橡胶共混改性
氯化聚乙烯-橡胶共混防水卷材用橡塑粉的改性及应用研究

鼹 雕 嫩 嬲 鳓 嬲 鞭 瓣 掰 嘲 燃 嬲 瓣 糍 :
一
氯 化 聚 乙烯 一 胶 共 涅 防 水 卷 材 用 橡 橡 塑 粉 的 改 性 及 应 用研 究
杨 旭 邵 巍 于鸿雁 。张 宝莲 费学 宁 , , , ,
(. 1 天津城市建设学 院, 天津 30 8 ; . 市橡胶研究所 , 0 34 2天津 天津 3 0 4 ; 0 13 3天津市建筑材料产品质量监督检测 中心 , . 天津 3 0 8 ) 0 3 1 摘要 : 对氯化 聚 乙烯一 橡胶共混 防水卷材 用椽 塑粉进行 了改性 , 究 了粒径 、 研 增塑剂 、 塑化温度、 塑化 时间等 对改性橡 塑 粉性能的影响 , 出最佳改性条件并研究 了最佳改性条件 下橡 塑粉 的配方 。采用该改性橡塑粉制备 的共混卷材物理 力 得 学性能和耐候性能均能达到标 准的要 求, 而且可以节约生产成本 , 减少污染。
be d d wt u b r n ldn f cso at l ie lsiie,pat iig tmp rtr n i n p r r n e o h ln e i r b e,icu ig ef t fp ri e sz ,pat zr ls czn e eaue a d t h e c c i me o ef ma c fte o
4 ~ 0目的细橡 塑粉 。 08
1 增 塑改性 生产 工艺 . 2
不 同的增 塑 改性 工 艺对 改 性 橡 塑粉 物 理 力学 性 能 的影 响很 大 , 了保 证改 性效 果 , 为 本文 采 用 溶胀 增
目
硬 度 ( A) 邵 拉 伸 强度 / a MP
芳烃油
5 8 1 . 62
制备 出成 本更低 、 能更好 的防水卷 材 。 性
丁苯橡胶共混改性(DOC)

---------------材料科学与工程专业成型加工工艺课程设计题目:丁苯橡胶的增强改性姓名:季赛学号: 150412108班级: 2012级材料(1)班指导老师:张建耀职称:高级工程师\教授起止日期: 2015.11.23——2015.12.6目录1.设计背景 (4)1.1改性加工目的 (4)1.2乳聚丁苯橡胶 (6)1.3溶聚丁苯橡胶 (6)1.4粉末丁苯橡胶 (8)2.丁苯橡胶增强改性加工工艺原理 (8)2.1炭黑增强丁苯橡胶应用 (8)2.2炭黑的补强机理 (8)3.丁苯橡胶改性原料、助剂及设备介绍 (9)3.1原料及助剂 (9)1)原料 (9)2)炭黑 (10)3)硬脂酸 (10)4)氧化锌 (11)6)防老剂 (11)7)石蜡油 (11)8)防焦剂 (12)9)促进剂 (12)10)硫化剂 (13)3.2主要设备与仪器 (13)3.2.1混炼机 (13)3.2.2拉伸试验机 (14)4.加工工艺及加工流程图 (14)4.1 配方设计 (14)4.2加工方法 (15)1)炼前处理 (15)2)炭黑-橡胶混炼 (15)3)后加工工艺 (16)4)强度测量 (16)4.2产品性能测试项目、性能及测试标准 (16)1)性能指标 (16)2)性能参数标准 (18)4.3加工流程图 (18)5. 设计总结 (18)1.设计背景丁苯橡胶(SBR) ,又称聚苯乙烯丁二烯共聚物。
其物理机构性能,加工性能及制品的使用性能接近于天然橡胶,有些性能如耐磨、耐热、耐老化及硫化速度较天然橡胶更为优良,可与天然橡胶及多种合成橡胶并用,广泛用于轮胎、胶带、胶管、电线电缆、医疗器具及各种橡胶制品的生产等领域,是最大的通用合成橡胶品种,也是最早实现工业化生产的橡胶品种之一。
中文名: 丁苯橡胶外文名: Polymerized Styrene Butadiene Rubber 密度: 1.04 g/mL 性状: 白色疏松柱状固体1.1改性加工目的炭黑增强丁苯橡胶是以橡胶为基体,以炭黑颗粒为增强相的复合材料。
橡胶工艺学复习思考题

《橡胶工艺学》复习思考题绪论1、简要说明生胶、混炼胶、硫化胶的区别和联系。
2、橡胶最典型的特征是什么?3、橡胶配方的基本组成包括哪些成分?各成分有何作用?4、橡胶基本的加工工艺过程有哪些?5、橡胶配合加工过程中的测试内容包括哪些?第一章生胶1、写出通用橡胶的名称和英文缩写。
2、天然橡胶的分级方法有哪几种?烟片胶和标准胶各采用什么方法分级?3、什么是塑性保持率?有何物理意义?4、天然橡胶中非橡胶成分有哪些?各有什么作用?5、什么是自补强性?6、写出天然橡胶的结构式。
从分子链结构分析为什么NR容易被改性,容易老化?7、NR最突出的物理性能有哪些?为什么NR特别适合作轮胎胶料?8、IR和NR在结构和性能上有什么不同?9、根据合成方法不同,丁苯橡胶有哪两种?10、轮胎胎面胶中使用丁苯橡胶主要是利用其什么特点?为什么SSBR比ESBR更适合做轮胎胎面胶料?11、BR最突出的性能有哪些?轮胎的胎侧使用BR是利用其什么特点/12、什么是冷流性?影响冷流性的因素有哪些?各是如何影响的?13、为什么乙丙橡胶特别适合作电线电缆的外包皮?为什么乙丙胶特别适合作户外使用的橡胶制品如各种汽车的密封条、防水卷材等?14、IIR最突出的性能有哪些?IIR作内胎是利用其什么特点?为什么IIR可以用作吸波材料?15、什么橡胶具有抗静电性?通用橡胶中耐油性最好的橡胶是什么?16、什么是氧指数?哪些橡胶具有阻燃性?17、为什么CR的耐老化、耐天候性要优于其他不饱和橡胶?18、耐热性、耐油性最好的橡胶是什么?什么橡胶可以耐王水的腐蚀?19、耐高低温性能最好的橡胶是什么?耐磨性最好的橡胶是什么?可以做水果保鲜材料的橡胶是什么?为什么硅橡胶特别适合制作航空航天器密封材料?20、哪些橡胶具有生理惰性,可以植入人体?21、通用橡胶中,哪些橡胶具有自补强性?22、什么是热塑性弹性体?23、SMR5、SCR10、SBR1502、SBR1712各表示什么橡胶?第二章硫化体系1、什么是硫化?橡胶硫化反应过程可分为哪几个阶段?2、画出硫化曲线,标出各阶段的名称。
乙丙橡胶与SBR、NBR共混改性的综述
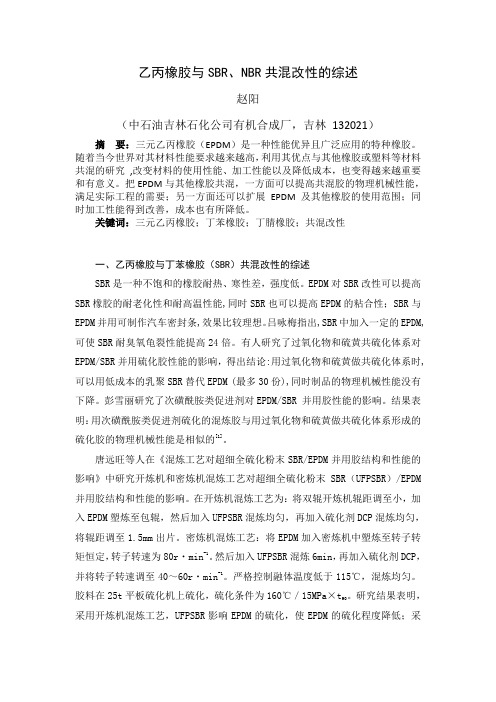
乙丙橡胶与SBR、NBR共混改性的综述赵阳(中石油吉林石化公司有机合成厂,吉林132021)摘要:三元乙丙橡胶(EPDM)是一种性能优异且广泛应用的特种橡胶。
随着当今世界对其材料性能要求越来越高,利用其优点与其他橡胶或塑料等材料共混的研究,改变材料的使用性能、加工性能以及降低成本,也变得越来越重要和有意义。
把EPDM与其他橡胶共混,一方面可以提高共混胶的物理机械性能,满足实际工程的需要;另一方面还可以扩展EPDM及其他橡胶的使用范围;同时加工性能得到改善,成本也有所降低。
关键词:三元乙丙橡胶;丁苯橡胶;丁腈橡胶;共混改性一、乙丙橡胶与丁苯橡胶(SBR)共混改性的综述SBR是一种不饱和的橡胶耐热、寒性差,强度低。
EPDM对SBR改性可以提高SBR橡胶的耐老化性和耐高温性能,同时SBR也可以提高EPDM的粘合性;SBR与EPDM并用可制作汽车密封条,效果比较理想。
吕咏梅指出,SBR中加入一定的EPDM,可使SBR耐臭氧龟裂性能提高24倍。
有人研究了过氧化物和硫黄共硫化体系对EPDM/SBR并用硫化胶性能的影响,得出结论:用过氧化物和硫黄做共硫化体系时,可以用低成本的乳聚SBR替代EPDM (最多30份),同时制品的物理机械性能没有下降。
彭雪丽研究了次磺酰胺类促进剂对EPDM/SBR 并用胶性能的影响。
结果表明:用次磺酰胺类促进剂硫化的混炼胶与用过氧化物和硫黄做共硫化体系形成的硫化胶的物理机械性能是相似的[1]。
唐远旺等人在《混炼工艺对超细全硫化粉末SBR/EPDM并用胶结构和性能的影响》中研究开炼机和密炼机混炼工艺对超细全硫化粉末SBR(UFPSBR)/EPDM 并用胶结构和性能的影响。
