塑胶模具设计指引
塑料模具课程设计指导书

塑料模具课程设计指导书(一)塑料模具课程设计的目的塑料模具课程设计是《塑料成型工艺与模具设计》课程中的最后一个实践性教学环节,也是一次对学生进行比较全面的塑料模具设计的训练,其目的是:(1)通过模具课程设计,要求学生综合应用《塑料成型工艺与模具设计》及其他相关课程的基本知识来解决工程实际中的具体设计问题,以进一步巩固和深化所学课程的知识。
(2)通过模具课程设计,学生进行了一次较为完整的塑料模具设计的实际训练,使学生初步掌握塑料模具设计的内容、步骤和基本方法,进一步提高学生的结构设计能力和独立工作能力,为毕业设计和今后从事模具设计与制造工作奠定基础。
(3)通过模具课程设计,提高学生查阅技术资料和手册的能力,熟悉并正确应用有关的技术标准。
(4)通过模具课程设计,培养学生认真负责、踏实细致的工作作风和严谨的科学态度,强化学生的质量意识和时间观念,使学生初步形成从业的基本素职。
(二)课程设计的任务塑料模具课程设计的题目,一般选择中等复杂程度的塑料注射模进行设计,要求学生在规定的时间内完成如下任务:(1)绘制塑料制件图一张(A4)(用计算机绘图)(2)绘制塑料注射模装配图一张(A1)(手工绘图)(3)绘制模具零件工作图2~3张(用计算机绘图)(4)编写设计说明书一份(三)塑料注射模具设计步骤1.塑件成型工艺分析(1)塑件成型特性的分析根据塑件图中标明的塑料品种,分析该塑料的使用性能及成型性能;查阅该塑料的比重、比容、收缩率及流动性等特性。
(2)塑件的结构工艺性分析认真阅读塑件图,审核塑件的几何形状、尺寸公差等级、表面粗糙度、塑件壁厚及其他技术要求,必要时还需阅读该塑件所属的部件图(或组件图)和了解该塑件的使用条件、使用寿命、载荷特性及其数值等。
据此分析塑料注射成型工艺的可行性和经济性。
(3)明确生产批量小批量生产时,为了降低成本,模具尽可能简单,通常采用单型腔;大批量生产时,应在保证塑件质量的前提下,尽量采用一模多腔或高速自动化生产,以缩短生产周期,提高生产率,因此对模具的推出机构、合模导向机构、塑件和浇注系统凝料的脱模以及凸、凹模的结构提出了严格的要求。
实用详细!塑胶模具设计思路与流程,建议收藏!

实用详细!塑胶模具设计思路与流程,建议收藏!一套可靠的模具设计,主要体现在所成型的塑料制品的质量(外观质量和尺寸稳定性),加工制造时方便、迅速、简练,既又省资金、人力,留有更正、改良余地、使用时安全、稳定、便于维修、在注射成型时有较短的成型周期和较长使用寿命以及具有合理的模具制造工艺性等方面。
1.工厂模具设计主要流程客户提供产品图→分析产品→确认塑料品种→确认模具材质→转工程图→乘缩水作镜相→完善组立图→订模胚→订模仁料→拔模→3D 分模→确定流道/浇口方式→参照排位图进行结构设计→拆镶件→更正3D→工程出图包括:(模仁/镶件/模胚/散件)→做 BOM 表→校对审核。
2.在设计应注意的几个方面1.我们在开始模具设计时,应多注意考虑几种方案,衡量每种方案优缺点,从中优选一种,对于T模,亦认真对待。
因为时间认识上的原因,当时认为合理的设计,经过生产使用实践也一定会有可能可以改进的地方。
2.在交出设计方案后,要与工厂多沟通,了解加工过程及制造使用中的情况。
每套模都应有一个固定分析经验,总结得失的过程,才能不断提高模具设计水平。
3.设计时多参考过去所设计的类似图纸,吸取其经验与教训。
4.模具设计部门理应是一个整体,不能每个设计成员各自为政,特别是模具设计总结结论方面,一定要有独特的的风格。
3.模具设计依据主要依据,就是客户所提供给我们的产品图纸及样板。
设计人员必须对产品及样板进行认真详细的分析与消化,同时在设计过程中,必须逐一核查一下所有项目。
•尺寸精度相关尺寸的正确性。
(1).外观要求高,尺寸精度要求低的熟料制品,如玩具等,具体尺寸除转配外,其余尺寸只要吻合较好即可。
(2).围观尺寸要求都很严的制品。
•脱模斜度是否合理。
•制品壁厚及均匀性。
•塑料种类。
(塑料种类想盗模具钢材的选择与确定缩水率)•表面要求。
•制品颜色。
一般情况,颜色对模具设计无直接影响。
当制品壁厚,外型较大时,易产生颜色不均匀;且颜色越深,制品缺陷暴露得越明显。
塑胶模具设计指引
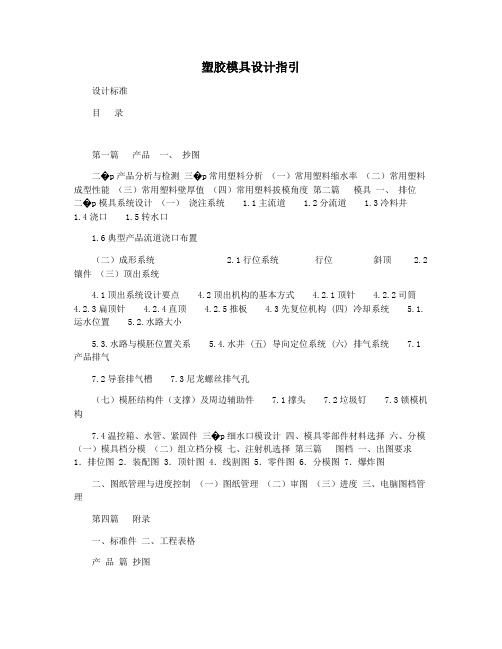
塑胶模具设计指引设计标准目录第一篇产品一、抄图二�p产品分析与检测三�p常用塑料分析(一)常用塑料缩水率(二)常用塑料成型性能(三)常用塑料壁厚值(四)常用塑料拔模角度第二篇模具一、排位二�p模具系统设计(一)浇注系统 1.1主流道 1.2分流道 1.3冷料井1.4浇口 1.5转水口1.6典型产品流道浇口布置(二)成形系统 2.1行位系统行位斜顶 2.2镶件(三)顶出系统4.1顶出系统设计要点 4.2顶出机构的基本方式 4.2.1顶针 4.2.2司筒4.2.3扁顶针 4.2.4直顶 4.2.5推板 4.3先复位机构 (四) 冷却系统5.1.运水位置 5.2.水路大小5.3.水路与模胚位置关系 5.4.水井 (五) 导向定位系统 (六) 排气系统 7.1产品排气7.2导套排气槽 7.3尼龙螺丝排气孔(七)模胚结构件(支撑)及周边辅助件 7.1撑头 7.2垃圾钉 7.3锁模机构7.4温控箱、水管、紧固件三�p细水口模设计四、模具零部件材料选择六、分模(一)模具档分模(二)组立档分模七、注射机选择第三篇图档一、出图要求1.排位图 2.装配图 3.顶针图 4.线割图 5.零件图 6.分模图 7.爆炸图二、图纸管理与进度控制(一)图纸管理(二)审图(三)进度三、电脑图档管理第四篇附录一、标准件二、工程表格产品篇抄图一.抄图前,先要看懂,看透产品线图,然后班顺思路,特别是外形面的画法。
抄好产品图要转为2D线图与设计部提供的平面线图套。
要保证主要的视图和边界线完全重合一致。
若有不重合、不一致的情况,首先分析是2D线图本身表达有问题,还是抄图时造成的。
若为2D线图表达问题则应及时标明,并与设计部沟通、反映;若为抄图问题,及时修改。
二.一个产品通常要多次转图与标题栏对上几次逐步确认(看版本),避免最后的问题堆积。
三.在抄图的整个过程中,最为重要的是基体外形面的控制和核对。
四.抄好的UG尽可能保证可以再生,以实现UG的参数设计功能。
塑胶模具结构设计

塑胶模具结构设计塑胶模具结构设计是制造业中至关重要的环节,它直接关系到产品的质量、生产效率和成本。
本文将围绕塑胶模具结构设计的基本原则、设计流程及注意事项进行详细阐述。
一、塑胶模具结构设计的基本原则1. 确保产品精度在设计塑胶模具时,要保证产品的尺寸精度和形状精度。
这要求设计师充分了解塑胶材料的收缩率、流动性等特性,并在模具设计中予以充分考虑。
2. 易于加工与装配模具结构应尽量简单,便于加工和装配。
复杂的设计不仅会增加制造成本,还可能影响模具的可靠性。
在设计过程中,要充分考虑模具零件的加工工艺性和装配顺序。
3. 高效生产塑胶模具结构设计应考虑生产效率,尽量减少生产过程中的辅助时间。
例如,通过优化流道设计、缩短冷却时间等措施,提高生产效率。
4. 安全可靠5. 维护方便模具在使用过程中难免会出现磨损、损坏等问题,设计时应考虑模具的维修便捷性,降低维护成本。
