井下作业工高级技能讲解
浅析井下作业大修工艺技术
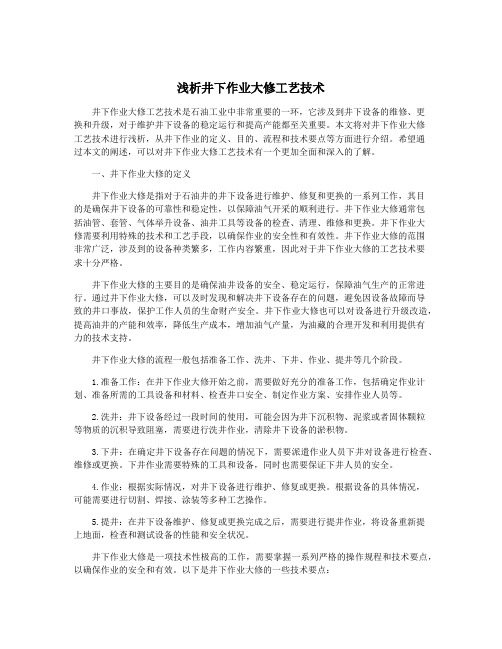
浅析井下作业大修工艺技术井下作业大修工艺技术是石油工业中非常重要的一环,它涉及到井下设备的维修、更换和升级,对于维护井下设备的稳定运行和提高产能都至关重要。
本文将对井下作业大修工艺技术进行浅析,从井下作业的定义、目的、流程和技术要点等方面进行介绍。
希望通过本文的阐述,可以对井下作业大修工艺技术有一个更加全面和深入的了解。
一、井下作业大修的定义井下作业大修是指对于石油井的井下设备进行维护、修复和更换的一系列工作,其目的是确保井下设备的可靠性和稳定性,以保障油气开采的顺利进行。
井下作业大修通常包括油管、套管、气体举升设备、油井工具等设备的检查、清理、维修和更换。
井下作业大修需要利用特殊的技术和工艺手段,以确保作业的安全性和有效性。
井下作业大修的范围非常广泛,涉及到的设备种类繁多,工作内容繁重,因此对于井下作业大修的工艺技术要求十分严格。
井下作业大修的主要目的是确保油井设备的安全、稳定运行,保障油气生产的正常进行。
通过井下作业大修,可以及时发现和解决井下设备存在的问题,避免因设备故障而导致的井口事故,保护工作人员的生命财产安全。
井下作业大修也可以对设备进行升级改造,提高油井的产能和效率,降低生产成本,增加油气产量,为油藏的合理开发和利用提供有力的技术支持。
井下作业大修的流程一般包括准备工作、洗井、下井、作业、提井等几个阶段。
1.准备工作:在井下作业大修开始之前,需要做好充分的准备工作,包括确定作业计划、准备所需的工具设备和材料、检查井口安全、制定作业方案、安排作业人员等。
2.洗井:井下设备经过一段时间的使用,可能会因为井下沉积物、泥浆或者固体颗粒等物质的沉积导致阻塞,需要进行洗井作业,清除井下设备的淤积物。
3.下井:在确定井下设备存在问题的情况下,需要派遣作业人员下井对设备进行检查、维修或更换。
下井作业需要特殊的工具和设备,同时也需要保证下井人员的安全。
4.作业:根据实际情况,对井下设备进行维护、修复或更换。
井下作业工艺技术

井下作业工艺技术嘿,朋友!你知道井下作业工艺技术吗?这可不像你在地面上随便溜达那么简单!想象一下,你身处深深的地下,周围是黑暗和未知。
井下作业就像是在一个神秘的世界里进行一场精密的冒险。
咱先说井下的环境,那可不是闹着玩的。
高温、高压,就像一个火爆脾气的家伙,随时可能给你来个下马威。
还有那些复杂的地质结构,就像一个迷宫,一不小心就会让你迷失方向。
再说这作业工具,每一个都有自己独特的脾气。
比如说钻头,那就是井下的先锋官,得足够锋利和坚韧,才能在坚硬的岩石中杀出一条路来。
这就好比一把利剑,只有够锋利,才能在战场上披荆斩棘,不是吗?而井下的测量技术,那可真是精细活。
就像给地下的世界做一次全方位的体检,任何一点小毛病都不能放过。
这就好像医生给病人做检查,一点点的偏差都可能导致大问题。
还有井下的压裂技术,这可是让油气流出来的关键一招。
就像是给地下的宝藏打开一扇门,让它们欢快地跑出来。
你能想象到那种场面吗?在井下作业中,安全更是重中之重。
每一个环节都不能有丝毫马虎,就像走钢丝一样,必须小心翼翼。
一旦出了差错,那后果可不堪设想。
这可不是吓唬你,想想看,如果在那么深的地方出了问题,救援都得费好大的劲。
另外,井下作业的工作人员,那可都是身怀绝技的勇士。
他们不仅要有专业的知识,还得有过人的胆量和毅力。
他们就像黑暗中的明灯,照亮了地下的世界,为我们带来宝贵的资源。
总之,井下作业工艺技术是一门高深的学问,它充满了挑战和机遇。
它就像一个神秘的宝藏,等待着我们去不断探索和挖掘。
你难道不想更深入地了解它吗?。
井下作业工技师手册

井下作业工技师手册一、井下作业基础概述本章节主要介绍井下作业的基本概念、特点、目的和意义,以及井下作业的分类和流程。
通过了解井下作业的基本知识,为后续学习打下基础。
二、井下设备与工具本章节详细介绍井下作业所需的设备和工具,包括钻井设备、采油设备、修井设备和井下工具等。
同时,对各种设备和工具的用途、使用方法及注意事项进行说明。
三、井下作业技术本章节重点介绍井下作业的核心技术,包括钻井技术、采油技术、修井技术和增产技术等。
通过学习这些技术,掌握井下作业的基本技能和方法。
四、井下作业安全本章节主要强调井下作业的安全管理,包括安全规章制度、安全操作规程、应急预案等方面的内容。
同时,结合案例分析,提高安全意识,确保井下作业安全顺利进行。
五、井下作业环境保护本章节重点介绍井下作业对环境的影响以及相应的环保措施。
通过学习环保知识,掌握井下作业中环境保护的方法和技巧,降低对环境的负面影响。
六、井下作业管理本章节主要介绍井下作业的管理体系和方法,包括质量管理、安全管理、进度管理等方面的内容。
通过学习管理知识,提高井下作业的效率和质量。
七、井下作业事故处理本章节重点讲解井下作业事故的预防和处理方法,包括事故原因分析、事故应急预案、事故处理流程等方面的内容。
通过学习事故处理知识,提高应对突发情况的能力。
八、井下作业法律法规本章节主要介绍与井下作业相关的法律法规和标准,包括安全生产法、环境保护法、石油天然气行业标准等方面的内容。
通过学习法律法规,规范井下作业行为,保障合法权益。
九、井下作业案例分析本章节选取典型的井下作业案例,进行深入剖析和讲解。
