CNC对刀方法图示
CNC(法兰克)对刀方法图示

序止:果为CNC自己是下速转动板滞,支配大意会制成很大的伤害,所以期视支配人员庄重依照央供做业,出有成马虎.正在每件产品第一件死成出去后,必须通过品检合格后,才不妨继承死产,而后将步调依照整件编号保存佳.一、对于刀前准备处事1、三坐标板滞归整原呆板正在举止所有做业之前必须三坐标板滞归整.2、刀盘换刀① Z坐标归整后,挨至脚动资料输进(参照附图),正在【PROG】MDI环境下输进“M06 TX;”(X为刀号,左下角不妨瞅到).②按【INSERT】键.③按【↑】键.④按绿色开用按钮.依照工艺卡上的央供一一对于应换佳所有刀具.二、X、Y坐标对于刀(普遍情况下皆是二个目标分中对于刀,如果编程分歧,需要单目标对于中,请工艺卡证明)1、换刀为分中棒刀位(时常使用为1号刀位),赋予转速①挨至脚动编程处,正在【PROG】MDI环境下输进“M03S500;”.②按【INSERT】键.③按【↑】键.④按绿色开用按钮.2、X目标觅找中面①通过脚摇支配,分中棒遇到整件X目标的一边.③通过脚摇支配,分中棒遇到整件相对于另一边.④正在POS相对于坐标环境下,记录下X轴目前数值,通过脚摇至目前数值的一半,而后输进“X”,按“起源”(大概者按“X0.”,按“setting”);大概者正在目前位子输进“X+一半目前数值”,按“setting”.⑤正在OFS/SET下坐标系里的G54的X数值处,按“X0.”,按“丈量”,找到目前X为0面时的千万于板滞坐标处.3、Y目标觅找中面①通过脚摇支配,分中棒遇到整件Y目标的一边.②正在POS相对于坐标环境下,输进“Y”,按“起源”(大概者按“Y0.”,按“setting”).③通过脚摇支配,分中棒遇到整件相对于另一边.④正在POS相对于坐标环境下,记录下Y轴目前数值,通过脚摇至目前数值的一半,而后输进“Y”,按“起源”(大概者按“Y0.”,按“setting”);大概者正在目前位子输进“Y+一半目前数值”,按“setting”.⑤正在OFS/SET下坐标系里的G54的Y数值处,按“Y0.”,按“丈量”,找到目前Y为0面时的千万于板滞坐标处.三、Z坐标对于刀(除分中棒除中,每把刀具皆要举止对于刀支配)1、换至任性一把刀具①通过脚摇至取工件出进一把刀位子处(普遍使用φ10刀,那样干预防对于刀时伤害工件表面)③正在OFS/SET下坐标系里的G54的Z数值处,按“Z0.”,按“丈量”,找到目前Z为0面时的千万于板滞坐标处.④正在补偿环境下,正在对于应刀号的形状补偿D下输进“-10”,正在中径补偿D处,输进一半刀具数值(如果刀具是φ8仄铣刀,则输进“”).⑤依照前一把刀具支配办法,对于每一把刀具举止对于刀,正在POS 相对于坐标环境下,记录下目前Z值,正在补偿环境下,正在对于应刀号的形状补偿H下输进“目前值-10”(如目前数值为5,则输进5-10=-5;如果目前值为-8,则输进-8-10=-18),正在中径补偿处,输进一半刀具数值.2、考证Z目标对于刀是可准确①三目标板滞坐标归整②脚动编程环境下输进“GO G90 G54 G43 H(目前刀号) Z10.;”③按【INSERT】键.④按【↑】键.⑤按绿色开用按钮.⑥脚摇工件至刀具处,考证对于刀是可准确.四、正在对于刀中断后,将三坐标板滞归整,所有进给速率调至最矮后,将旋钮挨至中部传输后,按下绿色按钮,等待电脑传输步调,乐成后瞅察呆板支配,有问题坐时停止,出创制问题,则回复央供进给战转速仄常处事.附图脚摇支配脚动编程板滞回整资料传输三坐标板滞回整明灯状态刀具号开用按钮停止按钮步调中断号;补偿战坐标系树坐POS位子隐现PROG步调环境步调确认POS相对于坐标界里脚动编程MDI界里补偿建改界里G54坐标设定界里。
数控车床对刀方法 ppt课件

(假设测量值为37.5)。单击 【录入方式】→ 、 (MDI页面下输入)
→ G50 →
→X37.5(测量的值)→ →【循环启动】。
ppt课件
上一页 下一页
9 返回
(1)在【手动方式】下,换2号刀【切断刀】,单击机床主轴正转,按方向键 将切断刀移到工件端面处轻碰端面,然后单击 、 【向下查找键】将光 标移到002处 → Z0 → 。
入门篇
课题四 对刀方法
ppt课件
1
ppt课件
上一4
ppt课件
上一页 下一页
3 返回
对刀是数控加工中较为复杂的工艺准备工作之一。对刀的好与差将直接影响 到加工程序的编制及零件的尺寸精度。通过对刀或刀具预调,还可同时测定其各 号刀的刀位偏差,有利于设定刀具补偿量。
(1)刀位点
ppt课件
上一页 下一页
10 返回
(2)切削外圆,X方向不动,方向退出→ 主轴停止, 测量(假设测量值为33.75), 然后单击 、 【向下查找键】将光标移到002处→ X33.75→ 。
ppt课件
上一页 下一页
11 返回
当设定偏置量时,如仅键入地址(U、W)后直接按输入键(无数字 键)时,则现在的相对坐标值作为与该地址对应的偏置量而被设置。
(3) 在录入方式下,按程序键,进入“MDI”页面,输入“G00 X(X轴外径 值)”,再按循环启动键,检查刀尖所在的位置是否相符。
ppt课件
上一页 下一页
15 返回
The end,thank you!
