设备各种无损检测方案
无损检测施工方案(高效)
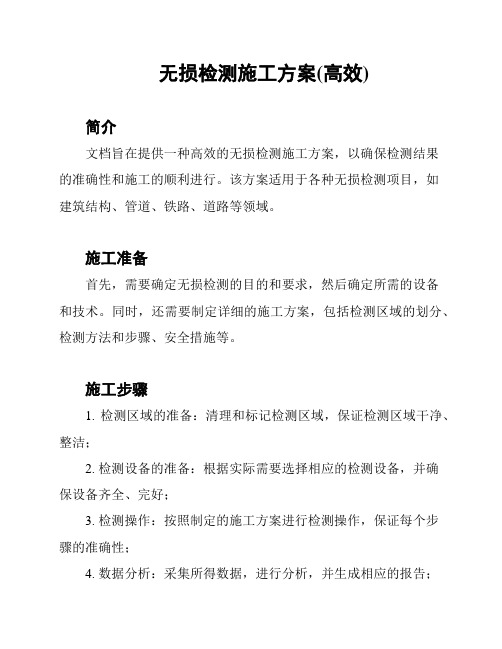
无损检测施工方案(高效)
简介
文档旨在提供一种高效的无损检测施工方案,以确保检测结果
的准确性和施工的顺利进行。
该方案适用于各种无损检测项目,如
建筑结构、管道、铁路、道路等领域。
施工准备
首先,需要确定无损检测的目的和要求,然后确定所需的设备
和技术。
同时,还需要制定详细的施工方案,包括检测区域的划分、检测方法和步骤、安全措施等。
施工步骤
1. 检测区域的准备:清理和标记检测区域,保证检测区域干净、整洁;
2. 检测设备的准备:根据实际需要选择相应的检测设备,并确
保设备齐全、完好;
3. 检测操作:按照制定的施工方案进行检测操作,保证每个步
骤的准确性;
4. 数据分析:采集所得数据,进行分析,并生成相应的报告;
5. 结果确认:针对检测结果进行确认,并在必要时进行重复检测;
6. 报告编制:根据检测结果编制详细的报告,报告中应包含检测目的、方法、结果等内容。
安全措施
在无损检测施工中,需要采取一系列安全措施,以确保施工过程中的安全性。
这些措施包括:
- 严格遵守安全操作规程;
- 设立安全防护措施,保证施工地点的安全性;
- 做好防腐、防火等工作,确保施工地点的安全性。
结论
该高效的无损检测施工方案,提供了详细的施工步骤和安全措施,以确保检测结果准确、施工过程安全。
在实际应用中,需要结合具体的项目和实际情况进行调整,以达到最佳的检测效果。
无损检测方案

无损检测方案本工程无损检测方法有RT(射线)探伤和UT(超声波)探伤。
一、无损检测委托程序二、无损检测程序管道检验按规范和图纸要求进行探伤。
管道的检测程序如下:三、无损检测方案1、作业前的准备检测时机:特种材质焊缝,必须在焊接完成经过24小时以后,方可进行检测作业。
检测前应确认材质和厚度,且经外观检查合格后才能进行操作。
2、无损检测人员要求⑴参与本工程的无损检测人员应具备国家相关部门颁发的检测资格证书。
⑴无损检测人员在实施检验前,须了解和熟悉有关监察规程、验收标准、技术文件要求,熟悉被检工件的规格、材质及其制造工艺、焊接工艺、检测工艺。
⑴I级检测资格人员只能在II级或II级以上资格人员指导和监督下从事检测操作,检测结果评定和报告签发及审核由II级或III级人员承担。
⑴检测人员应认真做好设备的维护、保养工作,执行安全防护制度。
⑴检测人员的校正视力不低于1.0,并要求评片人员距离400mm 能读出高为0.5mm,间隔0.5mm的一组印刷体字母。
⑴无损检测人员要牢固树立“质量第一”的观念,做到不漏检、不误判,准确执行检测标准。
⑴无损检测人员严格按照委托要求进行检测,做到检测比例执行率100%,扩探比例执行率100%。
3、射线检测方案⑴检测方法:采用X射线机进行双壁单影、双壁双影、单壁单影透照检测;检测设备:200/250/300KV X射线机;底片类型:JB4730-94;象质计:选用JB/T7902-99规定的R10系列线型金属丝象质计;增感屏:铅箔增感屏。
暗室处理:手工冲洗⑴检测工作流程⑴技术要求⑴底片标识底片上的显示包括工程编号、设备号或管道号、焊缝号、片位号、焊工号、规格厚度、返工标记、检验日期等。
所有标识紧密放置于工件表面与底之间,底片上的铅字影像齐全工整,并距离焊道影像5mm 以上。
如果业主或监理对焊口底片标识有进一步的要求,则应根据业主或监理要求补充标识内容和方式。
⑴象质计的放置采用单影法透照,线型象质计置于底片有效片长的1/4处,钢丝横跨焊缝并与焊缝方向垂直,每张底片都应显示象质计。
无损检测作业实施方案

无损检测作业实施方案一、前言。
无损检测是一种非破坏性检测方法,可以在不破坏被测物体的情况下,通过各种检测技术手段获取被测物体内部的缺陷信息,对被测物体的完整性和可靠性进行评估。
本文档旨在制定一套无损检测作业实施方案,以确保无损检测工作的准确性和高效性。
二、作业准备。
1. 设备准备,确保无损检测设备处于良好状态,检查设备的电源、传感器、探头等部件是否完好,必要时进行校准和调试工作。
2. 人员准备,安排有经验的无损检测人员进行作业,确保其具备相关的资质和证书,并了解被测物体的特性和检测要求。
3. 环境准备,选择适宜的环境进行无损检测作业,确保作业场所的温度、湿度等环境因素符合检测要求。
三、作业实施。
1. 检测方案制定,根据被测物体的特性和检测要求,制定相应的无损检测方案,包括选择合适的检测技术和方法,确定检测位置和方向等。
2. 作业流程安排,按照检测方案制定作业流程,明确各项作业步骤和责任人,确保每个环节的顺利进行和无差错。
3. 检测数据采集,严格按照检测方案和流程进行数据采集工作,确保数据的准确性和完整性,避免漏检和误检情况的发生。
4. 检测结果分析,对采集到的数据进行分析和评估,判断被测物体的完整性和可靠性,及时发现并记录缺陷信息。
5. 报告编制,根据检测结果编制检测报告,清晰地呈现检测数据和分析结论,提出相应的建议和措施。
四、作业总结。
1. 检测记录保存,将检测过程中采集到的数据和检测报告进行保存,建立完整的档案记录,为后续的评估和跟踪提供依据。
2. 作业经验总结,对本次无损检测作业进行总结和经验归纳,发现存在的问题和不足之处,并提出改进措施。
3. 资料交接和归档,将作业相关资料进行交接和归档,确保资料的完整性和安全性,为后续的工作提供支持。
五、作业安全。
1. 作业人员安全,无损检测作业人员要严格遵守相关的安全操作规程,正确使用检测设备,确保个人安全和设备完好。
2. 环境安全,作业场所要符合安全要求,确保无损检测作业不会对周围环境和人员造成影响。
无损检测技术的方案

无损检测技术的方案无损检测技术是一种非破坏性检测方法,主要用于检测材料的内部、表面缺陷或变形,并评估其质量和可用性。
在工业生产中,无损检测技术被广泛应用于航空航天、汽车制造、电力设备、石油化工等行业,以提高产品质量和安全性。
以下是一种基于超声波的无损检测技术的方案,用于检测金属材料的内部缺陷:1.设备准备准备一台超声波无损检测设备,其中包括超声发射器、接收器、探头和显示屏。
确保设备的电源和连接线路正常工作。
2.样本准备选择一块需要检测的金属材料样本,并清洁其表面,以确保无杂质影响检测结果。
3.设定检测参数根据样本的材料和尺寸,设定适当的超声波频率、脉冲宽度和探头角度等参数。
这些参数的设置会根据不同材料而异,需要根据实际情况进行调整。
4.发送超声波将超声波发射器固定在样本的一个位置,并发送超声波信号。
超声波信号会穿过材料并被内部缺陷或界面反射回来。
5.接收反射信号使用接收器接收反射回来的超声波信号,并将其转换为电信号。