二、塑胶模具结构设计流程1. 分析产品结构在设计模具前,要对产品结构进行分析,了解产品的尺寸、形状、技术要求等,为模具设计提供依据。
2. 确定模具类型根据产品结构特点和生产要求,选择合适的模具类型,如单腔模具、多腔模具、热流道模具等。
3. 设计分型面分型面是模具闭合时,分离塑胶制品和浇注系统的界面。
设计分型面时要考虑产品的脱模斜度、外观质量等因素。
4. 设计浇注系统浇注系统包括主流道、分流道、浇口等部分,其设计直接影响到塑胶制品的质量。
设计时应关注流道截面积、长度、浇口位置等因素。
5. 设计冷却系统冷却系统对塑胶制品的质量和生产效率具有重要影响。
设计时要考虑冷却水路的布局、冷却水流量、冷却水温度等因素。
6. 设计顶出系统顶出系统的作用是在模具开模时,将制品从模具中顺利取出。
设计时要确保顶出力均匀、可靠,避免产品变形或损坏。
7. 绘制模具零件图及装配图三、塑胶模具结构设计注意事项1. 充分考虑塑胶材料的特性,如收缩率、流动性、热稳定性等。
2. 优化模具结构,提高生产效率,降低生产成本。
塑胶模具开发设计的最常见方法及工艺三篇
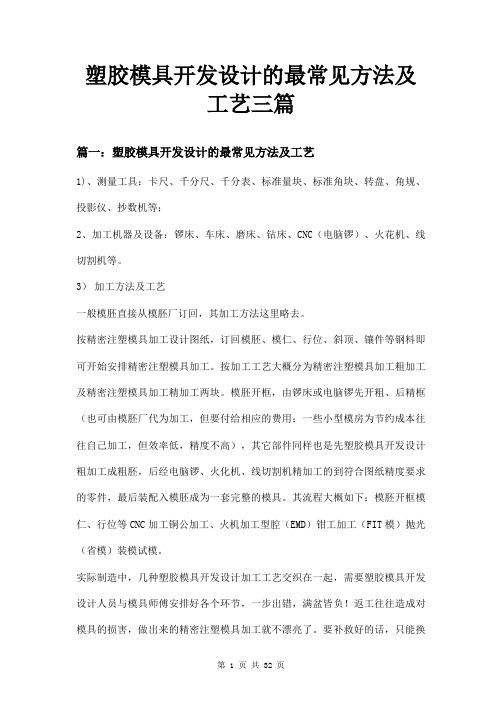
塑胶模具开发设计的最常见方法及工艺三篇篇一:塑胶模具开发设计的最常见方法及工艺1)、测量工具:卡尺、千分尺、千分表、标准量块、标准角块、转盘、角规、投影仪、抄数机等;2、加工机器及设备:锣床、车床、磨床、钻床、CNC(电脑锣)、火花机、线切割机等。
3)加工方法及工艺一般模胚直接从模胚厂订回,其加工方法这里略去。
按精密注塑模具加工设计图纸,订回模胚、模仁、行位、斜顶、镶件等钢料即可开始安排精密注塑模具加工。
按加工工艺大概分为精密注塑模具加工粗加工及精密注塑模具加工精加工两块。
模胚开框,由锣床或电脑锣先开粗、后精框(也可由模胚厂代为加工,但要付给相应的费用;一些小型模房为节约成本往往自己加工,但效率低,精度不高),其它部件同样也是先塑胶模具开发设计粗加工成粗胚,后经电脑锣、火化机、线切割机精加工的到符合图纸精度要求的零件,最后装配入模胚成为一套完整的模具。
其流程大概如下:模胚开框模仁、行位等CNC加工铜公加工、火机加工型腔(EMD)钳工加工(FIT模)抛光(省模)装模试模。
实际制造中,几种塑胶模具开发设计加工工艺交织在一起,需要塑胶模具开发设计人员与模具师傅安排好各个环节,一步出错,满盆皆负!返工往往造成对模具的损害,做出来的精密注塑模具加工就不漂亮了。
要补救好的话,只能换料,这将增加时间和成本,而很多时候时间是最重要的。
现在精密注塑模具加工行业竞争很激烈,客户给模房的时间都很急,不能按时交模,最终将失去客户!各加工机械设备的功能简介:1、锣床,用于人工铣、切较形状较简单、规则的工件,如直线、斜线;常用来加工精度不是很高的工件,模胚开框、模仁、行位开料等。
2、车床,主要用于圆形的工件加工,如唧嘴、定位环、法兰、圆形模呵(CORE)、圆形铜公等;精度可达较高的要求。
3、磨床,主要用于钢料磨平,磨基准等,可满足大部精度要求。
4、钻床,主要用于钻空、攻牙、打运水孔等。
众多XX模具厂都将参与这个展会塑胶模具加工行业的机会,注塑加工厂讲的是诚信,和品质,喷油厂及时交货,不偏色,无色差,平板电脑模具专业制造厂家,精密度高,自动喷涂等等服务。
塑胶模具设计手册
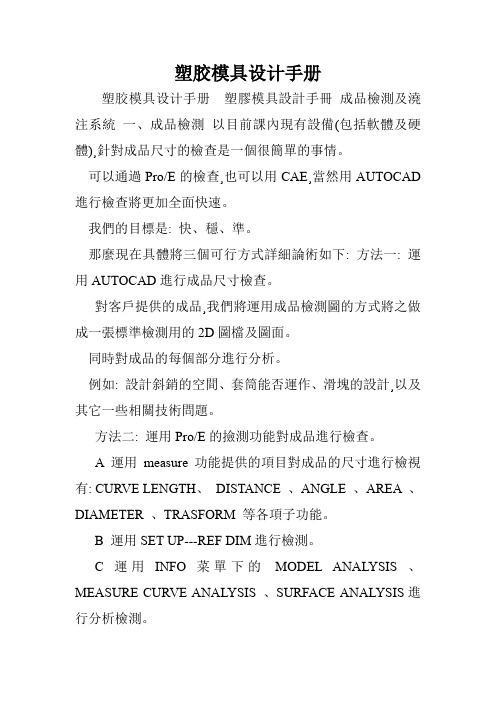
塑胶模具设计手册塑胶模具设计手册塑膠模具設計手冊成品檢測及澆注系統一、成品檢測以目前課內現有設備(包括軟體及硬體)¸針對成品尺寸的檢查是一個很簡單的事情。
可以通過Pro/E的檢查¸也可以用CAE¸當然用AUTOCAD 進行檢查將更加全面快速。
我們的目標是: 快、穩、準。
那麼現在具體將三個可行方式詳細論術如下: 方法一: 運用AUTOCAD進行成品尺寸檢查。
對客戶提供的成品¸我們將運用成品檢測圖的方式將之做成一張標準檢測用的2D圖檔及圖面。
同時對成品的每個部分進行分析。
例如: 設計斜銷的空間、套筒能否運作、滑塊的設計¸以及其它一些相關技術問題。
方法二: 運用Pro/E的撿測功能對成品進行檢查。
A運用measure功能提供的項目對成品的尺寸進行檢視有: CURVE LENGTH、DISTANCE 、ANGLE 、AREA 、DIAMETER 、TRASFORM 等各項子功能。
B 運用SET UP---REF DIM進行檢測。
C 運用INFO菜單下的MODEL ANALYSIS 、MEASURE CURVE ANALYSIS 、SURFACE ANALYSIS進行分析檢測。
方法三:運用CAE功能對成品進行檢測。
二、重量材質部分: 我們知道運用Pro/E的工程計算的功能可以很清楚地計算出成品的體積、重量。
我們運用CAE提供的資料庫將常用塑膠材料的特性進行匯編¸利用方便的塑膠特性選擇注塑成型機的大小。
三、投影面積的大小: 投影面積的大小也可以通過Pro/E 計算¸當然CAE的計算也是可以完成的。
只不過是CAE中投影面積的計算費時太長。
這不是方法上的問題¸而是技巧性的問題。
四、模流分析的結果。
塑膠材料的特性及進膠方式。
一些常見的高份子材料列如下表: 結晶性非結晶性PP 聚丙烯PS(ATACTIC)聚苯乙烯HDPE高密度聚乙烯PV AC 聚酯酸乙烯LDPE低高密度聚乙烯PMMA聚甲基丙烯酸甲酯PA(NYLON) EV A乙烯--醋酸乙烯共聚合物POM聚縮醛A V PTFE EV PEO CHLORINATED PE氯化聚乙烯PETP(PET)聚對苯二甲二乙酯ABS HIPS PPO 賽璐璐(cellulose)纖維素塑膠PC 聚碳酸酯PBT 聚對丁烯二甲二乙酯對一些常見的¸我們公司及客戶們經常使用的塑膠特性做一些簡單的介紹: 一、PC塑料(POLYCARBONATE): PC 兼具有耐熱性、耐沖擊性和透明性。
塑料模具设计指导书-

塑料模具设计指导书一、设计内容1、对塑件进行综合分析2、估算单个制品的体积及重量。
3、选择设备的类型和规格4、选择成型方案,确定模具的成型结构5、主要零部件的设计计算6、其他零部件的设计计算及选用7、绘制模具结构设计装配工作图8、绘制成型凸、凹模等零件的工作图9、编写设计说明书二、设计的要求及方法(一工艺分析,阅读塑件图纸,明确塑件的设计要求。
1了解塑件所采用的材料的流动性能、收缩率、透明度、吸水性能、对应力的敏感性、成型条件、成型特性等性能特点,从而对塑件的尺寸及精度、表面粗糙度、塑件的形状设计、塑料的物理力学性能、壁厚、有利于充模流动性、有利于排气补缩等成型工艺性能进行分析。
2了解塑件的用途,使用情况及工作要求,对于塑件图提出的塑件形状、尺寸精度,加工粗糙度等进行工艺分析,即从成型工艺,塑件的设计原则,模具的结构合理性等方面进行综合分析。
特别注意:要做到模具的结构简化、使模具制造工艺尽量简单,生产成本经济合理。
(二选择设备的类型及规格根据材料的密度、形状尺寸估算塑件的体积和重量,确定注射量,从而确定设备的类型及规格。
最后应校验所选注射机的能力(注射量、注射压力、锁模力、模具最大高度、最小高度、开模行程、模板间距、顶出位置等(三模具的结构设计1、型腔分型面的设计:注射模的分型面位置有垂直于、平行于以及倾斜于开模方向几种,分型面的形状有平面和曲面等。
分型面是否得当,对塑件的质量、操作难易、模具制造都有很大的影响。
