双连拱隧道施工工法
双连拱隧道正洞台阶开挖施工工法
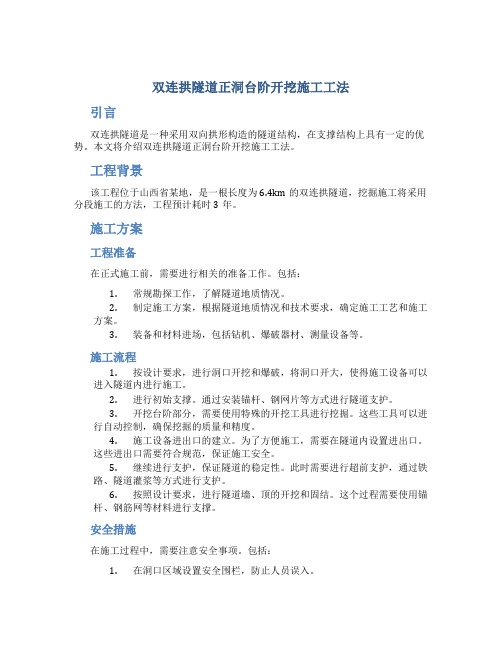
双连拱隧道正洞台阶开挖施工工法引言双连拱隧道是一种采用双向拱形构造的隧道结构,在支撑结构上具有一定的优势。
本文将介绍双连拱隧道正洞台阶开挖施工工法。
工程背景该工程位于山西省某地,是一根长度为6.4km的双连拱隧道,挖掘施工将采用分段施工的方法,工程预计耗时3年。
施工方案工程准备在正式施工前,需要进行相关的准备工作。
包括:1.常规勘探工作,了解隧道地质情况。
2.制定施工方案,根据隧道地质情况和技术要求,确定施工工艺和施工方案。
3.装备和材料进场,包括钻机、爆破器材、测量设备等。
施工流程1.按设计要求,进行洞口开挖和爆破,将洞口开大,使得施工设备可以进入隧道内进行施工。
2.进行初始支撑。
通过安装锚杆、钢网片等方式进行隧道支护。
3.开挖台阶部分,需要使用特殊的开挖工具进行挖掘。
这些工具可以进行自动控制,确保挖掘的质量和精度。
4.施工设备进出口的建立。
为了方便施工,需要在隧道内设置进出口。
这些进出口需要符合规范,保证施工安全。
5.继续进行支护,保证隧道的稳定性。
此时需要进行超前支护,通过铁路、隧道灌浆等方式进行支护。
6.按照设计要求,进行隧道墙、顶的开挖和固结。
这个过程需要使用锚杆、钢筋网等材料进行支撑。
安全措施在施工过程中,需要注意安全事项。
包括:1.在洞口区域设置安全围栏,防止人员误入。
2.保证施工现场通风。
3.施工人员穿戴好安全装备,保护好眼睛、呼吸道等器官。
4.对于施工设备进行定期检查,确保设备安全使用。
通过对双连拱隧道正洞台阶开挖施工工法的介绍,可以看出,这是一个比较复杂的工程,需要进行细致的规划和施工。
在施工过程中,需要加强安全管理,保证施工人员的安全。
复杂地质大跨度双连拱隧道三导洞并行施工工法(2)
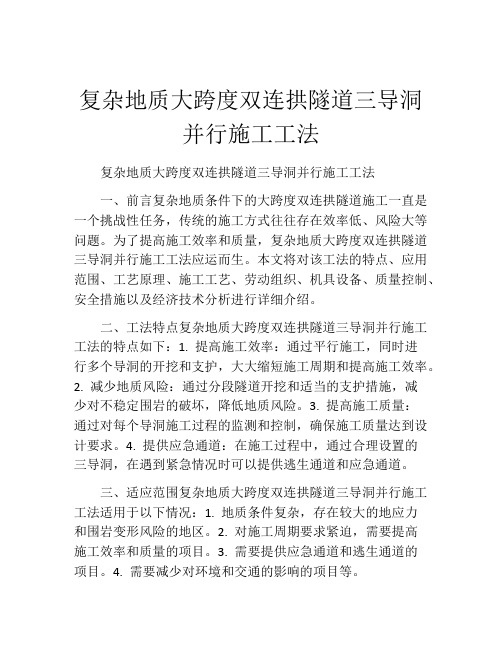
复杂地质大跨度双连拱隧道三导洞并行施工工法复杂地质大跨度双连拱隧道三导洞并行施工工法一、前言复杂地质条件下的大跨度双连拱隧道施工一直是一个挑战性任务,传统的施工方式往往存在效率低、风险大等问题。
为了提高施工效率和质量,复杂地质大跨度双连拱隧道三导洞并行施工工法应运而生。
本文将对该工法的特点、应用范围、工艺原理、施工工艺、劳动组织、机具设备、质量控制、安全措施以及经济技术分析进行详细介绍。
二、工法特点复杂地质大跨度双连拱隧道三导洞并行施工工法的特点如下:1. 提高施工效率:通过平行施工,同时进行多个导洞的开挖和支护,大大缩短施工周期和提高施工效率。
2. 减少地质风险:通过分段隧道开挖和适当的支护措施,减少对不稳定围岩的破坏,降低地质风险。
3. 提高施工质量:通过对每个导洞施工过程的监测和控制,确保施工质量达到设计要求。
4. 提供应急通道:在施工过程中,通过合理设置的三导洞,在遇到紧急情况时可以提供逃生通道和应急通道。
三、适应范围复杂地质大跨度双连拱隧道三导洞并行施工工法适用于以下情况:1. 地质条件复杂,存在较大的地应力和围岩变形风险的地区。
2. 对施工周期要求紧迫,需要提高施工效率和质量的项目。
3. 需要提供应急通道和逃生通道的项目。
4. 需要减少对环境和交通的影响的项目等。
工法的原理是通过分段施工和合理的支护措施来降低地质风险,同时通过对每个导洞施工过程的监测和控制,提高施工质量。
具体工艺原理如下:1. 分段施工:根据设计要求,将整个隧道分为多个段落,并逐段进行开挖和支护工作,有效控制施工过程中的地应力变化和围岩变形。
2. 合理支护:针对不同地质条件和围岩情况,采取合理的支护措施,包括钢拱架支护、喷射混凝土、锚杆和喷网等,保证施工安全和隧道的持久稳定。
3. 施工监测:通过对施工过程中的地应力、变形等参数的实时监测,及时调整施工工艺和支护措施,确保施工质量符合设计要求。
4. 并行施工:通过合理的施工计划和协调,同时对多个导洞进行开挖和支护工作,提高施工效率。
砂岩地层双连拱地铁隧道三导洞施工工法(2)

砂岩地层双连拱地铁隧道三导洞施工工法砂岩地层双连拱地铁隧道三导洞施工工法一、前言随着城市交通的发展,地铁成为现代城市中不可或缺的交通工具,地铁隧道的施工技术也日益重要。
砂岩地层是地铁隧道施工中常见的地质情况,如何在砂岩地层中稳定地开挖地铁隧道,并确保隧道的安全和质量,一直是施工者面临的挑战之一。
本文将介绍一种适用于砂岩地层的双连拱地铁隧道三导洞施工工法,详细阐述工法的特点、适应范围、工艺原理、施工工艺、劳动组织、机具设备、质量控制、安全措施、经济技术分析和工程实例。
二、工法特点双连拱地铁隧道三导洞施工工法具有以下特点:1.结构稳定:双连拱结构能够分散隧道顶部的荷载,在开挖过程中确保隧道的稳定性。
2.提高施工效率:该施工工法采用隧道分区连续作业的方式,可以同时进行开挖、支护和封闭,从而大大提高施工效率。
3.环保节能:施工过程中可以使用环保材料,减少噪音和粉尘的产生,保护环境和施工人员的健康。
4.适应性强:该工法适用于砂岩地层的地铁隧道施工,能够处理不同的地质条件,适应不同的隧道断面形式。
三、适应范围双连拱地铁隧道三导洞施工工法适用于以下情况:1.砂岩地层的地铁隧道施工,包括软砂岩、中硬砂岩和硬砂岩等不同性质的地层。
2.地铁隧道的施工需要高效率、高质量和节约成本,对施工周期要求较为紧迫的情况。
四、工艺原理双连拱地铁隧道三导洞施工工法的工艺原理主要包括施工工法与实际工程之间的联系和采取的技术措施。
具体分析和解释如下:1.施工工法与实际工程之间的联系:根据具体地质情况和隧道断面要求,确定施工工法的具体步骤和施工参数。
2.采取的技术措施:根据隧道的设计要求,选用合适的支护材料和支护结构,采用对砂岩地层适应性强的施工方法,确保隧道的安全和质量。
五、施工工艺双连拱地铁隧道三导洞施工工法的施工工艺分为以下几个阶段:1.前期准备:制定施工计划,组织人员和机具设备,开展现场勘察和地质调查,确定隧道设计参数。
2.导洞开挖:根据设计要求,在地面或洞外进行导洞开挖,采用先导后挖的方法,形成导洞。
超浅埋双连拱隧道三导坑开挖施工工法

超浅埋双连拱隧道三导坑开挖施工工法超浅埋双连拱隧道三导坑开挖施工工法一、前言超浅埋双连拱隧道三导坑开挖施工工法是一种适用于地质条件较好、土层相对较稳定的地区的隧道开挖施工工法。
它的特点是施工周期短、施工成本相对较低、施工安全性高,因此受到了广泛应用。
二、工法特点1. 采用双连拱结构:该工法采用双连拱结构,使得整个隧道的承载能力更高,能够有效承担上部结构的荷载,提高了隧道的稳定性和安全性。
