冷轧钢带65mn全氢罩式炉球化退火工艺研究及应用
全氢罩式退火炉工艺设备及工程化特点

柬工案技术
工 业 技 术
全氢罩 式退 火炉工艺设 备及工程化特 点
赵 云 飞
( 北京京诚凤凰工业炉工程技术有 限公 司 , 北京 1 0 0 1 7 6)
摘 要 :本文介 绍了全氢罩式退火 炉工艺及设备 主要特 点,并依托某钢厂 的冷轧退火线 ,从工程 的角度介 绍 了随着市场 的需求 ,对 退火钢卷的 需求不 断增 大,热处理 配置 需要进行相应提 升改造 ,本文针对其产品方案重点介绍 了产线 的工艺流程及 主体设备 的相 关参数及工程化特点
2 . 1 工 艺 流 程
7 5 0 ℃ 。2 )循环风机 电机功率 :2 2 k W;转速 :最大 2 2 0 0 r p m( v W ; 风量 :约 1 0 0 0 0 0 m / h ;气流温度 ( 最高 ):7 5 0 ℃。 ( 1 )选 择退火程序 。在 正常生产过程 中 , 退 火程序从 C OS 传 送 ( 2 )炉 台隔热保 温材料 。为耐 火纤 维 ,安 装炉 台 内部 ,以保护 到炉台 P L C , 并储 存 P L C中 ,直到接收新的退火程序 。 炉台钢结构及循环风机 电机 。温度 ( 最高 ):1 2 0 0 ( 2 )放置 内罩。炉 台上料后 ,将 内罩 放在 炉台上 ,然 后用液 压 2 . 2 . 3 冷 却 罩 夹紧机构夹紧 到水 冷炉台法兰的 圆形密封 件上 ,这样可 以达 到很 好的 采用风冷 +喷淋冷却 。每个冷却罩主要 由 2个冷却用离心风机 、 密封。 不锈钢罩体 、喷淋冷却装置 、导向臂 、冷却水及 电源的手动接头等 。 ( 3 ) 冷 泄漏测试 。泄 漏测试可 以在室温度 下 自动完成 。将 内罩 1 )风机 径向风机冷 却空气流量 :约 2 ×1 7 7 0 0 m / h 。电机功率 : 内的压力 自动地调节到约 5 0 0 0 P a ,并关 闭所有入 口和 出口阀门。 2 ×5 . 5 k W,1 0 0 0 r p m。2 )罩体 由不锈钢型 钢加固成 圆环 ,包括不锈 钢 ( 4 ) 初始 吹扫 。如果工作 空间无漏气 ,那 么将用氮气 动吹扫工 罩 壳、提升 梁、导向臂、支撑腿等。壳体材质 :0 C r l 8 N i 9 。3 )喷淋冷 作空气 。吹扫结束后 , 炉 台准备退 火。 却装置在 内罩 温度低于 2 5 0 ℃后对 内罩喷水进 行冷却 ,直到达到 出炉 ( 5 ) 压力控制 。为了使 内罩 内的压 力高 出外界压力 一定范 围, 温度。由顶部喷嘴、中部环形 喷嘴、 供水管道组成 。 喷淋 水压 力: 0 . 3 一 可以自 动控制 工作 区压 力。 O . 4 5 M P a 。温度 :3 3 ℃。流量 :2 8 m / h 。 ( 6 ) 加热 。加 热罩燃烧系统 由几个位于 加热罩周 围的高速烧 嘴 2 . 2 . 4 内罩 组成 。 为耐热钢板气 密焊接的钢结构 ,壳 体为波纹形状 。主 要 由波纹罩 ( 7 ) 温 度控 制 。对于 连续 控制 ,将 提供 两个单 独 的温度 控 制 体、 吊装环 、冷却 水法兰、导 向臂 、冷 却水手动接头 等。壳体材质 : 器 ( 分 别用 于加热 罩和 炉台 ) ;对于 开 /关控制 ,将 提供两 个其 它 0 Cr 2 3 Nj 1 3 控制器 ( 分别 用于加 热罩和 炉 台)。 ( 8 )连续 控制。 当加 热罩 ( 或 炉 台)控 制器 发出打 开信号 时 , 3 产 品方案 机动 阀将打 开 ; 当控 制器发 出 “ 关闭”信号时 ,它将逐渐关 闭。在 加 3 . 1 冷硬卷规格 热罩控制站配备有手动调节 的手动 /自动方式开关 。 带 钢 厚 度 :O . 3 - 2 5 m m;带 钢 宽 度 :9 0 0 - 1 6 5 0 mm;带 卷 内 径 : ( 9 ) 温度测 量 。如果加 热罩温度超过 设定点 2 O ℃, 燃烧 系统将 q  ̄ 6 1 0 m m。带 卷 外径 : 1 0 0 O ~ 2 ( ) ( 1 0 m m;最 大卷 重 :3 0 t 。钢 卷单 重 : 关 闭。如 果炉 台温度 超过 设定 点 1 O ℃, 为 了保 护带卷 过 热 ,应 关闭 最大 2 0 k g / m m,平均 1 6 k g / mm。性能等级 :C Q、DQ、H S S 。 燃烧 系统。 3 . 2 产品大纲 ( 1 0 ) 燃气蝶 阀渗 漏测试 。当燃烧系统接通时 ,渗漏探测器 ( 已 本工程 设计退 火能力 2 O . 1 1万吨 /年 ,热处理 品种 :C Q 占5 0 %、 证 明为安全装置 )将测试燃气蝶 阀和联 轴器是 否渗漏 。 