ppt课件
16
(3)在录入方式下,按程序键,进入“MDI”页面,输入“G00 X(X轴外 径值)”,再按循环启动键,检查刀尖所在的位置是否相符。
CNC加工中心是如何对刀
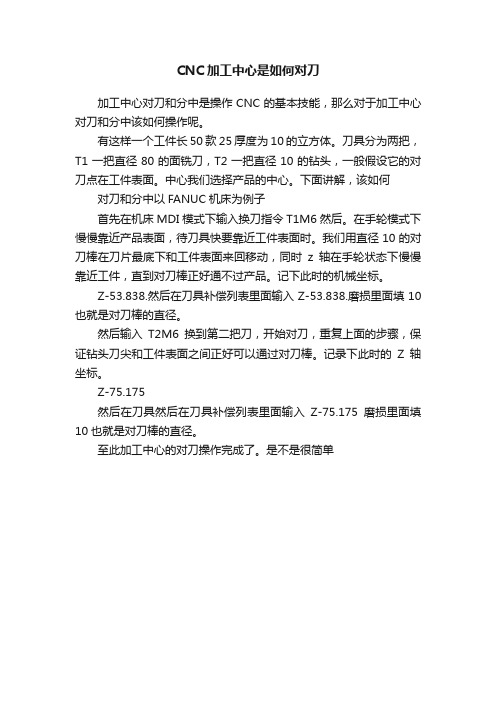
CNC加工中心是如何对刀
加工中心对刀和分中是操作CNC的基本技能,那么对于加工中心对刀和分中该如何操作呢。
有这样一个工件长50款25厚度为10的立方体。
刀具分为两把,T1一把直径80的面铣刀,T2一把直径10的钻头,一般假设它的对刀点在工件表面。
中心我们选择产品的中心。
下面讲解,该如何对刀和分中以FANUC机床为例子
首先在机床MDI模式下输入换刀指令T1M6然后。
在手轮模式下慢慢靠近产品表面,待刀具快要靠近工件表面时。
我们用直径10的对刀棒在刀片最底下和工件表面来回移动,同时z轴在手轮状态下慢慢靠近工件,直到对刀棒正好通不过产品。
记下此时的机械坐标。
Z-53.838.然后在刀具补偿列表里面输入Z-53.838.磨损里面填10也就是对刀棒的直径。
然后输入T2M6换到第二把刀,开始对刀,重复上面的步骤,保证钻头刀尖和工件表面之间正好可以通过对刀棒。
记录下此时的Z轴坐标。
Z-75.175
然后在刀具然后在刀具补偿列表里面输入Z-75.175磨损里面填10也就是对刀棒的直径。
至此加工中心的对刀操作完成了。
是不是很简单。
数控车床对刀步骤
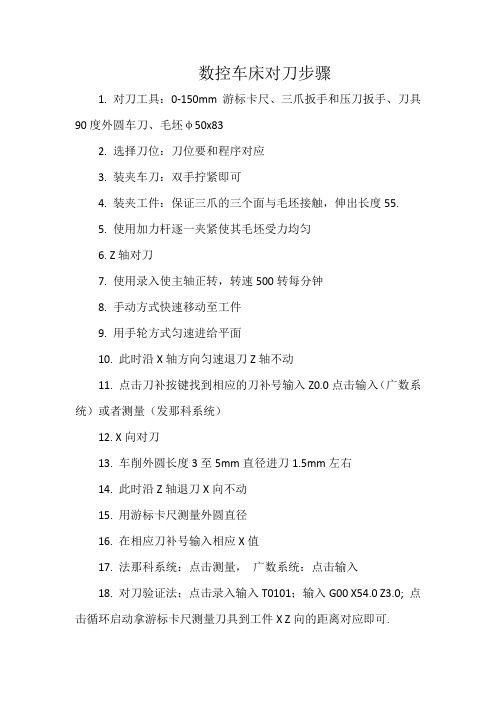
数控车床对刀步骤
1. 对刀工具:0-150mm游标卡尺、三爪扳手和压刀扳手、刀具90度外圆车刀、毛坯φ50x83
2. 选择刀位:刀位要和程序对应
3. 装夹车刀:双手拧紧即可
4. 装夹工件:保证三爪的三个面与毛坯接触,伸出长度5
5.
5. 使用加力杆逐一夹紧使其毛坯受力均匀
6. Z轴对刀
7. 使用录入使主轴正转,转速500转每分钟
8. 手动方式快速移动至工件
9. 用手轮方式匀速进给平面
10. 此时沿X轴方向匀速退刀Z轴不动
11. 点击刀补按键找到相应的刀补号输入Z0.0点击输入(广数系统)或者测量(发那科系统)
12. X向对刀
13. 车削外圆长度3至5mm直径进刀1.5mm左右
14. 此时沿Z轴退刀X向不动
15. 用游标卡尺测量外圆直径
16. 在相应刀补号输入相应X值
17. 法那科系统:点击测量,广数系统:点击输入
18. 对刀验证法:点击录入输入T0101;输入G00 X54.0 Z3.0; 点击循环启动拿游标卡尺测量刀具到工件X Z向的距离对应即可.。
CNC2000系统对刀操作

CNC2000系统对刀操作使用两把以上刀具的时候就需要对刀。
对刀的目的就是确保换刀后每把刀的切削点都在同一位置。
为保证准确快速对刀,请按以下步骤进行:1)将一任意大小棒料(最好是外圆和端面均已车削的)夹在卡盘上,作为基准用。
2)将需要对刀的刀尖移动到棒料外圆表面和端面处(实际是棒料的边缘),按一次“5”再按“Enter”确认键,系统即自动记忆当前刀尖的坐标位置。
3)将刀具让出一定距离,换至下一刀位,将此刀具如步骤2)移动到外圆表面和端面处(即与上把刀的刀尖重合),按一次“5”再按“Enter”确认键,系统自动记忆当前刀尖的坐标位置。
4)重复步骤3)的操作,依次将余下的刀具对好。
通过以上4个步骤即可简单地将数把刀具对好(整个对刀过程可以不进行任何切削,也不需要向数控系统输入数据),系统自动记忆每把刀尖的实际位置。
系统的记忆值存储在内存芯片中,操作人员无法看见。
在“自动”状态下,当执行换刀指令时,系统自动补偿刀尖之间的坐标差值。
在实际加工过程中经常遇到多把刀中的某一把损坏的情况,这时对某一把刀可按以下步骤进行:1)将一任意大小棒料(最好是外圆和端面均已车削)夹在卡盘上,作基准点用。
2)将任意一把未损坏的刀具(作基准刀)移动到棒料外圆表面和端面处(实际是棒料的边缘),按一次“5”(对刀)再按“T”键,系统便自动记忆当前刀尖的坐标值。
3)将刀具移动至不撞刀位置,按换刀键选择要对的刀尖,用新换(或新磨)的刀尖去接触棒料外圆表面和端面处,按一次“5”再按“Enter”确认键即可。
4)多把刀损坏时也可重复3)的操作,依次对完。
以上的对刀方式可能存在误差,对刀结束后,操作者需要通过“参数”状态中的“刀补”值进行修正,以免加工出废品。
华中数控对刀过程(配图版)

华中数控对刀过程(配图版)1、开机。
