现代液压成形技术
现代液压成型技术

现代液压成型技术现代液压成型技术第1部分:液压成形技术的种类在介绍它的种类和特点之前首先让我们先了解它的定义,什么是液压成形?定义:液压成形是指利用液体作为传力介质或模具使工件成形的一种塑性加工技术,也称液力成形。
(可能文字解释有点抽象,下面请大家看一段视频),很直观的可以看到它的成形工艺大致可分为三个阶段:第一个阶段,填充阶段,将管材放在下模内,然后闭合上模,使管材内充满液体(并排除气体),将管的两端用水平冲头压封;第二个阶段,成形阶段,对管内液体加压胀形的同时两端的冲头按照设定加载曲线向内推进补料,在内压和轴向补料的联合作用下使管材基本贴近模具;第三个阶段,整形阶段,提高压力是过度区圆角完全贴靠模具而成形为所需的工件,这个阶段基本没有补料,从截面看可以把管材变为矩形、梯形、椭圆形或其他异型截面。
1.1 按使用的液体介质不同可将液压成形分为水压成形和油压成形。
1.1.1 水压成形:使用的介质为纯水或水添加一定比例的乳化油组成的乳化液1.1.2 油压成形:油压成形的介质为液压传动油或机油1.2 按使用坯料不同,可分为管材液压成形、板材液压成形、壳体液压成形。
1.2.1管材液压成形:板料(≤100MPa)和壳体液压成形(≤50MPa)使用的成形压力较低,而管材液压成形使用的压力较高(一般不超过400MPa),又称内高压成形(Internal High Pressure Forming)通过管材内部施加高压液体和轴向补料把管材压入到模具型腔使其成形为所需工件,所需管材多为电阻焊管(ERW)因其成本低且成型性好,其次是无缝管、拉拔管(DOM)激光焊管(成型性最佳)。
1.2.1.1变径管内高压成形技术变径管内高压成形是以管材作坯料,通过管材内部施加高压液体和轴向补料把管材压入到模具型腔使其成形为所需工件,把管材的圆截面变为矩形、梯形、椭圆形或其他异型截面。
(板书演示)1.2.1.2弯曲轴线变截面管件内高压成形弯曲轴线管件内高压成形工艺过程包括弯曲、预成形、内高压成形等主要工序。
现代液压成形技术

薄壁多通管内高压成形技术
缺陷形式:支管顶部 破裂、主管起皱、Y 型支管过渡区内凹 多通管件的应用: 1.排气歧管:内壁光滑、 壁厚薄、质量轻
内高压成形设备和模具
内高压成形机由合模压 力机、高压源、水平缸、 液压泵站、水压系统和 计算机控制系统六部分 组成。 工作过程:闭合模具— 施加合模力—对管材内 填充加压介质—管端密 封—按加载曲线施加内 压和轴向进给—增压整 形—卸压—去合模力— 退回冲头—开模
板材充液拉深成形技术
介质传递载荷,使板材在传力介 质的压力作用下 贴靠凸模以实现金属零件的成形。 成形工艺过程如图所示; 板材充液拉深特点: 1.成形极限高 2.尺寸精度高、表面质量好 3、道次少 4、成本低 适用范围:适用于筒形、锥形、抛 物线形盒形领域的等变形程度超 过普通拉深成形极限的板材零件 eg:航天领域整流罩、头套以及汽 车领域的发动机等覆盖件。
现代液压成形技术
目录
一· 概论 二· 内高压成形技术 三· 液力胀接和液压冲孔 四· 板材充液拉深成形技术 五· 封闭壳体无模液压成形技术一· 概论
性
加工技术,也称为液力成形。 分类:按使用的液体介质不同,分为:水压成形和油压成形。 按使用的坯料不同,分为:1)管材液压成形(内高压成形)2)板料液压 成形.3)壳体液压成形 特点:(1)仅需要凹模或凸模,省去模具加工费用和时间,壳体液压成形不需要 凸 凹模 (2)液体具有实时可控性
基本原理:采用液体作为传力
封闭壳体无模液压成形技术
基本过程:先由平板或经过 辊弯的单曲率壳板组焊成封 闭多面壳体,然后再封闭多 面壳体内充满液体介质(通 常为水),并通过一个加压 系统向封闭多面壳体内施加 内压,在内压作用下,壳体 产生塑性变形而逐渐趋向于 球壳。 对于单曲率壳体,该工艺的 主要工序为:下料—弯卷— 组装焊接—液压成形
液压成型

图1 空心异形截面零件引言液压成形技术同冲压,焊接等传统的成形技术相比,是一门新型的金属成形技术。
为了解决汽车,航空航天等领域的一些复杂的工艺问题和技术要求,从20世纪50年代起,德、美、日等国科学家在相关领域内先后提出了内高压成形技术和板料液压成形技术。
1985年我国科学家王仲仁教授发明了球形容器无模液压成形技术,提出了壳体液压成形技术。
近几年,依托于计算机控制技术和高压液压系统的发展,液压成形技术迅速发展。
目前,很多复杂结构的零件都可以通过该技术批量地加工生产。
一、液压成形技术的概述1.1 液压成形的定义和分类液压成形也称为液力成形是指利用液体作为传力介质或模具使工件成形的一种塑性加工技术。
按使用的液体介质不同,液压成形分为水压成型和油压成型;按使用的配料不同,液压成形分为管材液压成形,板料液压成形和壳体液压成形。
板料和壳体液压成形使用的成形压力较低,而管材液压成形使用的压力较高,又称为内高压成形,本文中称管材液压成形为内高压成形。
1.2 液压成形的特点现代液压成形技术的主要特点表现在两个方面:①液压成形技术仅需要凸模和凹模中的一个,或者不使用任何模具,这样可以省去一半,甚至不需要花费制造模具的费用和加工时间,而且液体作为凸模可以成形很多刚性凸模无法成形的复杂零件。
②液体作为传力介质具有实时可控性,通过液压闭环伺服系统和计算机控制系统可以按给定的曲线精确控制压力,确保工艺参数在设定的数值内,并且随时间可变可调,大大提高了工艺柔性。
二、内高压成形技术2.1 内高压成形技术的原理及分类内高压成形技术是用管材作为原材,通过对官腔内施加液体压力及在轴向施加负荷作用,使其在给定模具型腔内发生塑性变形,管壁与模具内表面贴合,从而得到所需形状零件的成形技术。
内高压成形技术主要可以整体成型轴线为二维或三维曲线的异形截面空心零件,从材料的初始圆截面可以成形为矩形,梯形,椭圆形或其他异形的封闭界面,如图1所示。
先进液压成形技术与轻量化汽车零部件的研发