DQ 占 1 0 %、 DDQ/ E DDQ 占 3 0 %、 Hs I J A占 1 O %。 ( 1 1 )燃 烧室 预吹 扫。 当燃烧 系统打 开 时 ,预先 用 空气 吹扫燃 烧 室 。吹 扫时 间通 过 定时 继 电器 监督 。用 P L C 检 查该 继 电器 工作 4 工程特点及预期效 果 是 否正常 。 本工程建成后可达到如下预期效果 : ( 1 2 ) 冷却。将冷却罩放在内罩上 ,然后用空气和水混合 的冷却 其一 ,能够满足 产品结构调整调 整 ,提高冷轧深 冲钢产能和冷轧 系统 以高速将 带卷 冷却到大约 1 6 0 ℃。 产品竞争力 。本工程通过增建罩式 炉和市场 品种开 发 ,扩大深冲钢产 ( 1 3 ) 最终吹扫。冷却结束后 ,用氮气 吹扫工作 区。只有 当安全 能 ,产 品结构会大 幅改善 ,特别是深 冲钢热处理钢卷 的增加 ,其盈利 吹扫完成后 ,才能打开内罩。 能力和生存竞争能力会得到 明显 改善 。 2 . 2 设 备 特 点 其 二 ,能够 满足 上下 工序 产能 平衡 ,提升 冷轧 各机组 产 发挥 2 . 2 . 1 加热罩 规模 优势 ,降低 综合 成本 。工程建 成后 可 以扩大 退火产 能 ,酸洗 和 加热罩主要 由燃烧系统、罩体、排烟系统 、隔热保温材料组成 。 轧机 产能 也会 同步增 加 ,工序不 平衡 的矛盾 会得 到缓 解 ,吨钢综 合 设备主要参数 : ( 1 )罩体 。罩体 内径 :3 0 0 0 m m / 2 0 0 类型 ;罩体 成本 下降 。 内高 度 :6 5 9 0 m m / 2 0 0 ;类 型外 壳厚 度 :5 am r ;( 2 )燃烧 系 统。将 空 其 三 ,能够提升冷轧盈利 能力。可 以可提 升上 下各工序机组 作业 气、煤气 通过烧 嘴进行 燃烧 ,包括 烧 嘴、煤气系 统、空气 系统 。1 ) 率 ,降低成本 ,提 升冷轧 整体盈利能力 。
冷轧板带生产技术与管理之四-退火处理

焊机类型
焊机类型及型号说明
型号: MSW-C150D-26-2R2P) MSW: MASH SEAM WELDER(窄搭接焊机) C: C型架并带有铡刀式剪子 150D: 电源的额定容量是150KVA 2: 带钢最大厚度是2.3cm 6: 带钢最大宽度是1850cm 2R: 2个压轮和2个焊轮 2P: 2个通道(带有一个预载料通道)
八、全氢罩式退火炉的特点
九、退火方式比较
十、罩式退火工艺流程
60万吨的产能,约需 要退火炉35~40座, 投资大约6~7亿元人 民币。
例:年产60万吨的罩式退火机组构成
十一、罩式退火车间平面布置举例
十二、罩式退火工艺流程图
十三、全氢罩式退火炉控制界面举例
十四、罩式退火炉工艺曲线
连续退火篇
2、高强钢的退火原理
BH钢强化原理示意图
DP及TRIP钢种强化机理示意图
连退机组各钢种退火曲线
1、CQ
2、DQ(LC)
3、DQ(ULC)
4、DDQ
5、EDDQ
6、S-EDDQ
7、CQ-HSS 440
8、CQ-HSS 590
9、DQ-HSS 340 +DQ-HSS 440
10、DDQ-HSS 340 + DDQ-HSS 440
ULC类别钢种退火原理示意图
2、高强钢的退火原理
连续退火生产高强钢强化机理: 1)析出强化:通过在钢中形成分散状的、由碳与添加元素所形 成碳化物的析出物导致位错移动受阻,从而导致钢的强度增加。 析出强化采用的添加元素有钛、铌、钒等。 2)固溶强化:因固溶元素原子存在导致铁素体晶格产生畸变, 而导致位错运动受阻,并由此导致钢强度增加。通常采用的固溶 强化元素有硅、锰、磷等。 3)相变强化:由马氏体和贝氏体等低温相变生成物分散而导致 的强化; 4)晶粒细化:通过加快冷却速度,细化晶粒
冷轧罩式退火工艺及原理201807

应力过大造成的粘结风险,尤其对于特殊规格,根据实际温度差采用
相应时间的带罩缓慢冷却,降低冷却过程中的压应力,最大程度上减 少粘结风险;同时合理配炉,采用规格和卷位的合理搭配,减少易发
生粘结钢卷的粘结倾向。
• 平整生产的张力和速度控制:对于粘结较严重的钢卷在采用大张力和 高速生产,大于500m/min,使粘结情况减弱。
轧钢工培训材料
2018年7月
罩式退火工艺及原理
1、冷轧工序组织变化 2、退火原因 3、退火目的及作用 4、罩退与连续退火线比较 5、罩式退火工艺流程图 6、常用退火工艺曲线 7、罩式退火温度分布特点 8、退火粘结问题 9、钢卷在加热过程热应力分布
1、冷轧工序组织变化
酸轧工序压下率控制标准,以及带 钢组织演变机理和特点
加热过程的温度分布
冷却过程的温度分布
因钢卷整卷退火,在退火过程中温度存在差异。加热过程中,钢卷 外圈温度高芯部温度低,钢卷膨胀外圈受拉应力,内圈受压应力; 反之在冷却过程中外圈温度低芯部温度高,钢卷整体外圈受压应力 ,内圈受拉应力。
