铸造毛坯件检验规范
压铸件毛坯质量检验标准
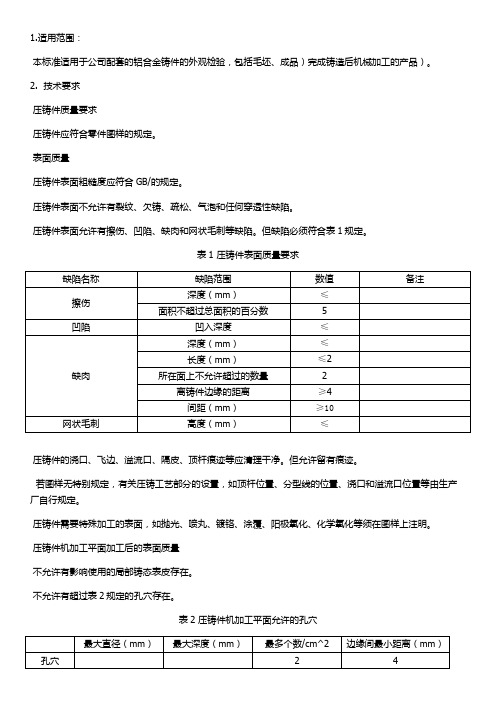
1.适用范围:本标准适用于公司配套的铝合金铸件的外观检验,包括毛坯、成品)完成铸造后机械加工的产品)。
2. 技术要求压铸件质量要求压铸件应符合零件图样的规定。
表面质量压铸件表面粗糙度应符合GB/的规定。
压铸件表面不允许有裂纹、欠铸、疏松、气泡和任何穿透性缺陷。
压铸件表面允许有擦伤、凹陷、缺肉和网状毛刺等缺陷。
但缺陷必须符合表1规定。
表1 压铸件表面质量要求压铸件的浇口、飞边、溢流口、隔皮、顶杆痕迹等应清理干净。
但允许留有痕迹。
若图样无特别规定,有关压铸工艺部分的设置,如顶杆位置、分型线的位置、浇口和溢流口位置等由生产厂自行规定。
压铸件需要特殊加工的表面,如抛光、喷丸、镀铬、涂覆、阳极氧化、化学氧化等须在图样上注明。
压铸件机加工平面加工后的表面质量不允许有影响使用的局部铸态表皮存在。
不允许有超过表2规定的孔穴存在。
表2 压铸件机加工平面允许的孔穴压铸件机械加工螺纹的表面质量压铸件机械加工螺纹的头两扣不允许有任何缺陷,其余部分螺纹不允许有表3所规定的孔穴缺陷。
表3 机械加工螺纹规定的孔穴缺陷范围压铸件不底孔加工后的螺纹表面质量见表4的规定表4 不铸底孔加工后的螺纹表面质量压铸件机械加工孔加工后表面的孔穴规定范围见表5。
表5 机械加工孔表面的孔穴规定范围压铸件内部质量压铸件若能满足其使用性能要求,则压铸件本质缺陷不作为报废的依据。
压铸件内部不允许有冷隔缺陷。
压铸件内部允许有气孔、疏孔、夹杂等缺陷,但孔穴缺陷最大直径不超过壁厚的1/8,孔穴数量在任何剖面上不超过2个/cm2 。
重要压铸件的受力部位须进行解剖检查,符合表6中的规定。
表6 压铸件指定解剖部位内部质量规定其它性能要求应符合GB/T15114的规定。
3 试验方法及检验规则化学成分铝合金化学成分的检验方法,检验规则和复检应符合GB/T15115的规定。
化学成分的试样也可取自压铸件,但必须符合GB/T15115的规定。
力学性能力学性能的检验方法,检验频率和检验规则应符合GB/T15115的规定。
QS GY-004-2014 模具外协毛坯铸件质量检验标准

模具外协毛坯铸件质量检验标准1 外观铸件表面应清理干净,修整飞边毛刺,去除补贴、粘砂、氧化铁皮及内腔残余物等。
应无影响使用的气孔、砂眼、夹渣、缩孔、缩松、裂纹、偏心、变形等缺陷。
毛坯如果出现缺陷,供应商应将缺陷的实际情况书面告知豪迈科技公司,由豪迈科技公司判定是否可以让步使用,工件毛坯面未经豪迈公司许可严禁焊补,详见“毛坯异常情况处理程序”。
2 外形尺寸有毛坯图的依据毛坯图进行检验。
有零件图的依据JB/T 5000.6-2007,检验余量大小。
3 硬度(HBS)将工作面磨去氧化皮得一光滑平坦表面后(粗糙度一般不低于Ra1.6um),检测硬度值,试验力作用方向应与试验面垂直。
4 理化分析4.1中国GB标准:一般工程用铸造碳钢件[GB/T 11352—2009]4.2中国GB标准:焊接结构用碳素钢铸件[GB/T 7659--2010]4.3中国GB标准:一般工程与结构用低合金铸钢件[GB/T14408—1993]4.4中国JB标准:大型低合金钢铸件[JB/T 6402-2006]4.5中国GB标准:球墨铸铁件[GB/T 1348-2009]4.6中国JB标准:重型机械通用技术条件(第6部分:铸钢件)[JB/T 5000.6-2007]5产品内部缺陷检验5.1铸件内部应无影响使用的气孔、砂眼、夹渣、缩孔、缩松等缺陷。
5.2中国JB标准:重型机械通用技术条件(第14部分:铸钢件无损探伤)[JB/T 5000.14-2007]6 拉伸试验与冲击试验6.1供应商发货时,提供与工件规格数量相对应的质量证明。
6.2在一般(无特殊要求说明)情况下,每炉次号提供1件随件Y形试块,以备检测时使用,注意将试样标识清楚。
另在毛坯采购时,特殊标明需要试棒的,按采购单提供试棒。
6.3在设计科特殊要求或重要零件难于控制质量的情况下,随工件提供“附铸试块”。
在“材料采购报表”中注明“附铸试块”字样。
7 标志与质量证明书7.1供应商锻坯供货标识应按豪迈公司指定方式进行。
毛坯检验规范

毛坯检验规范1、目的对产品毛坯进料检验作文件化规定,使检验过程规范化和标准化,避免和减少因毛坯的不合格造成后续作业的困难和产品的不合格。
2、范围适用于本公司所有铸造毛坯、锻造毛坯和压铸毛坯的进料检验过程。
3、依据1).国家相关标准如:《逐批检查计数抽样程序及检查表》GB2828-2008《铸造铜合金技术条件》GB1176-87《阀门铸铜件外观质量要求》GB12231《锌合金、铝合金、铜合金压铸件技术条件》等;JB2702-802).产品图样、技术要求及工艺要求;3).客户要求和合同要求等。
4、内容4.1毛坯尺寸规定4.1.1毛坯两端面的加工余量:1/4"--1/2"各为0.8-1.0mm;3/4"--11/4"各为1.0-1.2mm;11/2"--2"各为1.0-1.5mm;21/2"--4"各为1.2-2.0mm。
4.1.2外螺纹或外圆的半径方向加工余量:1/4"--1/2"为0.8-1.0mm;3/4"--11/4"为1.0-1.2mm;11/2"--2"为1.2-1.5mm;21/2"--4"为1.5-2.0mm。
4.1.3内孔或内螺纹半径方向加工余量:1/4"--1/2"为0.8-1.0mm;3/4"--11/4"为0.8-1.2mm;11/2"--2"为1.0-1.5mm;21/2:--4"为1.5-2.0mm。
4.1.4阀体中孔平面加工余量:0.5-1.0mm。
4.1.5内孔深度和外圆长度毛坯尺寸:与图纸加工尺寸相符。
