第8章 气辅成型模具
气辅注塑原理
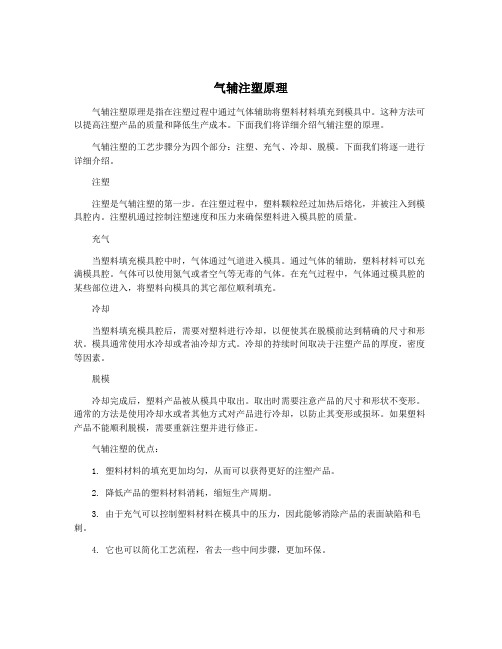
气辅注塑原理气辅注塑原理是指在注塑过程中通过气体辅助将塑料材料填充到模具中。
这种方法可以提高注塑产品的质量和降低生产成本。
下面我们将详细介绍气辅注塑的原理。
气辅注塑的工艺步骤分为四个部分:注塑、充气、冷却、脱模。
下面我们将逐一进行详细介绍。
注塑注塑是气辅注塑的第一步。
在注塑过程中,塑料颗粒经过加热后熔化,并被注入到模具腔内。
注塑机通过控制注塑速度和压力来确保塑料进入模具腔的质量。
充气当塑料填充模具腔中时,气体通过气道进入模具。
通过气体的辅助,塑料材料可以充满模具腔。
气体可以使用氮气或者空气等无毒的气体。
在充气过程中,气体通过模具腔的某些部位进入,将塑料向模具的其它部位顺利填充。
冷却当塑料填充模具腔后,需要对塑料进行冷却,以便使其在脱模前达到精确的尺寸和形状。
模具通常使用水冷却或者油冷却方式。
冷却的持续时间取决于注塑产品的厚度,密度等因素。
脱模冷却完成后,塑料产品被从模具中取出。
取出时需要注意产品的尺寸和形状不变形。
通常的方法是使用冷却水或者其他方式对产品进行冷却,以防止其变形或损坏。
如果塑料产品不能顺利脱模,需要重新注塑并进行修正。
气辅注塑的优点:1. 塑料材料的填充更加均匀,从而可以获得更好的注塑产品。
2. 降低产品的塑料材料消耗,缩短生产周期。
3. 由于充气可以控制塑料材料在模具中的压力,因此能够消除产品的表面缺陷和毛刺。
4. 它也可以简化工艺流程,省去一些中间步骤,更加环保。
气辅注塑是一种高效、环保、节能的注塑工艺。
它可以提高生产效率,降低生产成本,同时还能有效改善产品的质量和外观。
近年来,气辅注塑工艺广泛应用于各个领域。
它可以用于制造电子产品、医疗器械、汽车零配件、家用电器等。
它的灵活性和可塑性极高,满足了市场对产品多样化、品质一致化、成本低价化等需求。
在汽车零配件的制造中,气辅注塑的运用已成为一种趋势。
由于汽车零配件的尺寸和数量大,所以制造成本非常高。
而这里正是气辅注塑的优势所在。
利用气辅注塑工艺,能够更好的控制塑料材料在模具中的填充,从而提高产品的密度、强度和耐用性。
气辅成型模具

第三单元其他塑料模具简介随着塑料产品应用的广泛和塑料成型工艺的飞速发展,人们对塑料制品的要求也越来越高。
近几年来,除了注塑模以外,在其他的塑料模具方面也有了很大的发展,如压制成型模具、真空成型模具、多色注塑模、气辅成型、高光注塑模等课题七气体辅助注射成型及实例学习目标通过本课题的学习,你将了解气体辅助注射成型方面的基本知识,熟悉气体辅助注射成型的设计方法和制造特点等学习内容气辅成型原理、模具特点、辅助设备、成型工艺及特点等.家用电器部件:汽车塑料部件:电子设备部件:家具塑料部件:气辅技术可在家电、汽车、家具、日常用品、办公用品等几乎所有塑料制件领域得到应用。
采用气辅技术可以减少成型的锁模力,缩短成型周期,减少翘曲变形。
同时,由于成型所需注射压力的降低,从而可以在较小的注塑机上成型较大的制品。
从表面上看,气辅技术的优势源于利用高压气体把厚壁的内部掏空;从工程力学的原理上看,气辅技术的应用改变了材料在制品断面上的分布,使制件刚性和强度得以改善,承载力增加,这在汽车、飞机、船舶等交通工具的轻量化方面显示出了巨大且诱人的应用优势和前景。
气辅技术在美、日、欧等发达国家和地区正日益得到广泛应用,短短几年,该技术用于注塑制品成型的模具配套率已达10%。
随着时间的推移,在市场竞争极为激烈的情况下,更加完善的气辅技术一定会为更多的塑料制件制造商所接受。
气辅技术在国内的应用首先体现在壳类制品和轿车内饰件等家电、汽车、仪器、仪表、家具等行业。
气辅技术的最大应用领域是家电产品,就日本电视机行业来说,64cm 以上大屏幕彩电几乎90%以上采用气辅成型技术。
目前,中国年产电视机2500万台,其中彩电1200万台。
在彩色电视机份额中,占20%左右的64cm以上大屏幕彩电有240万台,而且大屏幕彩电的数量随市场的需求正逐年递增。
在汽车注塑件方面,美国福特汽车公司用气辅技术成型了汽车保险杠、汽车内饰件面板、仪表板等,还有美国克莱斯勒复合概念车整个车身以气辅注射成型,这些都为气辅技术在汽车注塑件上的应用开了先例。
《中文版Moldflow模流分析从入门到精通 2021版》读书笔记思维导图

3.2 网格的划 分
3 3.3
Autodesk Moldflo...
4 3.4
Autodesk Moldflo...
5 3.5
CADdoctor模 型修复医生
3.1.1 有限元 网格类型
3.1.2 认识网 格单元
3.2.2 生成网格
3.2.1 设置网格密 度
3.2.3 网格统计
3.3.1 网格诊 断技术
《 中 文 版 最新版读书笔记,下载可以直接修改 Moldflow模流分 析从入门到精通 2021版》
思维导图PPT模板
本书关键字分析思维导图
参数
文件
模流
模具
方法
浇口
解决
分析
工艺
成型 位置
气辅
案例
网格
缺陷
双色
创建
设计
教学
01 文前内容
目录
02 第1章 Autodesk Moldflo...