8、退火粘结问题
在冷硬卷的紧卷立卷再结晶退火过程中,经常发生相邻卷层间粘到一 起,增加了后道工序平整机的开卷张力,并且在开卷过程中会造成板 带撕裂,出现皱痕等情况,并且因同样的粘结力会造成不同程度板形 缺陷,这种缺陷就是我们通常称为的罩式炉粘钢。
4、罩退与连续退火线比较区别
• 罩式退火:生产周期长(几十个小时), 与清洗线、平整线分开布置,整体联成一条冷板生产流程,但 可选择的进行脱脂清洗,且钢种及规格对整体生产的影响较小, 可小批量灵活的组织生产,单炉台生产,炉台数量可根据产量 和品种变化随时增减,中间工序有库存缓冲,产量和品种适应 能力强,适合多品种,小批量生产及试验生产。 • 连续退火:生产周期短(几分钟),脱脂清洗、退火、平整联 成一条整体生产线,生产效率高,但受计划影响启停和规格品 种切换等成本高,产品规格覆盖范围不宜太宽, 产量不宜太低。 适合大批量,少品种生产。
冷轧65Mn带钢全氢罩式炉退火工艺的研究杨金龙
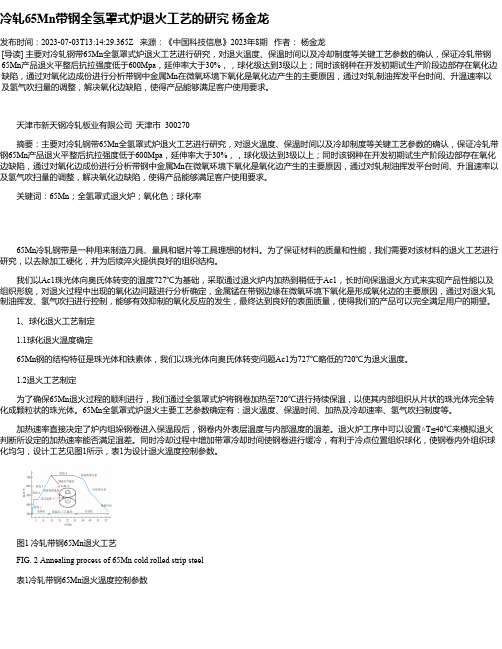
冷轧65Mn带钢全氢罩式炉退火工艺的研究杨金龙发布时间:2023-07-03T13:14:29.365Z 来源:《中国科技信息》2023年8期作者:杨金龙[导读] 主要对冷轧钢带65Mn全氢罩式炉退火工艺进行研究,对退火温度、保温时间以及冷却制度等关键工艺参数的确认,保证冷轧带钢65Mn产品退火平整后抗拉强度低于600Mpa,延伸率大于30%,,球化级达到3级以上;同时该钢种在开发初期试生产阶段边部存在氧化边缺陷,通过对氧化边成份进行分析带钢中金属Mn在微氧环境下氧化是氧化边产生的主要原因,通过对轧制油挥发平台时间、升温速率以及氢气吹扫量的调整,解决氧化边缺陷,使得产品能够满足客户使用要求。
天津市新天钢冷轧板业有限公司天津市 300270摘要:主要对冷轧钢带65Mn全氢罩式炉退火工艺进行研究,对退火温度、保温时间以及冷却制度等关键工艺参数的确认,保证冷轧带钢65Mn产品退火平整后抗拉强度低于600Mpa,延伸率大于30%,,球化级达到3级以上;同时该钢种在开发初期试生产阶段边部存在氧化边缺陷,通过对氧化边成份进行分析带钢中金属Mn在微氧环境下氧化是氧化边产生的主要原因,通过对轧制油挥发平台时间、升温速率以及氢气吹扫量的调整,解决氧化边缺陷,使得产品能够满足客户使用要求。
关键词:65Mn;全氢罩式退火炉;氧化色;球化率65Mn冷轧钢带是一种用来制造刀具、量具和锯片等工具理想的材料。
为了保证材料的质量和性能,我们需要对该材料的退火工艺进行研究,以去除加工硬化,并为后续淬火提供良好的组织结构。
我们以Ac1珠光体向奥氏体转变的温度727℃为基础,采取通过退火炉内加热到稍低于Ac1,长时间保温退火方式来实现产品性能以及组织形貌,对退火过程中出现的氧化边问题进行分析确定,金属锰在带钢边缘在微氧环境下氧化是形成氧化边的主要原因,通过对退火轧制油挥发、氢气吹扫进行控制,能够有效抑制的氧化反应的发生,最终达到良好的表面质量,使得我们的产品可以完全满足用户的期望。
冷轧罩式退火工艺及原理培训
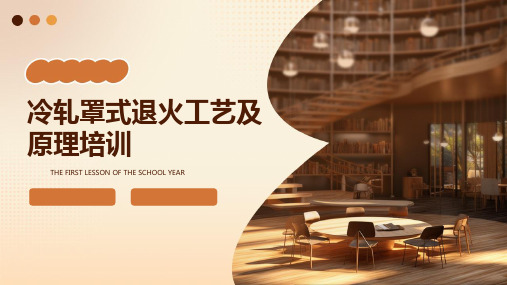
01
冷轧罩式退火工艺 实践操作
操作前的安全注意事项
佩戴防护眼镜和手套
在进行冷轧罩式退火工艺操作 前,务必佩戴合适的防护眼镜 和耐热手套,以防止高温和飞
溅物伤害。
检查设备状态
确保退火炉设备处于良好状态 ,炉门密封良好,无破损或老 化现象,以确保操作安全。
熟悉操作流程
操作前应详细了解冷轧罩式退 火工艺的操作流程和注意事项 ,避免因误操作引发安全事故 。
温度参数的优化
总结词
温度参数是冷轧罩式退火工艺中的关 键参数,对退火效果和产品质量具有 重要影响。
详细描述
通过调整温度参数,可以控制金属材 料的微观组织和性能。优化温度参数 可以提高产品的机械性能、韧性和延 展性,同时降低生产成本和能耗。
时间参数的优化
总结词
时间参数是冷轧罩式退火工艺中的重要因素,对退火效果和产品质量具有显著 影响。
。
热传导与对流
在退火过程中,热量通过热传导和 对流的方式传递给金属,影响退火 温度场的分布和均匀性。
热膨胀与热收缩
退火过程中金属会发生热膨胀和热 收缩,对金属的尺寸精度和组织结 构有一定影响。
01
冷轧罩式退火工艺 流程
冷轧罩式退火前的准备
清理设备
确保退火设备清洁,无残留物, 为退火过程提供良好的环境。
案例三
总结词
工艺参数调整
详细描述
该铜加工企业通过不断调整冷轧罩式 退火的工艺参数,如温度、气氛和时 间等,成功地提高了产品的机械性能 和耐腐蚀性,满足了市场需求。