接收器可以检测信号的振幅和时间延迟等参数。
6.信号处理将接收到的信号发送至信号处理模块,根据设定的参数进行信号增益、滤波和调幅等处理。
处理后的信号会显示在屏幕上,供操作员进行分析。
7.缺陷评估根据显示屏上的信号,操作员可以判断材料中是否存在缺陷,以及缺陷的类型、位置和大小。
根据实际需要,还可以进行数据记录和图像保存,以便后续分析和比对。
8.结果判定根据缺陷的大小和位置,结合材料的使用要求和标准,对检测结果进行判定。
如果缺陷超过了材料的承载能力或使用要求,则需要采取相应措施修理、更换或提前淘汰。
超声波无损检测技术的优点是操作简单、快速,可以在材料内部进行全方位的检测。
然而,特定材料的无损检测技术还需根据实际情况进行调整。
因此,在实际应用中需要根据材料的特点和要求进行相应的设备选择和参数调整。
无损检测施工方案
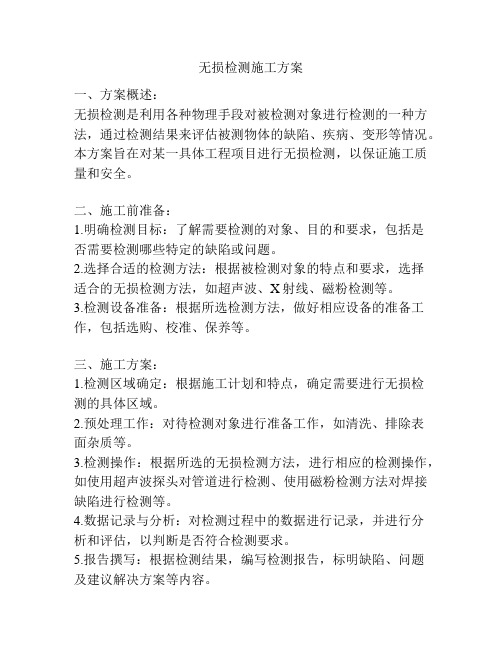
无损检测施工方案一、方案概述:无损检测是利用各种物理手段对被检测对象进行检测的一种方法,通过检测结果来评估被测物体的缺陷、疾病、变形等情况。
本方案旨在对某一具体工程项目进行无损检测,以保证施工质量和安全。
二、施工前准备:1.明确检测目标:了解需要检测的对象、目的和要求,包括是否需要检测哪些特定的缺陷或问题。
2.选择合适的检测方法:根据被检测对象的特点和要求,选择适合的无损检测方法,如超声波、X射线、磁粉检测等。
3.检测设备准备:根据所选检测方法,做好相应设备的准备工作,包括选购、校准、保养等。
三、施工方案:1.检测区域确定:根据施工计划和特点,确定需要进行无损检测的具体区域。
2.预处理工作:对待检测对象进行准备工作,如清洗、排除表面杂质等。
3.检测操作:根据所选的无损检测方法,进行相应的检测操作,如使用超声波探头对管道进行检测、使用磁粉检测方法对焊接缺陷进行检测等。
4.数据记录与分析:对检测过程中的数据进行记录,并进行分析和评估,以判断是否符合检测要求。
5.报告撰写:根据检测结果,编写检测报告,标明缺陷、问题及建议解决方案等内容。
四、施工要求:1.施工人员:由经过专业培训的无损检测人员进行,确保操作规范、准确性和安全性。
2.操作环境:提供适合的操作环境,如保持室温、降低干扰等,以确保检测过程的准确性。
3.保养维护:保养和维护无损检测设备,确保设备的正常运行。
4.安全防护:在无损检测过程中,使用符合要求的个人防护设备,确保施工人员的安全。
五、质量控制:1.制定质量控制计划:在施工前制定无损检测质量控制计划,包括检测要求、检测方法、操作标准等内容。
2.质量检查:在施工过程中进行质量检查,确保操作符合要求,并及时纠正不合格操作。
3.重要数据备份:对重要数据进行备份,以防止数据丢失造成损失。
六、施工管理:1.组织施工人员:组织好无损检测人员的工作安排和任务分配,确保施工进度和质量。
2.施工进度控制:配合工程进度安排,合理安排无损检测施工时间,确保无损检测工作的顺利进行。
无损检测方案
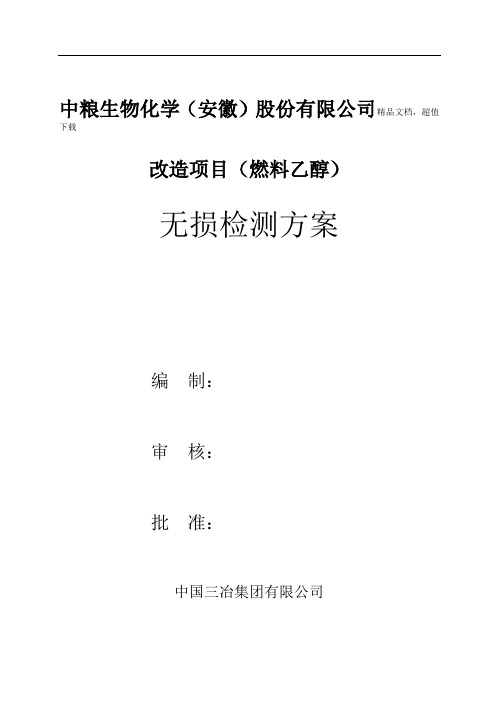
中粮生物化学(安徽)股份有限公司精品文档,超值下载改造项目(燃料乙醇)无损检测方案编制:审核:批准:中国三冶集团有限公司二〇一七年三月六日目录一、工程概述 (1)1.1工程概况 (1)1.2编制依据及验收规范 (1)1.3检测工程要求 (1)二、主要检测项目的保证措施 (1)2.1概述 (1)2.2射线检测方案 (1)2.3超声检测方案 (6)2.4渗透检测方案 (7)2.5磁粉检测方案 (10)2.6保证措施 (13)三、安全技术措施 (16)3.1人员要求 (16)3.2设备要求 (16)3.3人员防护 (16)3.4现场防护 (16)四、应急预案 (17)五、无损探伤JSA分析及防护方法 (18)无损检测方案一、工程概述:1.1工程概况中粮生物化学(安徽)股份有限公司(燃料乙醇)项目共有三十台储罐,依据相关规范及标准,对罐体进行无损检测工作。
1.2 编制依据及验收规范1.2.1 GB50128-2005《立式圆筒形钢制焊接储罐施工及验收规范》;1.2.2 NB/T47013.1~6-2015《承压设备无损检测》;1.2.3 GB50341-2014 《立式圆筒型钢制焊接油罐设计规范》;1.2.4 SH/T3167-2012 《钢制焊接低压储罐》;1.2.5 NB/T47015-2011 《压力容器焊接规程》;1.2.6 HG/T20569-2013 《机械搅拌设备》;1.2.7计图纸文件要求的其他规范、规程;1.2.8 GB18871-2005《射线卫生防护基本标准》。
1.3 检测工作要求1.3.1 发酵区储罐探伤要求:底及次圈罐壁纵焊缝100%射线探伤,Ⅲ级合格;底及次圈罐壁环焊缝和其余各圈纵焊缝20%射线探伤,Ⅲ级合格;其余各圈环焊缝2%探伤,Ⅱ级合格;罐壁所有丁字焊缝100%射线探伤,Ⅱ级合格;底圈壁板与罐底内外角焊缝100%磁粉探伤,Ⅰ级合格;罐底边缘板(外缘300mm)对接焊缝100%射线探伤,Ⅱ级合格;罐底板T型焊缝根部和表面100%磁粉探伤。
在线无损检测方案(一)
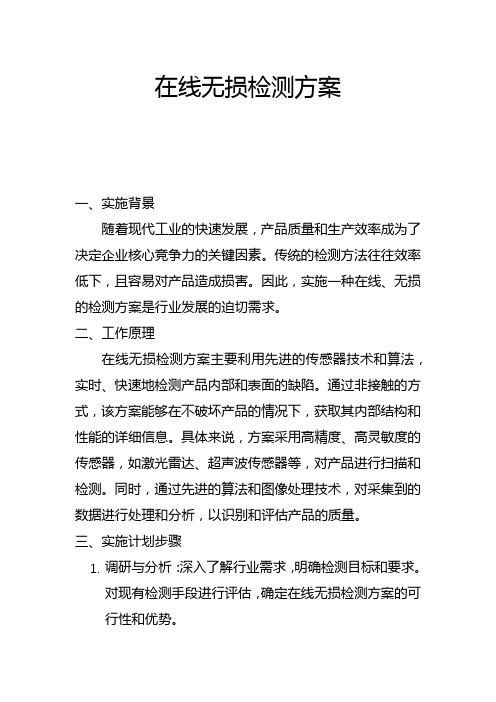
在线无损检测方案一、实施背景随着现代工业的快速发展,产品质量和生产效率成为了决定企业核心竞争力的关键因素。
传统的检测方法往往效率低下,且容易对产品造成损害。
因此,实施一种在线、无损的检测方案是行业发展的迫切需求。
二、工作原理在线无损检测方案主要利用先进的传感器技术和算法,实时、快速地检测产品内部和表面的缺陷。
通过非接触的方式,该方案能够在不破坏产品的情况下,获取其内部结构和性能的详细信息。
具体来说,方案采用高精度、高灵敏度的传感器,如激光雷达、超声波传感器等,对产品进行扫描和检测。
同时,通过先进的算法和图像处理技术,对采集到的数据进行处理和分析,以识别和评估产品的质量。
三、实施计划步骤1.调研与分析:深入了解行业需求,明确检测目标和要求。
对现有检测手段进行评估,确定在线无损检测方案的可行性和优势。
2.技术研发:开发适用于在线无损检测的传感器和算法。
进行实验和验证,确保方案的准确性和可靠性。
3.设备集成:将传感器与生产线设备集成,实现自动化检测。
优化设备布局,提高生产效率。
4.实验与验证:在多种产品上进行实验,验证方案的准确性和可靠性。
收集反馈意见,对方案进行改进和优化。
5.部署与实施:将方案部署到生产线,进行实际应用。
对操作人员进行培训,确保方案的顺利运行。
四、适用范围该方案适用于各种工业领域,如汽车制造、航空航天、电子制造等。