1分型面的选取应考虑:塑件在型腔中的方位。
一般只采取一个与注射机开模运动相垂直的分型面(当然还有点浇口式的双分型面,尽量避免与开模运动相垂直的方向有侧凹或侧孔,否则应增加分型面。
2分型面的位置:一般分型面应开设在塑件断面轮廓最大的地方外,还应考虑分型面的开设不影响塑件的外观质量、塑件要留在动模一边、考虑要求同心的部分应放在同一侧、考虑抽芯机构的行程、有力于排气以及容易出模和容易加工等因素。
塑胶模具结构设计要点
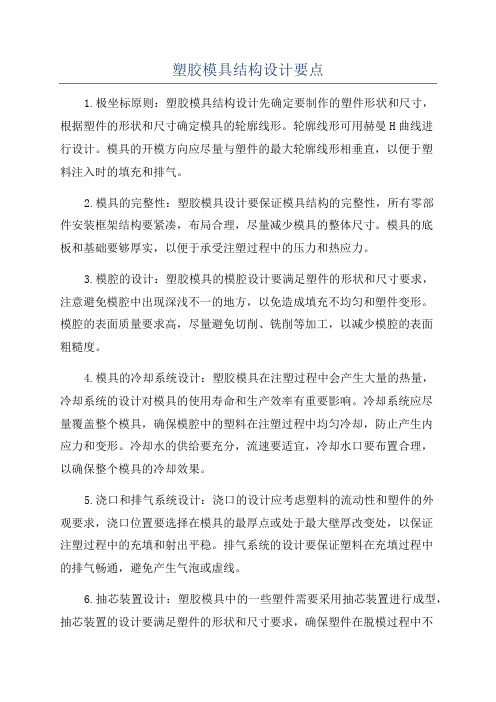
塑胶模具结构设计要点1.极坐标原则:塑胶模具结构设计先确定要制作的塑件形状和尺寸,根据塑件的形状和尺寸确定模具的轮廓线形。
轮廓线形可用赫曼H曲线进行设计。
模具的开模方向应尽量与塑件的最大轮廓线形相垂直,以便于塑料注入时的填充和排气。
2.模具的完整性:塑胶模具设计要保证模具结构的完整性,所有零部件安装框架结构要紧凑,布局合理,尽量减少模具的整体尺寸。
模具的底板和基础要够厚实,以便于承受注塑过程中的压力和热应力。
3.模腔的设计:塑胶模具的模腔设计要满足塑件的形状和尺寸要求,注意避免模腔中出现深浅不一的地方,以免造成填充不均匀和塑件变形。
模腔的表面质量要求高,尽量避免切削、铣削等加工,以减少模腔的表面粗糙度。
4.模具的冷却系统设计:塑胶模具在注塑过程中会产生大量的热量,冷却系统的设计对模具的使用寿命和生产效率有重要影响。
冷却系统应尽量覆盖整个模具,确保模腔中的塑料在注塑过程中均匀冷却,防止产生内应力和变形。
冷却水的供给要充分,流速要适宜,冷却水口要布置合理,以确保整个模具的冷却效果。
5.浇口和排气系统设计:浇口的设计应考虑塑料的流动性和塑件的外观要求,浇口位置要选择在模具的最厚点或处于最大壁厚改变处,以保证注塑过程中的充填和射出平稳。
排气系统的设计要保证塑料在充填过程中的排气畅通,避免产生气泡或虚线。
6.抽芯装置设计:塑胶模具中的一些塑件需要采用抽芯装置进行成型,抽芯装置的设计要满足塑件的形状和尺寸要求,确保塑件在脱模过程中不变形或损坏。
抽芯装置的操作要方便,可靠,要考虑到抽芯力和脱模力的大小,以确保抽芯的顺畅和模具的寿命。
7.快速更换系统设计:塑胶模具在生产过程中需要频繁更换不同的模腔,快速更换系统的设计能够极大地提高模具的使用效率和生产效率。
快速更换系统要求模腔结构尽量简单,易于拆卸和装配,以及固定方式的可靠性。
8.模具的加工工艺:塑胶模具的制作工艺要选择合适的材料和加工工艺,以确保模具的成型精度和表面质量。
001.塑胶模具基本原理和产品结构设计
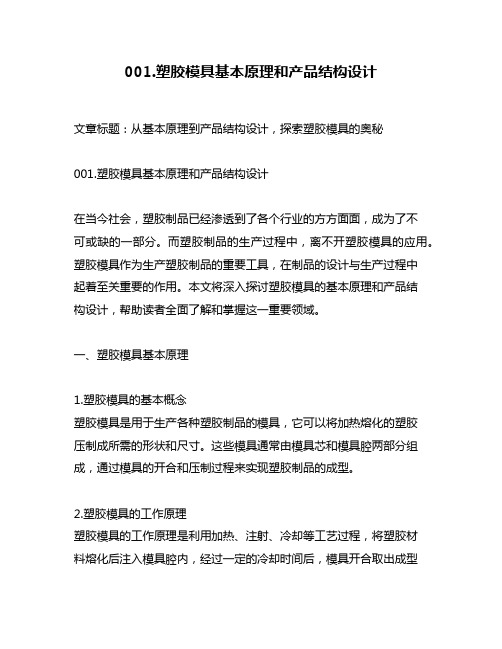
001.塑胶模具基本原理和产品结构设计文章标题:从基本原理到产品结构设计,探索塑胶模具的奥秘001.塑胶模具基本原理和产品结构设计在当今社会,塑胶制品已经渗透到了各个行业的方方面面,成为了不可或缺的一部分。
而塑胶制品的生产过程中,离不开塑胶模具的应用。
塑胶模具作为生产塑胶制品的重要工具,在制品的设计与生产过程中起着至关重要的作用。
本文将深入探讨塑胶模具的基本原理和产品结构设计,帮助读者全面了解和掌握这一重要领域。
一、塑胶模具基本原理1.塑胶模具的基本概念塑胶模具是用于生产各种塑胶制品的模具,它可以将加热熔化的塑胶压制成所需的形状和尺寸。
这些模具通常由模具芯和模具腔两部分组成,通过模具的开合和压制过程来实现塑胶制品的成型。
2.塑胶模具的工作原理塑胶模具的工作原理是利用加热、注射、冷却等工艺过程,将塑胶材料熔化后注入模具腔内,经过一定的冷却时间后,模具开合取出成型的塑胶制品。
这个过程需要严格控制温度、压力、冷却时间等参数,以确保成型的塑胶制品质量。
3.塑胶模具的分类根据不同的成型方法和产品要求,塑胶模具可以分为压缩模具、注射模具和吹塑模具等多种类型,每种类型都有其特定的适用范围和工艺要求。
二、塑胶模具产品结构设计1.产品设计的前期工作在进行塑胶模具产品结构设计之前,需要充分了解产品的使用场景、功能需求、外形尺寸等相关信息,以便为后续的模具设计工作提供有效的参考依据。
2.模具结构设计的要点模具结构设计需要考虑产品的成型过程、模具的制造工艺、使用寿命和维护保养等因素。
合理的模具结构设计可以有效提高模具的使用寿命和成型效率。
3.模具材料的选择模具材料的选择对于模具的使用寿命和成型效果有着至关重要的影响。
合理选择模具材料可以大大提高模具的性能和使用寿命。
三、个人观点与总结回顾通过对塑胶模具的基本原理和产品结构设计进行深入了解,我认为塑胶模具作为塑胶制品生产过程中的重要环节,其工艺和质量对最终成型产品的质量起着决定性的作用。
塑胶模具设计

一.总体结构设计1,分模面(Parting surface)为使产品从模具中取出模具必须分成公母模侧两部分此分界面称之为分模面它有分模和排气的作用但因模具精度和成型之差异易产生毛边结线有碍产品外观及精度选择分模面时注意:1.不可位于明显位置而影响产品外观2.开模时应使产品留在有脱模机构的一侧3.位于模具加工和产品后加工容易处4.对于同轴度要求高的产品尽可能将型腔设计在同一侧5.避免长抽芯考虑将其放在公模开模方向如一定要有应将抽芯机构尽量设在公模侧6.一般不采用圆弧部分分模这样会影响产品外观7.对于流动性好易溢边之塑料应采用插破方式分型可防治毛边产生8.对于高度高脱模斜度小之产品可取中间分模型腔分两边以有利于脱模一套模具的分模面可能有一个或多个在确定分模面时还应考虑如下因素:1.产品的形状尺寸壁厚详加研究分析找最佳方向来分模俗称“拆模”2.了解塑料性能和成型性以及浇注系统的布局3.注意排气和脱模简化模具结构操作方便加工容易它的形式有多种:水平阶梯斜面垂直曲面2.脱模斜度(Draft)为使产品容易从模具中脱出模具上必须设置脱模斜度其大小视产品形状塑料模具结构表面精度和加工方式不同而异一般为1—3目前尚无确切数值和公式大多是依经验值在不影响产品外观和性能之情形下脱模斜度愈大愈好1. 箱盒和盖2.栅格:栅格形状尺寸及肉厚不同应有不同的脱模斜度经验公式如下0.5(A---B)/H =1/12-1/14A二大端尺寸B二小端尺寸H二高度栅格节距在4mm以下之场合,脱模斜度为1/10左右,栅格肉厚超过8 mm斜度不可过份加大可在母模侧多留胶位处分模如栅格段胶位加大可考虑加大斜度3. 加强筋:可改善料流防止应力变形并起补强作用a.纵肋:0.5(A-B)/H=1/500—1/200b.底肋:0.5(A-B)/H=1/150—1/100c.凸柱:0.5(大端直径-小端直径)/H = 1/30—1/20 (内外孔在模具同一侧)母模侧:0.5(大端直径-小端直径)/H = 1/50—1/30公模侧:0.5(大端直径-小端直径)/H = 1/100—1/50 (内外孔在模具两侧)注:母模侧脱模斜度可较公模侧大些以利于脱模3. 肉厚(Thickness)产品的肉厚会直接影响到成型周期和生产效率并会因肉厚不均引起缩收下陷和应力产生设计模具时决定肉厚应注意:1.产品机械强度是否充分2.能否均匀分散冲击力和脱模力不发生破裂3.有埋入件时须防止破裂是否会因肉薄产生结合线而影响强度4.尽可能肉厚一致以防缩收下陷5.肉太薄是否会引起充填不足或阻碍料流以下为常见塑料标准肉厚参考:4.