板材零件成对液压成形新技术
以液体静压为基础的高压成型技术分析

以液体静压为基础的高压成型技术分析随着科技的发展,各个行业都在不断探索与改进新的技术。
制造业中液体静压成型技术就是一种被广泛应用的高新技术。
这种技术通过利用高压油液推动金属板材变形,以满足产品对于形状、尺寸、性能等各方面的要求。
本文将从液体静压成型的基本概念、原理,以及优点等方面来对该技术进行分析。
一、基本概念液体静压成型技术(Hydrostatic Forming Technology)又称液压成型、液态冲击成型或压力成型,是一种利用高压油液来推动金属板材形成目标形状的成型技术。
这种技术广泛应用于航空、汽车、骨科、建筑等领域的产品生产中。
传统的冷冲压成型技术的局限性在于其不能对比较厚的材料进行成型,而液压成型技术则可以克服这种局限,成型厚度可以达到几百毫米。
二、原理在液态静压成型技术中,先将金属板材加工成凸台形状,并将其安置在硅胶板上方。
然后在凸台顶端装置一片板状的油囊,将油囊充满高压液体(通常为油)。
随后在凸台上端加上塑料膜,然后启动高压油泵,将高压油液注入油囊内。
这时,油囊内的压力就会逐渐升高,由于油囊的切线上的液体的力会作用在管子上,从而让管子形成所需要的凸缓形状。
整个成型过程中,凸台下的硅胶板要充满高压液体以保持均衡压力。
该过程的原理在于物理学中的伯努利原理。
泵抽出油液经过高压泵前经过油箱、空气旋流分离器、油箱回流阀,然后油液进入高压泵,在高压泵内部被压缩,经过高压泵出口进入高压阀体,进入行程液压泵中的柱塞式泵体,接着经过阀体,油液进入行程缸,以压力将成形件顶起并使之伸出打水滴状填充油囊的空间成形。
三、优点液态静压成型技术相对于传统的成型技术有如下的几个优点:1.变形效果好:该技术可以满足更复杂、精密、高强度的产品成型需求。
2.成型质量高:成型后的产品表面平整度好、无疤痕,无内部缺陷。
3.适用性广:该技术适用于各种类型的材料,比如金属、非金属、塑料等。
4.节约材料:该技术对材料的浪费较少,可以让生产成本更低。
液压成型

图1 空心异形截面零件引言液压成形技术同冲压,焊接等传统的成形技术相比,是一门新型的金属成形技术。
为了解决汽车,航空航天等领域的一些复杂的工艺问题和技术要求,从20世纪50年代起,德、美、日等国科学家在相关领域内先后提出了内高压成形技术和板料液压成形技术。
1985年我国科学家王仲仁教授发明了球形容器无模液压成形技术,提出了壳体液压成形技术。
近几年,依托于计算机控制技术和高压液压系统的发展,液压成形技术迅速发展。
目前,很多复杂结构的零件都可以通过该技术批量地加工生产。
一、液压成形技术的概述1.1 液压成形的定义和分类液压成形也称为液力成形是指利用液体作为传力介质或模具使工件成形的一种塑性加工技术。
按使用的液体介质不同,液压成形分为水压成型和油压成型;按使用的配料不同,液压成形分为管材液压成形,板料液压成形和壳体液压成形。
板料和壳体液压成形使用的成形压力较低,而管材液压成形使用的压力较高,又称为内高压成形,本文中称管材液压成形为内高压成形。
1.2 液压成形的特点现代液压成形技术的主要特点表现在两个方面:①液压成形技术仅需要凸模和凹模中的一个,或者不使用任何模具,这样可以省去一半,甚至不需要花费制造模具的费用和加工时间,而且液体作为凸模可以成形很多刚性凸模无法成形的复杂零件。
②液体作为传力介质具有实时可控性,通过液压闭环伺服系统和计算机控制系统可以按给定的曲线精确控制压力,确保工艺参数在设定的数值内,并且随时间可变可调,大大提高了工艺柔性。
二、内高压成形技术2.1 内高压成形技术的原理及分类内高压成形技术是用管材作为原材,通过对官腔内施加液体压力及在轴向施加负荷作用,使其在给定模具型腔内发生塑性变形,管壁与模具内表面贴合,从而得到所需形状零件的成形技术。
内高压成形技术主要可以整体成型轴线为二维或三维曲线的异形截面空心零件,从材料的初始圆截面可以成形为矩形,梯形,椭圆形或其他异形的封闭界面,如图1所示。
天锻“板材成形液压机柔性制造系统”通过验收
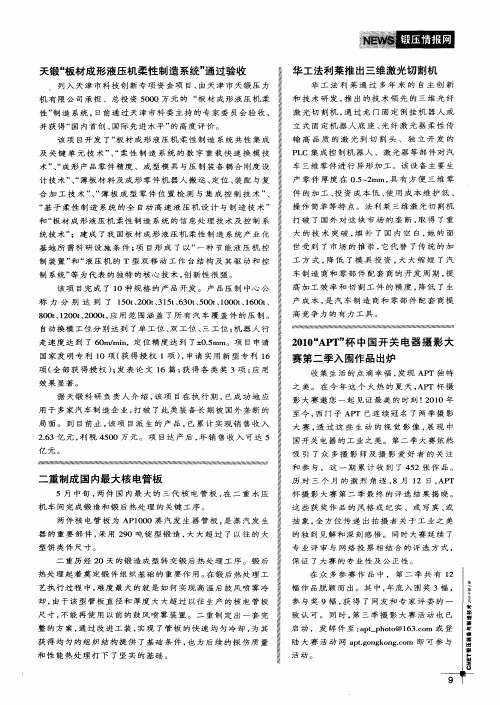
高竞 争力 的有 力工 具。
 ̄ lll lll l l llll ll lll lfl
自动 换 模 工 位 分 别 达 到 了 单 工 位 、 工 位 、 工 位 ; 器 人 行 双 三 机 走 速 度 达 到 了 6 m/ n 0 mi,定 位 精 度 达 到 了± .mm。项 目 申请 05
亿 元。
国 开 关 电器 的 工 业 之 美 。 第 二 季 大 赛 依 然
吸 引 了众 多 摄 影 师 及 摄 影 爱 好 者 的 关 注
和 参 与 , 这 一 期 累 计 收 到 了 4 2张 作 品 。 5
二重 制成 国 内最大核 电管板
5月 中 旬 , 件 国 内 最 大 的 三 代 核 电 管 板 , 二 重 水 压 两 在 机车 间完 成锻 造和锻 后 热处理 的关键 工序 。
打 破 了 国 外 对 这 块 市 场 的 垄 断 , 得 了 重 取
大 的 技 术 突 破 , 补 了 国 内 空 白 , 的 面 填 她