先进液压成形技术与轻量化汽车零部件的研发徐勇,工学博士,硕士生导师,副研究员,主要从事高性能薄壁零件先进液压成形技术和装备的研发应用及计算机辅助精确成形仿真技术的研究,拥有专利17项。
近年来碳排放超标,全球不断变暖以及能源过度开采及消耗等问题成为人们日益关注的焦点,因此以节省能源、减少尾气排放为目的的汽车轻量化成为了汽车制造业的重要研究课题,所以要加速实现传统结构类零部件的轻量化设计与改造。
轻量化的主要途径包括:材料轻量化、结构轻量化以及轻量化成形技术等。
而液压成形技术作为制造复杂形状薄壁板、管零件的先进制造技术,有利于零部件的轻量化、无余量化、高精度及整体化发展。
随着人们对产品性能以及减重要求的不断提升,希望能够将更多富有特色的材料纳入到液压成形技术的可行范围中,生产出品质更加优良并且结构更加复杂的新型汽车轻量化零部件,因此不断丰富液压成形理论、开发液压成形的新材料新工艺、并且提升大型智能液压成形装备制造水平,是液压成形技术未来发展的主要趋势。
液压成形工艺原理及优势液压成形是依托液体高压作用与模具型腔相配合,最终使金属坯料成形出整体化复杂变截面构件的先进制造技术。
按使用坯料的不同,可以分为三种类型:板材液压成形、壳体液压成形和管材液压成形。
其中管材液压成形是以金属管材为毛坯,借助专用液压设备向密封的管坯内注入液体介质,使管内液体产生高压(工作压力通常100~400MPa,最高达1000MPa),与此同时在管坯两端通过轴向冲头向内施加推力进行补料,在两种外力的作用下,管坯材料塑性变形,并最终与模具型腔内壁贴合,使金属管坯变形成为具有三维形状的空体构件,如图1所示,目前该技术在汽车零部件制造当中的应用也最为广泛。
但无论是管材液压成形或管材液压胀形、内高压成形等均是指同一种成形技术。
图1 管材液压成形工艺原理图液压成形技术能够提高生产效率,并可以显著地减轻零部件重量并增强其结构稳定性。
与传统机械加工、冲压焊接方式相比,液压成形具有以下几个显著的优点:减轻重量、提高零件的强度、刚度,尤其是疲劳强度、提高尺寸精度以及减少零件、工序和模具数量,降低生产成本等。
现代液压成形

26
充液拉深成形
用液体介质代替凹模传递 载荷,液压则作为辅助成 形的手段,可减小普通拉 深成形中凸、凹模之间坯 料的悬空区,使该部分坯 料紧贴凸模,零件形状尺 寸最终靠凸模来保证。
充液拉深成形中的液压作 用形成了坯料与凸模之间 的摩擦保持效果,提高了 凸模圆角区板料的承载能 力,抑制坯料减薄和开裂, 可有效提高成形极限、减 少成形道次。同时,液体 从坯料与凹模上表面间溢 出可形成流体润滑,促进 外围板材进入凹模,缓解
现代液压成形技术
1
2
3
4
5
目录
一、概述
1.液压成形技术分类和特点 2.现状与发展趋势
二、内高压成形(管材)
1.工艺与应用范围 2.主要工艺参数 3.缺陷、管材 4.内高压成形设备与模具
三、板材充液拉深
工艺、特点和适用范围
四、封闭壳体无模液压
工艺、特点和应用范围
6
1.液压成形技术分类和特点
种类:由内向外冲孔、由外向内冲孔。
管端切割:使用激光切割机。
22
内高压成形设备与模具
内高压设备组成 合模压力机、高压源、水平缸、液压泵站、
水压系统、计算机控制系统。
23
24
25
板材液压成形
采用液体作为传力介质以代替刚性的凸模 或凹模来传递载荷,使坯料在液体压力作 用下贴靠凹模或凸模,从而实现金属板材 零件的成形。
板料液压:筒形、锥形、盒形及复杂形状均可;材料涉及 碳钢、高强钢和铝合金等;材料厚度为0.2~3.2mm;拉深 比可达2.6。我国哈工大已能设计生产拉深力达4000kN, 成形液压达100MPa的双动液压拉深机,造价成本远低于 国外产品。但在超高压、计算机精确控制领域仍有较大差 距。发展趋势为大型复杂型面成形、低塑材料拉深等方向。
现代液压技术的应用及发展

现代液压技术的应用及发展液压技术是实现现代化传动与控制的关键技术之一,世界各国对液压工业的发展都给予很大重视。
由于液压技术广泛应用了高科技成果,如:自控技术、计算机技术、微电子技术、可靠性及新工艺新材料等,使传统技术有了新的发展,也使产品的质量、水平有一定的提高。
近年来,液压气动技术面临与机械传动和电气传动的竞争,如:数控机床、中小型塑机已采用电控伺服系统取代或部分取代液压传动。
其主要原因是液压技术存在渗漏、维护性差等缺点。
为此,必须努力发挥液压气动技术的优点,克服缺点,注意和电子技术相结合,不断扩大应用领域,同时降低能耗,提高效率,适应环保需求,提高可靠性,这些都是液压气动技术继续努力的永恒目标,也是液压气动产品参与市场竞争是否取胜的关键。
当前液压技术的发展主要集中在以下几个方面:(1)发展集成、交合、小型化和轻量化液压元件。
随着液压系统复杂化程度的提高,要求液压元件具有高可靠性,减少配管,节省安装空间、易维修等特点,必须发展上述类型的液压元件。
继集成块式、叠加阀式、插装阀式之后,近几年又出现了将控制元件附加在动力元件上的一体化复合液压装置。
(2)发展高性能的液压控制元件。
适应机电一体化主机发展的需要。
如开发低控功率阀门、研制适应野外条件的电液比例阀、高响应频率的电液伺服阀、低成本比例阀及不需要A/D 和D/A转换、可直接与计算机接口的数字阀。
(3)以环境保护、安全和满足可持续发展为目标的绿色开发研究。
如无污染的纯水液压技术及相关新材料,新工艺的开发和应用研究,降低元件和系统的噪声,减少泄漏和提高密封性能的应用研究。
(4)提高元件和系统的可靠性。
提高可靠性是一项系统工程,除科学设计,先进的材料及完善的工艺外,还应注意应用和维护的可靠性,系统的状况监测,故障诊断,降低元件对污染的敏感性。
加强污染控制与新型工程材料的应用研究,对提高元件和系统的可靠性有重要意义。
(5)以提高效率、降低能耗为目标的系统匹配设计理论、方法和计算机对液压系统进行自动适应控制手段研究。
液压成形
