连铸
连铸生产工艺流程
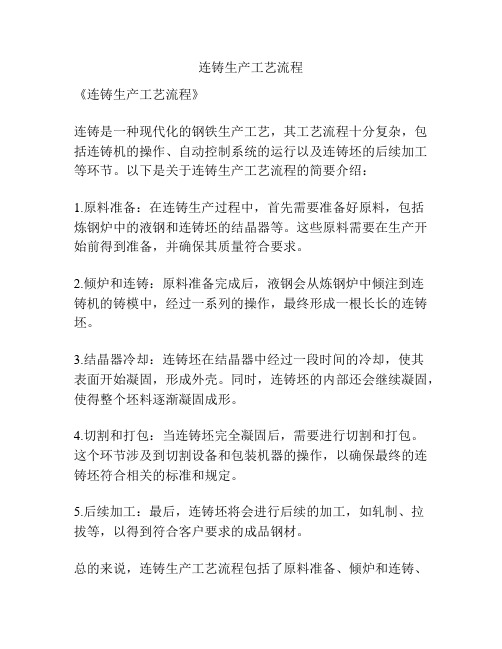
连铸生产工艺流程
《连铸生产工艺流程》
连铸是一种现代化的钢铁生产工艺,其工艺流程十分复杂,包括连铸机的操作、自动控制系统的运行以及连铸坯的后续加工等环节。
以下是关于连铸生产工艺流程的简要介绍:
1.原料准备:在连铸生产过程中,首先需要准备好原料,包括
炼钢炉中的液钢和连铸坯的结晶器等。
这些原料需要在生产开始前得到准备,并确保其质量符合要求。
2.倾炉和连铸:原料准备完成后,液钢会从炼钢炉中倾注到连
铸机的铸模中,经过一系列的操作,最终形成一根长长的连铸坯。
3.结晶器冷却:连铸坯在结晶器中经过一段时间的冷却,使其
表面开始凝固,形成外壳。
同时,连铸坯的内部还会继续凝固,使得整个坯料逐渐凝固成形。
4.切割和打包:当连铸坯完全凝固后,需要进行切割和打包。
这个环节涉及到切割设备和包装机器的操作,以确保最终的连铸坯符合相关的标准和规定。
5.后续加工:最后,连铸坯将会进行后续的加工,如轧制、拉
拔等,以得到符合客户要求的成品钢材。
总的来说,连铸生产工艺流程包括了原料准备、倾炉和连铸、
结晶器冷却、切割和打包以及后续加工等几个主要环节。
通过这些操作,连铸生产工艺可以实现高效、自动化的生产,为钢铁行业的发展做出了重要贡献。
连铸的原理

连铸的原理
连铸是一种先进的铸造工艺,它通过在同一设备上连续进行浇铸和凝固,实现了铸坯的一次成型,大大提高了生产效率和产品质量。
连铸的原理主要包括连续浇铸、连续凝固和连续切割三个方面。
首先,连续浇铸是指在连铸设备上通过连续浇注熔融金属,使金属液不间断地流入结晶器中。
这样可以避免浇注过程中的温度变化和氧化,保证了金属液的纯净度和温度稳定性。
同时,连续浇铸还可以减少浇注过程中的气体夹杂和金属液的氧化,提高了产品的内部质量。
其次,连续凝固是指在结晶器中,熔融金属通过连续往复的凝固过程,逐渐形成固态铸坯。
在这个过程中,结晶器内部的冷却系统不断地将热量带走,使金属液逐渐凝固成固态金属。
通过控制结晶器的温度和冷却速度,可以实现对铸坯组织和性能的精确控制,从而获得更高质量的产品。
最后,连续切割是指在连铸设备的出口处,通过连续的切割装置将凝固成型的铸坯切割成所需长度的产品。
这样可以避免传统浇铸中的冷却等待时间,提高了生产效率。
同时,连续切割还可以减少铸坯表面的氧化和变形,保证了产品的表面质量和尺寸精度。
总的来说,连铸的原理是通过连续浇铸、连续凝固和连续切割,实现了铸坯的一次成型,大大提高了生产效率和产品质量。
这种先进的铸造工艺在现代工业生产中得到了广泛应用,为各种金属制品的生产提供了可靠的技术保障。
连铸过程原理及数值模拟

连铸过程原理及数值模拟连铸是一种重要的金属成形工艺,广泛应用于钢铁、铝合金等金属材料的生产和加工中。
连铸过程原理及数值模拟是研究连铸工艺的关键内容,通过对连铸过程的原理分析和数值模拟,可以优化连铸工艺参数,提高产品质量和生产效率。
连铸过程是将熔融金属直接注入到连续运动的铸坯中,通过冷却和凝固过程,将熔融金属转化为固态铸坯。
连铸的基本原理是利用连续运动的铸坯带走热量,使熔融金属迅速凝固,形成连续的固态铸坯。
在连铸过程中,主要包括液相区、液固两相区和固相区三个区域。
在液相区,熔融金属通过连续浇注,填充到铸坯的空腔中。
熔融金属的温度高于固相线,处于液态状态。
随着熔融金属的注入,液相区的长度逐渐增加。
在液固两相区,熔融金属和正在凝固的铸坯同时存在。
由于熔融金属的温度高于固相线,所以熔融金属仍然保持液态。
而铸坯由于受到液相的热量传递,开始逐渐凝固。
在这个区域中,液相区的长度逐渐减小,凝固铸坯的长度逐渐增加。
在固相区,整个铸坯都已经完全凝固。
熔融金属已经完全转化为固态,形成连续的固态铸坯。
在这个区域中,液相区的长度为零,凝固铸坯的长度为整个连铸过程的长度。
为了研究连铸过程的细节和优化连铸工艺参数,数值模拟成为一种重要的方法。
数值模拟是通过数学模型和计算机仿真技术,对连铸过程进行模拟和分析。
数值模拟可以准确地计算连铸过程中的温度场、流场和凝固结构等关键参数,为工艺优化提供科学依据。
在连铸过程的数值模拟中,需要考虑多个物理过程的相互作用。
首先是流体力学过程,包括熔融金属的流动和铸坯带走热量的过程。
其次是热传导过程,包括熔融金属的冷却和凝固过程。
最后是凝固结构演化过程,包括铸坯的晶粒生长和偏析等现象。
为了建立连铸过程的数值模型,需要考虑材料的物理性质、流体力学和热传导方程等方面的参数。
同时,还需要考虑边界条件和初始条件等参数。
通过数值模拟,可以预测连铸过程中的温度分布、流速分布和凝固结构等重要参数,为工艺优化提供指导。
连铸技术的基本原理
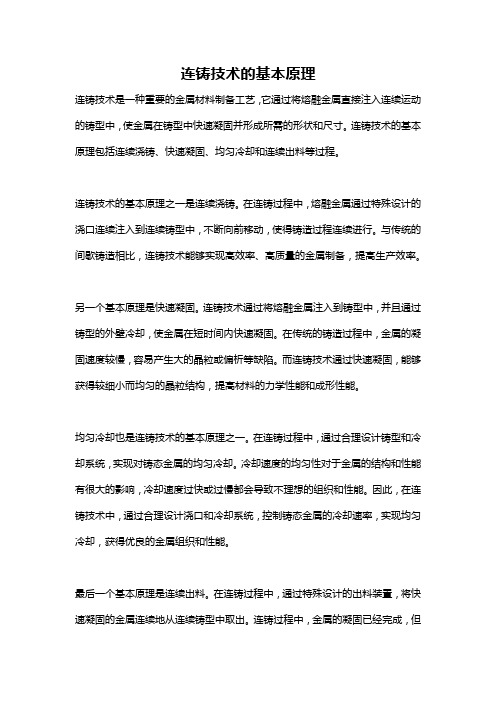
连铸技术的基本原理连铸技术是一种重要的金属材料制备工艺,它通过将熔融金属直接注入连续运动的铸型中,使金属在铸型中快速凝固并形成所需的形状和尺寸。
