磷化工艺与技术
钛合金的磷化处理工艺

钛合金的磷化处理工艺钛合金的磷化处理工艺是一种常用的表面处理方法,旨在改善钛合金的耐蚀性、耐磨性和附着力等性能。
在磷化处理中,钛合金表面与磷酸盐溶液发生化学反应,生成磷化层。
本文将从磷化处理的原理、工艺流程和优缺点等方面对钛合金的磷化处理工艺进行详细介绍。
一、磷化处理的原理磷化处理是利用磷酸盐与金属表面反应生成磷化物的化学反应。
在钛合金表面磷化处理时,钛合金表面会与磷酸盐发生反应,生成一层致密的磷化层。
这层磷化层在钛合金表面起到保护层的作用,能够提高钛合金的耐蚀性和耐磨性,增强其表面的附着力。
二、磷化处理的工艺流程1. 表面清洁:首先,需要将钛合金表面的油污、氧化物等杂质清除干净,通常使用酸洗等方法进行清洗。
2. 磷化处理剂配制:根据具体的磷化处理要求,将磷酸盐和其他添加剂按一定的比例和溶液配制成磷化处理剂。
3. 磷化处理:将清洗干净的钛合金样品放入磷化处理液中,控制温度和处理时间,使钛合金表面与磷酸盐发生反应生成一层磷化层。
4. 清洗:磷化处理后,需要将磷化剂残留物清洗掉,通常采用水洗和酸洗的方式进行清洗。
5. 中和处理:通过使用稀释剂和缓冲剂对钛合金进行中和处理,将磷化处理剩余的酸性溶液中的酸解除,以免继续腐蚀。
三、磷化处理的优缺点1. 优点:(1) 提高耐蚀性:经过磷化处理后的钛合金表面形成一层致密的磷化层,可以起到一定的耐蚀作用,延长钛合金的使用寿命。
(2) 增强耐磨性:磷化处理能够改善钛合金表面的硬度和耐磨性,使其在摩擦、磨损等环境中具有更好的性能。
(3) 改善附着力:磷化层与钛合金表面有着较好的粘结力,可以提高涂层的附着力,增强防腐涂层的耐久性。
(4) 工艺简单:磷化处理过程相对简单,操作方便,成本较低。
2. 缺点:(1) 耗能较大:磷化处理需要使用磷酸盐等化学药剂,废弃液处理和回收成本较高。
(2) 环境污染:磷化处理在废水处理和废酸危害方面存在一定的环境污染问题,对周围环境造成一定的影响。
(完整版)磷化实验方法

磷化实验方法1.磷化工艺流程脱脂—水洗—除锈—水洗—表调—磷化—水洗—干燥(1)脱脂除油脂的目的在于清除掉试样表面的油脂、油污、脏物,使磷化液与金属表面有良好的接触,从而得到质量良好的磷化膜。
目前低碱液除油逐渐被广泛应用,它是一种有效的除油方法,而且不损伤试样表面,它能把试样表面上的杂质彻底清洗干净,使磷化液与金属表面有良好的接触,充分润湿金属表面。
脱脂液的配制先将250 ml的水加入到烧杯中,慢慢加入三聚磷酸钠3克、硅酸钠2克、碳酸钠3克、磷酸钠2克、草酸1克,搅拌均匀,加水稀释至500ml,配制成低碱脱脂液。
处理条件在室温下浸泡2—5分钟。
(2)除锈采用磷酸与柠檬酸混合液酸洗除锈。
磷酸酸洗除锈有特殊的作用,在酸洗过程中可以在金属表面形成不溶性的磷酸亚铁。
磷酸亚铁在磷化处理过程中可起晶核作用,但是过多会妨碍磷化,加入有机阻蚀剂可以防止清洁的金属表面进一步受到磷酸酸液的侵蚀,同时又不妨碍磷酸对剩余氧化物起作用。
除锈处理液的配制将85%的磷酸5ml与3克柠檬酸,混合均匀,加水配制成250 ml的溶液。
处理条件将试样浸入该溶液中2—5分钟。
(3)水洗水洗的目的是去除试样表面残留的酸和碱。
经过脱脂和除锈的试样表面残留一定的碱和酸。
如果把这样的试样浸入磷化液中势必会影响磷化液的成分,进而影响磷化液膜的质量。
此外,磷化后的试样如不经过水洗,残留在磷化膜上的酸会降低磷化膜的耐蚀性能。
水洗液采用自来水为水洗液。
处理条件在室温浸泡5—10分钟。
(4)表调本实验采用酸性表调剂(草酸)对试样进行表面调整。
经过表面调整的试样,可以直接进行磷化处理,无需再经过水洗。
表面调整液的配制先将清水加入烧杯中至400ML,温度升至35摄氏度左右,将3克表调剂(草酸)加入烧杯中进行搅拌,待草酸完全溶解,加水至500ML彻底搅拌均匀。
表面调整的处理条件温度20—30摄氏度,时间30—150秒,处理方式为浸泡。
(5)磷化磷化液的配制(1)取适量的水放入500 ml的烧杯中,加热到25-35摄氏度。
磷化前的预处理和两种常用磷化工艺

磷化前的预处理和两种常用磷化工艺磷化是一种通过在金属表面形成一层磷化层来改善其表面性能的电解化学过程,通常使用盐酸或硝酸作为溶液。
在金属表面磷化之前,预处理是十分关键的步骤,因为它可以去除金属表面的污垢、氧化物和油脂等杂质,从而确保磷化质量的稳定和附着力的可靠性。
本文将介绍两种常用的磷化工艺和磷化前的预处理过程。
一、磷化前的预处理磷化前的预处理可以分为化学预处理和机械预处理两种类型。
化学预处理通常使用腐蚀剂和脱脂剂来清洁金属表面,而机械预处理则包括切割、砂光和打磨等步骤。
以下是一些常用的预处理工艺:1. 碱性清洗:使用氢氧化钠和氢氧化钾等碱性清洗剂可以去除金属表面的油脂、污垢和其他污染物。
2. 酸性清洗:使用酸性清洗剂,如盐酸或硝酸,可以去除金属表面的锈蚀和其他氧化产物。
3. 砂光:通过机械磨擦,使用砂纸和切割片等打磨工具,可以去除金属表面的较深层次的氧化物和污染。
4. 清水冲洗:使用清水彻底冲洗金属表面,以去除清洗和砂光后留下的污染物和化学残留物。
二、两种常用的磷化工艺1. 锌磷化锌磷化是一种常见的磷化工艺,通常用于不锈钢和钢铁等金属表面。
锌磷化的优点是其能够在金属表面形成一层较为均匀的磷化层,并且其耐腐蚀性能和附着力都很高。
在锌磷化之前,可以先使用碱性和酸性清洗剂进行表面处理,以确保金属表面干净无杂质。
磷化前的清洗处理可以使用高压冲洗机进行清洗处理,彻底去除表面密封处和蚀刻剂等残余物,确保磷化结果的均匀稳定。
2. 镍磷化镍磷化是另一种常见的磷化工艺,同样也适用于不锈钢和钢铁等金属表面。
镍磷化的优点是它能够为金属表面提供良好的耐腐蚀性能和良好的润滑性,从而可以延长金属件的使用寿命。