凸柱(Boss)一般为产品上凸出之圆柱它可增强孔的周边强度装配孔及局部增高之用必须防止因肉厚增加造成缩水和因聚集空气造成充填不满或烧焦现象设计时注意点:1.其高度以不超过本身直径之两倍为宜否则须增设加强筋2.其位置不宜太接近转角或侧壁以利于加工3.优先选择圆形以利于加工和料流如在底部可高出底面0.3—0.5mm5.孔(Hole)在多数产品上都有孔的存在其主要有三种方法来取得:1.在产品上直接成型2.在产品上先成型预留孔再机加工完成3.成型后完全由机加工钻孔设计时须注意以下几点:1.孔与孔之间距离须孔径2倍以上2.孔与产品边缘之距离应为孔径之3倍以上3. 孔之周边宜增加肉厚4.孔与产品侧壁之距离应为孔径0.75倍以上5.孔之直径在1.5mm以下时很容易产生弯曲变形须注意孔深不宜超过孔径2倍以上6.分模面在中间之通孔为防止偏心可将不重要一侧之孔径加大6.螺纹(scrow)为装配之用产品上有时会有螺纹设计它可以直接成型也可以在成型后再机械加工对于经常拆卸或受力大之螺纹则采用金属螺纹镶件设计时注意如下原则:1.螺距小于0.75mm之螺纹避免使用最大可使用螺纹5mm之螺纹2.因塑料收缩原因避免直接成型长螺纹以防螺距失真3.螺纹公差小于塑料收缩量时避免使用4.如内外螺纹配合须留0.1—0.4mm之间隙5.螺纹部分应有1--3脱模斜度6.螺牙不可延长至产品末端须设0.8mm左右之光杆部位以利于模具加工和螺纹寿命7.在一些类似瓶盖产品上它会设一些竖琨纹其间距宜大最小为1.5mm 一般为3.0mm在分模面设至少0.8mm平坦部位7.镶嵌件(Insert)为了防止产品破裂增加机械强度或作为传导电流之媒体及装饰之用在产品成型时常埋入镶嵌件注意要点:1.保证镶件牢靠性镶件周围胶层不能太薄2.镶件和镶件孔配合时须松紧合适不影响取放3.为使镶件与塑胶结合紧密埋入部分常设计成粗糙或凹凸之形状(压花钻孔冲弯切槽倒扣等)8.其他要点(Other)1.加强筋不可太厚一般不超过肉厚的一半以防缩水2.只要不影响外关和功能光面尽量改为咬花面这样可减少模具加工难度增加美感防止缩水产生3.在凸柱周边可除去部分肉厚以防止收缩下陷4.肉厚较薄之孔应将孔边及高度增加以便补强5.心芯梢受收缩力影响产品顶出时易造成破裂可设置凸边承受顶出力6.转角设区可改善强度防止应力集中有利于料流7.避免锐角薄肉部份易使材料充填不足8.外边有波纹之产品为方便后加工可改为加强边缘9.分模面有阶段形时模具加工不易考虑改为斜线或曲线分模10.贯穿之抽芯易发生故障改为两侧抽芯为佳11.因圆形比其他形状加工更易可降低成本优先选用12.在产品上加蚀文字或图案时如无特殊要求尽量设计凹字便于模具加工二.浇注系统设计浇注系统是塑模设计中一重要环节常分为普通和无流道浇注系统它跟所用塑料产品形状尺寸机台分模面有密切关系设计时注意以下原则:1.流道尽量直尽量短减少弯曲光洁度在Ra=1.6—0.8um之间2.考虑模具穴数按模具型腔布局设计尽量与模具中心线对称3.当产品投影面积较大时避免单面开设浇口以防注射受力不均4.浇口位置应去除方便在产品上不留明显痕迹不影响产品外观5.主流道设计时避免塑料直接冲击小型芯或小镶件以免产生弯曲或折断6.主流道先预留加工或修正余量以便保证产品精度1.主流道设计主流道是连接机台喷嘴至分流道入口处之间的一段通道是塑料进入模具型腔时最先经过的地方其尺寸大小与塑料流速和充模时间长短有密切关系太大造成回收冷料过多冷却时间增长包藏空气增多易造成气泡和组织松散极易产生涡流和冷却不足如流径太小热量损失增大流动性降低注射压力增大造成成型困难一般情况下主流道会制造成单独的浇口套镶在母模板上但一些小型模具会直接在母模板上开设主流道而不使用浇口套主流道设计要点:1.浇口套内孔为圆锥形(2--6 )光洁度在Ra=1.(-0.8um锥度须适当太大造成压力减少产生潮流易混进空气产生气孔锥度过小会使流速增大造成注射困难2.浇口套口径应比机台喷嘴孔径大1—2mm以免积存残料造成压力下降浇道易断3. 一般在浇口套大端设置倒圆角国=1—3mm)以利于料流4.主流道与机台喷嘴接触处设计成半球形凹坑深度常取3—5mm特别注意浇口套半径比注嘴半径大1—2mm 一般取R=19—22mm之间以防溢胶5.主流道尽量短以减少冷料回收料减少压力和热量损失6.主流道尽量避免拼块结构以防塑胶进入接缝造成脱模困难7.为避免主流道与高温塑胶和射嘴反复接触和碰撞一般浇口套选用优质钢材加工并热处理8.其形式有多种可视不同模具结构来选择一般会将其固定在模板上以防生产中浇口套转动或被带出2.分流道设计分流道是主流道的连接部分介于主流道和浇口之间起分流和转向作用分流道必须在压力损失最小的情况下将熔融塑胶以较快速度送到浇口处充模其截在截面积相等的条件下正方形之周长最长圆形最短面积如太小会降低塑料流速延长充模时间易造成产品缺料烧焦银线缩水如太大易积存过多气体增加冷料延长生产周期降低生产效率对于不同塑胶材质分流道会有所不同但有一个设计原则:必须保证分流道的表面积与其体积之比值最小即在分流道长度一定的情况下要求分流道的表面积或侧面积与其截面积之比值最小分流道型式有多种它因塑胶和模具结构不同而异常用型式有圆形半圆形矩形梯形U形正六边形如图设计时基本原则:1.在条件允许下分流道截面积尽量小长度尽量短2.分流道较长时应在末端设置冷料穴以容纳冷料和防止空气进入而冷料穴上一般会设置拉料杆以便于胶道脱模3.在多型腔模具中各分流道尽量保持一致长度尽量短主流道截面积应大于各分流道截面积之和4.其表面不要求过份光滑(Ra=1.6左右)有利于保温5.如分流道较多时应考虑加设分流锥可避免熔融塑胶直接冲击型腔也可避免塑料急转弯使塑胶平稳过渡6.分流道一般采用平衡式方式分布特殊情况可采用非平衡方式要求各型腔同时均衡进胶排列紧凑流程短以减少模具尺寸7.流道设计时应先取较小尺寸以便于试模后有修正余量一般的流道直径(尺寸)3.浇口设计浇口是指流道末端与型腔之间的连接部分是浇注系统的最后部分其作用是使塑料以较快速度进入并充满型腔它能很快冷却封闭防止型腔内还未冷却的热胶倒流设计时须考虑产品尺寸截面积尺寸模具结构成型条件及塑胶性能有关浇口尽量短小与产品分离容易不造成明显痕迹其类型多种多样主要有:浇口的种类及其特微9. 盘形浇口:沿产品外圆周而扩展进料其进料点对称充模均匀能消除结合线有利于排气水口常用冲切方式去除设计时注意冲切工艺10.扇形浇口:从分流道到模腔方向逐渐放大呈扇形适用于长条或扁平而薄之产品可减少流纹和定向应力扇形角度由产品形状决定浇口横面积不可大于流道断面积11.环形浇口:延产品整个外圆周扩展进胶它能使塑胶绕型芯均匀充模排气良好减少结合线但浇口切除困难它适用于薄壁长管状产品12.点浇口:是一种截面积小如针状之浇口一般用于流动较好之塑胶其浇口长度一般不超过其直径所以脱模后浇口自动切断不须再修正而浇口残痕不明显在箱罩盒壳体及大面积产品中应用相当广泛它可以使模具增加一个分模面便于水口脱模其缺点是因进浇口较小易造成压力损耗成型时产生一些不良(流痕烧焦黑点)其形状有菱形单点形双点形多点形13.侧浇口: 一般开设在模具一边分模面上由内侧或外侧进胶截面多为矩形适用于一模多穴14.直接浇口:直接由主流道进入模腔适用于单穴深腔壳形箱形模具其流道流程短压力损失少有利于排气但浇口去除不便会留明显痕迹15.潜伏浇口:其浇口呈倾斜状潜伏在分模面一方在产品侧面或里面进胶脱模时可自动切断针点浇口适用自动化生产设计要点:1.