瓶盖模具设计与工艺
啤酒瓶盖起子模具设计说明书
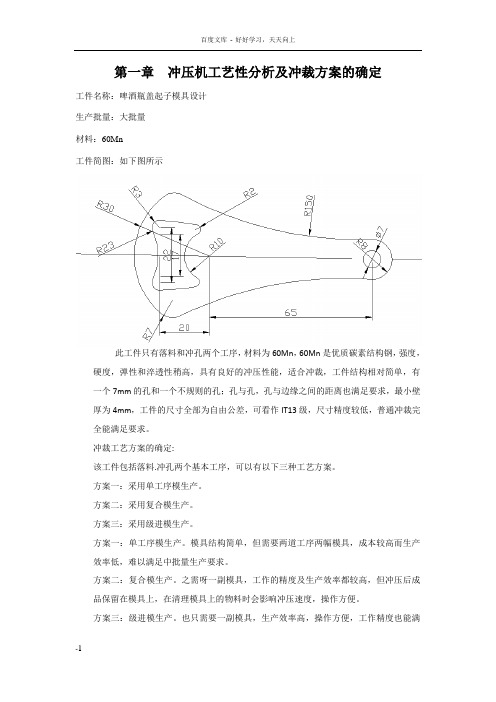
第一章冲压机工艺性分析及冲裁方案的确定工件名称:啤酒瓶盖起子模具设计生产批量:大批量材料:60Mn工件简图:如下图所示此工件只有落料和冲孔两个工序,材料为60Mn,60Mn是优质碳素结构钢,强度,硬度,弹性和淬透性稍高,具有良好的冲压性能,适合冲裁,工件结构相对简单,有一个7mm的孔和一个不规则的孔;孔与孔,孔与边缘之间的距离也满足要求,最小壁厚为4mm,工件的尺寸全部为自由公差,可看作IT13级,尺寸精度较低,普通冲裁完全能满足要求。
冲裁工艺方案的确定:该工件包括落料.冲孔两个基本工序,可以有以下三种工艺方案。
方案一:采用单工序模生产。
方案二:采用复合模生产。
方案三:采用级进模生产。
方案一:单工序模生产。
模具结构简单,但需要两道工序两幅模具,成本较高而生产效率低,难以满足中批量生产要求。
方案二:复合模生产。
之需呀一副模具,工作的精度及生产效率都较高,但冲压后成品保留在模具上,在清理模具上的物料时会影响冲压速度,操作方便。
方案三:级进模生产。
也只需要一副模具,生产效率高,操作方便,工作精度也能满足要求。
通过上述三种方案的分析比较,该件的冲压生产采用方案三为佳。
第二章主要设计计算排样方案的确定及计算设计级进模,首先要设计条料的排样图,啤酒瓶盖起子的形状具有一头大一头小的特点,直排样时材料利用率低,对于批量生产的零件,特别是零件材料较贵,为了节省材料,提高材料的利用率,应采用直对排样。
如图2-1所示的排样方法,设计成隔位冲压,可显著地减少废料,隔位冲压就是将第一遍冲压以后的条料水平方向旋转180,再冲第二遍,在第一次冲裁的间隙中冲裁出第二部分工件。
搭边值取2mm和,条料宽度为125mm和44mm,一个步距的材料利用率为52%。
查表2-1得最小搭边值:a=,a1=2mm条料宽度B:B=(D+2a1+nb1)第三章模具总体设计模具类型的选择模具类型分为三种分别是:单工序模,复合模和级进模。
单工序模又称简单冲裁模,是指在压力机一次行程内只完成一种冲裁工序的模具,如落料模,冲孔模,切断模切口模等。
小瓶盖塑料注塑模具设计说明书
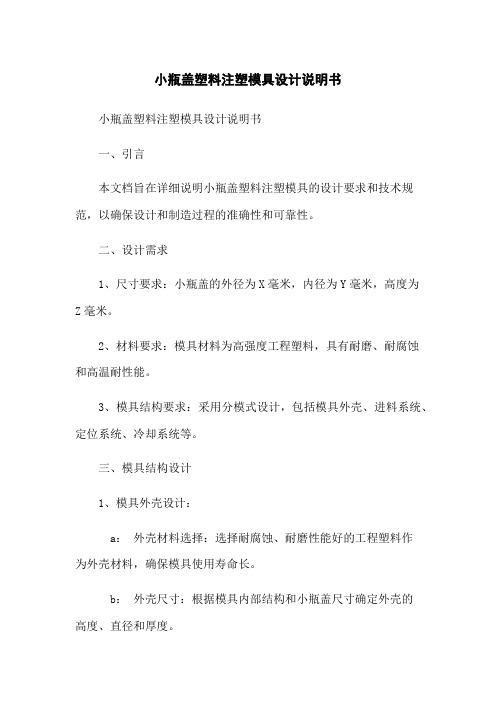
小瓶盖塑料注塑模具设计说明书小瓶盖塑料注塑模具设计说明书一、引言本文档旨在详细说明小瓶盖塑料注塑模具的设计要求和技术规范,以确保设计和制造过程的准确性和可靠性。
二、设计需求1、尺寸要求:小瓶盖的外径为X毫米,内径为Y毫米,高度为Z毫米。
2、材料要求:模具材料为高强度工程塑料,具有耐磨、耐腐蚀和高温耐性能。
3、模具结构要求:采用分模式设计,包括模具外壳、进料系统、定位系统、冷却系统等。
三、模具结构设计1、模具外壳设计:a:外壳材料选择:选择耐腐蚀、耐磨性能好的工程塑料作为外壳材料,确保模具使用寿命长。
b:外壳尺寸:根据模具内部结构和小瓶盖尺寸确定外壳的高度、直径和厚度。
c:模具外壳装配:确保外壳的装配牢固,能够承受注塑过程中的压力和冲击。
2、进料系统设计:a:进料口位置:进料口位于模具外壳上方,方便塑料材料的注入和冷却。
b:进料系统结构:进料系统包括进料管道、进料阀门和喷嘴等组成,确保塑料均匀流动。
3、定位系统设计:a:定位杆:在模具内部设置定位杆,以确保小瓶盖注塑时的位置准确性。
b:定位孔:在小瓶盖上开设定位孔,使得小瓶盖能够准确地套在定位杆上。
4、冷却系统设计:a:冷却通道:在模具内部设置冷却通道,以降低注塑过程中的温度,提高生产效率和产品质量。
b:冷却介质:选择高效的冷却介质,如冷水或冷气等,快速降低模具温度。
四、模具制造要求1、加工工艺:采用先进的数控加工设备和工艺,确保模具的加工精度和表面光洁度。
2、查漏测试:在模具制造过程中进行查漏测试,确保模具没有任何渗漏。
五、附录本文档涉及以下附件:1、小瓶盖的详细尺寸图纸。
2、模具的3D设计图纸。
六、法律名词及注释1、注塑模具:指用于塑料注塑成型的模具,可分为热流道模具和冷流道模具。
2、工程塑料:指具有高强度、耐磨、耐腐蚀和高温耐性能的塑料材料。
3、渗漏:指模具在注塑过程中出现塑料渗漏的现象,对产品质量产生负面影响。
矿泉水瓶盖注塑模具设计

3.冷料穴的设计:冷料 穴的作用是储藏流道前 锋冷料,以免影响塑件 质量。如右图