连铸技术的基本原理包括连续浇铸、快速凝固、均匀冷却和连续出料等过程。
连铸技术的基本原理之一是连续浇铸。
在连铸过程中,熔融金属通过特殊设计的浇口连续注入到连续铸型中,不断向前移动,使得铸造过程连续进行。
与传统的间歇铸造相比,连铸技术能够实现高效率、高质量的金属制备,提高生产效率。
另一个基本原理是快速凝固。
连铸技术通过将熔融金属注入到铸型中,并且通过铸型的外壁冷却,使金属在短时间内快速凝固。
在传统的铸造过程中,金属的凝固速度较慢,容易产生大的晶粒或偏析等缺陷。
而连铸技术通过快速凝固,能够获得较细小而均匀的晶粒结构,提高材料的力学性能和成形性能。
均匀冷却也是连铸技术的基本原理之一。
在连铸过程中,通过合理设计铸型和冷却系统,实现对铸态金属的均匀冷却。
冷却速度的均匀性对于金属的结构和性能有很大的影响,冷却速度过快或过慢都会导致不理想的组织和性能。
因此,在连铸技术中,通过合理设计浇口和冷却系统,控制铸态金属的冷却速率,实现均匀冷却,获得优良的金属组织和性能。
最后一个基本原理是连续出料。
在连铸过程中,通过特殊设计的出料装置,将快速凝固的金属连续地从连续铸型中取出。
连铸过程中,金属的凝固已经完成,但温度较高,通过连续出料并进行后续的热处理,可以获得所需的金属材料。
总的来说,连铸技术的基本原理包括连续浇铸、快速凝固、均匀冷却和连续出料。
这些原理相互作用,使得连铸技术成为一种高效、高质量的金属材料制备方法。
连铸技术的广泛应用,不仅能够提高金属材料的生产效率,提高材料的力学性能和成形性能,还能够减少金属材料的能源消耗和环境污染。
随着现代工业的发展,连铸技术在制造业中的地位和作用将越来越重要,对于推动金属材料制造业的发展具有重要的意义。
连铸絮流的原因

连铸絮流的原因
连铸絮流的原因可以归结为以下几个方面:
1. 液态金属流动不稳定:在连铸过程中,液态金属在急速凝固的条件下流动,容易受到外界因素的干扰,如震动、气泡等,导致流动不稳定,产生絮状流动。
2. 浇注速度过快:如果浇注速度过快,液态金属在流动过程中容易形成涡流或涡旋,从而形成絮状流动。
3. 浇注过程中的气体和杂质:连铸过程中,液态金属中可能存在气体和杂质,这些气体和杂质在流动过程中容易聚集在一起,形成絮状流动。
4. 浇注温度不均匀:连铸过程中,由于温度分布不均匀,液态金属在流动过程中可能出现冷凝现象,导致絮状流动的产生。
5. 浇注模具设计不合理:连铸模具的设计不合理,如出口形状不当、流道设计不合理等,会导致液态金属流动不稳定,形成絮状流动。
连铸絮流的原因主要包括液态金属流动不稳定、浇注速度过快、存在气体和杂质、浇注温度不均匀以及浇注模具设计不合理等因素。
连铸的名词解释
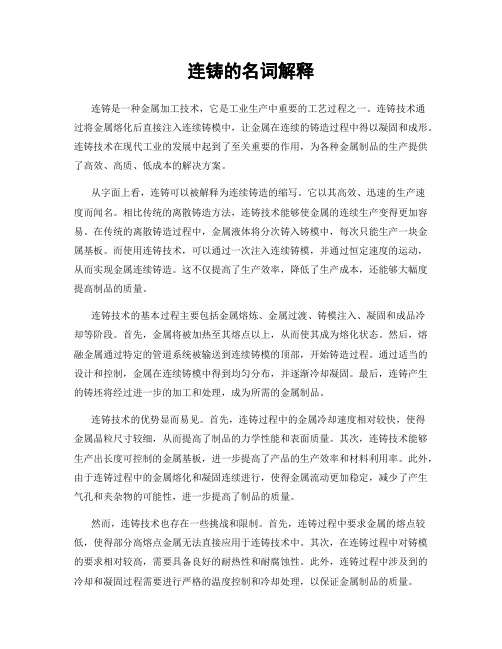
连铸的名词解释连铸是一种金属加工技术,它是工业生产中重要的工艺过程之一。
连铸技术通过将金属熔化后直接注入连续铸模中,让金属在连续的铸造过程中得以凝固和成形。
连铸技术在现代工业的发展中起到了至关重要的作用,为各种金属制品的生产提供了高效、高质、低成本的解决方案。
从字面上看,连铸可以被解释为连续铸造的缩写。
它以其高效、迅速的生产速度而闻名。
相比传统的离散铸造方法,连铸技术能够使金属的连续生产变得更加容易。
在传统的离散铸造过程中,金属液体将分次铸入铸模中,每次只能生产一块金属基板。
而使用连铸技术,可以通过一次注入连续铸模,并通过恒定速度的运动,从而实现金属连续铸造。
这不仅提高了生产效率,降低了生产成本,还能够大幅度提高制品的质量。
连铸技术的基本过程主要包括金属熔炼、金属过渡、铸模注入、凝固和成品冷却等阶段。
首先,金属将被加热至其熔点以上,从而使其成为熔化状态。
然后,熔融金属通过特定的管道系统被输送到连续铸模的顶部,开始铸造过程。
通过适当的设计和控制,金属在连续铸模中得到均匀分布,并逐渐冷却凝固。
最后,连铸产生的铸坯将经过进一步的加工和处理,成为所需的金属制品。
连铸技术的优势显而易见。
首先,连铸过程中的金属冷却速度相对较快,使得金属晶粒尺寸较细,从而提高了制品的力学性能和表面质量。
其次,连铸技术能够生产出长度可控制的金属基板,进一步提高了产品的生产效率和材料利用率。
此外,由于连铸过程中的金属熔化和凝固连续进行,使得金属流动更加稳定,减少了产生气孔和夹杂物的可能性,进一步提高了制品的质量。
然而,连铸技术也存在一些挑战和限制。
首先,连铸过程中要求金属的熔点较低,使得部分高熔点金属无法直接应用于连铸技术中。
其次,在连铸过程中对铸模的要求相对较高,需要具备良好的耐热性和耐腐蚀性。
此外,连铸过程中涉及到的冷却和凝固过程需要进行严格的温度控制和冷却处理,以保证金属制品的质量。
尽管如此,连铸技术在如今的工业生产中扮演了重要的角色。
连铸工艺流程

连铸工艺流程连铸是一种常用的铸造工艺,适用于生产长条状或板状金属材料。
它是通过将熔化的金属直接倒入连续流动的水冷铜板中,使其冷却并形成连续的长条状或板状产品。
