中,对焊接质量进行实时监控,如发现质量问题,及时调整焊接参数。
埋弧焊工艺

埋弧焊工艺一、埋弧焊工艺参数有焊接电流、电弧电压、焊接速度、焊丝直径、焊丝伸出长度、焊丝倾角、焊件倾斜等。
对焊缝成形和焊接质量影响最大的是:焊接电流、电弧电压和焊接速度。
1.焊接电流若其他因素不变,焊接电流增大,电弧吹力增强,焊缝厚度增大;焊丝熔化速度也加快,余高稍有增加;电弧摆动小,所以焊缝宽度变化不大。
焊接电流过大,易咬边或成形不良,热影响区增宽,甚至烧穿。
焊接电流过小,焊缝厚度减小,易产生未焊透缺陷,电弧稳定性差。
见下图2.电弧电压若其他因素不变,增加电弧长度,电弧电压增加。
随电弧电压增加,焊缝宽度显著增大,而焊缝厚度和余高减小。
原因是:电弧电压越高,电弧就越长,电弧的摆动范围就越大,焊件被电弧加热的面积越大,致使焊缝宽度增大。
但电弧长度增大以后,电弧热量损失加大,用于熔化母材和焊丝的热量减少,使得焊缝厚度和余高减少。
结论:电流是决定焊缝厚度的主要因素;电压是影响焊缝宽度的主要因素。
焊接电流和电弧电压必须良好匹配。
焊接电流/A 600~700700~850850~10001000~1200电弧电压/V34~3636~3838~4040~423.焊接速度:焊接速度对焊缝厚度和焊缝宽度都有明显影响,焊接速度增加,焊缝厚度和焊缝宽度都大为下降。
原因是:焊接速度增加,焊缝中单位时间内输入的热量减少。
影响趋势:焊速过大,易形成未焊透、咬边、焊缝表面粗糙不平等缺陷;焊速过小,则会形成易裂的“蘑菇形”焊缝或产生烧穿、夹渣、焊缝不规则的缺陷。
4.焊丝直径:焊接电流不变时,随着焊丝直径的增大,电流密度减小,电弧吹力减弱,电弧的摆动作用增强,使焊缝宽度增加而焊缝厚度减小;焊丝直径减小时,电流密度增加,电弧吹力增大,使得焊缝厚度增加。
表3—10焊接电流与电弧电压的匹配关系结论:用同样大小的电流焊接时,小直径焊丝可获得较大的焊缝厚度。
焊丝直径/mm2.03.04.05.06.0焊接电流/A 200~400350~600500~800700~1000800~12005.焊丝伸出长度焊丝伸出长度:导电嘴至焊丝端部的长度。
埋弧焊焊接作业指导书
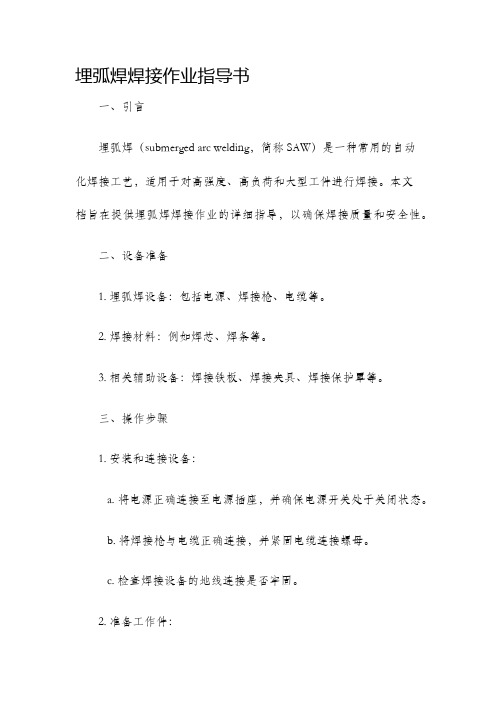
埋弧焊焊接作业指导书
一、引言
埋弧焊(submerged arc welding,简称SAW)是一种常用的自动
化焊接工艺,适用于对高强度、高负荷和大型工件进行焊接。
本文
档旨在提供埋弧焊焊接作业的详细指导,以确保焊接质量和安全性。
二、设备准备
1. 埋弧焊设备:包括电源、焊接枪、电缆等。
2. 焊接材料:例如焊芯、焊条等。
3. 相关辅助设备:焊接铁板、焊接夹具、焊接保护罩等。
三、操作步骤
1. 安装和连接设备:
a. 将电源正确连接至电源插座,并确保电源开关处于关闭状态。
b. 将焊接枪与电缆正确连接,并紧固电缆连接螺母。
c. 检查焊接设备的地线连接是否牢固。
2. 准备工作件:
a. 清洁工件表面,确保无杂质和油脂。
b. 对于大型工件,合理安排支撑和定位,确保稳固性和焊接位置的准确性。
3. 调整焊接参数:
a. 根据焊接工件类型和要求,选择合适的焊接电流和电压,并与设备的参数进行匹配。
b. 调整焊接速度,以保证焊接质量。
4. 开始焊接:
a. 将焊接枪对准工件焊接位置,确保角度和距离适宜。