4.分流道浇口:应选用 点浇口,浇口不能过大 否则会在塑件上产生疤 痕,也不能过小,会使 材料发热变质,如右图
பைடு நூலகம்-6-
冷料穴
绿线处为所设的 隐藏式的浇口
红线处为阶 梯分型面
分流道浇口设计 蚌埠学院2013届本科毕业答辩
-12蚌埠学院2013届本科毕业答辩
总结
1.本次设计的注射模具一般用来生产塑件的外表面不 允许留下印痕的瓶盖,该设计的模具结构简单 。采 用齿条齿轮自动脱螺纹机构,该机构能实现产品的 自动化,但生产效率较低。
2.此次设计的遗憾是没有设计矿泉水瓶盖的防伪圈, 在以后的设计中会继续钻研。
-13蚌埠学院2013届本科毕业答辩
3.进行锁模力和开模行程的校核。
-4蚌埠学院2013届本科毕业答辩
3.2 浇注系统的设计
1.主流道的设计:应从 锥角,内壁粗糙度,喷 嘴球半径,主流道长度 几个方面去考虑,如右
2.分流道的设计:采用 半圆形截面的流道,并 且采用平衡式布置的方 式,如右
-5-
浇口套
分流道与型腔布置方式 蚌埠学院2013届本科毕业答辩
-2蚌埠学院2013届本科毕业答辩
2 塑件的二维及三维图
矿泉水瓶盖三维结构实体图 矿泉水瓶盖三维结构概念图
-3蚌埠学院2013届本科毕业答辩
3.1 塑件分析和材料设备的选择
1.此次设计我们首先应选择合适的材料,综合力学性能, 材料的价格,我们选择聚丙烯。
2.然后进行注塑设备的选择,根据计算出的塑件的体积得 到最大注射量,确定注塑机的型号,再根据注塑机的锁模 力确定型腔的数目,取型腔数目为二。
PE塑料瓶盖模具设计
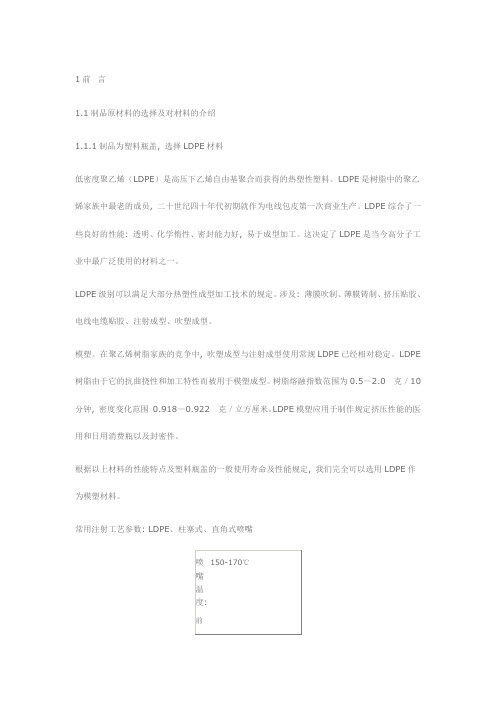
1前言1.1制品原材料的选择及对材料的介绍1.1.1制品为塑料瓶盖, 选择LDPE材料低密度聚乙烯(LDPE)是高压下乙烯自由基聚合而获得的热塑性塑料。
LDPE是树脂中的聚乙烯家族中最老的成员, 二十世纪四十年代初期就作为电线包皮第一次商业生产。
LDPE综合了一些良好的性能: 透明、化学惰性、密封能力好, 易于成型加工。
这决定了LDPE是当今高分子工业中最广泛使用的材料之一。
LDPE级别可以满足大部分热塑性成型加工技术的规定。
涉及: 薄膜吹制、薄膜铸制、挤压贴胶、电线电缆贴胶、注射成型、吹塑成型。
模塑。
在聚乙烯树脂家族的竞争中, 吹塑成型与注射成型使用常规LDPE已经相对稳定。
LDPE 树脂由于它的抗曲挠性和加工特性而被用于模塑成型。
树脂熔融指数范围为0.5—2.0克/10分钟, 密度变化范围0.918—0.922克/立方厘米。
LDPE模塑应用于制作规定挤压性能的医用和日用消费瓶以及封密件。
根据以上材料的性能特点及塑料瓶盖的一般使用寿命及性能规定, 我们完全可以选用LDPE作为模塑材料。
常用注射工艺参数: LDPE、柱塞式、直角式喷嘴模具温度: 30-45℃注射压力: 60-100MPa保压时间: 15-60S注射时间: 0-5S冷却时间: 15-60S成型时间: 40-140S1.1.2材料性能介绍(1)聚乙烯是结晶材料, 吸湿性小。
(2)流动性能极好, 溢边值为0.02mm左右, 流动性能对压力变化敏感。
(3)容易发生熔融破裂, 当与有机溶剂接触时可发生开裂。
(4)加热时间过长则发生分解烧伤。
(5)冷却速度较慢, 因此必须充足冷却, 宜设冷料穴, 在模具设计的时候应当设计冷却系统。
(6)聚乙烯材料的收缩率范围较大, 收缩值也大, 方向性明显, 易变形, 翘曲。
结晶度及模具冷却条件对收缩率影响大, 应控制模温, 保持冷却均匀, 稳定。
(7)宜用高压注射, 料温均匀, 填充速度应快, 保压应当充足。
瓶盖注塑模具设计
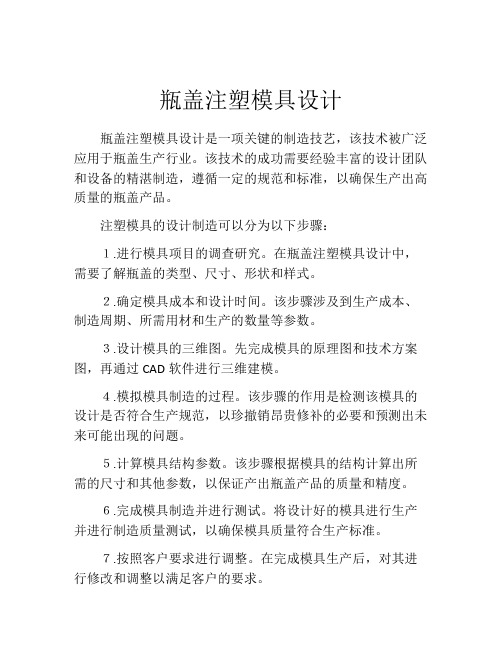
瓶盖注塑模具设计瓶盖注塑模具设计是一项关键的制造技艺,该技术被广泛应用于瓶盖生产行业。
该技术的成功需要经验丰富的设计团队和设备的精湛制造,遵循一定的规范和标准,以确保生产出高质量的瓶盖产品。
注塑模具的设计制造可以分为以下步骤:1.进行模具项目的调查研究。
在瓶盖注塑模具设计中,需要了解瓶盖的类型、尺寸、形状和样式。
2.确定模具成本和设计时间。
该步骤涉及到生产成本、制造周期、所需用材和生产的数量等参数。
3.设计模具的三维图。
先完成模具的原理图和技术方案图,再通过CAD软件进行三维建模。
