铝合金切削加工条件选择及其切削加工性能改善_熊建武
铝合金切削加工参数分析与选用
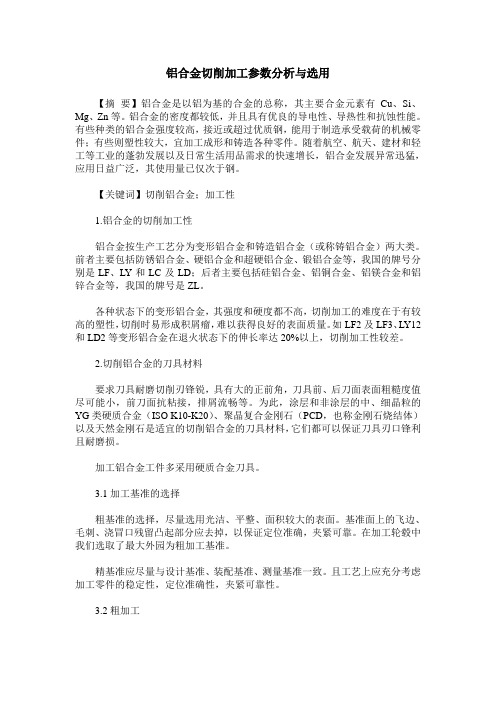
铝合金切削加工参数分析与选用【摘要】铝合金是以铝为基的合金的总称,其主要合金元素有Cu、Si、Mg、Zn等。
铝合金的密度都较低,并且具有优良的导电性、导热性和抗蚀性能。
有些种类的铝合金强度较高,接近或超过优质钢,能用于制造承受载荷的机械零件;有些则塑性较大,宜加工成形和铸造各种零件。
随着航空、航天、建材和轻工等工业的蓬勃发展以及日常生活用品需求的快速增长,铝合金发展异常迅猛,应用日益广泛,其使用量已仅次于钢。
【关键词】切削铝合金;加工性1.铝合金的切削加工性铝合金按生产工艺分为变形铝合金和铸造铝合金(或称铸铝合金)两大类。
前者主要包括防锈铝合金、硬铝合金和超硬铝合金、锻铝合金等,我国的牌号分别是LF、LY和LC及LD;后者主要包括硅铝合金、铝铜合金、铝镁合金和铝锌合金等,我国的牌号是ZL。
各种状态下的变形铝合金,其强度和硬度都不高,切削加工的难度在于有较高的塑性,切削时易形成积屑瘤,难以获得良好的表面质量。
如LF2及LF3、LY12和LD2等变形铝合金在退火状态下的伸长率达20%以上,切削加工性较差。
2.切削铝合金的刀具材料要求刀具耐磨切削刃锋锐,具有大的正前角,刀具前、后刀面表面粗糙度值尽可能小,前刀面抗粘接,排屑流畅等。
为此,涂层和非涂层的中、细晶粒的YG类硬质合金(ISO K10-K20)、聚晶复合金刚石(PCD,也称金刚石烧结体)以及天然金刚石是适宜的切削铝合金的刀具材料,它们都可以保证刀具刃口锋利且耐磨损。
加工铝合金工件多采用硬质合金刀具。
3.1加工基准的选择粗基准的选择,尽量选用光洁、平整、面积较大的表面。
基准面上的飞边、毛刺、浇冒口残留凸起部分应去掉,以保证定位准确,夹紧可靠。
在加工轮毂中我们选取了最大外园为粗加工基准。
精基准应尽量与设计基准、装配基准、测量基准一致。
且工艺上应充分考虑加工零件的稳定性,定位准确性,夹紧可靠性。
3.2粗加工由于铝合金零件加工尺寸精度和表面粗糙度预想达到高精度要求,在加工过程中必须遵循粗、精分开原则,尤其是形状复杂,精度要求较高且数量较多的零件,在精加工前对各加工面的加工余量予以去除。
铝合金切削加工条件选择及其切削加工性能改善_熊建武

2.切削条件的选择 2.1 刀 具 几 何 参 数 的 选 择 铝 合 金 的 强 度 和 硬 度 比 铜 合 金 低 , 宜 选取更大的前角( γ0) 。粗车时取 γ0=200~250, 精车时取 γ0=250~300,
25 0.03~0.1 ≤0.5 30~40 乳液 或切
20 0.03~0.1 ≤0.5 ≤30 削液
3.铝合金切削加工性能的改善
所 选 用 的 铝 合 金 及 其 硬 度 对 刀 具 寿 命 有 重 要 影 响 。铝 合 金 中 添 加 的合金元素, 既可处于固溶状态, 也可作为弥散的质点而处于不溶解 状态。不溶解状态的组分一般要比铝的基体更硬, 这些硬的质点将造 成 刀 具 的 磨 损 。如 果 通 过 固 溶 处 理 及 快 速 淬 火 使 这 些 硬 的 质 点 来 不 及 析出, 可以减轻对刀具的研磨效应。然而, 如果这些组分由子固溶缓 慢, 固溶处理后淬火不良, 或是过度时效而导致硬的质点增大, 则将加 速刀具的磨损。
拱之间填充直径 25mm 石棉绳。 2.2.9 锅 炉 顶 盖 砖 与 炉 墙 、鼓 筒 、集 箱 连 接 处 均 应 留 设 膨 胀 缝 , 并
铝合金的切削加 工 包 括 车 、铣 、钻 、镗 、锯 等 , 其 中 车 、铣 切 削 加 工 应 用 最 广 。铝 合 金 的 切 削 加 工 性 与 铜 合 金 有 许 多 相 似 之 处 。由 于 铝 合 金强度和硬度相对较低, 塑性较小, 对刀具磨损小, 且热导率较高, 使 切削温度较低, 所以铝合金的切削加工性较好, 属于易加工材料, 适于 较高切削速度切削。但铝合金熔点较低, 温度升高后塑性增大, 在高温 高压作用下, 切屑界面摩擦力很大, 容易粘刀; 特别是退火状态的铝合 金, 不易获得低的表面粗糙度。
铝合金薄壁筒形零件车削与夹具

铝合金薄壁筒形零件车削与夹具作者:吴延群来源:《科学与技术》2019年第06期摘要:为了满足铝合金薄壁零件机械加工的需要,要实现其加工系统的优化,促进其内部各个环节的有效协调,以满足日常工作。
在铝合金薄壁零件的机械加工过程中,通过对其加工模式、材料特性的有效分析,从而满足铝合金薄壁零件的加工需要,保证日常工作的质量效率的提升。
采取提高工艺系统刚度,进行多次工序间热处理,选择合理切削用量、充分冷却等措施,通过新设计的车削夹具及优化刀具角度等工艺方法的改进,提高了铝合金薄壁筒形零件的加工质量. 以薄壁筒体车端面和精车内、外圆为例,结合典型夹具结构,分析和介绍改进后的工艺方法。
关键词:铝合金薄壁筒形零件;车削夹具;切削用量;夹紧变形近年来,在国营大众机械厂的机加工生产过程中,铝合金零部件的加工数量逐渐加大,且形状越来越复杂,尺寸精度和粗糙度要求越来越高,尤其是铸造铝合金壳体类零部件,结构复杂,铸造壁薄,体积越来越大。
铝合金材料的塑性、韧性好,粘附性强,切屑不易分离,切削过程中很容易粘附在刀刃上产生刀瘤,铝合金薄壁件一般刚性较差,工件在加工中容易产生变形,铝的线膨胀系数(0.0000238)比钢的线膨胀系数(0.00001)大将近2.4倍,在切削加工过程中,热变形较大,铝合金材料的硬度偏低,在加工过程中,加工面容易划伤,很难达到表面粗糙度要求。
因此加工过程中,由于切削热及装夹变形对铝合金零部件的加工精度和表面粗糙度影响很大。
如何解决这个问题,以提高铝合金薄壁零件的成品合格率,这给机械加工工艺人员提出了新的课题。
我厂生产的一种铝合金薄壁筒形零件,长度为 400- 410 mm,直径 154 mm,壁厚为 1. 5mm,因其材料的线膨胀系数为钢的 2倍,弹性模量为钢的 1/3,加之径向刚度很低,在切削力、切削热及装夹力的作用下极易变形. 对此,除采取提高工艺系统刚度,进行多次工序间热处理,选择合理切削用量、充分冷却等措施外,还围绕减少工件所受非均匀径向力这一关键,设计了薄壁筒体加工系列夹具,工件装夹过程中,实行一次定位成型,施加较小的夹紧力,以减小人为误差,并相应调整了加工工步和刀具切削参数. 本文以薄壁筒体车端面和精车内、外圆为例,结合典型夹具结构,分析和介绍改进后的工艺方法.一、精车端面及夹具由于工件的径向刚度低,为减少工件的夹紧变形,在精加工筒体内、外圆时,宜采取轴向压筒体两端面的方式. 此时,如端面不平行,则会由于轴向压紧力的不均匀而在筒壁某处随机生成冗余的径向分力. 这种内应力失稳现象,在连续的切削过程中往往表现为肉眼可见的、非连续的数个切削表面,即筒体出现变形. 所以,对于精车内、外圆前的端面平行度,应引起足够重视并严加控制。
铝合金的切削特性分析和工艺技术研究

表 1 铝合金切削性能