(总电源总闸,机床后侧电闸)2、机械回零。
(开机必须回零,否则运行程序时会报警)方法:预先用手轮将刀具停放在工件的中心正上方略高位置,按[回参考点]→按[+Z]→按[+X]→按[+Y]→机床一般会先快递再慢速接近回零位置→耐心等待[+Z][+X][+Y]零点灯全部亮起则完成回零工作。
3、对刀:1)对X轴:步骤刀具位置机床面板第一步:[手轮]灯亮用手轮用X100档将铣刀移近工件左侧,再用X10档碰触注意有铝屑飞出即可。
第二步:X相对坐标清零[设置F5]→[相对清零F8]→[x轴清零F1] →[F10返回]第三步:将铣刀+Z提起,并移到工件右侧,同第一步方法碰触。
第四步:观察此时相对坐标x的数值(如右图中为120。
443),将这个数除以2就是x轴原点。
用手轮将移铣刀至这个数(图中例就是移到60.221)处。
第五步:X坐标清零确定.按[x轴清零F1],可见x相对实际坐标变成零。
2)同样方法对Y轴:碰后侧Y清零,碰前侧读数,移至除2处,再将Y清零。
3)对Z轴:第一步:[增量]灯亮用手轮将铣刀下移贴住工件上表面.第二步:Z相对坐标清零确定.4)G54抄数:按[坐标系设定F1]→[G54坐标系F1]→进入自动坐标系G54画面。
在坐标值中输入机床坐标系中的XYZ数值后enter回车。
5)G54确定。
按两次[返回F10]进入主菜单画面.按[MDI F3]进入“MDI运行画面”.按[单段]按钮灯亮,在“MDI 运行”中输入“G54”按循环启动按钮。
则对刀完成。
此时可按[返回F10]进入主菜单画面,再[显示切换F10],观察机床现在的机床坐标全部变成0.如下图所示:6)对刀校验。
第一步,用手轮摇开铣刀(随意远离位置)。
第二步,在主菜单画面。
按[MDI F3]进入“MDI运行画面”。
按[单段]按钮灯亮,在“MDI运行"中输入“G1X0Y0F500”按循环启动按钮。
按[循环启动]。
数控车床的对刀与刀具补偿(附图)

数控车床的对刀与刀具补偿(附图)一、对刀对刀的目的是确定程序原点在机床坐标系中的位置,对刀点可以设在零件上、夹具上或机床上,对刀时应使对刀点与刀位点重合。
数控车床常用的对刀方法有三种:试切对刀、机械对刀仪对刀(接触式)、光学对刀仪对刀(非接触式),如图3-9 所示。
1、试切对刀1 )外径刀的对刀方法如图3-10 所示。
Z 向对刀如(a) 所示。
先用外径刀将工件端面( 基准面) 车削出来;车削端面后,刀具可以沿X 方向移动远离工件,但不可Z 方向移动。
Z 轴对刀输入:“Z0 测量”。
X 向对刀如(b) 所示。
车削任一外径后,使刀具Z 向移动远离工件,待主轴停止转动后,测量刚刚车削出来的外径尺寸。
例如,测量值为Φ50.78mm, 则X 轴对刀输入:“X50.78 测量”。
2 )内孔刀的对刀方法类似外径刀的对刀方法。
Z 向对刀内孔车刀轻微接触到己加工好的基准面(端面)后,就不可再作Z 向移动。
Z 轴对刀输入:“Z0 测量”。
X 向对刀任意车削一内孔直径后,Z 向移动刀具远离工件,停止主轴转动,然后测量已车削好的内径尺寸。
例如,测量值为Φ45.56mm, 则X 轴对刀输入:“X45.56 测量”。
3 )钻头、中心钻的对刀方法如图3-11 所示。
Z 向对刀如(a )所示。
钻头( 或中心钻) 轻微接触到基准面后,就不可再作Z 向移动。
Z 轴对刀输入:“Z0 测量”。
X 向对刀如(b )所示。
主轴不必转动,以手动方式将钻头沿X 轴移动到钻孔中心,即看屏幕显示的机械坐标到“X0.0 ”为止。
X 轴对刀输入:“X0 测量”。
2、机械对刀仪对刀将刀具的刀尖与对刀仪的百分表测头接触,得到两个方向的刀偏量。
有的机床具有刀具探测功能,即通过机床上的对刀仪测头测量刀偏量。
3、光学对刀仪对刀将刀具刀尖对准刀镜的十字线中心,以十字线中心为基准,得到各把刀的刀偏量。
二、刀具补偿值的输入和修改根据刀具的实际参数和位置,将刀尖圆弧半径补偿值和刀具几何磨损补偿值输入到与程序对应的存储位置。
数控车床的对刀方法

数控车床的对刀方法一、对刀的基本概念对刀是数控加工中较为复杂的工艺准备工作之一,对刀的好与差将直接影响到加工程序的编制及零件的尺寸精度。
通过对刀或者刀具预调,还可同时测定其各号刀的刀位偏差,有利于设定刀具补偿量。
1 刀位点刀位点是指在加工程序编制中,用以表示刀具特征的点,也是对刀与加工的基准点。
关于车刀,各类车刀的刀位点见下图:2 对刀对刀是数控加工中的要紧操作。
