高纯生铁生产工艺论文
高纯生铁生产工艺浅析
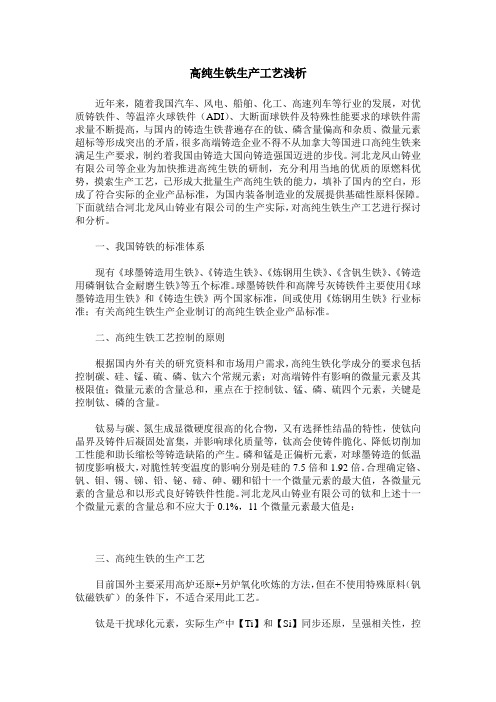
高纯生铁生产工艺浅析近年来,随着我国汽车、风电、船舶、化工、高速列车等行业的发展,对优质铸铁件、等温淬火球铁件(ADI)、大断面球铁件及特殊性能要求的球铁件需求量不断提高,与国内的铸造生铁普遍存在的钛、磷含量偏高和杂质、微量元素超标等形成突出的矛盾,很多高端铸造企业不得不从加拿大等国进口高纯生铁来满足生产要求,制约着我国由铸造大国向铸造强国迈进的步伐。
河北龙凤山铸业有限公司等企业为加快推进高纯生铁的研制,充分利用当地的优质的原燃料优势,摸索生产工艺,已形成大批量生产高纯生铁的能力,填补了国内的空白,形成了符合实际的企业产品标准,为国内装备制造业的发展提供基础性原料保障。
下面就结合河北龙凤山铸业有限公司的生产实际,对高纯生铁生产工艺进行探讨和分析。
一、我国铸铁的标准体系现有《球墨铸造用生铁》、《铸造生铁》、《炼钢用生铁》、《含钒生铁》、《铸造用磷铜钛合金耐磨生铁》等五个标准。
球墨铸铁件和高牌号灰铸铁件主要使用《球墨铸造用生铁》和《铸造生铁》两个国家标准,间或使用《炼钢用生铁》行业标准;有关高纯生铁生产企业制订的高纯生铁企业产品标准。
二、高纯生铁工艺控制的原则根据国内外有关的研究资料和市场用户需求,高纯生铁化学成分的要求包括控制碳、硅、锰、硫、磷、钛六个常规元素;对高端铸件有影响的微量元素及其极限值;微量元素的含量总和,重点在于控制钛、锰、磷、硫四个元素,关键是控制钛、磷的含量。
钛易与碳、氮生成显微硬度很高的化合物,又有选择性结晶的特性,使钛向晶界及铸件后凝固处富集,并影响球化质量等,钛高会使铸件脆化、降低切削加工性能和助长缩松等铸造缺陷的产生。
磷和锰是正偏析元素,对球墨铸造的低温韧度影响极大,对脆性转变温度的影响分别是硅的7.5倍和1.92倍。
合理确定铬、钒、钼、锡、锑、铅、铋、碲、砷、硼和铅十一个微量元素的最大值,各微量元素的含量总和以形式良好铸铁件性能。
河北龙凤山铸业有限公司的钛和上述十一个微量元素的含量总和不应大于0.1%,11个微量元素最大值是:三、高纯生铁的生产工艺目前国外主要采用高炉还原+另炉氧化吹炼的方法,但在不使用特殊原料(钒钛磁铁矿)的条件下,不适合采用此工艺。
炼铁高级技师技术论文(2)
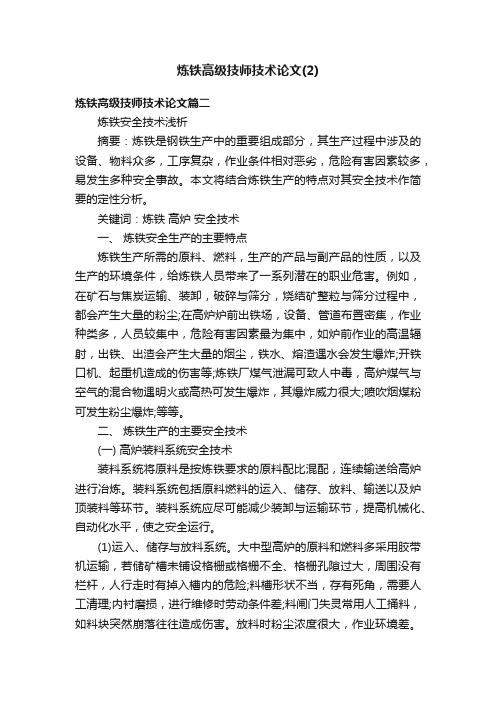
炼铁高级技师技术论文(2)炼铁高级技师技术论文篇二炼铁安全技术浅析摘要:炼铁是钢铁生产中的重要组成部分,其生产过程中涉及的设备、物料众多,工序复杂,作业条件相对恶劣,危险有害因素较多,易发生多种安全事故。
本文将结合炼铁生产的特点对其安全技术作简要的定性分析。
关键词:炼铁高炉安全技术一、炼铁安全生产的主要特点炼铁生产所需的原料、燃料,生产的产品与副产品的性质,以及生产的环境条件,给炼铁人员带来了一系列潜在的职业危害。
例如,在矿石与焦炭运输、装卸,破碎与筛分,烧结矿整粒与筛分过程中,都会产生大量的粉尘;在高炉炉前出铁场,设备、管道布置密集,作业种类多,人员较集中,危险有害因素最为集中,如炉前作业的高温辐射,出铁、出渣会产生大量的烟尘,铁水、熔渣遇水会发生爆炸;开铁口机、起重机造成的伤害等;炼铁厂煤气泄漏可致人中毒,高炉煤气与空气的混合物遇明火或高热可发生爆炸,其爆炸威力很大;喷吹烟煤粉可发生粉尘爆炸;等等。
二、炼铁生产的主要安全技术(一) 高炉装料系统安全技术装料系统将原料是按炼铁要求的原料配比混配,连续输送给高炉进行冶炼。
装料系统包括原料燃料的运入、储存、放料、输送以及炉顶装料等环节。
装料系统应尽可能减少装卸与运输环节,提高机械化、自动化水平,使之安全运行。
(1)运入、储存与放料系统。
大中型高炉的原料和燃料多采用胶带机运输,若储矿槽未铺设格栅或格栅不全、格栅孔隙过大,周围没有栏杆,人行走时有掉入槽内的危险;料槽形状不当,存有死角,需要人工清理;内衬磨损,进行维修时劳动条件差;料闸门失灵常用人工捅料,如料块突然崩落往往造成伤害。
放料时粉尘浓度很大,作业环境差。
因此,储矿槽的结构应是永久性的、坚固的。
各槽的形状应做到自动顺利下料,槽的倾角不应小于50°,以消除人工捅料的现象。
金属矿槽应安装振动器。
钢筋混凝土结构矿槽,内壁应铺设耐磨衬板;存放热烧结矿的内衬板应是耐热的。
矿槽上必须设置格栅,周围设栏杆,并保持完好。
高级纯铁冶炼工艺研究

(i unC aghn pc l t l o ,L . agn r p ScunJ nyu27 1 S ha hnee Sei e . t ,Pna Co ,i a i go6 10 ) c g aS eC d g u h a
Ab ta t rm e a p t fte s l t n o w ma a,s l n yEF,L n e nn y V s c :F o t s e  ̄o h ee i r md r h o f a met g b i F a d rf i b OD。te w oe p e f r i g h h l me  ̄ o
1 工 艺流 程及 技 术条 件
1 1 工 艺 流 程 .