在进行镍磷化之前,同样需要进行先进行表面清洗以去除金属表面的杂质和污染物。
接着,使用含有镍离子和磷酸盐的电解液进行磷化处理,镍磷磷化能够在金属表面形成一层厚度大约为1-20微米的镍合金层。
在磷化过程中,磷酸盐和镍离子是两个关键的组成部分,可以在镍磷磷化防腐体系的制备中,添加提高镍磷磷化涂层的附着力、防腐性能和电学性能。
磷化处理工艺程序及操作方法
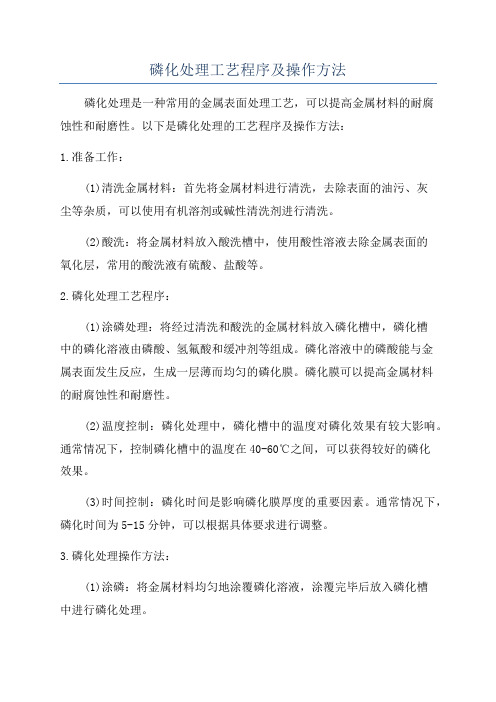
磷化处理工艺程序及操作方法磷化处理是一种常用的金属表面处理工艺,可以提高金属材料的耐腐蚀性和耐磨性。
以下是磷化处理的工艺程序及操作方法:1.准备工作:(1)清洗金属材料:首先将金属材料进行清洗,去除表面的油污、灰尘等杂质,可以使用有机溶剂或碱性清洗剂进行清洗。
(2)酸洗:将金属材料放入酸洗槽中,使用酸性溶液去除金属表面的氧化层,常用的酸洗液有硫酸、盐酸等。
2.磷化处理工艺程序:(1)涂磷处理:将经过清洗和酸洗的金属材料放入磷化槽中,磷化槽中的磷化溶液由磷酸、氢氟酸和缓冲剂等组成。
磷化溶液中的磷酸能与金属表面发生反应,生成一层薄而均匀的磷化膜。
磷化膜可以提高金属材料的耐腐蚀性和耐磨性。
(2)温度控制:磷化处理中,磷化槽中的温度对磷化效果有较大影响。
通常情况下,控制磷化槽中的温度在40-60℃之间,可以获得较好的磷化效果。
(3)时间控制:磷化时间是影响磷化膜厚度的重要因素。
通常情况下,磷化时间为5-15分钟,可以根据具体要求进行调整。
3.磷化处理操作方法:(1)涂磷:将金属材料均匀地涂覆磷化溶液,涂覆完毕后放入磷化槽中进行磷化处理。
(2)温度控制:调节磷化槽中的加热设备控制温度在40-60℃之间。
(3)时间控制:根据具体要求,控制磷化时间在5-15分钟之间。
(4)清洗:磷化处理完毕后,将金属材料从磷化槽中取出,使用清水进行冲洗,去除残留的磷化溶液和杂质。
(5)干燥:将清洗干净的金属材料放置在通风干燥的地方,等待其自然晾干。
4.注意事项:(1)操作安全:在进行磷化处理时,应佩戴个人防护装备,如手套、护目镜等,以保护自己的安全。
(2)剂量控制:在磷化溶液的配置中,应根据具体要求精确计量,以确保磷化效果的一致性。
(3)注意通风:磷化处理过程中会产生一定数量的有害气体,应选择通风条件良好的场所进行操作,以确保作业人员的健康安全。
(4)储存注意:磷化溶液应储存在阴凉、干燥的地方,并防止日晒和雨淋,避免阳光直射引起溶液质量变化。
磷化处理工艺操作规程
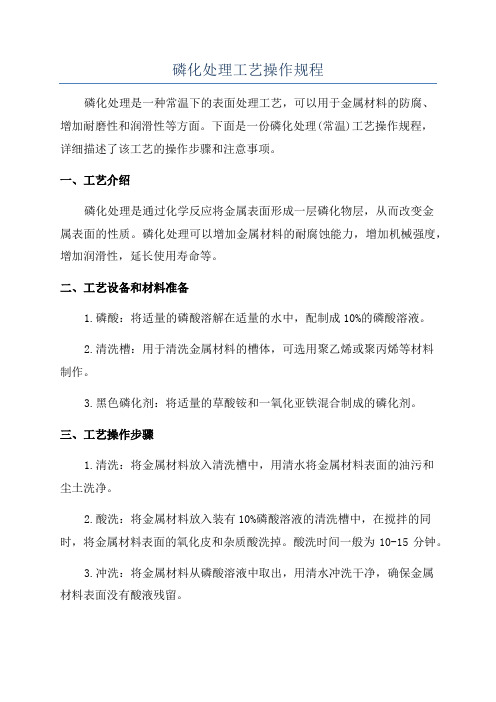
磷化处理工艺操作规程磷化处理是一种常温下的表面处理工艺,可以用于金属材料的防腐、增加耐磨性和润滑性等方面。
下面是一份磷化处理(常温)工艺操作规程,详细描述了该工艺的操作步骤和注意事项。
一、工艺介绍磷化处理是通过化学反应将金属表面形成一层磷化物层,从而改变金属表面的性质。
磷化处理可以增加金属材料的耐腐蚀能力,增加机械强度,增加润滑性,延长使用寿命等。
二、工艺设备和材料准备1.磷酸:将适量的磷酸溶解在适量的水中,配制成10%的磷酸溶液。
2.清洗槽:用于清洗金属材料的槽体,可选用聚乙烯或聚丙烯等材料制作。
3.黑色磷化剂:将适量的草酸铵和一氧化亚铁混合制成的磷化剂。
三、工艺操作步骤1.清洗:将金属材料放入清洗槽中,用清水将金属材料表面的油污和尘土洗净。
2.酸洗:将金属材料放入装有10%磷酸溶液的清洗槽中,在搅拌的同时,将金属材料表面的氧化皮和杂质酸洗掉。
酸洗时间一般为10-15分钟。
3.冲洗:将金属材料从磷酸溶液中取出,用清水冲洗干净,确保金属材料表面没有酸液残留。
4.磷化:将清洗干净的金属材料放入装有黑色磷化剂的磷化槽中,保持常温静置,时间根据材料的具体情况决定,一般为30-60分钟。
5.冲洗:将磷化完成的金属材料从磷化槽中取出,用清水冲洗干净,除去表面的磷化剂残留。
6.干燥:将冲洗干净的金属材料放入通风良好的地方,自然晾干。
四、注意事项1.操作时需佩戴防护手套和眼镜,以免酸液对皮肤和眼睛造成伤害。
2.操作过程中需注意防止酸液溅到周围环境或其他设备上,以免造成腐蚀。
3.磷化剂需按照一定比例混合制备,不得随意更改配方。
4.操作环境应通风良好,避免吸入磷化剂气体。
5.操作完成后,应及时清洁工作台和设备,避免磷化剂的残留。
五、工艺效果评估1.观察磷化处理后的金属材料表面是否呈现均匀的黑色。
2.通过化学测试,检测金属材料表面的磷化层厚度是否符合要求。
3.对磷化处理后的金属材料进行腐蚀试验,评估其耐腐蚀性能。
4.对磷化处理后的金属材料进行涂层附着力测试,评估其润滑性和耐磨性。
磷化处理工艺流程,表面处理黑色磷化工艺
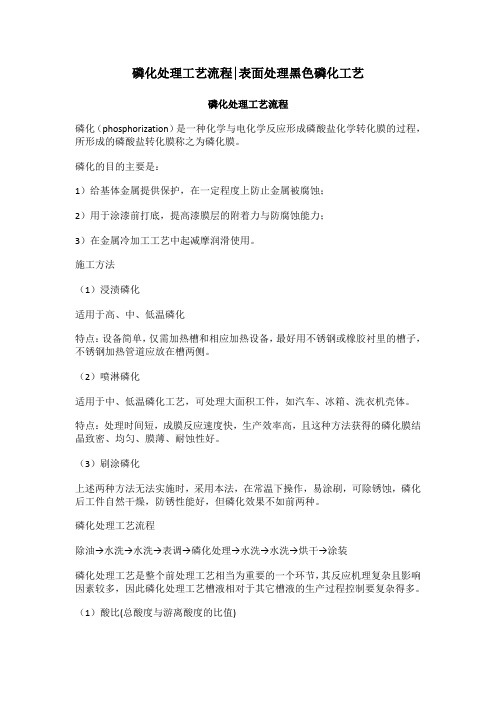
磷化处理工艺流程|表面处理黑色磷化工艺磷化处理工艺流程磷化(phosphorization)是一种化学与电化学反应形成磷酸盐化学转化膜的过程,所形成的磷酸盐转化膜称之为磷化膜。
磷化的目的主要是:1)给基体金属提供保护,在一定程度上防止金属被腐蚀;2)用于涂漆前打底,提高漆膜层的附着力与防腐蚀能力;3)在金属冷加工工艺中起减摩润滑使用。
施工方法(1)浸渍磷化适用于高、中、低温磷化特点:设备简单,仅需加热槽和相应加热设备,最好用不锈钢或橡胶衬里的槽子,不锈钢加热管道应放在槽两侧。
(2)喷淋磷化适用于中、低温磷化工艺,可处理大面积工件,如汽车、冰箱、洗衣机壳体。
特点:处理时间短,成膜反应速度快,生产效率高,且这种方法获得的磷化膜结晶致密、均匀、膜薄、耐蚀性好。
(3)刷涂磷化上述两种方法无法实施时,采用本法,在常温下操作,易涂刷,可除锈蚀,磷化后工件自然干燥,防锈性能好,但磷化效果不如前两种。