铝合金 合金含量 0% ~ 0.5% 铝铜合金 0.5% ~ 5.65% > 5.65% 铝镁合金 镁硅合金 铝硅合金 铝锰合金 铝锌合金 4% ~ 13% < 8% 9.5% ~ 11.5% 切削性能 不好 较好 良好 低劣 优良 优良 低劣 低劣 良好 加入适当 Cu,Mg,切削性改善 冷变形强化,切削性改善 LC4,LC5,LC6,ZL401,ZL402 ZL101,ZL103,ZL104,ZL105,ZL110 冷变形强化,切削性良好 改善措施 冷作处理后,切削性改善 代表合金 LD2 LD5-LD10D ZL202
铝合金本身的材料性能,引起工件在切削加工中出现粘 刀、变形、振动等问题。根据铝合金的切削性能,加工过程 中需合理选择刀具参数、切削参数等,设计恰当的工艺路线, 有效避免或减缓切削过程中的问题,确保工件切削质量。 2.1 刀具材料及刀具参数的选择 铝合金在切削过程中产生的切削力较小,可适于高速
表 2 切削铝合金的刀具材料
(1) 粘刀现象。 铝合金工件硬度小 (最高 120HB 左右) , 塑性较大,切削时工件变形大;切屑与前刀面的摩擦较大, 且接触面积也大;由摩擦和变形产生的热量,使工件表面 金属变软直至溶化。再者,铝合金切屑不容易断裂,热量 不能及时带走,加剧了工件材料的溶化。这样切屑滞留在 切削刃上,容易产生粘刀现象,从而进一步形成积屑瘤, 影响切削过程。ቤተ መጻሕፍቲ ባይዱ(2)切削变形。铝合金件的抗塑性变形能力差,在切 削力的作用下,工件表层容易产生塑性变形。在切削摩擦
钨钴类硬质合金刀具
超细晶粒硬质合金刀具 (聚晶)金刚石刀具 类金刚石碳涂层刀具 陶瓷刀具 聚晶立方氮化硼刀具
除刀具材料外,刀具的几何参数是影响加工质量的一 个重要因素。切削铝合金时,选用较大的刀具前角,一般 12°~ 18°。前角过大,切削刃和刀头强度降低,不利于 刀具散热,影响刀具寿命;前角过小,切屑变形增大,易 断屑,但切屑容易划伤工件已加工表面。粗加工时可适当 减小前角,精加工时可适当增大前角。刀具(副)后角有 利于减小(副)后刀面与工件的摩擦。由于铝合金弹性模 量小、易粘刀,切削摩擦严重,宜选择较大的后角。例如, 切削铸铝合金时,后角可取 12°。对于刃倾角的选择,冲 击较大的连续切削,取较大负值的刃倾角配合较大前角, 保证切削质量;精加工时宜取正刃倾角,防止切屑划伤已 加工表面。 切削时, 选用刀刃锋利的刀具, 前刀前研磨抛光, 选择尽可能小的刀尖圆弧半径,以防止积屑瘤和切削毛刺。 2.2 切削用量的选择 切削用量包括切削速度、进给量和背吃刀量三个切削 要素,表示切削过程中切削运动的大小以及刀具切入工件 的程度,直接影响到切削力、切削热、刀具寿命、工件表 面粗糙度等。对于铝合金这种适于高速切削又容易产生粘 刀、切削变形、振动等问题的材料,合理选择切削用量显 得尤为重要。一般情况下,粗加工时选用较大的切削深度 和进给量。例如,切削 2A12 时,速度可控制在 800r/min 左右;精加工时,切削深度 0.2 ~ 0.5mm,选择较高的切削 速度和较小的进给量。 2.3 切削液的合理选择 铝合金在高速切削下产生大量的切削热,极易使材料
铝合金高速切削有限元仿真及实验研究

铝合金高速切削有限元仿真及实验研究作者:汪健明刘康来源:《软件工程》2021年第12期摘要:为了研究不同切削参数对铝合金切削过程中切削力和切削温度的影响,以铝合金7075-T651为对象,采用仿真与实验验证结合的方法,利用金属有限元切削专用软件AdvantEdge建立了铝合金7075-T651的二维正交切削仿真模型,并进行合理的工件和刀具材料参数以及本构模型设置。
通过仿真分析,研究了切削力和切削温度与进给速度以及切削深度的关系,并通过实验进行验证。
仿真和实验结果表明:在一定范围内,随着进给速度和切削深度的增大,切削力和切削温度增大。
切削铝合金7075-T651时,应采用较小的切削深度和进给速度。
关键词:AdvantEdge;铝合金7075-T651;切削力;切削温度中图分类号:TP319 文献标识码:AAbstract: In order to study the influence of different cutting parameters on cutting force and cutting temperature in cutting process of aluminum alloy, this research uses aluminum alloy 7075-T651 as the object, and takes the method of combining simulation and experimental verification as the research method. This paper proposes to use special software AdvantEdge of metal finite element cutting to establish two-dimensional orthogonal cutting simulation model of aluminum alloy 7075-T651. Reasonable workpieces, tool material parameters and constitutive model are set. Through simulation analysis, the relationship between cutting force and cutting temperature, feed speed and depth of cut are studied and verified by experiments. Simulation and experimental results show that within a certain range, with the increase of feed speed and cutting depth, cutting force and cutting temperature increase. When cutting aluminum alloy 7075-T651, smaller depth of cutting and feed rate should be used.Keywords: AdvantEdge; aluminum alloy 7075-T651; cutting force; cutting temperature1 引言(Introduction)由于鋁合金7075-T651具有高比强度和良好的热加工性能,以及高韧性和良好的耐腐蚀性,近年来在航空航天、模具加工、机械设备以及夹具中得到了越来越多的应用[1-2]。
铝合金加工的新水平——航空工业从新的切削刀具开发中获益

铝合金加工的新水平——航空工业从新的切削刀具开发中获
益
山特维克可乐满
【期刊名称】《机械工程师》
【年(卷),期】2010(000)008
【摘要】@@ 航空工业铝合金零件的加工对刀具有很高的要求,刀具在具有高性价比的同时还必须满足高质量加工的需求.由于整体硬质合金刀具具有非常锋利的切削刃和槽型,其在铝合金精加工中切削力小,并且具有容屑空间大,排屑顺畅等优点,因此整体硬质合金刀具逐渐取代了传统的高速钢刀具.