4.模拟模具制造的过程。
该步骤的作用是检测该模具的设计是否符合生产规范,以珍撤销昂贵修补的必要和预测出未来可能出现的问题。
5.计算模具结构参数。
该步骤根据模具的结构计算出所需的尺寸和其他参数,以保证产出瓶盖产品的质量和精度。
6.完成模具制造并进行测试。
将设计好的模具进行生产并进行制造质量测试,以确保模具质量符合生产标准。
7.按照客户要求进行调整。
在完成模具生产后,对其进行修改和调整以满足客户的要求。
瓶盖注塑模具设计的需要考虑各种因素。
例如模架、模具部件、模具材料、尺寸和胶管尺寸等。
在设计模具时,必须保证有适当的空间以便于后期修复和调整。
模具的结构和制造质量是直接影响到瓶盖生产工艺和产品精度的因素之一。
使用高质量的钢材和其他金属材料使得模具的抗压、抗腐蚀和氧化能力更强。
在制造模具时还需要保证其精度和质量在高温和高压条件下仍然能够稳定性工作,保证生产稳定和高效率。
总之,瓶盖注塑模具设计是一项非常重要的制造工艺,需要高度专业的技术知识和经验。
通过合理设计和细致制造,可以生产出高精度、高质量的瓶盖产品。
输液瓶橡胶盖注射模具设计

输液瓶橡胶盖注射模具设计输液瓶橡胶盖注射模具设计
注射模具是制造塑料制品的重要工具之一,常用于生产如输液瓶等医用器械。
输液瓶橡胶盖注射模具是制造输液瓶橡胶盖的专用模具,本文将结合实际案例,详细介绍输液瓶橡胶盖注射模具的设计要点。
一、产品分析
输液瓶橡胶盖是常用于输液瓶的塑料配件,主要用于密封输液瓶口部,防止外部污染。
输液瓶橡胶盖一般由橡胶材料制成,口径大小和高度不尽相同,通常采用注射成型工艺制造。
二、模具设计
1. 模具结构
输液瓶橡胶盖注射模具通常采用两板式结构设计,由上模板、下模板、导柱、导套、滑块、顶出机构等组成。
上下模板及导柱导套需精加工,确保模件加工精度和表面质量,减少模具使用过程中的磨损。
2. 模具材料
模具材料一般采用优质钢材制造,其中上模板和下模板需优先选用优质钢材,经过调质、淬火等热处理工艺后,具备高强度和良好的耐磨性能,确保模具使用寿命和稳定性。
3. 模具结构布局
为了提高模具运行效率和减少模具更换时间,应考虑合理的模具结构布局,如:将输液瓶橡胶盖集中在模具中心,尽量减少模具中小零部件的使用,同时顶出机构、导柱等重要位置的阻拦避免均匀累积,以利于后续模具维护和修理工作的进行。
三、结论
输液瓶橡胶盖注射模具是一种极为实用的注射模具,其设计建立在产品、工艺、使用寿命等多个方面考虑的基础之上。
设计合理的输液瓶橡胶盖注射模具可以显著提高生产效率和产品质量,降低生产成本,具有广泛的应用前景。
塑料瓶盖的注塑模设计

塑料瓶盖的注塑模设计
本文将介绍塑料瓶盖的注塑模设计,主要包括模具结构设计、材料选择、加工工艺和质量控制等方面。
一、模具结构设计
塑料瓶盖的注塑模有两部分组成:注塑机侧模和移动模。
侧模由模板、模座、导向机构、射嘴和喷嘴组成。
移动模包含模板、模座、导向机构和射针等。
在设计时需要考虑的是塑料瓶盖的结构,包括拉丝环的位置、塞子的形状和直径等。
同时也需要考虑注塑机的尺寸,确保模具与注塑机的匹配。
二、材料选择
注塑模的材料需要具备高硬度、高耐磨、高耐腐蚀、高耐热和高精度等特性。
常用的材料有工具钢、合金钢、铝合金等。
不同的材料适用于不同的注塑产品,需要根据具体情况选择合适的材料。
三、加工工艺
在加工注塑模时,需要严格按照设计图纸进行制造。
首先进行铣床加工,对模板进行精度加工;接下来进行电脉冲加工,对导向孔、定位孔等进行精度加工;最后进行磨床加工,对加工表面进行精度加工。
在加工中需要严格控制尺寸,确保模具制造出来的瓶盖符合要求。
四、质量控制
对于注塑模的质量控制需要有严格的控制措施,包括在制造过程中对材料进行材质检测,进行制造工艺检测,对模具的加工、验收和防腐处理等工序进行检查。
在使用过程中需要对模具进行定期维护和保养,确保模具的使用寿命和稳定性。
同时也需要进行模具的性能测试和使用情况分析,以便提高模具使用效率和生产效益。
综上所述,塑料瓶盖的注塑模设计需要注意模具结构设计、材料选择、加工工艺和质量控制等方面,根据具体情况选择合适的制造方案,确保生产的塑料瓶盖达到设计目标。
饮料瓶瓶盖注射模具设计

饮料瓶瓶盖注射模具设计饮料瓶瓶盖注射模设计一塑料的工艺性分析1.塑件的原材料分析塑料的品种:PE(聚乙烯)。