磷化处理工艺流程除油→水洗→水洗→表调→磷化处理→水洗→水洗→烘干→涂装磷化处理工艺是整个前处理工艺相当为重要的一个环节,其反应机理复杂且影响因素较多,因此磷化处理工艺槽液相对于其它槽液的生产过程控制要复杂得多。
(1)酸比(总酸度与游离酸度的比值)提高酸比可加快磷化处理工艺反应速度,使磷化处理工艺膜薄而细致,但酸比过高会使膜层过薄,易引起磷化处理工艺工件挂灰;酸比过低,磷化处理工艺反应速度缓慢,磷化处理工艺晶体粗大多孔,耐蚀性低,磷化处理工艺工件易生黄锈。
一般来说磷化处理工艺yao液体系或配方不同其酸比大小要求也不同。
(2)温度槽液温度适当提高,成膜速度加快,但温度过高,会影响酸比的变化,进而影响槽液的稳定性,同时膜层晶核粗大,槽液出渣量增大。
(3)沉渣量随着磷化处理工艺反应的不断进行,槽液内的沉渣量会逐渐增多,过量的沉渣会影响工件表面的界面反应,导致磷化处理工艺膜发花、挂灰严重,甚至不成膜,因此槽液必须根据处理的工件量和使用时间适时进行倒槽,进行清渣除淤。
磷化处理工艺
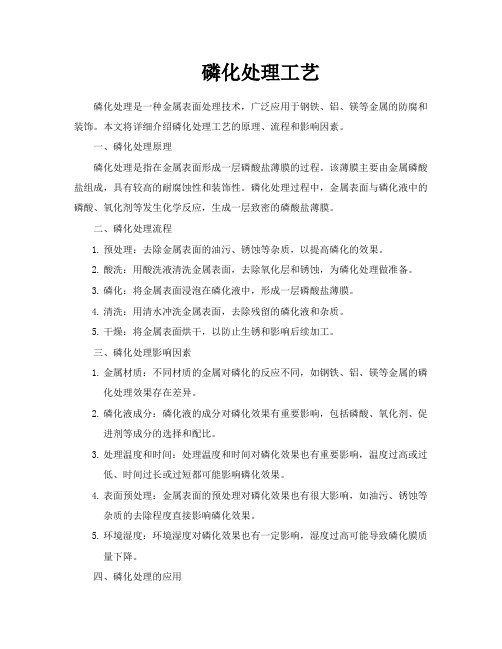
磷化处理工艺磷化处理是一种金属表面处理技术,广泛应用于钢铁、铝、镁等金属的防腐和装饰。
本文将详细介绍磷化处理工艺的原理、流程和影响因素。
一、磷化处理原理磷化处理是指在金属表面形成一层磷酸盐薄膜的过程。
该薄膜主要由金属磷酸盐组成,具有较高的耐腐蚀性和装饰性。
磷化处理过程中,金属表面与磷化液中的磷酸、氧化剂等发生化学反应,生成一层致密的磷酸盐薄膜。
二、磷化处理流程1.预处理:去除金属表面的油污、锈蚀等杂质,以提高磷化的效果。
2.酸洗:用酸洗液清洗金属表面,去除氧化层和锈蚀,为磷化处理做准备。
3.磷化:将金属表面浸泡在磷化液中,形成一层磷酸盐薄膜。
4.清洗:用清水冲洗金属表面,去除残留的磷化液和杂质。
5.干燥:将金属表面烘干,以防止生锈和影响后续加工。
三、磷化处理影响因素1.金属材质:不同材质的金属对磷化的反应不同,如钢铁、铝、镁等金属的磷化处理效果存在差异。
2.磷化液成分:磷化液的成分对磷化效果有重要影响,包括磷酸、氧化剂、促进剂等成分的选择和配比。
3.处理温度和时间:处理温度和时间对磷化效果也有重要影响,温度过高或过低、时间过长或过短都可能影响磷化效果。
4.表面预处理:金属表面的预处理对磷化效果也有很大影响,如油污、锈蚀等杂质的去除程度直接影响磷化效果。
5.环境湿度:环境湿度对磷化效果也有一定影响,湿度过高可能导致磷化膜质量下降。
四、磷化处理的应用1.防腐:磷化膜具有较高的耐腐蚀性,可用于钢铁、铝、镁等金属的防腐处理。
例如,在建筑、船舶、汽车等领域,磷化处理被广泛应用于金属结构的防腐保护。
2.装饰:磷化膜具有较好的装饰性,可用于金属表面的美化处理。
例如,在电子产品、家具等领域,磷化处理被广泛应用于产品的外观装饰。
3.耐磨:磷化膜还具有较好的耐磨性,可用于提高金属表面的耐磨性能。
例如,在机械零件、工具等领域,磷化处理被广泛应用于提高产品的耐磨性能。
4.粘合:磷化膜还可以作为粘合剂使用,将不同金属材料粘合在一起。
磷化处理工艺流程,磷化的影响因素及用途

磷化处理工艺流程| 磷化的影响因素及用途磷化是什么意思?磷化(phosphorization)是一种化学与电化学反应形成磷酸盐化学转化膜的过程,所形成的磷酸盐转化膜称之为磷化膜。
磷化的目的主要是给基体金属提供保护,在一定程度上防止金属被腐蚀;用于涂漆前打底,提高漆膜层的附着力与防腐蚀能力;在金属冷加工工艺中起减摩润滑使用。
磷化处理工艺应用于工业已有90多年的历史,大致可以分为三个时期:奠定磷化技术基础时期、磷化技术迅速发展时期和广泛应用时期。
磷化处理工艺流程:预脱脂→脱脂→除锈→水洗→(表调)→磷化→水洗→磷化后处理(如电泳或粉末涂装)。
磷化的影响因素:1、温度温度愈高,磷化层愈厚,结晶愈粗大。
温度愈低,磷化层愈薄,结晶愈细。
但温度不宜过高,否则Fe2+易被氧化成Fe3+,加大沉淀物量,溶液不稳定。
2、游离酸度游离酸度指游离的磷酸。
其作用是促使铁的溶解,已形成较多的晶核,使膜结晶致密。
游离酸度过高,则与铁作用加快,会大量析出氢,令界面层磷酸盐不易饱和,导致晶核形成困难,膜层结构疏松,多孔,耐蚀性下降,令磷化时间延长。
游离酸度过低,磷化膜变薄,甚至无膜。
3、总酸度总酸度指磷酸盐、硝酸盐和酸的总和。
总酸度一般以控制在规定范围上限为好,有利于加速磷化反应,使膜层晶粒细,磷化过程中,总酸度不断下降,反映缓慢。
总酸度过高,膜层变薄,可加水稀释。
总酸度过低,膜层疏松粗糙。
4、PH值锰系磷化液一般控制在2-3之间,当PH﹥3时,工件表面易生成粉末。
当PH‹1.5时难以成膜。
铁系一般控制在3-5.5之间。
5、溶液中离子浓度①溶液中Fe2+极易氧化成Fe3+,导致不易成膜。
但溶液中Fe2+浓度不能过高,否则,形成的膜晶粒粗大,膜表面有白色浮灰,耐蚀性及耐热性下降。
②Zn2+的影响,当Zn2+浓度过高,磷化膜晶粒粗大,脆性增大,表面呈白色浮灰;当Zn2+浓度过低,膜层疏松变暗。
磷化用途:(1)耐蚀防护用磷化膜①防护用磷化膜用于钢铁件耐蚀防护处理。
磷化工工艺流程
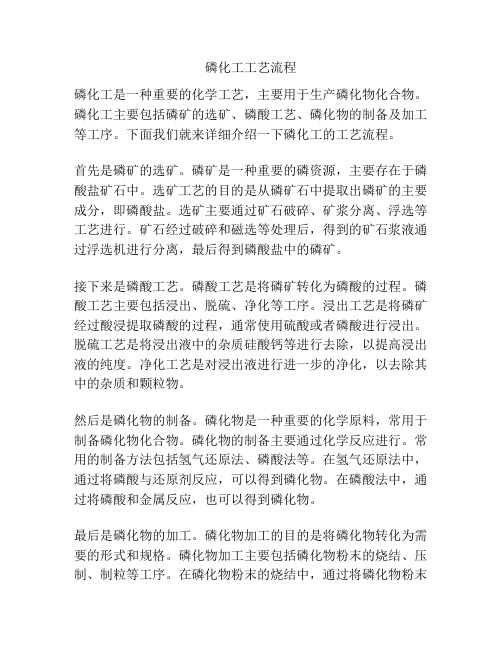
磷化工工艺流程磷化工是一种重要的化学工艺,主要用于生产磷化物化合物。
磷化工主要包括磷矿的选矿、磷酸工艺、磷化物的制备及加工等工序。
下面我们就来详细介绍一下磷化工的工艺流程。
首先是磷矿的选矿。
磷矿是一种重要的磷资源,主要存在于磷酸盐矿石中。
选矿工艺的目的是从磷矿石中提取出磷矿的主要成分,即磷酸盐。
选矿主要通过矿石破碎、矿浆分离、浮选等工艺进行。
矿石经过破碎和磁选等处理后,得到的矿石浆液通过浮选机进行分离,最后得到磷酸盐中的磷矿。