世 受 到 了 市 场 的 推 崇 , 代 替 了传 统 的 加 它
工 方 式 , 低 了 模 具 投 资 , 大 缩 短 了汽 降 大 车制 造 商 和零 部 件 配 套 商 的开 发周 期 , 提 高 加 工 效 率 和 切 割 工 件 的 精 度 , 低 了 生 降
P C集 成 控 制 机 器 人 、 激 光 器 等 部 件 对 汽 L 车 三 维 零 件 进 行 异 形 加 工 。该 设 备 主 要 生 产 零 件 厚 度 在 05 2 .~ mm, 有 方 便 三 维 零 具 件 的加 工 、 资 成本 低 、 用 成 本 维 护低 、 投 使 操 作 简 单 等 特 点 。 法 利 莱 三 维 激 光 切 割机
液压成形控制技术

形 压 力 一 般 在 6 MP '' 0 MP 0 a- 0 a范 围甚 至 更 高 , -2 成
别 通 过 粗一 细一 精 细 的滤 芯 进 行 过 滤 , 方 法 能 满 此 足 大 部 分 使用 要 求 , 需 要经 常清 洗 或 更换 滤 芯 。 但
工行业重要 制造技术之 一 , 国, 国, 美 德 日本 等发达 国
家均 已投入 大 量人 财物 力研 究 并 已经 投入 生产 或 试 生产 , 在其 它行 业 中的应用 也 不断扩 大 , 景十 分 它 前 广阔 。 目前 , 要 以板材 类和 管材类 如碳钢 、 主 不锈 钢 、 铜合金 、 铝合金 等为主 原料 。
的通道 ; 第二个用 途是堵 住金 属管 内 的液压 油 不让外 泄; 第三 个用途 是在成形 时推 动金 属管 向模 具 内移 动
1 引 言
液 压成 形 ( 也叫液 压胀形 ) 是最近 十 几年 来迅 速 发展起来 的一 门新 工艺 , 它一 出现 即受到制 造业 界 的 极大关注 而蓬勃发展 , 目前 已成 为 国外汽 车 、 船舶 、 轻
Hy r ul o mi n r l c n l g d a i F r ng Co to s Te h o o y c
W U a — u Xio y
艺 品和体育 用品等行 业 。缺 点是初 始投 资较大 , 制程
还 不太完 善, 大部分 生产 工 艺主要靠试 验总 结 。
( hn t r w sisttfrn ier g ein C i t e n t et tueo g ei s & a mid o h i e n nd g n
p e s r i r su e l o
液压成形
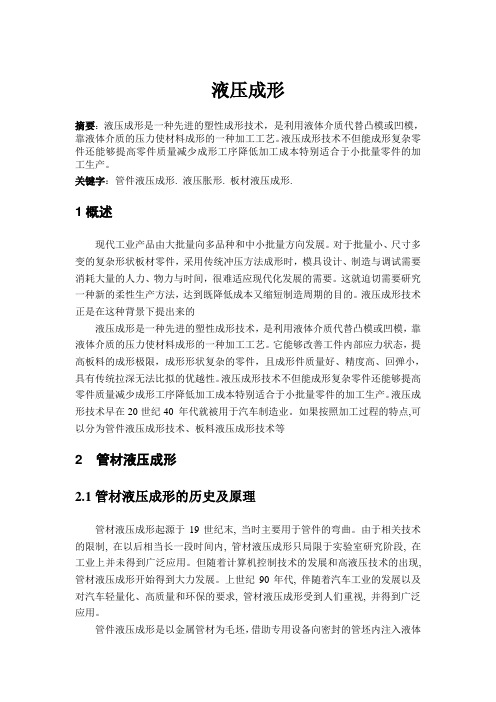
液压成形摘要:液压成形是一种先进的塑性成形技术,是利用液体介质代替凸模或凹模,靠液体介质的压力使材料成形的一种加工工艺。
液压成形技术不但能成形复杂零件还能够提高零件质量减少成形工序降低加工成本特别适合于小批量零件的加工生产。
关键字:管件液压成形. 液压胀形. 板材液压成形.1概述现代工业产品由大批量向多品种和中小批量方向发展。
对于批量小、尺寸多变的复杂形状板材零件,采用传统冲压方法成形时,模具设计、制造与调试需要消耗大量的人力、物力与时间,很难适应现代化发展的需要。
这就迫切需要研究一种新的柔性生产方法,达到既降低成本又缩短制造周期的目的。
液压成形技术正是在这种背景下提出来的液压成形是一种先进的塑性成形技术,是利用液体介质代替凸模或凹模,靠液体介质的压力使材料成形的一种加工工艺。
它能够改善工件内部应力状态,提高板料的成形极限,成形形状复杂的零件,且成形件质量好、精度高、回弹小,具有传统拉深无法比拟的优越性。
液压成形技术不但能成形复杂零件还能够提高零件质量减少成形工序降低加工成本特别适合于小批量零件的加工生产。
液压成形技术早在20世纪40 年代就被用于汽车制造业。
如果按照加工过程的特点,可以分为管件液压成形技术、板料液压成形技术等2 管材液压成形2.1管材液压成形的历史及原理管材液压成形起源于19世纪末, 当时主要用于管件的弯曲。
由于相关技术的限制, 在以后相当长一段时间内, 管材液压成形只局限于实验室研究阶段, 在工业上并未得到广泛应用。
但随着计算机控制技术的发展和高液压技术的出现,管材液压成形开始得到大力发展。
上世纪90年代, 伴随着汽车工业的发展以及对汽车轻量化、高质量和环保的要求, 管材液压成形受到人们重视, 并得到广泛应用。
管件液压成形是以金属管材为毛坯,借助专用设备向密封的管坯内注入液体介质,使其产生高压,同时还在管坯的两端施加轴向推力,进行补料,在两种外力的作用下,管坯材料塑性变形,并最终与模具型腔内壁贴合,得到形状与精度均符合技术要求的中空零件液压成形原理如图1 所示图1 管件液压成形原理示意图当零件轴线不是直线模腔分模面处截面小于管坯截面时,需进行弯管冲压等预工艺,以便管坯能顺利置入模腔中,如有必要,在液压成形之前还需进行退火处理2.2管材液压成形优点:与传统的冲压焊接工艺相比,管件液压成形工艺具有以下优点:(1 ) 减轻零件质量,节约材料; (2 ) 提高零件的强度和刚度,特别是疲劳强度; ( 3) 减少零件数量节约模具成本;(4) 零件整体成形,可减少后续机械加工和组装焊接量,简化生产流程,提高生产效率; (5) 提高加工精度,减少装配误差积累,可提高产品质量; (6)降低生产成本; (7) 结构形状设计更趋灵活优化。