成型特征:结晶型塑料,吸湿性小,流淌性较好,溢边值为0.02mm左右,流淌性对压力变化敏感,加热时间长则易发生分解,冷却速度快,务必充分冷却。
设计模具时要冷却料穴与冷却分流。
收缩率大,方向明显,易变形,扭曲结晶度及模具冷却条件对收缩率影响大,应操纵模温。
易用变压注射,料温要均匀,否则会增加内应力,使收缩不均匀与方向性明显。
2.塑料的尺寸精度分析影响塑料制品的尺寸精度的要紧因素是材料的收缩与模具的制造误差。
查教材上表2-11得此材料的收缩率为1.5%~2%。
塑料制品的公差也可通过教材上表2-12查得,塑料的精度等级选择7级精度。
3.塑件的表面质量分析塑件外表面要求粗糙度较低,表面光滑,内表面要求低点。
4.塑件结构的工艺性分析结构简图如图所示瓶盖主体外侧均匀分布120个增大摩擦力的防滑筋,瓶盖顶部有商标名称ZSM的字样。
瓶盖下部有一防伪圈与瓶盖主体通过8个直径为1mm高1mm的小圆柱相连,防伪圈内侧有8个均匀分布长为3mm直径为1.5mm的半圆形凸台。
瓶盖内部有螺呀为半圆形的螺纹及高为4mm截面直径为1mm的防伪圈与瓶子内径严密配合,而高为1mm,截面直径1mm的防伪圈与瓶子外径严密配合防止漏水。
综上所述可使用注射成型加工。
二确定成型设备选择与模塑工艺规程编制1.计算塑件体积与质量cmV=3.05 3M=2.9g选择注射机为SZ-30理论注射容积为373cm ,实际注射质量为33g ,螺杆直径为26 mm ,塑化能力3.6g/s ,注射压力170MPa 螺杆转速10~160r/min,螺杆行程70 mm ,锁模力为320KN ,拉杆有效间距300300⨯2mm ,模板行程110 mm ,模具最小厚度80 mm ,模具最大厚度110 mm ,最大开距220 mm ,模扳尺寸400400 ⨯2mm ,顶出行程50 mm ,喷嘴半径为12 mm ,高为2 mm 。
瓶盖注塑模具设计论文
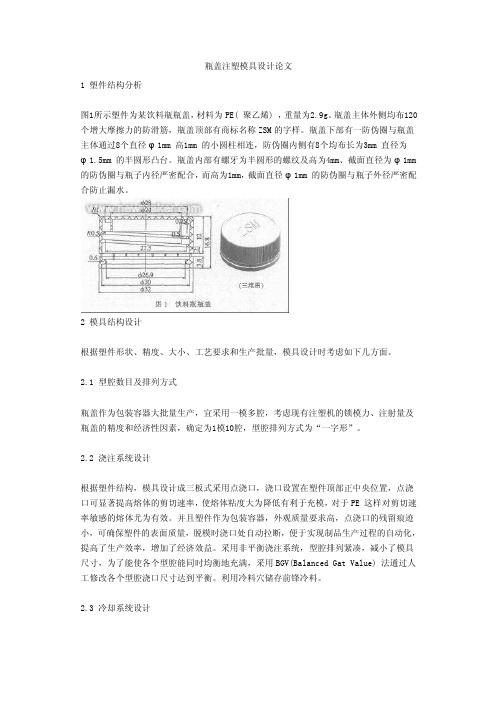
瓶盖注塑模具设计论文1 塑件结构分析图1所示塑件为某饮料瓶瓶盖,材料为PE( 聚乙烯) ,重量为2.9g。
瓶盖主体外侧均布120个增大摩擦力的防滑筋,瓶盖顶部有商标名称ZSM的字样。
瓶盖下部有一防伪圈与瓶盖主体通过8个直径φ1mm 高1mm 的小圆柱相连,防伪圈内侧有8个均布长为3mm 直径为φ1.5mm 的半圆形凸台。
瓶盖内部有螺牙为半圆形的螺纹及高为4mm、截面直径为φ1mm 的防伪圈与瓶子内径严密配合,而高为1mm,截面直径φ1mm 的防伪圈与瓶子外径严密配合防止漏水。
2 模具结构设计根据塑件形状、精度、大小、工艺要求和生产批量,模具设计时考虑如下几方面。
2.1 型腔数目及排列方式瓶盖作为包装容器大批量生产,宜采用一模多腔,考虑现有注塑机的锁模力、注射量及瓶盖的精度和经济性因素,确定为1模10腔,型腔排列方式为“一字形”。
2.2 浇注系统设计根据塑件结构,模具设计成三板式采用点浇口,浇口设置在塑件顶部正中央位置,点浇口可显著提高熔体的剪切速率,使熔体粘度大为降低有利于充模,对于PE 这样对剪切速率敏感的熔体尤为有效。
并且塑件作为包装容器,外观质量要求高,点浇口的残留痕迹小,可确保塑件的表面质量,脱模时浇口处自动拉断,便于实现制品生产过程的自动化,提高了生产效率,增加了经济效益。
采用非平衡浇注系统,型腔排列紧凑,减小了模具尺寸,为了能使各个型腔能同时均衡地充满,采用BGV(Balanced Gat Value) 法通过人工修改各个型腔浇口尺寸达到平衡。
利用冷料穴储存前锋冷料。
2.3 冷却系统设计模温调节系统直接影响到制品的质量和生产效率。
为提高型腔的冷却效率,采用如图2 所示的冷却回路,一条回路的进口位于另一条回路的出口附近;根据塑件形状及模具结构限制,定模冷却水道直径为φ12mm( 见图2) ,与模外软管连接形成循环冷却。
动模型芯直径较细,采用如图3 所示的钢管冷却方式,在型芯中心压入热导性能好的软铜芯棒,并将芯棒的一端伸到冷却水孔中冷却。
瓶盖塑料模具设计要点
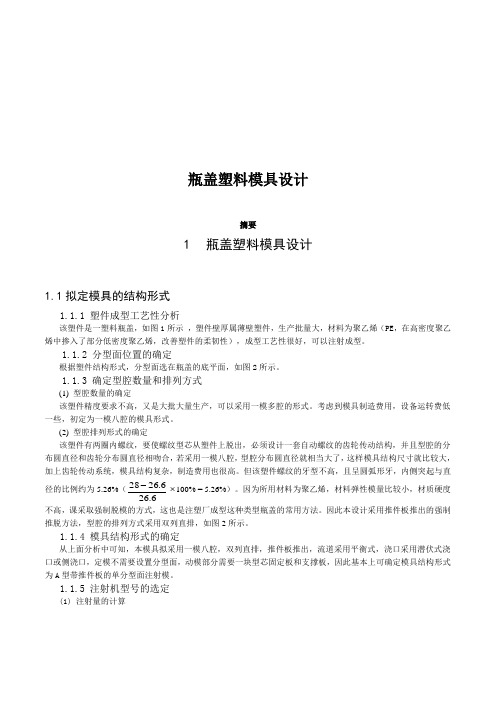
瓶盖塑料模具设计摘要1 瓶盖塑料模具设计1.1拟定模具的结构形式1.1.1 塑件成型工艺性分析该塑件是一塑料瓶盖,如图1所示,塑件壁厚属薄壁塑件,生产批量大,材料为聚乙烯(PE,在高密度聚乙烯中掺入了部分低密度聚乙烯,改善塑件的柔韧性),成型工艺性很好,可以注射成型。