4.1.6抛光的毛坯单向表面余量1/4"--1/2"为0.5-0.8mm;3/4"--1"为0.8-1.2mm;11/4"--2"为1.0-1.5mm。
QT450-10铸造毛坯件检验规范
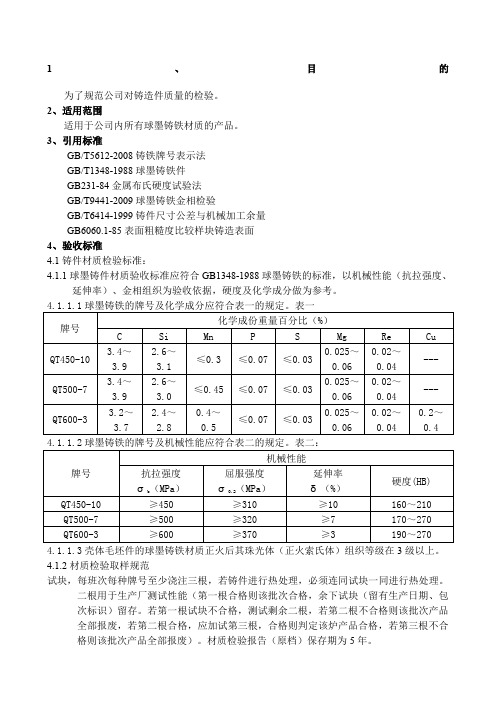
1、目的为了规范公司对铸造件质量的检验。
2、适用范围适用于公司内所有球墨铸铁材质的产品。
3、引用标准GB/T5612-2008铸铁牌号表示法GB/T1348-1988球墨铸铁件GB231-84金属布氏硬度试验法GB/T9441-2009球墨铸铁金相检验GB/T6414-1999铸件尺寸公差与机械加工余量GB6060.1-85表面粗糙度比较样块铸造表面4、验收标准4.1铸件材质检验标准:4.1.1球墨铸件材质验收标准应符合GB1348-1988球墨铸铁的标准,以机械性能(抗拉强度、延伸率)、金相组织为验收依据,硬度及化学成分做为参考。
4.1.1.3壳体毛坯件的球墨铸铁材质正火后其珠光体(正火索氏体)组织等级在3级以上。
4.1.2材质检验取样规范试块,每班次每种牌号至少浇注三根,若铸件进行热处理,必须连同试块一同进行热处理。
二根用于生产厂测试性能(第一根合格则该批次合格,余下试块(留有生产日期、包次标识)留存。
若第一根试块不合格,测试剩余二根,若第二根不合格则该批次产品全部报废,若第二根合格,应加试第三根,合格则判定该炉产品合格,若第三根不合格则该批次产品全部报废)。
材质检验报告(原档)保存期为5年。
球铁铸件从每包铁水的最后一型附铸金相试块或铸件本体进行金相检验,依次往前直到合格(或本包铁水所浇铸件检验完)为止。
附铸试块应能代表本体。
若试块不好,应对铸件本体破件进行检验。
若金相检验由问题,加倍抽查。
金相本体试块应按天分类以月为单位保存,保存期为6个月,检验报告保存期5年。
球化等级要求在3级以上,石墨大小要求为5~7级。
每炉铁水(炉前)及至少两炉铸件(炉后)的化学成分。
炉前主要化验C、Si和S,炉后所有元素全部化验。
每天第一炉溶清后必须检测C、Si、Mn、P和S,之后C、Si每炉化验检测。
化学成分记录要求齐全,记录表保存期5年。
金属布氏硬度试验法的规定进行,硬度试验可在铸件试块或铸件本体上的一个部位或几个部位上进行。
铸造毛坯件检验规范
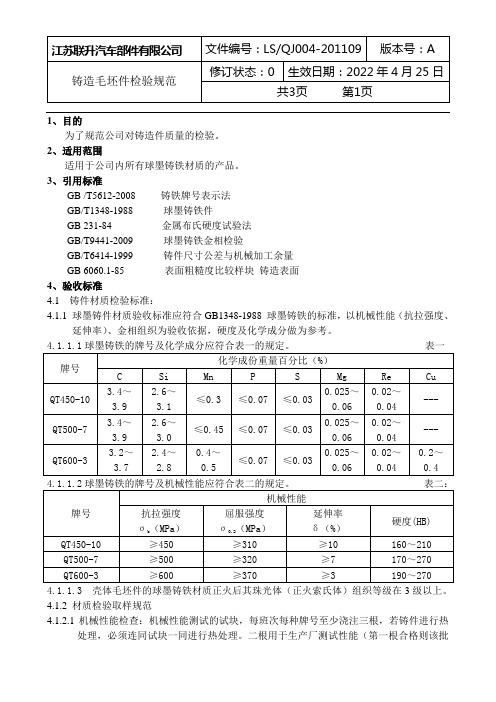
1、目的为了规范公司对铸造件质量的检验。
2、适用范围适用于公司内所有球墨铸铁材质的产品。
3、引用标准GB /T5612-2008 铸铁牌号表示法GB/T1348-1988 球墨铸铁件GB 231-84 金属布氏硬度试验法GB/T9441-2009 球墨铸铁金相检验GB/T6414-1999 铸件尺寸公差与机械加工余量GB 6060.1-85 表面粗糙度比较样块铸造表面4、验收标准4.1 铸件材质检验标准:4.1.1 球墨铸件材质验收标准应符合GB1348-1988 球墨铸铁的标准,以机械性能(抗拉强度、延伸率)、金相组织为验收依据,硬度及化学成分做为参考。
4.1.1.3 壳体毛坯件的球墨铸铁材质正火后其珠光体(正火索氏体)组织等级在3级以上。
4.1.2 材质检验取样规范4.1.2.1机械性能检查:机械性能测试的试块,每班次每种牌号至少浇注三根,若铸件进行热处理,必须连同试块一同进行热处理。
二根用于生产厂测试性能(第一根合格则该批次合格,余下试块(留有生产日期、包次标识)留存。
若第一根试块不合格,测试剩余二根,若第二根不合格则该批次产品全部报废,若第二根合格,应加试第三根,合格则判定该炉产品合格,若第三根不合格则该批次产品全部报废)。
材质检验报告(原档)保存期为5年。
4.1.2.2金相组织检查:球铁铸件从每包铁水的最后一型附铸金相试块或铸件本体进行金相检验,依次往前直到合格(或本包铁水所浇铸件检验完)为止。
附铸试块应能代表本体。
若试块不好,应对铸件本体破件进行检验。
若金相检验由问题,加倍抽查。
金相本体试块应按天分类以月为单位保存,保存期为6个月,检验报告保存期5年。
球化等级要求在3级以上,石墨大小要求为5~7级。
4.1.2.3化学成分检查:每天必须分析每炉铁水(炉前)及至少两炉铸件(炉后)的化学成分。
炉前主要化验C、Si和S,炉后所有元素全部化验。
每天第一炉溶清后必须检测C、Si、Mn、P和S,之后C、Si每炉化验检测。
毛坯铸钢件检验规范

11.1 铸造厂和检验部应对铸件进行认真检验,检验验收项目及验收方法按表 5 进行。
表5
序 检验项目
号
试制产品
供方
检验部
正常生产产品
供方
检验部
备注
确认文件/复
确认文件/复
1 化学成分 每个炉批号
每个炉批号
验
验
确认文件/复
确认文件/复
2 机械性能 每个炉批号
每个炉批号
验
验
每个热处理 3 热处理
批
确认文件
CF3
CF8M
A002 A202 E308L-16 E316-16
CF3M
A022 E316L-16
WC6
R307 E5515-B2
WC9
R407 E9015-B3
7.5 合同规定铸件进行 MT、RT 或 UT 的,在焊补热处理后应进行相同的无损检测方法对
铸造毛坯件质量检验规范
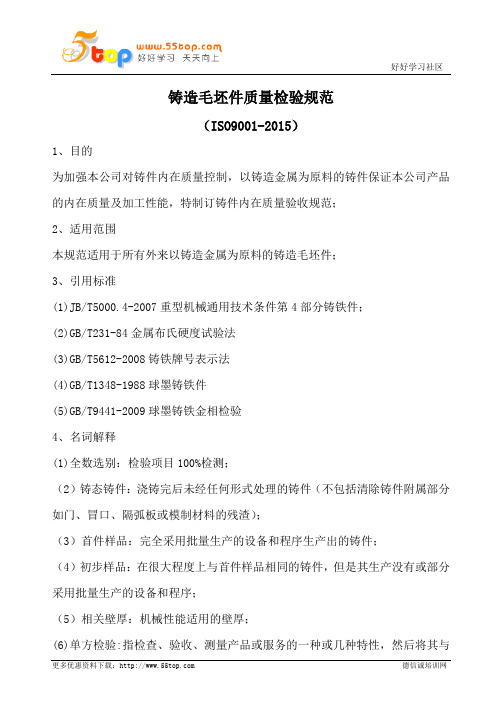