它适用于各种形状和尺寸的产品,无论是小型零件还是大型结构。
特别是在高精度、高质量要求的生产过程中,在线无损检测方案具有显著的优势。
五、创新要点1.先进的传感器技术:利用先进的传感器技术,实现高精度、高灵敏度的检测。
这包括激光雷达、超声波传感器等非接触式检测设备的应用。
2.智能算法:采用深度学习等算法,提高检测的准确性和效率。
通过图像处理和分析技术,实现对产品内部结构和性能的精确评估。
3.在线集成:将检测设备与生产线设备无缝集成,实现实时、连续的检测。
优化生产流程,提高生产效率。
无损检测项目实施方案
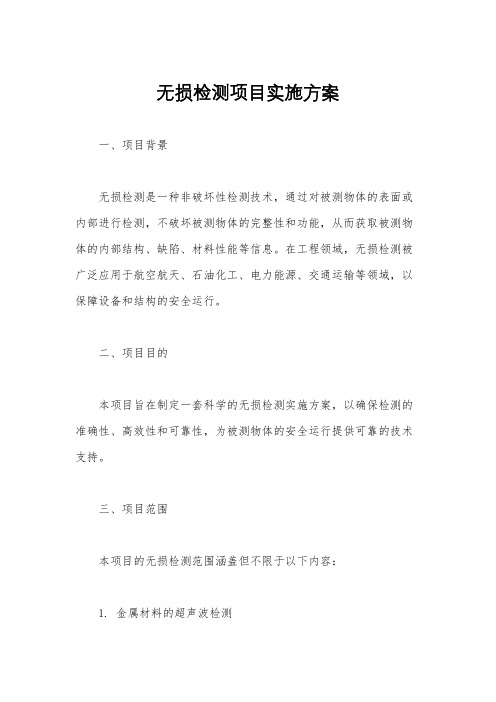
无损检测项目实施方案一、项目背景无损检测是一种非破坏性检测技术,通过对被测物体的表面或内部进行检测,不破坏被测物体的完整性和功能,从而获取被测物体的内部结构、缺陷、材料性能等信息。
在工程领域,无损检测被广泛应用于航空航天、石油化工、电力能源、交通运输等领域,以保障设备和结构的安全运行。
二、项目目的本项目旨在制定一套科学的无损检测实施方案,以确保检测的准确性、高效性和可靠性,为被测物体的安全运行提供可靠的技术支持。
三、项目范围本项目的无损检测范围涵盖但不限于以下内容:1. 金属材料的超声波检测2. 焊接接头的射线检测3. 压力容器的磁粉检测4. 电力设备的红外热像检测5. 建筑结构的声发射检测四、实施方案1. 确定检测方法:根据被测物体的材料、形状、缺陷类型等因素,选择合适的无损检测方法,如超声波检测、射线检测、磁粉检测、红外热像检测等。
2. 确定检测设备:选用符合国家标准和行业标准的无损检测设备,确保设备的性能稳定、精度高、操作简便。
3. 制定检测方案:根据被测物体的具体情况,制定详细的无损检测方案,包括检测位置、检测参数、检测步骤等内容。
4. 进行检测操作:由经过专业培训的无损检测人员,按照制定的检测方案进行实际操作,确保检测的准确性和可靠性。
5. 分析检测结果:对检测所得数据进行分析和评估,判断被测物体的安全状况,提出相应的建议和处理方案。
五、质量控制1. 严格遵守国家标准和行业标准,确保无损检测的准确性和可靠性。
2. 对无损检测设备进行定期维护和校准,保证设备的正常运行。
3. 对无损检测人员进行定期培训和考核,提高其专业技能和操作水平。
4. 对检测结果进行审查和复核,确保检测数据的准确性和可靠性。
六、安全措施1. 严格遵守无损检测操作规程,确保检测人员的人身安全和设备的安全运行。
2. 对检测现场进行安全评估,采取必要的安全防护措施,确保检测作业的安全进行。
七、项目成果1. 完成无损检测报告,对被测物体的安全状况进行评估和分析,提出相应的建议和处理方案。
无损检测管理方案
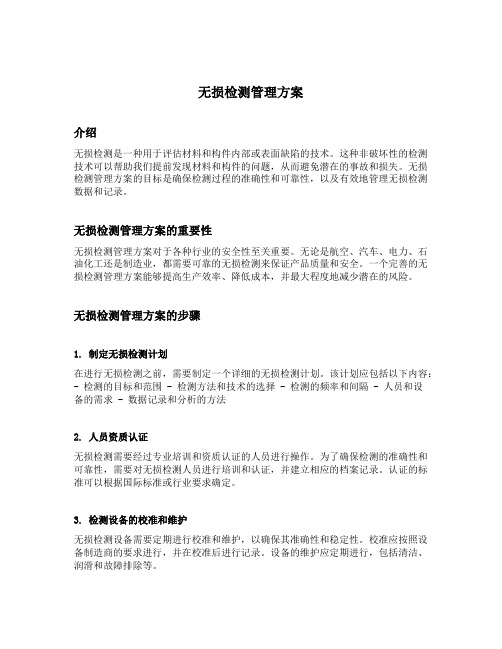
无损检测管理方案介绍无损检测是一种用于评估材料和构件内部或表面缺陷的技术。
这种非破坏性的检测技术可以帮助我们提前发现材料和构件的问题,从而避免潜在的事故和损失。
无损检测管理方案的目标是确保检测过程的准确性和可靠性,以及有效地管理无损检测数据和记录。
无损检测管理方案的重要性无损检测管理方案对于各种行业的安全性至关重要。
无论是航空、汽车、电力、石油化工还是制造业,都需要可靠的无损检测来保证产品质量和安全。
一个完善的无损检测管理方案能够提高生产效率、降低成本,并最大程度地减少潜在的风险。
无损检测管理方案的步骤1. 制定无损检测计划在进行无损检测之前,需要制定一个详细的无损检测计划。
该计划应包括以下内容:- 检测的目标和范围 - 检测方法和技术的选择 - 检测的频率和间隔 - 人员和设备的需求 - 数据记录和分析的方法2. 人员资质认证无损检测需要经过专业培训和资质认证的人员进行操作。
为了确保检测的准确性和可靠性,需要对无损检测人员进行培训和认证,并建立相应的档案记录。
认证的标准可以根据国际标准或行业要求确定。
3. 检测设备的校准和维护无损检测设备需要定期进行校准和维护,以确保其准确性和稳定性。
校准应按照设备制造商的要求进行,并在校准后进行记录。
设备的维护应定期进行,包括清洁、润滑和故障排除等。
4. 数据管理和记录无损检测生成的数据需要进行管理和记录。
应制定相应的数据管理方案,包括数据采集、存储、分析和报告等。
数据应进行备份,并按照一定的时限进行保存,以备将来可能的需求。
5. 评估和改进无损检测管理方案需要不断评估和改进。
可以通过内部审核、外部评估或科学研究等方式来评估管理方案的有效性。
根据评估结果,及时进行改进并进行相应的培训和沟通。
结论无损检测管理方案是保证无损检测准确性和可靠性的重要措施。
一个完善的管理方案能够帮助我们及早发现材料和构件的问题,降低事故风险和经济损失。
通过制定无损检测计划、人员资质认证、设备校准维护、数据管理和记录以及评估和改进等步骤,可以有效地管理无损检测过程,并及时采取措施解决问题。
无损检测方案

船舶无损检测方案一.总则例如:X-射线(RT)、超声波(UT)、磁粉(MT)、渗透(PT).无损检测数量、试验程序满足规范要求。
1.无损检测的认可标准:(1)RT:Ⅲ-Part3-CB/T 3558-94;(2)UT: Ⅲ-Part3-CB/T 3559-94;(3)MT: Ⅱ-Part3-JB/T 6061-92;(4)PT: Ⅱ-Part3-JB/T 6062-92;验收标准:CB/T3177-94二.焊缝区域等级划分1.一级焊缝在船中0.6L区, 外板横向对接缝、内底板横向对接缝;以及上甲板、纵舱壁,舭龙骨,纵桁的对接缝2.二级焊缝在船中0.6L范围外,外板横接缝;在船中0.6L范围内,外板纵接缝。
三.无损检测数量和范围1.一级焊缝(1)射线(RT)根据CCS材料与焊接规范对舯部0.6L区域内强力甲板和外板的射线拍片数量N=0.25(i+0.1Wt+0.1Wl).=0.25(644+0.1*1572+0.1*879)=222.25≈223i~~0.6L范围内纵、横向对接焊缝交叉处的总和Wt~~0.6L范围内横向对接焊缝的总长mWl~~0.6L范围内分段合拢的纵向对接焊缝的总长m具体位置见片位图纵横向对接焊缝交叉处的布片方向应平行于横向对接焊缝(2)超声波(UT)船底、舷侧和甲板纵骨的对接接头,在船中0.6L范围内每10个检查1个,0.6L范围内超声波检测位置范围见表1。