03 第2章 创建分析模型
2.1.1 创建节点
2.1.3 创建区域
1
2.2.1 平移实 体
2
2.2.2 旋转实 体
3
2.2.3 3点旋 转实体
4
2.2.4 缩放实 体
52.2Biblioteka 5 镜像实 体2.3.2 创建冷却系 统几何
2.3.1 创建浇注系 统几何
2.3.3 创建模具镶 件几何
第3章 网格规划与缺陷修复
1
3.1 有限元网 格概述
04
1.4.4 选 择分析类型
06
1.4.6 设 置工艺参数
05
1.4.5 选 择成型材料
1.4.7 设置注射 (进料口)位置
气体辅助注射成型【范本模板】
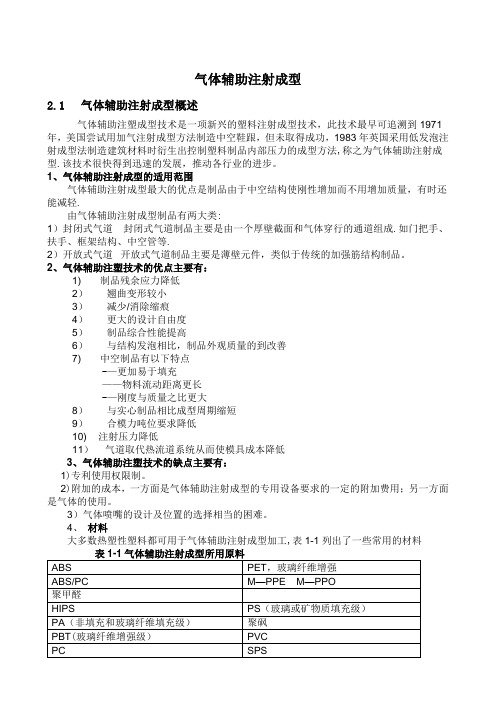
气体辅助注射成型2.1气体辅助注射成型概述气体辅助注塑成型技术是一项新兴的塑料注射成型技术,此技术最早可追溯到1971年,美国尝试用加气注射成型方法制造中空鞋跟,但未取得成功,1983年英国采用低发泡注射成型法制造建筑材料时衍生出控制塑料制品内部压力的成型方法,称之为气体辅助注射成型.该技术很快得到迅速的发展,推动各行业的进步。
1、气体辅助注射成型的适用范围气体辅助注射成型最大的优点是制品由于中空结构使刚性增加而不用增加质量,有时还能减轻.由气体辅助注射成型制品有两大类:1)封闭式气道封闭式气道制品主要是由一个厚壁截面和气体穿行的通道组成.如门把手、扶手、框架结构、中空管等.2)开放式气道开放式气道制品主要是薄壁元件,类似于传统的加强筋结构制品。
2、气体辅助注塑技术的优点主要有:1)制品残余应力降低2)翘曲变形较小3)减少/消除缩痕4)更大的设计自由度5)制品综合性能提高6)与结构发泡相比,制品外观质量的到改善7)中空制品有以下特点-—更加易于填充——物料流动距离更长-—刚度与质量之比更大8)与实心制品相比成型周期缩短9)合模力吨位要求降低10)注射压力降低11)气道取代热流道系统从而使模具成本降低3、气体辅助注塑技术的缺点主要有:1)专利使用权限制。
2)附加的成本,一方面是气体辅助注射成型的专用设备要求的一定的附加费用;另一方面是气体的使用。
3)气体喷嘴的设计及位置的选择相当的困难。
4、材料大多数热塑性塑料都可用于气体辅助注射成型加工,表1-1列出了一些常用的材料聚醚酰亚胺HDPE5、设计注意事项:气体辅助注射成型制品的优化设计需要注意以下三点:1)气道布局的优化2)气道尺寸与制品相关3)平衡物料填充方式气道在模腔内的布局既包括气体喷嘴的定位,也包括气道进入模具位置的选择,气体会沿着阻力最小的方向向前流动。
在物料进入模具之后,模腔中压力最小的地方必须靠近气道的末端,这个压力差会促使气流沿着预期流道前进,从而推动物料充满整个型腔。
气辅成型
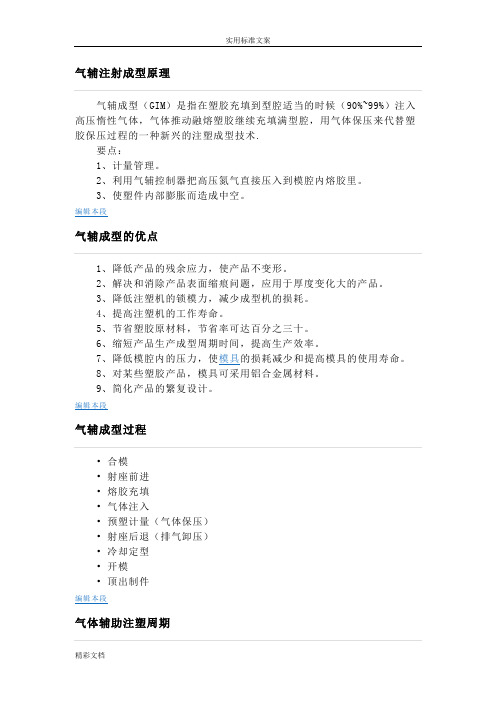
气辅成型(GIM)是指在塑胶充填到型腔适当的时候(90%~99%)注入高压惰性气体,气体推动融熔塑胶继续充填满型腔,用气体保压来代替塑胶保压过程的一种新兴的注塑成型技术.要点:1、计量管理。
2、利用气辅控制器把高压氮气直接压入到模腔内熔胶里。
3、使塑件内部膨胀而造成中空。
编辑本段气辅成型的优点1、降低产品的残余应力,使产品不变形。
2、解决和消除产品表面缩痕问题,应用于厚度变化大的产品。
3、降低注塑机的锁模力,减少成型机的损耗。
4、提高注塑机的工作寿命。
5、节省塑胶原材料,节省率可达百分之三十。
6、缩短产品生产成型周期时间,提高生产效率。
7、降低模腔内的压力,使模具的损耗减少和提高模具的使用寿命。
8、对某些塑胶产品,模具可采用铝合金属材料。
9、简化产品的繁复设计。
编辑本段气辅成型过程• 合模• 射座前进• 熔胶充填• 气体注入• 预塑计量(气体保压)• 射座后退(排气卸压)• 冷却定型• 开模• 顶出制件编辑本段气体辅助注塑周期1、注塑期以定量的塑化塑料充填到模腔内。
(保证在充气期间,气体不会把产品表面冲破及能有一理想的充气体。
)2、充气期可以注塑期中或后,不同时间注入气体。
气体注入的压力必需大于注塑压力,以致使产品成中空状态。
3、气体保压期当产品内部被气体充填后,气体作用于产品中空部分的压力就是保压压力,可大大减低产品的缩水及变形率4、脱模期随着冷却周期的完成,模具的气体压力降至大气压力,产品由模腔内顶出。
编辑本段气辅成型所需的条件• 注塑成型机• 气体的来源(氮气发生器)• 输送气体的管道• 控制氮气有效流动的设备(氮气控制台)• 带有气道设置的成型模具(气辅模具)编辑本段成型条件的设定1、注塑机的设定o 原材料的烘干温度与传统成型一致o 料筒的塑化温度比传统注塑偏高o 模温要求较严,冷却水路布置要使冷却效果均衡o 注塑压力与传统注塑基本一致o 注塑速度一般采用高速填充2、氮气设备的设定a、氮气发生器的压力一般设定在30MPA左右b、氮气控制台要素的设定(延迟时间、气体压入时间、气体保持时间、气体放气时间、压力的设定、气体速率)气辅注塑成型技术 2009-6-22 中国设备网文字选择:大中小气辅注塑工艺是国外八十年代研究成功,九十年代才得到实际应用的一项实用型注塑新工艺,其原理是利用高压隋性气体注射到熔融的塑料中形成真空截面并推动熔料前进,实现注射、保压、冷却等过程,使产品形成真空。