5.请简述液压成型技术加工方法原理及其优点

请简述液压成型技术加工方法原理及其优点液压成型技术是一种高效、精确、适用范围广、成本低、环保的加工方法。
下面将分别从高效性、精度高、适用范围广、成本低、环保性等方面介绍液压成型技术的原理及其优点。
1.高效性液压成型技术采用液体作为传力介质,通过施加高压液体来传递成型力,使得生产效率大幅提高。
在生产过程中,由于液压成型可以连续进行,减少了模具更换和调试的时间,进一步缩短了生产周期。
此外,液压成型技术可以同时进行多个工件的加工,提高了生产效率。
2.精度高液压成型技术采用液体作为传力介质,通过控制液体的压力和流量,可以精确控制成型力,从而保证了制品的精度和一致性。
此外,液压成型技术的模具精度高,从而进一步提高了制品的精度和质量。
3.适用范围广液压成型技术适用于各种材料和复杂形状的制品加工。
对于不同材质和厚度的材料,可以通过调整液体的压力和模具的形状来满足加工要求。
此外,液压成型技术可以加工各种复杂形状的制品,如曲面、镂空等,适用范围非常广泛。
4.成本低液压成型技术采用液体作为传力介质,可以重复利用液体,降低了能源成本。
此外,液压成型技术的模具更换和调试时间短,减少了人工成本。
同时,液压成型技术可以同时进行多个工件的加工,提高了生产效率,进一步降低了生产成本。
5.环保性液压成型技术采用液体作为传力介质,与传统的机械加工方法相比,噪音污染和废弃物减少。
在生产过程中,液压成型技术可以控制液体的使用量,避免浪费和污染环境。
此外,液压成型技术的模具可以重复使用,减少了资源浪费,进一步体现了环保性。
综上所述,液压成型技术具有高效性、精度高、适用范围广、成本低、环保性等优点。
在现代化的加工制造业中,液压成型技术已经成为一种重要的加工方法,为提高生产效率、降低成本、保护环境等方面做出了积极的贡献。
讲一讲将板材“玩弄”于模具之中的液压成形技术
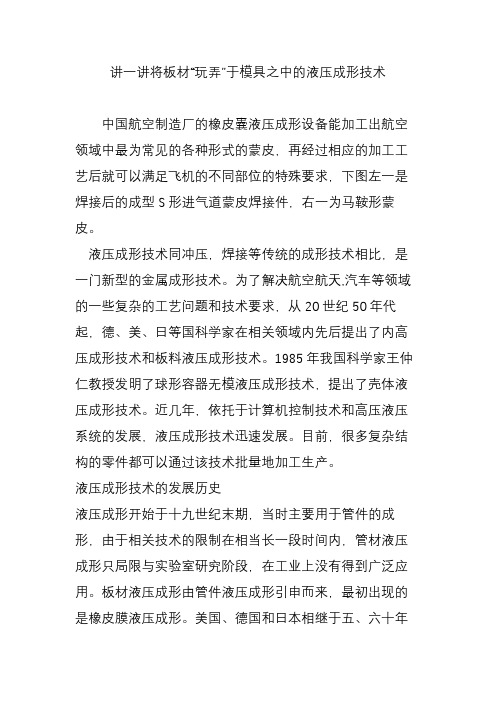
讲一讲将板材“玩弄”于模具之中的液压成形技术中国航空制造厂的橡皮囊液压成形设备能加工出航空领域中最为常见的各种形式的蒙皮,再经过相应的加工工艺后就可以满足飞机的不同部位的特殊要求,下图左一是焊接后的成型S形进气道蒙皮焊接件,右一为马鞍形蒙皮。
液压成形技术同冲压,焊接等传统的成形技术相比,是一门新型的金属成形技术。
为了解决航空航天,汽车等领域的一些复杂的工艺问题和技术要求,从20世纪50年代起,德、美、日等国科学家在相关领域内先后提出了内高压成形技术和板料液压成形技术。
1985年我国科学家王仲仁教授发明了球形容器无模液压成形技术,提出了壳体液压成形技术。
近几年,依托于计算机控制技术和高压液压系统的发展,液压成形技术迅速发展。
目前,很多复杂结构的零件都可以通过该技术批量地加工生产。
液压成形技术的发展历史液压成形开始于十九世纪末期,当时主要用于管件的成形,由于相关技术的限制在相当长一段时间内,管材液压成形只局限与实验室研究阶段,在工业上没有得到广泛应用。
板材液压成形由管件液压成形引申而来,最初出现的是橡皮膜液压成形。
美国、德国和日本相继于五、六十年代开发出了橡皮囊液压成形技术。
日本学者保日春男首先对此进行了改进,开发出了对向液压拉深技术。
随后欧、没等国家也相继开展这方面的工艺研究及设备的开发工作。
1967年,德国SMG公司提出液压机械拉深技术。
板材液压成形技术在九十年代后得到人们的重视和大力研究。
九十年代后,制造业迅猛发展,零件的形状日趋复杂,加之有大量采用铝、镁等质量较轻、但塑性较差的新材料,使得人们将注意力转向了板材液压成形技术。
到了九十年代后期,德国有关学者提出了一种板材成形新工艺--板材成对液压成形。
相对于国外来说,国内对于液压成形的研究较晚。
上世纪九十年代后,国内众多高校开始对液压成形进行研究,例如哈尔滨工业大学、燕山大学、华南理工大学、上海交通大学等分别对液压成形进行了理论分析和实验研究,总结了很多液压成形的数据和经验,但是对板材成对液压成形的研究相对较少,处于最初的探索阶段。
液压成形原理

液压成形原理
嘿,朋友!今天咱就来好好唠唠液压成形原理!
你想想看啊,液压成形就像是一场力量与智慧的舞蹈。
比如说,我们要把一块金属板材变成一个特定形状的部件,这就好像是要给这块金属施魔法一样!液压系统就像一个大力士,它能产生巨大的压力,推动着金属板材按照我们想要的样子变形。
就好比你要做一个超级酷的飞机模型,液压成形就是那个能帮你把一片片零件塑造成完美形状的神奇工具。
你知道吗?在这个过程中,液体就像是一群听话的小士兵,听从液压系统这个指挥官的命令。
当压力施加到液体上时,它们就齐心协力地去推动金属板材。
这多神奇啊!如果没有液压成形,那我们生活中的好多东西都没法制造出来呢!
再比如说汽车的零部件吧,那些复杂的形状,可不就是靠液压成形弄出来的嘛!它可比我们手工敲敲打打厉害多啦!
哎呀呀,我跟你说,液压成形的应用可太广泛了!从航空航天到日常生活用品,到处都有它的身影。
它不就是那个默默奉献,却让我们的生活变得更美好的幕后英雄吗?
