材料成型加工第一章 液态成型理论基础
第一章 金属液态成形理论基础

第一节 液态金属充型能力与流动性
0、什么是液态金属的充型能力
1)定义:
液体金属充满铸型型腔,获得尺寸精确、轮廓清晰的 成型件的能力,称为充型能力。
2)充型能力对成型的影响
充型能力不足时,会产生浇不足、冷隔、夹渣、气孔 等缺陷。
3)影响充型能力的因素
充型能力首先取决于金属本身的流动性(流动能力),同 时又受铸型性质、浇注条件和铸件结构等因素影响。
一、铸件的凝固方式
在铸件凝固过程中,其断面上一般存在三个区 域:固相区、凝固区和液相区。
1、分类
依据对铸件质量影响较大的凝固区的宽窄划分 铸件的凝固方式为如下三类:
(1)逐层凝固
纯金属和共晶成分的合金在凝固过程中不存在液、固并 存的凝固区,随着温度下降,固体层不断加厚,液体不 断减少,直达铸件中心,这种凝固方式称为逐层凝固。
机械应力
二、铸件的变形及其防止
1、变形的原因:
铸件内部残余内应力。 只有原来受拉伸部分产生压缩 变形、受压缩部分产生拉伸变 形,才能使铸件中的残余内应 力减小或消除。
平板铸件的变形
杆件的变形
床身铸件的变形
粱形铸件的弯曲变形
2、防止措施:
减小应力; 将铸件设计成对称结构,使其内应力互相平衡; 采用反变形法; 设置拉肋; 时效处理。
2、冷裂纹的特征
裂纹细小,呈连续直线状,裂缝内有金属光泽或轻 微氧化色。
3、防止措施
凡是能减少铸件内应力和降低合金脆性的因素 均能防止冷裂。 设置防裂肋亦可有效地防止铸件裂纹。
防裂肋
三、合金的吸气性
液态合金中吸入的气体,若在冷凝过程中不能溢 出,滞留在金属中,将在铸件内形成气孔。
一)气孔的危害
气孔破坏了金属的连续性,减少了其承载的有效 截面积,并在气孔附近引起应力集中,从而降低 了铸件的力学性能。 弥散性气孔还可促使显微缩松的形成,降低铸件 的气密性。
第一篇金属的液态成形

1. 金属的液态成形(铸造)1.0概述将金属材料加热到高温熔化状态,然后采取一定的成形方法,待其冷却、凝固后获得所需金属制品,这种制造金属毛坯的过程称为金属的液态成形。
金属的液态成形除了铸造之外,还有液态模锻。
1.0.1铸造的定义铸造是指将液态合金浇注到与零件的形状、尺寸相适应的铸型型腔中,待其冷却凝固后,获得所需形状、尺寸和性能的毛坯或零件的金属液态成形方法。
它是生产机器零件毛坯的主要方法之一。
1.0.2铸造的基本过程铸造生产的基本过程包括以下三个步骤:①根据零件的要求,准备一定的铸型;②把金属液体浇满铸型的型腔;③金属液体在铸型型腔中冷凝成形,获得一定形状和尺寸的铸件。
1.0.3铸造生产的特点铸造的实质就是液态金属(合金)逐步冷凝成形,具有以下特点:优点:①适应性广几乎所有金属及其合金,只要能够熔化成液态便能铸造,尤其是适合生产塑性差的材料。
②工艺灵活性大各种形状、尺寸(壁厚从0.5~1000mm、轮廓从几毫米至几十米)、重量(从几克~几百吨)和生产批量的铸件都能生产,能够制成如机床床身、箱体、机架、支座等具有复杂内腔的毛坯。
某些形状极其复杂的零件只能用铸造方法制造毛坯。
③省工省料铸件毛坯与零件形状相似,尺寸相近,加工余量小,金属利用率高,可以省工省料,精密铸件甚至不需切削加工,就可直接装配。
④生产成本低铸造用的原材料来源广泛,可直接利用报废的机件和切屑。
造型设备投资少,易操作。
缺点:①铸件内部晶粒比较粗大,组织疏松,容易产生气孔、夹渣等铸造缺陷,机械性能和可靠性不如锻件,尤其是冲击韧性较差,不宜制造受冲击或交变载荷作用的零件。
②生产过程比较复杂,工序多且一些工艺过程难以精确控制,铸件质量不稳定,废品率较高。
③工人劳动强度大,劳动条件差。
1.0.4铸造生产的发展历史我国是世界上最早掌握铸造生产的文明古国之一。
早在三千多年前,青铜铸器已有应用,二千五百多年前,铸铁工具也已相当普遍。
我国劳动人民对世界铸造业的三大贡献(三大铸造技术):泥型铸造(砂型铸造)、铁型铸造(金属型铸造)、失蜡铸造(熔模铸造)。
1.1液态金属成形理论基础全解
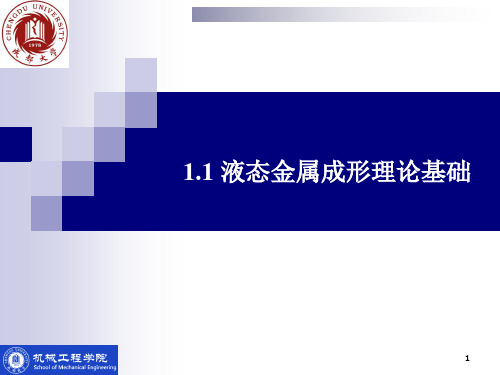
凡能形成低熔点化合物、降低合金液体粘度和 表面张力的元素,均能提高合金流动性,如 P 元素; 凡能形成高熔点夹杂物的元素,都会降低合金 流动性。如S、Mn等。
13
1.1.1 液态金属的流动性和充型能力
合金的结晶特点
金属在结晶状态下流动
(a)纯金属 (b)结晶温度范围宽的合金
14
1.1.1 液态金属的流动性和充型能力
3
概念和特点
铸造工艺的缺点
(1)铸件力学性能特别是塑性与冲击性能低于塑 性成形件; (2)铸造工序多,难以精确控制,铸件质量不稳 定; (3)砂型铸造劳动条件差; (4)铸件大多为毛坯件。
4
概念和特点
铸造方法的分类