2. 采用三导坑开挖:该工法采用三导坑开挖施工方式,即采用底部导坑和两侧导坑相结合的方式,可以有效降低施工风险,减少地下水涌入,提高开挖效率。
3. 沿线导坑相互支护:施工过程中,导坑之间通过支护系统相互支撑,使得整个施工过程相对稳定,减少了因为开挖所导致的结构破坏。
4. 施工周期短:由于采用了导坑开挖施工方式,整个施工周期相对较短,能够有效缩短工期,提高施工效率。
5. 施工成本低:与传统的隧道施工相比,超浅埋双连拱隧道三导坑开挖施工工法的施工成本相对较低,主要体现在原料费用和人工成本方面。
三、适应范围超浅埋双连拱隧道三导坑开挖施工工法适用于地质条件较好、土层相对较稳定的地区,特别适用于城市地铁、高铁隧道等需要快速建设的工程项目。
四、工艺原理施工工法与实际工程之间的联系主要是通过工艺原理来实现的。
首先,在施工前需要进行详细的地质勘探,获得地质资料并制定详细的施工方案。
然后,根据设计要求,在地下进行导坑开挖,形成底部导坑和两侧导坑。
导坑之间通过支护系统进行相互支护,以保证施工过程中的安全性和稳定性。
最后,利用开挖机械设备对隧道的上部进行开挖,完成整个隧道的开挖施工。
五、施工工艺1. 地质勘探:进行详细的地质勘探,获取地质资料,制定施工方案。
2. 三导坑开挖:按照施工方案,进行底部导坑和两侧导坑的开挖,形成导坑系统。
3. 导坑支撑:利用支护系统对导坑进行支撑,保证施工过程中的安全性和稳定性。
4. 上部开挖:利用开挖机械设备对隧道的上部进行开挖,完成整个隧道的开挖施工。
双连拱隧道正洞台阶开挖施工工法
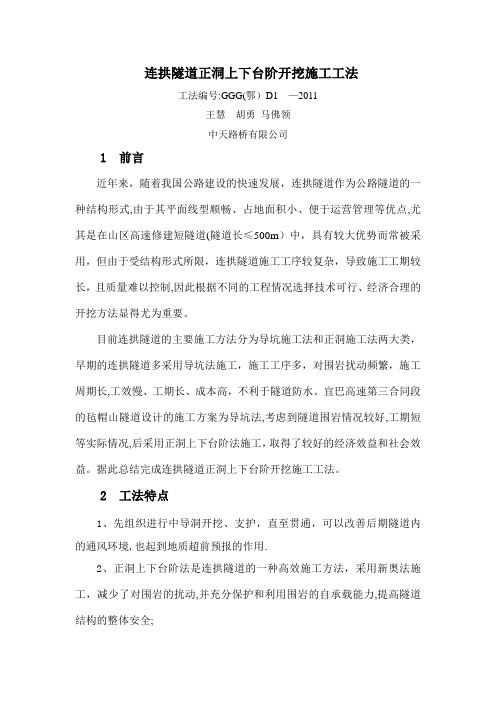
连拱隧道正洞上下台阶开挖施工工法工法编号:GGG(鄂)D1 —2011王慧胡勇马佛领中天路桥有限公司1 前言近年来,随着我国公路建设的快速发展,连拱隧道作为公路隧道的一种结构形式,由于其平面线型顺畅、占地面积小、便于运营管理等优点,尤其是在山区高速修建短隧道(隧道长≤500m)中,具有较大优势而常被采用,但由于受结构形式所限,连拱隧道施工工序较复杂,导致施工工期较长,且质量难以控制,因此根据不同的工程情况选择技术可行、经济合理的开挖方法显得尤为重要。
目前连拱隧道的主要施工方法分为导坑施工法和正洞施工法两大类,早期的连拱隧道多采用导坑法施工,施工工序多,对围岩扰动频繁,施工周期长,工效慢、工期长、成本高,不利于隧道防水。
宜巴高速第三合同段的毡帽山隧道设计的施工方案为导坑法,考虑到隧道围岩情况较好,工期短等实际情况,后采用正洞上下台阶法施工,取得了较好的经济效益和社会效益。
据此总结完成连拱隧道正洞上下台阶开挖施工工法。
2 工法特点1、先组织进行中导洞开挖、支护,直至贯通,可以改善后期隧道内的通风环境,也起到地质超前预报的作用.2、正洞上下台阶法是连拱隧道的一种高效施工方法,采用新奥法施工,减少了对围岩的扰动,并充分保护和利用围岩的自承载能力,提高隧道结构的整体安全;3、施工工艺及条件相对简单,质量容易控制;4、与导坑法相比,减少了两个侧壁导洞的开挖及临时支护,且工序简单,有效地降低了对围岩的扰动,缩短了施工周期,降低成本。
3 适用范围本工法可适用于公路、市政、铁路连拱隧道的IV类围岩,II、III类围岩也可参照本工法。
4 工艺原理本工法的基本理论基础为新奥法。
根据新奥法原理,采用光面爆破大断面开挖,使用锚、喷、网、钢拱架和超前导管及超前管棚等支护手段,先开挖贯通中导洞,浇筑中隔墙混凝土,然后采用上下台阶法开挖左右正洞,左右洞围岩经多次扰动,应力重新分布均衡后进行主洞二次衬砌。
施工过程中加强对围岩和支护监控量测,以量测信息反馈来指导施工.5 施工工艺流程及操作要点结合宜巴高速公路三合同段内毡帽山隧道的施工过程叙述施工工艺流程及操作要点.5。
城际轨道双连拱大断面隧道偏洞法开挖施工工法(2)

城际轨道双连拱大断面隧道偏洞法开挖施工工法城际轨道双连拱大断面隧道偏洞法开挖施工工法一、前言城际轨道双连拱大断面隧道偏洞法开挖施工工法适用于城际铁路等大型工程的隧道开挖,具有高效、安全、经济等特点。
本文将从工法特点、适应范围、工艺原理、施工工艺、劳动组织、机具设备、质量控制、安全措施、经济技术分析和工程实例等方面阐述该工法的具体内容。
二、工法特点城际轨道双连拱大断面隧道偏洞法开挖施工工法具有以下特点:1. 结构合理:采用双连拱结构,强度高、稳定性好,适应大断面隧道开挖的需求。
2. 施工周期短:通过优化施工工艺,能够缩短施工周期,提高工程进度。
3. 施工效率高:采用机械化作业,能够提高施工效率,降低人工投入。
4. 质量可控:通过严格的质量控制措施,能够保障开挖施工质量,提高工程的可靠性。
5. 安全可靠:采取多项安全措施,确保施工过程中的安全,减少事故风险。
三、适应范围城际轨道双连拱大断面隧道偏洞法开挖施工工法适用于大断面隧道的开挖,特别适合城际铁路等大型工程中对隧道开挖质量和工期有较高要求的情况。
四、工艺原理城际轨道双连拱大断面隧道偏洞法开挖施工工法的工艺原理是基于岩石力学理论和隧道工程实践经验的基础上,采取一系列技术措施保障施工过程的稳定和成功。
具体包括:在施工前进行地质勘探和力学测试,确定岩体的物理力学参数;根据勘探结果和设计要求,采取合理的支护措施,避免隧道塌方和坍塌;利用高效的机械设备进行挖掘,控制挖掘速度和进度;在挖掘过程中进行实时监测和控制,调整施工参数,确保隧道的稳定和安全。
五、施工工艺城际轨道双连拱大断面隧道偏洞法开挖施工工法的施工工艺分为以下几个阶段:1. 地质勘探和预处理:进行地质勘探,分析岩体的性质和力学参数,确定支护措施和决策依据。
2. 高效机械挖掘:采用大型隧道掘进机进行挖掘,控制挖掘速度和进度,避免地层坍塌和塌方。
3. 隧道支护:根据设计要求和地质勘探的数据,选择合适的支护方法,进行隧道支护,确保施工过程中的安全和稳定。
双连拱隧道施工方法