感谢观看
THANKS
THE FIRST LESSON OF THE SCHOOL YEAR
加工领域。
在钢铁工业中,该工艺主要用于 生产各种冷轧板卷、涂镀层钢板
冷轧带罩式炉退火后容易出现的问题原因及解决措施

冷轧带钢经罩式炉退火后容易出现的问题原因及解决措施退火后容易出现氧化,高温氧化及保护气体不纯氧化。
带钢过硬或软,带钢粘结可以降低出炉温度,Q料易氧化。
保温时间短升温速度快都会导致带钢硬。
轧机张力大会影响粘接,还有板型卷型等都有影响冷轧带钢在退火过程中发生哪些组织性能变化?退火:将金属缓慢加热到一定温度,保持足够时间,然后以适宜速度冷却(通常是缓慢冷却,有时是控制冷却)的一种金属热处理[1]工艺。
目的是使经过铸造、锻轧、焊接或切削加工的材料或工件软化,改善塑性和韧性,使化学成分均匀化,去除残余应力,或得到预期的物理性能。
退火工艺随目的之不同而有多种,如重结晶退火、等温退火、均匀化退火、球化退火、去除应力退火、再结晶退火,以及稳定化退火、磁场退火等等。
1、金属工具使用时因受热而失去原有的硬度。
2、把金属材料或工件加热到一定温度并持续一定时间后,使缓慢冷却。
退火可以减低金属硬度和脆性,增加可塑性。
也叫焖火。
退火的一个最主要工艺参数是最高加热温度(退火温度),大多数合金的退火加热温度的选择是以该合金系的相图为基础的,如碳素钢以铁碳平衡图为基础(图1)。
各种钢(包括碳素钢及合金钢)的退火温度,视具体退火目的的不同而在各该钢种的Ac3以上、Ac1以上或以下的某一温度。
各种非铁合金的退火温度则在各该合金的固相线温度以下、固溶度线温度以上或以下的某一温度。
重结晶退火应用于平衡加热和冷却时有固态相变(重结晶)发生的合金。
其退火温度为各该合金的相变温度区间以上或以内的某一温度。
加热和冷却都是缓慢的。
合金于加热和冷却过程中各发生一次相变重结晶,故称为重结晶退火,常被简称为退火。
这种退火方法,相当普遍地应用于钢。
钢的重结晶退火工艺是:缓慢加热到Ac3(亚共析钢)或Ac1(共析钢或过共析钢)以上30~50℃,保持适当时间,然后缓慢冷却下来。
通过加热过程中发生的珠光体(或者还有先共析的铁素体或渗碳体)转变为奥氏体(第一回相变重结晶)以及冷却过程中发生的与此相反的第二回相变重结晶,形成晶粒较细、片层较厚、组织均匀的珠光体(或者还有先共析铁素体或渗碳体)。
带钢退火工艺及其装备(全氢罩式退火炉)
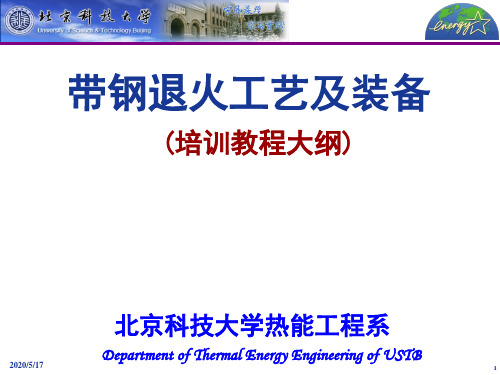
(培训教程大纲) 培训教程大纲)
北京科技大学热能工程系
2011-3-18
Department of Thermal Energy Engineering of USTB
1
第一部分—全氢罩式炉退火工艺及其装备 第一部分 全氢罩式炉退火工艺及其装备
一、发展历程(历史沿革) 发展历程(历史沿革) 二、基本构造与操作过程 三、炉内传热过程的分析 四、数值模拟与实验验证 五、参数优化及其分析 六、主要结论
38<t ≤ 58.5 f=f 0 + a 1 e -(t-t0)/x1 f 0 =0.79184 t 0 =38.03 a 1 =0.21853 x 1 = 3.07573 f=a+b 1 t+b 2 t 2 + b 3 t 3 a= -23.79697 b 1 =1.48994 b 2 =-0.02926 b 3 =1.89788 × 10 -4
2011-3-18
全氢罩式退火炉热过程 离线数学模型计算结果及分析
2011-3-18
8
加热过程
加热过程 均热过程
冷却过程
带加热罩冷却过程 辐射冷却过程 带冷却罩冷却过程 快速冷却(氢气旁路冷却或水喷淋冷却)
2011-3-18
9
建立数学模型的目的
建立全氢罩式炉退火过程数学模型, 建立全氢罩式炉退火过程数学模型 , 进行离线 预报钢卷退火工艺曲线, 预报钢卷退火工艺曲线 , 为今后实现钢卷温度 的在线跟踪和炉温的动态计算提供基础。 的在线跟踪和炉温的动态计算提供基础。 对不同来料、 不同产品的退火过程, 对不同来料 、 不同产品的退火过程 , 只要将原 始数据作为模型输入条件, 始数据作为模型输入条件 , 模型即可计算出相 应的退火曲线, 应的退火曲线 , 为工艺优化与过程控制提供依 据。 建立、 完善不同钢种、 建立 、 完善不同钢种 、 不同规格的钢卷在不同 产量条件下的优化退火工艺制度, 产量条件下的优化退火工艺制度 , 为今后实现 在线控制提供坚实的理论基础。 在线控制提供坚实的理论基础。
冷轧全氢罩式退火炉工艺研究

度热点与冷点温差过高 ,钢卷均热不够 ,粘结缺陷 所 占的 比例较大 、性能一致性较差 、延伸率 的富余 量 低 。 因此 冷轧 全 氢 罩式 退 火工 艺有 待 进一 步 的优