通过案例分析,总结经验教训,提高实际操作能力。
同时,为解决实际问题提供参考和借鉴。
井下作业工高级操作技能讲述
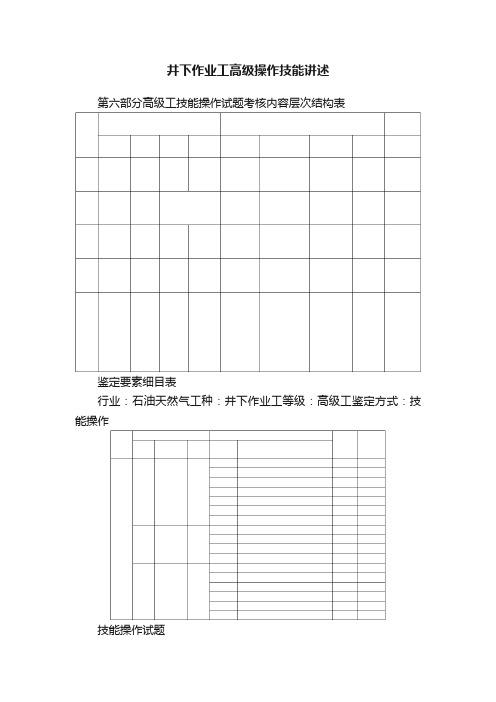
井下作业工高级操作技能讲述第六部分高级工技能操作试题考核内容层次结构表鉴定要素细目表行业:石油天然气工种:井下作业工等级:高级工鉴定方式:技能操作技能操作试题一、AA-001 调配水泥浆1.准备要求(2)工具、用具准备:(3)考场准备:室外作业场地20m×20m;平坦无积水。
2.操作程序的规定及说明(1)调前准备:劳保着装及工具齐全,并符合要求。
(2)按配水泥浆密度为1.85g/cm3的要求,根据水泥现场配比表能求出一袋干水泥清水用量和配浆量。
(3)将一袋干水泥调配水泥浆至密度为1.85g/cm3。
(4)违章操作或发生事故停止作业。
3.考核时间(1)考生提前15min进入考场。
(2)正式操作时间为40min。
每超过限时2min,从总分中扣5分;超过限时10min停止作业。
4.配分、评分标准本题分值100分;配分、评分标准见(评分纪录表)。
评分记录表试题名称:调配水泥浆操作时间:40min考评员:记分员:年月日二、AA-002套管刮削施工操作1.准备要求①室外作业井场60m×60m,平坦无积水。
②模拟井深260m,油补距2.46m,井内无管柱,重点刮削井段200~205m。
③井场内各种设备、工具、用具、材料齐全(已知泵车排量和井眼尺寸)。
2.操作程序的规定及说明(1)根据要求,选择刮削器;下入刮削管柱。
(2)刮削管柱至设计刮削井段以上10m,连接地面循环管线。
(3)边循环边下管柱刮削,至设计刮削井段刮削3次。
(4)停泵接换单根,刮削至设计位置,充分反洗井1.5周。
(5)起出刮削管柱。
3.考核时间(1)考生提前15min进入考场。
(2)在90min内完成。
每超限时2min,从总分中扣5分;超过10min,停止作业。
4.配分、评分标准本题分值100分;配分、评分标准见(评分纪录表)。
评分记录表考评员:记分员:年月日三、AA-003 按要求组配管柱、画管柱示意图1.准备要求(1)工具、用具准备:(3)考场准备:①室外作业场60m×60m,平坦无积水。
油田井下作业大修核心打捞技术

油田井下作业大修核心打捞技术油田井下作业指的是对井下设备进行维修、清洗、更换的一系列工作。
在这些作业中,核心打捞技术是非常重要的一环。
本文将从以下几个方面详细介绍油田井下作业大修核心打捞技术。
一、核心打捞技术的概念核心打捞技术是一种在井下设备作业中用来捞取设备的工艺方法,通常是在井下的油管里操作的。
它是一种快速、有效地提取井下管道、工具、泵浦和管道内淤泥等物质的方法,以达到井下设备维护的目的。
核心打捞技术的实现基础是通过绑扎套管、管道,利用钻管的下放压力和上升吸力,使其自由运动,将井下管道、工具卡住的物质拉出。
一般情况下,钻井管道的外径要小于套管的内径,因此在下放钻管时,可利用套管与管道之间的空隙打开套管,以发挥下放压力。
1.提高设备可利用率:在设备损坏或工作中途停止时,核心打捞技术可以尽快将器具提取出来,加速修理维护周期,缩短停机时间,提高工作效率。
2.保证作业安全:采用核心打捞技术可以减少风险,保持现场安全,减少作业人员受伤和财产损失。
3.降低油井作业成本:通过降低井下设备维护费用、缩短停机时间,基于节约成本的战略方案可以在井坑管理中发挥重要作用,使油井的生产成本更加经济实用。
1.选择合适的打捞器具和工具:打捞器具的选择要根据需要和实际情况,尽量选择质量好、性价比高、使用寿命长且方便维修维护的设备和工具。
2.设备检修前的检查:在进行设备检修之前,要做好检查工作,确保设备、工具及器具使用前无磨损、断裂等现象。
3.操作环境安全:在进行核心打捞作业时,必须保持空气流通良好、避免有毒有害气体、废气、瓦斯等越限现象,避免作业环境产生安全隐患。
4.打捞作业质量监控:对于已经上升到井口的器具和物资,要进行防腐、清洗、包装、目视检查等环节,可以通过惨青指数、洗脉重量、油污尘土的量等指标,对打捞作业质量进行实时监控。
总之,核心打捞技术是油井井下设备维修、清洗、更换的重要手段之一。
通过该技术的应用,不仅可以提高设备的可利用率,还能保证作业的安全性和降低作业成本。
现代井下作业大修技术

现代井下作业大修技术引言:井下作业是指在地下进行的各种工程施工和维护工作。
井下作业的复杂性和危险性要远远超过地上的工作, 因为情况更加恶劣, 环境更加艰苦。
为了确保井下作业的顺利进行和作业人员的安全, 现代井下作业大修技术得到了广泛的关注和研究。
本文将针对现代井下作业大修技术进行详细的介绍, 包括技术的定义、主要内容和应用案例等。
一、技术定义现代井下作业大修技术是指利用现代化的设备和技术手段, 对地下设施进行维护、保养和修复的技术方法。
该技术主要应用于地下管道、隧道、矿井等工程的维修和改造, 通过使用高科技设备和先进的工艺方法, 提高作业效率和质量, 达到节约资源和减少事故的目的。
二、技术内容1.设备技术: 现代井下作业大修技术的核心在于先进的设备技术。
随着科技的不断进步, 井下作业所使用的设备也越来越先进。
比如, 激光扫描设备可以实时获取地下设施的三维模型, 帮助作业人员更好地进行维护和修复工作。
无人机技术可以对井下设施进行实时监测和巡视, 减少人力和时间的浪费。