表一区域结构焊缝名称UT数量双层底纵骨HB02P/S~HB03C;HB03C~HB04C;HB04C~HB05C;HB05C~HB06C;HB06C~HB07C;HB07C~HB08C;HB08C~HB09C;HB09C~HB10C;HB10C~HB11C;HB11C~HB12C;HB12C~HB13C;HB13C~HB14C;HB14C-HB15C;4*13=52 纵桁HB02P/S~HB03C;HB03C~HB04C;HB04C~HB05C;HB05C~HB06C;HB06C~HB07C;HB07C~HB08C;HB08C~HB09C;HB09C~HB10C;HB10C~HB11C;HB11C~HB12C;HB12C~HB13C;HB13C~HB14C;HB14C-HB15C;2*13=26底边舱纵骨HS12DP/S~HB03P/S;HB03P/S~HB04P/S;HB04P/S~HB05P/S;HB05P/S~HB06P/S;HB06P/S~HB07P/S;HB07P/S~HB08P/S;HB08P/S~HB09P/S;HB09P/S~HB10P/S;HB10P/S~HB11P/S;HB11P/S~HB12P/S;HB12P/S~HB13P/S;HB13P/S~HB14P/S;HB14P/S~HB15P/S2*13*2=52 斜板HS12DP/S~HB03P/S;HB03P/S~HB04P/S;HB04P/S~HB05P/S;HB05P/S~HB06P/S;HB06P/S~HB07P/S;HB07P/S~HB08P/S;HB08P/S~HB09P/S;HB09P/S~HB10P/S;HB10P/S~HB11P/S;HB11P/S~HB12P/S;HB12P/S~HB13P/S;HB13P/S~HB14P/S;HB14P/S~HB15P/S2*13*2=52顶边舱纵骨HS12UP/S~HS13P/S;HS13P/S~HS14P/S;HS14P/S~HS15P/S;HS15P/S~HS16P/S;HS16P/S~HS17P/S;HS17P/S~HS18P/S;HS18P/S~HS19P/S;HS19P/S~HS20P/S;HS20P/S~HS21P/S;HS21P/S~HS22P/S;HS22P/S~HS23P/S;HS23P/S~HS24P/S;HS24P/S-HS25P/S2*13*2=52 斜板HS12UP/S~HS13P/S;HS13P/S~HS14P/S;HS14P/S~HS15P/S;HS15P/S~HS16P/S;HS16P/S~HS17P/S;HS17P/S~HS18P/S;HS18P/S~HS19P/S;HS19P/S~HS20P/S;HS20P/S~HS21P/S;HS21P/S~HS22P/S;HS22P/S~HS23P/S;HS23P/S~HS24P/S;HS24P/S-HS25P/S2*13*2=52UT数量总计:286舭龙骨对接焊缝100%UT.2.二级焊缝(1)射线(RT)0.6L以外的射线数量为0.6L范围呢的10%即23张,具体见片位图(2)超声波(UT)船底、舷侧和甲板纵骨的对接接头,在船中0.6L范围以外每20个检查1个.其他:1,波形壁分段焊缝10%UT,合拢焊缝10%UT2,海水箱周界100%UT3,分段内纵骨接头50%UT4,起重柱与甲板角焊缝100%UT5,顶边舱竖板与主甲板,底边舱斜板与内地板、外板100%UT6,水密与非水密肋板与舱壁内底板全焊透位置100%UT7,波形壁与底墩角焊缝100%UT,底墩侧板与底墩顶板100%UT8, 底墩侧板与底边舱斜板100%UT9, 直径大于75的一级管对接焊缝100%RT10, 直径大于100的二级管对接焊缝10%RT.11, 主基座对接接头100%用超声波(UT)检查,角接头10-20%用超声波(UT)检查12, 尾柱(铸钢件)和钢板之间的接头用超声波或者着色探伤,检测点根据CCS 验船师指定。
无损检测方案(DOC)

无损检测施工方案编制:审核:批准:###################年##月一、工程概况黑龙江省齐齐哈尔市富鹤供热公司供热扩建工程热水锅炉安装工程新装一台35T/H锅炉。
锅炉为单锅筒,自然循环,分散下降管,II型结构,半露天布置。
锅炉采用了近年发展起来的先进的节能燃烧技术,结构紧凑,由锅筒、水冷系统、过热器、省煤器、空气预热器、平台扶梯、炉墙、外护板等组成。
炉膛采用全悬吊结构,炉膛四周为膜式水冷壁结构、过热器及省煤器区域为护板炉墙,空气预热器为板式预热器。
二、编制依据1、《蒸汽锅炉安全技术监察规程》劳动部发[1996]276号2、《锅炉安装监督检验规程》TSG G7001-20043、《电力建设施工及验收技术规范》(焊接篇)5007-924、《钢制承压管道对接焊接接头射线检验技术规范》DL/T821-20025、《钢制承压管道对接焊接接头超声波检验技术规范》DL/T820-20026、《压力容器无损检测》JB4730-20047、《电力建设安全工作规程》DL/5009.1-2002三、工作量按有关规程,以下锅炉部件要求不低于25%X射线探伤、Ⅱ级合格(省煤器和水冷壁、热压弯头100%X射线探伤除外),锅炉受热面管子规格、材质及焊口数量如下表所示:四、参加作业人员的资格和要求1、任锅炉无损检测的探伤人员,必须按《锅炉压力容器无损检测人员资格考核规则》考试,取得相应的合格项目,并且至少有1个Ⅰ级和1个Ⅱ级或2个Ⅱ级以上资格人员参加。
2、有评片实际工作经历和经验。
3、具有良好的视力。
4、作业所需的机具、仪器,按工程要求XXX-2505携带式风冷探伤机一台和探伤附件一套,如胶片、增光屏、铅字、磁铁、象质计、黑度计、卷尺、暗袋、红灯、暗室、显影液、停影液、定影液等器材。
五、作业前应做的准备和条件1、线能的选择(1)射线能量过低,穿透力不够,结果是到达胶片的透照射线强度过小,造成黑度不足,灰雾度增大(2)射线能量过高,对射线照相的灵敏度有不利影响,衰减系数u减小,对比度ΔD降低,固有不清晰度增大2、焦距的选择可按下列公式计算:AB级L1≥10df·L22/3U g≤1/10×L21/3F=L1+L2F—焦距L1—透照距离L2—透照厚度d1—焦点尺寸U g—几何不清晰度3、曝光量的选择按商、中级射线检测培训教材,推荐曝光量是≤15mA.min4、透照方法的选择小口径(≤60mm)采用双壁双影一次透照方法,大口径(>89mm)的管子采用双壁单影透照法。
无损检测施工方案
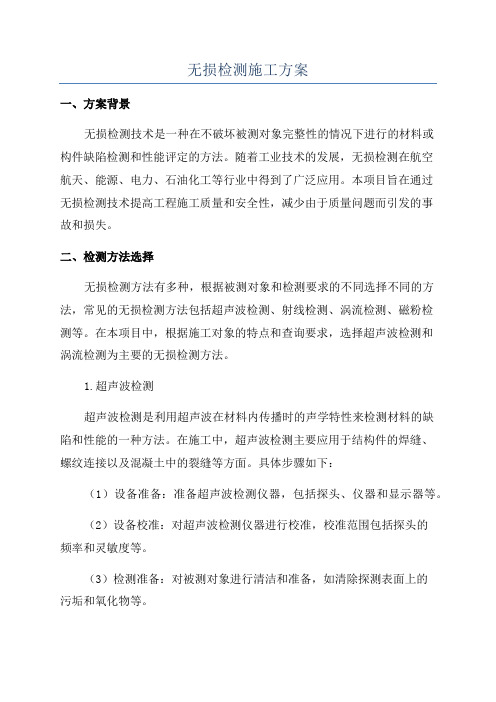
无损检测施工方案一、方案背景无损检测技术是一种在不破坏被测对象完整性的情况下进行的材料或构件缺陷检测和性能评定的方法。
随着工业技术的发展,无损检测在航空航天、能源、电力、石油化工等行业中得到了广泛应用。
本项目旨在通过无损检测技术提高工程施工质量和安全性,减少由于质量问题而引发的事故和损失。
二、检测方法选择无损检测方法有多种,根据被测对象和检测要求的不同选择不同的方法,常见的无损检测方法包括超声波检测、射线检测、涡流检测、磁粉检测等。