结合机床操作说明掌握有关对刀方法与技巧,具有十分重要的竟义。
在加工程序执行前,调整每把刀的刀位点,使其尽量重合于某一理想基准点,这一过程称之对刀。
理想基准点能够设定在刀具上,如基准刀的刀尖上;也能够设定在刀具外,如光学对刀镜内的十字刻线交点上。
二、对刀的基本方法目前绝大多数的数控车床使用手动对刀,其基本方法有下列几种:1 定位对刀法定位对刀法的实质是按接触式设定基准重合原理而进行的一种粗定位对刀方法,其定位基准由预设的对刀基准点来表达。
对刀时,只要将各号刀的刀位点调整至与对刀基准点重合即可。
该方法简便易行,因而得到较广泛的应用,但其对刀精度受到操者技术熟练程度的影响,通常情况下其精度都不高,还须在加工或者试切中修正。
2 光学对刀法这是一种按非接触式设定基准重合原理而进行的对刀方法,其定位基准通常由光学显微镜(或者投影放大镜)上的十字基准刻线交点来表达。
这种对刀方法比定位对刀法的对刀精度高,同时不可能损坏刀尖,是一种推广使用的方法。
3 试切对刀法在以上各类手动对刀方法中,均因可能受到手动与目测等多种误差的影响以至其对刀精度十分有限,往往需要通过试切对刀,以得到更加准确与可靠的结果。
a、直接用刀具试切对刀(FANUC series oi mate TB系统)1) 用外圆车刀先试切一外圆,测量外圆直径后,按→→输入“外圆直径值”,按键,刀具“X”补偿值即自动输入到几何形状里。
2) 用外圆车刀再试切外圆端面,按→→输入“Z 0”,按键,刀具“Z”补偿值即自动输入到几何形状里。
数控机床怎么对刀【图解】
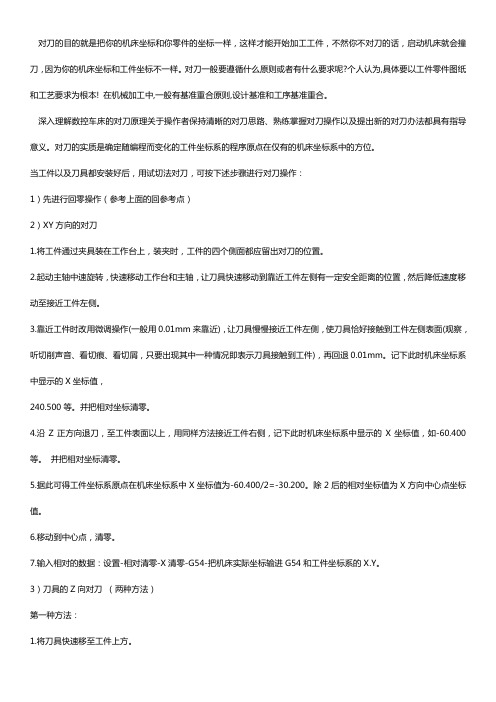
对刀的目的就是把你的机床坐标和你零件的坐标一样,这样才能开始加工工件,不然你不对刀的话,启动机床就会撞刀,因为你的机床坐标和工件坐标不一样。
对刀一般要遵循什么原则或者有什么要求呢?个人认为,具体要以工件零件图纸和工艺要求为根本! 在机械加工中,一般有基准重合原则,设计基准和工序基准重合。
深入理解数控车床的对刀原理关于操作者保持清晰的对刀思路、熟练掌握对刀操作以及提出新的对刀办法都具有指导意义。
对刀的实质是确定随编程而变化的工件坐标系的程序原点在仅有的机床坐标系中的方位。
当工件以及刀具都安装好后,用试切法对刀,可按下述步骤进行对刀操作:1)先进行回零操作(参考上面的回参考点)2)XY方向的对刀1.将工件通过夹具装在工作台上,装夹时,工件的四个侧面都应留出对刀的位置。
2.起动主轴中速旋转,快速移动工作台和主轴,让刀具快速移动到靠近工件左侧有一定安全距离的位置,然后降低速度移动至接近工件左侧。
3.靠近工件时改用微调操作(一般用0.01mm来靠近),让刀具慢慢接近工件左侧,使刀具恰好接触到工件左侧表面(观察,听切削声音、看切痕、看切屑,只要出现其中一种情况即表示刀具接触到工件),再回退0.01mm。
记下此时机床坐标系中显示的X坐标值,240.500等。
并把相对坐标清零。
4.沿Z正方向退刀,至工件表面以上,用同样方法接近工件右侧,记下此时机床坐标系中显示的X坐标值,如-60.400等。
并把相对坐标清零。
5.据此可得工件坐标系原点在机床坐标系中X坐标值为-60.400/2=-30.200。
除2后的相对坐标值为X方向中心点坐标值。
6.移动到中心点,清零。
7.输入相对的数据:设置-相对清零-X清零-G54-把机床实际坐标输进G54和工件坐标系的X.Y。
3)刀具的Z向对刀(两种方法)第一种方法:1.将刀具快速移至工件上方。
2.起动主轴中速旋转,移动工作台和主轴,让刀具移动到靠近工件上表面有一定安全距离的位置,然后降低速度移动让刀具端面接近工件上表面.3.靠近工件时改用微调操作(一般用0.01mm来靠近),让刀具端面慢慢接近工件表面,使刀具端面恰好碰到工件上表面,再将Z轴再抬高0.01mm,记下此时机床坐标系中的Z值,如-140.400等,则机床坐标系中的Z坐标值为-140.400。
CNC(法兰克)对刀方法图示
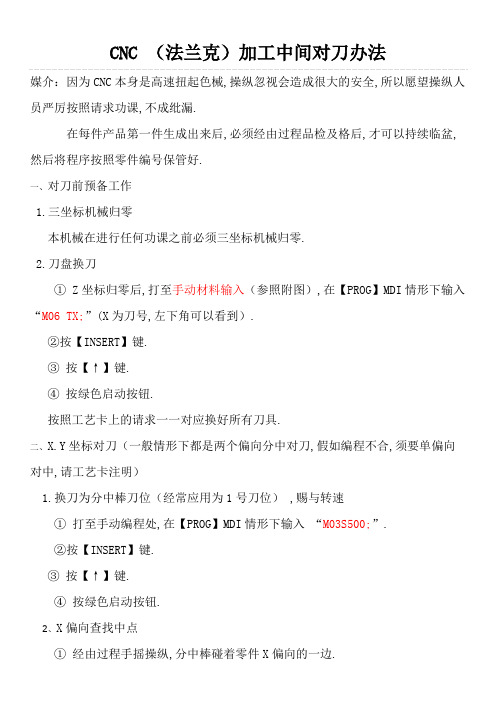