【总页数】3页(P前插14-前插16)
【作者】山特维克可乐满
【作者单位】
【正文语种】中文
【相关文献】
1.金刚石刀具切削铝合金时刀具材料和切削用量的选择 [J], 熊建武;周进;陈湘舜
2.精密切削铝合金时硬质合金刀具几何参数及切削条件对加工表面质量的影响 [J], 熊建成;罗正川
3.铝合金加工的新水平——航空工业从新的切削刀具开发中获益 [J],
4.把握新趋势打造智造时代新型切削加工——2018中国金属切削刀具产业峰会暨第四届中国金属切削刀具用户满意服务品牌评选颁奖典礼成功举行 [J], 曹婷婷;
5.航空工业难加工材料切削刀具的新发展 [J], 章宗城
因版权原因,仅展示原文概要,查看原文内容请购买。
铝合金的切削特性分析和工艺技术分析

铝合金的切削特性分析和工艺技术分析作者:郭改嫄来源:《中国科技博览》2017年第05期[摘要]铝合金作为一种复合金属材料,在人们的工作生活中有着广泛的应用。
但是铝合金材料的切削问题一直也是工艺切割制作中的一个重要问题,只有对铝合金的切削特性做出进一步的科学研究,同时在实际的工艺操作中,采用先进的工具以及合理的参数,才能保证铝合金的切削质量,提高铝合金设备的生产效率。
[关键词]铝合金;特性分析;工艺技术中图分类号:TB 文献标识码:A 文章编号:1009-914X(2017)05-0031-01引言随着我国工业的快速发展,铝合金设备的需求量进一步增大,同时对铝合金原材料进行加工时,工序也变的越来越繁杂,对于切削参数也是要求越来越精确。
因此,在工业中对铝合金材料进行切削时,应该对其切削特性以及工艺参数有更加深入的研究,保证在实际应用中,既能避免资源的浪费,又能保证工艺制作质量。
1、铝合金的切削特性分析受到铝合金本身物理特性的影响,切削的问题主要表现在这三个方面:粘刀现象、切削变形以及切削中的振动问题。
切削时,由于摩擦生热,导致铝合金材料的表面开始受热变软直到熔化。
并且由于铝合金具有很好的延展性,导致切屑不能及时掉落,受热之后就会粘在刀口上,造成粘刀现象;铝合金材料质地软,抗塑性变形能力差[1]。
在切削过程中,受热以及受到应力的作用都会导致工件变形,影响使用,造成资源的浪费;在使用刀具对铝合金材料进行切削时,会出现弹性回复的现象,这是由铝合金弹性模量小的原因造成的。
这就回导致切削刀具、给进系统的振动。
另外,切削中,残留在刀口的切屑在熔化以及脱落的过程中,都会产生不同程度的振动。
2、铝合金切削工艺技术了解到铝合金材料的自身特性,针对切削时出现的三个重要问题,对工艺流程进行设计,合理对刀具以及切削参数进行调整,才能够完成对铝合金材料的顺利切削工作,从而保证工件的质量。
2.1 选择刀具材料及参数由于铝合金相对较软的质地,切削铝合金材料时,需要的切削力度是比较小的。
铝合金高速数控铣削参数优化
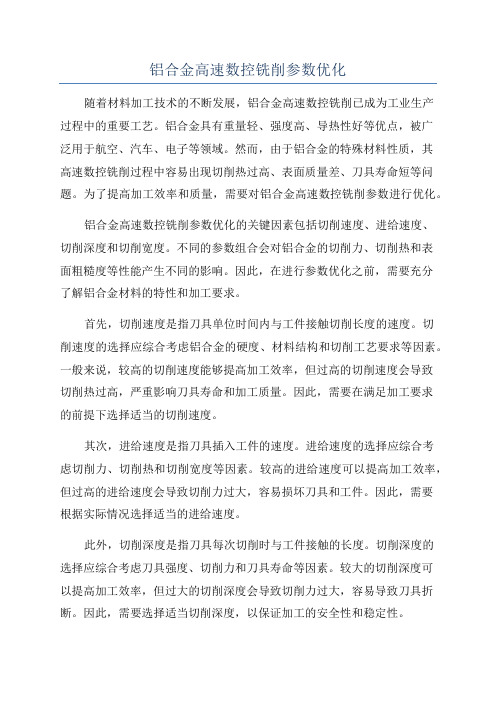
铝合金高速数控铣削参数优化随着材料加工技术的不断发展,铝合金高速数控铣削已成为工业生产过程中的重要工艺。
铝合金具有重量轻、强度高、导热性好等优点,被广泛用于航空、汽车、电子等领域。
然而,由于铝合金的特殊材料性质,其高速数控铣削过程中容易出现切削热过高、表面质量差、刀具寿命短等问题。
为了提高加工效率和质量,需要对铝合金高速数控铣削参数进行优化。
铝合金高速数控铣削参数优化的关键因素包括切削速度、进给速度、切削深度和切削宽度。
不同的参数组合会对铝合金的切削力、切削热和表面粗糙度等性能产生不同的影响。
因此,在进行参数优化之前,需要充分了解铝合金材料的特性和加工要求。
首先,切削速度是指刀具单位时间内与工件接触切削长度的速度。
切削速度的选择应综合考虑铝合金的硬度、材料结构和切削工艺要求等因素。
一般来说,较高的切削速度能够提高加工效率,但过高的切削速度会导致切削热过高,严重影响刀具寿命和加工质量。
因此,需要在满足加工要求的前提下选择适当的切削速度。
其次,进给速度是指刀具插入工件的速度。
进给速度的选择应综合考虑切削力、切削热和切削宽度等因素。
较高的进给速度可以提高加工效率,但过高的进给速度会导致切削力过大,容易损坏刀具和工件。
因此,需要根据实际情况选择适当的进给速度。
此外,切削深度是指刀具每次切削时与工件接触的长度。
切削深度的选择应综合考虑刀具强度、切削力和刀具寿命等因素。
较大的切削深度可以提高加工效率,但过大的切削深度会导致切削力过大,容易导致刀具折断。
因此,需要选择适当切削深度,以保证加工的安全性和稳定性。
最后,切削宽度是指切削刀具与工件之间的接触宽度。
切削宽度的选择应综合考虑切削力、表面粗糙度和刀具寿命等因素。
较大的切削宽度可以提高加工效率,但过大的切削宽度会导致切削力过大,降低表面质量。
因此,需要选择适当的切削宽度,以保证加工的质量和效率。
在铝合金高速数控铣削参数优化中,除了上述的关键因素外,还需要综合考虑刀具类型、冷却液使用和刀具磨损等因素。
7075_T651铝合金疲劳特性研究_韩剑

第30卷 第4期2010年8月 航 空 材 料 学 报J O U R N A LO FA E R O N A U T I C A LM A T E R I A L SV o l .30,N o .4 A u g u s t 20107075-T 651铝合金疲劳特性研究韩 剑, 戴起勋, 赵玉涛, 李桂荣(江苏大学材料科学与工程学院,江苏镇江212013)摘要:在不同的应力幅值下测试了7075-T 651铝合金的疲劳寿命,拟合试验数据得到合金S -N 曲线,估算疲劳极限为223M P a 。