我觉得啊,液压成形真的是超级厉害的技术,它让我们能制造出各种各样复杂又精美的东西,丰富了我们的生活!真的值得我们好好去了解和研究它呀!。
更具竞争力的液压成形技术

更具竞争力的液压成形技术与传统的冲压工艺相比,液压成形工艺在减轻重量、减少零件数量和模具数量、提高刚度与强度、降低生产成本等方面具有明显的技术和经济优势,在工业领域尤其是汽车工业中得到了越来越多的应用。
在汽车工业及航空、航天等领域,减轻结构质量以节约运行中的能量是人们长期追求的目标,也是先进制造技术发展的趋势之一。
液压成形(hydroforming)就是为实现结构轻量化的一种先进制造技术。
液压成形也被称为“内高压成形”,它的基本原理是以管材作为坯料,在管材内部施加超高压液体同时,对管坯的两端施加轴向推力,进行补料。
在两种外力的共同作用下,管坯材料发生塑性变形,并最终与模具型腔内壁贴合,得到形状与精度均符合技术要求的中空零件。
液压成形技术的优点对于空心变截面结构件,传统的制造工艺是先冲压成形两个半片,然后再焊接成整体,而液压成形则可以一次整体成形沿构件截面有变化的空心结构件。
与冲压焊接工艺相比,液压成形技术和工艺有以下主要优点:□ 减轻质量,节约材料。
对于汽车发动机托架、散热器支架等典型零件,液压成形件比冲压件减轻20%~40%;对于空心阶梯轴类零件,可以减轻40%~50%的重量。
□ 减少零件和模具数量,降低模具费用。
液压成形件通常只需要1套模具,而冲压件大多需要多套模具。
液压成形的发动机托架零件由6个减少到1个,散热器支架零件由17个减少到10个。
□ 可减少后续机械加工和组装的焊接量。
以散热器支架为例,散热面积增加43%,焊点由174个减少到20个,工序由13道减少到6道,生产率提高66%。
□ 提高强度与刚度,尤其是疲劳强度,如液压成形的散热器支架,其刚度在垂直方向可提高39%,水平方向可提高50%。
□ 降低生产成本。
根据对已应用液压成形零件的统计分析,液压成形件的生产成本比冲压件平均降低15%~20%,模具费用降低20%~30%。
图1为采用液压成形技术制造的欧宝发动机托架零件与传统冲压件的比较,其零件重量降低了30%,模具费用降低了60%,零件的生产成本降低了20%。
液压成型技术

板材液压成型
板材液压成型是利用液体作为传力介质来传递载荷, 使板材成型到单侧模具上的一种板材成型方法。 根据液体介质取代凹模或凸模可将之进一步分为: 1.充液拉深(用液体介质代替凹模)。 2.液体凸模拉深(以液体介质作为凸模)。
充液拉深
热态充液拉深,将材料的温热性能与充液拉深的技术 优势结合起来,可使铝合金及镁合金等成型性能差的 轻体材料成型能力得到提高,促进其在航空航天领域 的应用。
液压成型技术的现状
管材液压成型 现代液压成型压力一般达到400MPa,有时可达到 1000MPa。超高压精度达到0.2-0.5MPa,位移精度 达到0.5MPa。,现在已广泛应用到汽车、航空、自 行车、管路等当中,其中汽车应用最为广泛。 包括: 1.底盘类零件:副车架、纵梁、后轴、保险杠 2.车体结构:座椅框、仪表盘支梁、顶梁等 3.发动机和驱动系统:排气管凸轮轴 4.转向和悬挂系统:控制臂、摆臂等
管材成型工艺
它的成型工艺大致可分为三个阶段:第一个
阶段,填充阶段,将管材放在下模内,然后 闭合上模,使管材内充满液体(并排除气 体),将管的两端用水平冲头压封;第二个 阶段,成型阶段对管内液体加压胀型的同时 两端的冲头按照设定加载曲线向内推进补料, 在内压和轴向补料的联合作用下使管材基本 贴近模具;第三个阶段,整型阶段,提高压 力使过度区圆角完全贴靠模具而成型为所需 的工件,这个阶段基本没有补料,从截面看 可以把管材变为矩型、梯型、椭圆型或其他 异型截面。
液压成型技术的发展趋势
随着液压成型技术的成熟和人们都减轻质量,降低成本的需求的提高,该技术 近十年来在各个领域得到广泛应用。 板材液压成型: 1.进一步提高成型极限和零件质量的成型新技术。 2.低塑性材料的拉深成型。 3.大型复杂型面零件成型 4.与普通拉深工艺复合,提高效率 壳体液压成型: 1. 选用轻质传力介质 2. 应用高能束焊接技术和自动化工艺焊接封闭壳体 3. 铝合金等轻质材料球壳液压成型 管材液压成型: 1.超高压成型 2.新成形工艺不断发展 3. 超高强度钢成型 4. 热态内压成型
曲面板材零件液压成形技术解读

曲面板材零件液压成形技术来源:作者:发布时间:2008-12-20针对传统板材冲压成形中存在的成形极限低、模具型腔复杂,以及零件表面品质差等缺点,发展了板材液压成形技术。
其基本原理是采用液体作为传力介质以代替刚性的凸模或凹模来传递载荷,使坯料在液体压力作用下贴靠凹模或凸模,从而实现金属板材零件的成形。
自从该技术推出以来,在航空航天及汽车领域不断获得应用,特别适于结构形状复杂的零件及冷成形性能差的材料成形,如铝合金、高强钢、高温合金以及拼焊板等。
板材液压成形技术现也日渐成为国内外业界的研究热点,并产生了可控径向加压充液拉深技术及液体凸模拉深成形新技术。
板材液压成形原理及分类板材液压成形是利用液体作为传力介质来传递载荷,使板材成形到单侧模具上的一种板材成形方法,根据液体介质取代凹模或凸模可将之进一步分类为充液拉深成形和液体凸模拉深成形。
前者(图1)是用液体介质代替凹模传递载荷,液压则作为辅助成形的手段,可减小普通拉深成形中凸、凹模之间坯料的悬空区,使该部分坯料紧贴凸模,零件形状尺寸最终靠凸模来保证。
图1 充液拉深成形原理充液拉深成形中的液压作用形成了坯料与凸模之间的摩擦保持效果,提高了凸模圆角区板料的承载能力,抑制坯料减薄和开裂,可有效提高成形极限、减少成形道次。
同时,液体从坯料与凹模上表面间溢出可形成流体润滑,促进外围板材进入凹模,缓解了零件表面的划伤。
这一成形技术因其独特优势在国际上受到普遍重视,发展出主动背压(预胀)拉深法,其过程是预先胀形,然后拉深,通过预先胀形达到变形硬化的效果。
液体凸模拉深成形(图2)则是以液体介质代替凸模传递载荷,液压作为主驱动力使坯料变形,坯料法兰区逐渐流入凹模,最终在高压作用下使坯料贴靠凹模型腔,零件形状尺寸靠凹模来保证。
这一成形法通过合理控制压边力可使坯料产生拉-胀成形,应变硬化可提高曲面薄壳零件的刚性、压曲抗力和抗冲击能力。