第23卷 第2期重 庆 交 通 学 院 学 报2004年4月Vo1123No12JOURNA L OF CH ONG QI NGJ I AOT ONG UNI VERSITY Apr.,2004双连拱隧道施工方法唐 亮Ξ(重庆交通学院育才工程咨询监理有限公司,重庆400074)摘要:结合广西柳州市南二环路桐油山隧道、银仔山1#隧道、银仔山2#隧道双连拱隧道群施工中采取的施工技术方法,对双连拱隧道施工方法进行了较为全面的分析、比较和总结,对不同施工方法的采用提出了建议.关 键 词:双连拱隧道;施工技术;施工方法中图分类号:U45514 文献标识码:B 文章编号:10012716X(2004)022******* 随着高速公路和城市道路建设的发展,双连拱隧道以其节省征地拆迁,具有接线难度小、占地宽度少、利于环保的特点,在500m以下的特定地形地质条件下的短隧道设计中已普遍采用.广西柳州市南二环城市主干道Ι级道路K2+ 180—K3+810共1167km路段上共设计有桐油山隧道、银仔山1#隧道、银仔山2#隧道3座双连拱隧道.这3座隧道长度分别为455m、255m、205m,双跨净宽2616m,净高712m;隧道处在喀斯特岩溶地区,其中Ι、Ⅱ类围岩180m、Ⅲ类围岩155m、Ⅳ类围岩230m、Ⅴ类围岩350m,隧道群穿越主要不良地质有: 180m浅埋人工杂填土地层(埋深10m)、50m塌落堆积体、4Om粘土充填的大溶槽,围岩溶洞、溶隙十分发育.国内单洞隧道施工技术已十分成熟,而双连拱隧道这种隧道结构形式,其受力结构复杂,可供借鉴的施工经验还不多,其施工技术尚在探讨和摸索之中.在柳州市南二环路双连拱隧道群施工中,针对不同围岩情况,分别采取了相应的施工方法,并在实际施工中取得成功.1 施工方法双连拱隧道施工方法归纳起来可分为以下4种:①三导洞分步施工法;②中导洞施工法;③单洞施工法;④双洞全断面平行施工法.111三导洞分步施工法三导洞分步施工法其工序流程为:①中导洞开挖及支护;②中墙衬砌;③左导洞开挖及支护;④左侧边墙衬砌;⑤右导洞开挖及支护;⑥右侧边墙衬砌;⑦左洞上半断面开挖及支护;⑧左洞拱部衬砌;⑨右洞上半断面开挖及支护;⑩右洞拱部衬砌;λϖ左洞下半断面开挖及仰拱衬砌;λω右洞下半断面开挖及仰拱衬砌.三导洞分步施工法施工工序如图1示.这种施工方法的优点是:1)采用三导洞分步施工,确实安全可靠,特别是很好地处理了左右拱部施工由不对称性到左右洞拱部均施工完毕后的对称结构体系转换,确保了结构在施工过程中的安全;2)对于地质情况很差、埋深较浅的软弱围岩(Ⅰ类、Ⅱ类),如桐油山隧道180m浅埋人工杂填土地层中,采用了这种方法.该方法缺点是:1)由于施工工序多,对围岩和已建结构存在多次扰动,不同部位衬砌间隔时间长,使得施工缝更加明显化;2)拱墙衬砌分步施工,防水系统施工质量难以保证,特别是中墙顶处易出现渗漏水现象;3)从经济上考虑,由于多导洞开挖和支护,加大了成本,隧道造价高;4)多导洞施工工序多,耗时长,施工断面小,不利于大型机械作业.112中导洞施工法对于Ⅲ类或Ⅲ类以上围岩,可以考虑不设两侧导洞,而是中导洞中墙施工后,直接进行左、右正洞Ξ收稿日期:2003206210;修订日期:2003210216作者简介:唐 亮(1969-),男,重庆市人,工程师,从事高速公路隧道、桥梁及道路的监理咨询工作及材料力学的教学工作.图1 三导洞分步施工法施工工序的开挖,开挖方法可采取全断面法、正台阶法等.银仔山1#隧道进口端80m为Ⅲ类围岩地段,采用了中导洞施工法.中导洞施工法的施工工序流程为:①中导洞开挖及支护;②中隔墙浇筑;③左洞开挖及初期支护;④左洞二次衬砌;⑤右洞开挖及初期支护;⑥右洞二次衬砌.相对于三导洞分步施工法,采用中导洞施工法减少了两个边导洞的施工,拱墙采取整体一次衬砌,具有工序较简单、机械化程度较高、临时初期支护工作量小、施工进度较快,节约成本的特点;而且中导洞先施工,起到了超前探明隧道地质情况的作用,为左右正洞施工创造了条件.中导洞施工法施工工序如图2示.113单洞施工法单洞施工法的工序流程为:①左(或右)洞开挖、初期支护及中墙浇筑;②左(或右)洞二次衬砌施工;③右(或左)洞开挖及初期支护;④右(或左)洞二次衬砌.单洞施工法的特点是:1)减少了工序,降低了对围岩的扰动,缩短了图2 中导洞施工法施工工序全断面结构建成时间;2)采取了单洞防水系统,保证防、排水施工质量;3)减少了导坑开挖支护,降低了工程造价;4)工程进度快,工期较短.单洞施工法施工工序如图3示.由于单个隧道施工技术已很成熟,根据围岩情况可采用全断面法、正台阶法和其他分步施工方法23 重庆交通学院学报 第23卷图3 单洞施工法施工工序(如CRD法、眼镜法等),因此单洞施工法适用范围比较大.施工中左、右洞按单洞前后应错开施工.采用单洞施工法要注意的是:1)对于先施工的单洞,中墙部分也一并开挖支护和衬砌,中墙顶部围岩应根据具体情况加强支护;2)中墙顶部采用锚杆与围岩连接,给先施工的洞室提供支持力,保持结构平衡;3)后施工的单洞则应特别注意不对称受力的影响.后开挖的单洞,最好采用上、下台阶分步开挖,尤其要严格控制下台阶的开挖长度,下台阶开挖后要及时作二次衬砌,最大限度地缩短不对称结构,确保结构在时间和空间上的安全性.原则上,后开挖的洞要在先开挖的洞施工完主体结构后才能进行,尤其是要在仰拱施工后,使之形成闭合受力结构后施工;后开挖的洞,在开挖靠中墙部分的围岩时,可以通过控制爆破,减少对中墙的破坏.下台阶开挖时可采取先施工远离中墙一侧围岩,增加靠中墙一侧围岩的爆破临空面.114双洞平行施工法双洞平行施工法工序流程为:①左、右洞开挖及初期支护;②中墙开挖及中墙衬砌;③中墙顶部开挖及支护;④左、右洞衬砌.双洞平行施工法施工工序如图4示.图4 双洞平行施工法工序 双洞平行施工法的特点是:保留中墙岩柱,左、右正洞同步掘进.这种方法适用于Ⅳ类或Ⅴ类以上围岩的硬岩隧道.双洞平行施工法开挖左右洞时,要特别注意中隔墙岩柱的稳定,使之能平衡左右洞围岩传递来的应力.开挖中隔墙岩柱采取跳槽式开挖,如图5示,开挖长度控制在4-5m左右,开挖前采用长锚杆加固中隔墙顶部围岩,开挖后要立即施工中墙衬砌和及时施工左右洞二次衬砌.2 施工中特殊问题的处理2.1控制爆破,减小围岩扰动在柳州市南二环路隧道群施工过程中,根据其施工方法,开挖要分部进行,围岩将多次受到扰动,爆破距已施作的中墙砼很近,因此,实施好控制爆破,减小对围岩的扰动及对中墙砼的震动就显得尤为重要.在开挖爆破设计中制订以下几项原则:1)开挖中严格遵循“弱爆破、短进尺、强支护”的施工原则,Ⅲ类围岩进尺控制在018—115m,以减小每次爆破的炸药总用量,爆破一般采用光面爆破;2)尽量减小周边眼的间距,根据围岩情况的不同,一般控制在30-40cm,周边眼采用小直径药卷间隔装药技术,以控制开挖成型,减小爆破对围岩的扰动;3)每次爆破后利用断面仪对开挖面进行检查记录,并结合监控量测的信息反馈及时调整爆破参数.212中墙水平推力的平衡根据连拱隧道的结构特点,在中墙砼施作完成之后,将进行侧导洞和正洞的开挖支护.由于左右两33第2期 唐 亮:双连拱隧道施工方法 图5 中隔墙岩柱跳槽开挖示意洞的不对称施工,以及爆破的震动,分部施工的反复扰动,通过侧导洞和正洞的初期支护将压力传递到中墙造成中墙受力的不平衡.当中墙不能抵抗这种单侧的推力而发生较大位移时,将会引起拱部的支护开裂失稳,造成严重后果.