媒介:因为CNC本身是高速扭起色械,操纵忽视会造成很大的安全,所以愿望操纵人员严厉按照请求功课,不成纰漏.在每件产品第一件生成出来后,必须经由过程品检及格后,才可以持续临盆,然后将程序按照零件编号保管好.一、对刀前预备工作1.三坐标机械归零本机械在进行任何功课之前必须三坐标机械归零.2.刀盘换刀① Z坐标归零后,打至手动材料输入(参照附图),在【PROG】MDI情形下输入“M06 TX;”(X为刀号,左下角可以看到).②按【INSERT】键.③按【↑】键.④按绿色启动按钮.按照工艺卡上的请求一一对应换好所有刀具.二、X.Y坐标对刀(一般情形下都是两个偏向分中对刀,假如编程不合,须要单偏向对中,请工艺卡注明)1.换刀为分中棒刀位(经常应用为1号刀位) ,赐与转速①打至手动编程处,在【PROG】MDI情形下输入“M03S500;”.②按【INSERT】键.③按【↑】键.④按绿色启动按钮.2、X偏向查找中点①经由过程手摇操纵,分中棒碰着零件X偏向的一边.②在POS相对坐标情形下,输入“X”,按“来源”(或者按“X0.”,按“setting”).③经由过程手摇操纵,分中棒碰着零件相对另一边.④在POS相对坐标情形下,记载下X轴当前数值,经由过程手摇至当前数值的一半,然后输入“X”,按“来源”(或者按“X0.”,按“setting”);或者在当前地位输入“X+一半当前数值”,按“setting”.⑤在OFS/SET下坐标系里的G54的X数值处,按“X0.”,按“测量”,找到当前X为0点时的绝对机械坐标处.3.Y偏向查找中点①经由过程手摇操纵,分中棒碰着零件Y偏向的一边.②在POS相对坐标情形下,输入“Y”,按“来源”(或者按“Y0.”,按“setting”).③经由过程手摇操纵,分中棒碰着零件相对另一边.④在POS相对坐标情形下,记载下Y轴当前数值,经由过程手摇至当前数值的一半,然后输入“Y”,按“来源”(或者按“Y0.”,按“setting”);或者在当前地位输入“Y+一半当前数值”,按“setting”.⑤在OFS/SET下坐标系里的G54的Y数值处,按“Y0.”,按“测量”,找到当前Y为0点时的绝对机械坐标处.三.Z坐标对刀(除分中棒之外,每把刀具都要进行对刀操纵)1.换至随意率性一把刀具①经由过程手摇至与工件相差一把刀地位处(一般应用φ10刀,如许做防止对刀时损害工件概况)②在POS相对坐标情形下,输入“Z”,按“来源”(或者按“Z0.”,按“setting”).③在OFS/SET下坐标系里的G54的Z数值处,按“Z0.”,按“测量”,找到当前Z为0点时的绝对机械坐标处.④在抵偿情形下,在对应刀号的外形抵偿D下输入“-10”,在外径抵偿D处,输入一半刀具数值(假如刀具是φ8平铣刀,则输入“”).⑤按照前一把刀具操纵方法,对每一把刀具进行对刀,在POS相对坐标情形下,记载下当前Z值,在抵偿情形下,在对应刀号的外形抵偿H下输入“当前值-10”(如当前数值为5,则输入5-10=-5;假如当前值为-8,则输入-8-10=-18),在外径抵偿处,输入一半刀具数值.2、验证Z偏向对刀是否精确①三偏向机械坐标归零②手动编程情形下输入“GO G90 G54 G43 H(当前刀号) Z10.;”③按【INSERT】键.④按【↑】键.⑤按绿色启动按钮.⑥手摇工件至刀具处,验证对刀是否精确.四.在对刀停滞后,将三坐标机械归零,所有进给速度调至最低后,将旋钮打至外部传输后,按下绿色按钮,等待电脑传输程序,成功后不雅察机械操纵,有问题立刻停滞,没发明问题,则恢复请求进给和转速正常工作.附图手摇操纵手动编程机械回零材料传输三坐标机械回零亮灯状况刀具号启动按钮停滞按钮抵偿和坐标系设置POS地位显示PROG程序情形程序确认POS相对坐标界面手动编程MDI界面抵偿修正界面G54坐标设定界面。
超实用的加工中心对刀方法
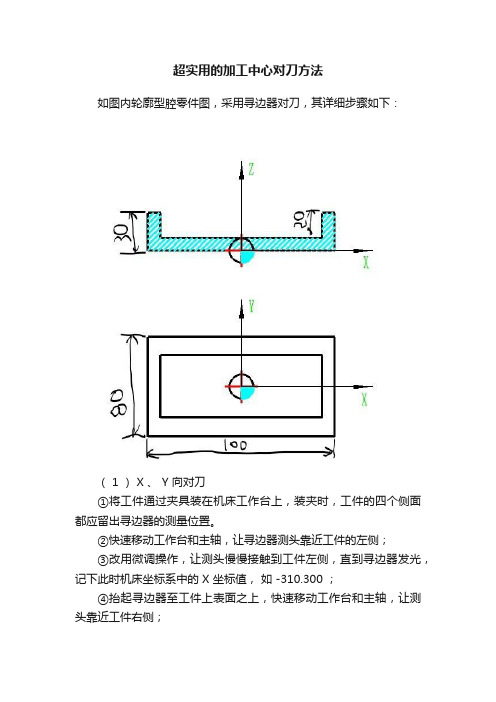
超实用的加工中心对刀方法如图内轮廓型腔零件图,采用寻边器对刀,其详细步骤如下:( 1 ) X 、 Y 向对刀①将工件通过夹具装在机床工作台上,装夹时,工件的四个侧面都应留出寻边器的测量位置。
②快速移动工作台和主轴,让寻边器测头靠近工件的左侧;③改用微调操作,让测头慢慢接触到工件左侧,直到寻边器发光,记下此时机床坐标系中的 X 坐标值,如 -310.300 ;④抬起寻边器至工件上表面之上,快速移动工作台和主轴,让测头靠近工件右侧;⑤改用微调操作,让测头慢慢接触到工件左侧,直到寻边器发光,记下此时机械坐标系中的 X 坐标值,如 -200.300 ;⑥若测头直径为 10mm ,则工件长度为 -200.300-(-310.300)-10=100 ,据此可得工件坐标系原点 W 在机床坐标系中的 X 坐标值为 -310.300+100/2+5= -255.300 ;⑦同理可测得工件坐标系原点 W 在机械坐标系中的 Y 坐标值。