连铸工艺具有高效率、低能耗、高品质等优点,广泛应用于钢铁、铝合金等行业。
连铸工艺流程主要包括准备工作、连续浇铸、冷却和切割四个阶段。
首先是准备工作。
这个阶段包括准备熔炉、铜板、铸模、流动水和其他所需设备和材料。
熔炉中加入合适的金属原料,加热使其熔化。
同时,准备好冷却水,并确保其具有足够的流动性和温度适宜。
铜板和铸模是制造连铸机的主要部件,需要进行充分的清洗和检查,以确保表面平整和无缺陷。
接下来是连续浇铸。
将熔化的金属倒入连铸机的铜板中,通过喷头将金属喷向铸模,并使其连续地流动。
连铸机的喷头是一个关键部件,可以调整金属流动的速度和方向,以保证产品的质量。
同时,需要控制好浇注速度和温度,以避免金属过热或过冷,影响产品的性能。
然后是冷却。
在连铸过程中,金属材料与铜板接触,通过快速传热,使金属迅速冷却并凝固。
冷却水通过铜板流过,吸收金属的热量,并保持适宜的温度。
冷却水的流量和温度需要根据不同金属材料进行调整,以确保产品的结晶组织和力学性能。
最后是切割。
冷却后的连铸坯可以根据需要进行切割成适当的长度,以便进一步加工。
切割可以通过割断或切削进行。
割断是指使用切割设备将连铸坯切成所需长度,并去除不良部分。
切削是指使用机械切割工具将连铸坯切割成规定的尺寸和形状。
总之,连铸工艺是一种高效、高品质的铸造工艺,适用于生产长条状或板状金属材料。
其主要流程包括准备工作、连续浇铸、冷却和切割。
通过合理调整浇注速度、温度和冷却设备,可以制造出具有良好结晶组织和优异性能的产品。
连铸工艺的应用范围广泛,为钢铁、铝合金等行业的发展提供了重要的支撑。
炼钢厂连铸工艺流程

炼钢厂连铸工艺流程1.钢水准备:从炼钢炉中输出得到熔化的钢水,然后通过脱氧、温度调节和脱气等工艺处理,得到适合连铸工艺的钢水。
2.连铸结晶器:将处理后的钢水通过倾转、倾倒和挤压等技术,直接浇注到连铸机结晶器中。
结晶器内部有一组多孔结晶器衬套,通过冷却水的循环,将钢水快速冷却并结晶。
3.凝固:钢水在结晶器中快速冷却,开始凝固成为连续铸坯。
凝固过程中,还会通过控制结晶器内的冷却水温度和流量,来调节钢坯的凝固速度和结晶器壁的温度。
4.伸展:连续铸坯凝固后,通过拉伸机构将钢坯从结晶器中拉出,使其变长,同时也能控制钢坯的截面形状。
这个过程中,还会进行坯底冷却,以控制坯底凝固的厚度。
5.切割:钢坯经过拉伸后,通过切割机构将其切断成合适的长度,以供后续工序使用。
6.冷却:切割成合适长度的连续铸坯通过冷却水箱,进行冷却。
冷却的目的是使钢坯的内部和外部温度均匀降低,以便后续的轧制工艺。
7.钢坯调整:冷却后的连续铸坯,根据需要可能需要进行尺寸调整。
这个过程中通常使用钢坯矫直机、切割坯边机等设备,对钢坯进行校直和修边,使其符合轧制工艺要求。
8.轧制:经过调整后的钢坯将被送入炼钢厂的轧机进行轧制。
根据需要,钢坯可能还会经过多道次的轧制和调整。
9.检测:轧制后的产品将进入质检环节,通过各种非破坏性和破坏性检测手段,对产品进行检测,以确保其质量符合要求。
10.成品:经过检测合格后,轧制后的产品成品将根据需求进行打包、标记和存储,以便销售和运输。
综上所述,炼钢厂连铸工艺流程是将熔化的钢水通过连续铸造技术直接浇注到连铸机结晶器中,经过凝固、伸展、切割、冷却、调整、轧制、检测等一系列工艺处理,最终得到质检合格的连续铸坯。
这种工艺流程具有工艺连续、设备高效、产品质量稳定等优点,已被广泛应用于炼钢厂的生产中。
连铸原理与工艺
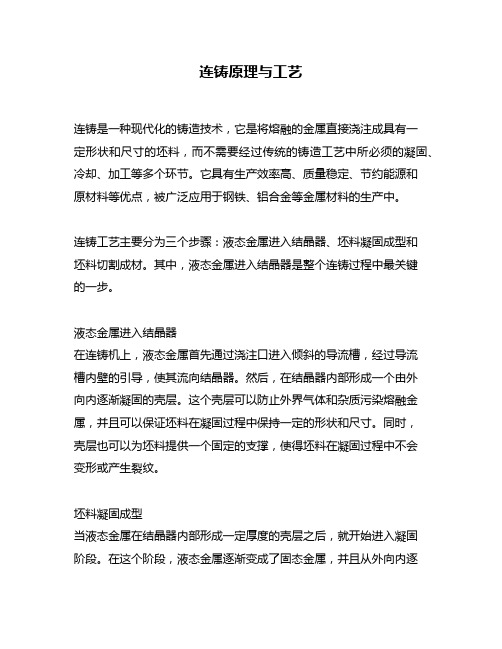
连铸原理与工艺连铸是一种现代化的铸造技术,它是将熔融的金属直接浇注成具有一定形状和尺寸的坯料,而不需要经过传统的铸造工艺中所必须的凝固、冷却、加工等多个环节。
它具有生产效率高、质量稳定、节约能源和原材料等优点,被广泛应用于钢铁、铝合金等金属材料的生产中。
连铸工艺主要分为三个步骤:液态金属进入结晶器、坯料凝固成型和坯料切割成材。
其中,液态金属进入结晶器是整个连铸过程中最关键的一步。
液态金属进入结晶器在连铸机上,液态金属首先通过浇注口进入倾斜的导流槽,经过导流槽内壁的引导,使其流向结晶器。
然后,在结晶器内部形成一个由外向内逐渐凝固的壳层。
这个壳层可以防止外界气体和杂质污染熔融金属,并且可以保证坯料在凝固过程中保持一定的形状和尺寸。
同时,壳层也可以为坯料提供一个固定的支撑,使得坯料在凝固过程中不会变形或产生裂纹。
坯料凝固成型当液态金属在结晶器内部形成一定厚度的壳层之后,就开始进入凝固阶段。
在这个阶段,液态金属逐渐变成了固态金属,并且从外向内逐渐缩小。
同时,由于液态金属的收缩率和晶粒长大率不同,所以在凝固过程中会形成一定数量的热裂纹和气孔。
为了解决这个问题,连铸工艺中采用了多种措施来控制坯料的凝固过程。
例如,在结晶器内部设置冷却水管道来降低壳层温度、使用高效保护气体来防止氧化等。
此外,在连铸工艺中还可以通过调整浇注速度、结晶器倾角、结晶器长度等参数来控制坯料的凝固速度和形状。