为确保中墙的稳定,施工中采取了以下几项措施:1)合理组织施工工序,作好控制爆破及控制进尺,减小对围岩的扰动;2)在中墙砼施工前,对中墙基底承载力及基底是否存在溶隙和溶洞进行检查,对于基底承载力不足的地段采用扩大基础或基底加强锚杆进行加强,对存在溶隙和溶洞的地段采用基底加强锚杆、挂多层钢筋网并浇筑砼或采用工字钢、挂多层钢筋网浇筑砼纵向跨过,以确保中墙在工序施工而引起的受力转换中不会因基底承载力不足而沉降,从而导致支护失稳;3)在中墙砼施工完成后,及时将中墙顶部与围岩之间的空隙用砼回填顶紧,并用夯填土及C10砼对中墙侧边进行回填,在偏压严重的地段可采用工字钢或方木侧向支撑,确保中墙稳定;4)尽快施作正洞仰拱及正洞二次衬砌,使中墙与支护体系形成一个共同体承受荷载,加大其抵抗不平衡推力的能力.3 体会和建议1)从上述介绍的4种施工方法中可以看出,各种施工方法都是围绕着中墙施工来进行的,双连拱隧道施工的核心在于中墙的施工,中墙是整个隧道受力转换和受力平衡的支撑点,在结构设计中其刚度稳定应作控制,在施工中要认真处理好中墙的基底承载力和回填反压平衡,确保中墙稳定;2)在双连拱隧道施工中,中墙顶防排水处理是双连拱隧道防排水的关键,要严格按照“以排为主、防、排、截、堵相结合”的综合治理原则,抓好工序质量控制,解决中墙顶漏渗水问题.通过施工实践表明,虽然可以通过各种措施对因中墙顶渗漏而引起的二次衬砌表面渗漏水进行治理,但如果双连拱隧道采取按两个单洞独立设置防排水系统将更加合理可靠,很好地解决中墙顶渗漏水问题;3)采取大断面施工是目前双连拱隧道施工的发展趋势,而双连拱隧道大多处在浅埋、偏压地质条件下,因此认真做好超前预支护对双连拱隧道施工十分重要,必要时采取预注浆等措施加固和改良地层,充分调动和利用围岩的自承作用,减少对围岩的扰动;4)在软弱围岩中双连拱隧道左、右正洞应错开施工,先施工的洞室要及时支护、衬砌和构建仰拱,形成封闭结构,后施工的洞室要在先施工洞室主体结构完成后进行,以确保隧道安全;5)在围岩稍好的情况下,双连拱隧道正洞施工采用下导超前的全断面法比较合适,如图6示.双跨图6 下导超前全断面施工工序43 重庆交通学院学报 第23卷连拱结构跨度大,开挖时采取多次爆破或大药量爆破加大了对围岩和已建结构的扰动和破坏,也不符合充分利用围岩自承作用的新奥法原理;而采取下导适度超前施工,既增加了全断面开挖的临空面,又减少了爆破用药量,大大减弱了爆破对围岩的破坏.4 结束语在双连拱隧道10多年的建设中,其施工方法也在不断完善,特别是近年来,使用了一些新颖的施工方法.笔者介绍的针对不同地质条件下建议采用的4种施工方法,希望能对双连拱隧道施工起到一定的参考作用.参考文献:[1] 交通部.公路隧道设计规范(J T J026-90)[S].北京:人民交通出版社,1990.[2] 交通部.公路隧道施工技术规范(J T J042-94)[S].北京:人民交通出版社,1995.[3] 唐 亮.柳州市南二环路桐油山隧道设计与施工[J ].广西交通科技,2002,(4):59262.Construction methods of twin 2arch tunnelsT ANG Liang(Chongqing Y ucai Engineering C onsultation &Supervision C ompany Ltd.,Chongqing Jiaotong University ,Chongqing 400074,China )Abstract :Based on the construction process of the building of twin 2arch tunnels of T ongy ou M ountain Tunnel ,Y inzi M ountain Tunnel 1and Y inzi M ountain Tunnel 2in S outh Second Ring R oad in city of Liouzhou in G uangxi Province ,practiced techniques in twin 2arch tunnels are thoroughly analyzed and summarized.Meanwhile ,several suggestions about the adoption of different construction methods for this special tunnel type are made.K ey w ords :twin 2arch tunnels ;construction techniques ;construction methods责任编辑:袁本奎(上接30页)[6] 张江涛,周志祥.横张预应力混凝土箱形梁的构造与工艺[A].中国公路学会桥梁与结构工程学会2001年桥梁学术讨论会论文集[C ].北京:人民交通出版社,2001.[7] 吕忠达.世纪长桥—杭州湾跨海大桥[A ].21世纪桥梁技术发展论坛论文集———纪念钱塘江大桥通车65周年[C].杭州:中国公路杂志社,2002.Discussion about solution to the key problems of application ofmodern nonmetallic structures in bridge engineeringSHI Y ing ,1 W ANG Jin ,2 LI Da 2hua3(1.School of Architecture &Civil Engineering ,Zhejiang University of T echnology ,Hangzhou 310014,China ;2.N orth China MunicipalEngineering Design and Research Institute.T ianjin 300074,China ;3.T ianjin Seism ological Bureau ,T ianjn 300201,China)Abstract :The evident advantages and application prospect of the m odern nonmetallic structures and the traditional new structure style are dis 2cussed base on the characteristics analysis of the nationality and high -tech in bridge engineering ,and the crucial requirements on the structures are met in aspects of high strength ,longspan ,corrosianrce ,sistance seismic ,stability fatigue ,intelligent control and s o on ,but the rest problems are deformation consistency of FRP composite with concrete and FRP tendon prestressing ,FRP tendon anchoring in the prestressed FRP con 2crete structures and s o on.K ey w ords :bridge ;m odern nonmetallic structures ;FRP concrete ;FRP composite materials ;deformation consistency ;prestress system责任编辑:袁本奎53第2期 唐 亮:双连拱隧道施工方法 。