气辅注塑成型模具设计

气辅注塑1.气体辅助注塑目前所指的气体辅助注塑:是指将氮气注射入产品内,使产品内部形成中空。
模具打开前,控制器会将塑胶工件内的氮气释放回大气中。
2.气辅注塑成形工艺的优势1)低射胶、低锁模力;2)压力分布均匀、收缩均匀、残余应力低、不易翘曲,尺寸稳定;3)消除凹陷,模面再现性高;4)省塑料,可用强度及价格更低的塑料;5)可用强度和价格更低的模具金属;6)厚薄件一体成型,减少模具及装配线数目;7)可用较厚的筋,角板等补强件,提高制品刚性,使得制件公称厚度得以变薄。
8)增强设计自由度。
3.气辅射胶控制工艺1)短射工艺,即胶料未完全充满型腔时,继之以氮气注射;2)满射工艺,塑胶熔体充满型腔之后,停止注射,继之以氮气注射。
短射工艺的特点:在气辅注塑中,塑胶注射取决于胶件形状及胶料性能,在以下条件才可进行短射。
1)胶件必须有独立完整的气体通道,即气流在穿透胶件时,无分支气道可走。
2)气体通道中多余胶料有足够的溢流空间。
3)胶料流动性优良,粘度不可太低,尽量避免使用含破坏高分子键的填充物的胶料。
4)胶料导热度较低,有可较长时间保持熔融状态的能力。
满射工艺特点:胶件射胶完成,通过气体代替啤机,防止胶件收缩。
其优点在于,啤机保压是以射胶量及压力来防止胶件收缩,气辅保压,则以气体穿透塑胶收缩后的空间,防止胶件表层埸陷。
4.气辅压力分析:现我们看以下气辅压力与啤机压力的对比:1)气辅压力a)低气压8002b)中气压1500psi=105.63 kg/cm2c)高气压250022)啤机压力a)100 TON注塑最大压力188Mpa=1917 kg/cm2b)280 TON注塑最大压力150Mpa=1530 kg/cm2c)650TON注塑最大压力153Mpa=1560 kg/cm2从以上压力对比可知,氮气压力只相当于普通啤机注塑压力的十分之一,甚至更少。
故在气辅注塑中,胶料保持熔融状态的时间,注塑胶料时间及胶料间有明显压力差显得非常重要,此点在后面的胶料性能中进行讨论。
气辅成型原理

气辅成型原理气辅成型原理是一种在工程设计中广泛应用的原理,它基于气体的特性,通过控制气体流动来实现对物体形状的改变。
这种原理在许多领域都有应用,比如汽车制造、航空航天、医学等。
本文将从人类视角出发,介绍气辅成型原理及其在不同领域中的应用。
气辅成型原理的基本思想是利用气体的流动来控制物体的形状。
在气辅成型过程中,首先需要设计一个特殊的模具,模具内部有许多小孔,通过这些小孔可以通过气体进行控制。
当气体通过小孔进入模具内部时,会对物体施加压力,从而改变物体的形状。
通过控制气体的流动方向和速度,可以实现对物体形状的精确控制。
气辅成型原理在汽车制造中有重要应用。
例如,在汽车车身制造中,使用气辅成型原理可以将金属板材通过气体的作用力推向模具,从而使其成型为车身的形状。
这种方法相比传统的机械成型方法更加高效和精确,能够大大提高生产效率和产品质量。
在航空航天领域,气辅成型原理也被广泛应用于飞机的制造过程中。
通过控制气体的流动,可以对飞机的复杂结构进行成型,从而满足飞机的空气动力学要求。
除了在制造领域中的应用,气辅成型原理在医学领域也有重要的应用。
例如,在手术中,医生可以使用气辅成型原理来控制手术器械的形状,从而更好地完成手术操作。
通过控制气体的流动,医生可以将手术器械变形为适合手术需求的形状,提高手术的准确性和安全性。
气辅成型原理是一种基于气体流动的控制方法。
它在汽车制造、航空航天、医学等领域中有着广泛的应用。
通过控制气体的流动方向和速度,可以实现对物体形状的精确控制。
这种原理的应用不仅提高了生产效率和产品质量,也在医学领域中起到了重要的作用。
气辅成型原理的应用为各个领域的发展带来了巨大的推动力,也为人类的生活带来了更多的便利和安全。
气辅成型制品与模具设计
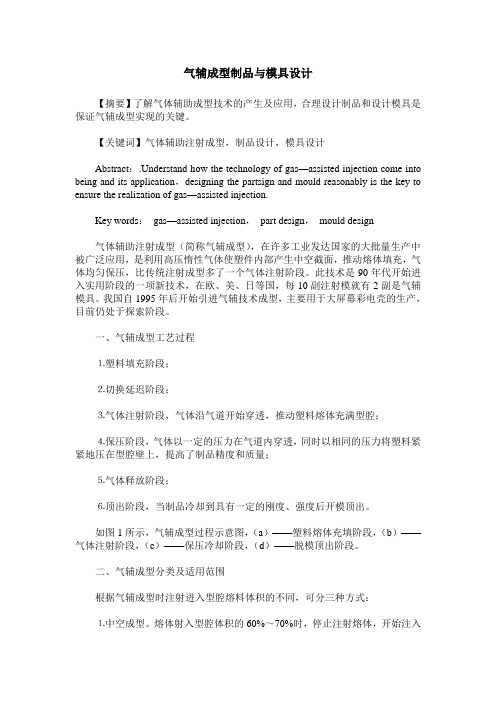
气辅成型制品与模具设计【摘要】了解气体辅助成型技术的产生及应用,合理设计制品和设计模具是保证气辅成型实现的关键。
【关键词】气体辅助注射成型,制品设计,模具设计Abstract:.Understand how the technology of gas—assisted injection come into being and its application,designing the partsign and mould reasonably is the key to ensure the realization of gas—assisted injection.Key words:gas—assisted injection,part design,mould design气体辅助注射成型(简称气辅成型),在许多工业发达国家的大批量生产中被广泛应用,是利用高压惰性气体使塑件内部产生中空截面,推动熔体填充,气体均匀保压,比传统注射成型多了一个气体注射阶段。