因此,它非常适于铝合金和高强钢等轻合金板料形状复杂(特别是局部带有小圆角)、深度较浅的零件成形。
液压成型工艺技术
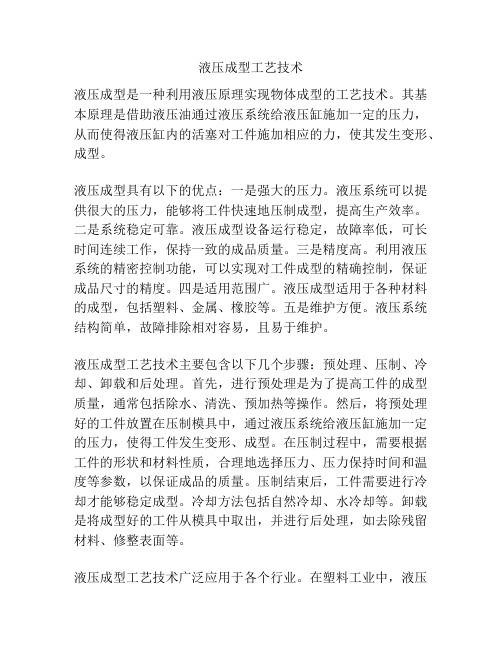
液压成型工艺技术液压成型是一种利用液压原理实现物体成型的工艺技术。
其基本原理是借助液压油通过液压系统给液压缸施加一定的压力,从而使得液压缸内的活塞对工件施加相应的力,使其发生变形、成型。
液压成型具有以下的优点:一是强大的压力。
液压系统可以提供很大的压力,能够将工件快速地压制成型,提高生产效率。
二是系统稳定可靠。
液压成型设备运行稳定,故障率低,可长时间连续工作,保持一致的成品质量。
三是精度高。
利用液压系统的精密控制功能,可以实现对工件成型的精确控制,保证成品尺寸的精度。
四是适用范围广。
液压成型适用于各种材料的成型,包括塑料、金属、橡胶等。
五是维护方便。
液压系统结构简单,故障排除相对容易,且易于维护。
液压成型工艺技术主要包含以下几个步骤:预处理、压制、冷却、卸载和后处理。
首先,进行预处理是为了提高工件的成型质量,通常包括除水、清洗、预加热等操作。
然后,将预处理好的工件放置在压制模具中,通过液压系统给液压缸施加一定的压力,使得工件发生变形、成型。
在压制过程中,需要根据工件的形状和材料性质,合理地选择压力、压力保持时间和温度等参数,以保证成品的质量。
压制结束后,工件需要进行冷却才能够稳定成型。
冷却方法包括自然冷却、水冷却等。
卸载是将成型好的工件从模具中取出,并进行后处理,如去除残留材料、修整表面等。
液压成型工艺技术广泛应用于各个行业。
在塑料工业中,液压成型被用于各种塑料制品的生产,如塑料瓶、塑料管道等。
在金属加工行业中,液压成型被用于金属板的冲压成型、弯曲成型等。
在橡胶工业中,液压成型被用于橡胶制品的成型,如橡胶管、橡胶密封垫等。
此外,液压成型还可以应用于汽车工业、航空航天工业、造船工业等领域。
总之,液压成型工艺技术是一种广泛应用于各个行业的成型技术,其具有强大的压力、稳定可靠、精度高、适用范围广、维护方便等优点。
通过合理使用液压成型工艺技术,可以实现对各种材料的高质量成型,提高生产效率,降低生产成本。
液压成形技术
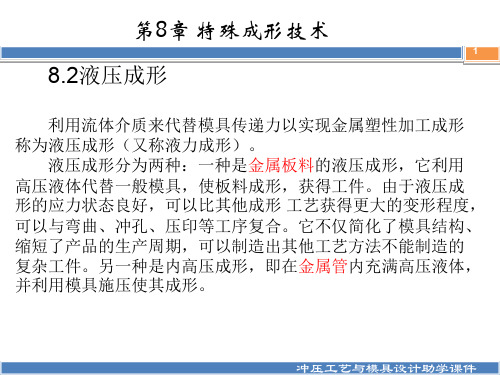
屈曲:当管材成形区长度过长,在成形初期还没有在管材 内建立起足够大的内压时,施加了过大的轴向力造成的。
皱纹:当轴向力过大时,工件在成形初期产生皱纹 。 皱纹可以分为二类,一类是后期加压整形无法展平,这类 皱纹称为死皱,它是一种缺陷。 另一类皱纹通过后期加压可 以展平,称为“有益皱纹”。这类皱纹不仅不是缺陷而且还可 作为一种预成形的手段,在成形初期将管材推出皱纹以补充材 料。但前提条件是后续整形压力能将皱纹展开。
有缘学习更多+谓ygd3076考证资料或关注桃报:奉献教育(店铺)
冲压工艺与模具设计助学课件
第8章 特殊成形技术
13
4.内高压成形设备 一条完整的内高压成形生产线主要由切管机、弯管机、预
成型压力机、内高压成形压力机等设备组成。其中最重要的设 备是内高压成形压力机, 它由合模压力机、高压源、水平缸、液 压泵站、水压系统和计算机控制系统等6部分组成, 其组成和工 作原理如图8-13和图8-14所示。
内高压成形工艺作为一种整体成形薄壁结构件的塑性加工方 法,最近几十年在汽车制造业、航空航天业及卫生洁具业中得到 了广泛的应用。
a)轿车副车架(有18个不同的截面形状和尺寸)
b) 排气歧管
图8-10典型汽车内高压成形零件
冲压工艺与模具设计助学课件
有缘学习更多+谓ygd3076考证资料或关注桃报:奉献教育(店铺)
根据受力和变形特点, 零件分为成形区和送料区2个区间。成 形区是管材发生塑性变形直径和形状发生变化的部分,送料区是 在模具内限制管材外径不变, 主要作用是向成形区补充材料。
冲压工艺与模具设计助学课件
第8章 特殊成形技术
10
板材液压成型

1.板材液压成形技术种类2011-12-13 16:12:18| 分类:试验机技术| 标签:板材液压成形|字号大中小订阅1.板材液压成形技术种类板材液压成形是采用液体做为传力介质使金属板材成为所需的形状曲面零件的成形工艺。
根据液体介质作用位置不同,板材液压成形可以分为充液拉深成形技术和液体凸模拉深成形技术。
充液拉深成形中液体作用在板材背面或凹模一侧使板材贴靠凸模,其原理如图1中右侧部分所示(左侧是普通拉深的示意图)。
充液拉深中首先将液体介质充满充液室,在凹模表面上放好板材,施加压边力;然后凸模开始压入充液室,此时依靠凸模压入自然增压或者通过液压系统使充液室的液体介质建立起压力将板材压靠在凸模上,同时液体沿板材法兰区下表面向外流出形成流体润滑,直至成形结束。
充液拉深与普通拉深工艺(图1左侧)的显著不同是板材背面存在液体压力使板材与凸模之间产生摩擦力Ff和在法兰区存在润滑油膜,如图2所示。
充液室压力或背压越大,摩擦力越大,该摩擦力有利于提高成形极限,又称为有益摩擦。
在充液室压力达到某一临界值时,液体压力作用使板材法兰区脱离凹模,形成一个润滑油膜,消除板材与凹模圆角之间的摩擦。
在没有密封的情况下(图2a),充液室内液体介质强行从法兰与凹模之间流出,在整个法兰区形成流体润滑,从而有效降低法兰与凹模间的摩擦,缺点是无法精确控制充液室压力。
如果采用密封(图2b),液体介质无法从法兰区流出,不能在全部法兰区形成流体润滑,但却可以通过溢流阀精确控制充液室压力。
图1 充液拉深成形原理(a) 无密封况(b) 有密封图2 充液拉深的有益摩擦与流体润滑在充液拉深基础上, 本中心发明了可控径向加压充液拉深成形技术,原理如图3所示。
该技术是在充液拉深的基础上,再施加独立于充液室压力的可控径向压力pr,来推动法兰区材料的向内流动,进一步提高成形极限。
对于低塑性材料的锥面、球面、抛物线母线零件和锥盒形零件,过大的充液室压力会导致曲面零件成形初期悬空区的破裂和锥盒形零件棱边角部起皱,因此采用普通充液拉深制造低塑性材料大高径比零件仍然困难。
壳体液压成形技术
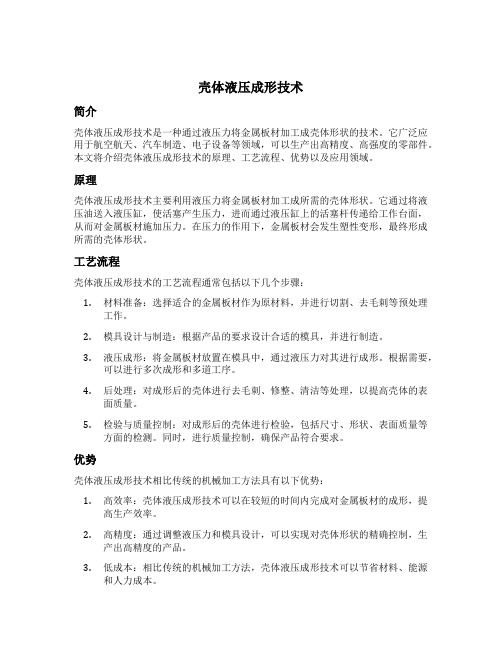
壳体液压成形技术简介壳体液压成形技术是一种通过液压力将金属板材加工成壳体形状的技术。
它广泛应用于航空航天、汽车制造、电子设备等领域,可以生产出高精度、高强度的零部件。