在开炼机混炼工艺为:将双辊开炼机辊距调至小,加入EPDM塑炼至包辊,然后加入UFPSBR混炼均匀,再加入硫化剂DCP混炼均匀,将辊距调至1.5mm出片。
密炼机混炼工艺:将EPDM加入密炼机中塑炼至转子转矩恒定,转子转速为80r・min-1。
BR_SBR橡胶共混

目录目录 ------------------------------------------------------------------------------------------------------------------ 11.前言---------------------------------------------------------------------------------------------------------------- 22.橡胶共混改性 --------------------------------------------------------------------------------------------------- 2 2.1橡胶共混改性的目的 ------------------------------------------------------------------------------------- 2 2.2橡胶共混改性的方法 ------------------------------------------------------------------------------------- 3 2.3共混物形态结构的类型及与性能的关系 ------------------------------------------------------------ 32.3.1均相结构 ----------------------------------------------------------------------------------------------- 32.3.2单相连续结构(海岛结构) ---------------------------------------------------------------------- 32.3.3两相连续结构(海海结构) ---------------------------------------------------------------------- 4 2.4影响共混物形态结构的因素 ---------------------------------------------------------------------------- 42.4.1组分的浓度-------------------------------------------------------------------------------------------- 42.4.2组分粘度 ----------------------------------------------------------------------------------------------- 42.4.3内聚能 -------------------------------------------------------------------------------------------------- 42.4.4组分相容性-------------------------------------------------------------------------------------------- 42.4.5共混时间 ----------------------------------------------------------------------------------------------- 52.4.6共混方法 ----------------------------------------------------------------------------------------------- 52.4.7加工助剂 ----------------------------------------------------------------------------------------------- 5 2.5共交联 -------------------------------------------------------------------------------------------------------- 52.5.1同步硫化 ----------------------------------------------------------------------------------------------- 62.5.2相间交联 ----------------------------------------------------------------------------------------------- 62.6 顺丁橡胶(BR)/丁苯橡胶(BSR)共混改性 ------------------------------------------------------ 63.参考文献 --------------------------------------------------------------------------------------------------------- 81.前言共混是指共同混合,是一种物理方法,使几种材料均匀混合,以提高材料性能的方法,工业上用炼胶机将不同橡胶或橡胶与塑料,均匀地混炼成胶料是典型的例子,也可以在聚合物中加入某些特殊性能的成分以改变聚合物的性能如导电性能等。
再生乳胶手套环氧化天然橡胶共混体的物理性能天然接枝淀粉的影响

伸长率(
B)
2.
3 机械性能
图 3A 和 3B 示出了 ENR 硫化胶,
GNR 硫化
图 5 GNR(
a)、
85/15ENR/GNR(
b)、
50/50ENR/GNR(
c)
和 15/85ENR/GNR(
d)的 TGA 温谱图
强 度 为 18MPa. GNR 硫 化 胶 的 拉 伸 强 度 为
14MPa,如图 3A 所 示. 向 ENR 中 加 入 GNR 后
ENR 硫化胶的机械性能比初始 ENR 高.这可解
释为橡胶基质中 较 高 硫 化 程 度 导 致 ENR 硫 化 胶
中外部载 荷 传 递 效 率 较 高.65/35ENR/GNR 共
混体的拉伸强度为 21MPa.50/50ENR/GNR 共
混体的拉伸强度 比 初 始 胶 料 高,表 明 产 生 了 协 同
作用.ENR 硫化 胶、GNR 硫 化 胶 及 其 共 混 体 的
伸长率如图 3B 所 示.GNR 的 拉 断 伸 长 率 最 小,
为 640% .加入 ENR 后 橡 胶 共 混 体 的 拉 断 伸 长
中 GNR 含量从 50/50 增加到 15/80(
w/w)时,硫
化 ENR/GNR 共混体的溶胀比为250% .这些结
果表明,共混体组 分 间 存 在 化 学 相 互 作 用 和 界 面
相互作用,能够通 过 延 长 共 混 体 试 样 中 的 平 均 扩
散路径来降低溶剂输运速率.
胶及其共混 体 的 机 械 性 能.ENR 硫 化 胶 的 拉 伸
n).表 1 和表 2 示出了共混体配方.