此技术是90年代开始进入实用阶段的一项新技术,在欧、美、日等国,每10副注射模就有2副是气辅模具。
我国自1995年后开始引进气辅技术成型,主要用于大屏幕彩电壳的生产,目前仍处于探索阶段。
一、气辅成型工艺过程⒈塑料填充阶段;⒉切换延迟阶段;⒊气体注射阶段,气体沿气道开始穿透,推动塑料熔体充满型腔;⒋保压阶段,气体以一定的压力在气道内穿透,同时以相同的压力将塑料紧紧地压在型腔壁上,提高了制品精度和质量;⒌气体释放阶段;⒍顶出阶段,当制品冷却到具有一定的刚度、强度后开模顶出。
如图1所示,气辅成型过程示意图,(a)——塑料熔体充填阶段,(b)——气体注射阶段,(c)——保压冷却阶段,(d)——脱模顶出阶段。
二、气辅成型分类及适用范围根据气辅成型时注射进入型腔熔料体积的不同,可分三种方式:⒈中空成型。
熔体射入型腔体积的60%~70%时,停止注射熔体,开始注入气体,直到保压冷却定型。
气辅成型模具
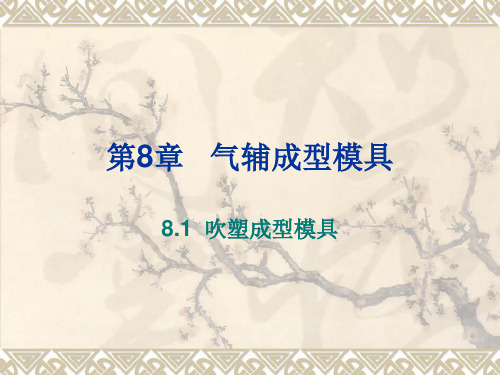
(2)无螺纹瓶颈 不采用螺纹瓶盖的一次性用瓶,多做成无螺纹的瓶 颈。瓶颈嵌件的做法与有螺纹瓶颈基本相同,不过 由于没有螺纹,分型面上的余料痕要求可以放宽。 (3)大口径瓶颈 瓶颈直径与瓶体直径之差很少。这种瓶颈需要和瓶 体同时吹成,在模具上另设吹口板。吹口板到瓶口 的一部分,在开模前被切掉。
瓶底切口设计的适当与否,直接影响到瓶底部的融合质量。 如图8-12(a)切口角度合适,瓶底缝融合良好,图8-12(b)切 口角度不合适,瓶底缝融合不够好。
图8-12 瓶底缝的融合情况
(2)注射吹塑时瓶底的成型
注射吹塑时,瓶坯是由瓶底部进料注射成的。
塑料熔体由瓶坯模的瓶底部注入,在瓶口部 成型螺纹。瓶坯模也是由两个半模合成,其 底部为注射瓶坯时的浇口。有些特殊形状的 瓶底,在做成瓶坯时已经将它预制而成。注 射吹塑的瓶底不存在切除余料问题,所以无 须做出切口。
中空零件以瓶类制品最为典型, 其规格和形状也十分繁多。所以, 本节将以瓶类制品为例,介绍吹 塑成型模具。无论采用何种吹塑 方法,所使用的模具结构均为由 两个半模组成,图8-1为吹塑模 的外观。两个半模各由三部分组 成,即:瓶颈部、瓶体部和瓶底 部,每个半模都有单独的冷却水 通路。
吹塑模具外观
1.瓶颈
吹塑模瓶颈部是与吹管配合的部位,同时又是形成不同形状 瓶颈的部位。瓶颈部的形状依设计方案而异,大致可分为有 螺纹瓶颈与无螺纹瓶颈两类。 (1)有螺纹瓶颈 用于旋上瓶盖的瓶颈。瓶盖可以是塑料的, 也可以是金属的。由于普通螺纹在两半模分开时易产生干涉 现象,损坏螺纹,所以吹塑瓶颈的螺纹设计成特殊截面形状。 塑料瓶螺纹截面形状分为两种。 ①通用螺纹 用于各种塑料瓶口,截面为梯形,螺纹有一圈、 一圈半和两圈三种; ②修正螺纹 用于瓶盖旋紧后有一定内压的瓶口,截面为斜 梯形。 (2)无螺纹瓶颈 用于一次性使用的瓶,瓶口有多种形式。
气辅成型技术

气辅成型技术在注塑业中又称气体辅助住宿和中空成型,在近10年来发展起来的革新成型技术,也可说是注塑技术的第二次革命。
目前该技术主要用于汽车、大型家电等大件注塑行业。
其主要原理是:先注入一定量的熔融塑胶(通常为90%-98%,以产品的总胶量而言)可通过分析计算+经验。
然后再在熔融塑胶内注入高压氮气,高压氮气在熔融的塑胶内沿预设的路径形成气道(最好是和流向一致当然有特殊具体情况你决定)。
使不到100%的熔融塑胶充满整个模腔,此后进入保压阶段,同时冷却,最后排气、脱模。
高压氮气进入塑料后自然会穿越粘度低(温度高)和低压的部位,并中在冷却过程中利用气体高压来保压而紧贴模具壁成型。
此项技术除需传统注塑设备外,还需所体辅助注塑控制系统(新科益有MDI控制器)。
与传统的注塑成型相比,气体辅助注塑成型有下列优点:1.减少内部的残留应力,从而减弱甚至完全消除翘曲变形状况,同时增加其机械强度和刚性。
2.成品壁厚部分的中央是中空的,可以减少原料,特别是短射和中空型的模具,塑料最多可以节约达30%。
3.减少或消除加强筋造成的表现收缩凹陷现象。
4.降低制品的收缩不均,提高制品的精密度。
5.设备耗减,大量减少锁模力,可以用小吨位的注塑机替代大吨位的注塑机。
6.利用气道来形成加强结构,提高成品的强度。
7.减少射入点。
8.缩短成期。
9.厚薄比大的制品也能通过气辅一次成型。
10。
改变传统成品设计观念,能使用一体化设计来减少附属的零组件。
缺点:1.由于所体具有压缩特征因而不容易作精确控制,加上对周围操作环境敏感,因此工艺的重复性与稳定性比传统工艺差。
2.国内技术和经验问题导致资源较浪费(废品率高)。
目前用于的产品有:汽车门把手、座椅、保险杠、门板、电视机外客、空调、冰箱、马桶........你说呢曾做过:汽车门把手、门板、雪上摩托前罩三类7款。
气体辅助注塑成型的预注塑部分与普通注塑成型一样,主要增加了一个氮气注射和回收系统。
根据注气压力产生方式的不同,目前,常用的气体注射装置有以下两种:(1)不连续压力产生法即体积控制法,如Cinpres公司的设备,它首先往汽缸中注入一定体积的气体(通常是氮气),然后采用液压装置压缩,使气体压力达到设定值时才进行注射充填。