软弱围岩公路双联拱隧道施工工法

软弱围岩公路双联拱隧道施工工法GZSJGF07-01-04中铁隧道集团二处:杨秀权许燕锋王凤忠一、前言采用上下行隧道分修是公路隧道设计中最常用的方式,但个别公路隧道因线路选线受地形条件等因素的限制而选用双联拱隧道。
采用双连拱隧道选线方案有少占地、减少挖方、运营安全等优点,但一般双连拱隧道具有浅埋、大跨、偏压、地质不良等特点,因此,技术难度高,施工风险大。
采用该工法可保证双连拱隧道安全、优质、快速建成。
二、工法特点和关键技术1、将监控量测技术、数据处理和信息反馈技术应用于施工,动态修正施工方法和支护参数,确保施工安全。
2、三导坑先墙后拱法开挖支护。
3、解决施工过程中力的转换是关键。
4、中柱防水技术是结构防水的关键。
三、适用范围1、本工法适用于新奥法指导施工的软弱围岩双联拱隧道。
2、本工法适用于山区高速公路软弱围岩双连拱隧道。
3、本工法适用于类似条件下的城市公路双连拱隧道工程、地下铁道工程。
四、施工方法(一)施工工序双联拱隧道采用三导坑先墙后拱的施工方法,先进行中导坑开挖①,滞后一定的距离相继进行左右侧导坑开挖②—1和②—2,中导坑贯通后施工中墙钢筋混凝土I,侧导坑贯通后相继施工侧墙二衬钢筋混凝土II—1和II—2,在二条导坑贯通且完成中墙和边墙衬砌后,进行左右线正洞隧道拱部开挖③—1和③—2,拱部二次衬砌III—1和III—2,随后开挖中部核心土体④—1和④—2,最后开挖下部仰拱土体⑤—1和⑤—2,施做仰拱二衬结构V—1和V—2,从而形成封闭的支护结构。
双联拱隧道施工工序见图—1。
图—1双联拱隧道施工工序图(二)施工重点及注意事项 1、施工准备做好进出口场地的“三通一平”工作。
隧道洞门仰坡处理遵循“早进晚出”的施工原则,少破坏山体植被,减少刷方和护坡工作量,确保隧道施工和今后的运营安全。
仰坡边坡开挖要一次到位,并及时进行坡面防护,如系统锚杆、网喷砼及截水天沟等要提前施工。
特别强调正面仰坡喷砼封闭必须密实坚固,达到设计要求厚度。
双连拱隧道联合套拱施工工法

双连拱隧道联合套拱施工工法双连拱隧道联合套拱施工工法一、前言隧道工程是现代交通建设的重要组成部分,为解决交通拥堵和扩大通行能力,隧道施工技术得到了广泛应用和发展。
双连拱隧道联合套拱施工工法是一种高效、安全可靠的隧道施工方法。
该工法采用了双连拱结构和套拱支护技术的结合,能够有效解决隧道施工中的土层变形和围岩稳定等问题,确保隧道的安全和稳定。
二、工法特点1. 结构优越性:双连拱隧道联合套拱施工工法采用了双连拱结构,使得隧道更加坚固和稳定。
与传统单连拱结构相比,双连拱结构在抗震性能、水力性能和荷载承载能力等方面更出色。
2. 施工效率高:该工法采用了套拱支护技术,能够实现快速施工,节省时间和人力成本。
同时,双连拱结构的设计和施工相对简单,大大提高了工程进度。
3. 土层适应性强:联合套拱施工工法采用了深基坑法和锚杆喷射法等地质处理技术,能够适应各种复杂的土质条件和地质构造。
可以应对不同地段的土层变形和压力变化。
4. 售后维护方便:双连拱结构的隧道相对稳定,不易出现变形和沉降等问题。
在施工完成后,可以方便进行检修和维护,延长隧道的使用寿命。
三、适应范围双连拱隧道联合套拱施工工法适用于地质条件复杂、土层变形大的地区,如山区、水域和地下沉积物丰富的地方。
特别适用于需要承受较大压力和载荷的地段,如高速公路、铁路和城市地铁等。
四、工艺原理双连拱隧道联合套拱施工工法的核心原理是采取合理的施工工法和适当的技术措施,确保隧道的稳定和安全。
具体的工艺原理主要包括以下几点:1. 土层处理:根据不同的地质条件,采用适当的土层处理技术,如深基坑法、锚杆喷射法等,以加强土层的稳定性和承载能力。
2. 套拱支护:采用套拱支护技术,通过安装钢筋混凝土套拱,增强隧道的整体承载能力和抗震性能。
3. 双连拱结构:采用双连拱结构,使隧道在荷载和地震力作用下更加安全可靠。
4. 施工监控:在整个施工过程中,采用相应的监测技术和仪器设备,对隧道变形、位移和围岩稳定等情况进行实时监测,及时调整和采取相应的措施。
高速公路双连拱隧道施工工法
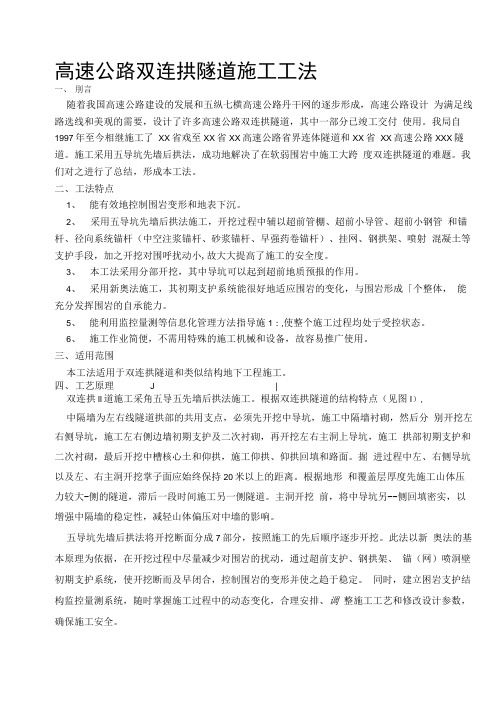
高速公路双连拱隧道施工工法一、刖言随着我国高速公路建设的发展和五纵七横高速公路丹干网的逐步形成,高速公路设计为满足线路选线和美观的需要,设计了许多高速公路双连拱隧道,其中一部分已竣工交付使用。
我局自1997年至今相继施工了XX省戏至XX省XX高速公路省界连体隧道和XX省XX高速公路XXX隧道。
施工采用五导坑先墙后拱法,成功地解决了在软弱围岩中施工大跨度双连拱隧道的难题。
我们对之进行了总结,形成本工法。
二、工法特点1、能有效地控制围岩变形和地表下沉。
2、采用五导坑先墙后拱法施工,开挖过程中辅以超前管棚、超前小导管、超前小钢管和锚杆、径向系统锚杆(中空注浆锚杆、砂浆锚杆、早强药卷锚杆)、挂网、钢拱架、喷射混凝土等支护手段,加之开挖对围呼扰动小,故大大提高了施工的安全度。
3、本工法采用分部开挖,其中导坑可以起到超前地质预报的作用。
4、采用新奥法施工,其初期支护系统能很好地适应围岩的变化,与围岩形成「个整体,能充分发挥围岩的自承能力。
5、能利用监控量测等信息化管理方法指导施1:,使整个施工过程均处亍受控状态。
6、施工作业简便,不需用特殊的施工机械和设备,故容易推广使用。
三、适用范围本工法适用于双连拱隧道和类似结构地下工程施工。
四、工艺原理J |双连拱ll道施工采角五导五先墙后拱法施工。
根据双连拱隧道的结构特点(见图I),中隔墙为左右线隧道拱部的共用支点,必须先开挖中导坑,施工中隔墙衬砌,然后分别开挖左右侧导坑,施工左右侧边墙初期支护及二次衬砌,再开挖左右主洞上导坑,施工拱部初期支护和二次衬砌,最后开挖中槽核心土和仰拱,施工仰拱、仰拱回填和路面。