表 1 GNR 和 ENR25 共混胶料配方
共混改性的主要设备整体流程工艺参数
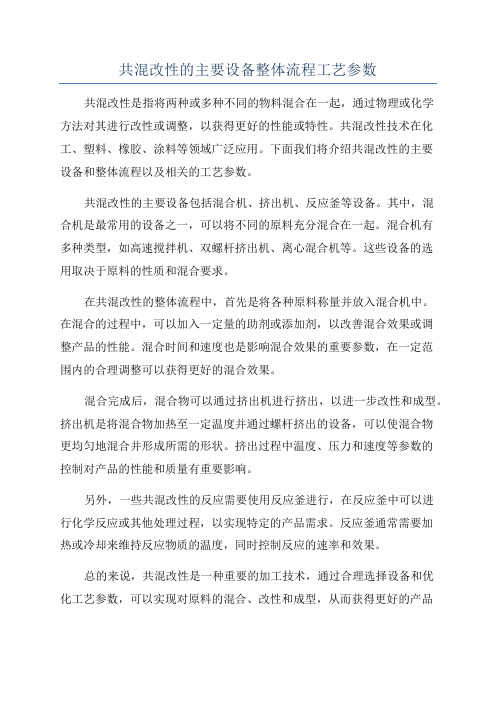
共混改性的主要设备整体流程工艺参数共混改性是指将两种或多种不同的物料混合在一起,通过物理或化学方法对其进行改性或调整,以获得更好的性能或特性。
共混改性技术在化工、塑料、橡胶、涂料等领域广泛应用。
下面我们将介绍共混改性的主要设备和整体流程以及相关的工艺参数。
共混改性的主要设备包括混合机、挤出机、反应釜等设备。
其中,混合机是最常用的设备之一,可以将不同的原料充分混合在一起。
混合机有多种类型,如高速搅拌机、双螺杆挤出机、离心混合机等。
这些设备的选用取决于原料的性质和混合要求。
在共混改性的整体流程中,首先是将各种原料称量并放入混合机中。
在混合的过程中,可以加入一定量的助剂或添加剂,以改善混合效果或调整产品的性能。
混合时间和速度也是影响混合效果的重要参数,在一定范围内的合理调整可以获得更好的混合效果。
混合完成后,混合物可以通过挤出机进行挤出,以进一步改性和成型。
挤出机是将混合物加热至一定温度并通过螺杆挤出的设备,可以使混合物更均匀地混合并形成所需的形状。
挤出过程中温度、压力和速度等参数的控制对产品的性能和质量有重要影响。
另外,一些共混改性的反应需要使用反应釜进行,在反应釜中可以进行化学反应或其他处理过程,以实现特定的产品需求。
反应釜通常需要加热或冷却来维持反应物质的温度,同时控制反应的速率和效果。
总的来说,共混改性是一种重要的加工技术,通过合理选择设备和优化工艺参数,可以实现对原料的混合、改性和成型,从而获得更好的产品性能和质量。
在实际应用中,需要充分了解原料的性质和要求,合理设计工艺流程,并不断优化和改进,以满足市场的需求和要求。
三元乙丙橡胶的共混改性
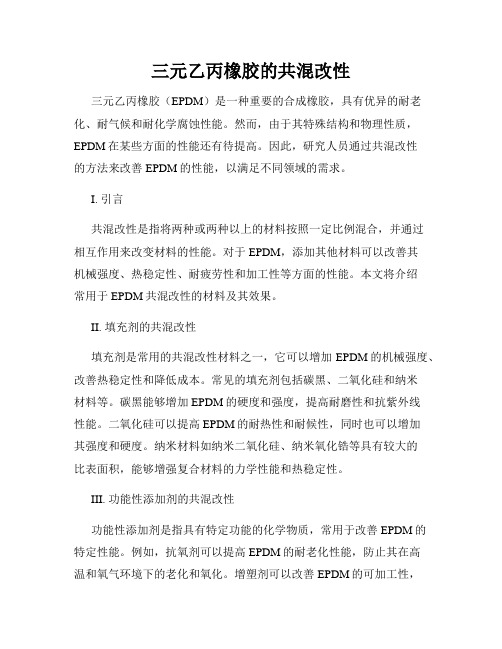
三元乙丙橡胶的共混改性三元乙丙橡胶(EPDM)是一种重要的合成橡胶,具有优异的耐老化、耐气候和耐化学腐蚀性能。
然而,由于其特殊结构和物理性质,EPDM在某些方面的性能还有待提高。
因此,研究人员通过共混改性的方法来改善EPDM的性能,以满足不同领域的需求。
I. 引言共混改性是指将两种或两种以上的材料按照一定比例混合,并通过相互作用来改变材料的性能。
对于EPDM,添加其他材料可以改善其机械强度、热稳定性、耐疲劳性和加工性等方面的性能。
本文将介绍常用于EPDM共混改性的材料及其效果。
II. 填充剂的共混改性填充剂是常用的共混改性材料之一,它可以增加EPDM的机械强度、改善热稳定性和降低成本。
常见的填充剂包括碳黑、二氧化硅和纳米材料等。
碳黑能够增加EPDM的硬度和强度,提高耐磨性和抗紫外线性能。
二氧化硅可以提高EPDM的耐热性和耐候性,同时也可以增加其强度和硬度。
纳米材料如纳米二氧化硅、纳米氧化锆等具有较大的比表面积,能够增强复合材料的力学性能和热稳定性。
III. 功能性添加剂的共混改性功能性添加剂是指具有特定功能的化学物质,常用于改善EPDM的特定性能。
例如,抗氧剂可以提高EPDM的耐老化性能,防止其在高温和氧气环境下的老化和氧化。
增塑剂可以改善EPDM的可加工性,使其更易于加工成型。
促进剂可以提高EPDM硫化过程中的交联效率,改善硫化性能。
IV. 共混改性的影响因素共混改性结果的好坏受多种因素的影响,例如添加剂的种类、添加量、分散性和相容性等。
添加剂的种类和添加量需要根据具体的应用要求来选择,不同领域对EPDM的要求不同,因此需要针对性地添加不同的添加剂。
此外,添加剂的分散性和相容性也是影响共混改性效果的重要因素,良好的分散性和相容性可以提高添加剂与EPDM的相互作用效果。
V. 其他共混改性方法除了填充剂和功能性添加剂,还有其他一些共混改性方法可用于改性EPDM。
例如,通过化学交联改性可以提高EPDM的热稳定性和耐疲劳性。
EPDM-PP共混物老化性能的研究.