化。
4 退 火 工艺优 化
家热轧原料的生产 ,退火后带钢性能合格率大大提 高 ,带钢表面黑斑 、黑带缺陷基本得到了解决 。 冷 轧厂从 2 0 1 1 年开始 使 用重 钢 1 7 8 0自产 的热卷 原 料 ,并 逐 步取 代 了外 购热 轧 卷 ,结 合 自产 原 料 的 技术 参数 , 目前 1 7 8 0 热 轧原 料 的退火 工艺 已经初步 形成 ,产品的质量也得到了较大的提升。但是也存
日 U
吹 扫
4 2 0 ℃
水冷
漏 测 试
H z 吹扫
——◆
1 0 0 ℃ 以 下
・ ● — — — —— 一
图 1 冷 轧 全 氢 罩 式 退 火 炉 退 火 工 艺 曲线 示 意 图
3 现 状
在 诸 多 的 厂 罩式 退 火炉 设 备 为奥 地  ̄ J I E B N E R 公 司设 计 制造 的H I C O N / H2全 氢罩 式退 火炉 ,型 号Ho g 1 9 0 / 5 4 0 S t — Hz — B,共 2 4座 ,包 括 2 4个 内罩 ,l 2 个 加热 罩 ,1 2个冷 却罩 ,设 计产 能为 2 0万 吨/ 年 。经 过 多年 的生 产摸 索 ,退火 工 艺 已经能 够 适应 不 同厂
C h o n g q i n g I r o n a n d S t e e l C o . , L t d . T o s t u d y t h e h e a t i n g , k e e p i n g w a r m, c o o l i n g p r o c e s s , S O a s t o a c h i e v e t h e o b j e c t i v e o f
冷轧板的退火工艺

冷轧板的退火工艺(共14页)--本页仅作为文档封面,使用时请直接删除即可----内页可以根据需求调整合适字体及大小--冷轧板的退火工艺:连续退火和罩式退火的比较冷轧产品是钢材中的精品,属高端产品,具有加工精细、技术密集、工艺链长、品种繁多、用途广泛等特点。
国际钢铁工业发展实践表明,随着经济社会发展,冷轧产品在钢材消费总量中的比重在不断提高,并发挥着越来越重要的作用。
冷轧后热处理是冷轧生产中的重要工序,冷轧板多为低碳钢,其轧后热处理通常为再结晶退火,冷轧板通过再结晶退火达到降低钢的硬度、消除冷加工硬化、改善钢的性能、恢复钢的塑性变形能力之目的。
冷轧板的再结晶退火在退火炉中进行,冷轧板退火炉分为罩式退火炉和连续退火炉,罩式退火炉又分为全氢罩式退火炉与普通罩式退火炉。
冷轧板退火技术的发展与罩式退火炉和连续退火炉的发展是密不可分的[10]。
退火工艺流程如图所示:图退火工艺流程示意图表某钢厂罩式退火炉工艺参数通过加热罩热电偶进行温度检测,超温<20℃热点/冷点温度CQ:710℃/640℃DQ:710 ℃/660℃DDQ:710 ℃/680℃HSLA:680℃/660℃一般生产中CQ、DQ热点和冷点温度差要大一些。
分别为90 ℃、70 ℃开始喷淋冷却温度内罩表面温度200 ℃,卷心温度:380℃左右生产调试中进行检测试验以确定不同钢卷开始喷淋冷却工艺出炉温度160 ℃出炉吊至终冷台冷却到平整温度约40 ℃图典型的罩式炉退火工艺温度曲线图罩式退火工艺罩式退火是冷轧钢卷传统的退火工艺。
在长时间退火过程中,钢的组织进行再结晶,消除加工硬化现象,同时生成具有良好成型性能的显微组织,从而获得优良的机械性能。
退火时,每炉一般以4个左右钢卷为一垛,各钢卷之间放置对流板,扣上保护罩(即内罩),保护罩内通保护气体,再扣上加热罩(即外罩),将带钢加热到一定温度保温后再冷却。
罩式退火炉发展十分迅速,2O世纪7O年代的普通罩式退火炉主要采用高氮低氢的氮氢型保护气体(氢气的体积分数2%~4%,氮气的体积分数为96%~98%)和普通炉台循环风机,生产效率低,退火质量差,能耗高;为了弥补普通罩式炉的缺陷,充分发挥罩式炉组织生产灵活,适于小批量多品种生产,建造投资灵活,可分批进行的优点,7O年代末奥地利EBNER公司开发出HICON/H 炉(强对流全氢退火炉),8O年代初德国LOI公司开发出HPH炉(高功率全氢退火炉)。
冷轧企业罩式退火技术工艺操作规程

1、生产前的准备工作和设备检查.1与气保站联系保护气体,保证生产后能持续供应。
.2检查将投入使用的保护罩、加热罩、炉台、各密封圈、抽烟风机等是否完备。
不能使用的应修好或更换。
.3开启厂房外水冷却塔,打开循环水泵,打开炉台及循环风机冷却水。
检查冷却水是否已通,流量是否足够。
.4试运行炉台的循环风机,试运行前先用手盘动叶轮,确认转动正常无异物后人员远离风机,才能低速启动运行,运行方向是否逆时针,如果不是,叫电工处理。