铸造毛坯件质量检验规范(ISO9001-2015)1、目的为加强本公司对铸件内在质量控制,以铸造金属为原料的铸件保证本公司产品的内在质量及加工性能,特制订铸件内在质量验收规范;2、适用范围本规范适用于所有外来以铸造金属为原料的铸造毛坯件;3、引用标准(1)JB/T5000.4-2007重型机械通用技术条件第4部分铸铁件;(2)GB/T231-84金属布氏硬度试验法(3)GB/T5612-2008铸铁牌号表示法(4)GB/T1348-1988球墨铸铁件(5)GB/T9441-2009球墨铸铁金相检验4、名词解释(1)全数选别:检验项目100%检测;(2)铸态铸件:浇铸完后未经任何形式处理的铸件(不包括清除铸件附属部分如门、冒口、隔弧板或模制材料的残渣);(3)首件样品:完全采用批量生产的设备和程序生产出的铸件;(4)初步样品:在很大程度上与首件样品相同的铸件,但是其生产没有或部分采用批量生产的设备和程序;(5)相关壁厚:机械性能适用的壁厚;(6)单方检验:指检查、验收、测量产品或服务的一种或几种特性,然后将其与指定要求相比较以确定产品是否合格的行为;(7)连续检验:指对生产一段时间后的大量相同规格的铸件的特性和/或生产参数进行定期检验;(8)跳跃检验:指对生产一段时间后的大量相同规格的铸件的特性和/或生产参数进行间断性检验;(9)试件:样品的一部分,有特定的尺寸,经过机械加工也可能没有经过机械加工,并严格遵守所要求的试验条件;5、铸件内在质量验收总则球墨铸件材质验收标准应符合GB1348-1988球墨铸铁的标准,以机械性能(抗拉强度、屈服强度、延伸率)、金相组织、硬度及化学成分为验收判定依据;5.1铸件化学成分(1)如果未在图纸或询价单或订单或者质保协议中另行规定,对于铸造材料的化学组成,应采用相关材料标准的要求;(2)如果未在图纸或询价单或订单或者质保协议中另行规定,铸造材料化学组成的有关数据应特指液体金属,即球化后浇筑前的(炉前)浇包分析;(3)如果相关材料标准和订单或询价单等都不含有铸造材料化学组成的任何有关数据,如只规定了材料的机械性能,则制造商可以自行选择适当的化学组成,但必须符合铸件使用地(毛坯或半成品或者成品的最终使用地点)的环保等法律法规要求;(5)化学组成在要求对某一铸件进行化学分析时,化学元素允许偏差要符合材料标准给出的偏差或符合采购方与制造商之间通过协议确定的偏差。
资料│球铁铸件验收标准

资料│球铁铸件验收标准一、引用标准GB9441-88 球墨铸铁金相检验GB6060.1-85 表面粗糙度比较样块铸造表面 GB321-81 硬度试验二、技术要求三、机械性能机械性能为铸态毛坯本体试块测试值。
1、金相组织按GB9441-88《球墨铸铁金相检验》2、石墨铸件毛坯本体的球化率在60%以上,球化级别80%为1-3级,最差部位不低于5级,球径为5-7级。
3、基体(参考)铸件本体的基础组织为:铁素体80%以上,碳化物含量小于2%。
4、几何形状与尺寸铸件应符合相应的毛坯图尺寸规定。
铸件错型≤0.5mm,砂芯歪斜量≤0.8mm。
5、表面质量①铸件毛坯表面应无粘砂、氧化皮等缺陷,铸件毛坯表面的浇冒口、出气孔、多肉、飞边、毛刺等清除干净。
②铸件毛坯不允许有裂纹、缩孔、疏松、冷隔等影响使用性能的铸造缺陷。
③铸造毛坯非加工表面粗糙度R a≤100粗糙度评定按GB6060.1-85的规定进行。
④铸造毛坯不允许有锈蚀。
⑤铸件外表气孔和渣孔加工部位:直径≤Φ3mm,最大深度≤1.5mm,Φ2mm以上气孔数量每侧面不多于4个,Φ2mm以下气孔数量每侧面不多于7个。
非加工部位:直径≤Φ2mm,最大深度≤1.5mm,Φ2mm以上气孔数量不多于2个,Φ2mm以下气孔数量不多于5个。
6、铸件上的缺陷不允许修补。
7、批次的标识铸件毛坯必须在其本体的表面铸出永久性炉次标志即炉号。
炉号用六位组成。
第一位表示年号,取年号尾数,第二、三位表示月号,第四、五位为H号,第六位为流水号(当一炉铁水分作多包球化浇注时)× ×× ×× ×年号尾数月号日号流水号四、检验方法1、在提供最处样件时,铸件必须经解剖检测,X射线检测或Y射线检测无缩孔、缩松、裂纹等缺陷;在正常生产时,为确保质量稳定,要定期进行上述方式检测。
并且抽1‰铸件进行解剖检测。
生产设备改变、材料改变、更换模具、更改工艺或更换操作者时,铸件必须经以上解剖与检测。
毛坯铸件检验规程
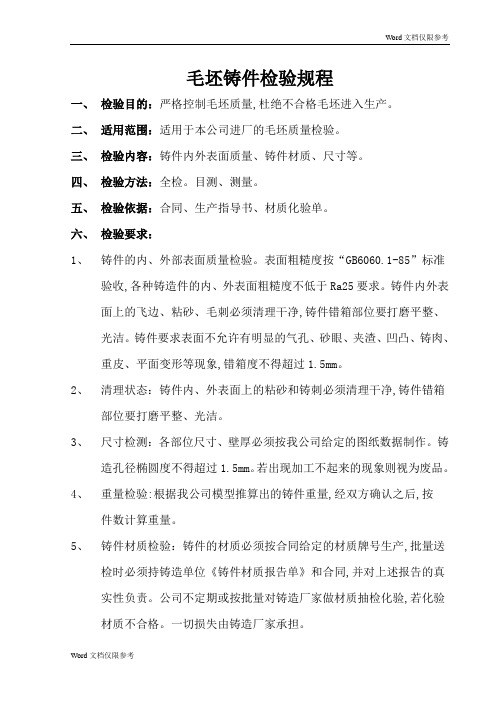
毛坯铸件检验规程一、检验目的:严格控制毛坯质量,杜绝不合格毛坯进入生产。
二、适用范围:适用于本公司进厂的毛坯质量检验。
三、检验内容:铸件内外表面质量、铸件材质、尺寸等。
四、检验方法:全检。
目测、测量。
五、检验依据:合同、生产指导书、材质化验单。
六、检验要求:1、铸件的内、外部表面质量检验。
表面粗糙度按“GB6060.1-85”标准验收,各种铸造件的内、外表面粗糙度不低于Ra25要求。
铸件内外表面上的飞边、粘砂、毛刺必须清理干净,铸件错箱部位要打磨平整、光洁。
铸件要求表面不允许有明显的气孔、砂眼、夹渣、凹凸、铸肉、重皮、平面变形等现象,错箱度不得超过1.5mm。
2、清理状态:铸件内、外表面上的粘砂和铸刺必须清理干净,铸件错箱部位要打磨平整、光洁。
3、尺寸检测:各部位尺寸、壁厚必须按我公司给定的图纸数据制作。
铸造孔径椭圆度不得超过1.5mm。
若出现加工不起来的现象则视为废品。
4、重量检验:根据我公司模型推算出的铸件重量,经双方确认之后,按件数计算重量。
5、铸件材质检验:铸件的材质必须按合同给定的材质牌号生产,批量送检时必须持铸造单位《铸件材质报告单》和合同,并对上述报告的真实性负责。
公司不定期或按批量对铸造厂家做材质抽检化验,若化验材质不合格。
一切损失由铸造厂家承担。
6、铸件不允许用捶击、堵塞、浸渍等方法消除渗漏缺陷,更不允许用焊接的方法对铸件的缺陷进行焊补。
7、铸件的硬度适中,易于切削加工,铸件的铸字必须按照合同规定铸造。
如果铸件的铸字出现错误、不清晰等现象则视为不合格品处理。
8、铸件在加工过程中出现气孔、夹渣、材料硬度过大等不良缺陷、加工尺寸不足导致加工不起来的情况,作为废品处理。
七、检验步骤:1、供应商登记进厂后,通知有关外协人员。
并提供以下资料:《生产指导书》号;采购合同;材质单。
有关外协人员填写到货检验报告交至质检科进行入厂检验,相关外协人员必须在场。