金属型铸造
砂型铸造 特种铸造
低压铸造
压力铸造 熔模铸造
离心铸造 陶瓷型铸造 实型铸造
4.铸件结构方面 模数(折算厚度) 模数大的铸件,由于与铸型的接触表面积相对较 小,热量散失比较缓慢,则充型能力较高;
铸件的壁越薄,模数越小,则越不容易被充满。
铸件的复杂程度:
铸件结构复杂,则型腔结构复杂,流动阻力大, 铸型的充填就困难。
合金的流动性; 合金的收缩性; 合金的吸气性。
7
1.1.1 液态金属的流动性和充型能力
液态金属浇注入铸型后,液体利用自身的流 动性而充填铸型。充型能力:液体金属充满 型腔,获得尺寸精确、轮廓清晰的成型件的 能力。 充型能力的影响因素: 合金液体的流动性; 铸型性质; 浇注条件; 铸件结构。
1.1.1 液态金属的流动性和充型能力
2.铸型性质 铸型的蓄热系数 铸型的温度
蓄热系数是指当某一足够厚度 单一材料层一侧受到谐波热作 用时,表面温度将按统一周期 波动,通过表面的热流波幅与 表面温度波幅的比值。其值越 大,材料的热稳定性越好。即 蓄热系数小时,受热来的快, 凉时去也快。
材料成型技术基础第一章第五节与液态成形相关的新工艺、新技术简介

第五节与液态成形相关的新工艺、新技术简介一、模具快速成形技术快速成形(Rapid Prototyping,简称RP):利用材料堆积法制造实物产品的一项高新技术。
它能根据产品的三维模样数据,不借助其它工具设备,迅速而精确地制造出该产品,集中体现在计算机辅助设计、数控、激光加工、新材料开发等多学科、多技术的综合应用。
传统的零件制造过程往往需要车、钳、铣、刨、磨等多种机加工设备和各种工装、模具,成本高又费时间。
一个比较复杂的零件,其加工周期甚至以月计,很难适应低成本、高效率生产的要求。
快速成形技术是现代制造技术的一次重大变革。
(一)快速成形工艺快速成形技术就是利用三维CAD的数据,通过快速成形机,将一层层的材料堆积成实体原型。
迄今为止,国内、外已开发成功了10多种成熟的快速成形工艺,其中比较常用的有以下几种:1.纸层叠法—薄形材料选择性切割(LOM法)计算机控制的CO2激光束按三维实体模样每个截面轮廓对薄形材料(如底面涂胶的卷状纸、或正在研制的金属薄形材料等)进行切割,逐步得到各个轮廓,并将其粘结快速形成原型。
用此法可以制作铸造母模或用于“失纸精密铸造”。
2.激光立体制模法—液态光敏树脂选择性固化(SLA法)液槽盛满液态光敏树脂,它在计算机控制的激光束照射下会很快固化形成一层轮廓,新固化的一层牢固地粘结在前一层上,如此重复直至成形完毕,即快速形成原型。
激光立体制模法可以用来制作消失模,在熔模精密铸造中替代蜡模。
3.烧结法—粉末材料选择性激光烧结(SLS法)粉末材料可以是塑料、蜡、陶瓷、金属或它们复合物的粉体、覆膜砂等。
粉末材料薄薄地铺一层在工作台上,按截面轮廓的信息,CO2激光束扫过之处,粉末烧结成一定厚度的实体片层,逐层扫描烧结最终形成快速原型。
用此法可以直接制作精铸蜡模、实型铸造用消失模、用陶瓷制作铸造型壳和型芯、用覆膜砂制作铸型、以及铸造用母模等。
4.熔化沉积法—丝状材料选择性熔覆(FDM法)加热喷头在计算机的控制下,根据截面轮廓信息作X-Y平面运动和高度Z方向的运动,塑料、石腊质等丝材由供丝机构送至喷头,在喷头中加热、熔化,然后选择性地涂覆在工作台上,快速冷却后形成一层截面轮廓,层层叠加最终成为快速原型。
材料成型基础第一章液态成形理论基础
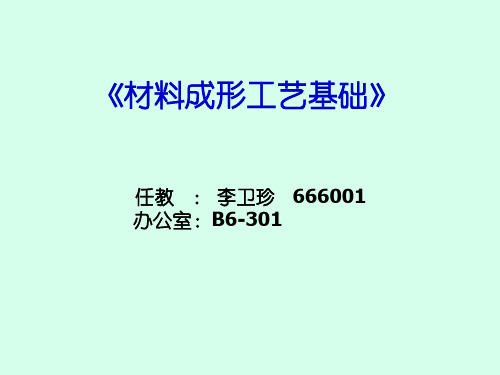
29
防止和减小铸造应力的措施
①合理设计铸件结构 铸件的形状愈复杂,各部分 壁厚相差愈大,冷却时温度愈不均匀,铸造应力愈 大。因此,在设计铸件时应尽量使铸件形状简单、 对称、壁厚均匀。 ②尽量选用线收缩率小、弹性模量小的合金。 ③采用同时凝固的工艺 所谓同时凝固是指采取一 些工艺措施,使铸件各部分温差很小,几乎同时进 行凝固,如下图所示。因各部分温差小,不易产生 热应力和热裂,铸件变形小。
凝固组织: 晶粒形态、大小、分布(宏观) 晶粒内部结构的形态、大小、分布(微观)
影响因素:炉料、铸件冷却速度、生产工艺
3
2、铸件的凝固方式
铸件的凝固一般存在3个区:固相、凝固、液相; 凝固区的宽度S决定了凝固方式。 (1)逐层凝固
动画3
只发生在纯金属或共晶成分合金 (2)糊状凝固
动画4
发生在结晶温度范围很宽的合金 (3)中间凝固
4
动画5
3、影响铸件凝固方式的主要因素: (1)合金的结晶温度范围
5
(2)铸件的温度梯度
(陡平程度)
6