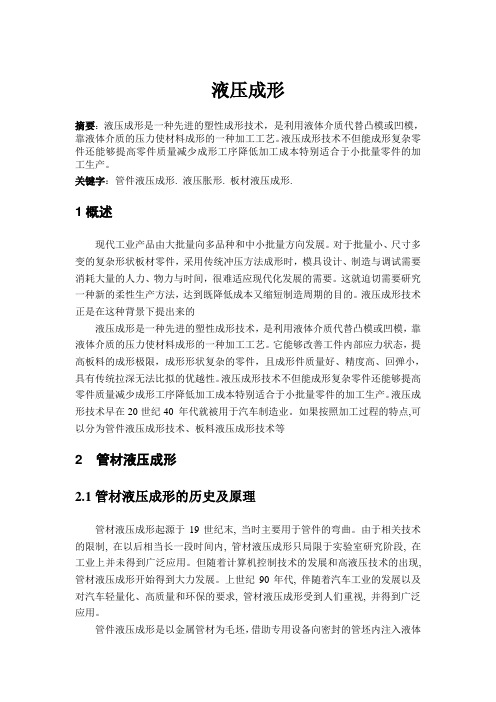
液压成形摘要:液压成形是一种先进的塑性成形技术,是利用液体介质代替凸模或凹模,靠液体介质的压力使材料成形的一种加工工艺。
液压成形技术不但能成形复杂零件还能够提高零件质量减少成形工序降低加工成本特别适合于小批量零件的加工生产。
关键字:管件液压成形. 液压胀形. 板材液压成形.1概述现代工业产品由大批量向多品种和中小批量方向发展。
对于批量小、尺寸多变的复杂形状板材零件,采用传统冲压方法成形时,模具设计、制造与调试需要消耗大量的人力、物力与时间,很难适应现代化发展的需要。
这就迫切需要研究一种新的柔性生产方法,达到既降低成本又缩短制造周期的目的。
液压成形技术正是在这种背景下提出来的液压成形是一种先进的塑性成形技术,是利用液体介质代替凸模或凹模,靠液体介质的压力使材料成形的一种加工工艺。
它能够改善工件内部应力状态,提高板料的成形极限,成形形状复杂的零件,且成形件质量好、精度高、回弹小,具有传统拉深无法比拟的优越性。
液压成形技术不但能成形复杂零件还能够提高零件质量减少成形工序降低加工成本特别适合于小批量零件的加工生产。
液压成形技术早在20世纪40 年代就被用于汽车制造业。
如果按照加工过程的特点,可以分为管件液压成形技术、板料液压成形技术等2 管材液压成形2.1管材液压成形的历史及原理管材液压成形起源于19世纪末, 当时主要用于管件的弯曲。
由于相关技术的限制, 在以后相当长一段时间内, 管材液压成形只局限于实验室研究阶段, 在工业上并未得到广泛应用。
但随着计算机控制技术的发展和高液压技术的出现,管材液压成形开始得到大力发展。
上世纪90年代, 伴随着汽车工业的发展以及对汽车轻量化、高质量和环保的要求, 管材液压成形受到人们重视, 并得到广泛应用。
管件液压成形是以金属管材为毛坯,借助专用设备向密封的管坯内注入液体介质,使其产生高压,同时还在管坯的两端施加轴向推力,进行补料,在两种外力的作用下,管坯材料塑性变形,并最终与模具型腔内壁贴合,得到形状与精度均符合技术要求的中空零件液压成形原理如图1 所示图1 管件液压成形原理示意图当零件轴线不是直线模腔分模面处截面小于管坯截面时,需进行弯管冲压等预工艺,以便管坯能顺利置入模腔中,如有必要,在液压成形之前还需进行退火处理2.2管材液压成形优点:与传统的冲压焊接工艺相比,管件液压成形工艺具有以下优点:(1 ) 减轻零件质量,节约材料; (2 ) 提高零件的强度和刚度,特别是疲劳强度; ( 3) 减少零件数量节约模具成本;(4) 零件整体成形,可减少后续机械加工和组装焊接量,简化生产流程,提高生产效率; (5) 提高加工精度,减少装配误差积累,可提高产品质量; (6)降低生产成本; (7) 结构形状设计更趋灵活优化。
绿色节能制造技术———液压成形研究现状及发展

浙江科技学院学报,第21卷第3期,2009年9月JournalofZhejiangUniversityofScienceandTechnologyVol.21No.3,Sep.2009收稿日期:2009-06-10基金项目:浙江省教育厅科研计划项目(Y200805385);宁波市自然科学基金资助项目(2006A610028)作者简介:刘小旦,(1981— ),女,浙江金华人,工程师,硕士,主要从事机械电子产品设计及成形工艺研究。
绿色节能制造技术———液压成形研究现状及发展刘小旦1,周 林2,程晓民2(1.杭州航天电子技术有限公司研发处,杭州310015;2.宁波工程学院机械工程学院,浙江宁波315016)摘 要:液压成形是依靠高压液体使金属坯料贴模成形的柔性加工工艺。
它具有成形产品质量轻、刚度好、形状及尺寸精度高、模具简单和生产周期短等诸多优点,目前已在国外汽车工业中得到广泛应用。
就液压成形工艺原理及分类进行了介绍,概述了液压成形设备发展及该技术在工业领域中的应用,并且总结了国内外相关研究进展及发展趋势。
关键词:液压成形;柔性加工;轻量化中图分类号:TG394 文献标识码:A 文章编号:1671-8798(2009)03-0243-04Currentsituationanddevelopmentofgreenenergyefficiencytechnology———hydroformingLIUXiao-dan1,ZHOULin2,CHENGXiao-min2(1.HangzhouAerospaceElectronicTechnologyCo.,Ltd.,Hangzhou310015,China;2.SchoolofMechanicalEngineering,NingboUniversityofTechnology,Ningbo315016,China)Abstract:Hydroformingisaflexibleprocessingtechniqueusinghydraulicpressureastheformingmedia.Hydroformedproductscanreduceweightandcostwhileimprovingstructuralstrengthandrigidity.Itiswidelyusedtodayinthemassproductionoflightweightcomponentsforautomotiveindustry.Inthispaper,theclassificationandfundamentalsofthistechniquewereintroduced;thedevelopmentsofformingequipmentandapplicationinindustrywerepresented.Theresearchstatusanddevelopmenttrendswerealsogeneralized.Keywords:hydroforming;flexibleprocessing;lightweigh 液压成形主要是指依靠高压液体作为传力介质,代替刚性的凹模或凸模,使坯料在传力介质的压力作用下贴合凸模或凹模成形的一种柔性加工工艺[1]。