( 2 ) Z 向对刀①卸下寻边器,将加工所用刀具装上主轴;②将Z 轴设定器(或固定高度的对刀块,以下同)放置在工件上平面上;③快速移动主轴,让刀具端面靠近 Z 轴设定器上表面;④改用微调操作,让刀具端面慢慢接触到Z 轴设定器上表面,直到其指针指示到零位;⑤记下此时机床坐标系中的 Z 值,如 -250.800 ;⑥若 Z 轴设定器的高度为 50mm ,则工件坐标系原点 W 在机械坐标系中的 Z 坐标值为 -250.800-50-( 30-20)=-310.800 。
( 3 )将测得的 X 、 Y 、 Z 值输入到机床工件坐标系存储地址中(一般使用 G54-G59 代码存储对刀参数)。
4、注意事项在对刀操作过程中需注意以下问题:( 1 )根据加工要求采用正确的对刀工具,控制对刀误差;( 2 )在对刀过程中,可通过改变微调进给量来提高对刀精度;(3 )对刀时需小心谨慎操作,尤其要注意移动方向,避免发生碰撞危险;(4 )对刀数据一定要存入与程序对应的存储地址,防止因调用错误而产生严重后果。
数控铣床(加工中心)常见对刀方法
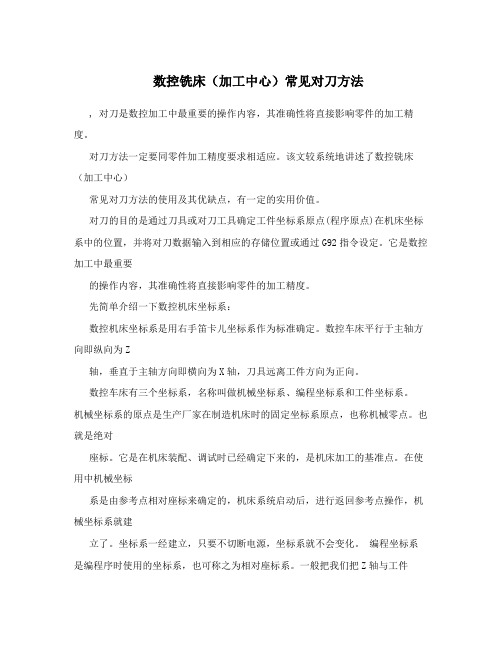
数控铣床(加工中心)常见对刀方法, 对刀是数控加工中最重要的操作内容,其准确性将直接影响零件的加工精度。
对刀方法一定要同零件加工精度要求相适应。
该文较系统地讲述了数控铣床(加工中心)常见对刀方法的使用及其优缺点,有一定的实用价值。
对刀的目的是通过刀具或对刀工具确定工件坐标系原点(程序原点)在机床坐标系中的位置,并将对刀数据输入到相应的存储位置或通过G92指令设定。
它是数控加工中最重要的操作内容,其准确性将直接影响零件的加工精度。
先简单介绍一下数控机床坐标系:数控机床坐标系是用右手笛卡儿坐标系作为标准确定。
数控车床平行于主轴方向即纵向为Z轴,垂直于主轴方向即横向为X轴,刀具远离工件方向为正向。
数控车床有三个坐标系,名称叫做机械坐标系、编程坐标系和工件坐标系。
机械坐标系的原点是生产厂家在制造机床时的固定坐标系原点,也称机械零点。
也就是绝对座标。
它是在机床装配、调试时已经确定下来的,是机床加工的基准点。
在使用中机械坐标系是由参考点相对座标来确定的,机床系统启动后,进行返回参考点操作,机械坐标系就建立了。
坐标系一经建立,只要不切断电源,坐标系就不会变化。
编程坐标系是编程序时使用的坐标系,也可称之为相对座标系。
一般把我们把Z轴与工件轴线重合,X轴放在工件端面上。
工件坐标系是机床进行加工时使用的坐标系,它应该与编程坐标系一致。
能否让编程坐标系与工坐标系一致,使操作的关键。
工件坐标系建立是通过系统的程序语句设定刀具当前所在位置的坐标值来确定。
加工前需要先对刀,对刀后将显示坐标清零,对其他刀时将显示的坐标值写入相应刀补参数。
然后测量出对刀直径Фd,将刀移动到坐标显示X=a-d Z=b 的位置,就可以运行程序了。
在加工过程中按复位或急停健,可以再回到设定的起点继续加工。
但如果出意外如:X或Z轴无伺服、跟踪出错、断电等情况发生,系统只能重启,重启后设定的工件坐标系将消失,需要重新对刀。
因而工件座标也可说是相对座标体系。
数控技术之数控铣床对刀要点(ppt 57页)

华中数控铣床对刀要点
1、铣床的一把刀对刀 2、多刀如何对刀? 3、铣床与车床建立工件坐标系的区别?
知识点
• 分清机床坐标系与工件坐标系的区别 • 分清G92与G54~59的区别 • 分清铣床中XY与Z轴对刀的不同。
铣床的对刀
1、单刀之对刀
1、X轴对刀 试切法 法一:将刀具在工件的X或Y的两边试切对齐,记 下分别的机床坐标系下的数据,如X1,X2,则 X=(X1+X2)/2。此X值即为G54之X值。 法二:只要对一边,记下X1,按公式计算。
T0101
;X和Z偏置有效。
G00X10Z35 ;X坐标移动到机床坐
标系中的10+(-400)处
Z移动到何处?
T指令与G54
G54是将同样的偏置写到G54的坐标上。 T是将同样的偏置写到刀具补偿的坐标上。
G54
比较二程序:
%1 T0101 G00X50 Z5 M03S400 …
%2 T0100 G00X(50+offsetX) Z(5+offsetZ) M03S400 …
T0101,表示一号刀之一号刀补,一号 刀补有什么内容,表示什么意思?