功冶炼 出 6 2600 高级纯铁钢锭 ( 炉 3. t 4 已轧制成坯 共 2159, 中轧制 10方坯 1684, 制  ̄10 0 .4t其 3 6 . t轧 7 0 圆坯 3 65) 另 7炉 因 C P S高而改 判为 纯 0 或 4.7t。 、、 l
t e v r t n o l ma o t ai i fu t t h ao i e
w T a zde pacl .no e Iuet n n # 一s d ueint om pt BIIdadd maepr n ee nl e m htay I dro ̄8r eCc t t h a y i l r t 1 h o e oi f r epr r o eu a a e s e et s o o o IM r n c
量合 格 。
化 学成 分要 求 如表 1 。 122 轧制规 格 : ..
10 m x10 m 方 坯 , 度 10 r 一10 r 3 m 3 m 长 50 m 7 0 m; a a 0 0 m 圆坯 。 10 m 长度 《l0 m 。 O0 m
高炉炼铁论文

高炉炼铁论文时间:2010-11-12 08:12:40|浏览:112次|评论:0条 [收藏] [评论] [进入论坛]本文针对高炉炼铁工艺的生产现状进行了其技术性研究,使其高炉炼铁具有规模大、效率高、成本低等诸多优势,随着技术的发展,高炉正朝着大型化、高效化和自动化迈进。
实现渣铁分离。
已熔化的渣…本文针对高炉炼铁工艺的生产现状进行了其技术性研究,使其高炉炼铁具有规模大、效率高、成本低等诸多优势,随着技术的发展,高炉正朝着大型化、高效化和自动化迈进。
实现渣铁分离。
已熔化的渣铁之间及与固态焦炭接触过程中,发生诸多反应,最后调整铁液的成分和温度达到终点。
故保证炉料均匀稳定的下降,控制煤气流均匀合理分布是高质量完成冶炼过程的关键。
关键词: 固态焦炭渣铁分离炉料均匀煤气流分布绪论高炉是炼铁的专用设备。
虽然近代技术研究了直接还原、熔融技术还原等冶炼工艺,但它们都不能取代高炉,高炉生产是目前获得大量生铁的主要手段。
高炉生产是可持续的,他的一代寿命从开炉到大修的工作日一般为7-8年,有的已达到十年或十年以上。
高炉炼铁具有规模大、效率高、成本低等诸多优势,随着技术的发展,高炉正朝着大型化、高效化和自动化迈进。
1.1我国钢铁工业生产现状近代来高炉向大型化发方向发展,目前世界上已有数座5000立方米以上容积的高炉在生产。
我过也已经有4300立方米的高炉投入生产,日产生铁万吨以上,日消耗矿石等近2万吨,焦炭等燃料5千吨。
这样每天有数万吨的原、燃料运进和产品输出,还需要消耗大量的水、风、电气,生产规模及吞吐量如此之大,是其他企业不可比拟的。
1.2加入世贸对我国钢铁经济的影响钢铁工业是人类社会活动中占有着极其重要的地位,对发展国民经济起着极其重要的作用。
无论工业、农业、交通、建筑及国防均离不开钢铁。
一个国家的钢铁生产水平,就直接反映了这个国家的科学技术发展和人民的生活水平。
那么自中国加入世贸组织之后,自2001年底以来,全球钢铁价格已上涨2倍,提升了该行业的盈利水平。
超高纯铁精矿氢气还原生产纯铁技术研究

超高纯铁精矿氢气还原生产纯铁技术研究以超高纯铁精矿氢气还原生产纯铁技术研究为题,我们将探讨超高纯铁精矿氢气还原生产纯铁的技术研究情况以及其在工业生产中的应用。
铁是一种重要的金属材料,广泛应用于建筑、机械、电子等领域。
高纯度的铁具有更好的物理性能和化学性质,因此在一些特殊领域有着重要的应用价值。
超高纯铁精矿氢气还原生产纯铁技术,就是一种通过氢气还原超高纯度铁精矿,从而获得高纯度铁的方法。
在超高纯铁精矿氢气还原生产纯铁的过程中,首先需要选择合适的铁矿石作为原料。
超高纯铁精矿是一种铁含量较高的矿石,含有少量的杂质。
选择合适的矿石可以有效提高生产纯铁的效率和质量。
接下来,需要将选取的超高纯铁精矿进行预处理。
预处理主要是去除矿石中的杂质和硫化物,以提高还原过程的纯度和效果。
预处理方法包括矿石破碎、磁选和浮选等。
在氢气还原过程中,需要将预处理后的超高纯铁精矿与氢气进行反应。
反应过程中,需要控制温度、气体流速和反应时间等参数,以确保反应的完全性和产物的纯度。
反应完成后,产物中含有高纯度的铁和少量的氧化铁。
产物中的高纯度铁可以通过磁选、浮选和重力选矿等方法进行进一步的分离和纯化。
这些方法可以去除产物中的杂质和氧化铁,从而提高铁的纯度。
在工业生产中,超高纯铁精矿氢气还原生产纯铁技术具有重要的应用价值。
首先,该技术可以获得高纯度的铁,满足一些特殊领域对高纯度铁的需求。
其次,该技术具有环保、节能的特点,不会产生大量的废气和废水。
此外,该技术还可以有效利用矿石资源,提高资源利用率。
值得注意的是,超高纯铁精矿氢气还原生产纯铁技术在实际应用中还存在一些问题和挑战。
例如,反应过程中的温度和气体流速需要精确控制,以确保反应的完全性和产物的纯度。
同时,原料的选择和预处理也对产物的质量和产量有着重要影响。
因此,在实际应用中需要不断优化和改进该技术,以提高生产效率和产物质量。
总结而言,超高纯铁精矿氢气还原生产纯铁技术是一种重要的铁矿石还原方法,可以获得高纯度的铁。
超纯净工业纯铁生产工艺研究

超纯净工业纯铁生产工艺研究随着科技的飞速发展,超纯净工业纯铁在众多领域的应用越来越广泛,如电子、能源、航空航天等。
为了满足不同领域对超纯净工业纯铁的需求,研究者们不断探索优化其生产工艺。
本文将对超纯净工业纯铁生产工艺的研究进行详细介绍。
超纯净工业纯铁是指杂质元素含量极低的铁金属,其主要应用于高精度、高要求的场合。
目前,超纯净工业纯铁的生产工艺主要包括电弧熔炼、电子束熔炼、真空感应熔炼等。
然而,在生产过程中,超纯净工业纯铁易受杂质污染,如何提高其生产工艺成为当前研究的热点。