用扫描电镜观察高低应力幅值下的疲劳试样断口,结果表明:合金的加工缺陷或粗大夹杂处往往为裂纹源,裂纹扩展伴随着小平面断裂的发生,高应力幅下疲劳裂纹扩展区出现犁沟和轮胎花样,而低应力幅下的疲劳裂纹扩展区中除有大量疲劳条带外,还出现了疲劳台阶和二次裂纹。
合金的疲劳瞬断区则存在着撕裂棱与等轴韧窝。
弥散分布的微小析出相对合金的疲劳性能有着积极的影响。
关键词:7075-T 651铝合金;S -N 曲线;疲劳断口D O I :10.3969/j .i s s n .1005-5053.2010.4.018中图分类号:T G 146.21 文献标识码:A 文章编号:1005-5053(2010)04-0092-05收稿日期:2009-04-21;修订日期:2009-06-16基金项目:国家863高技术研究项目(2007A A 03Z 548)作者介绍:韩剑(1984—),男,硕士研究生,从事高强铝合金组织与性能方面的研究,(E -m a i l )h a n j i a n m o o n @y a h o o .c o m .c n通讯作者:戴起勋,男,教授,博士生导师,(E -m a i l )q x d a i @u j s .e d u .c n 。
7075合金是美国较早开发的一种铝合金,是航空航天领域广泛使用的一种轻型结构材料。
7075-T6铝合金切削加工性能的影响机理研究

7075-T6铝合金切削加工性能的影响机理研究
宋爱利;岳修杰;刘俊伶;翟彦春;王鹏昊;张平;于晓
【期刊名称】《工具技术》
【年(卷),期】2022(56)11
【摘要】基于AdvantEdge软件建立了7075-T6铝合金高速切削二维模型,通过实验和仿真方法分析了切削参数对切削力、切削温度以及残余应力的影响规律,得到不同切削参数下工件表面二维和三维形貌。
研究结果表明:切削温度随切削速度的增大而增大,在切削速度达到3768mm/min后,切削温度逐渐减小;切削深度与切削温度呈正相关;当进给量较低时,切削温度随进给量的增大而增大,在进给量达到0.12mm/z后,切削温度呈现平稳的变化趋势;当切削速度较低时,工件表面粗糙度较大,表面有明显的切屑附着并伴随划伤现象;切削深度对已加工表面光洁度没有显著影响;随着进给量的增大,表面粗糙度也随之增大;切削加工后,表面残余应力主要表现为残余压应力,随切削参数的变化残余应力呈现先减小后增大再减小的变化趋势,并在40~70μm之间达到峰值。
【总页数】7页(P37-43)
【作者】宋爱利;岳修杰;刘俊伶;翟彦春;王鹏昊;张平;于晓
【作者单位】青岛黄海学院智能制造学院;烟台大学机电汽车工程学院
【正文语种】中文
【中图分类】TG146.21;TG501;TH162.1
【相关文献】
1.合金元素影响铸造铝合金切削加工性能研究
2.HBN粒径对7075-T6铝合金PEO膜结构和性能的影响
3.7075-T6铝合金干式切削表面完整性研究
4.电流对7075-T6铝合金双丝脉冲冷金属过渡焊接接头组织和力学性能的影响
5.加工参数对大应变挤出切削6061铝合金切削力影响的研究
因版权原因,仅展示原文概要,查看原文内容请购买。
高速切削加工技术的特点及应用要求_熊建武
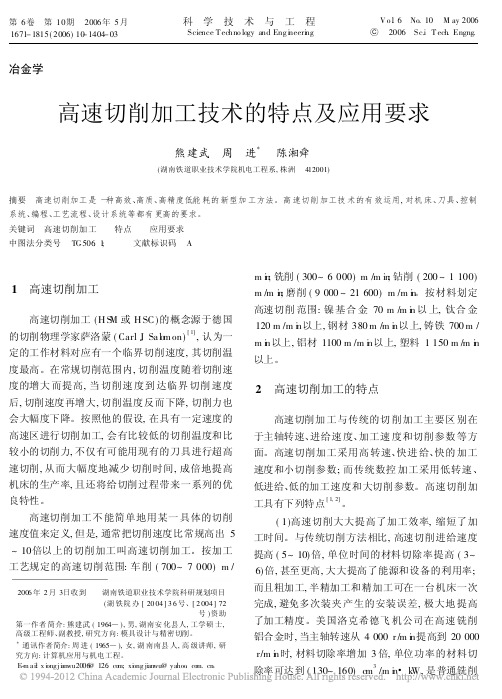
高速切削加 工与传统的切 削加工主要区 别在 于主轴转速、进给速 度、加工速 度和切削参数 等方 面。高速切削加工采用高 转速、快进 给、快的 加工 速度和小切削参数; 而传统数控 加工采用低转速、 低进给、低的加工速度和大切削参数。高速切削加 工具有下列特点 [ 1, 2] 。
Characteristics and Apply R equest of H igh Speed M achining Technology
XIONG Jianw u, ZHOU Jin* , CHEN X iangshun
( D epartmen t ofM ach in e and E lectricity E ngineering, H unan R ai lw ay Profess iona-l Techno logy C ollege, Zhuzhou 412001)
( 4) / 有利 于薄壁零 件加工 0。 由于切 削速度 高, 切削参数小, 切削力降低 30% ~ 90% , 尤其是径 向力大幅减小, 特别适用于薄壁细肋件的高速精密 加工。国外采用数控 高速切削加工技 术加工铝合 金、钛合金薄壁零件的最小壁厚可达 0. 005 mm。
( 5) 高速切削可加工各种难加工材料。对于镍 基合金和钛合金使用传统加工 方法, 切 削温度高, 刀具磨损严重, 而采用高速 切削加工, 切削速度可 达 ( 100- 1 000) m /m in, 可有效减少刀具磨损, 提高 加工质量。对于硬脆材料和高塑性材料, 采用高速 切削加工亦可得到较满意的加工质量。
m in; 铣削 ( 300~ 6 000) m /m in; 钻削 ( 200 ~ 1 100) m /m in; 磨削 ( 9 000 ~ 21 600) m /m in。按材料划定 高速切削 范围: 镍 基合 金 70 m /m in 以 上, 钛合 金 120 m /m in以上, 钢材 380 m /m in以上, 铸铁 700 m / m in以上, 铝材 1100 m /m in以上, 塑料 1 150 m /m in 以上。
高效车削铝合金刀具结构设计及切削性能研究
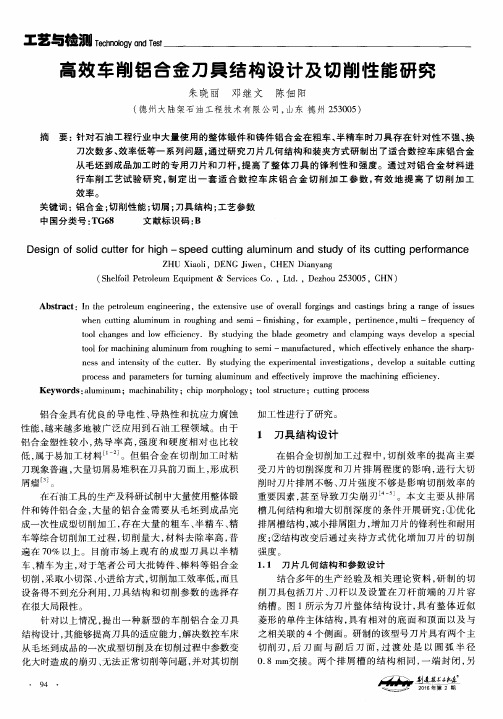