还有机器人和无人驾驶设备可以进行一些危险作业, 减少人员伤亡的发生。
2.安全管理: 井下作业的安全是最重要的。
现代井下作业大修技术强调安全管理的重要性, 包括监测和评估风险、设立安全防护措施、培训和教育作业人员等。
通过严格遵守安全标准和规定, 减少事故和伤亡的发生。
3.施工工艺:现代井下作业大修技术还包括施工工艺的研究和应用。
根据具体的地下设施和维修工作的需求,选择合适的工艺方法,保证作业质量和效率。
比如,使用无损检测技术对井下管道进行检验,通过无损检测仪器对管道的材料、强度和泄漏情况进行检测,提前发现问题并进行修复。
三、应用案例1.地下管道维修: 地下管道是城市发展的重要基础设施, 随着使用年限的增加, 管道出现老化和破损的情况越来越多。
现代井下作业大修技术可以应用于地下管道的维修工作, 通过高科技设备和工艺手段, 修复破损的管道, 保证供水和供气的正常运行。
004井下作业技术(油井)(起下油管、刮蜡、刮削)课件-004-2

上
2000m 1200m
6 股 900m 以上 700~900m 400~700m 400m 以下
8
二、起油管
3.起出油管挂 (1)上提管柱,将油管挂提出井控装置,在井内第
一根油管接箍下放好吊卡,下放管柱坐在吊卡上。 (2)卸掉油管挂. (3)再次调整井架绷绳,使井架天车、游动滑车、
井口三点成一直线。
(三)套管刮削器的工作原理
套管刮削器装配后,刀片、刀板自由伸出外径比所 刮削套管内径大2-5mm 左右。下井时,刀片向 内收拢压缩胶筒或弹簧筒体,最大外径则小于套 管内径,可以顺利入井。入井后,在胶筒或弹簧 的弹力作用下,刀片、刀板紧贴套管内壁下行, 对套管内壁进行切削。每一次往复动作,都对套 管内壁刮削一次,这样往复数次,即可达到刮削 套管的目的。(四)套管刮削器的用途:套管刮 削器主要用于常规作业、修井作业中清除套管内 壁上的死油、封堵及化堵残留的水泥、堵剂、硬 蜡、盐垢及射孔炮眼毛刺等的刮削、清除。
7
二、起油管
表 3—2 作业机各挡起油管深度规定
游动系统
各挡起下油管深度
井深
(有效绳数) 1 挡
2挡
3挡
4挡
2500m 以上 1200~2500m 1200m 以下
8 股 2500m 以 1650~ 1000~ 1000m 以
上
2500m 1650m
下
6 股 2000m 以 1200~ 700~ 700m 以下
9
二、起油管
4.起管柱 (1)提起管柱,移开吊卡,上提管
柱提出井内第一根油管的接箍,在接 箍下面放人吊卡,下放管柱坐在吊卡 上。
(2)重复以上工作起完井内油管. (3)起出的油管要顺滑道滑到油管桥
现代井下作业大修技术

现代井下作业大修技术井下作业是指在地下进行的各种修理和施工作业,在石油、煤矿、水井等行业中广泛应用。
由于井下作业环境复杂、狭小、危险性较大,因此需要采用特殊的技术来进行大修。
现代井下作业大修技术主要包括以下几个方面:安全技术、施工技术、设备技术和监测技术。
下面将详细介绍这些技术。
1. 安全技术井下作业环境危险性较大,因此安全是首要考虑因素。
安全技术包括安全措施、安全防护和安全教育等。
在井下作业大修过程中,需要制定详细的安全操作规程,并进行安全培训,确保每个参与作业人员都具备必要的安全意识和技能。
此外,还需要采取相应的安全防护设施,如防爆设备、防护装备等,以减少意外事故的发生。
2. 施工技术井下作业大修需要进行各种修理和施工作业,因此需要掌握相应的施工技术。
例如,在石油钻井作业中,需要进行井筒修复、井眼修整、井壁强化等作业,这些都需要专业的施工技术。
在煤矿作业中,需要进行巷道支护、策动粉末等施工作业,同样需要熟练的施工技术。
3. 设备技术井下作业大修需要采用各种设备进行作业,因此需要掌握相应的设备技术。
例如,在石油钻井作业中,常用的设备有钻机、固井设备、插入工具等,需要熟练掌握操作技术。
在煤矿作业中,常用的设备有推土机、装载机、钻机等,同样需要掌握相应的操作技术。
4. 监测技术井下作业大修过程中需要进行监测,以确保作业的顺利进行。
监测技术包括地质勘探、气体监测、温度监测等。
通过地质勘探,可以了解井下地质情况,预测潜在的危险和灾害。
通过气体监测,可以了解井下氧气、有害气体等参数,确保作业人员的安全。
通过温度监测,可以掌握井下温度变化情况,预测潜在的火灾和爆炸。
综上所述,现代井下作业大修技术是一门综合技术,包括安全技术、施工技术、设备技术和监测技术等。
通过不断提高这些技术的水平,可以提高井下作业大修的效率和安全性,确保作业的顺利进行。
同时,还需要加强技术研发和人员培训,不断推动井下作业大修技术的创新和进步。
浅析井下作业大修工艺技术
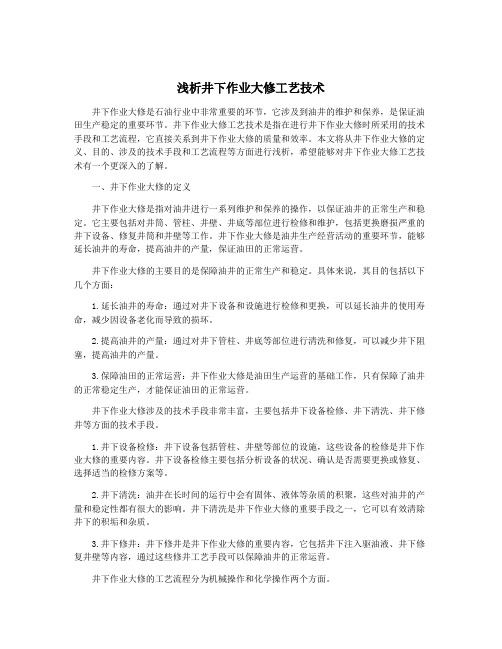
浅析井下作业大修工艺技术井下作业大修是石油行业中非常重要的环节,它涉及到油井的维护和保养,是保证油田生产稳定的重要环节。
井下作业大修工艺技术是指在进行井下作业大修时所采用的技术手段和工艺流程,它直接关系到井下作业大修的质量和效率。
本文将从井下作业大修的定义、目的、涉及的技术手段和工艺流程等方面进行浅析,希望能够对井下作业大修工艺技术有一个更深入的了解。
一、井下作业大修的定义井下作业大修是指对油井进行一系列维护和保养的操作,以保证油井的正常生产和稳定。