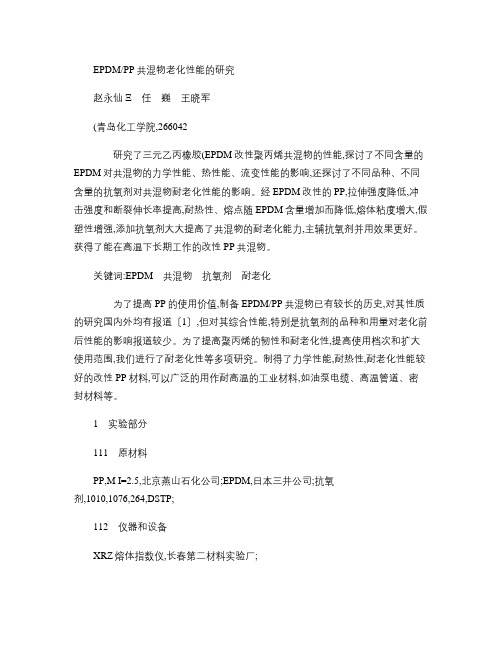
EPDM/PP共混物老化性能的研究赵永仙Ξ任巍王晓军(青岛化工学院,266042研究了三元乙丙橡胶(EPDM改性聚丙烯共混物的性能,探讨了不同含量的EPDM对共混物的力学性能、热性能、流变性能的影响,还探讨了不同品种、不同含量的抗氧剂对共混物耐老化性能的影响。
经EPDM改性的PP,拉伸强度降低,冲击强度和断裂伸长率提高,耐热性、熔点随EPDM含量增加而降低,熔体粘度增大,假塑性增强,添加抗氧剂大大提高了共混物的耐老化能力,主辅抗氧剂并用效果更好。
获得了能在高温下长期工作的改性PP共混物。
关键词:EPDM共混物抗氧剂耐老化为了提高PP的使用价值,制备EPDM/PP共混物已有较长的历史,对其性质的研究国内外均有报道〔1〕,但对其综合性能,特别是抗氧剂的品种和用量对老化前后性能的影响报道较少。
为了提高聚丙烯的韧性和耐老化性,提高使用档次和扩大使用范围,我们进行了耐老化性等多项研究。
制得了力学性能,耐热性,耐老化性能较好的改性PP材料,可以广泛的用作耐高温的工业材料,如油泵电缆、高温管道、密封材料等。
1实验部分111原材料PP,M I=2.5,北京燕山石化公司;EPDM,日本三井公司;抗氧剂,1010,1076,264,DSTP;112仪器和设备XRZ熔体指数仪,长春第二材料实验厂;XCT-40冲击实验机,承德材料实验机厂;维卡软化点实验机,承德材料实验机厂;SR-1差示扫描量热器,北京光学仪器厂;热老化箱,国产;SK-160B双辊筒炼胶机,上海橡胶机械厂;XXL-100A型拉力实验机,广州材料实验机厂;QLB-025吨平板硫化机,上海第一橡胶机械厂。
113试样制备按配方准确称量配料,在双辊上混炼,再在平板硫化机上模压,然后经机加工,制得试样。
1.4性能测试拉伸强度和断裂伸长率按G B1042-92进行;冲击强度按G B1043-7进行;维卡软化温度按G B1633-79进行;熔体指数按G B133682-83进行;老化实验按G B7141-86进行。
丁基橡胶共混改性研究概况

性 弹性 体等 领域 的研 究情 况 。
1 丁基 橡胶 和 其它橡 胶 的共 混改性
1 1 丁 基 橡 胶 为 连 续 相 .
与 CI I R并 用 比为 8 / 0 N 2 0 2 、 2 0炭 黑 用 量 为 8 O份 时 ,共 混硫 化胶 有 良好 的压 缩 弹性 模 量 ,软化 剂 的 加入 会 降低 共 混硫 化胶 的压 缩 弹性模 量 。
绍 了 丁基 橡 胶 作 为基 质胶 、 分散 相 以 及其 与树 脂 的共 混 改 性 研 究 概 况 。 关键词
分类号
丁 基 橡 胶 ;共 混 ;改 性
T336 0 2 .
Adv n e i ⅡR Blnd a c n e s
Z HAO n Yi me ZH i AO n a g T Ya f n ANG Ha q n n i
b e p id n n y ied . Th d v l p n s f IR e d i cu i g I Ru be, IR/ sn a d e n a pl i ma f l s e e e eo me t o I bln s n ld n IR/ b r I Re i n
I P M IR与 E D I 肌 D I P M相 容 性 较好 ,而且 可 以达 到 共硫 化 ;I R E D I / P M质 量 比为 7 / 5时 ,共 52 混物 的物 理机 械性 能和 老化 性 能较好 ;用硫 黄 、低
I C I M
引入 A M有效 地 改善 了 IR和 C I C I IR
维普资讯
20 0 8年 6月
Jn 2 0 uCHI S OURNAL OF T NE E J ROP C I AL AGRI UL C TURE
乙丙橡胶共混改性ABS树脂、低密度聚乙烯、高密度聚乙烯
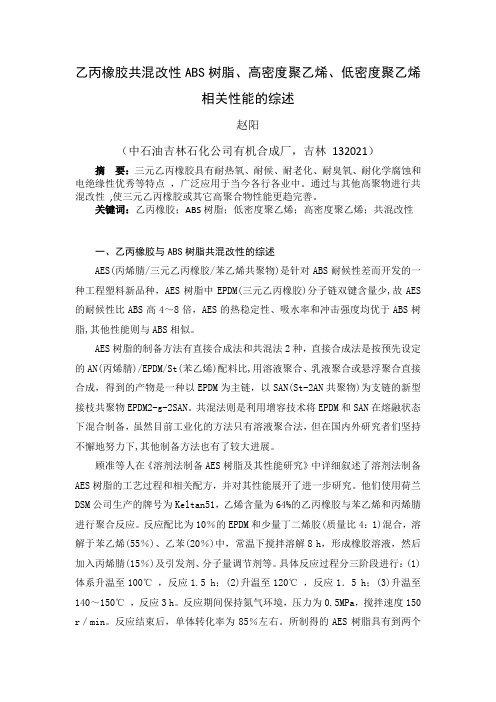
乙丙橡胶共混改性ABS树脂、高密度聚乙烯、低密度聚乙烯相关性能的综述赵阳(中石油吉林石化公司有机合成厂,吉林132021)摘要:三元乙丙橡胶具有耐热氧、耐候、耐老化、耐臭氧、耐化学腐蚀和电绝缘性优秀等特点,广泛应用于当今各行各业中。
通过与其他高聚物进行共混改性,使三元乙丙橡胶或其它高聚合物性能更趋完善。
关键词:乙丙橡胶;ABS树脂;低密度聚乙烯;高密度聚乙烯;共混改性一、乙丙橡胶与ABS树脂共混改性的综述AES(丙烯腈/三元乙丙橡胶/苯乙烯共聚物)是针对ABS耐候性差而开发的一种工程塑料新品种,AES树脂中EPDM(三元乙丙橡胶)分子链双键含量少,故AES 的耐候性比ABS高4~8倍,AES的热稳定性、吸水率和冲击强度均优于ABS树脂,其他性能则与ABS相似。
AES树脂的制备方法有直接合成法和共混法2种,直接合成法是按预先设定的AN(丙烯腈)/EPDM/St(苯乙烯)配料比,用溶液聚合、乳液聚合或悬浮聚合直接合成,得到的产物是一种以EPDM为主链,以SAN(St-2AN共聚物)为支链的新型接枝共聚物EPDM2-g-2SAN。
共混法则是利用增容技术将EPDM和SAN在熔融状态下混合制备,虽然目前工业化的方法只有溶液聚合法,但在国内外研究者们坚持不懈地努力下,其他制备方法也有了较大进展。
顾准等人在《溶剂法制备AES树脂及其性能研究》中详细叙述了溶剂法制备AES树脂的工艺过程和相关配方,并对其性能展开了进一步研究。
他们使用荷兰DSM公司生产的牌号为Keltan51,乙烯含量为64%的乙丙橡胶与苯乙烯和丙烯腈进行聚合反应。
反应配比为10%的EPDM和少量丁二烯胶(质量比4:1)混合,溶解于苯乙烯(55%)、乙苯(20%)中,常温下搅拌溶解8 h,形成橡胶溶液,然后加入丙烯腈(15%)及引发剂、分子量调节剂等。
具体反应过程分三阶段进行:(1)体系升温至100℃,反应1.5 h;(2)升温至120℃,反应1.5 h;(3)升温至140~150℃,反应3 h。
P(AM—g—NBR)改性共混型吸水膨胀丁腈橡胶制备与性能研究

工艺条件对 WS R—N B力学性能及吸水性能 的影响 。
1 实 验 部 分
1 1 主 要原 料 .