进胶口应开设在产品肉厚部分保证充模顺利和完全2.其位置应选在使塑胶充模流程最短处以减少压力损失有利于模具排气3.可通过模流分析或经验判断产品因浇口位置而产生之结合线处是否影响产品外观和功能可加设冷料穴加以解决4.在细长型芯附近避免开设浇口以免料流直接冲击型芯产生变形错位或弯曲5.大型或扁平产品建议采用多点进浇可防止产品翘曲变形和缺料6.尽量开设在不影响产品外观和功能处可在边缘或底部处7.浇口尺寸由产品大小几何形状结构和塑胶种类决定可先取小尺寸再根据试模状况进行修正8. 一模多穴时相同的产品采用对称进浇方式对于不'同产品在同一模具中成型时优先将最大产品放在靠近主流道的位置9.在浇口附近之冷料穴尽端常设置拉料杆以利于浇道脱模4.热流道目前浇注系统发展和改进的一个重要方向就是开发热流道模具它与一般注射模具的主要区别就是注射成型过程中浇注系统内之塑胶不会冷却拟固也不会形成浇道与产品一起脱模[[因此也称无流道模具在大型和精密模具设计中应用已越来越广泛它有以下优点:1.缩短成型周期省去剪浇口修整产品破碎回收等工序节约人力物力提高生产效率2.因无冷胶可减少材料消耗3.因生产中温度严格控制显著提高产品质量降低次品产生4.因浇注系统中塑胶始终处于融熔状态有利于压力传递可降低注射压力利于成型5.因无浇道产生所以可缩短开模行程有利于模具和机台寿命但热流道模具结构复杂温度控制要求严格需要精密的温控系统制造成本较高不适合小批量生产根据不同塑胶特性对热流道模具有不同要求见下表:三.顶出系统设计产品完成一个成形周期后开模产品会包裹在模具的一边必须将其从模具上取下来此工作必须由顶出系统来完成它是整套模具结构中重要组成部分一般由顶出复位和顶出导向等三部分组成一.按动力来分1.手动顶出:当模具开模后由人工操纵顶出系统顶出产品它可使模具结构简化脱模平稳产品不易变形但工人劳动强度大生产率低适用范围不广一般在手动旋出螺纹型芯时使用2.机动顶出:通过注射机动力或加设之马达来推动脱模机构顶出产品它可通机台上的顶杆\推顶针板来达到脱模目的也可在公母模板上安装定距拉杆或链条靠开模力拖动顶出机构顶出产品调模时必须注意控制开模行程适用于顶出系统在母模侧之模具3.液压顶出:在模具上安装专用油缸由注射机控制油缸动作其顶出力速度和时间都可通过液压系统来调节可在合模之前顶出系统先回位4.气动顶出:利用压缩空气在模具上设置气道和细小的顶出气孔直接将产品吹出产品上不留顶出痕迹适用于薄件或长筒形产品二.按模具结构分一次顶出机构二次顶出机构母模顶出机构浇注系统顶出机构螺纹顶出机构等设计原则:1.选择分模面时尽量使产品留在有脱模机构的一边2.顶出力和位置平衡确保产品不变形不顶破3.顶针须设在不影响产品外观和功能处4.尽量使用标准件安全可靠有利于制造和更换顶出系统形式多种多样它与产品之形状结构和塑胶性能有关一般有顶杆顶管推板顶出块气压复合式顶出等一.顶杆它是顶出机构中最简单最常见的一种形式其截面积形式主要有如下1.圆形因圆形制造加工和修配方便顶出效果好在生产中应用最广泛但圆形顶出面积相对较小易产生应力集中顶穿产品顶变形等不良在脱模斜度小阻力大等管形箱形产品中尽量避免使用当顶杆较细长时一般设置成台阶形的有托顶针以加强刚度避免弯曲和折断设计要点:1.顶出位置应设置在阻力大处不可离镶件或型芯太近对于箱形类等深腔模具侧面阻力最大应采用顶面和侧面同时顶出方式以免产品变形顶破2.产品阻力均衡时顶杆应对称设置使受力平衡3.当有细而深之加强筋时一般在其底部设置顶杆4.若模具上有镶件顶针设在其上效果更佳5.在产品进胶口处避免设置顶针以免破裂6.当产品表面不允许有顶出痕迹时可设置顶出耳再剪除7.对于薄肉产品在分流道上设置顶针即可将产品带出8.顶针与顶针孔配合一般为间隙配合如太松易产生毛边太紧易造成卡死为利于加工和装配减少摩擦面一般在模仁上预留10—15mm之配合长度其余部分扩孔0.5—1.0mm成逃孔9.为防止顶针在生产时转动须将其固定在顶针板上其形式多种多样须根据顶针大小形状位置来具体确定在此不一一列举10. 顶出系统托模以后在进行下一周期生产时必须退回原处其形式主要有强制回位拉杆回位弹簧回位油缸二.顶管又叫司筒或套筒顶针它适用于环形筒形或带中心孔之产品顶出由于它是全周接触受力均匀不会使产品变形也不易留下明显顶出痕迹可提高产品同心度但对于周边肉厚较薄之产品避免使用以免加工困难和强度减弱造成损坏三.推板此形式适用于各种容器箱形筒形和细长带中心孔之薄件产品它顶出平稳均匀顶出力大不留顶出痕一般会有固定连接以免生产中或托模时将推板推落但只要导柱足够长严格控制托模行程推板也可不固定.。
塑胶模具设计规范

模具设计规范(此规范主要应用于手机模具)一、模具排位1、根据产品大小、结构、产量、精密程度、材料或客户要求等因素确定模穴,如1X1、1X2等。
2、当几个产品出在同一套模具中时,考虑进胶的均匀性,应将大的产品排在中间位置,小的产品置于两边。
确保冲胶平衡,保证产品尺寸的精确性。
3、当几个分型面不规则的产品在同一模具中时,排位必须充分考虑其分型面连接的顺畅,且容易加工。
4、一模多穴模具中,当有镶拼,行位等结构时,不得使其发生干涉。
5、排位多时应综合模具每一方面,对流道,是否镶拼,行位,顶出,运水等结构要有一个全局性思考。
6、排位时产品在模上的定位基准要和产品图的基准一致,当一模出一件时,可以考虑以产品对称方向处分中。
7、内模钢料和模胚的大小尺寸如下图所示。
8.产品大小和胶位厚度有较大相差时尽量不要出在同一套模具中。
9.模具方铁高度尽量订做标准高度。
10.模胚型号和中托司使用情况一定要写清楚(细水口需注明SP长度)11.必要时需注明模胚吊模孔移位情况12.考虑需不需开精框及内模料材料和规格(确定后模要不要镶大呵,如需要则一起订料,此为粗料.)二、模具系统设计一)、行位系统当塑胶产品确定前后模开模方向后,有下列情况时一般会采用行位或斜顶等结构:1)、相对出模方向塑胶产品上有倒扣或零度面;2)、产品的出模斜度不够蚀纹的角度;3)、保证特殊的外观面不能有夹线。
1、后模行位:1)、后模行位统一做镶件压块,行位压块用螺丝固定,行位压块材料为油钢淬火至HRC48-52°。
2)、所有与行位相对运动的零部件的滑动面(包括行位底耐磨片,压条,铲基斜面)须锣(磨)油坑,油坑可为平行四边行、V形或圆环形。
3)、行位铲机钢材整体采用738H,在铲机斜面上镶耐磨片,耐磨片可突出斜面0.5mm,耐磨片厚度为6mm(如下图),材料为油钢,淬硬至HRC48-52°。
康铨公司的铲基采用国产S136淬硬至HRC46-50°。
2024版塑料模具设计教学(精选)

合金钢
具有较高的强度、韧性和 耐磨性,适用于制造大型、 复杂、高精度的塑料模具。
不锈钢
具有优良的耐腐蚀性和耐 磨性,适用于制造有腐蚀 性介质或外观要求较高的 塑料模具。
20
热处理工艺对性能影响
退火处理
消除内应力,提高塑性 和韧性,改善切削加工
性能。
2024/1/28
正火处理
细化晶粒,提高强度和 韧性,改善综合力学性
26
07 案例分析与实践 操作指导
2024/1/28
27
典型案例分析讨论
案例一
手机壳塑料模具设计
设计需求分析
探讨手机壳的材质、尺寸精度、表面处理等要求。
模具结构设计
分析分型面、浇注系统、冷却系统等关键设计要 素。
2024/1/28
28
典型案例分析讨论