它主要包括对井筒、管柱、井壁、井底等部位进行检修和维护,包括更换磨损严重的井下设备、修复井筒和井壁等工作。
井下作业大修是油井生产经营活动的重要环节,能够延长油井的寿命,提高油井的产量,保证油田的正常运营。
井下作业大修的主要目的是保障油井的正常生产和稳定。
具体来说,其目的包括以下几个方面:1.延长油井的寿命:通过对井下设备和设施进行检修和更换,可以延长油井的使用寿命,减少因设备老化而导致的损坏。
2.提高油井的产量:通过对井下管柱、井底等部位进行清洗和修复,可以减少井下阻塞,提高油井的产量。
3.保障油田的正常运营:井下作业大修是油田生产运营的基础工作,只有保障了油井的正常稳定生产,才能保证油田的正常运营。
井下作业大修涉及的技术手段非常丰富,主要包括井下设备检修、井下清洗、井下修井等方面的技术手段。
1.井下设备检修:井下设备包括管柱、井壁等部位的设施,这些设备的检修是井下作业大修的重要内容。
井下设备检修主要包括分析设备的状况、确认是否需要更换或修复、选择适当的检修方案等。
2.井下清洗:油井在长时间的运行中会有固体、液体等杂质的积聚,这些对油井的产量和稳定性都有很大的影响。
井下清洗是井下作业大修的重要手段之一,它可以有效清除井下的积垢和杂质。
3.井下修井:井下修井是井下作业大修的重要内容,它包括井下注入驱油液、井下修复井壁等内容,通过这些修井工艺手段可以保障油井的正常运营。
常见井下作业工艺技术讲座共125页文档

46、我们若已接受最坏的,就再没有什么损失。——卡耐基 47、书到用时方恨少、事非经过不知难。——陆游 48、书籍把我们引入最美好的社会,使我们认识各个时代的伟大智者。——史美尔斯 49、熟读唐诗三百首,不会作诗也会吟。——孙洙 50、谁和我一样用功,谁就会和我一样成功。26、机遇对于有准备的头脑有特别的 亲和力 。 27、自信是人格的核心。
28、目标的坚定是性格中最必要的力 量泉源 之一, 也是成 功的利 器之一 。没有 它,天 才也会 在矛盾 无定的 迷径中 ,徒劳 无功。- -查士 德斐尔 爵士。 29、困难就是机遇。--温斯顿.丘吉 尔。 30、我奋斗,所以我快乐。--格林斯 潘。
油田井下作业打捞工艺技术及应用探寻

油田井下作业打捞工艺技术及应用探寻油田井下作业是石油勘探开发中不可或缺的一项工作,它涉及到许多方面的技术与流程,其中打捞工艺技术更是重要的一环。
打捞工艺技术是指在油井作业中需要从井下提取管柱、工具或其他设备的一种技术,其目的是将损坏或遗留在井下的物品提取到地面。
下文将从打捞技术的种类、工作原理及其应用探寻等方面逐一介绍。
一、打捞技术的种类打捞技术的种类较多,按照不同应用领域可以分为水平井、垂直井、非常规井等不同类型。
1. 水平井打捞技术:水平井是油井中常用的一种,其特点是从垂直方向进入沉积岩石层,从而获得更多的产量。
水平井打捞技术主要包括原地打捞、液体打捞、吸附打捞等多种类型,主要应用于管柱等物品的提取。
2. 垂直井打捞技术:垂直井是传统的油井工程中最为常见的井筒类型,其特点是以垂直方向直接进入地层,线路短、操作简单,并且不受地形地貌、地下构造的限制。
垂直井打捞技术包括电视法、飞阴极法、立体声激光法等类型,主要应用于提取管柱、工具等设备。
3. 非常规井打捞技术:非常规井是指采用新型油气勘探开发技术时所用的井筒类型,如页岩气井、致密气井等。
非常规井打捞技术主要包括电子轨迹法、磁力定位法、声波法等多种类型,主要用于提取岩心、管柱等物品。
二、打捞技术的工作原理打捞技术的工作原理主要基于物理原理和机械原理。
1. 物理原理:打捞技术常常需要利用物理原理,如液体打捞技术中需要利用水压原理来提取管柱;电子轨迹法中需要利用电子运动的轨迹来确定物品的位置。
2. 机械原理:打捞技术中需要利用机械原理,如非常规井打捞技术中需要使用电磁铁或磁吸盘等设备来提取物品;垂直井打捞技术中需要采用抓钩、滑卡等设备来提取物品。
三、打捞技术的应用探寻打捞技术在油井作业中应用广泛,可根据需要选择不同的技术方式。
1. 维修作业:打捞技术可用于维修地面设备和井下工具。
如在维修钻具时,常常需要打捞防滑器、钻杆组等工具,以便进行整理、修理和检查,从而保证设备的正常使用。
井下作业工高级工(三级)理论知识
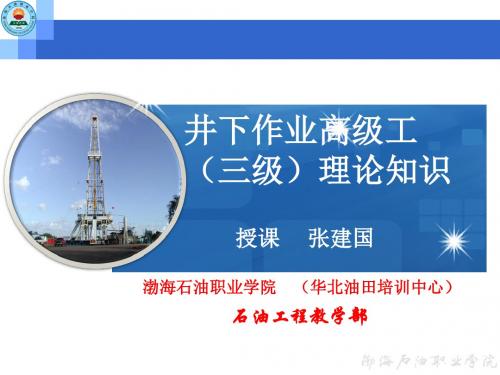
16 (A) 在原位置不动 (B) 等修好设备再施工 (C) 应迅速反洗出井内的全部水泥浆 (D) 等更换设备再施工 [答案] C 17.使用普通(密度为3.15 g/㎝3)油井水泥注水泥塞施工,配浆密度
(A) 1.75g/cm3 (B) 1.60g/cm3 (C) 1.4 g/cm3 (D) 1.90 g/cm3 [答案] A 18 (A) 为8h (B) 为10h (C) 为16h (D) 根据水泥型号及添加剂确定 [答案] D 19 (A) 3min (B) 2min (C) 1min (D) 30min [答案] D 20 (A) 3MPa (B) 0.5MPa (C) 1MPa (D) 1.5MPa [答案] B
11 (A) 5m (B) 10m (C) 15m (D) 25m [答案] B 12 (A) 5m (B) 10m (C) 15m (D) 20m [答案] A 13 作隔离液。 (A) 钻井液 (B) 卤水 (C) 盐水 (D) 清水 [答案] D 14 (A) 连好即可 (B)畅通即可 (C)试压合格 (D)可以不试 压 [答案] C 15 (A) 光油管 (B) 通井规 (C) 刮管器 (D) 封隔器 [答案] A