铸件的温度梯度主要取决于: 1)铸造合金的性质。如铸造合金的导热性愈好、 结晶潜热愈大,则铸件均匀温度的能力愈强,温 度梯度就愈小。 2)铸型的蓄热能力好,对铸件的激冷能力愈强, 使铸件的温度梯度愈大。 3)提高浇注温度,会降低铸型的冷却能力,从 而降低铸件的温度梯度。 总之,合金的结晶温范围愈小,铸件断面的温 度梯度愈大,铸件愈倾向于逐层凝固方式,也愈 容易铸造;所以铸造倾向于糊状凝固的合金铸件 时,如锡青铜和球墨铸铁等,应采用适当的工艺 措施,减小其凝固区。
热应力 相变应力
24
热应力
铸件因壁厚不均匀,或铸件中存在着较大的温差,在同 一时间内铸件各部分收缩不同,先冷却的部位阻碍了后 冷却部位的收缩,在其内部产生了内应力。
材料成型基本原理完整版

第一章:液态金属的结构与性质1雷诺数Re:当Re>2300时为紊流,Re<2300时为层流。
Re=Du/v=Duρ/η,D为直径,u 为流动速度,v为运动粘度=动力粘度η/密度ρ。
层流比紊流消耗能量大。
2表面张力:表面张力是表面上平行于切线方向且各方向大小相同等的张力。
润湿角:接触角为锐角时为润湿,钝角时为不润湿。
3压力差:当表面具有一定的曲度时,表面张力将使表面的两侧产生压力差,该压力差值的大小与曲率半径成反比,曲率半径越小,表面张力的作用越显著。
4充型能力:充型过程中,液态金属充满铸型型腔,获得形状完整轮廓清晰的铸件的能力,即液态金属充型能力。
5长程无序、近程有序:液体的原子分布相对于周期有序的晶态固体是不规则的,液体结构宏观上不具备平移、对称性,表现出长程无序特征;而相对于完全无序的气体,液体中存在着许多不停游荡着的局域有序的原子集团,液体结构表现出局域范围内的近程有序。
拓扑短程序:Sn Ge Ga Si等固态具有共价键的单组元液体,原子间的共价键并未完全消失,存在着与固体结构中对应的四面体局域拓扑有序结构。
化学短程序:Li-Pb Cs-Au Mg-Bi Mg-Zn Mg-Sn Cu-Ti Cu-Sn Al-Mg Al-Fe等固态具有金属间化合物的二元熔体中均有化学短程序的存在。
6实际液态金属结构:实际金属和合金的液体由大量时聚时散、此起彼伏游动着的原子团簇空穴所组成,同时也含有各种固态液态和气态杂质或化合物,而且还表现出能量结构及浓度三种起伏特征,其结构相对复杂。
能量起伏:液态金属中处于热运动的原子的能量有高有低,同一原子的能量也在随时间不停的变化,时高时低,这种现象成为能量起伏。
结构起伏:由于能量起伏,液体中大量不停游动的局域有序原子团簇时聚时散,此起彼伏而存在结构起伏。
浓度起伏:游动原子团簇之间存在着成分差异,而且这种局域成分的不均匀性随原子热运动在不时发生着变化,这一现象成为浓度起伏。
第一章液态成形理论基础
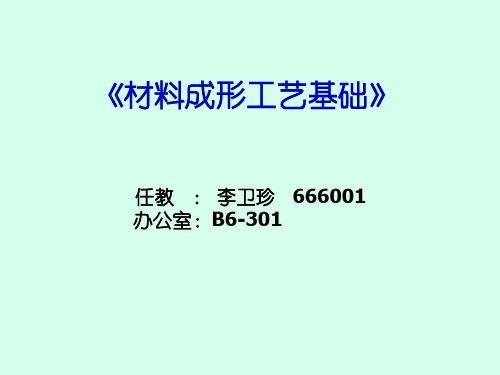
浇不足:铸件形状不完整
返回
冷隔:铸件看似完整,实际上有未完全融合的接缝 冷隔形成示意图
返回
铁碳合金中的共晶合金是含碳量为4.3%的合金。C点为 共晶点,温度为1147C,当铁水温度降低到该温度时, 液体会结晶成共晶体----莱氏体。 A L t浇 L+A D L+Fe3C F C 1147°C
缩孔率
/% 6.45 5.70 2.56 1.65 5.50
金属基体组织
铁素体-珠光体 莱氏体-珠光体 铁素体-珠光体 铁素体 珠光体-铁素体
18
基本结论(conclusions) 形状特征:缩孔 缩松 容积较大,多呈倒圆锥形 分散而细小
凝固方式:逐层凝固合金,易形成缩孔; 糊状凝固合金易形成缩松 缺陷部位:缩孔总是出现在铸件最后凝固的 部位,一般在上部; 缩松常分散在铸件壁厚的轴线区 域、厚大部位、冒口根部及内浇口附近。
泥石流
螺旋形流动性试样
铸铁和硅黄铜的流动性最好,铝硅合金的次之,铸钢的最差。
11
常用合金的流动性
表1-1
(砂型,试样截面8㎜×8㎜)
铸型 浇注温度/℃
1300 砂型 1300
合 金
铸铁:w(C+Si)=6.2%
螺旋线长度/mm
1800 1300
w(C+Si)=5.9%
w(C+Si)=5.2%
w(C+Si)=4.2%
《材料成形工艺基础》
任教 : 李卫珍 666001 办公室:B6-301
第一章 液态成形理论基础
§1 液态金属的凝固 §2 常用铸造合金 §3 铸造方法及其发展 §4 铸件结构与工艺设计
§1 液态成形理论基础
材料成形技术基础第一章重点知识点
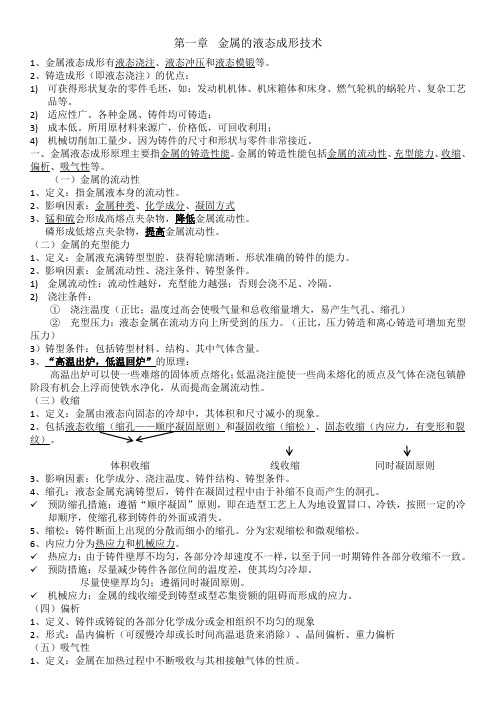
第一章金属的液态成形技术1、金属液态成形有液态浇注、液态冲压和液态模锻等。
2、铸造成形(即液态浇注)的优点:1)可获得形状复杂的零件毛坯,如:发动机机体、机床箱体和床身、燃气轮机的蜗轮片、复杂工艺品等。
2)适应性广。
各种金属、铸件均可铸造;3)成本低。
所用原材料来源广,价格低,可回收利用;4)机械切削加工量少。
因为铸件的尺寸和形状与零件非常接近。
一、金属液态成形原理主要指金属的铸造性能。