更具竞争力的液压成形技术

更具竞争力的液压成形技术与传统的冲压工艺相比,液压成形工艺在减轻重量、减少零件数量和模具数量、提高刚度与强度、降低生产成本等方面具有明显的技术和经济优势,在工业领域尤其是汽车工业中得到了越来越多的应用。
在汽车工业及航空、航天等领域,减轻结构质量以节约运行中的能量是人们长期追求的目标,也是先进制造技术发展的趋势之一。
液压成形(hydroforming)就是为实现结构轻量化的一种先进制造技术。
液压成形也被称为“内高压成形”,它的基本原理是以管材作为坯料,在管材内部施加超高压液体同时,对管坯的两端施加轴向推力,进行补料。
在两种外力的共同作用下,管坯材料发生塑性变形,并最终与模具型腔内壁贴合,得到形状与精度均符合技术要求的中空零件。
液压成形技术的优点对于空心变截面结构件,传统的制造工艺是先冲压成形两个半片,然后再焊接成整体,而液压成形则可以一次整体成形沿构件截面有变化的空心结构件。
与冲压焊接工艺相比,液压成形技术和工艺有以下主要优点:□ 减轻质量,节约材料。
对于汽车发动机托架、散热器支架等典型零件,液压成形件比冲压件减轻20%~40%;对于空心阶梯轴类零件,可以减轻40%~50%的重量。
□ 减少零件和模具数量,降低模具费用。
液压成形件通常只需要1套模具,而冲压件大多需要多套模具。
液压成形的发动机托架零件由6个减少到1个,散热器支架零件由17个减少到10个。
□ 可减少后续机械加工和组装的焊接量。
以散热器支架为例,散热面积增加43%,焊点由174个减少到20个,工序由13道减少到6道,生产率提高66%。
□ 提高强度与刚度,尤其是疲劳强度,如液压成形的散热器支架,其刚度在垂直方向可提高39%,水平方向可提高50%。
□ 降低生产成本。
根据对已应用液压成形零件的统计分析,液压成形件的生产成本比冲压件平均降低15%~20%,模具费用降低20%~30%。
图1为采用液压成形技术制造的欧宝发动机托架零件与传统冲压件的比较,其零件重量降低了30%,模具费用降低了60%,零件的生产成本降低了20%。
液压成型技术

板材液压成型
板材液压成型是利用液体作为传力介质来传递载荷, 使板材成型到单侧模具上的一种板材成型方法。 根据液体介质取代凹模或凸模可将之进一步分为: 1.充液拉深(用液体介质代替凹模)。 2.液体凸模拉深(以液体介质作为凸模)。
充液拉深
热态充液拉深,将材料的温热性能与充液拉深的技术 优势结合起来,可使铝合金及镁合金等成型性能差的 轻体材料成型能力得到提高,促进其在航空航天领域 的应用。
液压成型技术的现状
管材液压成型 现代液压成型压力一般达到400MPa,有时可达到 1000MPa。超高压精度达到0.2-0.5MPa,位移精度 达到0.5MPa。,现在已广泛应用到汽车、航空、自 行车、管路等当中,其中汽车应用最为广泛。 包括: 1.底盘类零件:副车架、纵梁、后轴、保险杠 2.车体结构:座椅框、仪表盘支梁、顶梁等 3.发动机和驱动系统:排气管凸轮轴 4.转向和悬挂系统:控制臂、摆臂等
管材成型工艺
它的成型工艺大致可分为三个阶段:第一个
阶段,填充阶段,将管材放在下模内,然后 闭合上模,使管材内充满液体(并排除气 体),将管的两端用水平冲头压封;第二个 阶段,成型阶段对管内液体加压胀型的同时 两端的冲头按照设定加载曲线向内推进补料, 在内压和轴向补料的联合作用下使管材基本 贴近模具;第三个阶段,整型阶段,提高压 力使过度区圆角完全贴靠模具而成型为所需 的工件,这个阶段基本没有补料,从截面看 可以把管材变为矩型、梯型、椭圆型或其他 异型截面。
液压成型技术的发展趋势
随着液压成型技术的成熟和人们都减轻质量,降低成本的需求的提高,该技术 近十年来在各个领域得到广泛应用。 板材液压成型: 1.进一步提高成型极限和零件质量的成型新技术。 2.低塑性材料的拉深成型。 3.大型复杂型面零件成型 4.与普通拉深工艺复合,提高效率 壳体液压成型: 1. 选用轻质传力介质 2. 应用高能束焊接技术和自动化工艺焊接封闭壳体 3. 铝合金等轻质材料球壳液压成型 管材液压成型: 1.超高压成型 2.新成形工艺不断发展 3. 超高强度钢成型 4. 热态内压成型
杆件液压成形技术.doc

文献综述专业机械设计制造及其自动化学生姓名郑健健班级 B 机制031学号0310110101指导教师吴乃领文献综述1 引言杆件液压成形技术是用杆材作为坯料,通过对杆腔内施加液体压力、轴向施加负荷作用,使其在给定模具型腔内发生塑性变形,杆壁与模具内表面贴合,从而得到所需形状零件的技术。
它主要用于制造空心零件,由于该工艺属于无切削加工,材料且零件集成度好,因此在国内外受到了广泛重视。
目前德国、美国、日本等国都对该技术做了大量研究,并逐步开始应用于航空、航天、汽车、化工、机械、民用等领域。
特别是最近几年来,由于汽车工业轻量化、安全性、经济性等方面的要求,采用杆件液压成形技术制造的杆状零件相比传统冲压、焊接工艺具有工序少、成本低,零件重量轻,零件强度刚度好,装配精度高等优点,因此受到汽车制造业的广泛关注。
2 成型工艺过程与设备杆件液压成形工艺过程要求液压成形设备既能提供预成形压力、合模力、内高压压力、端面密封、轴向进给等,又能实现密封、内压力与轴向进给匹配关系的精确控制,因此对设备控制方面的要求很高。
当前液压压力机设备的控制系统主要有以继电器、可编程控制器和工控机为主的几种类型。
以压力继电器为主控元件的传统型,这种类型的液压机其电路简单,相应的控制功能也较简单。
它主要用于成形工艺过程简单、对控制要求不高,单机工作,适应性不强的场合,比较适合于对产品精度要求不高的大批量生产。
可编程控制器的控制系统,目前正广泛被应用的新型工业自动控制系统。