为了提高超纯净工业纯铁的生产工艺,研究者们采用了诸多研究方法。
通过实验设计,研究者们对生产过程中的主要影响因素进行了详细研究,包括原料纯度、熔炼温度、熔炼时间等。
研究者们还采用了数据收集和分析的方法,以获取生产过程中不同阶段的数据,以便对生产工艺进行优化。
同时,在理论研究方面,研究者们结合计算材料学方法,对超纯净工业纯铁的原子结构和电子性质进行了深入研究。
在实验研究方面,通过调整熔炼温度和时间,研究者们成功地提高了超纯净工业纯铁的纯度。
同时,通过对比不同纯度的工业纯铁,研究者们发现,提高原料纯度对超纯净工业纯铁的生产具有重要意义。
在理论研究方面,计算材料学方法为超纯净工业纯铁的原子结构和电子性质提供了精确预测,有助于优化生产工艺。
本文对超纯净工业纯铁生产工艺的研究进行了详细介绍。
通过实验研究和理论研究,研究者们发现提高原料纯度和控制熔炼温度和时间是提高超纯净工业纯铁生产工艺的关键。
随着科技的不断进步,相信超纯净工业纯铁在未来的应用前景将更加广阔。
展望未来,我们期望在超纯净工业纯铁的生产工艺方面取得更多突破性成果。
需要进一步优化生产工艺参数,实现超纯净工业纯铁的大规模生产。
需要加强生产过程中的质量控制,确保产品的一致性和可靠性。
我们还应积极探索新型生产技术,如离子束熔炼、等离子体熔炼等,以满足更高层次的应用需求。
我们还应重视超纯净工业纯铁在环保和能源领域的应用研究。
炼铁高级技术论文
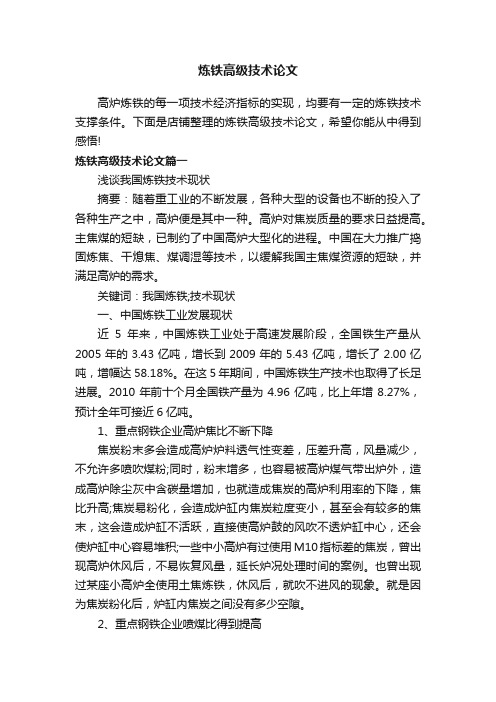
炼铁高级技术论文高炉炼铁的每一项技术经济指标的实现,均要有一定的炼铁技术支撑条件。
下面是店铺整理的炼铁高级技术论文,希望你能从中得到感悟!炼铁高级技术论文篇一浅谈我国炼铁技术现状摘要:随着重工业的不断发展,各种大型的设备也不断的投入了各种生产之中,高炉便是其中一种。
高炉对焦炭质量的要求日益提高。
主焦煤的短缺,已制约了中国高炉大型化的进程。
中国在大力推广捣固炼焦、干熄焦、煤调湿等技术,以缓解我国主焦煤资源的短缺,并满足高炉的需求。
关键词:我国炼铁;技术现状一、中国炼铁工业发展现状近5年来,中国炼铁工业处于高速发展阶段,全国铁生产量从2005年的3.43亿吨,增长到2009年的5.43亿吨,增长了2.00亿吨,增幅达58.18%。
在这5年期间,中国炼铁生产技术也取得了长足进展。
2010年前十个月全国铁产量为4.96亿吨,比上年增8.27%,预计全年可接近6亿吨。
1、重点钢铁企业高炉焦比不断下降焦炭粉末多会造成高炉炉料透气性变差,压差升高,风量减少,不允许多喷吹煤粉;同时,粉末增多,也容易被高炉煤气带出炉外,造成高炉除尘灰中含碳量增加,也就造成焦炭的高炉利用率的下降,焦比升高;焦炭易粉化,会造成炉缸内焦炭粒度变小,甚至会有较多的焦末,这会造成炉缸不活跃,直接使高炉鼓的风吹不透炉缸中心,还会使炉缸中心容易堆积;一些中小高炉有过使用M10指标差的焦炭,曾出现高炉休风后,不易恢复风量,延长炉况处理时间的案例。
也曾出现过某座小高炉全使用土焦炼铁,休风后,就吹不进风的现象。
就是因为焦炭粉化后,炉缸内焦炭之间没有多少空隙。
2、重点钢铁企业喷煤比得到提高提高高炉喷煤比是炼铁系统结构优化的中心环节,是世界炼铁技术发展的主流。
高炉喷吹煤粉是节约焦炭、降低炼铁成本的重要措施之一,同时可以改善钢铁工业能源结构,缓解我国主焦煤资源短缺的矛盾。
多喷煤,少用焦炭,就可以少建焦炉,从而降低炼铁系统的建设投资和生产运行费用,并减少焦炉生产过程中对环境的污染,还可大大提高钢铁企业的劳动生产率和市场竞争力。
高炉炼铁技术论文(2)
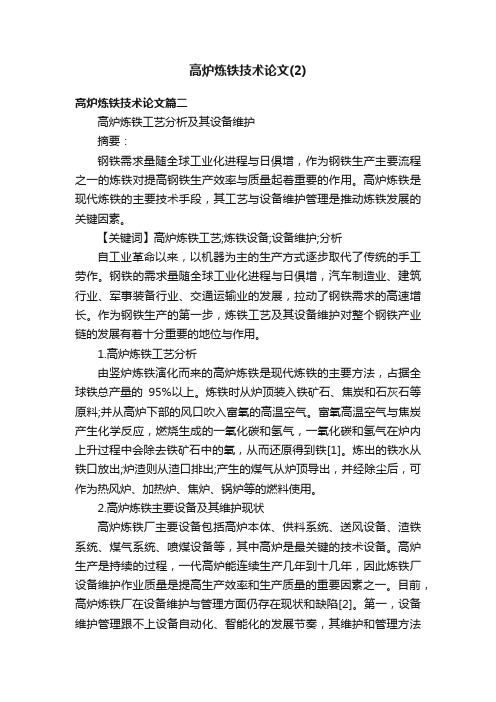
高炉炼铁技术论文(2)高炉炼铁技术论文篇二高炉炼铁工艺分析及其设备维护摘要:钢铁需求量随全球工业化进程与日俱增,作为钢铁生产主要流程之一的炼铁对提高钢铁生产效率与质量起着重要的作用。
高炉炼铁是现代炼铁的主要技术手段,其工艺与设备维护管理是推动炼铁发展的关键因素。
【关键词】高炉炼铁工艺;炼铁设备;设备维护;分析自工业革命以来,以机器为主的生产方式逐步取代了传统的手工劳作。
钢铁的需求量随全球工业化进程与日俱增,汽车制造业、建筑行业、军事装备行业、交通运输业的发展,拉动了钢铁需求的高速增长。
作为钢铁生产的第一步,炼铁工艺及其设备维护对整个钢铁产业链的发展有着十分重要的地位与作用。
1.高炉炼铁工艺分析由竖炉炼铁演化而来的高炉炼铁是现代炼铁的主要方法,占据全球铁总产量的95%以上。
炼铁时从炉顶装入铁矿石、焦炭和石灰石等原料;并从高炉下部的风口吹入富氧的高温空气。
富氧高温空气与焦炭产生化学反应,燃烧生成的一氧化碳和氢气,一氧化碳和氢气在炉内上升过程中会除去铁矿石中的氧,从而还原得到铁[1]。
炼出的铁水从铁口放出;炉渣则从渣口排出;产生的煤气从炉顶导出,并经除尘后,可作为热风炉、加热炉、焦炉、锅炉等的燃料使用。
2.高炉炼铁主要设备及其维护现状高炉炼铁厂主要设备包括高炉本体、供料系统、送风设备、渣铁系统、煤气系统、喷煤设备等,其中高炉是最关键的技术设备。
高炉生产是持续的过程,一代高炉能连续生产几年到十几年,因此炼铁厂设备维护作业质量是提高生产效率和生产质量的重要因素之一。
目前,高炉炼铁厂在设备维护与管理方面仍存在现状和缺陷[2]。
第一,设备维护管理跟不上设备自动化、智能化的发展节奏,其维护和管理方法滞后于设备的更新。
第二,炼铁厂在追求单位时间产量的同时忽略了设备的正常维护,致使设备超长时间、超负荷工作。
第三,工厂没有注重设备的前期管理。
设备出故障的原因往往来自设备的设计和制造。
选用先进、合理的设备,才能真正发挥其应有的作用,降低故障突发率。
年产630万吨生铁的高炉炼铁车间工艺设计毕业论文