2、质检人员进行入库检验时,必须按照检验要求进行检验。
铸造毛坯检验规程

灰铸铁铸件毛坯的机械加工余量表(一)
灰铸铁铸件毛坯尺寸偏差表(二)
备注:1、以上两个表是台州美机缝纫机有限公司灰铸铁毛坯机械加工余量参照表,此表摘自于JZ67-62二级精度铸件。
2、各表中所用的公称尺寸,是指两个相对加工面之间的最大距离,或者从基准面或中心线(铸件图或零件图上标出的)到加工
面的距离。
若几个加工对基轴线或基准面是平行的,则公称尺寸必须采用最远一个加工面到基准面的距离。
3、铸孔的机械加工余量,不管其所在位置如何,均采用各级的顶面加工余量。
毛坯检验规范

毛坯检验规范1、目的对产品毛坯进料检验作文件化规定,使检验过程规范化和标准化,避免和减少因毛坯的不合格造成后续作业的困难和产品的不合格。
2、范围适用于本公司所有铸造毛坯、锻造毛坯和压铸毛坯的进料检验过程。
3、依据1).国家相关标准如:《逐批检查计数抽样程序及检查表》 GB2828-2008《铸造铜合金技术条件》 GB1176-87《阀门铸铜件外观质量要求》 GB12231《锌合金、铝合金、铜合金压铸件技术条件》等; JB2702-802).产品图样、技术要求及工艺要求;3).客户要求和合同要求等。
4、内容4.1 毛坯尺寸规定4.1.1 毛坯两端面的加工余量:1/4"--1/2" 各为 0.8-1.0mm;3/4"--1 1/4" 各为 1.0-1.2mm;1 1/2"--2" 各为 1.0-1.5mm;2 1/2"--4" 各为 1.2-2.0mm。
4.1.2 外螺纹或外圆的半径方向加工余量:1/4"--1/2" 为 0.8-1.0mm;3/4"--1 1/4" 为 1.0-1.2mm;1 1/2"--2" 为 1.2-1.5mm;2 1/2"--4" 为 1.5-2.0mm。
4.1.3 内孔或内螺纹半径方向加工余量:1/4"--1/2" 为 0.8-1.0mm;3/4"--1 1/4" 为 0.8-1.2mm;1 1/2"--2" 为 1.0-1.5mm;2 1/2:--4" 为 1.5-2.0mm。
4.1.4阀体中孔平面加工余量:0.5-1.0mm。
4.1.5内孔深度和外圆长度毛坯尺寸:与图纸加工尺寸相符。
4.1.6抛光的毛坯单向表面余量1/4"--1/2" 为 0.5-0.8mm;3/4"--1" 为 0.8-1.2mm;1 1/4"--2" 为 1.0-1.5mm。
铸件外观质量检验规范
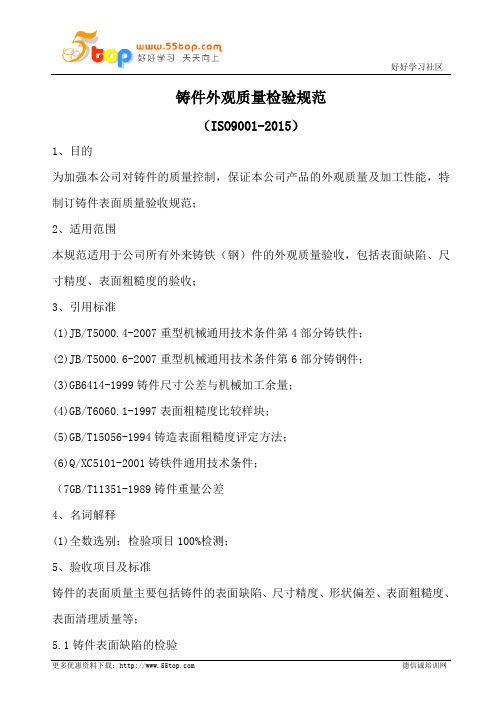
铸件外观质量检验规范(ISO9001-2015)1、目的为加强本公司对铸件的质量控制,保证本公司产品的外观质量及加工性能,特制订铸件表面质量验收规范;2、适用范围本规范适用于公司所有外来铸铁(钢)件的外观质量验收,包括表面缺陷、尺寸精度、表面粗糙度的验收;3、引用标准(1)JB/T5000.4-2007重型机械通用技术条件第4部分铸铁件;(2)JB/T5000.6-2007重型机械通用技术条件第6部分铸钢件;(3)GB6414-1999铸件尺寸公差与机械加工余量;(4)GB/T6060.1-1997表面粗糙度比较样块;(5)GB/T15056-1994铸造表面粗糙度评定方法;(6)Q/XC5101-2001铸铁件通用技术条件;(7GB/T11351-1989铸件重量公差4、名词解释(1)全数选别:检验项目100%检测;5、验收项目及标准铸件的表面质量主要包括铸件的表面缺陷、尺寸精度、形状偏差、表面粗糙度、表面清理质量等;5.1铸件表面缺陷的检验5.1.1表面缺陷检验的一般要求(1)铸件非加工表面上的浇冒口必须清理得与铸件表面同样平整,加工面上的浇冒口残留量应符合技术要求,若无要求,则按表8执行;(2)在铸件上不允许有裂纹、通孔、穿透性的冷隔和穿透性的缩松、夹渣等机械加工不能去除的缺陷;(3)铸件非加工表面的毛刺、披缝、型砂、砂芯等应清理干净;(4)铸件一般待加工表面,允许有不超过加工余量范围内的任何缺陷存在;重要加工面允许有不超过加工余量2/3的缺陷存在,但裂纹缺陷应予清除;加工后的表面允许存在直径*长度*深度小于等于2*2*2的非连片孔洞的铸造缺陷;(5)作为加工基准面(孔)和测量基准的铸件表面,平整度小于等于2.0毫米、粗糙度Ra50以内;(6)铸件表面气孔、砂眼、夹渣面积不大,但比较分散或者有连片麻点的表面不予接收;(7)除技术要求特别注明的铸件外,对于表面有气孔、缩孔、砂眼等缺陷的铸钢件允许补焊,但铸铁件未经允许不得焊补(铸铁件实行一案一判的原则)但补焊面积不允许超过铸件面积的10%,焊接质量应符合JB/T5000.7-2007标准要求,补焊后必须退火、机械性能达到图纸要求,且不得有渗漏及影响外观的缺陷;5.1.2铸件外观质量等级缺陷项目等级A B C飞边不允许飞边高度≤1.5毫米允许不易于伤手的飞边毛刺不允许允许不易于伤手的毛刺允许不易伤手的毛刺孔眼气孔 100cm 2面积内允许直径不大于φ2mm 深度不超过壁厚1/4的孔眼2个,两处距离>60mm ;整个铸件不超过4个100cm 2面积内允许直径不大于φ3mm 深度不超过壁厚1/3的孔眼2处,两处距离>60mm ;整个铸件不超过8个不致于影响强度,其余不做要求 针孔 渣眼 缩孔 不致于影响强度裂纹 不允许 不允许不允许 冷隔 沟槽 夹砂结疤 不允许 100cm 2面积内允许面积不超过8cm 2的缺陷2处;整个铸件不超过4处不致于影响强度 皱皮 不允许 不明显引人注意缩陷不允许不允许 不允许缺肉1、一般零部件采用B 级精度,在检查过程中,如有一个或多个项目超出B 级精度要求的零部件均判定为不合格;2、影响到零部件安全、性能的部位,外观质量采用A 级精度,如果有一个或多个项目超出规定级精度要求的零部件均判定为不合格;5.2铸件尺寸的检验 