如果是,再试高速运行,试好后关闭。
.5装炉的钢卷是否已经备好,对号认定。
并排出要装炉的卷号的顺序。
.6必须有足够的瓶装氮气或者液体汽化氮储备(安全生产的必要条件)。
.7自来水应保证供应(安全生产的必要条件)。
.8只要有炉台生产(或烘炉),任何情况下必须有人巡检冷却水、炉压、炉温、烟道积水程度(此项包括不生产时)等关键项目和部位,发现问题,及时处理。
2、装炉2.1 同一炉退火的钢卷,要尽量安排钢种、宽度、厚度、卷径相似的钢卷。
(以上四个项目,以重要程度为序)2.2 装炉时装吊一定要平稳,吊卷和吊空钩都应将夹具落到下死点,才能起吊,炉台钢卷座、钢卷和对流板应在一个同心轴上。
2.3 最下一层的钢卷,如果没有十字支撑架,应打径向捆带,或者点焊。
所有厚钢板则一定要点焊内、外径,气焊割除溢出边,方可装炉。
使用十字支撑架,如果发现水平变形,应翻面后再使用。
2.4 钢卷的宽度、厚度相同,外径不同时,应把外径大的放在下面,小的放在上面。
2.5 当钢卷厚度相同或不相同,外径相同,宽度不同时,宽的放在下面,窄的放在上面。
2.6 当外径和宽度相同,应把厚的放在下面,薄的放在上面。
2.7 严重的塔形卷、溢出边卷不能进罩式炉退火。
2.8 装炉和吊罩应有两人完成,不允许多人参与,以免造成混乱。
2.9 装炉完后,应将热点偶插入钢卷内,并固定好。
3、吊装保护罩3.1 吊装保护罩之前,炉台和保护罩要进行清扫,特别是密封圈结合处,然后在吊装保护罩。
冷轧带钢罩式炉退火工艺优化研究

冷 轧 带 钢罩 式 炉 退火 工 艺优 化 研 究
韩 平
( 溪 钢 铁 集 团公 司 冷 轧厂 , 宁 本 溪 17 0 ) 本 辽 100
摘要: 通过 对热处理机组的 实际生产情 况进行分析 , 确定 了退 火工艺优化 的方 向, 对加 热 与冷却 的控制 工 艺做 了优 化调 整 。在 生产 实践的基础上 , 进行 了大量 的工艺优化试验 , 取得 了较好 的效果 , 建立 了一套较为 完善 的退火制度。
( 般小于 9 一 o吨 ) 炉 台 , 必 采 用 控 制 加 热 的 模 式 , 以 的 不 可
完全采 用全速升温的加热模式 , 这样可 以最大 限度 的发挥机
组 的 加 热 能 力 , 效 减 少 加 热 周 期 , 而 提 高 机 组 产 能 。 由 有 进 于退 火 过 程 要 将 带 钢 表 面 残 留乳 化 液 全 部 挥 发 出 去 , 高 表 提
关键 词 : 冷轧带钢 ; 火; 艺优化 退 工
中 图 分 类 号 :G162 T 5 . 文 献 标 识 码 : A
0 前 言
本溪钢 铁集 团公司冷 轧厂共 建有 退火 炉 台 4 5座 , 计 设 产量为 8 0 0 2 0 0吨 , 冷轧 厂产量 目前 已经达到 10万吨 , 3 热处 理机组成 了冷轧生产 的瓶颈 , 提高机组的产能成 了必须研 究 的课题 。热处理 工序是本 钢冷 轧厂生 产过程 中 的一道重 要 工序 , 主要是通过罩式退火 炉对冷轧后的钢卷进行再结 晶退 火, 以保证冷轧产 品的质 量要求 。对冷轧带钢进行再结 晶光 亮退火 , 退火过程全部 由计算 机 自动控制 , 自动化程度较高 。 其优点是在纯氢 气状 态下退火 可以保证钢卷 不被氧化 , 且 并
冷轧带钢退火工艺优化探讨

钢卷号
钢种 厚度 / mm 宽度 / m 外径 / m 重量( g m m k)
火技术非 常先进 , 在保证 质量的基础上要想再提高 但
产量 , 就需要 缩短退火 时间 , 以根据全 氢罩式退 火 所 炉的实际生产情况 , 退火时 间 、 从 过剩 系数 K及 过程 气氛方 面对 生产工艺进行 了优化试验 , 在产 品质量和
平 均缩短 2h~4h 冷却时 间缩 短 了 7h~8h 产量 , ,
提 高了1. 9 6%。
行 定期取样 做热值 分析 , 定合适 的 “ 确 空燃 ” 同时 比。 采 取措施 减小燃气 压力 波动范 围。 证 K值稳定 在 保
03 0 _ . 。 ~ 4间
3 减小燃 气压力 波动范围, . 2 保证 K值稳定在 0 . 3~
品表 面质 量 提 高 。
关键词
冷轧 带钢
罩式炉 退 火 工艺参数
优化
1 概 述
天津鞍钢天铁钢板公 司选用 的是奥地 利 E N R BE
表 2 钢 卷信 息
公 司的全氢罩式退 火炉。 全氢罩式退火采用强对 流循 环、 全氢保护气氛和气一 水冷却 等先进技术 , 具有 效率 高、 质量好 、 能耗低等优势 , 正逐渐 成为冷 轧钢带 周期
极易 出现 同一钢 卷冷热点 温差过大 导致力学 性能不 均 的现象 。因此 , 在保证温差 的前提下尽可能地缩短
221 对退火 时间进行优化 . .