偏置补偿
绝对补偿
偏置
T指令
此时,机床回零,刀尖处于 机床坐标系的(0,0)位。
T
此时,刀具处于程序原点上,不能说 是工件坐标系的(0,0)位。
T指令与G54
现在,我们只要将这个机床坐标系原点与编程 原点的距离测量出来,便可以建立二者的补 偿关系。例如,X偏置为-400,Z为-500:
切削刃成螺旋状分布 在圆柱表面上,两端面 无切削刃。
常用来在卧式铣床上 加工平面,多用高速钢 整体制造,也可以镶焊 硬质合金刀条。
CNC(法兰克)加工中心对刀的方法

加工中心的对刀方法1. 加工中心的Z向对刀加工中心的Z向对刀一般有以下三种方法:1) 机上对刀方法一这种对刀方法是通过对刀依次确定每把刀具与工件在机床坐标系中的相互位置关系。
其具体操作步骤如下(如图9-16所示)。
(1) 把刀具长度进行比较,找出最长的刀作为基准刀,进行Z向对刀,并把此时的对刀值(C)作为工件坐标系的Z值,此时H03=0。
(2) 把T01、T02号刀具依次装在主轴,通过对刀确定A、B的值作为长度补偿值。
(此方法没有直接去测量刀具补偿,而是通过依次对刀确定的与方法三不同.)(3) 把确定的长度补偿值(最长刀长度减其余刀具长度)填入设定页面,正、负号由程序中的G43、G44来确定,此时一般用G44H—表示。
当采用G43时,长度补偿为负值。
这种对刀方法的对刀效率和精度较高,投资少,但工艺文件编写不便,对生产组织有一定影响。
2) 机上对刀方法二这种对刀方法的具体操作步骤如下(见图9-16):(1) ?XY方向找正设定如前,将G54中的XY项输入偏置值,Z项置零。
(2) 将用于加工的T1换上主轴,用块规找正Z向,松紧合适后读取机床坐标系Z项值Z1,扣除块规高度后,填入长度补偿值H1中。
(3) 将T2装上主轴,用块规找正,读取Z2,扣除块规高度后填入H2中。
(4) 依次类推,将所有刀具Ti用块规找正,将Zi扣除块规高度后填入Hi中。
(5) 编程时,采用如下方法补偿:T1;G91 G30 Z0;M06;G43 H1;G90 G54 G00 X0 Y0;Z100;…(以下为一号刀具的走刀加工,直至结束)T2;G91 G30 Z0;M06;G43 H2;G90 G54 G00 X0 Y0;Z100;…(二号刀的全部加工内容) (5)M30;3) 机外刀具预调+机上对刀这种对刀方法是先在机床外利用刀具预调仪精确测量每把刀具的轴向和径向尺寸,确定每把刀具的长度补偿值,然后在机床上用最长的一把刀具进行Z向对刀,确定工件坐标系。
数控机床对刀方法

对刀口诀“平断面,输Z0;车外圆,输直径”对刀步骤FANUC系统:一号刀:Z:平端面——切换界面OFFSET——补正——形状补正——在01刀补一行输入Z0——按测量(注意:平完端面退刀只能退X方向即竖着退)X:车外圆——退刀(只退Z轴)——停车测量刚车过的外圆直径——在01刀补一行输入X(直径值)——按测量(注意:切完外圆退刀只能退Z方向即横着退)二号刀:Z:靠端面(注:不能切端面,因为编程原点已定在端面上)——形状补正——在02刀补一行输入Z0——按测量X:车外圆——退刀(只退Z轴)——停车测量刚车过的外圆直径——在02刀补一行输入X(直径值)——按测量三号刀:Z:目测刀尖与端面对齐——形状补正——在03刀补一行输入Z0——按测量X:车外圆——退刀(只退Z轴)——停车测量刚车过的外圆直径——在03刀补一行输入X(直径值)——按测量西门子系统:一号刀:Z;切端面——单击,切换到“测量刀具界面”,然后点击软键,点击,切换到测量Z的界面,在“Z0”后的输入框中填写“0”,按下键,单击软键;完成了Z方向上的刀具参数设置,X;试切零件外圆,并测量被切的外圆的直径;按长度1将所测得的直径值写入后的输入框内,按下键,依次单击、,二号刀:将2号刀切换为当前刀具,换刀的具体过程是:点击按钮,进入到MDA模式,输入换刀指令“T2D1”,然后依次点击和来运行MDA程序;运行完毕之后,第二把刀被换为当前刀具。
Z:靠断面(注:不能切断面,因为编程原点已定在端面上依次点击、将光标停在“Z0”栏中输入“0”,并按下键,单击软键;X:试切零件外圆,并且测量被切削的外圆的直径;将所测得的直径值写入后的输入框内,按下键,依次单击、,其他刀具,都可以使用如上的方法进行对刀。
CNC对刀方法图示
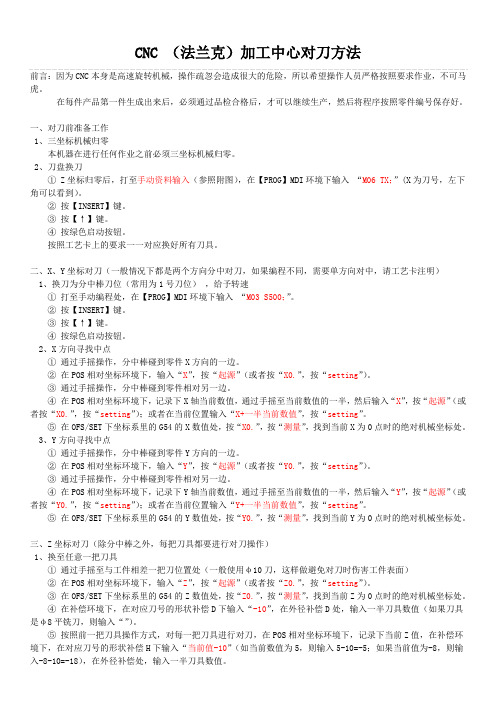
前言:因为CNC本身是高速旋转机械,操作疏忽会造成很大的危险,所以希望操作人员严格按照要求作业,不可马虎。
在每件产品第一件生成出来后,必须通过品检合格后,才可以继续生产,然后将程序按照零件编号保存好。
一、对刀前准备工作1、三坐标机械归零本机器在进行任何作业之前必须三坐标机械归零。
2、刀盘换刀① Z坐标归零后,打至手动资料输入(参照附图),在【PROG】MDI环境下输入“M06 TX;”(X为刀号,左下角可以看到)。
②按【INSERT】键。
③按【↑】键。
④按绿色启动按钮。
按照工艺卡上的要求一一对应换好所有刀具。
二、X、Y坐标对刀(一般情况下都是两个方向分中对刀,如果编程不同,需要单方向对中,请工艺卡注明)1、换刀为分中棒刀位(常用为1号刀位),给予转速①打至手动编程处,在【PROG】MDI环境下输入“M03S500;”。
②按【INSERT】键。
③按【↑】键。