气辅成型
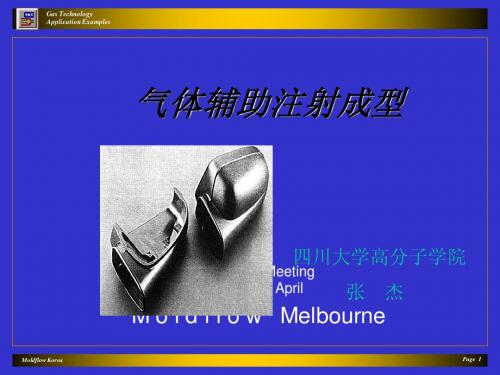
Third Stage : End of Gas Injection
Hydro-dynamic Layer Melt Polymer
至充满整个型腔,形成气道
Gas Channel
Frozen Layer
Position of gas front at end of polymer injection
穿透长度与气道形状的关系
Sha pe Fa c t or
0. 93
1. 045
1. 277
1. 2798
Pe net r a t i on
Bl ow Ra t i o
Moldflow Korea
Page 17
Gas Technology Application Examples
气体的手指现象
如果气道设计来 与聚合物熔体的 流动方向相交, 或气道与浇口太 近,可能产生手 指现象。 如果气道已定, 则提高压力来避 免手指现象
Moldflow Korea
Page 21
Gas Technology Application Examples
气体注射工艺条件要点(1)
1. 开始时可把延迟时间设为0.5 2. 通常,加气的几个阶段都可控制 3. 气体穿透应在第一或第二个阶段内完成 4. 通常,第一步需3~5sec ,第二步需4~6 sec, 共需要7 ~ 10 sec 5. 如果充模速度均衡,最好使用较低的气体压力
Fourth Stage : Gas Packing
Solidified (Frozen) polymer
Gas channel
在保压阶段,气体从内部对制 件施加保压力,补偿体积收缩 并保持零件的外部尺寸。
Position of Gas flow front at end of gas (packing) stage
气辅模具设计
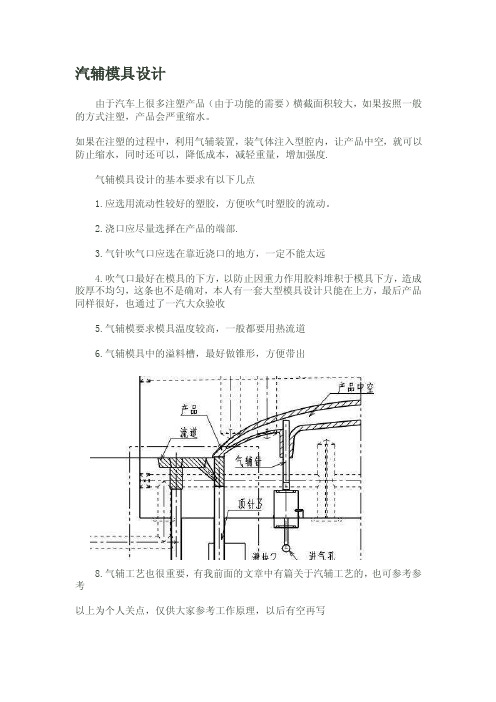
汽辅模具设计由于汽车上很多注塑产品(由于功能的需要)横截面积较大,如果按照一般的方式注塑,产品会严重缩水。
如果在注塑的过程中,利用气辅装置,装气体注入型腔内,让产品中空,就可以防止缩水,同时还可以,降低成本,减轻重量,增加强度.气辅模具设计的基本要求有以下几点1.应选用流动性较好的塑胶,方便吹气时塑胶的流动。
2.浇口应尽量选择在产品的端部.3.气针吹气口应选在靠近浇口的地方,一定不能太远4.吹气口最好在模具的下方,以防止因重力作用胶料堆积于模具下方,造成胶厚不均匀,这条也不是确对,本人有一套大型模具设计只能在上方,最后产品同样很好,也通过了一汽大众验收5.气辅模要求模具温度较高,一般都要用热流道6.气辅模具中的溢料槽,最好做锥形,方便带出8.气辅工艺也很重要,有我前面的文章中有篇关于汽辅工艺的,也可参考参考以上为个人关点,仅供大家参考工作原理,以后有空再写气辅成型工艺在气辅成型工艺调试时,需要注意以下因素:1. 对於气针式面板模具来讲,气针处压入放气时,最容易产生进气不平衡,造成调试更加困难。
其主要现象为缩水。
解决方法为放气时检查气体流畅性。
2. 胶料的温度是影响生产正常进行的关键因素之一。
气辅产品的质量对胶料温度更加敏感。
射嘴料温过高会造成产品料花、烧焦等现象;料温过低会造成冷胶、冷嘴,封堵气针等现象。
产品反映出的现象主要是缩水和料花。
解决方法为检查胶料的温度是否合理。
3. 手动状态下检查封针式射嘴回料时是否有溢料现象。
如有此现象则说明气辅封针未能将射嘴封住。
注气时,高压气体会倒流入料管。
主要现象为水口位大面积烧焦和料花,并且回料时间大幅度减少,打开封针时会有气体排出。
主要解决方法为调整封针拉杆的长短。
4. 检查气辅感应开关是否灵敏,否则会造成不必要的损失。
5. 气辅产品是靠气体保压,产品缩水时可适当减胶。
主要是降低产品内部的压力和空间,让气体更容易穿刺到胶位厚的地方来补压。
气辅成型优点1. 减少残余应力、降低翘曲问题。
气体辅助成型

氣體輔助射出成型技朮氣體輔助射出成型是在射出成型過程中將氮氣射入模穴內,並以氮氣進行保壓,因而使成品掏空減重,防止成品收縮凹陷並降低成型所需壓力,因此又稱為「氮氣中空射出成型」或「低壓中空射出成型」,簡稱氣輔。
氣體輔助成型技朮分內部成型和外部成型內部氣體輔助射出成型主要包含下列步驟:1.將定量塑料注入模具內。
2.氮氣射出:使成品掏空減重,並輔助塑料流動。
3.氮氣保壓:因塑料冷卻收縮,因此氮氣會進行二次滲透(secondary penetration),並防止成品凹陷翹曲。
4.釋放高壓氮氣:將模穴內的氮氣釋放出來。
內部氣體輔助射出成型有哪些優點?1. 對粗厚型成品:a.節省塑料,成品輕量化20~50%。
b.成型週期縮短(冷卻時間縮短)可達20%。
c.減少後加工。
2. 對平板型成品:a.設計多樣化。
b.外觀改良,電鍍效果佳。
c.消除成品厚肋骨的凹陷現象。
d.實現低壓成型、鎖模力降低。
e.成品殘留應力小、降低成品翹曲變形。
f.可用較厚的肋﹐角板等補強件﹐增加成品結構剛性﹐使產品的厚度減少。