金属的铸造性能包括金属的流动性、充型能力、收缩、偏析、吸气性等。
(一)金属的流动性1、定义:指金属液本身的流动性。
2、影响因素:金属种类、化学成分、凝固方式3、锰和硫会形成高熔点夹杂物,降低金属流动性。
磷形成低熔点夹杂物,提高金属流动性。
(二)金属的充型能力1、定义:金属液充满铸型型腔,获得轮廓清晰、形状准确的铸件的能力。
2、影响因素:金属流动性、浇注条件、铸型条件。
1)金属流动性:流动性越好,充型能力越强;否则会浇不足、冷隔。
2)浇注条件:①浇注温度(正比;温度过高会使吸气量和总收缩量增大,易产生气孔、缩孔)②充型压力:液态金属在流动方向上所受到的压力。
(正比,压力铸造和离心铸造可增加充型压力)3)铸型条件:包括铸型材料、结构、其中气体含量。
3、“高温出炉,低温回炉”的原理:高温出炉可以使一些难熔的固体质点熔化;低温浇注能使一些尚未熔化的质点及气体在浇包镇静阶段有机会上浮而使铁水净化,从而提高金属流动性。
(三)收缩1、定义:金属由液态向固态的冷却中,其体积和尺寸减小的现象。
2、包括液态收缩(缩孔——顺序凝固原则)和凝固收缩(缩松)、固态收缩(内应力,有变形和裂纹)。
体积收缩线收缩同时凝固原则3、影响因素:化学成分、浇注温度、铸件结构、铸型条件。
4、缩孔:液态金属充满铸型后,铸件在凝固过程中由于补缩不良而产生的洞孔。
✓预防缩孔措施:遵循“顺序凝固”原则,即在造型工艺上人为地设置冒口、冷铁,按照一定的冷却顺序,使缩孔移到铸件的外面或消失。
液态成形基础416PPT课件
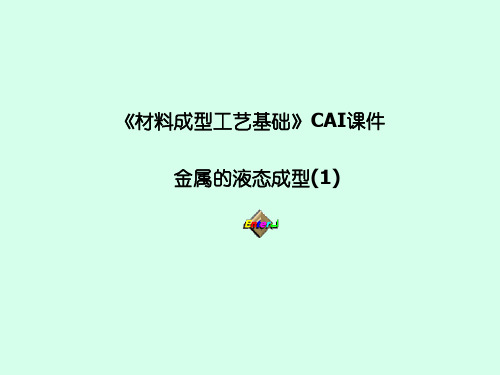
定向凝固的不足: (1)浪费金属和工时,增加成本; (2)易使铸件产生变形和裂纹;
用途: 主要用于必须补缩的场合,如铝青铜、
铸钢件等。 注意:
结晶范围很宽的合金,补缩效果很差, 难以避免显微缩松的产生
21 03.12.2020
3.铸造内应力(Internal stress) (1)内应力的形成
7 03.12.2020
二、液态合金的铸造性能 主要包括:充型能力、收缩性 1、合金的充型能力 充型能力:液态合金充满铸型型腔的能力
8 03.12.2020
影响合金充型能力的主要因素 (1)合金的流动性(液态合金本身的流动能力) 显然,流动性好,充型能力高
影响流动性的主要因素:合金的种类、 合金的成分、杂质等 1)合金的种类 与熔点、热导率、粘度等 有关;例铸钢
(1)收缩过程三阶段:
(1)液态收缩 从浇注温度t浇到凝固开始温 度t液间的收缩 (2)凝固收缩 从凝固开始温度t液到凝固终 止温度t固间的收缩 (3)固态收缩 从凝固终止温度t固到室温t室
间的收缩
14 03.12.2020
(2)影响收缩的因素:
1)化学成分 碳素钢,C%↑,凝固收缩↑ , 固态收缩↓; 灰铸铁,C%、Si%↑,收缩率↓ ;S%↑,收 缩率↑
由于合金的液态收缩和凝固收缩得不到补充而在 铸件内部形成的孔洞
(1)缩孔的形成 动画6
(2)缩松的形成 动画7
16 03.12.2020
基本结论(conclusions) 形状特征:缩孔 容积较大,多呈倒圆锥形 缩松 分散而细小 凝固方式:逐层凝固合金,易形成缩孔; 糊状凝固合金易形成缩松
缺陷部位:缩孔总是出现在铸件最后凝固的 部位,一般在上部
材料成型原理及工艺第一章液态成型工艺基础理论
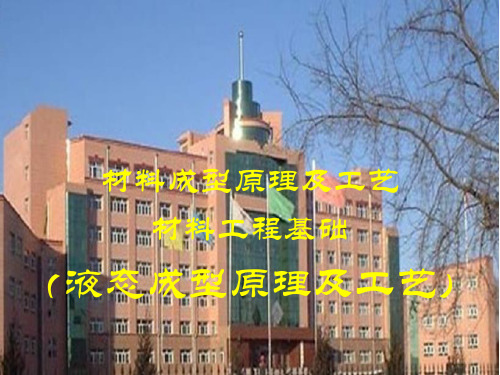
态 陷产生,导致成型件力学性能,
成 特别是冲击性能较低。
型 2. 涉及的工序很多,难以精确控
的 制,成型件质量不稳定。
缺 3.由于目前仍以砂型铸造为主,
点:
自动化程度还不很高,且属于热 加工行业,因而工作环境较差。
4.大多数成型件只是毛坯件,需 经过切削加工才能成为零件。
液态成型原理及工艺
冲天炉出铁
液态成型原理及工艺
绪论:
金属液态成型又称为铸造,
金 它是将固态金属熔炼成符合
属 液 态 成 型:
一定要求的液态金属,然后 将液态金属在重力或外力作 用下充填到具有一定形状型 腔中,待其凝固冷却后获得 所需形状和尺寸的毛坯或零 件,即铸件的方法。
制造毛坯或机器零件的重要方法。
液态成型原理及工艺
绪论:
的 游离原子
级,在此范围 内仍具有一定
近
液
的规律性。原
程
态
子集团间的空
结
空穴或裂纹 穴或裂纹内分
布着排列无规
有 序
构
则的游离的原
子。
液态成型原理及工艺
这样的结构不是静止的,而是 处于瞬息万变的状态,即原子 集团、空穴或裂纹的大小、形 态及分布及热运动的状态都处 于无时无刻不在变化的状态。 液态中存在着很大的能量起伏。
液 液态成型件在机械产品中占有重 态 要比例:
成 在机床、内燃机、重型机器中铸 型 件约占70%-90%;在风机、压
的 缩机中占60%-80%;在拖拉机