掘进过程中左、右侧导坑以及左、右主洞开挖掌子面应始终保持20米以上的距离。
根据地形和覆盖层厚度先施工山体压力较大-侧的隧道,滞后一段时间施工另一侧隧道。
主洞开挖前,将中导坑另--侧回填密实,以增强中隔墙的稳定性,减轻山体偏压对中墙的影响。
五导坑先墙后拱法将开挖断面分成7部分,按照施工的先后顺序逐步开挖。
双联拱隧道施工工艺

双联拱隧道施工工艺胡红卫中铁隧道集团一处453000摘要:双联拱隧道在其结构上与单拱隧道有较大区别,且为近年来才逐渐被应用于高等级公路中,如何在其施工过程中把握要点,吸取经验教训,逐渐熟悉并掌握其施工工艺有着非常重要的意义。
本文主要介绍元磨高速公路十一合同段老苍坡3#、4#、5#、6#隧道施工过程的工艺控制,包括双联拱隧道的结构特点、中导洞及三导洞开挖方法、衬砌施工工艺、特殊问题的处理等内容,并提出了自己对双联拱隧道设计及施工的看法及建议,以供其它双联拱隧道设计及施工参考。
关键词:双联拱隧道、施工工艺国家西部大开发的战略给西部地区的交通建设带来了机遇,在山区面积所占比例较大的西部地区设计修建的高等级公路大多处于山岭重丘地段,在地形地质条件复杂的山岭重丘地区的高等级公路中应用双联拱隧道具有重要的意义。
云南省元〔江〕-磨〔黑〕高速公路就是西部大开发战略中打通东南亚国际大通道昆明至曼谷公路中的一段,全长147km,沿线经过哀牢山和无量山脉,山高谷深,全线桥隧所占比例达30%以上,双联拱隧道在该公路上得到了广泛应用,全线共设计双联拱隧道15座,总长占全线隧道的65%,是我国目前双联拱隧道最多的一条公路。
本文主要结合元磨公路的施工情况从以下几个方面介绍双联拱隧道的特点及施工工艺。
1、设计概况及特点双联拱隧道是在高速公路通过的山势不高、纵向长度较短、横坡较陡、公路上下行线在此别离不开的地段设置的双跨连拱隧道,其单跨断面为单心圆结构,边墙为曲墙,中墙为直墙,单跨净宽11.4米左右,净高7.8米左右,上下行线隧道通过厚2米的钢筋砼中隔墙相连,初期支护根据地质情况分别采用工字钢及花拱架两种形式,WTD25锚杆、挂网、喷砼与单跨隧道根本相同,二衬采用模图1 双联拱隧道洞门筑钢筋砼结构。
联拱隧道通过地段地质条件的特殊性决定了其在设计和施工上具有以下特点:1.1埋深浅、长度短因联拱隧道通过的地段一般山势较低,其最大埋深一般在50至80米之间,长度一般在500米以下,在山势较高、纵向长度较长的地段一般不采用联拱隧道而采用上下行线分开的单拱隧道;1.2偏压联拱隧道通过地段一般地势较陡,上下行线两侧的埋深不同,整条隧道也就不同程度的存在偏压,特别是洞口段偏压比拟严重,这给隧道施工特别是洞口段施工带来了很大困难;1.3地质条件复杂由于埋深浅,联拱隧道通过地段一般地质条件比拟复杂,围岩软弱破碎,节理发育,地表水对隧道内涌水量的大小影响较大,雨季施工困难,元磨公路所在地区雨季集中,降雨量大,更给平安施工增加了难度;1.4跨度大与铁路隧道相比,单跨公路隧道本身跨度就较大,而联拱隧道将上下行线单拱隧道连在一起,其跨度是单拱隧道的两倍,最大开挖跨度在26.4米左右,相当于铁路车站隧道的跨度,而且结构复杂,施工非常困难;1.5施工工序复杂、工序间相互影响大双联拱隧道的设计特点决定了其施工必须分多个步骤进行,各个工序间相互影响又很大,这就要求双联拱隧道施工必须要有科学合理的施组设计,理清各个工序的先后顺序及相互关系,在施工过程中尽量减小各个工序之间的相互影响,并根据施工中的实际情况灵活的调整工序安排,保证平安、优质的建好双联拱隧道。
双连拱隧道联合套拱施工工法(2)
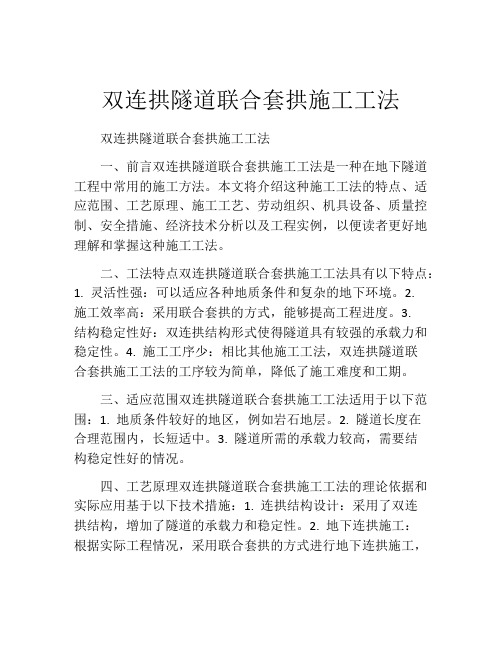
双连拱隧道联合套拱施工工法双连拱隧道联合套拱施工工法一、前言双连拱隧道联合套拱施工工法是一种在地下隧道工程中常用的施工方法。
本文将介绍这种施工工法的特点、适应范围、工艺原理、施工工艺、劳动组织、机具设备、质量控制、安全措施、经济技术分析以及工程实例,以便读者更好地理解和掌握这种施工工法。
二、工法特点双连拱隧道联合套拱施工工法具有以下特点:1. 灵活性强:可以适应各种地质条件和复杂的地下环境。
2.施工效率高:采用联合套拱的方式,能够提高工程进度。
3.结构稳定性好:双连拱结构形式使得隧道具有较强的承载力和稳定性。
4. 施工工序少:相比其他施工工法,双连拱隧道联合套拱施工工法的工序较为简单,降低了施工难度和工期。
三、适应范围双连拱隧道联合套拱施工工法适用于以下范围:1. 地质条件较好的地区,例如岩石地层。
2. 隧道长度在合理范围内,长短适中。
3. 隧道所需的承载力较高,需要结构稳定性好的情况。
四、工艺原理双连拱隧道联合套拱施工工法的理论依据和实际应用基于以下技术措施:1. 连拱结构设计:采用了双连拱结构,增加了隧道的承载力和稳定性。
2. 地下连拱施工:根据实际工程情况,采用联合套拱的方式进行地下连拱施工,加强结构的整体性。
3. 钻爆法开挖:采用钻爆法进行隧道的开挖,在确保安全的前提下,提高施工效率。
五、施工工艺双连拱隧道联合套拱施工工法的具体施工过程如下:1. 前期准备:确定施工方案、准备所需的材料和设备。
2. 隧道开挖:采用钻爆法进行隧道的开挖,并及时清理渣土。
3. 地下连拱施工:根据设计要求,在开挖好的隧道顶部进行地下连拱的施工,使用钢筋和混凝土进行加固。
4. 砌筑导流层:在地下连拱完成后,砌筑导流层,确保地下水和渗水能够顺利流出。
5. 隧道衬砌:进行隧道衬砌工作,使用预制混凝土或现浇混凝土进行隧道的内壁施工。
6. 环境保护:进行环境保护工作,采取合适的措施,减少施工对周围环境的影响。
六、劳动组织双连拱隧道联合套拱施工工法需要合理的劳动组织,包括人员配备、工作责任划分、工作协调等。
双连拱隧道双洞施工工法

8)施工区各洞室、料库等处均应设置有效而数量 足够的消防器材,并设明显的标志,定期检查、补充和 更换。 洞内及各洞室不得存放汽油、煤油、变压器油和 其他易燃物品。 洞内及库房周围严禁烟火。 7 结语
图 2 单跨隧道(洞)开挖方法
注 :图 中 (1)~(6)为 初 期 支 护 结 构 施 工 步 序 ; Ⅰ~Ⅵ 为二次衬砌结构施工步序
图 3 双连拱隧道双洞(台阶+CRD)法施工具体步序图
3. 2. 1 左侧(小断面)隧道施工 1)隧道开挖尺寸的确定 左侧隧道的开挖尺寸,主要取决于中隔墙或中间
核心混凝土土柱的尺寸。 由于渡线段隧道中隔墙厚 0.8 m(基础厚度 1.695 m),高 5.85 m,故确定左侧隧道 的开挖尺寸为 8.83 m×7.87 m。