g.減少零件數。
應用氣輔成型有無塑料的限制?氣輔成型已成功應用於各種熱塑性塑膠如PP、PE、ABS、PC/ABS、PC、PS、PVC、PPO、PBT、TPU…等塑料,但是熱固性塑膠較不適用,而高含量之填充材塑料則會有表面品質問題要使用氣體輔助射出技術需有下列設備:1.射出成型機2.氣體輔助射出裝置3.氮氣產生機或氮氣瓶4.空氣壓縮機5.必要的成型週邊設備氣體輔助射出成型所牽涉的技術包括模具設計、成品設計、氣針位置的分析設計、氣輔裝置本身的技術、射出成型技術、成型不良的排除、模流分析技術等。
模具設計時需注意﹕氣道盡可能循二或多面交匯處或粗厚處行﹐主氣道以一氣呵成(一氣道)為原則﹔避免閉路式氣道﹔避免氣道相臨太近﹔准確的熔膠射入量非常必要﹔均勻的冷卻非常必要﹔延伸氣道至最后充填處﹐最后充填處應處在非外觀面上﹔當氣道分支時﹐支氣道末端可以階梯式縮小﹐以防氣體加速﹔氣道太小可能引起滲透﹐太大可能引起融合線或氣陷。
气辅成型
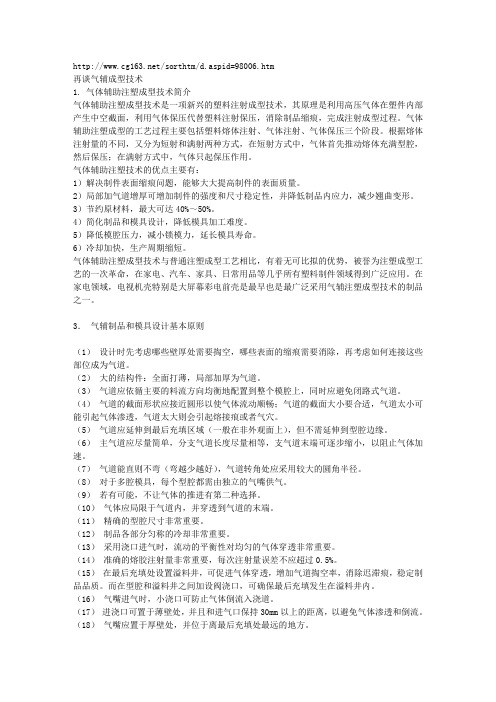
/sorthtm/d.aspid=98006.htm再谈气辅成型技术1. 气体辅助注塑成型技术简介气体辅助注塑成型技术是一项新兴的塑料注射成型技术,其原理是利用高压气体在塑件内部产生中空截面,利用气体保压代替塑料注射保压,消除制品缩痕,完成注射成型过程。
气体辅助注塑成型的工艺过程主要包括塑料熔体注射、气体注射、气体保压三个阶段。
根据熔体注射量的不同,又分为短射和满射两种方式,在短射方式中,气体首先推动熔体充满型腔,然后保压;在满射方式中,气体只起保压作用。
气体辅助注塑技术的优点主要有:1)解决制件表面缩痕问题,能够大大提高制件的表面质量。
2)局部加气道增厚可增加制件的强度和尺寸稳定性,并降低制品内应力,减少翘曲变形。
3)节约原材料,最大可达40%~50%。
4)简化制品和模具设计,降低模具加工难度。
5)降低模腔压力,减小锁模力,延长模具寿命。
6)冷却加快,生产周期缩短。
气体辅助注塑成型技术与普通注塑成型工艺相比,有着无可比拟的优势,被誉为注塑成型工艺的一次革命,在家电、汽车、家具、日常用品等几乎所有塑料制件领域得到广泛应用。
在家电领域,电视机壳特别是大屏幕彩电前壳是最早也是最广泛采用气辅注塑成型技术的制品之一。
3.气辅制品和模具设计基本原则(1)设计时先考虑哪些壁厚处需要掏空,哪些表面的缩痕需要消除,再考虑如何连接这些部位成为气道。
(2)大的结构件:全面打薄,局部加厚为气道。
(3)气道应依循主要的料流方向均衡地配置到整个模腔上,同时应避免闭路式气道。
(4)气道的截面形状应接近圆形以使气体流动顺畅;气道的截面大小要合适,气道太小可能引起气体渗透,气道太大则会引起熔接痕或者气穴。
(5)气道应延伸到最后充填区域(一般在非外观面上),但不需延伸到型腔边缘。
(6)主气道应尽量简单,分支气道长度尽量相等,支气道末端可逐步缩小,以阻止气体加速。
(7)气道能直则不弯(弯越少越好),气道转角处应采用较大的圆角半径。
模具设计第8章--其它塑料成型方法与模具设计简介

1. 凹模成型 凹模成型是简单而常用的热成型方法。其共分6步
来完成。如图8-9所示。
2. 凸模成型 凸模成型和凹模成型的步骤几乎完全一样,但也有
它的特点。
3.对模成型 对模成型的特点是:它不再需要别的成型力,如真
空或压缩空气,并可使塑件两面都有花纹。
23
4. 辅助模塞成型 这种成型法可看成是上述三种基本成型的总和
9
1. 棒类塑件 气辅成型技术在棒状塑件的成型中显示出明
显的优势。在进行棒状塑件气道的设计时应考虑 以下几方面: (1)塑件截面最好接近圆形。因为气体在气道中穿 透形成的中空部分截面趋向于圆形,这样塑件接 近圆形可避免因熔体的不均匀分布而造成壁厚不 均匀。 塑件设计应遵守以下原则: 1)外形尽量接近圆形; 2)避免尖角,采用大的圆角过渡; 3)避免熔体在角部产生堆积; 4)保证整个塑件壁厚均匀(见图8-2)
15
4. 气道长度的确定
气道长度的确定应依照下列步骤进行: (1)气道布置,预先给出气道设计长度; (2)根据材料p-v-T关系曲线图先查出材料的
体积收缩率; (3)计算体积收缩率; (4)计算塑件的体积收缩,并用此近似估算
所需注射气体的体积;
16
(5)根据塑件平均壁厚估算塑件气道截面尺寸 和气孔的平均直径;
气辅注射装置是单独于注射机之外的一套装 置,一般由以下具有生成惰性气体、提纯、加压、 时间控制、过滤等功能的设备组成:
(1)空气压缩机,将空气压缩为具有0.4~0.6MPa的 压缩空气;
(2)氮气发生器,将压缩后的空气用分离法提取 空气中的氮气,纯度达到98%以上,防止气体注 射过程中因含有氧气而产生爆炸;
(如注射开始时间、冷却时间、开模时间等),
- 1、下载文档前请自行甄别文档内容的完整性,平台不提供额外的编辑、内容补充、找答案等附加服务。
- 2、"仅部分预览"的文档,不可在线预览部分如存在完整性等问题,可反馈申请退款(可完整预览的文档不适用该条件!)。