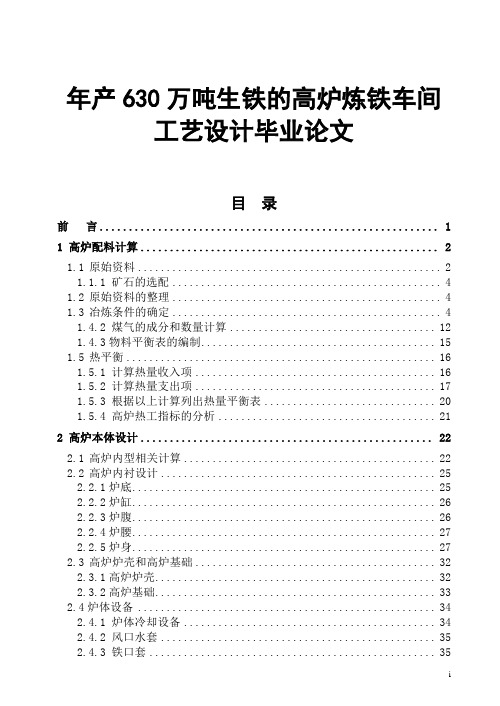
年产630万吨生铁的高炉炼铁车间工艺设计毕业论文目录前言 (1)1 高炉配料计算 (2)1.1原始资料 (2)1.1.1 矿石的选配 (4)1.2原始资料的整理 (4)1.3冶炼条件的确定 (4)1.4.2 煤气的成分和数量计算 (12)1.4.3物料平衡表的编制 (15)1.5热平衡 (16)1.5.1 计算热量收入项 (16)1.5.2 计算热量支出项 (17)1.5.3 根据以上计算列出热量平衡表 (20)1.5.4 高炉热工指标的分析 (21)2 高炉本体设计 (22)2.1高炉内型相关计算 (22)2.2高炉内衬设计 (25)2.2.1炉底 (25)2.2.2炉缸 (26)2.2.3炉腹 (26)2.2.4炉腰 (27)2.2.5炉身 (27)2.3高炉炉壳和高炉基础 (32)2.3.1高炉炉壳 (32)2.3.2高炉基础 (33)2.4炉体设备 (34)2.4.1 炉体冷却设备 (34)2.4.2 风口水套 (35)2.4.3 铁口套 (35)2.4.4炉喉钢砖 (35)2.4.5 炉顶保护板 (35)3 料运系统计算及装料布料设备 (36)3.1贮矿槽 (36)3.1.1 平面布置 (36)3.1.2 槽上运输方式 (36)3.1.3 储矿槽工艺参数 (36)3.1.4 槽下供料 (37)3.2料坑设备 (37)3.3碎焦运送设施 (38)3.4上料设备 (38)4 高炉鼓风机的选择 (39)4.1高炉鼓风量及鼓风压力的确定 (39)4.1.1 高炉入炉风量 (39)4.1.2 鼓风机出口风量 (39)4.1.3 高炉鼓风压力 (40)4.2高炉鼓风机能力的确定 (40)4.2.1 大气状况对高炉鼓风的影响 (40)4.2.2 鼓风机工况的计算 (40)4.2.3 鼓风机的选择 (41)4.3高炉鼓风机的工艺过程 (42)5 热风炉 (43)5.1计算的原始数据 (43)5.2燃烧计算 (44)5.2.1 煤气成分换算 (44)5.2.2 煤气发热值计算 (44)5.2.3 燃烧1标米3煤气的空气需要量 (45)5.2.4燃烧1标米3煤气生成的烟气量灰分分组成 (45)5.2.5理论燃烧温度和实际燃烧温度计算 (46)5.3热平衡计算 (48)5.3.1 计算鼓风从80℃提高到1200℃所增加的热含量 (48)5.3.2 加热1标米3鼓风需要的煤气量 (48)5.3.3 煤气消耗量及烟气量 (48)5.4蓄热室热工计算 (49)5.4.1 热工计算的原始条件 (51)5.4.2 蓄热室各部位的烟气及鼓风温度 (52)5.4.3 蓄热室面积及各段砖格子高度的计算 (53)5.4.4蓄热室面积及蓄热室各段高度的调整 (55)5.5热风炉的蓄热面积指标 (55)6 风口平台及渣铁处理系统 (57)6.1风口平台和出铁场布置 (57)6.1.1 铁口及出铁场数目的确定 (57)6.1.2 渣、铁沟及其流嘴布置 (58)6.2风口平台和出铁场设备 (58)6.2.1 泥炮 (58)6.2.2 开铁口机 (59)6.2.3堵渣口机 (59)6.2.4炉前吊车 (60)6.2.5铁水罐车 (60)6.2.6渣罐车 (61)6.3风口平台和出铁场结构 (62)6.3.1风口平台 (62)6.3.2 出铁场 (62)6.4铁水处理 (62)6.5渣的处理 (62)7 高炉煤气处理系统 (64)7.1工艺流程 (64)7.2煤气除尘设备 (64)7.2.1 粗除尘设备——重力除尘器 (64)7.2.2 精细除尘设备——布袋除尘器 (65)7.2.3 脱水器 (65)7.3煤气除尘系统附属设备 (66)7.3.1 粗煤气管道 (66)7.3.2 调节阀组 (66)7.3.3 煤气遮断阀 (66)7.3.4 煤气放散阀 (66)8 高炉喷吹煤粉系统 (67)8.1喷煤系统 (67)8.2喷吹工艺 (67)8.3主要设备 (68)8.3.1 混合器 (68)8.3.2 分配器 (68)8.3.3 喷煤枪 (68)8.3.4 喷氧枪 (68)9部分车间布置与总图运输 (69)9.1车间平面布置 (69)9.2厂区的选择 (69)9.3总图运输 (69)10参考文献 (70)致谢 (71)专题添加微量纳米铜粉在冶金制件烧结时的作用 (72)前言毕业设计是大学学习过程中的最后一个环节,对每个大学生的学习能力和以后的工作实践能力都会有很大的帮助与提高。
高炉炼铁技术论文

高炉炼铁技术论文现代高炉炼铁【摘要】对高炉炼铁工艺的生产现状进行了技术研究,使高炉炼铁具有规模大、效率高、成本低等优点。
随着技术的发展,高炉正朝着大型化、高效化、自动化的方向发展。
【关键词】固态焦炭;渣铁分离;炉料均匀;煤气流分布高炉是炼铁的专用设备。
虽然现代技术研究了直接还原法和熔融还原法等冶炼工艺,但它们不能取代高炉。
高炉生产是目前获取大量生铁的主要手段。
在现代,高炉已经向大规模发展。
目前,世界上有几座容积超过5000立方米的高炉在生产。
投产高炉4300立方米,日产生铁1万多吨,矿石近2万吨,焦炭等燃料5000吨。
这样,每天运输数万吨原材料和燃料以及产品产量也需要消耗大量的水、风和电。
生产规模和产量之大是其他企业无法比拟的。
1高炉炼铁工艺技术参数研究高炉冶炼过程在密闭竖炉中进行。
高炉冶炼过程的特点是在炉料和煤气的逆流运动过程中完成各种错综复杂的化学反应和物理变化。
由于高炉是一个密封的容器,除了给料和生产铁、渣、气外,操作人员不能直接观察反应过程的状态,只能用仪器仪表间接观察。
为了弄清这些反应和变化的规律,我们首先应该对整个冶炼过程有一个全面而全面的了解,这反映在对不同高度运行的高炉纵断面和横断面图像的正确描述上。
这将有助于正确理解和把握各种单一过程和因素之间的关系。