5.2.1铸件毛坯尺寸公差铸件尺寸公差应按毛坯图或技术条件规定的尺寸公差等级执行,当技术文件未规定尺寸公差时,则应以GB6414为依据,并按照下表选定公差值(粗线框内为推荐使用公差等级);毛坯铸件基本尺寸(mm )尺寸公差等级CT12CT13 CT14 CT15 CT16 ≤10~16 4.4 --- --- --- --- >16~25 4.6 6 8 10 12 >25~40 5.0 7 9 11 14 >40~63 5.6 8 10 12 16 >63~100 6 9 11 14 18 >100~160 7 10 12 16 20 >160~250 8 11 14 18 22 >250~400912162025>400~630 10 14 18 22 28 >630~1000 11 16 20 25 32 >1000~1600 13 18 23 29 37 >1600~2500 15 21 26 33 42 >25004000 17 24 30 38 49 >4000~6300 20 28 35 44 56 >6300~100002332405064注:1、毛坯铸件基本尺寸是指机械加工前毛坯铸件的尺寸,包括加工余量和起模斜度; 2、毛坯基本尺寸按铸件最大尺寸选取,该铸件较小尺寸公差等级与最大尺寸公差等级相同;3、壁厚采用低一级的公差等级;4、公差带应对称于毛坯铸件基本尺寸配置,例:基本尺寸30mm ,CT13公差值为±7mm ;如有特殊要求非对称式配置时,应在技术要求中单独列出公差范围;5.2.2铸件分型面处最大错型值应不得超过表2所示公差值,当需进一步限制错型量时,应从表中选取;公差等级CT 错型值(mm )11~13 1.5 14~162.55.2.3铸件加工余量应符合表的规定,有特殊要求的表面应在技术要求中单独标注加工余量;最大轮廓尺寸加工余量一个面顶面加量≤30 4 2>30~50 5 >50~180 6 >180~315 7 >315~500 8 >500~800 103>800~1250 12 >1250~1600 144>1600~250016>2500~3150 18>3150~4000 205>4000~6300 25>6300~10000 30 7注:1、属于该铸件的较小尺寸的加工余量与最大轮廓尺寸的加工余量相同;2、此表加工余量仅指一个面的加工余量,对于柱面和两面加工的铸件,铸件轮廓尺寸应为最终机械加工后成品尺寸与两倍加工余量之和;5.3表面粗糙度检测表面粗糙度总体检测原则依据图纸要求,当图纸无要求是执行国标GB/T15056;5.3.1一般情况下,表面粗糙度要求Ra50,铸件难以清理的部位,局部允许Ra100,待加工表面允许降低1级;5.3.2.使用面积法作为验收依据面积法常用的比较样块评定铸件表面粗糙度;方法如下:(1)铸造表面粗糙度比较样块应符合GB6060.1-1997标准;(2)按照国标BWZ001-88评定铸件表面粗糙度的等级;(3)铸件的浇道、冒口、修补的残余表面及铸造表面缺陷(如粘砂、结疤等)不列为被检表面;(4)以铸造表面粗糙度比较样块为对照标准,对被检铸件的铸造表面用视觉或触觉的方法进行对比;(5)用样块对比时,应选用适于铸造合金材料和工艺方法的样块进行对比;(6)被检的铸造表面必须清理干净,样块表面和被检表面均不得有锈蚀处;(7)用样块对比时,砂型铸造表面被检点数应符合表的规定;特种铸造表面被检点数应按表8的规定加倍;被检点应平均分布,每点的被检面积不得小于与之对比面的面积;被检铸造表面面积(cm2)<200 200~1000 100~10000 >10000被检点数(个) 不少于2 每200cm2不少于1 每1000cm2不少于1不少于40 (8)当被检铸造表面的粗糙度介于比较样块两级参数值之间者,所确定的被检铸造表面的粗糙度等级为粗的一级;(9)对被检铸造表面,以其80%的表面所达到的最粗表面粗糙度等级,为该铸造表面粗糙度等级;5.3.3铸件表面清理检测5.3.1铸件几何形状必须完整,非加工面上的清理损伤不应大于该处的尺寸偏差,加工面上的损伤不应大于该处加工余量的1/2;5.3.2允许铸件表面有少量的局部低凹或打磨痕迹,在直径不大于8mm,并能保证铸件规定的最小的壁厚;5.3.3为去除铸造缺陷而打磨后的铸件表面粗糙度应与一般铸件表面粗糙度基本一致;5.3.4除特殊情况外,铸件表面允许残留的浇冒口、毛刺,多肉残余量应按表8的要求进行;类别非加工面凸出高度(mm)加工面凸出高度(mm) 外表面非外表面浇冒口残余量-0.5~0.5 <2 <2~4毛刺残余量0 <2 <1~2多肉残余量<1 <2 <25.3.5铸件表面须经过防锈处理,保证在铸件进入面加工时不得有任何的锈蚀;5.3.6铸件表面如有油漆要求的,必须按有关涂装规定执行;5.4铸件重量检测5.4.1对于没有特殊要求的铸件,重量偏差可以不作为验收依据;如果技术条件有要求,供需双方协商后,铸件的重量偏差也应作为验收依据,一般应符合表的规定;公称重量(Kg) ≤200>200~500>500~1000>1000~5000>5000~10000>10000~30000>30000~50000>50000铸件重量上偏差(%)8 7.5 7 6.5 6 5.5 5 4.5。
铸造毛坯检验规定
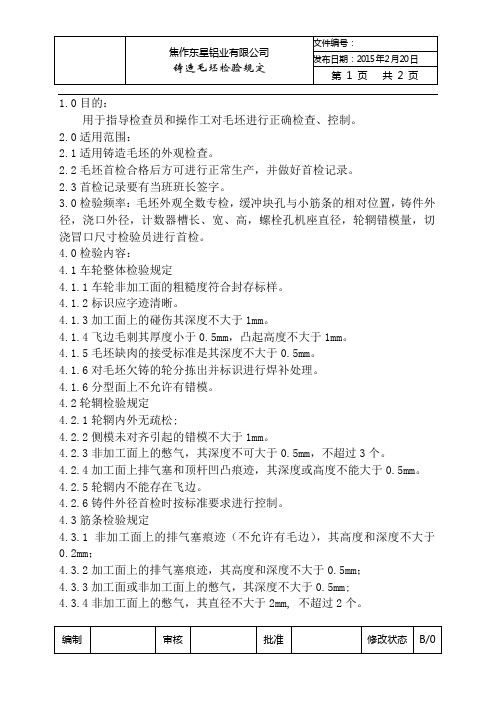
1.0目的:用于指导检查员和操作工对毛坯进行正确检查、控制。
2.0适用范围:2.1适用铸造毛坯的外观检查。
2.2毛坯首检合格后方可进行正常生产,并做好首检记录。
2.3首检记录要有当班班长签字。
3.0检验频率:毛坯外观全数专检,缓冲块孔与小筋条的相对位置,铸件外径,浇口外径,计数器槽长、宽、高,螺栓孔机座直径,轮辋错模量,切浇冒口尺寸检验员进行首检。