2024/1/28
制造工艺及装配
01
讲解模具的加工工艺、装配过程及调试方法。
脱模机构设计
脱模机构用于将制品从模具中脱出,其设计应保证制品完整无损且易于脱模。设计时需考虑脱模方式、脱模力大 小及方向等因素。同时,还需考虑模具结构、制品形状和尺寸等因素对脱模机构的影响。
2024/1/28
14
04 挤出成型模具设 计
2024/1/28
15
挤出成型原理及设备
挤出成型原理
通过挤出机螺杆的旋转和机筒的加热,使 塑料在机筒内熔融塑化,并在螺杆的推动 下,以一定的压力和速度通过机头模口挤 出,得到截面形状一定的塑料型材。
3
塑料材料特性
热塑性塑料
受热软化、冷却硬化,可反复加 热和冷却,具有良好的可塑性。 如聚乙烯(PE)、聚丙烯(PP)
塑胶模具设计指引
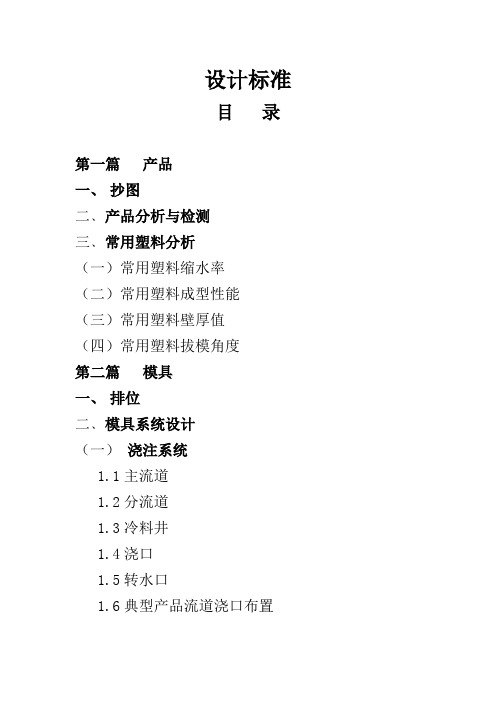
设计标准目录第一篇产品一、抄图二﹑产品分析与检测三﹑常用塑料分析(一)常用塑料缩水率(二)常用塑料成型性能(三)常用塑料壁厚值(四)常用塑料拔模角度第二篇模具一、排位二﹑模具系统设计(一)浇注系统1.1主流道1.2分流道1.3冷料井1.4浇口1.5转水口1.6典型产品流道浇口布置(二)成形系统2.1行位系统行位斜顶2.2镶件(三)顶出系统4.1顶出系统设计要点4.2顶出机构的基本方式 4.2.1顶针4.2.2司筒4.2.3扁顶针4.2.4直顶4.2.5推板4.3先复位机构(四) 冷却系统5.1.运水位置5.2.水路大小5.3.水路与模胚位置关系5.4.水井(五) 导向定位系统(六) 排气系统7.1产品排气7.2导套排气槽7.3尼龙螺丝排气孔(七)模胚结构件(支撑)及周边辅助件 7.1撑头7.2垃圾钉7.3锁模机构7.4温控箱、水管、紧固件三﹑细水口模设计四、模具零部件材料选择六、分模(一)模具档分模(二)组立档分模七、注射机选择第三篇图档一、出图要求1.排位图2.装配图3.顶针图4.线割图5.零件图6.分模图7.爆炸图二、图纸管理与进度控制(一)图纸管理(二)审图(三)进度三、电脑图档管理第四篇附录一、标准件二、工程表格产品篇抄图一.抄图前,先要看懂,看透产品线图,然后班顺思路,特别是外形面的画法。
抄好产品图要转为2D线图与设计部提供的平面线图套。
要保证主要的视图和边界线完全重合一致。
若有不重合、不一致的情况,首先分析是2D线图本身表达有问题,还是抄图时造成的。
若为2D线图表达问题则应及时标明,并与设计部沟通、反映;若为抄图问题,及时修改。
二.一个产品通常要多次转图与标题栏对上几次逐步确认(看版本),避免最后的问题堆积。
三.在抄图的整个过程中,最为重要的是基体外形面的控制和核对。
四.抄好的UG尽可能保证可以再生,以实现UG的参数设计功能。
五.通常抄图应先抄好影响模具结构之处,如外形面、行位处倒勾、前后模基面加减胶。
塑料模具设计指引

塑模開發手冊製品圖詳閱之事項A.設計變更的項目是否確實地記入最新版的成品圖內?B.有無機種替換?交換模仁之模具結構是否沒問題?是否方便於拆裝?C.樹脂相關的情報是否詳實?是否取得了物性表?1.樹脂名。
2.等級。
3.顏色。
4.成形收縮率。
5.收縮率和射出壓力(或模腔內壓)、保壓時間、肉厚、料管溫度、模具溫度等關係變化。
6.加工流動性(流動長或L / T比)和射出壓力、模具溫度、肉厚、料管溫度等之對應關係。
7.成形條件之最適範圍。
D.是否可做逃氣溝?(參考物性表或哪一種成形法),可作何種逃氣法?E.採用何種成形法?F.拆模:1.母模(製品表面側)要設計於塑膠機之固定側或可動側?2.拆模線(分模面、插破面、靠破面)是否理想?3.插破面之斜度是否足夠?(最好是3°以上)(插破量)4.製品表面的模仁線可有獲得客戶的承認?5.喇叭網孔脫模斜度是否足夠?其脫模斜度是否配合咬花?G.成品部是否會造成收縮之處?會收縮於哪一側?可有應付的解決辦法與判斷對策了?1.偏肉2.局部較厚之肉厚縮水痕跡如何克服?3.RIB與側壁(或板厚)相連處之肉厚比例,板厚,側壁與RIB之比例為最之極限2/3。
4.BOSS根元處之肉厚與該處板厚之比例。
是否有作全周盜料?5.局部之製品是否會因熱集中,不易冷卻而導致表面收縮?6.是否可確實的判定出收縮於哪一側(製品之表面或內側)?7.採用特殊之成形法是否可不用考慮收縮?例如發泡成形,或SINPRESS法等。
8.設計盜料之小模仁或模仁梢時是否達到平均肉厚之要求?H.短射:(充填不足)如何對策?1.肉厚過薄無法成形時。
2.RIB過薄或過深。
3.BOSS根元處肉厚過薄。
4.BOSS肉厚過薄或過深。
5.RIB或BOSS是否會太接近澆口?6.短射和逃氣溝之關係。
(客戶有提出排氣之指示?)I.短射和收縮二者之間如何取得平衡值?J.流道、澆口系統:(含補助湯道、堵料道)。
1.採用哪種流道(熱流道、冷流道、其他)?2.流道系統適切?(注道、流道之型式及尺寸,澆口之型式、個數、位置、尺寸等)流動平衡OK?3.流道距離/肉厚(L / T )適切?4.流道系統對整個成品之重量百分比合理?5.所採用的澆口型式是否會造成蛇紋或澆口附近產生色澤不均(如模糊、霧狀等)之現象。
塑料模具设计一般程序

分析试模结果,修正模具
分析数据
对试模过程中记录的数据进行分析,评估模具的 性能和产品的质量。
修正模具
根据分析结果和检查出的缺陷,对模具进行修正, 如修改浇口位置、增加排气孔等。
ABCD
检查缺陷
检查试模产品是否存在缺陷,如缩水、气泡、翘 曲等。
再次试模
对修正后的模具进行再次试模,重复以上步骤, 直到模具性能和产品质量符合要求为止。
编写设计说明书
设计说明书
编写详细的设计说明书,包括模具的设计思路、结构特点、使用注意事项等, 以便于其他人员理解和使用模具。
操作手册
编写操作手册,详细介绍模具的操作步骤、维护保养方法等,以便于操作人员 快速掌握使用技巧。
审核与校对
审核
对设计图纸和说明书进行审核,确保设计方案的正确性和可行性。
校对
设计主流道、分流道
根据塑料制品的形状和尺寸,设计出相应的主流道 、分流道,确保塑料能够以最佳流动状态充填型腔 。
选择浇注系统材料
根据塑料的种类和性能,选择合适的浇注系水道
根据模具结构和塑料制品的形状,设计出相应的冷却 水道,确保模具在冷却过程中能够均匀散热。
选择冷却介质
出、气动顶出等。
确定顶出位置
03
根据塑料制品的形状和尺寸,确定合适的顶出位置,确保塑料
制品能够顺利脱模且不变形。
03
后期工作
绘制模具装配图
模具装配图
根据模具设计方案,绘制出详细的模 具装配图,包括模具的整体结构、零 件组成、尺寸标注等。
模具零件图
根据装配图,绘制出各个模具零件的 零件图,包括零件的形状、尺寸、材 料等。
对图纸和说明书进行校对,纠正错误和遗漏,提高设计质量。
塑料模具设计指导书
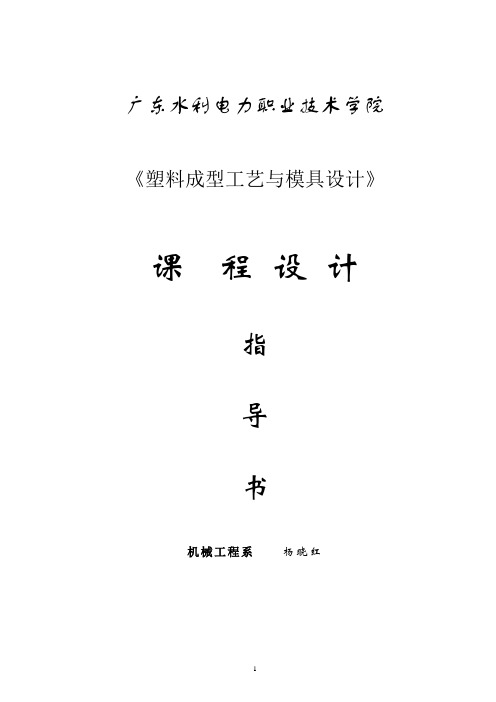
广东水利电力职业技术学院《塑料成型工艺与模具设计》课程设计指导书机械工程系杨晓红塑料模具课程设计指导书塑料模具课程设计是《塑料成型工艺与模具设计》课程教学中最重要的教学实践环节。
旨在培养学生综合应用塑料模具设计知识,系统地进行塑料模具设计,包括塑料模塑成型工艺编制、塑料模具设计、非标准模具零件设计等。