本文将介绍壳体液压成形技术的原理、工艺流程、优势以及应用领域。
原理壳体液压成形技术主要利用液压力将金属板材加工成所需的壳体形状。
它通过将液压油送入液压缸,使活塞产生压力,进而通过液压缸上的活塞杆传递给工作台面,从而对金属板材施加压力。
在压力的作用下,金属板材会发生塑性变形,最终形成所需的壳体形状。
工艺流程壳体液压成形技术的工艺流程通常包括以下几个步骤:1.材料准备:选择适合的金属板材作为原材料,并进行切割、去毛刺等预处理工作。
2.模具设计与制造:根据产品的要求设计合适的模具,并进行制造。
3.液压成形:将金属板材放置在模具中,通过液压力对其进行成形。
根据需要,可以进行多次成形和多道工序。
4.后处理:对成形后的壳体进行去毛刺、修整、清洁等处理,以提高壳体的表面质量。
5.检验与质量控制:对成形后的壳体进行检验,包括尺寸、形状、表面质量等方面的检测。
同时,进行质量控制,确保产品符合要求。
优势壳体液压成形技术相比传统的机械加工方法具有以下优势:1.高效率:壳体液压成形技术可以在较短的时间内完成对金属板材的成形,提高生产效率。
2.高精度:通过调整液压力和模具设计,可以实现对壳体形状的精确控制,生产出高精度的产品。
3.低成本:相比传统的机械加工方法,壳体液压成形技术可以节省材料、能源和人力成本。
4.强度高:由于壳体液压成形技术可以使金属板材发生塑性变形,从而提高了产品的强度和刚度。
应用领域壳体液压成形技术广泛应用于以下领域:1.航空航天:壳体液压成形技术可以用于制造飞机、火箭等航空航天器的壳体结构,满足轻量化和高强度的要求。
2.汽车制造:壳体液压成形技术可以用于汽车车身、车门、引擎罩等零部件的制造,提高产品的强度和安全性。
3.电子设备:壳体液压成形技术可以用于制造电子设备外壳、散热器等部件,提高产品的外观质量和散热性能。
板材成形加工的新技术与发展趋势
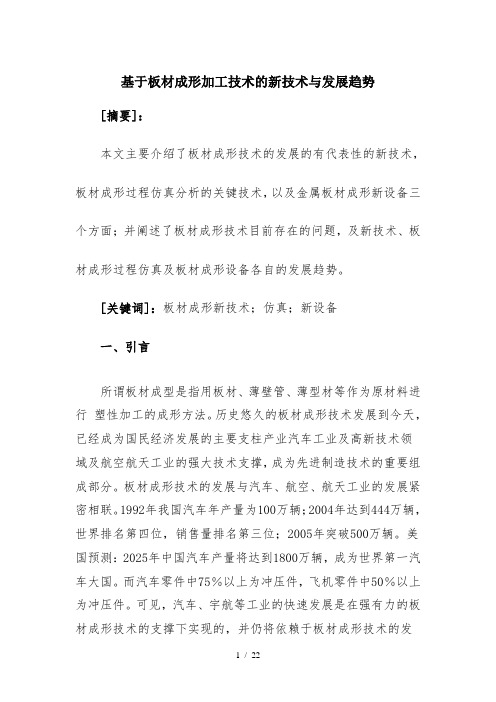
基于板材成形加工技术的新技术与发展趋势[摘要]:本文主要介绍了板材成形技术的发展的有代表性的新技术,板材成形过程仿真分析的关键技术,以及金属板材成形新设备三个方面;并阐述了板材成形技术目前存在的问题,及新技术、板材成形过程仿真及板材成形设备各自的发展趋势。
[关键词]:板材成形新技术;仿真;新设备一、引言所谓板材成型是指用板材、薄壁管、薄型材等作为原材料进行塑性加工的成形方法。
历史悠久的板材成形技术发展到今天,已经成为国民经济发展的主要支柱产业汽车工业及高新技术领域及航空航天工业的强大技术支撑,成为先进制造技术的重要组成部分。
板材成形技术的发展与汽车、航空、航天工业的发展紧密相联。
1992年我国汽车年产量为100万辆;2004年达到444万辆,世界排名第四位,销售量排名第三位;2005年突破500万辆。
美国预测:2025年中国汽车产量将达到1800万辆,成为世界第一汽车大国。
而汽车零件中75%以上为冲压件,飞机零件中50%以上为冲压件。
可见,汽车、宇航等工业的快速发展是在强有力的板材成形技术的支撑下实现的,并仍将依赖于板材成形技术的发展。
板材成形技术的发展与产品需求息息相关,正是面临着汽车产量的迅猛增长和宇航飞行器性能不断提升的挑战,才促使板材成形技术取得长足进步。
汽车更新换代的频繁化强烈要求缩短研发周期,这就加速了CAD/CAM/CAE/CAPP等计算机辅助技术在工艺分析和模具制造中的应用,并加速了汽车制造业的科学化、数字化和信息化进程。
强烈的市场需求和学科交叉催生了板材成形新工艺、新技术,使板材成形这一传统学科焕发了新的活力。
板材成形过程的计算机仿真实质上就是利用数字模拟技术分析给定模具和工艺方案所冲压的零件变形的全过程,从而判断模具和工艺方案的合理性。
每一次仿真就相当于一次试模的过程。
因此成熟的仿真技术不仅可以减少试模次数,在一定条件下还可使模具和工艺设计一次合格从而避免修模。
仿真技术的应用可大大缩短新产品开发周期,降低开发成本,提高产品品质和市场竞争力。
板材逐渐成形装备的技术创新与知识产权保护研究

板材逐渐成形装备的技术创新与知识产权保护研究近年来,随着工业化进程的不断推进,板材逐渐成形装备在制造业中的应用逐渐扩大。
随之而来的技术创新和知识产权保护问题也逐渐受到关注。
旨在推动制造业发展,保护创新成果,提高企业竞争力,技术创新和知识产权保护成为了板材逐渐成形装备行业所面临的重要议题。
本文将着重探讨板材逐渐成形装备的技术创新和知识产权保护,并提出相应的研究建议。
一、板材逐渐成形装备的技术创新板材逐渐成形装备是一种利用机械和热力等手段,对板材进行逐渐成形的制造工艺。
它逐渐取代了传统的局部成形工艺,能够大幅提高生产效率和产品质量。
然而,板材逐渐成形装备的技术创新面临着一些挑战。
首先,需要不断改进成形工艺和设备。
板材逐渐成形装备需要具备高精度、高效率和高可靠性的特点。
因此,研发新的成形工艺和设备是技术创新的重要内容。
例如,引入先进的数值模拟技术和控制技术,优化成形工艺参数,提高生产效率和质量。
其次,需要加强材料研发和应用。
板材逐渐成形工艺对材料的性能要求越来越高。
因此,研发具有高强度、高韧性和高耐磨性的新材料是技术创新的关键。
此外,通过合理设计复合材料和智能材料,可以进一步提升板材逐渐成形装备的性能。
另外,需要加强先进制造技术与信息技术的融合应用。
随着“工业4.0”时代的到来,先进制造技术和信息技术之间的融合应用将为板材逐渐成形装备的技术创新提供新的机遇。
例如,通过物联网技术实现设备之间的智能互联和远程监控,可以提高生产线的灵活性和智能化程度。
二、板材逐渐成形装备的知识产权保护知识产权保护是推动技术创新和鼓励创新投资的重要手段。
在板材逐渐成形装备行业,保护技术创新成果和知识产权具有重要意义。
首先,需要完善知识产权法律制度。
加强知识产权保护必须建立在健全的法律制度基础之上。
政府应加大对知识产权法律法规的制定和修订力度,提高保护力度和处罚力度,为企业提供更加稳定和可靠的知识产权保护环境。
其次,需要加强知识产权保护意识和能力建设。
板材液压成形专利技术综述

研究方向:金属铸造及热处理领域的发明专利实质审查工作。(等同于第一作者)
Copyright©博看网 . All Rights Reserved.