4.0检验内容:4.1车轮整体检验规定4.1.1车轮非加工面的粗糙度符合封存标样。
4.1.2标识应字迹清晰。
4.1.3加工面上的碰伤其深度不大于1mm。
4.1.4飞边毛刺其厚度小于0.5mm,凸起高度不大于1mm。
4.1.5毛坯缺肉的接受标准是其深度不大于0.5mm。
4.1.6对毛坯欠铸的轮分拣出并标识进行焊补处理。
4.1.6分型面上不允许有错模。
4.2轮辋检验规定4.2.1轮辋内外无疏松;4.2.2侧模未对齐引起的错模不大于1mm。
4.2.3非加工面上的憋气,其深度不可大于0.5mm,不超过3个。
4.2.4加工面上排气塞和顶杆凹凸痕迹,其深度或高度不能大于0.5mm。
4.2.5轮辋内不能存在飞边。
4.2.6铸件外径首检时按标准要求进行控制。
4.3筋条检验规定4.3.1非加工面上的排气塞痕迹(不允许有毛边),其高度和深度不大于0.2mm;4.3.2加工面上的排气塞痕迹,其高度和深度不大于0.5mm;4.3.3加工面或非加工面上的憋气,其深度不大于0.5mm;4.3.4非加工面上的憋气,其直径不大于2mm, 不超过2个。
4.3.5筋条上不能有疏松;4.3.6飞边、毛刺其厚度小于0.5mm,凸起高度不大于1mm。
4.3.7与轮辋交接处不允许有裂纹、缩松。
4.3.8筋条非加工面不允许有涂料脱落、凹凸不平等缺陷。
4.4轮鼓部位检验规定4.4.1轮鼓内各交接处无裂纹;4.4.2排气塞痕迹其深度不大于0.5mm,高度不大于0.3mm。
4.4.3轮鼓内的顶杆痕迹其高度和深度不大于1mm。
压铸件毛坯质量检验标准 (规范)
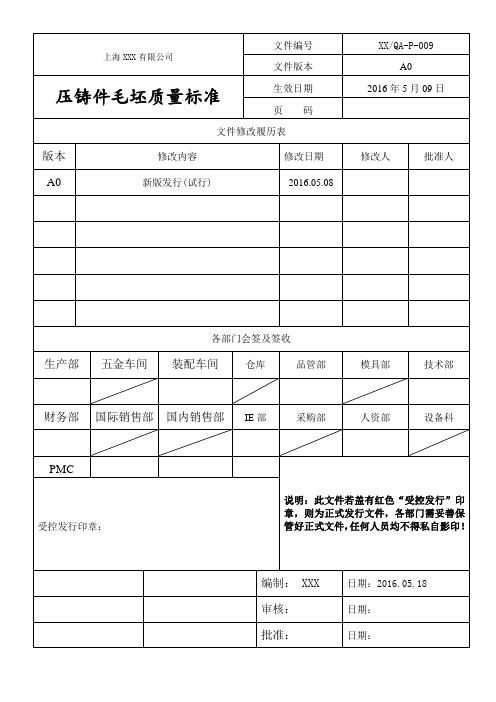
2.1压铸件质量要求
2.1.1压铸件应符合零件图样的规定。
2.1.2表面质量
2.1.2.1压铸件表面粗糙度应符合GB/T6060.1的规定。
2.1.2.2压铸件表面不允许有裂纹、欠铸、疏松、气泡和任何穿透性缺陷。
2.1.2.3压铸件表面允许有擦伤、凹陷、缺肉和网状毛刺等缺陷。但缺陷必须符合表1规定。
3.5压铸件表面粗糙度按GB/T6060.1的规定执行。
3.6压铸件需抛光加工的表面按GB/T 6060.4的规定执行。
3.7压铸件需喷丸、喷沙加工的表面按GB/T 6060.5的规定执行。
3.8压铸件内部质量的试验方法及检验规则可以包括:X射线照片、无损探伤试验、金相图片和压铸件剖面等,其检验结果应符合本标准2.1.6的规定。
表1压铸件表面质量要求
缺陷名称
缺陷范围
数值
备注
擦伤
深度(mm)
≤0.10
面积不超过总面积的百分数
5
凹陷
凹入深度(mm)
≤0.30
缺肉
深度(mm)
≤0.50
长度不大于(mm)
2
所在面上不允许超过的数量
2
离压铸件边缘距离(mm)
≥4
间距(mm)
≥10
网状毛刺
高度(mm)
≤0.2
2.1.2.4压铸件的浇口、飞边、溢流口、隔皮、顶杆痕迹等应清理干净。但允许留有痕迹。
设备科
PMC
说明:此文件若盖有红色“受控发行”印章,则为正式发行文件,各部门需妥善保管好正式文件,任何人员均不得私自影印!
受控发行印章:
编制:XXX
日期:2016.05.18
审核:
日期:
批准:
铝压铸毛坯件检验规程

铝压铸毛坯件检验规程1.范围本规程适应于铝压铸毛坯件,目的是对分厂铝压铸毛坯件完工检验及外协外购铝压铸毛坯件的进货检验进行统一规范,内容包括表面质量、外形质量、壁厚及断面检查、尺寸、内部质量、文字图案符号规定、材质、模具变更或修复共八个检查项目,并且规定了各个项目的判定标准、抽样方案和检测方法。
2、表面质量:2.1判定标准:铸件表面无鼠尾、沟槽、夹砂结疤、粘砂、表明粗糙、皱皮、缩陷、桔皮面、斑点、印痕、拉伤、裂纹、隔皮、飞翅、毛刺、外渗物、大面积脱模剂及锉刀痕、表面处理不能消除的拉痕、冷隔、气孔、积炭、缺肉等缺陷;压铸件内有嵌件的周围无包铝、生锈现象;型腔内无易脱落或造成零部件干涉的飞边、毛刺现象;表面质量有特殊要求的产品,按协商的封样件对比检查。
2.1.1鼠尾:铸件表面出现较浅(≤5mm)的带有锐角的凹痕;表面粗糙:铸件表明粗糙、凹凸不平,其微观几何特征超出铸造表明粗糙度测量上限,但未形成粘砂缺陷;缩陷:铸件的厚断面或断面交接处上平面的塌陷现象;印痕:因顶杆或镶块与型腔表面不平齐,而在压铸件表面相应部位产生的凸起或凹下的痕迹;皱皮:铸件上不规则的粗粒状或皱褶状的表皮,一般带有较深的网状沟槽;拉伤:压铸件表面由于与金属型啮合或粘结,顶出时顺出型方向出现的擦伤痕迹;冷隔:金属流相互对接或搭接未融合而出现的接痕;裂纹:合金基体被破坏或断开,形成细长的缝隙,呈不规则线状;隔皮:铸孔处应穿透而未穿透的金属层;飞翅:垂直铸件表面厚薄不均匀的薄片金属突起物;毛刺:铸件表面上刺状金属突起物。
2.2抽样方案:按GB2828中的IL=Ⅰ进行抽检,不合格判定数AQL=2.5。
2.3检测方法:目测、手感检查(检验员的校正视力标准不低于1.0)。
3、外形质量:3.1判定标准:铸件外形质量无浇不到、浇不满、型漏、跑火、损伤、变形、、欠铸、错模等影响外形的缺型缺陷;无缺(多)搭子,多(少)孔现象,非加工面平整无凸台、凹坑等影响密封性的结构;密封面宽度尺寸不小于3mm (必要时机加工确认),分型面侧抽芯等模具结合成型处无磕碰不平等缺陷,外形质量有特殊要求的产品,按协商的封样件对比检查。
铸造毛坯件质量检验规范
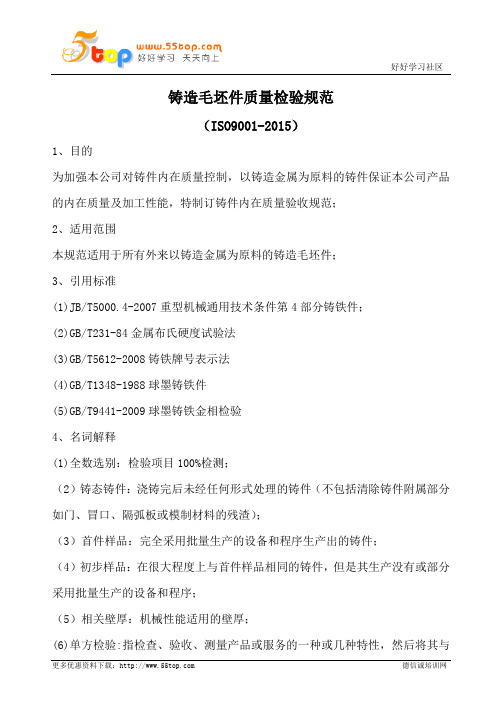