b. 按下电源开关,启动焊接设备。
c. 保持焊接枪稳定并均匀移动,控制焊接速度,确保焊缝的均匀性和质量。
d. 注意避免焊接过程中的晃动和颤动,以免影响焊接效果。
5. 完成焊接:
a. 焊接完成后,切断电源并等待焊缝冷却。
埋弧自动焊焊接工艺参数

埋弧自动焊焊接工艺参数焊接工艺参考1.不开坡口对接接头悬空双面焊的焊接条件工件厚度(mm) 焊丝直径(mm) 焊接顺序焊接电流(A)电弧电压(V) 焊接速(cm/min) 6 4 正380~420 30 58反430~470 30 558 4 正440~480 30 50反480~530 31 5010 4 正530~570 31 33反590~640反530~570590~640 3133 464612 4 正反620~660680~720 3535 424114 4 正反680~720730~770 3740 413815 5 正反800~850850~900 34~3636~38 634317 5 正反850~900900~950 35~3737~39 604318 5 正反850~900900~950 36~3838~40 604020 5 正反850~900900~1000 36~3838~40 424022 5 正反900~9501000 37~3938~40 5340注:装配间隙0~1mm.五.焊接工艺参考(续)2.对接接头预留间隙双面焊的焊接条件工件厚度(mm) 焊丝直径(mm) 装配间隙(mm) 焊接电流(A)电弧电压(V) 焊接速度(cm/min)6 3 0~1 380~400 30~32 57~608 3 0~1 400~420 28~32 53~5710 4 1~2 500~600 30~32 50~6012 4 1~2 550~580 38~40 50~5714 5 3~4 700~750 34~36 5016 5 3~4 700~750 34~36 4518 5 4~5 750~800 36~40 4520 5 4~5 850~900 36~40 4524 5 4~5 900~950 38~42 4228 5 5~6 900~950 38~42 3330 5 6~7 950~1000 40~44 2740 5 8~9 1100~1200 40~44 2050 5 10~11 1200~1300 44~48 173.开坡口工件的双面焊的焊接条件工件厚度(mm)坡口形式焊丝直径(mm)焊接顺序坡口尺寸焊接电流(A)电弧电压(V)焊接速度(cm/min)角度(0 )根高(mm)间隙(mm)14 Y型 5 正703mm 3mm 830~850 36~38 42 反600~620 36~38 7516 5 正700 3mm 3mm 830~850 36~38 33反600~620 36~38 7518 5 正700 3mm 3mm 830~860 36~38 33反600~620 36~38 7522 6 正700 3mm 3mm 1100 38~40 305 反600~620 36~38 7524 X型 6 正700 3mm 3mm 1100 38~40 405 反800 36~38 4730 6 正700 3mm 3mm 1000 36~40 30。
埋弧焊工艺与操作技巧