A bstract:In the petroleum engineering,the extensive use of overall forgings and castings bring a range of issues when cutting alum inum in roughing and semi— finishing,for example,peainence,multi—frequency of tool changes and low efficiency. By studying the blade geometry and clamping ways develop a special tool fo r m achining aluminum from roughing to semi— manufactured,which effectively enhance the sharp— ness and intensity of the cutter. By studying the experimental investigations, develop a suitable cutting process and parameters fo r turning alum inum and effectively improve the m achining efi ciency.
关键 词 :铝 合金 ;切 削性能 ;切 屑 ;刀具结 构 ;工艺 参数 中国分 类号 :TG68 文献标 识码 :B
Design of solid cutter for high —speed cutting aIum inum and study of its cutting performance ZHU Xiaoli,DENG Jiwen,CHEN Dianyang
7075-T651 铝合金铣削参数与刀具几何参数的多目标同步优化方法

第51卷第4期表面技术2022年4月SURFACE TECHNOLOGY·263·7075-T651铝合金铣削参数与刀具几何参数的多目标同步优化方法陈良骥1,2,魏子森1(1.天津工业大学 机械工程学院,天津 300387;2.桂林理工大学 机械与控制工程学院,广西 桂林 541006)摘要:目的降低铣削力和铣削热,以减小7075-T651铝合金工件的加工变形,并提高金属去除率。
方法提出一种面向2类参数(铣削参数和刀具几何参数:转速、进给量、径向切深、轴向切深、前角、后角)旨在实现多个目标(铣削力、铣削温度和金属去除率)同步优化的方法。
基于偏最小二乘法回归模型和7075- T651铝合金工件铣削有限元仿真模型,建立关于2类参数的铣削力、铣削温度及金属去除率的函数关系,并采用8种典型多目标优化算法进行求解。
结果通过Pareto前沿曲面的可视化和HV性能指标,筛选出适合解决本文问题的优化求解算法,获得的部分铣削参数,转速为5 966.30 r/min,进给量为0.08 mm/z,径向切深为4.53 mm,轴向切深为4.99 mm。
刀具几何参数分别为前角17.95°、后角2.00°,此时对应的铣削力为232.12 N、铣削温度为22.56 ℃、金属去除率为33.08 mm3/min。
结论上述优化结果可实现较低铣削力和铣削温度以及较高金属去除率等综合控制目标,对7075-T651铝合金工件铣削加工时降低工件变形量和提高加工效率等方面具有实际应用价值。
关键词:铣削参数;刀具几何参数;铣削力;铣削温度;多目标优化中图分类号:TG714 文献标识码:A 文章编号:1001-3660(2022)04-0263-12DOI:10.16490/ki.issn.1001-3660.2022.04.027Multi-objective Synchronous Optimization Method for Milling Parameters and Tool Geometric Parameters of 7075-T651 Aluminum AlloyCHEN Liang-ji1,2, WEI Zi-sen1(1. School of Mechanical Engineering, Tiangong University, Tianjin 300387, China; 2. College of Mechanical andControl Engineering, Guilin University of Technology, Guangxi Guilin 541006, China)ABSTRACT: This paper aims to reduce the milling force and milling heat in order to reduce the deformation of the 7075-T651 aluminum alloy workpiece and improve the metal removal rate. In this paper, a method for simultaneous optimization of two kinds of parameters (milling parameters and tool geometric parameters: rotation speed, feed rate, radial depth of cut, axial depth收稿日期:2021-04-27;修订日期:2021-10-15Received:2021-04-27;Revised:2021-10-15基金项目:广西自然科学基金(2021GXNSFAA220019);国家自然科学基金(52075110)Fund:Guangxi Natural Science Foundation (2021GXNSFAA220019); The National Natural Science Foundation of China (52075110)作者简介:陈良骥(1978—),男,博士,教授,主要研究方向为复杂曲面CAD/CAM、五轴CNC精密轨迹控制和精密加工。