一、目的和要求1、目的⑴、培养学生对具体设计任务的理解和分析能力;⑵、培养学生编制模塑成型工艺规程的能力;⑶、培养学生设计塑料模具的能力;⑷、培养学生综合运用专业理论知识、分析问题、解决问题的能力和严谨、科学的工作态度。
2、要求⑴、塑料模具课程设计题目为相当模具设计师考级程度的塑件,满足教学要求和生产实际的要求,应尽可能做到结合生产需要.⑵、查阅有关资料,作好设计准备工作,充分发挥自已的主观能动性和创造性;⑶、树立正确的设计思想,结合生产实际综合地考虑经济性、实用性、可靠性、安全性及先进性等方面的要求;⑷、要求模塑工艺计算正确,编制的塑料模塑工艺规程符合生产实际;⑸、要求模具结构合理,凡涉及国家标准之处均应采用国家标准,图面整洁,图样和标注符合国家标准;二、准备工作和注意事项1、预备知识塑料模具课程设计是在学生具备了机械制图,公差与技术测量,材料及热处理,机械设计基础,机械制造技术,塑料模具设计,机械与自动化,数控加工技术等必要的基础知识与专业知识的基础上进行的。
完成本专业教学计划中所规定的认知实训,也是保证学生顺利进行模具设计实训的必要的教学实践环节。
2、注意事项⑴、必须先准备好资料、手册、图册、计算器、报告纸等。
⑵、应对塑料模具设计的原始资料进行认真地消化,并明确设计要求再进行工作。
原始资料包括:塑料件零件图,原材料牌号与规格,成型设备的牌号与规格等。
⑶、画出的模具结构草图经指导教师认可后方能绘制正式装配图及零件图。
三、课程设计的任务1、编制模塑成型工艺规程.2、绘制注射模装配图.3、绘制非标准模具零件图。
塑胶模具设计讲义
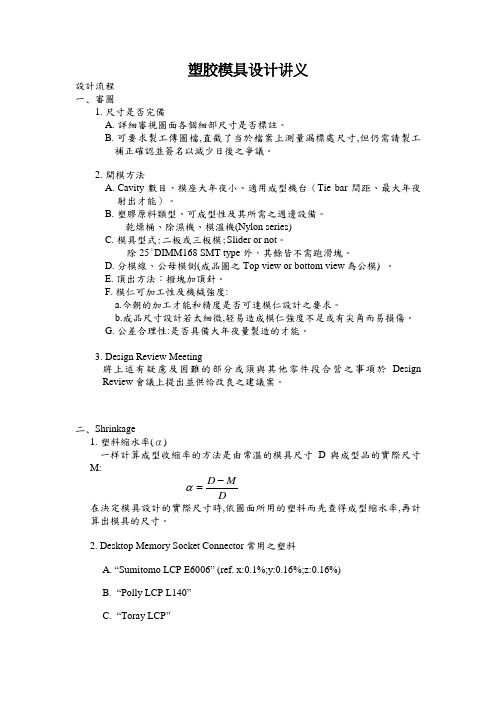
塑胶模具设计讲义設計流程一﹑審圖1.尺寸是否完備A.詳細審視圖面各個細部尺寸是否標註。
B.可要求製工傳圖檔,直截了当於檔案上測量漏標處尺寸,但仍需請製工補正確認並簽名以減少日後之爭議。
2.開模方法A.Cavity數目、模座大年夜小、適用成型機台(Tie bar間距、最大年夜射出才能)。
B.塑膠原料類型、可成型性及其所需之週邊設備。
乾燥桶、除濕機、模溫機(Nylon series)C.模具型式:二板或三板模;Slider or not。
除25°DIMM168 SMT type 外,其餘皆不需跑滑塊。
D. 分模線、公母模側(成品圖之Top view or bottom view為公模)。
E. 頂出方法:撥塊加頂針。
F. 模仁可加工性及機械強度:a.今朝的加工才能和精度是否可達模仁設計之要求。
b.成品尺寸設計若太細微,轻易造成模仁強度不足或有尖角而易損傷。
G. 公差合理性:是否具備大年夜量製造的才能。
3.Design Review Meeting將上述有疑慮及困難的部分或須與其他零件段合营之事項於Design Review會議上提出並供给改良之建議案。
二﹑Shrinkage1.塑料縮水率(α)一样計算成型收縮率的方法是由常溫的模具尺寸D與成型品的實際尺寸M:D MD-=α在決定模具設計的實際尺寸時,依圖面所用的塑料而先查得成型縮水率,再計算出模具的尺寸。
2. Desktop Memory Socket Connector常用之塑料A. “Sumitomo LCP E6006” (ref. x:0.1%;y:0.16%;z:0.16%)B.“Polly LCP L140”C.“Toray LCP”D. “Wuno LCP ”E. “南亞、耐特、晉綸PA66”F. “Arlen PA6T ”G. “DSM PA46(F8、HF5040)”3. 可過IR 製程之塑料為“Sumitomo LCP E6006” ,同时其收縮率专门小,尺寸安定性極佳,故平日以此種原料為設計基準,其他塑料則以實際射出之尺寸為該料號之圖面尺寸(今朝於DIMM 168與DDR 皆採用大年夜範圍之公差將不合原料之成品總長涵蓋,如140.9525.005.0-+;RIMM 則因為是高頻connector 且Intel 對生產製程尺寸之cpk 值要求专门嚴格,故採用E6006原料) 。
- 1、下载文档前请自行甄别文档内容的完整性,平台不提供额外的编辑、内容补充、找答案等附加服务。
- 2、"仅部分预览"的文档,不可在线预览部分如存在完整性等问题,可反馈申请退款(可完整预览的文档不适用该条件!)。
- 3、如文档侵犯您的权益,请联系客服反馈,我们会尽快为您处理(人工客服工作时间:9:00-18:30)。
设计标准目录第一篇产品一、抄图二﹑产品分析与检测三﹑常用塑料分析(一)常用塑料缩水率(二)常用塑料成型性能(三)常用塑料壁厚值(四)常用塑料拔模角度第二篇模具一、排位二﹑模具系统设计(一)浇注系统1.1主流道1.2分流道1.3冷料井1.4浇口1.5转水口1.6典型产品流道浇口布置(二)成形系统2.1行位系统行位斜顶2.2镶件(三)顶出系统4.1顶出系统设计要点4.2顶出机构的基本方式4.2.1顶针4.2.2司筒4.2.3扁顶针4.2.4直顶4.2.5推板4.3先复位机构(四)冷却系统5.1.运水位置5.2.水路大小5.3.水路与模胚位置关系5.4.水井(五)导向定位系统(六)排气系统7.1产品排气7.2导套排气槽7.3尼龙螺丝排气孔(七)模胚结构件(支撑)及周边辅助件7.1撑头7.2垃圾钉7.3锁模机构7.4温控箱、水管、紧固件三﹑细水口模设计四、模具零部件材料选择六、分模(一)模具档分模(二)组立档分模七、注射机选择第三篇图档一、出图要求1.排位图2.装配图3.顶针图4.线割图5.零件图6.分模图7.爆炸图二、图纸管理与进度控制(一)图纸管理(二)审图(三)进度三、电脑图档管理第四篇附录一、标准件二、工程表格产品篇抄图一.抄图前,先要看懂,看透产品线图,然后班顺思路,特别是外形面的画法。
抄好产品图要转为2D线图与设计部提供的平面线图套。
要保证主要的视图和边界线完全重合一致。
若有不重合、不一致的情况,首先分析是2D线图本身表达有问题,还是抄图时造成的。
若为2D线图表达问题则应及时标明,并与设计部沟通、反映;若为抄图问题,及时修改。
二.一个产品通常要多次转图与标题栏对上几次逐步确认(看版本),避免最后的问题堆积。
三.在抄图的整个过程中,最为重要的是基体外形面的控制和核对。
四.抄好的UG尽可能保证可以再生,以实现UG的参数设计功能。
五.通常抄图应先抄好影响模具结构之处,如外形面、行位处倒勾、前后模基面加减胶。
至于柱位、骨位可最后再抄。
六.要区别常用的做曲面命令。
七.分清结构线与效果线。
原则上结构线一定要与线图完全一致,效果线应尽可能接近。
八.抄整体产品外形,要考虑产品出模基体外形的出模角(拔模方向)应在最初放好,不然,到最好去做,通常是不会成动和很麻烦的。
九.特别注意,在倒角前应将拔模做好。
十.产品外形抄好后,应做一个全面、细致的抄图报告。
详细说明UG图与线图间的不同之处和处理方案。
二、产品分析与检测(一)、装配检测(二)、结构检测1.检查产品各部分结构是否合理,对加工、注射是否存在明显不利影响。
2.检查产品是否存在难出模或不能出模之处,如倒勾等。
(三)、拔模角检测1.首先在分析----形状----面----斜率指定与开模方向为一致的矢量方向,将最合最小值设为对称值(正负),选择产品确定就可以得到用颜色区分的拨模面角度颜色.拨模斜度要特别注意插穿位拔模角的大小,一般为3~5°。