铸造毛坯件质量检验规范(ISO9001-2015)1、目的为加强本公司对铸件内在质量控制,以铸造金属为原料的铸件保证本公司产品的内在质量及加工性能,特制订铸件内在质量验收规范;2、适用范围本规范适用于所有外来以铸造金属为原料的铸造毛坯件;3、引用标准(1)JB/T5000.4-2007重型机械通用技术条件第4部分铸铁件;(2)GB/T231-84金属布氏硬度试验法(3)GB/T5612-2008铸铁牌号表示法(4)GB/T1348-1988球墨铸铁件(5)GB/T9441-2009球墨铸铁金相检验4、名词解释(1)全数选别:检验项目100%检测;(2)铸态铸件:浇铸完后未经任何形式处理的铸件(不包括清除铸件附属部分如门、冒口、隔弧板或模制材料的残渣);(3)首件样品:完全采用批量生产的设备和程序生产出的铸件;(4)初步样品:在很大程度上与首件样品相同的铸件,但是其生产没有或部分采用批量生产的设备和程序;(5)相关壁厚:机械性能适用的壁厚;(6)单方检验:指检查、验收、测量产品或服务的一种或几种特性,然后将其与指定要求相比较以确定产品是否合格的行为;(7)连续检验:指对生产一段时间后的大量相同规格的铸件的特性和/或生产参数进行定期检验;(8)跳跃检验:指对生产一段时间后的大量相同规格的铸件的特性和/或生产参数进行间断性检验;(9)试件:样品的一部分,有特定的尺寸,经过机械加工也可能没有经过机械加工,并严格遵守所要求的试验条件;5、铸件内在质量验收总则球墨铸件材质验收标准应符合GB1348-1988球墨铸铁的标准,以机械性能(抗拉强度、屈服强度、延伸率)、金相组织、硬度及化学成分为验收判定依据;5.1铸件化学成分(1)如果未在图纸或询价单或订单或者质保协议中另行规定,对于铸造材料的化学组成,应采用相关材料标准的要求;(2)如果未在图纸或询价单或订单或者质保协议中另行规定,铸造材料化学组成的有关数据应特指液体金属,即球化后浇筑前的(炉前)浇包分析;(3)如果相关材料标准和订单或询价单等都不含有铸造材料化学组成的任何有关数据,如只规定了材料的机械性能,则制造商可以自行选择适当的化学组成,但必须符合铸件使用地(毛坯或半成品或者成品的最终使用地点)的环保等法律法规要求;(5)化学组成在要求对某一铸件进行化学分析时,化学元素允许偏差要符合材料标准给出的偏差或符合采购方与制造商之间通过协议确定的偏差。
QT450-10铸造毛坯件检验规范

1、目的为了规范公司对铸造件质量的检验。
2、适用范围适用于公司内所有球墨铸铁材质的产品。
3、引用标准GB /T5612-2008 铸铁牌号表示法GB/T1348-1988 球墨铸铁件GB 231-84 金属布氏硬度试验法GB/T9441-2009 球墨铸铁金相检验GB/T6414-1999 铸件尺寸公差与机械加工余量GB 6060.1-85 表面粗糙度比较样块铸造表面4、验收标准4.1 铸件材质检验标准:4.1.1 球墨铸件材质验收标准应符合GB1348-1988 球墨铸铁的标准,以机械性能(抗拉强度、延伸率)、金相组织为验收依据,硬度及化学成分做为参考。
4.1.1.3 壳体毛坯件的球墨铸铁材质正火后其珠光体(正火索氏体)组织等级在3级以上。
4.1.2 材质检验取样规范4.1.2.1机械性能检查:机械性能测试的试块,每班次每种牌号至少浇注三根,若铸件进行热处理,必须连同试块一同进行热处理。
二根用于生产厂测试性能(第一根合格则该批次合格,余下试块(留有生产日期、包次标识)留存。
若第一根试块不合格,测试剩余二根,若第二根不合格则该批次产品全部报废,若第二根合格,应加试第三根,合格则判定该炉产品合格,若第三根不合格则该批次产品全部报废)。
材质检验报告(原档)保存期为5年。
4.1.2.2金相组织检查:球铁铸件从每包铁水的最后一型附铸金相试块或铸件本体进行金相检验,依次往前直到合格(或本包铁水所浇铸件检验完)为止。
附铸试块应能代表本体。
若试块不好,应对铸件本体破件进行检验。
若金相检验由问题,加倍抽查。
金相本体试块应按天分类以月为单位保存,保存期为6个月,检验报告保存期5年。
球化等级要求在3级以上,石墨大小要求为5~7级。
4.1.2.3化学成分检查:每天必须分析每炉铁水(炉前)及至少两炉铸件(炉后)的化学成分。
炉前主要化验C、Si和S,炉后所有元素全部化验。
每天第一炉溶清后必须检测C、Si、Mn、P和S,之后C、Si每炉化验检测。
铝合金压铸件毛坯检验规范
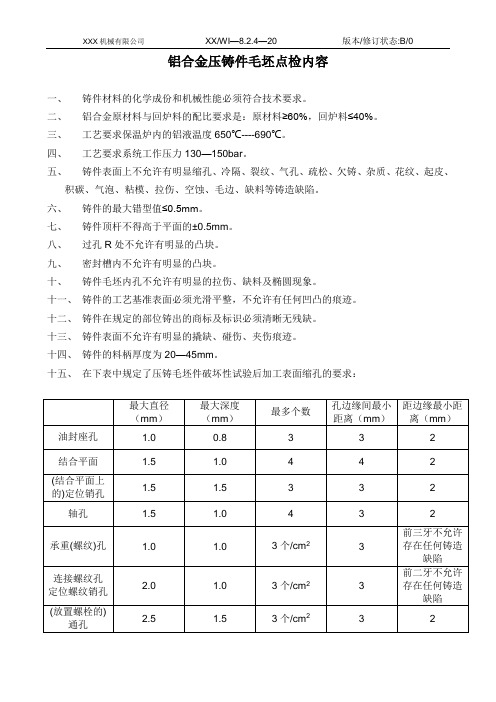
XXX机械有限公司XX/WI—8.2.4—20 版本/修订状态:B/0
铝合金压铸件毛坯点检内容
一、铸件材料的化学成份和机械性能必须符合技术要求。
二、铝合金原材料与回炉料的配比要求是:原材料≥60%,回炉料≤40%。
三、工艺要求保温炉内的铝液温度650℃----690℃。
四、工艺要求系统工作压力130—150bar。
五、铸件表面上不允许有明显缩孔、冷隔、裂纹、气孔、疏松、欠铸、杂质、花纹、起皮、
积碳、气泡、粘模、拉伤、空蚀、毛边、缺料等铸造缺陷。
六、铸件的最大错型值≤0.5mm。
七、铸件顶杆不得高于平面的±0.5mm。
八、过孔R处不允许有明显的凸块。
九、密封槽内不允许有明显的凸块。
十、铸件毛坯内孔不允许有明显的拉伤、缺料及椭圆现象。
十一、铸件的工艺基准表面必须光滑平整,不允许有任何凹凸的痕迹。
十二、铸件在规定的部位铸出的商标及标识必须清晰无残缺。
十三、铸件表面不允许有明显的撬缺、碰伤、夹伤痕迹。
十四、铸件的料柄厚度为20—45mm。
十五、在下表中规定了压铸毛坯件破坏性试验后加工表面缩孔的要求:。
铸件检验规范
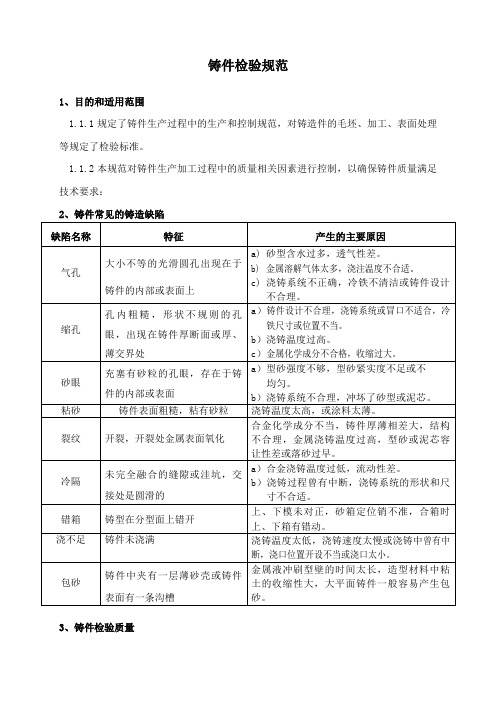
铸件检验规范1、目的和适用范围1.1.1规定了铸件生产过程中的生产和控制规范,对铸造件的毛坯、加工、表面处理等规定了检验标准。