接下来是磷酸工艺。
磷酸工艺是将磷矿转化为磷酸的过程。
磷酸工艺主要包括浸出、脱硫、净化等工序。
浸出工艺是将磷矿经过酸浸提取磷酸的过程,通常使用硫酸或者磷酸进行浸出。
脱硫工艺是将浸出液中的杂质硅酸钙等进行去除,以提高浸出液的纯度。
净化工艺是对浸出液进行进一步的净化,以去除其中的杂质和颗粒物。
然后是磷化物的制备。
磷化物是一种重要的化学原料,常用于制备磷化物化合物。
磷化物的制备主要通过化学反应进行。
常用的制备方法包括氢气还原法、磷酸法等。
在氢气还原法中,通过将磷酸与还原剂反应,可以得到磷化物。
在磷酸法中,通过将磷酸和金属反应,也可以得到磷化物。
最后是磷化物的加工。
磷化物加工的目的是将磷化物转化为需要的形式和规格。
磷化物加工主要包括磷化物粉末的烧结、压制、制粒等工序。
在磷化物粉末的烧结中,通过将磷化物粉末放置在高温和高压下进行热压,使其形成致密的块体。
在压制和制粒过程中,通过对磷化物粉末进行压缩和制粒,可以得到各种形状和尺寸的磷化物制品。
以上就是磷化工的工艺流程。
磷化工在农业、化工等众多领域有着重要的应用,通过上述工艺流程可以得到高纯度和高质量的磷化物化合物,为各个行业的发展提供了有力的支持。
磷化原理及工艺

磷化原理及⼯艺中⽂名称:磷化英⽂名称:phosphatizing其他名称:磷酸盐处理定义:把⼯件浸⼊磷酸盐溶液中,使⼯件表⾯获得⼀层不溶于⽔的磷酸盐薄膜的⼯艺。
所属学科:机械⼯程(⼀级学科);机械⼯程(2)_热处理(⼆级学科);化学热处理(三级学科)磷化(phosphorization)是⼀种化学与电化学反应形成磷酸盐化学转化膜的过程,所形成的磷酸盐转化膜称之为磷化膜。
磷化的⽬的主要是:给基体⾦属提供保护,在⼀定程度上防⽌⾦属被腐蚀;⽤于涂漆前打底,提⾼漆膜层的附着⼒与防腐蚀能⼒;在⾦属冷加⼯⼯艺中起减摩润滑使⽤。
磷化处理⼯艺应⽤于⼯业⼰有90多年的历史,⼤致可以分为三个时期:奠定磷化技术基础时期、磷化技术迅速发展时期和⼴泛应⽤时期。
磷化膜⽤作钢铁的防腐蚀保护膜,最早的可靠记载是英国Charles Ross 于1869年获得的专利(B.P. N o.3119)。
从此,磷化⼯艺应⽤于⼯业⽣产。
在近⼀个世纪的漫长岁⽉中,磷化处理技术积累了丰富的经验,有了许多重⼤的发现。
⼀战期间,磷化技术的发展中⼼由英国转移⾄美国。
1909年美国T.W.Coslet将锌、氧化锌或磷酸锌盐溶于磷酸中制成了第⼀个锌系磷化液。
这⼀研究成果⼤⼤促进了磷化⼯艺的发展,拓宽了磷化⼯艺的发展前途。
Parker防锈公司研究开发的Parco Power配制磷化液,克服T许多缺点,将磷化处理时间提⾼到lho 1929年Bonderizing磷化⼯艺将磷化时间缩短⾄10min, 1934年磷化处理技术在⼯业上取得了⾰命性的发展,即采⽤了将磷化液喷射到⼯件上的⽅法。
⼆战结束以后,磷化技术很少有突破性进展,只是稳步的发展和完善。
磷化⼴泛应⽤于防蚀技术,⾦属冷变形加⼯⼯业。
这个时期磷化处理技术重要改进主要有:低温磷化、各种控制磷化膜膜重的⽅法、连续钢带⾼速磷化。
当前,磷化技术领域的研究⽅向主要是围绕提⾼质量、减少环境污染、节省能源进⾏。
原理及应⽤磷化是常⽤的前处理技术,原理上应属于化学转换膜处理,主要应⽤于钢铁表⾯磷化,有⾊⾦属(如铝、锌)件也可应⽤磷化。
标准件磷化处理工艺流程

标准件磷化处理工艺流程:
除油→水洗→除锈→水洗→表调→磷化→水洗→水洗→烘干(或直接电泳)→喷涂→后处理。
①前处理的除油、除锈要彻底。
②表调剂的配制为2-4g/l,ph值9-10,溶液呈乳白混浊态。
可按每天添加10%表调剂进行调整,也可按具体情况操作,如表调液或透明状则视为失效。
工件表调后,可直接进入到磷化槽中磷化处理。
③磷化膜均匀、致密,灰色膜或灰色带浅金黄彩色膜。
处理的时间可随温度的升高而缩短,以达到工件磷化要求为准。
④阴极电泳时,磷化后经水洗,再用去离子水清洗后,直接进入电泳槽;
⑤当工件需进行喷粉或喷漆时,磷化、清洗后,需烘干后,再进行后续工序。
磷化工艺技术

磷化工艺技术磷化工艺技术是一种将金属表面覆盖上一层磷化膜的工艺,常用于金属防腐、增加金属表面硬度等方面。
下面是对磷化工艺技术的一些详细介绍。
磷化膜是一种由金属磷酸盐组成的覆盖在金属表面的一层化学膜层。
磷化膜具有很高的耐磨性、耐蚀性和防腐性,可以有效地保护金属表面,延长其使用寿命。
同时,磷化膜还可以增加金属材料的硬度,改善其表面质量。
磷化工艺技术分为化学磷化和电化学磷化两种。
化学磷化是通过将金属材料浸泡在含有磷酸盐和氯化盐的溶液中,利用化学反应在金属表面形成磷化膜。
电化学磷化是在电解质溶液中,将金属材料作为阳极,在施加电流的情况下,在金属表面上形成磷化膜。
磷化工艺技术的优点主要体现在以下几个方面:首先,磷化膜具有较高的耐磨性和耐腐蚀性,可以有效地保护金属材料;其次,磷化膜的形成过程简单,不需要复杂的设备和工艺步骤,成本较低;再次,磷化膜可以增加金属材料的硬度,提高其表面质量和使用寿命;最后,磷化膜可以增加金属材料的涂装附着力,使涂层更加牢固。
然而,磷化工艺技术也存在一些问题。
首先,磷化膜的厚度很难控制,在磷化过程中容易产生不均匀的情况。
其次,磷化过程需要一定的时间,不能够实时完成,导致生产周期较长。
此外,磷化溶液中的磷酸盐和氯化盐对环境有一定的污染。
为了解决这些问题,各个行业对磷化工艺技术进行了不断的改进和研究。
研究人员通过调节磷化溶液的组成和浓度,优化磷化工艺参数,提高磷化的效果和一致性。
此外,还发展了一些新的磷化工艺技术,如有机磷化、浸泡磷化等,以满足不同行业对磷化膜的需求。
总之,磷化工艺技术是一种重要的表面处理工艺,可以为金属材料提供保护和改良。