埋弧焊工艺与操作技巧引言埋弧焊是一种常用的焊接技术,广泛应用于钢结构、船舶、桥梁、石油化工等领域。
本文将介绍埋弧焊的基本原理、操作技巧以及注意事项。
一、埋弧焊的原理埋弧焊是一种根据电弧熔化焊条供料来进行焊接的方法。
其工作原理如下: 1. 焊条通过供电电源产生电弧。
2. 电弧在工件和焊条之间形成,熔化焊条并使其与工件熔合。
3. 熔化的金属在焊接缝中形成焊渣,保护焊缝避免氧气和杂质的侵入。
二、埋弧焊的操作技巧1.选择适当的焊接电流和电压。
根据工件的材料和类型,选择合适的焊接电流和电压可以保证焊缝的质量和稳定性。
2.控制焊接速度。
焊接速度的过快或过慢都会影响焊缝的质量。
应根据焊接材料和厚度,选择适当的焊接速度。
3.保持合适的焊接角度。
通常情况下,焊接角度应垂直于工件表面。
如果角度偏离,会导致焊缝质量下降和焊接变形。
4.注意电焊材料的质量。
合格的焊条和焊剂对焊接质量至关重要。
务必选择有质量保证的材料进行焊接操作。
5.确保焊接环境的通风良好。
焊接过程中会产生大量的烟尘和有害气体,应确保操作区域有良好的通风条件,以保护操作人员的健康。
三、注意事项1.安全操作。
焊接过程中需要注意防护措施,包括戴上防焊光眼镜、焊接手套和防护服等,以避免对皮肤和眼睛的损伤。
2.注意电焊设备的维护。
定期检查焊接设备的接线和电源,确保其正常工作,避免意外事故。
3.焊接接头的准备工作。
在进行埋弧焊前,应对接头进行清洁和打磨,以去除锈蚀和污垢,保证焊接质量。
4.控制焊接温度。
过高的焊接温度会导致焊缝脆性增加,影响焊接质量。
应根据材料要求和焊接规范,控制焊接温度。
5.注意焊接参数的选择。
除了焊接电流和焊接速度外,还应注意电弧长度、焊接间隙等参数的合理选择,以保证焊缝质量。
四、总结埋弧焊是一种常用的焊接技术,掌握埋弧焊的工艺和操作技巧对焊接质量至关重要。
本文介绍了埋弧焊的基本原理、操作技巧以及注意事项。
通过正确的操作和控制,可以实现优质的焊接效果,并确保焊缝的质量和稳定性。
埋弧焊工艺

埋弧焊工艺什么是埋弧焊埋弧焊是一种常见的电弧焊接工艺,它使用一根保护焊条和被焊接的金属工件之间的电弧,在高温下熔化焊条和金属工件表面,从而实现焊接的过程。
埋弧焊工艺适用于焊接中厚板和重型结构,尤其是焊接较大尺寸的工件。
埋弧焊的特点1. 高焊接效率埋弧焊工艺具有高焊接效率的特点。
在埋弧焊过程中,由于焊接电弧被保护在焊条和金属工件之间的粉末套管中,可以获得更高的电弧能量密度,从而提高焊接速度和生产效率。
2. 减少氧化和飞溅埋弧焊的另一个显著特点是减少氧化和飞溅。
由于焊接电弧被保护在粉末套管中,可以防止空气中的氧气与熔池中的铁发生氧化反应,减少氧化物生成。
同时,粉末套管还可以吸收和凝聚飞溅,防止其飞溅到周围的区域。
3. 保护气体非常重要在埋弧焊工艺中,选择合适的保护气体非常重要。
常用的保护气体有纯二氧化碳、纯氩气和混合气体。
不同的保护气体可以影响焊接过程中的电弧稳定性、焊缝质量和保护效果,需要根据具体的焊接要求进行选择。
埋弧焊的工艺参数1. 电流和电压埋弧焊的焊接电流和电压是两个重要的参数。
电流决定焊条熔化的速度和焊缝的形状,而电压影响焊接电弧的稳定性和熔化深度。
合理选择电流和电压可以确保焊缝质量和焊接速度的平衡。
2. 焊接速度焊接速度是指焊条通过焊缝的速度。
合理选择焊接速度可以确保焊接质量和焊接效率的平衡。