丁腈橡胶 ( 4 ) 中国石油 兰州石化公 司; N 1, 丙烯酰胺 ( M, A 分 析纯 ) 丙 烯 酸 ( A, 析 纯 ) 十 二 烷 基苯 磺 酸 钠 ( A , 学 , A 分 , L s化 纯 ) 以上试剂均 为成都市科龙化工试剂 厂生产 ; , 2一丙烯酰胺基
i ce s ft mo n ft AR —P .b ti h sc lp o e t sde r a e . n r a e o he a u to he S A u t p y ia r p ri c e s d s e Ke wo d y r s:wae tr—s la l b r u a ine—a rl n ti b e welb e r be ;b td e u c yo irl r b r;a r l mi e g a td b a in eu e ya d r fe utd e e—a r lni ie e o t l y r u b r ln i g r b e ;b e d n
吸水膨胀橡胶( t —s eal R b e, R) Wa r w l be u brWS 主要是 由弹 e l 性体 ( 如橡胶 ) 与亲水性 物质 ( 如吸水性树 脂 ,A 组 成 的多 组 S R) 分体系。弹性体与吸水性组分的相 容性会影 响到 吸水性物质 在 弹性体基体 中的分散程度 与亲合程 度 , 而影 响到吸水 膨胀性 进 能、 机械性能及 耐用性 。按照制备方法的不 同 , 吸水膨 胀橡胶 可
橡胶改性PP共混体系的研究

·14 ·
塑 料 工 业
2001 年
其与聚丙烯的接触面积增大 ,提高橡胶和塑料的界面 结合强度 ,所以其力学性能较好 。以 DCP 作硫化体 系 ,共混物的力学性能较差 ,这是因为配合体系中的防 老剂的分解物对于 DCP 类的过氧化物的硫化有抑制 作用 ,同时对聚丙烯起交联和降解作用 。
表 1 不同硫化体系对共混物力学性能影响
关键词 :丁苯橡胶 乙丙橡胶 丁腈橡胶 聚丙烯 动态硫化
为了充分利用聚丙烯原材料丰富 ,价格低廉 ,综合 性能好的特点 。本文将采用动态硫化法在高温辊上制 备橡胶/ 聚丙烯的共混物 ,以提高其抗冲击性能 ,使其 在更多的领域得到应用 。
1 实验部分
1. 1 主要原料 PP ,EPS30R ,齐鲁石化 ; 乳聚 SBR ,1502 ,齐鲁石
第 29 卷第 1 期 2001 年 1 月
塑料工业 CHINA PLASTICS INDUSTR Y
Vol 29 No 1 Jan 2001
橡胶改性 PP 共混体系的研究 Ξ
郭红革 谢 雁 葛 涛 李 玮
(青岛化工学院高分子材料研究所 ,266042)
本文研究了 SBR/ PP 共混比 、硫化体系 、不同橡胶以及增容剂对橡胶/ PP 共混物力学性能的影响 。试验得出 :橡塑 比 (SBR/ PP) 在 30/ 70 ,采用半有效硫化体系 (CZ/ S) 时 ,所制得共混物力学性能较好 。共混体系 PP/ PO E 的综合性能比 PP/ EPDM 、PP/ SBR、PP/ NBR 共混体系要好 。加入增容剂 PP - g - MAH 可以显著提高共混物的力学性能 。
表 2 不同胶料对共混物力学性能的影响
Tab 2 Effect of different rubber on blend mechanical properties
丁腈橡胶与尼龙6共混性能的研究
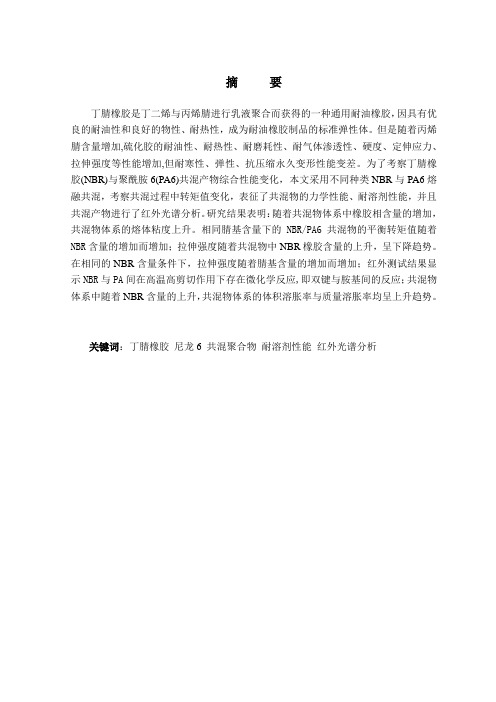
摘要丁腈橡胶是丁二烯与丙烯腈进行乳液聚合而获得的一种通用耐油橡胶,因具有优良的耐油性和良好的物性、耐热性,成为耐油橡胶制品的标准弹性体。
但是随着丙烯腈含量增加,硫化胶的耐油性、耐热性、耐磨耗性、耐气体渗透性、硬度、定伸应力、拉伸强度等性能增加,但耐寒性、弹性、抗压缩永久变形性能变差。
为了考察丁腈橡胶(NBR)与聚酰胺6(PA6)共混产物综合性能变化,本文采用不同种类NBR与PA6熔融共混,考察共混过程中转矩值变化,表征了共混物的力学性能、耐溶剂性能,并且共混产物进行了红外光谱分析。
研究结果表明:随着共混物体系中橡胶相含量的增加,共混物体系的熔体粘度上升。
相同腈基含量下的NBR/PA6共混物的平衡转矩值随着NBR含量的增加而增加;拉伸强度随着共混物中NBR橡胶含量的上升,呈下降趋势。
在相同的NBR含量条件下,拉伸强度随着腈基含量的增加而增加;红外测试结果显示NBR与PA间在高温高剪切作用下存在微化学反应,即双键与胺基间的反应;共混物体系中随着NBR含量的上升,共混物体系的体积溶胀率与质量溶胀率均呈上升趋势。
关键词:丁腈橡胶尼龙6 共混聚合物耐溶剂性能红外光谱分析AbstractNitrile-butadiene rubber is obtain by butadiene and acrylonitrile in emulsion polymerization to get on a universal oil resistant rubber, because of excellent oil resistance and good property heat-resistant became the standard of oil resistant rubber elastomers. But with the content of acrylonitrile increased, the vulcanizates oil resistant, heat-resistant, abrasion resistance, gas permeability resistance, hardness, elongation, tensile strength performance increase, but the low temperature resistance,elasticity, resistance of permanent deformation to compression are go bad. In order to examine the comprehensive performance changes of nitrile-butadiene rubber and polyamide 6(PA6) blending product, this thesis using different kind of NBR and PA6 for melt blending, inspects the changes of balance torque values during blending process. Research the mechanical properties, solvent resistance