随着科技的不断进步和需求的不断增加,磷化工艺技术将会不断发展,更好地满足社会的需求。
磷化工艺及技巧范文

磷化工艺及技巧范文磷化是一种通过在金属表面形成磷化物层来提高金属材料性能的表面处理方法。
磷化可以增强金属材料的耐腐蚀性能、润滑性能和磨损性能,同时还能提高金属材料的表面硬度和抗疲劳性能。
下面将介绍一些磷化工艺及技巧。
1.表面处理:在进行磷化之前,必须对金属表面进行适当的处理,以保证磷化层与金属基材之间的结合力。
表面处理的方法包括去油、除锈和机械处理。
去油可以使用溶剂或碱性清洗剂进行,除锈可以使用酸性溶液进行,机械处理可以通过打磨或喷砂等方法进行。
2.磷化溶液的制备:磷化溶液的制备是磷化工艺的关键环节。
一般情况下,磷化溶液是由磷酸盐、氧化剂、络合剂和助剂等组成的。
其中,磷酸盐是磷化溶液的主要成分,可以使用磷酸、亚磷酸或磷酸二氢钠等作为磷酸盐;氧化剂的主要作用是提供氧气,常用的氧化剂有过氧化氢、亚硝酸盐和氯酸盐等;络合剂的作用是增强磷化反应的速度和均匀性,可以使用氯化铵或柠檬酸等络合剂;助剂的作用是改善磷化层的性能,可以使用聚合物或胶体等助剂。
3.磷化操作条件的控制:在进行磷化操作时,需要严格控制磷化溶液的温度、浸泡时间和搅拌速度等操作条件,以确保磷化层的质量。
通常情况下,磷化温度在60-90摄氏度之间,浸泡时间在5-20分钟之间,搅拌速度一般为100-200转/分钟。
4.磷化层的改性:通过添加一些化学添加剂,可以改善磷化层的性能。
例如,添加硝酸盐可以增加磷化层的硬度;添加聚合物可以增强磷化层的附着力和抗磨损性能;添加颜料可以改变磷化层的颜色等。
5.磷化后的处理:在磷化之后,需要对金属材料进行进一步处理,以增加磷化层的抗氧化性能和耐蚀性能。
常见的处理方法包括沉积一层金属膜、电沉积或热处理等。
总之,磷化是一种重要的金属材料表面处理方法,可以显著改善金属材料的性能。
在进行磷化工艺时,需要注意表面处理、磷化溶液的制备、操作条件的控制、磷化层的改性以及磷化后的处理等方面的技巧。
通过合理选择和控制这些因素,可以得到质量良好的磷化层,提高金属材料的使用寿命和性能。
磷化工艺及注意事项

磷化工艺及注意事项磷化工艺是一种将磷元素与金属基底反应形成金属磷化合物的表面处理方法。
磷化工艺常用于提高金属材料的抗腐蚀性、硬度和润滑性,同时还可以改善金属的粘接性和涂装性能。
磷化工艺主要有化学磷化和热磷化两种方式。
化学磷化是通过在含磷酸盐溶液中浸泡金属材料,在化学反应的作用下产生金属磷化合物的一种表面处理方法。
其具体步骤如下:1. 除油脂:首先要将金属材料进行去油处理,以保证金属表面清洁。
2. 酸洗:将金属材料在酸性溶液中进行酸洗,去除表面氧化层和其他杂质。
3. 磷化:将酸洗后的金属材料浸泡在含磷酸盐溶液中,在一定的温度和时间条件下进行磷化反应。
磷化反应中,磷酸盐溶液中的磷酸根离子与金属表面发生化学反应生成金属磷化合物。
4. 中和:磷化后的金属材料需要经过中和处理,以去除残留的酸性物质。
5. 水洗:将中和后的金属材料进行水洗,去除中和剂残留。
6. 去漂白:一些情况下需要进行漂白处理,以提高金属表面的亮度。
热磷化是通过将金属材料加热至一定温度,与磷源反应生成金属磷化物的一种表面处理方法。
具体步骤如下:1. 除油脂:同样需要将金属材料进行去油处理。
2. 酸洗:将金属材料在酸性溶液中进行酸洗,去除表面氧化层和其他杂质。
3. 热磷化:将酸洗后的金属材料放入磷化炉中,在一定温度和时间条件下进行磷化反应。
磷化反应中,金属表面与流动的磷源气体反应生成金属磷化物。
4. 水洗:将热磷化后的金属材料进行水洗,去除残留的磷酸盐。
5. 去漂白:一些情况下需要进行漂白处理。
磷化工艺虽然可以提高金属材料的性能,但使用时也需注意以下事项:1. 温度和时间控制:磷化反应中的温度和时间会影响磷化层的质量和厚度,需要根据具体材料和要求进行合理的控制。
2. 酸洗控制:酸洗过程中的酸性溶液浓度、温度和时间等参数需要控制良好,以保证金属表面的干净和光洁。
3. 中和和水洗:磷化后的金属材料需要进行中和和水洗过程,以去除残留的酸性物质和盐类。
磷化工艺介绍

所谓磷化,是指把金属工件经过含有磷酸二氢盐的酸性溶液处理,发生化学反应而在其表面生成一层稳定的不溶性磷酸盐膜层的方法,所生成的膜称为磷化膜。
磷化膜的主要目的是增加涂膜附着力,提高涂层耐蚀性。
磷化的方法有多种,按磷化时的温度来分,可分为高温磷化(90-98℃),中温磷化(60-75℃),低温磷化(35-55℃)和常温磷化。
为提供良好的涂装基底,要求磷化膜厚度适宜,结晶致密细小。
中、高温磷化工艺,虽然磷化速度快,磷化膜耐蚀性好,但磷化膜结晶粗大,挂灰重,液面挥发快,槽液不稳定,沉渣多,而低、常温磷化工艺所形成的磷化膜结晶细致,厚度适宜,膜间很少夹杂沉渣物,吸漆量少,涂层光泽度好,可大大改善涂层的附着力、柔韧性、抗冲击性等,更能满足涂层对磷化膜的要求。
值得注意的是,过去一直认为磷化膜厚,涂装后涂层的耐蚀性高,磷化膜本身在整个涂装体系中并不单独承担多大的耐蚀作用,它主要起到使漆膜具有强粘附性,而整个涂层系统的耐蚀力则主要取决于漆膜的耐蚀力以及漆膜与磷化膜的优良配合所形成的强粘附力。
磷化液一般由主盐、促进剂和中和剂所组成。
过去使用的磷化液,大多采用亚硝酸钠(NaNO2)作促进剂,效果十分年、明显,但在NaNO2在磷化液中有很大危害:一是影响磷化液的稳定性,NaNO2在酸性条件下极不稳定,在极短的时间内就分解了。
因此,不得不经常添加。
NaNO2的这种特性,往往引起磷化液的主盐不稳定,磷化液沉淀较多,磷化膜挂灰严重,槽液控制困难,磷化质量不稳定;二是NaNO2是世界公认的致癌物质,长期接触危害人体健康,环境污染严重。
解决的方法:一是减少NaNO2的用量;二是寻找替代物。