·78·
板材液压成形专利技术综述
成形技术在中国的专利申请量出现了大幅度增长,并在 2010 年之后几年内均超越了全球专利申请量[1]。
第8期
图 3 液压成形技术在全球申请量分布
图 1 板材液压成形申请量分布
2.2 国内外重要申请人比较 2.2.1 国内重要申请人 如图 2 所示,国内申请量最高的申请人是哈尔滨工 业大学,其次是福特环球技术公司和北京航空航天大学, 可以看出国内的液压成形技术研究主要集中在高校。并 且由于国外技术发展成熟,并且为了涉足中国这个巨大 的市场,很多国外公司纷纷来华申请,如福特环球技术公 司,其从 2008-2014 年期间连续都有在华申请。然而,从 申请人统计结果中可以看出,国内公司申请量较少,表明 液压成形技术在产业中的应用并不多,这可能是由于技 术掌握不够成熟、设备制造难、成形精度差、未带来显著 的经济效益等多方面原因造成的[2]。
技术的发展提,从 1990 年开始,液
1 专利数据来源
压成形技术在国外申请量突飞猛进,并且在长达 15 年内 一直保持较高水平。
板材液压成形专利文献样本选自中国专利文摘数据
由于技术封闭,国内一直到 1987 年左右才开始对液
库(CNABS)和德温特世界专利库(DWPI)。以专利申请时 间为对象,从 1965 年开始统计,至 2014 年为止。在中国专 利文摘数据库中,采用板材液压成形的分类号 B21D26/
随着成形设备及相关控制技术的发展,以流体作传 类号检索并合并之后获得 525 篇专利,经过筛选后选择其
力介质的液压成形技术在国外发展迅速,广泛应用在汽 中的 425 篇并将其作为外文专利分析对象。
- 1、下载文档前请自行甄别文档内容的完整性,平台不提供额外的编辑、内容补充、找答案等附加服务。
- 2、"仅部分预览"的文档,不可在线预览部分如存在完整性等问题,可反馈申请退款(可完整预览的文档不适用该条件!)。
- 3、如文档侵犯您的权益,请联系客服反馈,我们会尽快为您处理(人工客服工作时间:9:00-18:30)。
文章编号:036726234(2000)0420007203板材零件成对液压成形新技术张士宏1,许 沂1,王忠堂1,郎利辉2,刘 钢2(1.中国科学院金属研究所,辽宁沈阳110015;2.哈尔滨工业大学材料学院,黑龙江哈尔滨150001)摘 要:板材成对液压成形技术是一种新的板材成形技术,具有成形性好、制造工期短、费用低等优点,特别适用于批量小、形状复杂板材零件的生产.介绍了板材成对液压成形技术的成形原理、成形过程、分类及研究现状.关键词:板料成形;液压成形;成形控制;胀形;拉深中图分类号:TG 394 文献标识码:AH ydroforming of sheet metal in pairsZH ANG Shi 2hong 1,X U Y i 1,W ANG Zhong 2tang 1,LANGLI 2hui 2,LI U G ang 2(1.Institute of Metal Research ,Chinese Academy of Sciences ,Shenyang 110015,China ;2.School of Materials Science and Engineering ,Harbin Institute of T echnology ,Harbin 150001,China )Abstract :Hydroforming of sheet metal in pairs is a new sheet metal forming process.With many advantages such as g ood formability ,short manufacturing cycle and lower cost ,and especially suitable for producing sheet metal parts with com plicated shapes in small batches.K ey w ords :sheet metal forming ;hydroforming ;in process control ;bulging ;deep drawing 随着现代工业的发展,产品品种越来越多,更新速度越来越快,由大批量向多品种和中小批量方向发展.制造业中常见的批量小、尺寸多变的复杂形状板材零件,采用传统冲压方法成形时,难度大,造价高,模具的设计制造与调试需要大量时间与人力物力.而采用手工钣金成形方法,虽然成本降低,但周期太长,质量也不易满足要求.这就迫切需要新的柔性生产方法,达到既降低成本又缩短制造周期的目的.于是,各种柔性化的塑性加工技术应运而生,液压成形工艺,近几年来得到了迅速发展.传统的液压成形法(Hydroforming )[1]有一定柔性和优点,已经小规模用于汽车、飞机零件成形和收稿日期:2000-03-10基金项目:中国科学院引进国外杰出人才基金资助项目、黑龙江省留学回国基金资助项目(L99-1)作者简介:张士宏(1962-),男,教授.其他制造业中.但这种工艺还有不少问题,例如压边不易控制,橡胶经常损坏,成形质量不稳定,已部分地被后来发展起来的充液拉深(Hydrome 2chanical deep drawing )工艺[2]所代替.充液拉深工艺的模具结构与传统冲压相似,采用刚性压边,不同的是凹模被液压腔取代,与液压成形法相比,橡胶膜被取消,可以将传统工艺的板料成形极限由1.8提高到2.7,生产效率也得到提高,适于批量生产.但该工艺型腔制造较难,灵活性不够.近年来由于汽车和飞机制造业的轻量化、高质量和环保要求,对柔性成形法的需求显著增加,又由于液压密封技术取得重要突破,使高内压液压胀形成为可能,很多管件和框架类零件可由高内压法成形,目前欧、美、日等国的企业和大学正集中力量研究高内压胀管技术[1,2].德国90年代提出了一种板料零件成形新工艺———板料零件成对液胀成形(Hydroforming of sheet metal pairs )[3~6],这种成形属内高压成形,因此又称为板材内高压成形,第32卷 第4期 哈 尔 滨 工 业 大 学 学 报 V ol.32,N o.42000年8月 JOURNA L OF H ARBI N I NSTIT UTE OF TECH NO LOGY Aug.,2000简称H BU 成形(H ochdruck -Blech -Um formung ).本项目组在此基础上进行了改进,提出了可替换凹模的思想,并研制了卧式和立式两种模具装置.1 板料零件成对液压成形的工艺原理与特点 板料零件成对液压成形时,首先将叠放的两块平板毛坯放置在上下凹模上,压边后充液预成形,边缘切割,对边缘采用激光焊接技术焊接.然后,在两板间充液加压进行最终校形,其过程示意图见图1.这种工艺适于成形舱体零件,将零件的焊接加工安排在成形过程中间.首先,通过焊接实现了两板间的密封,以保证高内压力,完成最后的贴模过程;另外,成形过程中,两板的定位准确,此时进行焊接可保证零件的精确配合,同时节省了焊接用的工装,另外,通过最后的校形可消除焊接引起的变形.根据零件的几何形状的不同,焊接工序可安排在成形前或如上述预成形之后.这种成形需要配套的焊接设备(激光焊和氩弧焊),设备工装较为复杂.