④按绿色启动按钮。
2、X方向寻找中点①通过手摇操作,分中棒碰到零件X方向的一边。
②在POS相对坐标环境下,输入“X”,按“起源”(或者按“X0.”,按“setting”)。
③通过手摇操作,分中棒碰到零件相对另一边。
④在POS相对坐标环境下,记录下X轴当前数值,通过手摇至当前数值的一半,然后输入“X”,按“起源”(或者按“X0.”,按“setting”);或者在当前位置输入“X+一半当前数值”,按“setting”。
⑤在OFS/SET下坐标系里的G54的X数值处,按“X0.”,按“测量”,找到当前X为0点时的绝对机械坐标处。
3、Y方向寻找中点①通过手摇操作,分中棒碰到零件Y方向的一边。
②在POS相对坐标环境下,输入“Y”,按“起源”(或者按“Y0.”,按“setting”)。
③通过手摇操作,分中棒碰到零件相对另一边。
④在POS相对坐标环境下,记录下Y轴当前数值,通过手摇至当前数值的一半,然后输入“Y”,按“起源”(或者按“Y0.”,按“setting”);或者在当前位置输入“Y+一半当前数值”,按“setting”。
- 1、下载文档前请自行甄别文档内容的完整性,平台不提供额外的编辑、内容补充、找答案等附加服务。
- 2、"仅部分预览"的文档,不可在线预览部分如存在完整性等问题,可反馈申请退款(可完整预览的文档不适用该条件!)。
- 3、如文档侵犯您的权益,请联系客服反馈,我们会尽快为您处理(人工客服工作时间:9:00-18:30)。
前言:因为CNC本身是高速旋转机械,操作疏忽会造成很大的危险,所以希望操作人员严格按照要求作业,不可马虎。
在每件产品第一件生成出来后,必须通过品检合格后,才可以继续生产,然后将程序按照零件编号保存好。
一、对刀前准备工作
1、三坐标机械归零
本机器在进行任何作业之前必须三坐标机械归零。
2、刀盘换刀
① Z坐标归零后,打至手动资料输入(参照附图),在【PROG】MDI环境下输入“M06 TX;”(X为刀号,左下角可以看到)。
②按【INSERT】键。
③按【↑】键。
④按绿色启动按钮。
按照工艺卡上的要求一一对应换好所有刀具。
二、X、Y坐标对刀(一般情况下都是两个方向分中对刀,如果编程不同,需要单方向对中,请工艺卡注明)
1、换刀为分中棒刀位(常用为1号刀位),给予转速
①打至手动编程处,在【PROG】MDI环境下输入“M03S500;”。
②按【INSERT】键。
③按【↑】键。
④按绿色启动按钮。
2、X方向寻找中点
①通过手摇操作,分中棒碰到零件X方向的一边。
②在POS相对坐标环境下,输入“X”,按“起源”(或者按“X0.”,按“setting”)。
③通过手摇操作,分中棒碰到零件相对另一边。
④在POS相对坐标环境下,记录下X轴当前数值,通过手摇至当前数值的一半,然后输入“X”,按“起源”(或者按“X0.”,按“setting”);或者在当前位置输入“X+一半当前数值”,按“setting”。
⑤在OFS/SET下坐标系里的G54的X数值处,按“X0.”,按“测量”,找到当前X为0点时的绝对机械坐标处。
3、Y方向寻找中点
①通过手摇操作,分中棒碰到零件Y方向的一边。
②在POS相对坐标环境下,输入“Y”,按“起源”(或者按“Y0.”,按“setting”)。
③通过手摇操作,分中棒碰到零件相对另一边。
④在POS相对坐标环境下,记录下Y轴当前数值,通过手摇至当前数值的一半,然后输入“Y”,按“起源”(或者按“Y0.”,按“setting”);或者在当前位置输入“Y+一半当前数值”,按“setting”。
⑤在OFS/SET下坐标系里的G54的Y数值处,按“Y0.”,按“测量”,找到当前Y为0点时的绝对机械坐标处。
三、Z坐标对刀(除分中棒之外,每把刀具都要进行对刀操作)
1、换至任意一把刀具
①通过手摇至与工件相差一把刀位置处(一般使用φ10刀,这样做避免对刀时伤害工件表面)
②在POS相对坐标环境下,输入“Z”,按“起源”(或者按“Z0.”,按“setting”)。
③在OFS/SET下坐标系里的G54的Z数值处,按“Z0.”,按“测量”,找到当前Z为0点时的绝对机械坐标处。
④在补偿环境下,在对应刀号的形状补偿D下输入“-10”,在外径补偿D处,输入一半刀具数值(如果刀具是φ8平铣刀,则输入“”)。
⑤按照前一把刀具操作方式,对每一把刀具进行对刀,在POS相对坐标环境下,记录下当前Z值,在补偿环境下,在对应刀号的形状补偿H下输入“当前值-10”(如当前数值为5,则输入5-10=-5;如果当前值为-8,则输入-8-10=-18),在外径补偿处,输入一半刀具数值。
2、验证Z方向对刀是否准确
①三方向机械坐标归零
②手动编程环境下输入“GO G90 G54 G43 H(当前刀号) Z10.;”
③按【INSERT】键。
④按【↑】键。
⑤按绿色启动按钮。
⑥手摇工件至刀具处,验证对刀是否准确。
四、在对刀结束后,将三坐标机械归零,所有进给速率调至最低后,将旋钮打至外部传输后,按下绿色按钮,等待电脑传输程序,成功后观察机器操作,有问题立即停止,没发现问题,则恢复要求进给和转速正常工作。
附图
手摇操作手动编程
机械回零资料传输三坐标机械回零亮灯状态
刀具号启动按钮停止按钮
PROG程序环境程序确认
POS相对坐标界面
手动编程MDI界面
补偿修改界面G54坐标设定界面。