坯料切割成材当坯料完全凝固之后,它会被自动切割成一定长度的材料。
在连铸工艺中,切割方式主要分为两种:火焰切割和机械切割。
火焰切割是利用氧炔火焰将坯料加热到一定温度后进行切割,适用于较大尺寸的坯料。
机械切割则是使用钢丝、钢锯等工具将坯料进行切割,适用于较小尺寸的坯料。
总之,连铸工艺是一种高效、节能、环保的现代化铸造技术。
它通过控制液态金属的流动和凝固过程,使得金属材料可以以一种更加稳定和高效的方式生产出来。
同时,在连铸工艺中还可以通过调整参数、优化设备等手段来不断提高产品质量和生产效率,为现代制造业的发展做出了重要贡献。
连铸工艺要点

连铸工艺要点连铸工艺是指连续铸造技术,是铁合金、钢铁等冶金行业中的一种主要生产工艺。
其工艺特点是连续铸造、高效能、高品质、节能环保等。
下面我们来了解一下连铸工艺的要点。
1. 连铸设备连铸设备是连铸工艺的核心,由铸机、结晶器、引伸器、切割机、输送机等组成。
铸机是整个设备的主体,结晶器是铸机的核心部分,引伸器是为了延长铸坯结晶器内的结晶长度,切割机是将连续铸坯切割成长度符合要求的坯料,输送机将坯料送到后续加工工序。
2. 连铸模具连铸模具是决定铸坯质量和工艺效果的重要因素,也是连铸设备的重要组成部分。
模具材料要求高强度、高温耐用、不易变形。
常用的模具材料有高硅铸铁、高铬铸铁、尿素醛树脂等。
模具结构形式有直立式、倾斜式、水平式等,不同结构形式适用于不同铸造条件。
3. 冷却水系统连铸过程中,冷却水系统起着非常重要的作用。
冷却水系统包括结晶器水口、结晶器壁面、引伸器、切割机等部位的冷却系统。
冷却水系统的稳定性和冷却效果直接影响铸坯的质量。
冷却水的温度、流量、压力等参数的调节需要精细控制。
4. 铸造工艺参数连铸工艺参数的优化对铸坯质量和生产效率有重要影响。
铸造参数包括结晶器冷却、引伸器速度、拉拔速度、切割位置等。
优化铸造参数可以控制铸坯中的缺陷、提高铸坯表面质量、降低成本并提高生产效率。
5. 质量控制质量控制是连铸工艺中的重要环节。
铸坯质量的稳定性和可控性直接影响产品的质量和生产效率。
质量控制包括铸坯表面质量检测、铸坯内部缺陷检测、坯料长度检测等。
不同的质量控制手段需要不同的检测设备和技术支持。
连铸工艺的要点包括连铸设备、连铸模具、冷却水系统、铸造工艺参数和质量控制。
在实际生产中,要根据不同的生产条件和产品要求,综合考虑这些要点,优化工艺流程,提高生产效率和产品质量。
连铸工艺流程

连铸工艺流程
《连铸工艺流程》
连铸工艺是一种现代金属材料生产工艺,它利用连续铸造设备,将熔化的金属直接连续铸造成坯料或板材,省去了传统铸造工艺中的铸型、浇注、凝固和脱模等环节,大大提高了生产效率和质量。
具体来说,连铸工艺流程包括以下几个关键步骤:
1. 熔炼:将原料金属经过熔炼炉的高温熔化,形成熔融金属。
2. 连铸机:熔融金属通过连铸机器,经过喷水冷却,以得到坯料或板材。
连铸机在正常情况下可连续工作数周甚至数月。
3. 切割:将冷却后的坯料或板材进行切割成所需长度。
4. 表面处理:对坯料或板材进行表面处理,以去除氧化层、锈蚀和杂质,得到光洁的表面。
5. 加工:对坯料或板材进行进一步的热处理、冷加工等工艺,以获得所需的最终产品。
连铸工艺流程的优点在于,它能够大幅提高金属材料的生产效率,减少人工干预,降低能源消耗,减少生产废料,提高产品质量和一致性。
因此,在诸如钢铁、铝合金等金属材料的生产中,连铸工艺已成为重要的生产方式。
总的来说,《连铸工艺流程》的不断改进和创新,将为金属材料生产带来更高效、更绿色、更经济的生产方式,对于促进工业制造业的可持续发展具有重要的意义。
连续铸造原理和连铸设备简介
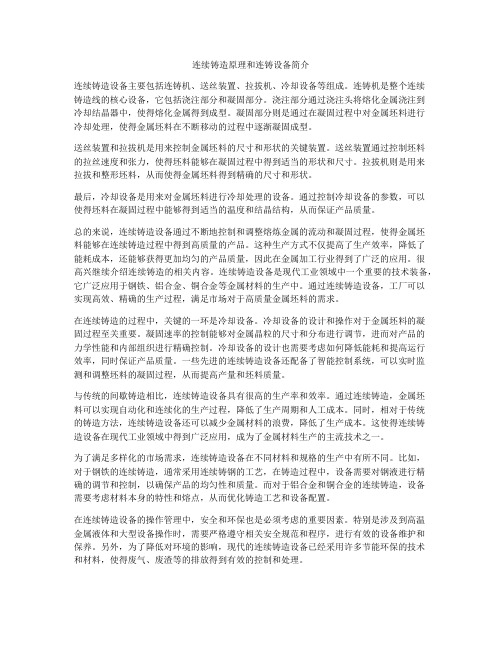
连续铸造原理和连铸设备简介连续铸造设备主要包括连铸机、送丝装置、拉拔机、冷却设备等组成。
连铸机是整个连续铸造线的核心设备,它包括浇注部分和凝固部分。
浇注部分通过浇注头将熔化金属浇注到冷却结晶器中,使得熔化金属得到成型。
凝固部分则是通过在凝固过程中对金属坯料进行冷却处理,使得金属坯料在不断移动的过程中逐渐凝固成型。
送丝装置和拉拔机是用来控制金属坯料的尺寸和形状的关键装置。
送丝装置通过控制坯料的拉丝速度和张力,使得坯料能够在凝固过程中得到适当的形状和尺寸。
拉拔机则是用来拉拔和整形坯料,从而使得金属坯料得到精确的尺寸和形状。
最后,冷却设备是用来对金属坯料进行冷却处理的设备。
通过控制冷却设备的参数,可以使得坯料在凝固过程中能够得到适当的温度和结晶结构,从而保证产品质量。
总的来说,连续铸造设备通过不断地控制和调整熔炼金属的流动和凝固过程,使得金属坯料能够在连续铸造过程中得到高质量的产品。
这种生产方式不仅提高了生产效率,降低了能耗成本,还能够获得更加均匀的产品质量,因此在金属加工行业得到了广泛的应用。
很高兴继续介绍连续铸造的相关内容。
连续铸造设备是现代工业领域中一个重要的技术装备,它广泛应用于钢铁、铝合金、铜合金等金属材料的生产中。