高炉冶炼的主要目的是利用铁矿石经济高效地获得所需温度和成分的液态生铁。
因此,一方面要实现矿石中铁、氧元素的化学分离,即还原过程;另一方面,还需要实现还原金属和脉石的机械分离,即熔融和结渣过程。
最后,控制温度与液态渣铁之间的相互作用,以获得温度和化学成分合格的铁水。
整个过程是在炉料与煤气自上而下紧密接触的过程中完成的。
在下落过程中,低温矿石逐渐被氧剥离,由外到内被气体还原,同时从高温气体中获得热量。
当矿石上升到一定的温度极限时,先软化后熔融滴落,实现渣铁分离。
铁水与固体焦炭接触时发生了许多反应,最终将铁水的成分和温度调整到终点。
注:因此,保证炉料均匀稳定下降,控制气流均匀合理分布,是高质量完成冶炼过程的关键。
高纯生铁冶炼
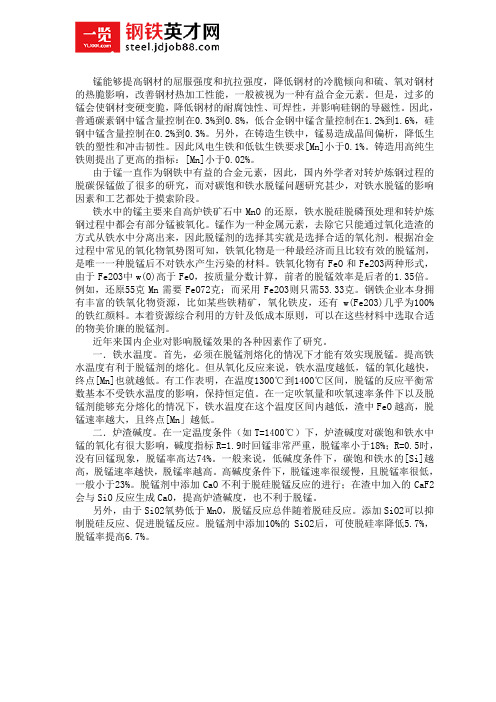
锰能够提高钢材的屈服强度和抗拉强度,降低钢材的冷脆倾向和硫、氧对钢材的热脆影响,改善钢材热加工性能,一般被视为一种有益合金元素。
但是,过多的锰会使钢材变硬变脆,降低钢材的耐腐蚀性、可焊性,并影响硅钢的导磁性。
因此,普通碳素钢中锰含量控制在0.3%到0.8%,低合金钢中锰含量控制在1.2%到1.6%,硅钢中锰含量控制在0.2%到0.3%。
另外,在铸造生铁中,锰易造成晶间偏析,降低生铁的塑性和冲击韧性。
因此风电生铁和低钛生铁要求[Mn]小于0.1%。
铸造用高纯生铁则提出了更高的指标:[Mn]小于0.02%。
由于锰一直作为钢铁中有益的合金元素,因此,国内外学者对转炉炼钢过程的脱碳保锰做了很多的研究,而对碳饱和铁水脱锰问题研究甚少,对铁水脱锰的影响因素和工艺都处于摸索阶段。
铁水中的锰主要来自高炉铁矿石中MnO的还原,铁水脱硅脱磷预处理和转炉炼钢过程中都会有部分锰被氧化。
锰作为一种金属元素,去除它只能通过氧化造渣的方式从铁水中分离出来,因此脱锰剂的选择其实就是选择合适的氧化剂。
根据冶金过程中常见的氧化物氧势图可知,铁氧化物是一种最经济而且比较有效的脱锰剂,是唯一一种脱锰后不对铁水产生污染的材料。
铁氧化物有FeO和Fe2O3两种形式,由于Fe2O3中w(O)高于FeO,按质量分数计算,前者的脱锰效率是后者的1.35倍。
例如,还原55克Mn需要FeO72克;而采用Fe2O3则只需53.33克。
钢铁企业本身拥有丰富的铁氧化物资源,比如某些铁精矿,氧化铁皮,还有w(Fe2O3)几乎为100%的铁红颜料。
本着资源综合利用的方针及低成本原则,可以在这些材料中选取合适的物美价廉的脱锰剂。
近年来国内企业对影响脱锰效果的各种因素作了研究。
一.铁水温度。
首先,必须在脱锰剂熔化的情况下才能有效实现脱锰。
提高铁水温度有利于脱锰剂的熔化。
但从氧化反应来说,铁水温度越低,锰的氧化越快,终点[Mn]也就越低。
有工作表明,在温度1300℃到1400℃区间,脱锰的反应平衡常数基本不受铁水温度的影响,保持恒定值。
钢铁生产流程论文
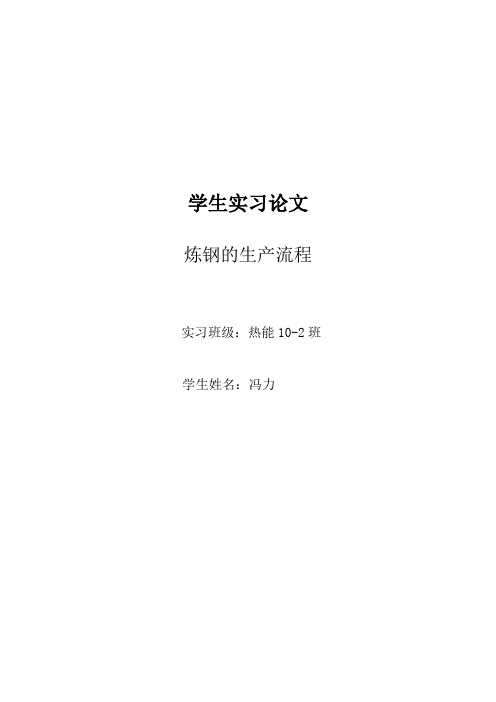
学生实习论文炼钢的生产流程实习班级:热能10-2班学生姓名:冯力一、炼钢的历史:中国是世界上最早生产钢的国家之一。
考古工作者曾经在湖南长沙杨家山春秋晚期的墓葬中发掘出一把铜格“铁剑”,通过金相检验,结果证明是钢制的。
这是迄今为止我们见到的中国最早的钢制实物。
它说明从春秋晚期起中国就有炼钢生产了,炼钢生产在中国已有2500多年的历史。
二、炼钢的生产流程与设备:把炼钢用生铁放到炼钢炉内按一定工艺熔炼,即得到钢。
钢的产品有钢锭、连铸坯和直接铸成各种钢铸件等。
通常所讲的钢,一般是指轧制成各种钢材的钢。
钢属于黑色金属但钢不完全等于黑色金属。
炼钢大体可以分为以下几个步骤:加热、造渣、出渣、熔池搅拌、脱磷、电炉底吹、熔化期、氧化期、精炼期、还原期、炉外精炼、钢液搅拌、钢包喂丝、钢包处理、钢包精炼、气体处理、预合金化、成分控制、增硅、增硅、终点控制、出钢。
炼钢安全生产的主要特点:铁水中含有C、S、P等杂质,影响铁的强度和脆性等,需要对铁水进行再冶炼,以去除上述杂质,并加入Si、Mn等,调整其成分。
对铁水进行重新冶炼以调整其成分的过程叫作炼钢。
炼钢的主要原料是含炭较高的铁水或生铁以及废钢铁。
为了去除铁水中的杂质,还需要向铁水中加入氧化剂、脱氧剂和造渣材料,以及铁合金等材料,以调整钢的成分。
含炭较高的铁水或生铁加入炼钢炉以后,经过供氧吹炼、加矿石、脱炭等工序,将铁水中的杂质氧化除去,最后加入合金,进行合金化,便得到钢水。
炼钢炉有平炉、转炉和电炉3种,平炉炼钢法因能耗高、作业环境差已逐步淘汰。
转炉和平炉炼钢是先将铁水装入混铁炉预热,将废钢加入转炉或平炉内,然后将混铁炉内的高温铁水用混铁车兑入转炉或平炉,进行融化与提温,当温度合适后,进入氧化期。
电炉炼钢是在电炉炉钢内全部加入冷废钢,经过长时间的熔化与提温,再进入氧化期。
(1)融化过程。
铁水及废钢中含有C、Mn、Si、P、S等杂质,在低温融化过程中,C、Si、P、S被氧化,即使单质态的杂质变为化合态的杂质,以利于后期进一步去除杂质。
年产330万吨生铁(其中炼钢生铁78%,铸造生铁22%)的高炉炼铁车间工艺设计
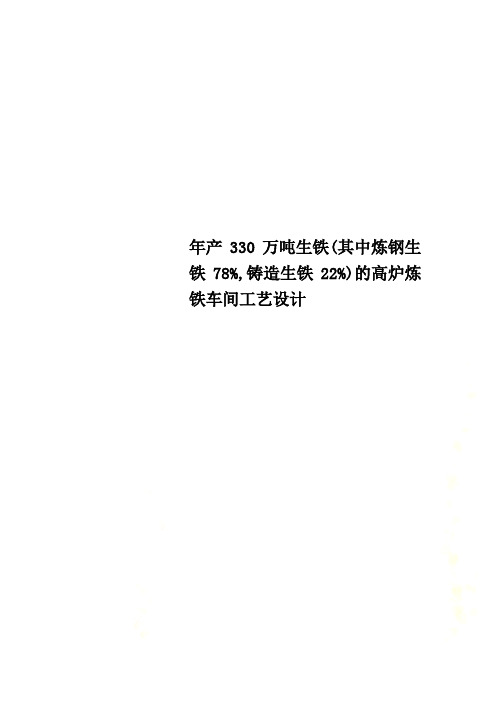