Байду номын сангаас
6 (A)2MPa (B) 10 MPa (C)5MPa (D) 25 MPa [答案] D 7 定。 (A) 温度计 (B) 粘度计 (C) 密度计 (D) 流量计 [答案] C 8 间。 (A) 顶替 (B) 反洗 (C) 探灰面 (D) 上提管柱候凝 [答案] D 9 (A) 大于 (B) 小于 (C) 等于 (D) 等于或小于 [答案] A 10 (A)过滤杂物 (B)缓凝 (C)增加灰塞强度 (D)防尘 [答案] A
浅析井下作业大修工艺技术

浅析井下作业大修工艺技术井下作业大修是指对石油、天然气井进行较大规模的维修和改造。
井下作业大修工艺技术是指在井下作业大修中所采用的一系列技术与工艺。
井下作业大修工艺技术是围绕着井身完整性和油气产能恢复的目标展开的。
井下作业大修的过程包括调查、检测、评估、设计、施工和后期跟踪等阶段。
针对井下作业大修的不同需求,工艺技术主要包括以下几个方面:井下作业大修的前期调查和检测技术。
在进行大修作业之前,需要对井口、井身、油气藏等进行全面的检测和调查。
这部分工艺技术包括井身完整性检测、油气藏产能评估、井底流体采样和分析等。
通过这些技术的应用,可以确定井下作业的具体需求,并制定相应的维修方案和施工计划。
井下作业大修的设计技术。
在完成调查和检测之后,需要针对井下作业的具体需求进行设计。
设计阶段主要包括施工工艺设计、施工参数设计、修井液配方设计和材料选型等。
施工工艺设计是井下作业大修的核心,需要根据实际情况选择合适的施工方法和工艺流程,确保作业的顺利进行。
井下作业大修的施工技术。
施工阶段是井下作业大修的实施过程,需要根据设计方案进行具体的施工作业。
在施工过程中,涉及到的工艺技术包括钻井技术、井下工具使用技术、修井液操纵和控制技术等。
这些技术的应用直接影响到井下作业的效果和质量,需要施工人员具备专业的技术知识和操作技能。
井下作业大修的后期跟踪和评估技术。
井下作业大修完成后,需要进行后期的跟踪和评估,以确保井下作业的效果和效益。
后期跟踪和评估技术涉及到对修井结果的监测和评价,以及对效益指标的统计和分析。
通过这些技术的应用,可以对井下作业大修的效果进行科学的评估和总结,并为今后的作业提供参考依据。
井下作业大修工艺技术是一项繁杂而综合性的工作,涉及到多种技术与工艺的应用。
只有在充分掌握了井下作业大修工艺技术的基础上,才能够针对具体情况制定合理的维修方案,高效地进行井下作业大修。
油田井下作业大修核心打捞技术

油田井下作业大修核心打捞技术随着石油开采技术的不断发展,井下作业大修无疑是油田开发中不可缺少的一环。
在大修过程中,常常需要使用一些特殊的工具和装备进行作业,如钻井平台、动力装置、井下大修设备及物料等。
其中,打捞技术对于油井大修起着举足轻重的作用,以下将着重介绍油田井下作业大修中的核心打捞技术。
I. 技术原理打捞技术是指利用特殊的工具设备将井下损坏的设备或部件提升到地面进行维修或更换。
井下作业大修的核心打捞技术主要采用:钻塞打捞法、摇摆捞取法、扭转振荡法、捣击推杆法等。
II. 钻塞打捞技术钻塞打捞是指利用井下冲击工具将被固定的设备或部件打入底部,并同时将井内物料顺势带出井口。
该技术需要在井口设置一个底部套筒和钻塞。
首先将钻塞接头安装于钻机下部,然后钻机下部将伸入套筒中,通过力量和冲击的作用将钻塞打入底部固定设备或部件上,当钻塞穿过底部过渡段后将打开液压回路,内部液体不断的对钻塞施加推力。
通过不断的推送,将被钻塞固定的设备或部件带出井口。
摇摆捞取是指利用井下冲击工具或夹头将需要打捞的设备或部件摆动,使其从井底解脱,接着将其牢固地卡住,再通过绳索或其它装备将其缓慢地拉回井口。
摇摆捞取技术需要选择适当的工具和装备。
首先将钻机下部伸入井口中,利用摇摆动力将被卡住的设备或部件从井底摇出。
当设备或部件上升到井口时,需要使用重型绳索或其它装备,将其缓慢地拖向井口,最终将其提升到地面进行维修或更换。
IV. 扭转振荡技术扭转振荡技术是指利用双向液压驱动机构使捞取钳完成扭转和振荡动作,以达到控制设备或部件卡夹的目的。
该技术需要使用带有双向液压驱动机构的捞取钳,通过液压驱动捞取钳进行扭转和振荡动作,使设备或部件摆脱井底固定,最终将其提升至地面进行更换或维修。
V. 捣击推杆技术捣击推杆技术是指利用长度可调的冲击推杆将设备或部件重重地敲打,以达到将其从井底解脱的目的。
该技术需要通过钻机下部将长度可调的冲击推杆伸入井内,并通过液压驱动马达动力推杆进行振荡冲击,最终使设备或部件解脱被固定的状态,从井口提升至地面进行更换或维修。
油田井下作业大修核心打捞技术

油田井下作业大修核心打捞技术
油田井下作业大修核心打捞技术主要是指在油井或天然气井的井下进行大修时,使用
打捞工具将井口设备和管道等重要部件从井下提取到地面的技术。
这项技术对于井下设备
的检修、更换和维护具有重要意义,可以减少停产时间、提高生产效率。
油田井下作业大修核心打捞技术可以分为两个主要步骤:上打捞和下打捞。
上打捞主要是指将井口设备和管道等重要部件从井下的井筒上端提取到地面的过程。
在进行上打捞时,首先需要在地面安装一个起重设备,通常是起重机或起重叉车。