在本项目中,根据施工对象的特点和查询要求,选择超声波检测和涡流检测为主要的无损检测方法。
1.超声波检测超声波检测是利用超声波在材料内传播时的声学特性来检测材料的缺陷和性能的一种方法。
在施工中,超声波检测主要应用于结构件的焊缝、螺纹连接以及混凝土中的裂缝等方面。
具体步骤如下:(1)设备准备:准备超声波检测仪器,包括探头、仪器和显示器等。
(2)设备校准:对超声波检测仪器进行校准,校准范围包括探头的频率和灵敏度等。
(3)检测准备:对被测对象进行清洁和准备,如清除探测表面上的污垢和氧化物等。
(4)检测操作:将超声波探头放置在被测对象上,并通过仪器观察显示器上的信号波形。
(5)数据分析:根据显示器上的信号波形,判断被测对象是否存在缺陷。
2.涡流检测涡流检测是一种通过利用涡流感应的原理,检测材料内或表面缺陷的方法。
施工中涡流检测主要应用于管道和金属构件的检测。
具体步骤如下:(1)设备准备:准备涡流检测仪器,包括探头、仪器和显示器等。
(2)设备校准:对涡流检测仪器进行校准,校准范围包括探头的频率和灵敏度等。
(3)检测准备:对被测对象进行清洁和准备,如清除探测表面上的污垢和氧化物等。
(4)检测操作:将涡流探头放置在被测对象上,并通过仪器观察显示器上的信号波形。
(5)数据分析:根据显示器上的信号波形,判断被测对象是否存在缺陷。
三、检测操作规范在实施无损检测时,需要严格按照操作规范进行操作,以确保检测结果的准确性和可靠性。
无损检测方案

无损检测施工方案1.编制说明1.1 编制依据:1)《压力容器安全技术监察规程》—1999。
2)《钢制压力容器》GBl50—98。
3)《压力容器无损检测》JB4730—94。
4)《压力容器质量保证手册》。
1.2 符号说明:NDT—无损探伤RT——射线探伤UT——超声探伤MT——磁粉探伤PT——渗透探伤VT——目视检查OK——合格Gr ——打磨2. 无损探伤人员2.1 从事无损探伤操作的人员,必须具有劳动部门颁发的相应无损探伤方法III 级以上资格,并经无损探伤责任工程师认可后方可从事NDT操作。
2.2 从事无损探伤结果评定及签发报告的人员,必须具有劳动部门颁发的相应无损探伤方法Ⅱ级以上资格,并经无损探伤责任工程师认可后方可从事NDT结果的评定及签发报告。
3.磁粉探伤工艺与质量控制3.1 适用范围:对接焊缝、角焊缝、坡口及清根、工卡具去除打磨处3.2探伤设备:型号:Y—6交流磁轭式。
提升力:>44N。
磁极间距:50~250mm。
试片:A型、C型。
3.3 探伤材料:黑磁粉。
磁粉应具有磁导率高、剩磁低和相互之间不吸引。
3.4 磁粉探伤工艺流程:3.5 灵敏度校验:每个班次开始和结束之前,都必须用A型或C型试片,对受检工件表面有效磁场强度、检测区、方向及磁化方法进行校验。
校验方法:将无人工缺陷的面朝外,平整放在被检面上用透明胶带粘贴固定,保证试片与被检面接触良好,磁痕显示清晰完整。
3.6 表面处理1)受检部位及四周25mm范围表面,可用砂轮或钢刷打磨去除飞溅等。
2)受检部位表面不得有油脂或粘附磁粉的物质。
3.7磁化及施加磁悬液1)每一受检区应进行2次独立检测,磁力线方向大致互相垂直。
2 )磁极间距应控制在200mm左右,检测的有效区域为两极连线两侧各50mm 范围内,磁化区域每次应有15mm的重叠。
3)采用连续法探伤,边磁化边施加磁悬液,通电时间1~3S,通电至少2次,停施磁悬液至少1S以后才能停止磁化。
无损检测施工方案
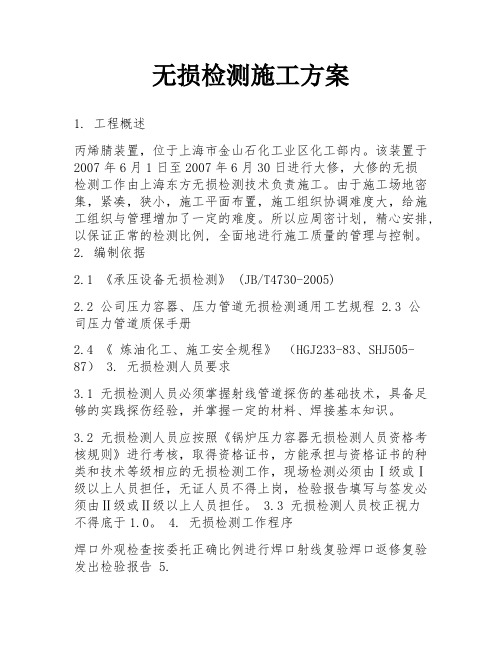
无损检测施工方案1. 工程概述丙烯腈装置,位于上海市金山石化工业区化工部内。
该装置于2007年6月1日至2007年6月30日进行大修,大修的无损检测工作由上海东方无损检测技术负责施工。
由于施工场地密集,紧凑,狭小,施工平面布置,施工组织协调难度大,给施工组织与管理增加了一定的难度。
所以应周密计划, 精心安排, 以保证正常的检测比例, 全面地进行施工质量的管理与控制。
2. 编制依据2.1 《承压设备无损检测》 (JB/T4730-2005)2.2 公司压力容器、压力管道无损检测通用工艺规程 2.3 公司压力管道质保手册2.4 《炼油化工、施工安全规程》(HGJ233-83、SHJ505-87)3. 无损检测人员要求3.1 无损检测人员必须掌握射线管道探伤的基础技术,具备足够的实践探伤经验,并掌握一定的材料、焊接基本知识。
3.2 无损检测人员应按照《锅炉压力容器无损检测人员资格考核规则》进行考核,取得资格证书,方能承担与资格证书的种类和技术等级相应的无损检测工作,现场检测必须由Ⅰ级或Ⅰ级以上人员担任,无证人员不得上岗,检验报告填写与签发必须由Ⅱ级或Ⅱ级以上人员担任。
3.3 无损检测人员校正视力不得底于1.0。
4. 无损检测工作程序焊口外观检查按委托正确比例进行焊口射线复验焊口返修复验发出检验报告 5.6. 无损检测设备6.1 射线检测采用Se 75。
考虑工艺管道现场情况复杂,管线规格不单一,采用Se 75拍片,其底片同X光底片相比,各项工艺参数相差不大。
(每种规格管径都作对比试验) 7. 检验标记、检验报告填写和签发及原始记录、报告存档保管。
7.1工艺管道检验部位必须用油漆记号进行标注,检验结束后,应对检验结果及检验部位进行详细记录,检测部位图应清晰、准确地反映实际检测的方位做到一一对应。
7.2 检验标记表示方法:7.2.1焊口标注以施工图为准。
7.3 及时发出检验报告,检验报告填写与签发必须由Ⅱ级或Ⅱ级以上人员担任,记录、检验报告、应准确、端正、清楚。
无损检测策划方案

无损检测策划方案1. 引言无损检测(NDE),也称为非破坏性检测,是一种重要的工业技术,用于检测材料和构件的内部和表面缺陷,而无需对其造成永久性的损坏。
无损检测在许多领域具有广泛的应用,如航空航天、制造业、核工业等。
本文档将介绍一个基本的无损检测策划方案,旨在为相关项目提供指导和规范。
2. 项目背景该无损检测策划方案适用于一项制造工程项目,旨在确保最终交付物的质量和安全性。
该项目涉及使用无损检测技术对所制造的构件进行测试,以确保其符合相关的技术要求和标准。
3. 目标本无损检测策划方案的目标是:- 确保所制造的构件不含任何内部或表面缺陷;- 提高项目交付物的质量和可靠性; - 减少质量控制测试的周期和成本; - 降低项目的风险和维修成本。
4. 策划步骤4.1 确定无损检测方法根据项目的要求和相关标准,确定适用的无损检测方法。