年产330万吨生铁(其中炼钢生铁78%,铸造生铁22%)的高炉炼铁车间工艺设计西安建筑科技大学本科毕业设计(论文)题目年产330万吨生铁(其中炼钢生铁78%,铸造生铁22%)的高炉炼铁车间工艺设计学生姓名学号院(系)冶金工程学院专业冶金工程指导教师时间2017年 6 月12 日西安建筑科技大学本科毕业设计(论文)任务书题目:年产330万吨生铁(其中炼钢生铁78%,铸造生铁22%)的高炉炼铁车间工艺设计院(系):冶金工程学院专业:冶金工程学生姓名:学号:指导教师(签名):主管院长(主任)(签名):时间:2017 年 2 月27 日一、毕业设计(论文)的主要内容(含主要技术参数)1.为了更好的完成毕业设计(论文) ,进行企业调研等工作,收集整理相关文献资料,制定工艺设计方案(论文研究方案);2.包括对各种高炉原、燃料的原始化学成分进行成分处理,熟悉冶金计算过程;3.对高炉炉型进行规划,高炉内型计算,本体结构设计料运系统方案设计;4.进行热风炉热工计算与结构设计;5.煤气处理工艺及流程设计、出铁场及渣铁处理系统工艺设计;6.主要设备选型和车间平面设计及总图运输方案的确定;7.生产组织编制及各项技术经济指标的确定;8.编制说明书一份(不少于三万字),绘制车间平面图(A0一张)、高炉砌砖图(A1一张)和热风炉砌砖图(A1一张)各一张;9.安全、环保、节能与消防10.完成专题研究报告一份;11.完成一篇外文文献的翻译。
二、毕业设计(论文)应完成的工作(含图纸数量)1.查阅相关文献,对收集的资料进行整理,制定工艺设计方案(论文研究方案),进行技术准备;2.完成设计任务,写出毕业设计说明书(不少于3万字);3.绘制设计图3张(绘制车间平面图(A0一张)、高炉砌砖图(A1一张)和热风炉砌砖图(A1一张));4.翻译与本专业有关的外文译文1篇,达到要求的工作量(不少于5000字);5.完成专题研究,参照科技论文的格式写出研究报告(不少于5000字)。
一种4n级高纯铁及其火法工业化生产方法
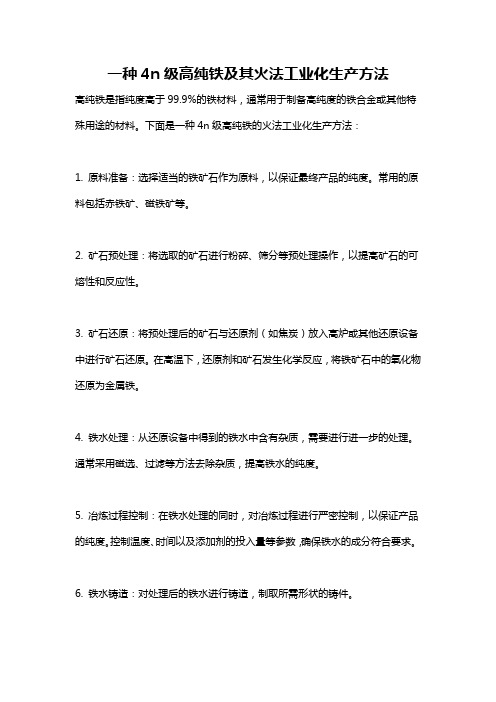
一种4n级高纯铁及其火法工业化生产方法
高纯铁是指纯度高于99.9%的铁材料,通常用于制备高纯度的铁合金或其他特殊用途的材料。
下面是一种4n级高纯铁的火法工业化生产方法:
1. 原料准备:选择适当的铁矿石作为原料,以保证最终产品的纯度。
常用的原料包括赤铁矿、磁铁矿等。
2. 矿石预处理:将选取的矿石进行粉碎、筛分等预处理操作,以提高矿石的可熔性和反应性。
3. 矿石还原:将预处理后的矿石与还原剂(如焦炭)放入高炉或其他还原设备中进行矿石还原。
在高温下,还原剂和矿石发生化学反应,将铁矿石中的氧化物还原为金属铁。
4. 铁水处理:从还原设备中得到的铁水中含有杂质,需要进行进一步的处理。
通常采用磁选、过滤等方法去除杂质,提高铁水的纯度。
5. 冶炼过程控制:在铁水处理的同时,对冶炼过程进行严密控制,以保证产品的纯度。
控制温度、时间以及添加剂的投入量等参数,确保铁水的成分符合要求。
6. 铁水铸造:对处理后的铁水进行铸造,制取所需形状的铸件。
7. 检验和精炼:对铸件进行检验,检测铸件的纯度和性能,并根据需要进行精炼处理以提高产品的纯度和品质。
常用的精炼方式包括真空冶炼、气氛冶炼等。
8. 成品包装:对最终产品进行包装和标识,以便储存和销售。
以上是一种常见的4n级高纯铁的火法工业化生产方法,具体的操作细节和设备配置可能会因厂家和地点而有所不同。
我国高纯生铁的生产和应用情况
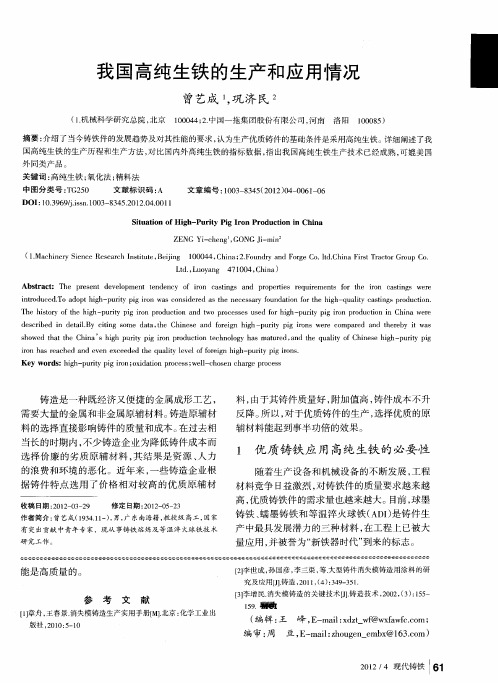
DOI 1.9 9 .s.0 3 8 4 .0 2 40 1 :03 6  ̄i n10 — 3 5 1 . . 1 s 2 0 0
Siuato ofH ih-Purt g r o t in g iy Pi I on Pr duc i n Chi ton i na
ZE — h n ’ GO NG Yi c e g , NG i mi J- n
Ld , u y n 4 1 0 , hn ) t.L o a g 7 0 4 C i a
Ab t a t T e r s n d v lp n tn e c o r n a t g a d r p ris e u r me t o t e r n a t g w r s r c : h p e e t e eo me t e d n y f i c si s n p o e t r q i o n e e n s r h io c s n s e e f i
我 国高纯 生铁 的生产和应用情况
曾艺成 1巩 济 民 2 ,
(. 械科学研究总院 , 京 1 机 北 104 ;. 一 拖 集 团 股 份有 限公 司 , 南 0 0 4 2中国 河 洛阳 10 8 ) 0 0 5
摘要 : 介绍了当今铸铁件 的发展趋势及对其性能 的要求 , 为生产优质铸件的基础条件是采用高纯生铁 。 认 详细阐述了我
1 优 质 铸 பைடு நூலகம் 应 用 高 纯 生铁 的 必要 性
io sr a he nd e e x e de h uaiy lve ff r in hih—p it g io . r n ha e c d a v n e c e d t e q lt e lo o eg g ur y pi r ns Ke y wor :hih— rt g io o i to o e s; l—c os n c r e p o e s ds g pu iy pi r n; xdai n pr c s we l h e ha g r c s
钢铁竟是这样炼成的作文1000字

钢铁竟是这样炼成的作文1000字钢铁的炼制主要分为两个步骤:炼铁和炼钢。
首先是炼铁,炼铁过程又分为高炉法和直接还原法。
高炉法是最常见的炼铁方法,它以铁矿石为原料,通过高温还原反应产生铁。
将矿石和燃料(通常是焦炭)放入高炉内,并加入石灰石作为熔化剂。
然后点火,燃烧的焦炭产生高温燃烧气体,将矿石还原成铁。
在高炉顶部喷入热风,促使还原反应进行。
反应完成后,从高炉底部排出熔化的铁水和炉渣。
铁水经过冷却和净化处理后,成为炼铁厂生产的生铁。
直接还原法是另一种炼铁方法,它以铁矿石和还原剂为原料,在直接还原反应中生成铁。