1.1.2本规范对铸件生产加工过程中的质量相关因素进行控制,以确保铸件质量满足技术要求:2、铸件常见的铸造缺陷3、铸件检验质量3.1.1铸件出现铸造缺陷后,并非都是废品,应根据铸件的具体技术要求判断,判断原则如下:a)铸件出现铸造缺陷后,其质量达不到技术要求,而又不能修补时,应列为废品;b)不重要的铸件或铸件的某些部位即使存在铸造缺陷,如不影响使用或者修补后不影响使用时,可以不列为废品;c)当铸件出现铸造缺陷,即使技术上可以修补,并且修补后不影响使用,但由于经济上不合算,或因此会给企业造成不良影响时,仍应不修补而列为废品。
3.1.2对铸件铸造缺陷的一般要求为:a)铸件不允许存在裂纹、冷隔和浇不足等铸造缺陷;b)当铸造缺陷位于铸件的加工面上,通过机械加工余量可以去除时;c)在非加工面上,缺陷的深度不超过铸件该处厚度的1/10~1/5时(重要铸件或铸件的重要部位取小值,一般铸件或铸件的一般部位取大值);3.1.3铸件质量检验是铸造生产的重要工序,其主要职能是:a)为铸件生产和管理部门提供质量信息;保证产品质量。
b)铸件的检验主要包括铸件表面质量检验、铸件内在质量检验以及铸件质量的综合鉴定。
其中,铸件的表面质量包括铸件的表面缺陷、尺寸精度、质量偏差、表面粗糙度等。
c)铸件外观质量优劣影响后续加工工艺、后续加工的消耗,也影响铸件的使用性能。
所有铸件都要按照规定的标准进行外观质量检验。
这些检验又常常需要分多次完成。
例如,铸件铸出后的初检只能发现明显的表面缺陷,细小的表面缺陷则要用专门的设备才能发现。
外部尺寸不难直接测量,内腔的某些形状与尺寸,则要切剖铸件才能测出。
4、铸件外观质量检验4.1.1检验的依据是铸件的有关标准、技术条件和图样。
铸件的表面质量主要包括铸件的表面缺陷、尺寸精度、质量偏差、形状偏差、表面粗糙度和铸件表面清理质量等多方面内容。
- 1、下载文档前请自行甄别文档内容的完整性,平台不提供额外的编辑、内容补充、找答案等附加服务。
- 2、"仅部分预览"的文档,不可在线预览部分如存在完整性等问题,可反馈申请退款(可完整预览的文档不适用该条件!)。
- 3、如文档侵犯您的权益,请联系客服反馈,我们会尽快为您处理(人工客服工作时间:9:00-18:30)。
1、目的
为了规范公司对铸造件质量的检验。
2、适用范围
适用于公司内所有球墨铸铁材质的产品。
3、引用标准
GB /T5612-2008 铸铁牌号表示法
GB/T1348-1988 球墨铸铁件
GB 231-84 金属布氏硬度试验法
GB/T9441-2009 球墨铸铁金相检验
GB/T6414-1999 铸件尺寸公差与机械加工余量
GB 表面粗糙度比较样块铸造表面
4、验收标准
铸件材质检验标准:
球墨铸件材质验收标准应符合GB1348-1988 球墨铸铁的标准,以机械性能(抗拉强度、延伸率)、金相组织为验收依据,硬度及化学成分做为参考。
壳体毛坯件的球墨铸铁材质正火后其珠光体(正火索氏体)组织等级在3级以上。
材质检验取样规范
机械性能检查:机械性能测试的试块,每班次每种牌号至少浇注三根,若铸件进行热处理,必须连同试块一同进行热处理。
二根用于生产厂测试性能(第一根合格则该批次合格,余下试块(留有生产日期、包次标识)留存。
若第一根试块不合格,测试剩余二根,若第二根不合格则该批次产品全部报废,若第二根合格,应加试第三根,合格则判定该炉产品合格,若第三根不合格则该批次产品全部报废)。
材质检验报告(原档)保存期为5年。
金相组织检查:球铁铸件从每包铁水的最后一型附铸金相试块或铸件本体进行金相检验,依次往前直到合格(或本包铁水所浇铸件检验完)为止。
附铸试块应能代表本体。
若试
块不好,应对铸件本体破件进行检验。
若金相检验由问题,加倍抽查。
金相本体试块应按天分类以月为单位保存,保存期为6个月,检验报告保存期5年。
球化等级要求在3级以上,石墨大小要求为5~7级。
化学成分检查:每天必须分析每炉铁水(炉前)及至少两炉铸件(炉后)的化学成分。
炉前主要化验C、Si和S,炉后所有元素全部化验。
每天第一炉溶清后必须检测C、Si、Mn、P和S,之后C、Si每炉化验检测。
化学成分记录要求齐全,记录表保存期5年。
硬度试验检查:布氏硬度试验应按GB231-84 金属布氏硬度试验法的规定进行,硬度试验可在铸件试块或铸件本体上的一个部位或几个部位上进行。
铸件尺寸检验标准:
铸件外形及尺寸应符合我公司提供的图纸、合同/订单的要求。
铸件尺寸的未注公差采用GB/T 6414-1999标准的9级公差检验,公差值为±1/2 CT9级。
如
铸件外观质量
铸字、标识:铸件上所要求的铸字、标识必须完整、清晰、正确,符合图纸要求。
错箱值:铸件最大错箱值不超过。
浇冒口、飞边残留高度:铸件上浇冒口、披缝等要清理干净,最大残留高度不超过。
表面粗糙度:铸件表面应光滑、平整,表面有粘砂、氧化皮、锈蚀等应清理干净,表面粗糙度应按GB 《表面粗糙度比较样块铸造表面》的规定,表面粗糙度不超过Ra 50。
铸件表面缺陷
生产交货的铸件表面质量应进行100%目测检验。
铸件上不允许存在影响性能的缺陷(裂纹、冷隔、缩孔、夹渣、浇不足、缩孔等)存在。
铸件的非加工表面不允许有直径超过1mm、深度超过的单孔洞存在,但每平方厘米面积范围内允许直径小于1mm、深度小于的孔不多于三处,相邻缺陷间隔在10mm以上。
但不允许在铸件壁厚的相应面上出现,不允许成片的孔眼类缺陷:
铸件加工面允许存在加工时可以去除的缺陷,一般控制在不超过加工余量的2/3尺寸。
铸件非加工表面每棱边上的磕碰砸伤不得多于2处,并且每处面积不得大于1mmx1mm。
铸件柄部在折弯的R角处不允许有孔眼类缺陷。
5、铸件表面防护处理
铸件表面的锈蚀、粘砂、氧化皮等应通过抛丸处理干净。
对铸件有特殊防腐处理要求的,应按指定的要求(喷涂、防锈油或防锈漆)进行表面处理,表面处理后颜色应一致且符合要求。
涂层均匀表面光滑,没有磕碰、划伤、堆集和气泡等明显缺陷。
表面洁净,无污物粘连。
编制:审核:批准:。