常用的无损检测方法包括:•超声波检测(UT):通过声波在材料中的传播和反射来检测缺陷;•射线检测(RT):通过使用高能射线(如X射线或伽马射线)来检测构件内部的缺陷;•磁粉检测(MT):通过在构件表面涂抹磁性粉末并施加磁场,检测材料内部的磁性缺陷;•渗透检测(PT):通过将液体渗透进入构件表面缺陷,并使用吸收性材料吸收液体,检测表面缺陷;•热红外检测(IRT):通过检测材料辐射的热量来检测潜在的热问题。
根据具体项目的需求和构件类型,选择适当的无损检测方法。
4.2 制定检测计划制定无损检测计划,包括确定检测的时间、地点和频率。
根据构件制造的不同阶段制定检测计划,例如: - 原材料检测:对原材料进行无损检测,确保其质量达标; - 制造过程中的检测:对加工过程中的构件进行无损检测,确保其没有任何制造缺陷; - 最终产品检测:对最终产品进行全面的无损检测。
4.3 确定人员资质和培训计划根据所选的无损检测方法,确定并培训适当的人员,使其具备必要的技能和知识来执行无损检测工作。
确保人员获得相关认证并定期进行培训,以保持其专业水平。
无损检测方案

无损检测方案无损检测是一种通过各种非破坏性手段来检测材料和构件内部缺陷的技术。
它在工程结构、航空航天、核能等领域具有重要应用。
本文将介绍几种常见的无损检测方案。
1. 超声波检测超声波检测利用超声波在材料中传播的特性来发现并定位缺陷。
它可以检测出金属材料中的气孔、夹杂、裂纹等缺陷。
超声波的频率、幅值和传播速度都可以提供关于缺陷的信息。
超声波检测设备通常包括超声发生器、探头和接收器。
该技术可应用于金属、塑料、陶瓷等材料的检测。
2. 磁粉检测磁粉检测是通过在被测零件的表面涂覆铁磁性材料,然后施加磁场来发现表面或近表面的裂纹、夹杂等缺陷的方法。
当有缺陷存在时,铁磁性材料会在缺陷周围产生漏磁场,从而形成磁粉堆积。
通过观察磁粉的分布情况和形态,可以确定缺陷的位置和形状。
磁粉检测适用于铁磁材料的表面和近表面缺陷的检测。
3. 渗透检测渗透检测是通过涂覆敏感液体(渗透剂)和吸附剂在被检测零件表面,然后去除表面多余的渗透剂,再施加显色剂来显示缺陷的方法。
渗透剂可以渗入缺陷,当显色剂施加后,渗入的渗透剂会显现出来,从而显示出缺陷的位置和形状。
渗透检测适用于金属、塑料、陶瓷等材料的表面缺陷的检测。
4. 射线检测射线检测是一种利用X射线或γ射线透射材料来显示隐藏在材料内部的缺陷的方法。
射线可以透过材料,当遇到缺陷时,部分射线会被吸收或散射,从而在胶片或探测器上形成缺陷的阴影。
射线检测广泛应用于金属材料的焊缝、铸件等的缺陷检测。
以上所述的无损检测方案只是其中的一部分,现实中还有许多其他的无损检测方法,如涡流检测、红外热成像等。
每种方法都有其适用的场景和具体应用。
无损检测的成功在很大程度上依赖于操作人员的经验和技术能力,同时设备的性能也会对检测结果产生影响。
无损检测在工程领域具有重要意义。
它可以在不破坏材料的情况下发现和评估缺陷,提高结构的安全性和可靠性。
例如,在航空航天行业,无损检测可以用于飞机零部件的质量检测和寿命评估。
无损检测方案

无损检测方案无损检测是一种非破坏性测试方法,用于评估各种材料和组件的质量和完整性。
无损检测技术广泛应用于航空航天、石油化工、电力、核工业、钢铁、汽车、船舶等行业,以确保设备和结构的可靠性和安全性。
本文将介绍几种常见的无损检测方案。
1.超声波检测:超声波检测是通过测量声波在材料内部传播的速度和特性,来评估材料中的缺陷和损伤。
这种方法可以检测出裂纹、毛细孔、夹杂物等各种缺陷,并且可以确定它们的位置和尺寸。
超声波检测广泛应用于管道、容器、焊接接头等结构的检测。
2.磁粉检测:磁粉检测是一种通过施加磁场和观察磁场中的磁性粉末分布来检测材料中的表面和近表面缺陷的方法。
该方法可以检测出裂纹、气孔、疲劳损伤等缺陷,并且可以确定它们的位置和形状。
磁粉检测广泛应用于钢铁制品、铸件、焊接接头等的检测。
3.X射线检测:X射线检测是通过照射物体,并观察被照射物体的透射或散射的X射线,来检测物体内部的缺陷和损伤。
X射线检测可以检测出金属和非金属材料中的裂纹、疲劳损伤、夹杂物等缺陷,并且可以确定它们的位置和尺寸。
X射线检测广泛应用于金属制品、焊接接头、压力容器等的检测。
4.红外热像检测:红外热像检测是通过检测物体放射出的红外辐射来评估物体的热分布和热特性。
该方法可以检测出材料中的热点、热源、热漏等问题,并且可以确定它们的位置和性质。
红外热像检测广泛应用于电力设备、电子设备、建筑物等的检测。
5.声发射检测:声发射检测是通过检测材料内部发出的声波信号来评估材料的完整性和稳定性。
该方法可以检测出材料中的裂纹、断层、疲劳损伤等问题,并且可以确定它们的位置和特性。
声发射检测广泛应用于桥梁、建筑物、工业设备等的检测。
无损检测方案需要根据被检测物体的材料、结构和使用环境来选择和设计。
在实施无损检测之前,需要进行系统的培训和认证,以确保检测人员具备足够的专业知识和技能。
此外,无损检测还需要进行设备校准和维护,以确保检测结果的准确性和可靠性。
无损检测技术方案

射线检测技术方案一、射线检测设备和原材料现场验收程序1)无损检测所用设备、材料的生产厂家、品牌必须由业主和监理工程师认可。
2)材料和设备到场后应由专人负责接货、验收。
审查随货配备材料合格证,材质证明书、说明书是否齐全,并根据装箱单对材料、设备进行外观检查,抽查、测试和鉴别标记,做好检查验收记录。
3)材料和设备到达现场经检查验收合格,并再经业主或监理认可方可使用。
4)不合格的材料和设备要坚决退货,合格的材料和设备按规定入库存放。
5)材料、设备的搬运和运输由设备材料负责人负责。
并做好材料、设备的运输、搬运、储存、防护和管理。
由技术质量负责人对此过程控制的执行情况进行监督和检查。
材料、设备的搬运和运输要做到轻拿轻放,防止剧烈颠簸,避免仪器、设备在搬运过程中因碰撞而出现故障,以防止胶片出现折痕,药粉泄漏等情况发生。
6)材料、设备的管理要设立专用库房。
库房内配备温度计,湿度计、灭火器具等,库房内保持通风、干燥。
库房内材料摆放要整齐,并按要求做好状态标识。
避免阳光直射。
材料和设备要专人、专岗进行保管,保证其从入库到发放期间储存得当,防止因保管不当造成材料和设备损坏、受潮、腐蚀和丢失。
7)对材料的入库和发放要认真检查并做好记录。
帐、卡、物相符。
保管期间,要定期进行抽检,防止失效、变质,保证材料的质量。
不合格的材料不能发放使用,杜绝不合格材料用到工程上。
对设备要定期维护保养,保证设备始终处于良好状态。
对有故障的设备要及时进行维修,保证生产需要。
二、射线检测质量控制管理工作程序1) 在接到监理检测指令后,随即依照指令对焊缝进行射线检测,应并在监理要求的时间内,将检测结果报送监理。