重 中占50%-70%;在农业机械中
要 占40%-70%;汽车中占20%-30
性 %。
液态成型原理及工艺
液 态 成 型 的 优 点:
(1) 适应性广,工艺灵活性大
《材料成型理论基础》课程大纲
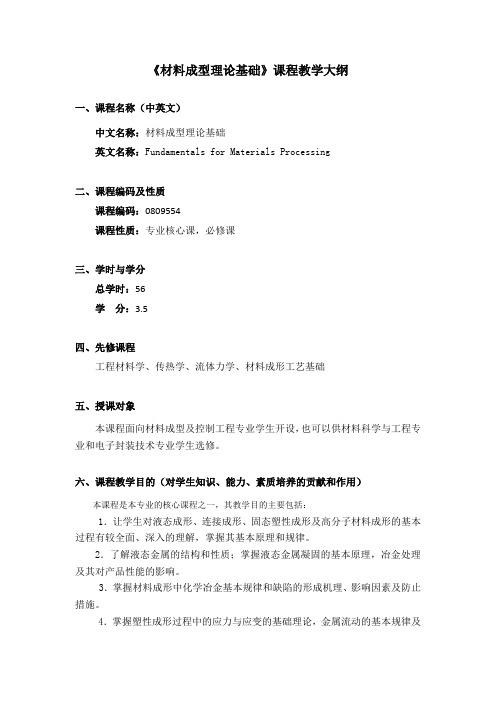
《材料成型理论基础》课程教学大纲一、课程名称(中英文)中文名称:材料成型理论基础英文名称:Fundamentals for Materials Processing二、课程编码及性质课程编码:0809554课程性质:专业核心课,必修课三、学时与学分总学时:56学分:3.5四、先修课程工程材料学、传热学、流体力学、材料成形工艺基础五、授课对象本课程面向材料成型及控制工程专业学生开设,也可以供材料科学与工程专业和电子封装技术专业学生选修。
六、课程教学目的(对学生知识、能力、素质培养的贡献和作用)本课程是本专业的核心课程之一,其教学目的主要包括:1.让学生对液态成形、连接成形、固态塑性成形及高分子材料成形的基本过程有较全面、深入的理解,掌握其基本原理和规律。
2.了解液态金属的结构和性质;掌握液态金属凝固的基本原理,冶金处理及其对产品性能的影响。
3.掌握材料成形中化学冶金基本规律和缺陷的形成机理、影响因素及防止措施。
4.掌握塑性成形过程中的应力与应变的基础理论,金属流动的基本规律及其应用。
5.了解高分子材料的组织转变及流动、成形的基本规律。
表1 课程目标对毕业要求的支撑关系七、教学重点与难点:教学重点:1)本课程以材料成形工艺的理论基础为主线,根据成形加工过程中材料所处或经历的状态,分为液态凝固成形、固态塑性成形、连接成形、塑料注射成形等几类,学习材料在成形过程中的组织结构、性能、形状随外在条件的不同而变化的规律性知识。
2)本课程着重利用前期所学的物理、化学等基础理论,以及传热学、流体力学等专业基础理论知识,学习液态成形、塑性成形、连接成形等基本材料成形技术的内在规律和物理本质,包括共性原理,同时也要注重个性规律性认识。
3)课程将重点或详细介绍三种主要材料成形方法中的主要基础理论和专门知识,阐述这些现象的本质,揭示变化的规律。
而对次要成形方法的基本原理或发展状况等只作简要介绍或自学。
4)重点学习的章节内容包括:第4章“单相合金与多相合金的凝固”(6学时)、第5章“铸件凝固组织的形成与控制”(6学时)、第7章“焊缝及其热影响区的组织和性能”(6学时)、第8章“成形过程的冶金反应原理”(6学时)、第11章“应力与应变理论”(4学时)、第12章“屈服准则”(6学时)。
工程材料成型 金属液态成形

1.2.2 特种铸造
脱壳和清理
蜡模压制
蜡模组装
撒砂
化学硬化 硬化 干燥处理
600~700°C 浇注
去浇冒口 毛刺清理
第1章 金属液态成形
1.2 砂型铸造
1.熔模铸造
1.2.2 特种铸造
录像 熔模铸造工艺过程 动画
第1章 金属液态成形
1.2 砂型铸造
1.熔模铸造
1.2.2 特种铸造
结壳前蜡模组
结壳后蜡模组
高度,可以提高充型能力 铸钢:1520~1620 ℃; 铸铁:1230~1450 ℃ ;
铝合金:680~780 ℃
第1章 金属液态成形
1.1 液态成形理论基础 1.1.1 熔融合金的流动性及充型
(2)影响合金流动性及充型的因素
铸型 铸型的温度低,热容量大 铸型的发气量大、排气能力低 浇注系统和铸型的结构越复杂
第1章 金属液态成形
1.2 砂型铸造
3.压力铸造
压力铸造是将熔融合金在高压、高速条件下充型, 并在高压下冷却凝固成型的精密铸造方法。压射比压为 30~70MPa,充满铸型时间为0.01~0.2S。 1.2.2 特种铸造
第1章 金属液态成形
1.2 砂型铸造
3.压力铸造
1.2.2 特种铸造
热压室式压铸机结构
1.2.2 特种铸造
※ 设备投资大 ※ 易产生气孔、缩孔和 缩松
第1章 金属液态成形
1.2 砂型铸造
4.低压铸造
低压铸造是液体在压力(0.02~0.06MPa)作用下自下而上充填型 腔形成铸件的一种方法。
1.2.2 特种铸造
动画
第1章 金属液态成形
1.2 砂型铸造
4.低压铸造
特点: 1.2.2 特种铸造
第1章 液态成型
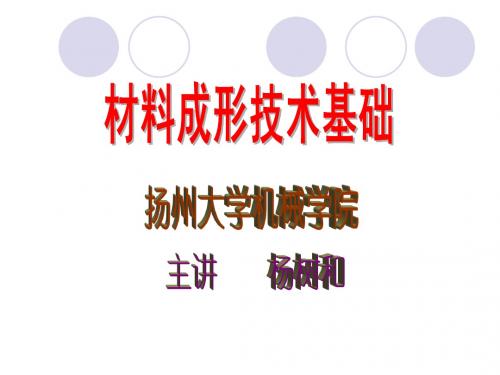
(2)影响收缩的因素 ①化学成分 铸钢和白口铸铁的收缩大,灰铸铁收缩小 ②浇注温度 浇注温度越高,液态收缩越大 ③铸件结构与铸型条件 铸件收缩时受阻越大,实际 收缩率就越小 3、铸件的缩孔和缩松
(1)缩孔 集中在铸件上部或最后凝固部位、容积较大 的孔洞。
形成条件: 逐层凝固方式; 液态收缩+凝固收缩>固态收缩。
0.45%C 铸钢:200mm 4.3%C 铸铁:1800mm