通过连续铸造设备,工厂可以实现高效、精确的生产过程,满足市场对于高质量金属坯料的需求。
在连续铸造的过程中,关键的一环是冷却设备。
冷却设备的设计和操作对于金属坯料的凝固过程至关重要。
凝固速率的控制能够对金属晶粒的尺寸和分布进行调节,进而对产品的力学性能和内部组织进行精确控制。
冷却设备的设计也需要考虑如何降低能耗和提高运行效率,同时保证产品质量。
一些先进的连续铸造设备还配备了智能控制系统,可以实时监测和调整坯料的凝固过程,从而提高产量和坯料质量。
与传统的间歇铸造相比,连续铸造设备具有很高的生产率和效率。
通过连续铸造,金属坯料可以实现自动化和连续化的生产过程,降低了生产周期和人工成本。
连铸连轧知识点

连铸连轧知识点连铸和连轧是金属工业中常见的两个工艺过程。
连铸是指将液态金属连续铸造成坯料的过程,而连轧是指将坯料经过一系列压制和变形操作,连续地轧制成所需尺寸的金属板、带材或线材的过程。
本文将介绍连铸和连轧的基本概念、工艺流程和主要应用。
一、连铸连铸是一种高效的金属铸造技术,具有生产速度快、坯料质量好等优点。
连铸主要应用于钢铁、铜、铝等金属的生产中。
1. 连铸的基本原理连铸的基本原理是将熔融的金属通过连续浇注的方式,直接铸造成连续的坯料。
具体原理如下:首先,将金属熔融至液态,并通过加热设备保持在一定温度范围内;然后,通过连续浇注系统,将熔融金属均匀地注入到连铸结晶器中;在连铸结晶器中,通过冷却剂的作用,使金属迅速凝固,并形成坯料;最后,通过一系列传动装置,将连续产生的坯料送往下游的轧制设备或其他后续处理过程中。
2. 连铸的工艺流程连铸的工艺流程一般包括以下几个关键步骤:(1)冶炼:将矿石等原料经过熔炼处理,得到液态的金属合金;(2)调温:通过加热设备将金属保持在一定的液态温度;(3)连续浇注:通过连续浇注系统,将熔融金属注入到连铸结晶器中;(4)结晶与凝固:在连铸结晶器中,通过冷却剂的作用,使金属迅速凝固,并形成坯料;(5)切割和输送:将连续产生的坯料切割成合适的长度,并送往下游的加工设备。
3. 连铸的应用连铸广泛应用于钢铁、铜、铝等金属的生产中。
在钢铁工业中,连铸可以直接将炼钢铁水铸造成连续坯料,用于后续轧制成钢板和钢材。
在有色金属工业中,连铸可以将液态金属铸造成连续的板材、带材和线材,用于制造电线电缆、汽车零部件等产品。
二、连轧连轧是一种将金属坯料经过多道次的压制和变形操作,连续地轧制成所需尺寸的金属板、带材或线材的工艺过程。
连轧具有高效快速、坯料成形完整等特点,广泛应用于钢铁、有色金属等工业领域。
1. 连轧的基本原理连轧的基本原理是通过一系列的压制和变形操作,使金属坯料逐渐减小厚度、增大长度,并达到所需的尺寸要求。
连续铸钢的名词解释

连续铸钢的名词解释近年来,随着科技的不断发展,连续铸钢技术在钢铁行业的应用越来越广泛。
它不仅提高了钢铁生产的效率和质量,还减少了环境污染。
那么,什么是连续铸钢?本文将对连续铸钢进行详细解释。
一、连续铸钢的概念连续铸钢是指在一个连续的过程中,将液态钢浇铸成连续的坯料。
相比于传统的间歇铸造方法,连续铸钢具有以下优势:1. 提高生产效率:连续铸钢不需要停机等待冷却和顶出钢坯,而是实现钢液的连续供给,大大缩短了生产周期。
2. 提高产品质量:由于连续铸造过程中的冷却速度比较快,钢材的晶粒细化,内部组织均匀,从而提高了产品的力学性能和外观质量。
3. 减少能源消耗:连续铸钢无需反复预热,避免了大量热能的浪费,降低了能源的消耗。
4. 减少环境污染:连续铸钢过程中无需大量排放烟尘和废气,减少了环境污染的程度。
5. 方便管理与自动化控制:连续铸钢系统能够实现全面自动化控制,减少了人工操作的难度,提高了管理的便捷性。
二、连续铸钢的工艺流程连续铸钢的工艺流程主要包括:钢车、过渡板、连铸机、定盘修边、冷却、切割、堆垛等环节。
1. 钢车:钢液从炼钢炉中通过钢包输送到铸钢车中进行储存和运输,维持钢液的合适温度和流动性。
2. 过渡板:钢液从钢车通过过渡管流向连铸机,过渡板起到连接钢车和连铸机的作用,确保钢液的平稳流动。
3. 连铸机:钢液在连铸机内通过结晶器,逐渐冷却凝固成坯料。
连铸机主要包括浇注系统、结晶器、拉拔机构和冷却装置等。
4. 定盘修边:连铸机出来的钢坯经过定盘修边,将坯料的尺寸修整至合适。
5. 冷却:修整后的钢坯通过冷却装置,降低温度,使钢材的内部结构得以稳定,提高其力学性能。
6. 切割:冷却后的钢坯通过切割机械进行切割,根据需要得到合适的长度。
7. 堆垛:切割好的钢材坯料按照规定的规格和堆垛方式进行堆放,便于后续的钢材加工和运输。
三、连续铸钢的应用领域连续铸钢技术广泛应用于钢铁行业的各个领域,如建筑、汽车、船舶、机械制造等。
连铸工艺流程

连铸工艺流程连铸工艺流程是指将熔化状态的钢水通过连铸机连续铸造成连续铸坯的工艺流程。
该工艺流程主要包括加热与保温、定量浇注、连续铸造、凝固与定形、剪断与冷却等几个过程。