高速铣削铝合金7055铣削力和铣削温度的仿真研究

高速铣削铝合金7055铣削力和铣削温度的仿真研究田荣鑫;姚倡锋;武导侠【摘要】采用有限元分析软件AdvantEdge模拟了航空铝合金7055高速铣削过程,获得了单个刀齿高速加工中铣削力变化曲线,预测了不同切削时间下工件及刀具上的温度分布,获得了刀具前刀面和后刀面的温度分布曲线;建立了高速铣削参数对铝合金7055铣削力和铣削温度的影响曲线,可辅助优化切削加工参数,有助于减小切削过程中刀具的磨损,改善刀具切削状态,提高刀具使用寿命.【期刊名称】《航空制造技术》【年(卷),期】2016(000)006【总页数】5页(P67-71)【关键词】铝合金7055;高速铣削;有限元仿真;铣削力;铣削温度【作者】田荣鑫;姚倡锋;武导侠【作者单位】西北工业大学现代设计与集成制造技术教育部重点实验室,西安710072;西北工业大学现代设计与集成制造技术教育部重点实验室,西安710072;西北工业大学现代设计与集成制造技术教育部重点实验室,西安710072【正文语种】中文高强度铝合金由于其密度低、比强度高、耐磨性好、加工性能好以及焊接性能良好等特点,被广泛应用于航空航天等领域[1]。
但是铝合金材质较软,加工易产生热变形,容易粘刀,形成积屑瘤;线膨胀系数大,装夹和加工时容易引起变形,影响尺寸精度。
使用铝合金制造飞机蒙皮、翼梁、隔框、长桁和起落架时,加工量非常大,而且许多精密部件需减小结构上的加工变形,铝合金大型壁板的加工变形问题已成为制约航空业高速发展的一大问题。
而加工变形主要是由切削过程中的切削力和切削温度引起的,所以研究切削过程中的切削力和切削温度很有必要。
国内外学者对铝合金高速铣削过程中的铣削力和铣削温度进行了大量的试验研究[2-4]。
然而,随着数值分析方法的发展及其在制造业中应用的推广,Ng等[5]运用有限元分析方法研究了刀具磨损对工件的温度和剪应力分布的影响。
由Strenkowski等[6]提出的正交切削的欧拉有限元模型可以对工件、切屑和刀具的温度进行预测。
铝合金的切削性能的简要研究
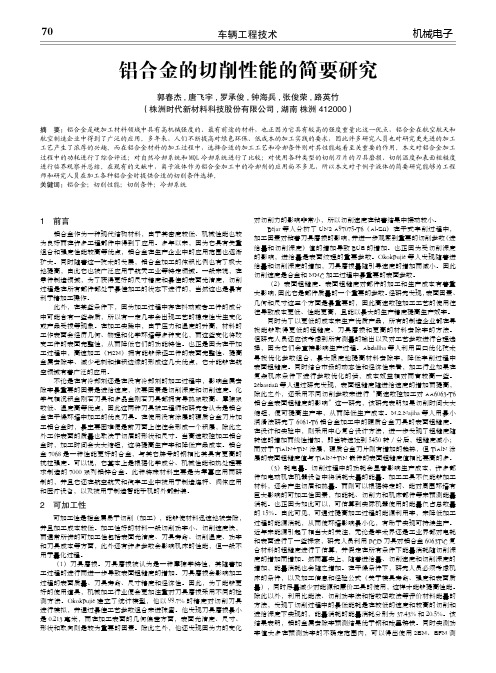
车辆工程技术70机械电子1 前言 铝合金作为一种现代结构材料,由于其密度较低、机械性能也较为良好而在许多工程部件中得到了应用。
多年以来,因为它具有失重组合和强度性能较高等优点,铝合金在生产企业中的应用范围也逐渐扩大。
同时随着这一技术的发展,铝合金加工的体积比例也有了极大地提高,由此它也被广泛应用于航天工业等特定领域。
一般来说,在零件制造领域,为了获得更好的尺寸精度和最佳的表面光洁度,切削过程是在所有部件都处于最佳加工的状态下进行的,当然这也是最有利于精加工操作。
此外,在某些条件下,因为加工过程中存在抖动或者工件的成分中可能含有一些杂质,所以有一定几率会出现工艺的稳定性发生变化或产品受损等现象。
在加工实践中,由于压力和温度的升高,材料的工作表面会经历几何、物理和化学环境等多种变化,而这些变化将改变工件的表面完整性,从而降低它们的功能特性。
也正是因为在干加工过程中,高速加工(HSM)拥有能够保证工件的表面完整性、提高金属去除率、减少毛刺和堆积边缘的形成这几大优点,它才能够在航空领域有着广泛的应用。
不论是在有冷却剂还是在没有冷却剂的加工过程中,影响金属去除率最重要的因素是进给速度,次要因素是切削深度和切削速度。
化学气相沉积金刚石刀具和多晶金刚石刀具都拥有导热系数高、摩擦系数低、温度高等优点,因此这两种刀具被工程师和研究者认为是铝合金在干燥环境中加工的优良刀具。
在使用没有涂层的硬质合金刀片加工铝合金时,最主要困难便是前刀面上往往会形成一个积层,除此之外工作表面的质量也取决于切屑的形状和尺寸。
当高速数控加工铝合金时,加工时间会大大缩短,这将提高生产率和降低产品成本。
铝合金7068是一种性能更好的合金,与其它牌号的钢相比其具有更高的抗拉强度。
可以说,它基本上是根据化学成分、机械性能和热处理要求制造的7000系列铝锌合金。
此种特殊材料主要是为军事应用而研制的,并且它还在航空航天和汽车工业中被用于制造连杆、阀体应用和医疗设备,以及被用于制造智能手机的外部封装。
铝合金及其切削加工性

铝合金及其切削加工性一、铝合金以铝为基的合金总称。
主要合金元素有Cu丶Si丶Mg丶Sn,次要有镍丶钛丶铬丶锂等。
铝合金密度低,塑性好可加工成型材,具有优良导电性丶导热性和抗腐蚀性,添加一定元素形成的合金在保持纯铝质轻等优点的同时还能具有较高的强度。
这样使得其“比强度”胜过很多合金钢,成为理想的结构材料,广泛用于机械制造丶运输机械丶动力机械及航空工业等方面,飞机的机身丶蒙皮丶压气机等常以铝合金制造,以减轻自重。
采用铝合金代替钢板材料的焊接,结构重量可减轻50%以上。
铝合金加工方式分类:按照加工方法分形变铝合金和铸造铝合金。
1、形变铝合金:形变铝合金又分为不可热处理强化型铝合金和可热处理强化型铝合金,其强度和硬度都不高。
切削加工的难度在于有较高的塑性,切削时易形成积屑瘤,难以获得良好表现,通过热处理来提高机械性能,只能通过冷加工变形来实现强化,它主要包括高纯铝丶工业高纯铝丶工业纯铝以及防锈铝等。
2、铸造铝合金:铸铝合金塑性低,伸长率一般在4%以下,不适合压力加工,大多以切削加工。
硅铝合金的铸造性能好,力学优良,是最广泛应用的铸造铝合金。
其中硅铝合金切削加工性与硅含量有关,其含量越高对刀具磨损越严重加工性能越差。