1.1.2 分型面位置的确定根据塑件结构形式,分型面选在瓶盖的底平面,如图2所示。
1.1.3 确定型腔数量和排列方式(1) 型腔数量的确定该塑件精度要求不高,又是大批大量生产,可以采用一模多腔的形式。
考虑到模具制造费用,设备运转费低一些,初定为一模八腔的模具形式。
(2) 型腔排列形式的确定该塑件有两圈内螺纹,要使螺纹型芯从塑件上脱出,必须设计一套自动螺纹的齿轮传动结构,并且型腔的分布圆直径和齿轮分布圆直径相吻合,若采用一模八腔,型腔分布圆直径就相当大了,这样模具结构尺寸就比较大,加上齿轮传动系统,模具结构复杂,制造费用也很高。
但该塑件螺纹的牙型不高,且呈圆弧形牙,内侧突起与直径的比例约为5.26%(6.266.2628-⨯100% = 5.26%)。
因为所用材料为聚乙烯,材料弹性模量比较小,材质硬度不高,课采取强制脱模的方式,这也是注塑厂成型这种类型瓶盖的常用方法。
因此本设计采用推件板推出的强制推脱方法,型腔的排列方式采用双列直排,如图2所示。
1.1.4 模具结构形式的确定从上面分析中可知,本模具拟采用一模八腔,双列直排,推件板推出,流道采用平衡式,浇口采用潜伏式浇口或侧浇口,定模不需要设置分型面,动模部分需要一块型芯固定板和支撑板,因此基本上可确定模具结构形式为A型带推件板的单分型面注射模。
1.1.5 注射机型号的选定(1) 注射量的计算通过计算或Pro/E建模分析,塑件质量m1为2.8g,塑件体积V1=ρ1m=91.08.2 = 3.077cm3,流道凝料的质量m2还是个未知数,课按塑件质量的0.6倍来估算。
从上述分析中确定为一模八腔,所注射量为M = 1.6nm1= 1.6 ⨯8⨯2.8 = 35.84g 。
塑料瓶盖模具设计
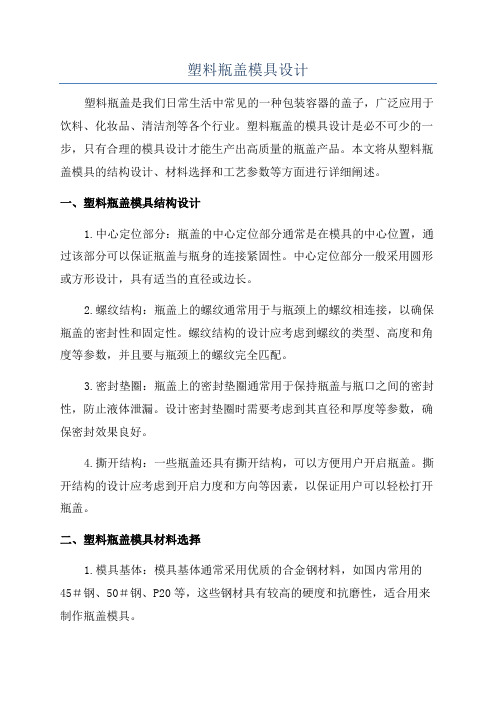
塑料瓶盖模具设计塑料瓶盖是我们日常生活中常见的一种包装容器的盖子,广泛应用于饮料、化妆品、清洁剂等各个行业。
塑料瓶盖的模具设计是必不可少的一步,只有合理的模具设计才能生产出高质量的瓶盖产品。
本文将从塑料瓶盖模具的结构设计、材料选择和工艺参数等方面进行详细阐述。
一、塑料瓶盖模具结构设计1.中心定位部分:瓶盖的中心定位部分通常是在模具的中心位置,通过该部分可以保证瓶盖与瓶身的连接紧固性。
中心定位部分一般采用圆形或方形设计,具有适当的直径或边长。
2.螺纹结构:瓶盖上的螺纹通常用于与瓶颈上的螺纹相连接,以确保瓶盖的密封性和固定性。
螺纹结构的设计应考虑到螺纹的类型、高度和角度等参数,并且要与瓶颈上的螺纹完全匹配。
3.密封垫圈:瓶盖上的密封垫圈通常用于保持瓶盖与瓶口之间的密封性,防止液体泄漏。
设计密封垫圈时需要考虑到其直径和厚度等参数,确保密封效果良好。
4.撕开结构:一些瓶盖还具有撕开结构,可以方便用户开启瓶盖。
撕开结构的设计应考虑到开启力度和方向等因素,以保证用户可以轻松打开瓶盖。
二、塑料瓶盖模具材料选择1.模具基体:模具基体通常采用优质的合金钢材料,如国内常用的45#钢、50#钢、P20等,这些钢材具有较高的硬度和抗磨性,适合用来制作瓶盖模具。
2.螺纹部分:瓶盖上的螺纹部分需要使用耐磨耐腐蚀的材料,如不锈钢等,以提高螺纹的使用寿命。
3.密封垫圈:密封垫圈通常采用橡胶材料,如硅胶、丁腈橡胶等,这些材料具有较好的耐热性和密封性能。
三、塑料瓶盖模具工艺参数1.注塑温度:注塑温度是指瓶盖模具中塑料熔融的温度,通常采用热流道系统进行注塑。
注塑温度需要根据所用塑料的熔点来确定,一般在塑料的熔点以上10至20°C左右。
2.注塑压力:注塑压力是指注塑机在注塑过程中对塑料施加的压力,用于充填模具腔体。
注塑压力需要根据塑料的流动性和模具结构来确定,一般为塑料的2至3倍。
3.注塑速度:注塑速度是指注塑机在注塑过程中对塑料的进给速度,用于控制瓶盖的充填时间。
瓶盖注射模设计及若干工艺问题探讨
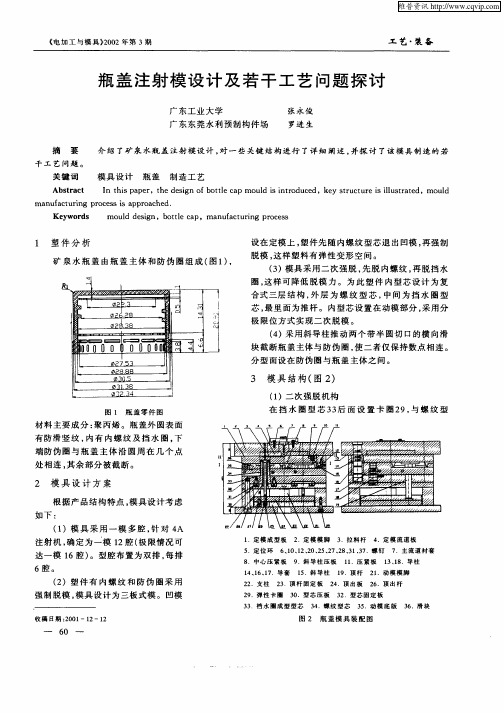
《 电加工与模具}02 20 年第 3 期
5 若 干 工 艺 问题 探 讨
( )滑块 半 圆切 口加 工 。滑 块 用 于 切 断瓶 盖 主 1
螺纹 型芯 3 4从 塑 件 抽 出时 , 挡水 圈 型芯 3 3保 持 不
动 。螺纹 型 芯 3 4继 续 运 动 碰 到 卡 圈 2 将 挡 水 圈 9, 型芯 3 3从 塑件 中抽 出 , 现 二次脱 模 。 实 ( )废 料 去 除 2