首先,加热与保温是连铸工艺的第一步。
钢水从炉中出来后,需要进行加热,使其达到适宜的铸造温度,一般为1500-1600℃。
然后,需要将加热后的钢水保温一段时间,以保持其熔化状态,一般保温时间为30-60分钟。
接下来是定量浇注过程。
在钢水进行保温的同时,需要将一定的钢水通过浇口定量地注入连铸机的浇注口。
这一过程需要控制好浇注速度和浇注时间,以确保钢水均匀地注入连铸机,避免铸坯出现缺陷。
随后是连续铸造过程。
连铸机将钢水从浇注口引入连铸机的结晶器中,结晶器内壁上涂有一层绝缘材料,以减小结晶器和铸坯之间的传热和冷却速度,使钢水逐渐凝固。
在结晶器中,钢水经过冷却后,开始凝固。
结晶器内还设有冷却水管,以维持适宜的结晶器温度,提高凝固质量。
凝固与定形是连铸工艺的关键过程。
当钢水进入结晶器后,在冷却的作用下,钢水开始凝固形成铸坯。
这一过程需要控制好结晶器的冷却温度和冷却速度,以确保钢水凝固成坯的过程中,铸坯的组织结构和尺寸能达到设计要求。
最后是剪断与冷却过程。
在连铸机的结晶器中,通过剪切装置将凝固成型的连续铸坯切断为定长的铸坯,同时进行冷却,使铸坯温度降低到适宜的水平。
然后,铸坯通过输送设备运输到下一道工序,如轧机进行轧制或其他后续加工工序。
总之,连铸工艺流程是一套将熔化状态的钢水连续铸造成连续铸坯的工艺流程。
该工艺流程主要包括加热与保温、定量浇注、连续铸造、凝固与定形、剪断与冷却等几个过程。
在每个步骤中,需要严格控制各个参数,以确保连铸坯的质量和成型效果。
同时,连铸工艺也具有高效、节能等优点,被广泛应用于钢铁工业。
连铸工艺要点

连铸工艺要点介绍如下:
1.设备:连铸工艺需要使用到连铸机、结晶器、拉拔机、气切割
机等各种设备。
这些设备需要保养、维修和更换,以确保工艺能够正常运行。
2.浇注:浇注是连铸工艺的核心步骤,需要控制浇注速度、浇注
角度和浇注位置等参数,以确保铸坯具有良好的表面质量和内部组织结构。
3.结晶器:结晶器是冷却钢水的设备,它的设计和使用对铸坯质
量有着重要的影响。
合理的结晶器设计可以提高铸坯的结晶质量,避免产生缺陷。
4.拉拔:拉拔是连铸工艺的最后一个步骤,它可以使铸坯逐渐变
形成为规定的形状和尺寸。
拉拔时需要控制速度和拉拔力度,以避免产生裂纹和变形等缺陷。
5.自动化:连铸工艺需要高度自动化的控制系统,以保证工艺的
稳定性和可靠性。
自动控制系统可以实现对浇注速度、温度、拉拔力等参数的实时监控和调整,提高工艺的自动化程度和生产效率。
以上是连铸工艺的要点,它们对于保证生产质量和提高生产效率都有着重要的影响。
立式连铸工艺流程

立式连铸工艺流程
立式连铸是一种常见的金属连铸工艺,用于生产连续铸造的金属坯料,通常用于生产铜、铝、钢等金属材料。
以下是立式连铸的典型工艺流程:
1. 熔炼金属:首先将金属原料(如铜、铝、钢等)加热熔化成液态金属。
2. 准备结晶器:准备一个立式结晶器,结晶器内部有水冷却系统,用于快速冷却金属。
3. 连续铸造:
将熔融金属通过喷嘴或浇口注入结晶器顶部,金属在结晶器内迅速凝固。
金属凝固后,通过拉坯机械将凝固的金属坯拉出,形成连续的坯料。
4. 切割成型:连续铸造的金属坯料经过冷却后,可以进行切割成所需长度的坯料。
5. 热处理:部分金属材料需要进行热处理,以改变其晶体结构和力学性能。
6. 质量检测:对连铸的金属坯料进行质量检测,确保其符合规定的标准和要求。
立式连铸工艺通过连续铸造的方式,可以高效地生产金属坯料,广泛应用于金属加工和制造领域。
这种工艺能够提高生产效率、降低生产成本,并且能够生产出质量稳定、形状规整的金属坯料,满足不同行业的需求。
连铸常用计算公式
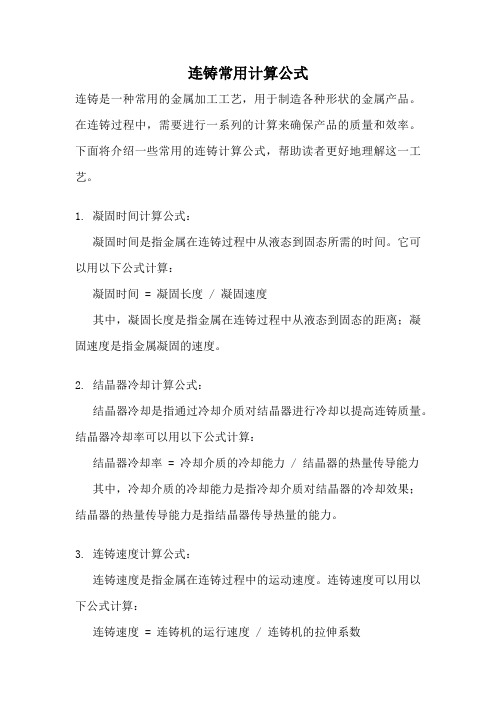
连铸常用计算公式连铸是一种常用的金属加工工艺,用于制造各种形状的金属产品。
在连铸过程中,需要进行一系列的计算来确保产品的质量和效率。
下面将介绍一些常用的连铸计算公式,帮助读者更好地理解这一工艺。
1. 凝固时间计算公式:凝固时间是指金属在连铸过程中从液态到固态所需的时间。
它可以用以下公式计算:凝固时间 = 凝固长度 / 凝固速度其中,凝固长度是指金属在连铸过程中从液态到固态的距离;凝固速度是指金属凝固的速度。
2. 结晶器冷却计算公式:结晶器冷却是指通过冷却介质对结晶器进行冷却以提高连铸质量。
结晶器冷却率可以用以下公式计算:结晶器冷却率 = 冷却介质的冷却能力 / 结晶器的热量传导能力其中,冷却介质的冷却能力是指冷却介质对结晶器的冷却效果;结晶器的热量传导能力是指结晶器传导热量的能力。
3. 连铸速度计算公式:连铸速度是指金属在连铸过程中的运动速度。
连铸速度可以用以下公式计算:连铸速度 = 连铸机的运行速度 / 连铸机的拉伸系数其中,连铸机的运行速度是指连铸机的实际运行速度;连铸机的拉伸系数是指连铸机拉伸连铸坯料的能力。
4. 结晶器长度计算公式:结晶器长度是指结晶器在连铸过程中的长度。