2) 检测责任人员在接到监理检测指令后,应对工件的结构、坡口形式、焊接方法及管壁厚度等进行了解,并核对监理指令与所透照工件是否相符,核对内容包括:项目名称、焊缝编号、管壁厚度等。
在对焊缝进行射线检测前,应对焊缝外观进行检查,外观不合格有权拒绝检查并通知监理工程师,待施工单位整改合格后重新进行检测。
电厂无损检测实施方案

电厂无损检测实施方案无损检测是指在不破坏被检物理性能和减少对生产过程的干扰的前提下,通过检测各种材料、构件或装备的人工或自动化的无损检测方法,发现、定量评定和评估材料或者结构内部的缺陷、杂质、应力等。
对于电厂来说,无损检测可以帮助发现并预防潜在的设备故障,保障设备的安全运行和电厂的正常生产。
下面是电厂无损检测的实施方案。
第一步:检测需求分析。
根据电厂设备的类型、规模和特点,确定需要进行无损检测的设备和部位。
一般来说,关键设备如锅炉、汽轮机、发电机等应作为无损检测优先检测对象。
第二步:制定无损检测计划。
根据设备检测需求,综合考虑检测难度和工作量,制定详细的无损检测计划。
计划包括检测项目、检测方法、检测人员、检测仪器设备、检测时间等。
第三步:检测人员培训。
对参与无损检测工作的人员进行培训,包括无损检测原理和方法、仪器设备的操作使用方法、安全操作规程等。
确保检测人员具备必要的专业技能和操作经验。
第四步:采购和维护检测仪器设备。
根据检测计划,采购适用的无损检测仪器设备,并确保其正常运行和定期维护,以保证检测结果的准确性和可靠性。
第五步:进行无损检测。
根据检测计划,按照规范和流程进行无损检测工作。
在检测过程中,要注意操作规程,保证人身安全,并及时处理检测过程中的问题和故障。
第六步:分析检测结果。
对检测结果进行分析和评估,包括判断设备的安全性和可用性,提供设备使用寿命评估和维修建议,对设备的健康状况进行监控。
第七步:记录和报告。
对无损检测的结果进行详细记录和整理,包括检测项目、检测日期、检测人员、检测方法、检测仪器、检测结果等,并撰写无损检测报告,提供给相关部门和管理人员参考。
第八步:指导和建议。
根据无损检测的结果和报告,向电厂管理人员提供设备管理方面的指导和建议,包括设备保养维护、修复措施等,以保证设备的正常运行和生产的安全性。
总结:电厂无损检测实施方案包括检测需求分析、制定无损检测计划、检测人员培训、采购和维护检测仪器设备、进行无损检测、分析检测结果、记录和报告、指导和建议等步骤。
- 1、下载文档前请自行甄别文档内容的完整性,平台不提供额外的编辑、内容补充、找答案等附加服务。
- 2、"仅部分预览"的文档,不可在线预览部分如存在完整性等问题,可反馈申请退款(可完整预览的文档不适用该条件!)。
- 3、如文档侵犯您的权益,请联系客服反馈,我们会尽快为您处理(人工客服工作时间:9:00-18:30)。
xx设备检测施工方案审核:编制:河北xx有限公司2020年06月11日一、工程概况设备由于年久设备存在老化、脱漆、部分损坏、灯具缺失、钢结构腐蚀、设备存在安全隐患等问题,已不能满足游览展陈需要。
本工程需对上述设备进行探伤及测试实验工作,一是对部分重要受力部件进行探伤实验检测;二是对所对应的探伤实验结果出具正式检测报告。
二、探伤检测范围本工程展陈设备检测对象包括:大码头、甲码头的设备共8台,如下所示。
1、门式起重机2台。
2、螺旋卸车机3台,灯架3台。
图1 门式起重机图2 螺旋卸车机三、施工工艺及方案1、钢结构设备检查:由于螺旋卸车机、门机等大型设备老化严重,特别是象鼻梁、回转平台、机房、驾驶室、主体钢结构等大型结构件,这些位置受到的承载力较大,且由于多年的腐蚀存在安全隐患。
需要对这些大型结构件的绞点座、主梁、立柱、扶手、走台等部位的安全可靠性进行检查,人员检查时要检查细致,各个位置需要进行全覆盖检查,够不到的必要的点位,需要搭设登高平台进行检查,通过检查确定各个设备探伤试验的测试点位。
2、焊缝、钢板、锻件进行探伤:☆针对大型非空腔结构件关键受力位置进行超声波探伤。
(1)用纵波可探测金属铸锭、坯料、中厚板、大型锻件和形状比较简单的制件中所存在的夹杂物、裂缝、缩管、白点、分层等缺陷;(2)用横波可探测管材中的周向和轴向裂缝、划伤、焊缝中的气孔、夹渣、裂缝、未焊透等缺陷;(3)用表面波可探测形状简单的铸件上的表面缺陷;(4)用板波可探测薄板中的缺陷。
☆针对结构件表面缺陷进行磁粉探伤。
(1)磁粉探伤利用工件缺陷处的漏磁场与磁粉的相互作用,它利用了钢铁制品表面和近表面缺陷磁导差异,可以检测如裂纹,夹渣,发纹等结构缺陷。
(2)清洗打磨:所有材料和试件的表面应无油脂及其他可能影响磁粉正常分布、影响磁粉堆积物的密集度、特性以及清晰度的杂质。
(3)磁悬液应采用软管浇淋或浸渍法施加于试件,使整个被检表面完全被覆盖,磁化电流应保持1/5~1/2秒,此后切断磁化电流,采用软管浇淋或浸渍法施加磁悬液。
(4)将零件放于直流电磁场中,不断改变电流方向并逐渐将电流降至零值。
大型零件可使用移动式电磁铁或电磁线圈分区退磁。
(5)本方式操作简便,无射线伤害,但是需要进行清洗及恢复,辅助人工用量较大。
☆针对结构件内部不易穿透的缺陷进行X射线探伤。
(1)X射线探伤是利用材料厚度不同对X射线吸收程度的差异,通过用X射线透视摄片法和工业电视实时成像,从软片和成像上显出材料、零部件及焊缝的内部缺陷。
(2)本方法不受电场和磁场的影响,可穿透物质,可检测如裂纹、缩孔、气孔、夹渣、未溶合、未焊透等缺陷,并确定位置和大小。
(3)根据观察其缺陷的性质、大小和部位,针对性的加固以提高安全性,从而防止由于材料内部缺陷等情况而引起的重大事故。
3、腐蚀钢板厚度检测:(1)用钢结构测厚仪对主要部件腐蚀严重的钢板测厚。
监测它们在使用过程中受腐蚀后的减薄程度。
(2)在一点处用探头进行两次测厚,在两次测量中探头的分割面要互为90°,取较小值为被测工件厚度值。
不能进行上述方法的部件,按照下面方法进行测厚。
(3)30mm 多点测量法:当测量值不稳定时,以一个测定点为中心,在直径约为30mm 的圆内进行多次测量,取最小值为被测工件厚度值。
4、涡流检测管壁磨损情况及厚度:(1)穿过式线圈是将被检测试样放在线圈内进行检测的线圈,适用于管、棒、线材的探伤。
适合检测扶手、钢管等管类结构件。
(2)内插式线圈是放在管子内部进行检测的线圈,专用来检查厚壁或钻孔内壁的缺陷。
适合检测受力钢管壁厚等情形。
(3)探头式线圈是放置在试样表面上进行检测的线圈,它不仅适用于形状简单的板材、板坯、方坯、圆坯、棒材及大直径管材的表面扫描探伤,也适用于形状较复杂的机械零件的检查。
适合检测受力钢板或大直径钢管壁厚等情形。
5、硬度检测:(1)用规定质量的冲击体在弹力作用下以一定速度冲击试样表面,用冲头在距试样表面1mm处的回弹速度与冲击速度的比值计算硬度值。