铸钢熔点高,在铸型中散 热快,流动性差 铝合金导热性好,流动性较差。
灰铸铁流动性最好, 硅黄铜、铝硅合金次之。
b.合金的成分
纯金属及共晶成分合金流动性好
TL-TS越大,流动性越差
温度(℃) 300 200 100 0 流动性(cm) 80 60 40 20 0
金属型铸造 铸型材料从石和泥、砂改用金属,从一次 型改进成为耐用性更高的所谓“永久”型。 1953年河北兴隆铁范的发现,证明我国早在战国时期 已经用白口铁的金属型浇注生铁铸件。这批铁范包括 锄、镰、斧、凿、车具等类共87件,大部完整配套。 其中,镰和凿是一范两件,锄和斧还采用了金属芯。 它们的结构十分紧凑,颇具特色。范的形状和铸件相 吻合,使壁厚均匀,利于散热。范壁带有把手,以便 握持,又能增加范的刚度。可以说是创造了一种中国 风格的金属型,并且在那个时候已经大体定型了。河 南泥池汉魏铁器窖藏中还有铸造成形铁板和矢镞的铁 范以及长达半米的大型铁犁范。
铸件占机床总重量75%以上,而生产成本仅占15-30%
3.铸件质量不稳定,废品率较高 。 力学性能较差。低于锻件。 4.生产条件较差,劳动强度高。
第一节 金属凝固成形理论基础
一、合金的铸造性能 (一)液态金属的充型能力 1.充型—液态合金填充铸型的过程。 充型能力—液态合金充满铸型型腔获得形状完整、 轮廓清晰的铸件的能力。 充型能力不足时,会产生浇不足、冷隔、夹渣、 气孔等缺陷。
材料成型原理与工艺一
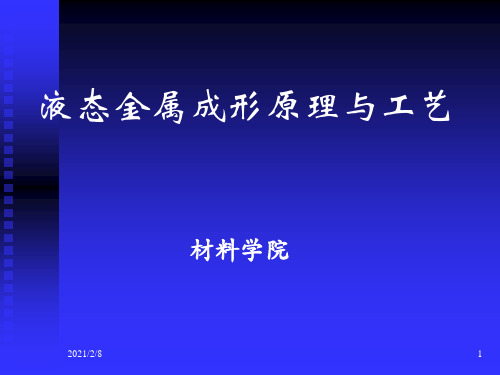
凝固
从传热学角度研究铸件与铸型的传热过程, 铸件断面上凝固区域的大小、凝固方式与铸 件质量的关系,以及铸件的凝固时间等。
2021/2/8
19
2021/2/8
20
、 1 液态金属凝固方式及与铸件质量的关系
2021/2/8
凝固区域
固相区、凝固区、液相区
凝固方式
逐层凝固方式 体积凝固(糊状凝固方式) 中间凝固方式
液态金属成形原理与工艺
材料学院
2021/2/8
1
第一节:液态金属成形概论
一、液态金属成形的概念及科学问题
液态金属成形的概念:
将金属加热到液态,使其具有流动性,然后浇入到具有一定形状的型腔的
铸型中,液态金属在重力场或外力场(压力、离心力)的作用下充满型腔, 冷却并凝固成具有型腔形状的铸件。
液态金属成形的优点:
晶体生长:晶核不断生长成晶体,直到互相相遇。
连续生长:粗糙界面的生长 侧向生长:平整界面的生长
2021/2/8
25
连续生长
侧向生长
2021/2/8
26
3、铸件晶粒组织的形成和控制
2021/2/8
27
细晶粒在铸造过程中的实现
增大冷却速度—整个断 面同时产生较大过冷
获得细等轴晶的措施
2021/2/8
2)铸型性质方面的因素 铸型的储热系数、铸型温度、铸型中的气体。
3)浇注条件方面的因素 浇注温度、充型压头(压力头)、浇注系统的结构。
4)铸件结构方面的因素 模数(或称换算厚度)、铸件的复杂程度。
2021/2/8
18
三 液态金属的凝固
凝固定义:
合金从液态转变为固态的状态变化,称为一次结晶或凝固。
液态成型理论基础
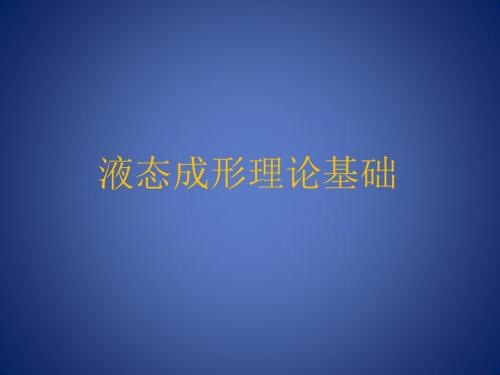
一层的运动速度差别越小,表明液体越不
容易流动,则液体粘度越大。
因此,粘度η是液体内摩擦阻力大小的表征
粘度的物理意义
τ= (1)
物理意义:作用于液体表面的应力τ大小与 垂直于该平面方向上的速度梯度dVx/dy的 比例系数。 应力τ一定时,产生的速度剃度dVx/dy大, 表明粘度η低。
方程(1)被称为液体粘度的牛顿定律。
§2 液态金属的性质
液态金属有各种性质。只讨论两个性质: 粘度和表面张力。
一.粘度
粘度系数,简称粘度。 根据牛顿提出的数学表达式定义
τ=
(1)
式中, τ为作用于液体表面的外切应力; Vx为液体在x方向的运动速度; 表示沿y方向的速度梯度 η为动力粘度
由于液体原子层之间的内摩擦力,液体 第一原子层沿运动方向受第二层阻碍,第 二层受第三层阻碍...... 内摩擦力越大,则每一原子层相对于下
3.在冒口补缩过程中
在铸件凝固过程中,因体积收缩而形成缩 孔和缩松,此时依靠冒口中液体的静压头 进行补缩。 补缩距离与η的平方根成反比。
二.表面张力
表面张力是表面上平行与表面切线方向且 各方向上大小相同的张力。 形成原因: 由于物体在表面上的质点受力不均所致。 原子间结合力越大,表面能越大,表面张力 越大 表面张力的单位:N/m;表面能:J/cm2 类似于表面张力,有界面张力 界面张力与界面两侧质点间结合力大小成反 比
1.润湿角θ
表面张力的大小也可以以润湿角大小表示。 两种物质接触,润湿与 不润湿取决于两种物质间的 亲和力,亲和力大就润湿, 否则就不润湿。 在图中的接触角,为锐角时为润湿,否则不 润湿。 平衡时,COSθ=