2.产品各骨位(火花直接打出)、柱位拔模角可不考滤。
3.当需增加拔模角时,一般原则是往减胶方向拔模,以利今后改模。
(四)、肉厚检测三、常用塑料分析(一)常用塑料缩水率以上均为热塑性通用塑料.拔 模四)常塑HIPS 35'~1°30' 30'~1°ABS 40'~1°20' 35'~1° 用料PE25'~45' 20°~45'PMMA35'~1°30'30'~1°角POM 35'~1°30' 30'~1°PC 35'~1° 30'~50'垫固性料 25'~1° 20'~50'度二 、模 具 篇一、排位1.根据产品大小、结构等因素确定模穴,如 1X1、1X2、1X3、1X4、1X8、1X16 等。
2.当几个产品出在同一套模具中时,考虑进胶的均匀性。
应将大的产品排在中间位置,小的产品置于两边。
3.当几个分型面不规则的产品在同一模具中时,排位必须充分考虑其分型面连接的顺畅。
4.一模多穴模具中,当有镶拼、行位等结构时,不得使其发生干涉。
5.排位时应综合模具每一方面,对流道,是否镶拼、行位、顶出、运水等结构要有一个全局性思考。
6.排位时以产品零线为定位基准。
当一模出一件时,可以考虑以产品对称方向外形分中。
二、模具系统设计浇注系统内模结构顶出系统冷却系统导向定位系统排气系统模胚结构件。
说明﹕在具体的模具设计过程中﹐不一定会严格遵守此程序﹐通常我们要返回上一步甚至上几步﹐修改部分数值﹐直至最后确认。
(一)﹑浇注系统浇注系统由主流道﹑分流道﹑冷料井和浇口等部分组成。
在设计浇注系统时,要考虑:制品最主要的要求是什么?外观还是强度或是尺寸精度,找出最主要的矛盾,设计时,立足主要矛盾,同时,在不与主要矛盾发生冲突的前提下,改善其它次要矛盾,要做到进浇的均匀与顺畅。
1.1.主流道主流道一般为圆锥形,角度2~4o主流道要设计的尽量的短。
1.2.分流道1.2.1.分流道的形状有圆形﹑梯形等几种,从减少压力和热量损失的角度来看,圆形流道是最优越的流道形状。
当分型面是平面或者曲面时,一般采用圆形流道;细水口模,选用梯形流道,当流道只开在前模或者后模时,则选用梯形流道。
1.2.2.布置一模多腔的流道时,应充分考虑进浇的均匀性,尽可能做到平衡进浇。
1.2.3.设计分流道大小时,应充分考虑制品大小,壁厚、材料流动性等因素,流动性不好的材料如PC料其流道应相应加大,并且分流道的截面尺寸一定要大于制品壁厚,同时应选适合成形品形状的流道长度。
流道长则温度降低明显,流道过短则剩余应力大,容易产生“喷池”,顶出也较困难。
1.2.4.梯形流道:W一般为5~8H一般为4~6H/W=2/3如图1-1:1.3.冷料井﹕为防止冷却的树脂流入型腔﹐在不通向型腔的流道末端要设置冷料井﹐包括主流道的大端和分流道拐角处.1.3.1.大水口模主流道大端的冷料井与顶针配合有抓料的作用。
常见形式如图1-21.3.2.分流道拐角处冷料井设置如图:1.3.3.细水口模冷表-1料井设置如图 1-4,正对主流道,尺寸与分流道尺寸相同。
1.4. 浇口常见浇口类型有直接浇口﹑侧浇口﹑潜伏式浇口﹑点浇口 等多种。
设计时应根据产品的不同要求选择适合的类型.尤其当制品外观有要求时, 要慎重选择。
见图表:1.4. 1 直接浇口对大型单一型腔制品成型效果好,需注意唧嘴底部与产品之间隔 10MM 。
例如底壳类制品.其尺寸要求如图:浇口类型 优点 缺点 适用产品直接浇口 熔融树脂直接入腔、 压力损失小、保压补 缩作用强.去除困难、浇口 痕迹明显、浇口周围应力大. CD 门、底壳.侧浇口加工容易、易保证浇 口加工精度.有浇口痕迹、浇口修改困难. CD 门、中层、镜件、 按钮、布网架、手挽、 电池门、CD 座、装饰 件、面板、盖板.潜伏式浇 口 浇口痕迹不明显、可 自动切断浇口.加工困难、浇口尺寸精度不易保 证. 齿轮、手挽、按钮(仅指 钮身高度大于 15MM 的 情况).点浇口开模时自动切断浇口、 浇口周围残留应力小、 痕迹小、可设置多点 浇口. 压力损失大、要 求较高的注射力. 底壳、面壳、按钮(仅指 钮周边均有骨位的情况) 例 CD109 钮组.1.4.2.侧浇口侧浇口设置于制品分型面处,制品允许有浇口痕迹才可采用,侧浇口包括边缘浇口和搭接浇口,其浇口尺寸与制品壁厚﹑大小﹑材料等诸多因素有关,一般规格如图1-5:在选择侧浇口时,必须充分考虑制品外观要求,尽量从靠近(避免直接正对碰穿位)制品大的碰穿孔位置进胶,例如大装饰件等制品.因为这样可以减少夹水纹。
边缘浇口与搭接浇口的选择见图:同时选择浇口位置时,应防止制品产生滞留现象,应远离厚﹑薄交接处,从厚的地方进浇,避免浇口正对柱位、碰穿位,防止型芯因冲击而变形。
顺流(良)喷流(差)喷流(差)顺流(良)1.4.3潜伏式浇口﹕潜伏式浇口有潜顶针﹑潜薄片﹑潜产品等几种.潜水也可以开在前模一侧。
如图:α=30~45oβ=15~20o潜水运用使得产品分型面无浇口疤痕,并且可自动切断浇口,同时也改善了制品表面因为喷射产生缺陷的可能,应用广泛。
1.4.4.点浇口点浇口垂直设置于制品表面,其尺寸如图:1.5.转水口一模多腔模具中,有时要设置转水口;转水口一般采用波子螺丝,即限位钢铢限位,大小为M8,转水口采用公司自制标准。
如图所示.1.6.唧嘴大水口模胚,若前模高度足够,则唧嘴沉入内模以减短主流道长度,结构如图示。
1.7.典型产品流道浇口布置。
1.7.1.按钮等电镀产品需设置环形流道,前模要加胶柱,其高度应超出制品前模部分的厚度2MM,并且按钮每一钮均需设进浇点,保证进料均匀。
1.7.2.镜类产品应从长度方向或靠近长度方向进胶,如图:1.7.3.底壳类制品一般采用直接浇口进浇,特殊情况细水口进胶。
1.7.4.手挽只设一个浇口,尽量从转柱位进浇,不能从转柱位进浇时,采用潜水方式但要避免从手握位进浇。
(二)内模结构※分型面在模具设计中,分型面的选择是一项非常重要的工作,确定分型面需从以下几个方面综合考虑:1).产品的质量与外观要求;2).开模后产品留前模或后模的方便性;3).易加工性(例钮CD座中间碰穿孔位);4).排气;5).客户指定。
设计时,考虑到产品的精度、加工的方便性、模具的强度、本公司的加工能力以及排气与冷却的因素,往往需要采用镶拼结构。
2.1.当产品某处需换呵,必须单独镶出。
2.2.当产品周围有止口时,需要整体镶呵,此时,镶呵并不镶通,并且其周边倒R6.0圆弧,例如大的底面壳等产品。
2.3.当产品骨位过深时要镶出,如图:h/t≧102.4.当产品某处结构复杂,难加工时要镶。
例如CD座上CD 门转轴柱位,前后模对碰前后模均需镶出。
2.5齿轮产品前后模均需做镶件,如图2.6.当产品上有细小的不规则碰穿孔时,一般要镶,例如中层采取前模线割方式。
2.7当产品上有文字标识时,一般要镶,镶件尽量不镶通,采用螺丝固定,镶嵌范围为文字标识处最外圈装饰线。
2.8.当按钮等制品对碰穿位大小有严格要求时,往往要镶(镶件为黄牌),以保护前模。
2.9当钮孔周围有环骨,且其深度超过5MM时,需镶。
2.10当镶件采用不超过M1/4的螺丝固定时﹐螺丝边与镶件边的最小距离为2.0mm。
2.11.CH型模胚前模镶针底要加压板。
2.12.固定内模的螺丝位于内模边时,其与内模边的尺寸对应关系见表﹕当需模胚厂开框时,开框深度不超过40MM,四角R10。
开框深度超过40MM,四角R16。