这种方法对于高磷、高硫的铁矿石适用,因为直接还原可以去除这些杂质。
将矿石和还原剂混合在一起,并在高温条件下进行还原反应。
这样可以将矿石中的氧气和杂质还原掉,得到高纯度的铁。
接下来是炼钢过程。
炼钢是将生铁转化为钢的过程,以提高钢的质量和性能。
常用的炼钢方法有转炉法和电弧炉法。
转炉法是使用大型转炉将生铁和废钢材料进行冶炼。
将生铁和废钢倒入转炉内,并加入适量的石灰石和其他调剂剂。
然后,通过吹入空气或氧气,使铁中的杂质氧化,产生大量的热能,也促进反应的进行。
在这个过程中,通过不断搅拌转炉熔池,将杂质从铁水中分离出来。
将炼好的钢水从转炉底部倒出。
电弧炉法是一种使用电弧加热的炼钢方法。
将废钢和生铁放入电弧炉中,并加入一定量的废石墨电极。
然后,通过高温电弧的加热和冶炼,将废钢和生铁融化在一起。
电弧炉法能够提供高温和搅拌效果,以便更好地控制杂质含量和炼钢的质量。
无论是高炉法还是直接还原法,以及转炉法和电弧炉法,都需要经过多道复杂的工艺流程,才能最终得到我们常见的钢材。
这些流程包括矿石破碎、矿石选矿、燃料供应、冶炼反应和冷却处理等。
每个环节都需要高精度的设备和操作技术,才能保证钢铁质量的稳定和合格。
钢铁竟是这样炼成的作文1000字

钢铁竟是这样炼成的作文1000字钢铁是一种重要的金属材料,用途广泛,被广泛应用于建筑、制造业等领域。
很少有人知道钢铁是如何炼成的,下面将向大家介绍钢铁的炼制过程。
钢铁最早的炼制方法可以追溯到几千年前的冶金时代,那时人们利用木炭和陶器制作的窑炉进行炼铁。
这种方法主要是通过加热铁矿石并加入木炭作为还原剂,使得铁矿石中的铁氧化物还原为金属铁。
但这种方法的效率很低,产量有限。
随着科技的发展,钢铁的炼制方法也不断改进。
如今,最常用的炼铁方法是高炉法。
高炉法的基本原理是将铁矿石与焦炭、石灰石一起放入高炉中炼制。
高炉传统上是由砖石建造的大型筒状结构,高数十米,并且内部装有耐火材料。
在高炉内,铁矿石首先经过焦炭的还原,生成金属铁,并与石灰石反应产生炼渣。
然后,金属铁与炼渣被分离,炼渣被排出高炉,而金属铁则下流至底部,并通过炼铁口取出。
高炉法是一种大规模的炼铁方法,具有高效率和高产量的优点。
高炉法也存在一些问题。
高炉法需要大量的能源,通常采用焦炭作为燃料,这会导致环境污染。
高炉炼制出的铁虽然成分纯度较高,但是硫、磷等杂质仍然较高,需要经过进一步的处理才能生产出高质量的钢材。
随着科技的不断进步,人们也研发出了其他的炼铁方法,例如电弧炉法和氧气转炉法。
电弧炉法是利用电弧产生高温,将废钢等回收材料熔化,然后经过调质、除氧等处理制成钢材。
电弧炉法具有灵活性高、操作简便等优点,被广泛应用于钢铁回收和特殊钢材的生产。
氧气转炉法则是通过注入氧气和其他搅拌装置,将炉内的炉渣产生氧气炸溅反应,吸收大量碳和硅等杂质,从而提高钢材的质量。
钢铁的炼制过程经历了数千年的发展和演变。
从最早的简易窑炉到现代高炉法、电弧炉法和氧气转炉法等,钢铁的炼制方法不断创新,使得钢铁的生产效率和质量得到了大幅提升。
炼铁过程中也面临一些问题,如能源消耗和环境污染等。
为了可持续发展,还需要进一步探索和研发更加环保和高效的炼铁方法。
钢铁竟是这样炼成的,这一过程不仅是实现了人类社会对钢铁的需求,也是冶金技术的发展和进步的体现。
毕业论文-- 年产150万吨生铁的炼铁厂设计
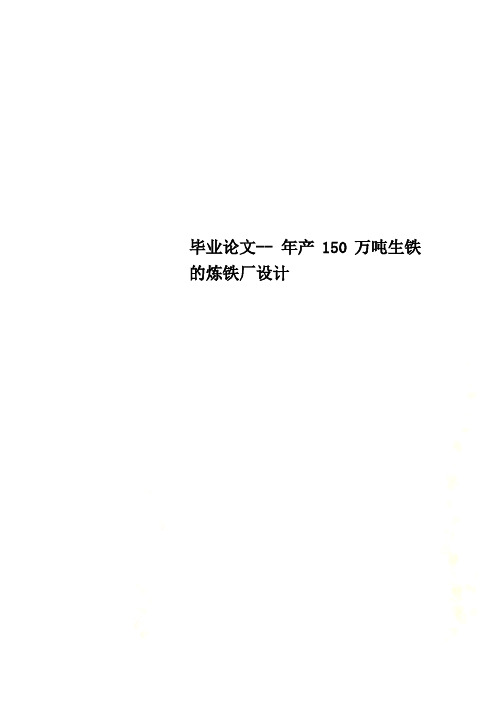
毕业论文-- 年产150万吨生铁的炼铁厂设计湖南化工职业技术学院毕业设计(论文)题目年产150万吨生铁的炼铁厂设计院(系)湖南化工职业技术学院应用化学系专业班级冶金技术1011班学生姓名陈轩学号************指导教师施丽丽职称讲师评阅教师___ _ 职称___ 2012年 12 月 1日目录中文摘要 ...................................................................................................................... I I ABSTRACT .. (III)1 绪论 (1)1.1我国高炉炼铁技术的进步 (1)1.2我国高炉炼铁技术的发展趋势 (2)2 高炉配料计算 (3)2.1配料计算的目的 (3)2.2配料计算时需要确定的已知条件 (3)2.3计算过程 (7)3 高炉物料平衡计算 (9)3.1高炉物料平衡计算的意义 (9)3.2高炉物料平衡计算的内容 (9)4 高炉热平衡计算 (14)4.1热平衡计算的目的 (14)4.2热平衡计算方法 (14)4.3热平衡计算过程 (15)5 高炉炉型设计 (21)5.1总述 (21)5.2高炉炉型计算 (21)5.3绘制高炉设计炉型图 (23)6高炉八大系统 (24)6.1高炉煤气回收除尘系统 (24)6.2高炉本体 (24)6.3高炉渣铁处理系统 (25)6.4高炉送料系统 (26)6.5高炉喷吹系统 (26)6.6炉顶装料系统 (27)6.7高炉送风系统 (28)6.8高炉动力系统 (29)结语 (30)参考文献 (31)致谢 (32)中文摘要高炉炼铁是获得生铁的主要手段,也是钢铁冶金过程中最重要的环节之一,在国民经济建设中起着举足轻重的作用。
高炉流程是一种古老的冶金工艺,近几十年来取得了巨大进步并在持续改进。
高炉炼铁需要大量的煤和焦炭作铁矿石的还原剂,导致CO2的排放。
- 1、下载文档前请自行甄别文档内容的完整性,平台不提供额外的编辑、内容补充、找答案等附加服务。
- 2、"仅部分预览"的文档,不可在线预览部分如存在完整性等问题,可反馈申请退款(可完整预览的文档不适用该条件!)。
- 3、如文档侵犯您的权益,请联系客服反馈,我们会尽快为您处理(人工客服工作时间:9:00-18:30)。