2.影响因素
(1)熔点 熔点越高,表面张力越大 (2)温度 T↑,表面张力↓
液态成形理论基础
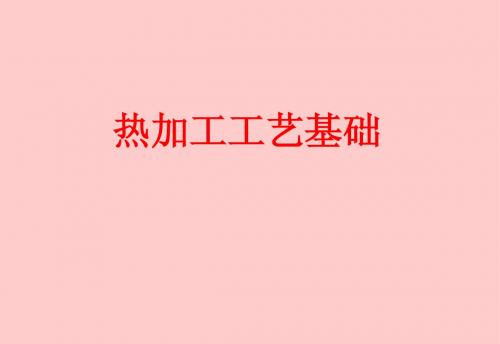
2、铸造生产的特点
• • • • • 1)适应性大(铸件重量、合金种类、零件形状都不受限制) 2)成本低 3)工序多,质量不稳定,废品率高 4)机械性能较同样材料的锻件差 原因:晶粒粗大,组织疏松,成分不均匀
• 含碳0.3%的铸钢与锻钢机械性能比较
σb (Mpa) 铸钢 锻钢 500 530
σs (Mpa) 280 310
• 3.相变应力:固态下发生相变的合金,由于部分部分 冷却速度不同,达到相变温度的时刻不同,且发生相 变的程度也不同消除铸造应力的措施
• A|、使铸件符合“同时凝固”的原则(内浇口开在 薄壁处、厚壁处安放冷铁) • B、造型工艺上,改善铸型或芯子的退让性
• C、铸件结构上尽量使铸件能自由收缩(壁厚均匀、 壁与壁的联接均匀等)
• 度、杂质含量及其物理性质有关。
• 充型能力:合金充满型腔,获得形状完整、轮廓清晰 的铸件的能力。 • 流动性好的合金,易于充满薄而复杂的型腔。有利于 气体和夹杂物上浮排除,有利于铸件凝固时的补缩。 流动性不好的合金,其充型能力差,易产生浇不足、 冷隔、气孔、缩孔、缩松、热裂纹等缺陷。
熔融合金的流动性通常以“螺旋形 试样”(图1-3)长度来衡量。在相同 的浇注条件下, 将液态合金浇注到螺旋形标准试样 所形成的铸型中,浇注冷凝后,测 出其实际螺旋线长 度,测得的螺旋线长度越长,表明 合金的流动性越好。
(2)浇注温度 浇注温度越高,过热度越大,使液态收缩增加,合金的 总收缩率加大。对于钢液,通常浇注温度提高100度,体收缩率增加约 1.6%,因此浇注温度越高,形成缩孔倾向越大。 (3)铸件结构和铸型条件 铸件在铸型中的冷凝过程中往往不是自由收
缩,而是受阻收缩。其阻力来源于:①铸件各部分的冷却速度不 同.引起各部分收缩不一致,相互约束而对收缩产生阻力。②铸型和 型心对收缩的机械阻力。因此,铸件的实际收缩率比自由收缩率要小 一些。铸件结构越复杂,铸型硬度越大.型心骨越粗大,则收缩阻力 亦越大。
- 1、下载文档前请自行甄别文档内容的完整性,平台不提供额外的编辑、内容补充、找答案等附加服务。
- 2、"仅部分预览"的文档,不可在线预览部分如存在完整性等问题,可反馈申请退款(可完整预览的文档不适用该条件!)。
- 3、如文档侵犯您的权益,请联系客服反馈,我们会尽快为您处理(人工客服工作时间:9:00-18:30)。
(3)铸件裂纹 有热裂和冷裂(弹性状态和塑性状态)
①热裂 在凝固后期或凝固后在较高温度下形成 的裂纹
裂纹断面严重氧化,无金属光泽,沿晶 常见于铸钢件、铝合金件
②冷裂 在较低温度下形成的裂纹 断面有金属光泽,或微氧化
常见于受拉的部位,特别是应力集中处
③防止裂纹的措施 ● 减少和消除应力 ●控制 S、P 含量
机械应力是暂时存在的应力 当形成应力的原因消除后便会消失
但机械应力一般是拉应力或切应力,铸件 在高温下强度低,若瞬间应力之和超过
其抗拉强度时,就可能产生裂纹。
② 热应力 凝固和冷却过程中,不同部位由于温差造
成不均匀收缩而引起的铸造应力
冷却后,热应力残留在铸件内部
形成过程:三个阶段
第一阶段
Τ1之前 粗细杆温度较高,易产生变形 虽冷却速度不同收缩不一致,但产生的内 应力将会引起微量变形而自行消除。
③合理应用冒口、冷铁、补贴 目的为使铸件顺序凝固
④加压补缩 使铸件在压力下凝固,可显著减少缩松 如压力铸造、离心铸造等
4.铸造应力、变形和裂纹
铸造应力——因凝固受阻产生
σs——变形 σb——开裂
(1) 铸造应力 有热应力和机械应力
① 机械应力(收缩应力) 在凝固收缩时,因铸型、型心、浇冒口及 铸件本身结构阻碍收缩而引起的应力。
三. 合金的吸气性
一般液态金属,在高温下会吸收大量气体, 若在其冷却过程中不能逸出,则在冷却后 使铸件内形成气孔缺陷。
气孔,减少铸件有效承载面积,降低性能 特别是韧性和疲劳性能
有三种类型的气孔
1. 侵入气孔
大量气体侵入金属液而形成 气体来源:浇注时,砂型及型心缩含水分
蒸发、有机物及附加物挥发 特征:位于砂型及型心表面附近
2)铸型特点
(1)铸型的蓄热能力(蓄热系数) (2)铸型形状 (3)铸型温度 (4)铸型中气体
3)浇注条件 (1)浇注温度 温度↑ ,金属液的粘度↓,↑流动 性
(2)充型压力 在流动方向上受到的压力↑,流动 性越好
二、合金的收缩
1. 收缩
从液态→室温; 尺寸减少 铸件的缩孔、缩松、裂纹、变形等都于 收缩有关
呈椭圆形或梨形
2. 析出气孔
溶解于金属液中的气体在冷却过程中,因 气体溶解度下降而析出,并在铸件中残留 特征:尺寸小,分布面积广,甚至遍布