铸造铝合金可以通过淬火和时效等热处理手段来提高机械性能,它包括硬铝丶锻铝丶超硬铝和特殊铝合金等。
二、切削加工性工业铝合金零件的加工对刀具有很高的要求,尤其是航空工业中的铝合金,刀具在具有高性价比的同时还必须满足高质量加工的需求。
由于整体硬质合金刀具具有非常锋利的切削刃和槽型,其在铝合金精加工中切削力小,并且具有容屑空间大,排屑顺畅等优点,因此整体硬质合金刀具逐渐取代了传统的高速钢刀具。
由于铝合金强度和硬度相对较低,塑性较小,对刀具磨损小,且热导率较高,使切削温度较低,所以铝合金的切削加工性较好,属易加工材料,切削速度较高,适于高速切削。
但铝合金熔点较低,温度升高后塑性增大,在高温高压作用下,切削界面摩擦力很大。
铝铣削的技巧

铝铣削的技巧
以下是铝铣削的几个技巧:
1. 选择合适的材料。
铝材质通常具有良好的可加工性和导热性,但不同的铝合金材质处理难度不同,需根据实际情况选择合适的材料。
2. 选择合适的铣刀。
通常使用高速钢铣刀和硬质合金铣刀,也可以使用涂层铣刀,以提高切削速度和效率。
3. 选择合适的冷却液。
铝材质具有良好的导热性,易产生高温,因此需要使用适当的冷却液进行冷却,以保护刀具和工件。
4. 调整合适的加工参数。
包括切削速度、进给速度和切削深度等。
5. 注意切削方式。
铝材质容易产生毛刺,需要注意合理的切削方式,避免毛刺产生。
6. 注意刀具的维护。
定期检查刀具的磨损和锋利度,及时更换刀具。
7. 合理固定工件。
铝材质较轻,易移动,需要采用合适的夹持方式固定工件,防止移位和形变。
- 1、下载文档前请自行甄别文档内容的完整性,平台不提供额外的编辑、内容补充、找答案等附加服务。
- 2、"仅部分预览"的文档,不可在线预览部分如存在完整性等问题,可反馈申请退款(可完整预览的文档不适用该条件!)。
- 3、如文档侵犯您的权益,请联系客服反馈,我们会尽快为您处理(人工客服工作时间:9:00-18:30)。
用硬质合金车刀粗车铝合金时, 一般可不用冷却润滑。用高速钢 刀 具 车 削 铝 合 金 时 可 用 切 削 液 冷 却 润 滑 。当 切 削 进 给 量 较 大 和 粗 车 铝 硅合金时, 可用 5%的乳化液, 精 加 工 时 由 于 铝 容 易 和 氢 起 化 学 作 用 , 使工件表面产生很细的针孔, 不宜采用水剂切削液。为减小摩擦和粘 刀, 一般常用煤油或煤油加全损耗系统用油( 机油) 的混合油作切削 液。
按铝合金的切削性能, 可将铝合金分为两类: Ⅰ类是指工业纯铝 和硬度小于 80HB 的退火状态的铝合金, Ⅱ类是指淬火时效状态的变 形铝合金。表 1~表 3 为铝合金的典型切削参数。
表 1 铝合金的典型切削参数
操 刀具 铝合金 切削速度 副后 纵向前 进给量 切削深 冷却 作 材料 材料 ( m/min) 角 ( 0) 角( 0) ( mm/r) 度( mm) 剂
铝合金的切削加工性随加入的合金元素及硬度的( 下转第 78 页)
24
科技信息
○机械与电子○
SCIENCE & TECHNOLOGY INFORMATION
2007 年 第 26 期
锅炉安装中膨胀缝的留设
李德强 丁兆飞 ( 临沂市锅炉压力容器检验所 山东 临沂 276003)
【摘 要】简述锅炉安装中炉墙膨胀缝留设的基本原则, 叙述膨胀缝的留设方法, 阐明膨胀缝的留设的重要性。 【关键词】锅炉; 膨胀缝; 留设
铝合金的切削加 工 包 括 车 、铣 、钻 、镗 、锯 等 , 其 中 车 、铣 切 削 加 工 应 用 最 广 。铝 合 金 的 切 削 加 工 性 与 铜 合 金 有 许 多 相 似 之 处 。由 于 铝 合 金强度和硬度相对较低, 塑性较小, 对刀具磨损小, 且热导率较高, 使 切削温度较低, 所以铝合金的切削加工性较好, 属于易加工材料, 适于 较高切削速度切削。但铝合金熔点较低, 温度升高后塑性增大, 在高温 高压作用下, 切屑界面摩擦力很大, 容易粘刀; 特别是退火状态的铝合 金, 不易获得低的表面粗糙度。
充。 2.2.4 炉墙和拱顶的膨胀缝除了填充石棉绳 外 , 拱 顶 上 部 缝 的 外
露部位要用一层平砌砖覆盖。 2.2.5 炉内的隔墙或折焰墙等部位的膨胀缝 需 要 伸 入 墙 内 , 应 伸
入 90- 95mm 为宜。 2.2.6 悬 挂 拱 通 常 采 用 靠 近 两 侧 墙 砖 列 的 侧 面 和 底 部 留 设 膨 胀
科技信息
○本刊重稿○
SCIENCE & TECHNOLOGY INFORMATION
2007 年 第 26 期
铝合金切削加工条件选择及其切削加工性能改善
熊建武 周 进 刘楚玉 ( 湖南铁道职业技术学院机电工程系 湖南 株洲 412001)
【摘 要】铝合金的切削加工主要是车、铣加工, 本文阐述了刀具材料的选择、典型切削参数以及改善铝合金切削加工性能的措施。 【关键词】铝合金; 刀具材料; 典型切削参数; 切削加工性能
缝, 缝内填充石棉绳。 2.2.7 砌体与钢架立柱、横梁等构件间应留设膨胀 缝 , 使 金 属 在 受
热时能自由膨胀。一般金属面与耐火砌体的接触面应铺贴石棉板。 2.2.8 炉 墙 内 管 子 、 集 箱 的 膨 胀 缝 必 须 在 管 子 上 缠 绕 直 径 10-
20mm 的石棉绳; 墙内铸件的膨胀缝在搁条的四周用 10- 15mm 的石棉 板作填充材料; 墙内鼓筒的膨胀缝要沿其四周砌筑圆形拱, 在鼓筒与
切削速度 ( m/min)
进给量 切削长屑合金的切 切削短屑合金的切
( mm/r)
削深度( mm)
削深度( mm)
≤3000 0.02~0.1
0.02~0.3
0.02~0.6
800~1400 0.02~0.1
0.02~0.3
0.02~0.6
操 刀具 作 材料
高速 钢
粗 铣