过高的焊接速度可能导致焊接质量下降,而过低的焊接速度会增加生产成本。
3. 保护气体流量保护气体流量是指保护气体在焊接过程中的流量大小。
合理选择保护气体流量可以确保焊接过程中的保护效果和焊接质量。
过高的保护气体流量可能导致焊接缺陷,而过低的保护气体流量会减弱保护效果。
4. 焊接角度和焊枪的位置焊接角度和焊枪的位置对于焊接质量和操作工人的劳动强度具有重要影响。
合理的焊接角度和焊枪的位置可以确保熔化深度和焊缝形状的一致性,并减轻操作工人的劳动强度。
埋弧焊的应用埋弧焊工艺被广泛应用于船舶、桥梁、压力容器、石油化工等重型结构的焊接。
埋弧焊 焊接的方法

埋弧焊焊接的方法埋弧焊(arcwelding)是一种焊接工艺,它通过产生电弧来熔化金属,以便合并或连接金属物体,铝和钢等金属材料都可以通过埋弧焊进行连接。
埋弧焊可以用于大量的焊接作业,如结构性焊接、装饰性焊接和去毛刺处理,也可以替代螺栓和螺母的连接,提高结构的强度和绝缘性能。
埋弧焊的工艺要求是在电流密度较低的情况下,电弧光维持在两个金属物体之间,在温度增加时将两个物体熔化,然后添加焊接材料,通过焊接材料将两个熔化的物体打通,使熔接处擦花平整,接头结合牢固。
埋弧焊需要调整变压器,控制电流的大小和电弧的长度,电弧的长度不能过长和过短,如果电弧的长度过长,就会增加焊接缺陷的概率,而且会有大量的毛刺和熔渣;如果电弧的长度太短,就会出现熔接失败的情况。
因此,在焊接的过程中,必须控制电流的大小,使电弧的长度保持在一定的水平,以获得良好的焊接效果。
为了获得良好的焊接效果,焊接前还需要对焊枪和焊接材料进行一定的准备工作,包括清洁熔接处,去除污垢和油渍,擦除焊接处的外表锈蚀,然后安装焊枪,上焊丝,调整焊枪和电流,采取合适的方式,有针对性地焊接。
埋弧焊有许多优点,如结构强度高,熔接固定牢固,焊接速度快,熔化深度范围大,焊缝均匀光洁,擦花较小,可以在自然环境空气中焊接,成本较低,熔接牢度好,坚固耐用,适用于大跨度、厚板及复杂结构。
然而,由于埋弧焊产生比较大的热量,使焊缝易于发生收缩、变形,同时也容易熔接不良,因此埋弧焊的过程需要遵循独特的工艺标准,以控制质量,确保熔接质量。
在埋弧焊的过程中,还需要采取措施,如安装焊接屏障,以防止电弧的放射污染环境。
总之,埋弧焊是一种常用的焊接工艺,它可以用来将金属物体连接在一起,具有良好的结构强度和绝缘性能,但是,为了获得更好的焊接效果,必须控制电流大小,调节焊接参数,并采取适当的措施,如安装屏障,以防止电磁辐射污染环境。
- 1、下载文档前请自行甄别文档内容的完整性,平台不提供额外的编辑、内容补充、找答案等附加服务。
- 2、"仅部分预览"的文档,不可在线预览部分如存在完整性等问题,可反馈申请退款(可完整预览的文档不适用该条件!)。
- 3、如文档侵犯您的权益,请联系客服反馈,我们会尽快为您处理(人工客服工作时间:9:00-18:30)。
埋弧焊工艺1、悬空埋弧焊是一种不用任何衬托和辅助设备、装置的埋弧焊工艺方法,埋弧焊焊接电流大,电弧压力大,电弧穿透能力强,在无任何衬托和辅助装置情况下,易造成焊穿或液态金属流失;为防止焊穿,减小正面第一层焊接电流,造成第一层厚度减薄,在施焊背面第一层时,焊接电流受正面第一层厚度限制而无法增大,不能保证接头熔透,出现连续性中心未焊透、大气孔。