- 3、如文档侵犯您的权益,请联系客服反馈,我们会尽快为您处理(人工客服工作时间:9:00-18:30)。
(2)无螺纹瓶颈 不采用螺纹瓶盖的一次性用瓶,多做成无螺纹的瓶 颈。瓶颈嵌件的做法与有螺纹瓶颈基本相同,不过 由于没有螺纹,分型面上的余料痕要求可以放宽。 (3)大口径瓶颈 瓶颈直径与瓶体直径之差很少。这种瓶颈需要和瓶 体同时吹成,在模具上另设吹口板。吹口板到瓶口 的一部分,在开模前被切掉。
(3)型腔表面 塑料瓶一般有比较高的外观要求。其表面大致有光 泽表面、不反光表面和花纹表面等几种。 (4)冷却系统 吹塑模的冷却效果直接影响到瓶子的表面质量, 所以冷却系统的设计在吹塑中很重要。如果冷却不 均匀,吹出的成品表面光泽便有明显的差异。
常用的冷却水通道的形式有以下几种。 ①循环水路的方式(如图8-6)
(4)自灌注密封瓶颈 这种特殊瓶子是用来装某些药品用的(如杀虫剂等),在吹塑 成型后,即由吹管中的注入管把液体灌入瓶内,然后在瓶颈 部加温并挤压,使它完全密封起来。图8-10瓶颈板结构的两 种形式。
图8-10 瓶口的校正与切断
3.瓶底部的设计
入式瓶底模
瓶底部的形状依瓶的用途及灌装方法的 不同而异,大致有:浅凹人式瓶底、深 凹入式瓶底、有止转沟的瓶底。 挤出吹塑瓶底成型方法与注射吹塑瓶 底成型方法不同。 (1)挤出吹塑时瓶底的成型 挤出吹塑的瓶坯为管形,在吹胀前要将 管形瓶坯夹在两个半模之间。底部的成 型是先由瓶底的切口处剪断。瓶底切口 由两个半模各构成其一半。可以用两块 整瓶底板做成,也可以用嵌件。在产量 大时,以用嵌件为好,便于更换,如图 8-11所示。
图8-6 循环水路方式 1-水堵 2-阻挡件 3-模体
4-螺旋板
②铸造水路方式(如图8-7)
图8-7 铸造水路
③喷淋冷却方式(如图8-8)
图8-8 喷淋冷却方式
2.瓶颈部的设计
瓶颈部是吹塑模的入料和送气吹胀的部位。其类型大致可分 为:有螺纹瓶颈、无螺纹瓶颈、大口径瓶颈、自灌注密封瓶 颈四类。 (1)有螺纹瓶颈 吹塑瓶螺纹的成型有两种方法。一是实体螺纹,螺纹截面全 部由塑料实体做成,可以用挤出吹塑或注射吹塑成型,制造 螺纹阴模时须注意螺纹的起始端和终止端必须设在半模的中 央。为了使螺纹能正确连续,两个半模上的瓶颈嵌件必须同 时加工。二是薄膜螺纹,一般用于螺距较大,螺纹截面大的 瓶,在不需要密封的条件下,可以吹成螺纹,这种螺纹很少 采用。 Nhomakorabea
吹塑模瓶颈部是与吹管配合的部位,同时又是形成不同形状 瓶颈的部位。瓶颈部的形状依设计方案而异,大致可分为有 螺纹瓶颈与无螺纹瓶颈两类。 (1)有螺纹瓶颈 用于旋上瓶盖的瓶颈。瓶盖可以是塑料的, 也可以是金属的。由于普通螺纹在两半模分开时易产生干涉 现象,损坏螺纹,所以吹塑瓶颈的螺纹设计成特殊截面形状。 塑料瓶螺纹截面形状分为两种。 ①通用螺纹 用于各种塑料瓶口,截面为梯形,螺纹有一圈、 一圈半和两圈三种; ②修正螺纹 用于瓶盖旋紧后有一定内压的瓶口,截面为斜 梯形。 (2)无螺纹瓶颈 用于一次性使用的瓶,瓶口有多种形式。
2.瓶底
塑料瓶的瓶底均为凹入式,目的是为了能在平面上直立放置, 如图8-2所示。也是为了自动灌装液体,在瓶底上做出止转 槽的形式。
图8-2 瓶底的形式
3.瓶体
图8-3 吹塑模具(压入式) 1-模口嵌件 2-模体 3-排气槽 4-导销 5-模底嵌件 6-堵头
瓶体部分为瓶的造型主要部 位,依用途不同而设计成各 种形状。但无论截面为何种 形状,必须能顺利脱模。因 为瓶体是制品中最薄的部分, 如略有阻碍,则制品脱模后 必然变形而成为废品。 吹塑模的典型结构如图8-3和 图8-4所示。图8-3为用压入 法嵌入瓶颈和瓶底嵌件的典 型结构;图8-4为用螺钉固定 法嵌入瓶颈和瓶底嵌件的典 型结构。
瓶底切口设计的适当与否,直接影响到瓶底部的融合质量。 如图8-12(a)切口角度合适,瓶底缝融合良好,图8-12(b)切 口角度不合适,瓶底缝融合不够好。
图8-12 瓶底缝的融合情况
(2)注射吹塑时瓶底的成型
注射吹塑时,瓶坯是由瓶底部进料注射成的。
塑料熔体由瓶坯模的瓶底部注入,在瓶口部 成型螺纹。瓶坯模也是由两个半模合成,其 底部为注射瓶坯时的浇口。有些特殊形状的 瓶底,在做成瓶坯时已经将它预制而成。注 射吹塑的瓶底不存在切除余料问题,所以无 须做出切口。
中空零件以瓶类制品最为典型, 其规格和形状也十分繁多。所以, 本节将以瓶类制品为例,介绍吹 塑成型模具。无论采用何种吹塑 方法,所使用的模具结构均为由 两个半模组成,图8-1为吹塑模 的外观。两个半模各由三部分组 成,即:瓶颈部、瓶体部和瓶底 部,每个半模都有单独的冷却水 通路。
吹塑模具外观
1.瓶颈
图8-4 吹塑模具(螺钉固定式) 1,2-模口嵌件 3-导销 4-排气槽 5-模体 6-盖板 7-冷却水路 8,9-模底嵌件
8.2.3 吹塑模具的设计
1.瓶体部的设计 (1)分型面 一般常见的瓶体截面形状如图8-5。
图8-5 瓶体截面几何形状与分型