2. 3 工艺原理 1) 该 工 法 的 基 本 理 论 基 础 是 新 奥 法 , 即 : 开 挖 后
允许围岩有一定的变形,从而释放部分地应力;通过监 控量测和适时支护来控制围岩变形,使围岩不会失稳; 喷锚与初期支护、大管棚等支护共同作用形成复合承 载结构。
2)遵循“管超前 、严注 浆 、短 开 挖 、强 支 护 、快 封 闭、勤量测”原则。 在加强超前注浆和加强初支的前提 下,将双连拱隧道中洞法施工的三洞改为双洞(如图 1 所示),以简化施工步序,缩短施工周期。 3 施工工艺 3. 1 施工步骤
北京市 108 国道(南村—石门营段)改建工程南村 隧道工程,“以排为主,防、排、截、堵相结合”为原则进 行设计,合理设置分区防水并采用自流集排水系统,可 靠的施工,防排水效果显著,目前无渗漏水现象。
高速公路双连拱隧道中导洞——主洞施工工法(2)
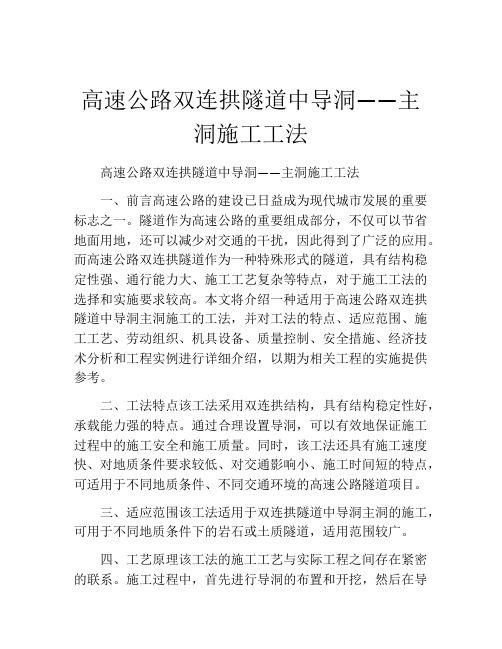
高速公路双连拱隧道中导洞——主洞施工工法高速公路双连拱隧道中导洞——主洞施工工法一、前言高速公路的建设已日益成为现代城市发展的重要标志之一。
隧道作为高速公路的重要组成部分,不仅可以节省地面用地,还可以减少对交通的干扰,因此得到了广泛的应用。
而高速公路双连拱隧道作为一种特殊形式的隧道,具有结构稳定性强、通行能力大、施工工艺复杂等特点,对于施工工法的选择和实施要求较高。
本文将介绍一种适用于高速公路双连拱隧道中导洞主洞施工的工法,并对工法的特点、适应范围、施工工艺、劳动组织、机具设备、质量控制、安全措施、经济技术分析和工程实例进行详细介绍,以期为相关工程的实施提供参考。
二、工法特点该工法采用双连拱结构,具有结构稳定性好,承载能力强的特点。
通过合理设置导洞,可以有效地保证施工过程中的施工安全和施工质量。
同时,该工法还具有施工速度快、对地质条件要求较低、对交通影响小、施工时间短的特点,可适用于不同地质条件、不同交通环境的高速公路隧道项目。
三、适应范围该工法适用于双连拱隧道中导洞主洞的施工,可用于不同地质条件下的岩石或土质隧道,适用范围较广。
四、工艺原理该工法的施工工艺与实际工程之间存在紧密的联系。
施工过程中,首先进行导洞的布置和开挖,然后在导洞内进行主洞的施工。
在施工过程中,采取了一系列的技术措施来确保施工的顺利进行,如设立施工平台,进行导洞的细分施工,合理处理导洞与主洞之间的连接等。
五、施工工艺施工工法的各个施工阶段包括导洞布置、导洞开挖、主洞施工和导洞与主洞连接等。
导洞布置阶段,根据实际情况对导洞位置进行定位,并计算出导洞的尺寸和位置。
导洞开挖阶段,根据导洞布置的位置,采用爆破、掘进等方式进行导洞的开挖。
主洞施工阶段,根据导洞的位置和尺寸,进行主洞的掘进、锚杆注浆等施工工序。
导洞与主洞连接阶段,根据导洞和主洞的位置和尺寸,采用灌浆或打钢板等方式进行连接,确保两者之间的结构稳定。
六、劳动组织在施工过程中,需要配备专业的施工人员和管理人员,以保证施工的质量和进度。
双连拱隧道工法

双连拱隧道中导洞-正洞施工工法前言中导洞-正洞施工工法是双连拱隧道施工的一种高效施工方法。
它根据新奥法原理,采用光面爆破大断面开挖,使用锚、喷、网、钢拱架和超前导管及超前管棚等支护手段,先开挖贯通中导洞,浇筑中隔墙混凝土,然后采用上下台阶法开挖左右正洞,最后进行全断面二次衬砌。
早期的双连拱隧道多采用三导洞法施工,对围岩扰动的次数多,施工周期长,工效慢、工期长、成本高,不利于隧道防水。
同三线浙江省境内的岵岫岭隧道设计的施工方案为三导洞法,后采用中导洞-正洞台阶法施工,效果良好。
一、工法特点(一)采用新奥法施工,尽量减少对围岩的扰动,充分保护和利用围岩的自承载能力,提高隧道结构的整体安全度。
(二)与三导洞法相比,减少了两个侧壁导洞,施工干扰少、临时支护量小,有效地降低了对围岩的扰动,缩短了施工周期,降低成本,减少工程投资。
二、适用范围本工法适用于双连拱山岭隧道的各种围岩情况,隧道的开挖方式则根据具体的情况来选择。
正台阶二步开挖法是全断面一次开挖法的改进方法,多用于围岩能短期内处于稳定的地层中。
台阶法根据台阶长度的不同,可划分为长台阶、短台阶和超短台阶三种,在IV类以上的围岩中一般采用长台阶,对于III、IV类围岩多采用短台阶,而对于II类以下的软弱中围岩则常采用超短台阶开挖法。
对于V、VI类整体性好的围岩,可采用全断面法;而对于土质围岩及软弱围岩则采用台阶分部开挖留核心土法。
三、工艺原理(一)本工法的基本理论基础是新奥法。
开挖后允许围岩有一定的变形,从而释放部分·1·地应力;通过监控量测和适时支护来控制围岩变形,使围岩不会失稳;围岩与锚喷等支护共同作用形成复合承载结构。
(二)中导洞-正洞法根据新奥法的基本原理,简化施工工序,采用薄膜支护,减少了开挖数量及衬砌圬工数量。
四、施工工艺(一)施工方法及顺序采用中导洞-正洞法施工,其步骤为先开挖中导坑,并做导坑临时支护直到中导洞贯通,然后由内向外浇筑中隔墙直到全部完成,铺设中隔墙顶防水材料,并将中隔墙相同标号的砼回填,打设长管棚注浆,然后开挖右洞上拱及初期支护,同时做好围岩的变形观测。
双连拱隧道双洞施工工法

先按 图 2要 求 的方 法开 挖含 中隔墙或 中间核 心混
早 期 的双 连 拱 隧 道 多采 用 中洞 法 三 洞施 工 , 围 所 示 ) 以简 化施 工步 序 , 对 , 缩短 施工 周期 。
岩扰 动次 数 多 , 工周 期 长 、 施 工效 慢 、 成本 高 , 不利 于 隧 3 施 工 工 艺 道 防 水 , 双 洞 施 工 工 法 则 避 免 了 上 述 弊 端 , 一 种 3 1 施 工步 骤 而 是 . 高 效快 速 的施 T 方法 。
快 速 地 完 成 了隧 道 施 工 , 保 了 连拱 隧 道 防水 效 果 , 短 了施 工周 期 , 快 了 T 效 , 低 了 施 工 成 本 , 得 了 良 好 的 技 术 确 缩 加 降 取 经济效益 。
关 键 词 : 道 ; 拱 ; 断 面 ; 洞 ; 工 隧 连 大 双 施 中 图 分 类 号 : 5 . U4 5 4 文献标志码 : B 文章 编 号 :0 9 7 6 ( 0 1 0 — 0 2 0 10 — 7 7 2 1 )3 0 8 — 4
隧 道 与 地 下 工 程 器
F nn 醴 Un er r un gi e ig u e ̄ d g o d En n ern
a 三 洞 法 )
图 1 双 连 拱 隧 道 二 洞 改 双洞 示 意 图 三
3 2 施 工 方 法 .
3 2 1 左侧 ( 断面 ) .. 小 隧道 施 T 1 隧道 开挖 尺寸 的确 定 )
2 2 适 用范 围 .