其次,为排除未焊透、气孔等缺陷,须通过提高电弧穿透力来增加焊缝熔深,必须增加焊接电流,焊接电流增大时:一方面,若坡口较窄,限制了熔池扩展,熔池深度增加,电弧搅拌作用增强,熔渣卷入熔池不易上浮,同时,熔融金属过热,熔渣高温时间长,金属、渣界面处渣中阴离子长大,使熔渣质点移动困难,粘度增大,进一步阻碍了渣的浮出,渣与界面金属紧密结合,造成脱渣困难和夹渣;另一方面,电弧搅拌作用增强,熔渣高温存在时间长,强制冷却成型作用弱化,焊缝表面成型粗糙;尤其环缝焊接时,熔池运动结晶,焊缝尺寸更难控制,造成成型不良;其三焊丝熔化量增大,造成余高过高;同时,焊接大线能量条件下,焊缝、热影响区组织晶粒严重长大,使接头性能,尤其是韧性受到显著影响。
如此,要改善悬空埋弧焊工艺应注意以下几方面问题:(1)降低每层热输入,保证接头性能。
(2)保证焊透,防止焊穿、气孔、裂纹等缺陷产生;(3)改善表面成型,降低余高,提高焊缝表面质量;(4)背面不清根,减少层间清渣、打磨量,降低劳动强度,减少污染。
考虑采用大坡口小钝边双面悬空埋弧焊工艺。
2、采用大坡口,小钝边双面悬空埋弧焊工艺方法,直流反接。
以厚度8㎜、10㎜、12㎜、14㎜、16㎜、18㎜、20㎜、22㎜等常用于压力容器的16MnR试板、筒体及其钛/钢复合板筒体焊缝焊接作为跟踪考察对象,进行工艺试验和参数优化。
3 坡口加工,机械加工方法进行试板或产品纵、环焊缝坡口加工,,根据工件厚度,其接头坡口型式如图1所示:4 焊接材料选用H10Mn2焊丝配HJ431焊剂, 焊丝直径Φ3.2㎜\Φ4㎜,焊剂焊前经250℃,2小时烘干。
5 焊接工艺参数开坡口工件焊接线能量相应不开坡口情况要小。
第一层焊接电流选择应防止焊穿,即保证一定电流值,以保证熔化50%以上钝边;背面第一层焊接时,焊接电流在防止焊穿的情况下尽可能大,以保证熔深,从而排除未焊透和气孔缺陷;其它道次焊接采用中等电流多层(道)次焊接。
参数选择上应注意焊接电流(I)、电压(U)、和速度(V)匹配,其焊接工艺参数如表2:6 接头组对及焊前准备组对前,将坡口两侧各30㎜范围内钢表面锈皮打磨处理直至露出金属光泽。
接头组对应保证错边量尽可能小,最大不超过1㎜,间隙小于0.5㎜;焊前,接头区域用高压风吹除(a) H=8、10㎜;(b) H=12、14、16㎜;(c) H=18、20、22㎜灰尘,适当方法清除焊接区水分和油污;焊丝伸出长度25-30㎜,始终保持焊丝与接头中心垂直,施焊环缝时根据筒体直径及参数,焊丝沿焊接反方向偏移40-100㎜的偏移量。
试验及应用结果分析利用以上试验参数进行埋弧焊试板及产品焊接。
外观检查:焊缝表面成型良好,表面光亮均匀,无表面气孔、咬边等缺陷,焊缝尺寸能满足工艺、标准要求;RT射线检测:焊缝洁净,黑度均匀,纵缝一次合格率达99%,环缝一次合格率达到95%,合格焊缝均为一级片,不合格焊缝,焊接缺陷一般为中心未焊透、气孔,且缺陷明显;接头弯曲试验(α=180o,D=4t)试样全部合格,且多层焊接头弯曲试样侧面焊缝层次清晰,中间有细晶层;大坡口悬空埋弧焊有利于提高接头质量。
大坡口悬空埋弧焊采用机加工制备坡口,坡口、钝边平整,洁净。
组对前,坡口两侧各30㎜范围内钢面氧化皮打磨清理干净,焊前将坡口内水分、油污等杂质清理干净,保证了焊接区内无污物存在,排除了气孔来源。