硬质 合金
高速 钢
精 铣
硬质 合金
2.膨胀缝的留设 2.1 膨胀缝的留设的基本原则 2.1.1 形体不长的炉子, 通常是依靠砖缝泥 浆 和 空 隙 的 压 缩 来 补
偿膨胀。 2.1.2 砌筑高温加热炉或形体大的炉子, 依 靠 灰 缝 的 收 缩 来 补 偿
炉墙的膨胀是不够的, 因而必须采取特殊的预防措施, 防止炉墙因膨 胀而破坏。为此, 在砌筑时, 要留设膨胀缝, 即留出炉墙受热后膨胀的 余量。
1.前言
2.2.3 膨 胀 缝 的 宽 度 通 常 为 20mm, 采 用 直 径 25mm 的 石 棉 绳 填
在锅炉安装过程中, 不但要求其流畅性、准确性、严密性、可靠性、 经济性, 而且要求其部件热膨胀灵活自由。由于锅炉安装工作是在常 温条件下进行的, 而锅炉在正常参数下运行时, 各部位材质不同、受热 不 同 、膨 胀 方 向 不 同 , 因 此 , 锅 炉 在 使 用 过 程 中 的 膨 胀 性 是 十 分 复 杂 的。所以对膨胀部位要留有足够的间隙, 保证膨胀时能灵活自由的胀 出或收缩时能回到相应温度条件的胀值位置。
切削刃要求磨得锋利, 刀具表面粗糙度值要小。由于铝合金的弹性模 量较小( 约为 70GPa) , 只有 45 钢 的 1/3 左 右 , 由 工 件 弹 性 恢 复 产 生 的 后面摩擦更为严重。所以, 应选取较大的后角( α0) , 粗车时取 α0=80~ 100, 精车 时 取 α0=100~120, 刃 倾 角 ( λs) 一 般 取 λs=00~100, 粗 加 工 取 小值, 精加工时取大值。
25 0.03~0.1 ≤0.5 30~40 乳液 或切
20 0.03~0.1 ≤0.5 ≤30 削液
3.铝合金切削加工性能的改善
所 选 用 的 铝 合 金 及 其 硬 度 对 刀 具 寿 命 有 重 要 影 响 。铝 合 金 中 添 加 的合金元素, 既可处于固溶状态, 也可作为弥散的质点而处于不溶解 状态。不溶解状态的组分一般要比铝的基体更硬, 这些硬的质点将造 成 刀 具 的 磨 损 。如 果 通 过 固 溶 处 理 及 快 速 淬 火 使 这 些 硬 的 质 点 来 不 及 析出, 可以减轻对刀具的研磨效应。然而, 如果这些组分由子固溶缓 慢, 固溶处理后淬火不良, 或是过度时效而导致硬的质点增大, 则将加 速刀具的磨损。
用 金 刚 石 。 精 加 工 时 、为 避 免 由 于 铝 与 陶 瓷 的 化 学 亲 和 力 而 产 生 粘 结 ( 切屑氧化即生成 Al2O3) , 一般不采用陶瓷刀具。
2.切削条件的选择 2.1 刀 具 几 何 参 数 的 选 择 铝 合 金 的 强 度 和 硬 度 比 铜 合 金 低 , 宜 选取更大的前角( γ0) 。粗车时取 γ0=200~250, 精车时取 γ0=250~300,
拱之间填充直径 25mm 石棉绳。 2.2.9 锅 炉 顶 盖 砖 与 炉 墙 、鼓 筒 、集 箱 连 接 处 均 应 留 设 膨 胀 缝 , 并
高速 Ⅰ 200~400 9~12 30~40 ≤1 3~15
无
钢 粗
Ⅱ 100~250 8~10 20~30 0.2~0.5 3~15
无
车 硬质
Байду номын сангаас
Ⅰ 600~1200 7~10 20~30 0.3~0.6 3~15
无
合金 Ⅱ 200~400 7~10 10~20 0.25~0.6 3~15
无
Ⅰ 400~900 8~10 40~50 0.05~0.3 0.3~2.5 乳液
某 化 工 企 业 2006 年 新 建 运 行 了 一 大 型 化 工 项 目 , 其 配 套 的 35 吨/小时的余热锅炉运行不到一年, 因为未留设膨胀缝, 造成炉墙局部 倒塌或开裂, 无法保证该锅炉的安全运行, 被迫系统停车进行检修, 直 接及间接经济损失达 100 多万元/天。在现场看到的情景令人 触 目 惊 心, 该余热锅炉炉墙损坏之严重令人难以置信。从这个现实可以看出, 锅炉炉墙膨胀缝的留设是多么的重要。
高速
钢 精
Ⅱ
200~500
7~9
30~40
0.03~ 0.25
0.3~2.5
或切 削液
车
硬质 Ⅰ
≤2400 8~10 20~30 ≤0.15 0.3~2.5 乳液或
合金 Ⅱ 250~700 7~9 10~20 0.05~0.1 0.3~2.5 切削 液
铝合金 材料
Ⅰ Ⅱ
表 2 金刚石刀具的典型切削参数
表 3 铝合金的典型铣削参数
铝合 金材
料
铣削速 度
( m/min)
主间 侧倾
铣削
进给量
隙角 角
深度
( 0) ( 0) ( mm/r) ( mm)
螺旋 线角 ( 0)
冷却 剂
Ⅰ 300~600 8 Ⅱ 150~400 6
25 0.1~0.5 2~20 30~40 无 20 0.1~0.5 2~20 ≤30 无
2.2 刀具切削表面粗糙度和磨削纹方向的选择 刀具切削表面条 件对于控制刀具磨损起重要作用。切削加工时, 硬度较低的铝合金( 也 包括某些较硬的铝合金) , 往往会焊在刀具表面上, 并形成积屑瘤。这 种积屑瘤将构成一个新的切削表面, 从而产生不稳定的切屑和较差的 表面粗糙度, 并引起刀具过热和过早失效。
改进的措施是在切屑流动的方向上磨削和超精研磨刀具, 使切屑 易于在刀具表面上滑移。还可加宽出屑槽, 使切屑流动畅通。但每道工 序对于刀具修磨费用应进行经济核算, 并和总的加工费用进行平衡。
2.3 切削进给量 切削进给量要足够大, 以保证刀具切削, 而不是 与工件摩擦。由于铝合金的硬度较低, 且导热性较好, 宜进行较高速度 切削。与车削 45 钢相比, 车削硬铝的切削速度可提高 3 倍左右。工件、 刀具和夹具必须安装牢固, 刀具应尽可能与工件接触于中心线。