图1 周边焊接坯料成对液压成形工艺过程Fig.1 Hydroforming of welded sheet metal pairs 对于非焊接成对液压成形,其过程是仅将两块平板毛坯放置在上下凹模上,压边后直接充液至最终贴模成形.这种方法成形时,两板料直接接触,在法兰区两板间存在摩擦,一板的拉入将对另一板产生影响,但影响不大,其大小决定于两板间的摩擦情况.当上下两板具有不同成形形状和厚度时,可以较自由的成形,但是两板间充液机构的设置较困难.德国学者还提出了一种有中间加压板的无焊缝对胀成形新工艺,其工艺过程见图2.这种工艺由于采用了中间加压板(有加压管路与外部压力泵相连接,同时也通往上下凹模腔),使上下两板料不再直接接触,两板的变形不再相互影响,实际上两板独立成形.这种成形技术是一种软凸模成形技术,具有很好的柔性,与一般的成形工艺相比可减少模具数量.因采用液压加载,模具不易损坏,寿命提高.该技术采用液压法成形,产品与模具贴合程度好,零件冻结性好,因此质量好,弹复变形小,通过高压塑性变形使残余应力接近完全消除,板材成形极限可明显超过拉深工艺和纯液压胀形工艺.这种工艺技术尤其适用于形状复杂、尺寸多变、批量不大的大型板料零件的生产,一次成形可生产一对产品,使复杂形状板材零件的生产简单化.与常规板材成形工艺相比,模具费用可降低30%以上.对于小批量生产,可节约费用35%,生产研制周期可缩短30%.在航空航天、汽车等工业部门,采用此法研制新产品可以节约模具费用,缩短研制及生产周期.图2 有中间压板的板料成对液压成形工艺Fig.2 Hydroforming of sheet metal pairs with intermediate plate2 研究现状板料对胀成形时,坯料在流体压力载荷的作用下产生拉伸变形,同时法兰边向模腔内流动(拉深变形),即板料发生胀形-拉深复合塑性变形,压边力与液体压力需要恰当合理的匹配,以避免坯料在变形时发生法兰起皱、悬空区拉裂及局部减薄过量等工艺缺陷.图3为非焊接板料对胀成形的加载区间示意图[3],其中A 区为压边力过低漏油区,B 为拉深-胀形复合变形区,C 为单纯胀形区,D 为破裂区.・8・ 哈 尔 滨 工 业 大 学 学 报 第32卷图3 加载区间图Fig.3 Diagram of loading 对于不同材料的板料,在不同条件下的加载区间可通过实验或计算方法确定.实际的成形工艺过程中,因为成形装置的限制,压边力的实时控制还很难实现,难以按照最佳加载路径进行.因此,迫切需要开发智能化的成形装置.目前,德国这种新工艺还处于实验室研究阶段,他们在工艺装置和理论研究方面已取得了一些研究成果,并采用计算机模拟对其成形过程进行了初步分析.关于坯料的成形机理和工艺缺陷形成机制还没有发表更详细的结果,工装结构还需要改进和创新.本课题组在充分考察研究国际板材成形先进技术的基础上,对压边机构和凹模结构进行了改进,提出可替换凹模结构,以提高本工艺的柔性和适应性,实验研究工作正在进行中.该工艺采用的装置由一块中间加压板(有加压管路与外部压力泵相连接,同时也通往上下凹模腔)、上下压边圈和上下镶嵌式凹模组成.针对不同零件,凹模尺寸、形状可在一定范围内改变,凹模材料可根据成形板料的材质、精度和批量选择金属、树脂、石膏、木材或水泥.零件成形时先将两张板材坯料分别置于中间加压板上下或两侧,然后闭合压边圈,利用压力泵充液加压,板材坯料在液体压力作用下,同时伴随一定的压边区拉入(拉深),发生胀形-拉深复合塑性变形,直至最终贴模,从而得到所需的板材零件.3 结束语在国际市场竞争日益激烈的态势下,发展柔性塑性加工技术以利于及时对产品的更新换代做出响应是先进塑性加工技术的重要发展趋势之一,板料成对液压成形技术正是在这一趋势下提出的塑性加工新工艺.板料成对液压成形技术具有很好的柔性,尤其适用于形状复杂、尺寸多变、批量不大的大型板料零件的生产,使复杂形状板材零件的生产简单化、柔性化,实现零件的快速制造.在航空航天、航空、汽车、电器等工业部门,采用此法研制新产品可节约模具费用,缩短生产及研制周期,提高企业竞争力,因而具有广阔的应用前景.参考文献[1]ZH ANG Shihong.Developments in hydroforming[J].J ofMaterials Processing T echnology,1999,91:2362244. [2]ZH ANG Shihong,DANCKERT J.Development of hy2dromechanical deep drawing[J].J of Materials ProcessingT echnology,1998,83:14225.[3]GEIGER M,V oollertsen,HEI N P.Hydroforming of sheetmetal pairs//.Proceedings of SheMet’98[C].[s.l.]:[s.n.],1998.37251.[4]K LEI NER M,K O LLECK R,RAUER J,et al.Die2lessforming of sheet metal parts//.Proceedings of SheMet’98[C].[s.l.]:[s.n.],1998,63270.[5]HEI N P,VOO LERTSE N F.Hydroforming of sheet metalpairs[J].J of Materials Processing T echnology,1999,87:1542164.[6]NOVOT NY S,HEI N P.Hydroforming of sheet metal pairsfrom aluminum alloys//.Proceedings of SheMet’99[C].[s.l.]:[s.n.],1999.5912606.(责任编辑 程建霞)(上接第6页)[3]崔岩梅.一种基于小波变换的多尺度多算子图像融合方法[J].光学技术,1999(7):37239.[4]M A LLAT S G.Multifrequency channel decom position ofimages and wavelet m odels[J].IEEE T rans Acoust,S peech,S ignal Processing,1989,37(12):209122110.[5]M A LLAT S G,ZH ANG S.Characterization of signal frommutiscale edges[J].IEEE T ransactions on Pattern Analy2sis and Machine Intelligence,1992,14(7):7102732.[6]M OON Peter,DE JAGER G erhard.An investigation intothe applicability of wavelet trans form to digital stereo imagematching//.Proc of1993IEEE S outh A frican Sym posiu2 m on C ommunication and S ignal Processing[C].Capetown:[s.n.],1993.75279.(责任编辑 程建霞)・9・ 第4期 张士宏,等:板材零件成对液压成形新技术 。