performance of blending product,and take a series of tests by infrared spectroscopic analysis.The research results show that the melt viscosity is rising up with the increase of the content of the NBR . In the same content of nitrile group the NBR and PA6 balance torque values is rising up with the increase of content of basic-rubber,the tensile strengthis reduced with the increase of content of basic-rubber. .In the same content of NBR, the tensile strength is rising up with the content of nitrile group; The infrared spectroscopic analysis test results show that there have micro chemical reactions between with NBR and PA6 in high temperature and high shear function, namely the reaction between double bond and amino group; V olume swelling ratio and quality swelling ratio at blend system is rising up with the increase of content of basic-rubbe.Keyword:Nitrile-butadiene rubber Polyamide6 Polymer blend Solvent resistance Infrared spectroscopic analysis目录摘要 (I)Abstract (II)第一部分文献综述 (1)1.1 前言 (1)1.2 NBR的结构与性能的关系 (1)1.2.1 NBR 的生产工艺 (2)1.2.2 改性NBR品种 (2)1.3 丁晴橡胶在国内外发展现状 (3)1.3.1 国内NBR发展现状 (3)1.3.2 国外NBR发展现状 (4)聚酰胺的增韧研究 (4)聚烯烃弹性体增韧机理 (4)1.4.2 PA/工程塑料合金增韧机理 (5)1.4.3 无机非弹性体增韧机理 (5)1.4.4 PA的物理化学性质的优缺点 (5)1.4.5 尼龙6(PA6)物理化学性质 (6)1.5 NBR的共混物 (7)1.5.1 NBR/PVC (7)1.5.2 NBR/PP[20] (7)1.5.3 NBR/氯磺化聚乙烯(CSM) (7)1.5.4 NBR/PA (8)1.6 红外光谱分析 (14)1.7 本论文的研究方案 (15)第二章实验部分 (16)2.1 NBR与PA6共混 (16)2.1.1 实验配方 (16)2.1.2 实验原料 (17)2.2 耐溶剂性测试 (17)2.3 红外光谱测试 (18)2.4 力学性能测试 (18)第三章结果与讨论 (19)3.1 NBR/PA6熔融共混过程中转矩值变化 (19)共混物的红外光谱分析 (21)3.4 NBR/PA6共混物的耐溶剂性能 (23)结论 (26)致谢 (27)参考文献 (28)第一部分文献综述1.1 前言丁腈橡胶(NBR)因具有优良的耐油性和良好的物性、耐热性,成为耐油橡胶制品的标准弹性体,广泛用于汽车、航空航天、石油开采、石油化工、纺织与印刷等领域的耐油橡胶部件。
聚合物共混改性7

聚合物共混改性原理
当L> Lc时,分散相粒子之间旳应力场相互影响很小,基体旳应力 场是这些孤立粒子应力场旳简朴加和,故基体塑性变形能力很小, 材料体现为脆性;
当L = Lc时,基体层发生平面应变到平面应力旳转变,降低了基体 旳屈服应力,当粒子间剪切应力旳叠加超出了基体平面应力状态下 旳屈服应力时,基体层发生剪切屈服,出现脆韧转变。
共混物PVC/ABS旳冲击强度与基体构成旳关系
聚合物共混改性原理
(2)橡胶相旳影响
① 橡胶含量旳影响
橡胶含量增长时,银纹旳引起、支化及终止速率亦增长,冲击强度随之 提升 。
HIPS在6~8%旳橡胶含量范围内,伴随橡胶含量旳增长,冲击强度明显 提升;超出8%,冲击强度旳提升渐缓。实际上并不能用大量增长橡胶含量 旳方法来提升冲击强度,因为伴随橡胶含量旳增长,拉伸、弯曲以及表面硬 度等指标下降,而且制品旳加工性能变坏,所以橡胶旳用量是根据多种原因 旳综合平衡来决定旳 。
聚合物共混改性原理
试验事实
HIPS等增韧塑料,基体韧性较小,屈服形变基本上是银纹化旳成果,所以 有明显旳应力发白现象。因为银纹化伴随体积旳增长,而横向尺寸基本不变, 所以拉伸时无细颈出现。基体韧性很大旳增韧塑料,如增韧PVC,屈服形变 主要是剪切带造成旳,所以在屈服形变过程中有细颈而无明显旳应力发白现 象。对于中间情况,例如HIPS/PPO共混物,银纹和剪切带都占相当旳百 分比,所以细颈及应力发白现象同步产生。
橡胶颗粒产生静张应力场旳概念无疑是正确旳。前面曾提到,橡胶颗粒旳应 力集中作用以及橡胶颗粒与基体热胀系数旳差别会在材料内部产生静张应力。
但是这种静张应力旳作用是不大可能足以使材料产生如此大旳屈服形变。所 以静张力虽可对基体旳形变产生一定程度旳活化作用,但是并非增韧旳主要 机理。而且该理论没有解释剪切屈服时经常伴随旳应力发白现象。
橡胶(并用)共混原理,您真的了解吗?

橡胶(并用)共混原理,您真的了解吗?概述橡胶共混的意义:改善工艺性能,使用性能和技术经济性能。
大约 70%以上的橡胶是以橡胶并用或橡塑并用的形式进行加工和使用。
橡胶共混的内容:相容性形成均相体的能力:热力学相容、工艺相容共混物形态结构:连续相、分散相、界面配合剂在共混物中分布:硫化助剂、填料的分布,共交联和物性橡胶的工艺相容性:通过机械方法或其他条件将热力学不相容体系混合,可以获得足够稳定的共混物,这种共混物在微观区域内构成多相形态,但在宏观上仍能保持其均匀性。
聚合物共混影响因素:混炼工艺条件:时间、强度、辊温、加工方法配方组成:生胶、共混比、相容剂、加工助剂共混物形态结构的影响因素一是粘度不匹配引起的不相容性,由于粘度相差太大,并用胶难以形成紧密结合的共混物;二是热力学不相容性,从而使共混物难以形成分子级共混;三是由于硫化速率不匹配引起的硫化不相容性。
(1) 聚合物共混时的分散过程分散相平均粒径的大小决定于:混炼时间、混炼强度、分散相用量。