然后,
用钢丝绳或链条将提取工具(如打捞备件)连接到起重设备上。
接下来,将起重装置降低
到井口设备处,将打捞备件与井口设备连接。
通过起重设备将井口设备提取至地面,并进
行检修、更换或维护。
下打捞主要是指将井口设备和管道等重要部件从井下的井筒下段提取到地面的过程。
下打捞技术通常使用更为复杂的工具和设备,如液压打捞器、余量打捞器等。
在进行下打
捞时,首先需要将打捞器安装在井筒中,通常是通过井筒下段的套管或井下管道进行安装。
接下来,将打捞器与井口设备连接。
然后,使用液压、电动或人力等方式对打捞器施加力,使其将井口设备和管道等从井下提取到地面。
在进行下打捞时,还需要注意井筒的稳定,
以防止产生安全事故。
井下作业工:高级井下作业工知识学习二
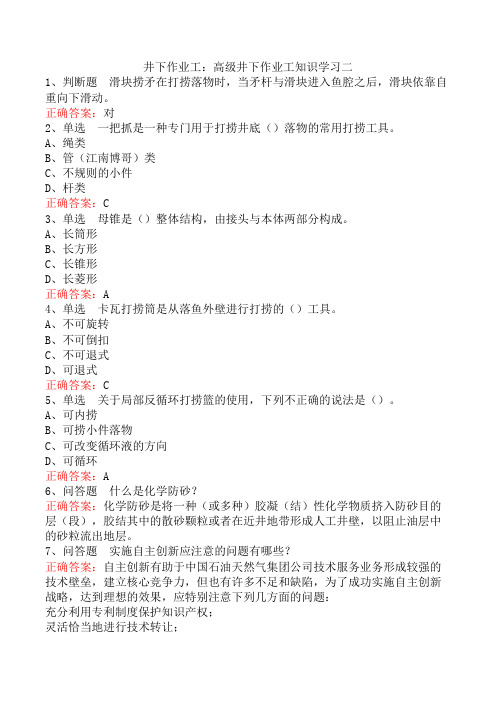
井下作业工:高级井下作业工知识学习二1、判断题滑块捞矛在打捞落物时,当矛杆与滑块进入鱼腔之后,滑块依靠自重向下滑动。
正确答案:对2、单选一把抓是一种专门用于打捞井底()落物的常用打捞工具。
A、绳类B、管(江南博哥)类C、不规则的小件D、杆类正确答案:C3、单选母锥是()整体结构,由接头与本体两部分构成。
A、长筒形B、长方形C、长锥形D、长菱形正确答案:A4、单选卡瓦打捞筒是从落鱼外壁进行打捞的()工具。
A、不可旋转B、不可倒扣C、不可退式D、可退式正确答案:C5、单选关于局部反循环打捞篮的使用,下列不正确的说法是()。
A、可内捞B、可捞小件落物C、可改变循环液的方向D、可循环正确答案:A6、问答题什么是化学防砂?正确答案:化学防砂是将一种(或多种)胶凝(结)性化学物质挤入防砂目的层(段),胶结其中的散砂颗粒或者在近井地带形成人工井壁,以阻止油层中的砂粒流出地层。
7、问答题实施自主创新应注意的问题有哪些?正确答案:自主创新有助于中国石油天然气集团公司技术服务业务形成较强的技术壁垒,建立核心竞争力,但也有许多不足和缺陷,为了成功实施自主创新战略,达到理想的效果,应特别注意下列几方面的问题:充分利用专利制度保护知识产权;灵活恰当地进行技术转让;注意自主创新产品的自我完善;重视对创新后续环节的投入。
8、单选开窗打捞筒在同一排窗口上有变形后的舌尖内径()落物最小外径。
A、必须大于B、等于C、略大于D、略小于正确答案:D9、单选倒扣捞矛需要退出落鱼,下击并右旋钻具,矛杆上的()限定了卡瓦与矛杆的相对位置,上提钻具卡瓦与矛杆锥面不再贴合,即可退出落鱼。
A、卡瓦B、定位螺钉C、花键套D、限位键正确答案:D10、单选在爆炸松扣工具系列中,()是系列工具中关键部件,由雷管和导爆索组成。
A、导向头B、加重杆C、爆炸杆D、电缆头正确答案:C11、判断题螺旋式抽油杆打捞筒是由上接头、筒体、螺旋卡瓦、引鞋所组成。
正确答案:对12、单选活动管柱解卡是在()上提下放活动管柱。
井下作业工:高级井下作业工考点巩固四

井下作业工:高级井下作业工考点巩固四1、问答题化学防砂分哪几种类型?各自有什么特点?正确答案:①一是树脂胶结地层砂;二是树脂人工井壁防砂;三是化学固砂。
②树脂胶结地层砂是将树脂注入地层(也可以在地下合成树脂),使其与(江南博哥)地层砂胶结,达到防砂的目的;③树脂人工井壁防砂是将人工井壁材料泵入地层,并挤入套管外地层孔隙中,形成密实充填,待这些材料凝固,形成一道挡砂屏障,阻止地层出砂;④化学固砂防砂由于限制条件太多,很少使用。
2、单选机械式内割刀的锚定机构中有()卡瓦牙及滑牙套、弹簧等,起锚定工具作用。
A、四个B、三个C、二个D、一个正确答案:B3、判断题下机械式内割刀时应防止正转管柱。
正确答案:对4、判断题爆炸松扣工具爆炸后即可旋转管柱。
正确答案:对5、单选XJ-K95型开式下击器的许用拉力()。
A、1150kNB、1400kNC、1250kND、1300kN正确答案:C6、单选聚能切割弹适应井温为()。
A、200℃B、300℃C、350℃D、400℃正确答案:B7、判断题目前现有的油井水泥可以满足各种条件下的注水泥塞施工要求。
正确答案:错8、单选砂岩油田油井堵水选井时要优先选择油层纵向渗透率级差大于()的油井。
A、1B、1.5C、2D、5正确答案:C9、单选在进行声幅测井找窜施工时,要下外径小于套管内径()的通井规,通井至被找窜层以下50m或设计深度。
A、4~6mmB、6~8mmC、10~12mmD、12~14mm正确答案:B10、判断题卡瓦打捞筒不能对遇卡管柱施加扭矩进行倒扣。
正确答案:错11、单选测卡仪能够准确的在直径为()的各种管内测卡。
A、20~60mmB、60~298mmC、300~400mmD、400~500mm正确答案:B12、判断题打捞外径为φ74mm管类落物可选用DLT-T89倒扣捞筒。
正确答案:错13、问答题使用通胀扩径法修复套管常用的下井工具有哪些?正确答案:主要工具有:①梨形胀管器、②偏心辊子整形器、③三锥辊子整形器、④旋转型震击式整形器及其他类型的整形器。
- 1、下载文档前请自行甄别文档内容的完整性,平台不提供额外的编辑、内容补充、找答案等附加服务。
- 2、"仅部分预览"的文档,不可在线预览部分如存在完整性等问题,可反馈申请退款(可完整预览的文档不适用该条件!)。
- 3、如文档侵犯您的权益,请联系客服反馈,我们会尽快为您处理(人工客服工作时间:9:00-18:30)。