坡口、钝边规则平整,间隙、错边量易于控制,间隙能控制在≤0.5㎜,错变量能控制在≤1.0㎜,以保证接头中心母材金属厚度均匀性和间隙均匀性,提高接头组对质量,有利于焊接过程中参数稳定。
大坡口存在,一方面,保障电弧自由扩散,焊接层厚度减薄,有利于焊缝中气体和熔渣上浮;为熔化焊丝提供了去处,有利于降低焊缝余高;另一方面,电弧拘束度降低,焊穿的几率降低,焊接电弧能顺利达到坡口根部,随钝边减小,增大了一次焊透率,有利于焊接质量和效率的提高。
钝边尺寸减小,单层焊接热输入减小,熔渣冷却加快,脱渣容易,熔渣强制成形作用凸现,焊缝成型优异。
同时焊接参数的减小,熔宽、余高相应降低。
大坡口双面悬空埋弧焊工艺,关键在正面第一层及背面第一层焊接电流的选择,如果焊接电流选择合适,焊接接头组对良好,焊接过程中利用埋弧焊大电流,熔池存在时间长,焊接适应性强的特点,焊接过程可实现不清根,不打磨。
从而减少了工作人员清根、打磨时间,减少了车间灰尘量,减少了工序,节约了时间、材料,劳动力,提高了劳动效率,改善了环境。
表2 大坡口双面悬空埋弧焊工艺参数根据试验及生产应用情况可以看出:1 大坡口双面悬空埋弧焊充分利用了埋弧焊焊接适应性强的特点,采用机械加工制备坡口,提高了组对质量,同时注意组对前清锈和焊前清理,提高了焊接过程的参数稳定性,排除气孔、夹渣、未焊透缺陷形成的可能性。
2 大坡口的存在,使电弧能自由扩散,熔池尺寸增大,在同样熔化速度下,焊接层厚度降低,有利于熔渣和气体上浮,减少了层间夹渣、清渣,降低焊缝余高;3大坡口,小钝边,降低了单层热输入,焊接层次增加,焊接电弧能到达坡口根部,在不清根条件下,提高了一次焊透率,熔渣强制成形作用增强,改善焊缝外观成型,增加层间焊道退火作用,提高了接头质量和性能,减少清根,改善劳动条件,降低劳动强度。
4大坡口悬空埋弧焊,焊接材料对接头性能影响明显,应注意根据不同母材选用焊材,保证合金元素合理过渡,从而有效保证接头性能;5 表明大坡口小钝边双面悬空埋弧焊工艺适于压力容器钢(碳钢、低合金钢)或钛/钢复合板筒体纵、环焊缝的焊接。
6、.主要焊接缺陷及其产生原因(1)气孔埋弧焊焊缝产生气孔的主要原因及防止措施如下:1)焊剂吸潮或不干净焊剂中的水分、污物和氧化铁屑等都会使焊缝产生气孔,在回收使用的焊剂中这个问题更为突出。
水分可通过烘干消除,烘干温度与肘间由焊剂生产厂家规定。
防止焊剂吸收水分的最好方法是正确储存和保管。
采用真空式焊剂回、收器可以较有效地分离焊剂与尘土,从而减少回收焊剂在使用中产生气孔的可能性。
2)焊接时焊剂覆盖不充分由于电弧外露并卷入空气而造成气孔。
焊接环缝时,特别是小直径的环缝,容易出现这种现象,应采取适当措施,防止焊剂散落。
3)熔渣粘度过大焊接时溶入高温液态金属中的气体在冷却过程中将以气泡形式溢出。
如果熔渣粘度过大,气泡无法通过熔渣,被阻挡在焊缝金属表面附近而造成气孔。
通过调整焊剂的化学成分,改变熔渣的粘度即可解决。
4)电弧磁偏吹焊接时经常发生电弧磁偏吹现象,特别是在用直流电焊接时更为严重。
电弧磁偏吹会在焊缝中造成气孔。
磁偏吹的方向、受很多因素的影响,例如工件上焊接电缆的联接位置:电缆接线处接触不良、部分焊接电缆环绕接头造成的二次磁场等。
在同一条焊缝的不同部位,磁偏吹的方向也不相同。
在接近端部的一段焊缝上,磁偏吹更经常发生,因此这段焊缝气孔也较多。
为了减少磁偏吹的影响,应尽可能采用交流电源;工件上焊接电缆的联接位置尽可能远离焊缝终端;避免部分焊接电缆在工件上产生二次磁场等。