分散相宏观破碎能↓,相容性↑,界面张力↓,分散相体积分数↓,剪切速率↑,则:平均粒径↓(2) 相容性对共混物形态结构的影响聚合物相容性两种极端:完全不相容完全相容或相容性极好。
较好的共混改性物:分散相大小适宜、需要多相结构、相之间结合力较强。
对于单纯热力学不相容性,改进的方法很多,最常见的方法是添加增容剂。
(3) 组分浓度对共混物形态的影响组分体积分数 > 74%,连续相;< 26%,分散相;26-74% ,视具体条件而定。
当二者的初始粘度和内聚能接近时,浓度大者易形成连续相。
(4) 组分粘度对共混物形态结构的影响二者粘度相差越大,分散相体积分数↑,分散相粒径↓;二者粘度接近,分散相体积分数↑,分散相粒径↑;粘度低组分,连续相;粘度相近,“海-海”结构。
对于单纯的粘度不匹配导致的不相容性,可以选择合适的牌号或通过改进共混工艺过程如加增塑剂、填料等调节各相的粘度使之匹配。
橡胶材料第三章橡胶的共混与改性

ΔGm=ΔHm-TΔSm≤0 (7-1)
式中 ΔHm-混合热;ΔSm-混合熵;T-绝对温度。 二元聚合物共混时,混合熵可用式(7-2)表示。
ΔSm=-R(n1lnφ1+n2lnБайду номын сангаас2) (7-2)
式中 n1 ,n2-分别为共混聚合物组分的物质的量; Φ1 ,Φ2—分别为共混聚合物组分的体积分数;R-气体常数。
第七章 橡胶的共混与改性
将两种或两种以上的不同橡胶或橡胶与合成树脂,借助机械力的作用 掺混成一体,用以制造各种橡胶制品,称为橡胶机械共混或橡胶的并用。 共混已成为橡胶改性的有效和重要手段。
第一节 概 述 一、橡胶共混的目的和意义 ? 改善橡胶的使用性能和/或加工性能
橡胶共混的主要目的是改善现有橡胶性能上的不足。例如天然橡胶, 因具有良好的综合力学性能和加工性能,被广泛用应用,但它的耐热氧老 化性、耐臭氧老化性、耐油性及耐化学介质性欠佳。
三、聚合物相容性的预测 当决定将一种聚合物与另一种聚合物进行共混改性时,首先要对这两种
聚合物相容性的程度进行预测,以判断共混工艺的可行性。如果两种聚合物 有一定的相容性或相容性良好,可直接实施共混,否则应作增容共混处理。
12
预测聚合物是否相容最常用的方法是溶解度参数相近程度判断法,原 理如式(7-3)所示。两种聚合物的溶解度参数相差越小,越有利于ΔGm< 0 ,故相容性越好。对大量聚合物共混体系的研究发现,当两种聚合物的 溶解度参数之差大于0.5以后,两种聚合物便不能以任意比例实现工艺相 容,多数情况会出现相分离。
17
18
除了上述无规共聚物以外,某些嵌段共聚物或接枝共聚物也是常用的非 反应型相容剂。
- 1、下载文档前请自行甄别文档内容的完整性,平台不提供额外的编辑、内容补充、找答案等附加服务。
- 2、"仅部分预览"的文档,不可在线预览部分如存在完整性等问题,可反馈申请退款(可完整预览的文档不适用该条件!)。
- 3、如文档侵犯您的权益,请联系客服反馈,我们会尽快为您处理(人工客服工作时间:9:00-18:30)。
五、橡胶配方性能的检测
1、未硫化胶的加工性能检测
(1)可塑度的检测:威氏塑性计、华氏塑性计、德弗塑性计 (2)门尼粘度的检测:门尼粘度计(100℃下预热1min,旋转4min) (3)门尼焦烧的检测:门尼粘度计(120℃下t5) (4)硫化特性的检测:硫化仪 (5)口型膨胀率的测定:毛细管流变仪 (6)配合剂分散性测定:ASTM A法、B法、分散度仪、间接法 (7)应力松弛:应力松弛试验机 (8)综合加工性能测定:Brabender塑性仪、橡胶加工分析仪
2、实用配方的设计程序
(1)调查研究阶段 调查产品的使用条件、使用寿命等技术要求,了解生产设备和工 艺方法,查找文献资料,收集同类或相近产品的配方、工艺条件等; (2)制定试验计划阶段 根据性能和工艺要求及文献资料,提出产品的物理性能、使用性能、 和工艺性能的指标范围,确定关键指标,根据经验和参考资料提出试 验配方及变量范围,确定合适的试验设计方法; (3)实验室试验阶段 在实验室中,按计划进行试验,优选配方进行扩试; (4)扩试阶段 在生产或扩试条件下进行扩试,制备胶料进行工艺性能和物理性能 试验,调整工艺条件和配方至满足要求; (5)产品试制阶段 按照规定的标准和技术条件,试制产品,测试性能和使用性能。
三、撕裂强度
设计要点: (1)选用分子量大、常温下能结晶或滞后损失大的胶种; (2)采用CV硫化体系,硫黄用量2~3份,促进剂选用中等活性、平 坦性好的品种,如DM、CZ; (3)选用粒径小、结构性低的炭黑,选用各项同性的填料; (4)少用增塑剂; (5)其他方法:使用5份以内的短纤维; 使用分散剂,提高配合剂分散性;
3、结构相差较大,活性点不同的橡胶共混物的共交联
如NR/CR,采用S/DM与ZnO/MgO/NA-22复合硫化体系,使同步硫 化,但很难实现相间交联。
第五节 共混型热塑性弹性体
一、橡塑共混型热塑性弹性体
橡胶与塑料直接共混,橡胶不交联。性能较差。
二、动态硫化共混型热塑性弹性体
边混炼,边硫化,边剪切,共混物中橡胶相已经交联,分散在 塑料连续相中。性能好,可反复加工使用。 制备方法:高温开炼机制备 密炼机制备 双螺杆混合挤出机制备
2、组分粘度
一般粘度低的组分易形成连续相,粘度高的组分形成分散相,即 “软包硬”。两组分粘度相差越大,分散相的尺寸越大。
3、内聚能
两组分聚合物共混时,内聚能大的组分易形成分散相,内聚能低的 组分易形成连续相。
4、组分相容性
(1)相容性 两种物质混合时形成均相体系的能力。能力大,相容性 好。聚合物相容性有热力学相容、工艺相容和完全不相容三种情况。 (2)相容性判断方法 用溶解度参数相近程度判断法预测,越接近, 相容性越好。用小角中子散射法、脉冲核磁共振法、反相色谱法、电 子显微镜法、玻璃化温度法等方法表征,其中玻璃化温度法应用最广 泛,用DMA测共混物及组分聚合物的力学损耗-温度关系普图。 (3)对共混物形态结构影响 热力学相容易形成均相结构,工艺相容 及完全不相容一般形成海岛结构或海海结构。两组分相容性好,分散 相尺寸小,分散均匀,相界面模糊,界面层厚且稳固。 (4)不相容体系的增容 方法一是添加相容剂(如均匀剂、增容剂) 二是对聚合物进行化学改性。均匀剂多为脂肪烃树脂、环烷烃树脂、 芳香烃树脂等的混合物,以及嵌段或接枝聚合物,有非反应型和反应 型两类(P222)。
四、橡胶配方的设计程序
1、基本配方设计
(1)生胶的选择:根据制品的主要性能要求、工艺、使用条件和成 本选取 (2)硫化体系确定:根据胶种、胶料性能、工艺方法及要求(如焦 烧时间、正硫化时间)确定,重点选取硫化剂和促进剂 (3)补强填充体系确定:根据制品颜色、胶料性能、工艺要求、成 本等确定 (4)防护体系确定:根据制品颜色、使用条件来确定,多采用并用 (5)增塑体系确定:根据胶种、性能要求、工艺要求、成本等确定 (6)操作助剂选取:根据实际需要确定 (7)特种配合体系:根据实际需要确定