退火 时间 , 提高 产量 , 即对 退火工艺进 行优化 是我们
十分关注 的课题 。 多冷轧薄板生产厂和研究单位对 许
炉 内温度 的分 布与控制 电偶 ( T C )和炉 台压紧 电偶 ( T 温度 的关系进行 了研究与实测 , 出了不 同冲压 B ) 得
全氢罩式退火生产工艺的优化实践

昆钢 科技 K n a gK j u gn e i
2 1年 1 0 1 月
全氢罩 式退火 生产 工艺 的优化 实践
钱 明 生 Biblioteka ( 生产管理 中心 ) 摘 要 本 文介 绍 了昆钢冷轧全氢罩式退 火生产工艺原理 ,通过分析黑斑 ( 黑带 )和 粘结的影 响 因素 ,提 出
的温 度制 度和 工艺气 氛 制度 ,并借 助计算 机 程序控
制实 现对 预定 物料 的加 热 、保 温 和冷却 ,从 而实现
最终 的退火 目的 。
昆钢 科技
2 1 年第 1 01 期
全氢罩式退火生产工艺 流程如下 :
发情 况几 乎都 不相 同 ,对 退火来 说 总是希 望轧制 油 能 在尽量 短 的时 间 内挥发 掉 。但 由于轧制 油本 身具
fc r o ba ks o(e ) n t kbek eea aye , t zt npo oa f H w r e at s f lc p t h a ds c ra s r n lzdo i ai rp sl o o b i w p mi o s HP eet n h
po oe . r p s d
Ke o ds o dr l n , y W r c l ol gHPH u a ep o u to e h o o ;r cie i f r c ;r d cin tc n lg p a tc s n y
不尽快解决 的首要课题 。
1 前 言
2 全 氢罩式退 火生产工 艺介 绍及存在
Abs r c n t s p p r h n e l e h o o y o t a tI hi a e ,t e a n a i t c n lg fHPH n c l oln fKI C wa nr d c d,fe t ng i od r l g o S s i to u e ef c i
冷轧带钢退火技术发展的探讨
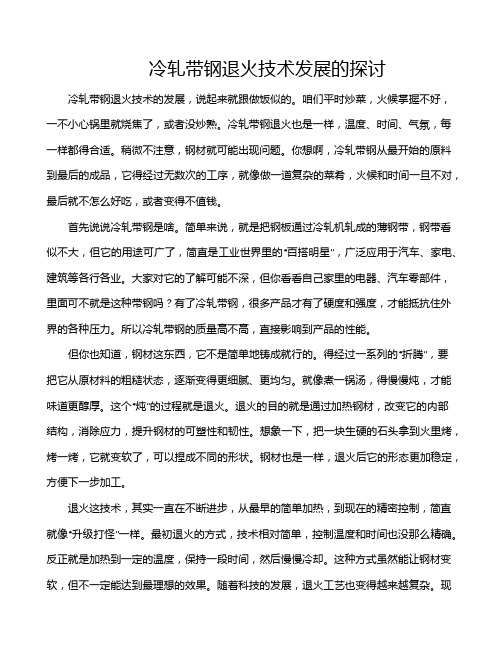
冷轧带钢退火技术发展的探讨冷轧带钢退火技术的发展,说起来就跟做饭似的。
咱们平时炒菜,火候掌握不好,一不小心锅里就烧焦了,或者没炒熟。
冷轧带钢退火也是一样,温度、时间、气氛,每一样都得合适。
稍微不注意,钢材就可能出现问题。
你想啊,冷轧带钢从最开始的原料到最后的成品,它得经过无数次的工序,就像做一道复杂的菜肴,火候和时间一旦不对,最后就不怎么好吃,或者变得不值钱。
首先说说冷轧带钢是啥。
简单来说,就是把钢板通过冷轧机轧成的薄钢带,钢带看似不大,但它的用途可广了,简直是工业世界里的“百搭明星”,广泛应用于汽车、家电、建筑等各行各业。
大家对它的了解可能不深,但你看看自己家里的电器、汽车零部件,里面可不就是这种带钢吗?有了冷轧带钢,很多产品才有了硬度和强度,才能抵抗住外界的各种压力。
所以冷轧带钢的质量高不高,直接影响到产品的性能。
但你也知道,钢材这东西,它不是简单地铸成就行的。
得经过一系列的“折腾”,要把它从原材料的粗糙状态,逐渐变得更细腻、更均匀。
就像煮一锅汤,得慢慢炖,才能味道更醇厚。
这个“炖”的过程就是退火。
退火的目的就是通过加热钢材,改变它的内部结构,消除应力,提升钢材的可塑性和韧性。
想象一下,把一块生硬的石头拿到火里烤,烤一烤,它就变软了,可以捏成不同的形状。
钢材也是一样,退火后它的形态更加稳定,方便下一步加工。
退火这技术,其实一直在不断进步,从最早的简单加热,到现在的精密控制,简直就像“升级打怪”一样。
最初退火的方式,技术相对简单,控制温度和时间也没那么精确。
反正就是加热到一定的温度,保持一段时间,然后慢慢冷却。
这种方式虽然能让钢材变软,但不一定能达到最理想的效果。
随着科技的发展,退火工艺也变得越来越复杂。
现在,很多冷轧带钢的退火技术,已经采用了真空退火、气氛控制退火等更为精密的工艺。
通过控制气氛的成分和温度,退火后的钢材不仅变得更加均匀,而且性能也大大提升。
不过呢,退火技术的进步,绝对不是一蹴而就的。
冷轧罩式退火工艺及原理201807ppt课件

粘结解决措施
• 张力控制方面:酸轧采用阶梯张力控制,最大程度的降低卷曲张力, 尤其对于薄规格。对于品种钢及特殊规格、钢种等流向脱脂清洗线, 既能提高板面质量而且能降张力,增加防粘层等,使粘结几率降低;
1、冷轧工序组织变化
酸轧工序压下率控制标准,以及带 钢组织演变机理和特点
1、冷轧工序组织变化