职工技能鉴定培训教程井下作业工(高级工)第一单元注水泥塞施工一、学习目标掌握注水泥塞工艺原理,现场能够正确进行注水泥塞操作。
二、准备工作1.施工工具、用具和设备的准备400型水泥车2台、8 m3计量罐2个、1 m3计量罐1个、1m钢板尺1个、计算器1个、密度计1个、氯根化验设备1套。
2. 编写施工设计1)资料收集(1)作业井的套管规格、层位、射孔井段、地层渗透率、温度、压力系数、产液量、液性、漏失情况。
(2)水泥性能。
2)设计原则(1)水泥塞厚度一般应在10m以上。
(2)被封堵层顶界到水泥塞面的距离必须大于5m。
(3)注水泥塞后井筒口袋深度应符合地质要求。
(4)用非清水压井注水泥塞时,修井液前后均必须替入适量清水作隔离液,井深超过3500m的井必须采用优质性能修井液。
3) 注水泥塞设计编写要求编写内容、格式应符合设计的要求,详见相关内容中的设计模式。
3. 施工用液准备根据施工设计要求备足符合要求的修井液和清水。
(1)在8m3储液罐内备足顶替用的修井液。
(2)在1m3罐中装入配灰浆用的清水。
4. 油井水泥准备(1)施工前要在实验室,对所用的油井水泥及添加剂的性能进行抽样化验。
(2)把油井水泥和添加剂按设计要求用量备足拉送到井场,并在现场检查水泥质量。
(3)将水泥摆放在配水泥浆的操作台上。
5. 清水的准备(1)将清水拉到井场,并做氯根化验。
(2)将合格的清水放入1 m3配水泥浆罐内。
6. 井筒及管柱准备(1)通井、刮削彻底清除井壁上污物。
(2)若在自喷井注水泥塞施工,施工前必须用合适的压井液进行压井,达到井筒液柱压力与地层压力相平衡。
(3)若井漏失严重,必须采取填砂或堵漏等工艺封堵漏失层段。
(4)准确计算、丈量、配好注水泥塞管柱,并做好记录。
7. 地面设施、设备准备(1)将水泥车与施工管线三通上装单流阀的一端用快速管线连接。
(2)接好刺水泥浆的刺枪。
(3)在水泥车后面装液斗内装清水1~1.5 m3。
(4)将水泥车上水线插入1 m3配水泥浆罐内。
(5)检查好提升动力设备、井架、游动系统、工具、用具。
(6)在现场必须有备用的水泥车。
三、操作步骤1.将注水泥塞管柱下入井内至设计要求深度,管柱尾部为光油管(见图4-1所示)。
2.连接进、出口管线,并试压。
3.循环井内液体,检查地面系统是否工作正常。
4.按设计要求在1 m3罐内配好施工所需的水泥浆。
水泥浆应混合均匀,不得混入杂物,密度不得低于1.85g/cm3。
5.正替设计规定量的水泥浆。
6.正顶替水泥浆(1)按设计要求,用与修井液相同密度的液体将水泥浆顶替到预定位置,停泵。
(2)卸管线、拆井口。
(3)上提油管将深度完成在预计水泥面以上1~2 m的位置。
(4)装好井口,上紧顶丝。
7.反洗水泥浆(1)接好反洗井管线。
(2)用修井液反洗井,洗出多余水泥浆。
8.上提油管将深度完成在预计水泥面以上100m的位置。
9.装好井口采油树,井筒内灌满修井液,关井候凝,时间按设计要求。
四、技术要求1.自喷井注水泥塞前,必须用压井液将井压平衡后,方可进行注水泥塞施工。
2.注水泥塞管线必须按标准试压,试验压力为25MPa,5min不刺不漏。
3.注水泥塞管柱必须丈量、计算准确,累计长度误差小于0.02%。
4.必须保证油管挂密封盘根完好或采用悬挂式井口装置。
5.井筒液柱压力与地层压力保持平衡,既不喷,也不漏。
6.如果地层漏失严重,可根据具体情况,先填砂或使用堵漏剂进行堵漏。
7.井筒内的液体要保持中性,矿化度不能太高,否则将使水泥浆在井筒内速凝或不凝固。
8.注水泥塞的管柱内壁要清洁,管柱和井口要密封,保证在液体循环过程中不会“短路”,保证水泥浆顶替深度的准确及反洗出多余的水泥浆。
9.计算顶替量必须准确。
10.要有专人指挥,专人计量。
11.反洗井时, 泵的排量要适当低一些,以免造成水泥塞位置下移。
12.替、顶、反洗水泥浆过程中,中途不得随意停泵。
13.在顶替水泥浆中途,若水泥车出现故障,应立即起出井内油管。
14.若顶替液将水泥浆顶替到预定位置,在上提油管时提升系统出现故障,应立即反洗出全部水泥浆。
15.从配水泥浆到反洗井开始所经历的作业时间要控制在水泥浆稠化时间的50%之内,反洗井中途不得停泵。
2. 注水泥塞的操作规程与质量标准1)注水泥塞的操作规程(1)压井起出井内管柱。
(2)下管柱预处理:A、漏失严重的地层应先堵漏或填砂。
B、大排量正洗井降温或脱气。
C、井深超过2000m , 被封夹层小于5 m的井段需要对管柱进行磁性定位校正深度。
(3)注水泥塞施工:A、按设计要求将管柱完成在注灰深度,座好井口。
B、连接施工管线,试压25MPa,5min不刺不漏为合格。
C、按设计要求的密度调配水泥浆。
D、按设计要求正注入前隔离液,再替水泥浆,然后替入后隔离液,接着泵入全部顶替液。
E、上提管柱,将油管完成在设计灰面以上1.0~2.0m,座好井口,用压井液反洗出多余灰浆。
F、上提油管100m,装好采油树,向井筒内灌满同性能的压井液。
G、关井24~48小时。
H、加深管柱探灰面,反复试探3次,每次加压5~10kN,确定灰面后,上提管柱20m,装好井口,装上压力表。
I、用水泥车反洗井后试压,试验压力见表4-4的规定。
表4-4 套管内注水泥塞试压标准2)质量标准(1)顶替水泥浆之前,要保证油管和套管液面在井口。