高纯生铁生产工艺浅析
中图分类号:tg 文献标识码:a 文章编号:1007-0745(2011)11-0143-01
近年来,随着我国汽车、风电、船舶、化工、高速列车等行业
的发展,对优质铸铁件、等温淬火球铁件(adi)、大断面球铁件及
特殊性能要求的球铁件需求量不断提高,与国内的铸造生铁普遍存
在的钛、磷含量偏高和杂质、微量元素超标等形成突出的矛盾,很
多高端铸造企业不得不从加拿大等国进口高纯生铁来满足生产要
求,制约着我国由铸造大国向铸造强国迈进的步伐。
河北龙凤山铸
业有限公司等企业为加快推进高纯生铁的研制,充分利用当地的优
质的原燃料优势,摸索生产工艺,已形成大批量生产高纯生铁的能
力,填补了国内的空白,形成了符合实际的企业产品标准,为国内
装备制造业的发展提供基础性原料保障。
下面就结合河北龙凤山铸
业有限公司的生产实际,对高纯生铁生产工艺进行探讨和分析。
一、我国铸铁的标准体系
现有《球墨铸造用生铁》、《铸造生铁》、《炼钢用生铁》、《含钒
生铁》、《铸造用磷铜钛合金耐磨生铁》等五个标准。
球墨铸铁件和
高牌号灰铸铁件主要使用《球墨铸造用生铁》和《铸造生铁》两个
国家标准,间或使用《炼钢用生铁》行业标准;有关高纯生铁生产
企业制订的高纯生铁企业产品标准。
二、高纯生铁工艺控制的原则
根据国内外有关的研究资料和市场用户需求,高纯生铁化学成
分的要求包括控制碳、硅、锰、硫、磷、钛六个常规元素;对高端铸件有影响的微量元素及其极限值;微量元素的含量总和,重点在于控制钛、锰、磷、硫四个元素,关键是控制钛、磷的含量。
钛易与碳、氮生成显微硬度很高的化合物,又有选择性结晶的特性,使钛向晶界及铸件后凝固处富集,并影响球化质量等,钛高会使铸件脆化、降低切削加工性能和助长缩松等铸造缺陷的产生。
磷和锰是正偏析元素,对球墨铸造的低温韧度影响极大,对脆性转变温度的影响分别是硅的7.5倍和1.92倍。
合理确定铬、钒、钼、锡、锑、铅、铋、碲、砷、硼和铅十一个微量元素的最大值,各微量元素的含量总和以形式良好铸铁件性能。
河北龙凤山铸业有限公司的钛和上述十一个微量元素的含量总和不应大于0.1%,11个微量元素最大值是:
三、高纯生铁的生产工艺
目前国外主要采用高炉还原+另炉氧化吹炼的方法,但在不使用特殊原料(钒钛磁铁矿)的条件下,不适合采用此工艺。
钛是干扰球化元素,实际生产中【ti】和【si】同步还原,呈强相关性,控制高炉铁水含【si】量的途径:控制焦炭、煤的灰分和原料中的sio2含量,降低焦比;改善炉料结构,合理布料促使煤气合理分布,控制滴落带高度,减少铁水吸硅量;增加炉缸渣中氧化性物质,促进铁水脱硅反应。
在充分利用企业设备、优质原燃料和人员技术的基础上,摸索研究,采取“精料+高炉精细作业+炉外专项处理”的技术路线,用
高炉直接冶炼出高纯生铁,主要的生产工艺为:
1.降低焦炭灰分和tio2,降低烧结矿中sio2和tio2,降低焦比。
通过对优质原材料的选用、配比和增加必要的细化分选工序,最大限度降低钛元素含量。
2.选择合理的炉料结构。
以高碱烧结矿占比65—70%,酸性球团矿占比30—35%,碱度为1.9—2.0(倍);增加装入料热流化,改善矿石高温冶金性能,提高炉料本身自熔温度,增加烧结矿中mgo 含量。
3.装料控制。
根据高纯生铁质量要求和出铁量,总料批确定按每小时6.5—7批料控制,连续4小时料批不能超规定批数上限;提前2小时根据炉温、料速与铁量关系预测下2小时负荷情况,稳定炉温;严禁空料线作业,分装入炉;合理布料,实现合理煤气流分布范围尽量缩小。
4.送风控制。
为使生铁含si量稳定,风量控制在1750—
1850m/min;密切关注各风口部位反映的参数作细节把握,压差反应快;考虑白天与黑夜环境温差对炉温的影响,夜里风温比白天高30℃左右。
5.热制度管理。
稳定炉温【si】含量控制0.4±0.1%,铁水物理热>1470℃-1520℃;严禁含si跳号波动,降低风口区温度减少sio 生成;冷却设备发现漏水及时控制更换,不影响炉缸的炉温。
6.造渣管理。
入炉碱度以炉渣r2≥1.15(倍),r3≥1.4(倍);炉渣流动性要好,脱硫能力强,mgo含量≥12%,al2o3≤14%。
7.喷煤管理。
视炉况反应、料速计算,按综合负荷加减喷煤量,喷枪均匀喷煤,堵枪要及时处理。
8.实行高顶压控制。
800m3高炉顶压控制在150kpa,既提高炉内压力,抑制sio生成,又能降煤气流速,提高利用率,降低焦比。
9.出铁量控制。
铁口深度≥1800mm,保证铁口堵泥耐冲刷力强、透气性好,无潮泥,出铁顺畅,按时出铁。
10.炉外处理。
高炉采取低【si】作业法,以获低【ti】铁水,由于不同牌号铁水有时需炉外增硅,由喂料机按计算量进行孕育;在铁水罐中,根据所需的脱【si】量,以氮气为载体进行喷mg粒操作,搅拌铁水,脱气、浮渣和均匀化学成分;以液面渣量多少决定是否捞渣,由捞渣机完成;浇锭时,使用高效孕育剂进行随流孕育,若白口没有完全消除,启动第二孕育装置进行补加,孕育剂加入时,应稳定均匀,孕育剂流要正对铁水流。
高纯生铁锭外观洁净,断口均匀呈细灰粒状,金相分析,石墨组织均呈a型石墨形态,细小,分布均匀。
高纯生铁在我国应用有着广泛的空间,需要针对不同用户的特定需求,严格炉料控制,强化工艺管理,细化工艺参数,总结生产经验,生产出符合要求的优质高纯生铁,实现批量替代进口,切实提高铸造生铁的附加值,推进我国高端铸件的全面发展。
参考文献:
[1]李克瑞、曾艺成、张忠仇:《优质生铁和高纯生铁—球铁稳
定生产的基础》,2007年中国铸造活动周论文集,355-362;
[2]李传栻:《如何面对铸造生铁中干扰元素的影响》;铸造纵横,2009(2);
[3]钱立:《企标之我见》,第八届全国铸铁及熔炼学术会议暨先进球化处理方法研讨会论文集,2010.7,160,162。