4 施 工 右侧 ( 断面 ) ) 大 隧道 ( 根据 洞 宽 和洞 高 合 理 选 择 台阶法 、 D法 或 C D法 开 挖 方式 ) 完成 右 侧 隧 C R , 道 初期 支 护 ; 5 分段 破 除 左 、 侧 隧 道 共 用 初 支 , 做 右 侧 隧 ) 右 施
- 1、下载文档前请自行甄别文档内容的完整性,平台不提供额外的编辑、内容补充、找答案等附加服务。
- 2、"仅部分预览"的文档,不可在线预览部分如存在完整性等问题,可反馈申请退款(可完整预览的文档不适用该条件!)。
- 3、如文档侵犯您的权益,请联系客服反馈,我们会尽快为您处理(人工客服工作时间:9:00-18:30)。
施工工艺
(一)工艺原理
双连拱隧道施工以新奥法的基本原理为依据,以“短开挖、快封闭、强支护、勤量测”为指导。
首先开挖中导洞并灌注中墙混凝土,然后开挖右洞,贯通后再进行左洞施工。
两洞在开挖中可根据不同的地质条件分成若干单元,分步开挖及时施作工字钢支撑、锚喷混凝土等初期支护,与围岩共同组成承荷系统,协同变形一承荷,充分利用围岩自承能力。
建立监控量测体系,实施信息化管理,根据反馈信息及时指导施工,确保安全、稳定。
(二)工艺流程
(三)施工方法
1、开挖及支护步骤
II类围岩采用中导坑加侧壁导坑法开挖,先墙后拱法衬砌。
开挖以中导坑超前并灌注中墙混凝土,然后侧壁导坑推进,衬砌边墙混凝土,上半断面开挖采用环形留核心土的方法,最后施作拱部二次衬砌,具体步骤见图。
III类围岩中导开挖并灌注中墙混凝土,正洞上下台阶法开挖(上下台阶
相距不小于10m),全断面二次衬砌,具体步骤见图。
W、V类围岩中导先行,正洞全断面开挖、全断面衬砌,具体步骤见
图。
2、开挖及运输方法
开挖I类围岩主要以风镐为主,人工装碴,1t四轮翻斗车运碴,开挖ni、W、V类围岩用简易钻孔台车人工操纵7655型凿岩机钻孔爆破,ZL40B装载机配合8t自卸汽车运碴。
简易钻孔台车是自行研制的能供20人同时钻孔的工作平台,钻架的高度、
宽度可根据开挖面的不同加以调整,它固定于东风车底盘上,进出方便,
不必拆卸,操作安全可靠。
3、控制爆破及中墙防护
在双连拱隧道正洞开挖过程中,因中墙混凝土已灌注,开挖时必须考虑爆破振动和飞石对中墙混凝土的影响,中墙混凝土厚度只有1.4m,且初期支护的工字钢支点已作用于中墙顶面,所以在施工中必须有严格保护措施,不得有任何影响和扰动。
办法是,111类围岩上下断面开挖,采用火雷管分段分区爆破,以减小爆破振动的叠加,把振动降低到最小程度。
具体见图。
W、V类围岩采用全断面光面爆破,但在靠中墙一侧预留1.0m保护层进行二次切割预裂爆破,具体爆破设计见图。
爆破时,在爆破的另一侧对中墙辅以I16工字钢横撑(纵向间距2m,支点距中墙顶2m)。
为防止飞石砸坏中墙混凝土表面,影响混凝土外观质量,对中墙不小于60m范围内全表面用厚2cm泡沫塑料覆盖防护。
4、初期支护
隧道采用新奥法原理施工,初期支护作为永久衬砌的一部分是施工中的重要一环,主要有系统锚杆、I16工字钢支撑及挂网喷射混凝土。
支护参数见表。
开挖后及时对围岩初喷5cm厚混凝土,尽快封闭岩面,形成封闭的受力圈,防止围岩松动,然后施作系统锚杆,锚杆采用ZP型早强锚固剂锚固,同时设置86钢筋网并与锚杆外露头绑扎牢固,最后准确架立工字钢支撑复喷混凝土至设计厚度。
喷混凝土用PH-30型喷射机,掺入STC型粘稠剂,采用半干湿式二次拌
合喷射工艺,集料在洞外拌合,用0.5m3混凝土运输车运至洞内,分次投料。
5、洞口辅助加强措施
由于洞口段围岩破碎且上覆层较薄,为了能早进洞,进好洞,洞口段应加强防护。
(1)仰坡防护为防止仰坡的剥落及受雨水冲刷而造成滑塌影响安
全施工,仰坡按设计坡率成型后及时进行喷锚混凝土防护,参数为:锚杆长4.0m,直径25,按梅花形布置,间距1.0m,钢筋网0 8,网格间距25cm,混凝土喷层厚15cm,施工时分2次喷射完成。
(2)洞口超前支护进出口段为浅埋区,围岩破碎且自成拱能力较
差,为保证施工安全,采取超前锚杆支护,具体布置见图。
6、施工过程中的受力体系转换
为保证中导洞的安全而施作的临时支护(工字钢、锚喷)虽不构成隧道的主体结构,但又是施工过程中不可缺少的重要一环,中导洞开挖并支护后形成的受力结构在正洞开挖时又须拆除,受力体系将发生转换。
安全转换受力体系是隧道施工的重点,只有在正洞初期支护支点作用于中墙顶面时方可拆除中导洞临时支护,同时为防止中导洞临时支护突然断开影响中导另半侧的安全,中墙顶面与中导拱顶初期支护之间用15cm X 15cm方木与另半侧工字钢支撑顶紧,中墙另一侧与中导边墙初期支护之间用工字钢顶紧,确保受力体系的安全转换和中墙的受力平衡。
在单洞进行初期支护和衬砌时,中墙较薄,因单洞的初期支护和衬砌给中墙造成偏压力,因此在中墙的另一侧用I16工字钢支撑加固中墙,以防中墙侧移或倾覆,该支撑在双洞边拱成型后方可拆除。
受力体系转换步骤见图。
7、防排水处理
由于各种预埋设施和行车的需要,高速公路对洞内防水要求非常高,必须做到滴水不渗。
防水以排为主,防排结合。
做法是:在二次衬砌与初期支护之间铺设一层250g/m2的无纺布和1mm厚阻燃型防水板,施工缝处设橡胶止水带,沿隧道轴向每隔6m设1道①5环向弹簧盲沟(即加劲透水软管)且与止水带交错布设,中墙顶设1Q 10环纵向弹簧盲沟,用三通管与埋在中墙内的PVC管连接,水从PVC管通过中墙排到洞内水沟,形成完整的排水系统。
隧道中墙只有1.4m厚,特别是在H类围岩段二次衬砌占去近1.25m,初期支护工字钢支撑点与纵向盲沟所剩空间较小,互相干扰较大。
为使纵向盲沟预埋定位准确,排水畅通,又不受工字钢支点的影响,施工时纵向弹簧盲沟与工字钢支撑一步到位,架立工字钢前先在中墙顶部预埋纵向盲沟,在工字钢落脚处放一20槽钢作支点,纵向盲沟从槽钢下通过,且在纵向盲沟与中墙间铺设一定长宽的无纺布与防水板。
为使槽钢不压破防水板,在槽钢与防水板之间增设3层无纺布,预埋的防水板与两正洞的防水板粘接,这样就解决了洞顶排水难的问题。
中墙排水及工字钢支点布置见图。
施工中一定要保证预埋的纵向盲沟不能被混凝土堵死。
防水板接头较多,接头又是防水最薄弱处,且又在工作面进行粘接,稍有不慎,就会在接头处出现渗漏水,所以粘接应注意:搭接宽度不小于10cm;将接头处用钢丝刷擦净晾干,然后用胶刷均匀地刷上粘胶剂(粘胶剂必须经试验合格后方可使用),刷胶时忌反复多次刷,以免“咬”起底胶;涂刷的胶浆宜薄不宜厚;待粘胶剂用手接触有粘性时(约5〜8min),将接头垫在托板(2cm X10cm X 50cm的光面木板)上,用手滚压,平顺地将接头面粘好,直至粘接平顺、牢固为止,不得有气泡和漏胶现象;将粘接好的防水板全面检查一遍,确保无破、无漏。
8、监控量测
隧道开挖后,在应力重分布和应力释放的过程中,围岩呈现出各种状态,如位移、性质变化等,特别是双连拱隧道开挖断面大,围岩自稳、成拱能力较
弱,且这种结构的隧道又没有成熟的经验可遵循,所以在施工中建立严密的监控量测是保证安全的主要手段,同时也是调整支护参数的信息来源。
为将变形量控制在允许范围内,必须制定出相应的控限标准,采用有限元法计算出的数据结合单洞控限标准,确定的双连拱隧道具体控限标准见表。
主要量测项目有:地表下沉、拱顶下沉、围岩收敛及地质变化情况。
测点布置见图。
(1)相对位移量测
用有限元计算结果,无论是左洞还是右洞,通过现场测得的结果,除进口段n类围岩呈不稳定状态外,其余ni、w、v类围岩经过一段时间,收敛值大部分未突破控限标准的80%就已趋于稳定,且后施工的隧道与先施工的隧道变形相差不大,说明支护参数和施工方法是安全、可行的,进口段n类围岩不稳定,及时施作了钢筋混凝土二次衬砌(衬砌厚度75cm),施工完后观测了拱顶下沉和位移收敛,无变化,说明洞口已稳定。
III类以上的围岩经过一段收敛变形后趋于稳定,说明采用的初期支护参数和施工方法是安全可行的。
(2)拱顶和地表下沉量测
隧道拱顶下沉洞口段n类围岩最大67mm,III类围岩最大39mm,W 类围岩最大8mm,V类围岩最大4mm。
与控限标准比,11、111类围岩要小的多,W、V类围岩按设计不发生下沉,实际有部分变形,是因为爆破振动后围岩自身要进行应力重分布和结构自稳,加之围岩较破碎有一定的下沉量也属正常变化,但很快便趋于稳定。
地表下沉进口浅埋段围岩较破碎,在洞口段地表埋设测点,开挖后至二次衬砌,测得最大下沉量为75mm。
对进口段及时施作二次衬砌后,经过一段
时间观测未再发生下沉现象。
出口为HI类围岩,地表下沉最大为30mm,在二次衬砌时下沉速度为0.1mm/d, 说明已呈稳定状态。