(2)冲击和反弹速度的测得,是将一永久磁铁组装于冲击体上,当冲击体通过线圈时,它向前和回弹时均在线圈内感应出有微小差别的电压。
这些电压正比于速度,经计算机处理在显示装置上显示出硬度值HL。
(3)适用于受压构件的检测,保证大型设备承重安全。
6、金相实验:(1)试样截取的方向,垂直于径向,长度不超过8mm;试样可用手锯等切取,取样时应注意试样的温度条件,必要时用水冷却,以避免正式试样因过热而改变其组织。
(2)准备好的试样,先在粗砂轮上磨平,候磨痕均匀一致后,即移至细砂轮上续磨,磨时须用水冷却试样,使金属的组织不因受热而发生变化。
(3)经砂轮磨好、洗净、吹干后的试样,随即依次在由粗到细的各号砂纸上磨制,可采用在预磨机上进行磨制,从粗砂纸到细砂纸、再换一次砂纸,试样须转90°角与旧磨良成垂直方向。
(4)经预磨后的试样,先在抛光机上进行粗抛光(•抛光织物为细绒布、抛光液为W2.5 金刚石抛光膏),然后进行精抛光(抛光织物为锦丝绒,抛光液为W1.5 金刚石抛光膏)•抛光到试样上的磨痕完全除去而表面像镜面时为止,即粗糙度为Ra0.04以下。
(5)精抛后的试样,便可浸入盛于玻璃皿之浸蚀剂中进行浸蚀。
浸蚀时,试样可不时地轻微移动,但抛光面不得与皿底接触。
(6)浸蚀剂一般采用4%硝酸酒精溶液。
浸蚀时间视金属的性质、检验目的及显微检验的放大倍数而定,以能在显微镜下清晰显出金属组织为宜。
(7)检测查看金属表面物理或化学之“不均一性”,包括裂纹、空隙等,并以此可做材料断面之“不均一性”即内部缺陷之检查。
或微观检查金属组织、压延、锻造及热处理等加工处理导致金相组织变化的情况,晶粒大小检查或非金属夹杂物等组织的分布情况、大小等及材料的破坏判断等。
7、光谱实验:(1)光谱分析法是根据物质的光谱来鉴别物质及确定其化学组成和相对含量的方法,包含三个主要过程:①能源提供能量;②能量与被测物质相互作用;③产生被检测讯号。
(2)光谱实验分析速度较快,可以快速得到零部件材料元素构成,为后续焊接加固选材提供必要的帮助。
四、施工工艺1.根据受检承压设备的材质、结构、制造方法、工作介质、使用条件和失效模式,预计可能产生的缺陷种类、形状、部位和方向,选择适宜的无损检测方法。
2.超声检测主要用于承压设备的内部缺陷的检测;磁粉检测主要用于铁磁性材料制承压设备的表面和近表面缺陷的检测;渗透检测主要用于非多孔金属材料和非金属材料制承压设备的表面开口缺陷的检测;磁粉检测主要用于可磁化金属表面缺陷探伤;厚度检测用于腐蚀钢板厚度测量;涡流检测可以检测管壁磨损情况及厚度;硬度检测适用于受压构件的检测,保证大型设备承重安全;金相实验检测材料“不均一性”即内部缺陷之检查;光谱实验分析速度较快,可以快速得到零部件材料元素构成,为后续焊接加固选材提供必要的帮助。
3.当采用两种或两种以上的检测方法对承压设备的同一部位进行检测时,应按各自的方法评定级别。
4.采用同种检测方法按不同检测工艺进行检测时,如果检测结果不一致,应以危险度大的评定级别为准。
5.进行设备无损检测的机构应按JB/T 4730的相关规定制定出符合要求的无损检测工艺规程。
6.检测记录和报告应准确、完整,并经相应责任人员签字认可。
7.施工难点:本工程因所处地在海边码头,施工作业地点特殊,需考虑大风、海水侵蚀等特殊作业条件,同时因本工程为游客游览区,人员密集,需对安全、噪音、卫生、施工时间多方因素进行考虑,增加施工围挡。
8.施工过程中要严格保证高空作业安全措施,大风等天气严禁作业;因港口设备腐蚀严重,涂装严格按照标准执行。
9.施工要避开游客游览高峰期,施工现场增加围挡;严格控制现场施工环境,垃圾、废料定时清理。
五、安全、文明施工措施1、通用安全管理1)严格遵守公司颁布的有关安全规章制度。
2)安全第一优先,确认任何工伤事故均可避免。
维护工作安全是每一人的责任。
任何工作场所都必须设置完备的安全防护设施。
必须遵守工地安全作业规定。
3)分部分项施工作业前,技术人员应对施工人员进行施工方案或作业指导书的安全技术交底,同时班组应做好每天站班安全交底工作。
4)从事高空、高温、粉尘、有毒、放射性物质等的作业人员必须经体格检查,合格者方可从事该项工作,并定期接受身体复查。
5)施工过程中特种作业人员均应持证上岗,各类证件均应在有效期内。
6)进入施工现场的人员必须正确穿戴使用劳防用品。
严禁穿拖鞋、凉鞋、高跟鞋或带钉的鞋,以及短袖上衣或短裤进入施工现场。
严禁酒后进入施工现场。
7)施工人员要落实“四不伤害”措施,发现不安全因素及时向施工负责人汇报。
2、临时用电安全1)施工现场用配电箱应使用合格的产品。
2)配电箱应装设在干燥、通风及常温场所,不得装设在易受外来固体物撞击及热源烘烤的场所。
3)配电箱应端正牢固,移动式配电箱应装设在坚固的支架上,并设置接地装置。
4)每台用电设备应有各自专用的开关箱,必须实行“一箱一机一闸一保护”制。
5)电源开关箱、发电机周围应设置干粉或二氧化碳手提灭火器,并贴安全告示,禁止堆放油品或其他易燃物品。
6)工作人员每日送电前,应执行安全检查,确认安全后方可送电,每日收工前或暂停工作时,应将电源切断,箱门关闭或电源插座拔出、电缆线收拾妥当,并检查确认安全后方可离开。
每日收工前或遇下雨天时,应将各项用电器具以防雨设施覆盖或移入不被雨淋场所放置。
3、高处作业安全1)高处作业中的安全围索、工具、劳防用品等在施工前加以检查,确认其完好,方能投入使用。
2)施工中对高处作业的安全技术措施,发现有缺陷和隐患时,必须及时解决;危及人身安全时,必须停止作业。
3)施工作业现场所有坠落可能的物件,应一律先行清除或加以固定;所用物料均应堆放平稳;工具应随手放入工具袋,较大的工具应系保险绳;拆下的物件及余料和废料均应及时清理运走,不得任意乱置或向下丢弃,传递物件禁止抛掷。
4)高处作业必须系好安全带,安全带应挂在上方的牢固可靠处;高处作业人员应衣着灵便,衣袖、裤脚应扎紧,穿软底鞋。
5)高处作业时,点焊物件不得移动;切割的工件、边角料等应放置在牢靠的地方或用铁丝扣牢并有防止坠落的措施。
4、起重作业1)起重人员必须坚持“十不吊”原则,使用吊机时,操作人员必须思想集中,听从指挥,信号不明不能操作,指挥人员信号要规范准确。
2)起吊物应绑牢。
吊钩悬挂点应与吊物的重心在同一垂线上,吊钩钢丝绳应保持垂直,严禁偏拉斜吊。
落钩时应防止吊物局部着地引起吊绳偏斜。
吊物未固定时严禁松钩。
3)起重钢丝绳的夹角一般不大于90度。
特殊情况时最大不得超过120度。
4)施工中除所指定的钢丝绳外,吊索具必须具备6倍以上的安全系数,捆绑用钢丝绳必须具备10倍以上的安全系数,并且做好钢丝绳的包角工作。