退火工序影响再结晶后晶粒大小的主要 因素是退火温度和保温时间:在一定的冷 变形条件下, 再结晶后的晶粒大小随退 火温度和保温时间的不同而变化,加热 温度越高,保温时间越长,晶粒越粗大。
晶粒尺寸
退火温度/*c
连续退火:经过脱脂清洗表面清洁,开卷加热带钢温度均匀,带 钢平直度,板形优良。适合生产表面要求较高的产品和薄规格 产品。
5、罩式退火工艺流程图 装料;内罩;加热罩;冷却
内罩
加热罩
冷却风机水水ຫໍສະໝຸດ 冷却 风机喷淋冷却
罩
式
退
内罩
火
炉
加热罩 钢卷
炉台
6、常用退火工艺曲线
6、常用退火工艺曲线
罩式退火工艺
4、罩退与连续退火线比较区别
• 罩式退火:生产周期长(几十个小时), 与清洗线、平整线分开布置,整体联成一条冷板生产流程,但 可选择的进行脱脂清洗,且钢种及规格对整体生产的影响较小, 可小批量灵活的组织生产,单炉台生产,炉台数量可根据产量 和品种变化随时增减,中间工序有库存缓冲,产量和品种适应 能力强,适合多品种,小批量生产及试验生产。
1、冷轧工序组织变化
经过冷轧加工后的钢卷,由于其晶粒被破碎拉长,晶格发生严重畸变, 使得钢的硬度增加,塑軔性降低,即产生加工硬化现象。通过将其加 热到再结晶温度以上,奥氏体转化温度以下,并保温一定时间,使晶 界上不稳定的原子由于热运动重 新排列,经过形核、长大这一过程, 形成新的等轴 晶粒,即产生再结晶现象。从而使钢的强硬度降低,塑 韧性增加,使得带钢获得良好的工艺及使用性能。再结晶的发生需要 一定的时间和温度,但随着温度的升高和时间的过分延长,已形成的 等轴晶粒其晶界之间会发生融合,新的等轴晶粒继 续长大,这一过程 将使钢的各项性能再次下降。 所以再结晶退火可概括为:通过加热和保 温,既要使经冷轧后的钢发生再结晶,同时又要防止其晶粒过分长大。
- 1、下载文档前请自行甄别文档内容的完整性,平台不提供额外的编辑、内容补充、找答案等附加服务。
- 2、"仅部分预览"的文档,不可在线预览部分如存在完整性等问题,可反馈申请退款(可完整预览的文档不适用该条件!)。
- 3、如文档侵犯您的权益,请联系客服反馈,我们会尽快为您处理(人工客服工作时间:9:00-18:30)。
冷轧钢带65mn全氢罩式炉球化退火工艺研究
及应用
1 概述
冷轧钢带65Mn是一种高强度、高硬度的低合金钢,因其卓越的机
械性能被广泛应用于机械制造等行业。
然而,冷轧后的钢带会产生强
烈的应力,影响其机械性能和形状稳定性,需要进行球化退火处理。
本文研究了全氢罩式炉球化退火工艺及其应用。
2 全氢罩式炉球化退火工艺原理
全氢罩式炉球化退火工艺是一种常用的球化退火工艺。
该工艺采
用氫气作为炉内退火气体,将钢带置于全氢罩式炉内进行加热、保温
和冷却。
由于氫氣分子小,能够快速渗透进入钢带内部,有效降低钢
带的内部应力和硬度。
在实际操作中,将退火炉内加入一定量的氫氣,形成一定浓度的
氫氣氛,将钢带置于在高温氫氣氛中进行加热,使钢带达到退火温度,并保持一定时间,然后在氫氣氛中冷却至室温,即完成了球化退火处理。
3 全氢罩式炉球化退火工艺的优点
(1)钢带表面无氧化皮、无碳化物和无金属污染,有利于表面质
量的提高和后续加工处理的降低。
(2)由于氫氣分子小,能够有效渗透进入钢带内部,减少内部氧
化并降低内应力和硬度,同时还能降低球化退火温度,大大缩短生产
周期和能耗。
(3)由于球化退火温度降低,钢带在退火过程中具有良好的韧性
和塑性,使得其具有更好的加工性能和形状稳定性。
4 实验分析
为了研究全氢罩式炉球化退火工艺的适用性,我们在实验室进行
了一系列实验。
首先,我们制备了一批65Mn冷轧钢带,将其分成两组,一组采用
常规的空气球化退火,另一组采用全氢罩式炉球化退火。
退火处理后,我们对两组样品进行性能测试,得到如下结果。
对比两组样品的硬度和拉伸强度,我们可以发现,采用全氢罩式
炉球化退火的样品的硬度和拉伸强度均显著低于常规空气球化退火的
样品。
这说明,全氢罩式炉球化退火能够有效降低外部和内部应力,
同时还能提高钢材的韧性和塑性,使其更适合进行后续加工。
5 工业应用
全氢罩式炉球化退火工艺具有广泛的工业应用价值。
例如在汽车、航空、军工等高端制造领域,对冷轧钢带的机械性能要求极高,采用
全氢罩式炉球化退火工艺能够满足这些行业对钢材性能、品质和稳定
性的要求。
此外,在大规模生产中,采用全氢罩式炉球化退火工艺还能够降
低生产成本、提高生产效率和节约能源,是一种具有实际应用价值的
钢板球化退火处理工艺。
6 结论
本文研究了全氢罩式炉球化退火工艺及其在冷轧钢带65Mn上的应用。
实验结果表明,采用该工艺能够有效降低钢材的外部和内部应力,提高钢材的韧性和塑性,适合于汽车、航空、军工等高端制造领域的
应用。
该工艺具有广泛的应用前景和经济效益。