结晶器长度可以用以下公式计算:结晶器长度 = 连铸坯料的凝固长度 + 连铸机的拉伸长度其中,连铸坯料的凝固长度是指连铸坯料在凝固过程中的长度;连铸机的拉伸长度是指连铸机拉伸连铸坯料的长度。
5. 连铸效率计算公式:连铸效率是指连铸过程中金属的利用率。
连铸效率可以用以下公式计算:连铸效率 = 连铸坯料的重量 / 连铸机的出口速度其中,连铸坯料的重量是指连铸机连铸坯料的重量;连铸机的出口速度是指连铸机连铸坯料的出口速度。
以上是一些常用的连铸计算公式,它们帮助工程师和操作人员在连铸过程中进行准确的计算和判断,以确保产品的质量和效率。
希望这些公式对读者有所帮助,更好地理解连铸工艺的重要性和复杂性。
- 1、下载文档前请自行甄别文档内容的完整性,平台不提供额外的编辑、内容补充、找答案等附加服务。
- 2、"仅部分预览"的文档,不可在线预览部分如存在完整性等问题,可反馈申请退款(可完整预览的文档不适用该条件!)。
- 3、如文档侵犯您的权益,请联系客服反馈,我们会尽快为您处理(人工客服工作时间:9:00-18:30)。
实验测定:
实验研究指出,树枝晶间距 l 与凝固速度 R 和温度梯度有关。
l CR m G n
雅可比试验不同温度梯度和凝固速度对树枝形态的影响,并测定 了 l 和 l 与 R 和 G 关系,如图4-13所示。由图可得出: 上述两经验式中,对一次晶间距,指数m、n值相差较大;对二次 晶间距,m、n值近似相等。不同作者得到的m、n值相差较大。 试验指出,二次枝晶间距与区域凝固时间 们的经验关系式:
(2) 成分过冷条件,由平衡相图可知:
dT dC m dx dx
dT dC 式中: 为凝固前沿液相线温度梯度; dx dx 固前沿浓度梯度; m为液相线斜率。
为凝
当液体中实际温度低于液相线温度时就产生了成分过冷 区。那么不产生过冷的条件应该是实际温度梯度大于或 等于液相线温度梯度。即: dT dC 或 ( 4-11) G m G dx x 0 dx x 0 式中:G为液体中实际温度梯度,它决定于向外界的传 热。
O O
O O
O O
钢 坯 清 理 O
加 热
轧 制
轧 钢 燃 料 消 耗 ×109J/t
2.01 0.92
O
O O
3 4 5
O O O
O O O
O
O O O
O O O
1.34 0.878 0.334
6
连铸坯直接轧 制CC-DR
O
O
角 部 补 热
O
4 连铸技术的发展历史
(1)19世纪中叶H.Bessemer提出了连续浇注金属的构想; (2)1933年,现代连铸的奠基人S.Junghans提出并发展 了结晶器振动装置,奠定了连铸的工业应用的基础; (3)本世纪30年代,连铸成功应用于有色金属; (4)1950年, S.Junghans和Mannesmann公司合作,建成 世界上第一台工业连铸机; (5)50年代,工业应用时期; 到50年代末,有连铸机30台,产量110t,连铸比0.34%. (6)60年代,稳步发展时期; 到60年代末,有连铸机200余台,产量4000万t. (7)70年代,迅猛发展时期; 1981年连铸比33.8%. (8)80年代,完全成熟时期; 1990年连铸比64.1%; (9)90年代,近终型连铸技术时代
(4)求 G 和
1 3 G (2 3 cos cos )( r G r 2 lc ) 3
3
r
:
( G ) 0 r
而
2 3 cos cos 0,
3
(2 3cos cos3 ) 2r lc r 2 G 0
505.7 605.7 931.7 1356 1493 1803 1725 1736
1.1.2 非均质形核
上图为一个平面的夹杂物上形成一个半球缺的固体晶核,晶核与液 体、固体有三个界面。处于平衡时:
式中:
为界面张力; 表示晶体在夹杂物表面的润湿倾向。
ls cs cos lc
参考书目
(1) 炼钢学原理 冶金工业出版社,曲英主编。 (2) 浇注与凝固 冶金工业出版社,蔡开科主编。 (3) 连续铸钢 科学出版社,蔡开科主编。
(4) 钢铁冶金学(炼钢部分)
冶金工业出版社, 陈家祥主编。
前 言
1 现代炼钢技术的发展(连铸技术的作用)
( 1)
1947年-1974年:
技术特点:转炉、高炉的大型化;以模铸-初轧 为核心,生产外延扩大。
1 凝固理论
1 凝固理论
1.1 钢液结晶与凝固结构
1.1.1 均质形核
(1)新核的形成引起系统的自由能的变化: · 体积自由能的下降: ΔGv=-(4/3)(πγ3 (GA-GB)) 式中:γ:球形晶核的半径;GA:A相体积自由能; GB:A相体积自由能 · 表面自由能的增加: ΔGF=4πγ2σ 式中:σ:A、B两相界面自由能 (2) 均质形核的条件: ΔGΣ=ΔGv+ΔGF=-(4/3)(πγ3 (GA-GB))+4πγ2σ
(2)产生新相界表面自由能
GF lc 2r 2 (1 cos ) ( cs ls )r 2 (1 cos2 ) r 2 lc (2 3 cos cos3 )
(3)总自由能变化 G :
Gr
:
1 G r 3 (2 3 cos cos 2 )G r 2 lc (2 3 cos cos 3 ) 3
由图4-1可知,当ΔGΣ达到最大值时的晶核大小叫临界半径,在 r r 时,求:
由(4-4)式可知,临界晶核半径是与过冷度成反比。由图(4-1)可知: — 晶核长大导致系统自由能增加,新相不稳定; — 晶核长大导致系统自由能减少,新相能稳定生长; — 形核和晶核溶解处于平衡。 结论是:在一定温度下,任何大于临界半径的晶核趋向于长大,
1.1.3 晶体的长大
1.1.3.1 晶体的长大的能量消耗
- 原子的扩散
- 晶体的缺陷
- 原子的粘附
- 结晶潜热的导出
1.1.3.2 晶核长大的驱动力-成分过冷理论
(1)成分过冷的产生 ·纯金属凝固:过冷是靠模壁向外传热控制 ·合金凝固:
选分结晶
溶质元素在固相和液相的再分配 溶质浓度的不同使液相线温度不同Fra bibliotek钢的凝固与连续铸造
•教学目的:
本部分课程从钢的凝固原理出发, 结 合钢的连铸工艺,使学生从理论上和实践上 掌握浇注和凝固过程中发生的主要的物理化 学现象,初步掌握连铸工艺与设备及其最新 发展,为将来从事冶金工程领域的工作,为 生产高质量的连铸坯,以及解决连铸生产中 的实际问题奠定理论基础。
课程大纲
1.1.4.4 凝固结构对产品性能的影响
(1)柱状晶的枝干较纯,而枝晶间偏析
故: 2r lc r 2 G 0
r
2 lc G
以
r 代入
G 得:
4 lc 3 G 2 3 cos cos 2 3(G)
2
(4-10)
非均质形核功与均质形核功相差
— 180 , cos180 0 ,晶体独立于液体中,形核功与均质形核相同;
小于临界半径晶核趋向消失。
表4-1纯液体金属结晶过冷度
金属
Sn Pb Al Cu Mn Fe Ni Co
熔点
f ( K )
过冷度
ΔT(k)
103 80 130 130 308 295 319 330
T T f
0.208 0.133 0.110 0.174 0.206 0.161 0.186 0.181
前言
1
凝固理论
·钢液的结晶
·晶体的长大 ·凝固结构
1.1 钢液结晶与凝固结构
·凝固结构控制
1.2 凝固偏析 ·凝固显微偏析
·凝固宏观偏析
1.3 凝固收缩 1.4 钢的高温力学性能 1.5 凝固过程中气体和非金属夹杂物
2
连铸工艺与设备
2.1 连铸机机型及特点 2.2 连铸工艺与设备
-钢包
-中间包 -结晶器 -二次冷却区 -拉坯矫直机 -切割机 2.3 连铸新技术
1.1.4 凝固结构
1.1.4.1 钢水凝固过程的冶金特点
(1)δ -γ相的转变 · 稳定的δ相(或γ相)凝固 例如: 铁素体的Cr钢 · δ相凝固后转变为奥氏体 例如:Ni-Cr奥氏体不锈钢 · δ相凝固后转变为γ,再转变为α相 例如:低碳钢
(2)钢液的流动 (3)凝固收缩 (4)裂纹敏感性 (5)凝固结构
2 2
晶核与夹杂物接触面积:
r (1 cos )
球缺体积:
1 3 r (2 3 cos cos 3 ) 3
球缺表面积:
2rh 2r 2 (1 cos )
形成晶核时系统自由能变化: (1)体积自由能 Gv: Gv
1 3 r (2 3 cos cos 3 )G 3
4-15表示了不同凝固方法的冷却速度与树枝晶间距关系。由 于冷却速度的差异,故连铸坯的树枝晶结构比钢锭的要细。加 大冷却速度,可以得到较细的树枝晶结构。 文献中对二次枝晶间距与冷却速度还有不同的经验式。铃木等 人提出 C 0.88% 的炭钢中:
l 709 0.395 ( : C 分,l : )
0.5
t c 关系如图4-14。它
l 0.00716 tc (1.5%C,1.1%Mn)
l 0.0518 tc
0.44
(0.6%C,1.1%Mn)
树枝晶间距对钢锭结构、显微偏析有重要影响。实际钢锭凝固时 凝固速度与温度梯度不可能彼此独立变化,而通过凝固时放出热 量来影响整个凝固过程。这样就可用冷却速度来控制树枝晶间距 ,以得到细的树枝结构。而影响冷却速度最重要的因素是凝固方 法。图
1 (2 3 cos cos 3 ) 。由(4-10)式可知 4
—
0 , cos0 1 液体中质点已是一个晶核,不需任何过冷度就可形核;
,依附于外来质点形成晶核。
— 0 180
结论是非均质形核有效性决定于润湿角 。越小 ,形核功就越小,就易形核 ,形核速率比较如图4-4。非均质形核的过冷度比均质形核大为减少。在实际生 产中主要是非均质形核,除模壁表面作为“依托”形成晶核外,液体金属中需含 有两类小质点:一类叫活性质点,如金属氧化物(Al2O3),其晶体结构与金属 晶体结构相似,它们之间界面张力小,可作为“依托”而形成核心。另一类是难 熔物质的质点,它们的结构虽然与金属晶体结构相差较远,但这些难熔质点表面 往往存在细微凹坑和裂纹,其中尚未熔化的金属,可作为“依托”而形成晶体核 心。因此,可以在钢液中加入形核剂以细化晶粒。
( 2)
1974年-1989年:
技术特点:全连铸工艺,以连铸机为核心。