体 与 防伪 圈 , 口为半 圆 , 个 半 圆构 成 一 个 整 圆 。 切 两 该零 件 加工 一般 采 用 线 切 割 加 工 , 切 不 可采 用 将 但 整 圆剖 分 为二 的 方 式 。 因 剖 分 时 对 中有 误 差 , 时 同 钼 丝直 径 和放 电 间隙也 会 破 坏 圆 的完整 性 。正 确 的 方 法是 通 过两 个半 圆分别 编 程 、 加工 , 证 两个 滑块 保
对 合后 成 为一个 完 整 的 圆 , 图 4 见 。
4 模 具 工 作 过 程
开模 后 , 模 后 移 , 先 在 II 分 型 , 件 随 动 首 .处 塑 型芯从 凹模脱 出 , 块 3 滑 6在 斜导 柱 和弹 簧 的作用 下
芯 , 里 面为 推 杆 。 内型芯 设 置在 动模 部 分 , 用 分 最 采 极 限位方 式 实现 二次 脱模 。
( )采 用斜 导柱 推 动 两个 带 半 圆切 口的横 向滑 4 块 截 断瓶 盖 主体 与 防伪 圈 , 二者 仅保 持数 点相 连 。 使 分型 面设 在 防伪 圈与 瓶 盖 主体 之 间 。
维普资讯
《 电加工与模具 ̄o2年第 3 2o 期
工 艺 ・ 备 装
瓶 盖 注 射 模 设 计 及 若 干 工 艺 问题 探 讨
瓶盖的塑料模具设计
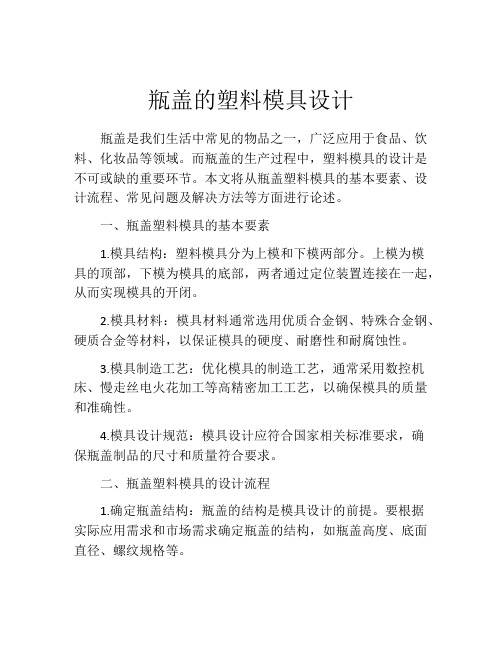
瓶盖的塑料模具设计瓶盖是我们生活中常见的物品之一,广泛应用于食品、饮料、化妆品等领域。
而瓶盖的生产过程中,塑料模具的设计是不可或缺的重要环节。
本文将从瓶盖塑料模具的基本要素、设计流程、常见问题及解决方法等方面进行论述。
一、瓶盖塑料模具的基本要素1.模具结构:塑料模具分为上模和下模两部分。
上模为模具的顶部,下模为模具的底部,两者通过定位装置连接在一起,从而实现模具的开闭。
2.模具材料:模具材料通常选用优质合金钢、特殊合金钢、硬质合金等材料,以保证模具的硬度、耐磨性和耐腐蚀性。
3.模具制造工艺:优化模具的制造工艺,通常采用数控机床、慢走丝电火花加工等高精密加工工艺,以确保模具的质量和准确性。
4.模具设计规范:模具设计应符合国家相关标准要求,确保瓶盖制品的尺寸和质量符合要求。
二、瓶盖塑料模具的设计流程1.确定瓶盖结构:瓶盖的结构是模具设计的前提。
要根据实际应用需求和市场需求确定瓶盖的结构,如瓶盖高度、底面直径、螺纹规格等。
2.绘制模具图纸:根据瓶盖结构要求,先进行模具的初步绘制,标明模具的上模和下模,然后针对各个零件进行分别绘制。
3.确定模具参数:根据实际需要,确定模具的参数,如上模重量、下模重量、模具尺寸等,以确保模具能够稳定运作。
4.进行模具铸造:完成模具设计后,选用合适的材料进行铸造,并将铸造完成的模具进行淬火处理,以确保模具的硬度和耐磨性。
5.进行加工处理:在模具铸造完成并淬火后,需要进行后期加工处理,将模具进行精细加工,以保证模具的精度和准确性。
三、瓶盖塑料模具的常见问题及解决方法1.模具加工不准确:模具加工的准确性对于瓶盖塑料模具的品质至关重要。
如果模具加工不准确,就会导致瓶盖的尺寸不准确,影响到瓶盖的使用效果。
解决方法可以采用高精度加工设备,如数控机床、慢走丝电火花加工等。
2.模具表面粗糙:模具表面粗糙会使得瓶盖的表面不光滑,影响到瓶盖的质量和美观度。
解决方法可以采用高精度磨床进行表面处理。
瓶盖注塑模具设计
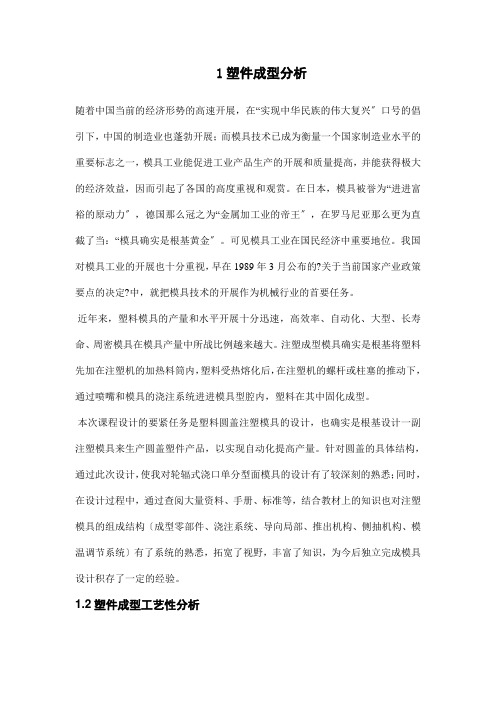
1塑件成型分析随着中国当前的经济形势的高速开展,在“实现中华民族的伟大复兴〞口号的倡引下,中国的制造业也蓬勃开展;而模具技术已成为衡量一个国家制造业水平的重要标志之一,模具工业能促进工业产品生产的开展和质量提高,并能获得极大的经济效益,因而引起了各国的高度重视和观赏。
在日本,模具被誉为“进进富裕的原动力〞,德国那么冠之为“金属加工业的帝王〞,在罗马尼亚那么更为直截了当:“模具确实是根基黄金〞。
可见模具工业在国民经济中重要地位。
我国对模具工业的开展也十分重视,早在1989年3月公布的?关于当前国家产业政策要点的决定?中,就把模具技术的开展作为机械行业的首要任务。
近年来,塑料模具的产量和水平开展十分迅速,高效率、自动化、大型、长寿命、周密模具在模具产量中所战比例越来越大。