(2)配水泥浆的水和隔离液的水必须与试验用水一致。
(3)顶替液量必须计量准确,保证油套管水泥浆面平衡。
(4)候凝时井内必须稳定,油套管液面必须在井口。
(5)对于高压不稳定井或层间干扰大的井应采取加压候凝,一般加压3~5 MPa。
(6)候凝时间按表4-5要求进行,保证水泥塞凝固质量。
表4-5 油井水泥候凝时间(7)水泥塞面必须达到设计要求。
(8)作业后套管无损坏。
(9)修井液对油层无污染。
(10)作业前明确分工,组织落实,统一指挥。
(11)作业提升设备工作正常。
第二单元封隔器找窜一、学习目标掌握封隔器找窜工艺原理,现场能够进行封隔器找窜操作。
二、准备工作1.找窜层间夹层厚度应符合表4-6的要求。
表4-6 找窜层间夹层厚度标准2.井内无落物,套管完好。
1)找窜井基础资料数据齐全,固井质量及找串井段上下套管接箍深度明确。
2)找窜井段不具备进出孔时,在怀疑井段的夹层部位补射观察孔。
0.5 m射4~5孔,孔眼要均匀分布。
3)按照管柱连接顺序配管柱:(1)单封隔器:自下而上为球座、节流器、封隔器、上部油管。
(2)双封隔器:自下而上为底部球座、封隔器、下部油管、节流器、封隔器、上部油管。
4)配备水泥车和符合施工要求的修井液。
5)编写施工设计。
三、操作步骤1. 压井1)按设计要求选择合适密度的压井液压井。
2)压井过程中注意观察井口泵压、进出口排量和压井液相对密度变化,做到压井既不致发生溢流、井喷,又不致造成井漏、压死油层。
2.起管柱1)拆井口,安装好与井口压力等级相配套的井口防喷器。
2)试提油管悬挂器,待大钩载荷正常后方可进行正常起管柱作业。
3.探砂面、冲砂下冲砂管柱(底部带冲砂笔尖)探砂面,若有砂则冲砂至人工井底。
4.通井1)通井规外径应小于套管内径6~8mm,长度大于1200 mm。
2)通井规通井至被找窜层以下50 m,不足50 m通至人工井底。
随时观察指重表读数。
若通井过程中发生遇阻,加压不超过30kN,严禁猛顿硬压。
5.刮削1)下套管刮削器刮削至被找窜层以下50 m,不足50 m刮削至人工井底。
2)刮削技术要求见套管刮削操作。
6.找窜1)下单封隔器找窜管柱至设计要求的验封位置,装井口。
2)单封隔器找窜管柱结构(自上而下):油管+K344型封隔器+节流器+球座。
3)接水泥车进出口管线,地面试压25MPa,5min不刺不漏为合格。
4)正循环洗井,待出口返出清水后投球。
5)验封,正憋压10MPa,时间10~30min,无返出量(溢流量)或套压无变化为合格。
6)调整管柱至找窜位置。
7)分别在8MPa、10MPa、8MPa三个压力点各正注10~30 min,观察记录套管压力或溢流量变化。
若套压变化大于0.5MPa或溢流量差值大于10L/min,则初步认为窜槽。
8)卸压,将封隔器上提至射孔井段以上坐封,验证封隔器的密封性,从而落实找窜数据的可靠性。
9)清水反洗井二周,将球洗出,起出找窜管柱,结束找窜施工。
四、技术要求i.新井找窜时应先进行套管刮削。
ii.修井液无杂质,管线、计量池清洁。
iii.地层出砂严重,测完一个点上提封隔器时,应活动泄压,缓慢上提,速度<10m/min,防止地层出砂造成卡钻事故。
iv.管柱丈量准确,封隔器坐在需测井段夹层部位并避开套管接箍。
v.找窜时在油层部位采用活性水或原油,防止污染油层。
不得将修井液或污物注入地层、窜槽部位。
vi.资料录取:(1)通井(刮削)、冲砂数据;(2)观察孔井段、射孔枪型、孔数;(3)找窜日期、找窜层位、井段;(4)管柱结构及示意图;(5)找窜用修井液的名称、性能、注(挤)泵压、观察时间、注入量、返出量(窜通量)、油、套压变化值;(6)油管及封隔器试漏情况;(7)结论。
第三单元封隔器堵水一、学习目标掌握封隔器堵水工艺原理,现场能进行封隔器堵水操作。
二、准备工作1.井况调查内容包括:井身结构、油层、射孔、历次施工、历年生产、测试资料、目前井下管柱等。
2.编写施工设计书选择最佳堵水方案,编写施工设计书。
3.现场调查内容包括:井位、井场条件、电源情况、道路交通情况、地面流程、井场设备情况等。
4.工具准备根据施工设计要求,配全堵水作业使用的井下工具。
井下工具主要包括:封隔器和井下配套工具。
5.设备准备根据施工内容、工艺参数及施工设计要求,备好如下主要设备:水泥车、水罐车等。
三、操作步骤1. 压井按设计要求选择合适的压井液进行压井,注意不污染地层。
2.起管起出井内管柱,起管前必须装好适当压力等级的井口防喷器。
3.通井、刮削用通井规通井至人工井底或设计深度50m以下。
4.下堵水管柱按设计要求下入堵水管柱至设计深度,坐封封隔器。
下井工具及油管必须清洁、丈量准确,油管要用内径规通过。
5.投产根据设计要求,打开井下相应开关,装油、套管压力表,分别对上、下层投产。
四、技术要求1.作业前应测静压和流压或由最近6个月内所测的压力数值资料。
2.装好检验合格的指重表或拉力计。
3.下井管柱、工具必须清洁干净,丈量准确,丈量累积误差不得大于0.02%。
4.仔细检查下井油管,下井前必须用通径规通过。
φ73mm油管使用的通径规直径59.5mm,长度800mm。
5.管柱下井前必须先通井至人工井底或设计深度50m以下。
6.压井时须注意保护油层,循环压井时要控制回压。
7.封隔器和配套工具必须有出厂合格证,地面检验合格方可下井。
8.下井油管螺纹必须涂密封脂,油管螺纹上紧。