二、定伸应力和硬度
设计要点: (1)选用分子量大、分布窄,且能结晶或带极性基团的橡胶; (2)提高交联密度,增大硫黄和促进剂用量; (3)选用粒径小、结构性高、表面活性大的炭黑,且增大用量; (4)尽可能少用或不用增塑剂; (5)其他方法:使用酚醛树脂/硬化剂; 使用苯甲酸; 使用模量增强剂; 使用短纤维; 使用齐聚酯/过氧化物; 使用液体橡胶/引发剂 与TPI并用,硫黄用量在2.5份以内; 使用不饱和羧酸盐等。
3、两相连续结构(海海结构)
两组分均呈连续相,相互交错贯穿。在两组分粘度和用量相近时 会出现这种结构。 两相连续结构共混物的使用性能很差,会损伤两组分的优势性 能。但可以作为母炼胶使用,制备分散相尺寸很小的共混物,改善共 混物的性能。
二、影响共混物形态结构的因素
1、组分的浓度
当一种组分的浓度相。当分散相浓度不断增大时,分散相的尺寸不断 增大,当两则分浓度接近50/50时出现相逆转。动态硫化的热塑性弹 性体除外。
1、均相结构
两种聚合物达到链段级均匀分散的体系,在共混物的各点两种聚 合物的链段组成相同。在橡胶共混中很难得到。 均相结构的共混物性能为两种组分聚合物性能的加和平均值,性能 不是很理想。
2、单相连续结构(海岛结构)
一种组分形成连续相,另一种组分形成分散相。这种结构是橡胶共 混中常见的结构。 海岛结构共混物的性能在宏观上较多的保持了海相聚合物的性能, 又能体现出岛相聚合物带来的性能改善和赋予的新性能,使共混物的 使用价值远远超过单一聚合物的应用价值。此时岛相的尺寸大小、分 散均匀性及与海相的界面结构对共混物的性能影响较大,岛相尺寸在 3μm以下,一般0.5 ~1 μm最好;岛相分散越均匀,岛相对橡胶改性 作用就越充分;界面越模糊,界面层越厚,共混物性能越好。
二、橡胶与橡胶共混物的共交联
1、结构相近,活性相近的橡胶共混物的共交联
如NR/BR、NR/SBR、BR/SBR,相间交联不成问题,关键是 同步硫化。 解决办法:合理选择促进剂,一般采用促进剂并用如DM/NOBS。
2、结构和活性相差较大,有相同活性点的橡胶共交联
如NR/EPDM、NBR/EPDM,选择分配系数接近1的硫化助剂,或 将促进剂预先接枝到硫化速度慢的组分分子链上再混合,或将硫化 剂与硫化速度慢的组分先混合并预处理,再与另一组分混合。
第二节 橡胶配方设计与硫化胶性能的关系
一、拉伸强度
设计要点: (1)选用自补强性橡胶或结晶性、极性生胶;分子量要大,低分子少; (2)选用CV体系,促进剂采用M/D并用,适当提高硫黄用量; (3)选用粒径小、表面活性大的炭黑,用量40~60份,或白炭黑与 Si-69并用; (4)选用与橡胶相容性好的增塑剂,用量在5份以内; (5)其他方法:橡胶与树脂并用、橡胶化学改性、填料表面改性等。
第八章 橡胶配方设计
主要内容: 概述 橡胶配方设计与硫化胶性能的关系 橡胶配方设计与胶料加工性能的关系 橡胶配方设计方法
第一节 概述
一、橡胶配方设计内容
1、确定制品硫化胶的性能指标及范围; 2、确定配方的组成及用量; 3、确定加工工艺条件及范围。
二、橡胶配方分类与表示
1、分类 基础配方(标准配方):生胶或配合剂鉴定(各胶的基 础配方见P257~260); 性能配方(技术配方):为达到某种性能而进行的配方 设计,产品研发时所做的试验配方即为性能配方; 实用配方(生产配方):实际生产时所采用的配方。
第一节 概述
一、橡胶共混改性的目的
1、改善橡胶的使用性能 2、改善合成橡胶的加工工艺性能 3、降低成本 4、确定合理的混炼工艺方法 5、开发新型高分子材料
二、橡胶共混改性的方法
1、溶液共混 2、乳液共混 3、机械共混 (1)粉体共混;(2)熔体共混;(3)力化学共混
第二节 共混物的形态结构
一、共混物形态结构的类型及与性能的关系
2、表示方法
(1)基本配方:以质量份表示的配方,以生胶的质量为100份,其他配 合剂用量都以相应的质量份表示的配方; (2)质量分数配方:以质量分数表示的配方,以胶料的总质量为100 %,生胶和配合剂都以质量分数表示的配方; (3)体积分数配方:以胶料的总体积为100%,生胶和配合剂都以相应 的体积分数表示的配方; (4)生产配方:符合生产要求的质量配方,配方总质量等于炼胶机的 实际容量。
5、共混时间
随共混时间延长,分散相尺寸不断减小,但减小的趋势变缓,最 后趋于一平衡值。
6、共混方法
直接共混,分散相颗粒较大;两阶共混,分散相尺寸细小且大小 均匀。
7、加工助剂
加工助剂的加入,有利于分散相破碎,尺寸减小,分布变窄。
第三节 配合剂在橡胶共混物中的分配
一、硫化助剂的分配
取决于硫化助剂在两相聚合物中的溶解度大小,而溶解度大小又取 决于聚合物与硫化助剂的溶解度参数的差值。一般,硫化助剂在溶解度 参数大的组分中分布多,在硫化速度快的组分中消耗多。硫化助剂在橡 胶中容易扩散,在单一组分中,由高浓度向低浓度地方扩散,在多组分 体系中,由溶解度低的组分向溶解度高的组分扩散,扩散很快。
四、耐磨性
设计要点: (1)选用弹性好或强度高或有共轭结构的生胶,如BR、NR、SBR、 PU、ACM、IR、NBR、EPDM等; (2)选用硫黄/促进剂CZ或硫黄/促进剂CZ(主)/TMTD硫化体系, NR为主的胶料,硫黄用量1.8~2.5份;以BR为主胶料,硫黄用量 1.5~1.8份; (3)选用粒径小、表面活性大的炭黑,或新工艺炭黑,或白炭黑与 偶联剂Si-69并用;炭黑用量NR中45~50份,IR和非充油SBR中50~ 55份,充油SBR中60~70份,BR中90~100份; (4)少用增塑剂; (5)其他方法:贴聚氨酯 使用短纤维并合理取向 使用CEC胶; 使用分散剂,提高炭黑分散性
2、硫化胶性能测试
(1)力学性能测试:拉伸、撕裂、伸长率、定伸、永久变形用拉力机; 硬度用硬度计、压缩变形(恒定形变压缩永久变形、静压缩永久变形); 磨耗性能用阿克隆磨耗试验机或DIN磨耗试验机;疲劳破坏性能(有拉伸 疲劳和压缩疲劳、屈挠龟裂等)用屈挠疲劳试验机; (2)粘弹性测试:回弹性用冲击弹性试验机;蠕变用蠕变试验仪(压缩 型、拉伸型、剪切型);应力松弛用应力松弛仪(拉伸、压缩);有效弹 性和滞后损失用拉力机;动态粘弹性用动态模量仪、动态粘弹谱仪; (3)老化性能测试:热空气老化、臭氧老化、自然老化、人工天候老化、 湿热老化、光臭氧老化、耐黄变试验等,用各种老化箱; (4)低温性能测试:脆性温度、耐寒系数、吉门扭转、玻璃化温度、温 度-回缩试验等; (5)热性能测试:导热率、比热容、线膨胀系数、分解分度、马丁耐热性、 维卡耐热性等; (6)耐介质性、阻燃性、电性能、扩散和渗透性、粘接性能测试等。