配方:XH-1B 4%+H2O4、钝化磷化膜的钝化技术,在北美和欧洲国家被广泛应用,采用钝化技术是基于磷化膜自身特点决定的,磷化膜较薄,一般在1-4g/m2,最大不超过10g/m2,其自由孔隙面积大,膜本身的耐蚀力有限。
有的甚至在干燥过程中就迅速生黄锈,磷化后进行一次钝化封闭处理,可以是磷化膜孔隙中暴露的金属进一步氧化,或生成钝化层,对磷化膜可以起到填充、氧化作用,使磷化膜稳定于大气之中。
磷化处理工艺流程

磷化处理工艺流程磷化处理是一种常见的金属表面处理方法,可以提高材料的耐腐蚀性能和润滑性能,广泛应用于汽车制造、机械加工、电子制造等领域。
下面将介绍磷化处理的工艺流程。
1.预处理预处理是为了保证金属表面的干净和平整。
首先,需要将脏污、油脂、氧化皮等杂质彻底清除。
常用的清洗方法包括水洗、碱洗和酸洗。
其中,水洗可以去除表面的灰尘和污垢;碱洗可以去除表面的油脂和污渍;酸洗可以去除表面的氧化皮和锈蚀。
清洗后,需要用清水冲洗表面,以确保废液彻底被去除。
2.磷化处理磷化处理是磷酸溶液与金属表面反应,生成磷化物膜。
磷化物膜可以提高金属表面的耐腐蚀性能和润滑性能。
通常,磷化处理可分为化学磷化和电化学磷化两种方法。
(1)化学磷化化学磷化是将金属制件浸泡在含有磷酸盐和助剂的酸性溶液中,通过物理和化学反应生成磷化物膜。
化学磷化的工艺流程包括浸泡、催化、磷化和中和几个步骤。
首先,金属制件被浸入磷酸盐溶液中,使其与金属表面产生化学反应,生成磷化物膜。
然后,使用铜催化剂加快反应速度,提高磷化膜的均匀性和致密性。
磷化时间和温度根据材料的不同进行调整,一般为数十分钟到数小时。
最后,通过中和处理将制件从磷酸溶液中取出,以减少酸性残留。
(2)电化学磷化电化学磷化是通过外加电压的作用,将金属制件浸泡在含有磷酸盐和助剂的电解液中,通过电化学反应生成磷化物膜。
电化学磷化的工艺流程包括预处理、电化学磷化和中和。
预处理与化学磷化中的预处理相似,即清洗和除油。
然后,金属制件被浸入电解液中,作为阳极连接到电源上,电解液中的磷酸盐和助剂通过电解反应在金属表面生成磷化物膜。
磷化电流密度、时间和温度根据材料的不同进行调整。
最后,通过中和处理将制件从电解液中取出,以减少酸性残留。
3.后处理后处理是为了进一步提高磷化膜的性能,防止其脱落和生锈。
后处理工艺包括清洗和封闭两个步骤。
清洗的目的是去除磷化过程中残留的酸性物质。
封闭是在磷化膜上涂覆一层封闭剂,增强膜的致密性和耐腐蚀性。
磷化工艺及技巧
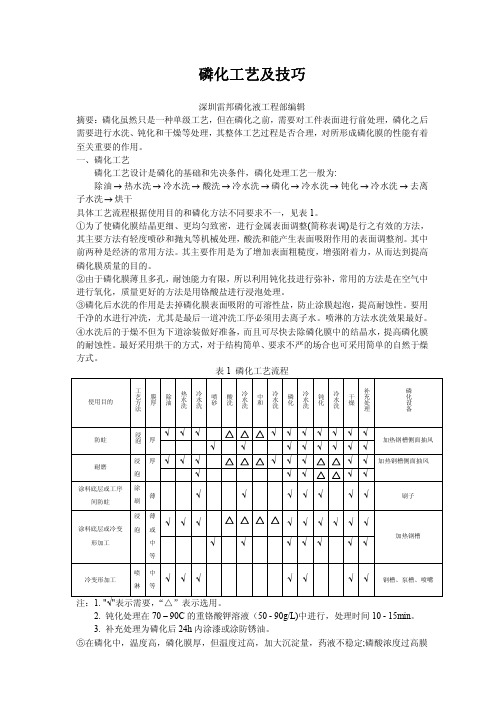
膜重/(g/m ) 晶核尺寸 结晶形状 结晶重金属含量/(mg/m2 ) 耐碱性 耐水二次附着性 耐疙形腐蚀性 镀锌板适应性 项 设备结构 设备制造 设备维护 对工件的机械力 磷化液管理 对复杂工件的处理 处理液槽体积 所需工艺时间 生产线长度 工作液热量损失 磷化膜的用途 对磷化液的适用性 对生产量的适用性 对磷化工件的适用性 目
1. 浸渍磷化的特点和流程 浸渍磷化处理,按照工艺流程,将工件顺序浸人磷化液槽中进行处理,大型工件可用吊 挂方式,小件用篮筐盛装。它是一种最早采用的磷化方式,但目前应用最广。 其优点是磷化槽液可以达到的地方均能进行处理, 即适合于各形状和结构的工件, 设备 维护工作量小,槽液浪费少,日常管理简单。 其缺点是没有喷淋工艺那样的机械冲刷的辅助作用, 处理速度相对较慢, 处理时间相对
ቤተ መጻሕፍቲ ባይዱ
磷化工艺及技巧
深圳雷邦磷化液工程部编辑 摘要:磷化虽然只是一种单级工艺,但在磷化之前,需要对工件表面进行前处理,磷化之后 需要进行水洗、钝化和干燥等处理,其整体工艺过程是否合理,对所形成磷化膜的性能有着 至关重要的作用。 一、磷化工艺 磷化工艺设计是磷化的基础和先决条件,磷化处理工艺一般为: 除油 热水洗 冷水洗 酸洗 冷水洗 磷化 冷水洗 钝化 冷水洗 去离 子水洗 烘干 具体工艺流程根据使用目的和磷化方法不同要求不一,见表 1。 ①为了使磷化膜结晶更细、更均匀致密,进行金属表面调整(简称表调)是行之有效的方法, 其主要方法有轻度喷砂和抛丸等机械处理, 酸洗和能产生表面吸附作用的表面调整剂。 其中 前两种是经济的常用方法。其主要作用是为了增加表面粗糙度,增强附着力,从而达到提高 磷化膜质量的目的。 ②由于磷化膜薄且多孔,耐蚀能力有限,所以利用钝化技进行弥补,常用的方法是在空气中 进行氧化,质量更好的方法是用铬酸盐进行浸泡处理。 ③磷化后水洗的作用是去掉磷化膜表面吸附的可溶性盐,防止涂膜起泡,提高耐蚀性。要用 千净的水进行冲洗,尤其是最后一道冲洗工序必须用去离子水。喷淋的方法水洗效果最好。 ④水洗后的于燥不但为下道涂装做好准备, 而且可尽快去除磷化膜中的结晶水, 提高磷化膜 的耐蚀性。最好采用烘干的方式,对于结构简单、要求不严的场合也可采用简单的自然于燥 方式。 表 1 磷化工艺流程
磷化工艺流程

磷化工艺流程
磷化技术是一种利用磷酸盐与金属表面反应生成磷化物保护层的
表面处理方法。
下面是一般的磷化工艺流程:
1. 清洗:将金属工件或零件进行清洗,去除表面的油脂、污垢
和氧化物等杂质。
常用的清洗方法有碱洗、酸洗和水洗等。
2. 预处理:在清洗完毕后,可以进行一些预处理,例如去氧化、除锈、去刺等。
这些步骤可以提高磷化层的附着力和均匀性。
3. 激活处理:为了增加金属表面的反应性,通常需要进行激活处理。
常用的激活方法包括酸洗、电解激活和活化剂处理等。
4. 磷化处理:将金属工件或零件浸入含磷酸盐的磷化液中,进行磷化
处理。
磷化液中一般还包含酸性添加剂、缓冲剂和表面活性剂等。
磷
化时间和温度可以根据具体要求进行控制。
5. 中和处理:在完成磷化后,需要将金属表面的过量磷酸盐和其他残
留物进行中和处理。
常用的中和剂有碱性溶液和水等。