注塑成型模具确实是根基将塑料先加在注塑机的加热料筒内,塑料受热熔化后,在注塑机的螺杆或柱塞的推动下,通过喷嘴和模具的浇注系统进进模具型腔内,塑料在其中固化成型。
本次课程设计的要紧任务是塑料圆盖注塑模具的设计,也确实是根基设计一副注塑模具来生产圆盖塑件产品,以实现自动化提高产量。
针对圆盖的具体结构,通过此次设计,使我对轮辐式浇口单分型面模具的设计有了较深刻的熟悉;同时,在设计过程中,通过查阅大量资料、手册、标准等,结合教材上的知识也对注塑模具的组成结构〔成型零部件、浇注系统、导向局部、推出机构、侧抽机构、模温调节系统〕有了系统的熟悉,拓宽了视野,丰富了知识,为今后独立完成模具设计积存了一定的经验。
1.2塑件成型工艺性分析塑件分析塑件模型如图1-1所示〔为计算需要仅标注几个重要尺寸本图见型中图〕图1-1塑料盖子塑件的结构及成型工艺性分析结构分析:该塑件为瓶子罐盖子,其结构应尽可能的简单且维度和钢管应满足需要,塑件的顶部没有两个对称的孔,用于安装提手,内部有简单的螺纹,用于和罐子连接紧密。
线性工艺性分析:1.精度等级:采纳一班精度4级2.脱模歪度:改塑件件壁厚1.5mm,其脱模歪度查表得到塑件材料为聚丙烯pp,其型腔脱横歪度为:25~45.其型蕊脱横歪度为:20~45.由于该塑件没有狭小部位,因此脱横歪度取1。
啤酒瓶起子模具设计
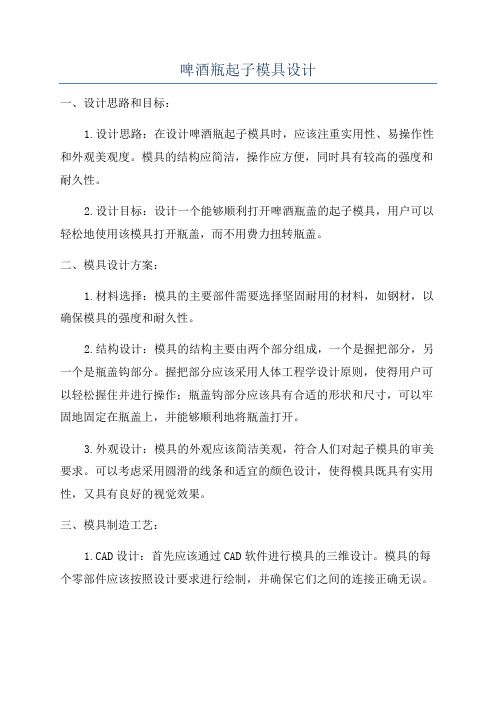
啤酒瓶起子模具设计一、设计思路和目标:1.设计思路:在设计啤酒瓶起子模具时,应该注重实用性、易操作性和外观美观度。
模具的结构应简洁,操作应方便,同时具有较高的强度和耐久性。
2.设计目标:设计一个能够顺利打开啤酒瓶盖的起子模具,用户可以轻松地使用该模具打开瓶盖,而不用费力扭转瓶盖。
二、模具设计方案:1.材料选择:模具的主要部件需要选择坚固耐用的材料,如钢材,以确保模具的强度和耐久性。
2.结构设计:模具的结构主要由两个部分组成,一个是握把部分,另一个是瓶盖钩部分。
握把部分应该采用人体工程学设计原则,使得用户可以轻松握住并进行操作;瓶盖钩部分应该具有合适的形状和尺寸,可以牢固地固定在瓶盖上,并能够顺利地将瓶盖打开。
3.外观设计:模具的外观应该简洁美观,符合人们对起子模具的审美要求。
可以考虑采用圆滑的线条和适宜的颜色设计,使得模具既具有实用性,又具有良好的视觉效果。
三、模具制造工艺:1.CAD设计:首先应该通过CAD软件进行模具的三维设计。
模具的每个零部件应该按照设计要求进行绘制,并确保它们之间的连接正确无误。
2.模具制造:根据CAD设计图纸,使用数控机床进行模具的加工制造。
首先将选好的钢材切割成所需的形状和尺寸,然后通过铣削、车削等工艺进行加工。
3.表面处理:为了增强模具的耐腐蚀性和美观度,可以对模具表面进行处理。
可以选择镀铬、喷涂或激光处理等方法,使得模具表面具有一定的硬度和光泽,并能够有效防止模具生锈。
四、模具性能测试:1.强度测试:使用专业的强度测试设备对模具进行力学性能测试,检测其承受外力时的强度和稳定性,确保模具在使用过程中不会发生失效。
2.操作测试:请一些经验丰富的用户进行模具的操作测试,并听取他们的反馈意见。
根据用户的意见进行改进,并不断完善模具的设计。
结语:啤酒瓶起子模具是一种便利工具,通过科学合理的设计和制造,可以更好地满足用户的需求。
该模具设计需要考虑实用性、易操作性、人体工程学和制造可行性等因素。
酒瓶盖注射模具设计讲解

需的注塑成型压力较高,因此塑件对型芯的包紧力较大,故塑件应采用较大的脱
模斜度。另外熔体黏度较高,使ABS制品易产生熔接痕,所以模具设计时应尽
量减少浇注系统对料流的阻力。ABS易吸水,成型加工前应进行干燥处理。在正
常的成型条件下,ABS制品的尺寸稳定性较好。
具有比聚苯乙烯更好的使用和工艺性能。ABS是一种常用的具有良好的综合力学
性能的工程塑料。ABS塑料为无定型塑料,一般不透明。ABS无毒、无味,成形
塑件的表面有较好的光泽。ABS具有良好的机械强度,特别是抗冲击强度高。
ABS还具有一定的耐磨性、耐寒性、耐油性、耐水性、化学稳定性和电性能。
ABS的缺点是耐热性不高,并且耐气候性较差,在紫外线作用下易变硬发脆。
产数量:年产量200万件
塑件颜色:米黄色
查文献得:
塑件材料物理性能:
Ra<1.6,无缺陷,内表面无特殊要求,所有过渡处有0.2圆角。
1酒瓶内盖塑件的工艺分析