它不仅可以进行数字逻辑控制,而且还可对模拟量进行控制。
可编程控制器与继电器相比有更高的稳定性和灵活性。
但与工业控制机的精度和灵活性还是有一定的差距。
在杆件液压成形中的内压力与轴向进给需按照事先设定的任意曲线高精度地实时变化,并且考虑到时间延时,采用PLC 并不能完全满足控制的要求。
应用工业控制计算机的高性能液压控制系统,这种控制方式是一种采用全计算机反馈控制方式。
它是以单片机作为主控处理单元,通过与外围的接口器件(如专用的A / D 和D / A 转换板)相连或直接应用一种所谓的数字阀实现对液压系统的实时控制,同时把各种传感器组成一个闭环式的回路,通过反馈控制系统,达到精确地控制液压系统动作的目的。
曲面板材零件液压成形技术解读

曲面板材零件液压成形技术来源:作者:发布时间:2008-12-20针对传统板材冲压成形中存在的成形极限低、模具型腔复杂,以及零件表面品质差等缺点,发展了板材液压成形技术。
其基本原理是采用液体作为传力介质以代替刚性的凸模或凹模来传递载荷,使坯料在液体压力作用下贴靠凹模或凸模,从而实现金属板材零件的成形。
自从该技术推出以来,在航空航天及汽车领域不断获得应用,特别适于结构形状复杂的零件及冷成形性能差的材料成形,如铝合金、高强钢、高温合金以及拼焊板等。
板材液压成形技术现也日渐成为国内外业界的研究热点,并产生了可控径向加压充液拉深技术及液体凸模拉深成形新技术。
板材液压成形原理及分类板材液压成形是利用液体作为传力介质来传递载荷,使板材成形到单侧模具上的一种板材成形方法,根据液体介质取代凹模或凸模可将之进一步分类为充液拉深成形和液体凸模拉深成形。
前者(图1)是用液体介质代替凹模传递载荷,液压则作为辅助成形的手段,可减小普通拉深成形中凸、凹模之间坯料的悬空区,使该部分坯料紧贴凸模,零件形状尺寸最终靠凸模来保证。
图1 充液拉深成形原理充液拉深成形中的液压作用形成了坯料与凸模之间的摩擦保持效果,提高了凸模圆角区板料的承载能力,抑制坯料减薄和开裂,可有效提高成形极限、减少成形道次。
同时,液体从坯料与凹模上表面间溢出可形成流体润滑,促进外围板材进入凹模,缓解了零件表面的划伤。
这一成形技术因其独特优势在国际上受到普遍重视,发展出主动背压(预胀)拉深法,其过程是预先胀形,然后拉深,通过预先胀形达到变形硬化的效果。
液体凸模拉深成形(图2)则是以液体介质代替凸模传递载荷,液压作为主驱动力使坯料变形,坯料法兰区逐渐流入凹模,最终在高压作用下使坯料贴靠凹模型腔,零件形状尺寸靠凹模来保证。
这一成形法通过合理控制压边力可使坯料产生拉-胀成形,应变硬化可提高曲面薄壳零件的刚性、压曲抗力和抗冲击能力。
因此,它非常适于铝合金和高强钢等轻合金板料形状复杂(特别是局部带有小圆角)、深度较浅的零件成形。
液压成型工艺技术
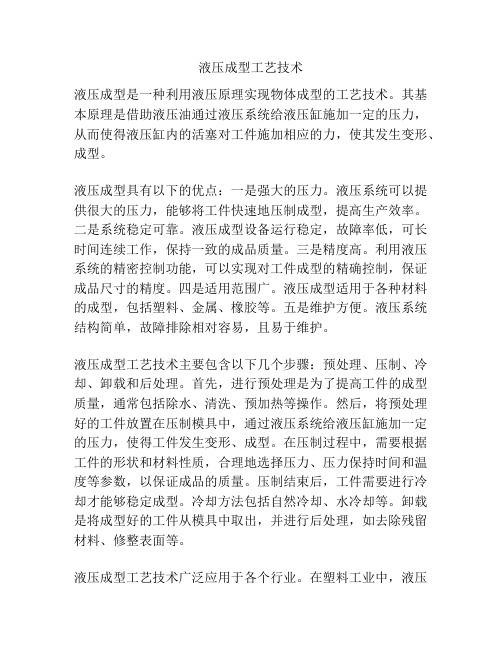
液压成型工艺技术液压成型是一种利用液压原理实现物体成型的工艺技术。
其基本原理是借助液压油通过液压系统给液压缸施加一定的压力,从而使得液压缸内的活塞对工件施加相应的力,使其发生变形、成型。
液压成型具有以下的优点:一是强大的压力。
液压系统可以提供很大的压力,能够将工件快速地压制成型,提高生产效率。
二是系统稳定可靠。
液压成型设备运行稳定,故障率低,可长时间连续工作,保持一致的成品质量。
三是精度高。
利用液压系统的精密控制功能,可以实现对工件成型的精确控制,保证成品尺寸的精度。
四是适用范围广。
液压成型适用于各种材料的成型,包括塑料、金属、橡胶等。
五是维护方便。
液压系统结构简单,故障排除相对容易,且易于维护。
液压成型工艺技术主要包含以下几个步骤:预处理、压制、冷却、卸载和后处理。
首先,进行预处理是为了提高工件的成型质量,通常包括除水、清洗、预加热等操作。
然后,将预处理好的工件放置在压制模具中,通过液压系统给液压缸施加一定的压力,使得工件发生变形、成型。
在压制过程中,需要根据工件的形状和材料性质,合理地选择压力、压力保持时间和温度等参数,以保证成品的质量。
压制结束后,工件需要进行冷却才能够稳定成型。
冷却方法包括自然冷却、水冷却等。
卸载是将成型好的工件从模具中取出,并进行后处理,如去除残留材料、修整表面等。
液压成型工艺技术广泛应用于各个行业。
在塑料工业中,液压成型被用于各种塑料制品的生产,如塑料瓶、塑料管道等。
在金属加工行业中,液压成型被用于金属板的冲压成型、弯曲成型等。
在橡胶工业中,液压成型被用于橡胶制品的成型,如橡胶管、橡胶密封垫等。
此外,液压成型还可以应用于汽车工业、航空航天工业、造船工业等领域。
总之,液压成型工艺技术是一种广泛应用于各个行业的成型技术,其具有强大的压力、稳定可靠、精度高、适用范围广、维护方便等优点。
通过合理使用液压成型工艺技术,可以实现对各种材料的高质量成型,提高生产效率,降低生产成本。
薄壁件液压成形新技术

薄壁件液压成形新技术发布时间:2009-3-17 18:15:01飞机、汽车等运输工具对减轻质量和降低成本的需求促进了液压成形技术的不断发展。
液压成形技术近十多年来在工业生产中得到了广泛应用,逐步成为薄壁零件制造的主流技术之一。
飞机、直升机等航空器使用的薄壁件包括异型截面管件和复杂曲面钣金件。
目前,异型截面管件的制造技术主要为半管成形再焊接,但存在焊接变形大、废品率高和可靠性差等问题。
小型复杂曲面钣金件制造技术主要为落锤砸压成形,它的主要问题是废品率高、尺寸精度一致性差,以及材料内部组织损伤影响零件的疲劳性能。
随着高性能铝合金和钛合金的广泛应用,同时镁合金的使用也逐渐增多,材料塑性成形难度越来越大,既有材料性能提高带来的困难,也有结构形状复杂带来的困难。
例如,铝合金的强度由150MPa提高到30MPa,塑性由30%降低到10%。
零件结构形状复杂表现为超薄壁、空心大截面差、高次函数空间曲面或非回转体零件等结构形式。