6. 漂洗:将磷化后的金属工件或零件进行漂洗,去除残留的中和剂和
其他有害物质。
漂洗可以使用水或有机溶剂等。
7. 除水处理:为避免磷化层产生氧化现象,对水洗后的磷化工件或零
件进行脱水处理。
常用的脱水方法有吹干、烘干和烘箱等。
8. 添加保护剂:为了增加磷化层的抗腐蚀性能和润滑性能,可以在磷
化层上添加一层保护剂,例如防锈油或涂料等。
以上是一般的磷化工艺流程,具体的磷化工艺会因金属种类、磷
化要求和工艺条件等不同而有所区别。
- 1、下载文档前请自行甄别文档内容的完整性,平台不提供额外的编辑、内容补充、找答案等附加服务。
- 2、"仅部分预览"的文档,不可在线预览部分如存在完整性等问题,可反馈申请退款(可完整预览的文档不适用该条件!)。
- 3、如文档侵犯您的权益,请联系客服反馈,我们会尽快为您处理(人工客服工作时间:9:00-18:30)。
Fe+3Zn(H2PO4)2 Zn3(PO4)2 ↓ +2FeHPO4 ↓ +3 H3PO4+2 H2 ↑ 放热 磷化分类 1 、按磷化处理温度分类 ( 1 )高温型 80—90 ℃处理时间为 10-20 分钟,形成磷化膜厚达 10-30g/m2, 溶液游离酸度 与总酸度的比值为 1 :( 7-8 ) 优点:膜抗蚀力强,结合力好。 缺点:加温时间长,溶液挥发量大,能耗大,磷化沉积多,游离酸度不稳定, 结晶粗细不均匀,已较少应用。
总述: 磷化是一种化学与电化学反应形成磷酸盐化学转化膜的过程,所形成的磷酸盐 转化膜称之为磷化膜。磷化的目的主要是:给基体金属提供保护,在一定程度上防 止金属被腐蚀;用于涂漆前打底,提高漆膜层的附着力与防腐蚀能力;在金属冷加 工工艺中起减摩润滑使用。 磷化处理工艺应用于工业己有 90 多年的历史,大致可 以分为三个时期 : 奠定磷化技术基础时期、磷化技术迅速发展时期和广泛应用时期。 磷化膜用作钢铁的防腐蚀保护膜,最早的可靠记载是英国 Charles Ross 于 1869 年获得的专利 (B.P.No.3119) 。从此,磷化工艺应用于工业生产。在近一个世 纪的漫长岁月中,磷化处理技术积累了丰富的经验,有了许多重大的发现。一战期 间,磷化技术的发展中心由英国转移至美国。 1909 年美国 T.W.Coslet 将锌、氧化 锌或磷酸锌盐溶于磷酸中制成了第一个锌系磷化液。这一研究成果大大促进了磷化 Parker 防锈公司研究开发的 Parco Power 工艺的发展, 拓宽了磷化工艺的发展前途。 配制磷化液,克服 T 许多缺点,将磷化处理时间提高到 lho 1929 年 Bonderizing 磷 化工艺将磷化时间缩短至 10min, 1934 年磷化处理技术在工业上取得了革命性的发 展,即采用了将磷化液喷射到工件上的方法。二战结束以后,磷化技术很少有突破 性进展,只是稳步的发展和完善。磷化广泛应用于防蚀技术,金属冷变形加工工业。 这个时期磷化处理技术重要改进主要有 : 低温磷化、各种控制磷化膜膜重的方法、连 续钢带高速磷化。当前,磷化技术领域的研究方向主要是围绕提高质量、减少环境 污染、节省能源进行。 (二)磷化是常用的前处理技术,原理上应属于化学转换膜处理,主要应用 于钢铁表面磷化,有色金属(如铝、锌)件也可应用磷化。 (三)磷化基础知识 磷化原理 1 、磷化 工件(钢铁或铝、锌件)浸入磷化液(某些酸式磷酸盐为主的溶液),在表面 沉积形成一层不溶于水的结晶型磷酸盐转换膜的过程,称之为磷化。 2 、磷化原理 钢铁件浸入磷化液(由 Fe(H2PO4)2 Mn(H2PO4)2 Zn(H2PO4)2 组成的酸性 稀水溶液,PH 值为 1-3 ,溶液相对密度为 1.05-1.10 )中,磷化膜的生成反应如下: 吸热
磷化(Ⅲ)——磷化工艺(1) 1 防锈磷化工艺 磷化工艺的早期应用是防锈,钢铁件经磷化处理形成一层磷化膜,起到防锈作用。 经过磷化防锈处理的工件防锈期可达几个月甚至几年(对涂油工件而言),广泛用于工 序间、运输、包装贮存及使用过程中的防锈,防锈磷化主要有铁系磷化、锌系磷化、锰 系磷化三大品种。 铁系磷化的主体槽液成分是磷酸亚铁溶液,不含氧化类促进剂,并且有高游离酸度。 这种铁系磷化处理温度高于 95℃, 处理时间长达 30min 以上, 磷化膜重大于 10g/m ,并且 有除锈和磷化双重功能。这种高温铁系磷化由于磷化速度太慢,现在应用很少。 锰系磷化用作防锈磷化具有最佳性能,磷化膜微观结构呈颗粒密堆集状,是应用最 为广泛的防锈磷化。加与不加促进剂均可,如果加入硝酸盐或硝基胍促进剂可加快磷化 成膜速度。通常处理温度 80~100℃,处理时间 10~20min,膜重在 7.5 克/m 以上。 锌系磷化也是广泛应用的一种防锈磷化, 通常采用硝酸盐作为促进剂, 处理温度 80~ 90℃, 处理时间 10~15min, 磷化膜重大于 7.5g/m ,磷化膜微观结构一般是针片紧密堆集 型。 防锈磷化一般工艺流程: 除油除锈——水清洗——表面调整活化——磷化——水清洗——铬酸盐处理——烘干 ——涂油脂或染色处理 通过强碱强酸处理过的工件会导致磷化膜粗化现象, 采用表面调整活化可细化晶粒。 锌系磷化可采用草酸、胶体钛表调。锰系磷化可采用不溶性磷酸锰悬浮液活化。铁系磷 化一般不需要调整活化处理。磷化后的工件经铬酸盐封闭可大幅度提高防锈性,如再经 过涂油或染色处理可将防锈性提高几位甚至几十倍,见表 1。 表 1 磷化膜与涂油复合对耐蚀性的影响 材料 裸钢 钢+涂油 钢+16g/m2 锌磷化 钢+锌磷化+涂油 出现锈蚀时间(h)(盐雾 ASTM B117-64) 0.5 15.0 4.0 550.0
2 2 2
摘自 Freeman D B.Phosphating and Metal Pretreatment Woodhead-Faukner,1986.