1.1塑件成形工艺分析
如图1-1为塑料酒瓶内盖的二维工程图及实体图,单位mm。
图1-1塑件图
产品名称:酒瓶内盖
产品材料:丙烯ABS
塑件材料特性:ABS塑料(丙烯腈—丁二烯—苯乙烯共聚物)是在聚苯乙烯分子
中导入了丙烯腈、丁二烯等异种单体后成为的改性共聚物,也可称改性聚苯乙烯,
姓名:余至彬专业:机械设计与制造班级:设计一班学号:
201236030152
设计题目:酒瓶内盖塑料模
塑料件简图:
塑料件主要技术要求:
1.材料:ABS,米黄色
2.年产量:200万件
3.未注公差:30,
44按MT2标注,其余按MT5计算,并且尺寸按入体原则
塑料瓶盖的注塑模设计

塑料瓶盖的注塑模设计塑料瓶盖是我们日常生活中必不可少的一种物品,它们的外形各异,但其中最常见的就是圆形和方形的瓶盖。
而这些瓶盖的生产离不开注塑模设计。
注塑模是生产塑料制品的关键工具之一。
注塑模的设计包括模具结构设计和注意事项。
在瓶盖注塑模设计时需要考虑的问题种类多样,因此,本文将从以下几个方面来探讨塑料瓶盖的注塑模设计。
一、模具结构设计在瓶盖注塑模的设计中,模具结构设计是最基本也是最重要的。
模具结构设计主要包括模芯、模架、顶针、定位销、导柱、衬套等部分。
模芯是注塑模的核心部分,其作用是决定瓶盖的内部结构,一般需要根据瓶盖的形状和大小来确定模芯的形状和大小,以便给瓶盖内部形状切削加工留出空间,避免瓶盖变形。
模架是模具的骨架,它负责承受注塑时的压力和冲击。
在瓶盖注塑模中,模架需要设计得强度高,保证工作稳定,避免出现翘曲或弯曲等现象。
顶针是模具用来卸料的一种机构,它的作用是为了让瓶盖浇注的材料能够从模具中顺利脱离,为注塑后的下一步操作提供便利。
定位销和导柱都是模具的定位装置,用来固定和定位模具的移动位置,避免在注塑过程中移动,影响产品的质量。
衬套是模具的配件之一,它主要用于保护模具面和表面防止被瓶盖的材料腐蚀,同时可以提高模具的使用寿命。
二、注意事项在塑料瓶盖注塑模的设计中,还要特别注意一些问题。
首先,需要确定注塑机的型号和规格等参数,以确定瓶盖注塑的资料。
其次,需要确定瓶盖的设计参数,例如瓶盖的形状、尺寸、厚度等,以确定瓶盖注塑模的结构设计。
此外,还需要注意瓶盖注塑模的加工精度和加工工艺,不仅包括模具结构的加工,还包括与之配合的注塑机的加工工艺。
这些都是与塑料瓶盖的质量息息相关的。
三、生产过程瓶盖的注塑模设计完成后,就需要进行生产过程。
在生产过程中,还需要注意以下几点。
首先,需要掌握注塑机的使用方法,如何使用注塑机进行瓶盖注塑。
其次,需要合理调整瓶盖注塑模的参数,以适应瓶盖材料的特点。
最后,注塑过程中,需要及时对注塑机和注塑模进行保养与维护,避免出现故障。
- 1、下载文档前请自行甄别文档内容的完整性,平台不提供额外的编辑、内容补充、找答案等附加服务。
- 2、"仅部分预览"的文档,不可在线预览部分如存在完整性等问题,可反馈申请退款(可完整预览的文档不适用该条件!)。
- 3、如文档侵犯您的权益,请联系客服反馈,我们会尽快为您处理(人工客服工作时间:9:00-18:30)。
瓶盖模具设计与工艺
缺料一般在塑料加工过程中,由于模具的型腔填充不满,从而造成零件的外形与设计不符的现象叫缺料。
下面是小编整理的关于瓶盖模具设计与工艺的相关介绍,大家一起来看看吧。
缺料
(1)设备方法
导致塑胶件缺料的工艺因素很多,其中最重要的原因是填充压力小,注射时间短和模具温度低三个因素造成的。
填充压力小时,注塑机在注塑成型时,会导致型腔的压力不足,塑胶很难填充满整个型腔,从而导致零件缺料;注射时间短也会导致塑胶未完全充满型腔,导致零件缺料;模具温度低,会加速塑胶凝固,液体流动性减小,也会导致塑胶不能充满整个型腔,造成缺料现象。
(2)设备原因
导致塑胶件缺料的设备原因主要是射嘴部分,一般为射嘴堵塞,一般方法是清理射嘴可以解决;射嘴漏胶也会导致缺料,此类故障一般需更换射嘴。
(3)模具原因
一般由于模具内部排气不通畅造成的,由于型腔内积累的空气无法排出,会造成塑胶填充量不足,从而导致缺料,采取的措施是降低塑胶的充填速度或在模具上增加相应的排气孔。
由于热流道堵塞或流动不平衡造成塑胶熔料流动不顺畅,造成零件的缺料,一般采取的措施是提高缺料产品相对应的热浇流道温度,并使用精致且干净的原料。
飞边
一般发生在模具的分型位置上,如:模具的分型面、滑块的配合。