因此,面向高性能轻质材料和复杂形状结构的塑性成形技术得到迅速发展。
本文重点介绍适合航空工业制造异型截面管件和复杂曲面钣金件的管材内高压成形、热态内压成形、充液拉深和液体凸模拉深等塑性成形新技术。
变径管内高压成形技术变径管内高压成形是以管材作坯料,通过管材内部施加高压液体和轴向补料把管材压入到模具型腔使其成形为所需工件,把管材的圆截面变为矩形、梯形、椭圆形或其他异型截面,如图1所示。
其特点是,通过轴向补料,可以减少壁厚减薄,提高成形极限,一次整体成形异型截面管件,没有焊缝,提高了可靠性。
用内高压成形技术制造的异型双锥形管件,材料为不锈钢1Cr18Ni9Ti,最大膨胀率达到110%,接近材料均匀延伸率的3倍。
由于为非对称形状,塑性变形不均匀,容易导致局部变薄开裂,因此需要特殊形状的预成形坯。
用内高压成形的飞机管路系统铝合金变径管,管材采用5A02铝合金,规格为Φ65mm×1.5mm。
液压成形技术
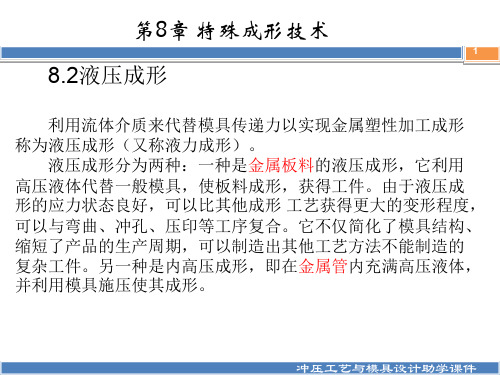
屈曲:当管材成形区长度过长,在成形初期还没有在管材 内建立起足够大的内压时,施加了过大的轴向力造成的。
皱纹:当轴向力过大时,工件在成形初期产生皱纹 。 皱纹可以分为二类,一类是后期加压整形无法展平,这类 皱纹称为死皱,它是一种缺陷。 另一类皱纹通过后期加压可 以展平,称为“有益皱纹”。这类皱纹不仅不是缺陷而且还可 作为一种预成形的手段,在成形初期将管材推出皱纹以补充材 料。但前提条件是后续整形压力能将皱纹展开。
有缘学习更多+谓ygd3076考证资料或关注桃报:奉献教育(店铺)
冲压工艺与模具设计助学课件
第8章 特殊成形技术
13
4.内高压成形设备 一条完整的内高压成形生产线主要由切管机、弯管机、预
成型压力机、内高压成形压力机等设备组成。其中最重要的设 备是内高压成形压力机, 它由合模压力机、高压源、水平缸、液 压泵站、水压系统和计算机控制系统等6部分组成, 其组成和工 作原理如图8-13和图8-14所示。
内高压成形工艺作为一种整体成形薄壁结构件的塑性加工方 法,最近几十年在汽车制造业、航空航天业及卫生洁具业中得到 了广泛的应用。
a)轿车副车架(有18个不同的截面形状和尺寸)
b) 排气歧管
图8-10典型汽车内高压成形零件
冲压工艺与模具设计助学课件
有缘学习更多+谓ygd3076考证资料或关注桃报:奉献教育(店铺)
根据受力和变形特点, 零件分为成形区和送料区2个区间。成 形区是管材发生塑性变形直径和形状发生变化的部分,送料区是 在模具内限制管材外径不变, 主要作用是向成形区补充材料。
冲压工艺与模具设计助学课件
第8章 特殊成形技术
10
液压成型技术综述
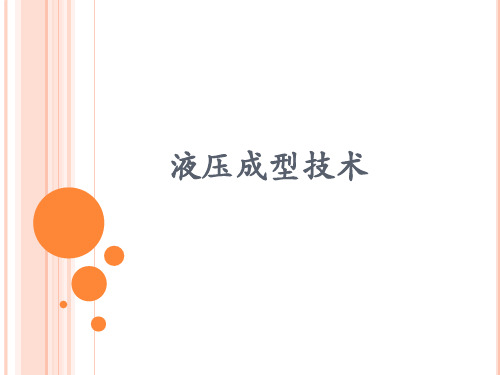
液压成型技术的发展趋势
随着液压成型技术的成熟和人们都减轻质量,降低成本的需求的提高,该技术 近十年来在各个领域得到广泛应用。 板材液压成型: 1.进一步提高成型极限和零件质量的成型新技术。 2.低塑性材料的拉深成型。 3.大型复杂型面零件成型 4.与普通拉深工艺复合,提高效率 壳体液压成型: 1. 选用轻质传力介质 2. 应用高能束焊接技术和自动化工艺焊接封闭壳体 3. 铝合金等轻质材料球壳液压成型 管材液压成型: 1.超高压成型 2.新成形工艺不断发展 3. 超高强度钢成型 4. 热态内压成型
以变径管为例
(a)
(b)
图3 变径管内高压成型技术工艺过程 (a)填充阶段;(b)成型阶段;(c)整型阶段。 (c)
管材液压成型特点
从工艺技术角度,管材液压成型与冲压焊接工艺相对 比的主要优点有: 1.减轻质量,节约材料。 ( 框、梁类 减轻20%-40%, 空心轴 可以减轻40%-50%) 2.减少零件和模具重量,降低模具费用。 3.可减少后续机械加工和组装焊接量,提高生产效率。 4.提高强度和刚度,尤其是疲劳强度。 5.材料利用率高。 (达到90%-95%) 6.降低生产成本。
管材成型工艺
它的成型工艺大致可分为三个阶段:第一个
阶段,填充阶段,将管材放在下模内,然后 闭合上模,使管材内充满液体(并排除气 体),将管的两端用水平冲头压封;第二个 阶段,成型阶段对管内液体加压胀型的同时 两端的冲头按照设定加载曲线向内推进补料, 在内压和轴向补料的联合作用下使管材基本 贴近模具;第三个阶段,整型阶段,提高压 力使过度区圆角完全贴靠模具而成型为所需 的工件,这个阶段基本没有补料,从截面看 可以把管材变为矩型、梯型、椭圆型或其他 异型截面。
板材液压成型技术特点
航空钣金薄壁结构件液压成型工艺
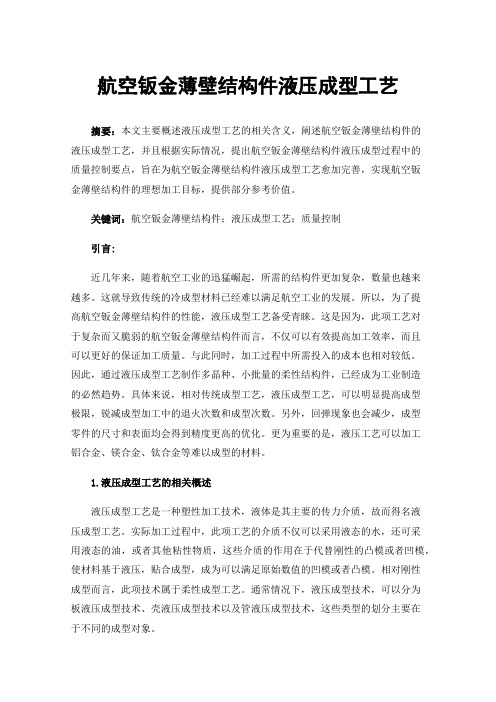
航空钣金薄壁结构件液压成型工艺摘要:本文主要概述液压成型工艺的相关含义,阐述航空钣金薄壁结构件的液压成型工艺,并且根据实际情况,提出航空钣金薄壁结构件液压成型过程中的质量控制要点,旨在为航空钣金薄壁结构件液压成型工艺愈加完善,实现航空钣金薄壁结构件的理想加工目标,提供部分参考价值。
关键词:航空钣金薄壁结构件;液压成型工艺;质量控制引言:近几年来,随着航空工业的迅猛崛起,所需的结构件更加复杂,数量也越来越多。
这就导致传统的冷成型材料已经难以满足航空工业的发展。
所以,为了提高航空钣金薄壁结构件的性能,液压成型工艺备受青睐。
这是因为,此项工艺对于复杂而又脆弱的航空钣金薄壁结构件而言,不仅可以有效提高加工效率,而且可以更好的保证加工质量。
与此同时,加工过程中所需投入的成本也相对较低。
因此,通过液压成型工艺制作多晶种、小批量的柔性结构件,已经成为工业制造的必然趋势。
具体来说,相对传统成型工艺,液压成型工艺,可以明显提高成型极限,锐减成型加工中的退火次数和成型次数。
另外,回弹现象也会减少,成型零件的尺寸和表面均会得到精度更高的优化。
更为重要的是,液压工艺可以加工铝合金、镁合金、钛合金等难以成型的材料。