2 耐磨减摩润滑磷化工艺 对于发动机活塞环、齿轮、制冷压缩机一类工件,它不仅承受一次载荷,而且还有 运动摩擦,要求工件能减摩、耐摩。锰系磷化膜具有较高的硬度和热稳定性,能耐磨损, 磷化膜具有较好的减摩润滑作用。因此,广泛应用于活塞环,轴承支座,压缩机等零部 件。 这类耐磨减摩磷化处理温度 70~100℃, 处理时间 10~20min, 磷化膜重大于 7.5g/m 。 在冷加工行业如:接管、拉丝、挤压、深拉延等工序,要求磷化膜提供减摩润滑性 能,一般采用锌系磷化,一是锌系磷化膜皂化后形成润滑性很好的硬脂酸锌层,二是锌 系磷化操作温度比较低,可在 40、60 或 90℃条件下进行磷化处理,磷化时间 4~10min, 有时甚至几十秒钟即可,磷化膜重量要求≥3g/m2 便可。工艺流程是: 耐磨减摩磷化 减摩润滑磷化(冷加工) 除油除锈 除油除锈 水清洗 水清洗 锰系磷化 锌系磷化 水清洗 水清洗 干燥 皂化(硬脂酸钠) 涂润滑油脂 干燥 3 漆前磷化工艺 涂装底漆前的磷化处理,将提高漆膜与基体金属的附着力,提高整个涂层系统的耐 腐蚀能力;提供工序间保护以免形成二次生锈。因此漆前磷化的首要问题是磷化膜必须 与底漆有优良的配套性,而磷化膜本身的防锈性是次要的,磷化膜细致密实、膜薄。当 磷化膜粗厚时,会对漆膜的综合性能产生负效应。磷化体系与工艺的选定主要由:工件 材质、油锈程度、几何形状;磷化与涂漆的时间间隔;底漆品种和施工方式以及相关场 地设备条件决定。 一般来说,低碳钢较高碳钢容易进行磷化处理,磷化成膜性能好些。对于有锈(氧 化皮)工件必须经过酸洗工序,而酸洗后的工件将给磷化带来很多麻烦,如工序间生锈 泛黄,残留酸液的清除,磷化膜出现粗化等。酸洗后的工件在进行锌系、锌锰系磷化前 一般要进行表面调整处理。 在间歇式的生产场合,由于受条件限制,磷化工件必须存放一段时间后才能涂漆, 因此要求磷化膜本身具有较好的防锈性。 如果存放期在 10 天以上, 一般应采用中温磷化,
3Zn(H2PO4)2 Zn3(PO4)2 ↓ +4H3PO4 或 3Mn(H2PO4)2 Mn3(PO4)2 ↓ +4H3PO4 钢铁工件是钢铁合金, 在磷酸作用下, Fe 和 FeC3 形成无数原电池, 在阳极区, 铁开始熔解为 Fe2+,同时放出电子。 Fe+2H3PO4 → Fe (H2PO4)2+H2 ↑ Fe → Fe2+ +2e在钢铁工件表面附近的溶液中 Fe2+不断增加,当 Fe2+与 HPO42-, PO43- 浓 度大于磷酸盐的溶度积时,产生沉淀,在工件表面形成磷化膜: Fe(H2PO4)2 FeHPO4 ↓ + H3PO4 Fe+ Fe(H2PO4)2 2FeHPO4 ↓ + H2 ↑ 3FeHPO4 Fe 3(PO4)2 ↓ + H3PO4 Fe+ 2FeHPO4 Fe 3(PO4)2 ↓ +H2 ↑ 阴极区放出大量的氢: 2H+ +2e- H2 ↑ O2 + 2H20 + 4e- 4OH总反应式: 吸热 3Zn(H2PO4)2 Zn3(PO4)2 ↓ +4H3PO4
( 2 )中温型 50-75 ℃,处理时间 5-15 分钟,磷化膜厚度为 1-7 g/m2 ,溶液游离酸度与总酸 度的比值为 1 :( 10-15 ) 优点:游离酸度稳定,易掌握,磷化时间短,生产效率高,耐蚀性与高温磷化 膜基本相同,目前应用较多。 ( 3 )低温型 30-50 ℃ 节省能源,使用方便。 ( 4 )常温型 10-40 ℃ 常(低)温磷化(除加氧化剂外,还加促进剂),时间 10-40 分钟, 溶液游离酸度与总酸度比值为 1 :( 20-30 ),膜厚为 0.2-7 g/m2 。 优点:不需加热,药品消耗少,溶液稳定。 缺点:处理时间长,溶液配制较繁。 2 、按磷化液成分分类 ( 1 )锌系磷化 ( 2 )锌钙系磷化 ( 3 )铁系磷化 ( 4 )锰系磷化 ( 5 )复合磷化 磷化液由锌、铁、钙、镍、锰等元素组成。 3 、按磷化处理方法分类 ( 1 )化学磷化 将工件浸入磷化液中,依靠化学反应来实现磷化,目前应用广泛。 ( 2 )电化学磷化 在磷化液中,工件接正极,钢铁接负极进行磷化。 4 、按磷化膜质量分类 ( 1 )重量级(厚膜磷化) 膜重 7.5 g/m2 以上。 ( 2 )次重量级(中膜磷化)膜重 4.6-7.5 g/m2 。 ( 3 )轻量级(薄膜磷化)膜重 1.1-4.5 g/m2 。 ( 4 )次轻量级(特薄膜磷化)膜重 0.2-1.0 g/m2 。 5 、按施工方法分类 ( 1 )浸渍磷化
ห้องสมุดไป่ตู้
表面调整工序并非必须,表调剂加到脱脂槽内也可达到相同效果。磷化后的去离子 水洗必不可少。磷化后的铬酸盐处理,可提高整个涂层系统的耐腐蚀性能(见表 2),但 由于铬的环境污染问题,因此应慎使用。 表 2 铬酸盐处理对漆膜耐蚀性能影响 去离子水洗 轻铁系 锌系 锌钙系 锌系 锌钙系 铬酸盐处理 0.5 2.0 1.2 2.0 2.5 划痕 3mm 扩散时间(h) (盐雾 ASTMB117-64) 48 144 216 192 264 96 240 288 312 360 * 数据来源与表 1 相同 3.3 混合件磷化处理工艺(锈蚀工件) ①脱脂 40~70℃ 3~8min ②水清洗 常温 0.5~1.0min ③酸洗 40~70℃ 3~8min ④水清洗 常温 0.5min ⑤中和 常温 0.5~1.0min ⑥表面调整 常温 0.5min ⑦磷化 35~60℃ 3~10min ⑧水清洗 常温 0.5~1.0min ⑨脱离子水洗 常温 0.5~1.0min ⑩铬酸盐水洗 40~70℃ 0.5~1.0min ⑾烘干 <180℃ 除非有足够的理由,酸洗工序一般不采用喷淋处理方式,喷淋会带来设备腐蚀以及 工件工序间生锈等一系列问题。其他各工序均可采用全喷淋或喷-浸相结合的施工方式。 对于混合件(无锈工件、有锈、氧化皮工件同时混合处理),采用脱脂除锈“二合一” 代替分步脱脂除锈的方法已经应用有几十年的历史,同样可获满意效果。对于酸洗和脱 脂除锈“二合一”一般采用非挥发性的无机酸较适宜。