(2)排气槽和排气孔 瓶体部分在闭模时有大量空气,在吹胀时应尽快地把空气 排出,以使瓶体能完整地成型,紧贴于模腔壁上。如果某一 局部有空气滞留,外形即不完整而成为废品。 最有效的排气法是在分型面上设排气槽,而瓶颈的肩部及瓶 底的转角处为容易滞留空气的死角,应设漏斗形排气孔,所 有突出部位以及截面突然改变处也应设排气孔。排气槽槽深 小于O.1mm,一般用平面磨床精磨而成,槽宽10~25mm, 依模具大小而定。每一副模具在分型面上的槽数也依型腔的 容积而定,在型腔的两边各开三条以上的排气槽。排气孔的 形式依具体情况而异排气孔径为0.6~1.2mm,深25~ 35mm。
1.型腔真空成型 如图8-14所示,板材被固定在型腔上方,为了防止空气从板 材外面进入到型腔中间,在板材固定处要安放密封圈。
图8-14 型腔真空成型
2.型芯真空成型 型芯真空成型如图8-15所示,图(a)所示为被夹紧的塑料 板材在加热器下软化;图(b)所示为板材加热后随框架一 起下降(或型芯上升)并使板材包在型芯上的情况;图(c)所 示为抽真空后塑料板材覆盖在型芯上成型时的情况。
真空成型模具在强度上不受大的外力,所以可以采用容易加 工的材料。 (1)木材 (2)硬石膏 (3)陶瓷烧结物 (4)环氧树脂 (5)铝合金 (6)低碳钢
8.2.3 真空吸塑模的主要部件设计
1.凹模 绝大多数吸塑都是用凹模成型的。现代的吸塑机工作面积 可达700mm×1000mm,可以一次成型几十个同样的塑件。 凹模是由多个单腔模排列组合成的。为了保证各个凹模之间 的相对位置精度(因为在下一步切边时必须尺寸准确),其外 形尺寸精度及形位精度要求较高,同时高度的偏差也必须很 小。用石膏或木材制造时往往达不到要求。 凹模的表面是成型塑件外形的,用于成型聚氯乙烯片材时, 表面粗糙度应不大于Ra0.8μm。而用于聚苯乙烯片材时,表 面粗糙度应不小于Ra0.8μm,最好用喷砂处理。因为聚苯乙 烯容易粘附在凹模表面不易脱出。 凹模上的气孔直径依所加工的材料而异,用于聚氯乙烯吸 塑成型时,直径取1.2mm,而用于其他材料时,为了避免在 塑件上留下吸气孔痕迹,以0.8mm以下为宜。孔的位置,一 般设在凹模底部、突出部、凹陷部;孔的数目不宜过多,发 现吸胀不足时,可以再增加。
图8-15 型芯真空成型
3.采用凹、凸模先后抽真空成型 采用凹、凸模先后抽真空成型如图8-16所示。
图8-16 采用凹、凸模先后抽真空成型
8.2.2 真空成型模具设计要点
1.模具的结构设计 (1)型腔尺寸 真空成型型腔尺寸的计算方法与注射模相同, 但不必像注射模那样精确。真空成型塑件的收缩量,大约有 50%是塑件从模具中取出时产生的,25%是取出后保持在室 温下1h内产生的,其余25%是在以后8~24h内产生的。一 般来说,在型腔上成型的塑件比型芯上成型的塑件收缩量大 25%~50%,这是因为在型腔上成型的塑件在取出前就产生 了收缩,而在型芯上成型的塑件取出以前无法产生收缩。 影响塑件尺寸变化的因素很多,如成型温度、模具温度、 冷却时间等。
(5)边缘密封结构 为使型腔外面的空气不进入真空 室,在塑料板材与模具接触的边缘处应设置密封装 置。 (6)加热冷却装置 对于板材的加热通常采用电阻丝 和红外线。电阻丝温度较高,通常采用调节加热器 和塑料板材之间距离的方法来控制成型温度。在生 产中一般由试验确定其具体值。
2.模具材料
(2)型腔表面粗糙度 一般真空成型模具都没有推出 装置,依靠压缩空气脱模。如果表面粗糙度值太大, 塑料会粘附在型腔表面上不易脱模。因此,型腔表 面粗糙度值不能太大,一般取Ra=1.6μm。真空成 型的成型表面最好用磨料打毛或进行喷砂处理,因 为在成型时型腔表面可以储存一部分空气从而避免 真空吸附现象。 (3)脱模斜度 真空成型的凹凸模都应该有一定斜 度,型腔的脱模斜度约为0.5°~1.0°;型芯的斜 度一般为2°~3°,同时模具的圆角半径应大于或 等于板料厚度值以避免弯角处应力集中。
图8-9 螺纹切口
成型螺纹时,由于瓶坯直径大 于瓶口直径,所以在两个半模 合模后要夹住瓶坯而把无用的 多余料切断。这就要求螺纹阴 模具有能切断余断的作用,称 为切口。切口的截面形状如图 8-9所示。切口有一段平面b, 其后做成能容纳余料的空间, 空间与切口的连接处成角θ。 为了使螺纹的分型面上少留余 料,b的尺寸应尽量小,根据 瓶颈直径的大小,可以做成 b=0.08~O.12mm,θ角为20°。
图8-18 同时切边的吸塑模
8.3 压缩空气成型模具
8.3.1 成型工艺及其特点 塑件成型过程是将塑料板材置于加热板和凹模之间,固定加 热板,如图8-19a所示;这时,塑料板材只被轻轻地压在模 具刃口上,然后,在加热板抽出空气的同时,从位于型腔底 部的空气口向型腔中送入空气,使被加工板材紧贴加热板, 如图8-19b所示;这样塑料板很快被软化,达到适合于成形 的温度。这时加强从加热板送出的空气,使塑料板材逐渐贴 紧模具。与此同时,型腔内的空气通过其底部的通气孔迅速 排出,最后使塑料板紧贴模具,如图8-19c所示;待板材冷 却后,停止从加热板喷出压缩空气,再使加热板下降,对塑 件进行切边,如图8-19d所示;在加热板回升的同时,从型 腔底部送人空气使塑件脱模后,取出塑件,如图8-19e所示。