整个铸件截面。也称“针孔” 针孔影响机械性能、气密性
3.反应气孔
液态金属与铸型材料、心撑、冷铁或熔渣 之间发生化学反应而产生气体形成的气孔 特征:分布在铸件表层1~2mm处,
收缩的三个阶段:
收缩的三个阶段
1)液态收缩 液面下降
2)凝固收缩 液态收缩和凝固收缩是铸件产生缩孔、
缩松的根本原因 3)固态收缩
铸件的外形尺寸减小;用线收缩率 产生铸造应力,变形、裂纹等的原因
2. 影响收缩的因素
1)化学成分
2)浇注温度 温度高,收缩大
3)铸型条件,铸件结构 由于各部分冷却速度不同,使收缩相互 制约而不能自由收缩
材料成型加工
第一篇金属的液态成型
俗称“铸造” 指熔炼一定成分的合金,制造铸型并将熔
融金属浇进铸型内,凝固后获得一定形 状和性能的铸件
优点: 1)最经济地制造外形和内腔很复杂的零件 2)适应性广 3)成型件的形状、尺寸接近零件 4)原材料来源广,价廉,设备投资少
第一章 液态成型理论基础
§1.1 液态金属的凝固 一、凝固组织 凝固过程是一个结晶过程,是形核和长大 过程 凝固组织:
(3)缩孔和缩松的防止
其产生使铸件的机械性能下降,甚至渗漏 ①采用顺序凝固原则
经冒口充型 向冒口和内浇道方向凝固 最终将缩孔转移到冒口中
可获得致密的铸件,但使铸件各部分 温差大,易产生内应力。冒口增加成本 用于收缩大,凝固温度范围窄的合金
②合理确定浇注系统和浇注工艺 浇注系统的位置影响铸型的温度分布, 进而影响其凝固顺序
2)糊状凝固 合金的结晶温度范围宽 在凝固前沿有液、固共存区,结晶温度范
围很宽的时候,共存区贯穿整个断面 3)中间凝固 介于两种凝固之间
影响凝固方式的因素: 1)合金的结晶温度范围 2)铸件断面的温度梯度 温度梯度↑ 凝固区宽度↓
§1.2 液态金属的工艺性能 称铸造性能 流动性、收缩性、吸气性、偏析等
吸气——气孔 破坏材质的连续性,↓承载能力; 应力集中; 渗漏
铸件的凝固方式
返回
热应力的形成
返回1
返回2
返回3
一、合金流动性与铸件质量关系
主要影响充型能力→影响质量
流动性好:完整、轮廓清晰、尺寸精确 流动性差:粘度大,易形成夹杂;浇不足 流动性太高:温度高,吸气;
冲刷型腔壁→粘砂、砂眼
二、合金的收缩性与铸件质量关系
收缩——缩孔、缩松 产生应力集中;气密性
收缩——应力,导致变形、开裂
三、合金的吸气与铸件质量
宏观:晶粒的形态、大小、分布等 微观:晶粒内部结构的形状、大小、 分布等
凝固组织对铸件的力学性能影响很大。 二、铸件的凝固方式 凝固过程中的三个区域:
固相区、 凝固区、 液相区 凝固方式是根据凝固区的宽度来划分 1)逐层凝固 不存在液、固共存的凝固区,有一平滑的
界面。 纯金属和 共晶合金的凝固方式 图
图
第二阶段
T1~T2之间 细杆温度已较低,难于产生塑性变形,但粗
杆温度仍较高 两个杆冷却速度不同,收缩不一致,但产生
的内应力将使粗杆产生微量的收缩而自行消 除。
图
第三阶段 T2之后 粗细杆温度均较低,难以产生塑性变形; 其中细杆已接近室温,收缩趋于停止; 粗杆温度较细杆高,仍会有较大的收缩, 因此将受到细杆阻碍而受拉,细杆受压
也称“皮下孔”
§1-2合金工艺性能与铸件质量关系
铸件质量:铸件本身能满足用户要求的程度 包括外观质量、内在质量、使用质量
①外观质量:指表面质量达到用户要求 粗糙度;表面质量;尺寸公差等
②内在质量:不能用肉眼检查出来的质量 化学成分;物理、力学性能等
③使用质量:能满足使用要求的性能 在高速、磨耗、高热等条件下 的工作性能;切削性能;焊接
3. 缩孔和缩松 凝固过程中由于补缩不良而产生孔洞。 集中孔洞——缩孔 分散孔洞——缩松
(1) 缩孔的形成
常出现在最后凝固的部位 纯金属、共晶合金、凝固范围窄的合金 易产生缩孔
(2)缩松的形成
分散而细小的孔洞 借助高倍放大镜——显微缩松 影响气密性,易渗漏
多发生在铸件的轴线附近和热节部位 凝固温度范围越宽,越易产生缩松
图
减少和消除热应力的方法
●合理设计铸件的结构 壁厚均匀、圆角过度等
●同时凝固原则 ●去应力退火
(2)铸件变形
铸件内应力存在,铸件总是力图趋于稳定 状态,故会自发地产生变形
一般,受拉应力部分——内凹 受压应力部分——凸出
防止措施: ①减少应力 ②增加铸件的刚性(如加强筋等) ③反变形法 造型时使型腔具有相反的预变形量 铸件凝固后抵消变形
一、流动性 1. 概念 流动性:合金流动的能力。是最重要的铸 造性能 充型能力:金属液充满铸型型腔,获得轮 廓清晰、形状准确的铸件的能力
流动性的测试:用螺旋形流动性试样长度 在相同的铸型及浇注条件下,流动性试样
长度越长,则合金的流动性越好
2. 影响流动性的因素
1)合金成分 主要影响其凝固方式,进而影响流动性 凝固方式: 层状凝固 糊状凝固 中间凝固