5)工件焊接部位被污染焊接坡口及其附近的铁锈、油污或其他污物在焊接时将产生大量气体,促使气孔生成,焊接之前应予清除。
(2)裂纹通常情况下,埋弧焊接头有可能产生两种类型裂纹,即结晶裂纹和氢致裂纹。
前者只限于焊缝金属,后者则可能发生在焊缝金属或热影响区。
1)结晶裂纹钢材焊接时,焊缝中的S 、P等杂质在结晶过程中形成低熔点共晶。
随着结晶过程的进行,它们逐渐被排挤在晶界,形成了“液态薄膜”。
焊缝凝固过程中,由于收缩作用,焊缝金属受拉应力,“液态薄膜”,不能承受拉应力而形成裂纹。
可见产生“液态薄膜”和焊缝的拉应力是形成结晶裂纹的两方面原因。
钢材的化学成分对结晶裂纹的形成有重要影响。
硫对形成结晶裂纹影响最大,但其影响程度又与钢中其他元素含量有关,如Mn与S 结合成MnS而除硫,从而对S的有害作用起抑制作用。
Mn还能改善硫化物的性能、形态及其分布等。
因此,为了防止产生结晶裂纹,对焊缝金属中的Mn/S值有一定要求。
Mn/S值多大才有利于防止结晶裂纹,还与含碳量有关。
图1 表示C 、Mn 、S含量与焊缝裂纹倾向的关系。
可见含C量愈高,要求Mn/S值也愈高。
Si和Ni的存在也会增加S的有害作用。
埋弧焊焊缝的熔合比通常都较大,因而母材金属的杂质含量对结晶裂纹倾向有很大关系。
母材杂质较多,或因偏析使局部C 、S含量偏高,Mn/S可能达不到要求。
可以通过工艺措施。
(如采用直流正接、加粗焊丝以减小电流密度、改变坡口尺寸等) 减小熔合比;也可以通过焊接材料调整焊缝金属的成分,如增加含Mn量,降低含C 、Si量等。
焊缝形状对于结晶裂纹的形成也有明显影响。
窄而深的焊缝会造成对生的结晶面,“液薄膜”将在焊缝中心形成,有利于结晶裂纹的形成。
焊接接头形式不同不但刚性不同,并且散热条件与结晶特点也不同,对产生结晶裂纹的影响也不同。
2)氢致裂纹这种裂纹较多的发生在低合金钢、中合金钢和高碳钢的焊接热影.响区中这可能在焊后立即出现,也可能在焊后几时、几天、甚至更长时间才出现。
这种焊后若干时间才出现的裂纹称为延迟裂纹。
氢致裂纹是焊接接头含氢量、接头显微组织、接头拘束情况等因素相互作用的结果。
在焊接厚度10mm 以下的工件时,一般很少发现这种裂纹。
工件较厚时,焊接接头冷却速度较大,对淬硬倾向大的母材金属,易在接头处产生硬脆的组织。
另一方面,焊接时溶解于焊缝金属中的氢,由于冷却过程中溶解度下降,向热影响区扩散。
当热影响区的某些区域氢浓度很高而温度继续下降时,一些氢原子开始结合成氢分子,在金属内部造成很大的局部应力,在接头拘束应力作用下产生裂纹。
焊接某些超高强度钢时,这种裂纹也会出现在焊缝金属中。
针对氢致裂纹产生的原因,可以从以下几方面采取措施。
a.减少氢的来源及其在焊缝金属中的溶解,采用低氢焊剂;焊剂保管中注意防潮,使用前严格烘干;对焊丝、工件焊口附近的锈、油污、水分等焊前必须清理干净。
通过焊剂的冶金反应把氢结合成不溶于液态金属的化合物,如高Mn 高Si 焊剂可以把H 结合成HF 和OH 两种稳定化合物进入熔渣中,减少氢对生成裂纹的影响。
b.正确的选择焊接工艺参数,降低钢材的淬硬程度并有利于氢的逸出和改善应力状态,必要时可采用预热。
c.采用后热或焊后热处理焊后后热有利于焊缝中的溶解氢顺利的逸出。
有些工件焊后需要进行熟处理,一般情况下多采用回火处理。