1.液压成型工艺的相关概述液压成型工艺是一种塑性加工技术,液体是其主要的传力介质,故而得名液压成型工艺。
实际加工过程中,此项工艺的介质不仅可以采用液态的水,还可采用液态的油,或者其他粘性物质,这些介质的作用在于代替刚性的凸模或者凹模,使材料基于液压,贴合成型,成为可以满足原始数值的凹模或者凸模。
相对刚性成型而言,此项技术属于柔性成型工艺。
通常情况下,液压成型技术,可以分为板液压成型技术、壳液压成型技术以及管液压成型技术,这些类型的划分主要在于不同的成型对象。
液压成型工艺的原理是,将液体充满在凹模之中,然后板料在凸模的带动之下,在与凹模交界之时,产生反向液压,然后促使板材成型。
具体来说,基于反向液压,凸模会与板材紧紧贴合。
- 1、下载文档前请自行甄别文档内容的完整性,平台不提供额外的编辑、内容补充、找答案等附加服务。
- 2、"仅部分预览"的文档,不可在线预览部分如存在完整性等问题,可反馈申请退款(可完整预览的文档不适用该条件!)。
- 3、如文档侵犯您的权益,请联系客服反馈,我们会尽快为您处理(人工客服工作时间:9:00-18:30)。
定义:液压成形是指利用液体作为传力介质或模具使工件成形的一种塑性加工技术,
种类 管材液压成形 板料液压成形 壳体液压成形
介 不超过100MPa 不超过50MPa
从20世纪80年代中期发展起来的现代液压成形技术的主要特点表现在两个方面: 一是仅需要凹模或凸模,液体介质相应地作为凸模或凹模,省去一半模具费用和加工 时间,还可以成形很多刚性凸模无 法成形的复杂零件。而壳体液压成形不使用任何模 具,也称无模液压成形。二是液体作为传力介质具有实时可控性,通过压力闭环私服 系统和计机家控制系统可以按给定的曲线精确控制压力。下面简单介绍一下三种不同 液压成形技术的特点:
2.1 变径管内高压成形
• 变径管内高压成形技术适用于 制造汽车进、排气系统、飞机 管路系统、火箭动力系统和空 调中使用的异形管件和复制截 面管件。此外,小型飞机发动 机的空心曲轴和传动系统中空 心阶梯轴也可以采用内高压成 形技术制造。
2.2弯曲轴线异型截面管件内高压成形
• 弯曲轴线异形截面空心构件的轴 线是二维或三维曲线,典型截面 形状包括矩形、梯形、椭圆形以 及这些形状之间的过渡形状。 • 弯曲轴线异形截面管件的内高压 成形工艺过程包括弯曲、预成形 和内高压成形等主要工序,如图 4所示。用于内高压成形的弯曲 件除了保证弯曲轴线形状尺寸满 足要求外,更重要的是控制弯曲 过程中的壁厚减薄,这是保证内 高压成形顺利进行的前提。
典型实例:轿车副车架主管件内高压成 形 弯曲轴线异形截面管内高压成形技术广 泛以用于汽车制造领域。目前,世界上 最长的低碳钢内高压成形件是美国通用 汽车公司制造的长度为12m的卡车纵梁。 最长的铝合金内高压成形件是Volvo大吉 普上的纵梁,长度达5m,铝管直径达 100mm。
2.3薄壁多通管内高压成形
目录
• • • • • 一·概论 二·管材液压成形技术 三·板材液压成形技术 四·壳体液压成形技术 五·热态液压成形技术简介
一·概论
1.1液压成形技术种类和特点
也称为液力成形。 分类:按使用的液体介质不同,分为:1)水压成形;2)油压成形。 按使用的坯料不同,分为:1)管材液压成形(内高压成形);2)板料液压 成形;3)壳体液压成形 特点:(1)仅需要凹模或凸模,省去模具加工费用和时间,壳体液压成形不需要 凸凹模; (2)液体具有实时可控性。
二·管材液压成形技术
• 管材液压成形技术的原理: 是用管材作为原材,在管材的内部施 加液体压力,同时在轴向施加负荷作 用,使其在给定模具型腔内发生塑性 变形,管壁与模具内表面贴合,从而 得到所需形状零件的成形技术。管材 液压成形技术主要可以整体成形轴线 为二维或三维曲线的异形截面空心零 件,从材料的初始圆截面可以成形为 矩形,梯形,椭圆形或其他异形的封 闭界面,如图1所示。 内高压成形技术根据坯料塑性变形的 特点可分为变径管成形、弯曲轴线管 成形和多通管成形等,下面对这三种 成形技术的基本原理进行介绍。 内高压成形是适应汽车和飞机等运输工具 结构轻量化发展起来的先进制造技术。
2.3薄壁多通管内高压成形
多通管的成形工艺过程分为三个阶段: ①自由胀形阶段:成形初期,中间冲 头不动,左右冲头进行轴向补料的 同时,向管材内施加一定的内压, 支管顶部尚未接触中间冲头,处于 自由胀形状态。 ②支管成形阶段:成形中期,从支管 顶部与中间冲头接触开始,内压继 续增加,按照给定的内压与三个冲 头匹配的曲线,左右冲头继续进给 补料,中间冲头开始后退,后退中 要保持与支管顶部接触,并对支管 顶部施加一定的反推力,以防止支 管顶部的过度减薄造成开裂。 ③整形阶段:成形后期,左右冲头停 止进给,中间冲头停止后退,迅速 增加内压进行整形使支管顶部过渡 圆角达到设计要求。如图5所示, 以Y形三通管为例,说明多通管内 高压成形的基本工艺过程。 • 视频2
视频1
图3 变径管内高压成形技术工艺过程
2.1变径管内高压成形
缺陷类型及解决方案:
• • 屈曲:成形初期没有建立足够的内 压,施加了过大的轴向力造成。 起皱:成形中后期,内压足够的情 况下也可造成起皱。(分为死皱
和有益皱纹)
• •
开裂:轴向压力及补料量不足的情 况下,在内压连续作用下管材过渡 膨胀超过其极限膨胀率而导致。 解决:均可通过改变加载曲线解决。
• (图为一个铝合金变截面管件,其成形过程为弯曲- 预成形-内高压成形,以获得各个不同位置的多个截 面形状,其最大减薄率为7.5%)。
2.2弯曲轴线异型截面管件内高压成形
• 缺陷类型:
• 开裂: 弯曲段外侧:管材弯曲过程造 成 多边形截面过渡区:加载曲线 的影响 焊缝热影响区:焊接条件 • 死皱:管材直径过大、分模面 形式,尤其是预成型分模面。 • 飞边:零件某处截面特殊,预 成型截面和内高压分模面设计 不合理导致,模具闭合时造成。
内高压成形的不足
就目前为止,内高压成形的主要缺点是: (1)由于内压高,需要大吨位液压机作为合模压力机。例如,对于内径 为100mm和长度为2.5m的管材,当成形压力为100MPa时,合模力为 25000kN;当成形压力为200MPa时,合模力为50000kN。 (2)高压源及闭环实时控制系统复杂,造价高。 (3)由于成形缺陷和壁厚分布与加载路径密切相关,零件试制研发费用 高,必须充分利用数值模拟进行工艺参数优化。
(a)
(b)
图2 两种典型的变径管 (a)对称变径管;(b)不对称变径管。
2.1变径管内高压成形
变径管内高压成形的工艺过程可以 分为三个阶段(见图3): ①填充阶段,将管材放在下模内,然 后闭合上模,使管材内充满液体, 并排除气体,将管的两端用水平冲 头密封; ②成形阶段,对管内液体加压胀形的 同时,两端的冲头按照设定的加载 曲线向内推进补料,在内压和轴向 补料的联合作用下使管材基本贴靠 模具,这时除了过渡区圆角以外的 大部分区域已经成形; ③整形阶段,提高压力使过渡区圆角 完全贴靠模具而成形为所需的工件, 这一阶段基本没有补料。
• 分类:根据液体介质取代凹模或凸模可将之进一步分类为
• 充液拉深成形 • 液体凸模拉深成形。
3.1 充液拉深成形技术
• 充液拉深成形是用液体介质代替凹 模传递载荷,液压则作为辅助成形 的手段,可减小普通拉深成形中凸、 凹模之间坯料的悬空区,使该部分 坯料紧贴凸模,零件形状尺寸最终 靠凸模来保证。如图6所示,其成 形工艺过程分为充液阶段,施加压 力阶段,成形阶段和成形结束四个 阶段。 充液拉深成形中的液压作用形成了 坯料与凸模之间的摩擦保持效果, 提高了凸模圆角区板料的承载能力, 抑制坯料减薄和开裂,可有效提高 成形极限、减少成形道次。同时, 液体从坯料与凹模上表面间溢出可 形成流体润滑,促进外围板材进入 凹模,缓解了零件表面的划伤。
•
图1 空心异形截面零件
2.1变径管内高压成形
• 变径管是指管件中间一处或几
处的管径或周长大于两端管径 或周长,其主要的几何特征是 管件直径或周长沿轴线变化, 轴线为直线或弯曲程度很小的 二维曲线,如图2所示,又分为 对称变径管和不对称变径管。 • 膨胀率是衡量变径管内高压成 形的技术水平和难度的一个重 要指标,它与零件材料,成形 区长度,润滑和加载路径有关。
2.6内高压成形技术的优势
(1)减轻质量,节约材料。
内高压成形件优势(与冲压焊接件相比)
(2)液压成形件的比强度、比刚度以及使用寿命均比传统的拼焊构件和 铸件高出许多。 (3)液压成形由于一般不涉及焊接等热加工工序,再加上高压介质的校 形作用,从而有效抑制了工件的热变形和回弹。因此,液压成形件的尺寸 比较精确而且稳定,表面质量很高。 (4)减少零件和模具数量,降低模具费用。 (5)设计具有灵活性。 (6)降低成本。
• 多通管结构形式有T形三通管、 Y形三通管、X形四通管和六通 管等。在各种多通管中Y形三通 管为上下左右非对称结构,成 形难度最大。多通管内高压成 形的主要指标是支管高,T形三 通管支管高度可以达到1倍原始 管径,Y形三通管支管高度可以 达到0.75倍原始管径。 • 传统工艺:1两个直管插焊2、 利用板料冲压成两个半管后再 焊接成 整管。 • 基本工艺过程:
图5 三通管内高压成形工艺过程 (a)自由胀形阶段;(b)支管成形阶段; (c)整形阶段。
2.3薄壁多通管内高压成形
• 缺陷形式:T型三通管内
高压成形的主要缺陷形式 有支管顶部破裂、主管起 皱,而Y型三通管由于结构 的不对称性还会出现支管 过渡区内凹的缺陷。
• 多通管件的应用: 1.排气歧管:内壁光滑、 壁厚薄、质量轻
什么是液压成形?
——一种新型成型工艺
液压成形发展现状
0.1内高压成形
1)早在20世纪50年代,该技术已用于生产管路中使用的铜合金T型三通管和自行车车架上的连接件,所用 成形压力小于25MPa,随着科技的发展现代液压成形压力一般达到400MPa,有时可达到1000MPa。超高 压精度达到0.2-0.5MPa,位移精度达到0.5MPa。20世纪80年代德国和美国的研究机构系统地开展了内高 压成形的基础研究和应用技术,现在已广泛应用到汽车、航空、自行车、管路等当中,其中汽车应用最为 广泛。包括1.底盘类零件:副车架、纵梁、后轴、保险杠2.车体结构:座椅框、仪表盘支梁、顶梁等 3) 发动机和驱动系统:排气管凸轮轴 4)转向和悬挂系统:控制臂、摆臂等 2)成形工艺比较单一 0.2 板材液压成形 早在1890年,就出现了类似于充液成形的方法,在板材与液体间用橡胶模割开,并在第二次世界大战 时期在美国得到应用(钢制头盔)。生产效率低,质量不稳定等逐渐淘汰。为解决上述问题20世纪60年代 日本学者(春日保男)提出将液体直接作用于坯料上,强制润滑拉深,这就是现在说的现代充液拉深技术 原型。20世纪70年代进一步发展,1977年,安徽拖拉机厂用该工艺生产了50拖拉机的油底壳,这是我国 首次将该技术应用生产。 目前应用夜拉深技术制造的零件类型有筒形件,锥形件,抛物线件,盒形件以及复杂型面件,设计材 料包括碳钢、高强钢、不锈钢、铝合金等,材料厚度为0.2mm-3.2mm,板材液压成形与普通拉深相比成 形极限和拉深比大。对于低碳钢筒形件最大拉深比达到2.6,不锈钢2.7.铝合金2.5,如果采取特殊工艺还 可进一步提高拉深比。如 调压等 0.3 壳体液压成形技术 1)自从1985年王仲仁教授发明了球形容器无模液压成形技术以来该技术经历了三个发展阶段 壳体结构有平板类多面壳体扩展到单曲率多面壳体。 2)由低压及常压球形容器发展到三类压力容器。 3)有球形壳体扩展到非球形壳体。 图为1992年哈工大王教授采用壳体液压成形技术成功研制 200mm3液化气储罐,直径7.1m,壁厚24mm材 料为低合金钢16MnR,最高工作压力位1.77MPa。(造纸球直径2m,厚12mm,压力供水装置直径2.7m, 厚6mm;通信塔长轴6m、3m,短轴3m、2m)